(完整版)加热炉计算

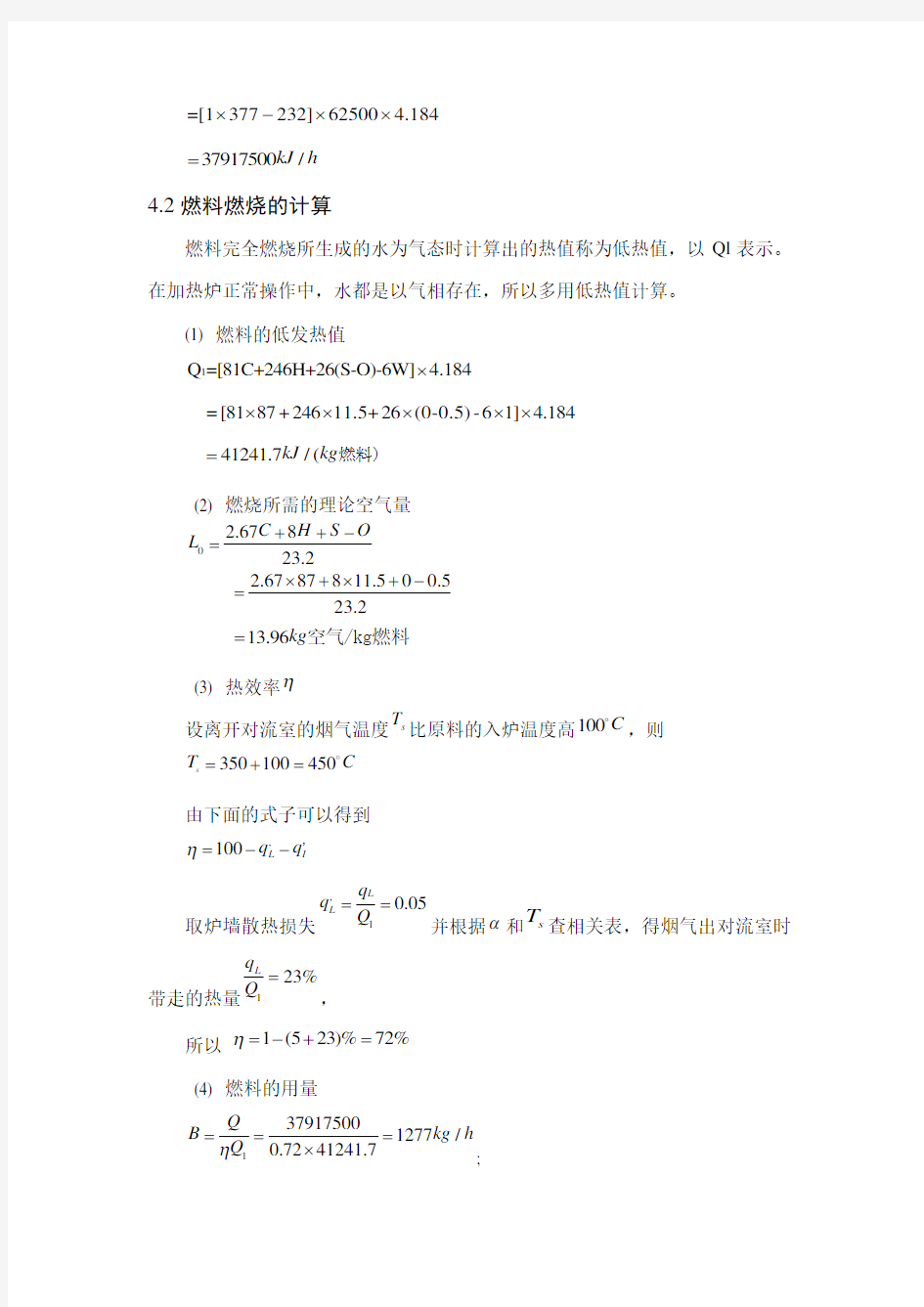
4.加热炉的计算
管式加热炉是一种火力加热设备,它利用燃料在炉膛内燃烧时产生的高温火焰和烟气作为热源,加热在管道中高速流动的介质,使其达到工艺规定的温度,保证生产的进行。在预加氢中需要对原料进行加热,以达到反应温度。预加氢的量较小,因此采用圆筒炉。主要的参数如下:
原料:高辛烷值石脑油; 相对密度:
20
40.7351
d =
进料量:62500/kg h
入炉温度:I τ=350C o
;
出炉温度:o τ=490C
o ;
出炉压强:2
15/kg cm
气化率: e=100%; 过剩空气系:α:辐射:1.35 对流段:1.40 燃料油组成:
87%,11.5%,0.5%,1%C H O W ====
加热炉基本参数的确定
4.1加热炉的总热负荷
查《石油炼制工程(上)》图Ⅰ-2-34可知,在入炉温度t1=350℃,进炉压力约15.0㎏/㎝2条件下,油料已完全汽化,混合油气完全汽化温度是167℃。
原料在入炉温度350C o ,查热焓图得232/i I kJ kcal
= 原料的出炉温度为490C o ,查热焓图得377/v I kcal kg =。
将上述的数值代入得到加热炉的总热负荷 Q = m[eIV+(1-e)IL-Ii]
=[1377232]62500 4.184?-??
37917500/kJ h =
4.2燃料燃烧的计算
燃料完全燃烧所生成的水为气态时计算出的热值称为低热值,以Ql 表示。在加热炉正常操作中,水都是以气相存在,所以多用低热值计算。
(1) 燃料的低发热值
1Q =[81C+246H+26(S-O)-6W] 4.184?
=[8187+24611.5+26(0-0.5)-61] 4.184????? 41241.7/(kJ kg =燃料) (2) 燃烧所需的理论空气量
0 2.67823.2C H S O L ++-=
2.6787811.500.52
3.2?+?+-=
13.96kg =空气/kg 燃料 (3) 热效率η
设离开对流室的烟气温度
s
T 比原料的入炉温度高100C o
,则
350100450s T C
=+=o
由下面的式子可以得到
,
100L I q q η=--,
取炉墙散热损失
,
1
0.05L
L q q Q =
=并根据α和s T 查相关表,得烟气出对流室时
带走的热量123%
L
q Q =,
所以 1(523)%72%η=-+= (4) 燃料的用量
1379175001277/0.7241241.7
Q B kg h Q η=
==?;
(5) 火嘴数量
假定火嘴的额定喷油能力比实际燃料大30%,选择标准火嘴的流量200kg/h ,则需要火嘴的数量为
1.3 1.312778.3
200200B n ?===
进行取整取9n = (6)烟道气流量
0(1.5)1277(1.5 1.413.96)
g W B L α=+=?+?
26873/kg h =
4.3加热炉相关参数计算
(1) 圆筒炉辐射室的热负荷
根据工艺要求和经验,参照表4-1,选取四反加热炉为圆筒炉。圆筒炉对流室较小,炉管较少,当用光管时,对流室热负荷QC 所占比例较小,现已知加热炉的总热负荷Q ,现在取辐射室的热负荷
R
Q 为全炉热负荷的75%,则
0.75
R Q Q =?
379175000.7521438125/R Q kJ h
=?=
(2) 辐射段管壁平均温度估算
55
2I o
w T ττ+=+
,()0.75
L o o I T τττ=--?
490(490350)0.75=--?
385C =o
385490554932w T C
+=+=o
(3) 辐射管表面积、管径及管心距 根据经验选用辐射表面热强度224125/()
R q kcal m h =
(4) 辐射管的表面积
228438125
28224125 4.184R R R Q A m q =
==?
(5)管径
同时选管道内油料质量流量,由《管式热炉》(穆文俊主编)表4-1知,经验
值为100-1502
/()kg m s ,故取2150/()F G kg m s =,N 增加,压降降低,但易出现偏
流,烧坏炉管;N 减少,压降增大,动力消耗增加。
取管程数9N =,则炉管的内径
i d =
=
0.128m =
=
根据国产炉管的规格选择炉管的尺寸为1528φ?的炉管 (6) 管心距 选用管心距为
10220.1520.304S d m
==?=
(7) 高径比
国内多为空心圆筒炉,管长受热不均,所以高径比Lef/D′=1.7—2.5。节圆直
径越大,高径比越小,取Lef/D′=2.1。选定炉子的高径比'
2.1
ef
L D
=,由下面的式
子计算节圆直径
'''()(2.1)
R ef C
A D L D D πππ
?==
' 5.2D m =
==
辐射管的有效长度
'2.1 2.1 5.210.92ef L D m
==?=
根据国产的炉管规格,取12ef L m
=。
(8) 对流段长
选用对流管1528φ?标准钉头管。
1.25 5.4 5.220.152 1.25 5.40.152
c L D
d =--=+?--?
