涂覆涂料前钢材表面处理 表面清洁度的评定试验 第6部分:可溶
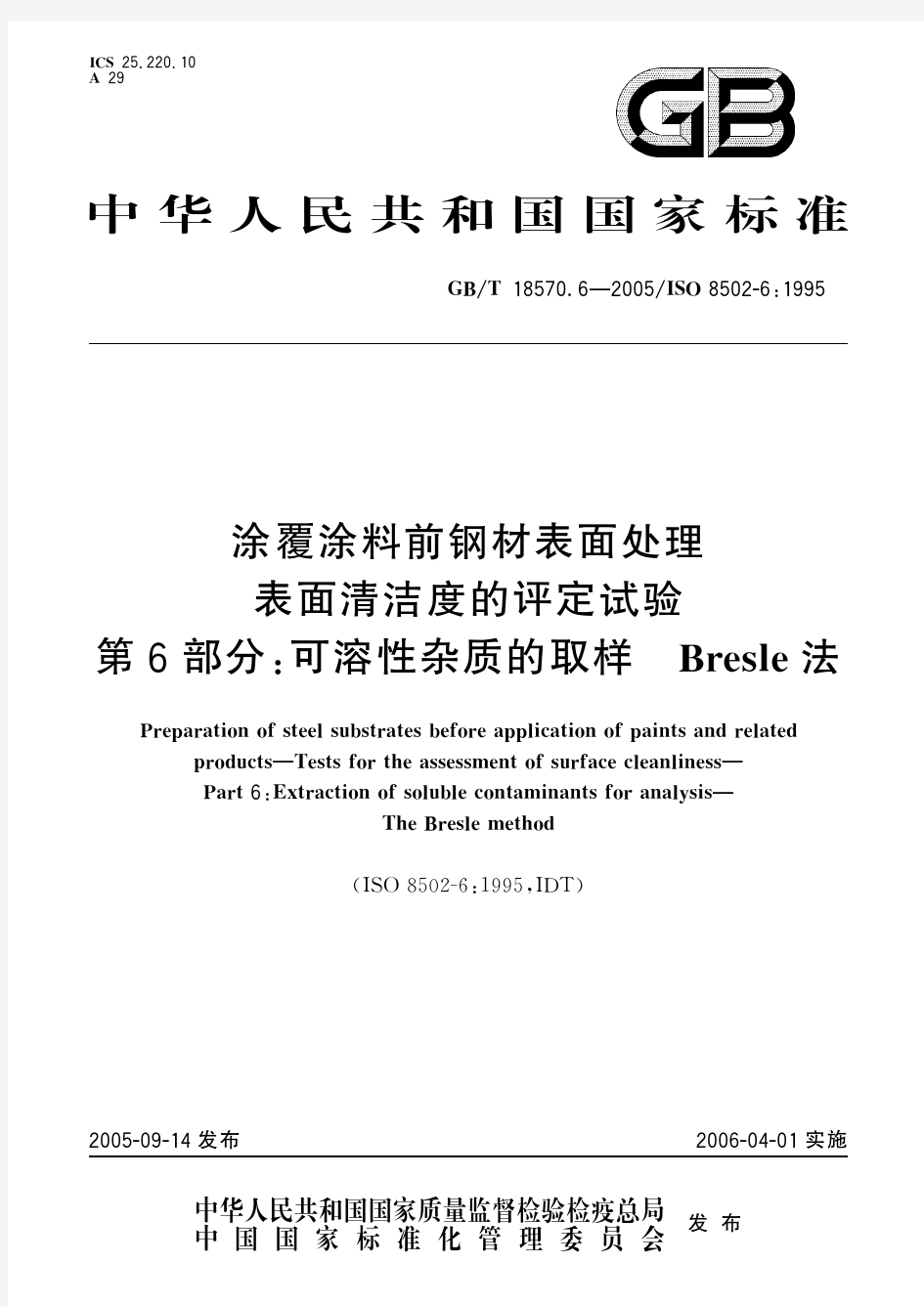
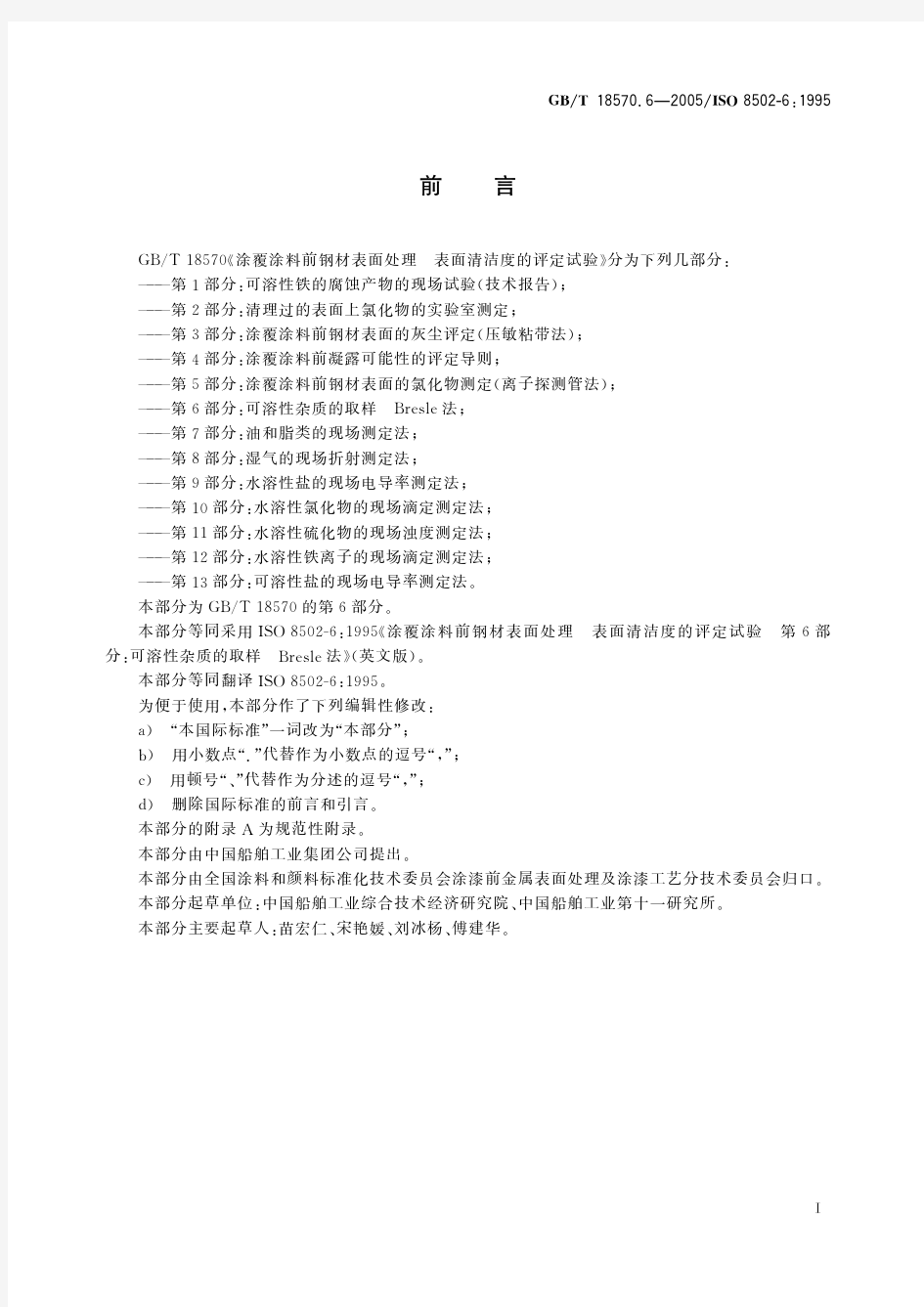
GB8923-88《涂装前钢材表面锈蚀等级和除锈等级》
涂装前钢材表面锈蚀等级和除锈等级 GB8923-88 Rust grades and preparation grades
of steel surfaces before application
of paints and related products
本标准规定了涂装前钢材表面锈蚀程度和除锈质量的目视评定等级。它适用于以喷射或抛射除锈、手工和动力工具除锈以及火焰除锈方式处理过的热轧钢材表面。冷轧钢材表面除锈等级的评定也可参照使用。 本标准等效采用国际标准ISO8501-1:1988 《涂装油漆和有关产品前钢材预处理——表面清洁度的目视评定——第一部分:未涂装过的钢材和全面清除原有涂层后的钢材的锈蚀等级和除锈等级》。 1. 总则 1.1 本标准将未涂装过的钢材表面原始锈蚀程度分为四个“锈蚀等级”,将未涂装过的钢材表面及全面清除过原有涂层的钢材表面除锈后的质量分为若干个“除锈等级”。钢材表面的锈蚀等级和除锈等级均以文字叙述和典型样板的照片共同确定。
1.2本标准以钢材表面的目视外观来表达锈蚀等级和除锈等级。评定这些等级时,应在适度照明条件下,不借助于放大镜等器具,以正常视力直接进行观察。 2. 锈蚀等级 钢材表面的四个锈蚀等级分别以A、B、C和D表示。这些锈蚀等级的典型样板照片见第5章,其文字叙述如下:
A全面地覆盖着氧化皮而几乎没有铁锈的钢材表面;
B已发生锈蚀,并且部分氧化皮已经剥落的钢材表面;
C氧化皮已因锈蚀而剥落,或者可以刮除,并且有少量点蚀的钢材表面;
D氧化皮已因锈蚀而全面剥离,并且已普遍发生点
RH-LF 和LF-VD 工艺生产管线钢洁净度的比较
RH-LF和LF-VD工艺生产管线钢洁净度的比较 一、电弧炉炼钢的时代特点 1、变为初炼炉 进入20 世纪80年代后,随着炉外精炼技术、工艺、装备的快速发展,原冶炼工艺中在电弧炉内完成的合金钢、特殊钢的脱氧、合金化、除气、去夹杂的电炉“重头戏”移到炉外精炼炉去进行了。电弧炉及转炉皆变为只须向炉外精炼炉提供含碳、硫、磷、温度、合金化合格或基本合格的钢水就算完成任务的炼钢初炼炉。改变和结束了原电弧炉的熔时长(三个多小时)、老三期操作(熔化期、氧化期、还原期)以及产量低、渣量大、炉容小、成本高的状况。 2、炉容大型化 随着电炉—炉外精炼—连铸—直接轧材工艺的发展,这种短流程(相对于焦化、烧结—高炉—转炉—炉外精炼炉—连铸—)轧材工艺而言的轧机产量要求电炉与之相匹配,例如长材年产50-80 万t、板材100-200 万t 、热轧卷年产200万t以上,因此单一匹配电炉的炉容量和生产率,生产速率必须与轧机相衔接. 目前, 较多采用公称炉容量80-120万t 左右的电弧炉,从趋势看炉容量仍在提高。变压器向超高功率发展(1000KV A/t)。 3 、电炉转炉化 氧气顶吹转炉依靠铁水为原料,吹氧冶炼故冶炼周期短(20min左右),产量高,即获得了比电炉高的多的生产率和生产速率( 科技工作者在20 世纪50年代在电弧炉上吹氧(炉门和炉顶)兑入约30%~50%的铁水(EOF 炉),把转炉的工艺优势移植过来,电炉的冶炼周期大大缩短,目前均在45min 左右( 故电炉顶吹氧、热装铁水、电炉双炉壳很快得到推广。 4、电弧炉钢产量大幅增长 在上述三项电炉自身工艺变化的同时,随着社会发电技术,能力的增长(核电站、水力发电等)及社会废钢量的增加,直接还原铁DRI、HBI、Fe3C 技术工艺的发展,都为电弧炉快速发展提供了条件. 因此,世界各国电弧炉钢产量由1950 年占世界总产钢量的6.5%增至1990 年的27.5% , 2003 年的36%. 5、提质、降耗、防污染使电弧炉获得新的活力 电弧炉使用废钢为原料与使用高炉铁水的转炉相比,总能耗是高炉-转炉工艺的1/2~1/3。
洁净室温湿度如何控制
如何对洁净室温湿度进行控制 洁净室的温湿度主要是根据工艺要求来确定,但在满足工艺要求的条件下,应考虑到人的舒适度感。随着空气洁净度要求的提高,出现了工艺对温湿度的要求也越来越严的趋势。净化工程具体工艺对温度的要求以后还要列举,但作为总的原则看,由于加工精度越来越精细,所以对温度波动范围的要求越来越小。例如在大规模集成电路生产的光刻曝光工艺中,作为掩膜板材料的玻璃与硅片的热膨胀系数的差要求越来越小。直径100 um的硅片,温度 洁净室的温湿度主要是根据工艺要求来确定,但在满足工艺要求的条件下,应考虑到人的舒适度感。随着空气洁净度要求的提高,出现了工艺对温湿度的要求也越来越严的趋势。 净化工程具体工艺对温度的要求以后还要列举,但作为总的原则看,由于加工精度越来越精细,所以对温度波动范围的要求越来越小。例如在大规模集成电路生产的光刻曝光工艺中,作为掩膜板材料的玻璃与硅片的热膨胀系数的差要求越来越小。直径100 um的硅片,温度上升1度,就引起了0.24um线性膨胀,所以必须有±0.1度的恒温,同时要求湿度值一般较低,因为人出汗以后,对产品将有污染,特别是怕钠的半导体车间,这种车间不宜超过25度。 湿度过高产生的问题更多。相对湿度超过55%时,冷却水管壁上会结露,如果发生在精密装置或电路中,就会引起各种事故。相对湿度在50%时易生锈。此外,湿度太高时将通过空气中的水分子把硅片表面粘着的灰尘化学吸附在表面耐难以清除。