高速铣削铝合金时切削力和表面质量影响因素的试验研究
高速铣削系统动态测试及切削力分析

高速铣削系统动态测试及切削力分析高速铣削系统是一种高效、精度高、操作简单的加工方式,在各种工件的加工过程中得到了广泛应用。
对于高速铣削系统的性能测试,主要分为静态测试和动态测试两种方式。
其中,动态测试是一种更加全面、准确的测试方式,可以对系统在实际切削过程中的性能进行评估。
同时,对于高速铣削系统的切削力分析,也是一种评估系统性能和优化工艺的重要手段。
一、高速铣削系统动态测试高速铣削系统的动态测试主要是指在实际切削过程中对系统性能进行评估。
这种测试方式可以反映系统的动态响应能力、切削稳定性、切削效率等方面的性能。
1.测试方法动态测试通常会选择一些标准化的加工工件,模拟实际加工过程,通过对加工过程中的各项数据进行采集和分析,对系统整体性能进行评估。
主要测试指标包括功率、转速、进给、切削深度、切削轮廓精度等方面的参数。
2.测试结果分析通过对测试数据的分析,可以得出以下结果:1)系统的功率和转速对切削稳定性有着重要的影响。
在适当的功率和转速范围内,系统的稳定性和加工效率都能得到最大化的提升。
2)切削深度和进给速度对切削效率的影响比较显著。
合理的切削深度和进给速度可以提高系统的加工效率和加工精度。
3)切削轮廓精度的提升是系统性能优化的重要手段之一。
通过适当的刀具选择、加工参数设置和工艺优化,可以提高系统的加工精度和一致性。
二、高速铣削系统切削力分析高速铣削系统的切削力分析可以为系统的性能评估和工艺优化提供重要参考。
切削力的大小和方向会直接影响系统的稳定性、切削效率和工件表面质量等方面。
1.切削力的来源切削力主要分为三个来源:1)弹性变形力:即由于被加工材料的弹性变形所产生的力,主要来自于材料的弹性模量、剪切模量等参数。
2)切削力:即由于刀具对材料切削所产生的力,与刀具刃口的形状、角度、材料等有关。
3)摩擦力:即由于切削面和加工物体表面之间的摩擦力所产生的力,主要受到机床和工件表面质量的影响。
2.切削力的分析方法切削力的分析方法主要有两种:1)理论计算法:通过对切削过程中各种力学参数的计算,得出切削力大小和方向的数值。
铝锂合金高速铣削表面粗糙度试验研究

铝锂合金高速铣削表面粗糙度试验研究丁悦;王焱;吴茂庆;刘畅【摘要】在对2198铝锂合金进行高速铣削试验的基础上,研究了切削参数对表面粗糙度的影响规律,观察了其铣削表面形貌。
结果表明:平直处表面粗糙度与拐角处表面粗糙度不一致是由机床主轴振动和实际进给量变化造成的;较小的每齿进给量和铣削宽度能够获得较好的表面质量;表面缺陷常发生在铣削刀痕交叉处。
%A series of tests are conducted based on high speed milling 2198 aluminum-lithium alloy. It is investigated that the cutting parameters could influence surface roughness and the surface topography. The experi-mental results show that the straight surface quality is better than the corner surface roughness. The difference is due to the chatter of milling and the variation of the actual feed per tooth. In addition, a low level of feed per tooth and milling width could get better surface quality. Moreover, surface defects are usually observed at the cross of tool paths.【期刊名称】《航空制造技术》【年(卷),期】2015(000)006【总页数】4页(P92-94,99)【关键词】铝锂合金;高速切削;表面粗糙度;表面形貌【作者】丁悦;王焱;吴茂庆;刘畅【作者单位】中航工业北京航空制造工程研究所;中航工业北京航空制造工程研究所;中航工业北京航空制造工程研究所;中航工业北京航空制造工程研究所【正文语种】中文铝锂合金是一种先进航空轻量化材料,具有减重效果明显、强度-韧性综合性能好、疲劳性能好和耐腐蚀等多项优点,在飞机设计中广泛应用于地板梁、机身蒙皮、长桁、框、梁、腹板等部位[1-3]。
