天然气催化燃烧催化剂的研究进展
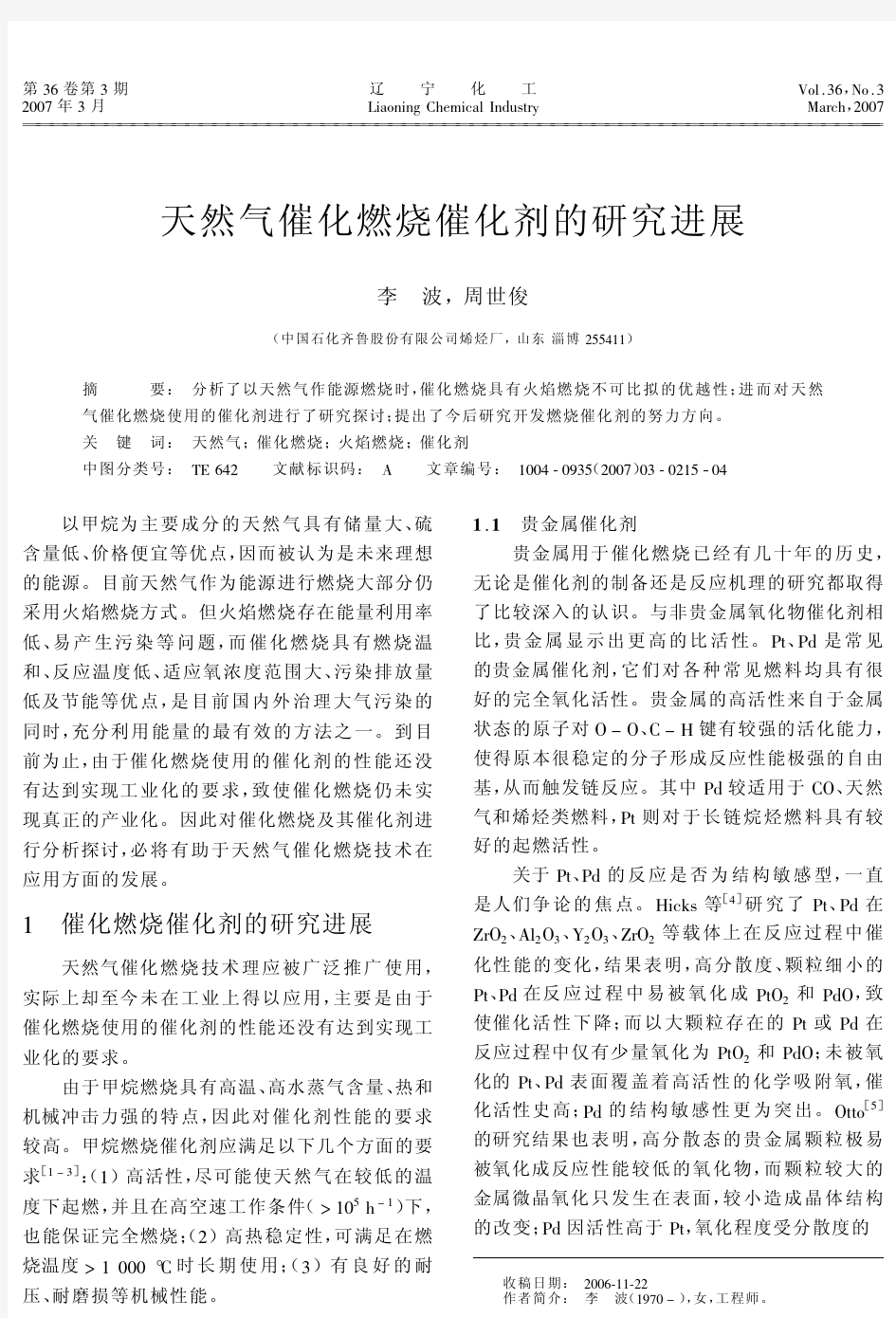

催化燃烧原理
催化燃烧原理 催化燃烧原理?下面就由安徽宝华环保科技有限公司来给大家简单介绍下吧!催化燃烧是用催化剂使废气中可燃物质在较低温度下氧化分解的净化方法。所以,催化燃烧又称为催化化学转化。由于催化剂加速了氧化分解的历程,大多数碳氢化合物在300~450℃的温度时,通过催化剂就可以氧化完全。与热力燃烧法相比,催化燃烧所需的辅助燃料少,能量消耗低,设备设施的体积小。但是,由于使用的催化剂的中毒、催化床层的更换和清洁费用高等问题,影响了这种方法在工业生产过程中的推广和应用。 在化学反应过程中,利用催化剂降低燃烧温度,加速有毒有害气体完全氧化的方法,叫做催化燃烧法。由于催化剂的载体是由多孔材料制作的,具有较大的
比表面积和合适的孔径,当加热到300~450℃的有机气体通过催化层时,氧和有机气体被吸附在多孔材料表层的催化剂上,增加了氧和有机气体接触碰撞的机会,提高了活性,使有机气体与氧产生剧烈的化学反应而生成CO2和H2O,同时产生热量,从而使得有机气体变成无毒无害气体。 催化燃烧装置主要由热交换器、燃烧室、催化反应器、热回收系统和净化烟气的排放烟囱等部分组成,如右图所示。其净化原理是:未净化气体在进入燃烧室以前,先经过热交换器被预热后送至燃烧室,在燃烧室内达到所要求的反应温度,氧化反应在催化反应器中进行,净化后烟气经热交换器释放出部分热量,再由烟囱排入大气。 安徽宝华环保科技有限公司拥有环保专业承包叁级资质和国家清洁生产咨询审核资质,根据市场需求,不断推陈出新,积极与国内科研院校建立战略合作关系,不断引进新技术与新人才,进一步提升业务能力与水平。公司在全体宝华人的努力下,逐渐发展成为具有影响力的环保综合服务商。公司秉承“客户至上、服务第一”的理念,依托强大的技术支持和完备的售后服务,为您解决身边的环境问题。全体宝华人愿与您携手并进,共建美丽中国,同创绿色地球。
吸附催化燃烧工艺简介
1、吸附-催化燃烧法原理 吸附浓缩-催化燃烧法,该设备采用多气路连续工作,设备多个吸附床可交替使用。含有机物的废气经风机的作用,经过活性炭吸附层,有机物质被活性炭特有的作用力截留在其内部,吸附去处效率达80%,吸附后的洁净气体排出;经过一段时间后,活性炭达到饱和状态时,停止吸附,此时有机物已被浓缩在活性炭内,之后按照PLC自动控制程序将饱和的活性炭床与脱附后待用的活性炭床进行交替切换。CO(催化氧化设备)自动升温将热空气通过风机送入活性炭床使碳层升温将有机物从活性炭中“蒸”出,脱附出来的废气属于高浓度、小风量、高温度的有机废气。 催化燃烧法:VOC-CH 型有机气体催化净化装置,是利用催化剂使有害气体中的可燃组 和分在较低的温度下氧化分解的净化方法。对于 CnHm 和有机溶剂蒸汽氧化分解生成CO 2 O并释放出大量热量。其反应方程式为: H 2 图3-1 VOC-CO原理图 活性炭脱附出来的高浓度、小风量、高温度的有机废气经阻火除尘器过滤后,进入特制的板式热交换器,和催化反应后的高温气体进行能量间接交换,此时废气源的温度得到第一次提升;具有一定温度的气体进入预热器,进行第二次的温度提升;之后进入第一级催化反应,此时有机废气在低温下部份分解,并释放出能量,对废气源进行直接加热,将气体温度提高到催化反应的最佳温度;经温度检测系统检测,温度符合催化反应的温度要求,进入催化燃烧室,有机气体得到彻底分解,同时释放出大量的热量;净化后的气体通过热交换器将热能转换给出冷气流,降温后气体由引风机排空。 有机物利用自身氧化燃烧释放出的热量维持自燃,如果脱附废气浓度足够高,CO 正常
使用需要很少的电功率甚至不需要电功率加热,做到真正的节能、环保,同时,整套装置安全、可靠、无任何二次污染。 2、处理工艺流程 根据行业要求及减少用户投资成本、运行维护费用,拟采用湿法除尘、干式过滤、活性炭吸附、催化燃烧脱附的方式对喷漆房污染综合治理,其中吸附浓缩-催化燃烧法工艺流程图如下: 图3-2 喷漆废气处理工艺流程图 本处理装置工艺采用湿法除尘+干式过滤+吸附+催化净化装置,工作方式为:一个湿式除尘塔+干式过滤器+若干个吸附床,经过除尘过滤去除漆雾后,有机废气进入吸附床中进行吸附工作,净化后的气体由风机排入排气筒达标排放。日常工作时吸附床中一个进行脱附再生工作,其余进行吸附工作。脱附时启动催化燃烧器中的电预热器,待温度达到起燃温度时,由脱附风机和补冷风机补入系统中的冷风,经混合后调到适当温度(140℃,其中废气中有机成分沸点:甲苯110.6℃,二甲苯138-144℃)后送入吸附床进行脱附操作,吹脱出的高浓度有机废气(可浓缩10-20倍)与燃烧后的热废气在热交换器中进行热交换得到预热后送入燃烧室,在燃烧室中升到起燃温度后由催化剂将有机物氧化分解为无害的 CO 2和H 2 O。燃烧后的废气经脱附出的气体热交换温度降低至180-200℃后用于脱附,多余废 气排入排气筒。 由多个吸附床轮流进行吸附和脱附再生,吸附与脱附之间切换,连续运行(工作时间可根据企业生产情况调节)。本工程设计废气浓度100ppm,浓缩后有机废气浓度可达到5000mg/m3以上,在燃烧器启动通过电加热升温至起燃温度后,可维持自燃。
