锻件尺寸检验
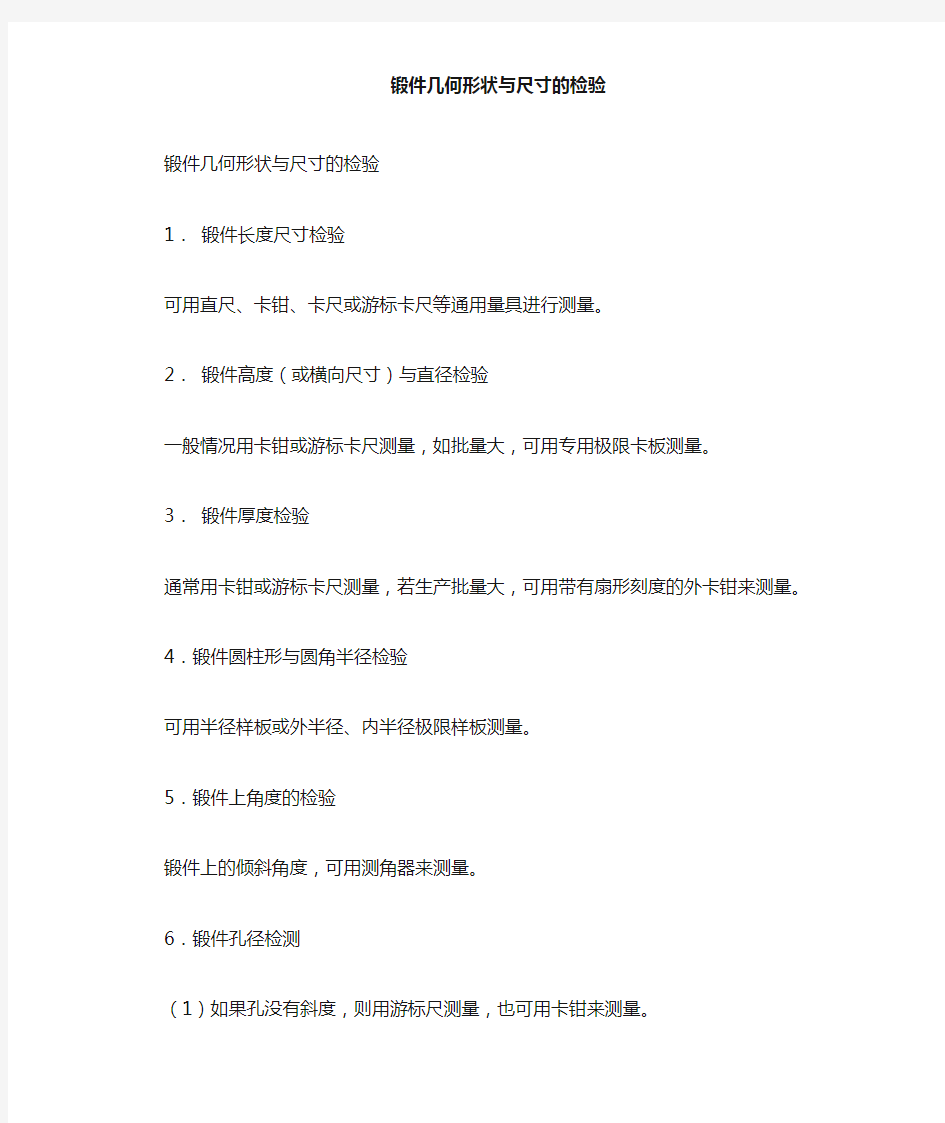

锻件几何形状与尺寸的检验
锻件几何形状与尺寸的检验
1.锻件长度尺寸检验
可用直尺、卡钳、卡尺或游标卡尺等通用量具进行测量。
2.锻件高度(或横向尺寸)与直径检验
一般情况用卡钳或游标卡尺测量,如批量大,可用专用极限卡板测量。
3.锻件厚度检验
通常用卡钳或游标卡尺测量,若生产批量大,可用带有扇形刻度的外卡钳来测量。
4.锻件圆柱形与圆角半径检验
可用半径样板或外半径、内半径极限样板测量。
5.锻件上角度的检验
锻件上的倾斜角度,可用测角器来测量。
6.锻件孔径检测
(1)如果孔没有斜度,则用游标尺测量,也可用卡钳来测量。
(2)如果孔有斜度,生产批量又大,则可用极限塞规测量。
(3)如果孔径很大,则可用大刻度的游标卡尺,或用样板检验。
7.锻件错位检验
(1)如果锻件上端面高出分模面且有7-10 度的出模斜度,或者分模面的位置在锻件本体中间,即可在切边前观察到锻件是否有错位。
(2)如错位不易观察到,则可将锻件下半部固定,对上半部进行划线检验,或者用专用样板检验。
(3)横截面为圆形的锻件,可用游标卡尺测量分模线的直径误差。
8.锻件挠度直径检验
(1)对于等截面的长轴类锻件,在平板上,慢漫地反复旋转锻件。即可测出轴线的最大挠度。
(2)将锻件两端支放在专门数据的V形块或滚棒上,旋转锻件,通过仪表即可测出锻件两支点间的最大挠度值。
9.锻件平面垂直度检验
如果要检验锻件上某个端面(如突缘)与锻件中心线的垂直度,则可将锻件放置在两个
V型块上,通过测量仪表测量该端面的跳动值。
10.锻件平面平行度检验
可选定锻件某一端面作为基准,借助测量仪表即可测出平行面间平行度的误差。
长度测量工具的发展
长度测量工具发展 工具简介 将被测长度与已知长度比较,从而得出测量结果的工具,简称测量工具。长度测量工具包括量规、量具和量仪。习惯上常把不能指示量值的测量工具称为量规;把能指示量值,拿在手中使用的测量工具称为量具;把能指示量值的座式和上置式等测量工具称为量仪。 智能之前 工具简史 最早在机械制造中使用的是一些机械式测量工具,例如角尺、卡钳等。 角尺卡钳 16世纪,在火炮制造中已开始使用光滑量规。1772年和1805年,英国的J.瓦特和H.莫兹利等先后制造出利用螺纹副原理测长的瓦特千分尺和校准用测长机。 瓦特千分尺新型测长机19世纪中叶以后,先后出现了类似于现代机械式外径千分尺和游标卡尺的测量工具。19世纪末期,出现了成套量块。 112块成套量块 继机械测量工具出现的是一批光学测量工具。19世纪末,出现立式测长仪,20世纪初,出现测长机。
新式测长仪测长机 到20年代,已经在机械制造中应用投影仪、工具显微镜、光学测微仪等进行测量。1928年出现气动量仪,它是一种适合在大批量生产中使用的测量工具。 浮标式气动量仪 电学测量工具是30年代出现的。最初出现的是利用电感式长度感应器制成的界限量规和轮廓仪。 界限量规轮廓仪 50年代后期出现了以数字显示测量结果的坐标测量机。60年代中期,在机械制造中已应用带有电子计算机辅助测量的坐标测量机。 三坐标测量机
至70年代初,又出现计算机数字控制的齿轮量仪,至此,测量工具进入应用电子计算机的阶。 计算机数字控制的齿轮量仪 工具分类 测量工具通常按用途分为通用测量工具、专类测量工具和专用测量工具3类。测量工具还可按工作原理分为机械、光学、气动、电动和光电等类型。这种分类方法是由测量工具的发展历史形成的。但一些现代测量工具已经发展成为同时采用精密机械、光、电等原理并与电子计算机技术相结合的测量工具,因此,这种分类方法仅适用于工作原理单一的测量工具。 通用测量工具 可以测量多种类型工件的长度或角度的测量工具。这类测量工具的品种规格最多,使用也最广泛,有量块、角度量块、多面棱体、正弦规、卡尺、千分尺、百分表(见百分表和千分表)、多齿分度台、比较仪、激光干涉仪、工具显微镜、三座标测量机等。 专类测量工具 用于测量某一类几何参数、形状和位置误差(见形位公差)等的测量工具。它可分为:①直线度和平面度测量工具,常见的有直尺、平尺、平晶、水平仪、自准直仪等;②表面粗糙度测量工具,常见的有表面粗糙度样块、光切显微镜、干涉显微镜和表面粗糙度测量仪等(见表面粗糙度测量);③圆度和圆柱度测量工具,有圆度仪、圆柱度测量仪等(见圆度测量);④齿轮测量工具,常见的有齿轮综合检查仪、渐开线测量仪、周节测量仪、导程仪等(见齿轮测量);⑤螺纹测量工具(见螺纹测量)等。 专用测量工具 仅适用于测量某特定工件的尺寸、表面粗糙度、形状和位置误差等的测量工具。常见的有自动检验机、自动分选机、单尺寸和多尺寸检验装置(见自动测量)等。
锻件检验标准
陕西博菲特流体控制装备制造有限公司 作 业 规 定 文件名称:锻造检验作业规定 文件编号: 版次: 发行日期: 受控状态:分发号: 核准:审查:编制:
