主生产计划和物料需求计划逻辑计算(数据略有变化:提供演算例题结果,有助于理解计算过程)20150106NEW

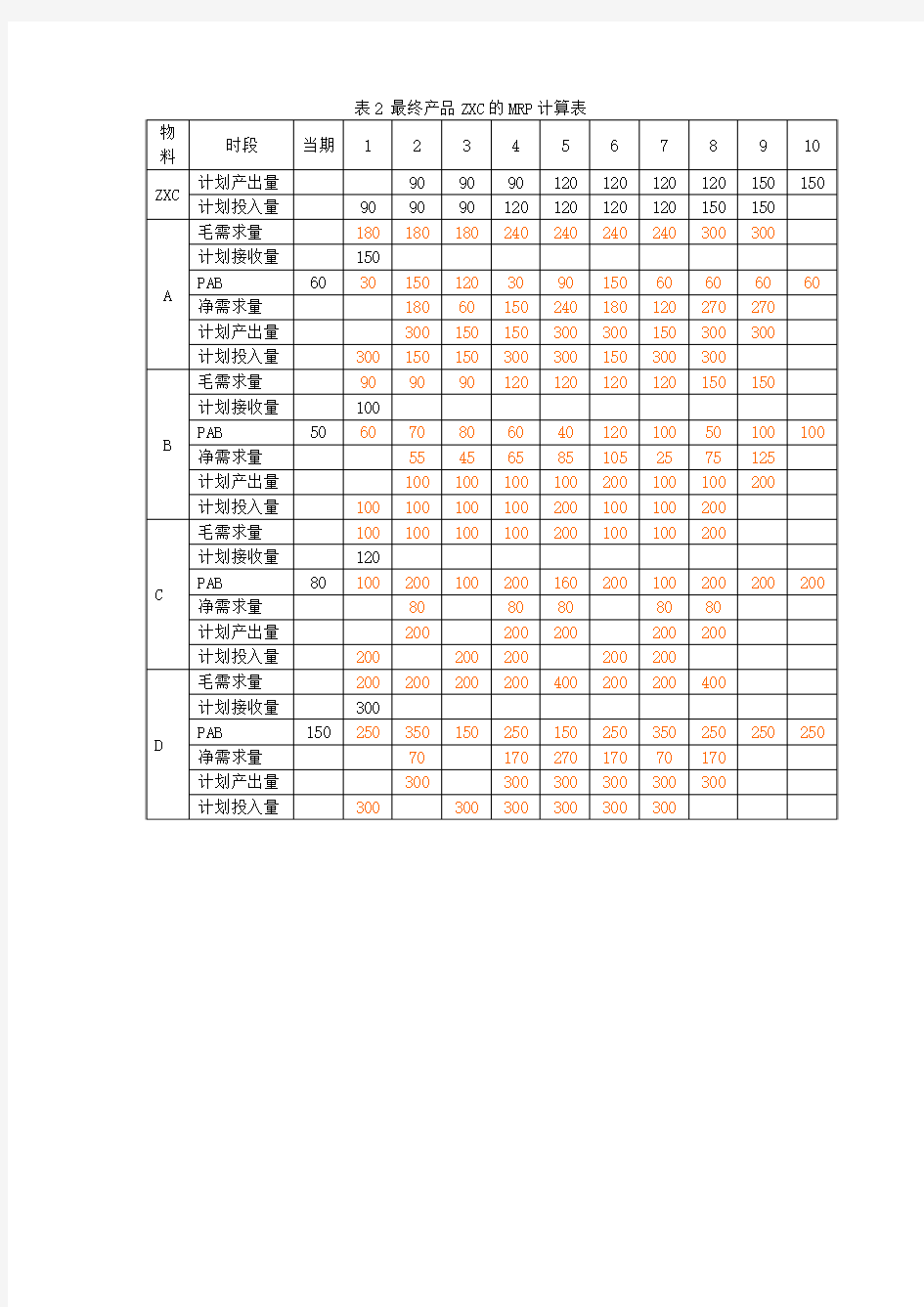
主生产计划(MPS)和物料需求计划(MRP)逻辑计算(数据略有变化:提供演算例题结果,有助于理解计算过程)20150106
【MPS逻辑计算例题】已知某独立需求物料的有关数据如下表1,现有库存量为150,安全库存量为50,生产批量为200,批量增量为200,提前期为1个时段。库存初值为150。预测量和订单量如下表1所示。试根据相关的法则完成该独立需求物料MPS计算过程,并将相应数据填入下表中。
【MRP逻辑计算例题】已知某独立需求物料(最终产品)ZXC的BOM结构如图1所示。每个ZXC由2个物料A和1个物料B组成,每个物料B由1个物料C和2个物料D组成。
图1 最终产品ZXC的BOM结构图
最终产品ZXC的MPS如表2前三行所示(即最终产品ZXC的装配提前期为1时段,表2中第2行和第3行分别给出其最终产品ZXC计划产出量和计划产出量的有关数据)。
表2还同时给出其他物料A、B、C、D有关数据。其中物料A的有关属性是:计划接收量为150,PAB初值为60,订货批量为150,安全库存量为30,提前期为1个时段。物料B的有关属性是:计划接收量为100,PAB初值为50,订货批量为100,安全库存量为25,提前期为1个时段。物料C的有关属性是:计划接收量为120,PAB初值为80,订货批量为200,安全库存量为80,提前期为1个时段。物料D的有关属性是:计划接收量为280,PAB初值为150,订货批量为300,安全库存量为120,提前期为1个时段。
试根据相关的法则完成物料A、B、C、D的MRP计算过程,并将相应数据填入下表中。
表2 最终产品ZXC的MRP计算表
MRPⅡ ERP原理与应用习题解答
第4章MRPⅡ原理:生产规划 思考练习题 (12) 完成MTS下的生产计划大纲的编制。 某公司的经营计划目标为:完成全年游戏机市场销售额的10%。据预测,全部市场的年销售额4800万元。要做到全年均衡销售,预计关键部件每月可提供9000台;现有能力工时为每月800小时。初始库存为1500台;未完成订单100台,期末所需库存800台。资源清单如下: 产品关键部件劳动力(小时) 单台收入(元) 游戏机10 1 500 参照书中例子,要求: ?按月编制生产计划大纲初稿,填写相应表格。 ?分析资源清单,计算并列出资源需求。 ?比较可用资源与需求。 解答:(1) 库存改变:–600,总生产量:9000。 (2)每台游戏机的资源清单为: 产品关键部件劳动力(小时) 游戏机10 1 每月游戏机的资源需求量为: 产品计划生产量关键部件需求量劳动力(小时) 游戏机750 10*750=7500 750
(3)可用资源为关键部件每月可提供9000台;现有能力工时为每月800小时,能够满足需求量。 (13) 完成MTO下的生产计划大纲的编制。 某公司的经营计划目标为:完成全年游戏机市场销售额的10%。据预测,全部市场的年销售额4800万元。要做到全年均衡销售,预计关键部件每月可提供9000台;现有能力工时为每月800小时。期初未交货数量1400台,交货日期为:1月750台;2月400台;3月200台;4月50台;期末未交货数量:800台。资源清单如下: 产品关键部件劳动力(小时) 单台收入(元) 游戏机10 1 500 参照书中例子,要求: ?按月编制生产计划大纲初稿,填写相应表格。 ?分析资源清单,计算并列出资源需求。 ?比较可用资源与需求。 解答:(1) 未完成订单的改变:-600,总产量:10200。 (2)每台游戏机的资源清单为: 产品关键部件劳动力(小时) 游戏机10 1 每月游戏机的资源需求量为: 产品计划生产量关键部件需求量劳动力(小时) 游戏机850 10*850=8500 850 (3)可用资源为关键部件每月可提供9000台;现有能力工时为每月800小时,能力工时不能够满足需求量,出现资源短缺,故计划需要调整,或增添资源。
物料需求计划(MRP)的基本计算模型
物料需求计划(MRP)的基本计算模型 物料需求计划(MRP)的制定需要三个关键信息:MPS、BOM、库存记录。MPS是指主生产计划,BOM是指物料清单。在MRP的制定过程中,库存记录的计算方法构成了MRP 的基本计算模型。所以,我们主要介绍一下MRP中的库存记录形式、以及如何计算和使用MRP的库存记录。 MRP中的库存记录又称为MRP表格。MRP表格在很多方面都与MPS记录表格类似。它所包括的内容有:计划因子、粗需求量、预计入库量、现有库存量、计划订货入库量和计划发出订货量等。它与MPS类似,将未来的需求分成一个个时间段来表示,这种时间段的单位通常是周,但有时也用日或月来表示。为了便于理解,下面结合一个例子来说明MRP表格的计算过程。 某办公家具公司,其两种主要产品(即企业要出厂的最终产品)是办公用椅A和B,其需求大致稳定:产品A每周需30个,产品B每周需20个。这两种产品都需要用到一种支架部件C。因此,对C的平均需求量是每周50个。A和B的装配期是1周。 下图1是办公椅A和B的主生产计划表格以及部件C的库存记录表格(尚未完成)。这种表格没有标准格式,该例所用的是一种常见格式。 如上图示,在这种格式中,左上方通常要标出产品名称及其性质(如上图中,表明C是支架部件),右上方表示计划因子,通常包括三项:生产批量、生产周期和安全库存量。在本例中,C的批量是230个,生产周期为2周,安全库存量为50个。这些计划因子的
