陶瓷胶态注射成型技术

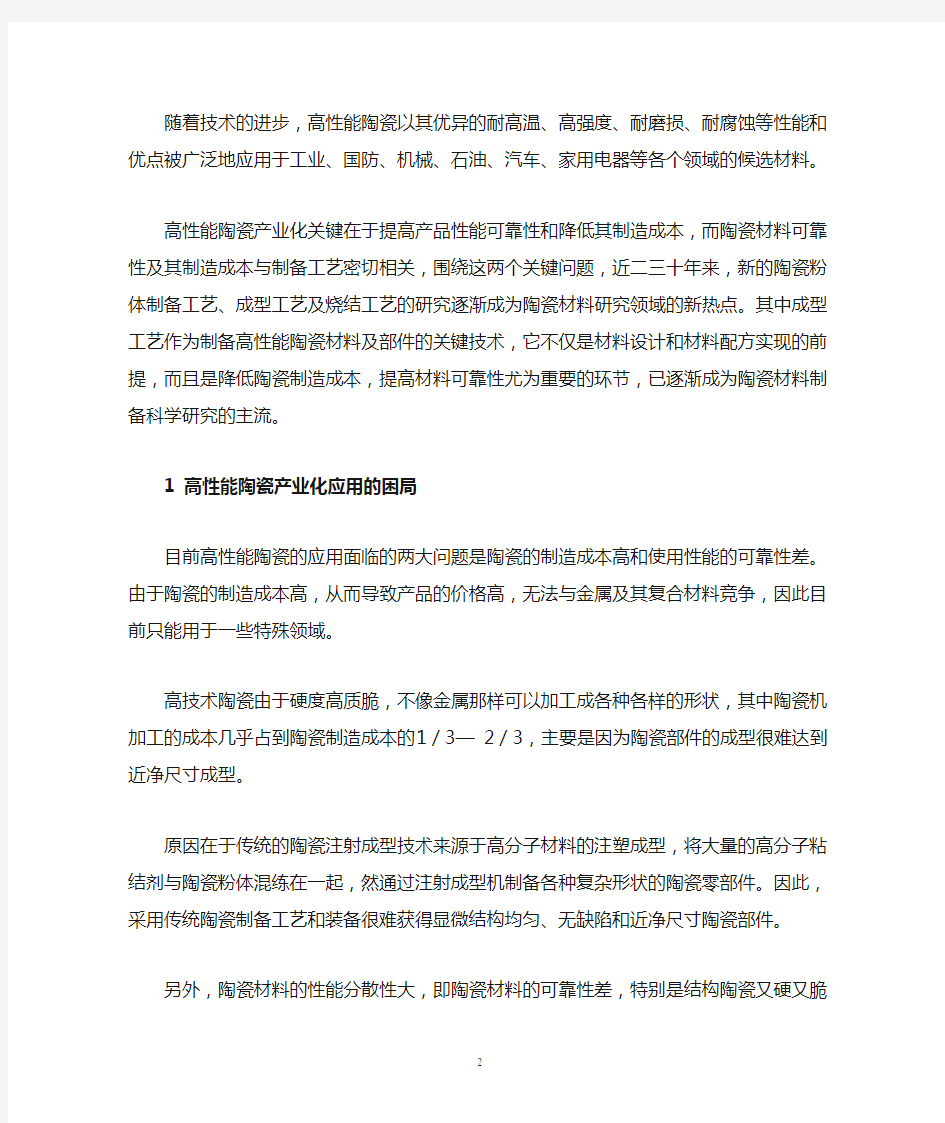
陶瓷胶态注射成型技术
摘要:结合注射成型和凝胶注模成型技术的优点,发明了陶瓷胶态注射成型技术,实现了水基非塑性浆料的注射成型。经过研究表明:通过调节工艺中的各项参数和添加适当的助剂,可以实现陶瓷浆料的可控固化;加入应力缓释剂调节高分子网络结构,能有效降低坯体中的内应力,制备出大尺寸陶瓷部件;利用胶态注射成型技术与设备,不仅能实现规模化大批量生产,而且产品具有较高的可靠性,具有广阔的应用前景。
关键词:胶态注射成型;水基非塑性浆料;可控固化;内应力;应力缓释剂
Colloidal Injection Molding of Ceramics
Abstract:Colloidal injection molding of ceramics(CIMC) is a new ceramic forming technique,which combines the advantages of gel-casting and injection molding, to achieve a non-plastic water-based slurry injection.After the study show that;all kinds of lectors which effect solidification of slurry is studied and then we can control solidification course.Internal stress of green body is also studied and large-size ceramic component can be got by adding moderator.So high performance ceramics with complex shape is manufactured by CIMC technique with high reliability,high automation and low cost.
Key words:colloidal injection molding;injection molding;controllable solidification;stress;stress release agent
引言
随着技术的进步,高性能陶瓷以其优异的耐高温、高强度、耐磨损、耐腐蚀等性能和优点被广泛地应用于工业、国防、机械、石油、汽车、家用电器等各个领域的候选材料。
高性能陶瓷产业化关键在于提高产品性能可靠性和降低其制造成本,而陶瓷材料可靠性及其制造成本与制备工艺密切相关,围绕这两个关键问题,近二三十年来,新的陶瓷粉体制备工艺、成型工艺及烧结工艺的研究逐渐成为陶瓷材料研究领域的新热点。其中成型工艺作为制备高性能陶瓷材料及部件的关键技术,它不仅是材料设计和材料配方实现的前提,而且是降低陶瓷制造成本,提高材料可靠性尤为重要的环节,已逐渐成为陶瓷材料制备科学研究的主流。
1 高性能陶瓷产业化应用的困局
目前高性能陶瓷的应用面临的两大问题是陶瓷的制造成本高和使用性能的
可靠性差。由于陶瓷的制造成本高,从而导致产品的价格高,无法与金属及其复合材料竞争,因此目前只能用于一些特殊领域。
高技术陶瓷由于硬度高质脆,不像金属那样可以加工成各种各样的形状,其中陶瓷机加工的成本几乎占到陶瓷制造成本的1/3— 2/3,主要是因为陶瓷部件的成型很难达到近净尺寸成型。
原因在于传统的陶瓷注射成型技术来源于高分子材料的注塑成型,将大量的高分子粘结剂与陶瓷粉体混练在一起,然通过注射成型机制备各种复杂形状的陶瓷零部件。因此,采用传统陶瓷制备工艺和装备很难获得显微结构均匀、无缺陷和近净尺寸陶瓷部件。
另外,陶瓷材料的性能分散性大,即陶瓷材料的可靠性差,特别是结构陶瓷
又硬又脆既难加工又容易产生突发性的断裂,因而导致高技术陶瓷的制造成本高、性能离散性大、产品生产再现性和使用性能可靠性差等。
使许多领域不敢涉足陶瓷产品。如果上述两个问题不解决,高性能陶瓷的市场就很难打开局面。
2 陶瓷注射成型技术的发展
陶瓷注射成型技术来源于高分子材料的注塑成型,借助高分子聚合物在高温下熔融、低温下凝固的特性来进行成型的,成型之后再把高聚物脱除。比传统的陶瓷加工工艺要简单的多,能制造出各种复杂形状的高精度陶瓷零部件,且易于规模化和自动化生产。
起初的陶瓷成型注射技术是将大量的高分子树脂与陶瓷粉体混在一起后得到混合料,然后装入注射机于一定温度注入模具,迅速冷凝后脱模而制成坯体[1~3]。该技术适合制备湿坯强度大,尺寸精度高,机械加工量少,坯体均一的产品,适于大规模生产。对形状复杂、厚度较薄产品的制备有着明显的优越性。但是由于含有大量的高分子粘结剂,使陶瓷坯体的脱脂成为不可逾越难题,并且有毛坯易变形,容易形成气孔等缺点。
陶瓷注射成型使用的有机载体包括粘接剂、增塑剂、润滑剂等。有机载体的选择重点考虑:体系内的相容性;注射悬浮体的流变特性;脱模特性与生坯强度。通常有机载体与陶瓷粉体混合后的结合强度主要取决于热塑性树脂高聚物;脱脂特性亦可由耐热性好的高聚物调节;可塑剂和润滑剂可改善体系流动性及脱模性能;表面活性剂具有综合调节作用。
在熔体注射充模冷凝形成坯体的过程中,坯体内产生的应力有两种,即温度应力和成型应力。对异型、大尺寸坯体的注射参数和充模过程的研究表明,过高的注射压力和注射温度使坯体内产生较大的成型应力和温度应力,增大了坯体变形和开裂的危险性。
由于注射成型加入大量有机载体,烧结前必须将其排除,即进行脱脂。脱脂耗时较长,容易使坯体产生缺陷。因此,脱脂是注射成型工艺的关键。影响脱脂过程的因素主要有:气氛、压力和温度制度。惰性气氛可避免有机物的氧化分解。一定的气氛压力,可缩小有机物挥发及分解产生的有效体积,从而减少由于体积膨胀引起的坯体开裂。另外,脱脂速率也直接受温度影响。在坯体软化,内部尚未形成气孔通道的温度段l50~300℃,升温速率必须严格控制。否则,坯体易发生变形、产生鼓泡及开裂等缺陷[4]。
为了避开陶瓷注射成型技术使用大量高分子粘结剂的缺点,九十年代后陶瓷成型技术的研究逐渐转向含有少量有机物的水基胶态成型技术的研究,新的成型技术不断涌现,如美国橡树里国家实验室发明的凝胶注模成型工艺、瑞士联邦理工大学发明的直接凝固注模成型技术等等。总之,2l世纪在非塑性水基浆料的胶态成型方面取得了很大进展。
3 陶瓷胶态注射成型技术新工艺
陶瓷胶态注射成型新工艺是把胶态成型和注射成型结合起来的“陶瓷胶态注射成型新工艺”,即水基非塑性浆料的注射成型。它是将低粘度、高固相体积分数的水基陶瓷浓悬浮体注射到非孔模具中,并使之原位快速固化,再经烧结,制得显微结构均匀、无缺陷和近净尺寸的高性能、高可靠性的陶瓷部件。该系由美国Allied Signal公司的研究人员发明,然后又经过一些研究中心的改进,得
到了发展和推广[5]。琼脂和琼脂糖常被用作水溶性有机载体,它能通过温度的变化而固定成型。琼脂糖由2种不同的糖分子交替组成,聚合物骨架上的羟基和水分子之间能形成氢键。水溶性浆料包括下列组分:陶瓷粉体、水、琼脂或琼脂糖、分散剂、润滑剂。最重要的步骤是注射成型前陶瓷悬浮体的分散,这一步通常是由加入分散剂进行球磨而实现。琼脂的用量被限制在质量分数1%~2%。再多的用量会增加陶瓷悬浮体的粘度。陶瓷悬浮体的固相体积分数不超过50%。注射后,有机体在模具中转变为胶态,提供给产品一定的强度。水在一般的炉子中会很容易地除去,也可用微波进行干燥。干燥后的坯体不用进行脱脂而能直接进行烧结。AIM技术可以很容易的实现自动控制,比起传统的注射成型来降低了成本。