一、目的:为确保锻件毛坯进厂检验时有据可依,规范锻件检验流程,提高对锻件的检验水平,特制定本标准 一、范围 所有的锻打件产品(含毛坯、半成品、成品) 二、权责 (一)本标准由技术部制订、更改、规范 (二)质检部负责本标准的实施,供应部、生产部及其它相关部门协助执行 三、内容 (一)外观及常见缺陷检验项目 1、裂纹 裂纹通常是锻造时存在较大的拉应力、切应力或附加拉应力引起的。裂纹发生的部位通常是在坯料应力最大、厚度最薄的部位。 2、折叠 折叠是金属变形过程中已氧化过的表层金属汇合到一起而形成的。它可以是由两股(或多股)金属对流汇合而形成;也可以是由一股金属的急速大量流动将邻近部分的表层金属带着流动,两者汇合而形成的;也可以是由于变形金属发生弯曲、回流而形成;还可以是部分金属局部变形,被压人另一部分金属内而形成。 3、大晶粒 大晶粒通常是由于始锻温度过高和变形程度不足、或终锻温度过高、或变形程度落人临界变形区引起的。铝合金变形程度过大,形成织构;高温合金变形温度过低,形成混合变形组织时也可能引起粗大晶粒,晶粒粗大将使锻件的塑性和韧性降低,疲劳性能明显下降。 4、晶粒不均匀 晶粒不均匀是指锻件某些部位的晶粒特别粗大,某些部位却较小。晶粒不均匀将使锻件的持久性能、疲劳性能明显下降。 5、冷硬现象 变形时由于温度偏低或变形速度太快,以及锻后冷却过快,均可能使再结晶引起的软化跟不上变形引起的强化(硬化),从而使热锻后锻件内部仍部分保留冷变形组织。这种组织的存在提高了锻件的强度和硬度,但降低了塑性和韧性。严重的冷硬现象可能引起锻裂。 6、龟裂 龟裂是在锻件表面呈现较浅的龟状裂纹。在锻件成形中受拉应力的表面(例如,未充满的凸出部分或受弯曲的部分)最容易产生这种缺陷。 7、飞边裂纹 飞边裂纹是模锻及切边时在分模面处产生的裂纹。 8、分模面裂纹 分模面裂纹是指沿锻件分模面产生的裂纹。原材料非金属夹杂多,模锻时向分模面流动与集中或缩管残余在模锻时挤人飞边后常形成分模面裂纹。 9、穿流 穿流是流线分布不当的一种形式。在穿流区,原先成一定角度分布的流线汇合在一起形成穿流,并可能使穿流区内、外的晶粒大小相差较为悬殊。
长度测量的几种常见方法
长度测量的几种常见方法 在长度测量中,常遇到一些物体的长度不能直接用刻度尺测量,如球的直径、一张纸的厚度等。但是,根据具体情况采取不同的特殊方法是可以测出它们的长度的。下面是在测量中常用到的几种长度的特殊测量方法; 一、曲直法。利用其它工具把曲线变成直线,再用刻度尺测量。 例1 你能利用刻度尺测出排球的直径吗? 提示:用一条弹性很小的柔软棉线沿排球的“赤道”绕一周,然后量出棉线的长度,再应用周长公式算出排球的直径。 二、轮替尺法。对于长而弯的曲线的测量,可借助圆轮沿曲线滚动,记下轮子滚过的转数,然后测出轮的周长,再用轮的周长乘以转数就得曲线的长度。 例2 怎样用你的玩具滚轮和一把米尺近似地测出你们学校跑道的总长? 三、斜正法。利用几何知道,用三角板和直尺测量如圆锥的高、圆柱体的直径和球的直径等。 例3 用直尺和三角板,你如何测出茶杯的深度和三棱锥的高度? 四、聚积法。把完全相同的物体重叠起来,先测出它们的总长,再算出所求部分的长。 例4 你能用一支铅笔,一把刻度尺近似地测出一根粗细均匀的铜丝的直径吗?写出你的操作过程。 提示:将金属丝在铅笔杆上密绕几十圈(不要叠合),测出其总长,然后除以圈数就可得到铜丝的直径。 五、割补法。对不规则图形面积的测量,将其轮廓描在方格纸上,先数占满方格的格数,再对没有占满方格的部分,按残缺的大小相互补充填满,得到占满的格数,然后测出每格的长和宽,算出每格的面积,乘以总格数就得到图形的近似面积。 例5 怎样利用直尺和印有方格的玻璃纸测出我国任何一省的面积。 六、影长法。利用太阳光或灯光和米尺,分别测出物体影长和米尺影长,根据几何知识算出物高=1米×物体影长/米尺影长。
锻件尺寸计算
二)计算坯料质量与尺寸 【坯料质量】坯料质量可按下式计算 G 坯料=G 锻件+G 烧损+G 料头 式中G 坯料——坯料质量 G 锻件——锻件质量 G 烧损——加热时由于坯料表面氧化而烧损的质量。第一次加热取被加热金属的2~3%,以后每次加热取1.5~2.0% G 料头——在锻造过程中冲掉或切掉的那部分金属的质量。如冲孔时坯料中部的料芯,修切端部的料头等。 当锻造大型锻件时,如采用钢锭作坯料,还要考虑应切掉的钢锭头部和尾部的质量。2.坯料尺寸根据坯料质量即可确定坯料尺寸。在计算坯料尺寸前,先要考虑锻造比。【锻造比】是指坯料在锻造前后的断面积的比值。 对于拔长工序来说,其锻造比R d 可按下式计算: R d =A 0 /A 1 或L 1 /L 0 式中A 0 、A 1 ——拔长前、后坯料的断面积; L 0 、L 1 ——拔长前、后坯料的长度。 对于镦粗工序来说,其锻造比(R u )可按下式计算: R u =A 1 /A 0 或H 0 /H 1 式中A 0 、A 1 ——镦粗前、后坯料的断面积; H 0 、H 1 ——镦粗前、后坯料的高度。 确定坯料的尺寸时,应满足对锻件的锻造比要求,并应考虑变形工序对坯料尺寸的限制。采用镦粗法锻造时,为避免镦弯,坯料的高径比(H 0 /D 0 <2.5)。但为下料方便,坯料高径比还应大于1.25。 根据坯料质量,由下式求出坯料体积V 坯。 V 坯=m 坯/ ρ ρ——金属密度。对于钢铁ρ =7.85kg/dm 3 。 然后,求出坯料横截面积A 0 。 采用拔长法锻造时,由公式: A 0 =R d A 1
因锻后横截面积A 1 可知,故可求出A 0 ( 坯料为钢锭时,锻造比R d 取2.3~3. 0;坯料为轧材时,R d 取l.3~1.5),最后可求出坯料直径或边长。 (三)制定锻造工序 根据不同类型的锻件选用不同的锻造工序。工序确定后,尚须确定所用的工夹具、加热设备、加热和冷却规范及根据锻件质量确定锻造设备。 (四)自由锻件的锻造工艺规程举例。 自由锻件的锻造工艺规程举例见下表。
锻件质量检验规范
XXXXX 【文件编号:XXXX】 锻件质量检验规范 受控状态: 分发编号: 版本号: 编制: 审核: 批准:
