稳定烧结矿碱度的研究
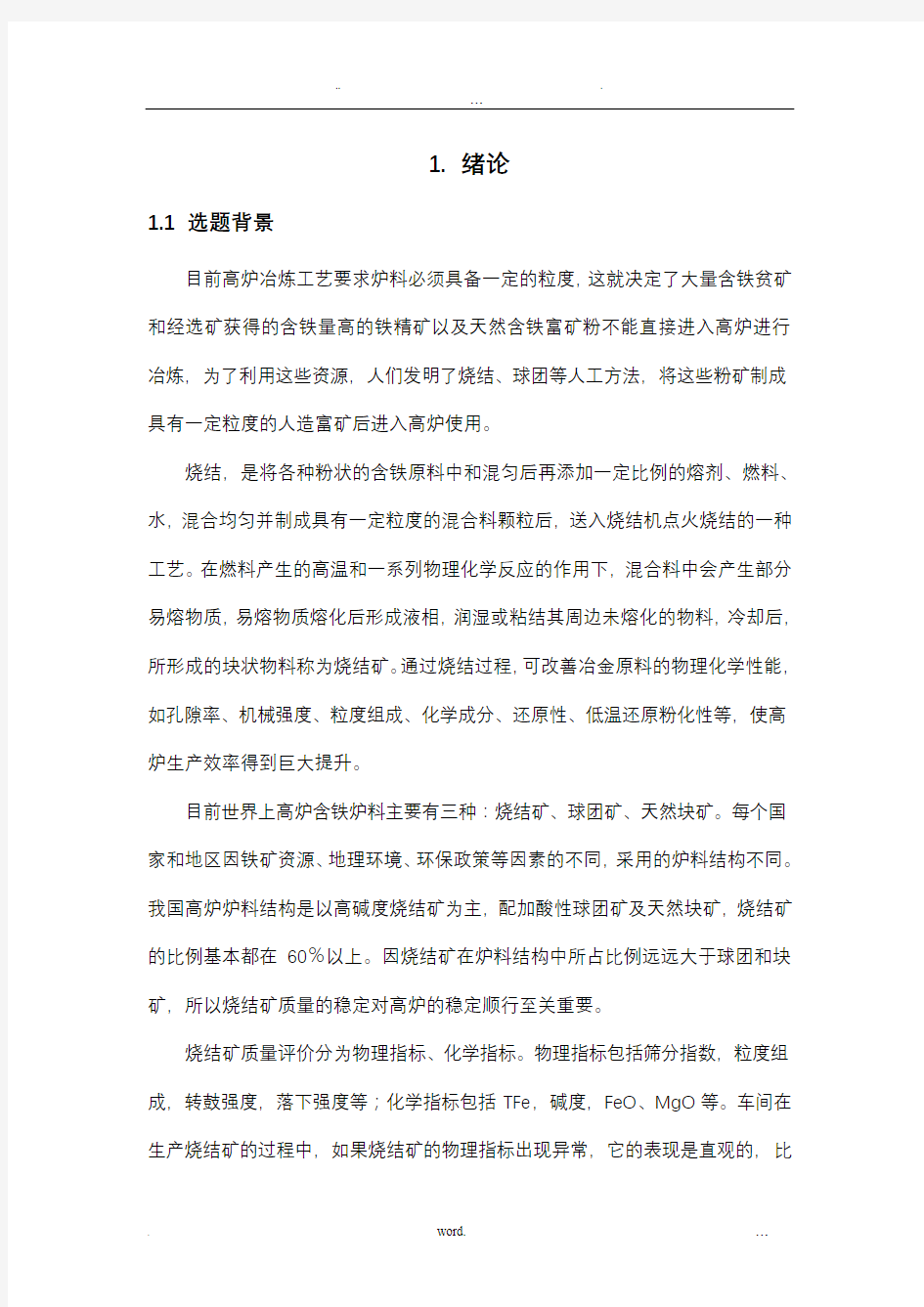

1. 绪论
1.1 选题背景
目前高炉冶炼工艺要求炉料必须具备一定的粒度,这就决定了大量含铁贫矿和经选矿获得的含铁量高的铁精矿以及天然含铁富矿粉不能直接进入高炉进行冶炼,为了利用这些资源,人们发明了烧结、球团等人工方法,将这些粉矿制成具有一定粒度的人造富矿后进入高炉使用。
烧结,是将各种粉状的含铁原料中和混匀后再添加一定比例的熔剂、燃料、水,混合均匀并制成具有一定粒度的混合料颗粒后,送入烧结机点火烧结的一种工艺。在燃料产生的高温和一系列物理化学反应的作用下,混合料中会产生部分易熔物质,易熔物质熔化后形成液相,润湿或粘结其周边未熔化的物料,冷却后,所形成的块状物料称为烧结矿。通过烧结过程,可改善冶金原料的物理化学性能,如孔隙率、机械强度、粒度组成、化学成分、还原性、低温还原粉化性等,使高炉生产效率得到巨大提升。
目前世界上高炉含铁炉料主要有三种:烧结矿、球团矿、天然块矿。每个国家和地区因铁矿资源、地理环境、环保政策等因素的不同,采用的炉料结构不同。我国高炉炉料结构是以高碱度烧结矿为主,配加酸性球团矿及天然块矿,烧结矿的比例基本都在60%以上。因烧结矿在炉料结构中所占比例远远大于球团和块矿,所以烧结矿质量的稳定对高炉的稳定顺行至关重要。
烧结矿质量评价分为物理指标、化学指标。物理指标包括筛分指数,粒度组成,转鼓强度,落下强度等;化学指标包括TFe,碱度,FeO、MgO等。车间在生产烧结矿的过程中,如果烧结矿的物理指标出现异常,它的表现是直观的,比
如整体偏碎、发黄,作为一名有经验的烧结看火工可以较为轻松且准确地通过烧结机尾烧结矿落入单辊前的整体状态以及落入单辊平台时引发的振动和声音判断烧结矿的强度如何,在看火以后沿线的岗位也可以第一时间发现烧结矿物理状态变化并联系上面工序做出调整,对于已经出现的物理指标较差的烧结矿一般都通过单独打入一个烧结成品矿仓,然后在生产正常时以较小流量混入正常烧结矿中送入高炉。因此对于烧结矿物理指标的波动对于高炉来说并不是那么可怕,不是说物理指标对高炉的影响小,而是因它的表现明显,可以被及时发现、调整、处置。当烧结矿的化学指标出现异常时,并不能第一时间通过目测得知;当通过化验发现成分异常时,有可能是从上次取样之后就开始异常了,到这次取样时才发现,意味着有些料可能已经进入高炉了。同时,能引起成分异常的原因在企业生产的环境大多于实验室环境,比如原料自身性质不稳定、中和混匀过程有问题、烧结配料室下料不准确、取样出现偏差、制样过程不标准等等。这些原因需要逐一排查。所以,要降低化学指标波动相对困难很多,主要是因为能引起烧结矿化学指标波动的因素贯穿从原料进场到烧结矿入炉前整个烧结矿生产流程,且呈现出短板效应,即使那些被认为是主要的因素被改善到了极致,一些看起来不太起眼的环节有漏洞,结果还是会功亏一篑。
在烧结矿诸多化学指标中,碱度是最重要的一项。烧结矿的碱度一般指二元碱度,即烧结矿中CaO与SiO2含量的比值,用R表示。稳定烧结矿碱度的意义首先体现在烧结矿质量上,一些研究者认为烧结矿碱度与烧结矿成品率、转鼓强度、低温还原粉化指数等指标存在密切关系[1-6];更为重要的是体现在高炉冶炼过程中。高炉冶炼过程不仅要求铁矿石还原出金属铁,还需要还原出的铁与未还原的脉石熔化,利用它们的密度不同达到分离的目的。铁经渗碳变成铁水,熔化后
的脉石成为炉渣,生铁和炉渣是在高炉生产中同时形成的两种液态产物。高炉炉渣的性质与其碱度有密切关系,不同碱度的炉渣具有不同的黏度、熔化性、稳定性和脱硫能力。以黏度来说,当炉渣黏度过大,阻损大,料柱透气性变坏,造成炉料下降及煤气上升困难,易引起崩料和悬料,同时,渣铁分离不好,渣铁间的反应速度降低等等;当炉渣黏度过小,炉衬容易受侵蚀,高炉寿命缩短。因此,高炉要想稳定顺行、高产高效,炉渣碱度稳定是前提之一。炉渣碱度的稳定取决于入炉料成分的稳定。目前国的入炉料结构大都为高碱度烧结矿+酸性球团矿+天然块矿。烧结矿一般都是主体炉料,比例占60%以上,而且烧结矿是由数种含铁原料加熔剂混合后烧结而成,其成分不稳定程度要大于天然块矿及配比相对单一的球团矿,因此,不管从质还是量看,烧结矿碱度的稳定都会对炉渣碱度的稳定产生最重要的影响。
1.2 影响烧结矿碱度稳定的因素
