制造二处机壳刮伤改善报告
玻璃加工划伤改善方法
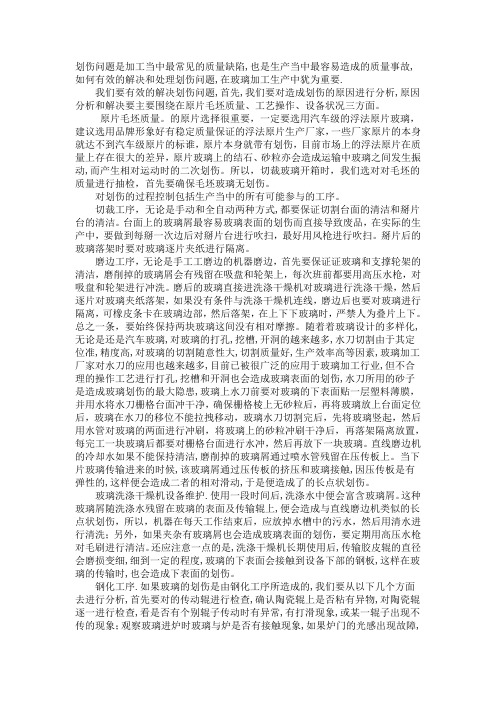
划伤问题是加工当中最常见的质量缺陷,也是生产当中最容易造成的质量事故,如何有效的解决和处理划伤问题,在玻璃加工生产中犹为重要.我们要有效的解决划伤问题,首先,我们要对造成划伤的原因进行分析,原因分析和解决要主要围绕在原片毛坯质量、工艺操作、设备状况三方面。
原片毛坯质量。
的原片选择很重要,一定要选用汽车级的浮法原片玻璃,建议选用品牌形象好有稳定质量保证的浮法原片生产厂家,一些厂家原片的本身就达不到汽车级原片的标谁,原片本身就带有划伤,目前市场上的浮法原片在质量上存在很大的差异,原片玻璃上的结石、砂粒亦会造成运输中玻璃之间发生振动,而产生相对运动时的二次划伤。
所以,切裁玻璃开箱时,我们选对对毛坯的质量进行抽检,首先要确保毛坯玻璃无划伤。
对划伤的过程控制包括生产当中的所有可能参与的工序。
切裁工序,无论是手动和全自动两种方式,都要保证切割台面的清洁和掰片台的清洁。
台面上的玻璃屑最容易玻璃表面的划伤而直接导致废品,在实际的生产中,要做到每掰一次边后对掰片台进行吹扫,最好用风枪进行吹扫。
掰片后的玻璃落架时要对玻璃逐片夹纸进行隔离。
磨边工序,无论是手工工磨边的机器磨边,首先要保证证玻璃和支撑轮架的清洁,磨削掉的玻璃屑会有残留在吸盘和轮架上,每次班前都要用高压水枪,对吸盘和轮架进行冲洗。
磨后的玻璃直接进洗涤干燥机对玻璃进行洗涤干燥,然后逐片对玻璃夹纸落架,如果没有条件与洗涤干燥机连线,磨边后也要对玻璃进行隔离,可橡皮条卡在玻璃边部,然后落架,在上下下玻璃时,严禁人为叠片上下。
总之一条,要始终保持两块玻璃这间没有相对摩擦。
随着着玻璃设计的多样化,无论是还是汽车玻璃,对玻璃的打孔,挖槽,开洞的越来越多,水刀切割由于其定位准,精度高,对玻璃的切割随意性大,切割质量好,生产效率高等因素,玻璃加工厂家对水刀的应用也越来越多,目前已被很广泛的应用于玻璃加工行业,但不合理的操作工艺进行打孔,挖槽和开洞也会造成玻璃表面的划伤,水刀所用的砂子是造成玻璃划伤的最大隐患,玻璃上水刀前要对玻璃的下表面贴一层塑料薄膜,并用水将水刀栅格台面冲干净,确保栅格棱上无砂粒后,再将玻璃放上台面定位后,玻璃在水刀的移位不能拉拽移动,玻璃水刀切割完后,先将玻璃竖起,然后用水管对玻璃的两面进行冲刷,将玻璃上的砂粒冲刷干净后,再落架隔离放置,每完工一块玻璃后都要对栅格台面进行水冲,然后再放下一块玻璃。
