钢结构表面检测工艺规程
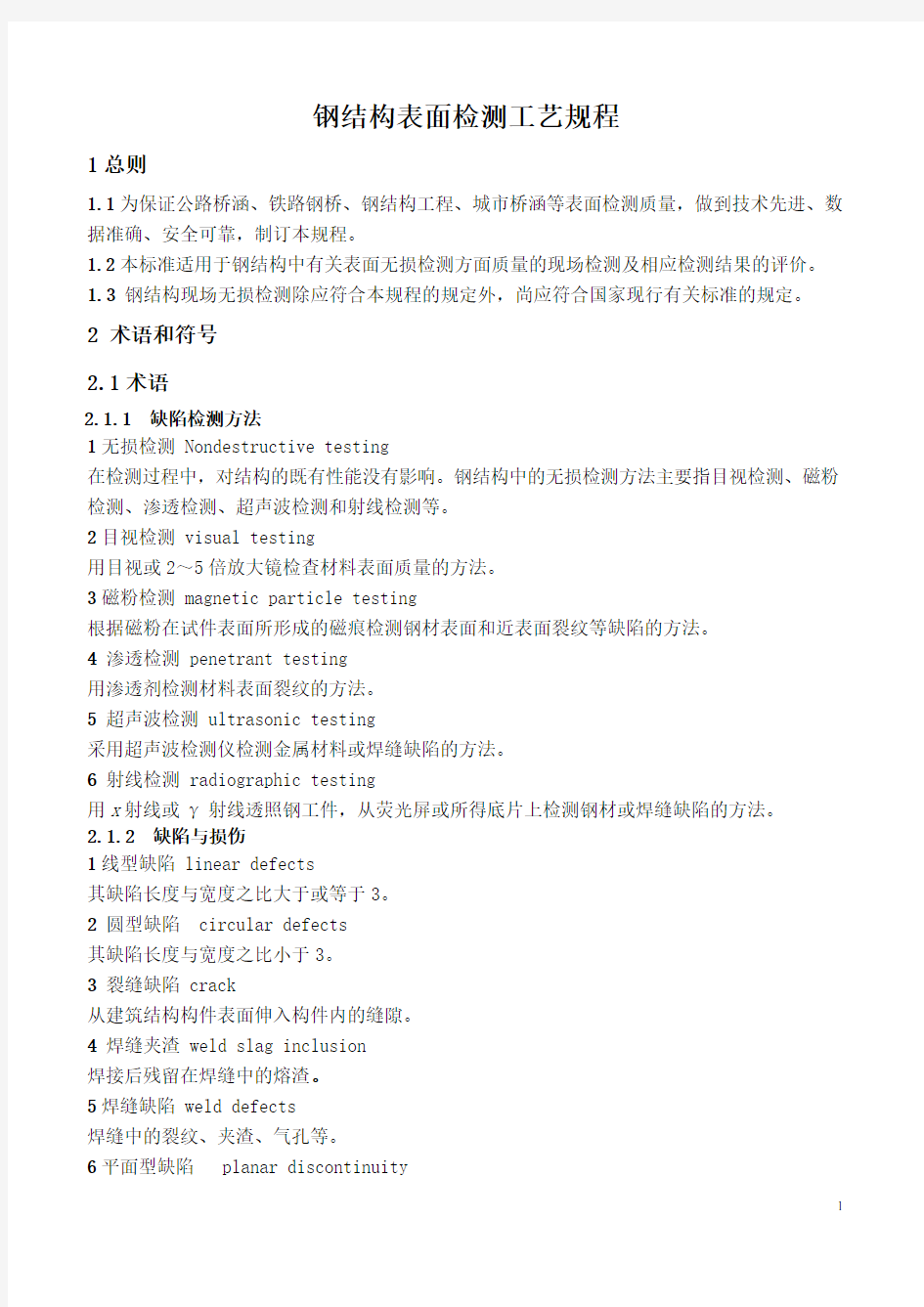

钢结构表面检测工艺规程
1总则
1.1为保证公路桥涵、铁路钢桥、钢结构工程、城市桥涵等表面检测质量,做到技术先进、数据准确、安全可靠,制订本规程。
1.2本标准适用于钢结构中有关表面无损检测方面质量的现场检测及相应检测结果的评价。
1.3 钢结构现场无损检测除应符合本规程的规定外,尚应符合国家现行有关标准的规定。
2 术语和符号
2.1术语
2.1.1 缺陷检测方法
1无损检测 Nondestructive testing
在检测过程中,对结构的既有性能没有影响。钢结构中的无损检测方法主要指目视检测、磁粉检测、渗透检测、超声波检测和射线检测等。
2目视检测 visual testing
用目视或2~5倍放大镜检查材料表面质量的方法。
3磁粉检测 magnetic particle testing
根据磁粉在试件表面所形成的磁痕检测钢材表面和近表面裂纹等缺陷的方法。
4 渗透检测 penetrant testing
用渗透剂检测材料表面裂纹的方法。
5超声波检测 ultrasonic testing
采用超声波检测仪检测金属材料或焊缝缺陷的方法。
6 射线检测 radiographic testing
用x射线或γ射线透照钢工件,从荧光屏或所得底片上检测钢材或焊缝缺陷的方法。
2.1.2 缺陷与损伤
1线型缺陷 linear defects
其缺陷长度与宽度之比大于或等于3。
2 圆型缺陷 circular defects
其缺陷长度与宽度之比小于3。
3 裂缝缺陷 crack
从建筑结构构件表面伸入构件内的缝隙。
4 焊缝夹渣 weld slag inclusion
焊接后残留在焊缝中的熔渣。
5焊缝缺陷 weld defects
焊缝中的裂纹、夹渣、气孔等。
6平面型缺陷 planar discontinuity
用某方法检测一个缺陷,若只能测出它的两维尺寸,则称为平面型缺陷。属于此类缺陷的有裂纹、未熔合等危险性缺陷。
7 体积型缺陷 volume discontinuity
用某方法检测一个缺陷,若能测出它的三维尺寸,则称为体积型缺陷。属于此类缺陷的有气孔、夹渣、夹杂等。
2.2.1 引用标准名录
《建筑结构检测技术标准》GB/T 50344
《钢结构工程施工质量验收规范》GB 50205
3基本规定
3.1钢结构检测的分类
3.1.1 钢结构的检测可分为在建和既有钢结构质量的检测。
3.1.2 当遇到下列情况之一时,应按在建钢结构的要求进行检测:
1 在钢结构施工质量的验收过程中需了解施工质量时;
2 对施工质量有怀疑或争议,需要通过检测进一步分析结构的可靠性;
3 发生工程事故,需要通过检测分析事故的原因及对结构可靠性的影响。
3.1.3 当遇到下列情况之一时,应按既有钢结构的要求进行检测:
1 钢结构安全鉴定;
2 钢结构抗震鉴定;
3 建筑大修前的可靠性鉴定;
4 建筑改变用途、改造、加层或扩建前的鉴定;
5 受到灾害、环境侵蚀等影响建筑的鉴定;
6 对既有钢结构的工程质量有怀疑或争议。
3.1.4 钢结构的现场检测应为钢结构质量的评定或钢结构性能的鉴定提供真实、可靠、有效的检测数据和检测结论。
3.2 检测工作程序与基本要求
3.2.1 钢结构检测工作的程序,宜按图3.2.1的框图进行。
图3.2.1 检测工作程序框图
3.2.2 现场和有关资料的调查,宜包括下列工作内容:
1收集被检测结构的设计图纸、设计变更、施工记录、施工验收和工程地质勘察等资料;
2调查被检测钢结构现状,环境条件,使用期间的加固与维修情况和用途与荷载等变更情况;3向有关人员进行调查;
4进一步明确委托方的检测目的和具体要求,并了解是否已进行过检测。
3.2.3现场检测应根据检测项目情况,制定相应的检测方案。检测方案宜包括下列主要内容:1概况,主要包括结构型式、建筑面积、总层数、设计、施工及监理单位,建造年代等;
2检测目的或委托方的检测要求;
3检测依据,主要包括检测所依据的标准及有关的技术资料等;
4检测项目和选用的检测方法以及检测的数量;
5检测人员和仪器设备情况;
6检测工作进度计划;
7所需要的配合工作;
8检测中的安全措施;
9检测中的环保措施。
3.2.4检测的原始记录,应记录在专用记录纸上,数据准确、字迹清晰,信息完整,不得追记、涂改,如有笔误,应进行杠改。当采用自动记录时,应符合有关要求。原始记录必须由检测及校核人员签字。
3.2.5当发现检测数据数量不足或检测数据出现异常情况时,应进行补充检测。
3.3 无损检测方法及选用原则
3.3.1钢结构中的无损检测方法主要指目视检测、磁粉检测、渗透检测、超声波检测和射线检测。
3.3.2 钢结构的检测,应根据检测项目、检测目的、建筑结构状况和现场条件选择适宜的检测方法。可按照表3.3.2选择无损检测方法。
表3.3.2 无损检测方法的选用
3.3.3 钢结构中的磁粉检测、渗透检测、超声波检测和射线检测,应经目视检测,外观检查合格后进行。
3.3.4 在对钢结构焊缝进行无损检测时,钢结构一级、二级焊缝质量等级与缺陷分级应符合表3.3.4的规定。
表3.3.4 钢结构一级、二级焊缝质量等级与缺陷分级
3.4 抽样比例
3.4.1当为下列情况时,检测对象可以是单个构件或部分构件;但检测结论不得扩大到未
检测的构件或范围。
1委托方指定检测对象或范围;
2因环境侵蚀或火灾、爆炸、高温以及人为因素等造成部分构件损伤时。
3.4.2 在建钢结构检验批的质量检测应按照《钢结构工程施工质量验收规范》GB50205规定的抽样比例进行。
3.4.3 既有钢结构按检测批检测时,其最小样本容量不应小于表3.4.3的限定值。
3.5 检测报告
3.5.1检测报告应做出所检测的项目是否符合设计文件要求或相应验收规范的规定。既有钢结构性能的检测报告应给出所检项目的检测结论,并能为钢结构的鉴定提供可靠的依据。
3.5.2检测报告应结论准确、用词规范、文字简练,对于当事方容易混淆的术语和概念可书面予以解释。
3.5.3 检测报告应包括以下内容:
1委托单位名称;
2建筑工程概况,包括工程名称、结构类型、规模、施工日期及现状等;
3建设单位、设计单位、施工单位及监理单位名称;
4检测原因、检测目的,以往检测情况概述;
5检测项目、检测方法及依据的标准;
6抽样方案及数量;
7检测日期,报告完成日期;
8检测项目的主要分类检测数据和汇总结果;检测结论;
9主检、审核和批准人员的签名。
3.6 检测设备和检测人员
3.6.1 钢结构检测所用的仪器、设备和量具有产品合格证、计量检定机构的有效检定(校准)证书或自校证书并处于正常状态。仪器设备的精度应满足检测项目的要求。
3.6.2 检测人员必须经过培训取得上岗资格,从事钢结构除目视检测外的无损检测人员应有相应的检测资格证书。
3.6.3 钢结构无损检测人员按技术等级分为高级(Ⅲ级)、中级(Ⅱ级)、初级(Ⅰ级)。取得不同无损检测方法的各技术等级人员,只能从事与该等级相对应的无损检测工作,并负相应的技术责任。
3.6.4 从事钢结构无损检测的人员,视力必须满足下列要求:
1每年应检查一次视力,其近距离视力(裸视力或校正视力)不得低于1.0。
2 从事磁粉、渗透检测的人员,不得有色盲、色弱。
3 从事射线检测的人员,应能辨别距离400mm远的一组高为0.5mm、间距为0.5mm的印刷字母。
3.6.5 现场检测工作应由两名或两名以上检测人员承担。
4 外观质量的目视检测
4.1 一般规定
4.1.1 本章适用于钢结构现场外观质量的目视检测。
4.1.2 直接目视检测时,眼睛与被测工件表面的距离不得大于610mm,视线与被测工件表面所成的视角不得小于30o。
4.1.3 被测工件表面应有足够的照明,一般情况下光照度不得低于160lx;对细小缺陷进行鉴别时,光照度不得低于540lx。
4.2 辅助工具
4.2.1 对细小缺陷进行鉴别时,可使用2~5倍的放大镜。
4.3 检测内容
4.3.1 检测人员在目视检测前,应了解工程施工图纸和有关标准,熟悉工艺规程,提出目视检测的内容和要求。
4.3.2 钢材表面的外观质量的检测可分为是否有夹层、裂纹、非金属夹杂和明显的偏析等项目。
