液压系统通用技术条件
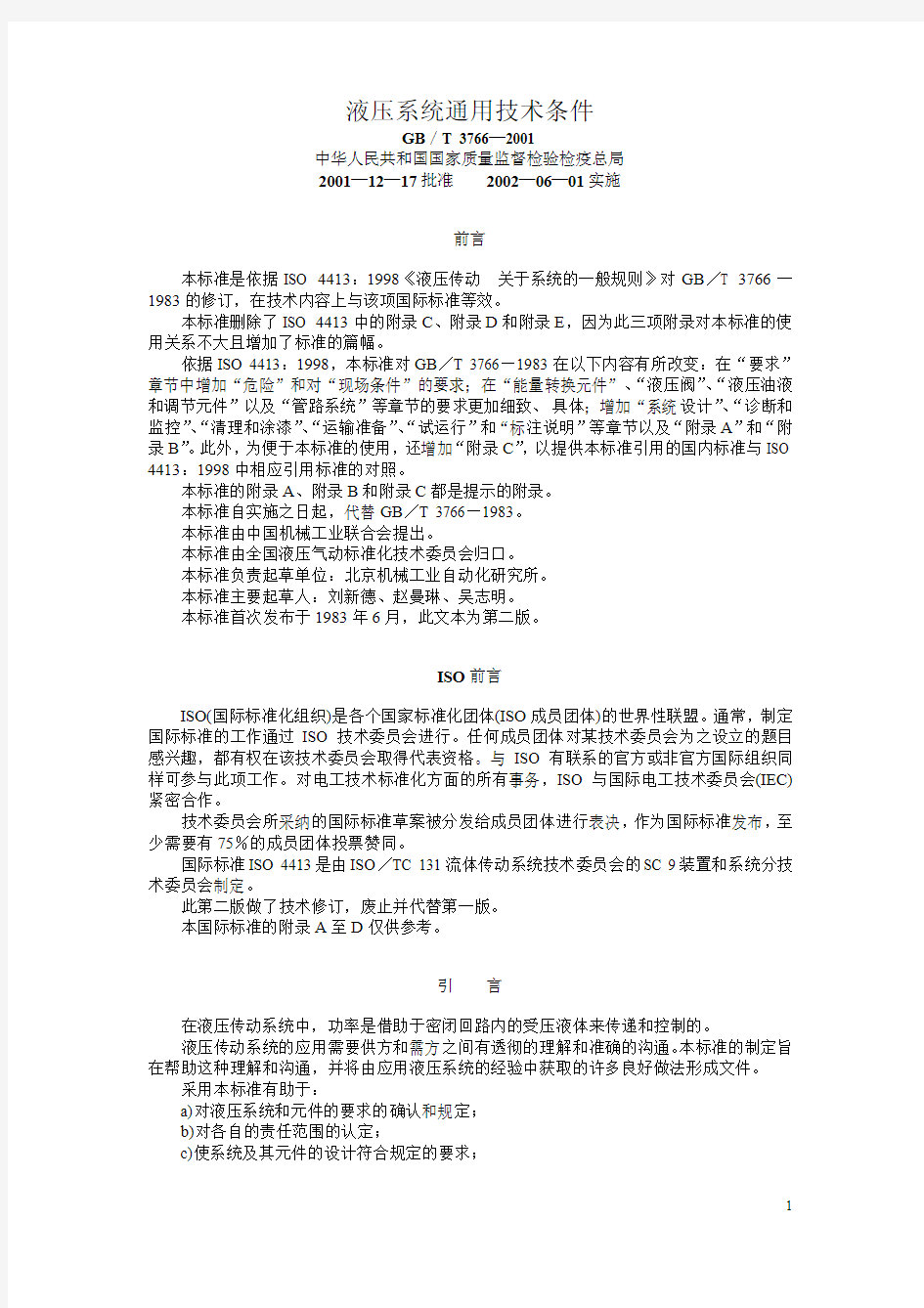
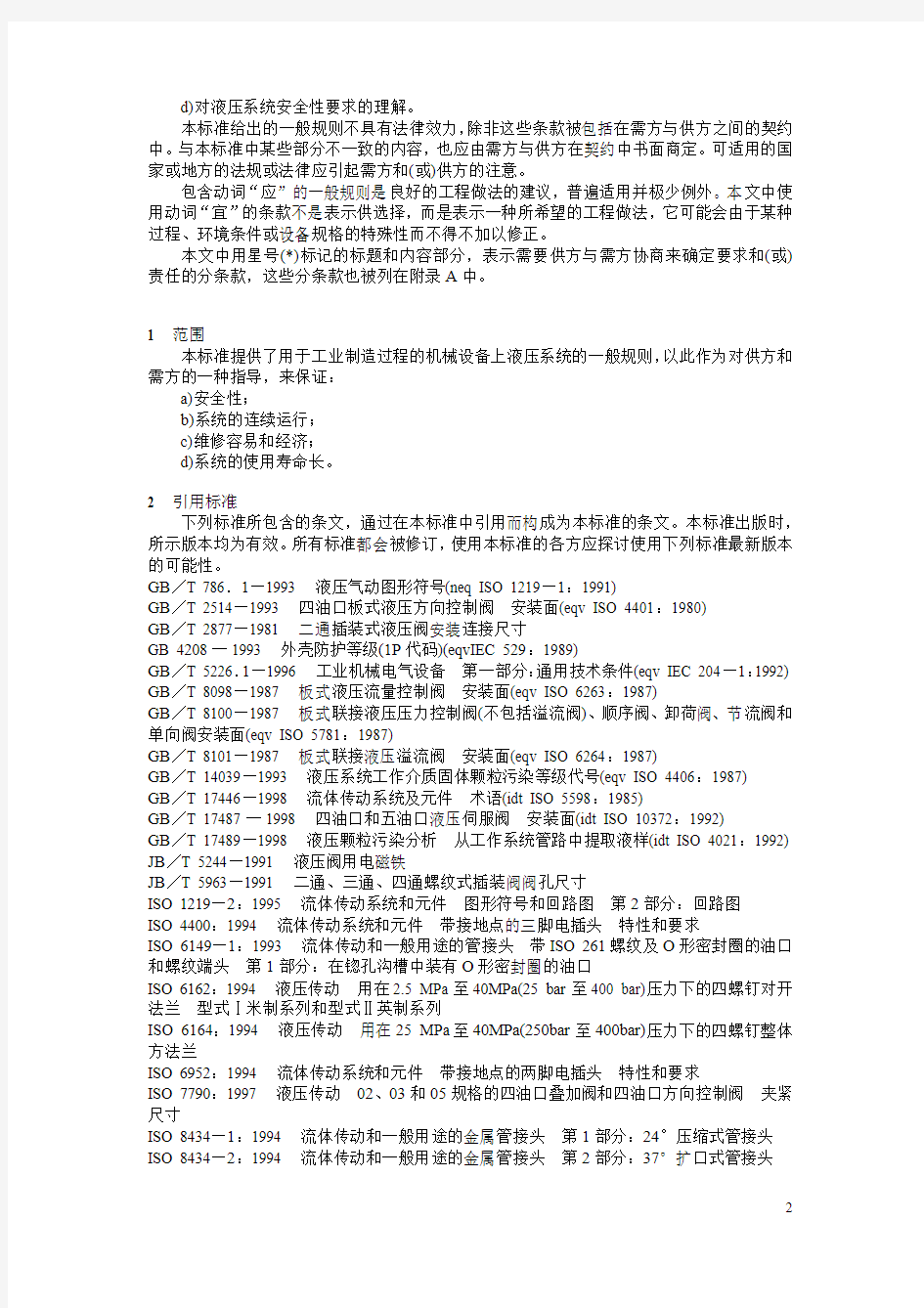
液压系统通用技术条件
GB/T 3766—2001
中华人民共和国国家质量监督检验检疫总局
2001—12—17批准2002—06—01实施
前言
本标准是依据ISO 4413:1998《液压传动关于系统的一般规则》对GB/T 3766一1983的修订,在技术内容上与该项国际标准等效。
本标准删除了ISO 4413中的附录C、附录D和附录E,因为此三项附录对本标准的使用关系不大且增加了标准的篇幅。
依据ISO 4413:1998,本标准对GB/T 3766—1983在以下内容有所改变:在“要求”章节中增加“危险”和对“现场条件”的要求;在“能量转换元件”、“液压阀”、“液压油液和调节元件”以及“管路系统”等章节的要求更加细致、具体;增加“系统设计”、“诊断和监控”、“清理和涂漆”、“运输准备”、“试运行”和“标注说明”等章节以及“附录A”和“附录B”。此外,为便于本标准的使用,还增加“附录C”,以提供本标准引用的国内标准与ISO 4413:1998中相应引用标准的对照。
本标准的附录A、附录B和附录C都是提示的附录。
本标准自实施之日起,代替GB/T 3766—1983。
本标准由中国机械工业联合会提出。
本标准由全国液压气动标准化技术委员会归口。
本标准负责起草单位:北京机械工业自动化研究所。
本标准主要起草人:刘新德、赵曼琳、吴志明。
本标准首次发布于1983年6月,此文本为第二版。
ISO前言
ISO(国际标准化组织)是各个国家标准化团体(ISO成员团体)的世界性联盟。通常,制定国际标准的工作通过ISO技术委员会进行。任何成员团体对某技术委员会为之设立的题目感兴趣,都有权在该技术委员会取得代表资格。与ISO有联系的官方或非官方国际组织同样可参与此项工作。对电工技术标准化方面的所有事务,ISO与国际电工技术委员会(IEC)紧密合作。
技术委员会所采纳的国际标准草案被分发给成员团体进行表决,作为国际标准发布,至少需要有75%的成员团体投票赞同。
国际标准ISO 4413是由ISO/TC 131流体传动系统技术委员会的SC 9装置和系统分技术委员会制定。
此第二版做了技术修订,废止并代替第一版。
本国际标准的附录A至D仅供参考。
引言
在液压传动系统中,功率是借助于密闭回路内的受压液体来传递和控制的。
液压传动系统的应用需要供方和需方之间有透彻的理解和准确的沟通。本标准的制定旨在帮助这种理解和沟通,并将由应用液压系统的经验中获取的许多良好做法形成文件。
采用本标准有助于:
a)对液压系统和元件的要求的确认和规定;
b)对各自的责任范围的认定;
c)使系统及其元件的设计符合规定的要求;
d)对液压系统安全性要求的理解。
