(新)高速线材活套控制

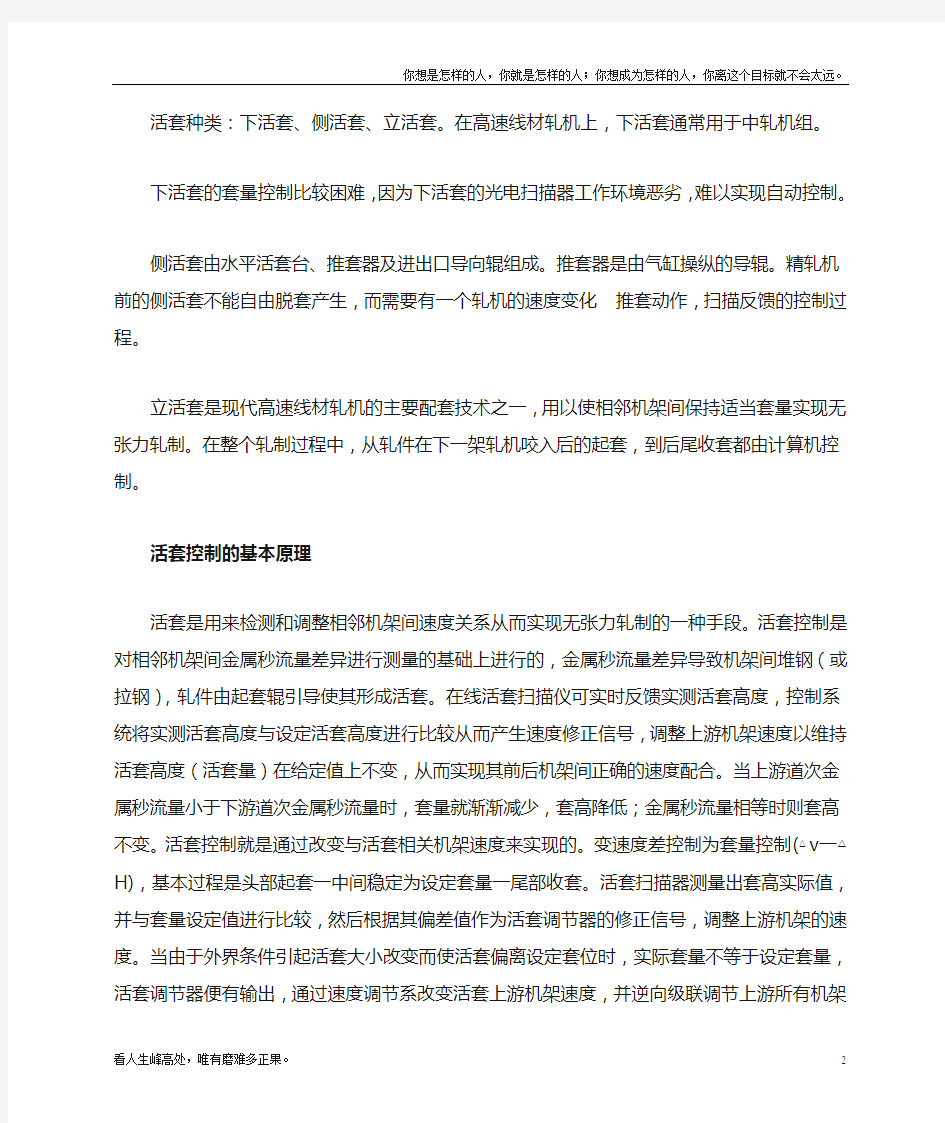
高速线材厂轧钢工艺培训
活套
现代高速线材轧机为保证产品尺寸精度,采用微张力及无张力轧制,以消除轧制过程中各种动态干扰引起的张力波动和由此引起的轧件尺寸波动。由于精轧机组为集体传动,故精轧采用微张力轧制,其微张力值由固定速比和各架给定孔槽面积保证,速比不会因控制而改变,轧件面积将因来料面积波动而波动。为了减少张力变化引起的精轧机的轧件尺寸波动,在精轧机前的预精轧、中轧机机组常设若干个活套,以消除连轧各架的动态速度变化的干扰、保证轧件精度。
活套定义及作用
通过自动控制系统调节相邻机架的速度使机架间产生“多余”轧件,该“多余”轧件在起套装置辅助下形成且能动态保持弧形的套状物,这个套状物就称为活套。活套控制功能适用于轧件断面小轧制速度较快的场合,能消除连轧机架的动态速度变化的干扰、保证轧件精度,活套可以实现无张力轧制。所谓无张力轧制即是在轧制过程中,机架间轧件不存在拉钢关系,是通过改变活套存储量来实现的。当相邻两机架间轧件受拉时,套量减小,可起缓冲作用,防止机架间产生张力,免使轧件断面拉缩,影响轧件尺寸的精度;另一方面吸收过量的轧件,防止堆钢而造成机架间的堆钢事故。但是活套的套量调节范围及套量的存储量是有限的,当相邻机架速度匹配不合理或其它原因而使起套量偏差太大,自动控制系统来不及或无法调节,就会引起堆钢。
活套由活套台、支撑辊、导槽、起套辊及活套扫描器等组成。支撑辊、起套辊起着对轧件的导向和支持作用。起套辊、转向导板均由气缸驱动,起套辊气缸由双电磁阀控制。
活套种类:下活套、侧活套、立活套。在高速线材轧机上,下活套通常用于中轧机组。
下活套的套量控制比较困难,因为下活套的光电扫描器工作环境恶劣,
难以实现自动控制。
侧活套由水平活套台、推套器及进出口导向辊组成。推套器是由气缸操纵的导辊。精轧机前的侧活套不能自由脱套产生,而需要有一个轧机的速度变化推套动作,扫描反馈的控制过程。
立活套是现代高速线材轧机的主要配套技术之一,用以使相邻机架间保持适当套量实现无张力轧制。在整个轧制过程中,从轧件在下一架轧机咬入后的起套,到后尾收套都由计算机控制。
活套控制的基本原理
活套是用来检测和调整相邻机架间速度关系从而实现无张力轧制的一种手段。活套控制是对相邻机架间金属秒流量差异进行测量的基础上进行的,金属秒流量差异导致机架间堆钢(或拉钢),轧件由起套辊引导使其形成活套。在线活套扫描仪可实时反馈实测活套高度,控制系统将实测活套高度与设定活套高度进行比较从而产生速度修正信号,调整上游机架速度以维持活套高度(活套量)在给定值上不变,从而实现其前后机架间正确的速度配合。当上游道次金属秒流量小于下游道次金属秒流量时,套量就渐渐减少,套高降低;金属秒流量相等时则套高不变。活套控制就是通过改变与活套相关机架速度来实现的。变速度差控制为套量控制(△v一△H),基本过程是头部起套一中间稳定为设定套量一尾部收套。活套扫描器测量出套高实际值,并与套量设定值进行比较,然后根据其偏差值作为活套调节器的修正信号,调整上游机架的速度。当由于外界条件引起活套大小改变而使活套偏离设定套位时,实际套量不等于设定套量,活套调节器便有输出,通过速度调节系改变活套上游机架速度,并逆向级联调节上游所有机架速度,这种调节会因每一条钢而有所不同,直到稳定为止。
活套的控制过程
起套
以14一15机架间立活套为例,其它活套类似。当14 机架活套扫描
器检测到轧件头部并延时t1秒,自动控制系统送一个起套信号给电磁阀,起套延时t1秒的确定(以14 到l5 机架的距离除以14 机架出口速度得到时间,来考虑气缸动作延时)应保证轧件刚好咬入l5 机架时,起套辊刚好启动。当起套辊启动后,活套上游的14 机架升速使14 、l5 之间生“多余”轧件以生成活套,起套过程结束后,14 机架恢复设定值。根据电机的动态特性,当轧件刚咬入l5机架时,电机会产生一个动态速降,但是控制系统预先给l5 机架以2~4%的动态速降补偿,可以保证不会因动态速降而使刚咬入时产生太多“多余”轧件,即起始套高度为0,这一点可以从不投入活套仍能平稳咬入得到确认。
稳定调节
起套完成后,即进入活套稳定控制阶段。根据活套扫描仪得到不断变化的套量,通过电控脉冲信号不断地传递给电控系统,系统按逆向级联控制的方向调整相邻上游14 机架的速度,这就相当于连续地修正上游相邻14机架的速度来保证活套的高度与设定值一致。活套调节是为了补偿轧件尺寸或温度变化而引起的套量变化。操作人员也要密切关注活套的远行情况,当活套高度超过允许最大高度或者存在严重拉钢的情况下,因超出活套自动控制调整范围,自动控制失效,应及时采取手动控制,以保证生产的安全进行。
收套阶段
当轧件尾部到13机架 (咬钢)信号,即进入收套阶段。仍然采用一个延时t2,自动控制系统送一个落套信号给电磁阀,落套延时t2,t2的确定(以13到l4机架的距离除以13 机架出口速度得到时间t2,来考虑气缸动作延时),应保证轧件刚好出l4机架时,起套辊刚好落下。为了安全收套并防止突然收套可能引起的甩尾,在收套阶段,要降低14 机架的速度以配合起套高度在轧件出14 机架降到0。起套辊不能落套过早,如果落套过早会使轧件在活套台处产生堆钢或甩尾,落套也不能太迟,如果太迟,下一轧件到来之前还未完全落套就会造成冲钢。
活套套形分析
在生产过程中,活套可能形成4种套形,如图所示。
(1)第1种套形是由于活套起套高度设定过大,轧件易在下一机架前产生堆钢及甩尾现象,不易控制。
(2)第4种套形是由于活套起套高度设定过小,轧件对起套辊压力较大,易导致套辊磨损快,机械故障多;另一方面轧件未能实现机架问无张力轧制,对红坯料形控制波动大。
(3)第2种套形是活套起套高度设定恰当,活套辊工作正常,轧件能实现机架间无张力轧制,对红坯料形控制较好,但如遇起套辊收套不及时,也易造成甩尾现象。
