铸钢件焊补工艺守则

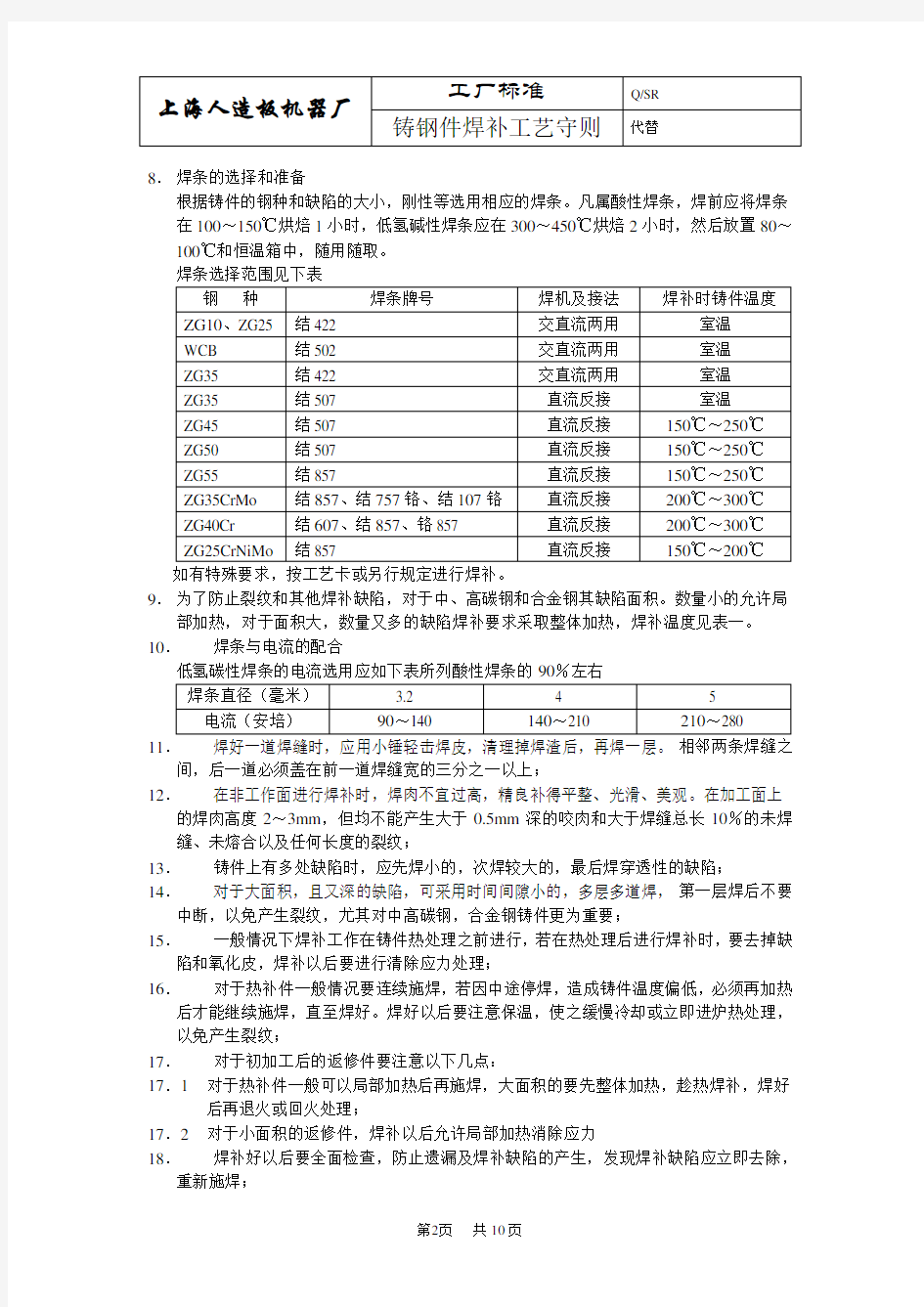
1.认真检查工具和焊机等设备,应符合《安全操作规程》中的各项规定,做到安全生产。2.铸件的裂纹、气孔、砂眼等缺陷的检查方法,一般用肉眼观察。对于耐高温、高压等关键产品,必要时可用渗透法等无损探伤的方法检查。
3.铸件缺陷的清除一般使用气割、碳弧气刨、风铲和砂轮等方法进行。
4.碳弧气刨清除缺陷时要注意碳刨工艺
4.1压缩空气的温度以室温为宜,压力为4~6公斤/平方厘米;
4.2电弧长度应选择在1~3毫米为宜;
4.3碳棒伸出长度在800~1000毫米,待烧剩到30毫米左右时停下调整;
4.4刨槽深度与碳棒倾角的选择如下表:
刨槽深度/m 2.5 3 4 5 6 7~8
碳棒倾角α25℃30℃35℃40℃45℃85℃4.5 碳素钢、普通低碳钢:用直流反接法
铸铁、铜及其合金:用直流正接
5.缺陷清除后的焊补坡口应是倾斜和圆滑过渡,表面不得有棱角和毛刺坡口,两侧氧化皮应清除。其坡口型式,应根据铸件的厚度缺陷形状、大小、深浅而定;
常用坡口型式有以下几种:
5.1未穿透的缺陷
5.2穿透的缺陷,穿透间隙较小者,且间隙小于20mm
5.3穿透的缺陷,穿透间隙较大者,且壁厚大于20mm
用t(3~4mm)铜板作垫板,焊后除去。
5.4空间尺寸很大的穿透缺陷,可以嵌入金属块焊补,其金属的材料应与铸件母材近似:
6.铸件缺陷周围50~60毫米内彻底清除油污、锈斑、水份等
7.铸件焊补一般采用如下工艺措施:
对于较短的裂纹或缺陷用直通式、焊接式、对称式焊接;
对于较长的裂纹或缺陷用逆向分段焊或跳焊法;
对于贯穿裂纹,间隙很大或刚性很大的铸件焊补时采用多层多道焊,轴孔可由上而下,逐圈堆焊,每次焊波相叠合不应小于三分之一焊波宽度;
8.焊条的选择和准备
根据铸件的钢种和缺陷的大小,刚性等选用相应的焊条。凡属酸性焊条,焊前应将焊条在100~150℃烘焙1小时,低氢碱性焊条应在300~450℃烘焙2小时,然后放置80~100℃和恒温箱中,随用随取。
焊条选择范围见下表
钢种焊条牌号焊机及接法焊补时铸件温度ZG10、ZG25 结422 交直流两用室温
WCB 结502 交直流两用室温
ZG35 结422 交直流两用室温
ZG35 结507 直流反接室温
ZG45 结507 直流反接150℃~250℃
ZG50 结507 直流反接150℃~250℃
ZG55 结857 直流反接150℃~250℃
ZG35CrMo 结857、结757铬、结107铬直流反接200℃~300℃
ZG40Cr 结607、结857、铬857 直流反接200℃~300℃
ZG25CrNiMo 结857 直流反接150℃~200℃如有特殊要求,按工艺卡或另行规定进行焊补。
9.为了防止裂纹和其他焊补缺陷,对于中、高碳钢和合金钢其缺陷面积。数量小的允许局部加热,对于面积大,数量又多的缺陷焊补要求采取整体加热,焊补温度见表一。10.焊条与电流的配合
低氢碳性焊条的电流选用应如下表所列酸性焊条的90%左右
焊条直径(毫米) 3.2 4 5 电流(安培)90~140 140~210 210~280 11.焊好一道焊缝时,应用小锤轻击焊皮,清理掉焊渣后,再焊一层。相邻两条焊缝之间,后一道必须盖在前一道焊缝宽的三分之一以上;
12.在非工作面进行焊补时,焊肉不宜过高,精良补得平整、光滑、美观。在加工面上的焊肉高度2~3mm,但均不能产生大于0.5mm深的咬肉和大于焊缝总长10%的未焊缝、未熔合以及任何长度的裂纹;
13.铸件上有多处缺陷时,应先焊小的,次焊较大的,最后焊穿透性的缺陷;
14.对于大面积,且又深的缺陷,可采用时间间隙小的,多层多道焊,第一层焊后不要中断,以免产生裂纹,尤其对中高碳钢,合金钢铸件更为重要;
15.一般情况下焊补工作在铸件热处理之前进行,若在热处理后进行焊补时,要去掉缺陷和氧化皮,焊补以后要进行清除应力处理;
16.对于热补件一般情况要连续施焊,若因中途停焊,造成铸件温度偏低,必须再加热后才能继续施焊,直至焊好。焊好以后要注意保温,使之缓慢冷却或立即进炉热处理,以免产生裂纹;
17.对于初加工后的返修件要注意以下几点:
17.1对于热补件一般可以局部加热后再施焊,大面积的要先整体加热,趁热焊补,焊好后再退火或回火处理;
17.2对于小面积的返修件,焊补以后允许局部加热消除应力
18.焊补好以后要全面检查,防止遗漏及焊补缺陷的产生,发现焊补缺陷应立即去除,重新施焊;
19.本操作规程适用于碳钢、低合金结构钢的一般铸钢件的缺陷焊补,如耐高压件及高合金钢铸件,按照有关工艺卡进行施焊。
铸件焊补工艺规程
铸件焊补工艺规程文件编码(GHTU-UITID-GGBKT-POIU-WUUI-8968)
铸件焊补工艺规程 本标准适用于铸钢件缺陷(疏松、缩孔、包砂、冷隔、裂纹、缺肉)的焊接修补及质量工作检查的依据。 1焊补前的准备 1.1焊接修补前必须用角磨机或电弧气刨将铸钢件缺陷内部、外部清理干净,不允许有油污、污垢、铁锈(氧化皮)粘砂等影响焊接修补质量的脏物。 1.2开出坡口,使铸件内部未氧化的金属露出,否则将会使电弧熄灭而无法焊补或重出现裂缝、气孔和未焊透的缺陷。 铸件缺陷坡口的确定 1.3对有可能延伸的裂纹应在裂纹两端钻截断孔,一般距离裂纹20mm,孔深超过裂纹深2-3mm,然后再铲坡口,截断孔作为坡口的两端包括在焊补之内。 2焊补工艺 2.1补焊要求 (1)由于焊补铸件表面不进行机械加工,所有焊前铸件不需预热 (2)贯穿裂纹间隙很大或刚性很大的铸件,焊补时可采用单面逐步堆焊法。