4.3.3 钢结构焊前目视检测的内容包括焊缝剖口形式、剖口尺寸、组装间隙;焊后目视检测的内容包括焊缝长度、焊缝外观质量。
4.3.4 对于焊接外观质量的目视检测,应在焊缝清理完毕后进行,焊缝及焊缝附近区域不得有焊渣及飞溅物。
4.4 检测结果的评价
4.4.1 钢材表面的外观质量应符合国家现行有关标准的规定,表面不得有裂纹、折叠,钢材端边或断口处不应有分层、夹渣等缺陷。
4.4.2 当钢材的表面有锈蚀、麻点或划伤等缺陷时,其深度不得大于该钢材厚度负偏差值的1/2。
4.4.3 焊缝剖口形式、剖口尺寸、组装间隙等应符合焊接工艺规程和相关技术标准的要求。4.4.4 焊缝表面不得有裂纹、焊瘤等缺陷。一级焊缝不允许有外观质量缺陷,二、三级焊缝外观质量应符合《钢结构工程施工质量验收规范》GB50205中附录A的要求。
5表面质量的磁粉检测
5.1 一般规定
5.1.1 本章适用于铁磁性材料熔焊焊缝表面或近表面裂纹的检测。
5.1.2 钢结构原材料的表面或近表面裂纹,可参照本章的基本原则进行检测。
5.2设备与器材的技术要求
5.2.1 磁粉探伤装置应适合试件的形状、尺寸、表面状态,并满足对缺陷的检测要求。 5.2.2 磁轭法检验装置,在极间距离为75mm ~150mm 时,交流电磁铁提升力应大于44N ,直流电磁铁提升力应大于177N 。
5.2.3 交叉磁轭检验装置,激励磁势不低于1300AT×2,提升力应大于88N ,四个磁极端面与探伤面之间的间隙不宜超过1.5mm ,跨越宽度不宜大于100mm 。
5.2.4 管子、轴类对接和其它特殊试件焊缝可采用线圈法、平行电缆法等其它装置。 5.2.5 铸钢件可采用触头法通过支杆直接通电,触头间距宜为75mm ~200mm 。
5.2.6 磁粉探伤仪的其它装置应符合《无损检测 磁粉检测》GB/T15822所规定的技术要求。 5.2.7 干法中的磁粉施加装置应有足够的气流使干燥的磁粉呈均匀分散地喷落到试件上。 5.2.8 湿法中的磁悬液施加装置应能均匀地喷洒磁悬液到试件上。
5.2.9 在配制磁悬液时,应首先把磁粉或磁膏用少量载液调成均匀状,然后在连续搅拌中缓慢加入所需载液,使磁粉均匀弥散在载液中,直至磁粉和载液之间达到规定比例。常用的油剂为无味煤油、变压器油、煤油和变压器油的混合液,常用的水剂为含有添加剂的水。
5.2.10 磁悬液中的磁粉浓度一般非荧光磁粉为10g/L ~25g/L ,荧光磁粉为1g/L ~2g/L 。磁悬液的配置及检验可按《无损检测 磁粉检测第二部分:检测介质》GB/T15822.2的方法进行。 5.2.11 用荧光磁粉或荧光磁悬液探伤时,应采用黑光灯照射装置,照射距离试件表面在380mm 时测定紫外线辐照度应大于8μW/mm 2。
5.2.12 灵敏度试片用于检查磁粉探伤装置、磁粉或磁悬液的综合性能以及用于检定被检区域内磁场的分布规律。
5.2.13 A 型灵敏度试片中有圆形和十字形人工槽;几何尺寸如图5.2.13。
10
20
图5.2.13 A型灵敏度试片
20
5.2.14 使用时,应将刻有人工槽的一侧与被检试件表面紧贴,可用胶纸在灵敏度试片边沿粘贴,不可贴没人工槽。
5.2.15 在试片上看到与人工刻槽相对应的磁痕清晰显示不代表实际能检测缺陷的大小。 5.2.16 A1型灵敏度试片是用100μm 厚的软磁材料制成,型号有1# ,2# ,3# 三种,其分子表示人工槽深度(μm ),分母表示试片厚度(μm )。
5.2.17 当使用A1型灵敏度试片有困难时,可用C 型灵敏度试片(直线刻槽试片)来代替。
5.2.18 C 型灵敏度试片其材质和A 型灵敏度试片相同,其试片厚度为50μm ,人工槽深度为8μm ,几何尺寸如图5.2.18。
人工槽
10
5
5550
55图5.2.18 C型灵敏度试片
55555分割线
5.3 检测步骤
5.3.1 磁粉检测包括预先准备、磁化、施加磁粉、磁痕观察与记录、后处理等步骤。 5.3.2 预先准备应符合下列要求:
1 对试件探伤面应进行处理,处理范围应由焊缝向母材方向延伸20mm 。
2 清除探伤范围内试件上的附着物,如油漆、油脂、涂料、焊接飞浅、氧化皮等,以免妨碍磁粉附着在缺陷上。
3 用干磁粉时,试件表面应干燥。
4 用磁悬液时,应根据试件表面的状况和试件使用要求,确定采用油剂载液还是水剂载液。
5 根据现场条件确定用荧光还是非荧光磁粉。
6 根据被测试件的形状,尺寸,缺陷性质来选定磁化方法。 5.3.3 磁化及磁粉施加应符合下列要求:
1 磁化时磁场方向应尽量与探测的缺陷方向垂直,与探伤面平行。
2 当不知缺陷方向或多个方向的缺陷时,应采用旋转磁场或采用两次不同方向的磁化。 采用两次不同方向的磁化时,两次磁化方向之间应垂直。
3 检测时,应先放置灵敏度试片在试件表面检验磁场强度和方向以及操作方法是否正确。
4 用磁轭检测时,应有覆盖区,磁轭每次移动的覆盖部分应在10mm ~20mm 之间。
5 用交叉磁轭装置检测时,四个磁极都必须与被检部位表面保持良好接触,在探伤面上的行走速度要力求均匀,移动速度一般不大于2m/min 。
6 用触头法时,每次磁化的长度范围75mm ~200mm ,检测时应保持触头端干净,触头与被检表面接触应良好,电极下宜采用衬垫,避免触头烧灼损坏被检表面。
7 探伤装置在被检部位放稳后才能接通电源,要移去时应先断开电源。
8 施加磁粉时,应使磁粉能均匀地分布在探伤范围的探伤面上,使之吸附在缺陷部位。 9 当探测试件表面粗糙时,宜采用干法喷洒。喷洒时必须确认试件表面干燥。
10 采用湿法时,可先喷洒一遍磁悬液使被测部位表面湿润,在磁化时再次喷洒磁悬液。 磁悬液一般应喷洒在行进方向的前方,磁化需一直持续到磁粉施加完成为止,形成的
磁痕不能被流动的液体所破坏。
5.3.4 磁痕观察与记录应符合下列要求:
1 磁痕的观察应在磁粉施加形成磁痕后立即进行。
2 非荧光磁粉的磁痕可在光线明亮的地方,用自然日光或灯光进行观察(亮度应大于
500lx)。
3 荧光磁粉的磁痕可在暗处(亮度小于20lx)用紫外线灯进行观察。
4 在观察时必须对磁痕进行分析判断,区分缺陷磁痕和非缺陷磁痕,当无法确定时,可采
用其它探伤方法(如渗透法等)进行验证。
5 磁痕的记录可采用照相,绘制草图或用透明胶带把磁痕粘下来等。
5.3.5 后处理应符合下列要求:
1 探伤完成后,根据需要应对被测试件进行退磁。
2 被测试件因剩磁会影响使用性能时,必须进行退磁。
3 对被测部位表面进行清理工作,除去磁粉,清洗干净,必要时应进行防锈处理。
5.4 检测结果的评价
5.4.1 磁粉探伤显示的缺陷磁痕可分为线型磁痕和圆型磁痕。
5.4.2 根据缺陷磁痕类型和长度对检测到的缺陷进行分级,缺陷磁痕分级应符合表5.4.2的规定。
表 5.4.2 缺陷磁痕分级
5.4.3 裂纹缺陷直接评定为不合格。
5.4.4 评定为不合格或超过要求质量等级要求的缺陷,在工艺条件允许情况下可以进行返修。
5.4.5 返修后应进行复检,并重新进行质量评定。
5.4.6 返修复检部位应在检测报告的检测结果中标明。
5.4.7 检测记录或检测报告中应包括下列内容(参照本标准附录C):
1磁粉探伤装置型号、生产厂家;
2磁粉的类型、粒度及颜色;
3磁悬液种类及浓度;
4磁极的布置和探伤行走速度;
5探伤灵敏度(试片型号);
6 检测件的材质、规格、尺寸;
7记录缺陷磁痕、所在位置、形状尺寸及缺陷类型等。
6 表面质量的渗透检测
6.1 一般规定
6.1.1 本章适用于焊缝表面开口性的裂纹和其他缺陷的检测。
6.1.2 钢结构原材料表面开口性的裂纹和其他缺陷,可参照本章的基本原则进行检测。
6.2 检测试剂
6.2.1渗透检测剂包括渗透剂、清洗剂、显像剂。渗透检测剂的质量应符合《渗透检测用材料技术要求》JB/T7523的要求,宜采用成品套装喷罐的渗透检测剂。渗透检测剂必须标明生产日期和有效期,并附带产品合格证和使用说明书。对于喷罐式渗透检测剂,其喷罐表面不得有锈蚀,喷罐不得出现泄漏。应使用同一厂家生产的同一系列配套检测剂,不应将不同种类的检测剂混合使用。
6.2.2 渗透检测剂的选用应符合以下要求:
现场检测宜采用非荧光着色渗透检测,渗透剂可采用喷罐式的水洗型或溶剂去除型,显示剂可采用快干式的湿显像剂。