(4)第3种套形是活套起套高度设定略小,但活套辊能正常工作,轧件也能实现机架间无张力轧制,对红坯料形控制较好,不易造成甩尾现象。因此,可根据设备和工艺条件选择第2、第3种套形。
活套事故分析
在实际生产中发现有多种原因引起活套不稳定或堆钢。
1)活套起套辊不起套,原因可能有以下几种:
·活套扫描器有故障,不能检测;
·活套扫描器受震动,没对准检测口;
·活套扫描器镜头脏,检测不稳;
·冷却水太大或天冷雾气大,影响扫描器的检测灵敏度;
·电气线路接触不良及其它原因引起断路,起套信号送不到电磁阀;·电磁阀线包烧坏,阀不能动作;
·电磁阀阀芯堵塞,阀不能动作;
·气源未打开或气管破损;
·气缸或起套辊机械卡死。
2) 活套起套辊不落套原因可能为:
·上游机架的上游机架信号错误;
·电磁阀线包烧坏,阀不能动作;
·气缸或起套辊机械突然卡死。
3) 活套区常堆钢现象分析:
活套起套后时序紊乱,不能正常落套,下一钢坯钻人起套辊造成堆钢。解决办法,加强现场检测元件维护,确保检测信号的准确,注意保持最佳出钢节奏。
水平活套处堆钢。因水平活套处两相连机架间距很大,起套过早容易飞钢,过晚又易产生张力,所以要注意起落套的设置。精轧前水平活套处常因换辊后精轧咬钢困难,加之19机架动态速降补偿时间过长而引起堆钢。解决办法是调整19机架动态速降补偿参数,控制出钢节奏,同时要注意水平活套套台冷却及禁止碎断钢头带人套台。
4) 活套套量不稳。
一般情况下,调试好的活套都是较稳定的。如果有不稳定现象发生不要轻易通过修改活套高度给定或升降相邻上游机架转速的方法来使活套稳定下来。活套的稳定性与有关机架速度控制系统动态特性及粗、中轧堆拉关系,活套区工艺调整有关。正常情况下,对于同一轧件由头部到尾部活套允许有±15mm的高度变化。
可能引起活套不稳定的几个因素:
电气原因
活套扫描器检测信号不稳,镜头脏,冷却水及雾气太大,检测口化铁皮较多,均易导致信号时有时无,影响活套控制。
机械原因
如果支撑辊、起套辊轴承烧毁,转动不灵活造成磨损不均及卡死,会引活套不稳;起套辊或支撑辊偏心引起套量波动,这种波动一般从形成活套后开始就出现波动一直延续到落套。
工艺原因
导卫安装不当或辊缝设置不当也会引起的活套不稳。
轧件温度变化导致套量波动,这种波动一般出现在轧件尾部或中部以后,操作人员应该及时通知加热炉,以保证钢温的正常。
头部起套太高。一种可能是椭圆孔压下太多,轧件与下道圆孔型进口导轮不匹配,轧件阻力太大;另一可能性是轧件头,尾部与中部尺
偏差太大。
(新)高速线材活套控制
高速线材厂轧钢工艺培训 活套 现代高速线材轧机为保证产品尺寸精度,采用微张力及无张力轧制,以消除轧制过程中各种动态干扰引起的张力波动和由此引起的轧件尺寸波动。由于精轧机组为集体传动,故精轧采用微张力轧制,其微张力值由固定速比和各架给定孔槽面积保证,速比不会因控制而改变,轧件面积将因来料面积波动而波动。为了减少张力变化引起的精轧机的轧件尺寸波动,在精轧机前的预精轧、中轧机机组常设若干个活套,以消除连轧各架的动态速度变化的干扰、保证轧件精度。 活套定义及作用 通过自动控制系统调节相邻机架的速度使机架间产生“多余”轧件,该“多余”轧件在起套装置辅助下形成且能动态保持弧形的套状物,这个套状物就称为活套。活套控制功能适用于轧件断面小轧制速度较快的场合,能消除连轧机架的动态速度变化的干扰、保证轧件精度,活套可以实现无张力轧制。所谓无张力轧制即是在轧制过程中,机架间轧件不存在拉钢关系,是通过改变活套存储量来实现的。当相邻两机架间轧件受拉时,套量减小,可起缓冲作用,防止机架间产生张力,免使轧件断面拉缩,影响轧件尺寸的精度;另一方面吸收过量的轧件,防止堆钢而造成机架间的堆钢事故。但是活套的套量调节范围及套量的存储量是有限的,当相邻机架速度匹配不合理或其它原因而使起套量偏差太大,自动控制系统来不及或无法调节,就会引起堆钢。 活套由活套台、支撑辊、导槽、起套辊及活套扫描器等组成。支撑辊、起套辊起着对轧件的导向和支持作用。起套辊、转向导板均由气缸驱动,起套辊气缸由双电磁阀控制。 活套种类:下活套、侧活套、立活套。在高速线材轧机上,下活套通常用于中轧机组。 下活套的套量控制比较困难,因为下活套的光电扫描器工作环境恶劣,
高速线材轧制过程中常见堆钢事故分析及处理措施
高速线材轧制过程中常见堆钢事故分析及处理措施 发表时间:2019-05-21T10:27:45.023Z 来源:《防护工程》2019年第3期作者:王建荣 [导读] 减少堆钢事故要从分析事故原因入手,及时找到故障点,总结经验,为以后的生产提供帮助。酒钢集团榆中钢铁有限责任公司甘肃兰州 730021 摘要:高速线材生产过程中由于工艺、设备等问题造成堆钢,影响轧线的机时产量、坯耗、动力能源指标,造成设备损坏。本文就轧制过程中的常见堆钢事故结合现场工艺和设备情况进行分析,总结经验,为以后的生产提供帮助。 关键词:张力;导卫;废品箱;导槽;活套;飞剪 1.简介 某公司高速轧机线材生产线生产的产品规格:φ6.0~14.Omm。轧机共28架,为全连续布置,其中粗轧机6架、中轧机6架、预精轧机6架、精轧机一6架,精轧机二4架,钢坯经粗轧机组轧制后1#飞剪切头、尾,中轧机组轧制6个道次,然后(中轧后设2#飞剪用于事故碎断)进入预精轧机组中继续轧制4~6道次,之后,经预精轧机组后水冷箱进行控制冷却,按不同钢种进行温度控制,然后,经飞剪切头后,进入精轧机组中轧制,根据不同成品规格,轧件在精轧机组中分别轧制4~10个道次,最终轧制成为要求的产品断面。轧线孔型系统除粗轧6架采用无孔型轧制,其余均采用椭-圆孔型系统。 粗、中轧机组间采用微张力控制轧制;在预精轧机组前、后以及预精轧机组各机架间设有水平活套和垂直活套,可实现活套无张控制轧制;精轧机组一、精轧机组二各机架间以及精轧机组一和精轧机组二之间实现微张力轧制。 2.