多年来,烧结工作者们对于常规的影响烧结矿碱度稳定的因素分析得很透彻了,但对于很多烧结厂来说,烧结矿碱度并没有因为他们的知己知彼而百战不殆,很重要的一个原因就是“知道了”不代表“做到了”。闫利娥利用6 sigma管理工具分析了影响太钢烧结矿碱度的因素,找出了17项影响因子[7],如图1.1;郭晓影利用同样的方法分析了影响本钢炼铁厂烧结矿碱度的因素[8],如图1.2。如何把这么多的因素同时控制好,没有先进的管理和技术水平是不可能做到的。从图中可以看出,上述二位分析出的因素有所不同,各因素所占权重也有较大差异,说明影响烧结矿碱度的因素可以参考其它厂,但不能照搬,每个厂与生产相关的各环节都可能存在其独特的地方,所以具体影响因素也会因厂而异。二位的分析很全面,但有的因素看起来比较抽象,比如“其他”因素,所以下面将对一些能显著影
响烧结矿碱度的“其他”因素做具体描述。
图1.1 闫利娥分析的影响碱度稳定的关键因素
图1.2 郭晓影分析的影响碱度稳定的关键因素
(1)腐败。正规厂家生产出的原料其成分虽然有波动,但会在一个较窄的、可控的围。一些情商远高于智商的厂家或者因朝里有人而成立的“厂家”,其产品质量就没那么有保证了。我曾连续查过一个厂家的碳化稻壳(铁水保温剂),固定碳含量严重不合格,同一时间另一厂家送的碳化稻壳固定碳30%-40%,而这一家每次送的大部分在10%-20%,最低的一次仅为6%,直接都烧成灰了。
还有一个厂家的生石灰,当由质检站单方取样检验时,CaO含量就没有低于78%的时候,但当我同质检站双方一起取样并分样分别化验时,数据就没有那么稳定了,最低的一次为60%。更为神奇的是,好几次当我同质检站人员一起取完样后,还没出车间大门,生石灰厂家居然联系到我远在另一个厂的好朋友给我打望照顾。厂家怎么知道我在车间取样?对于这么明显的异常情况,厂里计划针对生石灰上一套全自动取样设备,不过一年多过去了,这套设备还只是个计划。上这套设备看起来不错,但若病根不除,即使上了这套设备也没用,相反,相关人士可以利用这套设备做掩护更好的进行相关活动。因此,对于(不限于)稳定烧结矿碱度,如果有腐败问题则必须先解决腐败问题,之后才能谈技术问题,否则就是空谈,就会陷入天天分析、月月立项、年年亏损的怪圈,而烧结矿成分稳定只能是个美好的愿望。不过,打铁还需自身硬。
(2)检验结果造假。绝大部分烧结厂对于烧结车间有烧结矿指标考核,但如果考核方式不是很科学或者没有健全的防制度的话,就不能不考虑一种可能性:烧结车间联合烧结矿质检一起造假。如果烧结车间因为一些客观因素无法稳定住烧结矿成分(比如腐败),在不科学的考核方式下,车间的形象、利益都大受损失,当厂或者公司层面没有有效的防措施,对于车间来说,作弊是一种最快速有效的止损手段。虽然这样做会导致高炉在出现炉况波动时甚至都查找不出原因,但至少短时间烧结车间名利双收。对于一般人来说,在利益面前,职业道德是可以被忽略的。一些有头脑的人可能还会以此为基础立一些关于烧结矿成分稳定的项目、课题,在不做任何实际工作的前提下,几个月后宣布烧结矿碱度合格率上升了20%,然后结题、评奖、拿钱。而高炉呢?正在悬料和崩料中挣扎。鉴于人类的聪明和人性的弱点,相信这些不仅仅是假设。当一个烧结厂(车间)
原料并不怎么稳定、设备并不怎么先进、管理并不怎么严格、员工还不是机器人,但烧结矿的各项指标合格率非常高,那么就很可能存在问题。
优化考核方式和健全防制度可能比单纯考核带来的那点积极性更有意义,否则,没有人知道被考核的人会把那点积极性用在攻关上还是公关上。
(3)取样代表性。对于稳定烧结矿碱度所做的一切努力,其效果最后都要通过取样检验来反映,因此取样代表性的重要程度甚至大于其它所有稳定烧结矿碱度的措施。这一点对于拥有科学的全自动取制样机[9]的厂家来说不是问题,但对于那些还使用人工取制样的厂家来说,需要注意。我曾参观过某烧结厂的烧结矿检验室,他们的取样过程如下:通过自动取样机取料,为降低取样偏差,每个样本一共取三次,每两次取料间隔10分钟;取完料后人工用一个小铲子从装料的小车取一铲子约1KG左右的料,然后人工将他们认为“不合格”的料挑出去,最后将铲子剩下的料破碎、缩分、研磨、化验。上述取样过程问题很多。首先,样本量太少,而且总的样本不经过破碎混匀缩分,而直接用一铲子来代表,那之前自动取样机分开取三次有什么意义?因为那一铲子只能取到其中一次料的一小部分。这就好比一颗绿豆、一颗黄豆、一颗红豆在一起,化验三颗豆子的综合成分,如果只是取出一颗豆子进行化验,即使操作非常规,那颗豆子都代表不了三颗豆子的整体成分,正确做法应该是先把三颗豆子破碎、混匀后再取一部分进行化验。其次,“不合格”的料如何界定?是否每个检验员的判定标准都一致?最后,当总的样本中“不合格”的料的比例远高于铲子中“不合格”的料的比例时如何处理?