6.2.3 渗透检测必须配备铝合金试块(A型对比试块)和不锈钢镀铬试块(B型灵敏度试块),其技术要求应符合《无损检测-渗透检查A型对比试块》JB/T9213和《渗透探伤用镀铬试块技术条件》JB/T6064规定。
6.2.4 试块的选用应符合下列要求:
1 铝合金试块主要用于不同渗透检测剂的灵敏度对比试验,以及同种渗透检测剂在不同环境温度时,灵敏度对比试验。
2 不锈钢镀铬B型试块主要用于检验渗透检测剂系统灵敏度,以确定其是否满足要求及操作工艺正确性。
6.2.5 试块灵敏度的分级应符合以下要求:
1用不同灵敏度的渗透检测剂系统进行检测时,不锈钢镀铬B型试块上可显示的裂纹区号应如表6.2.5-1所示。
表6.2.5-1 灵敏度等级
2 不锈钢镀铬B型试块各裂纹区的直径显示尺寸如表6.2.5-2
表6.2.5-2 裂纹直径
6.2.6 检测灵敏度的选择应符合以下要求:
1 焊缝及热影响区采用“中灵敏度”检测,在不锈钢镀铬B型试块中可清晰显示“3~4”号裂纹;
2焊缝母材机加工坡口、不锈钢工件采用“高灵敏度”检测,在不锈钢镀铬B型试块中可清晰显示“4~5”号裂纹。
6.3 检测步骤
6.3.1渗透检测包括清理、清洗、施加渗透剂、清除多余渗透剂、干燥、施加显像剂、观察评定、复验、后处理等步骤。
6.3.2渗透检测操作应符合下列要求:
1 清理——对检测面上有碍渗透检测的铁锈、氧化皮、焊接飞溅、铁刺以及各种涂覆保护层进行清除,可采用机械砂轮打磨和钢丝刷。不允许用喷砂、喷丸等可能封闭表面开口缺陷的清理方法,清理范围应从检测部位边缘向外扩展30㎜。检测面的表面粗糙度Ra≤12.5μm,非机械加工面的粗糙度可适当放宽,但不得影响检测结果。
2 清洗——对清理完毕的检测面进行清洗,可采用溶剂、洗涤剂或喷罐套装的清洗剂。清洗后,检测面必须要经过充分干燥后,才能进行检测。
3 施加渗透剂——可以采用喷涂、刷涂等方法,将被检测部位完全被渗透剂覆盖,在环境温度10℃~50℃的条件下,以湿润状态至少保持15min。当环境温度条件不能满足时,应按第6.3.3条的要求进行灵敏度的对比试验。
4 清除多余渗透剂——可以先用纸巾或不掉纤维的洁净布进行擦拭,将检测面上大部分多余的渗透剂擦除,再用蘸有清洗剂或水的纸巾或布在检测面上朝一个方向擦洗,也可以用喷罐在距检测面约300㎜处喷撒少量清洗剂用纸巾或布擦洗,直至将检测面上残留渗透剂全部擦净。
5 干燥——经清洗处理后的检测面,可以自然干燥,也可用纸巾或布擦干,或用压缩空气吹干,或用热空气吹干,但检测面表面温度不能超过50℃。根据检测时的环境温度不同,干燥时间约为5min~10min。
6 施加显像剂——尽可能使用喷罐型的快干湿式显像剂,使用前充分摇动,将喷嘴距检测面约300㎜处实施均薄喷涂。
7 观察评定——在施加显像剂的同时仔细观察检测面上的痕迹显示情况,但对缺陷显示的最终确认应在显像剂施加完毕后10min~30min内完成。若显示不明显,可以适当延长观察时间。当检测面较大时,可以分区域检测,以保证每区域检测面可以在规定的时间内完成全部检测。对细小显示的观察可使用5~10倍放大镜对缺陷进行观察。观察应在光线充足的条件下进行,当发现不允许存在的缺陷,应及时作出标记。
8 复验——若出现下列情况之一,必须将检测面彻底清洗干净重新进行检测。
1)检测结束时,用试块验证检测灵敏度不符合要求;
2)难以确定痕迹是缺陷产生还是非缺陷的因素产生;
3)缺陷部位返修后。
9 后处理——检测结束后,必须将检测面清理干净。
6.3.3 不同环境温度时应进行灵敏度的对比试验。用标准温度和方法对试块A区进行检测,再将试块和渗透检测剂放在所需检测的环境温度下,待30min后各种检测器材均达到环境温度,即可开始对试块B区的检测试验,并注意在试验中始终保持这一温度。试验结束,比较试块A、B区的裂纹显示痕迹,如果显示痕迹基本相同,则可认定准备采用的方法经过鉴定是可行的。否则,需要调整检测工艺,若仍不能满足灵敏度要求,则不应采用渗透方法进行检测。
6.4 检测结果的评价
6.4.1 渗透检测显示的缺陷痕迹大致上可分为线型迹痕和圆型迹痕。
6.4.2 根据缺陷迹痕类型和长度对检测到的缺陷进行分级,缺陷迹痕分级应符合表6.4.2的规定。
6.4.4 评定为不合格或超过质量等级要求的缺陷,在工艺条件允许情况下可以进行返修。
6.4.5 返修后应进行复检,并重新进行质量评定。
6.4.6 返修复检部位应在检测报告的检测结果中标明。
6.4.7 缺陷迹痕的记录可根据需要和现场条件采用照相、绘图、粘贴等方法。
6.4.8 检测记录或检测报告中应包括下列内容(参照本规程附录D):
1检测剂名称、型号及生产厂家;
2检测面清理方法及清洗方法;
3渗透剂施加方法和渗透时间;
4 渗透剂去除方式、干燥方法及温度和时间;
5探伤灵敏度(试片型号);
6检测面表面状态;
7 检测件的材质、规格、尺寸;
8记录缺陷迹痕、所在位置、形状尺寸及缺陷类型等。
附录A 磁粉检测报告
A.0.1 钢结构磁粉检测报告应按表A.0.1进行记录。
附录B 渗透检测报告
B.0.1 钢结构渗透检测报告应按表B.0.1进行记录。
射线检测工艺规程
射线检测工艺规程 1 适用范围 本射线检测工艺适用于:碳素钢、低合金钢、不锈钢等材料制作的锅炉、压力容器及长输管道、钢质储罐熔化焊对接接头的射线透照检测工作。遇有特殊要求,应按相应的标准、规范执行。 2 引用标准 GB 11533—1989 标准对数视力表 GB 16357—1996 工业X射线探伤放射卫生防护标准 JB/T 7902—1999 线型像质计 JB/T4730-2005《承压设备无损检测》 SY/T4109-2005《石油天然气钢质管道无损检测》 GB50128-2005《立式圆筒形钢制焊接储罐施工及验收规范》 3 射线防护 3、1 X射线对人体有不良影响,应执行《检测作业安全防护指导书》与其它安全防护规定。 3、2 在现场工作人员应随身佩带个人剂量仪、射线个人报警器及防护服。 3、3 带一台射线剂量巡测仪,测定利用现场墙壁房屋及设备选择理想的屏蔽位置。 3、4 拍片现场划定“射线放射区”并放好警戒标记。 3、5 确认工作人员均已完成各自工作并离开辐射区,方可开启射线发生器进行透照。 3、6 每次透照完成后,均应用报警器确认射线就是否停止辐射后,方可进入辐射现场。 3、7 现场作业完成后对仪器进行清点、核对无误后清理现场,撤除警戒标志方可撤离现场。 3、8 从事放射性工作人员应定期进行体检,每年允许接受的剂量量为50 m SV。 4 人员要求 4、1 从事射线检测人员必须经过培训,持证上岗。只有取得质量技术监督部门颁发的射线检测技术等级证书的人员,方可独立从事与该等级相应的射线检测工作。 4、2 射线检测人员应具有良好的身体素质,其校正视力不得低于 5、0,并每年检查一次。从事评片人员应能辨别距离400mm远的一组高为0、5mm、间距为0、5mm
射线照相工艺规程
射线照相工艺规程 本规程适用于是我公司在制造压力容器和压力管道安装过程中必须遵循的射线探伤通用工艺. 本守则依据标准: GB150-1998钢制压力容器、 GB151-1999 钢制换热器 TSG R0004-2009固定式压力容器安全技术规程 TSG D0001-2009 压力管道安全技术检测规程-工业管道 GB50235-1997 工业金属管道工程施工及验收规范 GB50148-1993 工业金属管道工程质量检验 JB/T 4730-005 承压设备无损检测 第一章(适用于压力容器) 1、对射线照相各项技术要求,针对压力容器的结构特点,提供保证射线 探伤工作质量所需遵循的通用工艺方法,本工艺射线探伤法符合 JBT4730.2-2005标准所规定的AB级照相法. 2、射线照相人员应经国家质量监督检验检疫总局培训、考核所颁发的特 种设备检验检测人员证后,RTⅠ或RTⅠ级以上资格人员担任. 3、射线照相须在全过程中严格按照射线照相工艺卡的各项参数进行操 作.“射线照相工艺卡”应由RTⅡ及其以上资格人员逐项填写编制,并经 无损检测责任人批准后使用. 4、射线胶片的使用与暗室处理按“管理制度汇编”暗室工作及制度执行.