(3)在焊补过程中为减少焊接应力可进行敲击焊缝(除第一层和最后一层)。 (4)对于不预热的铸件或采用多层焊时,为减少焊补过热尽量用小直径焊条和小电流,间断焊补,使焊缝稍冷后,敲掉溶渣再继续焊补。 (5)焊接修补后焊肉及熔合区不得有夹渣、气孔、裂纹、未焊透、咬边、缺肉等缺陷。(6)对于焊接修补的非加工面都必须进行整形,消除焊补痕迹。整形可用砂轮打磨方法完成。 2.2焊补工艺参数 2.2.1焊材选用 焊条和焊丝类型的选择必须考虑工件的物理、机械性能和化学成份,一般先用成份与焊件金属相同或相近的焊条,参见表1 2.2.2焊条使用要求 (1)焊条在使用前应根据焊条药皮特性进行烘干处理,切忌急冷、急热、具体要求参见表2。烘干后焊条应及时装入保温筒随取随用。 (2)焊条严重受潮,黏在一起或药皮脱落,必须检验合格后方可使用。 (3)使用的焊条冷至室温4小时以后,必须按工艺重新烘干。 表2
铸钢件通用焊接工艺
铸钢件通用焊接工艺 编制: 审核: 批准: 湖南湘船重工有限公司 2014年11月1日
铸钢件通用焊接工艺 1.编制目的及适用范围 编制目的 为规范船体结构工程现场铸钢件的焊接质量,特编制此通用焊接工艺。 适用范围 本工艺适用于公司建造所有船舶的铸钢件现场焊接施工。 2.焊接方法的选择 平焊、横焊、立焊采用焊条电弧焊打底,CO2焊填充; 仰焊采用焊条电弧焊打底、填充。 3.焊接材料的选择 焊条电弧焊采用E5015(J507)焊条,φ、φ4; CO2焊采用ER50-6实芯焊丝,φ。 4.焊前准备 焊条在使用前必须按规定烘焙,E5015焊条的烘焙温度为350℃。烘焙1小时后冷却到150℃保温,随用随取,领取的焊条应放入保温筒内。 不得使用药皮脱落或焊芯生锈的变质焊条、锈蚀或折弯的焊丝。 二氧化碳气体的纯度必须大于%,含水率小于等于%,瓶装气体必须留1Mpa气体压力,不得用尽。 焊前,焊缝坡口及附近50mm范围内清除净油、锈等污物。 施焊前,复查组装质量,定位焊质量和焊接部位的清理情况,如不符合要求,修正合格后方可施焊。 焊条电弧焊现场风速不大于8m/s、气体保护焊现场风速不大于2m/s,当超过规定风速时应设防风装置。 焊接前,检查各焊接设备是否出于正常运行状态。 检查坡口尺寸是否达到要求。 焊工必须持证上岗。
5.焊接工艺 焊接工艺参数的选择 (1)立焊:焊条电弧焊打底,CO2焊填充; (2)横焊:SMAW打底,GMAW填充; (3)仰焊:SMAW打底,SMAW填充 预热与后热 (1)预热铸钢件与异种钢施焊前应进行焊前预热,采用2~3把烘枪进行火焰预热。预热温度为170℃。待温度降至150℃时方可进行焊接。 (2)后热焊接结束后,用烘枪对焊缝进行后热处理。后热温度为200℃,之后采用50mm的保温棉对焊缝后热处理部分进行包裹,缓冷至室温。 焊接坡口:所有对接缝位置均按照设计图纸开全焊透坡口 焊接工艺措施 5.4.1焊接层间温度应控制在200~250℃; 5.4.2打底焊接时,采用手工电弧焊多层多道焊接,每层焊缝高度约为焊条直径,当焊道宽度大于20mm时方可以进行二氧化碳气体保护焊; 5.4.3焊接前应将每个铸钢件焊缝的真实坡口形式记录备案, 5.4.4铸钢件与异种钢接头的焊接,应按厚板焊接的有关工艺规定进行施焊
铸钢件的焊接
铸钢件焊接 在船体结构中制造和修理中,经常会碰到铸钢件的焊接,比如舵叶、艉轴架等。由于一般铸钢件对强度要求较高,整体刚性很强,因此其焊接过程中的质量控制就显得极为重要,其中的重点就是防止焊接裂纹。 一、焊接方法及焊材 手工焊:碱性焊条CHE58-1 ф3.2或ф4.0 CO2焊:TWE-711 ф1.2 二、焊前准备 1、焊接之前应认真检查(外观检查、无损探伤)铸钢件是否存在砂眼、裂 纹、缩孔、气孔或夹渣等缺陷。若存在缺陷,应作适当的处理后再行焊 接。 2、坡口型式铸钢件坡口及其与板材的焊接节点具体要求须参考施工工艺。 典型的坡口有以下几种: 3、预热 点焊和正式焊接前都应对铸钢件进行预热,预热温度为100~150°C。 加热范围:焊缝坡口及其附近一侧至少100mm区域内用火焰加热,开始加热时注意摆动,以使铸钢件受热均匀。 三、焊接过程中的注意事项 1、施焊焊工必须要有相应部位的焊接资格证书。 2、点焊时的材料与正式焊接时的材料一致,只是点焊电流应较焊正式焊缝 时大10%~15%,点焊长度为50mm,间距为300mm。点焊后药皮药渣清除干 净,并且点焊焊缝不允许出现任何的缺陷,如出现缺陷,则必须清除干
净。 3、针对舵叶铸钢件的结构和位置特点,现场施工中严格管好节点全乎规范, 焊接中应尽量采用小电流、分散焊接。 4、层间温度焊接层间温度控制在100~250°C。 5、施焊过程中,各焊道或焊层的接头(起熄弧位置)应至少错开30~50mm。 6、焊后应立即用石棉布将焊接部位包起来,以保温缓冷。 四、焊后处理 1、当铸钢件的焊接工作量较大时,应在条件允许的范围内对其进行整体或 局部退火热处理,以消除应力,防止裂纹的产生,具体的退火工艺随铸 钢件的材料、厚度等不同而有所不同。 2、在退火处理完成后(如果有的话),对焊缝进行无损探伤,一般应做100% 的UT和100%的MT,确保焊缝质量达到要求。 最新阀门铸钢件的补焊处理方法! 最新阀门铸钢件的补焊处理方法! 补焊后处理 1、重要补焊 水压试验有渗漏的铸件、补焊面积>65cm2的铸件,深度>铸件壁厚20%或25mm的铸 件,ASTMA217/A217M-2007中均认为是重要补焊。对此种重要补焊A217标准中提出,都应进行去应力处理或完全再加热处理,而这种去应力处理或完全再加热处理,必须用经审定合格的方法进