堆钢原因分析 2.1粗轧区域堆钢事故分析 粗轧区域由于采用平立交替平辊轧制,且钢坯断面积较大,相对比较稳定,堆钢事故比较少。粗轧堆钢事故产生的主要原因有以下几点: (1)导卫影响:导卫松动或导卫底座松动、移位造成轧件翘头不能顺利咬入下一道次,或导卫掉落直接堆钢;(2)换辊换槽:换辊换槽后由于轧件打滑而堆钢,孔型高度设定超差或张力设置不当造成堆钢;(3)由于钢温过低造成断辊而堆钢。 预防措施: (1)轧制过程中岗位工要加强巡检,及时紧固导卫及导卫底座固定螺栓,控制好料型尺寸,减少由于料型不规则和尺寸严重超差对导卫的冲击; (2)换辊换槽后及时对新槽进行打磨,增加轧件和轧辊的摩擦力,按照要求设定孔型高度,主控台岗位做好换辊换槽速度调整;(3)加热炉按照工艺要求控制好出钢温度,严防低温钢。 2.2 中轧、预精轧区域堆钢事故分析 中轧7-14采用平立交替布置的闭口式二辊轧机轧机,15-18架采用平立交替悬臂辊轧机。中轧、预精轧主要堆钢原因:(1)料型不符合标准导致轧件头部挤在下一道次入口导卫处堆钢,钢坯头部变形不均匀,头部温度低及头部有夹杂等缺陷等造成轧件劈头堆钢; (2)滚动导卫开口随轧件磨损变大倒钢造成料型急剧变化,张力失控而堆钢;导卫处遗留前一根钢的翘皮导致下一根钢受阻堆钢;(3)轧件弯头:轧制线不对中,轧件在活套进出口、空过管碰弯头等堆钢,一般侧弯是由于进出口导卫和孔型不对中造成,上下弯的原因大概有三种:一是进出口导卫和孔型不对中造成,二是孔槽磨损不均导致上下辊工作辊径不一致,三是传动部件间隙大造成咬入瞬时上下辊速度不一致; (4)张力设定不当,实际处于堆钢轧制状态,轧件依靠前机架的微张力维持轧制,当尾部离开前机架时突然失去张力而堆钢;(5)该轧线有10架和11架之间、11架到12架之间,从主控台力矩反馈看没有堆钢,但实际已经堆钢的现象,主要原因是由于轧件断面尺寸比较小,当机架间拱钢时对力矩的影响不大,所以,从主控台力矩画面看不出张力变化或张力变化很小。预防措施: (6)轧制过程中根据孔槽磨损情况及时调整辊缝,保证料型在标准范围内。加热炉原料工做好入炉钢坯的质量把关,粗轧岗位工发现头部低温钢或头部缺陷钢坯用1#飞剪手动切除; (7)轧制过程对导卫要勤检查、勤调整,保证导卫开口度符合料型要求,发现导卫有拉翘皮的情况及时处理;(8)发现进出口导卫偏离轧制线或轧件有翘头迹象要及时停机检查、处理,对孔槽磨损不均的轧辊要及时换槽。如果传动部件存在间隙由设备组及时处理; (9)由于粗中轧采用轧机力矩和电流作为微张力控制的依据,自由力矩受轧件头部钢温、料型的影响,所以,微张力控制存在误差。对于断面比较大的轧件影响不大,对于断面比较小的轧件影响比较大。主控台岗位工要合理设置各机架间的张力,对于10架和11架之间、11架到12架之间的张力应要求中轧岗位工观察轧件的尺寸来判断张力的大小,配合主控台做好张力调整,如果轧件离开前一架后尺寸变大则说明前一机架和该机架间存在张力,根据轧件尺寸变化程度判断张力的大小。 2.3精轧区域堆钢事故分析 精轧机组共10架,为45°顶交型布置,其中精轧一6架,后设废品箱,精轧二4架,后设废品箱,吐圈直径3.018米。精轧区域由于轧件速度快、轧件尺寸小,受导卫磨损、导槽磨损、吐丝管磨损、冷却水阻力、设备运行参数、设备故障的影响,堆钢的原因比较复杂。轧机内机架间堆钢主要原因是辊缝设置不合理、轧件冲出口或导卫轮烧损倒钢造成;精轧一后废品箱堆钢主要是由于精轧一和减定径之间的张力过小。大部分的堆钢集中在减定径成品机架后的废品箱,主要有以下四种情况: 2.3.1 吐丝机吐约0-10圈堆钢(实际情况根据现场生产工艺情况): (1)水冷段气动阀、电器控制元件故障、轧件头尾信号未断开,造成常流水,轧件头部受阻堆钢;
线材控制轧制和控制冷却技术
线材控制轧制和控制冷却技术 【摘要】对控制轧制与控制冷却的概念,控制原理,控制轧制与控制冷却在棒线材生产中的应用,意义及发展现状进行了介绍,并对现代棒线材生产中控制轧制与控制冷却所存在的问题进行简单的介绍。 【关键词】控制轧制,控制冷却,棒线材轧 ABSTRAC the paper gives an introduction to the Controlled rolling and Controlled Cooling as well as their application in rod and wire product.Then it gives the introduction to the application of Controlled rolling and Controlled Cooling in rod and wire product resentlly. KEYWORDS rolling control cooling control 1前言 控制轧制与控制冷却相结合能将热轧钢材的两种强化效果相加,进一步提高钢材的强韧性和获得合理的综合性能。随着控制轧制与控制冷却机理研究的不断深入,除了在中厚板,热连轧带钢生产中采用控制轧制与控制冷却工艺之外,在棒线材生产中也取得了比较成熟定型的控制冷却工艺。控制轧制和控制冷却是热轧生产中的新技术和新工艺,是金属塑性加工专业的理论与实践不可缺少的一个重要组成部分,是金属压力加工专业的前沿技术。 2控制轧制与控制冷却 2.1控制轧制与控制冷却的概念 (1)控制轧制(Controlled rolling)是在热轧过程中对金属加热制度、变形制度和温度制度的合理控制,使热塑性变形与固态相变结合,以获得细小晶粒组织,使钢材具有优异的综合力学性能的轧制新工艺。 (2)控制冷却(Controlled Cooling)是控制轧后钢材的冷却速度达到改善钢材组织和性能的目的。
控制冷却