5、摄片时机对一般材料,应在焊后12小时进行,对有延迟裂纹倾向的材料 应在焊后24小时进行. 6、委托探伤的压力容器焊缝必须有委托单位履行的无损探伤申请委托 单,申请单上必须有焊缝外观检验合格的见证和焊接检验员的签名. 7、射线照相前应对焊缝外观进行复验,焊缝表面的不规则状态在底片上 的图象应不掩盖焊缝中的缺陷与之混淆,否则应做适当的修整. 8、射线照相过程中的电离辐射防护应符合GB16357-1996《工业X射线 探伤放射性防护标准》GB18871-2002《电离辐射及辐射源安全基本标准》的有关规定. 9、射线照相的工艺要素和基本步骤: (1)透照方法的确定 (2)探伤编号方法 (3)几何条件的确定 (4)定位标记、识别标记、象质计的选用及摆放; (5)贴片及屏蔽散射线的措施 (6)射线窗口对焦 (7)曝光量的选择及操作 (8)底片质量自检
钢结构工程检测办法
钢结构工程检测办法集团公司文件内部编码:(TTT-UUTT-MMYB-URTTY-ITTLTY-
钢结构工程检测方案 一、制作过程中的质量检测 1、原材料检验 (1)钢材验收 1)检验工具:万能试验机、半自动冲击机、布氏硬度机、冲击试样缺口手动拉床、微机CS 分析仪、RB-1试块、钢尺、游标卡尺等。 2)检验内容:核对材质证书、炉批号、产品名称、数量、规格、重量、品质、技术条件、主要标志等是否符合要求;检查钢板尺寸、厚度、钢板标记、表面质量;每炉号复验一组机械性能和化学成份。 3)检验过程:钢材到厂后,材料采购部提供一份材料到货清单及检验通知单给质检部。质检部接到通知单后,根据检验内容逐项组织钢材验收;钢材的复验按炉批号分批进行;Z向钢板将组织监理、市质监站赴钢厂进行出厂检验,进行事前控制。 4)合格产品:钢材的各项指标符合设计要求和国家现行有关标准的规定。不符合标准的钢材不能使用。 合格产品的资料整理、保管:钢材外观及复验检验合格后,填写《钢材验收清单》,对采购的材料需将产品证书、《材料来货报验单》、复验报告及《材料验收清单》由质检部一并整理成册,以便备查。材料来货验收确认后,由仓管员作好验收标记,并按规定进行材料保管和发放。 (2)焊材验收 1)检验内容:检验焊材证书的完整性,是否与实物相符,检验包装情况,焊丝、焊条是否有生锈等现象。
2)检验过程:焊材到货后,材料采购部将‘焊材到货清单’及‘检验通知单’送质检部,质检部接到通知单后应根据检验内容逐项验收,验收合格后填写《焊材验收清单》。焊材的复验分批次进行,每批焊材复验一组试样。 3)合格产品:焊材的各项指标符合设计要求和国家现行有关标准的规定。不符合标准的焊材不能使用。 4)合格产品的保管:钢材外观及复验检验合格后,送焊材二级库保管,并按规定手续发放。 (3)高强螺栓验收 1)检验内容:检验产品的质量合格证明文件,是否与实物相符,检验包装情况。 2)检验过程:涂料到货后,材料采购部将‘涂料到货清单’及‘检验通知单’送质检部,质检部接到通知单后应根据检验内容逐项验收。按有关规定按批进行复验,复验应送达国家法定检测机构进行复验,复验采用见证制度,在持见证员证书的监理工程师见证下共同取样送检。 3)只有复验合格的高强螺栓才能用于本工程的结构施工。 4)合格产品的保管:入库应按规定分类存放,防雨、防潮。螺纹损伤时不得使用。螺栓螺母、垫圈有锈蚀时应抽样检查紧固力,满足后方能使用。螺栓不得被泥土、油污沾染,始终保持洁净、干燥状态。 (4)涂料验收 1)检验内容:检验涂料证书的完整性,是否与实物相符,检验包装情况。 2)检验过程:涂料到货后,材料采购部将‘涂料到货清单’及‘检验通知单’送质检部,质检部接到通知单后应根据检验内容逐项验收。按有关规定按批进行复验,复验应送达国家法定检测机构进行复验,复验采用见证制度,在持见证员证书的监理工程师见证下共同取样送检。
完整word版射线检测工艺规程
射线检测通用工艺规程 1. 主题内容与适用范围本规程规定了焊缝射线人员具备的资格、所用器材、检测工艺和验收标准等内容。 本规程依据JB/T4730-2005的要求编写。适用于本公司板厚在2?30 mm钢制压力容器及壁厚T>2mm钢管对接焊接接头的X射线AB级检测技术。满足《压力容器安全技术监察规程》GB150、GB151 的要求。检测工艺卡内容是本规程的补充, 由n级人员按本规程等要求编写,其参数规定的更具体。 2. 引用标准、法规 JB/T4730 —2005《承压设备无损检测》 GB150-1998《钢制压力容器》 GB151-1999《管壳式换热器》 GB18871—2002《电离辐射防护及辐射源安全基本标准》 GB16357-1996《工业X射线探伤放射卫生放护标准》 JB/T7902《线型象质计》 特种设备无损检测人员考核与监督管理规则》 压力容器安全技术监察规程》 3. 一般要求 3.1射线检测人员必须经过技术培训,按《特种设备无损检测人员考核与监督管 理规则》考核并取得与其工作相适应的资格证书。 3.1.1检测人员应每年检查一次视力,校正视力玄1.0。评片人员还应辨别出 400mn距离处 高0.5mm间距0.5mm的一组印刷字母。 3.2 辐射防护 射线防护应符合GB18871 GB16357的有关规定。
透照厚度(W 范围、mm 应识别丝号 丝径(mm 3.3胶片和增感屏 胶片:在满足灵敏度要求的情况下,一般 X 射线选用T3或T2型胶片。 增感屏:采用前屏为0.03mm 后屏为0.03?0.10mm 的铅箔增感屏。. 3.4象质计 3. 4.1底片影像质量采用Fe 线型像质计测定。其型号和规格应符合 JB/T7902 的规定。象质计型号一般按下表 4选定。但对透照外径W 100mn 钢管环缝 时采用 JB/T4730附录F 的专用象质计。 3.4.2底片的象质计灵敏度选用 按透照厚度及不同的透照方法选择表 1至表3中要求达到的象质丝号。 3.4.3透照厚度W 射线照射方向上材料的公称厚度。多层透照时,透照厚度为 通过 的各层材料公称厚度之和。焊缝两侧母材厚度不同时,以薄板计。 表1象质计灵敏度值-单壁透照、象质计置于源側 (AB 级) 表2象质计灵敏度值-双壁双影透照、象质计置于源側 (AB 级) 表3象质计灵敏度值-双壁单影或双壁双影透照、象质计置于胶片側 (AB 级) 3.3.1 3.3.2 3.3.3 胶片和增感屏在透照过程中应始终紧密接触。
无损检测通常工艺标准规范标准规章
无损检测通用工艺规程 编制: ________________ 审核:________________ 批准:________________ 日期:________________
目录 第1章编制说明............................................... (3) 第2章射线检测通用工艺规程................................ (5) 第3章超声波检测通用工艺规程.................................... .21第1节承压设备对接焊接接头超声检测及质量分级.................... .24第2节承压设备钢板超声检测及质量分级............................ .29第3节承压设备用钢锻件超声检测及质量分级....................... .32第4章磁粉检测通用工艺规程.................................... .35第5章渗透检测通用工艺规程. (39) 第6章工艺卡附表............................................... .44第1节射线检测工艺卡.......................................... .44第2节超声检测工艺卡.. (45) 第3节磁粉检测工艺卡 (46)
第4节渗透检测工艺卡 (47)