铸件焊接焊补实用技术及焊补工艺规程
铸件焊补工艺规程 Q/HY-J12-2012 编制: 审核: 批准: 受控状态: 发文编号: 版本号: 2013年4月30日发布2013年5月10日实施
铸件焊补工艺规程 Q/HY-J12-2012 本标准适用于铸钢件缺陷(疏松、缩孔、包砂、冷隔、裂纹、缺肉)的焊接修补及质量工作检查的依据。 1 焊补前的准备 1.1焊接修补前必须将铸钢件缺陷内部、外部清理干净,不允许有油污、污垢、铁锈(氧化皮)粘砂等影响焊接修补质量的脏物。 1.2开出坡口,使铸件内部未氧化的金属露出,否则将会使电弧熄灭而无法焊补或重出现裂缝、气孔和未焊透的缺陷。 铸件缺陷坡口的确定 1.3对有可能延伸的裂纹应在裂纹两端钻截断孔,一般距离裂纹5-10mm,孔深超过裂纹深2-3mm,然后再铲坡口,截断孔作为坡口的两端包括在焊补之内。 1.4铸件的预热 1.4.1对于焊前需作预热的焊件,在焊接过程中必须保持焊件不低于规定的预热温度的下限值。 1.4.2对于不同钢种的不同铸件严格按照工艺要求选择不同的预热温度。 2 焊补
2.1扒挖后要将扒挖处打磨干净,磨掉增碳层,待确认清理干净后,方可进行焊接修补。 2.2根据铸件的不同钢种,按工艺要求选择合适的焊条牌号及规格,合适的焊机。 2.3根据铸件的不同缺陷选择合适的焊补方法。 2.3.1对于不同特点的裂纹可采用 a 焊补较短的裂纹可采用直通焊、逆向分段焊,对称焊。 b 焊补薄壁铸件及较长裂纹可采用跳焊、逐步退焊、交替焊。 2.3.2贯穿裂纹间隙很大或刚性很大的铸件,焊补时可采用单面逐步堆焊法。2.3.3圆形的不大缺陷孔用环形的焊缝焊补法。 2.4在焊补过程中为减少焊接应力可进行敲击焊缝(除第一层和最后一层)。 2.5对于不预热的铸件或采用多层焊时,为减少焊补过热尽量用小直径焊条和小电流,间断焊补,使焊缝稍冷后,敲掉溶渣再继续焊补。 2.6加工后发现缺陷,焊补时应在加工表面覆盖石棉板(或石棉布) 2.7对于不同要求,不同钢种的铸件焊补按特殊的工艺要求执行。 2.8焊接修补后焊肉及熔合区不得有夹渣、气孔、裂纹、未焊透、咬边、缺肉等缺陷。对于焊接修补的非加工面都必须进行整形,消除焊补痕迹。整形可用砂轮打磨方法完成。 2.9焊接修补后经检查确认不合格者,重新进行焊接修补。 2.10重大缺陷焊接修补后,操作者要认真填写“焊接修补记录单” 2.11焊补后需进行热处理的经检验合格后,交由热处理工序。 3 保温 3.1焊接修补完毕后,根据工艺要求需保温的铸件要采取覆盖保温材料进行保温,并填入《焊接修补记录单》。 3.2严格控制保温层厚度,确保保温时间。 4铸件焊接工艺(见附页) 5. 其他 对于铸钢件缺陷应在热处理前抛丸后进行,焊后进行热处理。若热处理后铸件经抛丸后发现缺陷,需再进行焊修的,焊后须重新进行热处理。 即:抛丸——缺陷焊补——热处理——抛丸——缺陷焊补——热处理——抛丸——机加工 本规定由生产技术部提出 本规定由生产技术部编制并负责解释 本规定由生产技术部负责实施
铸钢件缺陷焊补规程
铸钢件缺陷焊补规程 1.目的 规范阀体零件的补焊工艺,使被焊零件的性能稳定,保证阀门整体性能符合要求。 2.范围 本规程适用于本公司生产的阀门的铸钢件、阀体等的补焊。 3.职责 技术科负责补焊工艺评定和编制补焊工艺; 生产科负责组织补焊的实施; 车间焊工负责阀门零件的补焊; 质检科负责补焊件的PT检测和再次进行阀体压力试验; 公司办负责补焊操作人员的培训和上岗资格认可工作。 4.工作程序 对焊工、设备、环境的要求 从事焊接工作的焊工按要求进行考试合格。 工作前必须检查电源线是否漏电、二次线及外壳接地是否良好。一次与二次线路必须完整,焊钳必须绝缘良好。 工作前必须穿戴好防护用品,操作时(包括清渣)所有工作人员必须戴好防护眼镜或 面罩,扎紧袖口。 工作现场应保持干燥,通风良好。 焊接过程中应尽量避免多次引弧和电弧中断,在换焊条时,其接头一定要有很好的熔 合后方可继续焊接。 进行阀体补焊时,必须在消除体腔内压力后方可补焊,严禁带压补焊。 焊接设备应经常检修、擦拭。工作前应先让焊机空载运行2min~3min后方可焊接,以保证焊接设备处于良好的工作状态。 工作完毕后应先关闭电焊机,然后切断电源,切不可逆向停机;回收未用完的焊材,整理设备,清理现场。 焊前准备 阀体压力试验:当质检员发现阀体不上压后,应将阀门渗漏部位做出明显标记并口头通知焊工进行补焊。 检查所用设备(焊机、转胎等)运转情况是否正常,地线与工件连接是否紧固,避免因接触
不良损伤焊接表面。 检查焊条是否经过烘干处理。经过烘干的焊条放入保温筒;在烘干箱外停留时间不应超过1小时,以免焊条受潮。焊条尽量避免反复烘干。 认真清除焊道上的铁锈、油污、毛刺和水等。 补焊工艺 承压件的补焊 a.受压零件经水压试验后,在有缺陷位置打上标识。 b.补焊前,按已标注的缺陷位置用机械方法消除缺陷,然后打磨适当的坡口,其面积应在保证缺陷排除干净的前提下,尽量使打磨区窄小。保证凹槽无尖角,应平缓过渡,以免造成应力集中。对于裂缝,必须先在裂缝两端钻孔后,再用机械加工方法将缺陷清除。缺陷直径超过30mm 的阀体退回供方处理。 c.机械打磨排除缺陷后的待补件,应再用钢丝刷清理至露出金属光泽,经目测,确认缺陷已彻底排除为止。 d. 打磨合格的铸件,应将缺陷区周围15mm~20mm范围内的部分清理干净。凡待补焊件应仔细清除油污、脏物、铁锈。严格执行补焊规程并填写补焊记录。补焊后的阀体集中存放,随时或成批(如2吨左右)送供方退火处理。 e.补焊后的阀体要全部进行渗透试验,填写PT检验记录。 f.焊接时应注意层间清渣。 g.机械加工后的铸件,在同一缺陷位置,补焊次数不得超过二次。 h.清除焊渣、焊瘤。对焊缝进行打磨,使焊缝光滑过度到阀体表面,避免在焊趾部位造成应力集中而再次开裂。 焊接注意事项 a.应在引弧板或坡口内引弧,禁止在非焊接部位引弧。纵焊缝应在引出板上收弧,弧坑应填满,防止地线、电缆线、焊钳与焊件打弧。 b.电弧擦伤处的弧坑需经修磨,使其均匀过度到母材表面,修磨的深度应不大于该部位阀体厚度δs的5%且不大于2mm,否则应予补焊。 c.用焊条电弧焊补焊阀门时,一般应采用多层焊,各焊层焊道的接头应尽量错开,圆弧处应保证焊透与融合。 d.施焊过程中应控制层间温度不超过规定的范围,当焊件预热时,应控制层间温度不低于预热温度。 e.当PT检查结果不合格时,需进行焊缝修补,修补后的焊缝不允许出现未熔合、夹渣、咬边、