棒材生产中的控制轧制技术 摘要:控制轧制和控制冷却技术在棒材生产中具有重要作用,合理制定控轧控冷工艺就能改善棒材的组织和性能。本文着重叙述了线材生产中控制冷却技术的机理、特点,目的、技术关键。 关键词:线材生产;控制轧制 1 引言 过去几十年来,作为热轧钢材性能的强化手段,或是添加合金元素,或是轧后再进行热处理。这些措施既增加了成本,又延长了生产周期,对于产品使用性能,多数情况下是在提高强度的同时降低了韧性,对焊接性能也造成影响。但控制轧制和控制冷却则不同,它是通过控制热轧过程中的变形及轧后钢材的冷却速度,达到充分细化晶粒和改善钢材组织状态,从而提高钢材的综合性能。它是通过优化工艺控制来大幅度提高钢材的综合性能,具有节约合金、简化工序、节能降耗等优点,由于它具有形变强化和相变强化的综合作用,所以既能提高钢材的强度,又能改善钢材的韧性和塑性。 2 控制冷却 2.1控制冷却的概念 控制冷却是利用相变强化以提高钢材的强度。通过控制冷却能够在不降低韧性的前提下进一步提高钢的强度。控制冷却是通过控制热轧钢材轧后冷却条件来控制奥氏体组织状态、相变条件、碳化物析出行为、相变后钢的组织和性能。 2.1控制冷却的阶段和特点 热轧后控制冷却包括三个不同冷却阶段,一般称一次冷却、二次冷却及三次冷却(空冷)。三个冷却阶段的目的和要求是不相同的。 一次冷却是指从终轧温度开始到奥氏体向铁素体开始转变温度Ar3或二次碳化物开始析出温度Arc。范围内的冷却,控制其开始快冷温度、冷却速度和快冷终止温度。一次冷却的目的是控制热变形后的奥氏体状态,阻止奥氏体晶粒长大或碳化物析出,固定由于变形而引起的位错,加大过冷度,降低相变温度,为相变做组织上的准备。相变前的组织状态直接影响相变机制和相变产物的形态和性能。一次冷却的开始快冷温度越接近终轧温度,细化奥氏体和增大有效晶界面积的效果越明显。 二次冷却是指热轧钢材经过一次冷却后,立即进人由奥氏体向铁素体或碳化物析出的相变阶段,在相变过程中控制相变冷却开始温度、冷却速度(快冷、慢冷、等温相变等)和停止控冷温度。控制这些参数,就能控制相变过程,从而达到控制相变产物形态、结构的目的。参数的改变能得到不同相变产物、不同的钢材性能。 三次冷却或空冷是指相变之后直到室温这一温度区间的冷却参数控制。对于一般钢材,相变完成,形成铁素体和珠光体。相变后多采用空冷,使钢材冷却均匀,不发生因冷却不均匀而造成弯曲变形。此外,固溶在铁素体中的过饱和碳化物在慢冷中不断弥散析出,使其沉淀强化。对一些微合金化钢,在相变完成之后
铁路专用线与国铁接轨审批实施细则
铁路专用线与国铁接轨审批实施细则 (铁运[2011]209号 2011年12月24日) 第一章总则 第一条为做好铁路专用线(以下简称专用线)与国铁接轨审批管理工作,确保铁路运输安全,提高效率效益,根据《铁路专用线与国铁接轨审批办法》(铁道部令第21号),制定本细则。 第二条本细则适用于新建、改扩建专用线(铁路段管线除外)与国铁接轨的审批管理。 第三条专用线与国铁接轨应当履行专用线接轨行政许可手续,取得“铁路专用线与国铁接轨许可证”(以下简称“接轨许可证”,格式见附件1)。 第四条专用线接轨审批管理工作坚持“标准公开、程序透明、集体决策”的原则,做到公开、公平、公正。专用线接轨方案应当科学合理、技术经济可行。 第二章基本条件 第五条专用线建设应当符合地方经济发展规划,与铁路新线建设、既有线扩能改造和生产力布局优化调整相结合,促进铁路现代物流发展。与新建铁路接轨的专用线,应当与
接轨铁路同步规划、同步建设、同步开通;与既有铁路接轨的专用线,应当符合货运基础设施布局规划,提高铁路货运规模化、集约化程度。 第六条基本条件: (一)近期年到发运量不低于30万吨,涉及国防、科研或国家重点项目等特殊情况的除外; (二)符合铁路技术政策、路网规划和货运基础设施布局规划; (三)技术标准和技术设备符合国家、铁道行业有关标准和《铁路技术管理规程》等规定,满足铁路运输安全的要求; (四)与相关线路、车站的运输能力和技术设备协调匹配; (五)品类单一、设计近期年到发运量在500万吨及以下的集(疏)运型专用线应当集中设置,原则上50公里范围内只建设一处; (六)接轨配套工程投资、建设、施工安全管理等问题,有关各方已达成一致意见;
高速线材轧机间活套知识
高线轧机间活套基础知识 活套 现代高速线材轧机为保证产品尺寸精度,采用微张力及无张力轧制,以消除轧制过程中各种动态干扰引起的张力波动和由此引起的轧件尺寸波动。由于精轧机组为集体传动,故精轧采用微张力轧制,其微张力值由固定速比和各架给定孔槽面积保证,速比不会因控制而改变,轧件面积将因来料面积波动而波动。为了减少张力变化引起的精轧机的轧件尺寸波动,在精轧机前的预精轧、中轧几机组常设若干个活套,以消除连轧各架的动态速度变化的干扰、保证轧件精度。 活套定义及作用 通过自动控制系统调节相邻机架的速度使机架间产生“多余”轧件,该“多余”轧件在起套装置辅助下形成且能动态保持弧形的套状物,这个套状物就称为活套。活套控制功能适用于轧件断面小轧制速度较快的场合,能消除连轧机架的动态速度变化的干扰、保证轧件精度,活套可以实现无张力轧制。所谓无张力轧制即是在轧制过程中,机架间轧件不存在拉钢关系,是通过改变活套存储量来实现的。当相邻两机架间轧件受拉时,套量减小,可起缓冲作用,防止机架间产生张力,免使轧件断面拉缩,影响轧件尺寸的精度;另一方面吸收过量的轧件,防止堆钢而造成机架间的堆钢事故。但是活套的套量调节范围及套量的存储量是有限的,当相邻机架速度匹配不合理或其它原因而使起套量偏差太大,自动控制系统来不及或无法调节,就会引起堆钢。 活套由活套台、支撑辊、导槽、起套辊及活套扫描器等组成。支撑辊、起套辊起着对轧件的导向和支持作用。起套辊、转向导板均由气缸驱动,起套辊气缸由双电磁阀控制。 活套种类:下活套、侧活套、立活套。在高速线材轧机上,下活套通常用于中轧机组。 下活套的套量控制比较困难,因为下活套的光电扫描器工作环境恶劣,难以实现自动控制。
高速线材在轧制过程中堆钢事故的分析与处理.