陶瓷的胶态注射成型新工艺实现了水基瘠性料浆的注射成型。此前,胶态成型制备高性能陶瓷复杂部件主要经历了以下几个发展阶段:注浆成型、注射成型、胶态原位凝固成型。注浆成型利用瘠性料浆在石膏模中失水固化的机理来制备复杂陶瓷部件,这就使得操作时间比较长,而且坯体密度低、强度差,不适合制备高性能的陶瓷材料。注射成型可成型尺寸精度高、形状复杂的陶瓷部件,且易于自动化和规模化生产。但是该工艺需要添加大量有机物,使得排胶始终是制约其应用的一个关键环节,至今尚未完全突破。旨在提高陶瓷坯体均匀性和解决陶瓷材料可靠性,胶态原位凝固成型工艺应运而生,如凝胶注模成型和直接凝固成型。这些新工艺虽然避免了注射成型有机物含量高的缺点,但是仍然属于手工操作的范畴,自动化程度低,还不能满足高性能陶瓷大规模生产的要求。
陶瓷的注射成型与胶态成型的主要差别在于前者属于塑性成型的范畴,后者属于浆料成型,即浆料没有可塑性,是瘠性料。胶态成型由于浆料没有塑性,无法采用传统的陶瓷注射成型的思路。如果胶态成型同注射成型相结合,即利用专有的注射设备与胶态原位成型工艺所提供的新型固化技术,实现陶瓷材料的胶态注射成型。这一新工艺,既区别于一般的胶态成型,又区别于传统的注射成型,将既具有胶态原位凝固成型坯体均匀性好,有机物含量低的特色,又具有注射成型自动化程度高的优点,是胶态成型工艺的一种质的升华,将成为高技术陶瓷走向产业化最有潜在前景的途径之一,如图1[6]
图 1
4 陶瓷浆料的可控固化
陶瓷胶态注射成型必须解决以下两个重要的关键技术:陶瓷浓悬浮体的快速原位固化和注射过程的可控性。通俗而言即浆料在注射之前不能固化,流动性和稳定性良好,注射充模之后要实现快速原位固化,其关键之处是陶瓷浆料的可控
固化,能够找到一个很容易控制因素,如浆料的成分、压力、温度等。这就要求我们仔细研究影响浆料固化的各种因素,以达到可控固化的目的。
4.1 影响固化过程的内部因素
陶瓷浆料是一个复杂的多相体系,包括陶瓷粉体、分散剂、有机单体、交联剂、无机离子等成分,它们对聚合过程都有一定的影响。可以通过调节陶瓷浆料中这些化学物质,对固化过程进行调控,故而称它们为影响固化的内部因素。
通常陶瓷粉体都含有不同程度的可溶性杂质离子。其中还原性离子,如Fe2+,SO2-;与引发剂发生氧化还原反应,会显著加速引发剂的分解,缩短聚合诱导期。而Fe3+,Cu2+等高价离子,则会对聚合反应起到阻聚作用,延长诱导期。
4.2 影响固化过程的外部因素
在胶态注射工艺中,为了实现陶瓷浆料的可控固化,必须调整各项工艺参数和助剂。引发剂、催化剂的加入量,固化温度和压力,盛装浆料的容器材料和加入的阻聚剂都会影响浆料的固化过程。同时通过它们可以实现浆料的可控固化,因此将它们称为影响固化的外部因素。
引发剂和催化剂的加入量是控制浆料固化过程的主要因素之一。随着加入的引发剂浓度的升高,引发速率加快,聚合诱导期随之缩短,二者大致呈线性关系。当引发剂加入量过少(小于0.25 mmol/L时),由于溶于浆料中的氧阻聚,聚合反应不完全,坯体质量很差。如果不加入催化剂,仅加入引发剂,浆料可以稳定很长时间而不发生固化;加入催化剂后,引发剂分解活化能降低导致引发剂分解速率常数增大,加快了自由基生成速率,浆料的聚合诱导期变短;随催化剂加入量的增大,陶瓷浆料能在很短时间内完成固化。
图 2 同温度、压力条件对氧化铝浆料固化过程的影响
温度和压力同样对浆料固化有巨大影响。图2[7]显示体积分数为40%的Al
2O
3。
陶瓷浆料在不同温度和压力情况下的固化过程。由图中可以看出,固化温度升高,聚合诱导期缩短,反应速度加快。如常压下浆料的诱导期从固化温度25℃时的21min降低到固化温度为36℃时的4 min,降低了5倍左右。因此,温度能够促进凝胶反应的进行,缩短诱导期。在不同的固化温度下,随着反应外加压力的增加,
固化过程均呈加速趋势,如在固化温度25℃下的诱导期从常压时的21min降低到压强为83MPa时的9min,反应期从常压时的9min降低到压强为83MPa时的5min[8]。因此,外加压力能够促进凝胶反应的进行,缩短诱导期,增大聚合速率。在实际操作中,利用温度和压力的综合作用,可以有效地控制浆料的固化过程。在适当的压力和温度下,可使固化反应能在短时间内迅速完成。外加压力易于控制,且可控范围大,不会在浆料内产生梯度,因而更易于实现浆料固化的可控性。
5 内应力的产生与消除
胶态注射成型工艺与传统的注射成型相比,明显提高了坯体的密度均匀性。传统注射成型密度分布的标准离差为0.7%,而胶态注射成型的离差仅为0.2%。但胶态注射成型的坯体仍有可能在排胶阶段开裂。这主要是由于胶态注射成型工艺采用有机单体聚合的固化机制,在陶瓷浆料凝胶固化以及生坯干燥过程中,坯体各部分收缩不一致就可能产生内应力,内应力在后续的排胶或烧结过程释放出来就会造成坯体的宏观开裂,因而密度均匀的陶瓷坯体也可能因为坯体内的残余应力而在后续工艺中开裂。
胶态注射成型中,陶瓷坯体内的残余应力主要缘自于不同步固化产生的内应力。陶瓷浆料不同步固化主要是由于浆料中存在温度梯度所引起的。温度梯度在温度诱导陶瓷浆料固化的过程中普遍存在。所谓温度诱导固化,就是将陶瓷浆料注入热模具中,借助模具提供的热量,引发陶瓷浆料发生凝胶化反应。冷的浆料注入热模具中,势必使模具腔内存在温度分布上的梯度,尤其是成型大截面部了一个由外向内的传递过程。由于固化过程伴随收缩,内应力就在这种固化推移过程中产生。浆料注入模具后,近模具壁处的浆料首先固化,内部后固化的部分其收缩受到外部先固化部分的限制,因此坯体内层呈拉应力状态,外层呈压应力状态。在胶态注射成型工艺中,由于陶瓷浆料的固相含量较高,脱模后陶瓷湿坯的收缩并不显著(一般小于1%),而且湿坯的弹性模量也比较小(为10-1MPa的量级),但坯体在干燥过程中会有3%~4%的线收缩率,而且随着干燥的进行,坯体的弹性模量逐渐增大,干坯的弹性模量可达GPa量级,这就使得在固化阶段遗留下来的内应力会在干燥阶段进一步发展,形成可观的内应力。由于高分子链的联结作用,在干燥过程中一般不会出现材料的宏观破坏,但由于坯体中心部位经常有较大的残余拉应力,因而,在排胶过程中,当高分子链断裂后,内应力就会释放出来,产生放射状裂纹[9]。
为了降低坯体中的残余应力,获得性能良好的陶瓷坯体,许多研究者从陶瓷坯体中缺陷产生、遗传和变异的角度,寻求控制和消除陶瓷坯体内部缺陷的有效手段,经过大量的实验证明在胶态注射成型浆料体系中,引入应力缓释剂,可使固化后的高分子网络得到调节,可以有效地改进胶态注射成型工艺。
6 陶瓷胶态注射成型的创新点
陶瓷胶态注射成型新工艺是将低粘度、高固相体积分数的水基陶瓷浓悬浮体注射到非孔模具中,并使之原位快速固化,再经烧结,制得显微结构均匀、无缺陷和近净尺寸的高性能、高可靠性的陶瓷部件,并大大降低陶瓷制造成本。
经过多年的研究攻关,制备的陶瓷材料与制品的性能达到:坯体密度均匀(密度分布差小于0.5%)、坯体强度高(抗弯强度在20~30MPa)、易于加工;烧结后产品性能优异:氮化硅基陶瓷产品性能,抗弯强度大于900MPa,韦伯尔模数m稳定在20以上,最高可达到33;氧化铝基陶瓷抗弯强度700MPa,韦伯尔模数m大于
15(从部件上取样的试件)。
6.1 实现了陶瓷非塑性水基浆料的注射成型
陶瓷非塑性水基浆料的注射成型避免了使用大量有机物造成的脱脂难题,可以近净尺寸成型各种复杂形状的陶瓷零部件,产品均匀性好,批次稳定性高,烧结变形小,是一种理想的陶瓷制备技术。
6.2 压力诱导陶瓷非塑性水基浆料的快速原位成型
陶瓷胶态注射成型解决了两个重要的关键技术:陶瓷浓悬浮体的快速原位固化和注射过程的可控性[10]。通过深入研究发现压力可以快速诱导陶瓷浓悬浮体的原位固化,从而发明了压力诱导陶瓷成型技术,这一原创性的重大发现为该技术走向规模化生产和商品化奠定了坚实的基础。
7 新旧陶瓷成型工艺比较
7.1 陶瓷业现有的制造工艺见图3[11]所示
图 3
7.2陶瓷胶态注射成型新工艺见图4[11]所示
图 4
8 结论
