专业模具英语
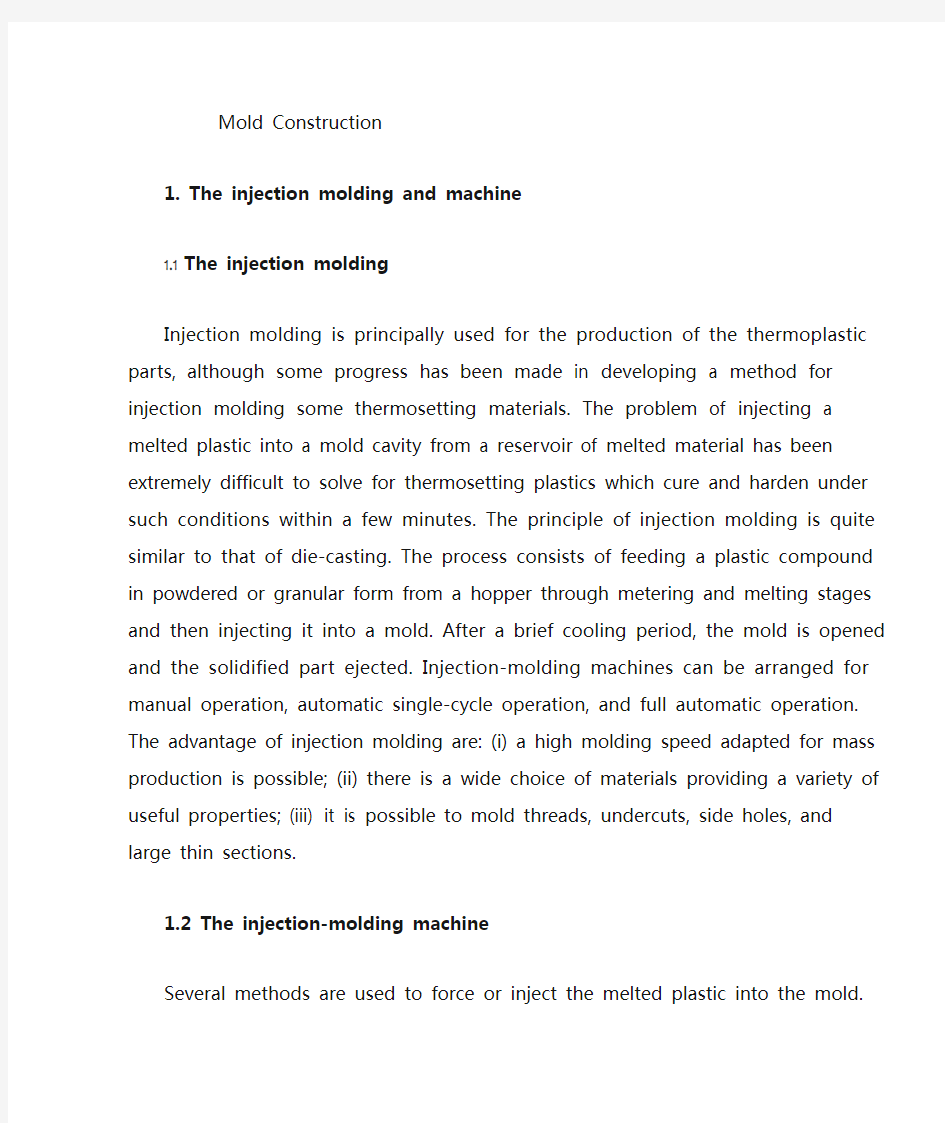

Mold Construction
1. The injection molding and machine
1.1The injection molding
Injection molding is principally used for the production of the thermoplastic parts, although some progress has been made in developing a method for injection molding some thermosetting materials. The problem of injecting a melted plastic into a mold cavity from a reservoir of melted material has been extremely difficult to solve for thermosetting plastics which cure and harden under such conditions within a few minutes. The principle of injection molding is quite similar to that of die-casting. The process consists of feeding a plastic compound in powdered or granular form from a hopper through metering and melting stages and then injecting it into a mold. After a brief cooling period, the mold is opened and the solidified part ejected. Injection-molding machines can be arranged for manual operation, automatic single-cycle operation, and full automatic operation. The advantage of injection molding are: (i) a high molding speed adapted for mass production is possible; (ii) there is a wide choice of materials providing a variety of useful properties; (iii) it is possible to mold threads, undercuts, side holes, and large thin sections.
1.2 The injection-molding machine
Several methods are used to force or inject the melted plastic into the mold. The most commonly used system in the larger machines is the in-line reciprocating screw . The screw acts as a combination injection and plasticizing unit. As the plastic is fed to the rotating screw, it passes through three zones: feed, compression, and metering. After the feed zone, the screw-flight depth is gradually reduced, forcing the plastic to compress. The work is converted to heat by shearing the plastic, making it a semifluid mass. In the metering zone, additional heat is applied by conduction from the barrel surface. As the chamber in front of the screw becomes filled, it forces the screw back, tripping a limit switch that activates a hydraulic cylinder that forces the screw forward and injects the fluid plastic into the closed mold. An antiflowback valve prevents plastic under pressure from escaping back into the screw flights.
The clamping force that a machine is capable of exerting is part of
the size designation .The injection-molding machine ,the
reciprocating-screw injection system and is measured in tons. A
rule-of-thumb can be used to determine the tonnage required for a particular job. It is based on two tons of clamp force per square inch of projected area. If the flow pattern is difficult and the parts are thin, this may have to go to three or four tons.
Many reciprocating-screw machines are capable of handing
thermosetting plastic materials. Previously these materials were handled by compression or transfer molding. Thermosetting materials cure or polymerize in the mold and are ejected hot in the range of 375~410℃. Thermoplastic parts must be allowed to cool in the mold in order to remove them without distortion. Thus thermosetting cycles can be faster. Of course the mold must be heated rather than chilled, as with thermoplastics.