对于烧结矿取样来说,如果没钱或认为没必要上全自动设备,那么一些必要的操作虽然有些累但是不能省略的,比如将总样本破碎混匀;如果既没钱又认为
没必要上自动设备还没有力气或心情人工破碎混匀,起码也要分点分层多取几铲子。当然,不排除他们做过这方面研究发现一铲子的代表性已足够。
(4)二次原料的使用。在烧结、炼铁、炼钢过程中会产生数种含铁二次原料,如除尘灰、瓦斯灰、高炉返矿、钢渣等。这些料一般会通过汽车运至烧结一次料场当作含铁原料重新参与配料。当一次料场场地受限,无法实现各种二次原料单独堆放时,这便会成为一个影响烧结矿碱度稳定的因素。如图1.3,某厂的所有二次原料全都混堆在一次料场的一角,从其色彩搭配上便可看出该料堆的成分均匀性很差,后来该厂针对这个问题采取了一些措施,如每天必须用挖掘机将二次原料堆翻倒混匀。该方法有一定效果,但并不理想。图1.4为用挖掘机翻倒混匀后的二次原料堆。
对于各种二次原料的使用,要尽可能创造条件单独堆放;无法实现所有品种单独堆放的,可将比例最大的品种单独堆放,其余的进行混堆,这样也可很大程度降低挖掘机的工作量以及增加混堆料堆的混匀效果。
图1.3 某厂一次料场二次原料堆
图1.4 用挖掘机翻倒混匀后的二次原料堆
(5)高炉返矿。烧结矿、球团矿、生块矿在入高炉前会过一次筛,将粉末筛除,保证高炉料柱的透气性。这些筛下物称为高炉返矿(以下简称高返)。高返会重新参与烧结,根据设备情况一般有两种方式:1、从烧结配料室直接配加;
2、返回一次料场重新参与混匀料配料。如果采用第1种方式,可能会对烧结矿碱度产生重要影响。高返是三种成分相差巨大的料组成,在振动筛状态不变的情况下,当球团和生块矿的粉末比例发生较大变化时,高返的整体成分也会发生较大变化,进而影响烧结矿的成分。以莱芜分公司炼铁厂二区为例,正常生产时,用的自产球团,-5mm粉末含量一般在1%-2%,当回转窑检修时,该区会外购一些球团,这些球团的-5mm粉末含量有时能达到20%以上。该区使用高返的方式是在烧结配料室直接配加,当高返中球团粉末突增10倍以上时,烧结矿碱度将会偏低。在烧结矿、球团、生块矿粉末比例不变的情况下,当振动筛出现严重磨损时(如断棒),也会造成相应料种的筛下物急剧增多,改变高返的整体成分。
要降低高返成分波动引起的烧结矿成分波动,在条件允许的情况下尽可能将
烧结矿与球团矿的比较
第一节烧结矿与球团矿的比较 烧结和球团都是粉矿造块的方法。但它们的生产工艺和固结成块的基本原理却有很大区别,在高炉上冶炼的效果也有各自的特点。 烧结与球团的区别主要表现在以下几方面: 1、原料条件:球团和烧结对原料条件要求的主要差别在于粒度不同。 1)球团对原料要求严格。要求造球料粒度细(-200网目大于80%),比表面 积大,原料的 品位要高,SiO2含量要少。 2)烧结对原料粒度要求可粗一些,对原料的适应性强。烧结原料中-150目粒 级的应小于 20%,一般SiO2含量要高于5%;可使用富矿粉和钢铁厂的其他副产品,如钢渣、炉尘、轧钢皮、焦粉等都可充分利用。 2、固结成块的机理不同: 1)烧结矿是靠液相固结的,为了保证烧结矿的强度,要求产生一定数量的液相 (一般>25%), 因此混合料中必须有燃料,为烧结过程提供热源。 2)球团矿主要是依靠矿粉颗粒的高温再结晶固结的,要避免产生过多液相 (<5%),防止 球团粘结;热量由焙烧炉内的燃料燃烧提供,混合料中不加燃料。 3、冶金性能: 1)球团矿粒度小而均匀,常温强度高,可作为商品买卖;含铁品位高,氧化度 高,还原性
好;酸性氧化球团的高温性能较差,需要防止还原膨胀率过高。 2)烧结矿是不规则的多孔质块矿,粒度不够均匀,最好分级入炉,运输和贮存 时粉末较多, 一般不作为商品买卖;含铁品位比球团矿低,高碱度烧结矿高温性能较好。4、冶炼效果:二者均属于人造富矿,与天然矿相比,具有含铁品位高、还原性 好、强度合 适、软熔温度高、有害杂质少等的优点。代替天然块矿冶炼时,能大幅度提高产量,改善煤气利用,降低焦比。 5、环境状况:球团矿的生产环境明显优于烧结。 1)球团矿的强度好,粉末少,料层透气性好,抽风负压低,烟气含粉尘量少, 除尘负荷轻, 排人大气的粉尘就少。 2)由于烧结是以固体燃料为主,与气、液体燃料相比,其含硫量较高,挥发分 中又含有氮。 1、设备投资和生产费用 带式焙烧机和链箅机—回转窑比带式烧结机设备复杂、庞大,加之增加了原料细磨与造球设备,因而球团的建厂投资费用要高于烧结。一般生产单位质量的球团矿比烧结矿的建厂投资约高15%左右。就生产费用而言,球团和烧结各有高低。球团磨矿和供风系统电耗高,但余热利用率高,热能消耗少,总能耗低于烧结。而烧结的维修费用比球团要少,从综合生产费用看,球团略高于烧结,但按含铁量计算,球团又比烧结略低一些。
在线分析控制烧结矿碱度
在线分析控制烧结矿碱度 发表时间:2017-03-16T15:03:07.600Z 来源:《科技中国》2017年1期作者:李振超 [导读] 安装在线分析仪,通过实时元素测量,优化熔剂的最优加料量,从而最终保证生产出碱度波动更稳定的烧结矿。 (唐山中厚板板材有限公司063000) 【摘要】安装在线分析仪,通过实时元素测量,优化熔剂的最优加料量,从而最终保证生产出碱度波动更稳定的烧结矿。 【关键词】分析仪碱度滤波通讯 一、分析仪的应用 1、分析仪安装在某钢铁厂240m2烧结机混合料皮带上,通过实时元素测量,优化熔剂的最优加料量,从而最终保证生产出碱度波动更稳定的烧结矿。 2、分析仪测定的各元素含量为烧失后元素含量。 3、主要控制元素的大概范围为:TFe:47~60%,SiO2:3~8%,CaO:6~14% 4、其他元素的大概范围为:TiO2:0~2%,Al2O3:0.6~5%,MgO:0.5~4%,K2O: 0~0.5%,Na2O:0~0.5%,ZnO:0~0.1%,Cl:0~0.1%。 5、分析仪组成:分析仪本体、电控箱、操作员控制台、 6、现场安装图例: 二、软件编程整体方案描述 1.通讯接口 OPCON到工厂局域网/控制系统的通讯(工厂接口) CB OMNI ELITE-S系统有能力在OPCON操控端和现在工厂控制系统或者第三方工艺控制包之间提供接口和交换信息。如果需要实现自动工厂控制,那么就有必要提供工厂接口。工厂接口提供一个可靠而省钱的方法,能够将原材料质量信息和工艺控制指令整合在一起。连接到工厂控制系统的通讯连接可以通过以下四种方式中的一种(或者必要的话,一种结合)。目前有的四种选项是:通过OPC协议和PLC网络或局域网的直接接口 模拟信号,使用Thermo Fisher提供的现场通讯单元(FIU) 串口接口,使用Thermo Fisher的“O-LINK”。 直接到Windows NT局域网的接口,使用ODBC格式。 2.软件编程整体方案 烧结配料的过程中,保证每个仓的精准下料量是十分关键的,保证单仓的下料量,既可以用设定输出百分数(0-100%)的形式,使下料量稳定在一个范围,但是如果操作人员想要变料时,就不太方便了,为此还可以直接设定下料量,程序内部会自动计算设定与反馈的偏差,根据偏差的大小,利用PID的调节参数:比例,积分,微分调节参数来控制输出的快慢,使之能在最短时间内,稳定在设定下料量左右,控制误差在0.5%之内, 为此程序首先对现场采集的数据进行动态分析,去掉干扰和不正常的数据,利用数组存储后期要用到的正常数据,对每个仓的下料量进行实时跟踪,以及下料量的水分跟踪,干料进行跟踪, 经过皮带,一混\二混,一直追踪到混合料仓料位,以便后面水分控制和分析仪采集数据进行成分对比分析,此次分析仪应用在国内炼铁烧结工艺上,尚数首次,因此结合分析仪的优势和一级控制计算,它的控制理念是十分先进的.对精矿粉、生石灰、灰石下料量和各自配比实时跟踪的数据到达分析仪时,分析仪进行射线采集,进行化验成分分析,分析仪将数据通过通讯传到PLC,PLC对分析仪采集的数据(Tfe、SiO2、CaO)进行周期滤波,去除不正常的数据,对滤波之后的数据建立半个小时数组进行跟踪,通过对跟踪的数据进行优化,存储混合料半个小时Tfe、SiO2、CaO的数据,在和标准标块下得出的数据进行比较,如果大于标值,则减少石灰石的下料量(减小灰石配比),反之,则增加石灰石的下料量。另外,烧结专家系统二级通过烧透模型计算返给一级的各种配料配比,和分析仪返给一级的配料配比进行优化对比,生产工艺的中控操作人员可选择接受与否。 三、应用达到的技术效果 1、在线分析仪CB Omni Elite-S对烧结混合料提供准确、实时的分析结果,相应的配料软件根据分析结果对物料配比进行优化计算,
