机械搅拌澄清池设计计算
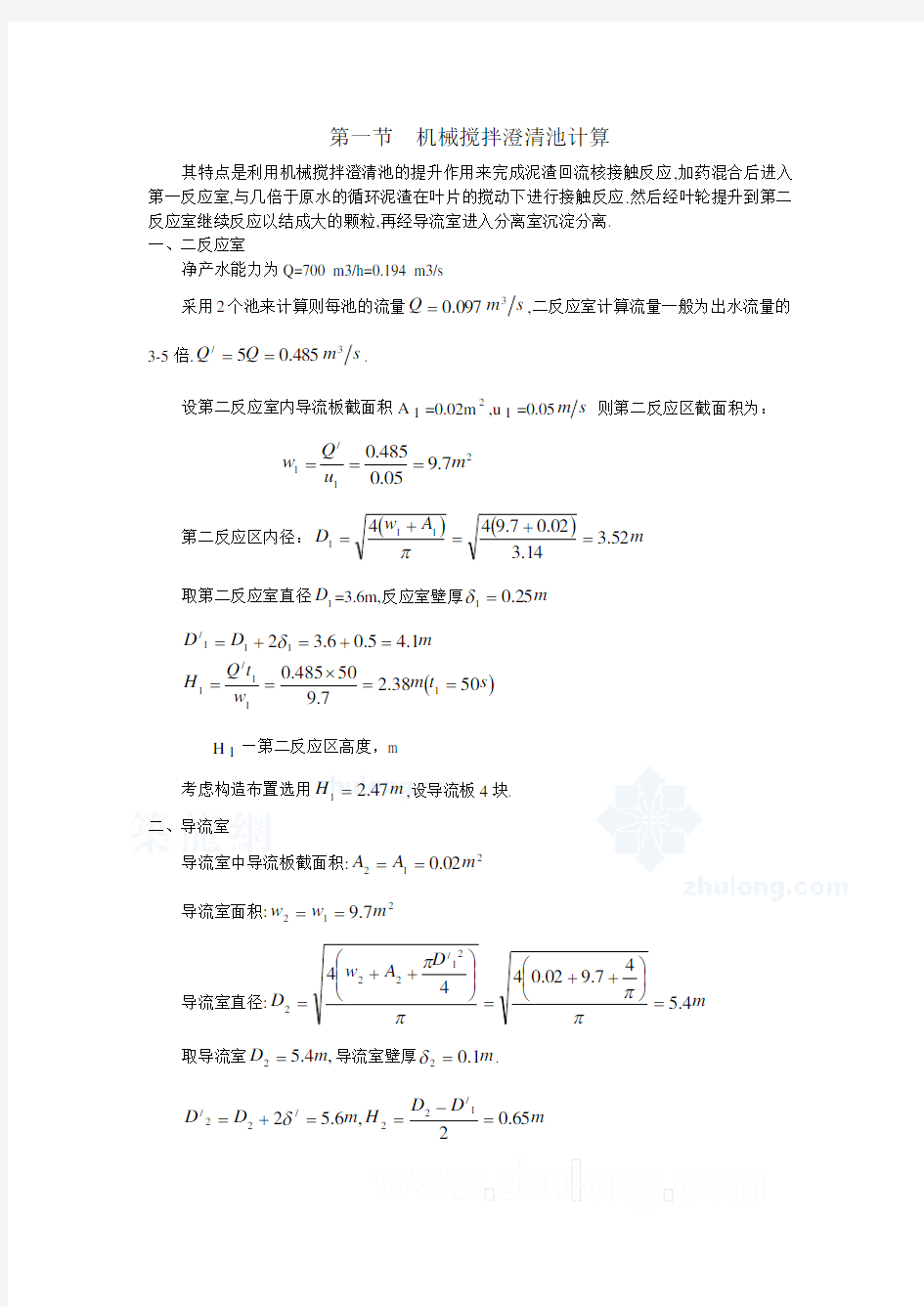

第一节 机械搅拌澄清池计算
其特点是利用机械搅拌澄清池的提升作用来完成泥渣回流核接触反应,加药混合后进入第一反应室,与几倍于原水的循环泥渣在叶片的搅动下进行接触反应.然后经叶轮提升到第二反应室继续反应以结成大的颗粒,再经导流室进入分离室沉淀分离. 一、二反应室
净产水能力为Q=700 m3/h=0.194 m3/s
采用2个池来计算则每池的流量m Q 3097.0=,二反应室计算流量一般为出水流量的3-5倍.s m Q Q 3/485.05==.
设第二反应室内导流板截面积A 1=0.02m 2
,u 1=0.05s m 则第二反应区截面积为:
21/17.905
.0485.0m u Q w ===
第二反应区内径:()
()m A w D 52.314
.302.07.944111=+=
+=
π
取第二反应室直径1D =3.6m,反应室壁厚m 25.01=δ
()
s t m w t Q H m
D D 5038.27
.950
485.01.45.06.32111/1111/==?===+=+=δ H 1—第二反应区高度,m
考虑构造布置选用m H 47.21=,设导流板4块. 二、导流室
导流室中导流板截面积:2
1202.0m A A == 导流室面积:2
127.9m w w ==
导流室直径:m D A w D 4.547.902.04442
1/222=?
?? ??
++=
???? ?
?++=
π
ππ
π
取导流室,4.52m D =导流室壁厚m 1.02=δ.
m D D H m D D
65.02
,6.521
/22/
22
/
=-==+=δ
导流室出口流速:s m u 05.06=,出口面积:26/37.905
.0485
.0m U Q A ===
则出口截面宽:()
()
m D D A H 65.01.44.514.37
.9221/233=+?=+?=
π
出口垂直高度:m H H 92.0233/=
三、分离室
分离区上升流速取s m u 0009.02=,分离室面积:2238.1070009
.0097.0m u Q w ===
。 池总面积:22
/342.1324
m D w w =+
=π
池的直径:m m w
D 1399.1242
.13244≈=?=
=
π
π
四、池深计算
池中停留时间T 设为1.5h 。
有效容积:3/8.5235.1097.036003600m QT V =??==
考虑增加4%的结构容积:()3
/
75.54404.01m V V =+=,取池超高m H 3.00=。
设池直壁高:m H 65.14=。池直壁部分的容积:342
19.2184
m H D w ==
π
313285.3259.21875.544m w V w w =-=-=+。
取池圆台高度m H 5.25=。池圆台斜边倾角450
,则池底部直径
m H D D T 851325=-=-=。
本池池底采用球壳式结构,取球冠高m H 16=。 圆台容积
[]32
25245.22025.2025.2925.42342
.922223m D D D D H w T T =++=?
?????????? ??+?
+???
??=π 球的半径:m H R 5.82
86
22=+=
球。 球冠体积:362
6364.25315.814.33m H R H w =??? ?
?
-=??? ??-
=球π
池实际容积:3/
332111.44704
.1.99.464m V
V m w w w V ===++=。 实际总停留时间:h T 28.18
.5235
.111.447=?=
池总高:m H H H H H 45.50.3165.13.06540=+++=+++= 五、配水三角槽
逆水流量增加1%的排泥水量,设槽内流速s m u 7.03=。三角槽直角边长为:
38.07
.0092
.010.110.131=?==
u Q B 三角配水槽采用孔口出流,孔口流速同3u 。 出水孔总面积=
2315.07
.0097
.010.110.1m u Q =?= 采用d=0.1m 的孔径,每孔面积为0.007854m 2
。则出水孔数=个42.191
.015
.042
=??π。 为施工方便采用沿三角槽每18
设置一孔,共20孔,孔口实际流速
s m u 68.020
1.04
097.01.12
3=????=
π 六、第一反应室
二反应室板厚m 15.03=δ。第一反应室上端直径为:
m B D D 16.515.0238.021.422311/3=?+?+=++=δ
第一反映室高:
06
.01.0094.04415.011.903.22
16
.59203.215.047.25.265.1424
42//473431/547===
===++=++=
=--+=--+=δπδ,设裙板厚为,取回流缝宽度:泥渣回流量取m B m u D Q
B Q Q s m u m H D D D m H H H H T
伞形板下端圆柱直径为:
()()
m H H H H m D D H m D D H m B D D T 77.035.041.053.135.02
8
7.8241.07.811.97.806.01.02211.922108795105484245=--=--==-=-=
=-=-==+?-=+-=。
按等腰三角形计算:
δ
H8—伞形板下檐圆柱体高度
H10—伞形板离池底高度
H9—伞形板锥部高度
七、容积计算
()()
()()
()()3
2
1
/
1
3
3
1
1
1
2/
2
1
2
1
2
3
3
5
5
10
8
2
5
5
5
3
2
3
9
1
29
.