本标准给出的一般规则不具有法律效力,除非这些条款被包括在需方与供方之间的契约中。与本标准中某些部分不一致的内容,也应由需方与供方在契约中书面商定。可适用的国家或地方的法规或法律应引起需方和(或)供方的注意。
包含动词“应”的一般规则是良好的工程做法的建议,普遍适用并极少例外。本文中使用动词“宜”的条款不是表示供选择,而是表示一种所希望的工程做法,它可能会由于某种过程、环境条件或设备规格的特殊性而不得不加以修正。
本文中用星号(*)标记的标题和内容部分,表示需要供方与需方协商来确定要求和(或)责任的分条款,这些分条款也被列在附录A中。
1 范围
本标准提供了用于工业制造过程的机械设备上液压系统的一般规则,以此作为对供方和需方的一种指导,来保证:
a)安全性;
b)系统的连续运行;
c)维修容易和经济;
d)系统的使用寿命长。
2 引用标准
下列标准所包含的条文,通过在本标准中引用而构成为本标准的条文。本标准出版时,所示版本均为有效。所有标准都会被修订,使用本标准的各方应探讨使用下列标准最新版本的可能性。
GB/T 786.1—1993 液压气动图形符号(neq ISO 1219—1:1991)
GB/T 2514—1993 四油口板式液压方向控制阀安装面(eqv ISO 4401:1980)
GB/T 2877—1981 二通插装式液压阀安装连接尺寸
GB 4208一1993 外壳防护等级(1P代码)(eqvIEC 529:1989)
GB/T 5226.1—1996 工业机械电气设备第一部分:通用技术条件(eqv IEC 204—1:1992) GB/T 8098—1987 板式液压流量控制阀安装面(eqv ISO 6263:1987)
GB/T 8100—1987 板式联接液压压力控制阀(不包括溢流阀)、顺序阀、卸荷阀、节流阀和单向阀安装面(eqv ISO 5781:1987)
GB/T 8101—1987 板式联接液压溢流阀安装面(eqv ISO 6264:1987)
GB/T 14039—1993 液压系统工作介质固体颗粒污染等级代号(eqv ISO 4406:1987)
GB/T 17446—1998 流体传动系统及元件术语(idt ISO 5598:1985)
GB/T 17487一1998 四油口和五油口液压伺服阀安装面(idt ISO 10372:1992)
GB/T 17489—1998 液压颗粒污染分析从工作系统管路中提取液样(idt ISO 4021:1992) JB/T 5244—1991 液压阀用电磁铁
JB/T 5963—1991 二通、三通、四通螺纹式插装阀阀孔尺寸
ISO 1219—2:1995 流体传动系统和元件图形符号和回路图第2部分:回路图
ISO 4400:1994 流体传动系统和元件带接地点的三脚电插头特性和要求