铝硅合金ADC12高速铣削力实验研究

步影 响刀具 的磨 损 以及 加工 表 面质量 等 。另外 ,高速 切 削过 程 中刀具 与工 件高 速碰 撞 ,特别 是对 于 立式 铣 削 这 种 断 续 切 削 过 程 ,高 频 冲 击 特 性 会 非 常 地 明 显 心引。因此 ,有必 要 对高 速 铣 削铝 硅 合 金 ADC12过 程 中切 削力 的大小及 变化规律展 开研究 。
1 高速铣削 力实验设计
1.1 实验 材料 实验 材料为某 E型发动 机 缸体 、缸 盖材 料一铝 硅
A bstract:In allusion to a type of engine cylinder block.cylinder head m ateria1.AD C12 aluminum silicon al— loy,four blades using hard alloy straight shank end m illing cutter head,high speed mi lling force single fac— t o r and orthogonal experim ent w ere carried out.The rule and the reason of cutting force under different cut— ting conditions changing with thechanging of cutting par am eters in th e process of high—speed end mi lling were explored.The influence of cutting param eters on th e cutting force to significant size can be obtained according to th e results of variance analysis.On th e basis of th e analysis of experimental results,the general r u les of selection of high speed cutting par am eters of the aluminum silicon alloy AD C12 were pointed out. K ey words:alum inum silicon alloy;high speed mi lling force;th e processing experim ent
6005A铝合金高速铣削加工数值模拟研究

目前,国内对于6005A 铝合金大型薄壁中空结构件的高速数控加工存在诸多问题,如数控加工效率较低、刀具损耗大、铣削速度较高时出现崩刃、打筋等,这些问题严重影响了企业生产效益。
因此,研究6005A 铝合金的高速铣削加工机理,以解决生产中出现的问题,具有重要的现实化高速铣削6005A 铝合金结构件的刀具几何参数提供依据。
6005A 铝合金材料特性6005A 合金是在6005合金的基础上发展的一种中等强度Al-Mg-Si 系合金,具有优良的挤压性、焊接性和耐腐蚀性,广泛应用于地铁和巴士车体结构件、铁塔平台、管道设施等。
6005A 铝合金的主要化学成分和材料基本性能参数如表1和表2所示。
有限元模型建立1 热力耦合有限元控制方程在金属切削加工时,随着刀具的进给,材料应力不断增加。
当应力超出弹性范围时,材料发生塑性变形。