铸钢件补焊工艺守则
铸钢件补焊工艺守则文件编号:GY—JS—04 编制: 校对: 会签 批准: 福建政和水轮机制造有限公司 2003年月日
铸钢件补焊工艺守则 一、适用范围: 适用于碳素钢铸件和低合金钢铸件缺陷的焊补。 二、焊前的准备: 1.缺陷部位的清理:焊补前需将铸件缺陷部位的粘砂、氧化皮、气孔、裂纹等缺陷清除干净,并开出净口,使铸件焊补处露出金属光泽。 清理方法:(1)碳弧气刨(2)砂轮打磨(3)火焰切割(4)电焊条挖等。 坡口形状:应根据铸件壁厚和缺陷的特点(大小、深浅)决定,见表一。 表一 铜板, 说明:(1)坡口示意图只用示意坡口各种相关尺寸,由具体实际情况决定。 (2)所有坡口及钝边间隙应要求焊缝能焊透。
2.焊条的选择:应根据母材的要求来选择,见表二 表二 3、焊条的焊干要求:碱性低氢型焊条在使用前要求烘干,并做到用多少拿多少,见表三。 表三 4、铸件的预热 由于材质、结构形状、大小的不同,焊补时会产生应力、变形甚至裂纹,因此焊前铸应进行预热。 一般情况:(1)碳当量Cep<0.45时不需预热,但厚度≥60气温低于-50C特大钢性构件时适当预热100~1500C。 注:冲击式转轮水斗焊补时均需预热。 (2)碳当量Cep≥0.45,铸件预热200~3000C,当壁厚较薄<10mm,形状简单,缺陷小的不重要件,可不进行预热。 四、焊补方法: 1、对于焊补短的裂纹可以用直通焊,对称焊,逐步退焊。 2、对于长的缺陷可用逆向分段焊,跳焊。
3、对于圆形的缺陷孔,可用环形的焊缝焊补。 4、铸件表面堆焊,焊纹重叠要求每道焊纹重叠≥1/3焊缝宽度。 5、在焊补过程中,可用小锤击焊缝以减少焊接应力。 6、于薄壁铸件或多层焊时,为避免过热,应尽量用小直径、小电流间断焊接,使焊 缝稍冷后再继续施焊。 7、焊接电流选择见表四 表四 8、补面积较大且缺陷在铸件重要部位,焊后应立即退火处理。 五、焊后检验 1、按铸件热处理工艺执行。 2、对已经热处理后铸件的补焊,如果面积大,缺陷严重及重要的受力部位,焊补后应进行消除内应力处理。
铸钢件焊接工艺规程说明书
JJS/WPS-2001-01 铸钢件的CO2半自动气体保护焊/手工电弧焊 焊接工艺规程说明书 编制:郭建华 审核:陈学亮 批准:张林坤 靖江造船厂
2001年5月
1. 范围 1. 1 焊接方法 CO2半自动气体保护焊/手工电弧焊 1. 2 应用范围 本说明书适用于船体铸钢件与碳钢的CO2半自动气体保护焊或手工电弧焊。 2. 焊接材料 焊接方法 材料名称牌号 尺寸 (mm) 级另U制造厂 CO2半自动气体 保护焊 药芯焊丝 SQJ501Ni①1.23YSAH10天津三英焊业有限公司 TWE-711①1.2 3SAHH 3YSA 天泰焊材工业股份有限公司气体:CO2纯度》99% 手工电弧焊焊条JH.E5015① 3.2, 4.03YH10江阴东青焊接材料有限公司3. 接头细节 3. 1 手工电弧焊焊接接头示意图 3. 2 CO2半自动气体保护焊焊接接头示意图
①单边深“ V ”形坡口: 厂 1): r 1 10~20° 30~50 L 上 10?14mm - —| 25~40 — — ②“ K ”形坡口: 注:②反面须碳刨清根 4. 焊接条件 4. 1 焊接要求 1. 焊接之前必须除去预加工边的锈蚀,油污,灰尘,潮湿等。 2. 施焊时若发现坡口处的间隙太大,则应先在碳钢侧堆焊,直到坡口间隙满足要求方 可按 相关工艺进行施工。 3. 各焊缝的焊接必须一次性完成,中途不得停止。 4. 每道焊层必须用钢丝刷清理打磨干净。 5. 如果坡口用碳弧气刨开设,坡口处的碳迹必须打磨干净。 6. 电焊条须经烘干处理(详见4.5),未经烘干的焊条不得使用。 7. 现场焊接施工须使用保温桶,且有相应的电加热保温措施。 8. 手工焊时焊条的摆动幅度应小于所用焊条直径的 3倍。 4. 2 预热 1. 焊缝预热温度为125~200C (预热范围距焊缝中心为 75mm ),用电加热器或火焰进 行 加热并覆盖以防火岩棉,预热时必须缓慢且均匀,以避免出现裂纹和变形(每小
铝合金铸件补焊工艺
