倒装芯片研究

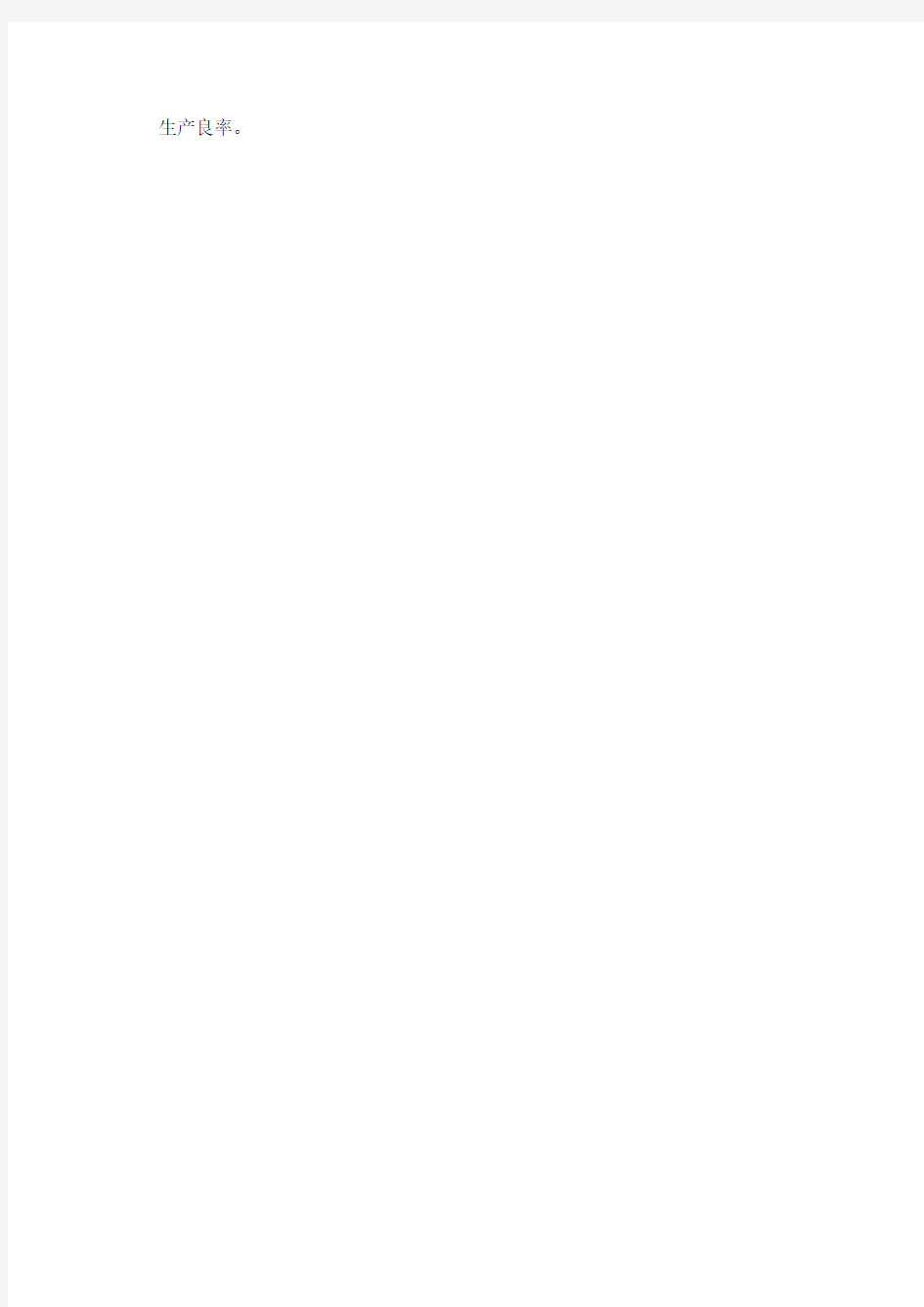
倒装芯片研究
1.为什么倒装?
(1)由于P型GaN传导性能不佳,为获得良好的电流扩展,需要通过蒸镀技术在P区表面形成一层ITO层。P区引线通过该ITO膜引出。为获得好的电流扩展,ITO层就不能太薄。为此,器件的发光效率就会受到很大影响,通常要同时兼顾电流扩展与出光效率二个因素。但无论在什麼情况下,ITO膜的存在,总会使透光性能变差。此外,引线焊点的存在也使器件的出光效率受到影响。采用GaN LED倒装芯片的结构可以从根本上消除上面的问题。而且p电极也会遮挡住部分光,限制了LED芯片的出光效率。
采用倒装结构的LED芯片,不但可以同时避开P电极上导电层吸收光和电极垫遮光的问题,还可以通过在p-GaN表面设置低欧姆接触的反光层来将往下的光线引导向上,这样可同时降低驱动电压及提高光强。另一方面,图形化蓝宝石衬底(PSS)技术和芯片表面粗糙化技术同样可以增大LED芯片的出光效率50%以上。
(2)散热更好。LED是靠电子在能带间跃迁产生光的,其光谱中不含有红外部分,所以LED的热量不能靠辐射散发。一旦LED的温度超过最高临界温度(跟据不同外延及工艺,芯片温度大概为150℃),往往会造成LED永久性失效。与传统正装结构以蓝宝石衬底作为散热通道相比,垂直及倒装焊芯片结构有着较佳的散热能力。垂直结构芯片直接采用铜合金作为衬底,有效地提高了芯片的散热能力。倒装焊(Flip-Chip)技术通过共晶焊将LED芯片倒装到具有更高导热率的硅衬底上(导热系数约120W/mK,传统正装芯片蓝宝石导热系数约20W/mK),芯片与衬底间的金凸点和硅衬底同时提高了LED芯片的散热能力,保障LED的热量能够快速从芯片中导出。
(3)防静电能力增强。抗静电释放(ESD)能力是影响LED芯片可靠性的另一因素。对于InGaN/AlGaN/GaN 双异质结,InGaN 活化簿层厚度仅几十纳米,对静电的承受能力有限,很容易被静电击穿,使器件失效。可以在LED芯片中加入齐纳保护电路防止静电。通常需要在封装过程中通过金线并联一颗齐纳芯片以提高ESD防护能力,不仅增加封装成本和工艺难度,可靠性也有较大的风险。通过在硅衬底内部集成齐纳保护电路的方法,可以大大提高LED芯片的抗静电释放能力(ESDHBM=4000~8000V),同时节约封装成本,简化封装工艺,并提高产品可靠性。
(4)在封装过程中通过焊线(Wire-bonding)的方式实现芯片与支架的电路连接,而焊接过程中瓷嘴对LED的芯片的冲击是导致LED漏电、虚焊等主要原因,传统正装和垂直结构LED,电极位于芯片的发光表面,因此焊线过程中瓷嘴的正面冲击极易造成发光区和电极金属层等的损伤,在LED芯片采取倒装结构中,电极位于硅基板上,焊线过程中不对芯片进行冲击,极大地提高封装可靠性和
生产良率。
倒装芯片(FC,Flip-Chip)装配技术
倒装芯片(FC,Flip-Chip)装配技术 时间:2010-05-27 23:04:25 来源:网络 倒装芯片焊接完成后,需要在器件底部和基板之间填充一种胶(一般为环氧树酯材料)。底部填充分为于“ 毛细流动原理” 的流动性和非流动性(No-follow )底部填充。 上述倒装芯片组装工艺是针对C4 器件(器件焊凸材料为SnPb 、SnAg 、SnCu 或SnAgCu )而言。另外一种工艺是利用各向异性导电胶(ACF )来装配倒装芯片。预先在基板上施加异性导电胶,贴片头用较高压力将器件贴装在基板上,同时对器件加热,使导电胶固化。该工艺要求贴片机具有非常高的精度,同时贴片头具有大压力及加热功能。对于非C4 器件(其焊凸材料为Au 或其它)的装配,趋向采用此工艺。这里,我们主要讨论C4 工艺,下表列出的是倒装芯片植球(Bumping )和在基板上连接的几种方式。 倒装倒装芯片几何尺寸可以用一个“ 小” 字来形容:焊球直径小(小到0.05mm ),焊球间距小(小到0.1mm ),外形尺寸小(1mm 2 )。要获得满意的装配良率,给贴装设备及其工艺带来了挑战,随着焊球直径的缩小,贴装精度要求越来越高,目前12μm 甚至10μm 的精度越来越常见。贴片设备照像机图形处理能力也十分关键,小的球径小的球间距需要更高像素的像机来处理。 随着时间推移,高性能芯片的尺寸不断增大,焊凸(Solder Bump)数量不断提高,基板变得越来越薄,为了提高产品可靠性底部填充成为必须。
对贴装压力控制的要求 考虑到倒装芯片基材是比较脆的硅,若在取料、助焊剂浸蘸过程中施以较大的压力容易将其压裂,同时细小的焊凸在此过程中也容易压变形,所以尽量使用比较低的贴装压力,一般要求在150g 左右。对于超薄形芯片,如0.3mm ,有时甚至要求贴装压力控制在35g 。 对贴装精度及稳定性的要求 对于球间距小到0.1mm 的器件,需要怎样的贴装精度才能达到较高的良率?基板的翘曲变形,阻焊膜窗口的尺寸和位置偏差,以及机器的精度等,都会影响到最终的贴装精度。关于基板设计和制造的情况对于贴装的影响,我们在此不作讨论,这芯片装配工艺对贴装设备的要求里我们只是来讨论机器的贴装精度。为了回答上面的问题,我们来
倒装芯片将成为封装技术的最新手段