Machines are available for molding sandwich parts. One cylinder and plunger injects measured amount of skin material into the die, and then a second cylinder squirts the filler inside the mass. Finally, a final spurt from the first cylinder clears the core material from the sprue. The aim is to produce composites with optimum properties. Either case or core may be foamed.
2.Feed system
It is necessary to provide a flow-way in the injection mould to connect the nozzle (of the injection machine) to each impression. This flow-way is termed the feed system. Normally the feed system comprises a sprue, runner and gate. These terms apply equally to the flow-way itself, and to the molded material which is removed from the flow-way itself in the process of extracting the molding.
A typical feed system for a four-impression, two plate-type mould. It is seen that the material passes through the sprue, main runner, branch runners and gate before entering the impression. As the temperature of
molten plastic is lowered while going through the sprue and runner, the viscosity will rise; therefore, the viscosity is lowered by shear heat generated when going through the gate to fill the cavity. It is desirable to keep the distance that the material has to travel down to a minimum to reduce pressure and heat losses. It is for this reason that careful consideration must be given to the impression layout and gate’s design.
Sprue
A sprue is a channel through which to transfer molten plastic injected from the nozzle of the injector into the mold. It is a part of sprue bush, which is a separate part from the mold.
Runner
A runner is a channel that guides molten plastic into the cavity of a mold.
Gate
A gate is an entrance through which molten plastic enters the cavity. The gate has the following functions: restricts the flow and the direction of molten plastic; simplifies cutting of a runner and moldings to simplify finishing of parts; quickly cools and solidifies to avoid backflow after molten plastic has filled up in the cavity.
Cold slug well
The purpose of the cold slug well, shown opposite the sprue, is theoretically to receive the material that has chilled at the front of the
nozzle during the cooling and ejection phase. Perhaps of greater importance is the fact that it provides positive means whereby the sprue can be pulled from the sprue bush for ejection purposes.
The sprue, the runner, and the gate will be discarded after a part is complete. However, the runner and the gate are important items that affect the quality or the cost of parts.
3 .RUNNER
The runner is a channel machined into the mould plate to connect the sprue with the entrance to the impression. The wall of the runner channel must be smooth to prevent any restriction to flow. Also, as the runner has to be removed with the molding, there must be no machine marks left which would tend to retain the runner in the mould plate.
There are some other considerations for the designer to bear in mind: (i) the shape of the cross section of the runner, (ii) the size of the runner ;(iii) the runner layout.
Runner cross-section shape
The cross-sectional shape of the runner used in a mould is usually one of four forms: fully round, trapezoidal, modified trapezoidal and hexagonal.
The criterion of efficient runner design is that the runner should provide a maximum cross-section area from the standpoint of pressure
transfer and a minimum contact on the periphery from the standpoint of heat transfer . The ratio of cross-sectional area to periphery will, therefore, give a direct indication of the efficiency of the runner design; the higher the value the greater the efficiency.
Runner layout
The layout of the runner system will depend upon the following factors: (i) the runner of impression, (ii) the shape of the components, (iii) the type of mould, (iv) the type of gate.
When designing a runner system there are two main considerations. The runner length should always be kept to a minimum to reduce pressure losses, and the runner system should be balanced.
Runner balancing means that the distance the plastic material from the sprue to the gate should be the same for each molding. This system ensures that all the impressions will fill uniformly and without interruption providing the gate lands and the gate areas are identical.
Runner layout
It is not always practicable, however, to have a balanced runner system and this particularly applies to moulds which incorporate a large number of differently shaped impressions. In these cases(as shows examples )balanced filling of the impression can be achieved by varying the gate dimensions that is by balanced gating.
4 .GATES
The gate is a channel or orifice connecting the runner with the impression. It has a small cross-sectional area when compared with the rest of the feed system. This small cross-sectional area is necessary so that: i) The gate freezes soon after the impression is filled so that the injection plunger can be withdrawn without the probability of void being created in the molding by suck-back. ii) It allows for simple degating and in some mould this degating can be automatic.ⅲ) After degating only a small witness mark remains.ⅳ) Better control of the filling of multi-impressions can be achieved.ⅴ) Packing the impression with material in excess of that required to compensate for shrinkage is minimized.
The size of the gate can be considered in terms of the gate
cross-sectional area and the gate length, the latter being known as gate land. The optimum size for a gate will depend on a number of factors including (i) the flow characteristics of the material to be molded (ii) the wall section of the molding, (iii) the volume of material to be injected into the
impression, (iv) the temperature of the melt (v) the temperature of the mould.
No theoretical size exists for the ideal gate. The gate size chosen in practice for a particular component is normally based on past experience. However, the reader may not have this experience upon which to base a decision and, therefore, a guide to the dimensions for each gate type is given. To the general case of a molding with a wall section between 0.75mm and 4 mm.
Figure 4-1 Types of gate
Type of gate
To obtain the optimum filling conditions the type of gate must be
carefully chosen. On most occasions, however, the choice will be obvious as only one type of gate will meet the particular requirements for the molding on hand. The types of gate (see Figure 4-1) commonly used are: sprue
gate(f), edge gate(n), overlap gate(a), fan gate(b), diaphragm gate(g), ring gate(h), film gate(c), pin gate(d), submarine gate(m) and tab gate(e).
5. Parting surface
The parting surfaces of a mould are those portion of both mould plates, adjacent to the impressions, which butt together to form a seal and prevent the loss of plastic material from the impression. The parting surface is classified flat and non-flat.