相对湿度越高,粘附的难去掉,但当相对湿度低于30%时,又由于静电力的作用使粒子也容易吸附于表面,同时大量半导体器件容易发生击穿。对于硅片生产最佳温度范围为35—45%。 洁净室中的气压规定 对于大部分洁净空间,为了防止外界污染侵入,需要保持内部的压力(静压)高于外部的压力(静压)。压力差的维持一般应符合以下原则: 1.洁净空间的压力要高于非洁净空间的压力。 2.洁净度级别高的空间的压力要高于相邻的洁净度级别低的空间的压力。 3.相通洁净室之间的门要开向洁净度级别高的房间。 压力差的维持依靠新风量,这个新风量要能补偿在这一压力差下从缝隙漏泄掉的风量。所以压力差的物理意义就是漏泄(或渗透)风量通过洁净室的各种缝隙时的阻力。 洁净室中的气流速度规定 这里要讨论的气流速度是指洁净室内的气流速度,在其他洁净空间中的气流速度在讨论具体设备时再说明。 对于乱流洁净室由于主主要靠空气的稀释作用来减轻室内污染的程度,所以主要用换气次数这一概念,而不直接用速度的概念,不过对室内气流速度也有如下要求; (1)送风口出口气流速度不宜太大,和单纯空调房间相比,要求速度衰减更快,扩散角度更大。 (2)吹过水平面的气流速度(例如侧送时回流速度)不宜太大,以免吹起表面微粒重返气流,而造成再污染,这一速度一般不宜大干0.2m/s。 对于平行流洁净室《习惯上称层流洁净室),由于主要靠气流的“活塞打挤压作用排除行染,所以截面上的速度就是非常重要的指标。过去都参考美国20gB标准,采用0.45m/s.但人们也都了解到这样大速度所需要的通风量是极大的,为了节能,也都在探求降低速一风速的可行性。 在我国,《空气洁净技术措施》和<洁净厂房设计规范))都是这样规定的 垂直平行流(层流)洁净室≥0.25m/s 水平平行流(层流)洁净室≥0.35 m/s 研究表明以上规定基本上满足控制污染的要求,但认为应区别不同情况分出不同的档别,更能体现节能的目的。
钢材除锈等级标准及对比图
钢材除锈等级标准 表面处理是取得良好涂装效果的关键。表面处理的投资相当可观,因此,对选择表面处理方法和油漆配套必须作周密的考虑。 用国际标准来衡量表面处理也是很重要的,如瑞典标准SIS055900或ISO8501。 锈蚀等级 表面处理标准的根本点是四个不同的锈蚀等级: A级钢材表面完全覆盖粘附的氧化皮,几乎无铁锈。 B级钢材表面已开始锈蚀,氧化皮开始成片状脱落。 C级钢材表面上的氧化皮已锈蚀或可刮除,但裸眼可看到轻微锈点。 D级钢材表面上的氧化皮已锈蚀剥落,裸眼可看到大量锈点。 根据SIS055900,这些锈蚀等级的表面处理是根据以下质量标准进行钢丝刷除锈和喷砂除锈的: St-钢丝刷除锈标准St2,St3 Sa-喷砂除锈标准Sa1,Sa2,,Sa3 喷砂除锈-Sa 喷砂除锈前应凿去所有的厚锈层,可见的油、脂和污物也应去除。喷砂除锈后,表面应清洁,无灰尘和碎悄屑。 Sa1级轻度喷砂除锈 表面应无可见的油脂、污物、附着不牢的氧化皮、铁锈、油漆涂层和杂质。 Sa2级彻底的喷砂除锈 表面应无可见的油脂、污物,氧化皮、铁锈、油漆涂层和杂质基本清
级非常彻底的喷砂除锈 表面应无可见的油脂、污物、不牢的氧化皮、铁锈、油漆涂层和杂质,残留物痕迹仅显示点状或条纹状的轻微色斑。 Sa3级喷砂除锈至钢材表现洁净 表面应无油脂、氧化皮、铁锈、油漆涂层和杂质,表面具有均匀的金属色泽。 钢丝刷除锈-St St2 彻底的手工和动力工具除锈 表面应无可见的油脂、污物、附着不牢的氧化皮,铁锈、油漆涂层和杂质。 St3 非常彻底的手工和动力工具除锈 同St2,但应比St2处理得更彻底,金属底材呈现金属光泽。
钢铁表面处理标准说明及各标准比较
钢铁表面主要表面处理标准 GB8923-88 中国国家标准 ISO8501-1:1988 国际标准化组织标准 SIS055900-1967 瑞典标准 SSPC-SP2,3,5,6,7和10 美国钢结构涂装协会表面处理标准 BS4232 英国标准 DIN55928 德国标准 JSRA SPSS 日本造船研究协会标准国标GB8923-88 对除锈等级描述: 喷射或抛射除锈以字母“Sa”表示。本标准订有四个除锈等级: Sa1 轻度的喷射或抛射除锈 钢材表面应无可见的油脂和污垢,并且没有附着不牢的氧化皮,铁锈和油漆涂层等附着物。Sa2 彻底的喷射或抛射除锈 钢材表面应无可见的油脂和污垢,并且氧化皮,铁锈和油漆涂层等附着物已基本清除,其残留物应该是附着牢固的。 Sa2.5 非常彻底的喷射或抛射除锈 钢材表面应无可见的油脂,污垢,氧化皮,铁锈和油漆涂层等附着物,任何残留的痕迹应仅是点状或条纹状的轻微色斑。 Sa3 钢材表面外观洁净的喷射或抛射除锈 钢材表面应无可见的油脂,污垢,氧化皮,铁锈和油漆涂层等附着物,该表面应显示均匀的金属色泽。 手工和动力工具除锈以字母“St”表示。本标准订有二个除锈等级: St2 彻底的手工和动力工具除锈 钢材表面应无可见的油脂和污垢,并且没有附着不牢的氧化皮、铁锈和油漆涂层等附着物。 St3 非常彻底的手工和动力工具除锈 钢材表面应无可见的油脂和污垢,并且没有附着不牢的氧化皮、铁锈和油漆涂层等附着物。除锈应比St2更为彻底,底材显露部分的表面应具有金属光泽。
我国的除锈标准与相当的国外除锈标准对照表: 注:SSPC中的Sp6比Sa2.5 略为严格,Sp2为人工钢丝刷除锈,Sp3为动力除锈。 表面粗糙度及其评定 喷砂、抛丸、手工和动力除锈,其目的除达到前述一定的表面清洁度外,还会对钢铁表面造成一定的微观不平整度,即表面粗糙度。对于涂漆前钢铁表面的粗糙度通常以一些主要的波峰和波谷间的高度值来表示。钢铁表面粗糙度对漆膜的附着力,防腐蚀性能和保护寿命有很大影响。钢铁表面合适的粗糙度有利于漆膜保护性能的提高,粗糙度太小,不利于漆膜的附着力的提高,粗糙度太大,如漆膜用量一定时,则会造成漆膜厚度分布的不均匀,特别是在波峰处的漆膜厚度不足而低于设计要求,引起早期的锈蚀,此外,粗糙度过大,还常在较深的波谷凹坑内截留住气泡,将成为漆膜起泡的根源。 对于常用涂料,合适的粗糙度范围以39—75um为宜。