317
38
.
45
44
.
84
11
.
447
38
.
45
25
.
20
13
.
25
4
4
44
.
84
12
5
12
m
V
V
V
V
m
B
H
D
D
H
D
V
m
W
D
D
D
D
H
H
D
D
D
D
D
H
V
T
T
=
+
-
=
+
-
=
=
+
=
-
-
+
=
=
+
+
+
+
+
+
+
=
π
π
π
π
π
V1—第一反应区容积
V2—第二反应区加导流区容积
V3—分离区容积
则实际容积比:
二反应室:一反应室:分离室=45.38:84.44:317.29=1:1.86:6.99
池各室停留时间:
第二反应室=分
8.7
7996
.7
85
.9
8.
76
99
.6
86
.1
1
8.
76
≈
=
=
+
+
第一反应室=分
5.
14
86
.1
796
.7=
?
分离室=7.796分
5.
54
99
.6=
?
其中第一反应室和第二反应室停留时间之和为22.3分。
八、进水系统
进水管选用s
m
v
mm
d8.0
,
400
6
=
=
出水管选用mm
d400
=
九、集水系统
本池因池径较小部水均匀性本身能达到要求。采用沿外圆周外侧作环行集水槽形式,按孔口出水方式,出水水质,小型的采用钢丝网水泥,结构较多,也有采用塑料制作的,但后者变形大,老化快,造价高,故采用不多。国外刚制的较多,由于防锈工作量大,故每年要维修孔。
孔口:2
1
2h
g
qυω
=
环行集水槽:s
m
v
q8.0
097
.0=
=,取流速
环
槽宽取0.3m,考虑施工方便槽底取为平底,槽内终点水深m
h4.0
3.0
8.0
097
.0
4
=
?
=
槽内起点水深m
h
h
h
h k46
.0
2
4
4
3
3
=
+
=
设槽内水深为0.43m,孔口出流孔口前水位0.05m,孔口出流跌落0.07m,超高0.3m 槽断面高为0.43+0.3+0.05+0.07=0.85m
总出水槽:设计流量s m Q 3097.0=,槽宽m b 5.0=,总出水槽按矩形渠道计算,槽内水流流速s m v 8.0=,槽坡降0.02m 。
槽内流速:0.9s m
槽内起点水深:0.41m 槽内终点水深:0.43m
设计取用槽内起点水深为0.4m 终点为0.45m ,超高0.3m ,h=0.45+0.3=0.75m
个。设计采用孔口数为个孔口数目:,孔口面积径为将塑料剔除集水孔的直,,,,孔口出流:孔孔696.68025.014.3135
.0135.006
.081.9232025.006.08.01146.02.16.02
2
=?==
=??=======d f n m q
f m m m d m h Q q s m v πυυ十、排泥及排水计算
污泥浓缩室总容积据经验按池总容积1%考虑
3/44711.411.44701.001.0m v v =?==
3235.2m v =斗
污泥斗上底面积:
m h m h S 24.089.15.13
2
1.15.12==??+
?=斗斗上, 下底面积:
205.0225.0225.0m S =?=下
污泥斗容积:()
39.405.089.105.089.13
2
.32m v =?++?=
斗 污泥斗容积是池容积的1%。
排泥历时:
设污泥斗排泥直径dg100,其断面w 01=0.00785m 2,管长5m ,排泥历时s t 98.1060= 放空时间:
设池底中心排空直径dg250mm ,20204909.0m w =,管长15m ,瞬时排泥量:
s m gH uw q 32/0223.02==。
放空时间:
(
)
()
h
a ctg H ctga H D H D k H H k t T T 79.15.5545.58345.56485.7285.35.5133625434225.223
2251/1/
211/21/
2/1=???
? ???+??+??+-?=?
?
? ??+++-= 十一、机械搅拌澄清池,搅拌机计算 1、提升叶轮
kw
n H Q N s
m m d r n s m s m Q Q c m Cnd
Q B 68.36
.010205
.046.010********.2.
min 2.946.0092.055,323.008.22.9346
.06060113312
1=???=====?====???==
ρ叶轮提升消耗功率:,叶轮外线流速:叶轮外径:,叶轮转速:出口宽度:
2、桨叶
()
kw
N N N m
h b b Z m R R m
d
R R m
h W C kw
Z R R g
h
W C N 21.468.3527.058.03
1
636.058.094.094.02
9.07.15.03.096
.03
.0527.04001222114
24
1
32=+=+===--=-=-==-----=-=提升和搅拌功率桨叶宽度片
桨叶数内半径桨叶外半径)取应室的桨叶高度(一般为一反叶轮旋转角速度阻力系数一般取桨叶消耗功率:ρ 3、驱动
电动机功率:采用自锁蜗杆时
电磁调速电动机效率为0.8,三角皮带传动效率为0.96,蜗轮减速器效率为0.7,轴承效率为0.9,则总效率为前面所有效率相乘既0.48 十二、刮泥机计算
采用悬挂式中心传动刮泥机:
刮泥机外缘直径为7.5m ,外线流速:3min m
功率计算:
刮泥机悬挂部件的重力w=10000N ,旋转支承的钢球直径为3.2m ,滚动摩擦力臂 K=0.05cm 安全系数为3旋转时的阻力N kn d w p 5.937305.022
.31000021=???=?=
设钢球槽的中心圆直径为0.5m 。min 157.05.01.0m D n V =??==ππ球臂球 旋转功率kw V P N 0024.060000
157
.05.93760000
11=?=
=
球
。
澄清池有效容积:326.23365.484
4m H D V =??=
=
π
π
池
进水量:m T V Q 374.15528
.16.233=== 干污泥量:h m SS Q Q 3660187.0104.03074.15510%=???=???=--?干 干污泥量换算成含水率为98%的污泥量为0.93h m 3。
刮泥机每转所需时间:r h r v
D t 3.0min 85.73
5
.7==?=
=
ππ板
刮泥机每转的刮泥量N g Q p 36.13110001.081.903.113.010002=????==μλ固
刮泥机功率:KW P N 0044.060000
3
222==
λ
设刮板按2/3的直线处线速度为2min m 。
电动机功率为:kw N N N W 014.05
.00044
.00024.021=+=+=
电
120-1200 1.2
本机械搅拌澄清池的搅拌机和刮泥机同S774(三)型。
搅拌器设计计算
