可逆式轧机翘头分析

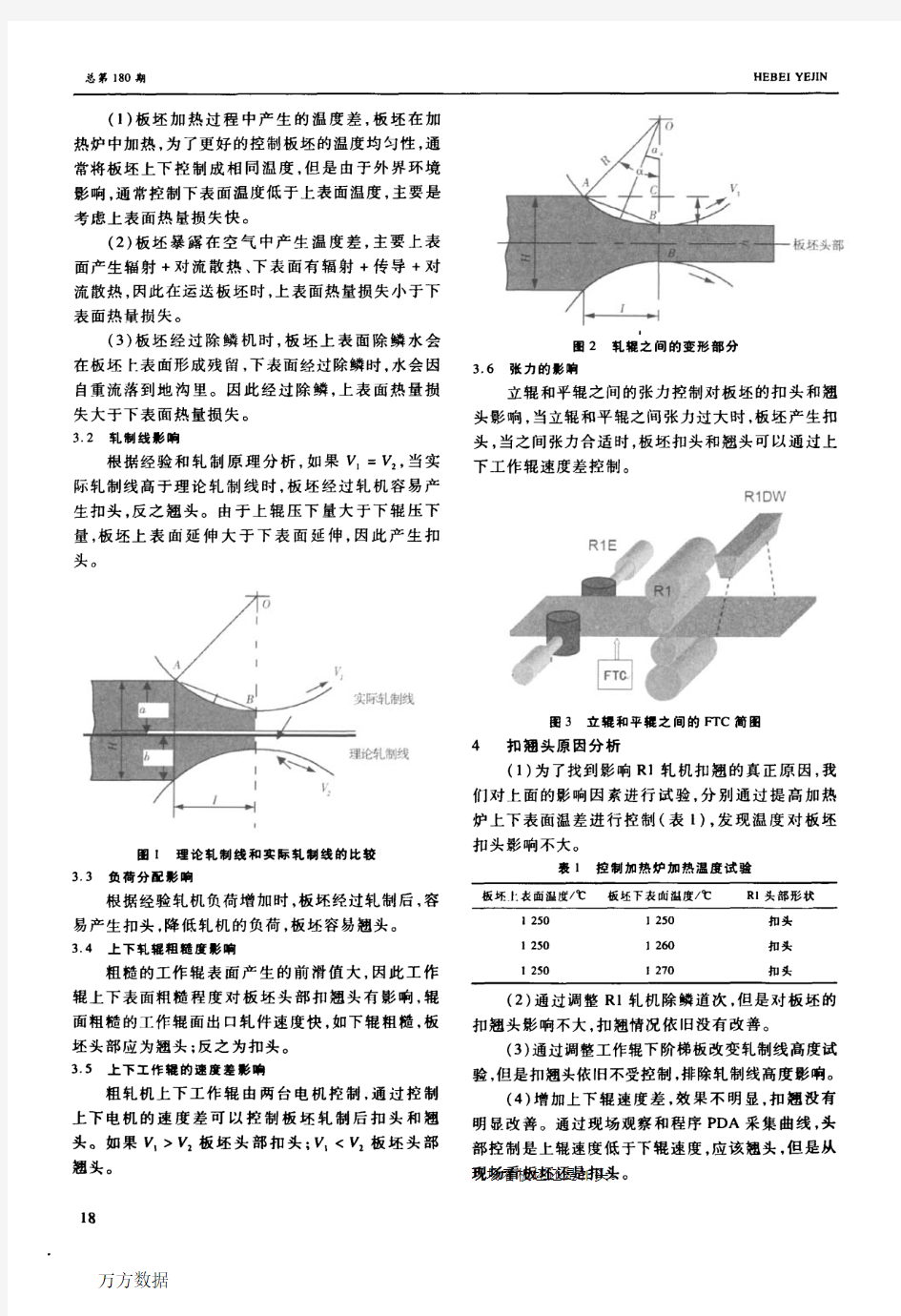
总第180期
(1)板坯加热过程中产生的温度差,板坯在加
热炉中加热,为了更好的控制板坯的温度均匀性,通
常将板坯上下控制成相同温度,但是由于外界环境
影响,通常控制下表面温度低于上表面温度,主要是
考虑上表面热量损失快。
(2)板坯暴露在空气中产生温度差,主要上表
面产生辐射+对流散热、下表面有辐射+传导+对
流散热,因此在运送板坯时,上表面热量损失小于下
表面热量损失。
(3)板坯经过除鳞机时,板坯上表面除鳞水会图2轧辊l之间的变形部分
在板坯卜表面形成残留,下表面经过除鳞时,水会因3.6张力的影响
自重流落到地沟里。因此经过除鳞,上表面热量损立辊和平辊之间的张力控制对板坯的扣头和翘失大于下表面热量损失。头影响,当立辊和平辊之间张力过大时,板坯产生扣3?2轧制线影响头,当之间张力合适时,板坯扣头和翘头可以通过上根据经验和轧制原理分析,如果Ⅵ=K,当实下工作辊速度差控制。
际轧制线高于理论轧制线时,板坯经过轧机容易产
生扣头,反之翘头。由于上辊压下量大于下辊压下
量,板坯上表面延伸大于下表面延伸,因此产生扣
头。
图l理论轧制线和实际轧制线的比较
3.3负荷分配影响
根据经验轧机负荷增加时,板坯经过轧制后,容易产生扣头.降低轧机的负荷,板坯容易翘头。
3.4上下轧辊粗糙度影响
粗糙的工作辊表面产生的前滑值大,因此工作辊上下表面粗糙程度对板坯头部扣翘头有影响,辊面粗糙的工作辊面出口轧件速度快,如下辊粗糙,板坯头部应为翘头;反之为扣头。
3.5上下工作辊的速度差彰响
粗轧机上下工作辊由两台电机控制,通过控制上下电机的速度差可以控制板坯轧制后扣头和翘头。如果V,>K板坯头部扣头;V。<V2板坯头部翘头。
18
图3立辊和平辊之间的PTC衙围
4扣翘头原因分析
(1)为了找到影响R1轧机扣翘的真正原因,我们对上面的影响因素进行试验,分别通过提高加热炉上下表面温差进行控制(表1),发现温度对板坯扣头影响不大。
表l控制加热炉加热温度试验
(2)通过调整Rl轧机除鳞道次,但是对板坯的扣翘头影响不大,扣翘情况依旧没有改善。
(3)通过调整工作辊下阶梯板改变轧制线高度试验,但是扣翘头依旧不受控制,排除轧制线高度影响。
(4)增加上下辊速度差,效果不明显,扣翘没有明显改善。通过现场观察和程序PDA采集曲线,头部控制是上辊速度低于下辊速度。应该翘头,但是从
现场看板坯还是扣头。
河北冶金2010年第6期
(5)从表2中的数据看出,立辊有压下量时,Rl轧机扣头不可控制,当立辊没有压下量时,板坯通过Rl轧机的上下电机速度差可以控制板坯的扣头和翘头。由此断定立辊和平辊在连轧时,速度不匹配,立辊和平辊之间张力过大,导致R1轧机扣头不受控制。
从图4中可以看出,立辊抛钢后,Rl平辊上下速度可以很好匹配,上下辊电机负荷平衡效果很好。
圈4RI扣头轧机速度曲线
通过空过立辊轧机。Rl轧机扣头和翘头明显受到控制,可以自由通过调整雪橇值控制控制板坯头部扣头和翘头形状。通过上面速度图4可以看出,影响RI扣头主要原因是El轧机,通过空过El轧机。Rl轧机单独可以控制扣头和翘头,平辊上下辊速度平衡良好。当立辊抛钢后,速度控制良好。5解决措施
找到真正原因后,由工艺人员、传动人员和一级人员进行分析,认为是由于立辊和平辊之间的张力不合理造成的。采取的措施是:修改RI轧机平辊后滑值,由原来20%降低到10%,调整雪橇值控制长度由原来600mm改为1200mm,负荷平衡投入时序由原来雪橇值控制结束后开始到延时500ms后开始,Rl的扣头和翘头明显好转。
圈5调整后RI轧机速度曲线
图4和图5对比,明显看出上下辊电机速度匹配良好,轧机扣头和翘头明显能够控制,对于提高轧机节奏,保护辊道和轴承寿命起到至关重要作用。调整完参数后。经过R1轧机轧制完成后,板坯头部形状良好,对后续轧制节奏提高和辊道寿命延长有很大作用。
19
轧机单独驱动辊道的结构分析