通过胶态注射成型技术,可以获得高密度、高均匀性和高强度的陶瓷坯体,这种成型技术可以消除陶瓷粉体颗粒的团聚体,减少烧结过程中复杂形状部件的变形、开裂,从而减少最终部件的机加工量,获得高可靠性的陶瓷材料与部件。
陶瓷胶态注射成型新工艺是一种较为理想的净近尺寸成型技术,避免了传统陶瓷注射成型使用大量有机物所导致的排胶困难,实现了胶态成型的注射过程。适合于规模化生产,是高技术陶瓷产业化的核心技术。
参考文献
[1] Nyborg L; Carlstrom E Guide to injection molding of ceramics and hard metals: special
considerationof fine powder,1998(01).
[2] Okada K Viscosity and powder dispersion in ceramic injection molding mixture ,2000(01).
[3] YANG J; Su L; Ma L Colloidal Injection Molding of Ceramics,2002(224/226).
[4] GaucklerLJ; Graule T J; Baader F H Ceramic Forming Using Enzyme Catalyzed Reactions,
1999.
[5] Yang Jinlong; SU Liang; MA Liguo Colloidal injection molding of ceramics,2002.
[6] 黄勇,龙月洋.高性能陶瓷创新工艺-陶瓷胶态注射成型技术[J].中国陶瓷,2006,42(5).
[7] 苏亮,杨金龙,马利国,戴春雷,黄勇.压力诱导陶瓷胶态注射成型新工艺[J].稀有金属
材料与工程,2002,31(1).
[8] 杨金龙,戴春雷,苏亮,黄勇.陶瓷胶态注射成型中压力的影响[J].硅酸盐学报,2004,32(6).
[9] 杨金龙,马利国,马天,黄勇.陶瓷胶态注射成型液固转变过程中内应力产生机制初探
[J].真空电子技术,2003(4).
[10] 杨金龙,戴春雷,马天,马利国,黄勇高.可靠性陶瓷部件胶态注射成型关键技术及装
备[J].中国有色金属学报,2004(14).
[11] 颜鲁婷,司文捷,苗赫濯.陶瓷成型技术的新进展[J].现代陶瓷技术,2002,23(1).
浅谈橡胶注射成型技术发展
目录 摘要 (1) ABSTRACT (2) 引言 (3) 1 橡胶注射成型技术发展概况 (3) 1.1橡胶注射成型简介 (3) 1.2橡胶注射成型发展历史 (4) 1.2.1 技术移植阶段 (4) 1.2.2 技术成熟阶段 (5) 1.2.3 发展创新阶段 (5) 2 几种常见的橡胶注射成型设备 (6) 2.1橡胶注射成型机种类及成型方法 (6) 2.1.1 柱塞式注射成型机 (6) 2.1.2 螺杆往复式注射成型机 (7) 2.1.3 螺杆柱塞式注射成型机 (8) 2.2螺杆柱塞式注射机主要装置结构和性能特点 (9) 2.2.1 预塑注射装置 (9) 2.2.2 合模装置 (10) 2.2.3 液压驱动及控制系统 (11) 3 橡胶注射成型设备发展前景 (14) 3.1国内橡胶注射机技术状况 (14) 3.2成型工艺与设备革新的注射成型 (15) 3.2.1 低压注射成型 (15) 3.2.2 振动技术在注射成型中的应用 (16) 3.2.3 共注射成型 (16) 3.2.4 磁场定向注射成型 (17) 3.2.5 叠层式注射成型 (17)
3.3橡胶注射成型设备的发展趋势 (18) 结论 (19) 致谢 (20) 参考文献 (21)
摘要 橡胶注射成型硫化机简称橡胶注射机或注压机,为工业橡胶模制品中三大成型硫化机种之一。主要应用于生产汽车配件、工业配件、电气绝缘零件、连接器插座、密封件、减震垫、防震罩、鞋、瓶塞、吸尘软管、护套、气门嘴垫、玩具和健身器具等。随着汽车工业发展,对密封件、电气连接器、减震器等的质量要求越来越高,橡胶注射制品的需求量增加了1.2万倍以上,强劲的市场需求为橡胶注射机的发展提供了契机。 本文从橡胶注射成型技术发展概况出发,介绍了几种常见的橡胶注射成型机,并对橡胶注射成型设备发展应用前景进行了阐述。 关键词:注射成型;注射机;橡胶制品
陶瓷胶态注射成型技术
陶瓷胶态注射成型技术 摘要:结合注射成型和凝胶注模成型技术的优点,发明了陶瓷胶态注射成型技术,实现了水基非塑性浆料的注射成型。经过研究表明:通过调节工艺中的各项参数和添加适当的助剂,可以实现陶瓷浆料的可控固化;加入应力缓释剂调节高分子网络结构,能有效降低坯体中的内应力,制备出大尺寸陶瓷部件;利用胶态注射成型技术与设备,不仅能实现规模化大批量生产,而且产品具有较高的可靠性,具有广阔的应用前景。 关键词:胶态注射成型;水基非塑性浆料;可控固化;内应力;应力缓释剂 Colloidal Injection Molding of Ceramics Abstract:Colloidal injection molding of ceramics(CIMC) is a new ceramic forming technique,which combines the advantages of gel-casting and injection molding, to achieve a non-plastic water-based slurry injection.After the study show that;all kinds of lectors which effect solidification of slurry is studied and then we can control solidification course.Internal stress of green body is also studied and large-size ceramic component can be got by adding moderator.So high performance ceramics with complex shape is manufactured by CIMC technique with high reliability,high automation and low cost. Key words:colloidal injection molding;injection molding;controllable solidification;stress;stress release agent 引言 随着技术的进步,高性能陶瓷以其优异的耐高温、高强度、耐磨损、耐腐蚀等性能和优点被广泛地应用于工业、国防、机械、石油、汽车、家用电器等各个领域的候选材料。 高性能陶瓷产业化关键在于提高产品性能可靠性和降低其制造成本,而陶瓷材料可靠性及其制造成本与制备工艺密切相关,围绕这两个关键问题,近二三十年来,新的陶瓷粉体制备工艺、成型工艺及烧结工艺的研究逐渐成为陶瓷材料研究领域的新热点。其中成型工艺作为制备高性能陶瓷材料及部件的关键技术,它不仅是材料设计和材料配方实现的前提,而且是降低陶瓷制造成本,提高材料可靠性尤为重要的环节,已逐渐成为陶瓷材料制备科学研究的主流。 1 高性能陶瓷产业化应用的困局 目前高性能陶瓷的应用面临的两大问题是陶瓷的制造成本高和使用性能的 可靠性差。由于陶瓷的制造成本高,从而导致产品的价格高,无法与金属及其复合材料竞争,因此目前只能用于一些特殊领域。 高技术陶瓷由于硬度高质脆,不像金属那样可以加工成各种各样的形状,其中陶瓷机加工的成本几乎占到陶瓷制造成本的1/3— 2/3,主要是因为陶瓷部件的成型很难达到近净尺寸成型。 原因在于传统的陶瓷注射成型技术来源于高分子材料的注塑成型,将大量的高分子粘结剂与陶瓷粉体混练在一起,然通过注射成型机制备各种复杂形状的陶瓷零部件。因此,采用传统陶瓷制备工艺和装备很难获得显微结构均匀、无缺陷和近净尺寸陶瓷部件。 另外,陶瓷材料的性能分散性大,即陶瓷材料的可靠性差,特别是结构陶瓷