铝合金铸件补焊工艺 补焊铸件的确定: 1、由检验人员确定补焊铸件,补焊部位应在铸件上标出。 2、允许补焊的缺陷如下:a)夹杂、砂眼、缩孔、气孔、冷隔等。b)机械加工产生的机械损 伤。 补焊材料: 1、补焊用的焊丝应与铸件材料相同。(以后采用铸造浇注的焊丝) 2、焊丝使用时的表面应干净,无氧化物、油污和锈蚀。 铸件缺陷的清理: 1、补焊前应用风动铣刀或其它工具对铸件缺陷部位进行打磨或扩修成坡口。 2、铸件缺陷部位开坡口应将缺陷完全排除,并保证坡口面光滑。 3、较大的穿透性缺陷清理后,应在背面垫上不锈钢或耐火砖片垫片,垫片应留有3-4mm 的间隙,便于完全焊透。 4、对需要补焊的部位,应在离坡口边界10-30mm的范围清除掉铸皮、氧化物和其他污物, 在开穿透性坡口的情况下,可从两面进行清理。 5、表面清理过的铸件应及时进行补焊,停放时间一般不超过5h. 铸件补焊前的预热 1、整体预热;适合各类型的铸件。 2、局部预热: 局部预热可用氧—乙炔焰进行,应用中性焰进行,预热时应避免穿堂风。 局部预热的铸件,加热面积应距离缺陷坡口边界不小于200mm的地方。 3、不预热 对单个的小缺陷和不易变形的铸件,可不预热。 预热要求预热温度一般为250-350度 补焊手工氩弧焊补焊时,应尽量小电流,短弧焊、小直径焊丝和小体积熔敷金属,补焊过程中,焊枪与零件表面的夹角60-70度。 补焊过程的控制 1、补焊时,焊缝均应有3-4mm的余高。 2、为防止铸件产生冷裂纹,补焊后应采用石棉布将其覆盖。 3、补焊时不允许近焊缝金属过热。 4、铸件的同一处允许补焊次数不超过三次。 补焊后的热处理 允许补焊后的铸件余同一牌号合金同炉热处理。 2011年6月26日
铸钢件焊补工艺守则
1.认真检查工具和焊机等设备,应符合《安全操作规程》中的各项规定,做到安全生产。2.铸件的裂纹、气孔、砂眼等缺陷的检查方法,一般用肉眼观察。对于耐高温、高压等关键产品,必要时可用渗透法等无损探伤的方法检查。 3.铸件缺陷的清除一般使用气割、碳弧气刨、风铲和砂轮等方法进行。 4.碳弧气刨清除缺陷时要注意碳刨工艺 4.1压缩空气的温度以室温为宜,压力为4~6公斤/平方厘米; 4.2电弧长度应选择在1~3毫米为宜; 4.3碳棒伸出长度在800~1000毫米,待烧剩到30毫米左右时停下调整; 4.4刨槽深度与碳棒倾角的选择如下表: 刨槽深度/m 2.5 3 4 5 6 7~8 碳棒倾角α25℃30℃35℃40℃45℃85℃4.5 碳素钢、普通低碳钢:用直流反接法 铸铁、铜及其合金:用直流正接 5.缺陷清除后的焊补坡口应是倾斜和圆滑过渡,表面不得有棱角和毛刺坡口,两侧氧化皮应清除。其坡口型式,应根据铸件的厚度缺陷形状、大小、深浅而定; 常用坡口型式有以下几种: 5.1未穿透的缺陷 5.2穿透的缺陷,穿透间隙较小者,且间隙小于20mm 5.3穿透的缺陷,穿透间隙较大者,且壁厚大于20mm 用t(3~4mm)铜板作垫板,焊后除去。 5.4空间尺寸很大的穿透缺陷,可以嵌入金属块焊补,其金属的材料应与铸件母材近似: 6.铸件缺陷周围50~60毫米内彻底清除油污、锈斑、水份等 7.铸件焊补一般采用如下工艺措施: 对于较短的裂纹或缺陷用直通式、焊接式、对称式焊接; 对于较长的裂纹或缺陷用逆向分段焊或跳焊法; 对于贯穿裂纹,间隙很大或刚性很大的铸件焊补时采用多层多道焊,轴孔可由上而下,逐圈堆焊,每次焊波相叠合不应小于三分之一焊波宽度;
精密铸造工艺规程
精密铸造工艺规程 编制: 审核: 批准: 日期: 1 / 23
文件目录 序号文件编号文件名称页码 1 JZQ-ZZ-GY01-2013 蜡型工艺规程 3 2 JZQ-ZZ-GY02-201 3 浇口棒蜡模工艺规程 5 3 JZQ-ZZ-GY03-2013 蜡模组焊工艺规程 6 4 JZQ-ZZ-GY04-2013 制壳工艺规程7 5 JZQ-ZZ-GY05-2013 脱蜡工艺规程9 6 JZQ-ZZ-GY06-2013 蜡处理工艺规程10 7 JZQ-ZZ-GY07-2013 焙烧工艺规程11 8 JZQ-ZZ-GY08-2013 熔炼工艺规程12 9 JZQ-ZZ-GY09-2013 浇注工艺规程14 10 JZQ-ZZ-GY10-2013 后处理工艺规程15 11 JZQ-ZZ-GY11-2013 热处理工艺规程16 12 JZQ-ZZ-GY12-2013 焊补工艺规程19 13 JZQ-ZZ-GY13-2013 试棒管理规程22 14 15 16 2 / 23
3 / 23 蜡型工艺规程 一、工艺参数 1.蜡料的配臵(﹪) 季 节 冬 季 夏 季 四 季 备注 编号 材料 (1) (2) (3) (4) (5) 5-10月按夏季 11-4月按冬季 回收蜡 95-97 85-87 92 82 硬脂蜡 3-5 8-10 8 13 50 石蜡 5 5 50 2.蜡料使用的温度 序号 名称 温度℃ 序号 名称 温度℃ 1 熔点 56—58 2 搅成糊状温度 47-49 3 熔化温度 90-95 4 蜡料压蜡温度 42-50 5 压蜡保温水温度 48-53 3.压缩空气工作压力0.25—0.4 MPa 4.搅料用碎蜡块加入量占蜡液的30%(碎蜡块30% 蜡液70%) 5.新蜡与硬脂酸的比例1∶1 6.作业环境温度0-30℃ 南京金正奇交通设备有限责任公司 铸造事业部 文件编号 JZQ-ZZ-GY01-2013 版 本 A 编制日期 2013-3-27
铸钢件检验规范
