齿轮传动效率及齿轮疲劳实验
齿轮传动的作用力及计算
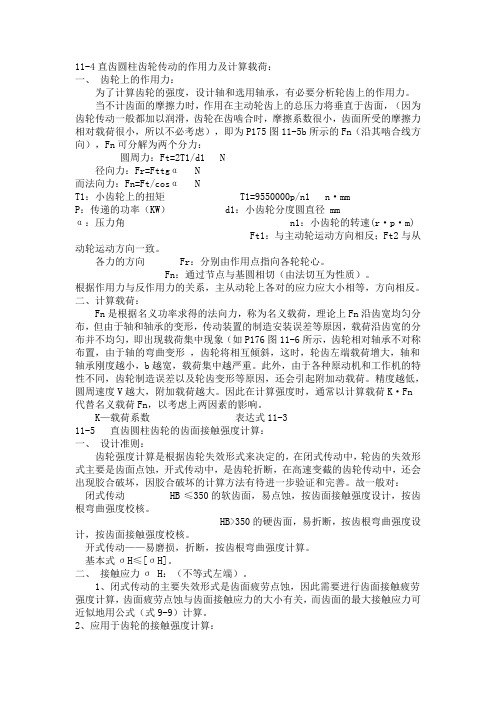
11-4直齿圆柱齿轮传动的作用力及计算载荷:一、齿轮上的作用力:为了计算齿轮的强度,设计轴和选用轴承,有必要分析轮齿上的作用力。
当不计齿面的摩擦力时,作用在主动轮齿上的总压力将垂直于齿面,(因为齿轮传动一般都加以润滑,齿轮在齿啮合时,摩擦系数很小,齿面所受的摩擦力相对载荷很小,所以不必考虑),即为P175图11-5b所示的Fn(沿其啮合线方向),Fn可分解为两个分力:圆周力:Ft=2T1/d1 N径向力:Fr=Fttgα N而法向力:Fn=Ft/cosα NT1:小齿轮上的扭矩 T1=9550000p/n1 n·mmP:传递的功率(KW) d1:小齿轮分度圆直径 mmα:压力角 n1:小齿轮的转速(r·p·m)Ft1:与主动轮运动方向相反;Ft2与从动轮运动方向一致。
各力的方向 Fr:分别由作用点指向各轮轮心。
Fn:通过节点与基圆相切(由法切互为性质)。
根据作用力与反作用力的关系,主从动轮上各对的应力应大小相等,方向相反。
二、计算载荷:Fn是根据名义功率求得的法向力,称为名义载荷,理论上Fn沿齿宽均匀分布,但由于轴和轴承的变形,传动装置的制造安装误差等原因,载荷沿齿宽的分布并不均匀,即出现载荷集中现象(如P176图11-6所示,齿轮相对轴承不对称布置,由于轴的弯曲变形,齿轮将相互倾斜,这时,轮齿左端载荷增大,轴和轴承刚度越小,b越宽,载荷集中越严重。
此外,由于各种原动机和工作机的特性不同,齿轮制造误差以及轮齿变形等原因,还会引起附加动载荷。
精度越低,圆周速度V越大,附加载荷越大。
因此在计算强度时,通常以计算载荷K·Fn代替名义载荷Fn,以考虑上两因素的影响。
K—载荷系数表达式11-311-5 直齿圆柱齿轮的齿面接触强度计算:一、设计准则:齿轮强度计算是根据齿轮失效形式来决定的,在闭式传动中,轮齿的失效形式主要是齿面点蚀,开式传动中,是齿轮折断,在高速变截的齿轮传动中,还会出现胶合破坏,因胶合破坏的计算方法有待进一步验证和完善。
齿轮传动

第四章齿轮传动基本要求:了解齿轮机构的模型及应用;了解齿廓啮合基本定律,渐开线及其性质、渐开线齿轮能保证定传动比;掌握齿轮各部分名称,渐开线标准齿轮尺寸计算;了解渐开线齿轮啮合过程;掌握渐开线齿轮正确啮合条件;了解渐开线齿轮切齿原理,根切现象及最少齿数齿轮;了解齿轮轮齿失效形式及计算准则,齿轮材料和热处理,齿轮的精度等;掌握直齿圆柱齿轮传动的受力分析、强度计算;了解斜齿圆柱齿轮机构的参数关系;了解直齿圆锥齿轮机构的齿廓曲面、背锥、当量齿数,受力分析;了解蜗杆传动的类型、应用;了解齿轮、蜗杆、蜗轮的构造。