陶瓷凝胶注模成型
凝胶注模成型工艺研究 夏培 (天津大学材料科学与工程学院,教育部先进陶瓷与加工重点实验室,天津300072) 摘要:凝胶注模成型是一种优于传统成型工艺的先进陶瓷成型方法,为净尺寸高性能复杂形状陶瓷的制备提供了有效的技术途径。本文对陶瓷凝胶注模成型的原理、工艺、成型体系、特点等进行了简单的概论介绍,综述了目前凝胶注模成型的研究现状、存在的问题和应用情况并展望了发展趋势。 关键词:凝胶注模;研究现状;问题与展望 Study on the gel-casting XIA Pei (Key Laboratory of Advanced Ceramics and Machining Technology, Ministry of Education, college of Material Science and Engineering, Tianjin University, Tianjin 300072, Tianjin, China) Abstract: Gel-casting process is an advanced manufacturing technology for ceramic forming, which is superior to the traditional one, and has provided an effective approach to prepare high performance net size ceramics with complicated shapes. The principles,procedures,forming system and character of gel-casting are simply discussed in this paper, moreover, the present research process,problems as well as applications are also included. Finally, the tendency of this technology is forecasted in a dialectical way. Key words: gel-casting; present research; problems and prospects
LSR(注射成型)最新技术详解-精
注射成型LSR的最新进展 在这一制品中,,用作滤 图1热塑性塑料/LSR包覆成型的一个应用是水龙头滤网 包覆成型的一个应用是水龙头滤网。。在这一制品中 网的LSR被包覆成型到尼龙66上 得益于材料、设备和工艺的改进与革新,液态硅橡胶(LSR)逐渐摆脱了小众需求的现状,扩大了应用领域。其中,大型、微型和发泡制品,以及多色或多材料的组合是LSR应用的新领域。 液态硅橡胶(LSR)对于注塑加工商的商业机会的拓宽,要归功于更新的成型工艺,如发泡、多色或者多硬度注射,以及热塑性塑料/热固性塑料包覆技术的涌现。材料、设备和模具的改进增加了产品的多功能性,提高了产品质量,降低了注塑加工商准入的门槛。
今天的LSR注塑加工商拥有更多的原材料选择、更大的模具选择余地以及更好的工艺技术,不但可以成型小至数千分之一g的制品,而且也能够加工32kg以上的巨大产品。 材料、模具和加工设备供应商表示,在过去的几年里,对LSR感兴趣的人逐渐增加。“一些塑料公司对此感兴趣,一些新公司也希望开拓他们的业务,同时医疗领域的加工商也更多地加入进来。”Roembke Mfg.&Design模具公司副总裁Greg Roembke说。“我们发现,汽车工业已开始应用LSR。也许传统的硅橡胶在汽车工业中的应用已达到了极致,下一步需要从LSR获得更多的东西。”他补充说。 图2LSR的双注射包覆成型通常在一个成型单元内完成, 而LSR和热塑性塑料则分别在不同的注射机上成型 LSR注塑加工商表示,他们已经从高温硅橡胶(HCR)、EPDM、乳胶、天然橡胶、TPE、PVC甚至陶瓷的应用领域中抢占了一些市场。Momentive Performance Materials(前GE Silicones)的弹性体和RTV总经理Bill French说,由于LSR惰性、耐热且耐化学品,因此可用于生产奶嘴和奶头、医用装置阀门或密封条、医疗植入体、医用手套和汽车密封条
全自动橡胶注射硫化成型机操作规程
编号:SM-ZD-97526 全自动橡胶注射硫化成型 机操作规程 Through the process agreement to achieve a unified action policy for different people, so as to coordinate action, reduce blindness, and make the work orderly. 编制:____________________ 审核:____________________ 批准:____________________ 本文档下载后可任意修改
全自动橡胶注射硫化成型机操作规 程 简介:该规程资料适用于公司或组织通过合理化地制定计划,达成上下级或不同的人员之间形成统一的行动方针,明确执行目标,工作内容,执行方式,执行进度,从而使整体计划目标统一,行动协调,过程有条不紊。文档可直接下载或修改,使用时请详细阅读内容。 1. 目的 确保操作人员正确使用设备,保证安全正常生产。 2. 使用范围 (QH系列)全自动橡胶注射硫化成型机操作。 3. 职责 操作员必须遵守本文件的规定和要求。车间负责人对本文件的实施进行监督。 4. 工作程序 4.1开机准备、检查 4.1.1 检查机台的清洁润滑、冷却状态良好,各活动部位无障碍物。 4.1.2 检查电热系统,液压系统,电气系统运行正常.手动或自动状态下,各操作是否正常。
4.1.3 检查安全开关,安全电眼,紧急停止开关等正常有效。 4.1.4 检查模具腔内腔外清洁,模具固定牢固。 4.2 设备参数调整、设定 4.2.1按生产工艺要求,进入人机界面设定加工工艺参数,在试生产过程中进行适当调整。 4.2.2 点击进入界面功能选择菜单,选择注射机自动化生产所需的最优化的新功能。 4.2.3选手动调整模具,须注意注射嘴与模具中心孔的同心度,紧固模具。 4.2.4安装好新模具后,点击进入开关模界面主菜单:先慢速合模重新设定开模总行程和开关模各分段的行程、锁模压力、速度、硫化时间等参数的设定。主缸锁模压力要以模具面积大小而设定。 4.2.5点击注射系统菜单:先设定该模具的注射量,再设定各分段的量程、射出和进料的压力、速度等参数。注意:射出和进料的压力与射出速度要视胶料硬度及韧度来调整。 4.2.6点击推脱模系统菜单:先设定该模具的进退模、脱
液体硅橡胶(LSR)注射成型工艺的设计
