SRH液相循环加氢技术的开发及工业应用
加氢工艺作业考试题库-加氢生产技术与主要灾害事故预防

当两种物体接触,其间距小于25x10-8cm时,将发生电 53 子转移,并在分界面两侧出现大小相等、极性相反的
两层电荷。当两种物体迅速分离时即可能产生静电。
异常带电指在正常情况下不应当带电的生产设施或其
54 中的部分设施意外带电。异常带电容易导致人员受到
两级高速离心泵。
在加氢装置中的新鲜氢气压缩机,用以补充反应所消
33
耗的氢气。由于这种压缩机的进出口压差比较大,流 量相较小,一般都使用往复式压缩机。
在加氢装置中的循环氢压缩机,其作用是将循环氢气
34
压缩,再送回反应器系统中,以维持反应器氢分压。 相对来说其流量较大,压差较小,一般都使用离心式
压缩机。
90 气,而且反应器内操作压力高、温度高,在发生泄漏
或超温超压时,有火灾爆炸的危险性。
91
加氢装置的高压分离器,是反应物汽液分离设备,但 不是反应系统的压力控制点。
加氢装置的高压分离器,液位过高会造成循环氢带液
92
损坏循环机,液位过低会导致高压系统窜入低压系统 。因此其玻璃液位计压力表调节阀等,任何一个失误
不大于10℃为宜。
提高压力有利于加氢反应的进行。氢分压增加可提高
4 加氢脱硫、脱氮过程的反应深度,提高反应压力有利
于延缓催化剂表面积炭速度,延长催化剂使用寿命。
对于加氢装置,进料量增加时,空速增大,原料油在
5 催化剂上的停留时间短,反应深度浅,反之反应深度
深。
对于加氢装置增加氢油比可以少量地增加脱硫率,降
护作用。
以晶体管逻辑元件组成的触点式电路具有稳定可靠、
43 功能完善、维修方便等优良性能,目前已在广泛应用
催化重整高氮原料预加氢技术的开发及工业应用
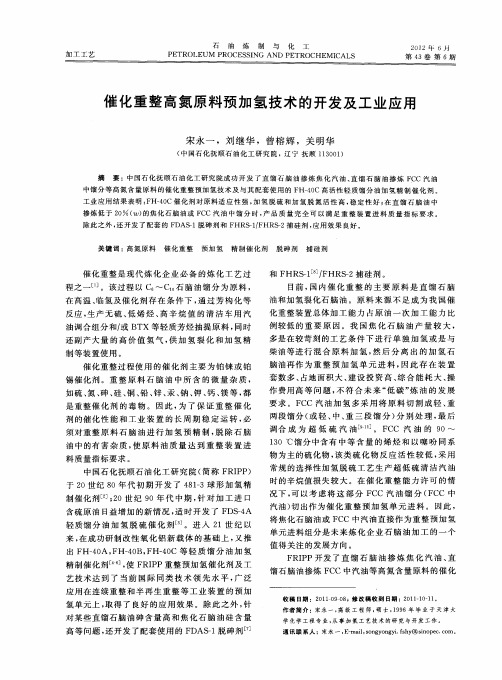
如硫 、 、 、 、 、 、 、 、 、 、 、 等 , 氮 砷 硅 铜 铅 锌 汞 钠 钾 钙 镁 都 是重 整催 化 剂 的毒 物 。因 此 , 了保 证 重 整催 化 为
剂 的催化 性 能 和 工 业 装 置 的长 周 期 稳 定 运 转 , 必 须对 重整 原 料 石 脑 油 进 行 加 氢 预 精 制 , 除 石 脑 脱
脑 油再作 为 重 整 预 加 氢 单 元 进 料 , 此 存 在 装 置 因 套数 多 、 占地 面积大 、 设 投 资 高 、 合 能耗 大 、 建 综 操 作 费用高 等 问题 , 符 合 未 来 “ 碳 ” 油 的发 展 不 低 炼 要 求 。F C汽 油 加 氢 多采 用 将 原 料 切 割 成 轻 、 C 重 两段 馏分 ( 轻 、 、 三段 馏 分 ) 别 处 理 , 后 或 中 重 分 最 调合 成 为 超 低 硫 汽 油[ 。 F C 汽 油 的 9 9 。 C 0~ 10℃馏分 中含 有 中等 含 量 的烯 烃 和 以 噻 吩 同 系 3 物 为主 的硫化 物 , 类 硫 化物 反 应 活 性 较 低 , 该 采用 常规 的选 择性 加氢 脱 硫 工艺 生 产 超低 硫 清 洁 汽 油 时的辛烷 值损 失较 大 。在 催 化 重 整 能力 许 可 的情 况 下 , 以 考 虑 将 这 部 分 F C汽 油 馏 分 ( C 中 可 C F C 汽油) 出作 为催 化 重 整 预加 氢 单 元 进料 。 因此 , 切 将焦化 石脑 油或 F C 中汽 油直接 作 为重整 预加 氢 C 单元进 料组 分是 未来 炼 化企 业 石 脑 油 加工 的一 个 值得关 注 的发展方 向。 F I P开发 了直 馏 石 脑 油 掺 炼 焦 化 汽 油 、 RP 直
含 硫 原 油 日益 增 加 的 情 况 , 时 开 发 了 F S4 适 D 一A
器外真硫化态加氢催化剂在柴油液相加氢装置上的首次工业应用