ISO 6149—1:1993 流体传动和一般用途的管接头带ISO 261螺纹及O形密封圈的油口和螺纹端头第1部分:在锪孔沟槽中装有O形密封圈的油口
ISO 6162:1994 液压传动用在2.5 MPa至40MPa(25 bar至400 bar)压力下的四螺钉对开法兰型式Ⅰ米制系列和型式Ⅱ英制系列
ISO 6164:1994 液压传动用在25 MPa至40MPa(250bar至400bar)压力下的四螺钉整体方法兰
ISO 6952:1994 流体传动系统和元件带接地点的两脚电插头特性和要求
ISO 7790:1997 液压传动02、03和05规格的四油口叠加阀和四油口方向控制阀夹紧尺寸
ISO 8434—1:1994 流体传动和一般用途的金属管接头第1部分:24°压缩式管接头ISO 8434—2:1994 流体传动和一般用途的金属管接头第2部分:37°扩口式管接头
ISO 8434—3:1995 流体传动和一般用途的金属管接头第3部分:O形圈端面密封管接头
ISO 8434—4:1995 流体传动和一般用途的金属管接头第4部分:带有O形圈密封的焊接接头体的24°锥面管接头
ISO 10763:1994 液压传动平管口、无缝的和焊接的精密钢管尺寸和标称工作压力ISO/TR 11688—1:1995 声学对低噪声机器和装置设计的推荐做法第1部分:方案ISO 12151—1:1999 液压传动和一般用途的管接头软管接头第1部分:带ISO 8434—30形圈端面密封端头的软管接头
ISO 12151—2:一1)液压传动和一般用途的管接头软管接头第2部分:带ISO 8434—1或ISO 8434—4 24°锥面O形圈密封端头的软管接头
ISO 12151—3:1999 液压传动和一般用途的管接头软管接头第3部分:带ISO 6162法兰端头的软管接头
ISO 12151—4:一1)液压传动和一般用途的管接头软管接头第4部分:带ISO 6149—2或ISO 6149—3螺纹端头的软管接头
ISO 12151—5:一1)液压传动和一般用途的管接头软管接头第5部分:带ISO 8434—2 37°扩口式端头的软管接头
注:1)将发布。
3 定义
本标准采用GB/T 17446中给出的定义和下列定义。
3.1 执行器actuator
把液压能转换成机械能的元件(例如:液压缸、液压马达)。
3.2 试运行commissioning
需方正式验收系统的程序。
3.3 元件component
液压传动系统的一个功能部分,由一个或多个零件组成的独立单元(例如:液压缸、液压马达、液压阀、液压过滤器,但管路除外)。
3.4 控制机构control mechanism
给元件提供输入信号的装置(例如:手柄、电磁铁)。
3.5 应急控制emergency control
把系统带人安全状态的控制功能。
3.6 功能标牌function plate
