铜箔表面处理技术
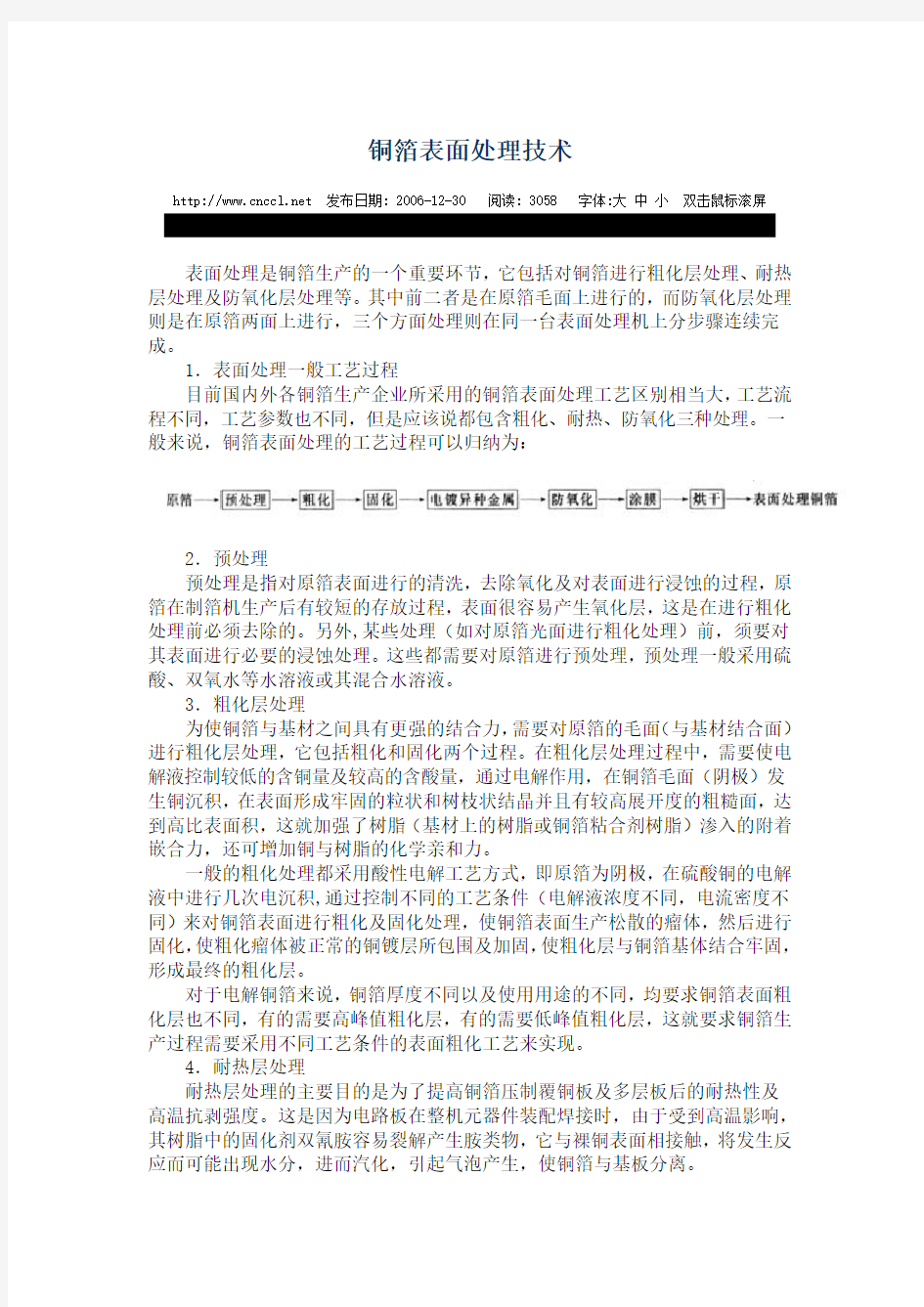

铜箔表面处理技术
https://www.360docs.net/doc/4d10005539.html, 发布日期: 2006-12-30 阅读: 3058 字体:大中小双击鼠标滚屏
表面处理是铜箔生产的一个重要环节,它包括对铜箔进行粗化层处理、耐热层处理及防氧化层处理等。其中前二者是在原箔毛面上进行的,而防氧化层处理则是在原箔两面上进行,三个方面处理则在同一台表面处理机上分步骤连续完成。
1.表面处理一般工艺过程
目前国内外各铜箔生产企业所采用的铜箔表面处理工艺区别相当大,工艺流程不同,工艺参数也不同,但是应该说都包含粗化、耐热、防氧化三种处理。一般来说,铜箔表面处理的工艺过程可以归纳为:
2.预处理
预处理是指对原箔表面进行的清洗,去除氧化及对表面进行浸蚀的过程,原箔在制箔机生产后有较短的存放过程,表面很容易产生氧化层,这是在进行粗化处理前必须去除的。另外,某些处理(如对原箔光面进行粗化处理)前,须要对其表面进行必要的浸蚀处理。这些都需要对原箔进行预处理,预处理一般采用硫酸、双氧水等水溶液或其混合水溶液。
3.粗化层处理
为使铜箔与基材之间具有更强的结合力,需要对原箔的毛面(与基材结合面)进行粗化层处理,它包括粗化和固化两个过程。在粗化层处理过程中,需要使电解液控制较低的含铜量及较高的含酸量,通过电解作用,在铜箔毛面(阴极)发生铜沉积,在表面形成牢固的粒状和树枝状结晶并且有较高展开度的粗糙面,达到高比表面积,这就加强了树脂(基材上的树脂或铜箔粘合剂树脂)渗入的附着嵌合力,还可增加铜与树脂的化学亲和力。
一般的粗化处理都采用酸性电解工艺方式,即原箔为阴极,在硫酸铜的电解液中进行几次电沉积,通过控制不同的工艺条件(电解液浓度不同,电流密度不同)来对铜箔表面进行粗化及固化处理,使铜箔表面生产松散的瘤体,然后进行固化,使粗化瘤体被正常的铜镀层所包围及加固,使粗化层与铜箔基体结合牢固,形成最终的粗化层。
对于电解铜箔来说,铜箔厚度不同以及使用用途的不同,均要求铜箔表面粗化层也不同,有的需要高峰值粗化层,有的需要低峰值粗化层,这就要求铜箔生产过程需要采用不同工艺条件的表面粗化工艺来实现。
4.耐热层处理
耐热层处理的主要目的是为了提高铜箔压制覆铜板及多层板后的耐热性及高温抗剥强度。这是因为电路板在整机元器件装配焊接时,由于受到高温影响,其树脂中的固化剂双氰胺容易裂解产生胺类物,它与裸铜表面相接触,将发生反应而可能出现水分,进而汽化,引起气泡产生,使铜箔与基板分离。
铜箔的耐热层处理一般采用电镀其他金属的办法,也就是在铜箔粗化层面上再镀一层其他金属,使铜表面不与基材直接接触,避免问题出现。
目前所镀金属一般有:镀一层锌,颜色为灰色,称为灰化处理,此种铜箔叫做镀锌铜箔;镀一层铜锌合金,即黄铜,颜色呈黄色,称为黄化处理,此种铜箔称为镀黄铜铜箔;镀一层镍,颜色为黑色,称为黑化处理,此种铜叫做镀镍铜箔。
耐热层处理不但可以阻挡胺类物对铜箔表面的攻击,而且有助于增加铜箔与基材的化学亲和力,进而提高抗剥强度。
5.防氧化处理
铜箔在贮存、运输及压板生产过程中,常会遇到一定湿度的空气及较高的温度,很容易使铜箔表面发生氧化变色,它会影响铜面的可焊性及对油墨的亲合性,并且引起铜箔厚度的微小变化及氧化层的产生,导致线路电阻增大,因此在铜箔生产过程中,要对铜箔表面进行
防氧化处理(有时也称钝化处理,稳定性处理)。
常见的防氧化处理有采用酸性工艺的,也有采用碱性工艺的。所谓酸性工艺就是所用溶液呈酸性,而碱性工艺的溶液则呈碱性,都是使铜箔作为阴极,通直流电,使得在铜箔表面形成以锌、铬为主体的结构复杂的防氧化膜,以使铜箔不直接与空气接触,达到防氧化目的。
6.表面处理过程中的其他工艺及条件
(1)涂膜工艺目前在某些铜箔生产过程中,在对铜箔进行粗化层处理、耐热层处理及防氧化层处理后,还要进行涂膜处理,它是一种有机膜,其作用有两个:一是进一步提高防氧化能力;二是有利于进一步提高铜箔与基材结合力。
(2)水洗表面处理是一个复杂的多种工艺过程,也是一个连续的生产工艺过程,在各步处理过程中都要有水洗过程,以清除表面附带的电解液。对所用的水要求很高,一般均采用离子交换水处理方式。它是采用离子交换树脂,使离子交换树脂中和水溶液中可交换离子之间发生符合等物质量规则的可逆性交换,使水中离子去除而离子交换树脂的结构并不发生实质性变化的一种水处理方式。
对于铜箔漂洗用水和电解液制备用水一般要求电导率应小于10 us/cm。
(3)烘干烘干是表面处理过程的最后一道必不可少的工序,它的目的是烘干去除铜箔表面的水分,防止残留水分对铜箔的危害。
根据铜箔处理速度的不同,烘干温度也就不同。一般以不低于100℃为原则,也有达到200℃甚至300℃以上的。原则上应完全彻底去除铜表面水分,又不能因温度过高而伤害铜箔。