第一章编制说明 1.1范围 本规程规定了对金属原材料、零部件和焊接接头进行射线检测、超声检测、磁粉检测、渗透检测的基本要求。 本规程适用于本公司钢制压力容器产品的无损检测工作。 1.2引用标准和编制依据 下列标准包含的条文,通过在本规程中引用而构成本规程的条文,在规程出版时,所有版本均为有效。所有标准都会被修订,使用本规程的各方应探讨使用下列标准最新版本的可能性。 压力容器安全技术监察规程(1999年版) GB150-1998 《钢制压力容器》 GB151-1999 《管壳式换热器》 JB/T4730.1?4730.6-2005 《承压设备无损检测》 《特种设备无损检测人员资格考核实施细则》 《放射卫生防护基本标准》 Q/JS.YLRQ--2008《质量保证手册》 1.3人员资格及职责 1.3.1从事无损检测的人员必须持有国家质量监察机构颁发的并与其工作相适应的资格等级证书。1.3.2从事无损检测的人员校正视力不得低于5.0,从事磁粉、渗透检测工作人员,不得有色盲、色弱。 1.3.3检测人员严格执行有关条例、规程、标准和技术规范,保证工作质量。 1.3.4评片人员的视力应每年检查一次,要求距离400mn能读出0.5mm的一组印刷体字母。 1.3.5检测操作人员必须按委托单要求并同时根据检测工艺规程进行操作,做好检测记录及签发检测报告。 1.3.3无损检测责任工程师的职责见《岗位职责》。 1.4无损检测方法使用原则
超声波检测工艺规程
超声波检测工艺规程 1适用范围 1.1 本工艺适用于板厚为6-250mm得板材、碳素钢与低合金钢锻件、母材壁厚8—400mm得全焊透熔化焊对接焊缝及壁厚大于等于4mm,管径为57—1200mm碳素钢与低合金石油天然气长输、集输与其她油气管道环向对接焊缝、钢质储罐对接焊缝得超声波检测等、 1。2 本工艺规定了使用A型脉冲反射式超声波探伤仪进行检测过程中,对受检设备做出准确判定应遵循得一般程序与要求。 1、3 引用标准 JB4730/T—2005《承压设备无损检测》 SY/T4109-2005《石油天然气钢质管道无损检测》 GB11345-89《钢焊缝手工超声波探伤方法与探伤结果得分级》 JB/T9214-1999《A型脉冲反射式超声探伤系统测试方法》 JB/T10062-1999《超声探伤用探头性能测试方法》 GB50128—2005《立式圆筒形钢制焊接储罐施工及验收规范》 2对检测人员得要求 2、1 从事超声波检测人员必须经过培训,持证上岗。只有取得质量技术监督部门颁发得超声波检测技术等级证书得人,方可独立从事与该等级相应得超声波检测工作、 2、2 检测人员应具有良好得身体素质,其校正视力不得低于 5.0,并每年检查一次。 2、3检测人员应严格执行《检测作业安全防护指导书》与其它安全防护规定,确保安全生产。 3检测程序 3、1根据工程特点与本工艺编制具体得《无损检测技术方案》。 3.2受检设备经外观检查合格后,由现场监理或检验员开据《无损检测指令》或《无损检测委托单》到检测中心。 3。3 检测人员按指令或委托单要求进行检测准备,技术人员根据实际情况编制《探伤工艺卡》、 3、4 检测人员按《超声波探伤仪调试作业指导书》等工艺文件进行设备调试。 3.5 外观检查合格后,施加耦合剂,实施检测,做好《超声波检测记录》。 3。7 根据检测结果与委托单,填写相应得回执单或合格通知单、若有返修,还应出据《返修通知单》,标明返修位置等。将回执单与返修通知单递交监理或检验员,同时对受检设备进行检验与试验状态标识。 3。8 返修后,按要求重新进行检测、
钢结构工程检测方案
钢结构工程检测方案 一、制作过程中的质量检测 1、原材料检验 (1)钢材验收 1)检验工具: 万能试验机、半自动冲击机、布氏硬度机、冲击试样缺口手动拉床、微机CS分析仪、RB-1试块、钢尺、游标卡尺等。 2)检验内容:核对材质证书、炉批号、产品名称、数量、规格、重量、品质、技术条件、主要标志等是否符合要求;检查钢板尺寸、厚度、钢板标记、表面质量;每炉号复验一组机械性能和化学成份。 3)检验过程:钢材到厂后,材料采购部提供一份材料到货清单及检验通知单给质检部。质检部接到通知单后,根据检验内容逐项组织钢材验收;钢材的复验按炉批号分批进行;Z向钢板将组织监理、市质监站赴钢厂进行出厂检验,进行事前控制。 4)合格产品:钢材的各项指标符合设计要求和国家现行有关标准的规定。不符合标准的钢材不能使用。 合格产品的资料整理、保管:钢材外观及复验检验合格后,填写《钢材验收清单》,对采购的材料需将产品证书、《材料来货报验单》、复验报告及《材料验收清单》由质检部一并整理成册,以便备查。材料来货验收确认后,由仓管员作好验收标记,并按规定进行材料保管和发放。 (2)焊材验收 1)检验内容: 检验焊材证书的完整性,是否与实物相符,检验包装情况,焊丝、焊条是否有生锈等现象。 2)检验过程:焊材到货后,材料采购部将‘焊材到货清单’及‘检验通知单’送质检部,质检部接到通知单后应根据检验内容逐项验收,验收合格后填写《焊材验收清单》。焊材的复验分批次进行,每批焊材复验一组试样。 3)合格产品:焊材的各项指标符合设计要求和国家现行有关标准的规定。不符合标准的焊材
不能使用。 4)合格产品的保管:钢材外观及复验检验合格后,送焊材二级库保管,并按规定手续发放。 (3)高强螺栓验收 1)检验内容: 检验产品的质量合格证明文件,是否与实物相符,检验包装情况。 2)检验过程:涂料到货后,材料采购部将‘涂料到货清单’及‘检验通知单’送质检部,质检部接到通知单后应根据检验内容逐项验收。按有关规定按批进行复验,复验应送达国家法定检测机构进行复验,复验采用见证制度,在持见证员证书的监理工程师见证下共同取样送检。 3)只有复验合格的高强螺栓才能用于本工程的结构施工。 4)合格产品的保管:入库应按规定分类存放,防雨、防潮。螺纹损伤时不得使用。螺栓螺母、垫圈有锈蚀时应抽样检查紧固力,满足后方能使用。螺栓不得被泥土、油污沾染,始终保持洁净、干燥状态。 (4)涂料验收 1)检验内容: 检验涂料证书的完整性,是否与实物相符,检验包装情况。 2)检验过程:涂料到货后,材料采购部将‘涂料到货清单’及‘检验通知单’送质检部,质检部接到通知单后应根据检验内容逐项验收。按有关规定按批进行复验,复验应送达国家法定检测机构进行复验,复验采用见证制度,在持见证员证书的监理工程师见证下共同取样送检。 3)只有复验合格的涂装材料才能用于本工程的涂装施工。 4)合格产品的保管:合格涂料应设专门的防爆、防燃涂装材料仓库进行保管。
射线检测通用工艺规程
射线检测通用工艺规程 1目的 对射线检测作业的工艺作出规程性的规定,以保证射线检 测过程符合有关的法规、标准以及公司《质量保证手册》及 《程序文件与管理制度汇编》的要求。 2 范围 适用于金属材料制容器的原材料、零部件和焊缝射线检测的作业过程。 3 引用标准 JB/T4730.1 -2005 《承压设备无损检测》第1部分通用 要求 JB/T4730.2-2005 《承压设备无损检测》第2部分射线 检测 4人员资格 4.1凡射线检测人员应按《锅炉压力容器无损检测人员资格鉴定考核规则》考核合格,并持有与工作相适应的有效资格证书。 4.2评片人员应每年做一次视力检查,矫正视力不得低于 1.0,并要求距离40mm能读出高为0.5 mm、间距为0.5 mm的印刷字母。
4.3取得不同射线检测资格级别的人员,只能从事与资格级 别相应的无损检测工作。检测原始记录应由相应□级或口级 以上资格人员核对,射线检测检测报告须经相应H级或□级 以上资格人员复核并签字后方能生效。 4.4从事射线检测人员上岗前应经辐射安全知识培训,并取 得放射工作人员证。 5检测设备、器材和材料 5.1检测设备 按本公司《无损检测仪器使用、维护管理规定》执行。 5.2射线胶片 5.2.1 胶片系统按照GB/T19384.1 - 2003《无损检测工业射 线照相胶片第一部分工业射线胶片系统的分类》分为四类, 即T1、T2、T3、T4。T1为最高类别,T4为最低类别。 5.2.2射线检测技术为A级、AB级时,应采用T3及以上类别的胶片,射线检测技术为B级时,应采用T2及以上类别的胶片。 5.3观片灯 —95 —
无损检测通用工艺规范培训文件
无损检测通用工艺规程 编制: 审核: 批准: 日期:
目录 第1章编制讲明 (3) 第2章射线检测通用工艺规程 (5) 第3章超声波检测通用工艺规程 (21) 第1节承压设备对接焊接接头超声检测及质量分级 (24) 第2节承压设备钢板超声检测及质量分级 (29) 第3节承压设备用钢锻件超声检测及质量分
级 (32) 第4章磁粉检测通用工艺规程 (35) 第5章渗透检测通用工艺规程 (39) 第6章工艺卡附表 (44) 第1节射线检测工艺卡 (44) 第2节超声检测工艺卡 (45) 第3节磁粉检测工艺卡 (46) 第4节渗透检测工艺卡 (47)