器外真硫化态加氢催化剂在柴油液相加氢装置上的首次工业应用马成功;董晓猛【摘要】中国石化安庆分公司2.2 Mt/a柴油液相加氢装置于2018年5月进行催化剂更换,更换为中国石化石油化工科学研究院开发的真硫化态催化剂组合RG-1 (TS)/RS-2100 (TS)/RS-2200 (TS),成为国内首套采用器外真硫化态加氢催化剂的加氢装置.通过对催化剂装填和开工过程进行总结,从安全环保、开工时间、开工成本等方面对采用真硫化态催化剂和氧化态催化剂的开工过程进行对比.结果表明:采用真硫化态催化剂开工,开工时间缩短约5天,开工过程无废水、废气排放,节约开工费用300多万元,开工过程简单、环保,产品质量满足国V柴油标准的要求.【期刊名称】《石油炼制与化工》【年(卷),期】2019(050)006【总页数】5页(P46-50)【关键词】器外真硫化;加氢催化剂;国V标准柴油;安全环保【作者】马成功;董晓猛【作者单位】中国石化安庆分公司,安徽安庆246000;中国石化安庆分公司,安徽安庆246000【正文语种】中文近年来,环保法规对车用汽柴油中杂质含量的要求越来越严格,脱除其中杂质最有效的方法是采用加氢处理将油品中的硫、氮、氧等杂质脱除。
因此,加氢处理装置在炼油厂中所占的比重越来越高。
各类加氢相关的新催化剂、新工艺、新技术、新设备层出不穷,为车用汽柴油质量升级提供了重要支持[1-3]。
中国石化安庆分公司(安庆分公司)为生产国Ⅴ标准柴油,于2013年10月建成一套2.2 Mt/a柴油加氢装置。
为降低运行过程中的能耗,装置采用由中国石化工程建设公司(SEI)和中国石化石油化工科学研究院(石科院)共同开发的连续液相柴油加氢技术。
装置于2013年采用氧化态催化剂一次开工成功,主要以生产国Ⅳ标准柴油产品为主。
2016年对该装置进行了国Ⅴ质量升级改造,在原有反应器(一反)后面新增1台反应器(二反),二反顶部设置有热高压分离器,并采用上流式低氢油比滴流床工艺设计[4-5]。
生产超低硫柴油S-RASSG技术新进展及工业应用

生产超低硫柴油S-RASSG技术新进展及工业应用宋永一;方向晨;郭蓉;刘继华【摘要】To meet the requirement for the production of Euro-Ⅳ and Euro-V clean diesel for refineries, Fushun research institute of petroleum & petrochemicals (FRIPP) has developed FHUDS series catalysts with W-Mo-Ni (Mo-Ni) or Mo-Co as active metals, which have a strong adaptability to different feedstocks. Based on different operating conditions and reaction characteristics of different catalyst beds in running cycle and in consideration of ultra desulfurization mechanisms of different types of catalysts, S-RASSG diesel ultra deep desulfurization technology with different catalyst stack loading has been developed by FRIPP. The commercial application results show that: when S-RASSG catalyst stack technology and its associated FHUDS-2/FHUDS-5 