3.433m =
取对流管长
4c L m
=
(9) 对流段宽
由《管式热炉》(穆文俊主编)附表查的1528φ?标准钉头管,管周边钉头数14,钉头直径12m 钉头纵向间距16mm ,钉头高25mm 。
每米钉头管所占面积
'''10001000
1210.1520.0140.025216
c c i p a
d d b d =?+
???=?+???
2
0.196m =
根据经验选择烟气质量流速23/()
g G kg m s =
选用管心距为
2c
d
/3600g g c c c w W G L S a L n =
-
则
26873/3600340.1964w S n =
-?
0.1520.304w
S n =+代入上式得:
268733[4(0.1520.304)0.784]3600w w n n ?+-=
4.35
w n =根
取
5
w n =根
0.1520.3045 1.67S m =+?=
(10) 确定节圆直径'
D 辐射管高度H 和炉膛直径D 遮蔽管面积=2
540.152 3.149.55m ???= 辐射壁管面积2
2829.55272.45m =-=
炉管根0272.45
47.6
3.140.15212
R ef A n d L π=
==??根
根据取炉管根数为54(9管程) 选用辐射9654n =?=管根,9管程。
实际节圆直径 所以炉膛的直径
'02 2.9020.152 5.534 5.6D D d m
=+=+?=≈
根据炉子结构设计辐射段高度比炉管长度长1m 。 炉膛的高度
112113ef H L m
=+=+=
(11) 当量冷平面面积 辐射管冷平面面积
21540.0.152212197cp ef A nS L m ==???=
管心距为
2d ,查图得到0.88α=
2
0.88197173.4cp A m α=?=
遮蔽管冷平面:
对流管拟选用和炉管相匹配的钉头管1528φ?。管心距为
2c
d .对流室每排为
5n ω=根炉管,采用三角形排列钉头管。
2
540.304 6.08cp A m =??= 及1α=
26.11 6.1CP A m α=?=
总的当量冷面积
2
173.4 6.1179.5CP A m α=+=
(12) 求有效暴露砖墙面积与当量冷平面
之比
22
5.613215.6277.84F m
ππ=??+??=∑ 有效的反射面积
2
272.45179.593R cp A A A m α=∑-=-=
比值:93
0.518179.5
R cp A A α==
(13) 烟气的黑度(辐射率)
已经知道过剩空气系数 1.35α=,由图表可以查到二氧化碳和水蒸汽的分压
'1
540.304
5.233.14
nS D m
π
?=
=
=w
cp
A A α
为
220.218CO H O m
P P atm ?+=
烟气的平均辐射长度为
5.6L D m ==
故0.218 5.6 1.22.PL atmm =?= 假定辐射室的出口烟气的温度为700g T C
=。,则查得烟气的黑度为
0.59
g ε=
(14) 总辐射交换因子
根据0.518w
cp
A A α=和
0.55
g ε=查图8得到0.59F =;
(15) 辐射室热平衡
10.5180.55(10.02)g w R g cp CP CP q A Q BQ
A A Q A F
εααα===--
其中:41127741241.7526710/BQ kJ h
=?=? 1
R q Q —辐射段热损失。取1
0.02R
q Q =。查图4当700g t C =。
,过剩空气系数 1.35α=时,得10.375R q Q =
则
4
22526710(10.020.375)300886/71914/179.50.59
w cp A kJ m h kcal m h A α?=--==?
(16) 求辐射室出口烟气温度 取图10-b 中关闭温度
443w t C
=。做吸收曲线如下图,当第一次假设
700g t C
=。
及
271914/w
cp
A kcal m h A α=时,交点A 画于图上,位于w
t 的上方。,再另设
900g t C
=。
重复上述计算过程,由图7查得气体辐射率
0.515
g ε=,0.57F =,由图4
查得1
0.5R
q Q =。则
4
22526710(10.020.5)247096/59057/179.50.57R CP Q kJ m h kcal m h
A F α?=--==?
作于图上得到B 点,连接两点,该直线与曲线的交点,就是辐射室的出口温度
796p t C
=。;如下图:
4.4校核
(1) 辐射室热负荷
R Q
由于辐射室出口的温度
796p t C
=。,查图4得;1
0.43
g
q Q =
44(10.020.43)526710289710/R Q kJ h
=--??=?
占加热炉的总热负荷的4
4
28971076.3%379210?=?
(2) 辐射管表面热强度
R
q
42228971096653.06/23100/540.15212540.152R q kJ m h kcal m h
ππ?===??-?
(3) 辐射室出口处油品的总焓值
4625001377 4.184985810/H kJ h ∑=???=?
在辐射室入口处每一千克油品的焓值
图10辐射发球烟气出口温度
44
9858102897101113.76/266/62500kJ h kcal h
?-?==
查油品的热焓图得390o
C
1390490
504902o C τ+=
+=与估算的493o
C 相近,故合适。
4.5 对流室的传热计算 4.
5.1 对流室热负荷
由下面的式子可以得到对流室的热负荷
443791750028971089510/C R Q Q Q kJ h
=-=-?=?
4.5.2 对流室的对数平均温差
烟气温度 800450o
C →
油品温度 390350o o C C ← 410 100
4.5.3 内膜传热系数
油品的平均温度 350390
3702o m t C +=
=
烟气的平均温度
370220590o f m T t t C =+?=+=
管壁的平均温度
5037050420o t m T t C
=+=+=
对流段平均粘度
查设计图表的原料油蒸汽的粘度为0.0000125Pa s g
循环氢粘度近似按照氢的粘度计算,370。C 时,其值为0.0000150Pa s g 按照式(1)计算氢与油混合物粘度
0.5
0.50.50.5
0.50.5
()(3.5/4.5) 3.40.000015(1/4.5)1090.0000125()
(3.5/4.5) 3.4(1/4.5)109i
i
i
i
i
y M Z Z y M ??+??=
=
?+?∑∑
410100
220
410
ln 100
t -?==
55
(2.14710 2.910)/(1.43 2.32)--=?+?+ 0.0134cp =
该粘度说明应按照低粘度公式计算。
则带入数值得到0.8
10000.1521330.023()0.372750/0.0134o i h kcal mh C
??=??=
考虑到关内污垢热阻且无保护气,得: 由表10查得
0.0008
i R =
*2469/o i h kcal m h C
=
4.5.4 管外膜传热系数
(1) 钉头表面传热系数
796490273904796ln 490T K
-?=+=
2/360026843/3600
2.7/4 1.670.19654g g c c c w
W G kg m s
L S a L n =
=
=-?-??
0.6670.320.333
2.879049.4461.7/12o
s h kcal m h C ?=?= **111
0.0050.0050.021261.7
s s h h =+=+=
得
*247.2/o s h kcal m h C
=
(2) 钉头效率
所采用的钉头为12φ标准钉头,钉头高为0.025m ,当261.7/o s h kcal m h C =时,
*11
i i i
R h h =+*
11
0.00080.0028750
i h =+=()
.tgh mb m b
Ω=
查图15得0.90Ω=。 (3) 光管管外对流传热系数
则
*223.4/oc o h kcal m h C
=
(4) 钉头管外膜传热系数
2
00.1520.477m απ==
则
**247.20.90.791323.40.3925
89.7/0.477o s s s s b
so o
h h h kcal m h C
αααΩ+??+?=
=
=
4.5.5 对流段总传热系数
**
2**89.746975.3/89.7469o o i c o i h h K kcal m h C
h h ?===++
4.5.6 对流管表面积及对流管排数
42
89510/4.18412975.3220c c c Q A m K t ?===??
129
13.5
540.152c c w c c A N n L d ππ=
==???排
选用对流管共14排,遮蔽管在对流管下部,所以对流管的总派数为15排,每排5根。
4.5.7对流室高度
由式(5-31)得
0.886(1)0.8860.304(141) 4.04c c c H S N m
=+=??+=
0.6670.320.333
2.79049.4426.5/152o
oc h kcal m h C ?=?=**110.0050.03770.0050.0427oc oc
h h =+=+=22
12
0.1520.0120.39254
0.016
b m π
απ=-
??
=22
12(0.0120.0250.012)0.79130.0164
s m π
απ=
?+?=
4.5.8 对流管表面热强度
4
22
8951062507/17363/1554 3.140.152c c c Q q kJ m h W m A ?====????