发布时间:X 实施时间: XXX 一主题内容与适用范围: 本标准规定了对锻造工艺进行全过程质量控制的通用原则和要求。本标准适用于锻造车间的锻造工艺质量控制。 二引用标准: GB 12361-2016 钢质模锻件通用技术条件 GB 12362-2016 钢质模锻件公差及机械加工余量 GB 13318 锻造车间安全生产通则 GB/T 12363-2005 锻件功能分类
JB 4249 锤上钢质自由锻件机械加工余量与公差 JB 4385 锤上钢质自由锻件通用技术条件 JB/T 6052 钢质自由锻件加热通用技术要求 JB/T 6055 锻造车间环境保护导则 GB/T7232金属热处理工艺 GB/T231-2009金属材料布氏硬度 GB/T13320-2007钢制模锻件金相组织评定图及评定方法 三.锻件分类本标准质量控制所涉及的锻件分类按GB/T 12363 执行。 四环境的控制: 锻造厂的工作环境包括厂房地面、天窗、温度、通风、照明、噪声、通道、管道以及坯料、锻件和工夹模具的存放等均应按GB 13318 第3 章和JB/T 6055 第3、4 章的要求和国家的有关法规、法律
制订本企业的具体实施要求。 五设备、仪表与工装的控制: 5. 1 设备、仪表 5. 1. 1 各类设备必须完好,并有操作规程和维修、检定制度。5. 1. 2 各类在用主要设备必须挂有完好设备标牌,并有检验有效期 及下次检定日期。不合格设备及超过检定合格有效期的设备 必须挂“停用”标牌。 5. 1. 3 设备的控制系统及检测显示仪表应定期检查,确保仪表和其精度的显示数值准确。 5. 1. 4 加热设备的温度显示及测点布置应正确反应加热区炉温及炉温均匀性。 5. 1. 5 所用设备都必须建立档案,其具体内容包括: a. 设备使用说明书 b.台时记录 c.故障记录 d.修理记录
锻件质量检验的内容和方法
锻件质量检验的内容和方法 (一)锻件质量检验的内容 锻件缺陷的存在,有的会影响后续工序处理质量或加工质量,有的则严重影响锻件的性能及使用,甚至极大地降低所制成品件的使用寿命,危及安全。因此为了保证或提高锻件的质量,除在工艺上加强质量控制,采取相应措施杜绝锻件缺陷的产生外,还应进行必要的质量检验,防止带有对后续工序(如热处理、表面处理、冷加工)及使用性能有恶劣影响的缺陷的锻件流人后续工序。经质量检验后,还可以根据缺陷的性质及影响使用的程度对已制锻件采取补救措施,使之符合技术标准或使用的要求。 因此,锻件质量检验从某种意义上讲,一方面是对已制锻件的质量把关,另一方面则是给锻造工艺指出改进方向,从而保证锻件质量符合锻件技术标准的要求,并满足设计、加工、使用上的要求。 锻件质量的检验包括外观质量及内部质量的检验。外观质量检验主要指锻件的几何尺寸、形状、表面状况等项目的检验;内部质量的检验则主要是指锻件化学成分、宏观组织、显微组织及力学性能等各项目的检验。 具体说来,锻件的外观质量检验也就是检查锻件的形状、几何尺寸是否符合图样的规定,锻件的表面是否有缺陷,是什么性质的缺陷,它们的形态特征是什么。表面状态的检验内容一般是检查锻件表面是否有表面裂纹、折叠、折皱、压坑、桔皮、起泡、斑疤、腐蚀坑、碰伤、外来物、未充满、凹坑、缺肉、划痕等缺陷。而内部质量的检验就是检查锻件本身的内在质量,是外观质量检查无法发现的质量状况,它既包含检查锻件的内部缺陷,也包含检查锻件的力学性能,而对重要件、关键件或大型锻件还应进行化学成分
分析。对于内部缺陷我们将通过低倍检查、断口检查、高倍检查的方法来检验锻件是否存在诸如内裂、缩孔、疏松、粗晶、白点、树枝状结晶、流线不符合外形、流线紊乱、穿流、粗晶环、氧化膜、分层、过热、过烧组织等缺陷。而对于力学性能主要是检查常温抗拉强度、塑性、韧性、硬度、疲劳强度、高温瞬时断裂强度、高温持久强度、持久塑性及高温蠕变强度等。 由于锻件制成零件后,在使用过程中其受力情况、重要程度、工作条件不同,其所用材料和冶金工艺也不同,因此不同的部位依据上述情况并按照本部门的要求将锻件分出类别,不同的部门,不同的标准对锻件的分类也是不同的。但不管怎么,对于锻件质量检验的整体来说都离不开两大类检验,即外观质量和内部质量的检验,只不过锻件的类别不同,其具体的检验项目、检验数量和检验要求不同罢了。例如,有的工业部门将结构钢、不锈钢、耐热钢锻件分成Ⅳ类进行检验,有的部门将铝合金锻件与模锻件按其使用情况分成Ⅲ类进行检验,还有的部门将铝合金、铜合金锻件分成Ⅳ类进行检验。表1-1是结构钢、不锈钢、耐热钢锻件分成Ⅳ类的检验要求,表1-2是铝合金锻件和模锻件质量检验要求。
锻件检验标准
陕西博菲特流体控制装备制造有限公司 文件名称: 锻造检验作业规定 文件编号: 版 次: 发行日期: 受控状态: 分发号: 核准: 审查: 编 制: 作 业 规 定
一、目的:为确保锻件毛坯进厂检验时有据可依,规范锻件检验流程,提高对锻件的检验水平,特制定本标准 一、范围 所有的锻打件产品(含毛坯、半成品、成品) 二、权责 (一)本标准由技术部制订、更改、规范 (二)质检部负责本标准的实施,供应部、生产部及其它相关部门协助执行 三、内容 (一)外观及常见缺陷检验项目 1、裂纹 裂纹通常是锻造时存在较大的拉应力、切应力或附加拉应力引起的。裂纹发生的部位通常是在坯料应力最大、厚度最薄的部位。 2、折叠 折叠是金属变形过程中已氧化过的表层金属汇合到一起而形成的。它可以是由两股(或多股)金属对流汇合而形成;也可以是由一股金属的急速大量流动将邻近部分的表层金属带着流动,两者汇合而形成的;也可以是由于变形金属发生弯曲、回流而形成;还可以是部分金属局部变形,被压人另一部分金属内而形成。? 3、大晶粒? 