FLAT PARTING SURFACE
The mature of the parting surface depends entirely on the shape of the component. The position of the parting surface will therefore be at the top of the molding, the parting surface itself being perfectly flat. For appearance this is the ideal arrangement as the parting line is not noticeable unless flash develops.
A further consideration is that the parting surface must be chosen so that the molding can be removed from the mould. The suitable choice for the parting line is on the centre of the double-bevel which allows for half of the required form to be die-sunk into each of the two mould halves.
The parting line must occur along the line round the position of
maximum dimension when viewed in the draw direction. Then is this line lies on a plane the parting surface will be flat.
NON-FLAT PARTING SURFACE
Many moldings are required which have a parting line which lies on a non-planar or curved surface. In these cases the mould’s parting surface must either be stepped, profiled or angled.
6. MOULD CAVITIES AND CORES
The cavity and core give the molding its external and internal shapes respectively, the impression imparting the whole of the form to the molding. We then proceeded to indicate alternative ways by which the cavity and core could be incorporated into the mould and found that these alternatives fell under two main headings, namely the integer method and the insert method. Another method by which the cavity can be incorporated is by means of split inserts or splits.
6.1 Integer cavity and core plates
When the cavity or core is machined from a large plate or block of steel, or is cast in one piece, it is termed an integer cavity plate or integer core plate. This design is preferred for single-impression moulds because of the strength, smaller size and lower cost characteristics. For
multi-impression moulds there are other factors such as alignment which must be taken into consideration. Of the many manufacturing processes available for preparing moulds only two are normally used in this case. These
are a direct machining operation on a rough steel forging or blank using the conventional machine tools, or the ‘precision’investment casting technique in which a master pattern is made of the cavity and core. The pattern is then used to prepare a casting of the cavity or core by a special process. A 4.25% nickel-chrome-molybdenum steel (BS 970-835 M30) is normally specified for integer mould plates which are to be made by the direct machining method. The precision investment casting method usually utilizes
a high-chrome steel.
6.2 Inserts for cavity and core
For moulds containing intricate impressions, and for multi-impression moulds, it is not satisfactory to attempt to machine the cavity and core plates from single blocks of steel as with integer moulds. The machining sequences and operation would be altogether too complicated and costly. The insert-bolster assembly method is therefore used instead. The method consists in machining the impression out of small blocks of steel. These small blocks of steel are known, after machining, as inserts, and the one which forms the male part is termed the core insert and, conversely, the one which forms the female part the cavity insert. These are then inserted and securely fitted into holes in a substantial block or plate of steel called a bolster.
In the majority of cases the insert-bolster method of construction is used, the ease of manufacture, mould alignment, and resulting lower mould
costs being the overriding factors affecting the choice.
7. Splits
The mould designer is frequently confronted with a component design that incorporates a recess or projection which prevents the simple removal of the molding from the mould. The mould design for this type of component is inevitably more complex than for the in line of draw component, as it necessitates the removal of that part of the impression which forms the undercut prior to ejection.
The splits can be incorporated in the mould design in several ways. The designer considers more complex systems where the splits are retained on the mould plate and actuated automatically. There are two basic designs: sliding and angled-lift splits. In both designs there are moving parts and it is necessary to arrange for (i) guiding the splits in the desired direction, (ii) actuating the splits, (iii) securely locking the splits in position prior to the material being injection into the mould.
Sliding splits
In this design, the splits are mounted in guides on a flat mould plate and they are actuated in one plane by mechanical or hydraulic means. The various methods which can be used to actuate the splits in relation to the mould plate consist of finger cam, dog-leg cam, cam track, compression spring and hydraulic. The basic operation with cam actuation is as follows.
As the mould is opened, the cams attached to the fixed mould half cause the splits to slide across the moving mould plate.
Angled-lift splits
In this design the splits are mounted in a chase-bolster which forms part of the moving half of the mould. The splits are caused to move out with an angular motion, the outward component of which relieves the undercut portion of the molding. The splits are normally actuated by the ejector system. This shows the moving half of an angled-lift split mould for producing a spool. It will be noted from this illustration that the guiding of the angled-lift is not as critical as for guiding the sliding splits. The alignment of the splits, when closed, is accomplished by their being seated in the chase-bolster. The main requirement of the guiding system is that the split must be restrained to move smoothly in the required plane.
The various alternative systems with respect to particular actuating methods are: (i) angled guide dowel actuating system, (ii) cam track actuating system, (iii) spring actuation.
8. Ejection
A molding is formed in mould by injecting a plastic melt, under pressure, into an impression via a feed system. It must therefore be removed manually. Furthermore, all thermoplastic materials contract as they solidify, which means that the molding will shrink on to the core which
forms it. This shrinkage makes the molding difficult to remove.
Facilities are provided on the injection machine for automatic actuation of an ejector system, and this is situated behind the moving platen. Because of this, the mould’s ejector system will be most effectively operated if placed in the moving half of the mould, i.e. the half attached to the moving platen. We have stated previously that we need to eject the molding from the core and it therefore follows that the core, too, will most satisfactorily be located in the moving half.
The ejector system in a mould will be discussed under three headings, namely: (i) the ejector grid; (ii) the ejector plate assembly; (iii) the method of ejection.
Ejector grid
The ejector gridis that part of the mould which supports the mould plate and provides a space into which the ejector plate assembly can be
fitted and operated. The grid normally consists of a back plate on to which is mounted a number of conveniently shaped‘support blocks ’.
Ejector plate assembly
The ejector plate assembly is that part of the mould to which the ejector element is attached. The assembly is contained in a pocket, formed by the ejector grid, directly behind the mould plate .The assembly consists of an ejector plate, a retaining plate and an ejector rod. One end of this latter member is threaded and it is screwed into the ejector plate. In this particular
design the ejector rod functions not only as an actuating member but also as a method of guiding the assembly. Note that the parallel portion of the ejector rod passes through an ejector rod bush fitted in the back plate of the mould.