洁净区人员控制管理制度
洁净区人员控制管理制度 目的:制定洁净室从员控制管理规定,确保洁净室洁净度不低于控制标准。 二、适用范围:适用于生产部洁净区各生产岗位。 三、责任者:生产部管理人员、生产操作者、QA监督员。 四、管理规定: 1.洁净室仅限于该区域生产操作人员、生产部管理人员和经批准的人员进入。 2.洁净室内生产操作人同定员上岗,限制操作人同和管理人员进入的人数。3.洁净室生产操作人员定员和允许进入的最多人员如下:
环境突发事故应急救援预案 目录 编写说明………………………………………………………………… 1.基本情况……………………………………………………………… 2.环境污染目标及其特性、对周围的影响…………………………… 3、应急救援组织机构、组成、职责划分…………………………… 4.报警、通讯联系方式………………………………………………… 5.事故发生后应采取的处理措施…………………………………… 6.人员紧急疏散、撤离……………………………………………… 7.危险区的隔离……………………………………………………… 8.检测、抢险、救援及控制措施…………………………………… 9.现场保护与现场洗消……………………………………………… 10.应急救援保障……………………………………………………… 11.事故应急救援终止程序…………………………………………… 12.应急救援培训计划………………………………………………… 13.附件: ……………………………………………………………… (1)组织机构名单………………………………………………… (2)值班联系电话………………………………………………… (3)组织应急救援有关人员联系电话…………………………… (4)政府有关部门联系电话…………………………………… (5)平面布置图…………………………………………………… (6)周边区域的单位、社区、重要基础设施分布图及有关联系方式,供电、供水单位的联系方式…………………………… (7)保障制度………………………………………………………
钢材表面锈蚀和除锈等级标准
【摘要】一、钢材表面锈蚀和除锈等级标准为国家标准GB8923-88《涂装前钢材表面锈蚀等级和除锈等级》。 二、标准将除锈等级分成喷射或抛射除锈、手工和电动除锈、火焰除锈三种类型。 三、喷射和抛射除锈,用字母“sa”表示,分四个等级: 一、钢材表面锈蚀和除锈等级标准为国家标准GB8923-88《涂装前钢材表面锈蚀等级和除锈等级》。 二、标准将除锈等级分成喷射或抛射除锈、手工和电动除锈、火焰除锈三种类型。 三、喷射和抛射除锈,用字母“sa”表示,分四个等级: sa1——轻度的喷射后抛射除锈。钢材表面无可见的油脂、污垢、无附着的不牢的氧化皮、铁锈、油漆涂层等附着物。 sa2——彻底的喷射或抛射除锈。钢材表面无可见的油脂、污垢,氧化皮、铁锈等附着物基本清除。 sa21/2——非常彻底的喷射或抛射除锈。钢材表面无可见的油脂、污垢、氧化皮、铁锈、油漆涂层等附着物,任何残留的痕迹仅是点状或条状的轻微色斑。 sa3——使钢材表面非常洁净的喷射或抛射除锈。钢材表面无可见的油脂、污垢、氧化皮、铁锈、油漆涂层等附着物,该表面显示均匀的金属色泽。 手工除锈等级: St2 彻底的手工和动力工具除锈 钢材表面应无可见的油脂和污垢,并且没有附着不牢的氧化皮、铁锈和油漆涂层等附着物。St3 非常彻底的手工和动力工具除锈 钢材表面应无可见的油脂和污垢,并且没有附着不牢的氧化皮、铁锈和油漆涂层等附着物。除锈应比St2更为彻底,底材显露部分的表面应具有金属光泽。 表面处理是取得良好涂装效果的关键。表面处理的投资相当值得。因此,对选择表面处理方法和油漆配套系统必须作周密的考虑。 用国际标准来衡量表面处理程度是很重要的,如瑞典标准:SIS055900或ISO08501。 锈蚀等级 表面处理标准的根本点是四个不同的锈蚀等级: A级钢材表面完全覆盖粘附的氧化皮,几乎无铁锈。 B级钢材表面已经开始锈蚀,氧化皮开始呈片状脱落。 C级钢材表面上的氧化皮已锈蚀,或可刮除,但裸眼可看到轻微锈点。 D级钢材表面上的氧化皮已锈蚀剥落,裸眼可看到大量锈点。 根据SIS055900,这些锈蚀等级的表面处理是根据以下质量标准进行钢丝刷除锈和喷砂除锈的: St - 钢丝刷除锈标准St2,St3 Sa - 喷砂除锈标准Sa1,Sa2,Sa2.5,Sa3 钢丝刷除锈- St St2 彻底的手工和动力工具除锈 表面应无可见的油脂、污物、氧化皮、铁锈、油漆涂层和杂质。 St3 非常彻底的手工和动力工具除锈 同St2,但应比St2处理得更彻底,金属底材呈金属光泽。 这些标准对表面处理有很大的指导和帮助,油漆供应商一般对每种类型的油漆规定有相应的表面处理标准和要求。 喷砂除锈- Sa 喷砂除锈前应去除表面所有的厚锈层,可见的油,脂和污物也应去除。喷砂除锈后表面应清
钢材表面清洁度的评定