倒装芯片将成为封装技术的最新手段 发布: 2009-6-10 | 作者: | 来源: 摘要:本文介绍了倒装芯片技术的特点并指出其工艺应用。关键词:倒装芯片;工艺应用 1 引言将芯片封装在一个封装体内或其表面上是封装界沿用了多年的一种传统的封装技术。如LPCC、TBGA、SOIC和DIPS等都采用这种封装方法。90年代以来,随着应用领域的大力驱动,封装技术不断取得日新月异的进展。单从封装技术新名词的涌现速度就足以说明封装技术的不断发展。近几年在各种期刊和会议录文章中出现的封装技术缩略词更是层出不穷,令人眼花缭乱,应接不暇。人们对铜引线框架的特性及其相关的工艺技术并不陌生。采用金线与其它合金(如铜等)的引线键合技术已接近完美的程度。最近几年,引线键合的节距(交错节距)不断减小,已由原来的100μm降至80μm、50μm、35μm,2002年已降至25μm。目前的封装多采用下列两种形式:1种是采用封帽的气密封装;另一种是采用模压化合物或液体密封剂的灌封方式,使最终的封装体能经受住可靠性测试。此外,与PCB的互连采用针式引线,其形状可分为直接鸥翼形成“J”形。三四年以前,制造产品的最终目的通常是最大限度地延长使用寿命。但如今的情况已大不相同了,消费类产品已达到极为丰富的程度。一旦产品出现故障,人们通常采用的方法是弃旧购新,因为购买新产品的价格甚至比维修还要划算。这也足以说明,大部分产品的价格已发生了许多变化。2 倒装芯片技术的发展30多年前,“倒装芯片”问世。当时为其冠名为“C4”,即“可控熔塌芯片互连”技术。该技术首先采用铜,然后在芯片与基板之间制作高铅焊球。铜或高铅焊球与基板之间的连接通过易熔焊料来实现。此后不久出现了适用于汽车市场的“封帽上的柔性材料(FOC)”;还有人采用Sn封帽,即蒸发扩展易熔面或E3工艺对C4工艺做了进一步的改进。C4工艺尽管实现起来比较昂贵(包括许可证费用与设备的费用等),但它还是为封装技术提供了许多性能与成本优势。与引线键合工艺不同的是,倒装芯片可以批量完成,因此还是比较划算。由于新型封装技术和工艺不断以惊人的速度涌现,因此完成具有数千个凸点的芯片设计目前已不存在大的技术障碍小封装技术工程师可以运用新型模拟软件轻易地完成各种电、热、机械与数学模拟。此外,以前一些世界知名公司专为内部使用而设计的专用工具目前已得到广泛应用。为此设计人员完全可以利用这些新工具和新工艺最大限度地提高设计性,最大限度地缩短面市的时间。无论人们对此抱何种态度,倒装芯片已经开始了一场工艺和封装技术革命,而且由于新材料和新工具的不断涌现使倒装芯片技术经过这么多年的发展以后仍能处于不断的变革之中。为了满足组装工艺和芯片设计不断变化的需求,基片技术领域正在开发新的基板技术,模拟和设计软件也不断更新升级。因此,如何平衡用最新技术设计产品的愿望与以何种适当款式投放产品之间的矛盾就成为一项必须面对的重大挑战。
倒装芯片(FC-Flip-Chip)装配技术
摘要:倒装芯片在产品成本,性能及满足高密度封装等方面体现出优势,它的应用也渐渐成为主流。由于倒装芯片的尺寸小,要保证高精度高产量高重复性,这给我们传统的设备及工艺带来了挑战。 器件的小型化高密度封装形式越来越多,如多模块封装(MCM )、系统封装(SiP )、倒装芯片(FC ,Flip-Chip )等应用得越来越多。这些技术的出现更加模糊了一级封装与二级装配之间的界线。毋庸置疑,随着小型化高密度封装的出现,对高速与高精度装配的要求变得更加关键,相关的组装设备和工 艺也更具先进性与高灵活性。 由于倒装芯片比BGA 或CSP 具有更小的外形尺寸、更小的球径和球间距、它对植球工艺、基板技术、材料的兼容性、制造工艺,以及检查设备和方法提出了前所未有的挑战。 倒装芯片的发展历史 倒装芯片的定义 什么器件被称为倒装芯片?一般来说,这类器件具备以下特点: 1. 基材是硅; 2. 电气面及焊凸在器件下表面; 3. 球间距一般为4-14mil 、球径为2.5-8mil 、外形尺寸为1 -27mm ; 4. 组装在基板上后需要做底部填充。 其实,倒装芯片之所以被称为“倒装”,是相对于传统的金属线键合连接方式(Wire Bonding)与植球后的工艺而言的。传统的通过金属线键合与基板连接的芯片电气面朝上(图1),而倒装芯片的电气面朝下(图2),相当于将前者翻转过来,故称其为“倒装芯片”。在圆片(Wafer)上芯片植完球后(图3),需要将其翻转,送入贴片机,便于贴装,也由于这一翻转过程,而被称为“倒装芯片”。 图1 图2
图3 倒装芯片的历史及其应用 倒装芯片在1964年开始出现,1969年由IBM发明了倒装芯片的C4工艺(Controlled Collap se Chip Connection,可控坍塌芯片联接)。过去只是比较少量的特殊应用,近几年倒装芯片已经成为高性能封装的互连方法,它的应用得到比较广泛快速的发展。目前倒装芯片主要应用在Wi- Fi、SiP、M CM、图像传感器、微处理器、硬盘驱动器、医用传感器,以及RFID等方面(图5)。 图4
芯片制造倒装焊工艺与设备解决方案
倒装键合(Flip Chip)工艺及设备解决方案 前言:倒装芯片在产品成本、性能及满足高密度封装等方面体现出优势,它的应用也渐渐成为主流。由于倒装芯片的尺寸小,要保证高精度高产量高重复性,这给我们传统的设备及工艺带来了挑战。 器件的小型化高密度封装形式越来越多,如多模块封装 ( MCM )、系统封装( SiP )、倒装芯片( FC=Flip-Chip )等应用得越来越多。这些技术的出现更加模糊了一级封装与二级装配之间的界线。毋庸置疑,随着小型化高密度封装的出现,对高速与高精度装配的要求变得更加关键,相关的组装设备和工艺也更具先进性与高灵活性。 由于倒装芯片比BGA或CSP具有更小的外形尺寸、更小的球径和球间距,它对植球工艺、基板技术、材料的兼容性、制造工艺,以及检查设备和方法提出了前所未有的挑战。 一.倒装芯片焊接的概念 倒装芯片焊接(Flip-chip Bonding)技术是一种新兴的微电子封装技术,它将工作面(有源区面)上制有凸点电极的芯片朝下,与基板布线层直接键合。一般来说,这类器件具备以下特点: 1. 基材是硅; 2. 电气面及焊凸在器件下表面; 3. 球间距一般为 4-14mil 、球径为 2.5-8mil 、外形尺寸为 1 -27mm ; 4. 组装在基板上后需要做底部填充。 其实,倒装芯片之所以被称为“倒装”,是相对于传统的金属线键合连接方式(Wire Bonding)与植球后的工艺而言的。传统的通过