烧结矿冶金性能的有关参数
烧结矿冶金性能的有关参数 一、低温还原粉化性能 (1)RDT-3.15 30%时RDT+6.3一般在41%左右 这个范围的低温还原粉化性能有一定恶化,但仍处在可维护中、小高炉冶炼所允许的范围之内。 (2)RDT-3.15 20—25%时RDT+6.3一般在60—50% 这个范围基本能满足较高冶强的顺行要求。 (3)RDT-3.15 17—19%时RDT+6.3一般在67—63% 这个范围的低温还原粉化性能应该说非常好,非常有利于改善高炉块状带的透气性,但要注意对还原性能的检验,还原度不能低于75%。 (4)RDT-0.5一般在6—7%范围 一般烧结矿中磁铁矿和硅酸铁含量的增加,有利于改善低温粉化性能,同时随着FeO%含量的相应提高(从6%逐步提高到12%以下)也有利于低温还原粉化性能的改善。 二、烧结矿的还原性能 还原度RI(900℃时)在75—80%左右时,应该是比较好的还原性能指标。 凡还原度的降低都不利于降低高炉冶炼燃料比,一般情况下,当采取减少低温粉化率措施的同时,还原度相应降低,它往往也与难还原的磁铁矿和硅酸铁含量的增加有关,FeO%>10%RG,还原度也会出现明显的降低趋势。 三、烧结矿荷重软化性能 一般烧结矿碱度在 1.85±0.1条件下,软化的开始温度在1200—
1220℃,软化终了温度在1320—1330℃,软化温度区间在110—120℃,凡软化温度区间(T2—T1)变小,对降低高炉软熔带的透气性是有利的。反之,如果软化开始温度↓软化温度区间自然变大,不利于软熔带透气性的改善,一般影响烧结矿荷重软化性能,主要有两个因素: 一是烧结矿的还原性能:烧结矿还原性能的改善有利于烧结矿在升温过程中形成液相的温度升高,导致烧结矿的软化开始温度升高。 二是烧结矿中脉石的熔点,在烧结矿碱度基本不变的条件下,烧结矿中脉石的熔点不变,R2低熔点低,R2高熔点高。
稳定烧结矿碱度的研究
1. 绪论 1.1 选题背景 目前高炉冶炼工艺要求炉料必须具备一定的粒度,这就决定了大量含铁贫矿和经选矿获得的含铁量高的铁精矿以及天然含铁富矿粉不能直接进入高炉进行冶炼,为了利用这些资源,人们发明了烧结、球团等人工方法,将这些粉矿制成具有一定粒度的人造富矿后进入高炉使用。 烧结,是将各种粉状的含铁原料中和混匀后再添加一定比例的熔剂、燃料、水,混合均匀并制成具有一定粒度的混合料颗粒后,送入烧结机点火烧结的一种工艺。在燃料产生的高温和一系列物理化学反应的作用下,混合料中会产生部分易熔物质,易熔物质熔化后形成液相,润湿或粘结其周边未熔化的物料,冷却后,所形成的块状物料称为烧结矿。通过烧结过程,可改善冶金原料的物理化学性能,如孔隙率、机械强度、粒度组成、化学成分、还原性、低温还原粉化性等,使高炉生产效率得到巨大提升。 目前世界上高炉含铁炉料主要有三种:烧结矿、球团矿、天然块矿。每个国家和地区因铁矿资源、地理环境、环保政策等因素的不同,采用的炉料结构不同。我国高炉炉料结构是以高碱度烧结矿为主,配加酸性球团矿及天然块矿,烧结矿的比例基本都在60%以上。因烧结矿在炉料结构中所占比例远远大于球团和块矿,所以烧结矿质量的稳定对高炉的稳定顺行至关重要。 烧结矿质量评价分为物理指标、化学指标。物理指标包括筛分指数,粒度组成,转鼓强度,落下强度等;化学指标包括TFe,碱度,FeO、MgO等。车间在生产烧结矿的过程中,如果烧结矿的物理指标出现异常,它的表现是直观的,比
如整体偏碎、发黄,作为一名有经验的烧结看火工可以较为轻松且准确地通过烧结机尾烧结矿落入单辊前的整体状态以及落入单辊平台时引发的振动和声音判断烧结矿的强度如何,在看火以后沿线的岗位也可以第一时间发现烧结矿物理状态变化并联系上面工序做出调整,对于已经出现的物理指标较差的烧结矿一般都通过单独打入一个烧结成品矿仓,然后在生产正常时以较小流量混入正常烧结矿中送入高炉。因此对于烧结矿物理指标的波动对于高炉来说并不是那么可怕,不是说物理指标对高炉的影响小,而是因它的表现明显,可以被及时发现、调整、处置。当烧结矿的化学指标出现异常时,并不能第一时间通过目测得知;当通过化验发现成分异常时,有可能是从上次取样之后就开始异常了,到这次取样时才发现,意味着有些料可能已经进入高炉了。同时,能引起成分异常的原因在企业生产的环境大多于实验室环境,比如原料自身性质不稳定、中和混匀过程有问题、烧结配料室下料不准确、取样出现偏差、制样过程不标准等等。这些原因需要逐一排查。所以,要降低化学指标波动相对困难很多,主要是因为能引起烧结矿化学指标波动的因素贯穿从原料进场到烧结矿入炉前整个烧结矿生产流程,且呈现出短板效应,即使那些被认为是主要的因素被改善到了极致,一些看起来不太起眼的环节有漏洞,结果还是会功亏一篑。 在烧结矿诸多化学指标中,碱度是最重要的一项。烧结矿的碱度一般指二元碱度,即烧结矿中CaO与SiO2含量的比值,用R表示。稳定烧结矿碱度的意义首先体现在烧结矿质量上,一些研究者认为烧结矿碱度与烧结矿成品率、转鼓强度、低温还原粉化指数等指标存在密切关系[1-6];更为重要的是体现在高炉冶炼过程中。高炉冶炼过程不仅要求铁矿石还原出金属铁,还需要还原出的铁与未还原的脉石熔化,利用它们的密度不同达到分离的目的。铁经渗碳变成铁水,熔化后
烧结矿的碱度计算
烧结矿的碱度计算 设计时配料计算与现场配料计算相比有以下的不同点:1)原料化学成分要齐全准确,计算前要调整到各成分的数量之与为100%;2)各配料比的总与应为100%;3)选用经验数据应可靠,计算力求准确;4)烧结矿的碱度使得高炉炉料中不添加或少添加石灰石。 烧结矿的碱度就是根据高炉冶炼时规定的炉渣碱度来确定的。高炉的炉渣碱度主要决定于入炉原料的碱度。在单一烧结矿入炉的条件下,炉渣的碱度则决定于烧结矿。由于炉渣碱度要求一定,烧结矿的碱度也应一定。最理想的烧结矿碱度应使高炉炉料中不再加入石灰石,炉渣的碱度就达到规定的要求,这种烧结矿称为自熔性烧结矿。有些炼铁厂,高炉炉料配比中有较多的天然矿石,为了不加或少加石灰石,使用高碱度烧结矿,这种烧结矿也称为熔剂性烧结矿。 烧结矿碱度有以下几种表示法: R为烧结矿碱度,CaO,MgO,SiO2,Al2O3,,为烧结矿中各成分的含量%、在原料中Al2O3及MgO含量波动不大的情况下,采用(3)式表示,只有Al2O3或MgO波动较大的情况才用(1)或(2)式。对于我国大多数烧结厂来说,其原料中的Al2O3及MgO都比较稳定,因此采用CaO/SiO2表示烧结矿的碱度。 自熔性烧结矿碱度可由以下步骤计算: 设烧结矿的碱度为R 炉渣的碱度为R′ 混合矿含铁Fe矿% 生铁含铁Fe生铁% 混合矿含CaO及SiO2为CaO矿及SiO2矿% 焦炭含CaO及SiO2为CaO焦及SiO2焦% 高炉焦比K千克/100千克生铁 1)每100千克生铁消耗的混合矿量为:
该式没有考虑生铁中Si要消耗SiO2,,也没有考虑到石灰石及焦粉配入烧结料中带入的SiO2,当焦比低时,生铁中含Si较高时误差较大,若考虑生铁中的Si消耗SiO2,以及焦粉带入的SiO2,则烧结矿的碱度应按下式计算: 式中K′———每100千克烧结矿消耗的焦粉千克数; SiO2焦′———焦粉中含SiO2; A———每千克生铁消耗的烧结矿千克数。 举例:高炉炉渣的碱度为1、05,生铁含Fe为94%,含Si为0、7%、混合矿含Fe为53%,SiO2为9、47%,每100千克烧结矿的焦粉消耗7、5千克。焦炭灰分为11、38%,其中CaO5、32%,SiO245、12,高炉焦比为575千克。 由(4)式可知:
(完整word版)烧结工(高)计算
1、(高级工,计算题,中等,无,辅助要素,标准库) 我厂1#2#两台烧结机上料量为80Kg/m,皮带速度为1.5m/s,混合料烧损为25%,能返矿为9Kg/m,皮带速度为1.75m/s,求烧结机台时产量? 解:烧结机台时产量=(上料量×皮带速度×开机时间×残存+冷返量×皮带速度×开机时间)/2×1000×开机时间 =(80×1.5×60×60×75%+1175×9×3600)/2×1000×1 =190.35t/台.h 2、(高级工,计算题,较易,无,辅助要素,标准库) 我厂3#抽烟机电机功率为3250kw,问风机空转8小时耗电为多少kw.h? 解:耗电=功率×时间=3250kw×8h=26000kwh 3、(高级工,计算题,较难,无,辅助要素,标准库) 我厂3#烧结机烧结有效面积为130m2,4月份设备故障率为12%,电器故障率为5%,操作故障率为3%,外部影响为7%,若全月产量为6.7万吨,试求3#烧结机利用系数为多少? 解:先求出作业时间作业时间 =日历时间×作业率=日历时间×(100%-故障率) =24×30×(100-12-5-3-7)% =720×73% =525.6小时 利用系数=台时产量/有效面积=烧结矿产量/(开机时间×面积)
=67000t/(525.6×130m2) =0.98t/(台m2h) 4、(高级工,计算题,中等,无,辅助要素,标准库) 我厂3#烧结机有效面积为115m2,4月份产量为13.6万吨、烧结机开机时间为700小时,计算烧结机的利用系数和作业率(全月30天)? 解:烧结机利用系数=产量/(开机时间×烧结机有效面积) =(13.6×105吨)/(700小时×115m2) =1.69吨/小时·m2 烧结机作业率=实际开机时间/日历时间×100% =700/(24×30)×100% =97.2% 5、(高级工,计算题,中等,无,辅助要素,标准库) 我厂配17皮带速度为64.2m/min,当每米皮带上料量为55kg时,12小时输送物料量为?(3分) 解:皮带12小时送料量=上料量×皮带速度×上料时间 =55kg/m×64.2m/min×12×60min =2542t 6、(高级工,计算题,难,无,辅助要素,标准库) 要求R=2.2,烧结用原燃料成分如下: H 2O 烧损 TFe SiO 2 MgO CaO 配比 混匀料 10 8 63.5 4.5 2.0 80 白灰 10 2.5 84.5 焦粉 14 85 6.5 5
烧结配料计算
烧结配料计算的方法 烧结过程是一个非常复杂的氧化还原过程,氧的得失很难确定,原料成分的波动和水分的大小均会对最终结果产生影响,而要精确进行烧结配料的理论计算,在烧结生产中显得尤为麻烦,并且要占用大量的时间,所以,现场配料计算一般多采用简易计算方法,即:反推算法。 所谓反推算法是先假定一个配料比,并根据各种原料的水分、烧损、化学成分等原始数据,计算出烧结矿的化学成分,当计算结果符合生产要求,即可按此料比进行组织生产,如果不否,再重新进行调整计算,直至满足生产要求为止。如果在实际生产中,所计算的配比和实际有误差,可分析其产生误差的原因,并再次进行调整计算。生产中如何确定配料比,也是大家所关心的一个问题,实际上配料比的确定常常是根据炼铁生产对烧结矿的质量指标的要求和原料供应状况以及原料成分等,并结合生产成本进行合理的搭配,反复计算,得出最终使用的配料比。 一、在进行反推算法计算时,首先要了解有关配料方面需要掌握的一些术语。 1、烧损:物料的烧损是指(干料)在烧结状态的高温下(1200—1400摄氏度)灼烧后失去重量对于物料试样重量的百分比。 2、烧残:物料的残存量即物料经过烧结,排出水分和烧损后的残存物量。 3、水分:烧结原料的水分含量是指原料中物理水含量的百分数,即一定的原料(100g—200g)加热至150摄氏度,恒温1h,已蒸发的水分重量占试样重量的百分比。 4、化学成分:原料的化学成分是指某元素或化合物含量占该种干原料试样重量的百分比。 二、具体计算公式 1、烧残量=干料配比×(1—烧损) 2、进入配合料中的TFe=该种原料含TFe 量×该种原料配比 3、进入配合料中的SiO2=该种原料含SiO2量×该种原料配比 4、进入配合料中的CaO=该种原料含CaO量×该种原料配比 5、进入配合料中的MgO=该种原料含MgO量×该种原料配比 6、进入配合料中的Mn=该种原料含Mn量×该种原料配比 7、烧结矿的化学成分 烧结矿TFe=各种原料带入的TFe之和÷总的烧残量烧结矿SiO2=各种原料带入的SiO2之和÷总的烧残量烧结矿CaO=各种原料带入的CaO之和÷总的烧残量烧结矿MgO =各种原料带入的MgO之和÷总的烧残量烧结矿Mn=各种原料带入的Mn之和÷总的烧残量如果还有其他指标要求,其计算公式同上。 三、配料计算 配料计算是以干料来进行计算的,目前有两种方法,一种是使用干配比配料,一种是使用湿配比配料,但其目的都是一样的,现在各个单位大部分都是用湿配比进行配料,由于无法上传计算表,这里只好省略了,有机会再给大家上传哦如果还有其他成分需要计算,可参照上述计算公式进行计算,直至符合本公司对烧结生产的要求为止,以上配料计算的大致步骤,仅供参考。 烧结配料计算的主要公式 1. 干料配比=湿料配比*(100-水分)% 2. 残存量=干料配比*(100-烧损)% 3. 焦粉残存=焦粉干料配比*(100-烧损)%=焦粉干配比*灰分% 4. 烧结残存率=(总残存/总干料)*100%
高炉炉渣碱度计算
浅谈炉渣碱度计算 摘要:通过计算机办公软件Microsoft Excel 编辑公式计算和分析炉渣碱度,并对现在玉钢炼铁作业区高炉工长核料计算提出改进意见。 关键词:碱度Excel 核料 The basicity on slag calculation Kang yun Abstract:through the computer software for office use Microsoft Excel edit formula calculation and analysis the basicity slag, and now working in the blast furnace ironmaking jade steel foreman nuclear material calculation improvements. Keywords: alkalinity Excel nuclear material 一、概论 玉钢炼铁作业区于2005年2月28日开炉投产,现有450m3高炉两座,1080m3高炉一座。开炉后高炉操作沿用昆钢老厂的核料计算,采用每批料需加石灰石量来作为碱度调整的依据,进行核料计算。由于现在炉料结构的变化,碱度调剂采用改变烧结矿和酸性炉料之间配比的方法,取代石灰石调整碱度。原来的核料计算已经不适应现在的生产需求,因此,探索和寻找新的核料方法具有重要的意义。 二、炉渣配料计算 1、Microsoft Excel 简介 Microsoft Excel是微软公司的办公软件Microsoft Office 的组件之一,是微软公司为Windows操作系统编写的一款表格处理软件,它可以进行各种数据的处理,统计分析和辅助决策操作,广泛地应用于管理、统计、金融等众多领域。 本文才用Excel的公式编辑计算炉渣碱度和炉料结构中烧结矿和球团矿的理论配比。解决原料大幅度变化时的配料计算。 2、核料计算 计算方法为:每批料所需的石灰石量=[(入炉点的SiO2量-还原生铁中的