第一章编制讲明 1.1 范围 本规程规定了对金属原材料、零部件和焊接接头进行射线检测、超声检测、磁粉检测、渗透检测的差不多要求。 本规程适用于本公司钢制压力容器产品的无损检测工作。 1.2 引用标准和编制依据 下列标准包含的条文,通过在本规程中引用而构成本规程的条文,在规程出版时,所有版本均为有效。所有标准都会被修订,使用本规程的各方应探讨使用下列标准最新版本的可能性。 压力容器安全技术监察规程(1999年版) GB150-1998 《钢制压力容器》 GB151-1999 《管壳式换热器》 JB/T4730.1~4730.6-2005 《承压设备无损检测》 《特种设备无损检测人员资格考核实施细则》 《放射卫生防护差不多标准》 Q/JS.YLRQ--2008《质量保证手册》 1.3 人员资格及职责
1.3.1从事无损检测的人员必须持有国家质量监察机构颁发的并与其工作相适应的资格等级证书。 1.3.2从事无损检测的人员校正视力不得低于5.0,从事磁粉、渗透检测工作人员,不得有色盲、色弱。 1.3.3检测人员严格执行有关条例、规程、标准和技术规范,保证工作质量。 1.3.4评片人员的视力应每年检查一次,要求距离400mm能读出0.5mm的一组印刷体字母。 1.3.5检测操作人员必须按托付单要求并同时依照检测工艺规程进行操作,做好检测记录及签发检测报告。 1.3.3 无损检测责任工程师的职责见《岗位职责》。 1.4 无损检测方法使用原则 1.4.1 射线和超声检测要紧用于承压设备的内部缺陷的检测;磁粉检测要紧用于铁磁性材料制承压设备的表面和近表面缺陷的检测;渗透检测要紧用于非多孔性金属材料和非金属材料制承压设备的表面开口缺陷的检测。 1.4.2 铁磁性材料表面检测时,宜采纳磁粉检测。 1.4.3 当采纳两种或两种以上的检测方法对承压设备的同一部位进行检测时,应按各自的方法评定级不。 1.4.4 采纳同种检测方法按不同检测工艺检测时,假如检测结果不一致,应以危险度大的评定级不为准。
焊缝超声波检测工艺规程
焊缝超声波检验规程 1范围 适用于金属材料制承压设备用原材料、零部件和设备的超声检测,也适用于金属材料制在用承压设备的超声检测。 与承压设备有关的支承件和结构件的超声检测,也可参照本部分使用. 2 规范性引用文件 下列文件中的条款通过JB/T 4730的本部分的引用而成为本部分的条款。凡是注日期的引用文件,其随后所有的修改单(不包括勘误的内容)或修订版均不适用于本部分,然而,鼓励根据本部分达成协议的各方研究是否可使用这些文件的最新版本。凡是不注日期的引用文件,其最新版本适用于本部分。 JB 4730.1—2005 承压设备无损检测第1部分:通用要求 JB/T 7913—1995 超声波检测用钢制对比试块的制作与校验方法 JB/T 9214—1999 A型脉冲反射式超声波探伤系统工作性能测试方法 JB/T 10061—1999 A型脉冲反射式超声波探伤仪通用技术条件 JB/T 10062—1999 超声探伤用探头性能测试方法 JB/T 10063—1999 超声探伤用1号标准试块技术条件 3一般要求 3.1 超声检测人员 超声检测人员的一般要求应符合JB/T 4730.1的有关规定。 3.2 检测设备 3.2.1 超声检测设备均应具有产品质量合格证或合格的证明文件。 3.2.2 探伤仪、探头和系统性能 3.2.2.1 探伤仪 采用A型脉冲反射式超声波探伤仪,其工作频率范围为0.5MHz~10MHz,仪器至少在荧光屏满刻度的80%范围内呈线性显示。探伤仪应具有80dB以上的连续可调衰减器,步进级每档不大于2dB,其精度为任意相邻12dB误差在±1dB以内,最大累计误差不超过1dB。水平线性误差不大于1%,垂直线性误差不大于5%。其余指标应符合JB/T10061的规定。 3.2.2.2 探头 3.2.2.2.1 晶片面积一般不应大于500mm2,且任一边长原则上不大于25mm。 3.2.2.2.2 单斜探头声束轴线水平偏离角不应大于2°,主声束垂直方向不应有明显的双峰。 3.2.2.3 超声探伤仪和探头的系统性能 3.2.2.3.1 在达到所探工件的最大检测声程时,其有效灵敏度余量应不小于10dB。 3.2.2.3.2 仪器和探头的组合频率与公称频率误差不得大于±10%。 3.2.2.3.3 仪器和直探头组合的始脉冲宽度(在基准灵敏度下):对于频率为5MHz的探头,宽度不大于10mm;对于频率为2.5MHz的探头,宽度不大于15mm。 3.2.2.3.4 直探头的远场分辨力应不小于30dB,斜探头的远场分辨力应不小于6dB。 3.2.2.3.5 仪器和探头的系统性能应按JB/T 9214和JB/T 10062的规定进行测试。 3.3 超声检测一般方法 3.3.1 检测准备 3.3.1.1 承压设备的制造安装和在用检验中,检测时机及抽检率的选择等应按法规、产品标准及有关技术文件的要求和原则进行。 3.3.1.2 检测面的确定,应保证工件被检部分均能得到充分检查。 3.3.1.3 焊缝的表面质量应经外观检测合格。所有影响超声检测的锈蚀、飞溅和污物等都应予以清除,其表
钢结构检测)复习题
红字部分为答案 填空题 1.《钢结构施工质量验收规范》规定,网架结构挠度检测时,测点挠度检测值不得大于测点挠度计算值的倍。 2. 网架结构、网壳结构常用的节点形式是螺栓球节点和焊接球节点 3. 焊接球节点抗拉承载力检测时,要求试件的极限承载力大于设计承载力的倍 4. 《钢结构工程施工质量验收规范》规定:钢网架的挠度检测应分别在总拼完成后及屋面工程完成后两个施工阶段分别进行。 判断题 (1)钢结构具有耐热性好,耐火性好的优点(错) (2)与混凝土结构相比,钢结构具有更好的绿色环保性能(对) (3)网架与网壳均属于空间网格结构形式(对) (4)螺栓球节点抗拉承载力检测时,试件的极限承载力需大于设计承载力的倍(错) 单项选择题 (1) 《钢结构施工质量验收规范》规定,网架结构挠度检测时,当网架的跨度小于24m,测点应为A A 跨中一点 B 四等分点 C 三等分点 D 变形最大点 (2) 摩擦型高强度螺栓连接的抗剪承载力随着摩擦面抗滑移系数的增大而B A 减小 B 增大 C 不变 D 两者之间无确定变化规律 (3)高强度大六角头螺栓连接副扭矩系数测试是为了进行A A 预拉力控制 B 抗滑移系数控制 C 外观质量控制 D 扭矩控制 多项选择题 (1) 根据《建筑结构检测技术标准》GB/T50344-2004的规定,建筑结构的检测可分为:AB A 建筑结构工程质量的检测 B 既有建筑结构性能的检测 C 可靠性检测 D 安全性检测 (2) 根据《钢结构现场检测技术标准》GB/T50621-2010的规定,钢结构的检测可分为:BC A 钢结构适用性检测 B 既有钢结构的检测 C 在建钢结构检测 D 钢结构安全性检测
射线探伤工艺规程
长沙天鹅工业泵股份有限公司 X射线探伤操作规程 TEJY8.2.4-2007A-09 1、目的 该项操作规程,对焊接件纵向焊缝的射线探伤实施有效控制。 2、适用范围 本规程适用于对焊接件纵向焊缝进行无损检测射线探伤前应做的准备工作和射线探伤中全过程的管理。 3、选择的前提 对给定工件进行射线探伤时,应根据有关规程和标准要求选择适当的探伤条件。应以国标ISO17636为选择条件的依据,焊缝透照按底片影像质量由低而高的要求分A级、AB级和B 级三种检验等级。焊接件纵向焊缝焊缝的射线探伤,至少应满足AB级的要求。 不同的象质等级对底片的黑度、灵敏度与不清晰度有不同的规定。要满足规定等级的象质要求,从探伤器材、方法、条件及程度等各个方面都要预先进行全面地部署。 4、照相规范的确定 在照相过程中,除了合理地选择透照方法外,还必须选择好透照规范,使小缺陷能够在底片上明显地辨别出来,从而达到高灵敏度。有关规范的选择: 1)、射线源的选择,应选择小尺寸的射线源; 2)、透照距离的选择。在透照中,焦距选择大多在600~700mm间; 3)、胶片与增感屏的选择。通常照相时将原度为0.01~0.13mm的铅箔增感屏与非增感形胶片一起使用。 5、几何参数的选择 几何参数是影响射线照相灵敏度的重要因素,因此必须综合考虑与合理选择。 1)、焦点或射线源尺寸:焦点大小对缺陷影响在射线底片上的显示对比度和清晰度都有很大影响; 2)、焦点尺寸和几何布置会引起的影像模糊及放大; 3)、焦点尺寸与射线底片对比度; 4)、照射场内的X射线强度分布; 5)、透照距离L1的选择——对Uy值和满足K值的有效长度要综合考虑。