量都需要预先选定。当这些值发生变化以后,管理人员必须及时更新库存记录。下面首先来看库存记录的内容和确定方法。 一、库存记录要素及其计算 1、粗需求量。上例中未来8周的粗需求量如图1所示。其需求量是根据C的最终产品A和B的主生产计划所决定的,但有时候需要加上一些作为配件(更换件)使用的量。对C的需求之所以比MPS中A、B的时间提前1周,是因为MPS中所表示的各周的量实际上是指当周应该完成的量。但由于生产或装配是需要一个周期的,因此该生产指令的发出必须给出这部分时间的提前量。在该例中,第2周需150个A,其装配周期为1周,故第1周应发出生产订单,开始装配。上图1中的第2个表格表示的是考虑了生产周期之后,MPS生产订单发出的时间和生产量。同样,MRP库存记录中粗需求的需要量是指当周应准备好的量,例如,为了在第2周装完150个A,第1周必须准备好150个C。 2、预计入库量(scheduled receipts,简称SR)。它是指订单已发出,、但货尚未收到的量。对于外购件,它现在可能处于几种状态之一:买方刚发出订单,供应商正在加工;正在从供应商至卖方的途中;已到买方、买方正在验货等。对于自加工件,它现在可能的状态包括:正在生产现场被加工;等待他的原材料和零件的到达;正在机床前排队等待加工;正从一个工序移至下一个工序等。第1周需150个C,其生产周期为2周,故至少在2周之前已发出了该生产的订单,但通常不会比提前2周更早地发出订单。 3、现有库存量(POH)。其概念与MPS中的概念相同,指每周需求被满足之后手头仍有的库存量。该记录随着每周进货或出货的情况而更新,未来各周的POH则可计算德出。 其计算公式为: 式中,It--t周末的POH; SR,t--t周的预计入库量; PR,t--t周的计划订货入库量; GR,t--t周的粗需求; 可见,上式与MPS中的计算方式是一致的,即SR,t+PR,t相当于MPS量,GR,t相当于max(Ft,COt),这里不存在预测值或订单值的选择,因为需求是相关的、确定的。上面图1只给除了前4周的POH,在第4周,POH只剩7个,少于所要求的50个安全库存量,这是一个要求生产的信号,即要求增加PR的信号。 4、计划订货入库量(planned receipts,简称PR)。其含义是,计划订货或生产、但订单尚未发出的订货量。这个量的意义是要保持POH的量不低于安全库存(在MPS中未考虑安全库存,保持POH非负即可)。对于某些不需要安全库存的中间物料,则如同MPS,其意义是要保持POH非负。在库存记录中所表示的PR量应包括这两种情况。 PR的确定方法如下: (1)在POH出现短缺(或为负值或小于安全库存量)的当周制订一个PR量,其值的大小应是POH大于等于安全库存; (2)继续计算其后各周的POH,当又出现短缺时,制订下一个PR量。 这两个步骤反复进行,直至整个计划期的POH记录和PR记录格都填满。 5、计划发出订货量(planned order release,简称POR)。它实际上是要说明订单的发出时间或开始生产时间。之所以将其称为“╳╳量”,是因为这种对时间的说明在库存记录中是通过将该订单的量记入相应的时间栏内来说明的。该时间的基本计算式是:到货时间减去生产周期。利用这一项可容易地导出构成某项物料的BOM中下一层物料的粗需求。
(生产计划)制定生产计划的常用方法
制定生产计划的常用方法 一、图表法 [例13-1] 已知H公司1999年上半年(为简化,只考虑上半年)满足需求量的生产安排,见表13-5。为实现此进度安排,拟采用三种不同的综合生产计划方案。 *保险储备量=1/4预测需求量 有关成本数据补充如下: 生产成本=100元/件; 存储费用=每月生产成本的1.5%(即每月每件1.5元); 标准工资率=每小时4元; 加班费=标准工资的150%或每小时6元; 缺货损失=5元/件; 外协比自制昂贵而增加的费用=每件产品2元; 招聘和培训费=每人200元; 提前解聘损失费=每人250元; 每件产品所需工时=5小时。 方案1的策略:在正常工作班次下,通过增减生产工人来生产出确切的需要量。 方案2的策略:固定生产工人数,工人数按6个月的平均产量来确定((8125件×5小时/件)/(143天×8小时/天)=36人);允许库存发生短缺,通过下月的生产来补足。 方案3的策略:按生产需要量(计划量)最低的4月份来确定所需工人数,并稳定在4月份这个水平上((850件×6月×5小时/件)/(143天×8小时/天)=22人;产量低于需求量部分通过外协来解决。 计划方案见表13-6 方案1:11600元 方案2:7460元 方案3:6182元
表13-7 三种方案的比较
二、运输表法 运输表法的基本假设是: 1.每一单位计划期内正常生产能力、加班生产能力以及外协量均有一定限制; 2.每一单位计划期的预测需求量是已知的; 3.全部成本都与产量呈线性关系。 h──单位计划期内单位产品的库存成本 I0──第1期期初库存 r──单位产品的正常生产成本 R t──t期的正常生产能力 c──单位产品的加班成本 OT t──t期的加班生产能力 S──单位产品的外协成本 S t──t期的外协生产能力 D t──t期的预测需求量
MRP计划表例题
- mrp计算原理:根据主生产计划(mps)、库存计划、物料清单(bom),制定物料需求计划(mrp) 主要公式:毛需求量=独立需求量+相关需求量 计划库存量=上期期末库存量+本期订单产出量+本期预计入库量-毛需求量 净需求量=本期毛需求量-上期库存量-本期预计入库量+安全库存量 bom中各物料的数量关系高层次与其下一层在数量上的倍数关系,由下一层旁边括号内的数字决定。例如: a b ┌───┼───┐ ┌───┼───┐ d(1) e(2) c(1) e(1) f(2) c(1) ┌─┴─┐ ┌─┴─┐ ┌─┴─┐ e(1) f(1) f(2) d(1) f(2) d(1) ┌─┴─┐ ┌─┴─ e(1) f(1) e(1) f(1) c、d、e、f的相关需求关系式为: c=a+b d=a+c e=2a+b+d f=2b+d+2c 计算mrp时注意三个问题 1.是否有安全库存 2.是否有批量限制 3.