Co基催化剂上甲苯催化燃烧的研究
Hans Journal of Chemical Engineering and Technology 化学工程与技术, 2019, 9(4), 299-304 Published Online July 2019 in Hans. https://www.360docs.net/doc/1610898516.html,/journal/hjcet https://https://www.360docs.net/doc/1610898516.html,/10.12677/hjcet.2019.94042 Study on Catalytic Combustion of Toluene on Co-Based Catalysts Shengkang Wang, Hua Pan*, Yiping Mao, Zhongyu Yang, Dingsheng Zhang, Yu Mei College of Biology and Environmental Engineering, Zhejiang Shuren University, Hangzhou Zhejiang Received: Jun. 14th, 2019; accepted: Jun. 28th, 2019; published: Jul. 4th, 2019 Abstract Co/CeO2 and Co/TiO2 catalysts were prepared by impregnation method. The catalytic behavior of Co/CeO2 and Co/TiO2 catalysts for catalytic combustion of toluene was investigated. It shows that the activity of Co/CeO2 catalyst is higher than that of Co/TiO2 catalyst. Co/CeO2 catalyst has a lower light-off temperature (T50= 210?C), while the conversion of toluene can be stabilized at 80% at 225?C on Co/CeO2. Co/CeO2 has a larger specific surface area, which increases the contact area of the reactants with the catalyst, resulting in the higher activity of the catalyst. The active compo-nent in the Co/CeO2and Co/TiO2catalysts is Co3O4. The higher content of O surf and Co3O4on the surface of Co/CeO2 catalyst may be the main reason for the higher activity of Co/CeO2 catalyst. Keywords Cobalt, Catalytic Combustion, Toluene Co基催化剂上甲苯催化燃烧的研究 王晟康,潘华*,毛益萍,杨仲余,张鼎盛,梅瑜 浙江树人大学生物与环境工程学院,浙江杭州 收稿日期:2019年6月14日;录用日期:2019年6月28日;发布日期:2019年7月4日 摘要 采用浸渍法制备了Co/CeO2和Co/TiO2催化剂,考察了Co/CeO2和Co/TiO2催化剂催化燃烧甲苯的催化行为。研究表明:Co/CeO2催化剂活性高于Co/TiO2催化剂活性。Co/CeO2催化剂具有较低的起燃温度(T50 *通讯作者。
催化燃烧原理及催化剂
催化燃烧的基本原理 催化燃烧是典型的气-固相催化反应,其实质是活性氧参与的深度氧化作用。在催化燃烧过程中,催化剂的作用是降低活化能,同时催化剂表面具有吸附作用,使反应物分子富集于表面提高了反应速率,加快了反应的进行。借助催化剂可使有机废气在较低的起燃温度条件下,发生无焰燃烧,并氧化分解为CO2和H20, 同时放出大量热能,其反应过程为: 2 催化燃烧的特点及经济性 2.1催化燃烧的特点 2.1.1起燃温度低,节省能源 有机废气催化燃烧与直接燃烧相比,具有起燃温度低,能耗也小的显著特点。在某些情况下,达到起燃温度后便无需外界供热。 二、催化剂及燃烧动力学 2.1催化剂的主要性能指标 在空速较高,温度较低的条件下,有机废气的燃烧反应转化率接近100%,表明该催化剂的活性较高[9]。