液体硅橡胶(LSR)注射成型工艺的设计 在过去的三到五年里,热固性液体硅橡胶(LSR)的注塑技术得到了快速的发展。LSR的注塑设计与刚性工程热塑料有着重要的差别,这主要是因为这两种橡胶的物理性质,如低粘度,流变学性质(快速固化),剪切变稀性质,以及较高的热膨胀系数等区别较大。 由于LSR的粘度较低,因此它在注射成型过程中,即使在注射压力较低的情况下,填充流速也可以较快,但是为了避免空气滞留,对模具通风的要求更加严格。总的来说,现代LSR的快速硫化的循环时间更短(某些情况下循环时间不到20秒),为了充分利用这一特性,加工机械、注射成型机以及部件转移系统等必须相互配合,作为一个高度集成的整体运作。 冷流道成型 现代冷流道体系充分利用了LSR剪切变稀的性质,真正达到了无浪费,无毛边成型。在过去的三到五年里,冷流道模塑在制造业中的优势地位急速上升,并导致橡胶产品的产量增加、废品减少、劳动成本降低等良好的势头。 LSR不会在模具中收缩,这一点和热塑性塑料类似。但是由于膨胀系数较高,加热时会发生膨胀,冷却时却仅有微小的收缩。因此,部件通常不能在模具中保持准确的侧边距,只有在表面积较大的空腔中才可以保持。 与热流道模塑相似,在冷流道加工中,热固LSR应保持较低温度和可流动性,以确保没有物料的损失。这种加工方法最适用于在清洁的室内环境中生产大小、结构相似的大体积部件。理想模型是在人为因素影响最小的设备中昼夜不停的运转,并逐步增大运转周期(日或周)。 目前所用的冷流道设备有两种基本类型,即闭合系统和开放系统,它们各有优缺点。注射循环中,闭合系统在每一个管道中都采用“开动销”或“针形阀”来控制LSR橡胶的流量。而开口系统则根据注射压力的大小,利用“收缩嘴”和阀门来控制物料的流量。 与开口系统相比较,闭合系统最典型的特点是在较低的注射压力下进行注塑。设备中可调控的“节流口”可以对不平衡的分流道以及物料的不同剪切变稀性能进行微调。缺点是对某些给定大小的部件和模具,设备需作额外的调整。 开放系统利用通过喷嘴或者阀门的高剪切速率,在注射压力降低时,进行截流。一般情况下,开放系统的空腔填充时间要比闭合系统稍微短一些。开放系统由于分流道和喷嘴较小,空腔密度较高。分流道则要求自然平衡,并与物料本身的流变性能严格匹配。因为开放系统的流道尺寸较小,所以通常不用可调“节流口”,只需普通阀门就可以很好的控制流量,并获得最佳的压力点。 分模线 设计液体硅橡胶注射成型模具时,首先要考虑分模线的位置,因为分模线内部需设置一些通道,利用这些通道完成通风任务,通风孔必须设置在注射物料最后到达的模具末端。预先考虑以上因素,有助于避免空气的夹带和焊接线边缝强度的损失。
新型陶瓷成型方法
新型陶瓷成型方法——凝胶注模成型 宋任娇 08120188 一.前言 随着陶瓷工业的发展及其在现代工业领域中应用的不断扩大,对陶瓷成型方法的要求也越来越高,上述传统陶瓷成型工艺由于存在不同的缺点,已难以满足工艺要求,为满足航天、汽车、电子、国防等行业的市场需求[1],人们要求采用高性能陶瓷的成型方法所成型的坯体应当具有高度均匀性、高密度、高可靠性以及高强度,并在形状的复杂程度上要求更高。因此,陶瓷原位凝固成型技术便应运而生了。 原位凝固胶态成型[3,2]就是指颗粒在悬浮体中的位置不变,靠颗粒之间的作用力或悬浮体内部的一些载体性质的变化,使悬浮体从液态转变为固态。在从液态转变为固态的过程中,坯体没有收缩或收缩很小,介质的量没有改变。在这类成型方法中,首先要制备稳定悬浮的浆料,然后通过各种途径使颗粒之间产生一定的吸引力而相互聚集,形成一个密实的坯体,并保持一定的强度和形状,由此可制成高密度的素坯。原位凝固胶态成型与其它胶态成型工艺之间的区别主要在于凝固技术的不同,这将会导致对浆料性质要求的差异和整个工艺过程的差异。 国内外的陶瓷学者不断总结经验,将胶体化学和表面化学的理论引入到陶瓷浆料的成型技术中,并利用各种物理的辅助手段,在传统的注浆成型的基础之上发展起来了多种新型的胶态成型技术,如:离心注模成型[3]和压滤成型[4]等成型方法。在80年代末90年代初,凝胶注模成型首次使用较低含量的有机物使陶瓷浓悬浮体实现原位凝固,进而在90年代掀起了陶瓷原位凝固胶态成型研究的热潮。 目前,原位凝固胶态成型工艺主要包括:凝胶注模成型工艺(Gelcasting)、直接凝固注模成型(Direct Coagulation Casting)[5]、温度诱导絮凝工艺(TemperatureInduced Flocculation)[6]、胶态振动注模成型(Colloid VibrationCasting)[7]和快速凝固注射成型(Quickset Injection Molding)[8]。 二.凝胶注模成型原理及工艺 凝胶注模成型技术是传统的注浆工艺与有机化学高聚合理论的完美结合,它通过引入一种新的定型机制,发展了注浆工艺。其原理是通过制备低粘度(<1Pa·s)、高固相体积分数(>50vol%)的浓悬浮体,在其中掺入低浓度的有机单体、交联剂,在催化剂和引发剂的作用下,使浆料中的有机单体与交联剂交联聚合成三维网状结构,将大部分水封于网络中而使浆料立即原位凝固,从而使陶瓷坯体原位定型[20]。然后进行脱模、干燥、去除有机物、烧结,即可获得所需陶瓷零件。其原理见图1.1。 该工艺与其它原位凝固胶态成型工艺的相同点是需要制备低粘度、高固相体积分数的浓悬浮体,不同点在于浓悬浮体的凝固技术不同,这将会导致坯体性能的差异[21-24]。 凝胶注模成型分为两类:一种是水溶性凝胶注模成型(aqueous Gelcasting),另一种是非水溶性凝胶注模成型(Non aqueous Gelcasting)[25]。前者适用于大多数陶瓷成型场合,后者主要适用于那些与水发生反应的系统的成型。该技术首先发明的是有机溶剂的非水凝胶注模成型,随后作为一种改进,又发明了用于水溶剂的水凝胶注模成型,并广泛应用于各种陶瓷中,非水溶性凝胶注模成型采用有机溶剂,要求溶剂有较低的蒸汽压。水溶性凝胶注模成型更进一步,有许多优点[26,27]:(1)成型过程与传统方法类似,简便易行;(2)干燥过程更加容易; (3)降低了预混液的粘度;(4)对环境污染小。因此,该方法被广泛应用。
陶瓷注射成型技术
陶瓷注射成型 刘明亮 (武汉理工大学材料学院武汉市湖北省430000) 摘要:陶瓷注射成型是一种近净尺寸陶瓷可塑成型方法,是当今国际上发展最快、应用最广的陶瓷零部件精密制造技术。详细阐述了陶瓷注射成型技术的关健因素,重点介绍了粘结剂、注射成型及脱脂等关健工艺及其研究现状,并在此基础上评价和展望了该技术的发展前景。 关键词:陶瓷注射成型;粘结剂;脱脂;现状 Ceramic Injection Molding Liu mingliang Abstract: Ceramic injection molding (CIM) is a near-net-shape forming process for fabricating ceramic components, which is extensively used in fabricating parts with high precision and complex shape and received great attention now. In this paper, the key steps of CIM are detailedly reviewed. Their research status and the techno1ogies involved including binder,injection process,debinding and so on are discussed. At last, the development of injection molding technology is also evaluated. Keywords:ceramic injection molding; binder; debinding; status 20世纪以来,特别是二次世界大战以后,随着原子能工业的兴起和电子工业的迅速发展,对于材料的高温、高耐磨、多功能等性能要求越来越苛刻,而先进的工程陶瓷所具有的优点基本上能满足上述的苛刻条件。如:高性能结构陶瓷以其优异的耐高温、高强度、耐磨损与耐腐蚀等优良性能,被作为陶瓷发动机零部件的候选材料; 还有许多高导热性、绝缘性能良好、光学性能优良的功能陶瓷,在信息转换、存储、传递和处理方面,应用日益广泛。在未来的产业领域中,工程陶瓷将更广泛的取代现代金属材料,成为材料科学中的重要角色。 在陶瓷材料的制备工艺过程中,成形过程是一个重要环节。成形过程就是将分散体系(粉料、塑性物料、浆料)转变成为具有一定几何形状和强度的块体,也称素坯。由于陶瓷材料本身固有的脆性和一些特殊陶瓷材料的高硬度,如采用传统粉末冶金工艺,即先将粉末压制成形,再进行机械加工的方法,成本高且难以制备体积微小、形状复杂、尺寸精度高的陶瓷零部件,而采用注射成形技术,由于坯体的成形形状接近制品的最终形状,使这一问题得到了解决。特别是对于尺寸精度高、复杂形状陶瓷制品的大批量生产来说,陶瓷的注射成形(Ceramic injection molding,CIM) 更有着显著的优势,它可一次性成形复杂形状制品,产品尺寸精度高,无需机械加工或只需微量加工,易于实现生产自动化且产品性能优异。 陶瓷注射成型技术(CIM)类似于20世纪70年代发展起来的金属注射成型(MIM)技术,它们均是粉末注射成型(PIM)技术的主要分支,均是在聚合物注射成型技术比较成熟的基础上发展而来的,是当今国际上发展最快、应用最广的陶瓷零部件精密制造技术[l,2]。 1 CIM流程路线及技术特点 1.1 注射成型工艺路线