在经验值9300-232602
/W m 之间,符合要求,并有一定潜力。
4.6 炉管压力降计算 4.6.1计算混合油气密度
由于原料以350o C 进炉,在152
/kg cm 压力下出炉,在167o C 下就完全汽化,
因此汽化段压降P ?就是全炉的压降。又知一段混氢的氢油比为3.5:1,混合油气的摩尔流率
原料油流量=62500/109573/kmol h = 循环氢摩尔流量=573 3.52005.5/kmol h ?= 由前面算的循环氢平均相对分子质量为3.4 则,循环氢质量流率=2005.5 3.46818.7/kg h ?= 总质量流率=625006818.769318.7/kg h +=
3.562500625003.52580/109109G G n kmol h
M M =+=+?=
加热炉平均温度为(350+490)/2=420 o
C ,平均压力2
15/kg cm ,混合油气平均
体积流量
34802731(5732005.5)22.410621/15273m nRT
V m h
p +=
=+???=
混合物的密度3
69318.7/10621 6.53/kg m ρ==
4.6.2混合气体流速
2262500
20.3/900900 6.530.1369m m G
m s
d N
ωπρπ=
=
=????????
4.6.3 摩擦系数
0.013550.01350.038
λ===
4.6.4 压力降
对流段当量长度
1454145(1)(1)300.13658.899c i nL n L d m
N N ????=+-=+-??= 辐射管当量长度 541254(1)(1)300.13692.499ef i nL n L d m
N N ??=+-=+-??= 则
58.892.4151.2e c ef L L L m
=+=+=
'22151.220.30.038 6.53
20.1362e m e m i L p d ωλρ?==???
2
56842.30.5680.58/Pa atm kg cm ===
4.7 烟囱的设计计算
烟囱是加热炉不可缺少的一部分,它主要的作用是产生一定的抽力使得烟气在加热炉中不断的流动,并将高温烟气向高空中排放,以减少对环境的污染。加热炉的烟囱可以用钢,砖或者混泥土制成,可以设置在炉子旁边也可以放在炉子顶部。不过一般中小型的圆筒炉的烟囱都是用钢材制成的,并且防止在炉子的顶部。总之,在采取自然通风的加热炉中,一个设计良好的烟囱,应该保持炉子内部保持一定的负压,使燃料燃烧所需的空气进入炉内,而且高温烟气不能够从炉内泄漏。
4.7.1烟气的阻力
对流段的阻力(交错排列钉头管) ① 钉头区域外部的烟气质量流速
'
1.81.8
0.2''()(
)()
g p si so go
s p
W d A A G N d -=
26873
7.46/3600g W kg s =
=
② 对流段截面积:2
4 1.67 6.68m ?= ③ 每排炉管(光管)所占截面积:
20.15245 3.04m ??=
④ 钉头所占截面积: 2
4.0
250.0120.0250.750.016m ????=
⑤ 自由通道截面积:2
6.68 3.040.75 2.89m --= ⑥ 对流段截面积:2
4 1.67 6.68m ?= ⑦ 每排炉管(光管)所占截面积:
20.15245 3.04m ??=
⑧ 钉头所占截面积: 2
4.0
250.0120.0250.750.016m ????=
⑨ 自由通道截面积:2
6.68 3.040.75 2.89m --= ⑩ 钉头区域外部的流通面积
2
[1.67(0.15220.025)10]5 2.64SO A m =-+???=
钉头区域内部的流通面积
2
2.89 2.640.25SI A m =-=
钉头与钉头之间的间隙
'0.077p d m
=
两相邻钉头管之间的间隙
''0.0160.0120.004p d m
=-=
将相关的数值代入下面的公式进行求解得到
'
1.81.8
0.2
"()()3600g
p SI SO go S p
m d A A G N d -=
将相关的数据代入得到
1.81.80.27.460.250.004(
2.64)()120.077go G -= 将数值代入得到
22.8/go G kg m s
=
因为烟气在对流室的平均温度为904K ,查得烟气的粘度为
20.55158.25s mmH O μ=?= (2) 各部分的局部阻力
对流室截面和辐射室截面之比 221
2.890.1175.64A A π==?
查表得到1
0.46ξ=
7962731069g T K
=+=
22.7/G kg m h =
2
421069 2.70.46[]0.5286940H mmH O
??=?=
(3) 烟气由对流段到烟囱的阻力,取烟囱直径
1.7s D m
=
20.785 1.70.785
2.89?==烟囱截面积对流段流通面积
查表得
20.168ξ=
450273723g T K
=+=
2
2
7.46 3.29/0.785 1.7g G kg m s =
=?
符合于2.5 2 52723 3.290.168[]0.196940H mmH O ??=?= (4) 烟囱挡板阻力 45055273668g T K =-+= 23.29/g G kg m s = 但自由截面为全截面的50%时, 34ξ= 代入公式得:252668 3.294[] 4.176940H mmH O ??=?= 4.7.2 烟气在烟囱中的摩擦损失及动能损失 (1) 烟气在烟囱中的摩擦损失 假定烟囱高度20m 668g T K = 0.013g cp μ= 1.7s D m = 23.29/g G kg m s = 1000 1.7 3.29Re 430231 0.013??== 查图17得0.045f = '2 2721120668 3.290.00450.2211735173517s g g s H H T G f mmH O D ?==????= (2) 烟气在烟囱中的动能损失 2 2 82668 3.29 1.0469406940g g T G H mmH O ??=== 4.7.3 烟囱的高度 根据前面烟囱阻力计算结果,烟囱所需的最小抽力: 28.250.5280.19 4.170.221 1.0414.399144D H mmH O Pa ?=+++++== 大气温度 27327300a T K =+= 烟囱底部烟气温度 723b T K = 查图15得 0.91s α= 烟囱内烟气平均温度 ()0.91(723300)685m s b a a T T T T K α=-+=?-= 为了能够吊装辐射管,烟囱必须有如下的最低高度。 22 28.762 33S ef H L =+=?+ 7.84m = 烟囱最小高度用下式计算: 1111355( )355()21.7300685D s a m H H m T T ?=+=?-= 因此,烟囱最小高度21.7m,根据实际情况,烟囱的实际高度应该高于21.7m 表4-1.结果汇总 项目 数据 总有效热负荷Q,kJ/h 37917500 辐射室热负荷,Q R , kJ/h 28438125 对流室热负荷,Q, kJ/h 8950000 辐射室炉管表面热强度,q R ,kcal/m 2h 26125 对流室炉管表面热强度,q c , kcal/m 2h 14940 辐射室烟气温度,t g ,℃ 796 对流室烟气温度,t,℃ 450 过剩空气系数α 1.35 理论空气用量,L o kg 空气/kg 燃料 13.96 燃料用量 B(kg/h)燃料/n(个) 1277及9 燃料低热值Qv(KJ/㎏燃料) 41241.7 炉子热效率η 72% 烟气流量Mg(㎏/h) 26873 烟气流速Wg(㎏/㎡·s) 3 对流室结构尺寸L C ×S×H C 4×1.67×4.04 辐射室结构尺寸 D×H 5.6×13 辐射管规格Ф×S′×L×n 152×8×12×54 辐射管管心距S ,管程数N 0.304,9 对流管管心距S ,管程数N 0.304,9 对流室管排数 14 遮蔽管根数 5 加热炉压力降atm 0.568 对流室规格 Ф152×8×3000×90 附录 符号说明 反应器 p C :平均比热容,kJ/kg o C ; o R :当量直径,m ; α:组分的重量分数; t :催化剂床层厚度,m ; H ?:焓值,kJ/kg 或kcal/kg ; ω床:床层线速,m/s ; j m :与焓值相关的斜率; μ:气体粘度Pas 或cp ; j b :与焓值相关的截距; ξ:阻力系数; 2 H X :氢气的纯度,%; Q ?:不均匀度,%; p ?:床层压降,kg/cm2或atm ; 加热炉部分 H :反应器高,m ; i τ:加热炉入口温度,o C ; Z :混合气体粘度Pas 或cp ; o τ:加热炉出口温度,o C ; D :反应器直径,m ; e :气化率,%; n :扇形筒个数; α:过剩系数; F F 分集 、:集、分气管面积,m2; l Q :低发热值,kJ/kg ; h :催化剂装入高度,m ; o L :理论空气量; e m D d 、:当量直径,m ; η:热效率,%; B :流道面积比参数; s T :对流室烟气温度o C ; K K 分集 、:分、集气管动量交换系数; 'L q :散热损失; ρ:流体密度,kg/m3; B :燃料用量,kg/h ; ?:开孔率; n :火嘴数; g W :烟道气流量,kg/h ; t T :管壁平均温度,o C ; c Q :对流室热负荷,kJ/h ; * i h :内膜传热系数,2 /o kcal m h C ; R Q :辐射室热负荷kJ/h ; *o h :外膜传热系数,2 /o kcal m h C ; w T :辐射段平均壁温,o C ; Ω:钉头效率; R q :辐射管表面热强度,2/kcal m h ; oc h :光管外对流传热系数,2/o kcal m h C ; R A :辐射管表面积,m2; so h :钉头管外膜传热系数,2/o kcal m h C ; i d :管内径,m ; c H :对流室高,m ; l S :管心距,m ; c q :对流管外表面热强度,2 /kcal m h ; ef L :辐射管有效长度,m ; m V :油气平均体积流量m3/h ; c a :单位长度钉头管所占面积,m2; m W :混合气体流速,m/s ; g G ;烟气质量流速kg/m2s ; λ:摩擦系数; S :对流段宽,m ; c L :对流段当量长度,m ; 'D :节圆直径,m ; e P ?:压力降,pas 或cp ; D :炉膛直径,m ; i H ?:烟气各部分阻力(压降),mmH2O ; cp A :辐射管冷平面面积,m2; D H ?:烟囱最小高度,m ; g ε:烟气辐射率; L :平均辐射长度,m ; t ?:对数平均温差,o C ; m t ?:油品平均密度,o C ; g T :出口烟气温度,o C ; f T :烟气平均温度,o C ; 冶金加热炉设计工作手册. 作:编委会 冶金工业出版社 2011年出版 16开 精装1本 光盘:0 定价:328元 优惠:180元 .. 详细:.......................................... ............ .......................................... ............ 冶金加热炉设计工作手册 第一篇冶金工厂加热炉的设计方法和原则 第一章加热炉的初步设计 第一节设计前的原始资料 第二节加热炉炉型的确定 第三节加热炉燃料的确定 第四节加热炉燃烧装置的确定 第五节预热装置的选择及安装 第六节鼓风系统和排烟系统 第七节炉子水冷系统的确定 第八节加热炉钢结构 第九节加热炉机械和自动调节 第一节绘制加热炉炉型示意简图 第二章加热炉的工艺计算和设计 第一节燃料燃烧计算 第二节加热炉的热制度 第三节钢坯加热温度和时间的计算 第四节炉子数量和基本尺寸的确定 第五节炉体筑炉材料确定 第六节力口热炉炉衬的设计 第七节钢架结构的设计 第八节炉子热平衡和燃料消耗量的计算 第九节燃烧装置的计算 第十节预热装置的计算 第十一节煤气(空气)管道和烟道的设计 第二篇钢铁厂加热炉设计实例 第三章120t/h步邂釉肋口热炉设计实例 第一节步进梁5勒口热炉设计基本情况 第二节步进梁5肋口热炉设计说明 第三节步进梁式加热炉及其附属设备的工艺性能 第四节步进梁式加热炉各结构说明 第六节图例 第四章15t/h推钢式连续加热炉设计实例 第—节加热炉炉型的选择 第二节燃料燃烧计算 第三节卿劾燃时间的计算 第四节炉子卸》Rl寸的决定及有关的J计嘴标 第五节热平衡计算及燃料消耗量的确定 第六节燃烧系统的设计 第七节烟道的设计 摘要 冶金工业消耗大量的能源,其中钢坯加热炉就占钢铁工业总能耗的四分之一。自70年代中期以来,各工业先进国对各种燃烧设备的节能控制进行了广泛、深入的研究,大大降低了能耗。 步进式加热炉不仅是轧线上最重要的设备之一,而且也是耗能大户。钢坯加热的技术直接影响带钢产品的质量、能源消耗和轧机寿命。因此步进式加热炉优化设定控制技术的推广对钢铁企业意义重大。步进式加热炉的生产目的是满足轧制要求的钢坯温度分布,并实现钢坯表面氧化烧损最少和能耗最小。由于步进式加热炉具有非线性、不确定性等特点,其动态特性很难用数学模型加以描述,因此采用经典的控制方法难以收到理想的控制效果,只能依靠操作人员凭经验控制设定值,当工况发生变化时,往往使工艺指标(如空燃比)实际值偏离目标值范围,造成产品质量下降消耗增加。针对以上情况,本文通过理论和仿真比较说明使用双交叉限幅控制系统是一种比较好的燃烧控制方法。 关键词:步进式加热炉;空燃比;双交叉限幅;系统仿真 Abstract Metallurgical industry consumes large amounts of energy, the billet heating furnace accounts for 1/4 of the total energy consumption of iron and steel industry. Since 70 time metaphase, the advanced industrial countries have conducted extensive research, in-depth on the energy saving control device of different combustion, greatly reduces the energy consumption. Reheating furnace is not only the most important one of the equipment of the rolling line, but also a large energy consumer. Billet heating technology directly affects strip steel product quality, energy consumption and mill life. The step type heating furnace optimal setting control technology is of great significance to the promotion of iron and steel enterprises. Step type heating furnace production is designed to meet the requirements of the temperature distribution of the billet rolling surface, and to achieve the fewest stock scale loss and energy consumption. Due to the characteristics of reheating furnace is a nonlinear, uncertainty, its dynamic characteristics is difficult to use mathematical model to describe, so using classic control theory to receive the ideal control effect, can only rely on the operation experience of the personnel to control the set value, when the conditions change, often make the process indicators (such as the air fuel ratio) the actual value is far from the target range, decrease the product quality consumption increase. In view of the above situation, this paper through theoretical and simulation results illustrate the use of double cross limiting control system is a good method for controlling combustion. Keywords: reheating furnace; air fuel ratio; double cross limit; system simulation 超临界压力600MW 中间再热凝汽式汽轮机在额定工况下的热经济指标计 机组型号:N600-24.2/566/566 汽轮机型式:超临界、单轴、三缸(高中压合缸)、四排汽、一次中间再热 凝汽式 蒸汽初参数:MPa p 2.240=,5660=t ℃;MPa p 51546.00=?, 再热蒸汽参数:冷段压力MPa p in rh 053.4=,冷段温度5.303=in rh t ℃;热段压 力MPa p out rh 648.3=,热段温度0.566=out rh t ℃;MPa p rh 4053 .0=?, 排汽压力:kPa p c 4.5= (0.0054MPa ) 抽汽及轴封参数见表1。