轧机单独驱动辊道的结构分析 单独驱动辊道每一个辊子或每两个辊子由各自的电动机驱动,一般用来运输长轧件。由于每个辊子承受负荷较小,所以采用单独驱动辊道可使辊道结构简单。 根据电动机固定方式,单独驱动辊道可分为普通地脚固定式、法兰盘式以及空心轴端部悬挂式。 当辊道速度较高时,辊子可以不通过减速装置而由电动机直接驱动。此时,如果采用地脚固定式或法兰盘式电动机,一般通过万向联轴节、齿轮联轴节或弹性联轴节与辊子连接。如果采用空心轴电动机,则将电动机直接装在悬臂轴上,通过键和螺栓固定。这种电动机外壳上有凸耳,通过弹簧支撑在辊子轴承座的凸耳上,以防电动机外壳转动。由于空心轴电动机悬臂地套在辊子轴上,对辊子轴及其轴承装置受力不利。现场使用时,往往出现辊子轴变弯,一侧轴承座螺栓松动等问题。 采用法兰盘式电动机的单独驱动辊道当辊道速度较高时,由于低速电动机价格较贵,一般都选用速度较高的电动机,通过齿轮减速后传动辊子。近年来,摆线或渐开线行星减速机在单独驱动辊道中也得到了应用。 集体驱动辊道集体驱动辊道由4~10个辊子组成一组,并由一台电动机驱动。它主要用来运输短而重的轧件,或用在辊道工作条件较繁重的场合。由于轧件重量集中在几个辊子上,使每个辊子承受较大的负荷,采用集体驱动则可以减少辊道电动机功率。 为了便于安装配置在一根长轴上的圆锥齿轮,圆锥齿轮与长轴采用动配合,而且用斜键固用斜键固定长轴上圆锥齿轮的结构形式,拆装不太方便,圆锥齿轮啮合性能也不太好。目前,有的辊道采用了无键连接结构。无键连接就是具有一定过盈量的静配合连接,靠配合面间的摩擦力矩传递扭矩。采用无键连接,可以不削弱长轴的强度,提高了承受冲击载荷的能力,结构简单,制造加工方便。中国冶金行业网 运输辊道的主要作用是运送轧件或钢锭。受料辊道是用来接受运锭车送来的钢锭,并将其送往钢锭旋转台辊道上。根据需要钢锭在旋转台上旋转180°后,通过辊道和输入辊道送往初轧机进行轧制。由初轧机轧出的轧件,则通过轧机输出辊道送往剪切机。
六辊可逆轧机生产中出现的问题解答
轧钢中出现的问题解答 1怎样控制轧制力? 轧制力大板型不好控制,轧辊温度不均,轧辊承受能力下降。新换工作辊一般用大张力可以减少轧制力,轧制2-3卷以后可以减小。 相对而言轧制力太小厚度不好控制。可以减小张力轧辊阻力增大轧制力相对也能大一些. 2怎样控制厚度波动? 轧制过程中出现厚度波动大首先降速和减少张力差,厚度波动大的可以把监控取消。 对于厚度波动在20ym以内速度应该在500米以下,波动在20ym以上速度在300米以下。 3裂边怎样造成的? 1轧辊边部粗糙度低。 2带钢边部出现色差。 3总变形量太高,最后道次压下量太大,有可能轧后产生边裂。 4原料有边浪起鼓涨裂。 5酸洗剪边不好。 4怎样控制裂边断带? 裂边严重时减少工作辊弯辊力,降低轧制速度,减少出口张力。使带钢边部承受的张力减小,不会把裂边拉断。发现带钢边部起鼓及时更换工作辊。\ 5在轧制过程中,带纲出现跑偏错卷的原因是什么?如何处理?
在轧制过程中,带钢出现跑偏一般在穿带或甩尾时发生,造成带钢跑偏的主要原因有以下几个方面: 1由于来料的原因来料板形不好,有严重的边浪或错边,使开卷机对中装置不能准确及时地进行有效调节,造成第一道次带钢跑偏,采取措施是轧制速度不要太高,及时调节压下量侧位置或及时停车。 2操作原因由于操作压下摆动调节不合理,造成带钢跑偏。 3电气原因由于在轧制过程卷取机张力突然减小或消失造成带钢跑偏、断带。4轧辊由于轧辊磨削后有严重的锥度,使压下找不准,在轧制中给操作压下摆动增加了难度,轻者会产生严重一边浪造成板形缺陷,重者造成跑偏断带。 5开卷对中装置故障、灯管或接受装置污染等,使跑偏装置失效造成第一道次跑偏。 6主控工、机前、机后怎样控制头尾勒辊? 1在轧制带头、带尾时,主控工应该及时的加大出口张力5KN左右,启车后轧制力减小时,在把出口张力调整到工艺要求的数量。由于带头、带尾速度较低,造成轧制力大、厚度不好控制,弯辊跟不上易勒辊。 2机前、机后要及时观察轧制力、板型。轧制力大时及时加大弯辊。观察板型及时调整辊缝调偏,以免造成跑偏勒辊。 7无压偏情况下出现勒辊注意事项有那些? 一般无压偏的情况下勒辊,注意事项有:道次变形量是否过大、轧制力是否过大、弯辊力是否太小以及启车时有无失张现象。 8轧制过程中带钢表面突然出现色差该这么办?