包含描述手动操作装置的性能(例如:开/关、进/退、左/右、升/降)或系统执行的功能状态(例如:夹紧、提升和前进)的信息的标识牌。
3.7 操作装置operating device
给控制机构提供输入信号的装置(例如:凸轮、电开关)。
3.8 管路piping
管接头、软管接头和连接件与硬管或软管的任何组合,这种组合使得液压油液能在元件之间流动。
3.9 需方purchaser
规定对机器、装置、系统或元件的要求,并评定产品是否满足这些要求的一方。3.10 供方supplier
承包提供满足需方要求的产品的一方。
3.11 系统system
由相互连接的元件组成的传递和控制液压能量的装置。
4 要求
4.1 概述
在4.1.1至4.5中给出的要求,适用于本标准范围内的所有系统。
4.1.1 说明书
液压系统应按照系统供方的说明书和建议来安装和使用。
4.1.2 语言*
需方和供方应商定用于机器标志和适用文件的语言。供方应负责保证译文与原文具有同样的含义。
4.2 危险*
当需方和供方商定时,应对附录B中所列危险进行评价。该评价可以包括液压传动系统对机器的其他部分、系统或环境的影响。列入附录B中的标准可用于该评价。
只要可行,就应通过设计消除所确认的那些危险。若做不到这一点,则设计应包含针对这些危险的防范措施。
4.3 安全性要求
4.3.1 设计方面的考虑
设计液压系统时,应考虑所有可能发生的失效(包括控制电源的失效)。
在所有情况下元件应该这样选择、应用、安装和调整,即:在发生失效时,应首先考虑人员的安全性。
应考虑防止对系统和环境的危害。
4.3.2 元件的选择
为保证使用的安全性,应对系统中的所有元件进行选择或指定。选择或指定元件应确保,当系统投入预定的使用时,这些元件应在其额定的极限内可靠地运行。尤其应注意它们的失效或误动作可能引起危险的那些元件的可靠性。
4.3.3 意外压力
应从设计上,防止系统所有部分的压力超过系统或系统任一部分的最高工作压力和任何具体元件的额定压力,否则应采取其他防护措施。
防止过高压力的可取的保护方法,是设置一个或多个溢流阀来限制系统所有部分的压力。也可以采用其他能满足使用要求的方法,如:采用压力补偿式变量泵。
系统的设计、制造和调试,应使冲击压力和增压压力减至最低。冲击压力和增压压力不应引起危险。
压力丧失或临界压降时,不应使人员面临危险。
4.3.4 机械运动
无论是预期的或意外的机械运动(包括如:加速、减速或提升和夹持物体产生的运动),都不应造成对人员有危险的状态。
4.3.5 噪声
有关低噪声机器和系统的设计见ISO/TR 11688—1。
4.3.6 泄漏
泄漏(内泄漏或外泄漏)不应引起危险。
4.3.7 温度
4.3.7.1 工作温度
系统或任何元件的整个工作温度范围,不应超出规定的安全使用范围。
4.3.7.2 表面温度
液压系统设计应通过布置或安装防护装置来保护人员免受超过触摸极限的表面温度的伤害。