搅拌器设计计算 令狐采学 (作者:纪学鑫) 一、设计数据: 1、混合池实际体积V=1.15m×1.15m×6.5m≈8.60m3 ∴设混合池有效容积V=8m3 2、混合池流量 Q=0.035m3/s 3、混合时间t=10s 4、混合池横截面尺寸 1.15m×1.15m ,当量直径D=πω4L =π 15.115.14??=1.30m 5、混合池液面高度H=24πD V =m ..π036301842 ≈?? ∴混合池高度H '=6.03m+(0.3~0.5)m=6.33~6.53 (m);取6.5m 6、挡板结构及装置尺寸()m 54.0036.0m 241361~)(~≈?? ? ??D ;数值根据《给水排水设计手册》表428查得,以下均已此手册作为查询依据。 7、取平均水温时,水的粘度值()s a ?P μ=1.14×103s a ?P 取水的密度3/kg 1000m =ρ 8、搅拌强度 1)搅拌速度梯度G ,一般取500~1000s1。 混合功率估算:NQ=KeQ(kw) Ke 单位流量需要的功率,Ke 一般=4.3~173/s kw m ? ∴混合功率估算:3/s kw 17~3.4m N Q ?=
取搅拌速度梯度1-s 740=G 2)体积循环次数'Z 搅拌器排液量'Q ,213.08.008.1385.0)/(333'=??==s m nd k Q q 折叶桨式,片,245=?=Z θ,流动准数385.0k q 取,见表427查取; n 搅拌器转速) (s /r ;d 搅拌器直径(m) 转速d 60n πν =;线速度v ,直径d ,根据表430查取。 3)混合均匀度 U ,一般为80%~90%。U 取80%。 9、搅拌机的安插形式、加药点设置。 1)立式搅拌机的安插:一般采取中央置入(或称顶部拔出)式。 2)搅拌器的位置及排泄标的目的:搅拌器的位置应避免水流直接影响正面冲击。搅拌器距液面的距离通常小于搅拌器直接的 1.5倍。 二、搅拌器的选用及主要参数 1. 选用折叶桨式 2. 桨叶数2=Z 3. 搅拌器直径0.8m d m 0.867~433.0m 32~31d ==??? ??=,取)()(D 4. 搅拌器螺距d s = 5. 搅拌器层数d H ,取7,(公司取层数4) 6. 搅拌器外缘线速度ν取(1.0~5.0)m/s 7. 搅拌器宽度:b=(0.1~0.25)d=(0.08~0.2)m,取0.11m 三、搅拌器转速及功率设计 1、根据要求的搅拌梯度G 值计算:
内支撑结构设计
一、内支撑结构可选用钢支撑、混凝土支撑、钢与混凝土的混合支撑。 二、内支撑结构选型应符合下列原则: 1、宜采用受力明确、连接可靠、施工方便的结构形式; 2、宜采用对称平衡性、整体性强结构形式; 3、应与主体地下结构的结构形式、施工顺序协调,应便于主体结构施工; 4、应利于基坑方开挖和运输; 5、需要时,可考虑内摘除结构作为施工平台。 三、内支撑结构应综合考虑基坑平面形状及尺寸、开挖深度、周边环境条件、主体结构形式等因素,选用有立柱或无立柱的下列内支撑形式: 1、水平对支撑或斜撑,可采用单杆、桁架、八字形支撑; 2、正交或斜交的平面杆系支撑; 3、环形杆或环形板系支撑; 4、坚向斜撑。 四、内支撑结构宜采用超静定结构。对个别次要构件失效会引起结构整体破坏的部位宜设置冗余约束。内支撑结构的设计应考虑地质和环境条件的复杂性、基坑开挖步序的偶然变化的影响。 五、内支撑结构分析应符合下列原则: 1、水平对撑与水平斜撑,应按偏心压力国建进行计算;支撑的轴向压力其支撑间距N 倍挡土构件的支点力之和;腰梁或冠梁应按宜支撑我支座的多跨连续梁计算,计算跨度可取相邻支撑点的中距; 2、矩形基坑支护的正交平面杆系支撑,可分解为纵横两个方向的结构单元,并分按偏心受压构件进行计算; 3、平面杆系支撑、环形杆系支撑,可按平面杆系结构采用平面有限元法进行计算;计算时应考虑基坑不同方向上的荷载不均匀性;建立的计算模型中,约束支座的设置应与支护结构实际位移状态相符,内支撑结构边界向基坑外应设置弹性约束支座,向基坑内位移处不应设置支座,与边界平行方向应根据支护结构实际位移状态设置支座;
4、内支撑结构应进行坚向荷载作用下的结构分析;设有立柱时,在坚向荷载作用下内支撑结构宜按空间框架计算,当作用在内支撑结构上的坚向荷载较小时,内支撑结构的水平构件和按连续梁计算,计算跨度可取相邻立柱的中法,对支撑、腰梁与冠梁、挡土构件进行整体分析。 六、内支撑结构分析时,应同时考虑下列作用: 1、有挡土都建传至内支撑结构的水平荷载; 2、支撑结构自重;当支撑作为施工平台时,尚应考虑施工荷载; 3、当温度改变引起的支撑结构内力不可忽略不计时,应考虑温度应力; 4、当支撑立柱下沉或隆起量较大时,应考虑支撑立柱与挡土构件之间差异沉降产生的作用。 七、混凝土支撑构件及其连接的受压、受弯、受剪承载力计算应符合现行国家标准《混凝土结构设计规范》GB50010水位规定;钢支撑结构构件及其连接受压、受弯、受剪承载力及各类稳定性计算应符合现行国家标准《钢结构设计规范》GB50017的规定。支撑的承载力计算应考虑施工偏心误差的影响,偏心距取值不宜小于支撑计算长度的1/1000,且对混凝土办职称不宜小于20mm,对钢支撑不宜小于40mm。 八、支撑构件的受压计算长度应按下列规定确定: 1、水平支撑在坚向平面内的受压计算长度,不设置立柱时,应取支撑的实际长度;设置立柱时,应取相邻立柱的中心距; 2、水平支撑在水平平面内的受压计算长度,对无水平支撑杆件交汇的支撑,应取与支撑相交的相邻水平支撑杆件的中心距;当水平支撑杆件的交汇点不子啊同一水平面内时,水平平面内的受压计算长度宜取与支撑相交的相邻水平支撑杆件中心距的1.5倍; 3、对坚向斜撑,应按条第1、2款的规定确定受压计算长度。 九、预加轴向压力的支撑,预加力值宜取支撑轴向压力标准值的(0.5~0.8)倍,且应与本规程中的支撑预加轴向压力一致。 十、立柱的受压承载力金额按下列规定计算:
机械搅拌澄清池操作说明
机械搅拌澄清池 操作说明书 江苏集成环境工程有限公司 2010-10 一、工艺原理及工艺参数 1、工艺原理 采用混凝沉淀法去除水中悬浮颗粒的工艺包括水和药剂的混合,反应以及絮凝体与水的分离三个阶段,澄清池是将这三个过程集于一个构筑物中完成的一种非凡形式的设施。澄清池的工作原理是:原水在澄清池中由下向上流动,澄清池中有一层呈悬浮状态的泥渣,泥渣层由于重力作用在上升水流中处于动态平衡状态;当原水中的悬浮颗粒与混凝剂作用而形成的微小絮凝体随水流通过泥渣层时,在运动中与泥渣层相对较大的泥渣接触碰撞就被吸附在泥渣颗粒表面而迅速除去,使水获得澄清;清水经由澄清池上部的清水槽被收集排出。因此,保持悬浮状态的、浓度稳定且均匀分布的泥渣区是保证澄清池处理效果的要害。 机械加速澄清池属于泥渣循环分离型,它是借助机械抽升作用,使泥渣在垂直方向不断循环,捕捉原水中形成的絮凝体,并在分离区加以分离。其特点是充分利用已形成泥渣的活性,增加碰撞机会,强化碰撞几率,提高处理设备的功能。在机械加速澄清池中心安装有机械搅拌设备,上部为提升叶轮,下部为搅拌浆,两者安装在同一轴上;提升叶轮将混合泥水提升至第二反应室,而搅拌浆使第一混合反应室的泥渣循环流动与拟处理原水进行混合和反应。 投药后的原水经进水管、配水槽进入第一混合反应室中,与回流泥渣混合并完成药剂与水的混合和反应过程;混合泥水从池中心提升至第二反应室,继续完成混凝过程;然后经由导流筒进入分离室完成泥水分离过程。