and FHUDS-6/FHUDS-5 catalysts are applied, the high sulfur feed blended with 60% SRGO and 40% LCO, coker diesel or vacuum tower diesel can be processed to stably produce product diesel with sulfur lower than 50×10-6 which meets Guo-Ⅳstandard specifications at reactor inlet pressure of 8.0 MPa, main catalyst LHSV of 1.85~2.25 h-1, and WABT of 350 ℃, etc. The product diesel with less than 10×10-6 sulfur, which meets Euro-Ⅴ standard ,can be produced with feed blended with 70%SRGO, 30%vacuum tower diesel and a small quantity of coker diesel under the conditions of reactor inlet pressure of8.0 MPa, main catalyst LHSV of 1.85 h-1,WABT of 350 ℃, etc. S-RASSG catalyst stack technology has provided a strong technology support forproduction of Euro-Ⅳ and Euro-Ⅴdiesels for refineries..%为满足炼油企业生产国Ⅳ及欧Ⅴ标准清洁柴油的需要,抚顺石油化工研究院(FRIPP)开发了适合不同原料、分别以W-Mo-Ni(Mo-Ni)及Mo-Co为活性金属的FHUDS系列催化剂,并根据加氢反应器内催化剂床层不同的工况条件和反应特点,结合不同类型催化剂的脱硫反应机理,开发了生产超低硫柴油的 S-RASSG 催化剂级配技术.工业应用结果表明:采用 S-RASSG 技术及配套的 FHUDS-2/FHUDS-5以及新一代FHUDS-6/FHUDS-5催化剂体系,加工常压柴油掺兑质量分数40%左右催化柴油及焦化汽柴油或减压柴油的高硫混合油,在反应器入口压力8.0 MPa,主催化剂体积空速1.85~2.25 h-1、平均反应温度350℃左右等条件下,可以长周期稳定生产硫质量分数小于50μg/g、满足国Ⅳ标准的低硫柴油;加工常压柴油掺兑质量分数30%左右减压柴油及少量焦化柴油的混合油,在反应器入口压力8.0 MPa,主催化剂体积空速1.85 h-1、平均反应温度350℃左右等条件下,可以稳定生产硫质量分数小于10μg/g、满足欧Ⅴ标准的超低硫柴油.S-RASSG催化剂级配技术为炼油企业生产满足国Ⅳ和欧Ⅴ标准的超低硫柴油提供了有力的技术支撑.【期刊名称】《当代化工》【年(卷),期】2013(000)002【总页数】4页(P208-211)【关键词】催化剂级配;清洁柴油;催化剂;加氢精制;加氢脱硫【作者】宋永一;方向晨;郭蓉;刘继华【作者单位】中国石化抚顺石油化工研究院,辽宁抚顺 113001;中国石化抚顺石油化工研究院,辽宁抚顺 113001;中国石化抚顺石油化工研究院,辽宁抚顺113001;中国石化抚顺石油化工研究院,辽宁抚顺 113001【正文语种】中文【中图分类】TE624随着国民经济的快速发展,市场对石油化工产品需求量不断增加,使得我国进口含硫原油加工量呈逐年上升的趋势。
加氢工艺技术
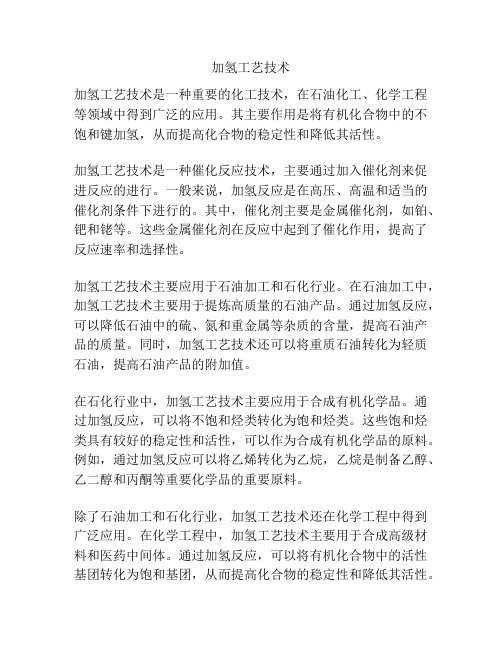