重点:齿轮各部分名称及标准直齿圆柱齿轮的基本尺寸;渐开线齿轮的正确啮合和连续传动条件;轮齿的失效和齿轮材料;直齿圆柱齿轮传动的受力分析、强度计算。
难点: 轮齿的根切现象及最少齿数;直齿圆柱齿轮传动的受力分析、强度计算;斜齿圆柱齿轮机构的参数关系;直齿圆锥齿轮机构的齿廓曲面、当量齿数。
学时:课堂教学:10学时,实验教学:2学时。
教学方法:多媒体结合板书。
第一节 齿轮传动的类型和特点4.1.1齿轮传动的类型4.1.1.1 根据其传动比(i 12=ω1/ω2)是否恒定分1、定传动比(i 12 = 常数)传动的齿轮机构,圆形齿轮机构。
2、变传动比(i 12按一定的规律变化)传动的齿轮机构,非圆形齿轮机构。
4.1.1,2 在定传动比中两啮合齿轮的相对运动是平面运动还是空间运动分 1、平面齿轮机(圆柱齿轮传动)⎧⎧⎪⎪⎨⎪⎪⎪⎪⎩⎨⎪⎪⎪⎪⎩外啮合齿轮传动(图4-1a)直齿圆柱齿轮内啮合齿轮传动(图4-1b)齿轮与齿条传动斜齿圆柱齿轮传动(图4-1c)人字齿轮传动(图4-1d)(a) (b) (c) (d)图4-1 齿轮传动类型2、空间齿轮机构⎧⎧⎪⎪⎨⎪⎪⎪⎪⎩⎨⎪⎪⎪⎪⎩直齿圆锥齿轮传动(图4-2a)圆锥齿轮传动(伞齿轮传动)斜齿圆锥齿轮传动(图4-2b)曲齿圆锥齿轮传动(图4-2c)交错轴齿轮传动(螺旋齿轮传动)(图4-2d)蜗杆传动(图4-2e)(d) (e)图4-2 齿轮传动类型4.1.2齿轮传动的特点 1.优点:①传动比准确; ②传动效率高; ③工作可靠、寿命长; ④结构紧凑; ⑤适用范围广。
减速器试验方法
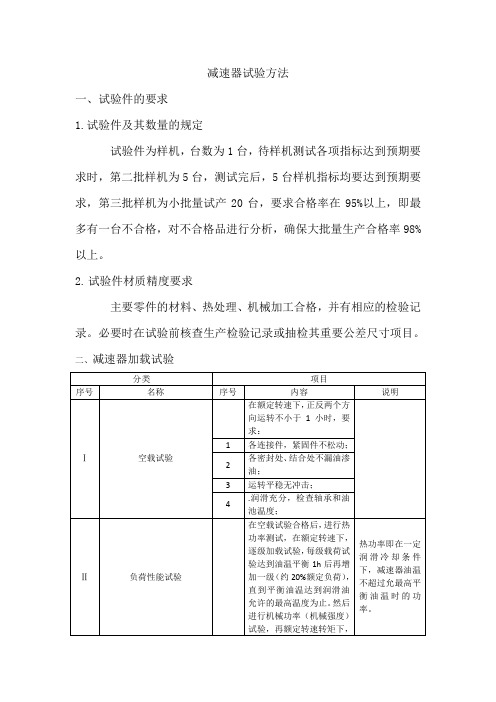
减速器试验方法一、试验件的要求1.试验件及其数量的规定试验件为样机,台数为1台,待样机测试各项指标达到预期要求时,第二批样机为5台,测试完后,5台样机指标均要达到预期要求,第三批样机为小批量试产20台,要求合格率在95%以上,即最多有一台不合格,对不合格品进行分析,确保大批量生产合格率98%以上。
2.试验件材质精度要求主要零件的材料、热处理、机械加工合格,并有相应的检验记录。
必要时在试验前核查生产检验记录或抽检其重要公差尺寸项目。
二、减速器加载试验以上允许工业应用试验代替疲劳寿命试验,但工业应用实际符合必须达到额定负荷,并有准确的日记记录,试验时间不小于3600h。
三、产品质量认证试验产品质量鉴定认证试验按表Ⅰ-Ⅲ各项目进行试验,齿面接触疲劳试验可免做。