金属线键合与基板连接的芯片电气面朝上(图1),而倒装芯片的电气面朝下(图2),相当于将前者翻转过来,故称其为“倒装芯片”。在圆片(Wafer)上芯片植完球后(图3),需要将其翻转,送入贴片机以便于贴装,也由于这一翻转过程而被称为“倒装芯片”。 图1 图2 图3 倒装芯片在1964年开始出现,1969年由IBM发明了倒装芯片的C4工艺(Controlled Collapse Chip Connection可控坍塌芯片联接)。过去只是比较少量的特殊应用,近几年倒装芯片已经成为高性能封装的互连方法,它的应用得到比较广泛快速的发展。目前倒装芯片主要应用在Wi-Fi、SiP、MCM、图像传感器、微处理器、硬盘驱动器、医用传感器,以及RFID等方面(图4)。
倒装芯片研究
倒装芯片研究 1.为什么倒装? (1)由于P型GaN传导性能不佳,为获得良好的电流扩展,需要通过蒸镀技术在P区表面形成一层ITO层。P区引线通过该ITO膜引出。为获得好的电流扩展,ITO层就不能太薄。为此,器件的发光效率就会受到很大影响,通常要同时兼顾电流扩展与出光效率二个因素。但无论在什麼情况下,ITO膜的存在,总会使透光性能变差。此外,引线焊点的存在也使器件的出光效率受到影响。采用GaN LED倒装芯片的结构可以从根本上消除上面的问题。而且p电极也会遮挡住部分光,限制了LED芯片的出光效率。 采用倒装结构的LED芯片,不但可以同时避开P电极上导电层吸收光和电极垫遮光的问题,还可以通过在p-GaN表面设置低欧姆接触的反光层来将往下的光线引导向上,这样可同时降低驱动电压及提高光强。另一方面,图形化蓝宝石衬底(PSS)技术和芯片表面粗糙化技术同样可以增大LED芯片的出光效率50%以上。 (2)散热更好。LED是靠电子在能带间跃迁产生光的,其光谱中不含有红外部分,所以LED的热量不能靠辐射散发。一旦LED的温度超过最高临界温度(跟据不同外延及工艺,芯片温度大概为150℃),往往会造成LED永久性失效。与传统正装结构以蓝宝石衬底作为散热通道相比,垂直及倒装焊芯片结构有着较佳的散热能力。垂直结构芯片直接采用铜合金作为衬底,有效地提高了芯片的散热能力。倒装焊(Flip-Chip)技术通过共晶焊将LED芯片倒装到具有更高导热率的硅衬底上(导热系数约120W/mK,传统正装芯片蓝宝石导热系数约20W/mK),芯片与衬底间的金凸点和硅衬底同时提高了LED芯片的散热能力,保障LED的热量能够快速从芯片中导出。 (3)防静电能力增强。抗静电释放(ESD)能力是影响LED芯片可靠性的另一因素。对于InGaN/AlGaN/GaN 双异质结,InGaN 活化簿层厚度仅几十纳米,对静电的承受能力有限,很容易被静电击穿,使器件失效。可以在LED芯片中加入齐纳保护电路防止静电。通常需要在封装过程中通过金线并联一颗齐纳芯片以提高ESD防护能力,不仅增加封装成本和工艺难度,可靠性也有较大的风险。通过在硅衬底内部集成齐纳保护电路的方法,可以大大提高LED芯片的抗静电释放能力(ESDHBM=4000~8000V),同时节约封装成本,简化封装工艺,并提高产品可靠性。 (4)在封装过程中通过焊线(Wire-bonding)的方式实现芯片与支架的电路连接,而焊接过程中瓷嘴对LED的芯片的冲击是导致LED漏电、虚焊等主要原因,传统正装和垂直结构LED,电极位于芯片的发光表面,因此焊线过程中瓷嘴的正面冲击极易造成发光区和电极金属层等的损伤,在LED芯片采取倒装结构中,电极位于硅基板上,焊线过程中不对芯片进行冲击,极大地提高封装可靠性和
倒装封装介绍
倒装封装介绍 什么是LED倒装芯片?近年来,在芯片领域,倒装芯片技术正异军突起,特别是在大功率、户外照明的应用市场上更受欢迎。但由于发展较晚,很多人不知道什么叫LED倒装芯片,LED倒装芯片的优点是什么?今天慧聪LED屏网编辑就为你做一个简单的说明。先从LED正装芯片为您讲解LED倒装芯片,以及LED倒装芯片的优势和普及难点。 要了解LED倒装芯片,先要了解什么是LED正装芯片 LED正装芯片是最早出现的芯片结构,也是小功率芯片中普遍使用的芯片结构。该结构,电极在上方,从上至下材料为:P-GaN,发光层,N-GaN,衬底。所以,相对倒装来说就是正装。 LED倒装芯片和症状芯片图解 为了避免正装芯片中因电极挤占发光面积从而影响发光效率,芯片研发人员设计了倒装结构,即把正装芯片倒置,使发光层激发出的光直接从电极的另一面发出(衬底最终被剥去,芯片材料是透明的),同时,针对倒装设计出方便LED封装厂焊线的结构,从而,整个芯片称为倒装芯片(Flip Chip),该结构在大功率芯片较多用到。 正装、倒装、垂直LED芯片结构三大流派
倒装技术并不是一个新的技术,其实很早之前就存在了。倒装技术不光用在LED行业,在其他半导体行业里也有用到。目前LED芯片封装技术已经形成几个流派,不同的技术对应不同的应用,都有其独特之处。 目前LED芯片结构主要有三种流派,最常见的是正装结构,还有垂直结构和倒装结构。正装结构由于p,n电极在LED同一侧,容易出现电流拥挤现象,而且热阻较高,而垂直结构则可以很好的解决这两个问题,可以达到很高的电流密度和均匀度。未来灯具成本的降低除了材料成本,功率做大减少LED颗数显得尤为重要,垂直结构能够很好的满足这样的需求。这也导致垂直结构通常用于大功率LED应用领域,而正装技术一般应用于中小功率LED。而倒装技术也可以细分为两类,一类是在蓝宝石芯片基础上倒装,蓝宝石衬底保留,利于散热,但是电流密度提升并不明显;另一类是倒装结构并剥离了衬底材料,可以大幅度提升电流密度。 LED倒装芯片的优点 一是没有通过蓝宝石散热,可通大电流使用;二是尺寸可以做到更小,光学更容易匹配;三是散热功能的提升,使芯片的寿命得到了提升;四是抗静电能力的提升;五是为后续封装工艺发展打下基础。 什么是LED倒装芯片 据了解,倒装芯片之所以被称为“倒装”是相对于传统的金属线键合连接方式(Wire Bonding)与植球后的工艺而言的。传统的通过金属线键合与基板连接的晶片电气面朝上,而倒装晶片的电气面朝下,相当于将前者翻转过来,故称其为“倒装芯片”。 