中国橡胶注射成型现状 发展瓶颈及突破
中国橡胶注射成型现状发展瓶颈及突破 2011-11-8 来源:网络文摘 【全球塑胶网2011年11月8日网讯】 随着橡胶工业的发展,橡胶制品成型技术也经历了不同发展阶段:模压阶段、转注阶段、注射阶段及在转注基础上的注射模压、注射转注等。 注射成型已成为橡胶加工主流方式 就橡胶本身的特性来说,注射成型以其独有的优势目前已经成为橡胶制品成型的主流方式。注射工艺就是通过塑化缸的加温和塑化螺杆的搅拌、剪切,将胶料温度升高到其流动性最好的状态,再通过较高的注射压力,将此状态的胶料注射到锁模(抽真空)的模腔中,进行加压和加温,使橡胶进行硫化。在整个过程中,时间、压力和温度三要素决定了生产的效率和质量。 首先,注射成型能够提高制品质量。通过先锁模后注射并进行保压,可以持续稳定的传递制品成型所需要的压力,使制品能够在可控的压力、温度和时间下进行硫化。注射成型能够提高制品的致密性和功能性(尤其是减震制品的功能性)。 其次,注射成型可大幅提高生产效率。通过注射单元的塑化功能,大幅度提高胶料的流动性,使其以比较高的温度充满模腔并立刻开始硫化,通过合理的参数设置,注射工艺可比模压工艺缩短30~50%的硫化时间。 再次,注射成型工艺能够大幅度降低工人劳动强度、减少胶料浪费和电力消耗等。 注射成型现状及发展瓶颈 与国外橡胶注射成型发展现状相比,国内橡胶注射技术目前还处于起步阶段,尽管已可用注射机生产产品,但是相关的工艺研究工作不足。一个典型的例子就是生产过程中大多不设定保压,只是通过注射压力来充满模腔,这就导致了容易在流道产生“大饼”,在制品上产生飞边等。 橡胶注射成型的发展离不开设备厂、模具供应商、制品厂的三方合作,共同推进注射成型应用和发展。但目前在国内来看,这三个环节基本上都是各自独立,缺少融合。 从注射成型机本身来说,目前国内的市场容量大约在4.5亿元人民币左右,年增长率大约在30~40%。目前中国市场有大大小小二十几个橡胶注射机“品牌”,大部分是从最初的台湾机或者大陆机演化而来。通常是注射机厂家找个投资商、照搬一家公司的图纸或在此基础上做些小更改进行制造生产,采用低价或者依靠与设备采购人员的个人关系,进行市场竞争,缺少创新和研发能力,这就导致了设备的技术革新不足,更谈不上研究橡胶注射工艺了。 国内橡胶注射机技术较普遍的问题主要体现在几个方面: 一是大多采用较低的21/22MPa的系统压力,标称300吨的机型,其实际只能提供2600KN的锁模力,锁模力不足;相应的泵、阀都采用比较廉价的日本或者台湾等品牌,容易漏油和损坏,使用寿命不长;液压管路等还使用分体式的阀、管等,容易出现故障并且维修困难。 二是机身结构设计不合理,开模空间不足,模具必须移出后才能在外部开模;导柱的设计不合理,锁紧螺母容易松脱,进而导致热板不平衡,容易造成飞边和“大饼”等。 三是落后的先进后出注射单元,每模都需要先射出大约20~30g的胶料,并且塑化缸的温度较低;清理和更换胶料非常繁琐,需要拆卸等。 实际使用起来,很多机器最致命的弱点就是不稳定,经常会出现各种各样的问题,影响客户使用和生产。另外,相关配套的模具和冷流道能力不足,主要表现在模具结构和概念比较原始、加工制造精度不高和表面处理不合理或干脆不做等。 国内缺乏专业的橡胶模具制造厂商,大部分都是专业做塑料模具,捎带做一些橡胶模具,对橡胶模具的
全自动橡胶注射硫化成型机操作规程(新编版)
( 操作规程 ) 单位:_________________________ 姓名:_________________________ 日期:_________________________ 精品文档 / Word文档 / 文字可改 全自动橡胶注射硫化成型机操 作规程(新编版) Safety operating procedures refer to documents describing all aspects of work steps and operating procedures that comply with production safety laws and regulations.
全自动橡胶注射硫化成型机操作规程(新 编版) 1.目的 确保操作人员正确使用设备,保证安全正常生产。 2.使用范围 (QH系列)全自动橡胶注射硫化成型机操作。 3.职责 操作员必须遵守本文件的规定和要求。车间负责人对本文件的实施进行监督。 4.工作程序 4.1开机准备、检查 4.1.1检查机台的清洁润滑、冷却状态良好,各活动部位无障碍物。
4.1.2检查电热系统,液压系统,电气系统运行正常.手动或自动状态下,各操作是否正常。 4.1.3检查安全开关,安全电眼,紧急停止开关等正常有效。 4.1.4检查模具腔内腔外清洁,模具固定牢固。 4.2设备参数调整、设定 4.2.1按生产工艺要求,进入人机界面设定加工工艺参数,在试生产过程中进行适当调整。 4.2.2点击进入界面功能选择菜单,选择注射机自动化生产所需的最优化的新功能。 4.2.3选手动调整模具,须注意注射嘴与模具中心孔的同心度,紧固模具。 4.2.4安装好新模具后,点击进入开关模界面主菜单:先慢速合模重新设定开模总行程和开关模各分段的行程、锁模压力、速度、硫化时间等参数的设定。主缸锁模压力要以模具面积大小而设定。 4.2.5点击注射系统菜单:先设定该模具的注射量,再设定各分段的量程、射出和进料的压力、速度等参数。注意:射出和进料的
橡胶注射成型技术工艺研究及趋势
龙源期刊网 https://www.360docs.net/doc/015506613.html, 橡胶注射成型技术工艺研究及趋势 作者:孙威 来源:《科技与创新》2016年第22期 摘要:随着我国经济的发展,橡胶注射成型技术已经得到了广泛的应用。橡胶注射成型 技术不仅能够实现橡胶制品的机械化、自动化生产,还能够降低劳动强度,从而有效提高橡胶模压制品的生产效率。所以从橡胶注射成型技术的4个方面阐述了橡胶注射成型技术的发展趋势。 关键词:橡胶;注射成型;机械;供料 中图分类号:TQ330.6+6 文献标识码:A DOI:10.15913/https://www.360docs.net/doc/015506613.html,ki.kjycx.2016.22.028 随着我国制造业的发展,橡胶模制品行业的发展也越来越迅速,并且传统的橡胶注射成型技术已经被新型的橡胶注射成型技术所替代。虽然新型的橡胶注射成型技术的投资成本较高,但是其生产效率和生产质量远高于传统的橡胶注射成型技术。可见,橡胶注射成型技术的发展是十分迅速的。 1 机械 橡胶注射成型技术包括机械、供料、材料和模具4个部分。机械是实现橡胶注射成型生产自动化的关键。就目前来看,橡胶注射成型机械应该具备能够自动控制精确度,进行无胶边成型操作的能力。这样不仅能够省去二次处理步骤,减少工作量,还能够有效缩短成品生产时间。另外,橡胶注射成型机械还应该能够脱模、嵌件、组装,这样才能减少人力投入成本,提高企业经济效益。 从热塑性和热固性弹性体注射成型行业的发展来看,目前很多工程师都是利用热塑性技术来实现橡胶注射成型的。橡胶模制品加工商已经在慢慢实现模压法向卧式注射机法。虽然卧式注射机法会增加成型操作的烦琐度,但是它能够实现脱模系统的自动化,推动橡胶注射成型技术的自动化发展。例如卧式机械中的单立轴刷除系统、简单单轴系统、线形关节型机械手都能够实现复杂制品的自动脱模。同时,卧式机械还能够降低供料难度。总的来说,卧式注射机是一种经济、高效的成型机械。除此之外,为了解决热固性弹性体在成型过程中出现残余物的问题,热固性行业还研发了一种集成涂刷式系统的成型机械。所谓“涂刷系统”,是指对模具进行定期涂刷,并保持擦刷力值不变。 为了提高成型机械的脱模效率,也可以利用自动喷雾系统、涂刷系统实现脱销的程序化控制。其具体做法是:将自动喷雾系统内置在涂刷系统结合部位,使自动喷雾系统能够将脱模机涂于模枪表面。尤其是我国模具设计的发展,立式注塑机、欧式注塑机、角式注塑机等成型机械的发展也越来越快。