加氢工艺技术加氢工艺技术是一种重要的化工技术,在石油化工、化学工程等领域中得到广泛的应用。
其主要作用是将有机化合物中的不饱和键加氢,从而提高化合物的稳定性和降低其活性。
加氢工艺技术是一种催化反应技术,主要通过加入催化剂来促进反应的进行。
一般来说,加氢反应是在高压、高温和适当的催化剂条件下进行的。
其中,催化剂主要是金属催化剂,如铂、钯和铑等。
这些金属催化剂在反应中起到了催化作用,提高了反应速率和选择性。
加氢工艺技术主要应用于石油加工和石化行业。
在石油加工中,加氢工艺技术主要用于提炼高质量的石油产品。
通过加氢反应,可以降低石油中的硫、氮和重金属等杂质的含量,提高石油产品的质量。
同时,加氢工艺技术还可以将重质石油转化为轻质石油,提高石油产品的附加值。
在石化行业中,加氢工艺技术主要应用于合成有机化学品。
通过加氢反应,可以将不饱和烃类转化为饱和烃类。
这些饱和烃类具有较好的稳定性和活性,可以作为合成有机化学品的原料。
例如,通过加氢反应可以将乙烯转化为乙烷,乙烷是制备乙醇、乙二醇和丙酮等重要化学品的重要原料。
除了石油加工和石化行业,加氢工艺技术还在化学工程中得到广泛应用。
在化学工程中,加氢工艺技术主要用于合成高级材料和医药中间体。
通过加氢反应,可以将有机化合物中的活性基团转化为饱和基团,从而提高化合物的稳定性和降低其活性。
这对于有机合成和药物研发具有重要的意义。
加氢工艺技术具有很高的技术含量和经济效益。
通过加氢反应可以提高石油产品的质量、降低污染物的含量,同时还可以提高合成有机化学品的产率和选择性。
因此,加氢工艺技术在石化和化工行业中具有广阔的应用前景。
总之,加氢工艺技术是一种重要的化工技术,主要应用于石油加工和化学工程中。
通过加氢反应,可以提高石油产品的质量,降低有机化合物的活性,从而提高化合物的稳定性和降低其附加值。
加氢工艺技术具有很高的技术含量和经济效益,在石化和化工领域中具有广阔的应用前景。
C4选择加氢催化剂SHB-01的工业应用

C4选择加氢催化剂SHB-01的工业应用皇甫协立;李世伟;赵多【摘要】中国石化上海石油化工研究院开发的C4选择加氢催化剂SHB-01在上海石油化工股份有限公司1号MTBE装置上成功进行工业应用.结果表明,反应过程的1-丁烯收率高,加氢产品中剩余丁二烯的量少,催化剂SHB-01具有初期活性高、选择性好、操作弹性大等特性.装置运行期间,催化剂表现出较好的稳定性,1-丁烯收率大于95.2%,加氢产品指标优异,剩余丁二烯质量分数小于10 μg/g,可满足聚合级1-丁烯产品的要求,是一种理想的C4选择加氢除丁二烯催化剂.【期刊名称】《石油炼制与化工》【年(卷),期】2018(049)008【总页数】4页(P28-31)【关键词】C4;选择性加氢;丁二烯;催化剂【作者】皇甫协立;李世伟;赵多【作者单位】中国石化上海石油化工股份有限公司,上海200540;中国石化上海石油化工股份有限公司,上海200540;中国石化上海石油化工研究院【正文语种】中文我国C4总量随着炼油、乙烯产能和MTO工艺的发展而增长[1-2]。
2015年全国原油加工量为478 Mt,炼油厂副产C4约6.0 Mt;乙烯产量16.23 Mt,副产C4约4.05 Mt(按产量比1∶4 计算)[3];新型煤化工甲醇制烯烃装置(已投产4 套),副产C4约0.2 Mt,C4资源总量已超过10 Mt。
此外,据不完全统计,我国将在3年内开工建设(含已投产和正在试车)的煤制烯烃项目有20多个,各地规划的煤制烯烃总产能已超过20 Mta,副产C4资源也将有较大增量。
FCC、MTO及抽余或醚后C4除含有正丁烯等主要组分外,还含有少量的双烯及炔烃,这些易聚物会导致正丁烯反应(烯烃聚合烯烃裂解烷基化)的催化剂快速失活,影响装置稳定运行[4-7]。
例如1-丁烯聚合工艺中,微量丁二烯的存在可减少聚合催化剂使用寿命并降低产品质量[8]。