倒装LED芯片,通过MOCVD技术在蓝宝石衬底上生长GaN基LED结构层,由P/N结发光区发出的光透过上面的P型区射出。由于P型GaN传导性能不佳,为获得良好的电流扩展,需要通过蒸镀技术在P区表面形成一层Ni- Au组成的金属电极层。P 区引线通过该层金属薄膜引出。为获得好的电流扩展,Ni-Au金属电极层就不能太薄。为此,器件的发光效率就会受到很大影响,通常要同时兼顾电流扩展与出光效率二个因素。但无论在什麼情况下,金属薄膜的存在,总会使透光性能变差。此外,引线焊点的存在也使器件的出光效率受到影响。采用GaN LED倒装芯片的结构可以从根本上消除上面的问题。 在倒装芯片的技术基础上,有厂家发展出了LED倒装无金线芯片级封装。 什么是LED倒装无金线芯片级封装 倒装无金线芯片级封装,基于倒装焊技术,在传统LED芯片封装的基础上,减少了金线封装工艺,省掉导线架、打线,仅留下芯片搭配荧光粉与封装胶使用。作为新封装技术产品,倒装无金线芯片级光源完全没有因金线虚焊或接触不良引起的不亮、闪烁、
FC倒装芯片装配技术介绍
FC倒装芯片装配技术介绍 器件的小型化高密度封装形式越来越多,如多模块封装(MCM)、系统封装(SiP)、倒装芯片(FC,Flip-Chip)等应用得越来越多。这些技术的出现更加模糊了一级封装与二级装配之间的界线。毋庸置疑,随着小型化高密度封装的出现,对高速与高精度装配的要求变得更加关键,相关的组装设备和工艺也更具先进性与高灵活性。 由于倒装芯片比BGA或CSP具有更小的外形尺寸、更小的球径和球间距、它对植球工艺、基板技术、材料的兼容性、制造工艺,以及检查设备和方法提出了前所未有的挑战。 倒装芯片的发展历史 倒装芯片的定义 什么器件被称为倒装芯片?一般来说,这类器件具备以下特点: 1. 基材是硅; 2. 电气面及焊凸在器件下表面; 3. 球间距一般为4-14mil、球径为2.5-8mil、外形尺寸为1-27mm; 4. 组装在基板上后需要做底部填充。 其实,倒装芯片之所以被称为“倒装”,是相对于传统的金属线键合连接方式(Wire Bonding)与植球后的工艺而言的。传统的通过金属线键合与基板连接的芯片电气面朝上(图1),而倒装芯片的电气面朝下(图2),相当于将前者翻转过来,故称其为“倒装芯片”。在圆片(Wafer)上芯片植完球后(图3),需要将其翻转,送入贴片机,便于贴装,也由于这一翻转过程,而被称为“倒装芯片”。 倒装芯片的历史及其应用 倒装芯片在1964年开始出现,1969年由IBM发明了倒装芯片的C4工艺(Controlled Collapse Chip Connection,可控坍塌芯片联接)。过去只是比较少量的特殊应用,近几年倒装芯片已经成为高
性能封装的互连方法,它的应用得到比较广泛快速的发展。目前倒装芯片主要应用在Wi- Fi、SiP、MCM、图像传感器、微处理器、硬盘驱动器、医用传感器,以及RFID等方面(图5)。 与此同时,它已经成为小型I/O应用有效的互连解决方案。随着微型化及人们已接受SiP,倒装芯片被视为各种针脚数量低的应用的首选方法。从整体上看,其在低端应用和高端应用中的采用,根据TechSearch International Inc对市场容量的预计,焊球凸点倒装芯片的年复合增长率(CAGR)将达到31%。 倒装芯片应用的直接驱动力来自于其优良的电气性能,以及市场对终端产品尺寸和成本的要求。在功率及电信号的分配,降低信号噪音方面表现出色,同时又能满足高密度封装或装配的要求。可以预见,其应用会越来越广泛。 倒装芯片的组装工艺流程 一般的混合组装工艺流程在半导体后端组装工厂中,现在有两种模块组装方法。在两次回流焊工艺中,先在单独的SMT生产线上组装SMT器件,该生产线由丝网印刷机、贴片机和第一个回流焊炉组成。然后再通过第二条生产线处理部分组装的模块,该生产线由倒装芯片贴片机和回流焊炉组成。底部填充工艺
倒装芯片工艺挑战SMT组装
倒装芯片工艺挑战SMT组装 1 引言 20世纪90年代以来,移动、个人数字助手(PDA)、数码相机等消费类电子产品的体积越来越小,工作速度越来越快,智能化程度越来越高。这些日新月异的变化为电子封装与组装技术带来了许多挑战和机遇。材料、设备性能与工艺操纵能力的改进使越来越多的EMS公司能够跃过标准的表面安装技术(SMT)直截了当进入先进的组装技术 领域,包括倒装芯片等。由于越来越多的产品设计需要不断减小体积,提高工作速度,增加功能,因此能够估量,倒装芯片技术的应用范畴将不断扩大,最终会取代SMT当前的地位,成为一种标准的封装技术。 多年以来,半导体封装公司与EMS公司一直在携手合作,在发挥各自特长的同时又参与对方领域的技术业务,力争使自己的技术能力更加完善和全面。在半导体工业需求日益增加的环境下,越来越多的公司开始提供\\\"完整的解决方案\\\"。这种趋同性是人们所期望看到的,但同时双方都会面临一定的挑战。 例如,以倒装芯片BGA或系统封装模块为例,随着采
纳先进技术制造而成的产品的类型由板组装方式向元件组装方式的转变,以往看起来不太重要的诸多因素都将发挥至关重要的作用。互连应力不同了,材料的不兼容性增加了,工艺流程也不一样了。不论你的新产品类型是否需要倒装芯片技术,不论你是否认为采纳倒装芯片的时刻合适与否,明白得倒装芯片技术所存在的诸多挑战差不多上十分重要的。 2 倒装芯片技术 \\\"倒装芯片技术\\\",这一名词包括许多不同的方法。每一种方法都有许多不同之处,且应用也有所不同。例如,就电路板或基板类型的选择而言,不管它是有机材料、陶瓷材料依旧柔性材料,都决定着组装材料(凸点类型、焊剂、底部填充材料等)的选择,而且在一定程度上还决定着所需设备的选择。在目前的情形下,每个公司都必须决定采纳哪一种技术,选购哪一类工艺部件,为满足以后产品的需要进行哪一些研究与开发,同时还需要考虑如何将资本投资和运作成本降至最低额。 在SMT环境中最常用、最合适的方法是焊膏倒装芯片组装工艺。即使如此,为了确保可制造性、可靠性并达到成本目标也应考虑到该技术的许多变化。目前广泛采纳的倒装芯片方法要紧是依照互连结构而确定的。如,柔顺凸