2、工艺参数 项目设计参数备注 机械搅拌澄清设备位号 数量 2 单池设计能力1330m3/h 主体材质碳钢防腐 尺寸Φ25000×H7500mm 池体直段高度1500mm 停留时间(1.2~1.5)h 总容积2095m3 第一反应室回流量(3~5)Q 第一反应室回流缝流速(0.10~0.20) m/s 第一反应室直径15600mm 第二反应室计算流量(3~5)Q 第二反应室内流速(0.04~0.07) m/s 第二反应室直径7800mm 导流室内流速(0.04~0.07) m/s 分离室上升流速(0.0008~0.0011) m/s 配水方式三角配水槽缝隙配水集水方式环形集水槽 排泥方式定时周期排泥 排泥斗数3个 管口表 进水管700mm 出水管700mm 排泥管100mm 放空管250mm
机械搅拌澄清池设计计算
第一节 机械搅拌澄清池计算 其特点是利用机械搅拌澄清池的提升作用来完成泥渣回流核接触反应,加药混合后进入第一反应室,与几倍于原水的循环泥渣在叶片的搅动下进行接触反应.然后经叶轮提升到第二反应室继续反应以结成大的颗粒,再经导流室进入分离室沉淀分离. 一、二反应室 净产水能力为Q=700 m3/h= m3/s 采用2个池来计算则每池的流量s m Q 3 097.0=,二反应室计算流量一般为出水流量的3-5倍.s m Q Q 3 / 485.05==. 设第二反应室内导流板截面积A 1=0.02m 2,u 1=s m 则第二反应区截面积为: 21/17.905 .0485.0m u Q w === 第二反应区内径:() ()m A w D 52.314 .302.07.944111=+= += π 取第二反应室直径1D =3.6m,反应室壁厚m 25.01=δ () s t m w t Q H m D D 5038.27 .950 485.01.45.06.32111/1111/==?===+=+=δ H 1—第二反应区高度,m 考虑构造布置选用m H 47.21=,设导流板4块. 二、导流室 导流室中导流板截面积:2 1202.0m A A == 导流室面积:2 127.9m w w == 导流室直径:m D A w D 4.547.902.04442 1/222=? ?? ?? ++= ???? ? ?++= π ππ π 取导流室,4.52m D =导流室壁厚m 1.02=δ. m D D H m D D 65.02 ,6.521 /22/ 22 / =-==+=δ
搅拌反应釜计算设计说明书
课程设计 设计题目搅拌式反应釜设 学生姓名 学号 专业班级过程装备与控制工程 指导教师
“过程装备课程设计”任务书 设计者姓名:班级:学号: 指导老师:日期: 1.设计内容 设计一台夹套传热式带搅拌的反应釜 2.设计参数和技术特性指标 简图设计参数及要求 容器内夹套 内 工作压力, MPa 设计压力, MPa 工作温 度,℃ 设计温 <100<150 度,℃ 蒸汽 介质有机溶 剂 全容积,m3 操作容积, m3 传热面积, >3 m2 腐蚀情况微弱 推荐材料Q345R 搅拌器型 推进式 式 250 r/min 搅拌轴转 速 轴功率 3 kW 接管表
3.设计要求 (1)进行罐体和夹套设计计算;(2)选择接管、管法兰、设备法兰;(3)进行搅拌传动系统设计;(4)设计机架结构;(5)设计凸缘及选择轴封形式;(6)绘制配料反应釜的总装配图;(7)绘制皮带轮和传动轴的零件图 1罐体和夹套的设计 1.1 确定筒体内径 当反应釜容积V 小时,为使筒体内径不致太小,以便在顶盖上布置接管和传动装置,通常i 取小值,此次设计取i =1.1。 一般由工艺条件给定容积V 、筒体内径1D 按式4-1估算:得D=1084mm. 式中 V --工艺条件给定的容积,3m ;
i ――长径比,1 1 H i D = (按照物料类型选取,见表4-2) 由附表4-1可以圆整1D =1100,一米高的容积1V 米=0.953m 1.2确定封头尺寸 椭圆封头选取标准件,其形式选取《化工设备机械基础课程设计指导书》图4-3,它的内径与筒体内径相同,釜体椭圆封头的容积由附表4-2 V 封=0.1983m ,(直边高度取50mm )。 1.3确定筒体高度 反应釜容积V 按照下封头和筒体两部分之容积之和计算。筒体高度由计算 H1==(2.2-0.198)/0.95=0.949m ,圆整高度1H =1000mm 。按圆整后的1H 修正实际容积由式 V=V1m ×H1+V 封=0.95×1.000+0.198=1.1483m 式中 V 封m --3封头容积,; 1V 米――一米高的容积3m /m 1H ――圆整后的高度,m 。 1.4夹套几何尺寸计算 夹套的结构尺寸要根据安装和工艺两方面的要求。夹套的内径2D 可根据内径1D 由 选工艺装料系数η=0.6~0.85选取,设计选取η=0.80。 1.4.1夹套高度的计算H2=(ηV-V 封)/V1m=0.758m 1.4.2.夹套筒体高度圆整为2H =800mm 。 1.4.3罐体的封头的表面积由《化工设备机械基础》附表4-2查的F 封=1.398。 1.4.4一米高的筒体内表面由《化工设备机械基础》附表4-1查的。F1m=3.46 1.4.5实际的传热面积F=4.166>3,由《化工设备机械基础》式4-5校核4.166〉3所以传热面积合适。
幕墙计算与支撑钢结构设计[详细]
第X章幕墙计算及幕墙后支撑钢结构的设计目录: 第一节、幕墙计算 一、荷载作用 二、荷载作用效应组合 三、材料的力学性能 四、面材的计算 五、立柱及横梁的计算 六、连接节点的计算 第二节、幕墙后支撑钢结构设计 一、幕墙后支撑钢结构体系分类 二、常用钢材的分类及其力学性能 三、幕墙支撑钢结构的计算 四、焊接节点的设计 五、高强度螺栓连接节点的设计与计算 六、普通螺栓连接节点的设计与计算 七、柱脚节点连接的设计与计算
第六章 幕墙计算及幕墙后支撑钢结构的设计 第一节、幕墙计算 一、荷载作用 1、幕墙所承受荷载的分类 幕墙所承受的荷载随时间的变异分类可分为下列三类: 永久荷载,例如结构的自重、静水压力、预应力等 可变荷载,例如风荷载、屋面活荷载、雪荷载等、施工及检修荷载 偶然荷载,地震作用、爆炸力、撞击力等 2、风荷载标准值的计算: 0ωμμβω???=z S gz K 式中: K ω—风荷载标准值(N/米米2); gz β—阵风系数. S μ—风荷载体形系数. z μ—风压高度变化系数. 0ω—基本风压. 基本风压0ω是根据全国各气象台历年来的最大风速记录,按基本风压的标准要求,将不同风仪高度和时次时距的年最大风速,统一换算为离地10米高,自记10米in 平均年最大风速(米/s).然后根据贝努利公式2 02 1v ρω= 确定基本风压.在《建筑结构荷载规范》附录D 中给出了 全国各个地区的经过换算的基本风压.在幕墙结构的设计中如果无特殊要求,基本风压取50年一遇. 风压高度变化系数z μ主要考虑的是风压随着建筑物高度变化的变化.其主要决定两个因素,一个是建筑物的高度;另外一个就是地面粗糙度类别,目前《建筑结构荷载规范》考虑了 四类地面类别: —A 类指近海海面和海岛、海岸、湖岸及沙漠地区; —B 类指田野、乡村、丛林、丘陵以及房屋比较稀疏的乡镇和城市郊区; —C 类指有密集建筑群的城市市区;