大晶粒通常是由于始锻温度过高和变形程度不足、或终锻温度过高、或变形程度落人临界变形区引起的。铝合金变形程度过大,形成织构;高温合金变形温度过低,形成混合变形组织时也可能引起粗大晶粒,晶粒粗大将使锻件的塑性和韧性降低,疲劳性能明显下降。 4、晶粒不均匀? 晶粒不均匀是指锻件某些部位的晶粒特别粗大,某些部位却较小。晶粒不均匀将使锻件的持久性能、疲劳性能明显下降。 5、冷硬现象 变形时由于温度偏低或变形速度太快,以及锻后冷却过快,均可能使再结晶引起的软化跟不上变形引起的强化(硬化),从而使热锻后锻件内部仍部分保留冷变形组织。这种组织的存在提高了锻件的强度和硬度,但降低了塑性和韧性。严重的冷硬现象可能引起锻裂。 6、龟裂? 龟裂是在锻件表面呈现较浅的龟状裂纹。在锻件成形中受拉应力的表面(例如,未充满的凸出部分或受弯曲的部分)最容易产生这种缺陷。 7、飞边裂纹 飞边裂纹是模锻及切边时在分模面处产生的裂纹。 8、分模面裂纹 分模面裂纹是指沿锻件分模面产生的裂纹。原材料非金属夹杂多,模锻时向分模面流动与集中或缩管残余在模锻时挤人飞边后常形成分模面裂纹。 9、穿流?
锻件质量无损检测方法
锻件质量无损检测方法 对于锻件的质量检验所采用的无损检测方法一般有:磁粉检验法MT、渗透检验法PT、涡流检验法ET、超声波检验法UT等。 磁粉检验法广泛地用于检查铁磁性金属或合金锻件的表面或近 表面的缺陷,如裂纹、发纹、白点、非金属夹杂、分层、折叠、碳化物或铁素体带等。该方法仅适用于铁磁性材料锻件的检验,对于奥氏体钢制成的锻件不适于采用该方法。 渗透检验法除能检查磁性材料锻件外,还能检查非铁磁性材料锻件的表面缺陷,如裂纹、疏松、折叠等,一般只用于检查非铁磁性材料锻件的表面缺陷,不能发现隐在表面以下的缺陷。 超声波检验法用以检查锻件内部缺陷如缩孔、白点、心部裂纹、夹渣等,该方法虽然操作方便、快且经济,但对缺陷的性质难以准确地进行判定。 随着无损检测技术的发展,现在又出现了诸如声振法,声发射法、激光全息照相法、CT法等新的无损检测方法,这些新方法的出现及在锻件检验中的应用,必将使锻件质量检验的水平得以大大地提高。 锻件质量的分析实际上是各种测试方法的综合应用及各个测试 结果的综合分析,对于大型复杂的锻件所出现问题不能单纯地依赖于某一种方法,从这一点上可以说各种试验方法在分析过程中是相辅相成的,各种试验方法的有机配合,并对各自试验结果进行综合分析,才能得出正确的结论。同时就锻件质量分析的目的而言,除了正确的检验外,还应进行必要的工艺试验从而找出产生质量问题的真正原因
并提出圆满的改进措施及防止对策。在实际工作中究竟选用那些检测方法,运用何种检测手段应根据锻件的类别和规定的检测项目来进行。在选择试验方法和测试手段时,既要考虑到先进性,又要考虑到实用性、经济性,不能单纯地追求先进性,能用一种手段解决问题就不要用二种或更多种,测试手段的选择应准确地判定缺陷的性质和确切找出缺陷产生的原因为出发点,有时测试手段选择得过于先进反而会导致不必要的后果以致造成不应有的损失。
锻件毛坯计算
锻件毛坯计算 如图,根据零件图绘制锻件图。 在1吨模锻锤上模锻,生产批量为成批生产,材料45钢。 解:计算过程如下 1、确定机械加工余量和公差 (1)计算锻件质量m ()2223313290463610036100107.8510222m kg πππ--????????=??+??--??????? ? ? ??????????? 5.76kg = (2)计算锻件复杂系数S ()2222132904636100361002220.5361321002S ππππ??????????+??--???? ? ? ?????????? ?==???? ??? S 在0.32~0.63G C =范围内,所以复杂系数为2S 级。
(3)材质系数M 45钢含碳量c%=0.42~0.50%<0.65% 所以材质系数为1M 级。 (4)由表2-2、表2-3查得零件加工余量 锻件厚度尺寸100mm ,余量2.0~2.5mm ,取2.5mm 。 锻件长度尺寸132mm ,余量2.0~2.5mm ,取2.5mm 。 内孔直径尺寸46mm ,余量2.6mm 。 (5)根据锻件质量m 、复杂系数S 、材质系数M ,由表2-4、2-6查公差 锻件尺寸132mm ,公差 2.11.13.2mm + -; 锻件尺寸90mm ,公差 1.90.92.8mm + -; 厚度尺寸100mm ,公差 2.70.93.6mm + -; 厚度尺寸36mm ,公差 1.90.62.5mm + -; 内孔直径46mm ,公差0.81.72.5mm + -; 错差1.2mm ; 残留飞边公差1.2mm ; 表面缺陷,不允许超过1.2mm 。 2、确定模锻斜度 由零件尺寸,查得,内表面拔模斜度10 ,外表面拔模斜度7 。 3、圆角半径 外圆角半径r=余量+a=2.5+2=4.5mm ,取r=5mm 。 内圆角半径R=(2~3)r ,根据需要,取R=8mm 。 4、冲孔连皮(当孔径为25~80mm 时,冲孔连皮厚度取4~8mm) 冲孔连皮:对于有内孔的模锻件,锤上模锻不能直接锻出通孔,必须在所锻成的盲孔内保留一层具有一定厚度的金属层。 冲孔连皮形式:
第三章 长度尺寸测量工具