提前期是多少 例题1:已知1个a由2个b和1个c组成,1个b由1个d和1个c组成,各物料的提 前期均为1周,下表是客户对产品a的订单需求表,运用mrp求a产品的物料需求计划。 例题2.某家具公司组装餐桌,具体部件包括4个桌腿和1个桌面,提前期分别为2周和 3周,组装需要1周的时间,公司接到40张餐桌的订单,需要在第5周交货,另外70张要在 第7周交货,当前库存中有6张完工的餐桌,80张桌腿和44张桌面,请利用mrp求出公司的 订货计划。 练习题: . 主生产计划: bom: 库存信息以及提前期: 物料的需求计划: 例题3:某厂生产产品x,产品x的需求量见表1,并已知安全库存为3件,批量为25 件,投入提前期为1周,期初库存为8件,期初计划到货为20件。1件产品x需要2个部件 y,并已知部件y每周作为备件外售需要量为4件,安全库存为12件,批量为60件,投入提 前期为1周,期初库存为18件,计划第1周入库50件,试用mrp方法编制x和部件y的生产 作业计划。表1 产品x的需求量 篇二:mrp计算题 mrp库存管理练习题 1、购买零件a的前置时间是4周,零件a现有数量为22件,另外在第4周的预计到达 量为20件,今后8周对零件a的需求量如表6-31所示。请用mrp系统计算表确定发出订单的 时间和数量。订货批量q不小于20件 表6-31 今后8周对零件a的需求量 & 解:今后8周零件a的mrp的运算结果表如下所示:零件a的mrp的运算表(lt=4) 零件a的mrp的运算表(lt=4) 表:产品产品a的错口式物料清单 解: 产品a的mrp计算表(lt=3) 2 零件b的mrp计算表(lt=2) 零件c的mrp计算表(lt=3) ! 零件d的mrp计算表(lt=1)
第十章 物料需求计划与企业资源计划习题
第十章物料需求计划与企业资源计划 一、判断题 1、MRP处理的是相关需求。 2、MRP的三项主要输入是产品出产计划、库存状态文件和物料清单文件。 3、牛鞭效应是指对零售商的订货量的波动大大高于对制造商的订货量的波动。 4、MRP的基本思想就是围绕物料转化组织制造资源,实现按需要准时生产。 5、MRP对产品结构树进行自底向上的分析,按产品结构层次向上累计需求。 6、产品结构文件是MRP系统产生的。 7、订单沿从顾客到生产方向移动,商品的订货数量呈现放大的现象,称为牛鞭效应。 二、选择题 1、以下哪项不是MRP的输入? A、生产大纲 B、产品出产计划 C、产品结构文件 D、库存状态文件 2、MRP的输出是: A、总需要量 B、净需要量 C、计划发出订货量 D、现有数 E、对所有零件和产品的需求计划 三、简答题 1、为什么一般制造企业的大多数物料(零部件)应当用MRP系统来控制? 2、MRP系统的三项主要输入是什么? 3、预计到达量和计划订货到达量两者含义有何不同? 4、何谓MRPII?它的主要功能模块哪些? 5、何谓MRP?它的主要作用有哪些? 6、简述DRP和MRP的异同。 7、简述闭环MRP的闭环含义。 8、简述MRPⅡ的特征。 四、计算题 1、设某产品的成本为50元,保管费率为2%,订货费用为120元。未来12周的净需求量如下表所示。期初库存量为零。试采用最小成本法确定在这12周内的订货时间和订货批量。 某产品未来12周的净需求量
时 123456789101112间 35101025200301020301020净 需求 量 2、假设产品P由2个单位A和3个单位B组成;A由2个单位C和3个单位D组成;D由1个单位B和2个单位E制成。各种物料的提前期分别为:P、A、C,1周;D,1周;B、E,3周。设在第14周需要P为50个单位。假设各物料目前没有库存;批量原则按照直接批量原则。 (1) 试画出产品结构树; (2) 制定一个MRP计划表。
多品种、小批量的生产计划编制方法
多品种、小批量的生产计划编制方法 针对数百种规格以上的多品种、小批量的生产情况,借助于excel电子表格软件的“统计描述”功能和统计函数(COUNT())、判断函数(IF())等函数,可以掌握销售量的数量特性和时间特性,从而进行销售量预测,为编制生产计划提供了关键信息。 标签:储备式生产描述统计统计函数离散系数库存生产计划 一、现状 在温州、宁波等地的电器、仪表等行业,一些企业的产品规格常在数百上千种之多。笔者调查过10家企业,每家销售的品种规格繁多,各规格不一定每月都销售,每月也可能新增规格销售。它们在2年内共销售16835种产品规格,2008年4月销售3834种,其中新增1362种。这种典型的多品种、小批量情况,对生产管理人员凭记忆、经验管理的传统方法提出了巨大挑战。笔者结合Excel 2003软件,提出多品种、小批量生产条件的生产计划编制方法。 二、储备式生产的基本问题 产品生产基本有两种模式:一是订单式生产,生产任务明确,其要点在于提前进行生产技术准备,完成订单的时间、数量和质量要求。二是储备式生产,在保持一定库存的基础上安排生产。这种模式的基本问题,是掌握生产的数量、时间规律,即生产期量标准。为此进行销售分析是必经之路。 三、销售分析 (一)分析方法以定性分析为基础,将定量分析与定性分析相结合。通过掌握的销售数据,与国家宏观经济政策、行业发展趋势、专家意见、个人经验相结合,综合分析,得出概括性、方向性意见,为定量分析的结果提供研究、判断的基础。 定量分析的方法很多,适应于不同的预测目标、预测精度、预测期限和预测费用条件。在实际的工作中。宜以2种或2种以上的方法独立预测,并结合起来分析、比较,以修正预测结果。在此,介绍Excel软件的“描述统计”等方法。 资料准备:平时应当收集产品的生产、销售数据。例如,某企业有500种产品规格,自2007年1月至2008年6月的销售量数据,按月录入在Excel的“C2:T501”中(A列:序号;B列:产品规格),并将销售量为“0”的单元格清“空”。 依次点击“工具”、“数据分析”、“描述统计”菜单,就打开“描述统计”对话框:输入区域($B$2:$T$102,经试算一次最多可输入128行);分组方式(选:逐行);勾选“标志位于第一行”;勾选汇总统计;勾选平均数置信度,输入置信概率;建