催化剂的活性分诱导活化、稳定、衰老失活3 个阶段,有一定的使用限期,工业上实用催化剂的寿命一般在2年以上。使用期的长短与最佳活性结构的稳定性有关,而稳定性取决于耐热、抗毒的能力。对催化燃烧所用催化剂则要求具有较高的耐热和抗毒的性能。有机废气的催化燃烧一般不会在很严格的操作条件下进行,这是由于废气的浓度、流量、成分等往往不稳定,因此要求催化剂具有较宽的操作条件适应性。催化燃烧工艺的操作空速较大,气流对催化剂的冲击力较强,同时由于床层温度会升降,造成热胀冷缩,易使催化剂载体破裂,因而催化剂要具有较大的机械强度和良好的抗热胀冷缩性能。 2.2催化剂种类 目前催化剂的种类已相当多,按活性成分大体可分3 类。2.2.1贵金属催化剂 铂、钯、钌等贵金属对烃类及其衍生物的氧化都具有很高的催化活性,且使用寿命长,适用范围广,易于回收,因而是最常用的废气燃烧催化剂。如我国最早采用的Pt-Al203 催化剂就属于此类催化剂。但由于其资源稀少,价格昂贵,耐中毒性差,人们一直努力寻找替代品或尽量减少其用量。2.2.2过渡金属氢化物催化剂 作为取代贵金属催化剂,采用氧化性较强的过渡金属氧化物,对甲烷等烃类和一氧化碳亦具有较高的活性,同时降低了催化剂的成本,常见的有Mn0x、CoOx和CuOx等催化剂。大连理工大学研制的含Mn02催化剂,在130C及空速13000h-1 的条件下能消除甲醇蒸气,对乙醛、丙酮、苯蒸气的清除也很有效果。
催化剂及催化燃烧技术
催化燃烧是借助催化剂在低温下(200~400℃)下,实现对有机物的完全氧化,因此,能耗少,操作简便,安全,净化效率高,在有机废气特别是回收价值不大的有机废气净化方面,比如化工,喷漆、绝缘材料、漆包线、涂料生产等行业应用较广,已有不少定型设备可供选用。 一、催化原理及装置组成 (1)催化剂定义催化剂是一种能提高化学反应速率,控制反应方向,在反应前后本身的化学性质不发生改变的物质。 (2)催化作用机理催化作用的机理是一个很复杂的问题,这里仅做简介。在一个化学反应过程中,催化剂的加入并不能改变原有的化学平衡,所改变的仅是化学反应的速度,而在反应前后,催化剂本身的性质并不发生变化。那么,催化剂是怎样加速了反应速度呢了既然反应前后催化剂不发生变化,那么催化剂到底参加了反应没有?实际上,催化剂本身参加了反应,正是由于它的参加,使反应改变了原有的途径,使反应的活化能降低,从而加速了反应速度。例如反应A+B→C是通过中间活性结合物(AB)过渡而成的,即: A+B→[AB]→C 其反应速度较慢。当加入催化剂K后,反应从一条很容易进行的途径实现: A+B+2K→[AK]+[BK]→[CK]+K→C+2K 中间不再需要[AB]向C的过渡,从而加快了反应速度,而催化剂并未改变性质。 (3)催化燃烧的工艺组成不同的排放场合和不同的废气,有不同的工艺流程。但不论采取哪种工艺流程,都由如下工艺单元组成。 ①废气预处理为了避免催化剂床层的堵塞和催化剂中毒,废气在进入床层之前必须进行预处理,以除去废气中的粉尘、液滴及催化剂的毒物。 ②预热装置预热装置包括废气预热装置和催化剂燃烧器预热装置。因为催化剂都有一个催化活性温度,对催化燃烧来说称催化剂起燃温度,必须使废气和床层的温度达到起燃温度才能进行催化燃烧,因此,必须设置预热装置。但对于排出的废气本身温度就较高的场合,如漆包线、绝缘材料、烤漆等烘干排气,温度可达300℃以上,则不必设置预热装置。 预热装置加热后的热气可采用换热器和床层内布管的方式。预热器的热源可采用烟道气或电加热,目前采用电加热较多。当催化反应开始后,可尽量以回收的反应热来预热废气。在反应热较大的场合,还应设置废热回收装置,以节约能源。 预热废气的热源温度一般都超过催化剂的活性温度。为保护催化剂,加热装置应与催化燃烧装置保持一定距离,这样还能使废气温度分布均匀。 从需要预热这一点出发,催化燃烧法最适用于连续排气的净化,若间歇排气,不仅每次预热需要耗能,反应热也无法回收利用,会造成很大的能源浪费,在设计和选择时应注意这一点。 ③催化燃烧装置一般采用固定床催化反应器。反应器的设计按规范进行,应便于操作,维修方便,便于装卸催化剂。 在进行催化燃烧的工艺设计时,应根据具体情况,对于处理气量较大的场合,设计成分建式流程,即预热器、反应器独立装设,其间用管道连接。对于处理气量小的场合,可采用催化焚烧炉,把预热与反应组合在一起,但要注意预热段与反应段间的距离。 在有机物废气的催化燃烧中,所要处理的有机物废气在高温下与空气混合易引起爆炸,安全问题十分重要。因而,一方面必须控制有机物与空气的混合比,使之在爆炸下限;另一方面,催化燃烧系统应设监测报警装置和有防爆措施。 二、催化燃烧用催化剂 由于有机物催化燃烧的催化剂分为贵金属(以铂、钯为主)和贱金属催化剂。贵金属为活性组分的催化剂分为全金属催化剂和以氧化铝为载体的催化剂。全金属催化剂是以镍或镍铬合金为载体,将载体做成带、片、丸、丝等形状,采用化学镀或电镀的方法,将铂、钯等贵金属沉积其上,然后做成便于装卸的催化剂构件。由氧化铝作载体的贵金属催化剂,一般是以陶
燃气锅炉燃烧控制系统.docx.