四、产品出厂验收试验一般应进行表Ⅰ-Ⅲ各项试验,但负荷性能试验与超载试验允许按实际负荷加载,且负荷试验运转时间允许达到温度平衡为止,不许达到N≥3X106次,批量生产时允许抽样试验,抽样数不小于批量数的10%,如果抽样试验发现不合格品,应再抽试10%,仍有不合格品,应全部试验。
五、测试数据与数据处理1.数据采集试验中采集的数据包括:加载转矩、功率、转速、温度、噪音、震动、齿轮磨损、时间等。
至少没半小时应采集的数据有:输入输出转速、输入输出转矩、功率值、润滑油温度轴承温度、室温(环境温度)。
输入输出转速、输入输出转矩、功率值每次应测试5组,并记录相应的测试时间。
噪音、振动每个负荷档次、每个转速档次测定一次,并记录噪声、振动值及相应的负荷转速与时间。
齿轮磨损、点蚀、胶合、断裂及齿面接触率的变化,一般至少每日观察记录一次,试验正常无损伤、声音无异常,记录时间间隔可较长,反正齿轮出现损伤、声音异常,记录时间应较短。
轴、轴承、箱体再试验中出现异常现象损伤,其种类,润滑油牌号等也应相应记录。
六、减速器传动效率计算减速器总效率=平均输入转矩/平均输出转矩/速比x100%七、试验合格指标1.疲劳寿命试验或工业应用试验合格指标在额定载荷下疲劳寿命试验或工业应用3600h以内的减速器,其合格的指标为:a.齿轮与各部件无断裂损坏。
齿轮齿面接触疲劳特性与寿命预测
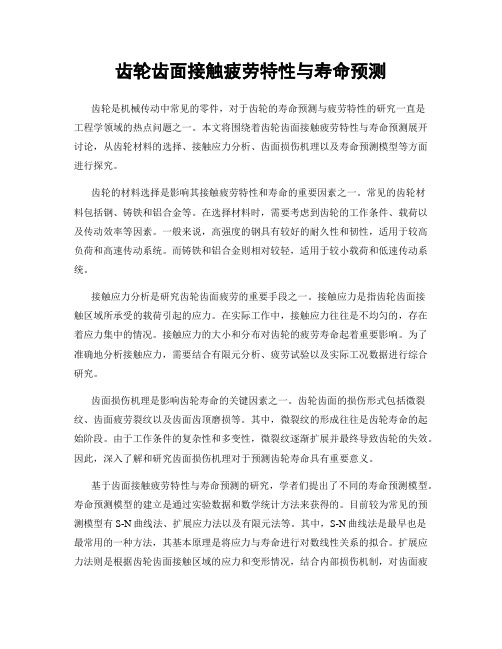
齿轮齿面接触疲劳特性与寿命预测齿轮是机械传动中常见的零件,对于齿轮的寿命预测与疲劳特性的研究一直是工程学领域的热点问题之一。
本文将围绕着齿轮齿面接触疲劳特性与寿命预测展开讨论,从齿轮材料的选择、接触应力分析、齿面损伤机理以及寿命预测模型等方面进行探究。
齿轮的材料选择是影响其接触疲劳特性和寿命的重要因素之一。
常见的齿轮材料包括钢、铸铁和铝合金等。
在选择材料时,需要考虑到齿轮的工作条件、载荷以及传动效率等因素。
一般来说,高强度的钢具有较好的耐久性和韧性,适用于较高负荷和高速传动系统。
而铸铁和铝合金则相对较轻,适用于较小载荷和低速传动系统。
接触应力分析是研究齿轮齿面疲劳的重要手段之一。
接触应力是指齿轮齿面接触区域所承受的载荷引起的应力。
在实际工作中,接触应力往往是不均匀的,存在着应力集中的情况。
接触应力的大小和分布对齿轮的疲劳寿命起着重要影响。
为了准确地分析接触应力,需要结合有限元分析、疲劳试验以及实际工况数据进行综合研究。
齿面损伤机理是影响齿轮寿命的关键因素之一。
齿轮齿面的损伤形式包括微裂纹、齿面疲劳裂纹以及齿面齿顶磨损等。