(4)溶液制备表面处理过程中的预处理、粗化、固化、镀异种金属、防氧化及涂膜工艺采用的溶液都有一个制备过程。有的采用配制,有的需要采用溶铜方式。这些溶液都需要独立的制备设备、净化设备及温度调节设备,这些作为表面处理工艺过程的配套条件是必不可少的。
激光表面处理技术及其进展讲解
激光表面表面处理技术及进展 许彦明指导老师:宋世涛 (河北科技师范学院理化学院化学0703班) 摘要:激光具有巨大的技术潜力,在冶金和材料加工中发展迅速,应用广泛。激光表面处理由于其对工业和生产作出了巨大贡献,已成为飞速成长的重要加工技术领域。本文较系统地介绍了国内外激光表面处理技术的研究与应用近况,指出了这项技术今后需解决的问题。 关键字:激光;表面处理;进展 0 前言 激光的出现时近代物理学的一个重大进展。第一台激光器于60年代初问世,对激光表面热处理工艺的研究早在激光器诞生后不久就已经开始,但直到60年代末、70年代初才在热处理生产中获得应用。 激光在金属热处理方面取得成功,标志此技术的应用进人了新灼阶段。随着大功率激光器的研制成功与不断完善,这一新工艺用于汽车转向器表面处理的生产线[1]。国内经过“六五”计划的联合攻关,已在汽缸套等零部件的表面热处理上获得成功,取得了一批科研成果。随之而发展的表面涂覆(cladding),表面上釉(Glazing)及表面合金化(SurfaeeAlloing)等工艺[2]也取得了相当大的进展。与上述工艺相比较,激光表面热处理是当前比较成熟、应用比较广泛的工艺。 1 激光表面处理技术的特点[3] 1)通过选择激光波长调节激光功率等手段,能灵活地对复杂 形状工件或工件局部部位实施非接触性急热、急冷。该技术易控制处理范围,热影响区小,工件产生的残余应力及变形很小。 2)可在大气、真空及各种气氛中处理,制约条件少,且不造成 化学污染。 3)通常,激光表面处理的改性效果比普通处理方法更显著 4)激光束能量集中,密度大,速度快,效率高,成本低。 5)可缩短工艺流程,处理过程中工件可以运动,故特别适合组织自动化处理线。 6)激光束便于通过导光系统准确地输人与定位,亦能导向多个工作台,可大大提高激光的使用率和处理的效率。 7)激光表面处理尤其适用于大批量处理生产线,其成本比传统的表面热处理低。 2 激光表面相变应化(LTH)
表面处理
表面处理--- 除锈程度 ISO8501-1:1988 锈蚀等级(Rust Grades) A:钢表面完全被粘附的氧化皮覆盖,极少量或无可见锈B:钢表面被氧化皮和锈覆盖 C:钢表面完全被锈覆盖,极少量或无可见点蚀 D:钢表面完全被锈覆盖,可见点蚀 除锈程度 Sa : 喷砂除锈 Sa1/Sa2/Sa2.5/Sa3(SSPC SP7/SP6/SP10/SP5) St : 手工或动力工具除锈 St2 / St3 Fl : 火焰清洁 AFl/BFl/CFl/DFl ISO8501-2 --- 已有涂层表面的表面处理等级 P Sa : 已有涂层表面局部彻底的喷砂处理 P Sa2/P Sa2.5/P Sa3 P St : 已有涂层表面局部手工和动力工具处理 P St2/P St3 P Ma : 已有涂层表面局部机械打磨处理 P Ma 下列国家标准,涉及了防腐蚀的各种要求: GB8923 涂装钢材表面锈蚀等级和除锈等级(相对国际标准ISO 8501-1:1988) GB6060.5 表面粗糙度比较样板抛(喷)丸、喷砂加工表面(相对国际标准.ISO8503-2 :1995)GB6484 铸钢丸 GB6485 铸钢砂 GB/T13312 钢铁件涂装前除油程度检验方法(验油试纸法) HG/T 3656 钢结构桥梁漆 JB/Z350 高压无气喷涂典型工艺 GB1764 漆膜厚度测定法 GB/T 5210 涂层附着力的测定法,拉开法 GB/T 1771 色漆和清漆耐中性盐雾性能的测定(相对国际标准ISO 7253:1984) GB/T 1865 色漆和清漆人工气候老化和人工辐射曝露(相对国际标准ISO 11341:1994) GB/T1740 漆膜耐湿热测定法 GB7692 涂装作业安全规程涂漆前处理工艺安全 GB6514 涂装作业安全规程涂漆工艺安全 GB/T15957-1995 大气环境腐蚀性分类 石油行业标准 SYJ0004-1999 钢质管道及储罐防腐蚀工程设计规范 SY4058-93 埋地钢质管道外防腐层和保温层现场补伤施工及验收规范 SY/T0007-1998 钢质管道及储罐腐蚀控制工程设计规范 SY/T0063-99 管道防腐层检漏试验方法 SY/T0087-95 钢质管道及储罐腐蚀与防护调查方法标准 SY/T0407-1997 涂装前钢材表面预处理规范
铜箔表面处理技术