燃气锅炉燃烧控制系统 摘要: 本文主要介绍了锅炉燃烧控制系统的设计过程。在设计过程中介绍了锅炉燃烧控制系统的控制任务和控制特点,对于燃烧控制系统的设计方案,根据不同的控制任务分别设计了蒸汽压力控制和燃料空气比值控制以及防脱火回火选择性控制系统,并在设计中给出了不同的设计方案,以对比各自的优缺点,选择最优的控制。然后,把分别设计的控制系统组合起来,构成完整的锅炉燃烧过程控制系统。最后,对设计好的控制系统进行仪表选型。 关键词:燃气锅炉,燃烧系统,比值控制,脱火回火
目录 1.引言 (3) 2.锅炉燃烧控制系统概述 (4) 2.1 燃烧控制的任务 (5) 2.1.1 维持蒸汽出口压力稳定 (5) 2.1.2 保证燃烧过程的经济性 (5) 2.1.3 保证锅炉安全运行 (6) 2.2 燃烧控制的特点 (6) 3.燃烧控制系统设计方案 (6) 3.1 蒸汽压力控制和燃料空气比值控制 (6) 3.1.1 基本控制方案 (7) 3.1.2 改进控制方案 (8) 3.2 防脱火回火选择性控制系统 (9) 3.2.1 防脱火选择性控制系统 (9) 3.2.2防脱火回火混合型选择性控制系统 (11) 3.3 燃烧控制总体方案 (12) 4. 燃烧控制系统的仪表选型 (13) 5. 总结 (14) 参考文献 (15)
1.引言 大型火力发电机组是典型的过程控制对象,它是由锅炉、汽轮发电机组和辅助设备组成的庞大的设备群。锅炉的燃烧控制过程是一个复杂的物理,化学过程,影响因素众多,并且具有强耦合,非线性等特性。 锅炉的自动化控制经历了三、四十年代的单参数仪表控制,四、五十年代的单元组合仪表,综合参数仪表控制,直到六十年代兴起的计算机过程控制几个阶段。尤其是近一、二十年来,随着先进控制理论和计算机技术的发展,加之计算机各项性能的不断增强及价格的不断下降使锅炉应用计算机控制很快得到了普及和应用。 电厂锅炉利用煤或煤气的燃烧发热,通过传热对水进行加热,产生高压蒸汽,推动汽轮机发电机旋转,从而产生强大的电能。在锅炉燃烧系统中,燃料供给系统,送风系统以及引风系统是燃烧控制系统的重要环节。锅炉生产燃烧系统自动控制的基本任务是使燃料所产生的热量适应蒸汽负荷的需要,同时还要保证经济燃烧和锅炉的安全运行。具体控制任务可分为三个方面:一,稳定蒸汽母管压力。二,维持锅炉燃烧的最佳状态和经济性。三,维持炉膛负压在一定范围(-20~-80Pa)。这三者是相互关联的。另外,在安全保护系统上应该考虑燃烧嘴背压过高时,可能使燃料流速过高而脱火;燃烧嘴背压太低又可能回火。 本次课程设计的题目为燃气锅炉燃烧控制系统的设计。主要内容包括燃烧控制系统的概述;燃烧控制系统的基本方案;以及燃烧控制系统的仪表选型。设计方案为以主蒸汽压力控制系统为主回路,燃料量与空气量比值控制系统为内回路,燃烧嘴防脱火回火选择控制系统为辅助安全保护系统。为节省篇幅,炉膛压力控制系统在这里暂不涉及,但在实际控制系统中炉膛压力控制系统是锅炉燃烧控制系统中必不可少的组成部分之一。
废气催化燃烧的原理及其工艺
往往业主在采购废气处理设备的时候会问一些技术性的问题以决定采用哪种技术,哪种技术最为适合该工艺,下面专门介绍本公司生产的,吸附+脱附+催化燃烧有机废气处理设备的技术原理及工艺流程。以供广大业主参考。 一、催化燃烧的基本原理 催化燃烧是典型的气-固相催化反应,其实质是活性氧参与的深度氧化作用。在催化燃烧过程中,催化剂的作用是降低活化能,同时催化剂表面具有吸附作用,使反应物分子富集于表面提高了反应速率,加快了反应的进行。借助催化剂可使有机废气在较低的起燃温度条件下,发生无焰燃烧,并氧化分解为CO2和H2O,同时放出大量热能,其反应过程为: 2 催化燃烧的特点及经济性 2.1 催化燃烧的特点 2.1.1起燃温度低,节省能源 有机废气催化燃烧与直接燃烧相比,具有起燃温度低,能耗也小的显著特点。在某些情况下,达到起燃温度后便无需外界供热。 二、催化剂及燃烧动力学 2.1 催化剂的主要性能指标 在空速较高,温度较低的条件下,有机废气的燃烧反应转化率接近100%,表明该催化剂的活性较高[9]。催化剂的活性分诱导活化、稳定、衰老失活3个阶段,有一定的使用限期,工业上实用催化剂的寿命一般在2年以上。使用期的长短与最佳活性结构的稳定性有关,而稳定性取决于耐热、抗毒的能力。对催化燃烧所用催化剂则要求具有较高的耐热和抗毒的性能。有机废气的催化燃烧一般不会在很严格的操作条件下进行,这是由于废气的浓度、流量、成分等往往不稳定,因此要求催化剂具有较宽的操作条件适应性。催化燃烧工艺的操作空速较大,气流对催化剂的冲击力较强,同时由于床层温度会升降,造成热胀冷缩,易使催化剂载体破裂,因而催化剂要具有较大的机械强度和良好的抗热胀冷缩性能。 2.2 催化剂种类 目前催化剂的种类已相当多,按活性成分大体可分3类。 2.2.1贵金属催化剂 铂、钯、钌等贵金属对烃类及其衍生物的氧化都具有很高的催化活性,且使用寿命长,适用范围广,易于回收,因而是最常用的废气燃烧催化剂。如我国最早采用的Pt-Al2O3催化剂就属于此类催化剂。但由于其资源稀少,价格昂贵,耐中毒性差,人们一直努力寻找替代品或尽量减少其用量。 2.2.2过渡金属氢化物催化剂 作为取代贵金属催化剂,采用氧化性较强的过渡金属氧化物,对甲烷等烃类和一氧化碳亦具有较高的活性,同时降低了催化剂的成本,常见的有MnOx、CoOx和CuOx等催化剂。大连理工大学研制的含MnO2催化剂,在130℃及空速13000h-1的条件下能消除甲醇蒸气,对乙醛、丙酮、苯蒸气的清除也很有效果。 2.2.3复氧化物催化剂 一般认为,复氧化物之间由于存在结构或电子调变等相互作用,活性比相应的单一氧化物要高。主要有以下两大类: (1)钙钛矿型复氧化物 稀土与过渡金属氧化物在一定条件下可以形成具有天然钙钛矿型的复合氧化物,通式为ABO3,其活性明显优于相应的单一氧化物。结构中一般A为四面体型结构,B为八面体形结构,这样A和B形成交替立体结构,易于取代而产生品格缺陷,即催化活性中心位,表面晶格氧提供高活性的氧化中心,从而实现深度氧化反应。常见的有几类如:BaCuO2、LaMnO3等。
催化燃烧的性质