LED倒装工艺流程分析
LED倒装工艺流程分析 近年来LED在电视机背光、手机、和平板电脑等方面的应用也迎来了爆发式的增长,LED具有广阔的应用发展前景。 倒装LED技术的发展及现状 倒装技术在LED领域上还是一个比较新的技术概念,但在传统IC行业中已经被广泛应用且比较成熟,如各种球栅阵列封装(BGA)、芯片尺寸封装(CSP)、晶片级芯片尺寸封装(WLCSP)等技术,全部采用倒装芯片技术,其优点是生产效率高、器件成本低和可靠性高。 倒装芯片技术应用于LED器件,主要区别于IC在于,在led芯片制造和封装过程中,除了要处理好稳定可靠的电连接以外,还需要处理光的问题,包括如何让更多的光引出来,提高出光效率,以及光空间的分布等。 针对传统正装LED存在的散热差、透明电极电流分布不均匀、表面电极焊盘和引线挡光以及金线导致的可靠性问题,1998年,J.J.Wierer等人制备出了1W倒装焊接结构的大功率AlGaInN-LED蓝光芯片,他们将金属化凸点的AIGalnN芯片倒装焊接在具有防静电保护二极管(ESD)的硅载体上。 测试结果表明,在相同的芯片面积下,倒装led芯片(FCLED)比正装芯片有着更大的发光面积和非常好的电学特性,在200-1000mA的电流范围,正向电压(VF)相对较低,从而导致了更高的功率转化效率。 2006年,O.B.Shchekin等人又报道了一种新的薄膜倒装焊接的多量子阱结构的LED(TFFC-LED)。所谓薄膜倒装LED,就是将薄膜LED与倒装LED的概念结合起来。 在将LED倒装在基板上后,采用激光剥离(Laser lift-off)技术将蓝宝石衬底剥离掉,然后在暴露的N型GaN层上用光刻技术做表面粗化。 随着硅基倒装芯片在市场上销售,逐渐发现这种倒装LED芯片在与正装芯片竞争时,其成本上处于明显的劣势。 由于LED发展初期,所有封装支架和形式都是根据其正装或垂直结构LED 芯片进行设计的,所以倒装LED芯片不得不先倒装在硅基板上,然后将芯片固定在传统的支架上,再用金线将硅基板上的电极与支架上的电极进行连接。 使得封装器件内还是有金线的存在,没有利用上倒装无金线封装的优势;而且还增加了基板的成本,使得价格较高,完全没有发挥出倒装LED芯片的优势。 为此,最早于2007年有公司推出了陶瓷基倒装led封装产品。这一类型的产品,陶瓷既作为倒装芯片的支撑基板,也作为整体封装支架,实现整封装光源的小型化。
FC(倒装)
倒装芯片 Flip chip(倒装芯片):一种无引脚结构,一般含有电路单元。设计用于通过适当数量的位于其面上的锡球(导电性粘合剂所覆盖),在电气上和机械上连接于电路。 起源于60年代,由IBM率先研发出,具体原理是在I/Opad上沉积锡铅球,然后将芯片翻转加热利用熔融的锡铅球与陶瓷板相结合,此技术已替换常规的打线接合,逐渐成为未来封装潮流。Flip Chip既是一种芯片互连技术,又是一种理想的芯片粘接技术.早在30年前IBM公司已研发使用了这项技术。但直到近几年来,Flip-Chip已成为高端器件及高密度封装领域中经常采用的封装形式。今天,Flip-Chip封装技术的应用范围日益广泛,封装形式更趋多样化,对Flip-Chip封装技术的要求也随之提高。同时,Flip-Chip也向制造者提出了一系列新的严峻挑战,为这项复杂的技术提供封装,组装及测试的可靠支持。以往的一级封闭技术都是将芯片的有源区面朝上,背对基板和贴后键合,如引线健合和载带自动健全(TAB)。FC则将芯片有源区面对基板,通过芯片上呈阵列排列的焊料凸点实现芯片与衬底的互连.硅片直接以倒扣方式安装到PCB从硅片向四周引出I/O,互联的长度大大缩短,减小了RC延迟,有效地提高了电性能.显然,这种芯片互连方式能提供更高的I/O密度.倒装占有面积几乎与芯片大小一致.在所有表面安装技术中,倒装芯片可以达到最小、最薄的封装。 Flip chip又称倒装片,是在I/O pad上沉积锡铅球,然后将芯片翻转佳热利用熔融的锡铅球与陶瓷机板相结合此技术替换常规打线接合,逐渐成为未来的封装主流,当前主要应用于高时脉的CPU、 GPU(GraphicProcessor Unit)及Chipset 等产品为主。与COB相比,该封装形式的芯片结构和I/O端(锡球)方向朝下,由于I/O引出端分布于整个芯片表面,故在封装密度和处理速度上Flip chip已达到顶峰,特别是它可以采用类似SMT技术的手段来加工,因此是芯片封装技术及高密度安装的最终方向。倒装片连接有三种主要类型C4(Controlled Collapse Chip Connection)、DCA(Direct chip attach)和FCAA(Flip Chip Adhesive Attachement)。 C4是类似超细间距BGA的一种形式与硅片连接的焊球阵列一般的间距为0.23、 0.254mm。焊球直径为0.102、0.127mm。焊球组份为97Pb/3Sn。这些焊球在硅片上可以呈完全分布或部分分布。 由于陶瓷可以承受较高的回流温度,因此陶瓷被用来作为C4连接的基材,通常是在陶瓷的表面上预先分布有镀Au或Sn的连接盘,然后进行C4形式的倒装片连接。C4连接的优点在于:
SMT环境中倒装芯片工艺与技术应用