6005A 铝合金高速铣削加工数值模拟研究大连交通大学机械工程学院 王 春 苏 彬 汤武初唐山轨道客车有限责任公司 程 浩 目前,国内对于6005A 铝合金大型薄壁中空结构件的高速数控加工存在诸多问题,如数控加工效率较低、刀具损耗大、铣削速度较高时出现崩刃、打筋等,这些问题严重影响了企业生产效益。
因此,研究6005A 铝合金的高速铣削加工机理,以解决生产中出现的问题,具有重要的现实意义。
王 春大连交通大学机械工程学院副教授,主要研究方向为数控及数字化技术与系统、复杂曲面测量与加工。
已发表论文17篇。
Numerical Simulation Study on High -Speed Milling for 6005A Aluminum Alloy意义。
在铣削加工过程中,切削力决定切削热的产生,并影响刀具使用寿命、加工精度和加工表面质量,研究切削力的规律和计算方法有助于分析铣削机理。
解析法和实验法是研究切削力的主要方法,但随着计算机技术的发展,有限元数值模拟方法为研究切削过程中的切削力提供了新的方法。
高速切削刀具系统动平衡技术研究

高速切削刀具系统动平衡技术研究摘要:介绍高速切削刀具系统动平衡技术的发展现状,并在此基础上提出相关问题进行讨论。
一、概述在高速旋转下,刀具系统(刀具-夹头-刀柄)的一点点不平衡都会产生较大的离心力,引起机床和刀具的振动,产生不均匀的切削力,不仅影响被加工工件的加工精度和表面质量,又会影响机床主轴轴承和刀具的不规则磨损,迅速降低其使用寿命。
高速旋转刀具的不平衡对加工表面粗糙度Ra的影响可用下面的实例说明。
实验目的:通过切削实验,比较用两种不平衡量的刀具系统进行切削,径向切深,对铣削加工表面粗糙度Ra的影响。
实验条件:试件材料为铝合金。
加工机Array床为瑞士米克郎公司产HSM600铣削中心,刀具选用Ø10mm超细晶粒硬质合金整体立铣刀,4齿,30°螺旋角,刀尖圆弧半径1mm ,两刀具系统不平衡量分别为u1=100g·mm、u2=2.5g·mm。
加工参数为主轴转速15,000r/min ,进给速度5.3m/min 。
实验结果分析:用两种不平衡量刀具进行切削,试件加工表面粗糙度Ra与径向切深a p的关系如图1所示。
从实验结果看,试件加工表面粗糙度Ra随径向切削深度a p的增大而增大,而且两种不图1 试件加工表面粗糙度Ra与a p关系平衡量刀具对其加工表面粗糙度的影响有较大差距。
因此,研究高速旋转刀具的动平衡技术是推广应用高速切削加工技术的重要内容。
目前,许多国家已对高速切削刀具的动平衡问题进行了广泛研究,如动平衡标准,动平衡方法、动平衡质量等级界定、动平衡仪器等。
二、刀具系统动平衡技术的发展现状1. 平衡标准旋转体的不平衡量,是指其质量重心偏离旋转中心的量。
不平衡量U在数值上等于旋转体质量M(g) 乘以偏心距e(mm),也等于等效不平衡质量m(g)乘以其回转半径r(mm),即:U=Me=mr(g·mm)不平衡量U可在动平衡机上测得。
就旋转刀具和刀柄来说,目前由于国内、外尚无统一的刀具平衡标准,世界各国和机床厂家采用的标准也不一样,往往借用旋转体平衡的国际标准ISO1940-1。
高速铣削加工实验报告

高速铣削加工实验报告一、实验目的本实验旨在探究高速铣削加工的原理和方法,验证其在工业生产中的应用价值。
二、实验原理高速铣削加工是指在高速转动的铣刀刀具下,通过削减工件的材料,使其形成需要的形状和表面质量。
该加工方法具有高效、高精度、高表面质量的特点。
三、实验步骤1. 准备实验所需设备:数控铣床、高速铣刀、工件材料、润滑剂等。
2. 将工件夹在数控铣床上,并调整好加工参数。
3. 启动数控铣床,通过程序控制铣刀的运动程式。
4. 对工件进行高速铣削加工,观察并记录加工过程中的各项数据。
5. 完成加工后,对加工件进行检查,评估其表面质量和尺寸精度。
四、实验结果与数据分析经过高速铣削加工后,我们得到了一批加工件。
通过检查和测量,我们得到了以下数据:1. 加工件的尺寸精度均匀在±0.02mm范围内,达到了我们的要求。
2. 加工表面的光洁度较高,无明显划痕和毛刺。
3. 加工过程中的切削力较小,表明高速铣削加工确实能够提高加工效率。
根据上述结果,我们可以得出以下结论:高速铣削加工在工业生产中具有重要的应用价值。