广州和风环境技术有限公司 https://www.360docs.net/doc/1610898516.html,/ 催化燃烧的性质是什么 催化燃烧是借助催化剂在低温下(200~400℃)下,实现对有机物的完全氧化,因此,能耗少,操作简便,安全,净化效率高,在有机废气特别是回收价值不大的有机废气净化方面,比如化工,喷漆、绝缘材料、漆包线、涂料生产等行业应用较广,已有不少定型设备可供选用。 一、催化原理及装置组成 (1)催化剂定义催化剂是一种能提高化学反应速率,控制反应方向,在反应前后本身的化学性质不发生改变的物质。 (2)催化作用机理催化作用的机理是一个很复杂的问题,这里仅做简介。在一个化学反应过程中,催化剂的加入并不能改变原有的化学平衡,所改变的仅是化学反应的速度,而在反应前后,催化剂本身的性质并不发生变化。那么,催化剂是怎样加速了反应速度呢了既然反应前后催化剂不发生变化,那么催化剂到底参加了反应没有?实际上,催化剂本身参加了反应,正是由于它的参加,使反应改变了原有的途径,使反应的活化能降低,从而加速了反应速度。例如反应A+B →C是通过中间活性结合物(AB)过渡而成的,即:A+B→[AB]→C 其反应速度较慢。当加入催化剂K后,反应从一条很容易进行的途径实现:A+B+2K →[AK]+[BK]→[CK]+K→C+2K 中间不再需要[AB]向C的过渡,从而加快了反应速度,而催化剂并未改变性质。 (3)催化燃烧的工艺组成不同的排放场合和不同的废气,有不同的工艺流程。但不论采取哪种工艺流程,都由如下工艺单元组成。 ①废气预处理为了避免催化剂床层的堵塞和催化剂中毒,废气在进入床层之前必须进行预处理,以除去废气中的粉尘、液滴及催化剂的毒物。 ②预热装置预热装置包括废气预热装置和催化剂燃烧器预热装置。因为催化剂都有一个催化活性温度,对催化燃烧来说称催化剂起燃温度,必须使废气和床层的温度达到起燃温度才能进行催化燃烧,因此,必须设置预热装置。但对于排出的废气本身温度就较高的场合,如漆包线、绝缘材料、烤漆等烘干排气,温度
催化燃烧废气处理设备的工艺以及维护
催化燃烧废气处理设备的工艺以及维护 近年来,催化燃烧废气处理设备的市场占有率越来越高,那么,催化燃烧废气处理设备的工艺是什么呢?以及平常应该怎么维护呢? 催化燃烧废气处理设备由预处理装置、预热装置、催化燃烧装置、防爆装置组成。 废气预处理:顾名思义,就是将废气的灰尘提前处理,防止催化剂床层堵塞。 预热装置:预热装置包括废气预热装置和催化剂燃烧器预热装置,因为催化剂都有一个催化活性温度,对催化燃烧来说称催化剂起燃温度,必须使废气和床层的温度达到起燃温度才能进行催化燃烧,因此,必须设置预热装置。但对于排出的废气本身温度就较高的场合,如漆包线、绝缘材料、烤漆等烘干排气,温度可达300℃以上,则不必设置预热装置。 催化燃烧装置:一般采用固定床催化反应器,反应器的设计按规范进行,应便于操作,维修就方便,便于装卸催化剂。 防爆装置:为膜片泄压防爆,安装在主机的顶部,当设备运行发生意外事故时,可及时裂开泄压,防止意外发生。 催化燃烧废气处理设备原理 催化燃烧是用催化剂使废气中可燃物质在较低温度下氧化分解的净化方法。所以,催化燃烧又称为催化化学转化。由于催化剂加速了氧化分解的历程,大多数碳氢化合物在300-500℃的温度时,通过催化剂就可以氧化完全。 催化剂首先对VOC分子的吸附,提高了反应物的浓度其次催化氧化阶段降低反应的活化能,提高了反应速率,借助催化剂可使有机废气在较低的起燃温度下,发生无氧燃烧,分解成CO2和H20,释放出大量热量,能耗较小,某些情况下达到起燃温度后无需外界供热,反应温度在250-400℃。 在化学反应过程中,利用催化剂降低燃烧温度,加速有毒有害气体完全氧化的方法,叫做催化燃烧法。 由于催化剂的载体是由多孔材料制作的,具有较大的比表面积和合适的孔径,当加热到300-450℃的有机气体通过催化层时,氧和有机气体被吸附在多孔材料表层的催化剂上,增加了氧和有机气体接触碰撞的机会,提高了活性,使有机气体与氧产生剧烈的化学反应而生
燃气燃烧机的安全控制要求
行业资料:________ 燃气燃烧机的安全控制要求 单位:______________________ 部门:______________________ 日期:______年_____月_____日 第1 页共10 页
燃气燃烧机的安全控制要求 我国天然气和煤制气(原料为煤)资源丰富,且属于洁净能源,顾有着良好的社会经济效益。燃气燃烧机符合我国产业政策,市场前景很好,大有发展前途。然而在燃气燃烧机研制设计中,燃气特性-易燃、易爆及毒性,安全控制的首要问题。下面介绍一下燃气燃烧机的安全控制要求: 根据燃气在炉膛内的燃烧特性,对其安全控制要求内容主要有预吹风、自动点火、燃烧状态监控、点不着火的保护、熄火的保护、燃气压力高低限保护、空气压力不足保护、断电保护、预防燃气泄漏事故的措施等。 1.预吹风 燃烧机在点火前,必须有一段时间的预吹风,把炉膛与烟道中余气吹除或稀释。因为燃烧机工作炉膛内不可避免地有余留的燃气,若未进行预吹风而点火,有发生爆炸的危险.必须把余气吹除干净或稀释,保证燃气浓度不在爆炸极限内。 预吹风时间与炉膛结构及吹风量有关一般设置为15-60秒 2.自动点火 燃气燃烧机宜采用电火花点火,便于实现自动控制。可用高压点火变压器产生电弧点火,要求其输出能量为:电压3.5KV、电流15mA,点火时间一般为:2~5秒。 3.燃烧状态监控 燃烧状态必须予以动态监控,一旦火焰探测器感测到熄火信号,必须在极短时间内反馈到燃烧机,燃烧机随即进人保护状态,同时切断燃 第 2 页共 10 页
气供给。 火焰探测器要能正常感测火焰信号,既不要敏感,也不要迟钝。因为敏感,燃烧状态如有波动易产生误动作而迟钝,反馈火焰信号滞后,不利于安全运行。 一般要求从熄火到火焰探测器发出熄火信号的响应时间不超过0.2秒。 4.点不着火的保护 燃烧机点火时,通入燃气,燃气着火燃烧。点火动作要求发生在燃气通入前,先形成点火温度场,便于着火燃烧。如果点不着火,火焰探测器感测不到火焰信号,燃烧机进入保护状态。 从点火到进入保护状态的时间要适当,既不能过短也不能过长。若过短,来不及形成稳定火焰;过长,点不着火时造成大量燃气时入炉膛。一般要求在通入燃气2-3秒,燃烧机对火焰探测器感测的火焰信号进行判断,未着火则进入保护状态,着火则维持燃烧。 5.熄火保护 燃烧机在燃烧过程中,若意外熄火,燃烧机进入保护状态。由于炉膛是炽热的.燃气进入易发生爆燃,故须在极短时间内进入保护状态,切断燃气供给。 从发生熄火到燃烧机进人保护状态,该过程的响应时间要求不超过1秒。 6.燃气压力高低限保护 燃气燃烧机稳定燃烧有一定范围,只允许燃气压力在一定范围内波动。限定燃气高低压的目的是确保火焰稳定性:不脱火、不熄火也不回火,同时限定燃烧机的输出热功率,保证设备安全经济运行。当燃气压 第 3 页共 10 页