SMT环境中倒装芯片工艺与技术应用 1、引言 倒装芯片的成功实现与使用包含诸多设计、工艺、设备与材料因素。只有对每一个因素都加以认真考虑和对待才能够促进工艺和技术的不断完善和进步,才能满足应用领域对倒装芯片技术产品不断增长的需要。 2、倒装芯片技术 “倒装芯片技术”这一名词包括许多不同的方法。每一种方法都有许多不同之处,且应用也有所不同。例如,就电路板或基板类型的选择而言,无论它是有机材料、陶瓷材料还是柔性材料,都决定着组装材料(凸点类型、焊剂、底部填充材料等)的选择,而且在一定程度上还决定着所需设备的选择。在目前的情况下,每个公司都必须决定采用哪一种技术,选购哪一类工艺部件,为满足未来产品的需要进行哪一些研究与开发,同时还需要考虑如何将资本投资和运作成本降至最低额。 在SMT环境中最常用、最合适的方法是焊膏倒装芯片组装工艺。即使如此,为了确保可制造性、可靠性并达到成本目标也应考虑到该技术的许多变化。目前广泛采用的倒装芯片方法主要是根据互连结构而确定的。如,柔顺凸点技术的实现要采用镀金的导电聚合物或聚合物/弹性体凸点。 焊柱凸点技术的实现要采用焊球键合(主要采用金线)或电镀技术,然后用导电的各向同性粘接剂完成组装。工艺中不能对集成电路(1C)键合点造成影响。在这种情况下就需要使用各向异性导电膜。焊膏凸点技术包括蒸发、电镀、化学镀、模版印刷、喷注等。因此,互连的选择就决定了所需的键合技术。通常,可选择的键合技术主要包括:再流键合、热超声键合、热压键合和瞬态液相键合等。 上述各种技术都有利也有弊,通常都受应用而驱动。但就标准SMT工艺使用而言,焊膏倒装芯片组装工艺是最常见的,且已证明完全适合SMT。 3、焊膏倒装芯片组装技术 传统的焊膏倒装芯片组装工艺流程包括:涂焊剂、布芯片、焊膏再流与底部填充等。但为了桷保成功而可靠的倒装芯片组装还必须注意其它事项。通常,成功始于设计。 首要的设计考虑包括焊料凸点和下凸点结构,其目的是将互连和IC键合点上的应力降至最低。如果互连设计适当的话,已知的可靠性模型可预测出焊膏上将要出现的问题。对IC键合点结构、钝化、聚酰亚胺开口以及下凸点治金(UBM)结构进行合理的设计即可实现这一目的。钝化开口的设计必须达到下列目
倒装芯片工艺与SMT组装探讨
倒装芯片工艺挑战SMT组装 1引言 20世纪90年代以来,移动电话、个人数字助手(PDA)、数码相机等消费类电子产品的体积越来越小,工作速度越来越快,智能化程度越来越高。这些日新月异的变化为电子封装与组装技术带来了许多挑战和机遇。材料、设备性能与工艺控制能力的改进使越来越多的EMS公司可以跳过标准的表面安装技术(SMT)直接进入先进的组装技术领域,包括倒装芯片等。由于越来越多的产品设计需要不断减小体积,提高工作速度,增加功能,因此可以预计,倒装芯片技术的应用范围将不断扩大,最终会取代SMT当前的地位,成为一种标准的封装技术。 多年以来,半导体封装公司与EMS公司一直在携手合作,在发挥各自特长的同时又参与对方领域的技术业务,力争使自己的技术能力更加完善和全面。在半导体工业需求日益增加的环境下,越来越多的公司开始提供\\\"完整的 解决方案\\\"。这种趋同性是人们所期望看到的,但同时双方都会面临一定的挑战。 例如,以倒装芯片BGA或系统封装模块为例,随着采用先进技术制造而成的产品的类型由板组装方式向元件组装
方式的转变,以往似乎不太重要的诸多因素都将发挥至关 重要的作用。互连应力不同了,材料的不兼容性增加了,工艺流程也不一样了。不论你的新产品类型是否需要倒装芯片技术,不论你是否认为采用倒装芯片的时间合适与否,理解倒装芯片技术所存在的诸多挑战都是十分重要的。 2 倒装芯片技术 \\\"倒装芯片技术\\\",这一名词包括许多不同的方法。每一种方法都有许多不同之处,且应用也有所不同。例如,就电路板或基板类型的选择而言,无论它是有机材料、陶瓷材料还是柔性材料,都决定着组装材料(凸点类型、焊剂、底部填充材料等)的选择,而且在一定程度上还决定着所需设备的选择。在目前的情况下,每个公司都必须决定采用哪一种技术,选购哪一类工艺部件,为满足未来产品的需要进行哪一些研究与开发,同时还需要考虑如何将资本投资和运作成本降至最低额。 在SMT环境中最常用、最合适的方法是焊膏倒装芯片组装工艺。即使如此,为了确保可制造性、可靠性并达到成本目标也应考虑到该技术的许多变化。目前广泛采用的倒装芯片方法主要是根据互连结构而确定的。如,柔顺凸点技术的实现要采用镀金的导电聚合物或聚合物/弹性体凸
倒装焊芯片
倒装焊芯片(Flip-Chip)是什么意思作者:佚名来源:https://www.360docs.net/doc/4a18787594.html, 发布时间:2010-3-4 14:08:08 [收藏] [评论] 倒装焊芯片(Flip-Chip)是什么意思 Flip Chip既是一种芯片互连技术,又是一种理想的芯片粘接技术.早在30年前IBM公司已研发使用了这项技术。但直到近几年来,Flip-Chip已成为高端器件及高密度封装领域中经常采用的封装形式。今天,Flip-Chip封装技术的应用范围日益广泛,封装形式更趋多样化,对Flip-Chip封装技术的要求也随之提高。同时,Flip-Chip也向制造者提出了一系列新的严峻挑战,为这项复杂的技术提供封装,组装及测试的可靠支持。以往的一级封闭技术都是将芯片的有源区面朝上,背对基板和贴后键合,如引线健合和载带自动健全(TAB)。FC则将芯片有源区面对基板,通过芯片上呈阵列排列的焊料凸点实现芯片与衬底的互连.硅片直接以倒扣方式安装到PCB从硅片向四周引出I/O,互联的长度大大缩短,减小了RC延迟,有效地提高了电性能.显然,这种芯片互连方式能提供更高的I/O密度.倒装占有面积几乎与芯片大小一致.在所有表面安装技术中,倒装芯片可以达到最小、最薄的封装。 而FC-BGA(Flip Chip Ball Grid Array:倒装芯片球栅格阵列)是一种较新的支持表明安装板的封装形式,采用C4可控塌陷芯片法焊接,大幅度改善电器性能,据称能提高封装成品率(没有查到具体数据是多少)。这种封装允许直接连接到底层,具体来说由倒装在元件底部上的硅核组成,使用金属球代替原先的针脚来连接处理器,如果把焊接比喻成缝衣的话,那么这种焊接方式可以让针脚均匀一致,连接距离更短引脚间距增大,避免了虚焊和针脚弯曲弯曲现象。FC-BGA封装共使用了479个直径仅为0.78毫米的封装球使得封装高度大为减小,怎么样,“针脚”的确够小吧?采用这种工艺带来的好处也是很明显的:那就是可以大大减小芯片封装后的尺寸(核心/封装比可做到1:1.5)令核心外露,热传导效率增加,毫无疑问,这种工艺非常适合高速芯片的封装。除此以外,因为芯片的引脚是由中心方向引出的,和基板距离缩短,因此干扰少,电信号传递更快速稳定而纯净,十分有助于超频。目前台湾主要的封装厂如全懋、日月光、景硕、南亚等都有能力做FC-BGA封装。当然喽,成本方面,FC-BGA比Wirebond封装要贵上许多(2.5美圆V S1美圆)!下面就是两种封装能达到的频率理论值: * 频率和晶体管数目/功耗等密切相关,以上注明的频率均针对VPU 我们看到,FC-BGA封装的理论极限大概是Wirbond的1.45倍! 普通版本的FX5600XT核心的售价是47美圆,FC-BGA封装的VPU要贵近20美圆,出货量之比是100:1,十分稀少。