WS轧机结构分析及设计要点
WS轧机结构分析及设计要点 钢材在国家经济发展及居民生活中发挥着重要的作用,现今,我国的钢铁产量居世界第一,在钢材的生产过程中,WS轧机是应用于板材生产中的重要设备,其主要采用的是一个工作辊可移动和工作辊弯辊技术,从而大幅度地提高板材生产的精度。在WS轧机的设计过程中,做好对于WS轧机的结构和零件的设计能够使得WS轧机的设计更为合理,产量和板材的生产精度更为优秀。 标签:四辊冷轧机;工作弯辊;辊横移;结构设计 前言 在经济快速发展的今天,对于板材的产量与生产精度提出了更高的要求,因此,做好对于新型板材的研制以满足对于板材精度的需要是现今乃至今后一段时间内轧机研究的重点。冷轧板带是近些年来应用较多的一种板材,同时随着经济的快速发展,冷轧板材的需求将会越来越大,做好对于WS轧机的研发和结构设计对于确保冷轧板材的生产有着十分重要的意义。 1 WS冷轧机工作原理 1.1 冷轧机板形控制中所面临的困难 四辊冷轧机是现今广泛应用于板材生产的重要设备,相对于二辊轧机,其通过采用较小的工作辊径和较大的支撑辊径来降低辊工作时轧制力所带来的挠度,但是,在使用过程中发现,当冷轧机的支撑辊径超过一定的范围后将会使得冷轧机无法降低其挠度对轧机所带来的影响,其主要是由于造成轧机工作辊的挠度多是由于支撑辊和工作辊之间的不均匀接触所带来的,为降低和控制外力所带来的挠度,可以采用在工作辊中突出原始磨削的凸度或是在冷轧机的工作辊中添加液压反弯装置。在辊表面添加凸度,由于凸度是定值,从而使得在冷轧机轧制过程中无法灵活的应对轧制力的变化,再加上在工作中由于热膨胀/磨损等所带来的影响将会使得冷轧板形的控制较为困难,其缺乏足够的控制能力,因此在冷轧机结构中应用不多。而在冷轧机中使用反弯装置能够更好的对板形进行控制,但是其在工作的过程中由于受到辊径强度以及轴承寿命方面的考虑,限制了其工作时的工作压力。同时对于L/D比较大的工作辊液压反弯容易使得轧制的冷轧钢带出现复合波。从而影响冷轧钢的轧制效果。随着科技的进步,现今还发展了通过加热或是冷却来对工作辊热凸度进行控制的方法或是通过改变辊内高压油压力来改变辊凸度的方法,但都并未达到预期效果,因此,需要加强对于板形控制的方法来提高板形的精度。 1.2 WS轧机的工作原理(如图1所示) 一般的四辊轧机在工作时由于结构的限制使得其在工作时支撑辊与工作辊的两端存在着“有害区”,其中“有害区”主要是指在工作中由于弯曲应力和辊变形
工程车辆传动系统扭转振动特性研究与分析
1工程车辆扭转振动动力学模型的建立 工程车辆传动系统一端通过离合器与发动机相连,输出端通过轮胎与工程车辆平动质量相连,组成了一个多质量的弹性扭转振动系统。在计算整个系统的固有频率和振型时,通常可忽略系统的阻尼,将整个传动系统看成是由多个刚性圆盘通过弹性轴连接的无阻尼振动系统。现在某型装备四缸柴油机的中型装载机传动系统为例,其扭转振动力学模型如图1-1所示。 1.1 当量转动惯量的计算 当量转动惯量J 是指将传动系统中与发动机曲轴不同转速旋转的零部件的转动惯量换算成与曲轴同转速旋转下的转动惯量,这种换算方法的原理是能量守恒。设传动轴的转动惯量为J,实际转速为ω曲轴转速为0ω,则将传动轴换算成曲轴转速0ω的当量转动惯量为 2 2 2 0212121??? ? ??=???? ??==g d d i J J J J J ω ωωω 式中,g i 为变速器的传动比。 1.2当量扭转刚度的计算 设两圆盘之间弹性轴的当量扭转刚度为d K ,则可以根据弹性变形量守恒的原理将系统中的时间扭转刚度K 换算过来。现以后桥半轴为例,相应的当量扭转刚度为 2 01??? ? ??=i i K K g d
式中,0i 为主减速器的传动比。 2传动系统扭转动力学方程 根据图1-1所示的简化的传动系统模型,可建立系统动力学方程组为 -0-)-)()(-----111010111111101010991010343332233232221122121111=+=+-=-+-=+=+)()(()()() (。。。。。。。。 。。 θθθθθθθθθθθθθθθθθθθθθK J K K J T K K J T K K J T K J (1) 方程组(1)中,111-θθ分别为对应质量的扭转角位移;41-T T 分别为发动机1-4缸的有效输出转矩。 为了简单起见,可以将(1)改为矩阵形式的动力学方程一般式,即 T K C J =++θθθ。 。。 式中,当量转动惯量矩阵??????? ? ????? ?? ?=111021 00J J J J J 阻尼矩阵C=[0];刚度矩阵; 圆盘的角位移矩阵[]T 114321 0θθθθθθ =。 一般以发动机振动激励为系统输入矩阵,则 []T T T T T T 004 321 = 2.1扭转系统固有特性的分析 这里的固有特性是指固有频率和主振型,多自由度系统的固有频率和主振型可以根据系统的无阻尼自由振动方程得到,即 0=+θθK J 。。 (2) 假设方程的解为 t n i e ωθA = (3) 式中,A 为系统自由振动时的振幅列向量,[]T m m m m A A A A A 1132 1 =。
018-十二辊双机架可逆式轧机
国产化1400双机架十二辊可逆式冷轧机 —昆钢建成国产双机架十二辊可逆式生产线 荣太新,白艳 (北京斯蒂尔罗林科技发展有限公司) 摘要:介绍了昆钢建成的国产化1400双机架十二辊可逆式冷轧机生产线,对其运行情况、性能、新技术进行了说明,并对国产化多辊轧机前景进行展望。 关键字:双机架十二辊可逆轧机;新技术、发展趋势 Homemdae 1400mm 12-Hi Double Stand Reversing Rolling Mill RONG Tai-xin BAI Yan (BEIJING STEEL ROLLING TECHNOLOGY DEVELOPMENT CO.,LTD) Abstract:The application situation ,performance and new technique of the 1400mm 12-Hi Double Stand Reversing Rolling Mill were introduced , which was homemade and used in Kunming steel Co., Ltd .The development tendency of homemade Multi-Hi Rolling Mill were pointed out. Key words: 12-Hi Double Stand Reversing Rolling Mill;new technique development tendency 昆钢集团于2006年建成由北京斯蒂尔罗林科技发展有限公司整体设计的十二辊双机架可逆式轧机生产线。目前己正常生产,运情情况良好,经昆钢工程质监站按国家冶金工程质量验收标准核算验为冶金工程优良项目。设计辊面宽1400mm,最高轧速10m/s,最高产量15万吨。现以昆钢为例介绍十二辊双机架可逆式轧机的基本情况。 1 生产线简介 两台十二辊可逆式冷轧机,入口配有三辊直头机以矫直带钢头,并使钢带头形成“蛇头”利于穿带,机前、机后各有一台卷取机,轧机出、入口及机架中间各配有一个测厚仪及激光测速装置。工艺流程:天车储料架上卷小车开卷机直头机垂直导卫对中张力辊测厚仪1#机架2#机架测厚仪除油机张力辊卷取机经合理道次轧制卷取机卸卷小车储料架打包称重入库 可逆式双机架机列简图