高速线材在轧制过程中堆钢事故的分析与处理 孙东海 (辽宁省本溪市北台钢铁集团北方高速线材 117000)摘要:高速线材在轧制过程中有时会发生堆钢现象,对线材产品的成材率和生产效率都有较大的影响。堆钢的种类有:直观性堆钢、多样性堆钢和复杂性堆钢。结合操作工艺、设备安装等方面对日常生产实践中所碰到的一些堆钢事故进行了分析,找出了堆钢产生的原因,并提出避免堆钢应采取的措施。从而有效控制堆钢事故的发生频率,不仅大大提高了成材率与设备利用系数,而且也提高了生产效率。 关键词:高速线材;堆钢;张力;活套;打滑;甩尾 Analysis and Treatment of Steel-Heaping Accidents In Rolling High Speed Wire Rod Sun dong hai ( Liaoning province,Benxi,beitai Steel Group, North High speed Line material 117000 ) Abstract: The phenomenon of piling-up of steel would happen sometimes while high speed wire rod is being rolled, which would greatly influence the product’s yield and production efficiency. It is pointed out in this article that steel-heaping has many forms, such as intuitionist one, multiplex one and complicated one. In combination with the operation process, equipment installation, etc., some steel-heaping accidents in daily production were analyzed, causes of steel-heaping were found out, measures taken to avert steel-heaping were put forward, and the frequency at which steel-heaping takes place were controlled effectively .All these greatly improve product’s yield, equipment utilization coefficient and productivity. Keywords: high speed wire rod;steel-heaping;tension;loop;slipping;tail-discarding 0 前言 二高线生产线主要轧制规格范围为:ф5.5—ф16mm光面高速线材,?8—?12mm螺纹高速线材。规格跨度大、钢种范围广。从目前的生产状态分析,?≤6.5mm的小规格线材产品,由于断面尺寸小、轧制速度快、轧制稳定性较差等原因,与中大规格相比,堆钢事故的发生率一直较高;而对于?>6.5mm的中大规格线材,在开轧稳定之后,中间过程产生堆钢事故的几率很小,大规格线材轧制需要注意的是高速区爆辊环事故的发生。本文分析了高速线材生产过程中一些典型堆钢事故的产生原因,并提出减少堆钢事故的相应控制措施。 1 线材的轧制工艺流程布置简图 线材的轧制工艺流程布置见图1。 轧件通过1H前的夹送辊顺利咬入1H后,依靠轧机的动力继续前进,经过粗轧机组轧制、S6飞剪切头切尾、中轧机组轧制、S12飞剪切头切尾、预精轧机组轧制、S18飞剪切头、精轧机组及减定径机组轧制后,一直到达夹送辊使轧件进入吐丝机并吐丝成圈。 2 堆钢事故的种类 在解决堆钢事故时,正确判断并分析堆钢的产生原因是非常重要的。准确地判断可以及时解决问题并避免以后重蹈覆辙。但是在实际生产中,由于影响因素的多样性,快速准 孙东海,男,无,无,从事轧钢,naihaihan@https://www.360docs.net/doc/032068043.html,
鄂钢质量证明书视频
电炉厂于2002年9月建成投产,生产的产品质量达到当今世界发达国家同类产品实物质量水平,成分控制精度较高,可生产优质碳素结构钢、合金结构钢、冷镦钢、齿轮钢、钎具钢、合金弹簧钢、预应力钢丝及钢绞线用钢、工具钢、模具钢、焊条钢等钢种。以电炉炼钢厂的钢坯为原料生产的优带荣获“湖北名优产品”。优质碳素机构钢热轧盘条、优质碳素结构钢热轧圆钢荣获“国家冶金产品实物质量金杯奖”,2006年轴承钢获得“全国工业产品生产许可证”。 现有1座70吨consteel电炉、1座lf精炼炉、1座vd真空炉、1台意大利进口四机四流高效合金钢连铸机,出钢量可达85吨。科生产规格150×150mm、200×200mm、150×245mm 的方坯和φ180mm、φ210mm、φ230mm的圆坯,优钢坯年生产能力达60万吨。 镀锌薄板全套工艺设备具有大型化、连续化、自动化和高速化的特点,产品质量稳定、可靠。主要设备:机组拥有先进窄搭接焊机、电解脱脂、全辐射立式退火炉、四锟湿光整机、静电涂油机等工艺设备以及在线产品质量测量设备――冷态锌层测厚仪,在线测量锌层厚度。热镀锌机组采用先进的热镀锌生产工艺,产品规格厚度0.25~1.5mm、宽度800~1350mm,设计年生产能力25万吨。 冷轧薄板厂全套工艺设备具有大型化、连续化、自动化和高速化的特点,产品质量稳定、可靠。主要设备:双机架6锟可逆轧机。主要控制技术:厚度控制系统(agc),工作锟正、负弯锟控制,中间锟横移预设定及正弯锟控制。主要检测设备:激光测速仪、x射线测厚仪、张力仪。产品规格厚度0.25~2.0mm、宽度800~1350mm,设计年生产能力60万吨。 武钢集团鄂钢公司宽厚板产线 (4300mm) 广泛采用世界最先进的工艺技术及装备。主要生产:各强度级别船板、碳素结构钢板、低合金高强度板、桥梁板、压力容器及锅炉板等产品。产品规格可达5~150mm×900~4100mm×3000~25000mm。产品按常规轧制态、控轧(cr) 及控轧控冷(tmcp) 态、热处理状态交货。可以满足用户对高等级宽厚钢板的高尺寸精度、高性能的要求。 武钢集团鄂钢公司宽厚板产线依托武钢集团本部对产品研发、生产的全过程实行质量管理控制,保证产品实物质量达到国内领先水平。 主要设备包括步进梁式加热炉、高压水除鳞机、四辊可逆式精轧机、mulpic加速冷却装置(acc+dq) 、9辊热矫直机、步进式冷床、超声波探伤装置、剪切线(包括滚切式切头剪、双边剪、定尺剪)、精整线、热处理线、成品火焰切割机及在线标记装置、推钢式加热炉、粗轧机、厚板冷床、冷矫直机等。1#热处理炉采用辐射管加热的无氧化辊底式炉,炉后带有辊压式淬火 机,2#热处理炉为明火加热炉,均由德国l0i公司负责设计并提供关键设备。 高速线材厂于2000年8月竣工投产,年生产能力61万吨,坯料尺寸150mm × 150mm ×9m? 盘重1.5吨左右,最高速度115米 /秒。产品规格为φ5.5~φ16.0mm 光面盘条和φ6.0~φ16.mm螺纹钢筋,产品钢种为碳素结构钢、优质碳素结构钢、低合金钢、优质合金钢、弹簧钢及轴承钢等。 2003年,在精轧后增加了一台从达涅利公司引进的在线测径仪,产品尺寸精度可达c级。可生产φ5.5、φ6.5、φ7.0、φ8.0、φ10.0、φ12.0、φ14.0mm光面盘条和φ10.0、φ12.0、φ14.0mm螺纹钢精,钢种又q196、q235、el08、swrm8、35-70#、20cr、40cr、20crmo、 20crmnmo、20mntib、30crmnti、b7、gcr15、65mn、60si2mn 、hrb335等。 高线产品获“湖北省名牌产品”称号,低碳钢热轧盘条、优质碳素结构钢热轧盘条获“国家冶金产品实物质量金杯奖”。 热轧带钢厂建于1993年10月,年生产能力58万吨。生产三大系列五大钢种的热轧窄带钢,主要用于焊管料、冷轧料、五金制品、冲压用钢、玩具用钢等。产品有普通非合金钢带、优质非合金钢带、特质费合金钢带、低合金结构钢带、特质合金钢带等。钢种有q195、q215