钢材表面清洁度的评定 为了充分发挥涂料的保护和装饰作用,必须进行彻底的表面处理已为人们公认。涂装成功与否主要取决于表面处理质量。通常表面清洁度(表面处理质量)越高,越能保证涂料的保护作用,但过高的要求也会造成极大的浪费。对钢材表面清洁度的进行评定是一项至关重要的工作。表面处理质量包括三个方面,即钢板表面的可视清洁度(锈蚀、氧化皮等)、粗糙度和不可视清洁度(油脂、可溶性铁盐、氯化物、硫化物、灰尘等),在这方面以船舶行业为代表,已经形成了较完善的检测标准和体系,其他行业一般均参照执行。 一、钢材表面可视清洁度(锈蚀、氧化皮)的评定 钢材表面可视清洁度(锈蚀、氧化皮)的评定,可分为定量和定性两种方法。 定量方法一般有两种,第一种为硫酸铜法:将硫酸铜溶液刷在处理后的钢板表面,除锈完全的部分呈金属铜的颜色,而大于0.5mm残留氧化皮的部分呈暗色,从而判断表面的清洁程度。可采用在每升含1gH2SO4的溶液中添加4~8gCu2SO4的方法配制硫酸铜溶液,或将36gCu2SO4·5H20加热溶于100ml水中,再加入过量的Cu(OH)放置24小时后,去除多余的Cu(OH)2的方法来配制硫酸铜溶液。第二种定量检测方法是利用氧化皮和铁电阻不同的特点,采用电阻测量仪测定处理后的表面与探头2 (直径1mm的球型笔状电极)之间的过渡电阻,通过各点的平均值判断表面清洁度。此外,还可利用带蓝色过滤器的光线反射测量仪进行表面清洁度检验。 仪器定量测量方法受光线、处理方法、原始状态和表面粗糙度等影响极大,而硫酸铜法又需要进行后处理,否则会留下腐蚀隐患,所以,更为可靠的方法还是定性的与标准照片进行对比的方法。 为了能正确、方便地评定钢材在除锈之后的表面处理质量,许多工业发达国家都先后制定了钢材除锈的质量等级标准,其中最显著的是瑞典工业标准SIS055900《涂装前钢材表面除锈标准》,长期以来为世界各国所引用。国际标准化组织色漆和清漆技术委员会涂装前钢材表面处理分会(ISO/TC 35/SC12)以瑞典标准SIS055900-1967为基础,制订了国际标准ISO8501-1:1988《涂装油漆和有关产品前钢材预处理-表面清洁度的目视评定-第一部分:未涂装过的钢材和全面清除原有涂层后的钢材的锈蚀等级和除锈等级》。我国标准为GB8923-88《涂装前钢材表面锈蚀等级和除锈等级》。 上述标准将未涂装过的钢材表面原始锈蚀程度分为四个“锈蚀等级”,将钢材表面除锈后的质量分为若干个“除锈等级”。钢材表面的锈蚀等级和除锈等级均以文字叙述和典型样板的照片共同确定。 1、锈蚀等级 除锈前钢材表面原始锈蚀状态对除锈的难易程度和除锈后的表面外观质量具有较大影响。因此,该标准根据钢材表面氧化皮覆盖程度和锈蚀状况将其原始锈蚀程度分为四个等级,分别以A、B、C、D表示。 A 全面地覆盖着氧化皮而几乎没有铁锈的钢材表面。 B 已发生锈蚀,并且部分氧化皮已经剥落的钢材表面。 C 氧化皮已因锈蚀而剥落,或者可以刮除,并且有少量点蚀的钢材表面。 D 氧化皮已因锈蚀而全面剥落,而且已普遍发生点蚀的钢材表面。 2、除锈等级 该标准对喷射或抛射除锈、手工和动力工具除锈、火焰除锈后的钢材表面清洁度规定了相应的除锈等级,分别以字母Sa、St、F1表示,字母后的阿拉伯数字则表示 1
洁净室温湿度如何控制精编版
洁净室温湿度如何控制公司标准化编码 [QQX96QT-XQQB89Q8-NQQJ6Q8-MQM9N]
如何对洁净室温湿度进行控制 提高,出现了工艺对温湿度的要求也越来越严的趋势。 净化工程具体工艺对温度的要求以后还要列举,但作为总的原则看,由于加工精度越来越精细,所以对温度波动范围的要求越来越小。例如在大规模集成电路生产的光刻曝光工艺中,作为掩膜板材料的玻璃与硅片的热膨胀系数的差要求越来越小。直径100 um的硅片,温度上升1度,就引起了线性膨胀,所以必须有±度的恒温,同时要求湿度值一般较低,因为人出汗以后,对产品将有污染,特别是怕钠的半导体车间,这种车间不宜超过25度。 湿度过高产生的问题更多。相对湿度超过55%时,冷却水管壁上会结露,如果发生在精密装置或电路中,就会引起各种事故。相对湿度在50%时易生锈。此外,湿度太高时将通过空气中的水分子把硅片表面粘着的灰尘化学吸附在表面耐难以清除。相对湿度越高,粘附的难去掉,但当相对湿度低于30%时,又由于静电力的作用使粒子也容易吸附于表面,同时大量半导体器件容易发生击穿。对于硅片生产最佳温度范围为35—45%。 洁净室中的气压规定 对于大部分洁净空间,为了防止外界污染侵入,需要保持内部的压力(静压)高于外部的压力(静压)。压力差的维持一般应符合以下原则: 1.洁净空间的压力要高于非洁净空间的压力。 2.洁净度级别高的空间的压力要高于相邻的洁净度级别低的空间的压力。 3.相通洁净室之间的门要开向洁净度级别高的房间。 压力差的维持依靠新风量,这个新风量要能补偿在这一压力差下从缝隙漏泄掉的风量。所以压力差的物理意义就是漏泄(或渗透)风量通过洁净室的各种缝隙时的阻力。 洁净室中的气流速度规定 这里要讨论的气流速度是指洁净室内的气流速度,在其他洁净空间中的气流速度在讨论具体设备时再说明。 对于乱流洁净室由于主主要靠空气的稀释作用来减轻室内污染的程度,所以主要用换气次数这一概念,而不直接用速度的概念,不过对室内气流速度也有如下要求; (1)送风口出口气流速度不宜太大,和单纯空调房间相比,要求速度衰减更快,扩散角度更大。 (2)吹过水平面的气流速度(例如侧送时回流速度)不宜太大,以免吹起表面微粒重返气流,而造成再污染,这一速度一般不宜大干s。 对于平行流洁净室《习惯上称层流洁净室),由于主要靠气流的“活塞打挤压作用排除行染,所以截面上的速度就是非常重要的指标。过去都参考美国20gB标准,采用s.但人们也都了解到这样大速度所需要的通风量是极大的,为了节能,也都在探求降低速一风速的可行性。 在我国,《空气洁净技术措施》和<洁净厂房设计规范))都是这样规定的 垂直平行流(层流)洁净室≥s 水平平行流(层流)洁净室≥ m/s 研究表明以上规定基本上满足控制污染的要求,但认为应区别不同情况分出不同的档别,更能体现节能的目的。