铜箔表面处理技术 https://www.360docs.net/doc/4d10005539.html, 发布日期: 2006-12-30 阅读: 3058 字体:大中小双击鼠标滚屏 表面处理是铜箔生产的一个重要环节,它包括对铜箔进行粗化层处理、耐热层处理及防氧化层处理等。其中前二者是在原箔毛面上进行的,而防氧化层处理则是在原箔两面上进行,三个方面处理则在同一台表面处理机上分步骤连续完成。 1.表面处理一般工艺过程 目前国内外各铜箔生产企业所采用的铜箔表面处理工艺区别相当大,工艺流程不同,工艺参数也不同,但是应该说都包含粗化、耐热、防氧化三种处理。一般来说,铜箔表面处理的工艺过程可以归纳为: 2.预处理 预处理是指对原箔表面进行的清洗,去除氧化及对表面进行浸蚀的过程,原箔在制箔机生产后有较短的存放过程,表面很容易产生氧化层,这是在进行粗化处理前必须去除的。另外,某些处理(如对原箔光面进行粗化处理)前,须要对其表面进行必要的浸蚀处理。这些都需要对原箔进行预处理,预处理一般采用硫酸、双氧水等水溶液或其混合水溶液。 3.粗化层处理 为使铜箔与基材之间具有更强的结合力,需要对原箔的毛面(与基材结合面)进行粗化层处理,它包括粗化和固化两个过程。在粗化层处理过程中,需要使电解液控制较低的含铜量及较高的含酸量,通过电解作用,在铜箔毛面(阴极)发生铜沉积,在表面形成牢固的粒状和树枝状结晶并且有较高展开度的粗糙面,达到高比表面积,这就加强了树脂(基材上的树脂或铜箔粘合剂树脂)渗入的附着嵌合力,还可增加铜与树脂的化学亲和力。 一般的粗化处理都采用酸性电解工艺方式,即原箔为阴极,在硫酸铜的电解液中进行几次电沉积,通过控制不同的工艺条件(电解液浓度不同,电流密度不同)来对铜箔表面进行粗化及固化处理,使铜箔表面生产松散的瘤体,然后进行固化,使粗化瘤体被正常的铜镀层所包围及加固,使粗化层与铜箔基体结合牢固,形成最终的粗化层。 对于电解铜箔来说,铜箔厚度不同以及使用用途的不同,均要求铜箔表面粗化层也不同,有的需要高峰值粗化层,有的需要低峰值粗化层,这就要求铜箔生产过程需要采用不同工艺条件的表面粗化工艺来实现。 4.耐热层处理 耐热层处理的主要目的是为了提高铜箔压制覆铜板及多层板后的耐热性及高温抗剥强度。这是因为电路板在整机元器件装配焊接时,由于受到高温影响,其树脂中的固化剂双氰胺容易裂解产生胺类物,它与裸铜表面相接触,将发生反应而可能出现水分,进而汽化,引起气泡产生,使铜箔与基板分离。
SSPC表面处理标准对照表
附录A SSPC表面处理标准 ? SP-1 溶剂清洗 ? SP-2 手工工具处理 ? SP-3 机动工具处理 ? SP-4 燃烧处理 ? SP-5 彻底喷砂(白金属) ? SP-6 中度喷砂(商用) ? SP-7 轻度喷砂(普通) ? SP-8 浸酸(化学处理) ? SP-9 风化后再以钢丝刷打磨 ? SP-10 彻底喷砂(接白) ? SP-11 机动工具处理至金属表层完全光泽暴露? SP-12 高压水喷射 ? SP-13 混凝土表面处理 ? SP-14 工业喷砂 附录B 表面处理等级 起始锈蚀程度:(图示从左至右分别为B、C、D)? 等级A 氧化层紧密附着于表面 ? 等级B 氧化层开始锈蚀 ? 等级C 氧化层已经锈蚀 ? 等级D 氧化层严重锈蚀,出现麻点
轻度喷砂: 商用喷砂: 近白喷砂: 白金属喷砂: 附录C 国际通用表面处理标准对比
钢结构油漆委员会Steel Structure Painting Council (SSPC) 国家防腐工程师协会National Association of Corrosion Engineers (NACE) 英国标准ISO 8501-1 / BSI BS 7079 瑞典标准Swedish Standard 国标GB-3092 / GB-8923-88
关于表面处理等级 1994年10月,NACE和SSPC发布了用于磨料清理的联合表面处理标准(这些标准大约相当于由最初的瑞典标准发展而来的ISO标准ISO8501-1SO-公布于1988年: NACE NO.I/SSPC-SP5“金属出白级喷砂” 相当于—Sa3“喷砂至可见清洁金属” NACE NO.2/SSPC-SP10“金属近于出白级喷砂” 相当于—Sa21/2“非常彻底的喷砂清理” NACE NO.3/SSPC-SP6“工业级喷砂” 相当于—Sa2“彻底的喷砂清理” NACE NO.4/SSPC-SP7“刷除锈级喷砂” 相当于—Sa1“轻喷砂清理” SSPC-SP1“溶剂清理” SSPC-SP2“手动工具清理” SSPC-SP11 “动力工具清理至裸钢” SSPC-SP8“酸洗” SSPC-SP3“动力工具清理” SSPC-SP11R “动力工具清理维修保养” 一、金属 (1) 新表面 A.钢铁 1.喷砂处理 实践证明,无论是在施工现场还是在装配车间,喷砂处理都是除去锻痕的最有效方法。这是成功使用各种高性能油漆系统的必要处理手段。喷砂处理的清洁程度必须规定一个通用标准,最好有标准图片参考,并且在操作过程中规定并控制表面粗糙度。表面粗糙度取决于几方面的因素,但主要受到所使用的磨料种类及其粒径和施力方法(如高压气流和离心力)的影响。