它能够快速、准确地加工各种形状的工件,并且保证工件的尺寸精度和表面质量。
此外,高速铣削加工还能够降低切削力,延长刀具的使用寿命,提高生产效率和经济效益。
五、实验总结通过本次实验,我们进一步了解了高速铣削加工的原理和方法,并验证了其在工业生产中的应用价值。
高速铣削加工不仅能够提高加工效率和精度,还能够改善加工表面的质量。
在以后的工作中,我们将进一步研究并优化高速铣削加工的工艺参数,提高其应用效果。
六、参考文献1. 《数控铣床操作与编程》,xxx,xxx出版社,2010年。
2. 《机械加工技术》,xxx,xxx出版社,2015年。
(注:以上文献仅作参考,具体引用请根据实际情况进行。
)以上是本次高速铣削加工实验的报告,感谢您的阅读。
铝合金高速数控铣削参数优化
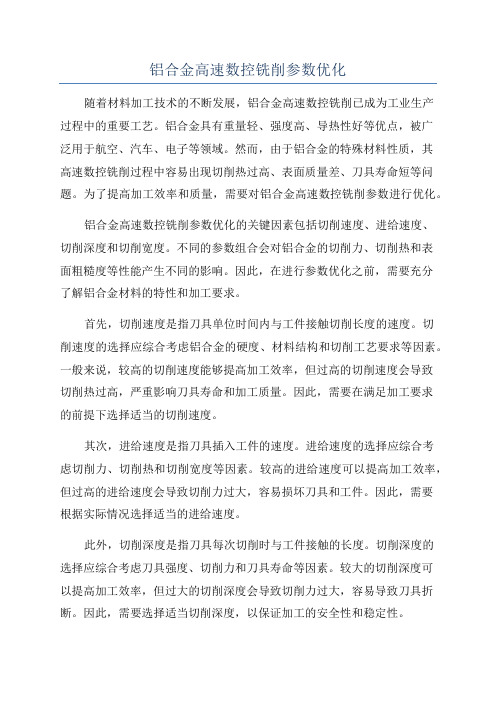
铝合金高速数控铣削参数优化随着材料加工技术的不断发展,铝合金高速数控铣削已成为工业生产过程中的重要工艺。
铝合金具有重量轻、强度高、导热性好等优点,被广泛用于航空、汽车、电子等领域。
然而,由于铝合金的特殊材料性质,其高速数控铣削过程中容易出现切削热过高、表面质量差、刀具寿命短等问题。
为了提高加工效率和质量,需要对铝合金高速数控铣削参数进行优化。
铝合金高速数控铣削参数优化的关键因素包括切削速度、进给速度、切削深度和切削宽度。
不同的参数组合会对铝合金的切削力、切削热和表面粗糙度等性能产生不同的影响。
因此,在进行参数优化之前,需要充分了解铝合金材料的特性和加工要求。
首先,切削速度是指刀具单位时间内与工件接触切削长度的速度。
切削速度的选择应综合考虑铝合金的硬度、材料结构和切削工艺要求等因素。
一般来说,较高的切削速度能够提高加工效率,但过高的切削速度会导致切削热过高,严重影响刀具寿命和加工质量。
因此,需要在满足加工要求的前提下选择适当的切削速度。
其次,进给速度是指刀具插入工件的速度。
进给速度的选择应综合考虑切削力、切削热和切削宽度等因素。
较高的进给速度可以提高加工效率,但过高的进给速度会导致切削力过大,容易损坏刀具和工件。
因此,需要根据实际情况选择适当的进给速度。
此外,切削深度是指刀具每次切削时与工件接触的长度。
切削深度的选择应综合考虑刀具强度、切削力和刀具寿命等因素。
较大的切削深度可以提高加工效率,但过大的切削深度会导致切削力过大,容易导致刀具折断。
因此,需要选择适当切削深度,以保证加工的安全性和稳定性。
最后,切削宽度是指切削刀具与工件之间的接触宽度。
切削宽度的选择应综合考虑切削力、表面粗糙度和刀具寿命等因素。
较大的切削宽度可以提高加工效率,但过大的切削宽度会导致切削力过大,降低表面质量。
因此,需要选择适当的切削宽度,以保证加工的质量和效率。
在铝合金高速数控铣削参数优化中,除了上述的关键因素外,还需要综合考虑刀具类型、冷却液使用和刀具磨损等因素。
实验四 切削要素对表面加工质量的影响

实验四切削要素对表面加工质量的影响实验项目性质:综合性实验计划学时:2学时一、实验目的1、了解加工表面粗糙度的影响因素。
2、了解降低加工表面粗糙度的工艺措施。
3、通过实验测出数据验证切削用量f、ap对加工表面粗糙度的影响,达到深化、巩固所学的基本概念和基本理论的目的。
4、研究切削速度、切削深度和走刀量等因素对加工质量的影响规律。
5、掌握确定切削参数的基本方法。
二、实验装备设备:CA6140普通车床;粗糙度对照样板块、粗糙度测量仪等;刀具:硬质合金车刀若干把。
三、实验的基本原理1、零件经切削加工后的质量包括精度和表面质量。
(1) 精度是指零件在加工之后,其尺寸、形状等参数的实际数值同它们绝对准确的各个理论参数相符合的程度。
符合程度越高,亦即偏差(加工误差)越小,则加工精度越高。
(2) 表面质量已加工表面质量(也称表面完整性)包括表面粗糙度、表层加工硬化的程度和深度、表层剩余应力的性质和大小。
2、影响表面粗糙度的因素1)切削加工影响表面粗糙度的因素(1)刀具几何形状的反映刀具相对于工件作进给运动时,在加工表面留下了切削层残留面积,其表面形状是刀具几何形状的反映。
减小主偏角、副偏角以及增大刀尖圆弧半径,均可减小残留面积的高度。