毕业设计---物料需求计划(MRP)的实例分析与编程
毕业设计(论文) 物料需求计划(MRP)的实例分析与编程 学院(系):物流工程学院 专业班级:物流工程专业0603班 学生姓名: 指导教师:
本科生毕业设计(论文)任务书 设计(论文)题目: 物料需求计划(MRP)的实例分析与编程 设计(论文)主要内容: 1、综述当前物料需求计划(MRP)的发展历程以及有关研究的国内外动态(资料来 源:在图书馆电子阅览室查询在中国期刊网查找中文资料,在https://www.360docs.net/doc/2614057645.html,查英文论文); 2、阐述和分析物料需求计划(MRP)的理论以及解决方案; 3、基于实例进行编程、计算和分析(可以选择LINGO,Xpress-MP,AMPL等优化软 件进行编程,辅助计算); 4、撰写论文、编写程序及使用说明书。 要求完成的主要任务: 1、整理毕业设计报告书(计算说明书)一份,字数不少于12000字。 2、文献资料检索不少于15篇,其中外文文献不少于2篇。 3、外文资料翻译不少于5000个中文字,需要提交外语原文和手译稿(提交电子文档)。 4、所建立的仿真模型、仿真系统需要写好文档(包括设计说明书和使用说明书)等 资料,分组刻录入光盘备案。 5、答辩用Microsoft PowerPoint演示。 6、其它要求参照《武汉理工大学毕业设计(论文)工作管理办法》。 必读参考资料: [1]F.S.Hillier,G.J. Lieberman.运筹学导论(英文,第8版)[M].清华大学出版社, 2007. [2]熊伟编著.运筹学[M].北京:机械工业出版社,2005. [3]谢金星,薛毅.优化建模与LINDO/LINGO软件[M].北京:清华大学出版社, 2005.7. [4]徐玖平,胡知能.李军编著.运筹学(I类).北京:科学出版社,2004. [5]徐玖平,胡知能.李军编著.运筹学(II类).北京:科学出版社,2004. [6]姚恩瑜,何勇,陈仕平.数学规划与组合优化[M].杭州:浙江大学出版社,2001.10. [7]Christelle Guéret,Christian Prins,Marc Sevaux.Xpress-MP优化实例精选. https://www.360docs.net/doc/2614057645.html,.2006.
物料需求计划试题【最新版】
物料需求计划试题 一、名词解释 1.MRP: 2.净需求量: 3.主生产计划(MPS):.物料清单(BOM): 二、单项选择 1.物料需求计划应根据()制定。 A.生产计划大纲 B.主生产计划 C.生产能力需求计划 D.总装配计划
2.MRP中工厂日历是用于编制计划的日历,它与普通日历的关系是( )。 A.与普通日历相同 B.由普通日历除去假日 C.由普通日历加上加班日期 D.由普通日历除去不生产的日子 3.不属于MRP的关键信息要素是()。 A生产纲领B.主生产计划C. 库存记录D.物料清单 4.MRP的主要功能是按时间分段计算的毛需求和净需求以及制定各库存项目的( )。 A. 成本计划 B.采购计划 C.订货计划 D.物料计划 5. MRPⅡ的最大成就在于把企业经营的主要信息完成了( ) 。
A.优化 B.集成 C.整合 D.贮存 6.汽车制造厂对汽车轮胎的需求属于哪一类需求?() A. 相关需求 B. 非相关需求C .一次性需求D. 重复性需求 7.运用MRP计算企业生产过程各阶段的计划任务时,应按照什么原理进行的?() A.原工艺路线 B.次工艺路线
C.反工艺路线 D. 随机工艺路线 8.MRP 中的BOM,指的是()。 A.物料清单 B.加工工艺数据 C.生产能力资源数据 D.工厂日历 9. C是A产品的配件,在编制C的物料需求计划时,应根据()制定。 A.生产计划大纲 B.A产品的计划提前订货量 C.主生产计划
D.总装配计划 三、判断题 1.MRP有三种输入信息,即主生产计划、物料清单和库存量。() 2.MRP是在订购点法的基础上发展起来的,可以克服订购点法的不足。() 3.在MRP 计算逻辑中每期的计划订单收到量必然等于当期的净需求量。( ) 4.物料需求计划主要用于离散型产品。() 5.MRP的关键要素有MPS、物料清单他库存记录。() 6.独立需求是指那些具有不确定性,企业自身迫切需要的需求。() 7.在闭环的MRP完成对生产计划与控制的基础上的进一步扩展,将经营、财务、生产管理子系统相结合,形成制造资源计划系统。()
生产计划编制步骤
生产计划编制步骤 生产计划,是对企业生产系统总体方面的计划。主要内容包括调查和预测社会对产品的需求、核定企业的生产能力、确定目标、制定策略、选择计划方法、正确制定生产计划、库存计划、生产进度计划和计划工作程序、以及计划的实施与控制工作。 生产计划的编制程序一般分为如下步骤: 1、了解生产状况、掌握市场信息。 销售计划是生产计划的基础,但不等于生产计划,还要根据企业生产能力、企业的资源及客户需求的情况做修正;而生产计划于生产计划也有影响,初步制订的销售计划也要根据企业的能力和资源做进一步修改。销售计划与生产计划都是企业总体经营战略的具体体现。 2、结合生产状况和外部市场条件,分析研究,提出初步生产计划指标。 生产计划是为生产处符合市场需要或顾客需求的产品,所确定的在什么时候生产,在哪个车间生产以及如何生产的总体计划。因此必须根据企业的经营目标和销售计划初步提出生产计划指标,包括品种、产量、质量水平和交货期等。 3、综合平衡,确定生产计划指标。 将初步制定的生产计划指标与生产能力、劳动力、技术准备工作、物资供应和资金占用等企业内部条件进行综合平衡,确定生产计划指标。 