对于高压气流,喷嘴的高压程及其对工件的角度是表面粗糙度的决定因素;而对于离心力或机械喷射方法来说,喷射操作中的速率是非常重要的。喷砂处理完成后必须立即上底漆。所有油脂及污染物必须在上漆前清除。 2.湿喷砂或砂洗 这种方法是使用砂浆及高压水来除去旧漆、锻痕及蚀物。使用这种方法,极大程度上克服了普通喷砂处理中粉尘对健康的危害。同样,表面粗糙度及清洁效率取决于水压及砂浆中磨料的浓度。 这种处理方法的一个主要缺点是清洁好的钢铁表面将立即开始生锈,因此与普通喷砂处理比较,表现出一种较次的表面。要在水中加入阻锈剂但必须十分小心,因为有些阻锈剂会影响随后漆膜的性能。 3.车间预上底钢结构 在车间经过自动喷砂处理并在装配前预上底漆的钢结构,在施以最后的保护性油漆系统前,通常需要进行特殊处理。所有损伤区域,会继续生锈,这些区域必须被重新喷砂处理,或用手工方法彻底清洁至可接受的标准。在施以高性能油漆体系前,通常需要重新喷砂处理,这需要在所有可能的场合做具体的规定。这种处理方法也通常用于焊接及焊接前无法上底漆的钢结构连接部分。 4.酸洗清洁酸洗清洁 是一种古老的车间处理方法,用于除去钢铁的锻痕。目前仍有几个步骤在被使用,通常为一个双重体系包括酸腐蚀及酸钝化。
常见表面处理技术介绍
常见表面处理技术介绍 电镀(电沉积) 化学镀阳极氧化(铝, 镁, 钛及它们的合金 化学氧化(铝及其合金,钢铁等等) 电化学及化学转化学铬酸监处理(钢铁上的锌,铬镀层,铝, 镁, 铜) 磷酸监处理(磷化) 热浸镀(常用的有热浸锌, 锡, 铝, 铅) 火焰喷涂 气喷涂 爆炸喷涂 热濆涂电弧喷涂 电濆涂等离子喷涂 高频感应喷涂 橡胶涂层 非金属涂覆塑料涂层 油漆涂层 渗镀 化学气象沉积 扩散涂镀真空镀膜 包镀 达克罗(Dacromet,浸入锌–铝,锌–铝等浆液中,形成涂层,然后烘烤干燥成膜) 1.磷酸监皮膜处理 大陆称为磷化处理 1.1磷酸监皮膜处理 2H3PO4+M→M(H2PO4)+H2 3M(H2PO4)2→4H3PO4+M3(PO4)2 M(H2PO4)2→MHPO4+H3PO4 生成的M3(H2PO4)2和MHPO4为磷酸监膜的主要成分 1.2磷酸监皮膜的性质和用途 (1)耐蚀性 在大气条件下很稳定,在有机油类,苯,苯及各种气种体燃料中有很好的耐蚀性.但磷酸监皮膜不耐酸,碱,
氨,海水及水蒸气等.磷酸监膜经过封闭处理后能大大提高其耐蚀性. (2)吸附性 磷酸监膜具有多孔构,有很好的吸附性,因此常用作油漆的底层和吸附润滑油后作为减摩层和润滑层. (3)电绝缘性 磷酸监膜是高电阻膜层,有很好的电绝缘性,击穿电压为240~250V,涂绝缘漆后可耐1000~1200V,又由于磷酸监膜不影响透磁性,因此常用作电磁装置的硅钢片. (4)不粘附熔融金属的特性 此特性用于在热浸锌,锡铅合金时保护不需要浸涂部分.在浇铸减摩合金和电机铸铝转子时,将钢膜作磷酸监处理,以防粘附. 1.3邻酸监膜成机理和构成 1.4分类 钢铁用化成处理剂 铝用化成处理剂 锌用化成处理剂 不锈钢用化成处理剂 铜用化成处理剂 镁用化成处理剂 其他化成处理剂 涂装打底用的化成处理剂 塑性加工用化成处理剂 防锈用化成处理剂 耐磨用化成处理剂 绝缘用化成处理剂 塑料迭片用化成处理剂 涂装打底用皮膜特点: 致密, 均匀, 薄得适当 结晶粗大会吸入涂料而减少光泽:不均匀会降低涂装后的耐蚀性;由于磷酸监膜很硬很脆,皮膜过厚的话,涂装后遭后到弯曲或冲击等外力时,即使别无缺陷,也可能脱落. 防锈用皮膜特点: 致密, 均匀, 厚度越厚越好,孔隙率越低越好. 表
表面处理工艺规程
工艺规程 文件编号:HD/GYGC2015-019 工艺类别:表面处理(通用) 编制: 校对: 审核: 批准: 生效日期凌海航达航空科技有限公司
目录 1. 总体要求........................................................ (2) 2. 目的........................................................ .. (2) 3. 适用范围........................................................ (2) 4. 产品概述........................................................ (3) 5. 依据........................................................ .. (3) 6. 工序级别定义........................................................ . (3) 7. 所用主要设备........................................................