此外,适当增大刀具的前角以减小切削时的塑性变形程度,合理选择润滑液及提高刀具刃磨质量以减小切削时的塑性变形和抑制刀瘤、鳞刺的生成,也是减小表面粗糙度值的有效措施。
(2)工件材料的性质加工塑性材料时,由刀具对金属的挤压产生了塑性变形,加之刀具迫使切屑与工件分离的撕裂作用,使表面粗糙度值加大。
工件材料韧性愈好,金属的塑性变形愈大,加工表面就愈粗糙。
加工脆性材料时,其切屑呈碎粒状,由于切屑的崩碎而在加工表面留下许多麻点,使表面粗糙。
(3)切削用量的选择切削三要素的选择也是影响表面粗糙度的重要因素。
切削三要素包括工件表面旋转线速度(V)、进给速度(F)、吃刀深度(Ap)。
合理的提高工件旋转线速度,降低进给速度,降低吃刀深度,都可以起到提高表面质量的作用。
- 1、下载文档前请自行甄别文档内容的完整性,平台不提供额外的编辑、内容补充、找答案等附加服务。
- 2、"仅部分预览"的文档,不可在线预览部分如存在完整性等问题,可反馈申请退款(可完整预览的文档不适用该条件!)。
- 3、如文档侵犯您的权益,请联系客服反馈,我们会尽快为您处理(人工客服工作时间:9:00-18:30)。
高速铣削铝合金时切削力和表面质量影响因素的试验研究
1 引言
高速铣削加工可获得较高的金属切除率、很高的加工精度和良好的加工表面质量,因此在现代制造业中受到普遍重视,发展很快。
高速铣削技术首先应用于航空制造业。
由于对高硬度材料进行高速铣削加工可在一定程度上替代效率较低的电火花加工从而缩短模具制造周期,因此目前高速铣削技术在模具制造业也得到广泛应用。
在航空制造业中,高速铣削的主要加工对象为铝合金构件。
为提高飞机性能,在飞机结构设计中大量采用铝合金整体框架和薄壁结构,而铝合金高速铣削技术使对此类构件的高效加工成为可能,从而在一定程度上推动了飞机结构的改进。
高速铣削时,由于主轴转速提高,在每齿进给量不变的情况下,进给速度会大幅增加,目前采用直线电机驱动的高速铣床的进给速度已达100m/min。
因此,在规划高速铣削的刀具轨迹时,必须考虑进给方向改变时机床进给系统的响应速度,以防止发生过切等现象。
针对典型铝合金框架结构的高速铣削工艺,本文通过切削试验研究了当金属去除率恒定时铣削工
艺数对铣削力和加工表面质量的影响以及铣削圆角时的铣削力
和表面粗糙度特征。
2 试验目的与方法
1) 试验目的
通过切削试验,主要研究径向切深ap、轴向切深ae对铣削力和加工表面粗糙度Ra的影响。
铣削力取连续测量50点峰值的平均值,加工表面粗糙度Ra取三次
测量的平均值。
2) 试验方法
试验条件:试件材料为7075预拉伸铝合金,试件结构见图1;加工机床为MICRON UCP710五坐标加工中心,主轴最大转速18,00m/min,功率15kW,最大进给速度20m/min;刀具选用f10mm超细晶粒硬质合金整体立铣刀,2齿,30°
螺旋角,刀尖圆弧半径R=1.5mm;所有铣削试验均采用油雾冷却。
点击此处查看全部新闻图片
图1 7075铝合金C 型框铣削试件
测量仪器:采用Kistler9265B, 三向动态压电测力仪、5019A电荷放大器和计算机数据采集系统测量、记录切削力;采用Mahr M1表面粗糙度测量仪测量加工表面粗糙度。
铣削参数:主轴转速18000r/min,对应铣削速度565m/min;为对比加工表面粗糙度,每齿进给量fz分别取0.05mm和0.1mm;径向切深ap和轴向切深ae的乘积恒定为2mm2。
3 试验结果与分析
加工图1所示试件时,由于铣削进给方向要发生改变,因此采用Fxy(Fx 与Fy的合力)和Fz作为切削力评价参数。
根据测量结果,切削过程中Fxy峰值切削力如图2所示。
Fz的峰值切削力变化趋势与图2类似,但Fz的大小仅为Fxy 的1/3。
(ap=2mm,ae=1mm,fz=0.1mm)
点击此处查看全部新闻图片
图
2 Fxy峰值切削力
1) ap对铣削力的影响
由图2可见,当刀具刚切入试件拐角处时,切削力迅速增大到加工试件直边时的约1.7倍,主要由于高速铣削中进给方向发生变化时,为防止过切,机床进给速度自动降低,造成每齿进给量(即切削厚度)下降;同时,在切削拐角处时,铣刀的切入角Yi增大(图4所示的切入角Yi为负值),每齿切削度增加,使尺寸效应在拐角处加剧。