4.4 系统要求
需方和供方应确定有关系统运行和功能的技术规格,其中包括:
a)工作压力范围;
b)工作温度范围;
c)所用液压油.液的类型;
d)循环速率;
e)负载循环特性;
f)元件的使用寿命;
g)动作顺序;
h)润滑;
i)起吊要求;
j)应急和安全性的要求;
k)涂漆或保护涂层的细节。
4.5 现场条件*
4.5.1 技术条件
需方应在询价书中,指定对于适当选择和应用系统所需要的所有资料。
所需的资料例如:
a)设备的环境温度范围;
b)设备的环境湿度范围;
c)可用的公共设施,例如:电、水、废物处理;
d)电网的细节,例如:电压及其容限;频率、可用的功率(如果受限制);
e)对电气装置的保护;
f)大气压力;
g)污染;
h)振动源;
i)可能发生起火或爆炸危险的严重性;
j)可得到的维修标准;
k)安全裕度,例如:流量、压力和体积;
l)维修、使用和通道所需的空间,以及为保证元件和系统在使用中的稳定性和牢固性的布置及安装;
m)可得到的冷却和加热介质及容量;
n)防护要求;
o)法律和环境的限制因素;
p)其他安全性要求。
4.5.2 图样
供方应提供由需方与供方商定的图样,这些图样指明:
a)平面布置,其中包括位置和安装尺寸;
b)基础要求,其中包括地面载荷;
c)供水要求;
d)供电要求;
e)管路布置(经商定,可以使用照片表示)。
5 系统设计
5.1 回路图
供方应提供符合ISO 1219—2的回路图。该回路图反映系统设计,标识元件并满足条款4的要求。
下列资料应包括在回路图中或随回路图提供:
a)所有装置的名称、目录编号、系列号或设计编号及制造商或供应商名称的标识;
b)硬管的口径、壁厚和技术条件及软管总成的通径和技术条件;
c)各个液压缸的内径、活塞杆直径、行程长度,以及估算的预期工作所需的最大推力和速度;
d)各个液压马达预期工作所需的排量、最大输出转矩、转速和旋转方向;
e)各个泵的流量和从驱动轴端观看的旋转方向;
f)各个泵的原动机的功率、转速和型号;
g)压力设定值;
h)滤网、过滤器和替换滤芯的型号;
i)将系统灌注至最高液位所需的液压油液体积;
j)推荐的液压油液类型和黏度;
k)当规定时,表示进行的操作(包括与电控、机械控制及执行器有关的功能)的时间顺序图;诸如:循环的时间范围和数据或文字,或两者;
l)包含在油路块内的任何子回路的清晰指示;为此可以采用边界线或边框线,边界线内应仅包括安装在油路块上或油路块内的元件的符号;
m)各执行器沿各个方向的功能的清晰指示;
n)蓄能器的充气压力和标称容积;
o)在回路中,压力测试点、液压油液取样点和放气点的口径、型式和位置;
p)所有元件或油路块的油口的标识(与在元件或油路块上标明的一致);
q)冷却介质的预期流量及最高和最低压力,以及冷却介质源的最高温度;
r)所有电信号变换器的标识,与在电路图上标明的一致。
5.2 标识