增加选择加氢单元脱除C4中易聚合组分,同时根据产品需要调整原料中1-丁烯和2-丁烯的比例,是工业上普遍采用的一条经济环保路线[9]。
加氢处理工艺与工程

加氢处理工艺与工程1.引言近年来,全球化进程加速,能源需求不断增加,化石燃料的使用已经成为世界各国共同的选择。
然而,化石燃料的使用不仅会造成地球环境的污染,而且能源的来源有限,对环境与经济造成的影响日益加剧。
因此,为了减轻环境和能源压力,开发高效环保的加氢处理工艺变得尤为重要。
2.加氢处理的定义和意义加氢处理是一种利用氢气或氢化物进行物质转化的重要工艺。
它广泛地应用于多种化学工业,比如石油化工、制药、食品等。
加氢处理的主要目的是将原料中的不饱和化合物(如烯烃或芳香烃)转化为饱和化合物(如烷烃),减少有害物质的排放,同时提高产物的化学稳定性和品质,减少生产过程中的能源消耗。
3.加氢处理的基本原理加氢处理的基本原理是将原料经过一定的气体或液体流动摆动控制后,与氢气在一定的温度、压力和催化剂作用下进行反应,生成目标产物。
反应主要的化学反应方程式为:CnH2n+2+H2→CnH2n+4此化学反应式具有饱和度高、反应量大、催化作用强等特点,使得加氢处理的效率大大提高,反应产物也更加高质量。
4.加氢处理中的催化技术催化剂是促进加氢反应的高效关键因素。
在加氢处理的催化过程中,一般采取纯金属、合金、氧化物和非晶体等催化剂进行反应。
其中,铂族元素常用于高价钢结构(如铂、钯催化剂),铬族、铁族和钍系元素常用于低价钢(如钼、镍、铁催化剂)中。
此外,不同催化剂的特定配比和不同的物理-化学结构也将影响加氢反应的效果,进而影响反应的产物性质。
5.加氢处理在石油加工中的应用石油加工是目前加氢处理的最大工业应用领域之一。
其中,焦化气、原油加工和催化裂化产生的液体原料是石油加工中最重要的原料之一。
通过石油加工中的加氢反应,可以将其化学性质进行调节,从而使其在市场中获得更好的销售效果。
催化裂化、加氢精制和加氢脱硫等工艺的应用,大大改善了石油加工的产业质量和资源利用效率。
6.加氢处理的未来发展随着全球环境问题的不断加剧,加氢处理技术也将面临更新、优化的挑战。
煤直接液化油加氢提质RCHU技术的工业应用
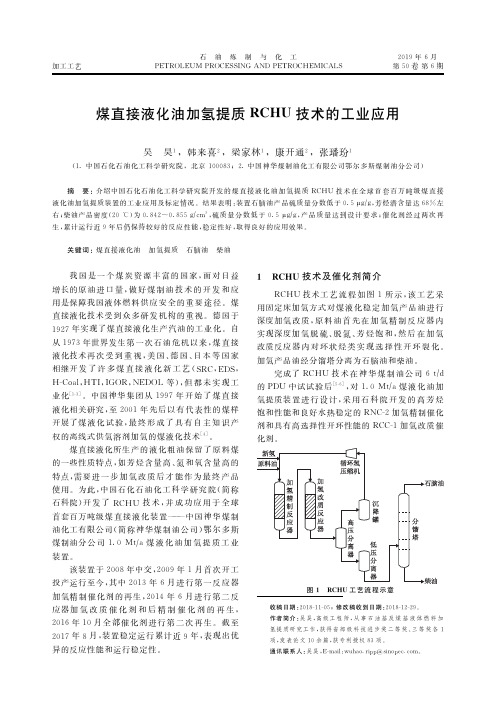
8
石 油 炼 制 与 化 工 2019年 第50卷
2 第 一 周 期 反 应 性 能
2010年6月21—24日进行了装置第一周期运行 标定。标定期间加工煤液化柴油馏分8664t,加工煤 液化石脑油馏分1473t,合计10137t(140.8t?h),实 际加工负荷为105%(设计加工能力134.375t?h)。
关 键 词 :煤 直 接 液 化 油 加 氢 提 质 石 脑 油 柴 油
我 国 是 一 个 煤 炭 资 源 丰 富 的 国 家,面 对 日 益 增长的原 油 进 口 量,做 好 煤 制 油 技 术 的 开 发 和 应 用是保障我国液体燃料供应安全的重要途径。煤 直接液化技术受到众多研发机构的重视。德国于 1927年实现了煤直接液化 生 产汽 油的工 业 化。 自 从1973年世界发生 第 一 次 石 油 危 机 以 来,煤 直 接 液化技术再 次 受 到 重 视,美 国、德 国、日 本 等 国 家 相继开 发 了 许 多 煤 直 接 液 化 新 工 艺 (SRC,EDS, HCoal,HTI,IGOR,NEDOL 等 ),但 都 未 实 现 工 业化 。 [13] 中国神 华 集 团 从 1997 年 开 始 了 煤 直 接 液化相关研究,至 2001 年 先 后 以 有 代 表 性 的 煤 样 开展了煤 液 化 试 验,最 终 形 成 了 具 有 自 主 知 识 产 权的离线式供氢溶剂加氢的煤液化技术 。 运行至今,其中 2013 年 6 月 进 行 第 一 反 应 器 加氢精 制 催 化 剂 的 再 生,2014 年 6 月 进 行 第 二 反 应器加 氢 改 质 催 化 剂 和 后 精 制 催 化 剂 的 再 生, 2016年10月 全 部 催 化 剂 进 行 第 二 次 再 生。 截 至 2017年8月,装置稳定运行累 计近 9 年,表 现 出 优 异的反应性能和运行稳定性。