烧结矿碱度调整操作管理制度
烧结矿碱度调整操作管理制度 一、操作制度 1、原料成分稳定:铁料SiO2含量波动幅度在±0.3%内,石灰粉中CaO 的含量波动幅度在±2%内; 2、流量稳定:各种原料波动幅度在±2%内,总料比波动幅度在±3%内; 3、冷返矿量占总料比(含冷返)20%内,白云石配比在5%以内。 4、计算 A、铁料比G B、碱度指标R0 C、前三批检测的SiO2平均值S,当天石灰粉中CaO的含量C D、修正值为0.7 E、石灰粉调整配比量X F、碱度调整公式: X=S* R0*G*0.7/C 5、铁料中SiO2含量波动幅度在±0.3%以上,或连续三批上下波动无规律可循,则烧结矿中SiO2含量S的值由前面5批结果的平均值进行计算; 6、石灰粉中CaO的含量波动幅度在±3%以上,则石灰粉中CaO的含量C 的值为前三天内的平均值进行计算; 7、冷返矿量占总料比25%以上,冷返矿百分比在20%的基础上每增加5%增加1吨石灰粉,为平衡冷返矿量中CaO的含量所加的石灰粉,必须在147分钟加上冷返矿仓存量消耗时间之后回调石灰粉,回调量为平衡冷返矿量中CaO所加的量。 8、白云石配比和高返配比调整时,修正值要作相应的调整。 9、调整后的信息反馈 (1)加减石灰粉由配料作业长决定,必须通知主控室; (2)主控室必须在40分钟后,把生产情况如:机速、透气性、烧结液相等与前期比较反馈给配料;
(3)配料根据主控室反馈的信息进行跟踪,加减石灰粉是否到位。(4)在流量、水、碳稳定的前提下,机速、透气性发生明显变化时,要及时与配料取得联系,对各石灰粉情况进行检查; (5)配料如发现石灰粉质量发生明显变化,及时进行调整,并与主控室取得联系。 二、考核制度 1、碱度±0.1每班全部达标,奖励配料横班10元/批,碱度±0.05每班全部达标,奖励配料横班30元/批; 2、一个班出现碱度不达标,第一批考核配料横班30元,第二批考核配料横班50元/批; 3、出现连续三批(含三批)以上不达标,直接考核配料横班100元/批,衔接班出现连续三批(含三批)以上不达标,由上班承担主要责任; 4、碱度超过执行标准±0.2以上,扣100元/批,连续两批考核车间主任100元,情况严重按事故处理; 5、碱度±0.1合格率大于88%,奖励车间主任300元,技术员200元,碱度±0.1合格率小于85%,扣罚车间主任300元,技术员200元;碱度 ±0.05合格率大于65%,奖励车间主任500元,技术员300元。 6、如发现操作、记录中存在弄虚作假行为将对责任人严厉考核。 二炼铁厂 2006-10-19
烧结矿的质量评价及检验方法
烧结矿的质量评价及检 验方法 文稿归稿存档编号:[KKUY-KKIO69-OTM243-OLUI129-G00I-FDQS58-
烧结矿的质量评价及检验方法 摘要:由粉矿和高品位铁精矿生产的烧结矿是目前高炉炼铁的优选原料。随着高炉炉料中烧结矿比例的增加以及高炉不断的大型化,对烧结矿质量的要求越来越高。尤其需要生产粒度尽可能大和机械强度高的烧结矿。 关键词:烧结矿质量评价;烧结矿质量的检验方法。 1、前言: 21世纪钢铁工业将继续发展和进步,钢铁材料仍是最主要的结构材料和用量最大的工程材料。烧结矿作为我国高炉的主要原料,随着钢铁产量的日益增加,对烧结矿的质量要求越来越大,因此烧结矿的质量就显得尤为重要,烧结矿的质量要求主要包括化学成分、物理性能与冶金性能三方面内容。 2、烧结矿的质量评价及检验指标: 具体的质量评价与检验指标主要有:化学成分及其稳定性、粒度组成与筛分指数、转鼓强度、落下强度、低温还原粉化性、还原性、软化-软熔特性等。化学成分及其稳定性:化学成分主要检测:TFe,FeO,CaO,SiO2,MgO,Al2O3,MnO,TiO2,S,P等,要求有效成份高,脉石成份低,有害杂质(P、S等)少。 烧结矿化学成分稳定是高炉顺行的前提条件。烧结矿含铁量和碱度波动会引起高炉炉温和造渣制度波动,严重时会引起悬料、崩料等现象,使冶炼过程难以操作,导致焦比升高,生铁产、质量下降。烧结矿品位高低及波动大小,对高炉冶炼的影响很大。品位提高,单位炉容装入的铁量增加,高量减少,有利于提高高炉利用系数和焦比降低。鞍钢高炉生产实践
证明,烧结矿品位提高1%,可降低焦比2%,高炉增产3%。 2.1粒度组成与筛分指数: 筛分指数:取100Kg试样,等分为5份,用筛孔为5X5的摇筛,往复摇动10次,以lt;5mm出量计算筛分指数:C=(100-A)/100*100,其中C为筛分指数,A为大于5mm粒级的量。 粒度组成:烧结矿中小于5毫米粉末每增加10%,高炉减产6%~8%,焦比升高。烧结矿均匀,可以增加料柱空隙度,增加透气性和改善气流分布,有利于增产节焦。 2.2落下强度: 评价烧结矿冷强度,测量其抗冲击能力,试样量为20±0.2Kg,落下高度为2m,自由落到大于20mm钢板上,往复4次,用10mm筛分级,以大于10mm的粒级出量表示落下强度指标。F=m1/m2X100,其中F为落下强度,m1为落下4次后,大于10mm的粒级出量,m2为试样总量。F=80~83为合格烧结矿,F=86~87为优质烧结矿。强度好的烧结矿有利于强化高炉的冶炼。烧结矿在运往炼铁,装入高炉的过程中及在炉内的运动都受到冲击、摩擦、挤压等作用而使其破碎。强度差的烧结矿产生大量的粉末,使炉料透气性恶化,破坏顺行,影响生产。 2.3转鼓强度: 转鼓强度反映了烧结矿耐冲击、耐挤压、耐磨的能力。a.高碱度烧结矿的转鼓强度随FeO含量的增加而降低,采取低配炭烧结,把焦粉配比控制在5%一6%之间.以降低烧结还原气氛。b.改善熔剂和焦粉的粒度,使粒度在3一ornm达90%以上。C.稳定返矿圆盘的热返矿量,加强圆筒混合制粒,严格控制混合料水分。d.严格布料工艺,做到料面平整,不拉钩,布料不宜过紧过松,以反射板1/3锉料适宜。及时清理混合料仓四周粘料,保证料仓2/3仓料以上。e.加强同燃调的联系,保证点火煤气的发热值不低于6500kJ/m3,保证点火温度在(11。。士5。)C,以提高烧结矿表层质量。f.配加少量钢渣、轧钢皮等,提高液相量。
高品位烧结矿的研究与发展