《铸钢件检验规范》执行情况会议纪要 2009年09月24日下午1点在福建海源公司四楼会议室,我司有关技术人员与三重技术人员就《检验规范》进行探讨,并针对近期铸钢件质量下滑等问题进行讨论。现将会议主要内容纪要如下: 一、关于《检验规范》使用:我司王总工程师提出,《检验规范》的制订是根据我司二十年压机制造过程中,结合实际情况,参照国家铸造标准范围内的,外协铸造厂家完全能做到的。三重张总工程师也同意了以上观点,双方同意以《检验规范》为产品检验判定标准。 二、会议就近期铸钢件质量下滑提出暂时解决方案,要求三重铸锻公司在一个月之内(过渡时间为一个月),需达到我司《检验规范》的质量要求。出厂的产品因铸造缺陷而进行焊补,导致我司上下架超出两次,第二次及以上由此引起的经济损失(如机加工费)由铸造厂家负责,并按最后成品的时间来考核交货时间,超出时间,按合同规定执行。因尺寸缺陷而进行焊补的,由此引起的延误工期,按合同规定的超出时间,给予扣款执行。 三、会议就因质量问题判定退回厂家进行返工的,如大面焊补,较大裂纹等,请厂家按合同规定,返工送达我司时,需提供缺料报告,焊补与修复工艺,退火纪录,探伤报告,与质量承诺书。 四、关于判定废品的程序。在我司检验部门按公司规定程序执行,不合格品判定,按规定销毁,不得重复交付废品的铸件。 五、对现场四件HF1100上梁返工回我司,要求三重铸锻公司派探伤人员现场与我司质检人员共同探伤复检,9月26日之前人员到位。 六、关于新产品图纸进行技术交流问题,要求铸造厂接到新产品图纸时,因铸造工艺需要,需与我司技术中心沟通,并以文字形式备案。 参加人员 三重公司:张总工程师与高伟峰经理 海源公司:王总、曹工、管代、郑祥光、唐建新、林森清、蒋荣辉、何建新
几种常见铸钢件缺陷的补焊方法和经验
几种常见铸钢件缺陷的补焊方法和经验 https://www.360docs.net/doc/381668797.html, 2011年12月10日09:40 点击数:306 核心提示:本文介绍了常见阀门铸钢件的缺陷及补焊方法,铸钢件缺陷的科学补焊,是一项节能的再制造工程技术。本文就缺陷处理判断,剔除作了详细讲解。 本文介绍了常见阀门铸钢件的缺陷及补焊方法,铸钢件缺陷的科学补焊,是一项节能的再制造工程技术。本文就缺陷处理判断,剔除作了详细讲解。对补焊的方法,次数,补焊后的处理经验给予解答。总结了缺陷补焊中经济、有效的实用经验。 1、缺陷处理 缺陷剔除 在工厂里一般可采用碳弧气刨吹去铸造缺陷,然后用手提角磨机打磨缺陷部位至露出金属光泽。但生产实践中更多的是直接用碳钢焊条大电流除去缺陷,并用角磨机磨出金属光泽。一般铸件缺陷剔除,可用<4mm-J422焊条,160~180A电流,将缺陷除干净,角磨机将缺陷口打磨成U形,减少施焊应力。缺陷清除的彻底,补焊质量好。 缺陷判断 在生产实践中,有些铸件缺陷不允许补焊,如贯穿性裂纹、穿透性缺陷(穿底)、蜂窝状气孔、无法清除的夹砂夹渣和面积超过65cm2的缩松等,以及双方合同中约定的其他不能补焊的重大缺陷。在补焊前应判断缺陷的类型。 缺陷部位预热 碳素钢和奥氏体不锈钢铸件,凡补焊部位的面积<65cm2,深度<铸件厚度的20%或25mm,一般无需预热。但ZG15Cr1Mo1V、ZGCr5Mo等珠光体钢铸件,由于钢的淬硬倾向大,冷焊易裂,应作预热处理,预热温度为200~400℃(用不锈钢焊条补焊,温度取小值),保温时间应不少于60min。如铸件不能整体预热,可用氧-乙炔在缺陷部位并扩展20mm后加热至300-350℃(背暗处目测观察微暗红色),大号割炬中性焰枪先在缺陷处及周边做圆周快速摆动几分钟,然后改为缓慢移动保持10min(视缺陷厚度而定),使缺陷部位充分预热后,迅速补焊。 2、补焊方法 要求 对奥氏体不锈钢铸件进行补焊时,要在通风处,使之快速冷却。对珠光体低合金钢铸件和补焊面积过大的碳钢铸件则应选背风处或用挡风板遮挡,避免快冷造成裂纹。补焊一个堆层的,补焊后应立即清除药渣,并沿缺陷中心向外均匀地锤击,降低补焊应力。若补焊分几层进行(一般3~4mm为一补焊层),则每层补焊后均要及时清除药渣和锤击补焊区域。如在冬季施焊,ZG15Cr1Mo1V类的珠光体合金钢铸件,每补焊一层还应用氧-乙炔反复加热,再迅速补焊,以避免产生焊接裂纹。
铸钢焊接工艺
1 汽轮机用铸钢 铸造是零件毛坯最常用的方法之一,具有一定形状和使用性能的铸件广泛用于机械制造,是现代大型工业的基础。铸钢在强度和韧性比铸铁或其他铸件都优越,焊接性也良好,因此铸钢作为重要部件广泛用在汽轮机制造中。不但铸钢作为部件占汽轮机结构占一定比重,而且,铸钢件的焊接和补焊又占有焊接工作的很大的工作量。 汽轮机汽缸、蒸汽室、主汽阀、调解阀容器部件都由铸钢制造。诸如汽缸等盛汽容器部件内承受的压力和温度高,同时,工作状态承受着内、外压差,蒸汽流出的反作用力和各种连接管道热状态时对部件的作用力等,所以这些部件均要求具有足够的强度和刚度。这就使扥部件壁厚、形状复杂、体积大,属于大型铸钢件。 铸钢的化学成分与轧材、锻件几乎完全相同,具有一定的力学性能,随着合金成分的增加具有相当的高温性能。对高温下工作的铸件还必须具有一定持久强度和蠕变强度、良好的抗热疲劳性能和抗氧化性。 随着机组的工作参数不同,汽轮机铸钢件分别采用碳素铸钢、铬-钼铸钢、铬-钼-钒铸钢铬12%铸钢。铬-钼钢的工艺性能、抗裂纹扩展性能和塑、韧性较鉻-钼-钒钢好,但鉻-钼-钒钢热强性较高。随着超临界和超超临界汽轮机工作温度的进一步提高,发展并采用了改良型和新型鉻12%铸钢。随着汽轮机的发展,作为重要部件的铸钢技术伴随着提高和进步。近几年,改良型9%Cr 钢的使用逐渐增多,而相应的焊接和铸钢件的补焊工作量明显增加。 铸钢与锻钢比较,在截面尺寸不很大,形状和热处理条件相似的情况下,铸
钢和锻钢的力学性能大致相似。铸钢的强度和塑性介于纵向和横向性能的变化范围之内,铸钢还有各向同性的优点。但是随着铸钢件壁厚的增加,冶金缺陷如气孔、疏松、铸态组织等对力学性能的影响要比锻件更为突出,因此厚壁铸钢件尽管强度和锻件相似,但塑性和韧性要比锻件低。对于大型铸钢件多采用正火、回火作为最终热处理的力学性能等级比同钢号的锻件低。因此在设计选材和焊接必须给予考虑。 汽轮机铸缸件按使用材料性质可以分为碳素钢铸件、低合金钢铸件和高合金钢铸件。汽轮机主要铸钢件材料见表1: 表1 汽轮机铸钢件
焊补检验规程