各行业无尘室及洁净度特点
各行业无尘室及洁净度特点 电子制造业: 随着计算机、微电子和信息技术的发展,推动了电子制造业的飞速发展,也带动了洁净室技术的发展,同时对洁净室的设计提出了更高的要求,电子制造业的无尘车间设计是一项综合的技术,只有充分了解电子制造业的无尘车间设计特点,做到设计合理,才能让电子制造产业的产品次品率降低,提高生产效率。 电子制造业洁净室的特点: 洁净度等级要求高,风量、温度、湿度、压差、设备排风按需受控,照度、洁净室截面风速按设计或规范受控,另外该类洁净室对静电要求极其严格。其中对湿度的要求尤甚。因为过于干燥的厂房内极易产生静电,造成CMOS集成损坏。一般来说,电子厂房的温度应控制在22℃左右,相对湿度控制在50-60%之间(特殊洁净车间有相关温湿度规定)。这时可有效地消除静电,并使人也感觉舒适。芯片生产车间、集成电路无尘室和磁盘制造车间是属于电子制造行业洁净室的重要组成部分,由于电子产品在制造、生产过程中对室内空气环境和品质的要求极为严格,主要以控制微粒和浮尘为主要对象,同时还对其环境的温湿度、新鲜空气量、噪声等作出了严格的规定。 1、电子制造厂万级洁净室内的噪声级(空态):不应大于65dB(A)。 2、电子制造厂洁净室垂直流洁净室满布比不应小于60%,水平单向流洁净室不应小于40%,否则就是局部单向流了。 3、电子制造厂洁净室与室外的静压差不应小于10Pa,不同空气洁净度的洁净区与非洁净区之间的静压差不应小于5Pa。
4、电子制造行业万级洁净室内的新鲜空气量应取下列二项中的最大值: (1)补偿室内排风量和保持室内正压值所需的新鲜空气量之和。 (2)保证供给洁净室内每人每小时的新鲜空气量不小于40m3。 (3)电子制造行业洁净室净化空调系统加热器,应设置新风,超温断电保护,若采用点加湿时应设置无水保护,寒冷地区,新风系统应设置防冻保护措施。无尘室的送风量,应取下面三项最大值:保证电子制造厂无尘室空气洁净度等级的送风量;根据热,湿负荷计算确定电子厂洁净室的送风量;向电子制造厂洁净室内供给的新鲜空气量。 生物制造业: 生物制药工厂的特点: 1、生物制药工厂不仅设备费用高、生产工艺复杂、洁净级别和无菌的要求高,而且对生产人员的素质有严格的要求。 2、在生产过程中会出现潜在的生物危害,主要有感染危险,死菌体或死细胞及成分或代谢对人体和其他生物致毒性、致敏性和其他生物学反应,产品的致毒性、致敏性和其他生物学反应,环境效应。 洁净区: 需要对环境中尘粒及微生物污染进行控制的房间(区域),其建筑结构、装备及其使用均具有防止该区域内污染物的引入、产生和滞留的功能。 气锁间: 设置于两个或数个房间之间(如不同洁净度级别的房间之间)的具有两扇或多扇门的隔离空间。设置气锁间的目的是在人员或物料出入其间时,对气流进
钙处理工艺对低碳冷镦钢洁净度的影响
118 2007年炉外精炼年会论文集 钙处理工艺对低碳冷镦钢洁净度的影响 高振波1)梁海庆1)吴坚1)胡义贵1)李颂1)杜松林1, 2) 1) 马钢第三钢轧总厂,安徽马鞍山,243000 2) 北京科技大学冶金与生态工程学院,北京100083 摘要本文对钙处理工艺过程中夹杂物变性处理需要的钙含量以及硫化钙的生成条件进行了 热力学计算,确定了LF处理后硫含量需控制的上限和钙处理后钙含量所需的下限;并对温度和 喂钙线量对钙的收得率的影响、钙处理后弱吹氩时间对钢中钙和铝的损失进行了试验摸索。以理 论计算和试验结果为基础,优化钙处理工艺,保证LF处理后钢液含硫不大于0.007%,按每炉钢 喂钙线100~200m、喂钙线后弱吹氩15~30分钟,最终提高低碳冷镦钢夹杂物合格率达到92%。 关键词冷镦钢;钙处理;弱吹氩;洁净度;夹杂物 冷镦钢主要用于制造紧固件产品,客户对冷 镦钢的使用性能和加工性能要求很高,这样要求冷镦钢具有较好的内部质量,夹杂物大小、分布、数量、种类均较好。作为衡量钢材质量的一个重要指标—夹杂物等级,通过电镜扫描、能谱分析等手段,根据冷镦钢夹杂物评级标准,检测到马钢第三钢轧总厂(以下简称三钢轧)冷镦钢夹杂物合格率83%,B类和DS类夹杂物超标较多。实践证明,钙处理是控制夹杂物的重要环节。本文通过理论计算和试验并结合生产实践,提出了钙处理工艺优化的方向,并付诸实践,有效提高了低碳冷镦钢洁净度。1工况条件简介 1.1 工艺路线 铁水预处理—50t复吹转炉—吹氩合金微调站—70t LF炉—六机六流140mm方坯连铸机—高速线材轧机 LF工序配备双管喂线机; 140mm方坯连铸机浇注方式为“外装式浸入水口+保护渣”。 1.2 钢种内控成份 冷镦钢成分请见表1 表1 马钢冷镦钢内控成分/% Table 1 controlled component of cold heading steel/% wt/% C Si Mn S P Al ≤0.10 ≤0.08 0.20~0.5≤0.015 ≤0.030 0.020~0.040 1.3 检测方法 (1)使用瑞士ARL-4460型光谱仪快速分析钢中C、Si、Mn、P、S、Al等元素; (2)通过电镜扫描观察夹杂物形态,能谱分析夹杂物组成; (3)采用小样电解分析夹杂物总量; (4)采用TOS针状全氧取样器取样,检验全氧、氮。 2 试验结果及分析 钙处理主要目是使高熔点的Al2O3变性为低熔点的铝酸钙,再经过一段时间弱吹氩,降低非金属夹杂物含量,从而改善钢液的可浇性,提高钢液的洁净度。 由于钙的沸点低(约1487℃)、蒸气压大、在钢中溶解度低,向钢包钢液内喂钙线进行钙处理过程钢液沸腾非常严重,这必然导致钢液的二次氧化,因此,怎样既能达到钙处理的目的,又能使二次氧化程度降到最小,以及喂过钙线后弱吹氩时间的掌握成为钙处理技术的关键。 2.1 钙处理前钢中硫含量对钙处理效果的影响 在钢包和中间包取样,通过电镜扫描和能谱分析,结果在钢包样里发现了少量硫化钙,在中间包样发现了更多硫化钙夹杂,请见图1和图2 。