机械搅拌澄清池设计说明书
1设计任务 1.1设计题目 机械加速搅拌澄清池工艺设计 1.2设计要求 设计规模为1600m3/h, 水厂自用水量为5 %, 净产水能力为1600m3/d×1.05= 1680m3/d =0.4667m3/s 1.3设计内容 完成机械加速搅拌澄清池工艺设计说明书一份,手绘1号图纸一张 2设计说明 2.1机械搅拌澄清池的工作原理 机械搅拌澄清池是利用转动的叶轮使泥渣在池内循环流动,完成接触絮凝和澄清的过程。 该型澄清池由第一絮凝室、第二絮凝室和分离室组成。在第一和第二絮凝室内,原水中胶体和回流泥渣进行接触絮凝,结成大的絮体后,在分离室中分离。清水向上集水槽排出。下沉的泥渣一部分进入泥渣浓缩室经排泥管排除,另一部分沿回流缝在进入第一絮凝室进行絮凝。 2.2机械搅拌澄清池的工作特点 机械搅拌(原称机械加速)澄清池属泥渣循环型澄清池,其特点是利用机械搅拌的提升作用来完成泥渣回流和接触反应。加药混合后的原水进水进入第一反应室,与几倍于原水的循环泥渣在叶片的搅动下进行接触反应。然后经叶轮提升至第一反应室继续反应,以结成较大的絮粒。再通过导流室进入分离室进行沉淀分离。这种水池不仅适用于一般的澄清也适用于石灰软化的澄清。 2.3机械搅拌澄清池设计要点及数据 (1)二反应室计算流量(考虑回流因素在内)一般为出水量的3~5倍; (2)清水区上升流速一般采用0.8~1.1mm/s,当处理低温低浊水时可采用0.7~0.9mm/s; (3)水在池中的总停留时间为 1.2~1.5h,第一絮凝室和第二絮凝室的停留时间一般控制在20~30min,第二反应室按计算流量计的停留时间为0.5~1min (4)为使进水分配均匀,可采用三角配水槽缝隙或孔口出流以及穿孔管配水等;为防止堵塞,也可采用底部进水方式。 (5)加药点一般设于池外,在池外完成快速混合。一反应室可设辅助加药管以备投加助凝剂。软化时应将石灰投加在以反应室内,以防止堵塞进水管道。 (6) 第二反应室内应设导流板,其宽度一般为直径的0.1左右 (7)清水区高度为1.5~2.0m; (8)底部锥体坡角一般在45°左右,当设有刮泥装置时也可做成平底
搅拌桨叶的选型和设计计算
第二节搅拌桨叶的设计和选型一、搅拌机结构与组成 组成:搅拌器电动机 减速器容器 排料管挡板 适用物料:低粘度物料 二、混合机理 利用低粘度物料流动性好的特性实现混合 1、对流混合 在搅拌容器中,通过搅拌器的旋转把机械能传给液体物料造成液体的流动,属强制对流。包括两种形式: (1)主体对流:搅拌器带动物料大范围的循环流动 (2)涡流对流:旋涡的对流运动 液体层界面强烈剪切旋涡扩散 主体对流宏观混合 涡流对流 2、分子扩散混合 液体分子间的运动微观混合 作用:形成液体分子间的均匀分布 对流混合可提高分子扩散混合 3、剪切混合 剪切混合:搅拌桨直接与物料作用,把物料撕成越来越薄的薄层,达到混合的目的。 高粘度过物料混合过程,主要是剪切作用。 电 动 机 减速器 搅 拌 器 容 器 排料管
三、混合效果的度量 1、调匀度I 设A 、B 两种液体,各取体积vA 及vB 置于一容器中, A B A B a b 则容器内液体A 的平均体积浓度CA0为: (理论值) 经过搅拌后,在容器各处取样分析实际体积浓度CA ,比较CA0 、CA , 若各处 CA0=CA 则表明搅拌均匀 若各处 CA0=CA 则表明搅拌尚不均匀,偏离越大,均匀程度越差。 引入调匀度衡量样品与均匀状态的偏离程度 定义某液体的调匀度 I 为: (当样品中CA CA0时) 或 (当样品中CA CA0时) 显然 I ≤1 若取m 个样品,则该样品的平均调匀度为 当混合均匀时 2、混合尺度 设有A 、B 两种液体混合后达到微粒均布状态。 B A A A V V V C +=00A A C C I =0 11A A C C I --=m I I I I m +??++=- 211 =- I
搅拌器功率计算
搅拌器功率计算 搅拌器功率分为运转功率和启动功率,运转功率是指远转时桨叶克服液体的摩擦阻力所消耗的功率;启动功率是指在启动时桨叶克服液体静止惯性所消耗的功率。 一、 运转功率计算 以平浆式为例: d n P i m 5 3 ???=ρξ转 式中:ξ m --- 常数项; ρ----- 液体密度,kg/m 3; n----- 桨叶转速,r/min; d i ---- 桨叶直径,mm; 根据对运转功率的进一步分析,得出如下结论: 1、 采用倾斜桨叶,在改善结构和降低运转功率方面都是有宜的。 2、 在搅拌跟多液体时,应首先考虑增加桨叶数量,而不应增加桨叶长度。 3、 实际运转功率大于理论功率,这是因为还存在其它阻力,因此应在计算功率的基础 上适当增加。 4、 容器内壁粗糙时,运转的实际功率应比计算功率增加10-30%。 5、 容器内有加热蛇管时,应增加2倍。 6、 容器内有挡板时,应增加2-3倍。 二、 惯性功率计算 d n P i b 4 393.1???=ρ阻 令b/ d i =a;b=a d i .则: d n P i a 5 393.1???=ρ阻 令k=1.93a.为常数项,则: d n P i k 5 3 ???=ρ阻 符号意义同上。 三、 总功率 搅拌器的总功率消耗P W 为: P W =P 转 +P 阻=d n i m k 5 3 )(???+ρξ 以此式计算的功率值在1kw 以上时误差叫小,小于1kw 时则与实际功率有较大出入,将以用一下数值对功率作调整:
当负荷功率≥1kw时,P实=(1.1-1.2)P W 当负荷功率≥0.1kw时,P实=(1-4)P W 当负荷功率≤0.1kw时,P实=10P W 当负荷功率≥0.1kw时,P实=(1-4)P W 如果只对功率作粗略估算,P W=(2-3)P转 电动机应选用防潮型、具有接触环的异步电动机,它具有较大的启动转矩,而一般的三相同步电动机是不适应的。 搅拌器形式适应条件 液体单位体积的平均搅拌功率的推荐值
搅拌机设计流程
摘要 搅拌机是搅拌设备的心脏。在搅拌机设计及使用过程中,合理的选取搅拌机的结构,运动和工作参数,直接关系到混凝土等材料的搅拌质量和搅拌效率。论文对搅拌臂的排列、搅拌叶片的安装角、拌筒长宽比、搅拌机转速和搅拌时间等主要参数的选取进行分析与试验研究。通过归纳,给出了双卧轴搅拌机的主要参数,包括搅拌臂排列、叶片安装角、拌筒长宽比、搅拌线速度等;给出了评价搅拌机参数合理与否的准则;给出了搅拌臂排列的基本原则。论文通过试验研究,建议用叶片推动的物料量与该搅拌机的公称容量的比值rl,来综合评定搅拌臂的个数,叶片面积和其他参数匹配的合理性,并作为设计时的参考;双卧轴搅拌机的叶片的安装角范围为3l一45,对国内广泛使用的宽短型双卧轴搅拌机叶片安装角度推荐为45;对目前国内外普遍使用的双卧轴搅拌机,它的长宽比的选择范围为0.7—1.3,推荐使用值为小于1;搅拌机的转速主要受搅拌过程中混合料不发生离析现象所限制,对目前常用的双卧轴搅拌机,推荐的叶片线速度为1.4m /s-1.7m/s/;合理的搅拌时间是保证搅拌质量符合要求条件下的最短搅拌时间,它受充盈率等多种因素影响,合理的搅拌时间应通过试拌来确定。 [关键词]:搅拌机、主要参数、合理性、实验研究