铸钢件缺陷焊补操作检验规程 一.焊前准备工作 1.根据不同缺陷选择不同清理方法:对大型铸件及合金钢铸,清 除缺陷前必局 部或全部铸件预热,预热温度100~150℃。 (1)、缺肉、浇不足等缺陷应打磨光铸件表皮,露出金属基体后方可补焊。 (2)、各种适宜剖口型式按上图规定。 2. 一般铸件的缺陷清理可用气割,碳弧气刨,风铲进行,精加工的铸件缺陷可用碳弧气刨、风铲进行。对较大的缺陷可用气割进行。 3. 铸件缺陷周围50毫米内如有油、锈、砂子等焊前需清理干净。 4. 所有剖口在准备工作中应保证将缺陷清理彻底,剖口处应保证
圆滑,氧化皮要用风铲打净。 5. 焊前准备工作完毕,检查合格方可施焊。 二. 焊补工艺 1. 对于含碳量0.35%以下的钢号,如:ZG25、ZG35、ZG20MnSi (1)、根据缺陷性质选择相应的剖口,按前边规定做好焊前准备工作。 (2)、对上述钢号补焊,原则上不预热,但对大件重要部位应进行预热焊,预热温度100~150℃,焊后要保温缓冷。 (3)、焊补过程应仔细清除熔渣及金属溅斑。 (4)、焊补较宽的缺陷时,为减小应力,除焊补过程用锤击方法以外,焊接程序可以参照下列方法,即先沿剖口堆1~2层(如下图),然后堆满凹下部位(图2b),再沿前剖口堆焊数层(图2c)以此类推,直至堆满整个剖(图2d),应绝对避免焊宽焊道(图2e)。
(图2) (5)、如果铸件上有多处缺陷时,应先焊小的,后焊大的,最后焊穿透的缺陷。 (6)、经加工发现的缺陷,焊补过程应注意以下几点: a. 缺陷处周围加工面应用石棉布(板)挡上,防焊接的飞溅物落上影响光洁度。 b. 不应使焊接部位有过热现象,因此应间断焊接。并尽量采用小直径和小电流焊接。采用的焊条,如THJ422、THJ506、507、606、607 2. 对于含碳量较高的碳钢和低合金钢的铸件,如:ZG45、ZG55、ZG35SiMn、ZG40Mn、ZG42SiMn焊接规范如下: (1)、焊前准备工作同前 (2)、焊补上述钢号铸件,一定了解清除铸件具体钢号及有无特殊热处理要求(调质或表淬)加工后的工件要了解是什么状态,以便选择焊补方法。 (3)、铸件焊补一般是在热处理正火后进行,焊后回火需要调质的应调质以前焊补。 (4)、铸件表面缺陷(个别包砂、重皮)面积不大的,可在热处理前进行焊补,但焊后必须立即热处理。 (5)、缺陷是裂纹或较大的缺陷,必须焊前预热焊补。 (6)、焊补上述牌号的铸件,应保证在焊补过程中焊补处的工作温
铸件焊补工艺规程
铸件焊补工艺规程 本标准适用于铸钢件缺陷(疏松、缩孔、包砂、冷隔、裂纹、缺肉)的焊接修补及质量工作检查的依据。 1 焊补前的准备 1.1焊接修补前必须用角磨机或电弧气刨将铸钢件缺陷内部、外部清理干净,不允许有油污、污垢、铁锈(氧化皮)粘砂等影响焊接修补质量的脏物。 1.2开出坡口,使铸件内部未氧化的金属露出,否则将会使电弧熄灭而无法焊补或重出现裂缝、气孔和未焊透的缺陷。 铸件缺陷坡口的确定 1.3对有可能延伸的裂纹应在裂纹两端钻截断孔,一般距离裂纹20mm,孔深超过裂纹深2-3mm,然后再铲坡口,截断孔作为坡口的两端包括在焊补之内。 2 焊补工艺 2.1补焊要求 (1)由于焊补铸件表面不进行机械加工,所有焊前铸件不需预热 (2)贯穿裂纹间隙很大或刚性很大的铸件,焊补时可采用单面逐步堆焊法。(3)在焊补过程中为减少焊接应力可进行敲击焊缝(除第一层和最后一层)。(4)对于不预热的铸件或采用多层焊时,为减少焊补过热尽量用小直径焊条和小电流,间断焊补,使焊缝稍冷后,敲掉溶渣再继续焊补。 (5)焊接修补后焊肉及熔合区不得有夹渣、气孔、裂纹、未焊透、咬边、缺肉
等缺陷。 (6)对于焊接修补的非加工面都必须进行整形,消除焊补痕迹。整形可用砂轮打磨方法完成。 2.2焊补工艺参数 2.2.1焊材选用 焊条和焊丝类型的选择必须考虑工件的物理、机械性能和化学成份,一般先用成份与焊件金属相同或相近的焊条,参见表1 2.2.2焊条使用要求 (1)焊条在使用前应根据焊条药皮特性进行烘干处理,切忌急冷、急热、具体要求参见表2。烘干后焊条应及时装入保温筒随取随用。 (2)焊条严重受潮,黏在一起或药皮脱落,必须检验合格后方可使用。 (3)使用的焊条冷至室温4小时以后,必须按工艺重新烘干。 表2 2.2.3焊条直径的选用见表3 表3
zk汽轮机铸钢件补焊技术条件
ZB K54 039-90 汽轮机铸钢件补焊技术条件 代替 JB/DQ 1030-81 1 主题内容与适用范围 本标准规定了汽轮机铸钢件的补焊及其验收要求. 本标准适用于汽轮机汽缸、主汽阀、调节阀、蒸汽室、喷嘴室和隔板等铸钢件的补焊. 2 引用标准 ZB K54 038 汽轮机铸钢件技术条件 GB 5677 铸钢件射线照相及底片评定 ZB K54 003 汽轮机承压件水压实验技术条件 ZB K54 004 汽轮机铸钢件磁粉探伤及质量分级方法 ZB K54 007 汽轮机主汽管、汽缸、蒸汽室、进出汽接管及阀壳焊接技术条件 ZB K54 010 汽轮机铸钢件超声波探伤及质量分级方法 3 一般规则 3.1 补焊铸钢件的化学成分和力学性能应符合ZBK54 038的规定. 3.2 补焊应在铸钢件热处理后进行. 3.3 铸钢件的补焊,应由经考试合格的焊工担任. 3.3.1 从事承压铸钢件补焊的焊工,必须持有地、市一级劳动部门发给的焊工合格证. 3.3.2 焊工所能从事的焊接方法和焊接位置等,应与焊工合格证上考试合格工程相符. 3.4 补焊用焊接材料(焊条、焊丝、焊剂和保护气体等)应符合图样或工艺文件的规定. 3.4.1 手工电弧焊焊条可按附录A选用.采用其他焊接方法时,应根据铸钢件的化学成分、力学性能和工作条件选择相应的焊接材料.