铸轧机的结构设计
铸轧机的结构设计 一台机械能否正常运转不仅与其传动系统有着密切的关系, 而且还与结构设计的合理性有着更紧密的关系, 所以本章内容的设计及说明成为本次设计关键部分.铸轧机的主要结构部分包括:轧辊装置,上机架,下机架,侧封装置,和清辊装置. 由于双辊铸轧技术是一种用双辊的表面来冷却液态钢水并使之凝固以生产薄带钢的方法,其工艺特点是液体金属在结晶凝固的同时承受压力加工和塑性变形,在很短的时间内完成从液体金属到固态薄带的全过程. 所以铸轧辊的设计是轧机能够生产高质量棒线材的核心技术. 下面我将从辊芯, 辊套及其冷却方面开始设计。 2.1 铸轧辊套材料的选择及结构设计铸轧辊主要是由一个中心部位钻有进,出水孔,表面带有沟槽的辊芯和一个辊套组成的。它是铸轧机中最关键的部件,直接响影着产品的质量。所以辊芯,辊套从材料的选择,结构的设计,加工的顺序,装配的方法到使用过程每一步都显得十分重要。 2.1.1 铸轧辊辊套材料的选择 2.1.1.1 铸轧辊辊套的工作负荷 在铸轧过程中,熔铝进入连铸机轧制区并直接同辊套外表面接触,而这个辊套的内侧则受到冷却,就是为了吸收液铝中过多的热量,把它转变成固态铝。因此,这种铸轧辊的工作能力直接取决于辊套材料的热导性,而辊套被装到辊芯上,为了保障这种辊套在高温下都能牢固的固定在辊芯上,这种辊套材料应该有很低的热膨胀率,即必须在温度为600℃时显现出足够的强度和良好的塑性。由于在运行时受到复杂载荷的作用,在辊套的表面上会产生不同程度的网状热裂纹,裂纹的扩展速率主要是由力学性能和工艺特点决定的,特别是强度和可塑性的比率。 2.1.1.2 铸轧辊材料的选择 辊套材料应具备下述特性:导热性好,耐热变负载,有相当高的强度与刚度,不与铝熔体反应,所以确定辊套时要做综合考虑,根据多方面资料搜索,铸轧机辊套通常采用如下两种材料(见表一)这两种材料能使上述所要求的性能之间达到适当的匹配!保
传动系统振动
汽车动力传动系振动分析 [ 摘要]综述了车辆动力传动系振动的研究进展从振动的角度看,车辆动力传动系可分为 弯曲振动系统和扭转振动系统目前主要采用试验模态分析和有限元等研究方法对动力传动系弯曲振动特性进行研究,建立了较为理想的弯曲振动分析模型在动力传动系扭转振动的 研究方面,许多学者对此进行了有益探索研究,并取得了一定的进展但限于分析条件,车辆 动力传动系弯曲、扭转振动耦合的研究尚不十分完善,尤其在国内,这一研究尚处于起步阶段因此,在动力传动系弯曲、扭转振动的研究已相对成熟的基础上,动力传动系的弯曲、扭 转振动耦合对其振动特性影响的研究将是今后一段时间的主要研究内容车辆是一个复杂的振动系统,它是由多个具有固有振动特性的子系统组成,作为子系统之一 的动力传动系,即包括动力总成、传动轴、驱动桥总成组成的系统是车辆振动和噪声的重要激励源从振动的角度看,车辆动力传动系可分为两个振动系统:弯曲振动系统和扭转振动系 统车辆动力传动系的弯曲振动系统和扭转振动系统不仅有各自的固有振动特性,而且还存 在一定程度的振动耦合这些不同形式的振动及其耦合,是影响车辆行驶平顺性,乘坐舒适性及动力传动系零部件使用寿命的主要原因之一,因此对车辆动力传动系的整体振动进行深入细致的研究,显得十分必要 1 动力传动系弯曲振动研究车辆动力传动系弯曲振动在很大的频率段内对车辆振动和噪声有着重要影响,动力传动系低频段内的刚体振动直接影响车辆的乘坐舒适性, 而较高频段内的弹性振动将会引起车辆 的结构共振和声学共振近年来,随着对提高乘坐舒适性、减小汽车振动要求的提高,对动力传动系弯曲振动特性的进一步研究,已显得十分迫切,国内外对动力传动系弯曲振动的研究 起步较早,在理论研究方面取得一定进展,试验研究也较为成熟建立由离散的集中质量、弹 簧、阻尼器组成的力学模型是对动力传动系弯曲振动特性进行研究分析的一种行之有效的方法後藤进[1 ]建立了具有1 1个自由度的动力传动系的弯曲振动力学模型,并通过试验验证 试验结果和计算结果取得较好一致文献[2 ]也建立了动力传动系弯曲振动多自由度力学模型,指出系统的弯曲振动是由发动机运动部件往复惯性力、传动轴的不平衡等引起的, 并通 过实验测定有关参数值,计算系统的固有频率、振型隋军[3、4]建立包括动力总成及传动轴的 5 个自由度的弯曲振动力学模型,计算系统的固有振动特性和响应, 指出动力总成的弯 曲振动是汽车飞轮壳损坏的主要原因这种建模方法及其实用性已为大量的计算和试验分析结果所证实,并且已总结出了确定模型集中质量、弹性和阻尼的一般原则,能有效地用于分析解决车辆动力传动系弯曲振动问题日臻完善的试验模态分析技术,在动力传动系弯曲振动特性的研究中得到广泛应用试验模态分析在动力传动系弯曲振动特性研究中的应用, 经历了从单个总成发展到多个总成直至整个动力传动系的过程隋军[4] 、张建文[5]对动力传动 系动力总成进行了试验模态分析,认为动力总成的弯曲振动是造成汽车离合器壳开裂的主 要原因余龄[6] 利用试验模态分析技术测定了包括动力总成及传动轴的组合系统的一阶弯曲振动频率,张金换[7]则通过模态试验分析研究动力传动系传动轴的临界转速孙方宁[8, 9] 、俄延华[1 0 ] 在整车条件下,对动力传动系弯曲振动进行模态试验,得到整个动力传动系弯曲 振动的模态参数高云凯[1 1 ] 在台架及整车条件下,对汽车动力总成弯曲振动试验模态分析中的非线性特性进行研究,结果表明这一非线性特性仅存在于整车条件下的试验模态分析 试验模态分析具有快速、简便地识别结构固有特性的特点,但其精度主要取决于试验者的经 验和所使用的测试仪器、分析程序模态综合法是对动力传动系弯曲振动进行分析的有效方法,其基本思想是将动力传动系分为若干个子系统,在完成对各子系统的模态分析后, 建立 自由模态的综合方程,再利用平衡条件和约束条件将自由度简化,最后获得一个自由度大为
轧机的结构型式和性能