(3)
8. 工艺流程........................................................ (3) 9. 检验定义........................................................ (3) 10. 工作记录........................................................ . (3) 11. 具体工艺要求........................................................ .. (4) 12. 工艺重要关联与补充........................................................ .. (6) 附录 《生产工艺&过程检验卡》(PM-QCP-006-01)——表面处理
铜箔生产线设备说明(MFN-01)
铜箔生产线设备说明(MFN-01) 1、生箔机 生箔机主要由阳极槽体、进液流量分配装置、阴极辊驱动装置、阴极辊导电装置、阴极辊、“O”形圈循环装置、边部密封装置、辅助阴极装置、张力控制装置、清洗装置、烘干装置、收卷装置、酸气水汽收集罩和防护罩、电气设备和控制系统等组成。主要用于铜箔毛箔的生产。 生箔机的工作原理:由阴极辊和生箔机组成生箔机组。阳极槽体接电源的正极,阴极辊接电源的负极,当硫酸铜电解液进入阳极槽体后,正负极间形成电场,在电场作用下,铜离子向阴极辊表面迁移并沉积,沉积出来的铜很薄,从阴极辊上剥离并收卷在另外一只辊子上,这样电解液连续不断的循环,铜离子在电场作用下源源不断向阴极辊沉积,连续剥离并收在收卷轴上。其余“O”形圈循环装置、边部密封装置、辅助阴极装置、张力控制装置、清洗装置、烘干装置、收卷装置、阴极辊电气设备和控制系统等均是为了保证铜箔质量要求及连续生产可靠性而设置的必要装置。 2、阴极辊 阴极辊为钢钛铜复合辊,是生箔机组的一个部件,一台生箔机组对应装配一个阴极辊。由辊体、导电环、轴承、PVC挡板及固定钛螺栓、链轮、轴承等组成。 阴极辊的工作原理:阴极辊作为电源的负极的导电体,要
将电源在阴极辊面分布均匀,这样铜离子就会均匀地沉积在阴极辊表面,同时阴极辊表面必须按照电解铜箔质量的要求研磨成特定的表面形状(需用阴极辊磨辊机及阴极辊在线抛光装置),以确保铜箔的质量。 3、电子铜箔用表面处理机 表面处理机主要由放卷装置、张力控制装置、速度控制装置、动力系统、导电系统、喷洗干燥装置、有机耦联剂喷淋装置、放收卷位置调节装置、液下辊传动密封装置、收卷装置、安全/防护装置、电气设备和控制系统、机架及电解水洗槽等组成。工作任务是处理生箔机生产的毛箔,目的是为了提高铜箔的抗剥离强度、抗氧化等性能。电子铜箔用表面处理机需和生箔机组连续工作,不可分割,否则毛箔会被氧化。 工作原理:生箔机生产出来的铜箔称为原箔或毛箔,并不能满足下游生产需要,必须通过在毛箔的表面进行电镀处理,通过镀铜、镀锌及镀铬来提高毛箔的各种性能指标,如抗剥离性能指标,抗氧化性能指标等。 4、阴极辊磨辊机和阴极辊在线抛光装置 阴极辊磨辊机主要由基础框架、轴承座支架、轴承座、主驱动装置、气动装置、冷却液装置、接液装置、控制系统、操作平台、电缆及风管、液管移动支架等组成。阴极辊在线抛光装置由基础框架、轴承座支架、轴承座、主驱动装置、抛光辊驱动装置、抛光辊摆动装置、抛光辊调节装置,抛光辊气缸压紧装置、
对压延铜箔的认识与思考
对压延铜箔的认识与思考 压延铜箔在当今的电子信息技术这块上面的应用可谓是显得越来越重要了,主要是在于其能够满足当今不断发展的电子技术上的要求,在现在其铜箔制造的相关领域上的电解铜箔占统治地位的基础之上,又需要重视压延铜箔了,压延铜箔相对于电解铜箔来说主要就是在生产工艺及成本,在生产技术水平及难度上面目前还是处于一种比较空白和靠前的,目前国内能够生产压延铜箔并且具备先进的技术水平的企业还很少,或者说处于起步的阶段,根本不能够满足目前国内兴起的电子信息技术行业的需求,也有一些企业同高校之间的联合从技术上去争取取得突破,如今年4月份广源铜带股份有限公司与北京科技大学在压延铜箔方面的签约合作研究,属于尖端靠前的研究领域,在电子信息技术发展前提下,其应用显得越来越重要与不可替代性,目前在压延铜箔这块的产品也基本上一处于依赖进口的现状,而且价格十分昂贵,压延铜箔生产方面的相关技术国外严格保密,在国内比较的研究比较缺乏的基础之上也引起了国家科技发展部的高度重视,在其公布的铜加工行业科技“铜材短流程生产关键技术开发与工程化”项目中就包含了压延铜箔方面的这个课题,说明此生产技术的发展和研究是很重要的。 当今在铜箔的生产制造与加工的这一块,日本和美国的生产技术水平是最领先的,特别是日本,有一定的历史研究基础和实力,在东亚地区其他国家也有相关的的发展,国内主要是随着经济的发展以来带动的电子信息技术发展的需要而发展起来的,这是当今世界铜箔的发展的其相关外部环境,整体上也还是以电解铜箔为主,压延铜箔为补充的基本格局,在覆铜板最初的生产时期,世界上大多数都是使用压延铜箔。发展到20世纪60年代末至70年代初,由于它在幅宽(目前可工业化生产的最大宽度在550— 800mm范围内)上难于满足大面积覆铜板生产的需要,且在成本上也较高,因此目前在刚性覆铜板的生产中,开始不再大批量采用压延铜箔,而是采用电解铜箔,在电解铜箔的开发一来,由于之前的压延铜箔生产的技术落后与成本及生产工艺及幅宽的因素而逐渐被电解铜箔替代了。而压延铜箔由于其自有的特性在电子技术发展的今天其重要性又凸显了出来,引起重视,是一个值得去研究和开发的领域。 压延铜箔按化学式可以分为电子管用无氧铜箔,无氧铜箔和紫铜箔,以及添加有微量元素的耐蚀合金铜箔和耐热性合金铜箔。紫铜箔的用途主要是用于柔性印制电路板,纸板电路印刷板,电磁屏蔽带,复合扁电缆,绕组和锂电池的层电极等。在本课题下根据生产规划及目标与任务,主要是针对于紫铜箔及其存在的相关技术问题与分析。 要生产与现代的电子技术相适应的压延紫铜箔,弥补电解铜箔在高频信息传输与精细线路及挠性印制电路领域的空缺,其在生产技术上面遇到的主要关键问题就应该包括如下几个方面:
表面处理技术汇总
第一章金属材料 SPCC 一般用钢板,表面需电镀或涂装处理 SECC 镀锌钢板,表面已做烙酸盐处理及防指纹处理 SUS 301 弹性不锈钢 SUS304 不锈钢 镀锌钢板表面的化学组成------基材(钢铁),镀锌层或镀镍锌合金层,烙酸盐层和有机化学薄膜层. 有机化学薄膜层能表面抗指纹和白锈,抗腐蚀及有较佳的烤漆性. SECC的镀锌方法 热浸镀锌法: 连续镀锌法(成卷的钢板连续浸在溶解有锌的镀槽中 板片镀锌法(剪切好的钢板浸在镀槽中,镀好后会有锌花. 电镀法: 电化学电镀,镀槽中有硫酸锌溶液,以锌为阳极,原材质钢板为阴极. 1-2产品种类介绍 1.品名介绍 材料规格后处理镀层厚度 S A B C*D*E S for Steel A: EG (Electro Galvanized Steel)电气镀锌钢板---电镀锌 一般通称JIS 镀纯锌EG SECC (1) 铅和镍合金合金EG SECC (2) GI (Galvanized Steel) 溶融镀锌钢板------热浸镀锌 非合金化GI,LG SGCC (3) 铅和镍合金GA,ALLOY SGCC (4) 裸露处耐蚀性2>3>4>1