3.4.2 焊接材料必须按有关标准进行检验,未经检验或检验不合格的不得进行补焊. 3.5 对于铸钢件的缺陷,凡能够采取一定的技术措施,确保补焊质量的,一般允许补焊.只有当缺陷波及面广而无法清除干净或补焊不能保证质量时,才不允许补焊. 4 缺陷清理 4.1 清除缺陷可用机械加工、铲凿、气割或碳弧气刨等方法. 4.1.1 使用气割或碳弧气刨时,可按附录A推荐的温度进行预热. 4.1.2 缺陷应清除干净,补焊坡口及其周围10mm范围的表面须露出金属光泽. 4.2 缺陷清除后,必须进行外观检查,凡属裂纹性质的缺陷,清除后应进行磁粉探伤、渗透检查或酸清检查. 4.3 在保证补焊质量和操作方便之下,补焊坡口应尽量小,且坡口形状不应呈急剧变化,表面应平整,底部应平缓,不允许有尖角存在. 4.4 补焊前应对坡口表面及其周围存在的油、水和锈等污物进行清理. 5 预热 5.1 需要预热的铸钢件,可按附录A推荐的温度进行预热. 5.2 在焊接过程中,要始终保持热温度,同时要严格控制层间温度不超过预热温度100℃. 5.3 预热可采用整体预热或局部预热.当局部预热时,加热速度不宜过快,并应保证离坡口边缘100mm范围内,不低于所要求的预热温度. 6 补焊 6.1 补焊应按经焊接工艺评定后所制定的焊接工艺规程进行补焊. 6.2 有下列情况之一者,须重新进行焊接工艺评定,重新制定焊接工艺规程,方可对产品进行补焊. a.铸钢件材料改变。 b.焊接材料成份改变。 c.焊接方法改变。
承压铸钢件焊补技术条件
承压铸钢件焊补技术条件 1.准备焊补的铸钢件缺陷,必须经过检查人员的检查,认为允许焊补后才能进行焊 补。焊补工作应按焊补工艺规程进行,并应由经过考试合格的熟练的焊工担任。 2.正确加工焊补坡口的尺寸和形状,是保证焊补质量的必要条件,坡口的形状不应 有急剧的变化,坡口表面要平整,不允许有尖角存在,底部应平缓,以尽可能减少焊补应力。对合金钢铸件,在裂纹清除后,焊前应进行磁粉探伤检查,焊补前缺陷的修整或坡口的制备质量不符合要求时,焊工有权拒绝进行焊补。 3.准备焊补的铸件,必须将缺陷全部清除干净,直到露出完好的金属再进行焊补。 4.铸钢件允许焊补的缺陷,累计长度不得超过该方向总长度的1/6。法兰径向的缺陷 不得大于法兰宽度的1/3。 5.在不影响铸钢件强度及外观质量时,允许不修整或不焊补的缺陷范围如表1. 表1 注:超过表1 规定的范围应进行焊补。 6.铸钢件缺陷为下列情况时,无论缺陷位于什么部位,均不允许焊补应予报废。 (1)超出第7条表2允许焊补范围的砂眼、夹渣、气孔、疏松及裂纹或铸件具有的缺陷位于无法进行焊补及虽能焊补,但不能保证焊补质量的部位时; (2)铸钢件在精加工后发现的缺陷,如经焊补不能保证零件的质量时,或焊补对密封面等重要位置有影响时; (3)铸钢件精加工后,在同一法兰上需焊补的螺孔数多于两个或两个需焊补的螺孔相邻时; (4)非承压部位穿透性的孔大于9cm2。
7.铸钢件允许焊补的缺陷范围如表2.。 表2 注:①表2所指的面积和深度,系指一处缺陷修整后所具有的实际面积和深度。为了寻找缺陷和便于焊补(加工焊补坡口)而不得不扩大的面积,不得超过表2规定的面积一倍。其扩大的面积部份深度h: 当壁厚S≤25mm, 则h≤1/3S 当壁厚S=26-36mm, 则h≤1/4S 当壁厚S≥37mm, 则h≤10mm ②缺陷在不超过表2规定数量内的总合面积时,允许超出规定的缺陷焊补数量; ③若缺陷数量没有达到表2所规定的数量时(即只限一处)。则缺陷本身的实际面积可作如下放宽: 当Dg=100-150mm 面积≤30 cm2 当Dg≥200mm 面积≤40 cm2 ④超过表②和注①、③所规定的缺陷面积,深度和处数时,应予报废。 8.铸钢件在水压试验时,如发现渗漏,原则上不允许焊补,如需焊补必须经采购商 单位的设计、工艺、检查等有关部门共同协商同意后,方可按规定的要求进行焊补,焊补后须重新进行水压试验,如再有漏水现象,应予报废,不得进行第二次同一缺陷的焊补。 注:焊补的铸钢件如需进行热处理,则水压试验必须在热处理之后进行。
铸钢件工艺
模具、芯骨、工装、夹具、专用检测器具、专用加工设备 原辅材料、备品、备件 检验 检验冶炼造型 浇注 铸件待冷却铸件出型清砂铸件清理铸件热处理铸件毛坯精整机加工 发运 包装 油漆 抛丸 检验 检验 检验 检验 检验 检验检验 检验检验检验
2、产品主要成份、性能、技术质量指标 (1)材质要求具体化学成份为(%):C 0.17~0.23;Si≤0.60;Mn 1.0~1.50;P≤0.020;S≤0. 015;Cr≤0. 30;Mo≤0. 15;Ni≤0.40;Al≤0.020 ; Re0.2~0.35(加入量) (2)机械性能要求 屈服强度≥230Mpa 抗拉强度≥450Mpa 延伸率≥22% 冲击功≥40J 1)按GB11352标准要求随炉提取试样,每一个炉号制备二组试样,其中一组备查。 2)为确保具有良好的焊接性能,节点铸件碳当量控制在CE≤0.42。 3)铸件表面质量符合设计要求,表面粗糙度达到GB6060.1标准要求。 4)铸件的探伤要求,按GB7233探伤, 采用6㎜探测头,管口焊 缝区域150mm以内范围超声波100%探伤,质量等级为Ⅱ级, 其余外表面10%超声波探伤,质量等级为IV级。不可超声波 探伤部位采用GB9444磁粉表面探伤,质量等级为III级。 5)节点的外形尺寸符合图样要求,管口外径尺寸公差按负偏差 控制。 6)热处理按照Q/32182HQA05-2002标准要求,铸件进行正火处 理(920±20℃,出炉空冷,加640±20℃回火处理)。 7)涂装处理要求:表面采用抛丸或喷砂除锈,除锈等级Sa2.5
级,随即涂水性无机富锌底漆,厚度50μm,环氧云铁中间漆 2×30μm。 3、铸造工艺参数 (1)加工余量按照GB/T11350-89,CT12H/J级。 (2)模样线收缩率2.0% 铸件毛坯尺寸偏差符合GB6414-86中CT12要求。 4、铸造工艺说明 (1)为保证叉管与杆件相交处质量,考虑尽可能将支管水平放置,分二箱造型,在铸件上平面分型,整体分两半实模。 (2)冒口采用标准保温冒口套Φ400×h600,5件, (3)型砂:铸型和泥芯均采用树脂砂,表面涂锆英粉涂料二遍,用煤油喷枪辅助烘干。 (4)铸件毛重约6000㎏,浇冒口约重3000kg,工艺出品率 66.7%。
铸件焊补工艺规程
铸件焊补工艺规程 Company Document number:WTUT-WT88Y-W8BBGB-BWYTT-19998
铸件焊补工艺规程 本标准适用于铸钢件缺陷(疏松、缩孔、包砂、冷隔、裂纹、缺肉)的焊接修补及质量工作检查的依据。 1 焊补前的准备 焊接修补前必须用角磨机或电弧气刨将铸钢件缺陷内部、外部清理干净,不允许有油污、污垢、铁锈(氧化皮)粘砂等影响焊接修补质量的脏物。 开出坡口,使铸件内部未氧化的金属露出,否则将会使电弧熄灭而无法焊补或重出现裂缝、气孔和未焊透的缺陷。 铸件缺陷坡口的确定 对有可能延伸的裂纹应在裂纹两端钻截断孔,一般距离裂纹20mm,孔深超过裂纹深2-3mm,然后再铲坡口,截断孔作为坡口的两端包括在焊补之内。 2 焊补工艺 补焊要求 (1)由于焊补铸件表面不进行机械加工,所有焊前铸件不需预热 (2)贯穿裂纹间隙很大或刚性很大的铸件,焊补时可采用单面逐步堆焊法。(3)在焊补过程中为减少焊接应力可进行敲击焊缝(除第一层和最后一层)。(4)对于不预热的铸件或采用多层焊时,为减少焊补过热尽量用小直径焊条和小电流,间断焊补,使焊缝稍冷后,敲掉溶渣再继续焊补。
(5)焊接修补后焊肉及熔合区不得有夹渣、气孔、裂纹、未焊透、咬边、缺肉等缺陷。 (6)对于焊接修补的非加工面都必须进行整形,消除焊补痕迹。整形可用砂轮打磨方法完成。 焊补工艺参数 焊材选用 焊条和焊丝类型的选择必须考虑工件的物理、机械性能和化学成份,一般先用成份与焊件金属相同或相近的焊条,参见表1 焊条使用要求 (1)焊条在使用前应根据焊条药皮特性进行烘干处理,切忌急冷、急热、具体要求参见表2。烘干后焊条应及时装入保温筒随取随用。 (2)焊条严重受潮,黏在一起或药皮脱落,必须检验合格后方可使用。 (3)使用的焊条冷至室温4小时以后,必须按工艺重新烘干。 表2 焊条直径的选用见表3 表3 各种直径焊条对应电流见下表