Ejector techniques
When a molding cools, it contracts by an amount depending on the material being processed. For a molding which has no internal form, for example a solid rectangular block, the molding will shrink away from the cavity walls, thereby permitting a simple ejection technique to be adopted. However, when the molding has internal form, the molding, as it cools, will shrink onto the core and some positive type of ejection is necessary.
The designer has several ejection techniques from which to chose ,but, in general, the choice will be restricted depending upon the shape of the molding. The basic ejection techniques are as follows: (i) pin ejection; (ii) sleeve ejection; (iii) stripper plate ejection ;(iv) air ejection.
模具专业英文术语大全
模具英语专业术语 模具述语 一、入水:gate 进入位: gate location 水口形式:gate type 大水口:edge gate 细水口: pin-point gate 水口大小:gate size 转水口: switching runner/gate 唧嘴口径: sprue diameter 二、流道: runner 热流道: hot runner,hot manifold 热嘴冷流道: hot sprue/cold runner 唧嘴直流: direct sprue gate 圆形流道:round(full/half runner 流道电脑分析:mold flow analysis 流道平衡:runner balance 热嘴: hot sprue 热流道板:hot manifold 发热管:cartridge heater 探针: thermocouples 插头: connector plug 插座: connector socket 密封/封料: seal 三、运水:water line 喉塞:line lpug 喉管:tube 塑胶管:plastic tube 快速接头:jiffy quick connector plug/socker 四、模具零件: mold components 三板模:3-plate mold 二板模:2-plate mold 边钉/导边:leader pin/guide pin 边司/导套:bushing/guide bushing 中托司:shoulder guide bushing 中托边L:guide pin 顶针板:ejector retainner plate 托板: support plate 螺丝: screw 管钉:dowel pin 开模槽:ply bar scot 内模管位:core/cavity inter-lock 顶针: ejector pin 司筒:ejector sleeve 司筒针:ejector pin 推板:stripper plate 缩呵:movable core,return core core puller 扣机(尼龙拉勾):nylon latch lock 斜顶:lifter 模胚(架): mold base 上内模:cavity insert 下内模:core insert 行位(滑块): slide 镶件:insert 压座/斜鸡:wedge 耐磨板/油板:wedge wear plate 压条:plate 撑头: support pillar 唧嘴: sprue bushing 挡板:stop plate 定位圈:locating ring 锁扣:latch 扣鸡:parting lock set 推杆:push bar 栓打螺丝:S.H.S.B 顶板:eracuretun 活动臂:lever arm 分流锥:spure sperader 水口司:bush 垃圾钉:stop pin 隔片:buffle 弹弓柱:spring rod 弹弓:die spring 中托司:ejector guide bush 中托边:ejector guide pin 镶针:pin 销子:dowel pin 波子弹弓:ball catch 喉塞: pipe plug
外资企业模具英文常用对话
1. XXX!你现在有空吗,我可以问你一些问题吗? Could I ask you some questions if you are free?/ Are you free now? May I ask you some questions (a question)? 2.请问此产品的面是否为外观面?表面做什么处理?是晒纹/抛光? Can you tell me whether the surface of this part is a visible/esthetic one? What will we do for its surface? Texture or Polishing? 3.请问产品这个面可否加顶针或顶块?产品允许加扁顶针吗? Does this part need an ejector pin or an ejector bar? Can we add an ejector blade? 4.这个产品的柱位我们打算做司筒。(或镶针)可以吗? Can we add ejector sleeves or ejector pins in the boss of this part? 5.产品的这个位置不能出模,我们打算做行位,在此面上会有分模线,你接受吗? There's an undercut at this position and it needs a slider. It will also have a parting line on this side, is that OK? 6.产品里面的这个位置我们打算做斜顶或内行位,有问题吗? We will make the lifter and (inner) slider in this position, will that be a problem? 7.你提供的2D产品图与3D产品图不一致,请问以哪一个图面为准? The 2D and 3D drawing you provided is not the same, can you tell me which one is correct? 8.你提供的3D产品图有的地方没有出模角,有的地方胶位太厚,有的地方胶位太溥,这些产品问题我们可以自己修改吗?修改后会给交给你确认。 There is no draft angle in the 3D drawing, some materials are too thick, and some place are too thin. Can we modify this part by ourselves? We will send the drawing to you for you to check after we modify it.