高速线材常见事故处理
常见事故分析 概述:生产过程中的堆钢原因及处理 生产过程中经常会遇到一些堆钢的事故。调整工应经常不断地、定时地对轧件尺寸、堆拉关系、轧件表面、扭转角度、导卫的使用情况、冷却水等进行检查。堆钢可分为头部堆钢、中部堆钢和尾部堆钢。所有的堆钢从现象上看是一样的,但产生原因却有所不同。 一、什么是头部堆钢,产生原因是什么,如何解决? 现象:头部堆钢是指轧件头部未进入下一架轧机之前就发生的堆钢现象。 原因:(1)、由于上道次轧件尺寸不符合要求(过高或过宽)引起轧件挤在该道次进口导卫中受阻而堆钢,事故发生后要对轧件头部进行测量,观察轧件头部受阻的痕迹,做出判断,并对前一道次乃至前若干道次的辊缝作调整。 另外,由于轧槽磨损而引起轧件的尺寸变化,应相对地缩小各架的辊缝。一般来说,椭孔的磨损较快,方或园孔的磨损较慢。所谓“两次椭一次圆”,实践告诉我们,缩小椭孔辊缝见效快,缩小圆孔辊缝轧机稳定时间长,应视情况而定。 (2)、由于钢坯头部在大压下量轧制时的不均匀变形,头部低温或冶废、夹杂等都可能形成“劈头”,或者上一根遗留下大片翘皮在进口导卫中而引起堆钢。 (3)、由于扭转导卫磨损严重或固定螺丝松动,致使轧件扭转角度不对,而引起堆钢。只需观察轧件头部正反对角两侧有被进口导
卫挤压之痕迹就可以判断。处理方法为调整滚动扭转导卫开口度,是固定式扭转导卫应更换。 (4)、由于上道进口导卫磨损严重(或固定螺丝松动),上道次来料过小,致使轧件与导卫间隙过大,造成头部倒钢,使轧件在该道次进口导卫中受阻而引起堆钢。处理方法:检查上道次轧件尺寸,更换上道次进口导卫。 (5)、滚动进口导卫也可能缺油,造成辊环烧坏。夹持辊严重磨损,夹持辊表面粘铁,调节开口度的固定螺丝松动等引起头部倒钢。 (6)、轧件弯头也可能造成下道不进,引起堆钢。弯头可能是进出口导卫中心线与孔型中心线不直,轧件在行进过程中不断地被强迫改变方向所致。也可能是上、下轧辊磨损不均匀,或者传动部件间隙过大,造成上下不同步而引起弯头,另外,上、下轧辊辊径不同,从而造成线速度不同,亦可引起轧件弯头。因此,遇到弯头现象发生时,应当根据情况加以分析,再着手处理。 棒三常见冒料统计如下: 1、未进K1导致冒料的原因是什么? 原因分析:(1)、K1进口导板粘有氧化铁,导致轧件无法通过; (2)、导卫轴承缺少油气润滑或缺水冷却,导致K1进口导轮卡死。 (3)、导轮间隙太小或过大,导致轧件无法进入或进入不稳; (4)、K2出口导卫翻身不到位,导致K2来料无法进K1;
网络线生产品质控制
网络线制造与质量控制 质量管理部:汤代斌 当今信息高速公路的建设已成为风靡全球的产业,而网络作为信息的载体,近年来在我国的发展也非常迅猛,光缆以其传播速度快,信息容量大成为广域网传输介质的道选。 但是,局域局的大楼通信综合布线系统中,由于光缆敷设费用太高,且接头费用和终端光-电转换费用昂贵,因此其造价非常昂贵。为些,须寻求一种价廉物美的数据通信电缆来担任最后100m的传输任务,这样,cat5,cat5e,cat6类缆应运而生。 目前cat5类UTP电缆主要用于大楼通信综合布线系统的工作区通信引出端到办公区域通信接线盒的水平布线。根据EIA/TIA-568B规定,水平布线一般是4对100ΩUTP电缆。 以下通过对公司串列式芯线押出机(金东SPL-1200)生产cat5及cat5e 和cat6类缆生产过程及制程中出现影响电气性能的一些要素作出管控。 一,Cat5及cat5e和cat6类缆的生产制造: 5类缆生产流程简图 1.绝缘单线的押出: 由于高速数据传输电缆传输100MHz以上的高频,对电缆结构尺寸的稳定性和均匀性要求严格,因此电缆生产过程中的每一道工序都可能把自身的问题带到成品中去,而制造过程中的第一道工序——绝缘单线押出是整个生产的中心环节。 良好的控制单线制过程是生产高性能电缆的基础。线芯绝缘不偏心是阻
抗保持稳定的前提,而且在轴向要求达到均匀一致加工精度。在生产中公司采用上海金东SPL-1200型串列拉丝绝缘生产线,其具有拉丝,退火,预热,绝缘押出各参数在线控制等高速串列生产单线功能。 1)生产线速度为800m/min~1000m/min,具有x-y双轴全自动外径闭环反馈控制系 统,实时监 控外径的偏 差,精密的 张力自动控 制系统保证 了导线外径 的均匀性, 同心度控制 在96%以 上,铜线外径偏差+/-0.002mm,导体椭圆度为±0.002.绝缘外径偏差为+/-0.01mm.,采用预热装置(温度规范:120℃-130℃)使导线与绝缘层之间的粘附力恒导体预热及退火电压控制 导体外径,椭圆度,偏芯度在线控制
高速线材生产中的活套控制系统
高速线材生产中的活套控制系统 摘要:本文介绍了高速线材生产中活套控制系统的组成、活套量的计算模型、活套的控制运算和实际数字PID控制参数的配置方法;同时也介绍了活套扫描器的工作原理、安装要求、以及活套扫描器对活套调节精度和稳定性的影响;阐述了活套控制系统在高速线材生产中的重要性。 关键词:活套;套量计算;活套控制;数字PID 引言 在高速线材生产中为保证轧出优质线材,其主要因素之一就是要保证预精轧各机架之间、预精轧和中轧机间以及预精轧和精轧机间实现无张力轧制。由于轧制速度快以及其它方面原因的影响,要完全靠两机架本身的调速控制系统来保证无张力轧制而又不堆钢是难以实现的。因此,在这些机架之间各设一活套控制环节,各活套控制环节通过级联关系构成一活套控制系统,保证轧件在这些机架间在有一定的套量下进行轧制,以实现无张力轧制的要求。 活套的型式根据工艺布置有二种。一种是水平活套,即活套构成的平面与水平面平行,它的套的形成是靠调节相应机架的速度自由形成或靠推套辊帮助起套,它对套量的存贮相对要大些,另一种是立活套,即活套构成的平面与水平面垂直,立活套由推套辊帮助起套并靠推套辊支撑。一般预精轧机和中轧机之间以及预精轧机和精轧机之间采用水平活套,预精轧各机架之间采用立活套。本文是以某高速线材厂为例对活套控制系统加以阐述,整个活套控制系统由五个活套组成,三个立活套和两个水平活套,采用逆调的方式。 1.3.实际套量检测部分即活套扫描器。 活套调节部分主要是由PID调节器构成,其作用是对实际套量进行调节。活套的逻辑控制部分是用于处理活套调节的逻辑联锁关系和顺序控制。活套扫描器是套量的检测元件,它的灵敏度和精度直接影响着活套控制能否正常工作。 活套控制系统是由全线中各活套控制环节所组成,它们之间的顺序控制关系由逻辑控制部分来完成。 2.活套量的计算模型 活套量一般定义为物料活套的弧长减去此弧对应的弦长。虽然人机接口设定的活套控制参数为活套的高度,但在活套控制系统中常把它转换成套量来进行控制。下面我们来分析套量与活套高度存在什么关系。 首先我们假定活套形状为一弓形圆弧,在控制过程中弓形圆弧的弦长为常数,弓形圆弧的弦高将随设定高度而变化,因此形成的曲率半径是一个变量。3.