轧机的结构型式和性能 主要决定于轧辊的布置形式(图6)和主机座的布置形式。 1 二辊轧机:结构简单、用途广泛。它分为可逆式和不可逆式。前者有初轧机、轨梁轧机、中厚板轧机等。不可逆式有钢坯连轧机、叠轧薄板轧机、薄板或带钢冷轧机、平整机等。80年代初最大的二辊轧机的辊径为1500毫米,辊身长3500毫米,轧制速度3~7米/秒。 2 三辊轧机:轧件交替地从上下辊缝向左或向右轧制,一般用作型钢轧机和轨梁轧机。这种轧机已被高效二辊轧机所取代。 3 劳特式三辊轧机:上下辊传动,中间辊浮动,轧件从中辊的上面或下面交替通过。因中辊的直径小,可减少轧延力。常用于轧制轨梁、型钢、中厚板,也可用于小钢锭开坯。这种轧机渐为四辊轧机所取代。 4 四辊轧机:工作辊直径较小,传递轧制力矩,轧延压力由直径较大的支承辊承受。这种轧机的优点是相对刚度高、压下量大、轧延力小,可轧制较薄的板材。有可逆和连轧两种,广泛用作中厚板轧机、板带热轧或冷轧机以及平整机等。 5 五辊轧机:有两种:一种是C-B-S(接触-弯曲-拉直)轧机,它是一种带有使轧件弯曲的小直径(为工作辊的1/20)空转辊的四辊轧机,其压下量比通常的四辊轧机大许多倍。轧件围绕小空转辊发生塑性弯曲变形,可轧制难变形的金属和合金带材。另一种是泰勒轧机,中间小辊的位置可沿轧机入口或出口方向调节,以保持轧件正确的厚度,用来轧制厚度公差很小的不锈钢、碳钢和有色金属带材。 6 HC轧机:高性能的、可控制辊型凸度的轧机。相当于在四辊轧机的工作辊与支承辊之间增设一对可轴向移动的中间辊,并将两中间辊辊身的相应端部分别调整到与带钢两边缘对应的位置,以提高压力分布和工作辊弹性压扁的均匀性,保证带钢的尺寸精度并可减少其边缘的超薄量和开裂等缺陷。HC轧机宜用作冷轧宽带钢。 7 偏八辊轧机:它是四辊轧机的变型。工作辊直径为支承辊的1/6,且作相对的偏移,以防止工作辊的水平弯曲,轧制力比四辊轧机小一半。工作辊的稳定性好、水平刚度高,可用以轧制须用二十辊轧机轧制的部分产品。它的结构及其调整却比二十辊轧机简单得多。这种轧机可改装为二、四、八、十六辊几种型式,适宜多品种的需要,因而又称多用途轧机。它有可逆和连轧两种,用于冷轧难变形钢、硅钢和有色金属带材。 8 六辊轧机:由一对工作辊和两对支承辊组成,有较稳定的辊系。但它的刚性与四辊轧机相仿,且操作不便,因而应用不广,一般用于轧制高精度海底电缆的铜带。 9 多辊轧机:有十二辊、二十辊和三十六辊 3种型式。轧机中部一对直径最小
炉卷轧机的发展与典型结构
炉卷轧机的发展与典型结构 萧其林 摘要:按照传统型、改造型、现代型三个阶段叙述了炉卷轧机的发展,并对炉卷轧机的典型布局与结构进行分析。 关键词:炉卷轧机;发展;典型布局;结构 1 炉卷轧机的发展 炉卷轧机,又称斯特克尔轧机(Steckel轧机)。自美国于1932年研制出第一台试验性炉卷轧机并于1949年正式应用于工业生产以来,到现要已有近70年。近70年来炉卷轧机经历了传统型、改造型、现代型三个发展阶段。随着现代冶金技术的发展和现代传动、控制技术的应用,炉卷轧机已步入了蓬勃发展时期。本文依照传统型、改造型、现代型三个阶段对炉卷轧机的发展予以阐述。 1.1传统型炉卷轧机(1932~1960年) 炉卷轧机发明于20世纪30年代。该发明解决了成卷热轧薄板轧制过程中温度降低太快的问题,使得带卷在轧制过程中进行可逆式的往复轧制,直到轧制过程完成,这就是所谓的炉卷轧制方法。图1-1为其示意图。 图1-1 炉卷轧机示意图 1——带保温炉的卷取机;2——送料辊;3——四辊可逆轧机;4——升降导板 图1-2 炉卷轧机工艺设备布置图 1-再加热炉 2-除鳞机 3-立辊轧机 4-粗轧机 5-辊道 6-切头剪 7-左卷取炉 8-炉卷机 9-右卷取炉 10-冷却辊道 11-地下卷取机 1.1.1炉卷轧机生产工艺流程与设备布置 炉卷轧机的生产工艺流程和设备布置如图1-2。板坯在连续式加热炉中加热后,通过高压水除鳞,然后在带立辊的四辊粗轧机上分别轧制一定道次,将板坯轧成厚10~20mm的带坯,在飞剪上切除头尾,然后送入炉卷轧机进行可逆轧制。当第一道带坯头部出炉卷轧机后,右边的升降导板抬起,将带坯的头部引入右边卷取炉的卷鼓中进行卷取。卷取炉卷鼓与轧机之间带钢的张力不大,其总张力为30000N。当第一道轧件尾部一出轧辊,右边的夹送辊下降,整个机组反转,开始第二道轧制,此时左边的夹送辊和升降导板抬起,又将带钢导入左边的卷取炉进行卷取,如此反复轧制几道,即轧成所需要的带卷。由于每道轧制时轧件端部均需通过轧辊,因而每道次开始时都需以导入速度(0.5~2.5m/s)轧制,
1100HC六辊可逆式冷轧机的设计-文献综述
附录2 文献综述 一、课题的国内外现状 HC 轧机全名为HITACHI HIGH CROWNCONT ROLMILL,即日立中心高性能轧辊凸度控制轧机。该机型是日立公司于1972 年研究开发的轧机,两年后正式投入工业化应用。它具有普通四辊冷轧机不能达到的性能和优点,首先在日本得到推广使用,继而受到全世界的瞩目,广泛用于热轧和冷轧生产中的单机可逆轧机、连轧机和平整机。其主要结构特点是:在支撑辊和工作辊之间加入一对能够沿着轧辊轴向相对移动的中间辊,通过中间辊的相对移动来改变轧制压力在带钢方向上的分布,加上工作辊的正负弯辊作用,对改善带钢板形起到了明显的效果。 在国外,除日本各大钢铁公司普遍采用HC轧机机型外,美国、德国、加拿大、瑞典、巴西、墨西哥、韩国等国家均从日本引进了该轧机。 在国内,武汉钢铁公司为生产镀锡板基板,1987年首先引进1250HC六辊轧机,之后上海宝钢、辽宁鞍钢等国内各大钢铁公司先后引进了这种轧机机型。在引进设备的同时,国内相关单位也开始跟踪并开发国产的HC六辊轧机。国产大型六辊轧机已成功地用于工业生产,而且主要的技术水平和功能已达到国外同类设备水平。但是,六辊轧机种工作辊弯辊、中间辊横移、中间辊弯辊三种方式与带材板型的检测、控制相结合,实施有效的闭环控制,目前国内虽然在这方面也取得了不少成绩,但在精确度和稳定性方面仍然需要花大力气研究。 二、现有的主要研究成果 随着科学技术的不断进步,日本最近几年又在HC轧机的结构上进行了改进,推出了一些新型的HC轧机。例如,HCMW 轧机是综合HC轧机和HCM轧机的优点,其特点是中间辊和工作辊都能轴向移动。 在国内,HC轧机方面的研究也取得了很多可喜的成绩:降低轧辊表面缺陷的措施,预防轧辊剥落的措施,预防轧辊断裂的措施。近几年来,随着控制理论的发展,人们不断把一些新型控制方法引入板形自动控制系统中,以弥补PID控制中很难满足高精度控制要求的不足,比如基于动态负荷分配的板形控制方法。在日本,成品机架或成品道次采用软刚度的方法
含有故障的齿轮系统扭转振动分析