主机厂质量问题改善报告

主机厂质量问题改善报告一、前言在主机厂的生产过程中,质量问题的出现是不可避免的。
然而,及时发现、深入分析并采取有效的改善措施,对于提高产品质量、提升客户满意度以及增强企业竞争力具有至关重要的意义。
本报告旨在对主机厂近期出现的质量问题进行全面的梳理和分析,并提出相应的改善方案。
二、质量问题概述(一)问题类型在过去的一段时间里,主机厂主要面临以下几种类型的质量问题:1、零部件缺陷:部分零部件在生产过程中存在尺寸偏差、材质不合格等问题,导致装配困难或影响产品性能。
2、装配工艺问题:装配过程中操作不规范,如拧紧力矩不足、装配顺序错误等,影响产品的稳定性和可靠性。
3、外观瑕疵:产品表面存在划痕、磕碰、掉漆等现象,影响产品的美观度。
(二)问题分布质量问题在不同的产品线和生产环节中分布不均。
其中,具体产品线 1的质量问题较为突出,主要集中在具体生产环节 1;而具体产品线2的问题则相对较少,主要出现在具体生产环节 2。
(三)影响程度这些质量问题对主机厂的生产和经营产生了不同程度的影响。
一些轻微的问题导致了产品的返工和维修,增加了生产成本;而严重的问题则引发了客户投诉,损害了企业的声誉和市场份额。
三、原因分析(一)人员因素1、操作人员技能不足:部分新员工对生产工艺和质量标准不够熟悉,操作失误较多。
2、工作态度不认真:部分员工责任心不强,在生产过程中存在敷衍了事的情况。
(二)设备因素1、设备老化:部分生产设备使用时间较长,性能下降,精度无法满足生产要求。
2、设备维护不到位:设备的日常维护和保养工作不够及时和规范,导致设备故障频发。
(三)原材料因素1、供应商管理不善:对供应商的审核和监督不够严格,导致部分原材料质量不稳定。
2、原材料检验不严格:在原材料入库时,检验标准执行不严格,一些不合格的原材料流入生产线。
(四)工艺方法因素1、工艺文件不完善:部分生产工艺文件存在漏洞和错误,导致操作人员在生产过程中无章可循。
2、工艺改进不及时:随着市场需求和技术的发展,部分生产工艺已经落后,但未能及时进行改进和优化。
划伤异常回复报告-5why_8D报告案例
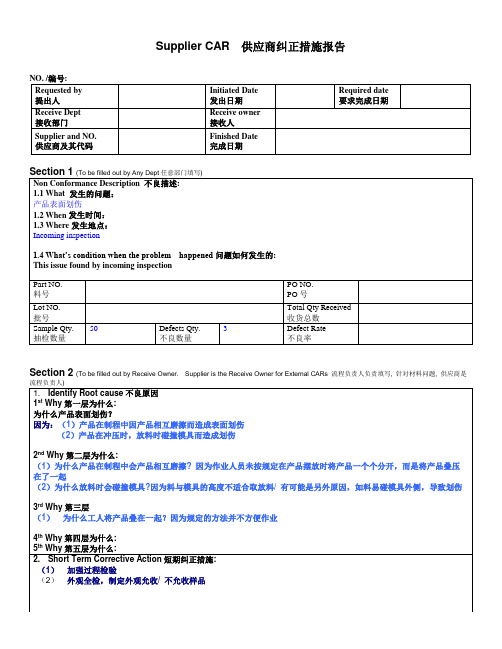
Part NO.
料号
PONO.
PO号
Lot NO.
批号
Total Qty Received
收货总数
Sample Qty.
抽检数量
50
Defects Qty.