斯太尔摩控冷工艺在高速线材生产中的应用模板
斯太尔摩控冷工艺在高速线材生产中的应用模板
斯太尔摩控冷工艺在高速线材生产中的应用1.概况 13mm盘卷, 5.5mm---唐钢高速线材厂是引进的具有八十年代国际装备水平的线材生产线。该生产线轧制速度为90m/s, 最高可达108m/s,产品规格为12mm螺纹盘卷。该厂主要生产工艺流程如下: 10mm---210精轧机----三段水冷箱水冷----夹送辊夹送----吐丝机吐丝----斯太尔摩风冷辊道风冷----剪尾----集卷筒集卷----运卷小车运卷、卸卷----P/F线运输----剪头、检查----打包机打包----电子称称重----卸卷----入库300预精轧机(机架间有立活套) ----预水冷----3#切头飞剪、转向器----侧活套----废品卡断剪----10*400中轧机----2#切头、切废飞剪----6*500粗轧机----1#切头、切废飞剪----5*连铸坯(135mm*135mm)----步进加热炉加热----出炉----夹送、废品或事故卡断剪----4* 2.控制冷却工艺特点线材轧后的控制冷却是整个线材生产中产品质量控制的重要手段之一, 它对线材成品的内部组织、力学性能及二次氧化均有重要的影响。控制冷却的实质是利用轧件轧后的轧制余热, 以一定的控制手段控制其冷却速度, 从而获得所需要的组织和性能, 以达到提高产品质量的目的。1964年, 加拿大斯太尔柯钢铁公司和美国摩根公司联合研制的高速线材轧机, 首次采用了线材散卷控制冷却工艺, 称之为斯太尔摩控制冷却方法。这是线材生产发
展史上的重大技术革命之一, 并在世界高速线材轧机控冷线上得到了广泛的应用。斯太尔摩控冷工艺有三种类型: ( 1) 标准型: 采用标准型冷却时, 从精轧机出来的线材以压力水进行快速冷却, 根据不同的钢种和用途将线材冷却到接近相变的开始温度( 760--900℃) , 冷却后的线材经吐丝机形成线环状, 呈散卷状叠放在运输机上, 线卷在运输过程中鼓风进行散卷冷却。标准型斯太尔摩冷却的运输速度为0.25—1.3m/s,冷却速度为4--10℃/s。( 2) 缓慢型: 缓慢型与标准型的不同之处是在运输机的前部加了可移动的带有加热烧嘴的保温炉罩。运输机的速度设定的更低些, 可使盘卷以很缓慢的冷却速度冷却。缓慢型冷却运输速度为0.05—1.3m/s, 冷却速度为0.25--10℃/s。(3)延迟型:延迟型是在标准型的基础上,结合缓慢型冷却的工艺特点加以改进而成。它是在运输机两侧装上绝热材料的保温墙, 并在保温墙的上方装有开关灵活的保温罩盖。当保温罩盖打开时, 可进行标准型冷却; 若关闭保温罩盖, 降低运输机速度, 又能达到缓慢冷却的效果, 但比缓慢冷却型结构简单而经济。延迟型冷却的运输速度为0.05—1.3m/s, 冷却速度为1--10℃/s。标准型适用于高碳钢线材, 缓冷型适用于低碳钢及低合金钢线材。由于缓冷型冷却需要附加加热设备, 投资大、能耗高, 而被延迟型冷却所替代。延迟型冷却适应性广、工艺灵活、投资适中, 因此得到了广泛的应用。唐钢高速线材厂的辊式延迟型斯太尔摩控冷线, 不但能进行延迟型冷却, 也能进行标准型冷却, 其冷却速度最低可控制在1℃/s以下, 最高可达
控制轧制于控制冷却
控制轧制于控制冷却
1、控制轧制:在热轧过程中,通过对金属加热制度、变形制度和温度制度的合理控制, 使热塑性形变与固态相变相结合,以获得细小的晶粒组织,使钢材具有优异的综合力学性能的轧制技术2、控制冷却:通过对控制轧后的钢材的冷却速度来改善钢材的组织性能。 3、金属的强化:通过合金化,塑性变形和热处理等手段来提高金属的强度。 4、固溶强化:添加溶质元素使固溶体强度提高的方法。 5、韧性:材料在塑性变形和断裂所吸收能量的能力。 6、微合金钢:钢种的合金含量小于0.1%。 7、IF钢:无间隙原子钢 8、不锈钢:具有良好的抗腐蚀性能和抗氧化性的钢。 9、变形抗力:在一定条件下材料变形单位面积的抵抗变形的力。10、在线常化工艺:在热轧无缝钢管中在轧管延伸工序后将钢管按常化热处理要求冷却到某一温度后在进加热炉然后就行减径轧制按照一定的速度冷却到常温。11、变形温度贝氏体处理化工艺:在钢管轧制过程中不直接加热到马氏体温度一下,而是快速冷却带中温以后再置于静止的空气中冷却、以变形奥氏体转变为贝氏体省去回火工序。12、高温变形淬火:钢管在稳定的奥氏体区域变形,而且一般温度在再结晶温度以上然后进行淬火,已获得马氏体组织。13、低温相变淬火:将钢管加热到奥氏体状态,经一段保温冷却到Ac1高于M的某一中间温度进行变形后淬火的工艺。14、非调质钢:将调质钢的化学成分进行调解并对轧制过程进行控制不进行调制其性能达到调制的水平。1、控制轧制是指在热轧过程中通过对金属加热制度,温度制度,保险制度的控制而获得细小的晶粒2、控制冷却是控制轧后钢材的冷却速度来改善组织性能。3、钢材的强化方法有固溶强化,变形强化,沉淀强化,弥散强化,亚晶强化,细晶强化,相变强化。4、影响材料韧性有,化学成分,气体和夹杂物,晶粒细化,形变的影响,形变细化5、动态结晶是晶粒细化提高扩孔性的手段6、控制轧制的目标是为了获得较小的铁素体组织7、加快冷却速度可以获得细小的铁素体晶粒所以不产生奥氏体组织为界限8、贝氏体是结构性能钢有校坏的塑形焊接性能强韧性微合金钢是指钢中的合金元素总量小于0.1%的钢在控制轧制中使用最多的微合金元素有银,钛,钒9、钢通常是指含碳量在0.28-2.1的铁碳合金10、温度小,压下量打,有利于细化晶粒 1、提高金属强度的措施?(1)固溶强化(2)形变强化(3)沉淀强化与弥散强化(4)结晶强化(5)亚晶强化(6)粗变强化。 2、提高教师材料韧性的措施?(1)化学成分(2)气体和夹杂物的影响(3)细晶强化(4)形变的影响(5)相变组织的影响3.、微合金钢的作用?提高材料的强度,韧性降低生产成本4、控制轧制与一般轧制的区别?(1)控制轧制的温度在950-1050温度降低了(2)加入了3V,Nb,Ti等合金元素,使金属的强度和韧性都大大提高(3)控制轧制生产出来的钢材组织性能号成本低5、控制冷却分为哪几个阶段。分别有何作用?三个,第一阶段,控制相变奥氏体组织状态为相变做组织上的准备,第二阶段,通过控制冷却速度和冷却终止温度来控制相变过程以保证冷却得到钢材所需要的组织,第三阶段,对于低碳钢没有什么影响对冷却钢来说在冷却过程中会发生硫物析出,对生成的贝氏体产生轻微的同化效果,对高碳钢来说在冷却过程中会阻止硫化物的析出从而达到保持固溶强化的目的。6、中厚板控制冷却的目的/?(1)控制钢材冷却过程增大过冷度,降低变形奥氏体向铁素体珠光体转变,以得到细状的铁素体晶粒。(2)在奥氏体未再结晶区终轧后快冷,可以将变形奥氏体中的亚结构,强压机制保持相变Tbm组织中进行保持钢的强度。(3)在保持综合力学性能不变的前提下采用控制冷却工艺可以降低钢中的含碳量,提高钢板的焊接性能,低温韧性和冷塑性。(4)在钢核成分不变条件下采用不同的轧后冷却工艺,可以生产不同强度级别的钢板(5)轧后利用在线淬火工艺可以简化工艺节约能耗降低成本。7、中碳钢控制轧制的特点?(10)以铁素体为主的钢以细化铁素体晶粒来提高强度和韧性不论采用哪种控制轧制方法都可以达到目的。(2)以珠光体为主的钢通过控制轧制会使强度降低韧性提高,其强度降低的原因是由于珠光体