第1章前言 1.1国内外研究现状及发展趋势 19世纪40年代,在德、美、俄等国家出现了以蒸气机为动力源的白落式搅拌机,其搅拌腔由多面体状的木制筒构成,一直到19世纪80年代,才开始用铁或钢件代替木板,但形状仍然为多面体。1888年法国申请登记了第一个用于修筑战前公路的混凝土搅拌机专利。20世纪初,圆柱形的拌筒自落式搅拌机才开始普及,其工作原理如图1.2所示。形状的改进避免了混凝土在拌筒内壁上的凝固沉积,提高了搅拌质量和效率。1903年德国在斯太尔伯格建造了世界上第一座水泥混凝土的预拌工厂。1908年,在美国出现了第一台内燃机驱动的搅拌机,随后电动机则成为主要动力源。从1913年,美国开始大量生产预拌混凝土,到1 950年,亚洲大陆的日本开始用搅拌机生产预拌混凝土。在这期间,仍然以各种有叶片或无叶片的自落式搅拌机的发明与应用为主?。自落式搅拌机依靠被拌筒提升到一定高度的物料的自落完成搅拌。工作时,随着拌筒的转动,物料被搅拌筒内壁固定的叶片提升到一定高度后,依靠自重下落。由于各物料颗粒下落的高度、时问、速度、落点和滚动距离不同,从而物料各颗粒相互穿插、渗透、扩散,最后达到均匀混合。自落式搅拌机结构简单,可靠性高,维护简单,功率消耗小,拌筒和叶片磨损轻,但搅拌强度不高,生产效率低,搅拌质量不易保证。此种搅拌机适于拌制普通塑性混凝土,广泛应用于中小型建筑工地。按拌筒形状和卸料方式的不同,有鼓筒式搅拌机、双锥反转出料搅拌机、双锥倾翻出料搅拌机和对开式搅拌机等,其中鼓简式搅拌机技术性能落后,已于1987年被我国建设部列为淘汰产品。随着多种商品混凝土的广泛使用以及建筑规模的大型化、复杂化和高层化对混凝土质量、产量不断提出的更高要求,有力地促进了混凝土搅拌设备在使用性能和技术水平方面的提高与发展。各国研究人员开始从混凝土搅拌机的结构形式、传动方式、搅拌腔衬板材料以及搅拌生产工艺等方面进行改进和探索。20世纪40年代后期,德国ELBA公司最先发明了强制式搅拌机,和自落式搅拌机的工作原理不同,强制式搅拌机利用旋转的叶片强迫物料按预定轨迹产生剪切、挤压、翻滚和抛出等强制搅拌作用,使物料在剧烈的相对运动中得到匀质搅拌。强制式
机械搅拌澄清池设计说明书资料讲解
机械搅拌澄清池设计 说明书
1设计任务 1.1设计题目 机械加速搅拌澄清池工艺设计 1.2设计要求 设计规模为1600m3/h, 水厂自用水量为5 %, 净产水能力为1600m3/d×1.05= 1680m3/d =0.4667m3/s 1.3设计内容 完成机械加速搅拌澄清池工艺设计说明书一份,手绘1号图纸一张 2设计说明 2.1机械搅拌澄清池的工作原理 机械搅拌澄清池是利用转动的叶轮使泥渣在池内循环流动,完成接触絮凝和澄清的过程。 该型澄清池由第一絮凝室、第二絮凝室和分离室组成。在第一和第二絮凝室内,原水中胶体和回流泥渣进行接触絮凝,结成大的絮体后,在分离室中分离。清水向上集水槽排出。下沉的泥渣一部分进入泥渣浓缩室经排泥管排除,另一部分沿回流缝在进入第一絮凝室进行絮凝。 2.2机械搅拌澄清池的工作特点 机械搅拌(原称机械加速)澄清池属泥渣循环型澄清池,其特点是利用机械搅拌的提升作用来完成泥渣回流和接触反应。加药混合后的原水进水进入第一反应室,与几倍于原水的循环泥渣在叶片的搅动下进行接触反应。然后经叶轮提升至第一反应室继续反应,以结成较大的絮粒。再通过导流室进入分离室进行沉淀分离。这种水池不仅适用于一般的澄清也适用于石灰软化的澄清。
2.3机械搅拌澄清池设计要点及数据 (1)二反应室计算流量(考虑回流因素在内)一般为出水量的3~5倍; (2)清水区上升流速一般采用0.8~1.1mm/s,当处理低温低浊水时可采用 0.7~0.9mm/s; (3)水在池中的总停留时间为1.2~1.5h,第一絮凝室和第二絮凝室的停留时间一般控制在20~30min,第二反应室按计算流量计的停留时间为0.5~1min (4)为使进水分配均匀,可采用三角配水槽缝隙或孔口出流以及穿孔管配水等;为防止堵塞,也可采用底部进水方式。 (5)加药点一般设于池外,在池外完成快速混合。一反应室可设辅助加药管以备投加助凝剂。软化时应将石灰投加在以反应室内,以防止堵塞进水管道。 (6) 第二反应室内应设导流板,其宽度一般为直径的0.1左右 (7)清水区高度为1.5~2.0m; (8)底部锥体坡角一般在45°左右,当设有刮泥装置时也可做成平底 (9)方式可选用淹没孔集水槽或三角堰集水槽,过孔流速为0.6m/s左右。池径较小时,采用环形集水槽;池径较大时,采用辐射集水槽及环形集水槽。集水槽中流速为0.4~0.6m/s,出水管流速为1.0m/s左右。考虑水池超负荷运行和留有加装斜板(管)的可能,集水槽和进水管的校核流量宜适当增大。 (10)进水悬浮物含量经常小于1000mg/L,且池径小于24m时可用采污泥浓缩斗排泥和底部排泥相结合的形式,一般设置1~3个排泥斗,泥斗容积一般为池容各的1%~4%;小型水池也可只用底部排泥。进水悬浮物含量超过1000mg/L或池径24m时应设机械排泥装置。
搅拌桨叶的选型和设计计算
一、搅拌机结构与组成 组成:搅拌器 电动机 减速器 容器 排料管 挡板 适用物料:低粘度物料 二、混合机理 利用低粘度物料流动性好的特性实现混合 1、对流混合 在搅拌容器中.通过搅拌器的旋转把机械能传给液体物料造成液体的流动.属强制对流。包括两种形式: (1)主体对流:搅拌器带动物料大范围的循环流动 (2)涡流对流:旋涡的对流运动 液体层界面 强烈剪切 旋涡扩散 主体对流 宏观混合 涡流对流 2、分子扩散混合 液体分子间的运动 微观混合 作用:形成液体分子间的均匀分布 对流混合可提高分子扩散混合 3、剪切混合 剪切混合:搅拌桨直接与物料作用.把物料撕成越来越薄的薄层.达到混合的目的。 高粘度过物料混合过程.主要是剪切作用。
三、混合效果的度量 1、调匀度I 设A 、B 两种液体.各取体积vA 及vB 置于一容器中. 则容器内液体A 的平均体积浓度CA0为: (理论值) 经过搅拌后.在容器各处取样分析实际体积浓度CA.比较CA0 、CA . 若各处 CA0=CA 则表明搅拌均匀 若各处 CA0=CA 则表明搅拌尚不均匀.偏离越大.均匀程度越差。 引入调匀度衡量样品与均匀状态的偏离程度 定义某液体的调匀度 I 为: (当样品中CA CA0时) 或 (当样品中CA CA0时) 显然 I ≤1 若取m 个样品.则该样品的平均调匀度为 当混合均匀时 2、混合尺度 设有A 、B 两种液体混合后达到微粒均布状态。 混合尺度分 设备尺度 微团尺度 分子尺度 对上述两种状态: 在设备尺度上:两者都是均匀的(宏观均匀状态) 在微团尺度上:两者具有不同的均匀度。 在分子尺度上:两者都是不均匀的(当微团消失.称分子尺度的均匀或微观均 匀) 如取样尺寸远大于微团尺寸.则两种状态的平均调匀度接近于己于1。 如取样尺寸小到与b 中微团尺寸相近时.则b 状态调匀度下降.而a 状态调匀度不变。 即:同一个混合状态的调匀度随所取样品的尺寸而变化.说明单平调匀度不能反映混合物的均匀程度 四、搅拌机主要结构 1、搅拌器 搅拌器由电动机带动.物料按一定规律运动(主体对流).桨型不同.物料产生的流型不同。 桨作用于物料.物料产生三个方向的速度分量: 轴向分量 B A A A V V V C +=00A A C C I =0 11A A C C I --=m I I I I m +??++=- 211 =-I