熔接性2>4>1>3 涂漆性4>2>1>3 加工性1>2>3>4 B: 所使用的底材 C (Cold rolled) : 冷轧 H (Hot rolled): 热轧 C: 底材的种类 C: 一般用 D: 抽模用 E: 深抽用 H: 一般硬质用 D: 后处理 M: 无处理 C: 普通烙酸处理---耐蚀性良好,颜色白色化 D: 厚烙酸处理---耐蚀性更好,颜色黄色化 P: 磷酸处理---涂装性良好 U: 有机耐指纹树脂处理(普通烙酸处理)--- ---耐蚀性良好,颜色白色化,耐指纹性很好A: 有机耐指纹树脂处理(厚烙酸处理)---颜色黄色化,耐蚀性更好 FX: 无机耐指纹树脂处理---导电性 FS: 润滑性树脂处理---免用冲床油 E: 镀层厚 1-4物理特性 膜厚---含镀锌层,烙酸盐层及有机化学薄膜层,最小之膜厚需0.00356mm以上. 测试方法有磁性测试(ASTM B499), 电量分析(ASTM B504), 显微镜观察(ASTM B487) 表面抗电阻---一般应该小于0.1欧姆/平方公分. 1- 5 盐雾试验----试片尺寸100mmX150mmX1.2mm, 试片需冲整捆或整叠铁材中取下,必须在镀烙酸盐后24小时,但不可超过72小时才可以用于测试,使用5%的盐水,用含盐的水汽充满箱子,试片垂直倒挂在箱子中48小时。 测试后试片的镀锌层不可全部流失,也不能看到底材或底材生锈,但是离切断层面6mm范围有生锈情况可以忽略。
铜箔表面处理机操作说明书
铜箔处理机电气控制系统操作说明书 一、控制系统功能和组成: 1.处理机电气控制系统由:放卷部分、中间处理槽部分(14个槽,7台电机)、加热烘箱、收卷部分组成。 装置有:主控制柜3个、收卷操作台、中间操作盒、放卷操作台、机列中继盒等组成。 2.放卷部分、收卷部分是分别由:张力检测器(LX-200TD)、张力放大器(LM-10TA)、PLC运算、电机构成的全自动张力控制系统。分别控制放卷、收卷的张力,保证材料以设定张力值运行。 3.中间机列分为7段张力控制,其中1号槽电机控制整机的线速度,其他6台电机分别控制6段张力,每段张力由张力传感器、张力放大器、PLC 运算输出构成闭环全自动张力控制系统。 4.控制台和操作盒:收卷、放卷、中间操作台分别装有操作按钮和触摸屏,不同位置的相同功能的操作按钮的优先级是同等的,触摸屏的操作优先级也是同等的,也就是说操作者无论在哪个位置操作机器,操作权都是同等的。操作台上安装自动、手动、停车按钮和对应的指示灯,另外还有:正转/反转选择开关、联系警铃按钮、急停按钮等。 5.整个系统可以控制材料按照设定张力和速度稳定运行,通过停止按钮停止运行,可以通过收/放卷的正/反转开关和运转启/停按钮实现收放卷的单独运转,可通过触摸屏手动运行画面实现每一个电机的单独运行或任选多个电机的联动运行。 二、操作台的功能和操作方法: 1.自动按钮:按自动按钮,收卷、放卷、机列电机启动,并按照设定张
力值自动控制各段材料的张力,张力值和线速度值可以在自动运行的过程中修改。 2.停车按钮:无论在什么状态按下停止按钮,机器将停止运行,整机在断电重接通电源时都在停止状态。注意:在紧急情况下要求机器立即停机,请不要使用停止按钮,请使用急停按钮。 3.手动按钮:手动按钮按下时机器转到手动状态运行,进入手动运行状态后,可在触摸屏上选择需要运转的电机,并可以选择联动正传或联动反转,也可以单独操作任意几个电机的正反转。 4.收卷(放卷)运行/停止按钮:在手动操作状态,按一次这个按钮可改变收卷(放卷)电机的运转和停止状态。 5.收卷(放卷)正/反转开关:在手动操作模式下,选择收卷(放卷)电机的运转方向,在电机运转时不用将电机停止,也可以改变开关状态。 6.急停按钮:紧急情况下按急停按钮,机器立即停止。 三、触摸屏的操作方法 触摸屏分为:主画面、“张力设定”画面、“手动模式”画面、“参 数I”画面等。 1.主画面是正常运行时监控画面,可监视和控制:收卷、放卷、机列槽的张力值,线速度值,材料走料长度累计值。控制泵、加热、风机的开/关。只有白色数据框可以手动修改,其他数据框只能监视用,数据无法修改。
铜箔资料
铜箔资料 铜箔是制造印刷电路板的关键导电材料,按照不同的制造工艺可分为电解铜箔和压延铜箔两大类 (1)压延铜箔(Rolled Copper Foil) 是将铜板经过多次重复辊轧而制成的原箔(也叫毛箔),根据要求进行粗化处理。由于压延铜箔加工工艺的限制,其宽度很难满足刚性覆铜板的要求,所以压延铜箔在刚性覆铜箔板上使用极少。由于压延铜箔耐折性和弹性系数大于电解铜箔,故适用于柔性覆铜箔板上。 (2)电解铜箔(Electrode Posited copper)是将铜先经溶解制成溶液,再在专用的电解设备中将硫酸铜电解液在直流电的作用下,电沉积而制成原箔,然后根据要求对原箔进行表面处理、耐热层处理及防氧化处理等一系列的表面处理。电解铜箔不同于压延铜箔,电解铜箔两面表面结晶形态不同,紧贴阴极辊的一面比较光滑,称为光面;另一面呈现凹凸形状的结晶组织结构,比较粗糙,称为毛面。电解铜箔和压延铜箔的表面处理也有一定的区别。由于电解铜箔属柱状结晶组织结构,强度韧性等性能要逊于压延铜箔,所以电解铜箔多用于刚性覆铜板的生产,进而制成刚性印制板。 主要生产商:三井金属,日矿材料,福田金属、古河电工等日商,再有韩国日进金属;长春、南亚塑胶,circuit foil,积德集团,金居开发铜箔(台湾) 国内:建滔化工集团公司、上海金宝铜箔有限公司,广东梅县梅雁电解铜箔有限公司,灵宝华鑫铜箔,招远金宝电子有限公司,咸阳电子
材料厂,西北铜加工厂铜箔,中科英华高科技股份有限公司,九江福莱克斯有限公司
项目一:广东超华年产8000吨高精度电子铜箔工程(电解),该项目占地面积13566平方米,总投资5亿元,年销售收入
表面处理技术标准
表面处理技术标准 厦门盈趣科技股份有限公司
目录 1 范围.............................................................................. (3) 2 规范性引用文件 (3) 3 定义.............................................................................. . (4) 4 材料.............................................................................. . (4) 5 表面处理盐雾试验的要求 (4) 6 铜合金电镀表面处理标准....................................................... 5-6 7 锌合金/铝合金电镀表面处理标准...........................................6-7 8 塑料电镀表面处理标准............................................................ 7-8 9 不锈钢电镀表面处理标准..........................................................8-9 10 烤漆表面处理标准............................................................... ….9-11 11 PVD 表面处理标准............................................................... ..11-12 12 铝合金阳极氧化表面处理标准................................................12-13 13 CASS 试验(醋酸铜盐雾试验)与ASS 试验(乙酸盐雾试验)等效对照表 (14) 附录A 百格试验方法 (15) 附录B 漆膜铅笔硬度试验方法 (16)