给水泵出口压力MPa p pu 376.30=,凝结水泵出压 力为MPa 84.1。机械效率、发电机效率分别取为99.0=m η,988.0=g η。 汽动给水泵用汽系数pu α为0.05177 表1 N600-24.2/566/566型三缸四排汽汽轮机组回热抽汽及轴封参数 解: 1.整理原始资料 (1)根据已知参数p 、t 在s h -图上画出汽轮机蒸汽膨胀过程线,得到新 汽焓等。0.33960=h kg kJ ,82.2970=in rh h kg kJ ,2425.3598=out rh h kg kJ , 9.62782.29702425.3598=-=rh q kg kJ 。 (2)根据水蒸汽表查的各加热器出口水焓wj h 及有关疏水焓'j h 或d wj h ,将机 组回热系统计算点参数列于表2。 图1 超临界压力600MW三缸四排汽凝汽式机组蒸汽膨胀过程线 井口加热炉热工检测方案 一、项目来源 根据胜利油田采油工程处部署,对胜利油田在用的各厂家的各种类型井口加热炉进行热效率测试。本次测试工作由胜利油田技术检测中心能源监测站承担。 二、检测目的: 检测加热炉在实际运行工况下的加热炉的热效率。 三、依据标准: SY/T6381-1998 加热炉热工测定 SY/T6275-1997 石油企业节能检测综合评价方法 四、测试基本检测方法及测试数量 4.1 测试方法 测试方法采用正平衡法与反平衡法相结合的测试方法。当现场不满足正平衡测试条件时,则以反平衡测试方法进行测试。 正平衡法:通过直接测量加热炉输入热量和输出热量而计算出效率的方法。 反平衡法:通过测定加热炉各项热损失而计算出效率的方法。 4.2测试数量 因本次需测试的加热炉数量众多,故采取抽样测试的方式进行,抽测比例不低于30%。具体按各厂家加热炉(包括各种型号的加热炉)数量的30%进行。 五、测试工况要求: 1 、时间要求: (1)、测试应在加热炉热工况稳定和燃烧调整到测试工况1h后开始进行。 (2)、测试的持续时间不少于1h,烟气成分和排烟温度每隔15min读数记录数据一次。 2 、燃料要求:测试时加热炉所用燃料应符合加热炉设计要求。 3 、加热炉液位要求:测试结束时,加热炉液位应与测试开始时保持一致。 4 、加热炉负荷应在符合工艺要求(被加热介质出口温度达到外输要求)的工况。 七、测试项目 主要测试项目如下: 1)液体燃料元素分析、低位发热量、密度、含水量; 2)燃料消耗量; 3)燃烧器前燃油(气)压力; 4)燃烧器前燃油(气)温度; 5)被加热介质流量; 6)被加热介质密度; 7)被加热介质含水量; 8)加热炉进口、出口介质温度; 9)加热炉进口、出口介质压力; 10)排烟温度; 11)排烟处烟气成分分析; 12)入炉空气温度; 13)炉体外表面温度; 14)当地大气压力; 15)环境温度; 第三章 热力分析 3.1汽轮机主要参数 汽轮机类型:600-24.2/566/566 蒸汽初参数 ;024.2p MPa =, 0566t =.0℃ 再热蒸汽参数:冷段压力 4.33in rh p MPa =,冷段温度314.9in rh t =℃: 热段压力 3.90out rh p MPa =,热段温度566.0out rh t =℃。 排气压力:0.00490c p MPa = 。 抽汽及轴封参数见表3-1和表3-2。机械效率、发电机效率分别取为0.99m η=、 0.988g η=。 表3-1 项目 单位 各 段 回 热 抽 汽 参 数 加热器编号 — H1 H2 H3 H4 H5 H6 H7 H8 抽汽压力 j p MPa 5.62 4.33 2.31 1.16 0.438 0.128 0.0619 0.0237 抽汽温度j t ℃ 349.2 314.9 483.9 379.6 261.3 139.8 86.8 63.8 表3-2 项 目 单 位 1sg α 2sg α 3sg α 来 源 高压杆漏汽 低压缸后轴封 漏汽 高中压缸之间漏汽 轴封汽量sg α 0.0006339 0.001038 0.00007958 轴封汽比焓sg h kJ/kg 3396.0 2753.7 2993.7 去 处 H8 SG H2 原则性热力系统图3-1如下: 图 3-1 3.2热平衡法 热平衡式一般有两种写法:一是吸热量=放热量×h η,h η为加热器的效率;另一种方法是流入热量=流出热量。为了在同一系统计算中采用相同的标准,应采用统一的,h η故热平衡式的写法,在同一热力系统计算中也采用同一个方法。 拟定热平衡式时,最好根据需要与简便的原则,选择最合适的热平衡范围。热平衡范围可以是一个加热器或数个加热器,乃至全部加热器,或包括一个水流混合点与加热器组合的整体。 3.2.1 整理原始资料 加热功率计算公式 Q 总 =( Q 有效 +Q 热损失) xa Q 有效 :工件加热吸收的有效热 Q 热损失 :包括炉墙、炉门、风扇等处热辐射损失 a:系数,加热炉一般取 1.2 预氧化炉、回火炉一般取 1.1 1.按实际产量计算 : Q 有效 =Jm (kw) J: 金属的比能(查表 AJW (kw/Kg) 奥地利经验值表格) m:每小时最大装炉量(kg) Q 热损失 =Q1+Q2+Q3+ Q4+Q5+Q6 Q1=2kw x N1(N1: 炉门个数 ) Q2=1kw x N2(N2: 炉顶风扇个数 ) Q3=0.5kw x N3(N3: 电辐射管个数,燃气管 散热损失取1kw) Q4=1.5kw x N4 Q5=2kw Q6=Kxa (N4: 横向推料装置) (观察窗、热电偶、气氛消耗 (K: 炉体表面积 , a:炉墙外表面热损失 炉外表温度65oC 炉外表温度60oC 炉外表温度55oC ) 时取 时取 时取 0.5 kw /m2 0.45 kw /m2 0.4 kw /m2 举例 某预氧化炉,炉内 4 盘料,料盘600x600,每盘装料 温度 <60℃, 炉体尺寸: 3200x1800x1700则炉体表面积30m2 周期时间为15 分钟则每小时装料1200kg 加热采用9 支辐射管 300kg,炉内温度450℃,要求炉外墙 1.计算 Q 有效 查表 AJW,450 ℃比能 J=0.07kw/kg Q 有效 =Jm=0.07x1200=84 kw 2.计算Q 热损失 Q1=2kw x 2=4kw (N1: 炉门个数) Q2=1kw x 1=2kw (N2: 炉顶风扇个数) Q3=0.5kw x9 =4.5kw Q5=2kw (N3: 电辐射管个数) (观察窗、热电偶、后限位) Q6=Kxa=0.45x30=13.5kw (K: 炉体表面积30m2, a:炉外表 60oC 时取 0.45 kw /m2) Q热损失 =Q1+Q2+Q3+Q5+Q6= 26kw 3.Q 总=( Q 有效 +Q 热损失) xa=(84+26)x1.1=121kw 4.加热炉的计算 管式加热炉是一种火力加热设备,它利用燃料在炉膛内燃烧时产生的高温火焰和烟气作为热源,加热在管道中高速流动的介质,使其达到工艺规定的温度,保证生产的进行。在预加氢中需要对原料进行加热,以达到反应温度。预加氢的量较小,因此采用圆筒炉。主要的参数如下: 原料:高辛烷值石脑油; 相对密度: 20 40.7351 d = 进料量:62500/kg h 入炉温度:I τ=350C o ; 出炉温度:o τ=490C o ; 出炉压强:2 15/kg cm 气化率: e=100%; 过剩空气系:α:辐射:1.35 对流段:1.40 燃料油组成: 87%,11.5%,0.5%,1%C H O W ==== 加热炉基本参数的确定 4.1加热炉的总热负荷 查《石油炼制工程(上)》图Ⅰ-2-34可知,在入炉温度t1=350℃,进炉压力约15.0㎏/㎝2条件下,油料已完全汽化,混合油气完全汽化温度是167℃。 原料在入炉温度350C o ,查热焓图得232/i I kJ kcal = 原料的出炉温度为490C o ,查热焓图得377/v I kcal kg =。 将上述的数值代入得到加热炉的总热负荷 Q = m[eIV+(1-e)IL-Ii] =[1377232]62500 4.184?-?? 37917500/kJ h = 4.2燃料燃烧的计算 燃料完全燃烧所生成的水为气态时计算出的热值称为低热值,以Ql 表示。在加热炉正常操作中,水都是以气相存在,所以多用低热值计算。 (1) 燃料的低发热值 1Q =[81C+246H+26(S-O)-6W] 4.184? =[8187+24611.5+26(0-0.5)-61] 4.184????? 41241.7/(kJ kg =燃料) (2) 燃烧所需的理论空气量 0 2.67823.2C H S O L ++-= 2.6787811.500.52 3.2?+?