影响倒装芯片底部填充胶流动的因素分析解读
第2卷第2期 2008年6月 材料研究与应用MATERIALSRESEARCHANDAPPLICATION Vo112,No12Jun12008 文章编号:167329981(2008)0120151204 影响倒装芯片底部填充胶流动的因素分析 张良明 (广州大学,广东广州510006) 摘要:材料特性对倒装芯片底部填充胶流动的影响因素主要有表面张力、1在考虑焊球点影响的情况下,主要影响因素有焊球点的布置密度及边缘效应.关键词:倒装芯片;填充胶;焊球点;表面张力;接触角中图分类号:O35文献标识码:A 在对外形尺寸要求苛刻的中,,在温,使连接芯片与电路基板的焊球点(凸点)断裂,从而使元件的电热阻增加,甚至使整个元件失效.解决这个问题既直接又简单的办法是,在芯片与电路基板之间填充密封剂(简称填充胶).这样可以增加芯片与基板的连接面积,提高二者的结合强度,对凸点起到保护作用.底部填充是倒装芯片互连工艺的主要工序之一,对倒装芯片可靠性的影响很大,所以研究填充胶的流动性有着重 要的意义. σ为填充胶流动前端与空气之间的表式(1)中: 面张力,xf为填充胶流动前端所走过的距离,θ为填充胶流动过程中与芯片所形成的接触角,μ为牛顿流体的填充胶的粘度,h为芯片与电路底板之间的缝隙高度.当填充完成时,填充胶流动的距离L即为方形芯片的长度.在不考虑焊球的影响和假设填充胶是牛顿流体的情况下,上述因素都会影响填充胶的流动.1.1.1表面张力 填充胶在流动的过程中,壁面的粘滞力是其在晶片与基板间隙间流动的唯一推动力.表面张力σ与压力差VP和接触角θ之间的关系[3]可以表示为: VP= . h (2)
采用热压焊工艺实现金凸点芯片的倒装焊接_张彩云
采用热压焊工艺实现金凸点芯片的倒装焊接 张彩云,霍灼琴,高敏,张晨曦 (中国电子科技集团公司第二研究所,山西 太原 030024) 摘 要:金凸点芯片的倒装焊接是一种先进的封装技术。叙述了钉头金凸点硅芯片在高密度薄膜陶瓷基板上的热压倒装焊接工艺方法,通过设定焊接参数达到所期望的最大剪切力,分析研究 互连焊点的电性能和焊接缺陷,实现了热压倒装焊工艺的优化。同时,还简要介绍了芯片钉头金凸点的制作工艺。 关键词:倒装焊;热压焊;金凸点芯片;薄膜基板中图分类号:T N 60 文献标识码:A 文章编号:1001-3474(2008)01-0028-03 A s s e m b l y o f F l i pC h i pG o l d B u m p s Wi t h T h e r m o -c o m p r e s s i o nB o n d i n g P r o c e s s Z H A N G C a i -y u n ,H U O Z h u o -q i n ,G A OMi n ,Z H A N G C h e n -x i (C E T CN o .2R e s e a r c hI n s t i t u t e ,T a i y u a n 030024,C h i n a A b s t r a c t :A s s e m b l y o f f l i pc h i pg o l db u m p s i s a na d v a n c e de l e c t r o n i c p a c k a g i n g t e c h n o l o g y .D e -s c r i b e t h e a s s e m b l y o f S i c h i p s b u m p e d A u s t u d s o n h i g h d e n s i t y t h i c k f i l mc e r a m i c s u b s t r a t e s w i t h t h e r m o -c o m p r e s s i o n b o n d i n g .I n o r d e r t o o p t i m i z e t h e t h e r m o -c o m p r e s s i o n b o n d i n g p r o c e s s ,t h e b o n d i n g p a -r a m e t e r s w e r e o p t i m i z e d w i t h r e s p e c t t o t h e m a x i m u ms h e a r s t r e n g t h ,e l e c t r i c a l q u a l i t y o f t h e i n t e r c o n n e c -t i o n a n d p o s s i b l e d e f e c t s o n c h i p w e r e i n v e s t i g a t e d .S i m u l t a n e i t y i n t r o d u c e t h e b u m p i n g t e c h n o l o g y o f A u s t u d s o f c h i p s . K e y w o r d s :F l i p C h i p a s s e m b l y ;T h e r m o -c o m p r e s s i o n b o n d i n g ;G o l d b u m p s ;T h i c k f i l m s u b s t r a t e s D o c u m e n t C o d e :A A r t i c l e I D :1001-3474(2008)01-0028-03 近年来,电子工业产品向小型化、高密度和多功能性方向发展,电子组装和封装技术是实现此目的的关键技术之一。