超声波检测规程
超声波检测规程 1校准与复核 校准应在试块上进行,校准中应使超声主声束垂直对准反射体的轴线,以获得稳定和最大的反射信号。 在开始使用仪器时,应对仪器的水平线性和垂直线性进行测定,在使用过程中,每隔三个月至少应对仪器的水平线性和垂直线性进行一次测试。 在探头开始使用时,应对探头进行一次全面的性能校准。斜探头在使用前应进行前沿距离、折射角、主声束偏离、灵敏度余量和分辨力的校准。使用过程中,每次使用前应校准前沿距离、折射角和主声束偏离。直探头的始脉冲占宽、灵敏度余量和分辨力应根据使用的频度每隔一个月或三个月检查一次。 2检测工艺 对于具体部件的检测,中级或高级检验人员应根据相应的标准编制检测工艺卡,经审批后实施。工艺卡应包括如下内容:检验等级、材料种类、规格、检验时机、坡口形式、焊接工艺方法、表面状态及灵敏度补偿、耦合剂、仪器型号、探头及扫查方式、灵敏度、试块、缺陷位置标定方法、报告要求、操作人员资格、执行标准等。 3检验程序 工件准备一表面检查、委托检验一接受委托、指定检验员一了解焊接情况一确定检测工艺卡一选定无损检测方法、仪器、探头、试块一校准仪器和探头一制作距离波幅曲线一调整无损检测灵敏度一校准与复核一涂布耦合剂一粗无损检测一标示缺陷位置一精无损检测一评定缺陷一复核一记录一报告一审核一存档。对于不合格焊缝的重新无损检测,仍然遵从此程序的要求。 4检验前的准备 根据被检部件的材质、规格、性质和结构形状选定无损检测标准,确定检验等级,确定检测工艺卡。 对选定的仪器、探头的性能及其组合性能应进行测试,并符合要求。 制作距离一波幅曲线及综合补偿测定: 斜探头前沿距离、K值的测定应在SGB-4试块上进行,前沿距离、K值至少应测量三次,取其平均值。 调节扫描速度、扫描比例,按照选定的标准要求制作距离波幅曲线,并计入综合补偿,绘制在坐标纸上。 综合补偿测定按选定的标准进行。 检测面和检测范围的确定应保证检查到工件被检部分的整个体积,检验前应用80#或100#砂纸去除检测面上的毛刺等,以利于声耦合和探头的移动并减少探头磨损。 5检验 按照选定标准的规定确定无损检测灵敏度,并对扫描线和灵敏度进行复核。 扫查时应尽量扫查到工件的整个被检区域,探头移动速度不应大于 150mm/S。 可以采用不同的扫查方式,以检测不同走向的缺陷。检测纵向缺陷时,探头沿焊缝在母材上均匀做锯齿形或矩形扫查,在保持探头移动方向与焊缝中心线基本垂直的同时,还要作10°-15°的摆动;检测焊缝和热影响去的横向缺陷应采用平行扫查。初探时,如发现评定线及以上的反射波时,可先用记号笔在部件上
射线检测工艺规程
工艺规程 1.编写铸钢件射线检测工艺规程 2.液化气钢瓶环焊缝射线检测工艺规程 3.管板焊缝射线检测工艺规程 4.锅炉筒体焊缝射线检测工艺规程 5.T形接头焊缝射线检测工艺规程 6.天然气输气管道对接环焊缝射线检测工艺规程 7.有一管线工程要做射线检测工作,其有关施工说明除依照合约NDT-RT-003的规定外,均依()。合约NDT-RT-003的规定如下:(1)检测范围:对接环缝,φ28x3mm、φ83x12mm、φ127x14mm的碳钢管线及管件;(2)检测时机:焊接完成冷至室温后;(3)检测比率:对接焊缝100%;(4)射源:照相厚度18mm以下用X光机,超过18mm者可用铱192;(5)胶片:杜邦65(Du Pont 65),尺寸300x80mm;(6)像质计:线条型,置于底片侧,双壁照像双壁判读应置于底片中央焊缝上。双壁照像单壁判读则放置与底片两端的焊缝上,距底片边缘15mm,细线靠外;(7)检测方法:外径89mm以下双壁照像双壁判读,超过89mm 时双壁照像单壁判读;(8)黑度:1.5-3.0;(9)灵敏度:1.5%以下;(10)标志:左上角为工程编号及位置编号;右上角为检测厚度,T之后加以mm为单位的阿拉伯数字;左下角为焊工编号及射线检测人员编号,分别以W及R表示;下中为同一焊口的张数编号及中心点符号,以A、B、C表示;右下角为照像日期,年月日均以两位数字表示,不足两位数者以零填补;(11)底片两边重叠时最少重叠25mm;(12)接受基准:()级。试编写其X射线透照的工艺规程。 8.右图所示中:板厚32mm,存在有 a.夹渣, b.气孔, c.夹渣与气孔, d.未焊透(熔穿不足),尺寸大小 如图示,按()判定,该焊道应 判定为几级? 9.右图所示中:板厚32mm,存在有 a.夹渣, b.夹渣, c.气孔, d.裂缝, 尺寸大小如图示,按()判定, 该焊道应判定为几级? 10.承上题,右图所示中的b夹渣 和c气孔应各自独立判为几级? 11.母材厚度5mm的钢板对接焊缝射线照相底片中发现长3mm,宽2mm的缺陷,按()判定,应为第几级? 12.母材厚度30mm的钢板对接焊缝射线照相底片中发现:a.一处长8mm,宽2mm的缺陷和相隔40mm处的b.一处密集点状缺陷(直径1mm,计有10个),按()判定,两处缺陷应各自独立判为几级? 13.母材厚度22mm的钢板对接焊缝射线照相底片中发现:a.一处长8mm,宽2mm的缺陷和相
超声波检测工艺规程(DOC 148页)
超声波检测工艺规程
1 超声检测通用工艺规程 2 承压设备用钢板超声检测专用工艺 3 承压设备用锻件超声检测专用工艺 4 承压设备用奥氏体钢超声检测专用工艺 5 承压设备用无缝钢管超声检测专用工艺 6 承压设备用复合钢板超声检测专用工艺 7 承压设备对接焊接接头超声检测专用工艺 8 承压设备T型焊接接头超声检测专用工艺 9 钢制承压设备管子和管道环向对接焊接接头超声检测专用 10 承压设备用钢螺栓坯件超声检测专用工艺 11 在用承压设备超声检测专用工艺 12 超声测厚检测通用工艺 13 模拟式超声检测仪操作规程 14 数字式超声检测仪操作规程 15超声波探伤仪系统自校规程 16 超声测厚仪操作规程
1 超声检测通用工艺规程 1.1 范围 1.1.1 本工艺规定了承压设备采用A型脉冲反射式超声波探伤仪检测工件缺陷的超声检测方法。 1.1.2 本工艺适用于金属材料制承压设备用原材料、零部件和焊接接头的超声检测,也适用于金属材料制在用承压设备的超声检测。 1.2 引用标准 1.2.1 GB150-98《钢制压力容器》。 1.2.2劳部发[1996]276号《蒸汽锅炉安全技术监察规程》。 1.2.3 JB/T4730-2005《承压设备无损检
测》 1.3 一般要求 1.3.1 检测人员 (1)凡从事超声波检测的人员,必须经过国家劳动部门考核,取得各级资格的人员是能从事与其资格相适应的工作。(2)检测人员必须掌握仪器的综合性能,并能独立进行检测。 (3)检测人员必须熟悉超声波检测有关标准,能按标准要求选择适当方法校正仪器,并能进行熟练的检测操作。 (4)检测人员应能根据被检工件的材质、规格、加工工艺过程、材料曲率等,预计缺陷可能产生的部位和类型,并能进行正确的定位和定量。
钢结构工程制作与安装检测方案
钢结构工程制作与安装检测方案 一、制作过程中的质量检测 1、原材料检验 (1)钢材验收 1)检验工具: 万能试验机、半自动冲击机、布氏硬度机、冲击试样缺口手动拉床、微机CS分析仪、RB-1试块、钢尺、游标卡尺等。 2)检验内容:核对材质证书、炉批号、产品名称、数量、规格、重量、品质、技术条件、主要标志等是否符合要求;检查钢板尺寸、厚度、钢板标记、表面质量;每炉号复验一组机械性能和化学成份。 3)检验过程:钢材到厂后,材料采购部提供一份材料到货清单及检验通知单给质检部。质检部接到通知单后,根据检验内容逐项组织钢材验收;钢材的复验按炉批号分批进行;Z向钢板将组织监理、市质监站赴钢厂进行出厂检验,进行事前控制。 4)合格产品:钢材的各项指标符合设计要求和国家现行有关标准的规定。不符合标准的钢材不能使用。 合格产品的资料整理、保管:钢材外观及复验检验合格后,填写《钢材验收清单》,对采购的材料需将产品证书、《材料来货报验单》、复验报告及《材料验收清单》由质检部一并整理成册,以便备查。材料来货验收确认后,由仓管员作好验收标记,并按规定进行材料保管和发放。 (2)焊材验收 1)检验内容: 检验焊材证书的完整性,是否与实物相符,检验包装情况,焊丝、焊条是否有生锈等现象。 2)检验过程:焊材到货后,材料采购部将‘焊材到货清单’及‘检验通知单’送质检部,质检部接到通知单后应根据检验内容逐项验收,验收合格后填写《焊材验收清单》。焊材的复