其中,微裂纹的形成往往是齿轮寿命的起始阶段。
由于工作条件的复杂性和多变性,微裂纹逐渐扩展并最终导致齿轮的失效。
因此,深入了解和研究齿面损伤机理对于预测齿轮寿命具有重要意义。
基于齿面接触疲劳特性与寿命预测的研究,学者们提出了不同的寿命预测模型。
寿命预测模型的建立是通过实验数据和数学统计方法来获得的。
目前较为常见的预测模型有S-N曲线法、扩展应力法以及有限元法等。
其中,S-N曲线法是最早也是最常用的一种方法,其基本原理是将应力与寿命进行对数线性关系的拟合。
扩展应力法则是根据齿轮齿面接触区域的应力和变形情况,结合内部损伤机制,对齿面疲劳寿命进行预测。
有限元法则通过建立齿轮的数值模型,对接触应力进行详细分析,从而得到齿面疲劳寿命的预测结果。
总之,齿轮齿面接触疲劳特性与寿命预测是机械工程领域中的重要研究方向。
传动齿轮疲劳寿命的仿真分析

劳、 点蚀和胶合 等 。其 中 , 劳破坏是 常见 的一种破坏 疲
形式 。 目前齿 轮在实 际负荷下 的疲劳 寿命分 布计算一
般可 以通过疲 劳试 验来 完成 。然 而 , 常 由 于试 验条 常
件、 时间的限制 , 使得 疲 劳试 验 难 以实 现 。因此 , 讨 探
一
种有效 的计算方 法是 十分必要 的。 圆柱齿 轮主要 有 两种 失效 形 式 , 即接 触 疲 劳失 效
和 弯 曲疲劳 失效 。弯 曲疲 劳发 生 主要 在 齿根 部 , 是 这
因为轮齿在 载荷作 用下 , 根 部所 产生 的弯 曲应 力 最 其
大 , 在齿根 过渡 圆角处 有应力 集 中。同时 , 且 齿轮在转
Absr t Ge r d v swi ey u e n t e r d ra t n ape e t lta miso y tm.Atp e e ti i e eo tac : a r e i d l s d i h a a n e n d sa rns si n s se i r s n t sd v l - p n o r ih s e d,lw os ig twa d h g p e o n ie,lg tweg ta d h g r cso ih i h n ih p e iin.T satce f c s so h h r ce si s hi ril o u e n t e c a a tr tc i
电 子 机 械 工 程
56
Elc r e t o— M e h c ania c lEng n e i i e rng
21 0 0年第 2 6卷第 6期
2 0. L 6 No 6 01 V0 2 .