攀钢质量证明书
攀钢质量证明书 篇一:压力容器安装质量证明书 压力容器安装竣工资料 工程名称:攀钢热轧板厂零星压力容器更换安装使用单位:攀钢集团攀枝花钢钒有限公司热轧板厂施工单位:中国十九冶集团有限公司机械设备安装分公司编制人:吴晓东 20XX年10月10日 压力容器安装质量证明书 压力容器技术资料检查记录表 设备安装精平记录 立式容器安装检查表 篇二:产品质量保证书 产品质量保证书 首先,感谢您使用南京舜美科技有限公司的的产品—奥凯斯通工业无线遥控器。本公司在遥控器的维修,安装,工厂行车遥控系统的改造,工程机械的遥控系统改造方面积累了丰富经验。现已发展成为一家相对专业且特色分明的公司。公司先后为上海宝钢、攀钢、南钢、唐钢等国内众多大型企业提供遥控产品。同时为二重等大型重工业及其制造业、冶金、电解铝、造纸、造船、工程机械等行业产品提供产品和服务。并在长期合作中树立了良好的口碑,客户遍布
全国。 产品采用了无线遥控控制,操作人员只需携带轻巧的发射系统,就可以自由地走动并选择最佳的视觉位置,实现对起重设备的控制,消除了以往操作上由于视线不清、环境恶劣或指挥配合不协调等因素而带来的不便,消除事故隐患,既保证了安全操作又大幅度地提高了生产效率。奥凯斯通产品根据人体工程学设计,使用起来得心应手。产品防护等级高,抗摔抗震,密封性超好,防尘防灰,防高温,抗低温,任何恶劣的操作环境都可以放心使用,将出错率降到最低。 品质保证 1. 本系统使用AKERSTROMS公司所拥有的多项国际专利。 2. 奥凯斯通保证本产品在出厂时,完全符合其所公布的各项规格,只要正确地安装,均可正常使用。 3. 本系统部分技术不公开,原厂随时可能增加新功能,其说明可能 与系统不符。 4. 本系统及相关文件之专利权属于本公司所有,非经许可不得全部或部分挪用。 产品维护 本产品自使用日起享有保修期:系统内之电子部件,自使用之日起,高频部分享有五年年免费保修;主板部分三年
常用线材线缆标识
常用线材线缆标识 1. 字母代号及其意义 类别、用途导体绝缘内护层特征铠装置外护层 N- 农用电缆L- 铝线芯V- 聚氯乙烯H- 橡套CY- 充汕0- 无0- 无 V- 聚氯乙烯塑料绝缘电缆X- 橡皮F- 氯丁橡皮护套D- 不滴流1- 1- 纤维层 X- 橡皮绝缘电缆Y- 聚乙烯L- 铝套F- 分相护套 2- 双钢带2- 聚氯乙烯套 YJ- 交联聚乙烯绝缘电缆Q- 铅套P- 贫油干绝缘3- 细圆钢丝3- 聚乙烯套 ZQ- 纸绝缘电缆V- 聚氯乙烯P- 屏蔽4- 粗圆钢丝 Y- 聚乙烯套Z- 直流 2. 型号、名称和使用范围: 型号名称使用范围 铜芯铝芯
VV VLV 聚氯乙烯绝缘聚氯乙烯护套电力电缆敷设在室内、管道内、隧道内 VV VLV 聚氯乙烯绝缘聚乙烯护套电力电缆敷设在室内、管道内、隧道内 VV22 VLV22 聚氯乙烯绝缘钢带铠装聚氯乙烯护套电缆敷设在地下,能承受机械外力作用 VV23 VLV23 聚氯乙烯绝缘钢带铠装聚乙烯护套电缆RVVP :铜芯聚氯乙烯绝缘屏蔽聚氯乙烯护套软电缆电压300V/300V 2-24 芯 用途:仪器、仪表、对讲、监控、控制安装 RG :物理发泡聚乙烯绝缘接入网电缆用于同轴光纤混合网( HFC )中传输数据模拟信号 UTP :局域网电缆用途:传输电话、计算机数据、防火、防盗保安系统、智能楼宇信息网 KVVP :聚氯乙烯护套编织屏蔽电缆用途:电器、仪表、配电装置的信号传输、控制、测量
SYWV ( Y )、SYKV 有线电视、宽带网专用电缆结构:(同轴电缆)单根无氧圆铜线+ 物理发泡聚乙烯(绝缘) + (锡丝+ 铝) + 聚氯乙烯(聚乙烯) RVV ( 227IEC52/53 ) 聚氯乙烯绝缘软电缆用途:家用电器、小型电动工具、仪表及动力照明 AVVR 聚氯乙烯护套安装用软电缆 SBVV HYA 数据通信电缆(室内、外)用于电话通信及无线电设备的连接以及电话配线网的分线盒接线用RV 、RVP 聚氯乙烯绝缘电缆 RVS 、RVB 适用于家用电器、小型电动工具、仪器、仪表及动力照明连接用电缆 BV 、BVR 聚氯乙烯绝缘电缆用途:适用于电器仪表设备及动力照明固定布线用 RIB 音箱连接线(发烧线) KVV 聚氯乙烯绝缘控制电缆用途:电器、仪表、配电装置信号传输、控制、测量 SFTP 双绞线传输电话、数据及信息网 UL2464 电脑连接线
高速线材生产的质量控制(DOC42页)
线材生产的质量控制及 缺陷说明书 线材的表面要求光洁和不得有妨碍使用的缺陷,即不得有耳子、裂纹、折叠、结疤、夹层等缺陷,允许有局部的压痕、凸块、凹坑,划伤和不严重的麻面。线材无论直接用于建筑还是深加工成各类制品,其耳子、裂纹、折叠、结疤、夹层等直接影响使用性能的缺陷都是绝对不允许有的。至于影响表面光洁度的一些缺陷可根据使用要求予以控制,直接用作钢筋的线材表面光洁程度影响不大。用于冷墩的线材对划伤比较敏感,凸块则影响拉拔。 几种线材表面缺陷的深度限量 5.5~9mm线材的表面缺陷深度限量,mm 线材的表面氧化铁皮越少越好,要求氧化铁皮的总量<10kg/t, 控制高价氧化铁皮(Fe 2O 3 、Fe 3 O 4 )的生成要严格控制终轧温度、吐 丝温度和线材在350℃以上温度停留的时间. 冷拉、冷墩用线材的脱碳层要求 缩孔、夹杂、分层、过烧等都是不允许存在的缺陷。
热轧盘条的质量控制 高速线材轧机生产的热轧盘条的质量通常包括两个方面的内容:一是盘条的尺寸外形,即尺寸精度及外表形貌;二是盘条的内在质量,即化学成分、微观组织和各种性能。前者主要由盘条轧制技术控制,后者除去轧制技术之外,还严重受上游工序的影响。 任何质量控制都要靠严格的完整的质量保证体系,靠工厂工序的保证能力,靠质量控制系统的科学、准确、及时的测量、分析和反馈。高速线材轧机是高度自动化的现代轧钢设备,其质量控制概念也必须着眼于全系统的各个质量环节。为了准确的判断和控制缺陷,首先要把缺陷产生的原因分析清楚,并设法将它控制消灭在最初工序。缺陷的清理或钢材的判废越早,损失越少。 (一)外形尺寸 高速线材轧机精轧机组的精度很高,轧辊质量很好,当速度控制系统灵敏,孔型轧制制度合理,并且调整技术熟练时,它生产的盘条精度可以大大超过老式盘条的精度。 热轧盘条尺寸精度允许的偏差(GB/T14981)