- 1、下载文档前请自行甄别文档内容的完整性,平台不提供额外的编辑、内容补充、找答案等附加服务。
- 2、"仅部分预览"的文档,不可在线预览部分如存在完整性等问题,可反馈申请退款(可完整预览的文档不适用该条件!)。
- 3、如文档侵犯您的权益,请联系客服反馈,我们会尽快为您处理(人工客服工作时间:9:00-18:30)。
SRH液相循环加氢技术的开发及工业应用摘要:抚顺石油化工研究院(FRIPP)近期开发的SRH液相循环加氢技术是利用油品的溶解氢进行加氢反应,高压设备少,热量损失小,投资费用和操作费用均低,是低成本实现油品升级很好的技术。
该技术于2009年10月进行工业化试验,取得良好试验结果。
工业试验结果证明,SRH液相循环加氢技术成熟可靠,设备运行稳定,在装置建设投资和操作费用方面具有明显竞争优势,可以在适宜工艺条件下加工处理各种柴油原料,能够满足低成本柴油产品质量升级的需要。
关键词:清洁柴油液相加氢工业应用前言环保法规日益严格,柴油的硫含量标准在逐年修订,发展和使用超低硫甚至无硫柴油是当今世界范围内清洁燃料发展的趋势。
欧盟法规规定2005年欧洲车用柴油执行欧洲Ⅳ类柴油标准,限制柴油中的硫含量在50μg/g以下,2009年欧盟法规限制车用柴油的硫含量在10μg/g以下。
美国在2006年限制车用柴油的硫含量在15μg/g以下。
我国轻柴油规格标准GB252-2000对柴油硫含量的要求是不大于2000μg/g,城市车用柴油国家标准GB/T19147-2003参照欧洲Ⅱ类标准制定,其硫含量要求小于500μg/g,2011年7月1日将执行的城市车用柴油国家标准GB/T19147-2009规定硫含量小于350μg/g。
北京、上海等城市已率先执行参照欧Ⅳ制定的京标C、沪4标准,即要求硫含量小于50μg/g。
为应对新排放标准柴油的生产,开发装置投资低、操作费用低的柴油深度加氢技术非常必要。
目前,柴油深度加氢精制主要采用氢气循环的单段工艺技术和两段工艺技术。
单段工艺非常普遍,采用传统的加氢脱硫催化剂通过增加反应苛刻度如提高反应温度、氢分压或是降低反应空速等,实现柴油的深度脱硫甚至超深度脱硫,但由于在较高反应温度下操作时,会导致产品颜色变差和催化剂寿命缩短,而降低空速则意味着处理量的减少等,所以单段工艺生产低硫柴油甚至超低硫柴油,经济上不一定合适。
采用两段法加氢技术生产低硫低芳烃柴油在现阶段仍具有很大吸引力,但是两段法投资大,操作复杂,目前工业装置不是很多。
1 SRH液相循环加氢技术在常规的固定床加氢工艺过程中,为了控制催化剂床层的反应温度和避免催化剂积炭失活,通常采用较大的氢油体积比,在加氢反应完成后必然有大量的氢气富余。
这些富余的氢气通常经循环氢压缩机增压并与新氢混合后继续作为反应的氢气进料。
该工艺循环氢压缩机的投资占整个加氢装置成本的比例较高,氢气换热系统能耗较大。
如果能够将加氢处理过程中的氢气流量减小并省去氢气循环系统和循环氢压缩机,则可以为企业节省装置建设投资,并降低清洁燃料生产成本。
为此,FRIPP近期开发了SRH液相循环加氢技术。
该技术反应部分不设置氢气循环系统,依靠液相产品大量循环时携带进反应系统的溶解氢来提供新鲜原料进行加氢反应所需要的氢气,反应器采用与滴流床反应器相近结构反应器。
SRH液相循环加氢技术的优点是可以消除催化剂的润湿因子影响。
由于循环油的比热容大,从而大大降低反应器的温升,提高催化剂的利用效率,并可降低裂化等副反应。