传 动齿 轮疲 劳 寿命 的仿 真分 析 Βιβλιοθήκη 魏忠 良 , 陈玉振 。 岳振 兴
毕业设计齿轮传动设计
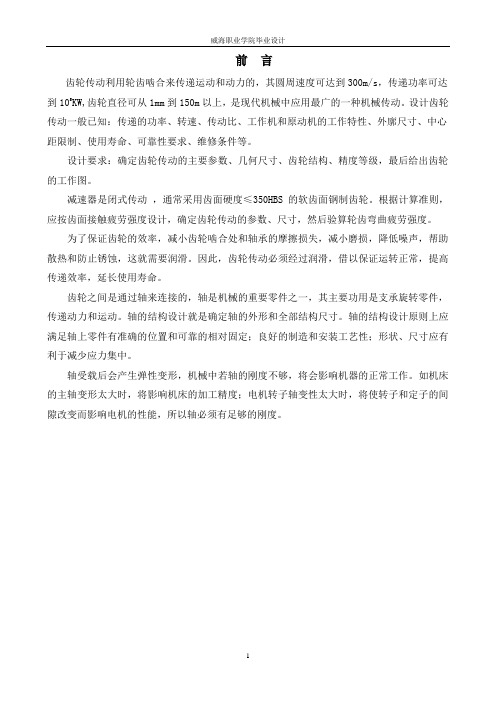
齿轮传动利用轮齿啮合来传递运动和动力的,其圆周速度可达到300m/s,传递功率可达到105KW,齿轮直径可从1mm到150m以上,是现代机械中应用最广的一种机械传动。设计齿轮传动一般已知:传递的功率、转速、传动比、工作机和原动机的工作特性、外廓尺寸、中心距限制、使用寿命、可靠性要求、维修条件等。
2、渗碳淬火:将碳的质量分数为0.15%~0.25%的低碳钢和低碳合金钢,例如20钢,20Cr等,进行渗碳淬火后,齿面硬度可达56~62HRC,齿面接触强度高,而磨性好,而齿心部仍保持较高的韧性,常用于受冲击载荷的重要齿轮传动。通常渗碳淬火后而磨齿。
3、正火:正火热处理能消除内应力、细化晶粒、改善力学性能和切削性能。机械强度要求不高的齿轮可用中碳钢正火热处理。大直径的齿轮可用铸钢正火处理。
我国已制定了齿轮强度计算的标准;GB 3480-1997“渐开线圆柱齿轮承载能力计算方法”及GB 10063-88“通用机械渐开线圆柱齿轮承载能力简化计算方法”以及GB 6413-86“渐开线圆柱齿轮胶合承载能力计算方法”及齿轮胶合承载能力计算方法”可作为齿轮传动承载能力计算依据。
三、齿轮的材料及热处理
齿宽系数φd
齿轮相对于轴承的位置
齿面硬度
软齿面(≤350HBS)
硬齿面(>350HBS)
对称布置
0.8~1.4
0.4~0.9
不对称布置
0.6~1.2
0.3~0.6
悬臂布置
0.3~0.4
0.2~0.25
标准减速器中齿轮的齿宽系数也可表示为φa=b/a,其中a为中心距。对于一般减速器可取φa=0.4。
3、模数的选择:
根据圆柱齿轮的设计方法,标准直齿圆柱齿轮传动设计计算,大致按以下步骤进行。
解决设计齿轮传动时齿面接触疲劳强度不够的问题
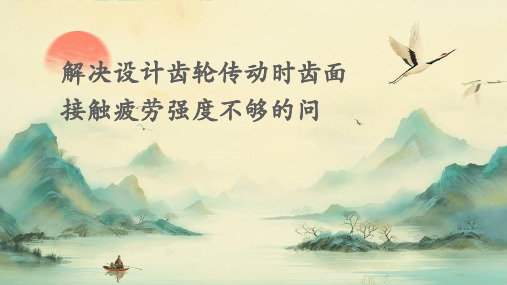
理论研究
深入研究齿面接触疲劳的机理,建立更为精确的理论模型,为设 计提供更为准确的指导。
新材料与新工艺
探索和开发具有更高强度、耐磨性和耐热性的新材料和加工工艺。
智能化设计
利用人工智能和数值模拟技术,实现齿轮传动的智能化设计和优化。
对实际应用的建议
优化设计
01
在设计阶段充分考虑齿面接触疲劳强度,通过优化几何参数和
03
解决策略与方案
材料选择与处理
选用高强度材料
选择具有高强度和耐磨性的材料, 如合金钢、不锈钢等,以提高齿 面的抗疲劳性能。
材料热处理
通过适当的热处理工艺,如淬火、 回火等,改善材料的硬度和韧性, 增强齿面的耐磨性和抗疲劳性能。
表面强化处理
采用喷丸、碾压、渗碳淬火等表面 强化处理技术,提高齿面的硬度和 抗疲劳性能。
解决设计齿轮传动时齿面 接触疲劳强度不够的问
• 问题概述 • 问题原因分析 • 解决策略与方案 • 案例分析 • 结论与建议
01
问题概述
齿面接触疲劳强度的定义
01
齿面接触疲劳强度是指齿轮在接 触应力作用下抵抗疲劳破坏的能 力。
02
齿面接触疲劳强度取决于齿轮材 料的机械性能、热处理方式、表 面处理、齿轮参数以及工作条件 等因素。
优化设计
改进齿形设计
优化齿形参数,减小应力 集中,改善齿面接触状况, 降低接触疲劳应力。
增加润滑设计
合理设计润滑系统,确保 齿轮在传动过程中得到充 分润滑,减少摩擦和磨损。
优化装配设计
确保齿轮装配精度,减小 装配误差,提高齿轮传动 的平稳性和可靠性。
制造工艺改进
精密加工
质量检测与控制