4、编制生产计划大纲,组织实施生产作业目标。 生产计划大纲的内容包括:生产计划的主要指导思想、生产计划指标、完成计划的难点及重点环节、采取的关键措施,以及生产计划表。 在编制生产计划的过程中,要使编制计划具有合理性和可操作性,必须注意一下几点: ①要多方收集资料,掌握企业生产现状,要深入基层,掌握第一手资料,为编制计划提供可靠的依据。 ②要搞好预测,主要是市场预测、外部主要生产条件预测,这是非常重要的一个环节。在市场经济条件下,只有准确掌握产品的市场供求情况,制定切实可行的生产计划,才能生产适销对路的产品,提高企业效益。 ③要进行综合平衡,通过综合平衡,确定计划指标。综合平衡要从需求与实际生产能力出发,量力而行,留有余地,统筹合理安排。 宏智瑞达企业生产管理咨询总结评论:生产计划的实施和控制,是调度工作的重点,调度要围绕计划所制定的目标来组织均衡稳定的生产,完成目标计划。生产计划统计与分析工作,属于生产的事后总结提高阶段。通过对计划的实施,要认真总结成功的经验,找出不足及失败的原因,为下一步计划拟定提供改进依据。 生产计划管理是工厂管理内部运作的核心。一个优秀的工厂,其内部管理应该是围绕着生产计划来进行的。生产计划有月度计划、周计划、日计划。不过随着MRP的使用,“主生产计划”成为控制工厂内部运做的核心了。生产计划管理是企业管理的开始,当前,制造业企业所处的经济环境瞬息万变,企业面临的经营压力不断增大,唯有提升管理,方能在大浪淘沙般的市场竞争中,立于不败之地。对于制造业企业而言,客户订单变更、插单、改单等情况时有发生,是管理的重中之重,无疑成为制造企业提升竞争力的关键。生产计划的计划对象主要是把生产规划中的产品系列具体化以后的出厂产品,通称最终项目,所谓“最终项目”通常是独立需求件,对它的需求不依赖于对其他物料的需求而独立存在。但是由于计划范围和销售
物料需求计划例子doc
物料需求计划例子 篇一:某工厂制作物料需求计划的案例 16、某工厂制作物料需求计划的案例 要生产成品就会有物料需求,其需求可以按照下面步骤进行: (1)分为季、月、周计划建立生产计划表。 计划表内应有生产单号码、品名、数量、生产日期等内容。 (2)计算标准用量 将生产计划表内各品名、使用物料分析表,按照该品名的材料(BOM)的标准用料量进行备料。 (标准部门用料量×计划生产量)×(1+设定标准不良率)=标准用量。 也可以说生产某一产品的某项材料,生产部门按照生产计划的生产数所需要的材料标准领料。 (3)查库存数及调查该项材料,查出现有库存数及应发出还未发出的数量。 库存数-应发数≥标准需求,则表示此一材料,生产分析这张订单没问题,并记入物料分析表内。 库存数-应发数<标准需求,其差数要提出申购。 (4)查订购方式。 从材料目录表内查出此材料是存量管制的方式,还是按
照订单的方式订购。 假如此材料属于按照“存量订购”则此材料按照存量订购的方式订购。 如果是按照订单购材料,则进入下步骤,提出申购单。 (5)材料采购 采购按照申购单内的材料内容、数量及所要求日期,向供应商提出订购单,并按照申购者的要求,排定进货时间及数量,以配合已定的生产计划时间。 (6)进料控制 采购人员及物料控制(MC)人员按照进料时间控制。 遇有迟延状况时最迟应于三天前通知生管,以方便变更生产计划。 (7)收料 仓库管理部门使用收料单收料。 (8)生产备料 仓库按照生产计划或备料单的日期,于领用前一天准备好所需的物料 篇二:物料需求计划及其运算 工业工程本科课程设计(论文) 学院(系): 专业: 学生姓名:聂开政
主生产计划及物料需求计划测试题
MPS/MRP系统 背景资料: 主生产计划(MPS)及物料需求计划(MRP)系统是ERP 管理软件的核心,也是ERP系统发展的基础。通过MPS/MRP 系统将企业外部销售市场对企业的销售需求转化为企业内部的生产需求和采购需求,将销售计划转化为生产计划和采购计划。MPS/MRP 管理方式可以解决“需要什么什么时候需要需要多少”三大难题。相对与手工管理来说,MPS/MRP 计划可以大大提高计划下达的效率,并大大增加计划的准确性、及时性,从根源及计划层面杜绝不必要的库存,减少浪费。 某ERP系统的主生产计划管理系统融先进的MRP 管理思想与软件设计之中,通过主生产计划MPS(Master Production Schedule),将独立的需求(销售或预测)作为需求,考虑现有库存、已分配量、预计入库等因素,通过BOM 向下展开需求,得到主要产品(MPS 类物料)的计划量。主计划员可以对该计划量进行维护、确认或进行粗能力计划,将能力的影响体现在计划的改变上。对确定的计划订单,也可作为预计入库量,实现滚动计划功能。MPS 计算产生的计划订单经过确认,除可以生成本身的生产计划外,还可以将相关需求传输到MRP 系统,作为MRP 的需求来源。 主生产计划的需求来源分为两个方面,一个是客户订单,另一个是预测订单。客户订单与预测订单两者形成MPS/MRP的需求有三种方式即仅为客户订单,仅为预测订单和客户订单+预测订单的某种组合。这种组合关系系统提供了五种处理方式: 客户订单+预测订单,不冲销 客户订单+预测订单,向前冲销 客户订单+预测订单,向后冲销 客户订单+预测订单,先向前冲销再向后冲销 客户订单+预测订单,先向后再向前冲销。 企业计划员可以根据实际情况选择冲销策略,并设定相应的冲销范围。系统内部冲销的顺序为:按指定的最早的N日开始冲销,再进行N+1日的冲销,直至冲销完毕或超过设定的日期。 在进行MPS/MRP 计算时,可以定义不同的计划方案。计划方案的参数不同,计算的结果也完全不一样。需要设定的参数包括六类,分别为:需求参数、计算参数、合并参数、投放参数、仓库参数、其他参数。 MPS计算的步骤为: 1、预检查 该步骤实现运算前对BOM 的合法性、完整性及物料的低位码进行检查及维护,从而保证MPS/MRP 运算结果的正确性。包括:BOM 单嵌套检查、BOM 单完整性检查、低位码维护,产生物料的低位码,为进行MPS/MRP 计算时进行需求传递做好准备。 2、指定计划方案 该步骤用以选择运算编号、运算方案和设置运算开始、结束日期。 3、获取需求 该步骤根据〖计划方案〗设置的计划计算范围展示要参与本次计算的需求信息,主要是获取参与运算的需求单据和物料。计划计算范围共分四种:全部计划对象、指定需求单据、指定物料、指定计划员。 4、显示预计量 本步骤将对参与本次计算的所有预计量信息进行展示。根据需求的获取,已经确定了要