桨叶式搅拌机的设计
1前言 建材产品的生产,从原料、燃料到半成品都需要进行破碎和粉磨,其目的是使物料的表面积增加,以提高物理作用的效果及化学反应的速度,如促进均匀混合,提高物料的流动性,便于贮存和运输,提高产量等。水泥熟料和石膏一起磨碎成最终产品,其磨碎的粒度越细,表面积越大,则水泥的标号就越高。改善和提高产品的质量和数量,减少动力消耗,降低生产成本,对达到优质、高产、低消耗具有重要意义。 机械冲击粉碎是建材行业材料破碎的主要手段,其设备效率是重要的技术和经济指标。目前在搅拌机的设计研究中,主要集中在耐磨材料和常规设计的改进。 在水泥行业、选矿电力等工业领域中广泛使用粉磨机械,但各类粉磨机械都有生产效率低,能耗高的缺点。当前的发展趋势是“以破代磨”,借助加强粉磨机前的粉碎,降低入料粒度,可大幅度提高粉磨机产量,降低综合能耗。本课题是结合市场上所使用的各类型号的搅拌机及由厂家在使用过程中所反馈的信息,分析其问题的来源,并相互比较综合各类搅拌机的优点,经师生讨论而确定的。 设计要求:a、最大进料粒度:<150mm;b、出料粒度:<10mm;c、生产能力:25-30t/h。 使用范围:桨叶式搅拌机既可以用于生料的破碎,又可以用于熟料的破碎。它适用于粉碎水泥熟料、粒状高炉矿渣、石灰石、砂岩、页岩、煤矸石、煤块、铝块石、金矿石、钼矿石等多种物料。它广泛应用于:建材、化工、冶金、电力、煤炭、矿山等工业部门。 技术要求:机械设计应保证其功能良好、使用可靠、维护方便;零件结构设计要选择合理的毛坯型式和材料,并尽可能的采用标准件和通用件,并具有良好的工艺性。 设计方法:采用二维CAD绘制图纸和在UG平台上创建三维模型相结合的方法,更加直观地将所要设计的结构表达出来。 本课题着重解决如何将反击式搅拌机和锤式搅拌机的优点结合、锤头磨损问题和机体平衡问题、搅拌机在工作过程中的粉尘泄露问题及搅拌机的各工作参数的优化确定方法等。 本设计具有很强的实用价值。因为采用了很多新的结构,大大降低了制造和维护的费用,减少了机器调整的次数,保证了生产的连续性。
内支撑结构设计
、内支撑结构可选用钢支撑、混凝土支撑、钢与混凝土的混合支撑。 二、内支撑结构选型应符合下列原则: 1、宜采用受力明确、连接可靠、施工方便的结构形式; 2、宜采用对称平衡性、整体性强结构形式; 3、应与主体地下结构的结构形式、施工顺序协调,应便于主体结构施工; 4、应利于基坑方开挖和运输; 5、需要时,可考虑内摘除结构作为施工平台。 三、内支撑结构应综合考虑基坑平面形状及尺寸、开挖深度、周边环境条件、主体结构形式等因素,选用有立柱或无立柱的下列内支撑形式: 1、水平对支撑或斜撑,可采用单杆、桁架、八字形支撑; 2、正交或斜交的平面杆系支撑; 3、环形杆或环形板系支撑; 4、坚向斜撑。 四、内支撑结构宜采用超静定结构。对个别次要构件失效会引起结构整体破坏的部位宜设置冗余约束。内支撑结构的设计应考虑地质和环境条件的复杂性、基坑开挖步序的偶然变化的影响。 五、内支撑结构分析应符合下列原则: 1、水平对撑与水平斜撑,应按偏心压力国建进行计算;支撑的轴向压力其支撑间距N 倍挡土构件的支点力之和;腰梁或冠梁应按宜支撑我支座的多跨连续梁计算,计算跨度可取 相邻支撑点的中距; 2、矩形基坑支护的正交平面杆系支撑,可分解为纵横两个方向的结构单元,并分按偏心受压构件进行计算; 3、平面杆系支撑、环形杆系支撑,可按平面杆系结构采用平面有限元法进行计算;计 算时应考虑基坑不同方向上的荷载不均匀性;建立的计算模型中,约束支座的设置应与支护结构实际位移状态相符,内支撑结构边界向基坑外应设置弹性约束支座,向基坑内位移处不应设置支座,与边界平行方向应根据支护结构实际位移状态设置支座;
4、内支撑结构应进行坚向荷载作用下的结构分析;设有立柱时,在坚向荷载作用下内 支撑结构宜按空间框架计算,当作用在内支撑结构上的坚向荷载较小时,内支撑结构的水 平构件和按连续梁计算,计算跨度可取相邻立柱的中法,对支撑、腰梁与冠梁、挡土构件进行整体分析。 六、内支撑结构分析时,应同时考虑下列作用: 1、有挡土都建传至内支撑结构的水平荷载; 2、支撑结构自重;当支撑作为施工平台时,尚应考虑施工荷载; 3、当温度改变引起的支撑结构内力不可忽略不计时,应考虑温度应力; 4、当支撑立柱下沉或隆起量较大时,应考虑支撑立柱与挡土构件之间差异沉降产生的作用。 七、混凝土支撑构件及其连接的受压、受弯、受剪承载力计算应符合现行国家标准《混凝土结构设计规范》GB50010水位规定;钢支撑结构构件及其连接受压、受弯、受剪承载力 及各类稳定性计算应符合现行国家标准《钢结构设计规范》GB50017的规定。支撑的承载力 计算应考虑施工偏心误差的影响,偏心距取值不宜小于支撑计算长度的1/1000 ,且对混凝 土办职称不宜小于20mm对钢支撑不宜小于40mm 八、支撑构件的受压计算长度应按下列规定确定: 1、水平支撑在坚向平面内的受压计算长度,不设置立柱时,应取支撑的实际长度;设 置立柱时,应取相邻立柱的中心距; 2、水平支撑在水平平面内的受压计算长度,对无水平支撑杆件交汇的支撑,应取与支 撑相交的相邻水平支撑杆件的中心距;当水平支撑杆件的交汇点不子啊同一水平面内时,水平平面内的受压计算长度宜取与支撑相交的相邻水平支撑杆件中心距的倍; 3、对坚向斜撑,应按条第1、2款的规定确定受压计算长度。 九、预加轴向压力的支撑,预加力值宜取支撑轴向压力标准值的(~)倍,且应与本规 程中的支撑预加轴向压力一致。 十、立柱的受压承载力金额按下列规定计算: 内支撑结构设计 1、在坚向荷载作用下,内支撑结构按框架计算时,立柱应按偏心受压构件计算;内支
搅拌器毕业设计--(很实用)