验分批次进行,每批焊材复验一组试样。 3)合格产品:焊材的各项指标符合设计要求和国家现行有关标准的规定。不符合标准的焊材不能使用。 4)合格产品的保管:钢材外观及复验检验合格后,送焊材二级库保管,并按规定手续发放。 (3)高强螺栓验收 1)检验内容: 检验产品的质量合格证明文件,是否与实物相符,检验包装情况。 2)检验过程:涂料到货后,材料采购部将‘涂料到货清单’及‘检验通知单’送质检部,质检部接到通知单后应根据检验内容逐项验收。按有关规定按批进行复验,复验应送达国家法定检测机构进行复验,复验采用见证制度,在持见证员证书的监理工程师见证下共同取样送检。 3)只有复验合格的高强螺栓才能用于本工程的结构施工。 4)合格产品的保管:入库应按规定分类存放,防雨、防潮。螺纹损伤时不得使用。螺栓螺母、垫圈有锈蚀时应抽样检查紧固力,满足后方能使用。螺栓不得被泥土、油污沾染,始终保持洁净、干燥状态。 (4)涂料验收 1)检验内容: 检验涂料证书的完整性,是否与实物相符,检验包装情况。 2)检验过程:涂料到货后,材料采购部将‘涂料到货清单’及‘检验通知单’送质检部,质检部接到通知单后应根据检验内容逐项验收。按有关规定按批进行复验,复验应送达国家法定检测机构进行复验,复验采用见证制度,在持见证员证书的监理工程师见证下共同取样送检。 3)只有复验合格的涂装材料才能用于本工程的涂装施工。 4)合格产品的保管:合格涂料应设专门的防爆、防燃涂装材料仓库进行保管。
特种设备射线检测通用工艺规程(按NBT47013修订)
XXX有限公司 特种设备射线检测通用工艺规程 1、范围 本规程规定了承压设备金属熔化焊对接接头的X射线检测技术和质量分级要求。 本规程适用于承压设备受压元件的制造检测中对接焊缝、管座角焊缝和管子管板角焊缝的射线检测。用于制作焊接接头的金属材料包括碳素钢、低合金钢、不锈钢。 本规程规定的射线检测技术分为三级:A级一一低灵敏度技术;AB级一- 中灵敏度技术;B级一一高灵敏度技术。 承压设备的有关支承件和结构件的对接焊接接头的射线检测,也可参照使用2、规范性引用文件 下列文件中的条款,通过在本规程中的引用而成为本规程的条款。凡是注日期的引用文件,其随后所有的修改单(不包括勘误的内容)或修订版不适用于本规程。凡是不注日期的引用文件,其最新版本适用于本规程。 NB/T47013-2015 承压设备无损检测 GB11533-2011 标准对数视力表 GBZ117-2015 工业X射线探伤放射卫生防护标准 GB18871-2002 电离辐射防护与辐射源安全基本标准 GB11924-1989 辐射安全培训规定 GB/T12604.2-2005 无损检测术语射线检测 HB7684-2000 射线照相用线型象质计 JB/T7902-2006 线型象质计 JB/T7903-1999 工业射线照相底片观片灯 3、一般要求 射线照相检验的一般要求除应符合NB/T47013.1-2015的有关规定外,还应符 合下列规定。 3.1 射线检测人员
XXX有限公司 特种设备射线检测通用工艺规程 3.1.1从事射线检测人员上岗前应进行按GB11924的规定进行辐射安全知识的培训,并取得放射工作人员证。 3.1.2射线检测人员未经矫正或经矫正的近(距)视力和远(距)视力应不低于 5.0 (小数记录值为1.0),测试方法应符合GB11533的规定。从事评片的人员应每年检查一次视力。 3.2射线胶片 3.2.1射线胶片系统分为6类,即C1、C2、C3、C4、C5、C6类。C1为最高类别,C6为最低类别。胶片系统的特性指标和常见牌号胶片所属的胶片系统类别见附录A (资料性附录)。 3.2.2A级和AB级射线检测技术应采用C5类或更高类别的胶片,B级射线检测技术应采用C4类或更高类别的胶片。 3.3观片灯 3.3.1观片灯的主要性能应符合GB/T19802的有关规定。 3.3.2观片灯的最大亮度应能满足评片的要求。 3.4黑度计(光学密度计) 3.4.1黑度计可测的最大黑度应不小于4.5,测量值的误差应不超过土0.05。 3.4.2黑度计首次使用前应进行核查,以后至少每六个月应进行一次核查,形成核查报告。在工作开始时或连续工作超过8h后应在拟测量黑度范围内选择至少两点进行检查。 3.5增感屏 射线检测一般应使用金属增感屏或不用增感屏,金属增感屏应满足JB/T5075 的要求,增感屏应完全干净、抛光和无纹道。增感屏的选用应符合表1的规定。 3.6象质计 3.6.1底片影像质量采用线型像质计或孔型像质计测定。通用线型像质计和等径线型像质计的型号和规格应符合JB/T 7902的规定,孔型像质计型号和规格应满 足GB/T 23901.2的规定 3.6.2象质计的材料、代号和不同材料的象质计适用的工件材料范围应符合表 2 的规定。
钢结构工程检测考核试题
工程质量检测人员考核试卷 四、(钢结构工程检测部分) 姓名:单位:准考证号: 1.名词解释(每题4分,共16分) (1)抗滑移系数 (2)高强度螺栓连接副 (3)空间刚度单元 (4)超生波探伤灵敏度 2.填空题(每题2分,共20分) (1)钢结构焊缝超声波探伤中DAC曲线由、和,三条曲线组成。 (2)焊缝质量等级为一级的焊缝当采用超声波进行探伤时,焊缝探伤比例为,焊缝合格评定等级为。 (3)超声探伤中为确定焊缝中缺陷位置、方向、形状,常采用的四种探头基本扫查方式为、、、。 (4)高强螺栓头部顶面的标志“10.9S”中,9代表公称屈服强度与公称抗拉强度的比值为。 (5)对于母材厚度为25mm以下的钢板对接焊缝,超声波探伤中应选用K值为和的探头。 (6)10.9S级高强度大六角头螺栓连接副的扭矩系数平均值应为,扭矩系数标准偏差应小于或等于。 (7)钢网架结构总拼完成后及屋面工程完成后应分别测量其挠度值,所测挠度值不应超过相应设计值的倍。 (8)钢结构涂装工程中,当设计对涂层厚度无要求时,涂层干漆膜厚度室外应为
μm,室内应为μm,其允许偏差为μm 。 (9)单层钢结构主体结构的整体平面弯曲允许偏差为,且不应大于mm。 (10)紧固高强度螺栓应分为初拧、终拧,初拧应使螺栓的紧固轴力达到螺栓预拉力标准值的左右。 3.单项选择题(每题2分,共20分) (1)普通螺栓作为永久性连接螺栓时,当设计有要求或对其质量有疑义时,应进行()。 A、扭矩系数实验 B、化学成分分析 C、硬度实验 D、螺栓实物最小拉力载荷实验 (2)扭剪型高强度螺栓连接副终拧后,除因构造原因无法使用专用扳手终拧掉梅花头外,未在终拧中拧掉梅花头的螺栓数不应大于节点螺栓数的()。 A、1% B、2% C、5% D、10% (3)高强度大六角头螺栓连接副终拧扭矩检测应在()的时间内进行。 A、24h后 B、1h后,48h内 C、24h内 D、2h后,48h内 (4)钢结构工程现场安装焊缝的探伤比例应按()计算百分比。 A、同一类型、同一施焊条件的焊缝条数 B、每条焊缝 C、所有焊缝总条数 D、以上都可以 (5)单层钢结构主体的整体垂直度允许偏差为() A、H/1000,且不应大于25mm B、H/2000,且不应大于25mm C、H/1000,且不应大于20mm D、H/2000,且不应大于20mm (6)钢网架焊接球节点承载力试验中,试验破坏载荷值应()。 A、大于或等于1.0倍设计承载力 B、大于或等于1.2倍设计承载力 C、大于或等于1.6倍设计承载力 D、大于或等于2.0倍设计承载力 (7)大六角头高强度螺栓连接副扭矩系数保证期为自出厂之日起( )内。 A、二年内 B、一年内 C、三个月内 D、六个月内 (8)钢结构焊缝超声波探伤中当最大反射波幅位于Ⅱ区的缺陷其指示长度小于10mm 时,应按()mm计。 A、0 B、5 C、10 D、以实测长度为准 (9)钢结构普通钢板焊缝超声波探伤中,制定DAC曲线最常用的对比试块是()。 A、RB-Ⅰ、RB-Ⅱ B、CSK-ⅠA C、CSK-ⅡA D、ⅡW (10)GB11345-89规范中根据焊缝质量要求,检验等级分为A、B、C三级,其中等级最高,难度系数最大的是()级。 A、A B、B C、C D、都一样