不良数量
3
Defect Rate
不良率
Section 2(To be filled out by Receive Owner. Supplier is the Receive Owner for External CARs流程负责人负责填写,针对材料问题,供应商是流程负责人)
Section 1(To be filled out by Any Dept任意部门填写)
Non Conformance Description不良描述:
1.1 What发生的问题:
产品表面划伤
1.2 When发生时间:
1.3 Where发生地点:
Incoming inspection
1.4 What’s condition when the problem happened问题如何发生的:
(1)加强过程检验
(2)外观全检,制定外观允收/不允收样品
Implementation Date执行日期:2007.10.28
3.Long Term Corrective Action长期预防措施:
(1)制作吸塑盘或其它便于作业的方式
(2)更改料的放置高度/在模具外侧增加防划伤的措施
Implementation Date执行日期:2007/10/28
4.Verification of the Effectiveness of the solution implementation对策验证有效性:
经典制程改善案例可做改善报告模板

制作专用盒子盛放
改 善 结 果
螺丝有专用盒子放,明显整齐
改善成果个案
项目名称 项目类别
友利通面板
提案人 实施人
邹龙庚 邹龙庚
提案时间 完成时间
09/08/ 14 09/08/ 14
提案部门 确 认人
IE 车间
贴胶纸改善
Before(图片)
After(图片)
问 题 点
改 善 前
胶纸割的长短不一,导致贴胶纸NG
1,手动压紧PC贴片效果不太好 2,每次压一个速度较慢 1,手动压力不均匀,没有持续时间压 倒一切,每次只压一个. 制做液压形式的治具 做成一出四的治具. 改 善 后 现 状 已执行
改善对策
改 善 结 果
压力平整 速度加快,时间由原来5秒降到3秒 /PCS
改善成果个案
项目名称 项目类别
M8底壳
提案人 实施人
车间 IE
5S改善
Before(图片)
After(图片)
问 题 点
改 善 前
批锋到处飞
产品为尼龙料,批锋多,用刀批时风 扇将批锋吹得到处。 将用大胶盒放到桌面,在盒上批后批 锋将掉在盒子中。 改 善 后 现 状 已执行
原因分析
改善对策
改 善 结 果
5S明显改善.
改善成果个案
项目名称 项目类别
创维3020面板
问 题 点
改 善 前
产品用水口剪花时间长
改 善 后 现 状 已执行
原因分析
水口剪要剪八次
改善对策
制做一个治具来切。
改 善 结 果
时间从20秒减少到10秒/PCS。
改善成果个案
项目名称 项目类别
大金成品
提案人 实施人
施工机械维修整改报告

施工机械维修整改报告一、维修概述施工机械作为现代建筑施工的重要设备,承担着关键的作用。
然而,由于长时间的使用以及操作不当等原因,施工机械可能会出现各种问题和故障。
本报告旨在总结对某施工机械进行的维修整改工作,以确保机械的正常运行并提高工作效率。
二、故障检测与问题分析在对该施工机械进行检测时,我们发现了以下故障和问题:1. 润滑系统故障:润滑系统出现漏油现象,导致机械各动力部件的润滑不足,进而影响机械的运行效率和寿命。
2. 电子控制系统异常:电子控制系统出现故障,导致机械的操作功能无法正常实现,给施工工作带来了困扰。
3. 传动系统异响:传动系统出现明显的异响,给施工作业带来了噪音污染,并且可能会影响机械的正常运行。