装置高压设备少,热量损失小,投资费用和操作费用均低,是低成本实现油品质量升级的较好技术。
2 SRH液相循环加氢技术特点2.1 SRH液相循环加氢技术具有良好的气液分散性在化学反应过程中,催化剂的浸润程度越高、催化剂的润湿因子越高,催化剂的有效利用率越高。
SRH液相循环加氢的氢气溶解在原料油里,而原料油又浸泡整个催化剂床层,这样不需要额外工艺设备来确保氢气与油混合,液相在催化剂上获得良好分散,也不需要提供一个良好的传质环境,反应器内构件简单。
2.2 SRH液相循环加氢技术大大稀释原料中的杂质浓度有机氮化物是加氢催化剂的毒物,对加氢脱氮、加氢脱硫和加氢脱芳反应有明显的抑制作用。
这种抑制作用主要是由于有些氮化物和大多数氮化物的中间反应产物与催化剂的加氢反应活性中心具有非常强的吸附能力,从竞争吸附角度抑制了其他加氢反应的进行。
而通过加氢产物循环将大大稀释原料中的杂质浓度,有利于发挥催化剂的性能。
2.3 SRH液相循环加氢技术催化剂利用率高由于油品热容较大,采用液相循环油加氢可大幅度降低反应器催化剂床层温升,使反应器在更接近于等温的条件下操作,反应器的操作温度与等温条件越接近,催化剂的寿命就越长。
2.4 SRH液相循环加氢技术反应效果明显用加氢难度很大的镇海混合柴油原料,进行了SRH液相循环加氢与常规气相循环加氢对比试验。
对比试验结果见表1。
工艺条件气相循环液相循环气相循环液相循环液相循环反应压力/MPa 5.5 5.5 5.5 5.5 5.5反应温度/℃375 360 365 360 365体积空速/h-10.8 3.2 1.6 3.2 2.0循环比- 3:1 - 3:1 3:1氢油体积比350 - 350 - -油品性质原料油精制油精制油精制油精制油精制油密度(20 ℃)/( g.cm-3) 0.8557 0.8352 0.8430 0.8350 0.8430 0.8349 馏程范围/℃ 168/374 163/371 168/370 163/369 168/370 163/367 硫/(μg.g-1) 11700 13 1008 9 1008 8氮/(μg.g-1) 1026 18 386 9 386 9十六烷指数49.4 56.2 54.6 56.9 54.6 57.0由表1对比试验结果可见,处理难度非常大的镇海混合柴油时,采用组合工艺(即在常规加氢装置上增设SRH液相循环加氢单元),在总体积空速1.1 h-1条件下可以生产硫含量小于10 μg/g的精制柴油。
采用2 次混氢的SRH液相循环加氢工艺,在总体积空速1.2 h-1条件下就可以生产硫含量小于10 μg/g的精制柴油。
采用原来工艺流程,将体积空速降至0.8 h-1,反应温度提高至375 ℃,精制柴油硫含量才为13 μg/g,也没有达到小于10 μg/g。
SRH液相循环加氢技术具有良好反应效果,在较高空速下即可实现深度加氢精制目的。
2.5 SRH液相循环加氢工艺对复杂结构硫的脱除率较高在反应压力5.5 MPa、反应温度360 ℃、体积空速3.2 h-1、循环比2:1条件下,进行了1 次混氢的SRH液相循环加氢精制试验,考察SRH液相循环加氢技术对复杂结构硫的脱除效果,见表2。
表2 原料油和SRH精制柴油硫结构分析结果名称原料油SRH精制柴油非噻吩类硫117.3 0噻吩硫及烷基噻吩硫0.6 0苯并噻吩及烷基苯并噻吩硫 2 604.3 233.0二苯并噻吩及烷基二苯并噻吩硫 1 543.4 481.7总硫 4 265.6 714.7苯并噻吩类硫脱除率,% 91.1二苯并噻吩类硫脱除率,% 68.8 由表2可见:原料油经过SRH液相循环加氢反应后,苯并噻吩类硫脱除率91.1%,二苯并噻吩类硫脱除率68.8%。
说明SRH液相循环加氢工艺对难脱除的硫化物的脱除率较高。