物料需求计划MRP的基本计算模型
物料需求计划M R P的基 本计算模型 Document number:PBGCG-0857-BTDO-0089-PTT1998
物料需求计划(MRP)的基本计算模型 物料需求计划(MRP)的制定需要三个关键信息:MPS、BOM、库存记录。MPS是指主生产计划,BOM是指物料清单。在MRP的制定过程中,库存记录的计算方法构成了MRP的基本计算模型。所以,我们主要介绍一下MRP中的库存记录形式、以及如何计算和使用MRP的库存记录。 MRP中的库存记录又称为MRP表格。MRP表格在很多方面都与MPS记录表格类似。它所包括的内容有:计划因子、粗需求量、预计入库量、现有库存量、计划订货入库量和计划发出订货量等。它与MPS类似,将未来的需求分成一个个时间段来表示,这种时间段的单位通常是周,但有时也用日或月来表示。为了便于理解,下面结合一个例子来说明MRP表格的计算过程。 某办公家具公司,其两种主要产品(即企业要出厂的最终产品)是办公用椅A和B,其需求大致稳定:产品A每周需30个,产品B每周需20个。这两种产品都需要用到一种支架部件C。因此,对C的平均需求量是每周50个。A和B的装配期是1周。 下图1是办公椅A和B的主生产计划表格以及部件C的库存记录表格(尚未完成)。这种表格没有标准格式,该例所用的是一种常见格式。 如上图示,在这种格式中,左上方通常要标出产品名称及其性质(如上图中,表明C是支架部件),右上方表示计划因子,通常包括三项:生产批量、生产周期和安全库存量。在本例中,C的批量是230个,生产周期为2周,安全库存量为50个。这些计划因
子的量都需要预先选定。当这些值发生变化以后,管理人员必须及时更新库存记录。下面首先来看库存记录的内容和确定方法。 一、库存记录要素及其计算 ????1、粗需求量。上例中未来8周的粗需求量如图1所示。其需求量是根据C的最终产品A和B的主生产计划所决定的,但有时候需要加上一些作为配件(更换件)使用的量。 对C的需求之所以比MPS中A、B的时间提前1周,是因为MPS中所表示的各周的量实际上是指当周应该完成的量。但由于生产或装配是需要一个周期的,因此该生产指令的发出必须给出这部分时间的提前量。在该例中,第2周需150个A,其装配周期为1周,故第1周应发出生产订单,开始装配。上图1中的第2个表格表示的是考虑了生产周期之后,MPS生产订单发出的时间和生产量。同样,MRP库存记录中粗需求的需要量是指当周应准备好的量,例如,为了在第2周装完150个A,第1周必须准备好150个C。 2、预计入库量(scheduled?receipts,简称SR)。它是指订单已发出,、但货尚未收到的量。对于外购件,它现在可能处于几种状态之一:买方刚发出订单,供应商正在加工;正在从供应商至卖方的途中;已到买方、买方正在验货等。对于自加工件,它现在可能的状态包括:正在生产现场被加工;等待他的原材料和零件的到达;正在机床前排队等待加工;正从一个工序移至下一个工序等。第1周需150个C,其生产周期为2周,故至少在2周之前已发出了该生产的订单,但通常不会比提前2周更早地发出订单。 3、现有库存量(POH)。其概念与MPS中的概念相同,指每周需求被满足之后手头仍有的库存量。该记录随着每周进货或出货的情况而更新,未来各周的POH则可计算德 出。其计算公式为: 式中,It--t周末的POH; ?????SR,t--t周的预计入库量; ?????PR,t--t周的计划订货入库量; ?????GR,t--t周的粗需求; 可见,上式与MPS中的计算方式是一致的,即SR,t+PR,t相当于MPS量,GR,t相当于max(Ft,COt),这里不存在预测值或订单值的选择,因为需求是相关的、确定的。上面图1只给除了前4周的POH,在第4周,POH只剩7个,少于所要求的50个安全库存量,这是一个要求生产的信号,即要求增加PR的信号。 4、计划订货入库量(planned?receipts,简称PR)。其含义是,计划订货或生产、但订单尚未发出的订货量。这个量的意义是要保持POH的量不低于安全库存(在MPS中未考虑安全库存,保持POH非负即可)。对于某些不需要安全库存的中间物料,则如同MPS,其意义是要保持POH非负。在库存记录中所表示的PR量应包括这两种情况。
生产计划改进方案
生产计划改进方案 生产计划是依据公司经营目标的要求,合理地制定工厂在计划期的生产规模、方向目标以及计划期的产出量和相应资源的投入量等指标,合理有效的配置生产资源,以最低的成本按规定的技术要求和期限生产满足市场所需要的最佳质量的产品,以实现公司战略目标要求。以下是本人通过对工厂生产计划问题的研究,得出方案不合理,从而探讨对生产计划改进方案设计 本公司是一家已经建厂多年的企业,存在的问题一般都不是一朝一夕所致,仔细考虑后发现,之所以生产计划方面会出现这么多不合理的现象,而且此类现象还能一直持续至今,究其根本,都有着其更深层次的大原因,有些属于该行业的“通病”,而有些,则是我们公司所特有的。下面,分别从现状中的各个不足之处开始分析其产生的原因。 一、生产计划的不足之处与产生的原因 (1)生产计划的制定依据不全面,且可参考性不高。由于管理方式上的缺陷,再加之内部员工多年来并没有接受相关的知识培训,于是在做计划时往往只是凭借自身的经验来做,时间久了,也就不会去考虑加入其它方面的制约因素作为计划的制定依据了。另外,对于生产能力的考虑问题,一方面是由于公司的特殊性所致。我们知道,我们公司既要生产玉石,又要负责金属加工;而且我们公司是批发零售,因此我们公司的订单一般都是采取订单或预投的方式来生产,这样所造成的结果就是给生产部门带来巨大的生产压力,在做计划时不考虑工厂的生产能力,直接下达生产命令。 (2)基础数据不够真实。A)各个工序的生产能力只能使用经验总结的方法来核算;B)就是产品零部件的生产提前周期,计划部不能准确推算出各个产品零部件的出产时间;C)工时定额基本上没有;其原因是:工厂发展较快,产品款式增加、机器设备也在增多等复杂性因素,工厂管理、配套人员未能及时跟进,于是导