采用先进的加工设备和工艺,提高齿 轮的加工精度和表面光洁度,减小齿 轮的制造误差。
车桥英语

车桥英语1零部件名称制动鼓brake drum轮毂wheel hub桥壳housing制动蹄片brake shoes2专业术语2.1技术术语静强度分析Static Strength Analysis热耦合分析Thermal Coupling Analysis内孔径Inner hole diameter加强筋strengthening rib载荷Actual Loading制动力brake power2.2质量术语渗碳层深度Carburized layer depth表面硬度surface hardness心部硬度core hardness粗糙度Roughness合格Qualified金相组织检验结果Metallurgical Structure Test Result实测结果Inspection result材质检测结果Material Inspection Result失效件名称Failure Part失效模式Failure Mode龟裂Cracking几何尺寸检验结果Geometric dimension inspection result 2.3试验术语疲劳分析Fatigue Analysis台架试验Bench Test总成温升试验Assembly oil temperature test总成齿轮疲劳试验Assembly gear fatigue test差速器总成差速试验differential test传动效率试验transmission efficiency test垂直弯曲刚性试验Vertical bending stiffness test垂直弯曲静强度试验Vertical bending static strength test垂直弯曲疲劳试验Vertical bending fatigue test驱动桥总成静扭试验Drive axle assembly static torsion test半轴静扭试验axle shaft static torsion test制动器静制动力矩试验Brake static brake torque test试片的摩擦系数、磨损率试验Friction factor of test piece, weary rate test试样的耐腐蚀性试验Anti-corrosion test of testing sample中重型驱动桥试验台Medium and heavy duty drive axle test bench屏显式液压脉动疲劳试验机Screen displaying hydraulic pulse fatigue test machine静扭试验台Static torsion test bench定速式摩擦试验机Constant-speed friction test machine盐雾试验机Salt spray test machine全自动盐雾试验机Automatic salt spray test machine半轴扭转疲劳试验机Axle shaft torsion fatigue test machine汽车半轴和传动轴的扭转疲劳试验及转间隙Torsion fatigue test and rotating gap of axle shaft and transmission shaft静扭转刚度、强度试验Static torsion stiffness and strength test差速器总成静扭试验Differential assembly torsion test测量范围Measuring range中、后桥总成耦合疲劳试验台Coupling fatigue test bench for middle and rear axle assembly驱动桥总成耐久试验:测试齿轮组的磨损、凹痕、剥落、裂纹和断裂。