第三章长度尺寸测量工具 一、简易量具 1、钢直尺 1)钢直尺结构与规格 钢板尺俗称钢尺或直尺,如图1所示,是用来测量长度的一种最常用的简单量具,可直接测量工件尺寸。尺边平直,尺面有米制或英制的刻度,可以用来测量工件的长度、宽度、高度和深度。有时还可用来对一些要求较低的工件表面进行平面度检查。 图1钢板尺 钢板尺测量范围基本取决于钢尺的长度。测量范围主要有:0~150 mm、0~200 mm、0~300 mm、0~500 mm等规格,其测量范围就是所能测定的最大长度。钢板尺最小刻度一般为0.5 mm或l mm。 2)使用方法 要根据被测件的形状和尺寸大小灵活掌握使用钢板尺的方法。应根据测量尺寸的大小,选择恰当长度的钢板尺。实际测量工件时,应将钢板尺拿稳,用拇指贴靠工件。图2(a)所示为正确的测量方法;图2(b)所示为错误的测量方法。手指位置不对,易使钢板尺不稳定,造成测量不准确。读数时,应使视线与钢板尺垂直,而不应倾斜,否则会影响测量的准确度。 钢板尺起始端是测量的基准,应保持其轮廓完整,以免影响测量的准确度。如果钢板尺端部已经磨损,应以另一刻度线作为基准。 (a)正确 (b)不正确 图2钢板尺测量工件 2、卡钳 卡钳是一种间接测量的简单量具,不能直接读出测量数值,必须与钢板尺或其他带有刻度的量具一起使用才尺或其他带有刻度的量具一起使用才行。 1)卡钳的种类 卡钳还分为普通卡钳和弹簧卡钳。普通卡钳结构简单,是用铆钉或螺钉连接两个卡脚的;弹簧卡钳是用弹簧连接两个卡脚的,通过调整螺母来限制卡脚张开的大小,如图3所示。
图3 卡钳 1—卡钳 2—铆钉或螺钉 3—弹簧 4—螺钉 5—调整螺母卡钳分外卡钳和内卡钳,外卡钳是由两个弧形卡脚连接起来的,两个钳口是相对的,可用来测量外尺寸,如外圆直径、厚度、宽度等。内卡钳是由两个直形卡脚连接起来的,两个钳口是向外的,可用来测量内尺寸,如内孔、沟槽等。 卡钳适合用来测量铸、锻件毛坯。 在精加工过程中,卡钳应与千分尺配合使用,对某一加工尺寸,用预先调整好的卡钳进行测试,可提高测量精度和工作效率。 2)卡钳的调整方法 普通卡钳的调整 卡钳卡脚张开的大小,称为卡钳的开度。调整普通卡钳的开度时,先用两手进行大致调整,开度接近需要的大小时,用手捏住连接处,轻轻敲击卡脚,使它微微张大或缩小来进行细微调整。图4(a)、(b)是轻敲卡脚的外边(图示箭头为敲击方向),使它由大调小;图4(c)、(d)是轻敲卡脚的内边,使它由小调大。 (a)(b) (c)(d)
锻件质量检验全
锻件质量检验
属表 属表
表2 分类名称: 锻件几何形状与尺寸的检验 内容描述:1.锻件长度尺寸检验 可用直尺、卡钳、卡尺或游标卡尺等通用量具进行测量。 2.锻件高度(或横向尺寸)与直径检验一般情况用卡钳或游标卡尺测 量,如批量大,可用专用极限卡板测量。 3.锻件厚度检验通常用卡钳或游标卡尺测量,若生产批量大,可用带有扇形刻度的外卡钳来测量。 4.锻件圆柱形与圆角半径检验可用半径样板或 外半径、内半径极限样板测量。 5.锻件上角度的检验锻件上的倾斜角 度,可用测角器来测量。 6.锻件孔径检测 (1)如果孔没有斜度,则用游标尺测量,也可用卡钳来测量。 (2)如果孔有斜度,生产批量又大,则可用极限塞规测量。 (3)如果孔径很大,则可用大刻度的游标卡尺,或用样板检验。 7.锻件错位检验 (1)如果锻件上端面高出分模面且有 7-10 度的出模斜度,或者分模面的位置在锻件本体中间,即可在切边前观察到锻件是否有错位。 (2)如错位不易观察到,则可将锻件下半部固定,对上半部进行划线检验,或者用专用样板检验。 (3)横截面为圆形的锻件,可用游标卡尺测量分模线的直径误差。 8.锻件挠度直径检验 (1)对于等截面的长轴类锻件,在平板上,慢漫地反复旋转锻件。即可测出轴线的最大挠度。 (2)将锻件两端支放在专门数据的V形块或滚棒上,旋转锻件,通过仪表即可测出锻件两支点间的最大挠度值。
9.锻件平面垂直度检验如果要检验锻件上某个端面(如突缘)与锻件中心线的垂直度,则可将锻件放
置在两个V型块上,通过测量仪表测量该端面的跳动值。 10.锻件平面平行度检验可选定锻件某一端面作为基准,借助测量仪表即可测出平行面间平行度的误差。
锻件尺寸检验
锻件几何形状与尺寸的检验 锻件几何形状与尺寸的检验 1.锻件长度尺寸检验 可用直尺、卡钳、卡尺或游标卡尺等通用量具进行测量。 2.锻件高度(或横向尺寸)与直径检验 一般情况用卡钳或游标卡尺测量,如批量大,可用专用极限卡板测量。 3.锻件厚度检验 通常用卡钳或游标卡尺测量,若生产批量大,可用带有扇形刻度的外卡钳来测量。 4.锻件圆柱形与圆角半径检验 可用半径样板或外半径、内半径极限样板测量。 5.锻件上角度的检验 锻件上的倾斜角度,可用测角器来测量。 6.锻件孔径检测 (1)如果孔没有斜度,则用游标尺测量,也可用卡钳来测量。 (2)如果孔有斜度,生产批量又大,则可用极限塞规测量。 (3)如果孔径很大,则可用大刻度的游标卡尺,或用样板检验。 7.锻件错位检验 (1)如果锻件上端面高出分模面且有7-10 度的出模斜度,或者分模面的位置在锻件本体中间,即可在切边前观察到锻件是否有错位。 (2)如错位不易观察到,则可将锻件下半部固定,对上半部进行划线检验,或者用专用样板检验。 (3)横截面为圆形的锻件,可用游标卡尺测量分模线的直径误差。 8.锻件挠度直径检验 (1)对于等截面的长轴类锻件,在平板上,慢漫地反复旋转锻件。即可测出轴线的最大挠度。 (2)将锻件两端支放在专门数据的V形块或滚棒上,旋转锻件,通过仪表即可测出锻件两支点间的最大挠度值。 9.锻件平面垂直度检验 如果要检验锻件上某个端面(如突缘)与锻件中心线的垂直度,则可将锻件放置在两个 V型块上,通过测量仪表测量该端面的跳动值。 10.锻件平面平行度检验 可选定锻件某一端面作为基准,借助测量仪表即可测出平行面间平行度的误差。
锻件图的绘制