mrp等计算题
MRP计算原理:根据主生产计划(MPS)、库存计划、物料清单(BOM),制定物料需求计划(MRP) 主要公式:毛需求量=独立需求量+相关需求量 计划库存量=上期期末库存量+本期订单产出量+本期预计入库量-毛需求量 净需求量=本期毛需求量-上期库存量-本期预计入库量+安全库存量BOM中各物料的数量关系 高层次与其下一层在数量上的倍数关系,由下一层旁边括号内的数字决定。 例 如: A B ┌───┼───┐┌───┼───┐ D(1) E(2) C(1) E(1) F(2) C(1) ┌─┴─┐┌─┴─ ┐┌─┴─┐ E(1) F(1) F(2) D(1) F(2) D(1) ┌─┴─ ┐┌─┴─
E(1) F(1) E(1) F(1) C、D、E、F的相关需求关系式为: C=A+B D=A+C E=2A+B+D F=2B+D+2C 计算MRP时注意三个问题 1.是否有安全库存 2.是否有批量限制 3.提前期是多少 例题1:已知1个A由2个B和1个C组成,1个B由1个D和1个C组成,各物料的提前期均为1周,下表是客户对产品A的订单需求表,运用MRP求A产品的物料需求计划。 表1
例题2.某家具公司组装餐桌,具体部件包括4个桌腿和1个桌面,提前期分别为2周和3周,组装需要1周的时间,公司接到40张餐桌的订单,需要在第5周交货,另外70张要在第7周交货,当前库存中有6张完工的餐桌,80张桌腿和44张桌面,请利用MRP求出公司的订货计划。
练习题:主生产计划: BOM: 现有库存量 净需求量 计划订单产出量 计划订单投入量 桌面的生产作业计划12345678毛需求量 计划到货量 现有库存量 净需求量 计划订单产出量 计划订单投入量
MRP计划表例题
mrp计算原理:根据主生产计划(mps)、库存计划、物料清单(bom),制 定物料需求计划(mrp) 主要公式:毛需求量=独立需求量+相关需求量 计划库存量=上期期末库存量+本期订单产出量+本期预计入库量-毛 需求量 净需求量=本期毛需求量-上期库存量-本期预 计入库量+安全库存量 bom中各物料的数量关系 高层次与其下一层在数量上的倍数关系,由下一层旁边括号内的数 字决定。 例如: a b ┌───┼───┐ ┌───┼───┐ d(1) e(2) c(1) e(1) f(2) c(1) ┌─┴─┐ ┌─┴─┐ ┌─┴─┐ e(1) f(1) f(2) d(1) f(2) d(1) ┌─┴─┐ ┌─┴─ e(1) f(1) e(1) f(1) c、d、e、f的相关需求关系式为: c=a+b d=a+c e=2a+b+d f=2b+d+2c 计算mrp时注意三个问题 1.是否有安全库存 2.是否有批量限制 3. 提前期是多少 例题1:已知1个a由2个b和1个c组成,1个b由1个d和1个c组成,各 物料的提前期均为1周,下表是客户对产品a的订单需求表,运用mrp求a 产品的物料需求计划。 例题2.某家具公司组装餐桌,具体部件包括4个桌腿和1个桌面,提 前期分别为2周和3周,组装需要1周的时间,公司接到40张餐桌的订 单,需要在第5周交货,另外70张要在第7周交货,当前库存中有6张完 工的餐桌,80张桌腿和44张桌面,请利用mrp求出公司的订货计划。 练习题: 主生产计划: bom: 库存信息以及提前期: 物料的需求计划: 例题3:某厂生产产品x,产品x的需求量见表1,并已知安全库存为 3件,批量为25件,投入提前期为1周,期初库存为8件,期初计划到货 为20件。1件产品x需要2个部件y,并已知部件y每周作为备件外售需要 量为4件,安全库存为12件,批量为60件,投入提前期为1周,期初库存 为18件,计划第1周入库50件,试用mrp方法编制x和部件y的生产作业计 划。 表1 产品x的需求量 篇二:mrp计算题
物料需求计划(MRP)
物料需求计划(MRP ) 主 题:计划体系、MRP 计算逻辑 案例目的 (1)了解制造企业基于MRP 的计划体系,了解MRP 的输入与输出。 (2)掌握MRP 的计算逻辑方法,并总结计算步骤。 (3)能够针对企业产品,开发出相应的物料需求计划。 案例内容 深圳物流设备公司生产一种工业设备用手推车,这种手推车的设计及产品结构树如图所示。
企业现有4个车轴(编码C205)和2个车轮配件(编码C206)的存货。未来5周的需求量如下:150,180,200,120,50。运用逐批法(LFL),开发所有组件的MRP。 回答如下问题: (1) 如果改变第三层组件的订货批量方法,MRP会有何变化? (2) 手推车有无必要设立安全库存? (3) 手推车的安全库存设为15或120,观察MRP的变化。 进一步练习:福特汽车公司的一系统供应商生产X,Y两种部件,福特公司对X的需求量:第三周为300台,第六周200台,第八周250台;Y的需求量为第七周400台。该供应商的现有库存:X为100,Y为30,A为70,B为0,C为200,D为800。供应商确定的安全库存:X为50,Y为30。现已知:1单位X由1单位A,2单位B组装而成,1单位B由1单位C与1单位D装配而成;1单位Y由1单位C与4单位D装配成。A的订货批量为250,D的订货批量为2000,其它物料项目的订货根据逐批法(LFL)确定。只有X 存在在途量,预计第2周收到250台。各物料提前期如下表。试写出BOM表,并使用MRP 表格开发X、Y的MRP计划。 物料项目X Y A B C D 提前期 2 3 3 2 1 2 案例提示 (1)体会BOM对MRP的重要性,了解MRP需要的输入数据; (2)体会订货批量方法的改变以及安全库存的设立对MRP 的影响; (3)进一步的练习重点体会组件D的物料需求计划的形成。