高品位烧结矿的研究与发展 张瑞堂刘振林陈松 (济钢集团有限公司科技质量部,济南 250101) 摘要本文主要介绍了近年来国内外高品位烧结矿的研究和技术方面取得的长足进步,主要体现在瑞典皇家工学院的Edstrom等人的高铁高氧化钙烧结矿、高铁高氧化镁优化烧结矿的技术开发以及以SFCA为代表的优质粘结相生成理论研究等方面。 关键词高品位烧结 SFCA 开发 The Investigation and Progress of High Grade Sinter Zhang Ruitang Liu Zhenlin Chen Song (Technology and Quality Department of Jinan Iron and Steel Co, Jinan , 250101) Abstract The paper introduces the great progress of technology and latest studies of high grade sinter domestic and overseas. The progress mainly noted as the technology development about high iron content high CaO sinter, high iron content high MaO sinter and the theoretics of high quality bonding phrase formation such as SFCA in Sweden's Royal Institute of Technology was discussed. Key words high grade, sinter, SFCA, development 长期以来,高炉冶金工作者,希望生产一种含铁量很高的炉料,以获得高炉生产低渣量,低燃料消耗。当球团矿含铁量超过66%时,高炉使用效果很好。因此,冶金工作者们很希望生产出含铁量超过60%~61%并具有满足高炉生产需要的烧结矿。在这种希望下,瑞典皇家工学院Edstrom等人开始研究生产“优化烧结矿” 并取得了长足的进展。“优化烧结矿”的含义是:具有高的含铁量(65%~66%)和自熔性。 1 高品位烧结矿的开发 高品位烧结矿的研究与生产主要集中在北欧国家和钢铁厂,其中研究成果最突出的是瑞典皇家工学院的Edstrom等人。他们从1986年下半年开始,在皇家工学院和Oxelosund钢厂的实验室中,使用大约装150kg 混合料的烧结杯上进行研究高品位烧结矿的各种工艺方案,主要包括:磁铁精矿、赤铁矿(精矿)以及磁—赤混合精矿生产“优化烧结矿”。在实验中,各种实验流程见图1。 张瑞堂,男,工学学士,高级工程师,从事炼铁工艺技术管理。 刘振林,男,硕士,高级工程师,从事铁前系统工艺技术管理,jglzl@https://www.360docs.net/doc/537682685.html,。 陈松,男,学士,工程师,从事科技管理工作。
矿物组成、结构及其对烧结矿高高质量地影响
烧结矿是烧结过程的最终产物,是许多种矿物的复合体,矿物组成非常复杂。影响烧结矿矿物组成的因素包括:燃料用量、烧结矿碱度、脉石成分和添加物种类以及操作工艺条件等。烧结矿中各矿物通过自身的强度和还原性影响烧结矿的强度和还原性。 5.5.4.1 烧结矿的矿物组成 由于原料条件和烧结工艺条件不同,烧结矿的矿物组成不尽相同,但是总是由含铁矿物及脉石矿物两大类组成的液相粘结在一起的。酸性烧结矿矿物主要为磁铁矿、赤铁矿、浮氏体、金属铁、铁橄榄石、钙铁橄榄石、玻璃体、铁酸钙、硅钙石、石英等;主要胶结物为铁橄榄石和少量的钙铁橄榄石、玻璃体等。 自熔性烧结矿矿物主要为磁铁矿、赤铁矿、浮氏体、金属铁、钙铁橄榄石、橄榄石类、铁酸钙、硅酸钙、钙铁辉石、钙铁辉石-钙镁辉石固溶体、石英、石灰等;主要胶质物为钙铁橄榄石、玻璃体等。 高碱度烧结矿的矿物主要是磁铁矿、赤铁矿、钙质浮氏体、铁酸钙和硅酸二钙等;主要胶质物为铁酸二钙。 当烧结矿脉石中含有较多的Al2O3或烧结料中Fe2O3较多时,粘结相还有铝黄长石、铁铝酸四钙、铁黄长石、钙铁榴石(3CaO·Fe2O3·3SiO2)。MgO含量较多时会出现钙镁橄榄石、镁黄长石、镁蔷薇辉石等。脉石中含有萤石时,烧结矿中则含有枪晶石。烧结含钛铁矿时会出现钙钛石(CaO·TiO2,3CaO·2TiO2)、梢石(CaO·TiO2·SiO2)。 对某一烧结矿来说,不一定全部含有上述矿物,而且数量也不相等。磁铁矿和浮氏体是各种烧结矿的主要含铁矿物,非铁矿物以硅酸盐类矿物为主。表5-6给出了武钢不同碱度烧结矿的矿物组成。 表5-6 武钢不同碱度烧结矿的矿物组成 烧结矿矿物组成,(体积)%
烧结矿质量波动原因及稳定措施
烧结矿质量波动原因及稳定措施 一、铁精粉 现在国内粉配加比例为30%~35%,在原料配比中当国内粉中的SiO2每波动1%时烧结矿碱度波动是±0.1%,当CaO每波动1%时烧结矿碱度波动为±0.05%。 1、铁精粉化学成分波动趋势图。 表1:1日铁精粉成分曲线表: 1日烧结矿中SiO2最小值6.1,最大值8.5相差2.4;CaO最大值4.2,最小值0.1,相差4.1. 表2:2日铁精粉成分曲线表:
2日烧结矿中SiO2最小值5.9,最大值8.1相差2.2;CaO最大值0.9,最小值0.5,相差0.4. 表3:3日铁精粉成分曲线表: 3日烧结矿中SiO2最小值5.6,最大值7.6相差2.0;CaO最大值0.6,最小值0.3,相差0.2.
表4:4-5日铁精粉成分曲线表: 4-5日烧结矿中SiO2最小值6.1,最大值7.9相差1.8;CaO最大值2.3,最小值0.4,相差1.7. 表5:6日铁精粉成分曲线表: 6日烧结矿中SiO2最小值6.3,最大值8.3相差2.0;CaO最大
值1.7,最小值0.3,相差1.4. 表6:7日铁精粉成分曲线表: 7日烧结矿中SiO2最小值6.0,最大值8.5相差2.5;CaO最大值1.2,最小值0.3,相差0.8. 表7:8日铁精粉成分曲线表:
8日烧结矿中SiO2最小值5.8,最大值9.5相差3.7;CaO最大值1.6,最小值0.3,相差1.6. 2、措施: ①提高碱度稳定率。 每次铁精粉上料时,在配料矿槽上的铁3皮带取样,料头和料尾各一个。根据化验结果和配料矿槽仓存情况,及时调整配比,提高碱度稳定率。负责人:配料班长、主控,监督人:当班值班工长。 ②减少化学成分波动的影响。 在条件允许的情况下,成分不稳定的铁精粉参加造堆。负责人:罗展远。 二、熔剂 我厂熔剂要求粒度<3mm的所占比例大于85%(方眼筛子);工艺要求<3mm的所占比例大于90%(园眼筛子)。
烧结配料的计算调整
烧结配料的计算调整 一、现场简易计算调整 1、干料配比=湿料配比×(100-水分)% 2、残存量 =干料配比×(100-烧损)% 3、焦粉残存=焦粉干料配比×(100-烧损)% =焦粉干料配比×灰分 4、烧结矿残存率=(总残存量÷总干料量)×% 5、进入配合料中TFe=原料含铁量×干料配比 SiO2=原料SiO2含量×干料配比 CaO=原料CaO含量×干料配比 6、烧结矿碱度R的工业计算 R2=(CaO矿×矿石量+ CaO灰×灰石量) ÷(SiO2矿×矿石量+ SiO2灰×灰石量﹍+S(0.5-1.5)) 7、配合料及烧结矿的化学成分 TFe料=各种物料带入TFe之和÷各种干原料之和 TFe矿=各种物料带入TFe之和÷总残存量 SiO2料=各种物料带入SiO2之和÷各种干原料之和 SiO2矿=各种物料带入SiO2之和÷总残存量 CaO料=各种物料带入CaO之和÷各种干原料之和 CaO矿=各种物料带入CaO之和÷总残存量 二、配用石灰石的计算公式(阿尔希波夫公式) 100×(k×a-b)/【k×(a-c)+(d-b)】=加入量%