4. 液压系统泄漏:液压系统存在泄漏问题,导致机械的工作力度不稳定,直接影响了施工的效率和质量。
经过对以上问题的分析,我们决定进行相应的维修整改,以保证施工机械的正常运行和性能。
三、维修措施与实施过程针对上述故障和问题,我们采取了以下维修措施:1. 清洗和更换润滑系统中的油液,并检查润滑管路和接头的连接情况,以消除油液泄漏。
2. 对电子控制系统进行全面检查和诊断,并修复或更换有问题的电子元件,确保机械的各项功能能够正常运行。
3. 对传动系统进行全面检测和维护,检查齿轮和传动皮带等传动部件的磨损情况,及时更换有问题的配件。
4. 对液压系统进行系统性的维修,检查液压元件的密封情况,修复泄漏问题,并对系统进行液压油的更换和液压管路的检查,以确保液压系统的正常工作。
在实施过程中,我们严格按照施工机械维修的标准操作流程进行操作,并充分考虑现场的实际情况和施工进度,以最大限度地减少停工时间和影响。
四、维修效果评估经过维修整改后,该施工机械的故障和问题得到了有效解决,具体效果如下:1. 润滑系统正常:经过清洗和更换油液,并及时修复润滑管路和接头的漏油问题后,机械的各动力部件得到了充分润滑,提高了机械的运行效率和寿命。
05-VXXX项目前壳组装段三伤改善专案报告0525
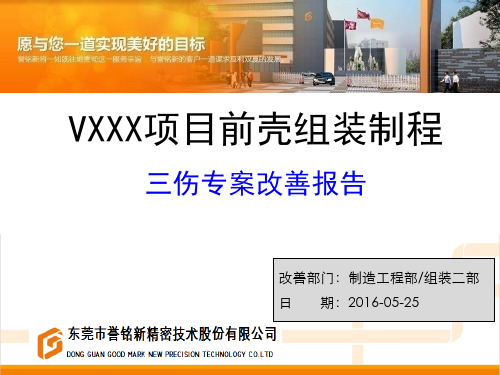
龚红林
11
左侧、右侧铝条/底部铝条扣位 擦胶清洁
高
擦胶清洁过程堆积产品未按规定 要求作业员严格按照包装要求,吸 摆放在吸塑盒内,同时吸塑盒未 塑盒必须垫膜,同时产品必须摆放 垫膜,容易造成铝条高光磨花 在吸塑盒内
龚红林
12 卡槽实配堵塞检测
低
/
/
/
13 电源键、音量键检查/卡托检查
中
卡托检查完成后,拆卡托过程插 对插PIN头部进行抛光锐化尖角,防
三伤专案管理规划—推行计划
三伤专案管理规划—改善目标设定
专案活动主题 VXXX前壳组装制程碰划伤改善
17.3%
专案活动目标
现状
3.0%
目标
1.0%
挑战目标
各工站三伤隐患排查—打螺钉段
No.
工站名
隐患 风险
原因
改善对策
责任人 完成日期
1
(正面,顶面,右侧面)来料 检查/装泡棉盒
低
/
/
/
/
2
(背面,底部,左侧面)来料 检查
91
8 全检销钉高度/镭雕
91
9 弹片/雷雕区域电阻测试
91
10 RF测试
91
11 插销段全检
91
三伤数量
三伤不良比 例
不良位置分布
TP面棱角
铝条上部高 铝条下部高
光面
光面
0
0.0%
0
0
0
0
0.0%
0
0
0
0
0.0%
0
0
0
0
0.0%
0
0
0
2
2.2%
2
0
0
金面刮伤改善报告ppt课件
使用棕化板测试层别设备输送滚 轮刮伤位置并进行修复;修复中
四、改善成效
通过改善措施的不断落实执行,1751周开始,化金不良趋势已开始呈现明显下降趋势,目前持续 跟进中。
报告完毕 谢谢
3
点状刮伤
人 作业动作异常造成的异物碰撞伤;
同上;
4
孔口刮伤
人 挂PIN对位过程,PIN钉碰撞刮伤;
同上;
5
不规则刮伤
人 作业动作异常造成的板面擦伤;
6
条状刮伤
机 设备输送轮或皮带造成的刮伤;
同上;
使用棕化板测试层别设备刮伤位置并针对设备 存在刮伤位置进行整修;
三、改善措施
原流程:化金→贴蓝胶→镀金→撕蓝胶→V-CUT→锣板→斜边→水洗→电测
102.0% 100.0% 98.0% 96.0% 94.0% 92.0% 90.0% 88.0% 86.0% 84.0%
二、原因分析-前三大异常料号分析 P612098
料号
总数量 (set)
总不良数 (set)
项目 缺陷名称
金面刮伤
漏镍
缺陷名称(set) 板面擦花 假性漏铜 金面粗糙