物料需求计划计算例题物料需求计划(MRP)的基本计算模型
物料需求计划计算例题物料需求计划(MRP)的 基本计算模型 物料需求计划(MRP)的基本计算模型 物料需求计划(MRP)的制定需要三个关键信息:MPS、BOM、库存记录。MPS是指主生产计划,BOM是指物料清单。在MRP的制定过程中,库存记录的计算方法构成了MRP的基本计算模型。所以,我们主要介绍一下MRP中的库存记录形式、以及计算和使用MRP的库存记录。 MRP中的库存记录又称为MRP表格。MRP表格在很多方面都与MPS记录表格类似。它所包括的内容有:计划因子、粗需求量、预计入库量、现有库存量、计划订货入库量和计划发出订货量等。它与MPS类似,将未来的需求分成一个个时间段来表示,这种时间段的单位通常是周,但有时也用日或月来表示。为了便于理解,下面结合一个例子来说明MRP表格的计算过程。 某办公家具公司,其两种主要产品(即企业要出厂的最终产品)是办公用椅A和B,其需求大致稳定:产品A每周需30个,产品B每周需20个。这两种产品都需要用到一种支架部C。因此,对C的平均需求量是每周50个。A和B的装配期是1周。
下图1是办公椅A和B的主生产计划表格以及部C的库存记录表格(尚未完成)。这种表格没有标准格式,该例所用的是一种常见格式。 如上图示,在这种格式中,左上方通常要标出产品名称及其性质(如上图中,表明C是支架部),右上方表示计划因子,通常包括三项:生产批量、生产周期和安全库存量。在本例中,C的批量是230个,生产周期为2周,安全库存量为50个。这些计划因子的量都需要预先选定。当这些值发生变化以后,管理人员必须及时更新库存记录。下面首先来看库存记录的内容和确定方法。 一、库存记录要素及其计算 1、粗需求量。上例中未来8周的粗需求量如图1所示。其需求量是根据C的最终产品A和B的主生产计划所决定的,但有时候需要加上一些作为配(更换)使用的量。 对C的需求之所以比MPS中A、B的时间提前1周,是因为MPS中所表示的各周的量实际上是指当周应该完成的量。但由于生产或装配是需要一个周期的,因此该生产指令的发出必须给出这部分时间的提前量。在该例中,第2周需150个A,其装配周期为1周,故第1周应发出生产订单,开始装配。上图1中的第2个表格表示的是考虑了生产周期之后,MPS生产订单发出的时间和生产量。同样,MRP库存记录中粗需求的需要量是指当周应准备好的
主生产计划及物料需求计划测试题(含答案)
MPS/MRP系统 背景资料: 主生产计划(MPS)及物料需求计划(MRP)系统就是ERP 管理软件得核心,也就是ERP系统发展得基础。通过MPS/MRP 系统将企业外部销售市场对企业得销售需求转化为企业内部得生产需求与采购需求,将销售计划转化为生产计划与采购计划。MPS/MRP管理方式可以解决“需要什么?什么时候需要?需要多少?”三大难题。相对与手工管理来说,MPS/MRP 计划可以大大提高计划下达得效率,并大大增加计划得准确性、及时性,从根源及计划层面杜绝不必要得库存,减少浪费。 某ERP系统得主生产计划管理系统融先进得MRP管理思想与软件设计之中,通过主生产计划MPS(MasterProduction Schedule),将独立得需求(销售或预测)作为需求,考虑现有库存、已分配量、预计入库等因素,通过BOM向下展开需求,得到主要产品(MPS 类物料)得计划量。主计划员可以对该计划量进行维护、确认或进行粗能力计划,将能力得影响体现在计划得改变上。对确定得计划订单,也可作为预计入库量,实现滚动计划功能。MPS 计算产生得计划订单经过确认,除可以生成本身得生产计划外,还可以将相关需求传输到MRP 系统,作为MRP 得需求来源。 主生产计划得需求来源分为两个方面,一个就是客户订单,另一个就是预测订单。客户订单与预测订单两者形成MPS/MRP得需求有三种方式即仅为客户订单,仅为预测订单与客户订单+预测订单得某种组合。这种组合关系系统提供了五种处理方式: ?客户订单+预测订单,不冲销 ?客户订单+预测订单,向前冲销 ?客户订单+预测订单,向后冲销 ?客户订单+预测订单,先向前冲销再向后冲销 ?客户订单+预测订单,先向后再向前冲销。 企业计划员可以根据实际情况选择冲销策略,并设定相应得冲销范围。系统内部冲销得顺序为:按指定得最早得N日开始冲销,再进行N+1日得冲销,直至冲销完毕或超过设定得日期、 在进行MPS/MRP 计算时,可以定义不同得计划方案。计划方案得参数不同,计算得结果也完全不一样。需要设定得参数包括六类,分别为:需求参数、计算参数、合并参数、投放参数、仓库参数、其她参数。 MPS计算得步骤为: 1、预检查 该步骤实现运算前对BOM得合法性、完整性及物料得低位码进行检查及维护,从而保证MPS/MRP 运算结果得正确性。包括:BOM 单嵌套检查、BOM 单完整性检查、低位码维护,产生物料得低位码,为进行MPS/MRP 计算时进行需求传递做好准备、 2、指定计划方案 该步骤用以选择运算编号、运算方案与设置运算开始、结束日期。 3、获取需求 该步骤根据〖计划方案〗设置得计划计算范围展示要参与本次计算得需求信息,主要就是获取参与运算得需求单据与物料。计划计算范围共分四种:全部计划对象、指定需求单据、指定物料、指定计划员。 4、显示预计量 本步骤将对参与本次计算得所有预计量信息进行展示。根据需求得获取,已经确定了要