锻件图的绘制 圆角半径 (一)圆角半径的确定 锻件上的凸角圆角半径为外圆角半径r,凹角圆角半径为内圆角半径R(见图14)。外圆角作用是避免锻模的相应部分因产生应力集中造成开裂;内圆角作用是使金属易于流动充满模膛,避免产生折叠,防止模膛压塌变形。 为保证锻件凸角处的最小余量,按下式计算: r1=余量+零件的倒角值 若零件无倒角,按: r2=余量 圆角半径(r、R)的数值根据锻件各部分的高度与宽度比值H/B(见图14),查表16确定。
表16 圆角半径计算表(JB3835-85) 为了简化制造模具所用刀具的规格,圆角半径应按以下系列选用: 1 1.5 2 2.5 3 4 5 6 8 10 12 15mm。圆角半径大于15mm时,逢5递增。 (二)圆角半径公差 一般情况下内外圆角半径公差不要求检查,需要时可按表15查得。 示例 某一齿轮零件的外径为171.8mm,全高48mm,计算其锻件重量为4.63kg,包容体重量为10.18kg,形状复杂系数为S3级;材料牌号18CrMnTi,材质系数为M1级;精度等级为普通级。由表1、表2、表3、表5、表8查得锻件的机械加工余量及公差绘制出锻件图(见图20)。由于需方未提出特殊要求,其技术要求按一般锻件质量要求列于锻件图下方。 图20 齿轮锻件图 技术要求 1.未注明模锻斜度7° 2.未注明圆角半径R3mm
3.错差可达1mm 4.残留飞边可达1mm 5.平面度可达0.8mm 6.表面缺陷深度在加工表面不大于实际加工余量的1/2;不加工面不大于厚度公差的1/3。7.热处理硬度d B≥4.2~4.8(HB156~207) 8.清除氧化铁皮 冲孔连皮及肓孔 当孔径d≥25mm,冲孔深度h不大于冲头直径d时,此类锻件可在模锻过程中进行冲孔,然后在切边压力机上冲去连皮,获得带透孔的锻件。冲孔连皮肓孔可分为如下四类:(一)平底连皮 按照锻件的孔径和高度尺寸由图15查出平底连皮的厚度尺寸。 图15 平底连皮图16 斜底连皮(二)斜底连皮 当锻件的孔径较大(d>60mm),平底连皮较薄,阻碍金属外流,易使锻件内孔产生折叠和造成冲头号压塌。采用斜底连皮(见图16),连皮斜度增加了连皮和内孔接触处的连皮厚度,促进金属往外流动,避免产生折叠,冲头不易损坏,斜底连皮的尺寸如下: S max=1.35S S min=0.65S
机械加工件检验标准
机械加工件检验标准 1. 目的 规范机械加工件的检验标准,以使各工序过程的产品质量得以控制。 2. 适用范围 本标准适用于机械加工件的检验, 图纸和技术文件并同使用。如与国家标准和技术规范冲突时,以国家标准和技术规范为准。 3. 引用标准 本标准的尺寸未注单位为mm 。 JB/T 5000.9 《重型机械通用技术条件切削加工件》 GB/T 1031 《表面粗糙度参数及其数值》 GB/T 1800.4 《极限与配合标准公差等级和孔轴的极限偏差表》 GB/T 3 《普通螺纹收尾、肩距、退刀槽和倒角》 GB/T 197 《普通螺纹公差》 GB/T 1184 《形状和位置公差未注公差值》
GB/T 1804 《一般公差未注公差的线性和角度尺寸的公差》GB/T 5277 《紧固件螺栓和螺钉通孔》 4. 原材料检验 机械加工件所用板料, 棒料的材质, 规格和数量是否符合按图加工所需。详细做好原材料入库记录。不合格材料办理好退货手续。 5. 工序质量检验 5.1 零件加工后应符合产品图样和技术条件及JB/T 5000.9《重型机械通用技术条件切削加工件》规定。 5.2 零件应按工序检查、验收,在前道工序检查合格后方可转入下道工序。 5.3 铸钢件、铸铁件、有色金属铸件、锻件加工后如发现有砂眼、缩孔、夹渣、裂纹等缺陷时, 在不降低零件强度和使用性能的前提下, 允许按照相关标准的有关规定修补, 经检验合格后方可继续加工。 5.4 加工后的零件不允许有毛刺,除产品图样有要求外,不允许有尖棱、尖角。
5.5 精加工后的零件不允许直接摆放在地面上,应采取必要的支撑、保护措施。加工面不允 许有锈蚀和影响性能、寿命或外观的磕碰、划伤等缺陷。 5.6 精加工后的配合面、摩擦面和定位面等工作表面不允许打印标记。 5.7 最终工序为热处理的零件,热处理后表面不应有氧化皮。精加工后的配合面、齿面不应有退火、发蓝、变色的现象。 5.8 对于生产图样中要求电镀锌或热镀锌的零件,图中要求的配合面尺寸为含镀层后的尺寸。 5.9 表面电镀锌涂层的质量要求: 1)镀层外观光滑细致、无起泡、起层、剥落、烧焦及海绵状沉淀; 2)经铬酸钝化后,应具有绿黄略带有红色的彩虹色; 3)镀层表面允许有不严重的流痕及轻微的刮痕印,允许工件边缘色彩稍淡; 4)钝化膜有一定的光泽,不到呈暗褐无光的泥巴色; 5)钝化膜应牢固,用布揩擦不掉;在50℃~60℃的热水中煮1小时,颜色无显著减退。
长度测量工具
现代常用的测量工具:测量工具,是测量某个性质的工具。包括长度、温度、时间、质量、力、电流、电压、电阻、声音、无线电、折射率和平均色散。 长度测量:米尺,游标卡尺,卷尺,外径千分尺 时间测量:秒表,普通钟表,电子表 电流测量:电流表,万用表,电笔 重量测量:台秤,电子称,地磅,天平 温度测量:温度计 各种专业测量用具:如建筑施工中用到的经纬仪,水准仪,全站仪,GPS测量仪。 长度测量工具 最早在机械制造中使用的是一些机械式测量工具,例如角尺、卡钳等。16世纪,在火炮制造中已开始使用光滑量规。1772年和1805年,英国的J.瓦特和H.莫兹利等先后制造出利用螺纹副原理测长的瓦特千分尺和校准用测长机。19世纪中叶以后,先后出现了类似于现代机械式外径千分尺和游标卡尺的测量工具。19世纪末期,出现了成套量块。继机械测量工具出现的是一批光学测量工具。19世纪末,出现立式测长仪,20世纪初,出现测长机。到20年代,已经在机械制造中应用投影仪、工具显微镜、光学测微仪等进行测量。1928年出现气动量仪,它是一种适合在大批量生产中使用的测量工具。电