铜穿
防焊空泡 金面不良
0.0%
80.9% 金面刮伤
88.7%
占比
贡献度
93.9%
95.7%
97.4%
漏镍
板面擦花
假性漏铜
金面粗糙
120.0%
98.3%
99.1%
100.0% 100.0% 80.0%
60.0%
40.0%
20.0%
铜穿
防焊空泡
金面不良
0.0%
产品刮花剖析报告
辅助工具不良容易造成刮花
按钮灯珠大部是用螺 丝刀敲入,但螺丝刀表面 一个磨损、粗糙度容易造 成产品刮花。
产品光面朝下放在流水线槽内作业,槽清洁度不够,有细小 颗粒,容易刮花产品。
产品放于木槽内 作业,木槽粗糙度影 响产品表面刮花情 况。
产品光面朝下直接 在拉线上打螺丝,风批 扭力带动产品转动,存 在刮花隐患。
注:头巾颜色区分为一个方案,现 场可依实际情况采用其他方法区分
。
老员工配戴 黄色头巾
新员工配戴 蓝色头巾
⑵、针对员工一个技能培训改善
问题点: * 员工熟练度不够 * 品质观念不强
* 对作业标准理解不够
改善措施:
针对以上问题点,各车间制订定期员工培训计划表,分批 次 、层级进行培训。例:
××车间培训计划表(样表)
较好包装,产品横着层叠放 在箱内,层与层之间加放泡棉, 对光面产品保护效果较好。
ⅱ、仓储
仓库发料时,当涉及尾数不是整箱物料时,经常是从其 他箱内取出,然后随意堆放在一个箱内。存在刮花隐患。
ⅲ、移印
按钮等移印时堆积,容易造成产品刮花。我们大部分按 钮扣位均比较尖,叠放时容易相互摩擦造成刮花。
ⅳ、装配 光面产品堆积容易造成表面刮花
产品作业存在刮花隐患。
ቤተ መጻሕፍቲ ባይዱ
改善措施: 购买防刮性更强绒布,同时制定清洁标准,培训员工执行。
等级 区分
7 5 5 8 5 4 6 8 6 4
8
4 3
注:等级区分以10分制,对产品刮花影响越严重,分数越高。
2.2 原因分级
对上述表格进行剖析,并通过问题点严重度、发生频率、难检 度进行等级区分,汇总对产品刮花原因主要有以下几方面,以严重 度顺序排列如下:
CNC不良分析及改善报告
CNC不良分析及改善陈述之巴公井开创作CNC不良分析及改善1.来料抽检是否存在崩角严重划伤或尺寸偏小改善措施:抽检来料杜绝不良产品上机既浪费人力物力财力,不良产品退上工序。
2. 正确的操纵手势和操纵流程以免在后续的生产中给本工序或后工序造成良率效率的下滑。
改善措施;严格依照作业指导书进行操纵或在适当的时间对员工加强培训。
3. 崩。
改善措施;1程序存在优化2是否是刀具造成,更换刀具3添加适量的切削液4转速在程控且在%1004.划伤改善措施; 1改善现有夹具通气糟的宽度深度限定为1MM(现已贴呵护膜)2检查来料3正确的放料手势防止与夹具相互摩擦(具体见作业指导书)4进行隔行插架防止取放料相互碰撞5呵护膜一个班更换一次6切削液至少一个月完全更换一次5.裂改善措施;1来料为异形超出CNC规定的切削量1改善现有夹具通气糟的宽度深度限定为1MM 2刀具磨损严重,更换刀具6.阴阳边改善措施; 1调机应秉承确认确认再确认的原则在进行生产2生产中进行自检管理者隔2小时巡检一次3每10分钟清理夹具概况4刀具磨损严重,更换刀具7尺寸不良改善措施; 1调完尺寸的机台应进行投影确认再进行生产尺寸为CNC的雷区,因为在后工序没有在检测尺寸的工序,尺寸不良的产品一旦流入客户,后果不堪设想。
8.未车到改善措施; 1正确的操纵手势2靠角磨损3气压缺乏导致移位目前CNC存在的问题很多,从产品上机到产品下机都没有完整的作业流程。
上机前应该做什么(例如:检查刀具是否存在磨损,水泵正常开启,呵护膜是否需要更换)。
生产中应该注意哪些,防止问题的发生(生产中应当进行自检)。
下机生产完每架产品进行抽检,防止不良品流入下工序。