+-= 13.96kg =空气/kg 燃料 (3) 热效率η 设离开对流室的烟气温度 s T 比原料的入炉温度高100C o ,则 350100450s T C =+=o 由下面的式子可以得到 , 100L I q q η=--, 取炉墙散热损失 , 1 0.05L L q q Q = =并根据α和s T 查相关表,得烟气出对流室时 带走的热量123% L q Q =, 所以 1(523)%72%η=-+= (4) 燃料的用量 1379175001277/0.7241241.7 Q B kg h Q η= ==?; 第1章加热炉控制系统 加热炉控制系统工程背景及说明 加热炉自动控制(automatic control of reheating furnace),是对加热炉的出口温度、燃烧过程、联锁保护等进行的自动控制。早期加热炉的自动控制仅限控制出口温度,方法是调节燃料进口的流量。现代化大型加热炉自动控制的目标是进一步提高加热炉燃烧效率,减少热量损失。为了保证安全生产,在生产线中增加了安全联锁保护系统。 影响加热炉出口温度的干扰因素很多,炉子的动态响应一般都比较迟缓,因此加热炉温度控制系统多选择串级和前馈控制方案。根据干扰施加点位置的不同,可组成多参数的串级控制。使用气体燃料时,可以采用浮动阀代替串级控制中的副调节器,还可以预先克服燃料气的压力波动对出口温度的影响。这种方案比较简单,在炼油厂中应用广泛。 这种控制的主要目的是在工艺允许的条件下尽量降低过剩空气量,保证加热炉高效率燃烧。简单的控制方案是通过测量烟道气中的含氧量,组成含氧量控制系统,或设计燃料量和空气量比值调节系统,再利用含氧量信号修正比值系数。含氧量控制系统能否正常运行的关键在于检测仪表和执行机构两部分。现代工业中都趋向于用氧化锆测氧技术检测烟道气中的含氧量。应用时需要注意测量点的选择、参比气体流量和锆管温度控制等问题。加热炉燃烧控制系统中的执行机构特性往往都较差,影响系统的稳定性。一般通过引入阻尼滞后或增加非线性环节来改善控制品质。 在加热炉燃烧过程中,若工艺介质流量过低或中断烧嘴火焰熄灭和燃料管道压力过低,都会导致回火事故,而当燃料管道压力过高时又会造成脱火事故。为了防止事故,设计了联锁保护系统防止回火和温度压力选择性控制系统防止脱火。联锁保护系统由压力调节器、温度调节器、流量变送器、火焰检测器、低选器等部分组成。当燃料管道压力高于规定的极限时,压力调节系统通过低选器取代正常工作的温度调节系统,此时出料温度无控制,自行浮动。压力调节系统投入运行保证燃料管道压力不超过规定上限。当管道压力恢复正常时,温度调节系统通过低选器投入正常运行,出料温度重新受到控制。当进料流量和燃料流量低于允许下限或火焰熄灭时,便会发出双位信号,控制电磁阀切断燃料气供给量以防回火。 随着节能技术不断发展,加热炉节能控制系统正日趋完善。以燃烧过程数学模型为依据建立的最佳燃烧过程计算机控制方案已进入实用阶段。例如,按燃烧过程稳态数学模型组成的微机控制系统已开始在炼油厂成功使用。有时利用计算机实现约束控制,使加热炉经常维持在约束条件边界附近工作,以保证最佳燃烧。 1.F RNC-5软件的引进与使用概况 中石化集团公司下属的若干设计院(石化工程公司)从1997年开始引进了多套美国PFR公司的通用加热炉工艺计算软件FRNC-5。此软件在加热炉工艺计算中得到很好的应用,发挥了重大作用。 美国PFR公司全称为PFR工程系统公司(PFR Engineering System,Inc )。公司设在美国洛杉矶,创建于1972年1月,从事热力学系统设计分析和人员培训。该公司的软件产品拥有六十多个用户,遍布六大洲的十五个以上的国家。其中FRNC-5PC软件有二十年以上的使用经验。 本软件可以优化加热炉设计,并可对现有加热炉进行操作分析、加强管理,是一个较为优秀的软件。 2.F RNC-5软件功能与特点 2.1 软件应用范围 本程序可用于炼油、石油化工及热电联合等装置中大多数火焰加热炉及水管锅炉的性能模拟及效率预测。程序采用经过证明了的技术,通过综合迭代,将工艺物流模拟、传热和压力降计算等过程组合在一起。 程序沿物流及烟气流程,逐个管组逐个炉段严格迭代求解,能精确确定加热炉的工艺参数。计算中还指明不利操作状态,如发出炉膛正压、管壁和扩面元件超温、超临界流动以及酸露点腐蚀等警告信息。 程序会算出与显示加热炉的以下工艺参数或不利操作状态: (1)加热炉总热负荷、总热效率,辐射室热负荷 (2)辐射室出口温度(桥墙温度)与烟囱入口处温度 (3)辐射和对流热强度的均值和峰值 (4)辐射段遮蔽段和对流段中所有管组的管壁金属温度和翅片尖端温度的峰值和均值(5)两相流流型及沸腾状态的确定 (6)管内两相流的传热和压降 (7)管外传热和阻力 (8)“阻塞”、“干锅”或“冷端”腐蚀的可能性 2.2 适用的加热炉类型 (1)常减压装置加热炉 (2)铂重整、铂铼重整和强化重整等装置加热炉 (3)重沸炉和过热炉 (4)一氧化碳加热炉和锅炉 (5)脱硫装置原料预热炉 (6)焦化炉和减粘加热炉 (7)润滑油蒸馏和蜡油加热炉 目录 第1章加热炉控制系统工艺分析 (1) 1.1 加热炉的工艺流程简述 (1) 1.2 加热炉控制系统的组成 (2) 第2章加热炉控制系统设计 (3) 2.1 步进梁控制 (3) 2.2 炉温控制 (4) 2.3 紧急停炉保护和连锁 (5) 第3章基于REALINFO的加热炉系统监控程序设计 (7) 3.1加热炉的主控界面 (7) 3.2加热炉的趋势界面 (8) 3.3加热炉的仪表界面 (9) 第4章结论与体会 (10) 参考文献 (11) 第1章加热炉控制系统工艺分析 在炼油化工生产中常见的加热炉是管式加热炉。其形式可分为箱式、立式和圆筒炉三大类。对于加热炉,工艺介质受热升温或同时进行汽化,其温度的高低会直接影响后一工序的操作工况和产品质量。 加热炉是传统设备的一种,同样具有热量传递过程。热量通过金属管壁传给工艺介质,因此他们同样符合导热与对流的基本规律。但加热炉属于火力加热设备,首先由燃料的燃烧产生炙热的火焰和高温的气流,主要通过辐射传热将热量传给管壁,然后由管壁传给工艺介质,工艺介质在辐射室获得的热量约占总符合的70%~80%,而在对流段获得的热量约占热负荷的20%~30%。因此加热炉的传热过程比较复杂,想从理论上获得对象特性是很困难的。 当炉子温度过高时,会使物料在加热炉内分解,甚至造成结焦而烧坏炉管。加热炉的平稳操作可以延长炉管使用寿命。因此,加热炉出口温度必须严加控制。 加热炉的对象特征一般基于定性分析和实验测试获得。从定性角度出发,可以看出其传热过程为:炉膛炽热火焰辐射给炉管,经热传导、对流传热给工艺介质。所以与一般传热对象一样,具有较大的时间常数和纯滞后时间。 特别是炉膛,它具有较大的热容量,故滞后更为显著,因此加热炉属于一种多容量的被控对象。根据若干实验测试,并做了一些简化,可以用一介环节加纯滞后来近似,其时间常熟和纯滞后时间与炉膛容量大小及工艺介质停留时间有关。 炉膛容量大,停留时间长,则时间常数和纯滞后时间大,反之亦然。 1.1 加热炉的工艺流程简述 随着工业自动化水平的迅速提高,工业控制自动化技术正在向智能化、网络化和集成化方向发展,从而反映出当今自动化技术的发展方向。 现加热炉控制系统主要特点: (1)生产能耗大幅度降低。 (2)产量大幅度提高。 (3)生产自动化水平非常高,原加热炉的控制系统大多是单回路仪表和继电逻辑控制系统,传动系统也大多是模拟量控制式的供电装置,现在的加热炉的控制系统都是PLC或DCS系统,而且大多还具有二级过程控制系统和三级生产管理系统。 本系统的工艺流程图如下图: 汽轮机火用分析方法的热力系统计算 前言 在把整个汽轮机装置系统划分成若干个单元的过程中,任何一个单元由于某些因素而引起的微弱变化,都会影响到其它单元。这种引起某单元变化的因素叫做“扰动”。也就是说,某单元局部参量的微小变化(即扰动),会引起整个系统的“反弹”,但是它不会引起系统所有参数的“反弹”。就汽轮机装置系统而言,系统产生的任何变化,都可归结为扰动后本级或邻近级抽汽量的变化,从而引起汽轮机装置系统及各单元的火用损变化。因此,在对电厂热力系统进行经济性分析时,仅计算出某一工况下各单元火用损失分布还是不够的,还应计算出当某局部参量变化时整个热力系统火用效率变化情况。 1、火用分析方法 与热力系统的能量分析法一样,可以把热力系统中的回热加热器分为疏水放流式和汇集式两类(参见图1和图2),并把热力系统的参数整理为3类:其一是蒸汽在加热器中的放热火用,用q’表示;其二是疏水在加热器中的放热火用,用y 表示;其三是给水在加热器中的火用升,以r’表示。其计算方法与能量分析法类似。 对疏水式加热器: 对疏水汇集式加热器: 式中,e f、e dj、e sj分别为j级抽汽比火用、加热器疏水比火用和加热器出口水比火用。1.1 抽汽有效火用降的引入 对于抽汽回热系统,某级回热抽汽减少或某小流量进入某加热器“排挤”抽汽量,诸如此类原因使某级加热器抽汽产生变化(一般是抽汽量减少),如果认为此变化很小而不致引起加热器及热力系统参数变化,那么便可基于等效焓降理论引入放热火用效率来求取某段抽汽量变化时对整个系统火用效率的影响。 为便于分析,定义抽汽的有效火用降,在抽汽减少的情况下表示1kg排挤抽汽做功的增加值;在抽汽量增加时,则表示做功的减少值;用符号Ej来表示。