模具专业英语词汇大全
模具专业英语词汇 A abrasion n. 磨损 abrasion resistance n. 耐磨损性 abrasive n. 磨料 accelerator n. 促进剂 accuracy n. 准确性 accurate die casting 精密压铸 air trap 积风 acrylic n. 丙烯酸 /压克力 ì active plate 活动板 additive n. 添加剂 adhere v. 黏附 adhesion n. 黏合 adhesive n. 胶粘剂 air-cushion eject-rod 气垫顶杆 air cushion plate 气垫板 air entrapment n. 困气 anneal v. 退火 assemble v. 总成 B back pressure 背压 bismuth mold 铋铸模 baffle plate 挡块 barrel n. 机筒 /料筒 / bending block 折刀 bottom block 下垫脚 bottom plate 下托板(底板) bushing bolck 衬套 barrel temperature 料筒温度 blush 发 blank through dies 漏件式落料模 burnishi blow molding n. 吹塑成型 blow molding machine n. 吹塑机 brittle adj. 脆性 bubble n. 气泡 burr 毛刺 button d by-product n. 副产品 C calendering n. 压延 carbon steel n. 碳素钢 casting n. 铸造 catalyst n. 催化剂 cavity n. 型腔 chemical resistance n. 耐化学腐蚀性 chip v. 削 /凿
模具专业英语——注塑模
Injection Mold Technical Terms 特克内克腾目思 (一)模具专业基本用词 Professional Terms Intensification Factor 增强比 Scientific molding 科学注塑英腾次分克深发克偷 塞音特菲克计数器counter康特 Specific Injection Pressure (Psi)特殊注塑压力 思呗色服克 1.塑料—plastic, resin瑞申油管:Oil pipe 尼龙--------nylon 2.样件—sample 调节板-------adjust plate 3.钢料—steel A板--------a plate 4.注塑机—injection machine, press 定位圈----locating ring 喽客厅令 5.产品—part, product, moulding 斜导柱-----angular pin 安给拉PIN 6.模具—mold, mould, tool B板--------- b plate A 简易模(样板模)—prototype mold B 量产用模具—production mold 7.三维造型(数模)—3D model, 滚珠导套-------ball ejector bush 8.二维产品图—2D part drawing 拽应扁顶针--------blade ejector pin 布累得 9.设计—design 低赛应下模板--------bottom clamping plate 抱腾 10.制造—manufacture, 上模型腔------cavity main insert 11.检验—check, 上模镶件------cavity sub insert 12.测量—measure, 妹试司筒针--------center pin 深特 13.修改—change, modify 下模型芯------core main insert 14.工程更改—engineer change 下模镶针------core pin 15.质量—quality 快乐体下模镶件------core sub insert 16.数量—quantity 宽体踢延迟顶针-------delay ejector pin 17.基准—datum, reference 拉杆限位钉--------distance bolt (二)如何解析2D 产品图?How to read 2D part drawing? 一.产品几何Geometry 顶距限位柱--------distance spacer 1.点—point 销钉-------dowel pin 2.线(边)—line, edge 顶块--------ejector bar 3.面face 顶板导套-----ejector leader pin A 侧面—side塞得 B表面—surface射飞思 C 外观面—appearance surface安皮尔思射飞思4.壁厚—wall thickness 我射克来思顶板导柱----ejector leader pin李德拼 5.加强筋(骨位)—rib 瑞布顶针-------ejector pin 6.孔—hole后顶针地板------ejector plate 7.细长的槽—slot 顶针面板-----ejector retain plate 瑞腾 8.柱位—boss 抱死顶棍------ejector rod
模具专业英文术语大全
实用文案 模具英语专业术语 模具述语开模槽:ply bar scot 内模管位:一、入水:gate core/cavity inter-lock 顶针:ejector pin 进入位:gate location 司筒:ejector sleeve 水口形式:gate type 司筒针:edge gate ejector pin 大水口:推板:细水口:stripper plate pin-point gate 缩呵:gate size movable core,return core core 水口大小:puller switching runner/gate 转水口:扣机(尼龙拉勾):nylon latch lock sprue diameter 唧嘴口径:斜顶:lifter : runner 二、流道模胚(架):mold base hot runner,hot manifold 热流道:上内模:cavity insert : hot sprue/cold runner 热嘴冷流道下内模:core insert : direct sprue gate 唧嘴直流行位(滑块):slide round(full/half runner 圆形流道:镶件:insert mold flow analysis 流道电脑分析:压座/斜鸡:wedge :runner balance 流道平衡耐磨板/油板:wedge wear plate hot sprue 热嘴:压条:plate hot manifold 热流道板:撑头: support pillar cartridge heater 发热管:唧嘴:sprue bushing : thermocouples 探针挡板:stop plate connector plug 插头:定位圈:locating ring connector socket 插座:锁扣:latch seal 封料:/密封扣鸡:parting lock set water line 三、运水:推杆:push bar line lpug 喉塞:栓打螺丝:S.H.S.B tube 喉管:顶板:eracuretun plastic tube 塑胶管:活动臂:lever arm jiffy quick connector 快速接头:分流锥:spure sperader plug/socker 水口司mold components 四、模具零件::bush 垃圾钉:三板模:3-plate mold stop pin 隔片:buffle 二板模:2-plate mold 弹弓柱:导边:/leader pin/guide pin spring rod 边钉弹弓:die spring 导套:边司/bushing/guide bushing 中托司:ejector guide bush 中托司:shoulder guide bushing 中托边:ejector guide pin guide pin :L中托边镶针:ejector retainner plate 顶针板:pin 销子:托板:support plate dowel pin 波子弹弓:ball catch screw 螺丝:: pipe plug dowel pin 管钉:喉塞文案大全. 实用文案 锁模块:lock plate Mold repair 模具维修 angle from pin 斜顶:Molds 模具
模具英语专业术语