学测量工具是30年代出现的。最初出现的是利用电感式长度传感器制成的界限量规和轮廓仪。50年代后期出现了以数字显示测量结果的坐标测量机。60年代中期,在机械制造中已应用带有电子计算机辅助测量的坐标测量机。至70年代初,又出现计算机数字控制的齿轮量仪,至此,测量工具进入应用电子计算机的阶段。 质量测量工具 弹簧秤,分压力和拉力两种类型,压力弹簧秤的托盘承受的压力等于物体的重力,秤盘指针旋转的角度指示所受压力的数值。拉力弹簧秤的下端和一个钩子连在一起(这个钩子是与弹簧下端连在一起的),弹簧的上端固定在壳顶的环上。将被测物挂在钩上,弹簧即伸长,而固定在弹簧上的指针随着下降。由于在弹性限度内,弹簧的伸长与所受之外力成正比,因此作用力的大小或物体重力可从弹簧秤的指针指示的外壳上的标度数值直接读出。 托盘天平,依据杠杆原理制成,在杠杆的两端各有一小盘,一端放砝码,另一端放要称的物体,杠杆中央装有指针,两端平衡时,两端的质量(重量)相等。是一种常用衡器。精确度不高,一般为0.1 或0.2克。荷载有100g、200g、500g、1000g等。由托盘、横梁、平衡螺母、刻度尺、指针、刀口、底座、标尺、游码、砝码等组成。由支点(轴)在梁的中心支着天平梁而形成两个臂,每个臂上挂着或托着一个盘,其中一个盘(通常为右盘)里放着已知重量的物体(砝码),另一个盘(通常为左盘)里放待称重的物体,游码则在刻度尺上滑动。
锻件检验指导书修订版
锻件检验指导书 HUA system office room 【HUA16H-TTMS2A-HUAS8Q8-HUAH1688】
锻件检验指导书 一、目的:为确保锻件毛坯进厂检验时有据可依,规范锻件检验流程,提高对锻件的检 验水平,特制定本标准 二、范围 所有的锻打件产品(含毛坯、半成品、成品) 三、权责 (一)本标准由技术部制订、更改、规范 (二)质检部负责本标准的实施,供应部、生产部及其它相关部门协助执行 四、内容 (一)外观及常见缺陷检验项目 1、裂纹 裂纹通常是锻造时存在较大的拉应力、切应力或附加拉应力引起的。裂纹发生的部位通常是在坯料应力最大、厚度最薄的部位。 2、折叠 折叠是金属变形过程中已氧化过的表层金属汇合到一起而形成的。它可以是由两股(或多股)金属对流汇合而形成;也可以是由一股金属的急速大量流动将邻近部分
的表层金属带着流动,两者汇合而形成的;也可以是由于变形金属发生弯曲、回流而形成;还可以是部分金属局部变形,被压人另一部分金属内而形成。 3、局部充填不足? 局部充填不足主要发生在筋肋、凸角、转角、圆角部位,尺寸不符合图样要求。 4、欠压? 欠压指垂直于分模面方向的尺寸普遍增大 5、错移? 错移是锻件沿分模面的上半部相对于下半部产生位移。 6、轴线弯曲? 锻件轴线弯曲,与平面的几何位置有误差。 7、其它缺陷: 表面麻坑、锈蚀、表面气泡、缩孔、疏松、白点、异金属夹杂等 (二)材料及性能要求按图纸要求及国家相关规定 附表一、锻件用碳素结构钢与合金结构钢牌号及化学成分(摘自GB/T17017-1997) 表1
表2
(三)尺寸及公差要求: 1、关键性尺寸(产品中心距、角度以及其它影响产品装配的尺寸,机加工时用到 的装夹面尺寸等)必须严格按图纸要求 2、机加工表面加工余量: (1)厚度方向一般为单面1.5mm,最小不得低于1mm (2)直径上为最终成品尺寸+2mm,最小不得低于1mm (3)长度方向尺寸可加1.5-3mm 3、未注非机加工尺寸: (1)图纸有公差标示的,按图纸尺寸 (2)图纸无公差的,按下表规定(QC/T270): 孔类尺寸未注公差
长度测量工具的发展演示教学
长度测量工具的发展
长度测量工具发展 工具简介 将被测长度与已知长度比较,从而得出测量结果的工具,简称测量工具。长度测量工具包括量规、量具和量仪。习惯上常把不能指示量值的测量工具称为量规;把能指示量值,拿在手中使用的测量工具称为量具;把能指示量值的座式和上置式等测量工具称为量仪。 智能之前 工具简史 最早在机械制造中使用的是一些机械式测量工具,例如角尺、卡钳等。 角尺卡钳 16世纪,在火炮制造中已开始使用光滑量规。1772年和1805年,英国的J.瓦特和H.莫兹利等先后制造出利用螺纹副原理测长的瓦特千分尺和校准用测长机。 瓦特千分尺新型测长机 19世纪中叶以后,先后出现了类似于现代机械式外径千分尺和游标卡尺的测量工具。19世纪末期,出现了成套量块。 112块成套量块 继机械测量工具出现的是一批光学测量工具。19世纪末,出现立式测长仪,20世纪初,出现测长机。
新式测长仪测长机 到20年代,已经在机械制造中应用投影仪、工具显微镜、光学测微仪等进行测量。1928年出现气动量仪,它是一种适合在大批量生产中使用的测量工具。 浮标式气动量仪 电学测量工具是30年代出现的。最初出现的是利用电感式长度感应器制成的界限量规和轮廓仪。 界限量规轮廓仪50年代后期出现了以数字显示测量结果的坐标测量机。60年代中期,在机械制造中已应用带有电子计算机辅助测量的坐标测量机。 三坐标测量机