针对CNC上次生产大量不良做出以上分析及改善措施,在以后的生产中将会以基本方针不良对策3原则 1不接收不良品2不制造不良品 3不流出不良品。
在后期将会在各方面进行改善及优化:比方加强员工的品质意识。
励志提高CNC良率,包管CNC一定能达到预期的目标。
损坏工具整改报告模板
损坏工具整改报告模板
一、事件概述
事件时间
[填写事件发生的具体时间]
事件地点
[填写事件发生的具体地点]
工具名称
[填写损坏的工具名称]
工具型号
[填写损坏的工具型号]
工具供应商
[填写工具的供应商,如果有的话]
事件描述
[简洁明了地描述事件发生的经过,包括工具损坏的原因和过程]
二、事件分析
损失情况
[填写工具损坏所造成的经济损失]
事故隐患分析
[对事件的严重性和隐患性进行分析,包括造成的影响和可能导致的后果等] 案件分析
[对事件进行细致的分析,列出导致该事件发生的主要因素]
三、整改措施
设计措施
[根据事件的原因和分析结果,提出改进措施,防止类似事故再次发生]
工艺措施
[对影响工艺质量的问题进行分析,提出改进措施]
管理措施
[对管理方面存在的问题进行分析,并对改进措施进行具体分析和提出]
四、整改方案
责任部门
[确定整改的责任部门]
整改计划
[具体提出整改计划,包括整改时间、整改措施、整改后的效果等]
整改完成情况监控
[监控整改进展情况,及时发现和解决问题]
五、总结
整改效果评价
[对整改效果进行评价,分析整改措施的有效性和相关成本]
未来预防措施
[总结本次事件,制定针对性的预防措施,防止此类事故再次发生]
说明和建议
[对整体的事件和整改进行简要的说明和建议,供未来参考]
结语
本报告仅供参考,不代表所有情况下的最终措施。
如有任何疑虑,请向有关部门咨询。
- 1、下载文档前请自行甄别文档内容的完整性,平台不提供额外的编辑、内容补充、找答案等附加服务。
- 2、"仅部分预览"的文档,不可在线预览部分如存在完整性等问题,可反馈申请退款(可完整预览的文档不适用该条件!)。
- 3、如文档侵犯您的权益,请联系客服反馈,我们会尽快为您处理(人工客服工作时间:9:00-18:30)。
更换机壳
更换比例
2875
6.1%
2752
4.3%
1635
4.1% 1.8%
更换比例 8.0% 6.0% 4.0% 2.0% 0.0% 9月 10月 11月 12月 6.1% 4.3% 4.1% 1.8%
D1→D2→ D3 →D4(初步分析 &暂时对策)→D5 →D6 →D7 → D8
流程
… 包装测试 LQC
Before After
胶皮老化后变硬
已更换新胶皮
D1→D2→ D3 →D4→D5 (根本原因 &长期对策)→D6 →D7 → D8 老化房带孔胶皮变形
Before After
带孔胶皮老化后变形
已更换新胶皮
D1→D2→ D3 →D4→D5 (根本原因 &长期对策)→D6 →D7 → D8 老化房铁丝网外露
包装外观刮伤数据分析
日期 11.25 A面 0 标贴面 16 下壳底面 9 面盖 1 DC线材侧 3 侧盖 2
11.26
11.27 12.11 12.12 12.16 12.17 12.18 12.19 12.2 12.22 合计
0
1 5 5 4 3 3 6 11 1 39
7
13 5 7 3 2 0 0 0 0 53
D1 改善主题
D2 紧急处理
D3 现状分析 D4 初步分析 及暂时对策 D5 根本原因 及长期对策 D6 效果确认
D7 水平展开
D8 标准化
专案改善成员
总负责人:王朝维 负责人:俸文举
指导顾问:郭绍元
资料整理:秦永培
制 造
丁 荣
王见明
I E
陈 适
T E
贾战卫
Q E
武宗建
主题选定原因及理由