搅拌器毕业设计 第一章绪论 搅拌可以使两种或多种不同的物质在彼此之中互相分散,从而达到均匀混合;也可以加速传热和传质过程。在工业生产中,搅拌操作时从化学工业开始的,围绕食品、纤维、造纸、石油、水处理等,作为工艺过程的一部分而被广泛应用。 搅拌操作分为机械搅拌与气流搅拌。气流搅拌是利用气体鼓泡通过液体层,对液体产生搅拌作用,或使气泡群一密集状态上升借所谓上升作用促进液体产生对流循环。与机械搅拌相比,仅气泡的作用对液体进行的搅拌时比较弱的,对于几千毫帕·秒以上的高粘度液体是难于使用的。但气流搅拌无运动部件,所以在处理腐蚀性液体,高温高压条件下的反应液体的搅拌时比较便利的。在工业生产中,大多数的搅拌操作均系机械搅拌,以中、低压立式钢制容器的搅拌设备为主。搅拌设备主要由搅拌装置、轴封和搅拌罐三大部分组成。其结构形式如下:(结构图) 第一节搅拌设备在工业生产中的应用范围很广,尤其是化学工业中,很多的化工生产都或多或少地应用着搅拌操作。搅拌设备在许多场合时作为反应器来应用的。例如在三大合成材料的生产中,搅拌设备作为反应器约占反应器总数的99%。。搅拌设备的应用范围之所以这样广泛,还因搅拌设备操作条件(如浓度、温度、停留时间等)的可控范围较广,又能适应多样化的生产。 搅拌设备的作用如下:①使物料混合均匀;②使气体在液相中很好的
分散;③使固体粒子(如催化剂)在液相中均匀的悬浮;④使不相溶的另一液相均匀悬浮或充分乳化;⑤强化相间的传质(如吸收等); ⑥强化传热。 搅拌设备在石油化工生产中被用于物料混合、溶解、传热、植被悬浮液、聚合反应、制备催化剂等。例如石油工业中,异种原油的混合调整和精制,汽油中添加四乙基铅等添加物而进行混合使原料液或产品均匀化。化工生产中,制造苯乙烯、乙烯、高压聚乙烯、聚丙烯、合成橡胶、苯胺燃料和油漆颜料等工艺过程,都装备着各种型式的搅拌设备。 第二节搅拌物料的种类及特性 搅拌物料的种类主要是指流体。在流体力学中,把流体分为牛顿型和非牛顿型。非牛顿型流体又分为宾汉塑性流体、假塑性流体和胀塑性流体。在搅拌设备中由于搅拌器的作用,而使流体运动。 第三节搅拌装置的安装形式 搅拌设备可以从不同的角度进行分类,如按工艺用途分、搅拌器结构形式分或按搅拌装置的安装形式分等。一下仅就搅拌装置的各种安装形式进行分类说明。 一、立式容器中心搅拌 将搅拌装置安装在历史设备筒体的中心线上,驱动方式一般为皮带传动和齿轮传动,用普通电机直接联接。一般认为功率3.7kW一下为小型,5.5~22kW为中型。本次设计中所采用的电机功率为18.5kW,故为中型电机。
机械搅拌设备的设计方法及要点分析
机械搅拌设备的设计方法及要点分析 管永俊 摘要:文章介绍了机械搅拌设备进行设计时的思路,在满足工艺条件下进行搅拌设备结构设计。分析了搅拌过程原理、搅拌器型式和搅拌罐体及搅拌轴的设计计算。 关键词:搅拌设备;设计方法;设计计算 搅拌操作可以使两种或两种以上的物料在外界力的作用下加速流动,从而使不同的物料在彼此之间相互分散,达到均匀混合,加速传热和传质的目的。搅拌的物料可以是液相、固相和气相,其中液相流体较多。通过搅拌设备的工艺过程可以使相溶的液相物料均匀混合,使不相溶的另液相均匀乳化,使气体在液相中均匀的分散,使固体粒子在液相中均匀悬浮。搅拌设备在工业生产中被用于物料混合、溶解、乳化、吸收、萃取、化合以及传热等工艺过程。在食品、医药、化工、水处理等工业生产中,带有搅拌装置的化工设备应用范围很广。由于机械搅拌操作条件可控范围较大,能适应多样化的工业生产,因此机械搅拌设备得到广泛应用。 机械搅拌设备由搅拌罐体和搅拌装置两大部分组成。搅拌罐体是搅拌液相流体为主体介质进行各种物理、化学过程的容器。搅拌装置由搅拌器、搅拌轴、轴封和传动装置组成,传动装置包括驱动电机、减速机、联轴器和机架。机械搅拌设备在工作中,由搅拌器的运动加速物料在罐体中完成物理、化学工艺过程。 由于搅拌设备的使用目的不同,机械搅拌操作可用于不同的行业,搅拌设备的结构也是多种多样,但都是通过物料的流动达到搅拌的目的。在搅拌罐体内,物料的流动状态与搅拌罐体的形状、有无挡板及搅拌器的形状、安装位置、转速等因素相关。因此在设计机械搅拌设备时,应对这些相关的因素进行设计,在满足所需工艺参数的前提下,利用最小的功率消耗达到搅拌的目的。 1 工艺参数的设定 为了设计机械搅拌设备应有工艺条件参数。了解搅拌设备的工作条件,如压力、温度,熟悉在工作条件下的物料特性,如密度、粘度、毒性、腐蚀性等。同时还应确定搅拌的目的及相应的操作方法,如加料方式。搅拌物料中是否有固体粒子,若有应确定固体粒子的存在形式,如溶解、悬浮、沉淀等。根据这些参数或工艺要求进一步确定与物料接触的部件的材质,判定电动机的工作环境和减速机的负载情况,确定轴封的使用条件。根据搅拌容积和充装系数设定搅拌罐体的结构及尺寸。根据搅拌过程中物料的流动状态可选定搅拌器的型式并确定是否设置挡板。 2 搅拌设备的设计 2.1 搅拌罐体的结构及尺寸 机械搅拌设备一般为立式圆筒形结构,上部分有椭圆形封头、平盖结构,分可拆和不可拆,下部分有椭圆形封头、锥形底、平底结构。换热型式分为内部换热和外部换热。依据工艺要求,内部换热可选盘管、蛇形管等换热装置,外部换热可采用整体型夹套、半圆管等结构进行换热。搅拌罐体属于压力容器范围时,应按照GB150进行设计。当罐体和夹套有压力时,一般选用椭圆形封头,为了出料需要也可选用圆锥形的罐底。搅拌罐体的容积一般为搅拌容积的1.25倍,对于发酵罐类的情况需适当增加罐体容积。搅拌罐体高度与内经之比(H/Di)通常情况下可取1~2,发酵罐类可取1.7~2.5。为了物料有上下方向的循环流动,罐体内部可设置挡板,挡板垂直安装,宽度为罐体内径的1/12~1/8。挡板与罐体内壁要有间距避免物料在挡板处停滞。 罐体尺寸可按照公式计算:
机械搅拌澄清池
实验四机械搅拌澄清池的实验 一、实验目的 1.通过机械搅拌澄清池模型的模拟实验,进一步了解其构造和工作原理。 2.熟悉机械搅拌澄清池运行的操作方法。 二、基本概念与工作原理 澄清池主要由集水槽、支撑桥、变速驱动装置、进出水管、加药管、取样管、泥渣排放管、底部轴承及轴承座、底部轴承润滑管、底部轴承支架、角度调整夹、第一反应室延长段、第一反应室、第二反应室、导流板、泥渣搅拌浆、搅拌叶轮、搅拌机轴、刮泥机轴、刮泥机臂、顶部支撑钢结构等部件组成。 机械搅拌澄清池是混合室和反应室合二为一,即原水直接进入第一反应室中,在这里由于搅拌器叶片及涡轮的搅拌提升,使进水、药剂和大量回流泥渣快速接触混合,在第一反应室完成机械反应,并与回流泥渣中原有的泥渣再度碰撞吸附,形成较大的絮粒,再被涡轮提升到第二反应室中,再经折流到澄清区进行分离,清水上升由集水槽引出,泥渣在澄清区下部回流到第一反应室,由刮泥机刮集到泥斗,通过池底排泥阀控制排出,达到原水澄清分离的效果。 三、机械搅拌澄清池的基本构造 机械搅拌澄清池的构造如图1所示。 图1 机械搅拌澄清池示意图
四、实验设备及仪器 1.有机玻璃模型—套。 2.浊度仪。 3.pH计。 4.投药设备。 5.玻璃仪器。 6.混凝剂A12(S04)3。 7.化学试剂等。 五、实验方法与步骤 首先熟悉机械搅拌澄清池的构造与工作原理,检查其各部件是否漏水,水泵与闸阀等是否完好。 1.在原水中加入混凝剂。 2.开启搅拌浆进行搅拌。 3.加大或减小进水流量,测出不同负荷下运行时的进出水浊度,并计算其去除率。 4.改变混凝剂的投加量,或调节池顶的升降阀来改变原水流量与泥渣回流量的比值,来寻求最优运行工况,并记录下来,供今后实验参考。 实验记录填入表1中。 表1 实验记录表 注:在流量选定时,以清水区上升流速不超过1.1mm/s为宜,如上升流速过大,效果不好。 六、实验结果与讨论 1.绘制搅拌速度与去除率的关系曲线。