第22卷 第4期2007年12月 北京机械工业学院学报 Journa l of Be ijing Institute o fM ach i nery V o.l22N o.4 D ec.2007 文章编号:1008-1658(2007)04-0013-05 含有故障的齿轮系统扭转振动分析 朱艳芬1,陈恩利1,申永军1,王翠艳2 (1.石家庄铁道学院 机械工程分院,石家庄050043;2.石家庄铁道学院 工程训练中心,石家庄050043) 摘 要:建立了故障单自由度齿轮系统扭转振动的数学模型,采用加入脉冲的形式进行故障模拟,并利用数值方法进行对该模型进行仿真,进行定性研究。作出了系统模型的幅频响应曲线,与无故障时的曲线相比较,发现在低速时脉冲对系统的影响较大。另外,还对该模型进行了参数研究,分别比较了在不同阻尼比和不同激振力情况下的脉冲对系统幅频曲线的影响。 关 键 词:单自由度直齿轮系统;扭转振动;数值方法;幅频响应曲线;参数研究 中图分类号:TH113 文献标识码:A Analysis of torsional vibration of a spur gear system w ith faults ZHU Y an-fen1,C H E N Een-li1,SH E N Yong-jun1,WANG Cu-i yan2 (1.Schoo l ofM echan i calEng i neeri ng,Shiji az huang Rail w ay Ins tit u te,Sh iji az huang050043; 2.Eng i neeri ng Tra i n i ng C enter,Sh iji az hu ang Rail w ay I n stitute,Sh ijiazhuang050043) Abstract:The torsional v i b ration m odel o f the spur sing le-DOF gear syste m w it h fau lts is bu il,t and the for m o f the pulses is adop ted to si m u late the faults.Th i s m ode l is ca lculated by usi n g the num erica l m ethod.The response o f the m ode l is ana lyzed,and the Am p litude frequency Curves are p l o tted,and t h e greater fl u ence of the pu lse is found in the lo w frequency.The para m eters of the mode l are researched, and the Am plitude-frequency Curves under vari o us da m pi n g ratio and under vari o us exc iting-v ibration force are co m pared respectively. Key w ords:spur si n gle-DOF gear syste m;torsi o na l v ibration;num erica lm ethod;t h e Am plitude-fre-quency Curves;para m eters study 齿轮作为机械系统中的重要传动装置,在机械、化工、航天等行业的装备中起着非常关键的作用。为了满足航空、航天及机器人等技术发展的需要,采用传统的线性分析和控制理论已难以满足这一要求。由于零部件间的间隙、运动负重的摩擦及时变刚度等因素,实际的齿轮传动系统都是非线性系统,传统的线性分析和控制是对其进行的一种近似处理,只有对齿轮传动系统实施非线性分析和非线性控制才能获得精度高、振动小和噪声低等性能的齿轮传动系统。齿轮的工作状态正常与否对运动和动力的传输具有重要的影响[1]。因此,研究齿轮系统的动力学与故障诊断具有重要的理论价值和工程意义。 关于带故障的齿轮系统动力学建模及动力学分析则见于Parey的文章[2],其中的缺陷主要包括摩擦、磨损、点蚀和剥落等,介绍了带有故障的各种齿轮动力学模型等,另外,Kuang[3]等人建立了考虑齿面磨损的齿轮动力学方程,齿面磨损会影响啮合过程中的齿面轮廓,从而会影响到啮合刚度、阻尼力以及摩擦力等,这样将会使得系统的方程非常复杂。 本文从单自由度齿轮系统入手,经过模型简化,模拟了齿轮系统故障引起的刚度变化后的齿轮模型,并定性地分析了其动力学特性。 1故障单自由度齿轮系统理论模型 首先建立正常直齿轮副扭转振动的数学模型。扭转振动模型是仅考虑系统扭转振动的模型,在齿轮系统的振动分析中,若不考虑传动轴的横向和轴向弹性变形以及支承系统的弹性变形,则可将系统简化成纯扭转的振动系统,在实际工程中许多复杂 收稿日期:2007-09-04 基金项目:国家自然科学基金资助项目(10602038) 作者简介:朱艳芬(1976-),女,河北藁城人,石家庄铁道学院机械工程分院硕士研究生,主要从事机械系统动力学控制等研究。
四辊可逆式冷轧机辊系设计
太原科技大学 毕业设计(论文)设计(论文)题目:四辊可逆式冷轧机的辊系设计 姓名 学院(系) 专业 _ 年级 _08级 指导教师 2011年 6月10日
太原科技大学毕业设计(论文)任务书 学院(直属系):时间:2011 年 6 月10 日 说明:一式两份,一份装订入学生毕业设计(论文)内,一份交学院(直属系)。
目录 摘要................................................................... II A BSTRACT................................................................... III 第1章绪论. (1) 1.1冷轧机的发展概况 (1) 1.2四辊可逆式冷轧机的发展 (1) 1.3冷轧带钢生产发展与新技术 (2) 1.3.1冷轧带钢生产技术设备的发展 (2) 1.3.2冷轧窄带钢轧机的技术特点 (3) 第2章轧辊 (5) 2.1冷轧轧辊的组成 (5) 2.2轧辊材质的选择 (5) 2.3辊系尺寸的确定 (6) 2.4轧辊力能参数计算 (7) 2.4.1基本参数 (7) 2.4.2艾克隆德方法计算轧制时的平均单位压力 (8) 2.4.3轧辊传动力矩 (11) 2.5轧辊的强度校核 (12) 第3章轧辊轴承 (16) 3.1轴承的选择 (16) 3.2轴承寿命计算 (16) 3.3轧辊轴承润滑 (17) 参考文献 (18) 致谢 (19) 附录1英文原稿 (20) 附录2英文翻译 (24)