RCO催化燃烧设备说明书简介
RCO催化燃烧设备净化原理 在工业生产过程中,排放的有机尾气通过引风机进入设备的旋转阀,通过旋转阀将进口气体和出口气体分开。气体先通过陶瓷材料填充层(底层)预热后发生热量的储备和热交换,其温度几乎达到催化层(中层)进行催化氧化所设定的温度,这时其中部分污染物氧化分解;废气继续通过加热区(上层,可采用电加热方式或气加热方式)升温,并维持在设定温度;其再进入催化层完成催化氧化反应,即反应生成CO2和H2O,并释放大量的热量,以达到预期的处理效果。经催化氧化后的气体进入其它的陶瓷填充层,回收热能后通过旋转阀排放到大气中,净化后排气温度仅略高于废气处理前的温度。系统连续运转、自动切换。通过旋转阀工作,所有的陶瓷填充层均完成加热、冷却、净化的循环步骤,热量得以回收。 RCO催化燃烧设备主要由阻火器,热交换器,催化反应床,风机这几个主要部件 组成。与直接燃烧相比,催化燃烧温度较低,燃烧比较好。催化燃烧用的是表面具有贵金属和金属氧化物的催化剂,将有机污染物的废气在催化剂铂、钯的作用下,可以在较低的温度下将废气中的有机污染物氧化成二氧化碳和水。催化剂的加入并不能改变原有的化学平衡,所改变的仅是化学反应的速度,而在反应前后,催化剂本身的性质并不发生变化。 RCO催化燃烧设备产品性能特点: 1.操作方便,设备工作时,实现自动控制,可靠。 2.设备启动,仅需15~30分钟升温至起燃温度,耗能仅为风机功率,浓度较低时 自动补偿。 3.采用当今先进的贵金属钯、铂浸渍的蜂窝状陶瓷载体催化剂,比表面积大,阻力小,净化率高。 4.余热可返回烘道,降低原烘道中消耗功率;也可作其它方面的热源。 5.使用寿命长,催化剂一般两年换,并且载体可循环使用。 6.不产生氮氧化物(NOX)等二次污染物; 7.可靠性高、净化效率高达99%以上; 8.热量回收率,热回收效率≥95%。 RCO催化燃烧设备能对苯、醇、酮、酯、汽油类等有机溶剂的废气进行吸附净化,适用于低浓度大风量或高浓度间歇排放废气的作业环境,它能有效地净化环境、消除污染、改善工作环境,确保工人身体健康,治理达标排放。因此,化工、轻工、涂装、电子、机电、印刷、家电、制鞋、电池(电瓶)、塑料、薄膜、橡胶、涂料、制药、家具、船舶、汽车、石油等行业产生的有害有机废气的净化及臭味的消除均可选用。 RCO催化燃烧设备使用旋转阀替代了传统设备中众多的阀门以及复杂的液压设备。有机物去除率可以达到98%以上,热回收率达到95-97%。 RCO催化燃烧设备选型及注意事项 (1)废气成分中,不能含有下列物质:有高粘性的油脂类。如磷、铋、砷、锑、汞、铅、锡;高浓度的粉尘。 (2)设备选0型时,注明废气的成份、浓度及出口温度。 (3)设备安装场所无腐蚀性气体,并有良好的防雨措施。 (4)设备所需电源为:三相交流380V,频率50Hz。 (5)注明是否有特殊要求
燃气锅炉燃烧控制系统
燃气锅炉燃烧控制系统 李凯凯 (山东建筑大学热能工程学院山东省济南市 250101) 摘要:此次论文主要目的是以标准燃烧器为基本设备,结合汽包压力控制、炉膛压力控制的特点和需要,设计燃气锅炉燃烧控制系统。主要方法是通过锅炉情况介绍、燃烧器类型选择、燃烧与汽压控制设计、节炉膛压力控制设计、仪表装置选型等步骤,逐一计算所需数据并选择设备类型,然后根据所得参数查阅有关资料按标准设计符合设备的控制系统。由最终设计结果可知此方法可行。 关键词:燃气锅炉、燃气控制、汽包压力、炉膛压力 0 引言 近几年来,我国城市燃气结构有了很大变化,尤其是西气东输工程的加速实施,以及不断签署的燃气协议,为长期受限制的燃气锅炉的应用推广创造了条件。一方面,燃气锅炉的燃料价格相对较高,因此应尽量提高燃料的利用效率;另一方面,气体燃料易燃易爆,燃气锅炉的危险性大,控制系统的生产保证和安全保障要求严格。国外燃气锅炉的研究历史较长,燃气燃烧控制技术比较成熟,但是燃气锅炉的燃烧控制,多为单回路常规控制,远不能适应我国各地区及各部门条件多变的需要。为了提高燃气锅炉的热效率和安全生产水平,有必要对燃所锅炉的燃烧控制技术进行研究。 1 锅炉情况 本次论文采用一台卧式三回程火管式燃气蒸汽锅炉,使用天然气为燃料,额定蒸发量2T/h,额定汽压1.25MPa,额定蒸汽温度194℃;额定耗气量160Nm3/h,排烟温度230℃,热效率90%。 1.1 燃气蒸汽锅炉的组成 结构组成:具体结构由主要部件和辅助设备组成。主要部件有炉膛、省煤器、锅筒、水冷壁、燃烧设备、空气预热器、炉墙构架组成;辅助设备主要有引风设备、除尘设备、燃料供应设备、除尘除渣设备、送风设备、自动控制设备组成。 系统组成:燃气锅炉主要是由燃烧器和控制器两个大的部分组成,其中燃烧器又能分为五个小的系统,分别为送风系统,点火系统,监测系统,燃料系统和电控系统。 1.2 燃气蒸汽锅炉的工作原理 燃气蒸汽锅炉是用天然气、液化气、城市煤气等气体燃料在炉内燃烧放出来的热量加热锅内的水,并使其汽化成蒸汽的热能转换设备。水在锅筒中不断被炉里气体燃料燃烧释放出来的能量加热,温度升高并产生带压蒸汽,由于水的沸点随压力的升高而升高,锅是密封的,水蒸气在里面的膨胀受到限制而产生压力形成热动力作为一种能源广泛使用。 燃气蒸汽锅炉的工作原理见下图。
天然气低碳催化燃烧法
天然气低碳催化燃烧法 在未来的某一天,也许路边的烧烤摊上不会再见到烟熏火燎的状况,烤串用的烧烤炉被一种封闭式的烤箱代替。锅炉也不会再因为废气排放对大气造成污染,危害人类的生命健康。而这一切,得益于一项新型的燃烧方式——催化燃烧的应用。它的神奇之处就在于使超低浓度的燃料得到完全的燃烧氧化,转化效率接近100%。2013年第2期《前沿科学》发表了张世红、Valerie Dupont 和Alan Williams的《天然气低碳催化燃烧特性与应用》一文,向我们介绍了天然气催化燃烧的特性、理论和应用。 天然气催化燃烧的理论研究 催化燃烧的研究最早可以追溯到19世纪初。然而直到进入20世纪70年代,人们意识到催化燃烧能够带来巨大的经济效益和环境效益,才开始进行广泛的研究和应用开发。对催化剂的进一步开发和研究为催化燃烧的研究开辟了新的途径。直到今天,催化燃烧的主要研究集中在催化剂及制备工艺和催化装置及控制技术两方面。 在对贫甲烷/氧气/氮气混合气体燃烧进行的理论研究中,使用的是滞止点流动反应器实验装置。内部铝支架的中间是固定在陶瓷框架里面的催化剂铂金属薄箔。