压延铜电解铜区别
它们使用在FPC中有何区别?谢谢! 最佳答案 电解铜顾名思义就是通过电解的方法使铜离子吸附在基材上而形成铜箔,所以它的特点是,导电性强,但耐弯折度相对较弱 压延铜是通过挤压的方法得到铜箔,它的特点是耐弯折度好,但导电性弱于电解铜,主要用于翻盖手机里的摄像头之类的 从外观上看,电解铜发红,压延铜偏黄 解析挠性电路板压延,电解,高延展电解材料 众所周知,在挠性电路板制作工艺中,选材相当重要,从材料厚度,可焊性,熔点,导电性,阻焊等各方面都有很具体的要求,在这里我们重点讲到铜箔的选择。 一,挠性电路板用的铜箔材料主要分为压延铜(RA)和电解铜(ED)两种,他是粘结在覆盖膜绝缘材料上的导体层,经过各制程加工等蚀刻成所需要的图形。选择何种类型的铜材做为挠性电路板的导体,需要从产品应用范围及线路精度等方面考量。从性能上比较,压延铜材料压展性,抗弯曲性要优于电解铜材料,压延材料的延伸率达到20-45%,而电解铜材料只有4-40%。但电解铜材料是电镀方法形成,其铜微粒结晶结构,在蚀刻时很容易形成垂直的线条边缘,非常利于精细导线的制作,另外由于本身结晶排列整齐,所形成镀层及最终表面处理后形成的表面较平整。反之压延材料由于加工工艺使层状结晶组织结构再重结晶,虽压展性能较好,但铜箔表面会出现不规则的裂纹和凹凸不平,形成业界里面的铜面粗糙问题。针对电解材料的缺点材料供应商研发了高延电解材料,就是在常规加工过后将材料再次进行热处理等工艺使铜原子重结晶,使其达到压延材料所拥有的特性。 二,电解铜,压延铜材料加工工艺:电解铜箔是通过酸性镀铜液在光亮的不锈钢辊上析出,形成一层均匀的铜膜,经过连续剥离,收卷而获得;压延铜箔则是用一定厚度(20cm)的铜锭或铜块,经过反复压延,退火加工形成所需要的铜箔厚度。 三,铜箔材料的微观结构:因加工艺不一样,在1000倍显微镜下观察材料断面,压延材料铜原子结构呈不规则层状强晶,对经过热处理的重结晶,所以不易形成裂纹,铜箔材料弯曲性能较好;而电解铜箔材料在厚度方向上呈现出柱状结晶组织,弯曲时易产生裂纹而断裂;同样,在经过热处理等特殊加工的高延电解铜箔材料断面观察时,虽还是以柱状结晶为主,但在铜层中以形成层状结晶,弯曲时也不易断裂。见以下示意图。 压延铜箔材料断面示意图电解铜箔材料断面示意图
金属热处理及表面处理工艺规范
北京奇朔科贸有限公司 部分金属材料热处理及表面处理工艺规范 第一版 编写:赵贵波 审核: 批准: 北京奇朔科贸有限公司 二零一二年六月
目录 1.0 热处理的工艺分类及代号---------------------------------------------------------------------3 1.1 基础分类-----------------------------------------------------------------------------------------------3 1.2 附加分类-----------------------------------------------------------------------------------------------3 1.3 热处理工艺代号--------------------------------------------------------------------------------------4 1.4 图样中标注热处理技术条件用符号--------------------------------------------------------------7 2.0 金属材料的热处理方法和应用目的-------------------------------------------------------8 2.1 钢的淬火-----------------------------------------------------------------------------------------------8 2.2 热处理的过程方法和应用目的--------------------------------------------------------------------9 3.0 部分金属材料的热处理规范-----------------------------------------------------------------17 3.1 渗碳钢的热处理工艺--------------------------------------------------------------------17 3.2 渗氮钢的热处理工艺--------------------------------------------------------------------------------20 3.3 调质钢的热处理工艺-------------------------------------------------------------------------------21 3.4 -弹簧钢的热处理工艺------------------------------------------------------------------------------23 3.5 轴承钢的热处理工艺-------------------------------------------------------------------------------25 3.6 合金工具钢的热处理工艺------------------------------------------------------------------------- 26 3.7 碳素工具钢的热处理工艺--------------------------------------------------------------------------29
超低轮廓压延铜箔表面处理生产工艺研究