四辊可逆式冷轧机的辊系设计 摘要 这篇文章主要讲述了冷轧机生产与发展概述,通过运用已知参数,如钢板的厚度、宽度、轧制速度和压下速度等,对工作辊、支撑辊及相关尺寸进行了计算和校核,然后选择合适的轧辊材质和轴承,并对轴承寿命进行计算和校核。 四辊可逆式冷轧机,衔接连铸后的技术工艺,减少工艺,可实现往返可逆轧制。四辊轧机还能提供较大的轧制压力,提高软件的可轧硬度范围,实现产品规格多样化。 关键词:四辊可逆式;冷连轧;工作辊
炉卷轧机的发展与典型结构精编
炉卷轧机的发展与典型结 构精编 High quality manuscripts are welcome to download
炉卷轧机的发展与典型结构 萧其林 摘要:按照传统型、改造型、现代型三个阶段叙述了炉卷轧机的发展,并对炉卷轧机的典型布局与结构进行分析。 关键词:炉卷轧机;发展;典型布局;结构 1 炉卷轧机的发展 炉卷轧机,又称斯特克尔轧机(Steckel轧机)。自美国于1932年研制出第一台试验性炉卷轧机并于1949年正式应用于工业生产以来,到现要已有近70年。近70年来炉卷轧机经历了传统型、改造型、现代型三个发展阶段。随着现代冶金技术的发展和现代传动、控制技术的应用,炉卷轧机已步入了蓬勃发展时期。本文依照传统型、改造型、现代型三个阶段对炉卷轧机的发展予以阐述。 1.1传统型炉卷轧机(1932~1960年) 炉卷轧机发明于20世纪30年代。该发明解决了成卷热轧薄板轧制过程中温度降低太快的问题,使得带卷在轧制过程中进行可逆式的往复轧制,直到轧制过程完成,这就是所谓的炉卷轧制方法。图1-1为其示意图。 图1-1 炉卷轧机示意图 1——带保温炉的卷取机;2——送料辊;3——四辊可逆轧机;4——升降导板
图1-2 炉卷轧机工艺设备布置图 1-再加热炉 2-除鳞机 3-立辊轧机 4-粗轧机 5-辊道6-切头剪 7-左卷取炉 8-炉卷机 9-右卷取炉 10-冷却辊道 11- 地下卷取机 1.1.1炉卷轧机生产工艺流程与设备布置 炉卷轧机的生产工艺流程和设备布置如图1-2。板坯在连续式加热炉中加热后,通过高压水除鳞,然后在带立辊的四辊粗轧机上分别轧制一定道次,将板坯轧成厚10~20mm的带坯,在飞剪上切除头尾,然后送入炉卷轧机进行可逆轧制。当第一道带坯头部出炉卷轧机后,右边的升降导板抬起,将带坯的头部引入右边卷取炉的卷鼓中进行卷取。卷取炉卷鼓与轧机之间带钢的张力不大,其总张力为30000N。当第一道轧件尾部一出轧辊,右边的夹送辊下降,整个机组反转,开始第二道轧制,此时左边的夹送辊和升降导板抬起,又将带钢导入左边的卷取炉进行卷取,如此反复轧制几道,即轧成所需要的带卷。由于每道轧制时轧件端部均需通过轧辊,因而每道次开始时都需以导入速度(0.5~2.5m/s)轧制,使轧件端部平滑进入卷鼓的槽口。导入后,卷鼓和轧机同步升速到正常轧制速度。而在每道次终了时,则必须及时制动,以防轧件尾部进入保温炉内。这样频繁改变的操作制度必须依赖自动控制才能实现,同时也限制了轧
单机架六辊可逆冷轧机电气自动化技术方案(精)
1200六辊可逆冷轧机电气自动化系统控制方案
1概述 根据《1200六辊可逆冷轧机技术规格电气招标书》所提供的工艺设备和技术要求,并参考了同类型的单机架六辊可逆冷轧机的工艺技术,编写了本电气传动及基础自动化控制的技术方案。 2 供电 2.1 电气设备运行条件 1)电气设备运行环境要求 环境温度 现场:0~40?C 电气室:10~35?C 操作室:25±5?C 空气湿度:相对湿度≤95%且无凝露; 污染等级:III级,无火灾爆炸危险、无导电性尘埃、不腐蚀金属物及不破坏绝缘介质的环境。 2)电气设备运输及储存环境要求 环境温度-20~65?C ; 空气湿度及污染等级要求与运行时相同。 3)电气设备使用的电压等级及技术条件 本机组所使用电气设备电压等级符合我国国家标准,主要用电设备的电压等级为: ◆供电电压及频率:10±5%kV,50±1Hz ◆低压供电电压:AC380/220V ◆交流电动机电压:AC380V ◆直流电动机电压:DC440~660V ◆电磁阀:DC24V
◆电磁抱闸:AC220V ◆控制电压:AC220V,DC24V ◆保护地:接地电阻<4Ω ◆系统地:接地电阻<4Ω 2.2低压供配电 辅传动供电系统 (1)辅传动供电系统单线图见MCC单线图。 (2)MCC设备(见附表) 由于本机组负荷较小,因此不设负荷中心。本机组负荷MCC(即马达控制中心)将采用GGD3柜,包含MCC的受电、馈出回路、UPS 系统、比例、伺服阀控制回路和照明开关柜,开关柜额定短路短时承受能>80kA/s。 额定短路分断能力与电网短路电流相适应,Icu >50kA 根据需要配置必要的电流、电压表计,端子板采用Phoenix端子。 单机架可逆冷轧机组设一套MCC,不同容量不同控制类型的回路至少有一个备用回路。 注①:主传动电动机均配置有空间加热器,这些加热器是在长期停机时防止电机绕组受潮而设置的。由本MCC供电。 注②:为了保证乳化液站的检修供电,需要检修电源或者备用一路供电回路。 (3) UPS电源 为保证控制系统运行的可靠性,机组设置一套容量为10kV A的UPS 电源为机组控制系统(PLC、AGC控制器、HMI设备等)提供可靠稳定电源。电池和逆变器选用进口产品。 容量:10kV A,30min;进线:220V AC
950可逆式轧机压下系统的设计
950可逆式轧机压下系统的设计 摘要 随着世界经济的迅猛发展,市场对钢铁的需求量随着提高,对质量的要求也不断的提高,轧钢生产中,初轧机无可替代,初轧机起着很关键的作用,而在初轧机中,压下系统装置尤为重要,此文中设计的是φ950可逆式轧机的压下系统。在文中大致的介绍初轧机发展的情况以及发展的趋势,了解φ950可逆式轧机的主传动,考虑压下螺丝的阻塞问题,确定了φ950可逆式轧机的压下系统的方案选择,通过φ950钢坯轧制表中断面尺寸和压下量计算轧制力,确定压下系统合适的电机、减速机、联轴器、以及压下系统中重要的零件部分,压下螺丝和压下螺母的尺寸,通过计算对压下螺丝和压下螺母进行校核,除此之外,设计合适尺寸的蜗轮蜗杆,最后说明一下机械设备的润滑、环保、以及经济性分析。 关键词:压下系统;涡轮蜗杆;校核