纯净钢好
纯净钢 纯净钢一般是指钢中杂质元素磷、硫、氧、氮、氢、碳和非金属夹杂物含量很低的钢。在这里的杂质是随钢种变化的,这是因为某一类元素在某钢种内是有害杂质,但可能在另一种钢内其有害程度会减轻或者甚至是有益元素。也就是说对于钢性能要求不同,纯净钢所要求的控制因素和控制力度也不同。 纯净钢要求钢中硫含量小于50PPM,磷含量小于50PPM,氧含量小于10PPM,氢含量小于30PPM,氮含量小于50PPM。对于具体钢种会用不同标准。 钢材中的夹杂物可引起许多缺陷,钢的洁净度取决于钢中非金属夹杂物的数量、形态和尺寸分布, 因钢种及其用途不同而定义不同。 研究和控制钢的洁净度的关键是其精确的评价方法, 在炼钢生产的各个阶段测定夹杂物的数量、尺寸分布、形状和化学成分。尽管测定技术有多种(有精确而昂贵的直接测定法, 还有快速而廉价的间接测定法) , 只有可靠性是相对的选择依据。 直接测定法: (1) 金相显微镜观测(MMO );(2) 图像扫描( I A )法;(3) 硫印法;(4) 电解(蚀)法;(5) 电子束熔炼(EB)法;(6) 水冷坩埚熔炼法(CC);(7) 扫描电子显微术(SEM );( 8) 脉冲鉴别分析光谱测量法(O ES -PDA );(9) 曼内斯曼夹杂物检测法(M I DA S) ;(10) 激光衍射颗粒尺寸分析法(LDPSA );(11) 常规的超声波法(CU S);(12) 锥形样品扫描法;(13) 分级热分解法(FTD);(14) 激光显微探针质谱分析法(LAMM S);(15) X2射线光电子光谱法(XPS);(16) 俄歇电子光谱法(AES);(17) 光电扫描法;(18) 库尔特计数分析法;(19) 液态金属洁净度分析法(L I MCA );(20) 钢水超声技术。 间接方法: (1)定氧;(2)吸氮检测;(3)溶解铝减少值的检测;(4)炉渣成分检测;(5)检测浸入式水口结瘤。
《管道内部清洁度质量控制管理规定》
管道内部清洁度质量控制管理规定 (A版) 中国石油工程建设公司 宁夏石化炼油项目经理部
前言 本管理规定是根据《项目质量计划》(A 版)的要求编写的,是《项目质量计划》的支持性文件。 本规定由项目QA/QC 部提出。 本规定由QA/QC 部起草并负责管理。 本规定主要起草人:高安翔 审核人:张志 批准人:王家君
目录 1. 适用范围 (4) 2. 目的 (4) 3. 职责 (4) 4. 工作程序及要求 (4) 5. 相关资料 (9) 6. 附则 (9) 7. 附表 (9)
1. 适用范围 本管理规定适用于宁夏石化500 万吨/年炼油改造项目工程建设的管道内部清洁度质量控制。 2. 目的 明确和规范管道施工全过程各环节内部清洁度质量控制要求,确保设备、管线内清洁无异物,缩短管道吹扫、清洗、试车时间。 3. 职责 3.1 QA/QC 部: 3.1.1 3.1.2 3.2 3.2.1 3.2.2 负责项目管道内部清洁度质量控制管理规定的制定和修订; 监督、检查管道内部清洁度质量控制的实施情况。 施工技术部: 对施工承包商管道内部清洁度质量控制情况进行全程管理; 对管道内部清洁度质量控制不达标的施工承包商进行处理、 整顿。 3.3 采购部: 3.3.1 负责总承包单位采购的管道组成件的到货检验和发放施工承包商前的仓储管理。 3.4 3. 4.1 3.4.2 施工承包商: 在管道施工全过程对管道内部清洁度实施质量控制; 对管道系统内部清洁度进行自检,并形成确认记录。 4. 工作程序及要求 4.1 管道内部清洁度的质量控制应贯穿材料保管、防腐、预制、安
钢材除锈等级标准及对比图
钢材除锈等级标准及对 比图 The manuscript was revised on the evening of 2021
钢材除锈等级标准 表面处理是取得良好涂装效果的关键。表面处理的投资相当可观,因此,对选择表面处理方法和油漆配套必须作周密的考虑。 用国际标准来衡量表面处理也是很重要的,如瑞典标准SIS055900或 ISO8501。 锈蚀等级 表面处理标准的根本点是四个不同的锈蚀等级: A级钢材表面完全覆盖粘附的氧化皮,几乎无铁锈。 B级钢材表面已开始锈蚀,氧化皮开始成片状脱落。 C级钢材表面上的氧化皮已锈蚀或可刮除,但裸眼可看到轻微锈点。 D级钢材表面上的氧化皮已锈蚀剥落,裸眼可看到大量锈点。 根据SIS055900,这些锈蚀等级的表面处理是根据以下质量标准进行钢丝刷除锈和喷砂除锈的: St-钢丝刷除锈标准 St2,St3 Sa-喷砂除锈标准Sa1,Sa2,,Sa3 喷砂除锈-Sa 喷砂除锈前应凿去所有的厚锈层,可见的油、脂和污物也应去除。喷砂除锈后,表面应清洁,无灰尘和碎悄屑。 Sa1级轻度喷砂除锈 表面应无可见的油脂、污物、附着不牢的氧化皮、铁锈、油漆涂层和杂质。 Sa2级彻底的喷砂除锈 表面应无可见的油脂、污物,氧化皮、铁锈、油漆涂层和杂质基本清除,残留物应附着牢固。 级非常彻底的喷砂除锈 表面应无可见的油脂、污物、不牢的氧化皮、铁锈、油漆涂层和杂质,残