模具英语专业术语上内模:cavity insert 模具述语下内模:core insert 一、入水:gate行位(滑块):slide 进入位:gate location 镶件:insert 水口形式:gate type 压座/斜鸡:wedge 大水口:edge gate 耐磨板/油板:wedge wear plate 细水口:pin-point gate 压条:plate 水口大小:gate size 撑头: support pillar 转水口:switching runner/gate 唧嘴:sprue bushing 唧嘴口径:sprue diameter挡板:stop plate 二、流道: runner 定位圈:locating ring 热流道:hot runner,hot manifold锁扣:latch 热嘴冷流道: hot sprue/cold runner 扣鸡:parting lock set 唧嘴直流: direct sprue gate推杆:push bar 圆形流道:round(full/half runner 栓打螺丝:S.H.S.B 流道电脑分析:mold flow analysis顶板:eracuretun 流道平衡:runner balance 活动臂:lever arm 热嘴:hot sprue 分流锥:spure sperader 热流道板:hot manifold水口司:bush 发热管:cartridge heater 垃圾钉:stop pin 探针: thermocouples 隔片:buffle 插头:connector plug 弹弓柱:spring rod 插座:connector socket 弹弓:die spring 密封/封料:seal中托司:ejector guide bush 三、运水:water line中托边:ejector guide pin 喉塞:line lpug 镶针:pin 喉管:tube 销子:dowel pin 塑胶管:plastic tube 波子弹弓:ball catch 快速接头:jiffy quick connector plug/socker 喉塞: pipe plug 四、模具零件:mold components 锁模块:lock plate 三板模:3-plate mold斜顶:angle from pin 二板模:2-plate mold斜顶杆:angle ejector rod 边钉/导边:leader pin/guide pin 尼龙拉勾:parting locks 边司/导套:bushing/guide bushing 活动臂:lever arm 中托司:shoulder guide bushing 复位键、提前回杆:early return bar 中托边L:guide pin 气阀:valves 顶针板:ejector retainner plate 斜导边:angle pin 托板:support plate 术语:terms 螺丝:screw 承压平面平衡:parting surface support balance 管钉:dowel pin 模排气:parting line venting 开模槽:ply bar scot 回针碰料位:return pin and cavity interference 内模管位:core/cavity inter-lock模总高超出啤机规格:mold base shut hight 顶针:ejector pin 顶针碰运水:water line interferes withejector pin 司筒:ejector sleeve 料位出上/下模:part from cavith (core) side 司筒针:ejector pin 模胚原身出料位:cavity direct cut on A-plate,core direct cut 推板:stripper plate on B-plate. 缩呵:movable core,return core core puller 不准用镶件:Do not use (core/cavity) insert 扣机(尼龙拉勾):nylon latch lock用铍铜做镶件:use beryllium copper insert 斜顶:lifter 初步(正式)模图设计:preliinary (final) mold design 模胚(架):mold base 反呵:reverse core 弹弓压缩量:spring compressed length 稳定性好:good stability,stable 强度不够:insufficient rigidity 均匀冷却:even cooling 扣模:sticking 热膨胀:thero expansion 公差:tolorance 铜公(电极):copper electrode Mold & die components 模具单元 Mold changing systems 换模系统 Mold core 模芯 Mold heaters/chillers模具加热器 /冷却器 Mold polishing/texturing模具打磨/磨纹Mold repair模具维修
模具专业英文术语大全
模具专业英文术语大全
模具英语专业术语 模具述语 一、入水:gate 进入位:gate location 水口形式:gate type 大水口:edge gate 细水口:pin-point gate 水口大小:gate size 转水口:switching runner/gate 唧嘴口径:sprue diameter 二、流道: runner 热流道:hot runner,hot manifold 热嘴冷流道: hot sprue/cold runner 唧嘴直流: direct sprue gate 圆形流道:round(full/half runner 流道电脑分析:mold flow analysis 流道平衡:runner balance 热嘴:hot sprue 热流道板:hot manifold 发热管:cartridge heater 探针: thermocouples 插头:connector plug 插座:connector socket 密封/封料:seal 三、运水:water line 喉塞:line lpug 喉管:tube 塑胶管:plastic tube 快速接头:jiffy quick connector plug/socker 四、模具零件:mold components 三板模:3-plate mold 二板模:2-plate mold 边钉/导边:leader pin/guide pin 边司/导套:bushing/guide bushing 中托司:shoulder guide bushing 中托边L:guide pin 顶针板:ejector retainner plate 托板:support plate 螺丝:screw 管钉:dowel pin 开模槽:ply bar scot 内模管位:core/cavity inter-lock 顶针:ejector pin 司筒:ejector sleeve 司筒针:ejector pin 推板:stripper plate 缩呵:movable core,return core core puller 扣机(尼龙拉勾):nylon latch lock 斜顶:lifter 模胚(架):mold base 上内模:cavity insert 下内模:core insert 行位(滑块):slide 镶件:insert 压座/斜鸡:wedge 耐磨板/油板:wedge wear plate 压条:plate 撑头: support pillar 唧嘴:sprue bushing 挡板:stop plate 定位圈:locating ring 锁扣:latch 扣鸡:parting lock set 推杆:push bar 栓打螺丝:S.H.S.B 顶板:eracuretun 活动臂:lever arm 分流锥:spure sperader 水口司:bush 垃圾钉:stop pin 隔片:buffle 弹弓柱:spring rod 弹弓:die spring 中托司:ejector guide bush 中托边:ejector guide pin 镶针:pin 销子:dowel pin 波子弹弓:ball catch 喉塞: pipe plug 锁模块:lock plate 斜顶:angle from pin
模具专业英语45315461