Design of 950 reversible mill system Abstract With the rapid development of the world economy, market demand for iron and steel with the increase, of quality requirements are also constantly improve rolling production, blooming mill is irreplaceable, blooming mill plays a very crucial role, and in blooming mill, the pressure system device is particularly important. In this paper, the design of the is Phi 950 reversing mill pressure system. In this paper we introduce the bloomingmill development situation and development trend, understand the main drive with 950 reversible rolling mill, considering blocking screw, determine the choice of the 950 reversible rolling mill press down system, the section size of phi 950 billet rolling table and calculating rolling force, pressure system determine the appropriate motor, reducer, coupling, and some important parts of the system under pressure, pressure screw and nut size under pressure, through the calculation of the pressure screw and nut pressure check, in addition, the design of suitable worm size, the analysis of mechanical equipment lubrication, environmental protection, and economic. Keywords: pressure system;turbine worm;check
传动系统振动
汽车动力传动系振动分析 [摘要 ]综述了车辆动力传动系振动的研究进展从振动的角度看 ,车辆动力传动系可分为弯曲振动系统和扭转振动系统目前主要采用试验模态分析和有限元等研究方法对动力传动系弯曲振动特性进行研究 ,建立了较为理想的弯曲振动分析模型在动力传动系扭转振动的研究方面 ,许多学者对此进行了有益探索研究 ,并取得了一定的进展但限于分析条件 ,车辆动力传动系弯曲、扭转振动耦合的研究尚不十分完善 ,尤其在国内 ,这一研究尚处于起步阶段因此 ,在动力传动系弯曲、扭转振动的研究已相对成熟的基础上 ,动力传动系的弯曲、扭转振动耦合对其振动特性影响的研究将是今后一段时间的主要研究内容 车辆是一个复杂的振动系统,它是由多个具有固有振动特性的子系统组成,作为子系统之一 的动力传动系,即包括动力总成、传动轴、驱动桥总成组成的系统是车辆振动和噪声的重要激励源从振动的角度看,车辆动力传动系可分为两个振动系统:弯曲振动系统和扭转振动系统车辆动力传动系的弯曲振动系统和扭转振动系统不仅有各自的固有振动特性,而且还存在一定程度的振动耦合这些不同形式的振动及其耦合,是影响车辆行驶平顺性,乘坐舒适性及动力传动系零部件使用寿命的主要原因之一,因此对车辆动力传动系的整体振动进行深入细致的研究,显得十分必要 1 动力传动系弯曲振动研究 车辆动力传动系弯曲振动在很大的频率段内对车辆振动和噪声有着重要影响,动力传动系低频段内的刚体振动直接影响车辆的乘坐舒适性,而较高频段内的弹性振动将会引起车辆的结构共振和声学共振近年来,随着对提高乘坐舒适性、减小汽车振动要求的提高,对动力传动系弯曲振动特性的进一步研究,已显得十分迫切,国内外对动力传动系弯曲振动的研究起步较早,在理论研究方面取得一定进展,试验研究也较为成熟建立由离散的集中质量、弹簧、阻尼器组成的力学模型是对动力传动系弯曲振动特性进行研究分析的一种行之有效的方法後藤进[1 ]建立了具有 1 1个自由度的动力传动系的弯曲振动力学模型,并通过试验验证,试验结果和计算结果取得较好一致文献[2 ]也建立了动力传动系弯曲振动多自由度力学模型,指出系统的弯曲振动是由发动机运动部件往复惯性力、传动轴的不平衡等引起的,并通过实验测定有关参数值,计算系统的固有频率、振型隋军[3、4]建立包括动力总成及传动轴的5个自由度的弯曲振动力学模型,计算系统的固有振动特性和响应,指出动力总成的弯曲振动是汽车飞轮壳损坏的主要原因这种建模方法及其实用性已为大量的计算和试验分析结果所证实,并且已总结出了确定模型集中质量、弹性和阻尼的一般原则,能有效地用于分析解决车辆动力传动系弯曲振动问题日臻完善的试验模态分析技术,在动力传动系弯曲振动特性的研究中得到广泛应用试验模态分析在动力传动系弯曲振动特性研究中的应用,经历了从单个总成发展到多个总成直至整个动力传动系的过程隋军[4]、张建文[5]对动力传动系动力总成进行了试验模态分析,认为动力总成的弯曲振动是造成汽车离合器壳开裂的主要原因余龄[6]利用试验模态分析技术测定了包括动力总成及传动轴的组合系统的一阶弯曲振动频率,张金换[7]则通过模态试验分析研究动力传动系传动轴的临界转速孙方宁[8, 9]、俄延华[1 0 ]在整车条件下,对动力传动系弯曲振动进行模态试验,得到整个动力传动系弯曲振动的模态参数高云凯[1 1 ]在台架及整车条件下,对汽车动力总成弯曲振动试验模态分析中的非线性特性进行研究,结果表明这一非线性特性仅存在于整车条件下的试验模态分析试验模态分析具有快速、简便地识别结构固有特性的特点,但其精度主要取决于试验者的经验和所使用的测试仪器、分析程序模态综合法是对动力传动系弯曲振动进行分析的有效方法,其基本思想是将动力传动系分为若干个子系统,在完成对各子系统的模态分析后,建立自由模态的综合方程,再利用平衡条件和约束条件将自由度简化,最后获得一个自由度大为缩减又保持了系统特性的运动方程,即组合系统方程孙方宁[8, 9]将一大型客车动力传动系划分为五个子系统,通过试验模态分析获得各子系统的模态参数,然后利用模态综合方法建立整个系统的理论分析模型,编制计算程序,对该大型客车动力传动系弯曲振动的固有振动特性进行计算,并在激振试验台上进行整个动力传动系弯曲振动的试验模态分析,结果表明理论计算和试验结果具有很好的一致性应用模态综合方法,只需获得动力传动系各子系统的模态参数,就可以通