Sa3级喷砂除锈至钢材表现洁净 表面应无油脂、氧化皮、铁锈、油漆涂层和杂质,表面具有均匀的金属色泽。 钢丝刷除锈-St St2 彻底的手工和动力工具除锈 表面应无可见的油脂、污物、附着不牢的氧化皮,铁锈、油漆涂层和杂质。 St3 非常彻底的手工和动力工具除锈 同St2,但应比St2处理得更彻底,金属底材呈现金属光泽。
洁净钢新技术
洁净钢生产技术 摘要:钢的洁净度是反映钢的总体质量水平的重要标志,是钢的内在质量的保证指标。生产洁净钢,一是要提高钢的洁净度,二是严格控制钢中非金属夹杂物的数量和形态。文章总结了洁净钢的传统生产工艺以及部分的洁净钢生产新技术。 关键词:洁净钢;夹杂物;脱硫 洁净钢的概念是由Kiessling[1],在给英国钢铁学会的学术报告中首次提出的,泛指O,S,P,H,N及Pb,As,Cu,Zn 等杂质含量低的钢。一般意义上的洁净钢是指钢中五大杂质元素[S、P、H、N、O]含量很低,且对非金属夹杂物(泛指氧化物和硫化物)进行严格控制的钢种,而随着科学技术的发展,对钢材性能要求日益严格,对钢材质量要求不断提高,进一步减少钢中夹杂含量,提高钢的洁净度,是本世纪发展方向。 钢的洁净度是反映钢的总体质量水平的重要标志,是钢的内在质量的保证指标。钢的洁净度通常由钢中有害元素含量以及非金属夹杂物的数量、形态和尺寸来评价。为了获得“清洁和纯净” 的钢,常常要降低和控制钢的C、P、S、N、H 和T. O,因为这些元素的单一或综合作用的结果,可以大大地影响钢的性能,如抗拉强度、成型性、韧性、可焊性、抗裂纹和抗腐蚀性、各向异性、疲劳性能等[2]。因此,为了改善钢的性能,当今钢铁冶金技术特别注意降低钢中的P、S、N、H、T.O,并根据钢种需要降低和控制钢中C的含量。近半个世纪以来,特别是钢铁产品面临被新型工程材料如铝、塑料、玻璃等取代的巨大压力和挑战的今天,提高钢的洁净度越来越成为钢铁冶金技术研究的重要课题,也可以说提高钢的洁净度已成为每一个钢铁产品的任务。生产洁净钢,一是要提高钢的洁净度,二是严格控制钢中非金属夹杂物的数量和形态。不同钢种对洁净度的要求和对夹杂物的敏感性不同[3]。 1 传统生产工艺 1.1 铁水预处理 铁水预处理按处理任务不同可分为预脱硫、预脱磷和同时脱磷脱硫( 包括预脱硅) 。大规模工业生产,70年代采用KR机械搅拌法与喷吹法的预脱硫已能将铁水[S]降到0.001% ,80年代喷吹法预脱磷已能经济地将铁水[P]降到0.005% ~0.015% ,同时脱硫将[S]降到0.002% ~0.010%[4]。 20世纪80年代以来,铁水预处理已成为生产优质低磷、低硫钢必不可少的经济工序。其目标是将入转炉的铁水磷、硫含量脱至成品钢要求水平。欧美各国铁水预处理一般以预脱硫为主,而日本铁水“三脱” 预处理比例在90%以上[5]。目前,基于铁水预处理的转炉生产纯净钢工艺主要有两种流程:一种是基于铁水深度预脱硫,转炉强化脱磷,钢水炉外喷粉脱磷、脱硫、升温、真空精炼; 另一种是基于铁水三脱预处理,复吹转炉少渣吹炼,钢水炉外喷粉脱硫、真空精炼。后者具有生产效率高、石灰等造渣料消耗少、过程温降小、生产周期短、成本低等优点,经济效益显著高于前者,适宜于我国转炉钢厂采用。其中铁水三脱预处
涂装前钢材表面锈蚀等级和除锈等级
中华人民共和国国家标准 GB8923-88《涂装前钢材表面锈蚀等级和除锈等级》 前言 本标准规定了涂装前钢材表面锈蚀程度和除锈质量的目视评定等级。它适用于以喷射或抛射除锈、手工和动力工具除锈以及火焰除锈方式处理过的热轧钢材表面。冷轧钢材表面除锈等级的评定也可参照使用。 本标准等效采用国际标准ISO 8501-1:1988《涂装油漆和有关产品前钢材预处理——表面清洁度的目视评定——第一部分:未涂装过的钢材和全面清除原有涂层后的钢材的锈蚀等级和除锈等级》。 1 总则 1.0.1 为保证涂装前钢材表面的预处理质量,提高涂层的附着力和涂层质量,制定本规范。 1.0.2本规范适用于涂装前钢材表面的预处理。 1.0.3涂装前钢材表面的预处理除应符合本规范外,尚应符合国家现行的有关强制性标准的规定。 2 锈蚀等级 钢材表面的四个锈蚀等级分别以A、B、C和D表示。这些锈蚀等级的典型样板照片见第5章,其文字叙述如下: A 全面地覆盖着氧化皮而几乎没有铁锈的钢材表面; B 已发生锈蚀,并且部分氧化皮已经剥落的钢材表面; C 氧化皮已因锈蚀而剥落,或者可以刮除,并且有少量点蚀的钢材表面; D 氧化皮已因锈蚀而全面剥离,并且已普遍发生点蚀的钢材表面。 3 除锈等级 3.1通则 3.1.1 钢材表面除锈等级以代表所采用的除锈方法的字母“Sa”、“St"或“F1”表示。如果字母后面有阿拉伯数字,则其表示清除氧化皮、铁锈和油漆涂层等附着物的程度等级。 3.1.2钢材表面除锈等级的文字叙述见3.2、3.3和3.4条,这些等级的典型样板照
片见第5章。 注:①本章各除锈等级定义中,“附着物”这个术语可包括焊渣、焊接飞溅物,可溶性盐类等。 ②本章中,当氧化皮、铁锈或油漆涂层能以金属腻子刮刀从钢材表面剥离时,均应看成附着不牢。 3.2 喷射或抛射除锈 3.2.1喷射或抛射除锈以字母“Sa”表示。 3.2.2喷射或抛射除锈前,厚的锈层应铲除。可见的油脂和污垢也应清除。喷射或抛射除锈后,钢材表面应清除浮灰和碎屑。 3.2.3对于喷射或抛射除锈过的钢材表面,本标准定有四个除锈等级。其文字叙述如下: Sa1 轻度的喷射或抛射除锈 钢材表面应无可见的油脂和污垢,并且没有附着不牢的氧化皮、铁锈和油漆涂层等附着物。参见照片BSa 1、CSa 1和DSa 1。 Sa 2 彻底的喷射或抛射除锈 钢材表面会无可见的油脂和污垢,并且氧化皮、铁锈和油漆涂层等附着物已基本清除,其残留物应是牢固附着的。