液态硅橡胶注塑成型工艺解读
液态硅橡胶注塑成型工艺解读 硅胶在市场上的运用因其不会释放有毒物质且触感柔软舒适,能耐高温及低温(-60c~+300c) 良好物化性而被广泛运用,很少有他种聚合物可与它匹敌。强而有力的弹性体,且更胜过橡胶的密封性,优异的电绝缘性及对化学品、燃料、油、水的抵抗力,可应付不良环境之良好材料。工业上如: 油封、键盘按键、电器绝缘料、汽车另件,生活用品如: 奶嘴、人工导管、呼吸器、蛙镜、皮鞋球鞋内垫、食品容器……等,硅胶可区分固态及液态,前者加工方式以热压移转,后者原料则以射出成型为主,液态在设备投资及原料成本上虽较高,但其生产速度快,加工程度低及废料少等因素来观察,利用液态硅胶射出成型,在追求精准、速度、自动化的注塑生产工业,必定是未来导向趋势。 从注塑机厂家的角度来看,发展LSR射出成型机也是很有前景的,LSR射出成型机在机器配备上和一般塑料射出成型机最大的不同在于供料系统,其余针对材料的特性改变料管、螺杆、模具及控制系统的设计,这对当前国内注塑机制造厂而言是另一项拓展商机及机器附加价值的方式,目前普通注塑机市场竞争已趋白热化,相当激烈。展望未来市场及顾客需求,发展硅胶射出成型专用机,是另辟蹊径的好途径。 液态硅胶(Liquid Silicone Rubber),分为A胶与B胶,利用定量装置控制两者为1:1之比例,再透过静态混合器(Static Mixer)予以充份混合,注入射出料管后再进行射出成型生产。 将液态硅胶射入热浇道模具,制作硅胶制品,可达到一次成型)无废料及可自动化等优点。 在过去的三到五年里,热固性液体硅橡胶(LSR)的注塑技术得到了快速的发展。LSR的注塑设计与刚性工程热塑料有着重要的差别,这主要是因为这两种橡胶
全自动橡胶注射硫化成型机操作规程通用版
操作规程编号:YTO-FS-PD770 全自动橡胶注射硫化成型机操作规程 通用版 In Order T o Standardize The Management Of Daily Behavior, The Activities And T asks Are Controlled By The Determined Terms, So As T o Achieve The Effect Of Safe Production And Reduce Hidden Dangers. 标准/ 权威/ 规范/ 实用 Authoritative And Practical Standards
全自动橡胶注射硫化成型机操作规 程通用版 使用提示:本操作规程文件可用于工作中为规范日常行为与作业运行过程的管理,通过对确定的条款对活动和任务实施控制,使活动和任务在受控状态,从而达到安全生产和减少隐患的效果。文件下载后可定制修改,请根据实际需要进行调整和使用。 1. 目的 确保操作人员正确使用设备,保证安全正常生产。 2. 使用范围 (QH系列)全自动橡胶注射硫化成型机操作。 3. 职责 操作员必须遵守本文件的规定和要求。车间负责人对本文件的实施进行监督。 4. 工作程序 4.1开机准备、检查 4.1.1 检查机台的清洁润滑、冷却状态良好,各活动部位无障碍物。 4.1.2 检查电热系统,液压系统,电气系统运行正常.手动或自动状态下,各操作是否正常。 4.1.3 检查安全开关,安全电眼,紧急停止开关等正常有效。 4.1.4 检查模具腔内腔外清洁,模具固定牢固。
4.2 设备参数调整、设定 4.2.1按生产工艺要求,进入人机界面设定加工工艺参数,在试生产过程中进行适当调整。 4.2.2 点击进入界面功能选择菜单,选择注射机自动化生产所需的最优化的新功能。 4.2.3选手动调整模具,须注意注射嘴与模具中心孔的同心度,紧固模具。 4.2.4安装好新模具后,点击进入开关模界面主菜单:先慢速合模重新设定开模总行程和开关模各分段的行程、锁模压力、速度、硫化时间等参数的设定。主缸锁模压力要以模具面积大小而设定。 4.2.5点击注射系统菜单:先设定该模具的注射量,再设定各分段的量程、射出和进料的压力、速度等参数。注意:射出和进料的压力与射出速度要视胶料硬度及韧度来调整。 4.2.6点击推脱模系统菜单:先设定该模具的进退模、脱模和顶模的压力、快慢速度等参数。注意:压力与速度参数调整完成后,为了避免造成模具和设备的损毁,切记在生产过程中严禁更改速度和压力的参数。 4.2.7点击计时系统菜单:设定硫化功能计时器和特殊功能计时器的计时参数。合理设定计时器参数能有效地提高和优化设备的产能。
橡胶注射成型技术
橡胶注射成型技术 在橡胶制品中,主要成型技术有:模压法成型技术、传递法成型技术、缠贴法成型技术和注射法成型技术。在这些方法中,注射成型具有显著的优点:①简化工艺,减少操作人员数量;②降低能耗约10%;③提高生产效率4~ 7倍;④提高制品的均匀性、稳定性、尺寸精确性和合格率;⑤减少飞边,节省胶料;⑥操作方便,劳动强度低,机械化和自动化程度高。因此,近年来,注射成型技术越来越受到重要关注,并在橡胶制品生产中得到了迅猛发展。 目前全球注射机的拥有量为数万台,现已成为汽车、电子等橡胶制品的主流设备;而在注射机生产规模方面,世界年生产注射机产量也在突飞猛进,全球销售额超过了5.0亿美元。随着橡胶制品应用领域的不断拓展和生产规模的不断扩大,橡胶注射成型技术的应用前景将十分广阔,市场占有额也将显著增加。 1橡胶注射成型设备及工艺 1.1 橡胶注射成型设备与相应成型方法 塑料工业早在上世纪30年代就已开始应用注射成型法来生产塑料制品, 但由于橡胶本身具有的高黏度、易焦烧的特性,使得它从模压成型到注射成型经历了一段漫长的时间。到目前为止,橡胶注射成型已经历了3个阶段,即柱塞式注射、螺杆往复式注射和螺杆、柱塞式注射。并相应出现了柱塞式注射成型机、螺杆式注射成型机和螺杆一柱塞式注射成型机¨j。从生产过程上看,柱塞式注射、螺杆往复式注射和螺杆、柱塞式注射三种成型技术均需要经过胶料塑化和注射两个步骤才能完成。随着注射成型技术的不断发展,科研人员又对两步法注射工艺进行了改进,提出了胶料塑化和注射同步进行的一步法工艺,并研制了一步法注射成型机。 1.1.1 柱塞式注射成型机 柱塞式注射成型机是最早使用的橡胶注射成型设备。 注射成型方法是:将胶料从喂料口喂人料筒后,由料筒外部的加热器对胶 料进行加热、塑化,使胶料达到易于注射而又不会焦烧的温度为止,最后由柱塞将已塑化胶料高压注入模具中。 1.1.2 螺杆式注射成型机 螺杆式注射成型机是在挤出机的基础上加以改进,将螺杆的纯转动改成 既能转动以进行胶料的塑化,又可以进行轴向移动以将胶料注人到模腔中的橡胶成型设备。
液体硅橡胶LSR注射成型工艺的设计
液体硅橡胶L S R注射成型 工艺的设计 The following text is amended on 12 November 2020.