当从靠近凝汽器侧开始,研究各级抽汽有效火用降时,Ej的计算是从排挤l kg抽汽的火用降(e j-e c)ηej中减去某些固定 2 10 步进式加热炉设计计算 2.1 热工计算原始数据 (1) 炉子生产率:p=245t/h (2) 被加热金属: 1) 种类:优质碳素结构钢(20#钢) 2) 尺寸:250 >2200 >3600 (mm )(板坯) 3) 金属开始加热(入炉)温度:t 始=20r 4) 金属加热终了(出炉)表面温度:t 终=1200C 5) 金属加热终了(出炉)断面温差:t < 15C (3) 燃料 1) 种类:焦炉煤气 2) 焦炉煤气低发热值:Q 低温=17000kJ/标m 3 3) 煤气不预热:t 煤气=20 °C 表1-1焦炉煤气干成分(%) ⑷ 出炉膛烟气温度:t 废膛=800C ⑸空气预热温度(烧嘴前):t 空 =350 C 2.2燃烧计算 2.2.3 计算理论空气需要量L c 1 1 m L o 4.76 —CO -H 2 (n —)C n H m 2 2 4 把表2-1中焦炉煤气湿成分代入 1 1 3 3 3 -H 2S O 2 2 2 3 3) 10 (m /m ) L0 4.76 8.7939 険5741 2 24?8184 3 2?8336。碍 2 10 =4.3045m3/m3 V n V CO 2 V H 2O V N 2 V O 2 224计算实际空气需要量Ln 查《燃料及燃烧》,取n=1.1代入 L n nL o 1.1 4.3045 4.7317 标 m 3/标 m 3 实际湿空气消耗量 L n 湿(1 0.00124g) nL o =(1 0.00124 18.9) 4.7317 =6.0999 标 m 3/标 m 3 2.2.5计算燃烧产物成分及生成量 V c°2 (CO nC n H m CO 2) 100 1 79 1.2702 丄 79 4.7317 100 100 =3.7507 标m 3/标m 3 V 02 (L n L 0)标 m /标 m 100 21 4.7317 4.3045 100 =0.0897 标 m 3/标 m 3 燃烧产物生成总量 (56.5741 2 1 24.8184 2 2.8336 2.2899) 100 0.00124 18.9 4.7317 标m 3/标m 3 标m 3/标m 3 (24.8184 8.7939 2 2.8336 3.0290) 1 100 =0.4231 标 m 3/标 m 3 V H 2O (H 2 m C H n m 2 H 2S H 2O) 1 100 0.00124gL n 标 m 3/标 m 3 V N 2 N 2 100 100 Ln 标说标 m =1.2526 第一节25MW汽轮机热力计算 一、设计基本参数选择 1. 汽轮机类型 机组型号: N25-3.5/435。 机组形式:单压、单缸单轴凝器式汽轮机。 2. 基本参数 额定功率:P el=25MW; 新蒸汽压力P0=3.5MPa,新蒸汽温度t0=435℃; 凝汽器压力P c=5.1kPa; 汽轮机转速n=3000r/min。 3. 其他参数 给水泵出口压力P fp=6.3MPa; 凝结水泵出口压力P cp=1.2MPa; 机械效率ηm=0.99 发电机效率ηg=0.965 加热器效率ηh=0.98 4. 相对内效率的估计 根据已有同类机组相关运行数据选择汽轮机的相对内效率,ηri=83% 5. 损失的估算 主汽阀和调节汽阀节流压力损失:ΔP0=0.05P0=0.175Mpa。 排气阻力损失:ΔP c=0.04P c=0.000204MPa=0.204kPa。 二、汽轮机热力过程线的拟定 (1)在h-s图上,根据新蒸汽压力P0=3.5MPa和新蒸汽温度t0=435℃,可确定汽轮机进气状态点0(主汽阀前),并查得该点的比焓值h0=3303.61kJ/kg,比熵s0=6.9593kJ/kg (kg·℃),比体积v0= 0.0897758m3/kg。 (2)在h-s图上,根据初压P0=3.5MPa及主汽阀和调节汽阀节流压力损失ΔP0=0.175Mpa 可以确定调节级前压力p0’= P0-ΔP0=3.325MPa,然后根据p0’与h0的交点可以确定调节级级前状态点1,并查得该点的温度t’0=433.88℃,比熵s’0= 6.9820kJ/kg(kg·℃),比体积v’0= 0.0945239m3/kg。 (3)在h-s图上,根据凝汽器压力P c=0.0051MPa和排气阻力损失ΔP c=0.000204MPa,可以确定排气压力p c’=P c+ΔP c=0.005304MPa。 (4)在h-s图上,根据凝汽器压力P c=0.0051MPa和s0=6.9593kJ/kg(kg·℃)可以确定气缸理想出口状态点2t,并查得该点比焓值h ct=2124.02kJ/kg,温度t ct=33.23℃,比体积v ct=22.6694183 m3/kg,干度x ct=0.8194。由此可以的带汽轮机理想比焓降 1179.59kJ/kg,进而可以确定汽轮机实际比焓降 步进式加热炉设计计算 2.1 热工计算原始数据 (1)炉子生产率:p=245t/h (2)被加热金属: 1)种类:优质碳素结构钢(20#钢) 2)尺寸:250×2200×3600 (mm)(板坯) 3)金属开始加热(入炉)温度:t 始=20℃ 4)金属加热终了(出炉)表面温度:t 终=1200℃ 5)金属加热终了(出炉)断面温差:t ≤15℃ (3)燃料 1)种类:焦炉煤气 2)焦炉煤气低发热值:Q 低温=17000kJ/标m 3 3)煤气不预热:t 煤气=20℃ 表1-1 焦炉煤气干成分(%) 废膛(5)空气预热温度(烧嘴前):t 空=350℃ 2.2 燃烧计算 2.2.3 计算理论空气需要量L 0 )3322220/(1023)4(212176.4m m O S H H C m n H CO L m n -??? ? ???-++++=∑ 把表2-1中焦炉煤气湿成分代入 2 0103909.08336.238184.2425741.56217939.82176.4-??? ????-?+?+?+?=L =33/3045.4m m 2.2.4 计算实际空气需要量Ln 查《燃料及燃烧》,取n=1.1代入 7317.43045.41.10=?==nL L n 标m 3/标m 3 实际湿空气消耗量 0)00124.01nL g L n ?+=(湿 =7317.4)9.1800124.01(??+ =6.0999 标m 3/标m 3 2.2.5 计算燃烧产物成分及生成量 100 1 )(22? ++=∑CO H nC CO V m n CO 标m 3/标m 3 100 1)0290.38336.227939.88184.24(?+?++= =0.4231 标m 3/标m 3 n m n O H gL O H S H H C m H V 00124.0100 1 )2(2222+? +++=∑ 标m 3/标m 3 7317 .49.1800124.01001)2899.28336.228184.2425741.56(??+?+?+?+= = 1.2526 标m 3/标m 3 n N L N V 100 79100122+? = 标m 3/标m 3 7317.4100 7910012702.1?+? = =3.7507 标m 3/标m 3 )(100 21 02L L V n O -= 标m 3/标m 3 ()3045.47317.4100 21 -= =0.0897标m 3/标m 3 燃烧产物生成总量 2222O N O H CO n V V V V V +++= 目录 第1章绘制控制工艺流程图 (1) 1.1工艺生产过程简介 (1) 1.2加热炉的基本控制 (1) 1.3加热炉的单回路控制方案 (4) 第2章节流装置的计算方法和计算机辅助设计计算 (6) 2.1GB/T2624-93概述 (6) 2.2计算实例 (6) 第3章调节阀口径计算 (11) 3.1调节阀的选型 (11) 3.2调节阀口径计算 (11) 3.3计算实例 (12) 第4章结论与体会 (14) 参考文献 (15) 附录 (16) 第1章绘制控制工艺流程图 1.1工艺生产过程简介 在炼油化工生产中常见的加热炉是管式加热炉。其形式可分为箱式、立式和圆筒炉三大类。对于加热炉,工艺介质受热升温或同时进行汽化,其温度的高低会直接影响后一工序的操作工况和产品质量。当炉子温度过高时,会使物料在加热炉内分解,甚至造成结焦而烧坏炉管。加热炉的平稳操作可以延长炉管使用寿命。因此,加热炉出口温度必须严加控制。 加热炉是传统设备的一种,同样具有热量传递过程。热量通过金属管壁传给工艺介质,因此它们同样符合导热与对流传热的基本规律。但加热炉属于火力加热设备,首先由燃料的燃烧产生炽热的火焰和高温的气流,主要通过辐射传热将热量传给管壁,然后由管壁传给工艺介质,工艺介质在辐射室获得的热量约占总热负荷的70%~80%,而在对流段获得的热量约占热负荷的20%~30%。因此加热炉的传热过程比较复杂,想从理论上获取对象特性是很困难的。 加热炉的对象特征一般基于定性分析和实验测试获得。