多功能和小型化将直接转化为高密度芯片互连工艺,需要载带自动焊(T A B )和倒装焊接(F C )等先进组装技术。与其它组装技术相比,倒装焊技术具有较高的互连密度和优越的高频、低延迟、低串扰的电路特性,因此越来越受到关注,将成为芯片互连技术的主流,广泛地应用于先进电子器件和组件的封装制造。 热压焊工艺是通过加热和加压,使焊区发生塑形变形,同时破坏压焊界面上的氧化层,从而使原子间产生吸引力达到“键合”,此外由于两金属界面的 不平整,加热加压也可使上下金属相互镶嵌,从而达到焊接的目的。热压焊工艺已在液晶显示(L C D )的玻璃板上芯片(C O G )和光电器件中的铟凸点芯片焊接中成功应用。而金凸点芯片的倒装焊接常规使用热超声焊接工艺完成。本文所述内容是在借鉴国外先进工艺的基础上,开展的金凸点芯片的热压倒装焊接技术研究。1 芯片凸点制作 倒装互连工艺已研发出基于焊料和胶剂技术的多种方法,其中大多数方法需要采用半导体圆片后道工艺制作芯片凸点。然而许多场合需要更柔性的凸点制作方法,即在划片后的标准芯片上单独形成 作者简介:张彩云(1969-),女,毕业于燕山大学,高级工程师,主要从事微电子专用设备及其工艺技术的研究工作。 28 电子工艺技术E l e c t r o n i c s P r o c e s s T e c h n o l o g y 第29卷第1期 2008年1月 DOI :10.14176/j .issn .1001-3474.2008.01.008
芯片倒装技术及芯片封装技术
芯片倒装技术及芯片封装技术 引言世纪90年代以来,移动电话、个人数字助手(PDA)、数码相机等消费类电子产品的体积越来越小,工作速度越来越快,智能化程度越来越高。这些日新月异的变化为电子封装与组装技术带来了很多挑战和机遇。材料、设备机能与工艺控制能力的改进使越来越多的EMS 公司可以跳过尺度的表面安装技术(SMT)直接进入提高前辈的组装技术领域,包括倒装芯片等。因为越来越多的产品设计需要不断减小体积,进步工作速度,增加功能,因此可以预计,倒装芯片技术的应用范围将不断扩大,终极会取代SMT当前的地位,成为一种尺度的封装技术。 多年以来,半导体封装公司与EMS公司一直在通力进行,在施展各自特长的同时又介入对方领域的技术业务,力争使自己的技术能力更加完善和全面。在半导体产业需求日益增加的环境下,越来越多的公司开始提供\\\"完整的解决方案\\\"。这种趋同性是人们所期望看到的,但同时双方都会面对一定的挑战。 例如,以倒装芯片BGA或系统封装模块为例,跟着采用提高前辈技术制造而成的产品的类型由板组装方式向元件组装方式的转变,以往好像不太重要的诸多因素都将施展至关重要的作用。互连应力不同了,材料的不兼容性增加了,工艺流程也不一样了。不论你的新产品类型是否需要倒装芯片技术,不论你是否以为采用倒装芯片的时间合适与否,理解倒装芯片技术所存在的诸多挑战都是十分重要的。 倒装芯片技术倒装芯片技术\\\",这一名词包括很多不同的方法。每一种方法都有很多不同之处,且应用也有所不同。例如,就电路板或基板类型的选择而言,不管它是有机材料、陶瓷材料仍是柔性材料,都决定着组装材料(凸点类型、焊剂、底部填充材料等)的选择,而且在一定程度上还决定着所需设备的选择。在目前的情况下,每个公司都必需决定采用哪一种技术,选购哪一类工艺部件,为知足未来产品的需要进行哪一些研究与开发,同时还需要考虑如何将资本投资和运作本钱降至最低额。 在SMT环境中最常用、最合适的方法是焊膏倒装芯片组装工艺。即使如斯,为了确保可制造性、可靠性并达到本钱目标也应考虑到该技术的很多变化。目前广泛采用的倒装芯片方法主要是根据互连结构而确定的。如,和婉凸点技术的实现要采用镀金的导电聚合物或聚合物/弹性体凸点。 焊柱凸点技术的实现要采用焊球键合(主要采用金线)或电镀技术,然后用导电的各向同性粘接剂完成组装。工艺中不能对集成电路(1C)键合点造成影响。在这种情况下就需要使用各向异性导电膜。焊膏凸点技术包括蒸发、电镀、化学镀、模版印刷、喷注等。因此,互连的选择就决定了所需的键合技术。通常,可选择的键合技术主要包括:再流键合、热超声键合、热压键合和瞬态液相键合等。 上述各种技术都有利也有弊,通常都受应用而驱动。但就尺度SMT工艺使用而言,焊膏倒装芯片组装工艺是最常见的,且已证实完全适合焊膏倒装芯片组装技术传统的焊膏倒装芯片组装工艺流程包括:涂焊剂、布芯片、焊膏再流与底部填充等。但为了桷保成功而可靠的倒装芯片组装还必需留意其它事项。通常,成功始于设计。 首要的设计考虑包括焊料凸点和下凸点结构,其目的是将互连和IC键合点上的应力降至最低。假如互连设计适当的话,已知的可靠性模型可猜测出焊膏上将要泛起的题目。对IC 键合点结构、钝化、聚酰亚胺启齿以及下凸点治金(UBM)结构进行公道的设计即可实现这一目的。钝化启齿的设计必需达到下列目的:降低电流密度;减小集中应力的面积;进步电迁移的寿命;最大限度地增大UBM和焊料凸点的断面面积。 凸点位置布局是另一项设计考虑,焊料凸点的位置尽可能的对称,识别定向特征(去掉一个边角凸点)是个例外。布局设计还必需考虑顺流切片操纵不会受到任何干扰。在IC的有