液体硅橡胶(LSR)注射成型工艺的设计 在过去的三到五年里,热固性液体硅橡胶(LSR)的注塑技术得到了快速的发展。LSR的注塑设计与刚性工程热塑料有着重要的差别,这主要是因为这两种橡胶的物理性质,如低粘度,流变学性质(快速固化),剪切变稀性质,以及较高的热膨胀系数等区别较大。 由于LSR的粘度较低,因此它在注射成型过程中,即使在注射压力较低的情况下,填充流速也可以较快,但是为了避免空气滞留,对模具通风的要求更加严格。总的来说,现代LSR的快速硫化的循环时间更短(某些情况下循环时间不到20秒),为了充分利用这一特性,加工机械、注射成型机以及部件转移系统等必须相互配合,作为一个高度集成的整体运作。 冷流道成型 现代冷流道体系充分利用了LSR剪切变稀的性质,真正达到了无浪费,无毛边成型。在过去的三到五年里,冷流道模塑在制造业中的优势地位急速上升,并导致橡胶产品的产量增加、废品减少、劳动成本降低等良好的势头。 LSR不会在模具中收缩,这一点和热塑性塑料类似。但是由于膨胀系数较高,加热时会发生膨胀,冷却时却仅有微小的收缩。因此,部件通常不能在模具中保持准确的侧边距,只有在表面积较大的空腔中才可以保持。 与热流道模塑相似,在冷流道加工中,热固LSR应保持较低温度和可流动性,以确保没有物料的损失。这种加工方法最适用于在清洁的室内环境中生产大小、结构相似的大体积部件。理想模型是在人为因素影响最小的设备中昼夜不停的运转,并逐步增大运转周期(日或周)。 目前所用的冷流道设备有两种基本类型,即闭合系统和开放系统,它们各有优缺点。注射循环中,闭合系统在每一个管道中都采用“开动销”或“针形阀”来控制LSR橡胶的流量。而开口系统则根据注射压力的大小,利用“收缩嘴”和阀门来控制物料的流量。 与开口系统相比较,闭合系统最典型的特点是在较低的注射压力下进行注塑。设备中可调控的“节流口”可以对不平衡的分流道以及物料的不同剪切变稀性能进行微调。缺点是对某些给定大小的部件和模具,设备需作额外的调整。 开放系统利用通过喷嘴或者阀门的高剪切速率,在注射压力降低时,进行截流。一般情况下,开放系统的空腔填充时间要比闭合系统稍微短一些。开放系统由于分流道和喷嘴较小,空腔密度较高。分流道则要求自然平衡,并与物料本身的流变性能严格匹配。因为开放系统的流道尺寸较小,所以通常不用可调“节流口”,只需普通阀门就可以很好的控制流量,并获得最佳的压力点。 分模线
陶瓷成型技术
陶瓷成型技术 摘要: 成型技术是制备陶瓷材料的一个重要环节。陶瓷制造经历数千年历史,直到20世纪中叶因为烧结理论的创立获得了飞速发展。上世纪七八十年代关于超细粉体制备和表征的发展,促使陶瓷工艺第二次大发展。当前阻碍陶瓷材料进一步发展的关键之一是成型工艺技术没有突破.压力成型不能满足形状复杂性和密度均匀性的要求。本文评述了国内外陶瓷现代成型技术,讨论了上述成型方法的基本原理和特点。 关键词:陶瓷, 成型, 技术,进展 一引言 成型工艺是陶瓷材料制备过程的重要环节之一,在很大程度上影响着材料的微观组织结构,决定了产品的性能、应用和价格[1]。过去,陶瓷材料学家比较重视烧结工艺,而成型工艺一直是个薄弱环节,不被人们所重视。现在,人们已经逐渐认识到在陶瓷材料的制备工艺过程中,除了烧结过程之外,成型过程也是一个重要环节。在成型过程中形成的某些缺陷(如不均匀性等)仅靠烧结工艺的改进是难以克服的,成型工艺已经成为制备高性能陶瓷材料部件的关键技术,它对提高陶瓷材料的均匀性、重复性和成品率,降低陶瓷制造成本具有十分重要的意义。本文简单回顾了陶瓷成型方法的发展及技术特点。 二成型方法 1 胶态浇注成型[2] 胶态浇注成型是将具有流动性的浆料制成可自我支撑形状的一种成型方法。该法利用浆料的流动性,使物料干燥并固化后得到一定形状的成型体。主要包括以下几种方法: ①注浆成型(Slip Casting) 是将浆料注入具有渗透性的多孔模具(如石膏)中,模具内部的形状即为所需要的素坯形状,利用多孔模具的毛细管力而使液体排除,从而固化。注浆成型的模具要具有一定的强度,吸水性好,吸水速度适中。注浆成型工艺成本低,过程简单,易于操作和控制,但成型形状粗糙,注浆时间较长,坯体密度、强度也不高。80年代中期,人们在传统注浆成型的基础上,相继发展产生了新的压滤成型(Pressure Filtration)和离心注浆成型(Centrifugal Casting),借助于外加压力和离心力的作用,来提高素坯的密度和强度,而且几乎不需要使用有机添加剂,因而避免了注射成型中复杂的脱脂过程,但由于坯体均匀性差,因而不能满足制备高性能高可靠性陶瓷材料的要求 ②流延成型(Tape Casting)〔1-2〕 也称带式浇注,或刀片法(Doctor-blade)。它是将粉料与塑化剂混合得到可流动的粘稠浆料,然后将浆料均匀地流到或涂到转动着的基带上,或用刀片均匀地刷到支撑面上,形成浆膜,干燥后得到一层薄膜,带膜厚度一般为0.01-1mm。60年代中期,由Wentworth等首次将流延法用于铁电材料的浇注成型。此外,它还被广泛用于多层陶瓷、电子电路基板、压电陶瓷等器件的生产中。 随着工业上对更大尺寸、更复杂形状陶瓷零部件需求的不断提高,用注射成型等传统的成型技术来制造已难以实现。它们都受到来自部件壁厚和复杂程度等方面的严重限制。围绕提高陶瓷材料的均匀性和可靠性问题,人们在传统成型工艺的基础上进行了不断深入的研究,并在90年代初期出现了一系列令人耳目一新的原位凝固成型工艺,其中最具代表性也是目前研究最活跃的两种成型方法是注凝成型和直接凝固注模成型,此外还有胶态振动注模成型、温度诱导絮凝成型等,原位凝固成型工艺受到了普遍的重视。 ③注凝成型(Gel Casting)
全自动橡胶注射硫化成型机操作规程
仅供参考[整理] 安全管理文书 全自动橡胶注射硫化成型机操作规程 日期:__________________ 单位:__________________ 第1 页共5 页
全自动橡胶注射硫化成型机操作规程 3.职责 操作员必须遵守本文件的规定和要求。车间负责人对本文件的实施进行监督。 4.工作程序 4.1开机准备、检查 4.1.1检查机台的清洁润滑、冷却状态良好,各活动部位无障碍物。 4.1.2检查电热系统,液压系统,电气系统运行正常.手动或自动状态下,各操作是否正常。 4.1.3检查安全开关,安全电眼,紧急停止开关等正常有效。 4.1.4检查模具腔内腔外清洁,模具固定牢固。 4.2设备参数调整、设定 4.2.1按生产工艺要求,进入人机界面设定加工工艺参数,在试生产过程中进行适当调整。 4.2.2点击进入界面功能选择菜单,选择注射机自动化生产所需的最优化的新功能。 4.2.3选手动调整模具,须注意注射嘴与模具中心孔的同心度,紧固模具。 4.2.4安装好新模具后,点击进入开关模界面主菜单:先慢速合模重新设定开模总行程和开关模各分段的行程、锁模压力、速度、硫化时间等参数的设定。主缸锁模压力要以模具面积大小而设定。 4.2.5点击注射系统菜单:先设定该模具的注射量,再设定各分段的量程、射出和进料的压力、速度等参数。注意:射出和进料的压力与射出速度要视胶料硬度及韧度来调整。 第 2 页共 5 页
4.2.6点击推脱模系统菜单:先设定该模具的进退模、脱模和顶模的压力、快慢速度等参数。注意:压力与速度参数调整完成后,为了避免造成模具和设备的损毁,切记在生产过程中严禁更改速度和压力的参数。 4.2.7点击计时系统菜单:设定硫化功能计时器和特殊功能计时器的计时参数。合理设定计时器参数能有效地提高和优化设备的产能。 4.2.8点击温控系统菜单:先合上模具打开所有加热开关,设定模板及媒油温度。必须待加热系统温控全部稳定后,先清机以除去料筒原有过期或已硫化余料,并储料到设定位置才可试模生产。 4.3生产过程及注意事项 4.3.1开机生产过程中,检查马达、泵浦、管路、电磁开关,有无异音或有无不良震动。 4.3.2生产中注意检查射出头与射出嘴之间有无溢料,注意调整射座油缸及压力开关的压力。 4.3.3注意观察所有模板电热温控、媒油温控及冷却水循环是否正常。 4.3.4设备发生红灯闪烁时,或设备出现异常时有显示报警提示或原因。点击查看界面中主菜单的报警显示栏内报警显示原因,及时排除故障。同时要向上级主管人员报告,或请相关技术人员解决。 4.3.5突发停电、停水等原因无法生产时,请关闭电源。恢复供电后,按上级指示打开电源及加热系统,开模后提高媒油温度,高压射出、清除料筒里的胶料。 4.3.6遇任何突发性紧急事故时,迅速按下紧急停止钮,并与现场管理人员联系,避免造成人身、模具及设备伤害。 第 3 页共 5 页