K----规定的碱度 a----料中SiO2+AI2O3的含量(石灰石中的除外)b----料中CaO+MgO的含量(石灰石中的除外) c----石灰石中SiO2+AI2O3的含量% d----石灰石中CaO+MgO的含量% 三、燃料配用量和配比的计算公式 Q燃=C混×(Q配+Q返)-C返×Q返/C煤kg B燃=Q燃÷Q配% 式中:Q燃、Q配、Q返分别为燃料配用量、配料室总流量、返矿流量 C混、C返、C煤----分别为混合料固定碳、返矿残碳、煤粉固定碳% B燃----为燃料配比% 四、白云石配加量(干)的简易计算公式 白云石配比=(MgO A- MgO A‵)%×A/(1-H2O白%) ×MgO白% 式中:MgO A----烧结矿要求的MgO A% MgO A‵--未加白云石烧结矿的MgO A% H2O白----白云石中含H2O% 五、已知高炉渣中MgO含量,求烧结矿MgO含量。计算公式 MgO矿=A*MgO渣*Fe矿/ Fe铁 式中:MgO矿---烧结矿的MgO% A---渣铁比一般为0.4--0.7
高低碱度
酸性和高碱度烧结矿合理搭配的 高炉炉料结构研究 范建军蔡涓夏 (太原钢铁集团有限公司,太原030003;) 摘要: 按照山西某钢铁厂的原料条件,为开发代替原来碱度1. 5的质量较差的烧结矿,进行了碱度0. 6一2. 3的不同碱度烧结矿的烧结性研究和不同碱度烧结矿综合炉料性研究,结果表明:对酸性烧结矿(R=0.6,0. 8、1. 0),碱度1.0的烧结矿其烧结性能指标相对碱度0. 6 , 0. 8的要好,且44%碱度1.05的烧结矿配.加44%碱度1. 87的烧结矿和12 %的球团矿其综合炉料性能优于原来的86%碱度1. 5的烧结矿配加14 %球团矿的炉料结构。 关键词:酸性烧结矿烧结特性熔滴特性 山西某地方钢铁厂,近两年在建设高炉的同时,配套建设厂两台烧结机,且烧结矿生产能力较大,但没有配套建设酸性球团矿生产线。因此,自高炉投产以来,为充分发挥烧结机的产能,烧结矿的配比达到86%左右,外购球团矿的比例为14%左右。烧结矿比例在86%左右时,为平衡高炉炉渣碱度,烧结矿的碱度在1. 5左右,生产中发现烧结矿的质量较差,特别是自然粉严重,不能落地存储。 以往的试验研究和经验表明,碱度1. 5左右的烧结矿由于处于自熔性烧结矿到高碱度烧结矿的过度阶段,因此,矿物组成较复杂,而碱度1. 0以下的酸性烧结矿矿物组成相对简单,自然粉化不是相对较轻;高碱度烧结矿由于铁酸钙含量比较高,其质量比较好。因此,该钢铁厂同太钢技术中心合作进行厂试验研究,重点研究能否生产酸性烧结矿和高碱度烧结矿搭配使用以代替日前的碱度1. 5左右烧结矿,以改善烧结矿的质量。 1烧结性能试验研究 1.1工艺参数及原料化学成分 烧结性能试验研究在小300 mm x 600 mm的烧结杯上进行,其方法同常规方法相同,有关操作参数如下:点火负压:转速:8 r/min ,5 kPa,烧结负压:10 kPa,点火时间:2 min。混料机规格为小800 mm x 1200 mm ,混料机混料时间:4 min },试验所用原料化学成分见表 1. 2不同碱度烧结矿烧结性试验结果及分析 按照该厂的原料条件,设计烧结矿碱度为0.6, 0.8, 1.0, 1.4, 1.8, 2.0, 2.3七个水平进行厂烧结杯试验研究,重点考察厂不同碱度烧结矿其垂直燃烧速度、烧结转股强度、烧结粒度组成等指标的变化。具体试验结果见表2
烧结矿碱度波动影响因素探讨
Ser i a l N o.482 June.2009现 代 矿 业 M ORDEN M I N I NG 总第482期 2009年6月第6期 李建华,066326河北省秦皇岛市。烧结矿碱度波动影响因素探讨 李建华 康 健 成富全 (首秦金属材料有限公司) 摘 要:针对首秦烧结矿合格率低的情况,通过理论计算和实际情况分析,探讨了碱度波动的影响因素,提出了碱度稳定措施,提高了碱度合格率和烧结矿质量,稳定了烧结矿生产。 关键词:烧结矿;碱度;合格率 中图分类号:TF046.4 文献标识码:B 文章编号:1674-6082(2009)06-0098-02 精料 是提高铁水产量及质量,使高炉达到高产、优质、低耗、长寿和高效运行的基础。烧结矿作为主要入炉原料,必须具备高品位、高强度、高冶金性能;化学成分稳定、冶金性能稳定、粒度大小及组成稳定;粉末少、有害杂质少的特征。其中烧结矿的碱度稳定率是提高烧结矿产量、质量的关键影响因素,有必要对影响烧结矿碱度因素进行了探讨。 1 烧结矿生产现状 秦皇岛首秦金属材料有限公司(以下简称 首秦 )目前烧结矿碱度中线为1.83(R 0.05、R 0.1分别为首秦烧结矿碱度一级品与合格品指标),表1是首秦2008年下半年碱度指标完成情况。 表1 2008年7~11月碱度指标完成情况(%)项目7月8月9月10月11月 合格率88.2595.298.2998.3793.45 一级品率77.9382.5280.7477.8772.93 由于国内外购原料成分波动较大,且厂内没有原料混匀场,导致烧结原料成分波动较大,烧结矿碱度一级品率较低,尤其是2008年11月份,碱度一级品率出现大幅度下滑,只有72.93%,影响全年指标任务的完成。 2 原料成分和配比波动对碱度合格率的影响 2.1 原料成分 表2是原料成分,主要包括铁原料及熔剂。 2.2 原料成分和配比波动临界值计算 为了分析比较每种原料成分波动及配比的变化对烧结矿碱度的影响程度,引入一个 临界值 的概念,即假设在其它原料成分或配比不发生任何波动的条件下,该种原料的最大允许波动量,以比较各种原料波动对烧结矿TFe和碱度波动的影响力。 表2 原料成分(%)项目TFe H2O湿配比干配比S i O2C a O Ig残存矿粉A65.979.771513.537.380.45 2.0713.25矿粉B61.518.052220.23 5.20.09 5.0319.21矿粉C66.266.781614.92 1.390.045 2.3714.56矿粉D67.726.4376.55 1.670.110.95 6.49矿粉E588.482018.30 5.470.1211.0416.28灰石031211.64 5.9247.5542.64 6.68白灰0044 5.1771.9215.49 3.38 由:P i(1-W i) C a O i Si O2=0.05(1)得: Ca O= 0.05 S i O2 P i(1-W i) ,(2)由: Ca O Si O2+P i(1-W i) S i O2i=R0-0.05,(3) 得: S i O2= 0.05 S i O2 (R0-0.05)(1-W i) ,(4)由: Q i(1-W i)C a O i+ C a O i Q i(1-W i)S i O2+ Si O2i=R0+0.05,(5) 得: Q i= 0.05 S i O2 (1-W i)[Ca O-(R0+0.05)S i O2i] ,(6)式中,P i为第i种矿粉的湿配比;W i为第i种矿粉的水分; S i O2为各种原料中S i O2之和; Ca O为各种原料中Ca O之和; Ca O i为第i种矿粉Ca O波动量对碱度影响的临界值; S i O2i第i种矿粉S i O2波动量对碱度影响的临界值; Q i为第i种矿粉配比波动量对碱度影响临界值。 由式(2)、式(4)、式(6)计算可得表3。 2.3 临界值波动影响因素分析 2.3.1 原料成分波动对碱度的影响 从表3可以看出,含铁原料中矿粉A的临界值最小,允许波动的最大临界值仅为0.47%,对碱度影响最大。计算结果也与实际情况一致,首秦矿粉A为外购原料,由于全球经济危机对钢铁行业的影响,因价格原因,矿粉A货源组织出现困难,致使出 98