在燃烧时,铂元素与反应物一起参与到反应中去,形成热循环,在反应过后试验气体成为尾气排放,铂恢复原状并继续参与下一个这样的循环。通过反复的试验和数值模拟发现,因为有催化剂因素的存在,可燃气体能在低浓度的情况下发生催化燃烧并完全氧化,不形成CO、氮氧化物和未完全燃烧的碳氢化合物,燃烧发生在常规气相易燃极限之外,因此燃烧更加稳定。催化剂表面的异相反应抑制了气相氧化反应的程度,提高了单相点燃的表面温度。 天然气催化燃烧的开发应用研究 张世红研究团队以催化燃烧机理和应用研究为课题,对近零污染物排放,催化剂中毒特性和贫天然气/空气混合比如何调节等问题进行了深入的工业产品和产业化研究。开发研制了天然气催化燃烧V型冷凝锅炉、天然气催化燃烧烤箱、天然气催化燃烧炉窑。 在对天然气催化燃烧V型冷凝锅炉的研究中,燃烧炉采用催化燃烧的方式以后,可以避免火焰燃烧方式的诸多缺点。张世红研究团队通过对普通快速型燃气热水器和家用燃气灶的烟气进行了测量,发现燃气热水器及燃气灶排放的烟气虽然都被空气明显稀释过,但污染物排放浓度仍然比催化燃烧高很多,因此证明催化燃烧贫CH4的异相燃烧方式能够产生节约燃料和减少环境污染的效果是十分明显的。试验数据表明,催化燃烧V型冷凝锅炉的热效率明显比普通燃气锅炉要高。利用分析仪测量催化燃烧和气相燃烧两种情况下的烟气成分及含量发现目前的催化燃烧几乎已经达到了燃烧完全的程度和近零污染物排放。
催化燃烧机理
催化燃烧的原理 催化燃烧是借助催化剂在低温下(200~400℃)下,实现对有机物的完全氧化,因此,能耗少,操作简便,安全,净化效率高,在有机废气特别是回收价值不大的有机废气净化方面,比如化工,喷漆、绝缘材料、漆包线、涂料生产等行业应用较广,已有不少定型设备可供选用。 一、催化原理及装置组成 (1)催化剂定义催化剂是一种能提高化学反应速率,控制反应方向,在反应前后本身的化学性质不发生改变的物质。 (2)催化作用机理催化作用的机理是一个很复杂的问题,这里仅做简介。在一个化学反应过程中,催化剂的加入并不能改变原有的化学平衡,所改变的仅是化学反应的速度,而在反应前后,催化剂本身的性质并不发生变化。那么,催化剂是怎样加速了反应速度呢了既然反应前后催化剂不发生变化,那么催化剂到底参加了反应没有?实际上,催化剂本身参加了反应,正是由于它的参加,使反应改变了原有的途径,使反应的活化能降低,从而加速了反应速度。例如反应A+B→C是通过中间活性结合物(AB)过渡而成的,即: A+B→[AB]→C 其反应速度较慢。当加入催化剂K后,反应从一条很容易进行的途径实现: A+B+2K→[AK]+[BK]→[CK]+K→C+2K 中间不再需要[AB]向C的过渡,从而加快了反应速度,而催化剂并未改变性质。 (3)催化燃烧的工艺组成不同的排放场合和不同的废气,有不同的工艺流程。但不论采取哪种工艺流程,都由如下工艺单元组成。 ①废气预处理为了避免催化剂床层的堵塞和催化剂中毒,废气在进入床层之前必须进行预处理,以除去废气中的粉尘、液滴及催化剂的毒物。 ②预热装置预热装置包括废气预热装置和催化剂燃烧器预热装置。因为催化剂都有一个催化活性温度,对催化燃烧来说称催化剂起燃温度,必须使废气和床层的温度达到起燃温度才能进行催化燃烧,因此,必须设置预热装置。但对于排出的废气本身温度就较高的场合,如漆包线、绝缘材料、烤漆等烘干排气,温度可达300℃以上,则不必设置预热装置。 预热装置加热后的热气可采用换热器和床层内布管的方式。预热器的热源可采用烟道气或电加热,目前采用电加热较多。当催化反应开始后,可尽量以回收的反应热来预热废气。在反应热较大的场合,还应设置废热回收装置,以节约能源。 预热废气的热源温度一般都超过催化剂的活性温度。为保护催化剂,加热装置应与催化燃烧装置保持一定距离,这样还能使废气温度分布均匀。 从需要预热这一点出发,催化燃烧法最适用于连续排气的净化,若间歇排气,不仅每次预热需要耗能,反应热也无法回收利用,会造成很大的能源浪费,在设计和选择时应注意这一点。 ③催化燃烧装置一般采用固定床催化反应器。反应器的设计按规范进行,应便于操作,维修方便,便于装卸催化剂。 在进行催化燃烧的工艺设计时,应根据具体情况,对于处理气量较大的场合,设计成分建式流程,即预热器、反应器独立装设,其间用管道连接。对于处理气量小的场合,可采用催化焚烧炉(见图16-13),把预热与反应组合在一起,但要注意预热段与反应段间的距离。
VOCs催化燃烧的催化剂原理、应用及常见问题
VOCs催化燃烧的催化剂原理、应用及常见问题催化燃烧技术作为VOCs废气处理工艺之一,因为其净化率高,燃烧温度低(一般低于350℃),燃烧没有明火,不会有NOx等二次污染物的生成,安全节能环保等特点,在环保市场应用有了很好的发展前景。催化剂作为催化燃烧系统的关键技术环节,催化剂的合成技术及应用规则就显得尤为重要。 1、催化燃烧反应原理 催化燃烧反应原理是有机废气在较低温度下在催化剂的作用下被完全氧化和分解,达到净化气体目的。催化燃烧是典型的气固相催化反应,其原理是活性氧参与深度氧化作用。在催化燃烧过程中,催化剂的作用是降低反应的活化能,同时使反应物分子富集在催化剂表面上以提高反应速率。借助于催化剂,有机废气可以在较低的起燃温度下无焰燃烧并且在释放大量热量,同时氧化分解成CO2和H2O。 催化燃烧的催化剂反应原理图 2.什么是低温催化剂
低温催化剂性能指标:起燃温度≤200℃,氧化转化效率≥95%,孔密度200-400cpsi,抗压强度≥8MPa。 3.VOCs催化剂在催化燃烧系统中的作用与影响 通常VOCs的自燃烧温度较高,通过催化剂的活化,可降低VOCs 燃烧的活化能,从而降低起燃温度,减少能耗,节约成本。 另外:一般(无催化剂存在)的燃烧温度都会在600℃以上,这样的燃烧会产生氮氧化物,就是常说的NOx,这也是要严格控制的污染物。催化燃烧是没有明火的燃烧,一般低于350℃,不会有NOx 生成,因此更为安全和环保。 4.什么是空速?影响空速的因素有哪些 在VOCs催化燃烧系统中,反应空速通常指体积空速(GHSV),体现出催化剂的处理能力:反应空速是指规定的条件下,单位时间单位体积催化剂处理的气体量,单位为m3/(m3催化剂?h),可简化为h-1。例如产品标注空速30000h-1:代表每立方催化剂每小时能处理30000m3废气。空速体现出催化剂的VOCs处理能力,因此和催化剂的性能息息相关。 5.贵金属负载量与空速的关系,贵金属含量是越高越好吗?