从定性角度出发,可以看出其传热过程为:炉膛炽热火焰辐射给炉管,经热传导、对流传热给工艺介质。所以与一般传热对象一样,具有较大的时间常数和纯滞后时间。特别是炉膛,它具有较大的热容量,故滞后更为显著,因此加热炉属于一种多容量的被控对象。根据若干实验测试,并做了一些简化,可以用一介环节加纯滞后来近似,其时间常熟和纯滞后时间与炉膛容量大小及工艺介质停留时间有关。炉膛容量大,停留时间长,则时间常数和纯滞后时间大,反之亦然。 1.2加热炉的基本控制 加热炉进料一般分为几个支路。常规的控制方法是:在各支路上安装各自的流量变送器和控制阀,而用炉出口总管温度来调节炉用燃料量。这样的调节方法根本没有考虑支管温度均衡的控制,支管温度均衡的控制由操作工凭经验根据分支温差来调节分支流量差。这种人为操作显然无法实现稳定的均衡控制,往往是各支管流量较均衡,而分支温度有相当大的差异,某一炉管因局部过热而结焦的可能性很大。为了改善和克服这种情况,需要采用支路均衡控制方法。近年来出现的差动式平衡控制、解藕控制以及多变量预测控制等方法能够收取一定的效果。其中差动式方法不仅效果不错,而且实现简单,操作简便,对于长期运行有一定的优势。另外,针对系统的非线性、强耦合特性,模糊控制等智能控制方法也能实现较好的控制。 加热炉出口总管温度是加热炉环节最为重要的参数,出口温度的稳定对于后续工艺的生产稳定、操作平稳甚至提高收率至关重要。最简单的控制方法就是采用单回路的反馈控制。单回路反馈控制简单实用,有它的使用价值。但该方法没有考虑燃料量变化的影响,所以出口温度不容易稳定,在一定程度上也会造成燃料的浪费。在简单反馈控制方案的基 600MW汽轮机原则性热力系统设计计算 目录 毕业设计............... 错误!未定义书签。内容摘要 (3) 1.本设计得内容有以下几方面: (3) 2.关键词 (3) 一.热力系统 (4) 二.实际机组回热原则性热力系统 (4) 三.汽轮机原则性热力系统 (4) 1.计算目的及基本公式 (5) 1.1计算目的 (5) 1.2计算的基本方式 (6) 2.计算方法和步骤 (7) 3.设计内容 (7) 3.1整理原始资料 (9) 3.2计算回热抽气系数与凝气系数 (9) 回热循环 (10) 3.2.1混合式加热器及其系统的特点 (10) 3.2.2表面式加热器的特点: (11) 3.2.3表面式加热器的端差θ及热经济性 (11) 3.2.4抽气管道压降Δp j及热经济性 (12) 3.2.5蒸汽冷却器及其热经济性 (12) 3.2.6表面式加热器的疏水方式及热经济性 (13) 3.2.7设置疏水冷却段的意义及热经济性指标 (14) 3.2.8除氧器 (18) 3.2.9除氧器的运行及其热经济性分析 (19) 3.2.10除氧器的汽源连接方式及其热经济性 (19) 3.3新汽量D0计算及功率校核 (23) 3.4热经济性的指标计算 (26) 3.5各汽水流量绝对值计算 (27) 致谢 (32) 参考文献 (33) 600MW汽轮机原则性热力系统设计计算 内容摘要 1.本设计得内容有以下几方面: 1)简述热力系统的相关概念; 2)回热循环的的有关内容(其中涉及到混合式加热器、表面式加热器的特点,并对其具有代表性的加热器作以细致描述。表面式加热器的端差、设置疏水冷却段、蒸汽冷却段、疏水方式及热经济性、除氧器的运行及其热经济性分析、除氧器的汽源连接方式及其热经济性) 3)原则性热力系统的一般计算方法 2.关键词 除氧器、高压加热器、低压加热器 循环流化床锅炉热力计算 循环流化床锅炉热效率计算 我公司75t/h循环流化床锅炉,型号为UG75/3.82-M35,它的热效率计算为: 三、锅炉在稳定状态下,相对于1Kg燃煤的热平衡方程式如下: Q r=Q1+Q2+Q3+Q4+Q5+Q6 (KJ/Kg),相应的百分比热平衡方程式为: 100%=q1+q2+q3+q4+q5+q6 (%) 其中 1、Q r是伴随1Kg燃煤输入锅炉的总热量,KJ/Kg。 Q r= Q ar+h rm+h rs+Q wl 式中Q ar--燃煤的低位发热量,KJ/Kg;是输入锅炉中热量的主要来源。Q ar=12127 KJ/KgJ h rm--燃煤的物理显热量,KJ/Kg;燃煤温度一般低于30℃,这一项热量相对较小。 h rs--相对于1Kg燃煤的入炉石灰石的物理显热量,KJ/Kg;这一项热量相对更小。 Q wl--伴随1Kg燃煤输入锅炉的空气在炉外被加热的热量,KJ/Kg;如果一、二次风入口暖风器未投入,这一部分热量也可不计算在内。 2、Q1是锅炉的有效利用热量,KJ/Kg;在反平衡热效率计算中,是利用其它热损失来求出它的。 3、Q4是机械不完全燃烧热损失量,KJ/Kg。 Q4= Q cc(M hz C hz+M fh C fh+M dh C dh)/M coal 式中Q cc--灰渣中残余碳的发热量,为622 KJ/Kg。 M hz、M fh、M dh--分别为每小时锅炉冷渣器的排渣量、飞灰量和底灰量,分别为15、7、2t/h。 C hz、C fh、C dh--分别每小时锅炉冷渣器的排渣、飞灰和底灰中残余碳含量占冷渣器的排渣、飞灰和底灰量的质量百分比,按2.4%左右。 M coal--锅炉每小时的入炉煤量,为20.125t/h。 所以Q4= Q cc(M hz C hz+M fh C fh+M dh C dh)/M coal =622(15*2.4+7*2+3.5*2.4)/20.125 =1694 KJ/Kg q4= 100Q4/Q r(%) =100*1694/12127=13.9% 4、Q2是排烟热损失量,KJ/Kg。 Q2=(H py-H lk)(1-q4/100) 式中H py--排烟焓值,由排烟温度θpy (135℃)、排烟处的过量空气系数αpy(αpy =21.0/(21.0 - O2py))=1.24和排烟容积比热容C py=1.33 (KJ/(Nm3℃))计算得出,KJ/Kg。 H py=αpy (V gy C gy+ V H2O C H2O)θpy+I fh 由于I fh比较小可忽略不计 =1.24*( 5.05*1.33+0.615*1.51) *135 =1229 加热炉的温度自动控制系统 一.系统设计的目的及意义 加热炉被广泛应用于工业生产和科学研究中。由于这类对象使用方便,可以通过调节输出功率来控制温度,进而得到较好的控制性能,故在冶金、机械、化工等领域中得到了广泛的应用。 在一些工业过程控制中,工业加热炉是关键部件,炉温控制精度及其工作稳定性已成为产品质量的决定性因素。对于工业控制过程,PID 调节器具有原理简单、使用方便、稳定可靠、无静差等优点,因此在控制理论和技术飞跃发展的今天,它在工业控制领域仍具有强大的生命力。 在产品的工艺加工过程中,温度有时对产品质量的影响很大,温度检测和控制是十分重要的,这就需要对加热介质的温度进行连续的测量和控制。 在冶金工业中,加热炉内的温度控制直接关系到所冶炼金属的产品质量的好坏,温度控制不好,将给企业带来不可弥补的损失。为此,可靠的温度的监控在工业中是十分必要的。 二.控制要求 加热炉设备的控制任务是根据生产负荷的需要,供应热量,同时要使加热炉在安全、经济的条件下运行。按照这些控制要求,加热炉设备将有主要的控制要求: 加热炉燃烧系统的控制方案要满足燃烧所产生的热量,适应物料负荷的需要,保证燃烧的经济型和加热炉的安全运行,使物料温度与燃料流量相适应,保持物料出口温度在一定范围内。 三.系统介绍 本加热炉温度控制系统采用单回路控制方案,即可实现控制要求。在运行过程中,当物料出口温度受干扰影响改变时,温度检测元件测得的模拟信号也会发生对应的改变,该信号经过变送器转换后变成调节器可分析的数字信号,进入调节器, 将变动后的信号再与给定相比较,得出对应偏差信号,调节器将给定温度与测得的温度进行比较得出偏差值,然后经PID 算法给出输出信号,执行器接收调节器发来的信号后,根据信号调节阀门开度,进而控制燃料流量,改变物料出口温度,实现对物料出口温度的控制。不断重复以上过程,直至物料出口温度接近给定,处于允许范围内,且达到稳定。由此消除干扰的影响,实现温度的控制要求。 四.具体控制系统设计 1 测温元件 本控制系统的测温元件采用Pt100热电阻,工业用铂电阻作为温度测量变送器,通常用来和显示、记录、调节仪表配套,直接测量各种生产过程中从0 ~ 500℃ 范围内的液体、蒸汽和气体介质以及固体等表面温度。 2 调节控制器件 DDZ-III 型PID 调节器TDM-400性能指标如下表所示: 表 DDZ-III 型PID 调节器性能指标 被控量 给定量冶金加热炉设计工作手册.1
加热炉燃烧控制系统设计与仿真
600MW凝汽式汽轮机组的热力计算
加热炉热工检测方案
600MW汽轮机汽水热力计算
(完整版)加热炉功率计算.doc
(完整版)加热炉计算
加热炉控制系课程设计
1.加热炉工艺计算软件FRNC5使用入门剖析
加热炉控制系统要点
汽轮机火用分析方法的热力系统计算
步进式加热炉设计计算模板
N25-3.5435汽轮机通流部分热力计算
步进式加热炉设计计算模板
加热炉控制系统
汽轮机600MW汽轮机原则性热力系统设计计算
循环流化床锅炉热力计算
加热炉的温度自动控制系统