模具工程常用词汇 die 模具 figure file, chart file图档 cutting die, blanking die冲裁模 progressive die, follow (-on)die 连续模 compound die复合模 punched hole冲孔 panel board镶块 to cutedges=side cut=side scrap切边 to bending折弯 to pull, to stretch拉伸 Line streching, line pulling线拉伸 engraving, to engrave刻印 upsiding down edges翻边 to stake铆合 designing, to design设计 design modification设计变化 die block模块 folded block折弯块 sliding block滑块 location pin定位销 lifting pin顶料销 die plate, front board模板 padding block垫块 stepping bar垫条 upper die base上模座 lower die base下模座 upper supporting blank上承板 upper padding plate blank上垫板 spare dies模具备品 spring 弹簧 bolt螺栓 document folder文件夹 file folder资料夹 to put file in order整理资料 spare tools location手工备品仓 first count初盘人 first check初盘复棹人 second count 复盘人 second check复盘复核人 equipment设备 waste materials废料 work in progress product在制品 casing = containerazation装箱 quantity of physical invetory second count 复盘点数量quantity of customs count 会计师盘,点数量 the first page第一联 filed by accounting department for reference会计部存查 end-user/using unit(department)使用单位summary of year-end physical inventory bills 年终盘点截止单据汇总表 bill name单据名称 This sheet and physical inventory list will be sent to accounting department together (Those of NHK will be sent to financial department) 本表请与盘点清册一起送会计部-(NHK厂区送财会部) Application status records of year-end physical inventory List and physical inventory card 年终盘点卡与清册使用- 状况明细表 blank and waste sheet NO. 空白与作废单号 plate电镀 mold成型 material for engineering mold testing工程试模材料 not included in physical inventory不列入盘点sample样品 incoming material to be inspected进货待验description品名 steel/rolled steel钢材 material statistics sheet 物料统计明细表 meeting minutes会议记录 meeting type 会别 distribution department分发单位 location地点 chairman主席 present members出席人员 subject主题 conclusion结论 decision items决议事项 responsible department负责单位 pre-fixed finishing date预定完成日 approved by / checked by / prepared by核准/审核/承办 PCE assembly production schedule sheet PCE组装厂生产排配表 model机锺
模具专业英语词汇.doc
模具专业英语词汇 landed plunger mold 有肩柱塞式模具burnishing die 挤光模英语站landed positive mold 有肩全压式模具button die 镶入式圆形凹模 loading shoe mold 料套式模具center-gated mold 中心浇口式模具loose detail mold 活零件模具 chill mold 冷硬用铸模 loose mold 活动式模具 clod hobbing 冷挤压制模 louvering die 百叶窗冲切模composite dies 复合模具 manifold die 分歧管模具 counter punch 反凸模 modular mold 组合式模具 double stack mold 双层模具 multi-cavity mold 多模穴模具electroformed mold 电铸成形模multi-gate mold 复式浇口模具expander die 扩径模 offswt bending die 双折冷弯模具extrusion die 挤出模 palletizing die 叠层模 family mold 反套制品模具 plaster mold 石膏模 blank through dies 漏件式落料模porous mold 通气性模具 duplicated cavity plate 复板模positive mold 全压式模具 fantail die 扇尾形模具 pressure die 压紧模 fishtail die 鱼尾形模具 profile die 轮廓模 flash mold 溢料式模具 progressive die 顺序模 gypsum mold 石膏铸模 protable mold 手提式模具 hot-runner mold 热流道模具prototype mold 雏形试验模具 ingot mold 钢锭模 punching die 落料模
模具英语专业术语
模具(MOULD/MOLD,TOOL): CAVITY:前模 CORE:后模(定模) DIMENSION:寸法 GATE:浇口/水口/入水口 PIN GATE:点水口/点浇入水 SIDE GATE:边水口/侧浇入水/大水口APPERANCE SURFACE:体裁面WARPAGE DIRECTION:变形方向 DRAFT ANGEL:脱模斜度 PARTING LINE/P。L:分模线 EJECT PIN/E。P:注塑顶针 BLAST/TEXTURE:喷啥,蚀纹 MIRROR FINISH:镜面(抛光)处理POLISH:抛光 EMD:放电加工 WELD:熔接加工(烧焊) LATHE:车床 MILLING CUTTER:铣刀 MILLING MACHINE:铣床 WIRE CUT:线切割 CNC:主加工中心 POWER DRILL:电钻 DRILLING:钻孔 FRITING:烧结 ANNEALING:淬火 注塑术语(INJECTION) SCREW:螺杆 WELD LINE:熔接线 SINK MARK:缩水 DRAG MARK:脱花 BURR:批锋 FLOW MARK:流纹 SHADOW MARK/GLOSS DIFFERENCE:光影SHORT:缺胶 INJECTION CYCLE:成型周期
注塑英语 型厚大小 Thick size 锁模结构(机绞/直压) Mode locking structure(machine twists/straight pressure) 最大开模距离 The biggest die sinking is away from 动模板最大模具重量 Moves the template maximum mold weight 哥林柱间距 Elder brother forest column spacing 顶出形式(电动五点,油压五点,油压十三点) Goes against the form (electrically operated five spots, flowing tubing head pressure five spots, flowing tubing head pressure 13 spots) 顶出长度 Goes against the length 顶棍孔直径 Goes against the stick hole diameter 顶棍孔中心矩 Goes against the stick hole central moment 螺杆材质(合金) Screw rod material quality (alloy) 螺杆转速 Screw rod rotational speed 最大射出体积 Projects the volume most greatly 最大射出量 Projects the quantity most greatly 射出率 Ejection rate 每10mm射出量(理论) Each 10mm projects the quantity (theory) 射咀直径 Shoots ju the diameter 射咀R值 Shoots ju the R value 射咀空径 Shoots ju the spatial diameter 定位环直径 Locating ring diameter 溶胶能力 Sol ability 驱动方式(全自动/全液压)