机壳不良已不容忽视 目前更换机壳的成本较高 DELL/联想对此越来越重视
包装第一站 数据采集点2
D1→D2→ D3 →D4(初步分析 &暂时对策)→D5 →D6 →D7 → D8 HK350-55BP面定义
风扇面
下底面
A面
DC线材面
标贴面
D1→D2→ D3 →D4(初步分析 &暂时对策)→D5 →D6 →D7 → D8
准备记录表
D1→D2→ D3 →D4(初步分析 &暂时对策)→D5 →D6 →D7 → D8
组装外观刮伤数据分析
日期 11.25 11.26 11.27 12.11 12.12 12.16 A面 12 10 6 4 6 6 标贴面 1 2 1 2 0 0 下壳底面 23 7 0 3 3 3 面盖 0 0 0 4 1 1 DC线材侧 0 0 0 0 0 2 侧盖 1 0 4 0 0 1
12.17
使用回收袋
使用出货袋
D1→D2→ D3 →D4→D5 (根本原因 &长期对策)→D6 →D7 → D8 其它
产线使用海绵垫放置产品
D1→D2→ D3 →D4→D5 (根本原因 &长期对策)→D6 →D7 → D8 周转车改造
周转车垫上静电皮(废品利用)
对产线上换下的废旧静电皮进行裁剪
将裁剪好的废旧静电皮粘贴在周转车上
序号 1 2 3 4 5 6 7 8 9 10 11 12 13 14 15 16 17 18 19 20 21 22 原因 周转车隔板上有异物 线体边条裸露 皮带上有异物 老化房横梁间距太窄 老化房胶皮变硬 老化房带孔胶皮变形 老化房铁丝网外露 栈板存放时分隔纸板有钉 工作台面剪钳放置不规范 工作台面在制品数量没有管控 工作台面在制品间距无要求 老化房作业人员取放产品时会磕碰横梁 栈板存放时中间2排A面靠A面 锁风扇与盖上盖工位分开作业 产品流速时快时慢 周转车上产品存放间距无要求 摆机员工作业时动作不规范 流水线上员工取放产品时会碰到其他的产品 流水线上员工存放产品时间距无要求 机壳来料不良 在制品包装袋薄且小 发生频次 5 9 3 9 7 7 7 3 3 9 9 7 9 9 9 9 9 9 9 3 9 难易度 7 7 3 1 9 9 9 9 9 9 9 3 9 9 9 9 9 7 9 5 9 是否容易 被验证 9 9 7 9 9 9 9 9 9 9 9 5 9 9 9 9 9 5 9 3 9 得分 315 567 63 81 567 567 567 243 243 729 729 105 729 729 729 729 729 315 729 45 729 是否 本次改善 是
D1→D2→ D3 →D4→D5 (根本原因 &长期对策)→D6 →D7 → D8 工作台面在制品数量没有管控
Before After
有交叉的、有靠在一起的
要求每个工位不超过3台
D1→D2→ D3 →D4→D5 (根本原因 &长期对策)→D6 →D7 → D8 工作台面在制品间距无要求
Before After
机壳刮伤专案改善
8D 报告
Dept.: 制造二处
Reported 俸文举
Date:2008.10.10
改善计划
计划进度
拓展流程
10-7 10-8 10-9 10-10 10-11 10-12 11-20 11-21 11-22 11-23 11-24 11-30 12-1
实际进度
改善推移图
12-2 12-3 12-4 12-5 12-6 12-7 12-15 12-16 12-17 12-18 12-19 12-20 12-30 1-18
线长:_______组长:__________________
稽核内容
时间点:_____
星期一 星期二 星期三 星期四 星期五 星期六