第46卷第2期 2018年1月广 州 化 工 Guangzhou Chemical Industry Vol.46No.2 Jan.2018 超低轮廓压延铜箔表面处理生产工艺研究 陈 宾,王海军,张春阳 (中色奥博特铜铝业有限公司,山东 临清 252600) 摘 要:低轮廓铜箔具有直流电阻小二介电常数小特点,尤其是在高频高速信号传输中,存在趋肤效应的现象,导体内部的电流的不均匀,电流趋向在导体表面富集,频率越高趋肤效应越强,导致损耗越大三重点从压延铜箔表面处理粗化的工艺(电流密度二铜离子浓度二溶液温度二添加剂)等方面进行研究,以实现铜箔毛面粗糙度降低(Rz≤1.5),同时保证铜箔抗剥离强度(≥ 0.8N/mm)满足基板的需求,从而保证终端电子产品的可靠性三 关键词:电流强度;温度;粗糙度;抗剥离强度 中图分类号:TG178 文献标志码:A 文章编号:1001-9677(2018)02-0026-03 Study on Production Process of Surface Treatment of Ultra Low Profile Rolled Copper Foil CHEN Bin,WANG Hai-jun,ZHANG Chun-yang (CNMC Albetter Albronze Co.,Ltd.,Shandong Linqing252600,China) Abstract:Low profile copper foil has the characteristics of small direct current resistance and small dielectric constant.Especially in the high-frequency and high-speed signal transmission,there exists the phenomenon of skin effect,the uneven current in the conductor,the current tends will be concentrated on the conductor surface.The higher the frequency,the stronger the skin effect,results in greater loss.The roughening process(current density,copper ion concentration,solution temperature,additives)of rolled copper foil surface were focused on in order to reduce the roughness of copper foil matte surface(Rz≤1.5)Peel strength(≥0.8N/mm)to meet the needs of the substrate,so as to ensure the reliability of the terminal electronic products. Key words:current strength;temperature;roughness;peel strength 近年全球信息技术向数字化二网络化的迅速发展,超大容量的信息传输,超快速度及超高密度的信息处理,且终端电子产品向超薄二超轻发展,成为信息及通讯设备技术发展所追求的目标三这些目标的实现对系统设计二终端产品加工二PCB (FPC)二CCL(FCCL)二铜箔的制造等,等都提出了较大的挑战[1]三实现基板的信号高传输二低损失从基板材料角度上讲,它需要的成分构成主要为:树脂二玻纤布(木浆纸)二填料二铜箔三考虑到高频电路会产生 趋肤效应”影响,为减少信号传输损失,低粗糙度铜箔应用于越来越广泛三低轮廓铜箔具有直流电阻小二介电常数小特点,尤其是在高频高速信号传输中,传输线受到变频场的作用,存在趋肤效应的现象,导体内部的电流的不均匀,电流趋向在导体表面富集,频率越高趋肤效应越强,导致损耗越大三所以,发展低轮廓铜箔也是一种趋势,高速覆铜板普遍采用低轮廓铜箔或超低轮廓铜箔甚至是平滑铜箔三铜箔表面的粗糙度(Rz)越小所构成基板的传输损失就越小,越是高频这种对应关系就越凸显三但采用这种铜箔所带来的负面效应也特别明显如:抗剥离强度的减低二PCB加工性能变差二可靠性降低三所以兼顾铜箔低粗糙度二高抗剥性能成为铜箔制造技术的关键三1 粗化面沉积过程 电镀结晶过程实际上是金属的电结晶过程,在形成金属晶 体的同时进行着晶核生成及生长的过程,这两个过程的速度决 定了金属结晶的粗细程度三在电镀过程中当晶核的生成速度大 于晶核的成长速度就能获得结晶细致二排列紧密的镀层,晶核 生成的速度大于晶核成长速度的程度越大,镀层结晶越细致紧 密,相反晶核的成长速度大于晶核的生成速度结晶就会粗 大[1-2]三实践证明:提高金属电结晶时的阴极极化作用可提高晶核的生成速度,使铜箔毛面结晶细致紧密三但阴极极化作用 不是越大越好,当超过一定范围时,会导致氢气的大量析出, 从而使镀层变得多空二粗糙二疏松二甚至呈现粉末状(铜箔生 产表面处理的粗化过程就是此现象)质量反而下降[3-4]三因此如何把控电镀过程中阴极极化在合适的范围之内,从而得到较为细致紧密的镀层,就需要对影响阴极极化的条件做出研究三在已知的影响阴极极化的主要条件为:溶液的成分浓度二溶液的温度二电流密度二溶液的添加剂[5]三通过实验分别固定其中的三项数据(实际经验值)改变其中的一项数据进行试验,对实验数据(抗剥离强度二粗糙度)进行比对,以得出兼顾两者性能的最优化结果(保证抗剥离强度的前提下粗糙度最低)三
图纸上的技术要求汇总知识分享
图纸上的技术要求汇 总
图纸技术要求 一、一般技术要求 制件去除表面氧化皮; 制件不得有划痕、擦伤等损伤零件表面的缺陷; 去除毛刺飞边; 锐角倒钝; 未注倒角均为0.5×45%%d; 未注越程槽均为1.2×0.3; 表面平整无毛刺; 二、未注公差技术要求(金属件) 未注公差尺寸的极限偏差按GB/T 1804-m; 未注形位公差按GB/T 1184-K; 未注长度尺寸允许偏差±0.5; 三、表面处理技术要求 表面镀白(黑)锌处理; 表面喷漆(喷塑)处理; 表面发黑处理; 表面电泳处理; 表面镀铬处理; 表面抛光处理; 表面滚花,直纹(网纹)m=0.4 GB/T 6403.3; 四、热处理技术要求
制件氮化450-480HV; 制件毛坯须调质处理220-260HB; 制件调质处理30-35HRC; 制件高频淬火45~50HRC; 制件渗碳处理,深度>0.1; 制件进行高温回火处理; 制件整体淬火40-45HRC; 五、铸件技术要求 1、压铸件技术要求 未注公差尺寸的极限偏差按GB/T 1804-m; 未注形位公差按GB/T 1184-K; 未注倒角均为0.5×45%%d; 未注壁厚2.5;未注筋板1.5~2; 未注过渡圆角R0.5-R2;未注脱模斜度≤1%%d; 制件饱满光洁、无气孔、缩松、裂纹、夹渣、缺料等缺陷; 各脱模顶料推杆压痕均应低于该制件表面0.2; 制件要求符合GB/T 15114《铝合金压铸件》标准规定; 表面喷漆(喷塑)处理,不得污染到已加工表面; 加工表面在表面处理后加工,加工后涂油保护; 未注尺寸参照三维造型; 制件表面处理及其它要求按客户定; 2、砂型铸造技术要求