- 1、下载文档前请自行甄别文档内容的完整性,平台不提供额外的编辑、内容补充、找答案等附加服务。
- 2、"仅部分预览"的文档,不可在线预览部分如存在完整性等问题,可反馈申请退款(可完整预览的文档不适用该条件!)。
- 3、如文档侵犯您的权益,请联系客服反馈,我们会尽快为您处理(人工客服工作时间:9:00-18:30)。
齿轮传动效率及齿轮疲
劳实验
Document number:PBGCG-0857-BTDO-0089-PTT1998
齿轮传动效率及齿轮疲劳实验
(附加机械功率、效率测试实验)
一.实验目的
1. 了解封闭(闭式)齿轮实验机的结构特点和工作原理。
2. 了解齿轮疲劳实验的过程,及通过实验测定齿轮疲劳曲线的方法。
3. 在封闭齿轮实验机上测定齿轮的传动效率。
4. 介绍机械功率、效率测定开式实验台,了解一般机械功率、效率的测试
方法。
二.实验设备及工作原理
1. 封闭(闭式)传动系统
封闭齿轮实验机具有2个完全相同的齿轮箱(悬挂齿轮箱7和定轴齿轮箱
4), 每个齿轮箱内都有2个相同的齿轮相互啮合传动(齿轮9与9',齿轮5与
5'),两个实验齿轮箱之间由两根轴(一根是用于储能的弹性扭力轴6,另一根
为万向节轴10)相联,组成一个封闭的齿轮传动系统。当由电动机1驱动该
传动系统运转起来后,电动机传递给系统的功率被封闭在齿轮传动系统内,既
两对齿轮相互自相传动,此时若在动态下脱开电动机,如果不存在各种摩擦力
(这是不可能的),且不考虑搅油及其它能量损失,该齿轮传动系统将成为永
动系统;由于存在摩擦力及其它能量损耗,在系统运转起来后,为使系统连续
运转下去,由电动机继续提供系统能耗损失的能量,此时电动机输出的功率仅
为系统传动功率的20%左右。对于实验时间较长的情况,封闭式实验机是有利
于节能的。
1.悬挂电动机 2.转矩传感器 3.转速传感器 4.定轴齿轮箱 5.定轴齿轮副 6.弹性
扭力轴 7.悬挂齿轮箱 8.加载砝码 9.悬挂齿轮副 10.万向节轴 11.转速脉冲
发生器
2. 电动机的输出功率
电动机1为直流调速电机,电动机转子与定轴齿轮箱输入轴相联,电动机采
用外壳悬挂支承结构(既电机外壳可绕支承轴线转动);电动机的输出转矩等
于电动机转子与定子之间相互作用的电磁力矩,与电动机外壳(定子)相联的
转矩传感器2提供的外力矩与作用于定子的电磁力矩相平衡,故转矩传感器测
得的力矩即为电动机的输出转矩T
0
;电动机转速为n,电动机输出功率为 P
0
=n·T
0
/ 9550 (KW)。
3. 封闭系统的加载
当实验台空载时,悬挂齿轮箱的杠杆通常处于水平位置,当加上载荷W
后,对悬挂齿轮箱作用一外加力矩WL,使悬挂齿轮箱产生一定角度的翻转,
使两个齿轮箱内的两对齿轮的啮合齿面靠紧,这时在弹性扭力轴内存在一扭矩
T9(方向与外加负载力矩WL相反),在万向节轴内同样存在一扭矩T9'(方
向同样与外加力矩WL相反);若断开扭力轴和万向节轴,取悬挂齿轮箱为隔
离体,可以看出两根轴内的扭矩之和(T
9+T9
')与外加负载力矩WL平衡(即
T9+T9'=WL);又因两轴内的两个扭矩(T9和T9')为同一个封闭环形传动链
内的扭矩,故这两个扭矩相等(T
9=T9'),即2T9=WL, T9
=WL/2(Nm);由
此可以算出该封闭系统内传递的功率为:
P9=T9 n / 9550=WLn /19100 (KW)
其中:n--电动机及封闭系统的转速(rpm);