3 SRH液相循环加氢技术主要试验结果3.1 SRH液相循环加氢技术处理航煤试验结果在1 次混氢的SRH液相循环加氢中试装置上,进行了镇海常一线油加氢试验。
由于航煤加氢目的是脱除硫醇硫,装置氢耗很低,新鲜进料中溶解氢气即可满足要求,因此装置采用生成油1 次通过流程,生成油不循环的操作模式。
原料油和试验结果见表3。
表3 镇海常一线高空速SRH加氢试验结果项目数值工艺条件条件1 条件2反应压力/MPa 1.8 1.8反应温度/℃220 230体积空速/h-1 6.6 8.0油品性质常一线油精制油精制油密度(20 ℃)/( g.cm-3) 0.7886 0.7881 0.7885馏程范围/℃146~233 142~232 145~232硫/(μg.g-1) 1 258 1 088 1 095博士试验通过通过硫醇硫/(μg.g-1) 99.7 6.5 9.7常一线油加氢试验结果表明,在体积空速6.6 h-1和8.0 h-1工艺条件下,航煤硫醇硫由99.7 μg/g 分别降到6.5 μg/g和9.7 μg/g,博士试验通过,实际胶质为1 mg/100 mL,说明常一线油在高空速下加氢效果较好。
如果将生成油进行部分循环加氢,溶解氢气量增加,反应效果会更好。
所以,SRH液相循环加氢技术处理航煤原料油时,产品完全满足生产3#喷气燃料产品质量的需要。
3.2 SRH液相循环加氢技术处理镇海常二线柴油试验结果在1 次混氢的SRH液相循环加氢中试装置上,对镇海常二线进行循环加氢试验。
采用生成油部分循环操作。
试验结果见表4。
表4 镇海常二线柴油SRH液相循环加氢试验结果项目数值工艺条件条件3 条件4反应压力/MPa 6.4 6.4反应温度/℃350 350体积空速/h-1 3.0 4.5循环比1:1 1:1生成油性质原料油生成油生成油密度(20 ℃)/( g⋅cm-3) 0.8225 0.8132 0.8122S/(μg⋅g-1) 3469 5 10.0N/(μg⋅g-1) 24 1.0 1.0脱硫率,% 99.7 99.4 常二线柴油加氢试验结果表明,在循环比(循环油:新鲜进料)1:1条件下,即使新鲜进料体积空速高达到4.5 h-1,SRH液相循环加氢技术可以直接得到硫含量小于10 μg/g的低硫柴油。
3.3 SRH液相循环加氢技术处理镇海混合原料的试验结果原料油取自镇海炼化分公司,原料油组成为焦化柴油:常二直馏柴油:常三直馏柴油=50%:25%:25%,油品性质见表5。
由表5可见,镇海混合柴油的硫含量为11 700 μg/g,实际胶质为824 mg/100 mL,十六烷指数为49.44,终馏点为374 ℃,原料油性质很差。
主要是焦化柴油及常三线柴油馏分较重,50%点分别为309 ℃、316 ℃;95%点分别为373 ℃、365 ℃;密度分别为0.8761 g/cm3、0.8556 g/cm3,所以该混合油加氢难度相当大。
表5 镇海混合柴油性质原料名称常二柴油常三柴油焦化柴油混合柴油密度(20 ℃)/( g.cm-3)0.8225 0.8556 0.8761 0.8557馏程/℃初馏点/10% 168/214 205/278 152/260 168/24330%/50% 236/247 302/316 287/309 274/29770%/90% 259/273 330/354 332/360 323/35795%/终馏点281/294 365/374 373/375 373/374硫/(μg.g-1) 3 469 8 300 14 000 11 700氮/(μg.g-1) 24 318 1 833 1 026实际胶质/(mg.(100 mL)-1) 159 1 472 824十六烷指数50.5 51.6 45.0 49.4由于镇海混合原料性质较差,生产硫含量小于10 μg/g柴油时,反应氢耗较大,因此宜采用2次混氢的SRH液相循环加氢工艺。