模具专业英语
1.模具常用名称中英文: DATE CODE 日期印DATUM 基準 ALIGNMENT 垂直 BINDING 夾緊 CAVITY (CAV.) 模腔 COLOR 顏色 CORNER/OUTSIDE RADIUS 外轉角 DETAIL 詳圖 DRAFT (DFT.) 出模角度 DWG NO. 圖紙編號ENGRAVE 雕字 FILLET/INSIDE RADIUS(R)內轉角FINISH 光潔度 FLUSH 平凹 GATE 入水位 KISS-OFF 枕位碰穿LOGO 商嘜 MATERIAL (MAT’L) 膠料OPENING 穿孔 PART NO. (P/N) 產品編號RAISED 凸高REFERENCE (REF.) 參考REVISION (REV.) 修正SHRINKAGE FACTOR 縮水率SHUT OFF/ (S/O ) 擦位RECESSED 凹入TEXTURE 皮紋 TITLE/PART NAME 產品名稱TOLERANCE (TOL.) 公差TYPICAL (TYP.) 類型VENTING 疏氣/排氣UNDERCUT(U’CUT) 倒扣WALL THICKNESS 胶位厚度 2.模具专业英语 入水:gate 进入位:gate location 水口形式:gate type 大水口:edge gate 细水口: pin-point gate 水口大小:gate size 转水口:switching runner/gate 唧嘴口径: sprue diameter 3.流道: runner 热流道:hot runner,hot manifold 热嘴冷流道: hot sprue/cold runner 唧嘴直流: direct sprue gate 圆形流道:round(full/half runner 流道电脑分析:mold flow analysis 流道平衡:runner balance 热嘴:hot sprue 热流道板:hot manifold 发热管:cartridge heater 探针: thermocouples 插头:connector plug 插座: connector socket 密封/封料: seal 4.运水:water line 喉塞:line plug 喉管:tube 塑胶管:plastic tube 快速接头:jiffy quick connector plug/socket 5.模具零件:mold components 三板模:3-plate mold 二板模:2-plate mold 边钉/导边:leader pin/guide pin 边司/导套:bushing/guide bushing 中托司:shoulder guide bushing 中托边L:guide pin 顶针板:ejector retainner plate 托板:support plate 螺丝: screw 管钉:dowel pin 开模槽:ply bar scot
模具专业英文术语大全
模具英语专业术语 模具述语顶针:ejector pin 司筒:一、入水:gate ejector sleeve 司筒针:ejector pin 进入位:gate location 推板:stripper plate 水口形式:gate type 缩呵:edge gate movable core,return core core 大水口:puller pin-point gate 细水口:扣机(尼龙拉勾):nylon latch lock gate size 水口大小:斜顶:lifter switching runner/gate 转水口:模胚(架):mold base sprue diameter 唧嘴口径:上内模:cavity insert : runner 二、流道下内模:core insert hot runner,hot manifold 热流道:行位(滑块):slide : hot sprue/cold runner 热嘴冷流道镶件:insert : direct sprue gate 唧嘴直流压座/斜鸡:wedge round(full/half runner 圆形流道:耐磨板/油板:wedge wear plate mold flow analysis 流道电脑分析:压条:plate :runner balance 流道平衡撑头: support pillar hot sprue 热嘴:唧嘴:sprue bushing hot manifold 热流道板:挡板:stop plate cartridge heater 发热管:定位圈:locating ring : thermocouples 探针锁扣:latch connector plug 插头:扣鸡:parting lock set connector socket 插座:推杆:push bar seal 密封封料:/栓打螺丝:S.H.S.B water line 三、运水:顶板:eracuretun line lpug 喉塞:活动臂:lever arm tube 喉管:分流锥:spure sperader plastic tube 塑胶管:水口司:bush jiffy quick connector 快速接头:垃圾钉:stop pin plug/socker 隔片:四、模具零件:mold components buffle 弹弓柱:spring rod 三板模:3-plate mold 弹弓:die spring 二板模:2-plate mold 中托司:导边:/边钉leader pin/guide pin ejector guide bush 中托边:bushing/guide bushing ejector guide pin 导套:/边司镶针:pin shoulder guide bushing 中托司:销子:guide pin :中托边Ldowel pin 波子弹弓:顶针板:ejector retainner plate ball catch 喉塞托板:support plate : pipe plug 锁模块:lock plate screw 螺丝:斜顶:dowel pin 管钉:angle from pin 斜顶杆:开模槽:ply bar scot angle ejector rod parting locks 尼龙拉勾:core/cavity inter-lock 内模管位: 活动臂:lever arm Quick mold change systems 快速换模系统 三、模具early return bar 复位键、提前回杆:塑料模具气阀:valves mould of plastics 注塑模具斜导边:angle pin injection mould 冲压模具die 术语:terms
注塑模具行业专业英语对照表
内容来源网络,由“深圳机械展(11万㎡,1100多家展商,超10万观众)”收集整理! 更多cnc加工中心、车铣磨钻床、线切割、数控刀具工具、工业机器人、非标自动化、数字化无人工厂、精密测量、3D打印、激光切割、钣金冲压折弯、精密零件加工等展示,就在深圳机械展. 注塑、模具专业英语: 1.SurfaceAppearance外观 2.Glossiness/glossfinish光洁度、粗糙度 3.Mattfinish/mattsurface毛面 4.Glassfiberrichsurface/glassemergenceonthesurface玻纤外露、浮纤 5.Blooming/surfaceblooming表面析出 6.Whitepatchesonsurface表面白斑 7.Silvermarks/silverstreak银纹 8.Splaymark水纹、料花 9.Flowmark流纹 10.Brittle/brittleness脆、脆性 11.Bubbles/trappedgas气泡/困气 12.Void孔、气泡 13.Burnmarks烧伤 14.FRfailed阻燃不合格
15.FlameratingV-2阻燃等级V-2 16.Poordispersion分散不好 17.FR/PTFE…agglomeratesetc阻燃剂/PTFE…结块 18.Pelletporous颗粒料孔隙 19.Lowimpact/tensilestrengthetc低冲击强度/拉伸强度等 20.Highflow/fillercontentetc高流动性/过度填充 21.Longs/fines/doubles长粒/碎屑/连粒 22.Poorcut粒形不好 23.Bristle/voids表面有小气泡/孔 24.Glassbundles纤维结团 25.Productwasrejecteddueto产品不能接受因为… 26.Highmoisturelevel高水分、高湿度 27.Warpage/warped翘曲/变形 28.Shrinkage/shrink收缩/收缩率 29.Sinkmarks凹陷、缩水 30.Shortshot/shortmolding打不满、欠注 31.Distortion变形 32.Overdimension尺寸过大