参见照片BSa 2、CSa 2和DSa 2。 Sa 2 1/2非常彻底的喷射或抛射除锈 钢材表面会无可见的油脂、污垢,氧化皮、铁锈和油漆涂层等附着物,任何残留的痕迹应仅是点状或条纹状的轻微色斑。参见照片ASa 2 ,BSa 2 1/2、CSa 2 1/2和DSa 2 1/2。 Sa 3 使锕材表观洁净的喷射或抛射除锈 钢材表面应无可见的油脂、污垢,氧化皮、铁锈和油漆涂层等附着物,该表面应显示均匀的金属色泽。参见照片ASa 3、BSa 3、CSa3和DSa 3。 3.3手工和动力工具除锈 3.3.1用手工和动力工具,如用铲刀、手工或动力钢丝刷、动力砂纸盘或砂轮等工具除锈,以字母“St”表示。 3.3.2手工和动力工具除锈前,厚的锈层应铲除,可见的油脂和污垢也应清除。手工和
钢洁净度的评定和控制
钢洁净度的评定和控制 1前言 市场对洁净钢的需求逐年增加,除了要求降低钢中非金属氧化物夹杂含量和控制其形态、化学成分及尺寸分布外,还要求降低钢中杂质元素(如:S、P、H、N、甚至C)和痕量元素(如:As、Sn、Sb、Se、Cu、Pb及Bi)含量。表1为普通用钢内杂质元素对其机械性能的影响。 钢材中的夹杂物可引起许多缺陷,例如,美国国家钢公司Midwest厂低碳铝镇静钢发生边部裂纹,经鉴定,该裂纹是由脱氧和二次氧化产物Al2O3夹杂、来自中间包覆盖剂的铝酸钙和夹带的结晶器保护渣而引起。纵向裂纹发生在带钢表面平行于轧制方向,裂纹可导致低碳铝镇静钢汽车板表面缺陷和可成型性问题,正如美国内陆钢公司4号BOF车间和国家钢公司大湖厂多项研究论文所述,钢中的铝酸盐夹杂物来自裹入结晶器的脱氧产物和复合非金属夹杂物。 钢的洁净度取决于钢中非金属夹杂物的数量、形态和尺寸分布,因钢种及其用途不同而定义不同,如表2所示。
由于大型宏观夹杂对钢的机械性能危害最大,其尺寸分布非常重要。据报道,1kg典型的低碳铝镇静钢含107~109个夹杂物(其中,仅含80~130Lm夹杂物400个,130~200Lm夹杂物10个,200~270Lm 夹杂物少于1个)。显然,检测少量大型夹杂物是非常困难的。尽管大型夹杂物在数量上比小型夹杂物少得多,但其总体积分数可能较大,有时一个大型夹杂物能引起整个一炉钢的灾难性缺陷。因此,洁净钢不仅要控制钢中夹杂物平均含量,而且还要避免夹杂物尺寸超过对产品有害的临界尺寸。由此,表2中列出了许多钢材对夹杂物最大尺寸的限定值。夹杂物尺寸分布的重要性在图1中得到了进一步解释。测试结果表明,大于30Lm的夹杂物由钢包内的1.61×10-4%降到中间包的0.58×10-4%。因此,尽管钢包内钢水总氧含量稍高且夹杂物总量较多,中间包内的钢水还是较洁净的。 图1钢包和中间包内Al2O3夹杂物尺寸分布 非金属夹杂物来源很多,包括:
洁净室温湿度如何控制
如何对洁净室温湿度进行控制 的提高,出现了工艺对温湿度的要求也越来越严的趋势。 净化工程具体工艺对温度的要求以后还要列举,但作为总的原则看,由于加工精度越来越精细,所以对温度波动范围的要求越来越小。例如在大规模集成电路生产的光刻曝光工艺中,作为掩膜板材料的玻璃与硅片的热膨胀系数的差要求越来越小。直径100 um的硅片,温度上升1度,就引起了0.24um线性膨胀,所以必须有±0.1度的恒温,同时要求湿度值一般较低,因为人出汗以后,对产品将有污染,特别是怕钠的半导体车间,这种车间不宜超过25度。 湿度过高产生的问题更多。相对湿度超过55%时,冷却水管壁上会结露,如果发生在精密装置或电路中,就会引起各种事故。相对湿度在50%时易生锈。此外,湿度太高时将通过空气中的水分子把硅片表面粘着的灰尘化学吸附在表面耐难以清除。相对湿度越高,粘附的难去掉,但当相对湿度低于30%时,又由于静电力的作用使粒子也容易吸附于表面,同时大量半导体器件容易发生击穿。对于硅片生产最佳温度范围为35—45%。 洁净室中的气压规定 对于大部分洁净空间,为了防止外界污染侵入,需要保持内部的压力(静压)高于外部的压力(静压)。压力差的维持一般应符合以下原则: 1.洁净空间的压力要高于非洁净空间的压力。 2.洁净度级别高的空间的压力要高于相邻的洁净度级别低的空间的压力。 3.相通洁净室之间的门要开向洁净度级别高的房间。 压力差的维持依靠新风量,这个新风量要能补偿在这一压力差下从缝隙漏泄掉的风量。所以压力差的物理意义就是漏泄(或渗透)风量通过洁净室的各种缝隙时的阻力。 洁净室中的气流速度规定 这里要讨论的气流速度是指洁净室内的气流速度,在其他洁净空间中的气流速度在讨论具体设备时再说明。 对于乱流洁净室由于主主要靠空气的稀释作用来减轻室内污染的程度,所以主要用换气次数这一概念,而不直接用速度的概念,不过对室内气流速度也有如下要求; (1)送风口出口气流速度不宜太大,和单纯空调房间相比,要求速度衰减更快,扩散角度更大。 (2)吹过水平面的气流速度(例如侧送时回流速度)不宜太大,以免吹起表面微粒重返气流,而造成再污染,这一速度一般不宜大干0.2m/s。 对于平行流洁净室《习惯上称层流洁净室),由于主要靠气流的“活塞打挤压作用排除行染,所以截面上的速度就是非常重要的指标。过去都参考美国20gB标准,采用0.45m/s.但人们也都了解到这样大速度所需要的通风量是极大的,为了节能,也都在探求降低速一风速的可行性。 在我国,《空气洁净技术措施》和<洁净厂房设计规范))都是这样规定的 垂直平行流(层流)洁净室≥0.25m/s 水平平行流(层流)洁净室≥0.35 m/s 研究表明以上规定基本上满足控制污染的要求,但认为应区别不同情况分出不同的档别,更能体现节能的目的。