以上两种因素综合作用的结果使铣刀在铣削试件拐角处时切屑平均厚度减小,由尺寸效应引起铣削力急剧增大。
点击此处查看全部新闻图片
表1 铣削试验切削力测量结果
根据表所列试验结果,得到铣削力Fxy、Fz与进给量ap的关系(见图3)以及加工试件直边与拐角处时Fz的对比情况(见图4)。
由图可见,当切深大于铣刀的刀尖圆弧半径R时(f16mm铣刀R=1.5mm),Fxy变化不大,而Fz随ap的增大而增大,图中的Fz负值则表示刀具受拉力作用(切削试验中,当ap=16mm时,加工至拐角处时f16mm立铣刀曾被折断)。
当主轴转速较高时,刀具的夹紧力因受离心力影响而下降,当切深较大时,在较大拉力作用下可能造成刀具夹紧力不足而发生拉刀现象。
当每齿进给量从0.05mm增大到0.10mm时,Fxy仅增大约15%;而在相同切削面积和进给量条件下(即金属去除率恒定),当ap小于刀尖圆弧半径时(ap<1.5mm),切削力则迅速减小。
该结果对于减小高速铣削时的加工变形具有一定指导意义。
点击此处查看全部新闻图片
图3 铣削力Fxy、Fz 与进给量ap的关系
点击此处查看全部新闻图片
图4 加工试件直边与拐角处时Fz的对比
2) ap对加工表面粗糙度的影响
切削试验中分别采用了顺铣和逆铣两种铣削方式。
由于逆铣时切屑厚度是由薄变厚,当刀刃刚接触试件时,后刀面与试件之间摩擦较大,容易引起振动;切削试件拐角处时,因切入角Yi和铣削长度的增加(见图5),逆铣的摩擦效应也会引起切削振动,并在拐角处产生振纹。
而顺铣时则正好相反,虽然顺铣时切削力稍大于逆铣,但顺铣时切屑厚度是由厚变薄,刀具后刀面与试件之间摩擦效应较小,在拐角处不易引起切削振动。
但由于顺铣对工件和刀具的冲击力均较大,因此加工时应尽可能减小刀具悬伸长度和增加工件刚性。
点击此处查看全部新闻图片
图5 铣削时的切入角Yi和切出角Yo
试件加工表面粗糙度与ap的关系如图6所示。
测量结果表明,试件拐角处的表面粗糙度Ra值略高于试件直边处的Ra值,逆铣时在试件拐角处出现了斜向振纹;但当Ra=0.5mm时,试件拐角处的Ra值反而小于直边处的Ra值,这是由于切削厚度变化引起的铣削力波动会对加工表面粗糙度产生一定影响,当轴向切深较小时,随着铣削力的减小,铣削力波动对加工表面粗糙度的影响也随之减小,因此,随着轴向切深的减小,表面粗糙度Ra值呈下降趋势。
点击此处查看全部新闻图片
(a)每齿进给量
Ra=0.05mm (b)每齿进给量Ra=0.10mm
图6 试件加工表面粗糙度Ra与ap的关系
当采用较大进给量ap进行铣削加工时,工件直边处出现垂直于进给方向的振纹,但对表面粗糙度Ra影响不大(见图7)。
由于振纹处表面粗糙度曲线的峰间距基本上等于铣削时的每转进给量,因此可判定该振纹主要是由于刀具高速旋转时的动平衡偏心量造成两个刀齿的径向尺寸产生偏差而引起的。
(ap=6mm,ae=0.33mm,fz=0.1mm/z,顺铣)
点击此处查看全部新闻图片
图7 振纹处的表面粗糙度测量曲线
根据试验数据和分析结果可知:使用圆柱铣刀对铝合金材料进行高速铣削时,应选用较大的径向切深量(约为刀具直径的40%~80%)和较小的轴向切深量(小于
刀具直径的30%)。
由于径向加工余量较大,可在一定程度上增加工件刚性,加上径向铣削力和加工表面粗糙度值均较小,因此加大径向切深既能满足加工工艺要求,又可通过调整工艺参数最大限度地减小加工变形。
4 结论
高速铣削铝合金材料时,在金属去除率恒定的情况下,选用较小的轴向切深和较大的径向切深比选用较大轴向切深和较小径向切深更为有利。
高速铣削铝合金材料时,选用较小的轴向切深不仅可大幅度降低切削力,而且可获得更好的表面加工质量。
从减小切削变形的角度选择切削用量时,选用较大的径向切深不仅可降低切削力,而且可增加工件刚性。
由切削试验数据可知,在满足加工要求和机床、刀具条件允许的前提下,还可进一步增大进给量和切削面积,以达到提高加工效率的目的。
发布时间:2006-4-2
•相关主题关键字:
•高速
•铣削
•试验
•加工。