W--所加砝码的重力(N);
L--加载杠杆(力臂)的长度,L= 0.3 m。
L
W
T
9
T9'
n
4. 单对齿轮传动效率
设封闭齿轮传动系统的总传动效率为η;
封闭齿轮传动系统内传递的有用功率为P9;
封闭齿轮传动系统内的功率损耗(无用功率)等于电动机输出功率P0,即:
P0=(P9 /η)-P9
η=P9 /(P0+P9)=T9 /(T0+T9 )
若忽略轴承的效率,系统总效率η包含两级齿轮的传动效率,故单级齿轮的
传动效率为:
90
9
1
TTT
5. 封闭功率流方向
封闭系统内功率流的方向取决于由外加力矩决定的齿轮啮合齿面间作用力
的方向和由电动机转向决定的各齿轮的转向;当一个齿轮所受到的齿面作用力
与其转向相反时,该齿轮为主动齿轮,而当齿轮所受到的齿面作用力与其转向
相同时,则该齿轮为从动齿轮;功率流的方向从主动齿轮流向从动齿轮,并封
闭成环。
6.齿轮疲劳试验及疲劳曲线的求法
将两对试验齿轮分别安装在悬挂齿轮箱和定轴齿轮箱内,由加载砝码通过加
载杠杆施加一定的外载荷,在该载荷下由电动机驱动运转,直至齿轮轮齿发生
疲劳破坏,记录该载荷(应力)下所对应的运转循环次数;在不同的外载荷
下,试验得到一系列相应的循环次数,由这些试验数据即可绘制出该齿轮的疲
劳曲线。可以看出,通过试验测定齿轮的疲劳曲线,需要比较长的试验时间,
学生实验只体会实验过程。
7.机械功率、效率测定开式实验台简介
开式机械功率、效率实验台的组成如图所示。原动机(电动机)为被测机械
提供动力,制动器作为被测机械的负载。由原动机输出的动力经被测机械传递
到制动器,所传递的能量在制动器“消耗掉”(转化成其它形式的能,如热
能),形成开式传动系统。开式传动实验台的组成简便灵活,但能耗较大,适
用于被测设备类型多变,实验周期较短的情况。
为了测量被测机械所传递的功率及传动效率,将转矩转速传感器串接在被
测机械的输入轴和输出轴上,分别测出两轴上所传递的扭矩和转速,即可算出
被测机械的输入功率和输出功率,输出功率与输入功率之比即为传动效率。
由指导教师在开式实验台上演示机械传动效率的测试过程。
三.实验方法及注意事项
1. 打开电源前,应先将电动机调速旋钮逆时针轻旋到头,避免开机时电动
机突然启动。
2. 打开电源,按一下“清零键”进行清零;此时,转速显示“0”,电动机转矩
显示“· ”,说明系统处于“自动校零”状态;校零结束后,转矩显示为“0”。
3. 在保证卸掉所有加载砝码后,调整电动机调速旋钮,使电动机转速为
600 r/min。
4. 在砝码吊篮上加上第一个砝码(10N),并微调转速使其始终保持在预
定转速(600r/min)左右,在待显示稳定后(一般调速或加载后,转速和转
矩显示值跳动2-3次即可达到稳定值),按一下“保持键”,使当时的显示值
保持不变,记录该组数值;然后按一下“加载键”,第一个加载指示灯亮,并
脱离“保持”状态,表示第一点加载结束。
5. 在砝码吊篮上加上第二个砝码,重复上述操作,直至加上8个砝码,8
个加载指示灯全亮,转速及转矩显示器分别显示“8888”,表示实验结束。
6. 记录下各组数据后,应先将电机转速慢慢调速至零,然后再关闭实验台
电源。
7. 由记录数据,作出齿轮封闭传动系统的传动效率(η-T9)曲线。
四.思考题
1. 封闭式传动系统为什么能够节能
被测机械
转矩转转矩转
制动原动
2. 封闭齿轮传动如何区分主动与被动齿轮
3. 欲改变功率流方向,采用什么方法
4. 改变齿轮工作面采用什么方法
五. 实验报告
1. 记录对应外载荷下的转速n、扭矩T9,并计算出系统效率和单对齿轮的效
率
1
。
2. 绘制9T及90TT的变化曲线。
3. 回答思考题。