1 所有的待作业机壳是否超过三台 2 产线半成品摆放间距是否一指宽 3 周转车上产品摆放间距是否一指宽 4 员工作业时是否连海绵一起拿放 5 流水线是否按照一格一台机摆放 6 产品离线拿取时只允许一手一台 7 维修工位台面保持清洁,不得有锡渣、线脚、零件等 8 周转车是否保持清洁,不得有锡渣、线脚、零件等 9 产线上每一台机是否都垫上海棉 10 各个维修工位台面是否垫上海棉 11 摆放在栈板上的产品不得超过三层 12 老化员上下机动作是否平进平出
维修
补焊 老化 装箱 ATS1点胶 上老化车 QA
机壳入料
装EMI 组装上下盖 CQA 点白胶 锁风扇 仓库
从上图可以得知,能造成机壳刮伤的制程主要为红色框 内的工位
D1→D2→ D3 →D4(初步分析 &暂时对策)→D5 →D6 →D7 → D8
设点记录数据
主要问题集中区
组装+老化+包装的图片
组装最后一站 数据采集点1
备注:线长每天带领对应产线组长和IPQC组长按次查核表巡线,所有人员/物料符合所描述的情况,划V,如不符合划X
D1(问题描述)→D2 → D3→D4 →D5 →D6 →D7 → D8
What: 机壳刮伤
When: 9月 Who: P7线组装段人员,老化房人员、包装段人员与维修人员 Where: P7线组装段、老化、包装段与维修 How many:机壳刮伤不良率6.1%(2875/47500)
How much: 2875*5=14375RMB(按一个机壳5元计算)
Before After
铁丝网外露
因老化缩水变短,使用绑 线将静电皮固定,尽可能 将外边的铁丝网盖住
D1→D2→ D3 →D4→D5 (根本原因 &长期对策)→D6 →D7 → D8 栈板存放时分隔纸板有钉
Before After
摆栈板的纸皮上有钉子
对待老化或者是带包装 的栈板摆放的纸皮不允 许有钉子
是 是 是 是 是 是 是 是 是 是 是 是 是 是
D1→D2→ D3 →D4→D5 (根本原因 &长期对策)→D6 →D7 → D8 线体铝边外露
Before After
传送带金属框架裸露
已更换新静电皮
D1→D2→ D3 →D4→D5 (根本原因 &长期对策)→D6 →D7 → D8 老化房胶皮变硬
圆孔 变形
老化 变硬 老化房 胶皮 铁丝网
隔板
外露
有异物 周转车 皮带线接口 裸露 流水线 皮带
锡渣 皮带上有异 物 有钉 剪钳 分隔纸板 放置不规范
机壳 刮伤
来料不良 机壳 薄且小 包装袋
Material
工作台面 数量 随意(有多有少) 在制品→D4→D5 (根本原因 &长期对策)→D6 →D7 → D8
200
2.0%
6.1% 4.3% 3.4% 2.9% 2.3% 2.3% 2.0%
1.8%
9月
10月
11月
WO849 WO850 W0851 WO852 WO853
D1→D2→ D3 →D4→D5→D6 →D7 → D8(水平展开及标准化) 日常稽核表
机壳刮伤巡线问题查核表
日期:________
NO.
12.18 12.19 12.2 12.22 合计
1
0 0 0 1 46
1
0 0 1 0 8
6
3 10 1 5 64
1
0 13 0 0 20
0
0 0 0 0 2
0
2 1 2 1 12
结论:造成组装外观刮伤的主要区域是:下底、A面与面盖,是重 点改善对象。
D1→D2→ D3 →D4(初步分析 &暂时对策)→D5 →D6 →D7 → D8
用脚垫区隔
D1→D2→ D3 →D4→D5 (根本原因 &长期对策)→D6 →D7 → D8 摆机员工作业时动作不规范
Before After
手拿着线材放置没保证
手握住上端再放置
D1→D2→ D3 →D4→D5 (根本原因 &长期对策)→D6 →D7 → D8 在制品包装袋薄且小