至70年代初,又出现计算机数字控制的齿轮量仪,至此,测量工具进入应用电子计算机的阶。 计算机数字控制的齿轮量仪 工具分类 测量工具通常按用途分为通用测量工具、专类测量工具和专用测量工具3类。测量工具还可按工作原理分为机械、光学、气动、电动和光电等类型。这种分类方法是由测量工具的发展历史形成的。但一些现代测量工具已经发展成为同时采用精密机械、光、电等原理并与电子计算机技术相结合的测量工具,因此,这种分类方法仅适用于工作原理单一的测量工具。 通用测量工具 可以测量多种类型工件的长度或角度的测量工具。这类测量工具的品种规格最多,使用也最广泛,有量块、角度量块、多面棱体、正弦规、卡尺、千分尺、百分表(见百分表和千分表)、多齿分度台、比较仪、激光干涉仪、工具显微镜、三座标测量机等。 专类测量工具 用于测量某一类几何参数、形状和位置误差(见形位公差)等的测量工具。它可分为:①直线度和平面度测量工具,常见的有直尺、平尺、平晶、水平仪、自准直仪等; ②表面粗糙度测量工具,常见的有表面粗糙度样块、光切显微镜、干涉显微镜和表面粗糙度测量仪等(见表面粗糙度测量);③圆度和圆柱度测量工具,有圆度仪、圆柱度测量仪等(见圆度测量);④齿轮测量工具,常见的有齿轮综合检查仪、渐开线测量仪、周节测量仪、导程仪等(见齿轮测量);⑤螺纹测量工具(见螺纹测量)等。 专用测量工具
长度测量常见的几种特殊方法
长度测量常见的几种特殊方法长度的测量是最基本的测量,日常生活中最常用的工具有钢卷尺、三角尺、直尺,而像游标卡尺、螺旋测微器较精密仪器并不常用。当我们手边测量工具仅有直尺和三角尺时,而测量的对象却是不规则(或者非直线形)物体,用常规方法不能直接测出其长度,现举一些长度测量常见的特殊方法,有利于学生扩展视野,提高兴趣,活跃思维。 1. 化曲为直法适用范围:这种方法适用于测量较短的曲线。 具体做法:把棉线的起点放在曲线的一端点处,让它顺着曲线弯曲,标出曲线另一端点在棉线处的记号作为终点,然后把棉线拉直,用刻度尺量出棉线起点至终点间的距离,即为曲线长度。 实例:测圆形空碗的碗口边缘的长度、测地图上两点间的距离、硬币的周长、圆柱的周长、胸围、腰围等。 2. 滚轮法 适用范围:这种方法适用于测量比较长的曲线。具体做法:用一轮子,先测出其直径,后求出其周长,再将轮沿曲线滚动,记下滚动的圈数,最后将轮的周长与轮滚动的圈数相乘,所得的积就是曲线的长度。 实例:测操场跑道的长度、测一个椭圆形花坛的周长。 3. 辅助法 适用范围:这种方法适用于部分形状规则的物体,某些长度端点位置模糊,或不易确定。 具体做法:用刻度尺将不能直接测出的物体长度,借助于三角
板或桌面将待测物体卡住,把不可直接测量的长度转移到刻度尺上,从而直接测出该长度。如图所示(注意用三角板的直角边夹住物体,并与刻度尺垂直)。 实例:测硬币、球、圆柱的直径,圆锥的高、人的身高等。 4. 累积法适用范围:某些难以用常规仪器直接准确测量的物理量。具体做法:把某些难以用常规仪器直接准确测量的物理量用累积的方法, 将小量变大量,不仅可以便于测量,而且还可以提高测量的准确程度, 减小误差。 实例:测一张纸的厚度,可将100 张叠起来测量,除以100 算出平均数。测量细铜丝的直径,把细铜丝在铅笔杆上紧密排绕n圈成螺线管,用刻度尺测出螺线管的长度L,则 细铜丝直径为L/n 。将细铜线密绕在铅笔上,用总宽度除以匝数算出铜线的直径。 5. 几何法 适用范围:对于不能分割或攀登的某些较高的树木、旗杆或建筑物等。 具体做法:利用被测物和参照物及其阳光下的影子组成相似图形,通过它们之间的比例关系求出被测物的高度。如借 助于一长度可测的木杆或人自身的高度,根据物体与影长构 造出两个相似三角形,然后利用相似三角形的性质求得树木或建筑物的高度。 实例:要测一旗杆AB的高度
机械加工余量和锻件尺寸公差的确定
机械加工余量和锻件尺寸公差的确定 (一)主要参数及影响因素 1.锻件重量(G1) 根据锻件图的尺寸计算锻件的重量。对于杆部不参与变形(不锻棒料部分)的平锻件重量只计算 镦锻部分(见图2a)。若不锻棒料部分的长度与其直径之比小于2时,可看作一个完整的锻件来计算其重 量(见图2b)。若平锻件的两端分两次镦锻时,前一道镦锻成形部分连同不锻棒料杆部部分,视为第二道 镦锻部分的不锻棒料部分(见图2c)。 2.锻件形状复杂系数(S) 锻件形状复杂系数为锻件重量(G1)与相应的锻件外廓包容体重量(G2)的比值。即: S= 图2 镦锻件重量计算特点 a)一头一长杆;b)一头一短杆;c)二头一杆; A 镦锻部分; B 不锻棒料部分; C 第一道成形 圆形锻件的外廓包容体重量(见图3): 式中:ρ—密度(7.85/cm3) 图3 圆形锻件的外廓包容体 非圆形锻件外廓包容体重量(见图4):
图4 非圆形锻件外廓包容体 锻件形状复杂系数分为四级: 简单:S1>0.63~1 一般:S2>0.32~0.63 较复杂:S3>0.16~0.32 复杂:S4≤0.16 特例:当锻件为薄形圆盘或法兰件(见图5a),其圆盘厚度和直径之比L/d≤0.2时,取形状复杂系数S4。 当L1/d1≤0.2或L2/d2>4时(见图5b),采用形状复杂系数S4。 当冲孔深度大于直径的1.5倍时,形状复杂系数提高一级。 图5 锻件形状复杂特例 3.锻件的材质系数 锻件的材质系数分为二级: M1:钢的含碳量小于0.65%的碳钢,或合金元素总含量小于3.0%的合金钢。 M2:钢的含碳量大于或等于0.65%的碳钢,或合金元素总含量大于或等于3.0%的合金钢。 4.零件的机械加工精度 零件表面粗糙度低于R a1.6,机械加工余量从余量表查得;粗糙度高于R a1.6,加工余量要适当加大;对扁薄截面或在锻件相邻部位截面变化较大的零件(如图6),在长度L范围内应适当加大局部的余量。 图6 应局部增大余量的零件 5.加热条件