燃气热水器之燃烧系统5-浓淡燃烧(万和新电气股份有限公司)
之燃烧系统5-浓淡燃烧 编制:热水器研发 代先锋 dai_money@https://www.360docs.net/doc/1610898516.html, 燃烧是物质因剧烈氧化而发光、发热的现象,也称之为火。 燃气热水器研发
NO X 来源、特性与危害 NO X 生成机理 案例 低氮氧化物技术现状 浓淡燃烧法
NO X来源、特性与危害 氮氧化物是矿物燃料(如石油、煤、天然气等)与氧在高温燃烧时产生的。 其包括一氧化二(N2O)、一氧化氮(NO)、三氧化二氮(N2O3)、二氧化氮(NO2)、四氧化二氮(N2O4)、五氧化(N2O5 ),一般来说,NOX是指NO2和NO。NO是无色无臭的气体,它在空气中极易氧化为NO2。NO2是一种红棕色有害的恶臭气体。 其含量为0.1ppm时可嗅到,1-4 ppm时,有恶臭,而达到25ppm时,则恶臭难闻。 空气中NO2含量为3.5ppm 持续1小时,开始对人有影响; 含量为20—50ppm时,对人眼睛有刺激作用; 当含量达到150ppm时。对人的呼吸器官则有强烈的刺激。特别危险的是,器官经过刺激暂时恢复以后,只要3—8小时会发生肺气肿,引起致命的危险。 二氧化氮在阳光作用下,经过系列连锁反应可生成臭氧。 臭氧是一种有毒的、危险的刺激物。
NO、NO2都是毒性很强的气体,与CO一样,NO与血液中的血色素(Hb)的结合能力远大于氧原子与血色素(Hb)的结合能力,因而当空气中NO含量达到一定浓度时,人体将因血液中缺氧而引起中枢神经麻痹。由于NO比CO更易于血色素(Hb)结合,因而其引起人体不良反应的最大允许值比CO更低(表1)。NO在空气中极易形成NO2,NO2对呼吸器官有极强的刺激作用,NO2对心脏、肝脏、肾脏都有不同程度的影响。
RCO催化燃烧技术
RCO催化燃烧VOCs有机废气处理技术 挥发性有机化合物(VOCs)是一类毒性大、污染严重的化学物质。目前VOCs的污染问题日益受到各国的高度重视,我国颁布的《大气污染物综合排放标准》,规定了各类有机污染物在空气中严格的排放标准。国内外VOCs污染控制方法目前主要有吸附法、吸收法、生物处理技术、膜分离技术、直接燃烧法、催化燃烧法等。其中,催化燃烧法是一种高效清洁燃烧技术,主要利用催化剂使有机废气在较低的温度条件下充分燃烧。相对其他处理技术,催化燃烧具有显著的优点:起燃温度低能耗少,处理效率高,无二次污染等,使之成为目前前景广阔的VOCs有机废气治理方法之一。高效催化燃烧催化剂是催化燃烧技术的关键核心,以块状载体作为骨架基体的催化剂称为规整结构催化剂,也称为整体式催化剂。由于具有特殊孔道结构,这类催化剂改善了催化反应床层上的物质传递,提高了催化效率,降低了压力,减少了操作费用,在石油化工、精细化工等多相催化反应中得到越来越广泛的应用。 RCO有机废气催化燃烧技术在日本、美国和西欧被广泛地应用于VOCs的治理,工艺设备非常成熟,相关的技术标准和使用规范已经非常完善,一些大公司都有自己的企业标准,对工艺设计、催化剂的性能要求、反应器制造和工程控制措施等都有详细的规定。不同的燃烧工艺组合,形成4种基本的燃烧工艺方式:催化燃烧(换热),直接燃烧(换热),回热催化燃烧(RCO),回热燃烧(RTO)。在此基础上还形成了转轮富集燃烧,陶瓷过滤器等方式。RCO有机废气催化燃
烧技术是指在催化剂的作用下,使有机废气中的碳氢化合物在温度较低的条件下迅速氧化成水和二氧化碳,达到彻底治理的目的。 一、RCO有机废气催化燃烧工艺原理: 催化净化是典型的气固相催化反应,其实质是活性氧参与的深度氧化作用。在催化净化过程中,催化剂的作用是降低活化能,同时催化剂表面具有吸附作用,使反应物分子富集于表面提高了反应速率,加快了反应的进行;借助催化剂可使有机废气在较低的起燃温度条件下,发生无焰燃烧,并氧化分解为CO2和H2O,同时放出大量热能,从而达到去除废气中的有害物的方法。 在将废气进行催化净化的过程中,废气经管道由风机送入热交换器,将废气加热到催化燃烧所需要的起始温度。 经过预热的废气,通过催化剂层使之燃烧。由于催化剂的作用,催化燃烧法废气燃烧的起始温度约为250~300摄氏度,大大低于直接燃烧法的燃烧温度650~800摄氏度,高温气体再次进入热交换器,经换热冷却,最终以较低的温度经风机排入大气。 二、RCO有机废气催化燃烧装置的工艺流程: 废气经阻火器过滤后,通过主进阀、旁通阀的同步反向切换调节进入热交换器,热交换器的热气升高一定温度后进入预热室、经过预热室的加热使废气升温到催化起燃温度(250度)然后进入催化反应床,在催化剂的活性作用下,有机废气进行氧化反应生成无害的水和二氧化碳,并放出一定的热量。反应后的高温气体再次进入热交换器,经换热后,最后以较低的温度经引风机排入大气。催化燃烧是借助催