5.2.1 元件
供方应提供下列详细资料,如可能,应在所有元件上以永久的和明显的形式表示出来:
a)制造商或供应商的名称和简要地址;
b)制造商或供应商的产品标识;
c)额定压力;
d)符合GB/T 786.1的图形符号,包括全部油口的正确标记。
在可用空间不足可能导致文字太小而看不清楚的场合,可将资料提供在补充材料上,如:说明/维修活页、目录活页或辅助标签上。
5.2.2 系统内的元件
应给每个元件一个唯一的元件号和(或)字母,此元件号应用在所有的原理图、清单和图样中标识该元件,并应被清晰地和永久地标注在设备上紧邻该元件的地方,而不在该元件上。
叠加组件的顺序应清晰地标明在紧邻叠加块的地方,而不在该叠加块上。
5.2.3 油口
应对所有油口、动力输出点、测试点和放气点及泄油口(例如:油箱放油),做出清晰的和明显的标识。该标识应与回路图上的资料一致。
当元件带有由供应商提供的标准油口标识时,这些标识应以与回路图一致的标识进行增补(见5.2.1和5.2.2)。
5.2.4 阀的控制机构
5.2.4.1 电的控制机构
电的控制机构(电磁铁和它们配带的插头或电缆)应采用同样的标识标明在电路图和液压回路图中。
5.2.4.2 非电的控制机构
非电的控制机构及其功能应采用与回路图相同的标识清晰地和永久地标明。
5.2.5 内部装置
布置在油路块、安装板、底座或管接头中的插装阀和其他功能元件(阻尼器、通道、梭阀、单向阀等),应在邻近它们的插入孔处加上标识。当插入孔位于一个或几个元件下面时,如可能应在该元件附近设置标识,并标明“内装”。
5.2.6 功能标牌
每个控制台都应设置一块功能标牌,并且要位于易读到的位置。功能标牌上的信息应恰当和易懂,并应提供所控制的系统功能的明确标识。
5.3 安装、使用和维修
应按照供方的说明书和建议,选择、应用、安装和使用元件和管路。
宜选择按照认可的国际标准或国家标准制造的元件。
5.3.1 元件更换
为了便于维修,应提供相应措施或采取适当的方式安装元件。当为维修而把元件从系统拆下时:
a)不应导致过多的液压油液损失;
b)不宜要求油箱放油;
c)不宜过多地拆卸相邻的零件。
5.3.2 维修要求
设计和构成系统时,应将元件布置在易于接近并能安全地调整和检修的位置。
液压元件,包括管路,应易于接近并安装成便于调整或维修。应特别注意需要定期维修的系统和元件的布置。
5.3.3 起吊设施
质量大于15kg的所有元件或部件应有起吊设施。
5.3.4 元件安装
元件的安装宜便于从安全的工作位置(例如:地面或工作平台)接近而没有危险。
通常,元件下边缘的安装高度宜在工作平台之上至少0.6 m,而其上边缘不.宜高于工作平台之上1.8 m。
5.4 标准件的使用
系统供方宜使用市场上能买到的零件(键、轴承、填料、密封件、管接头、垫圈、插头、紧固件等)和符合现行国家标准规定并带有统一编号的元件连接安装尺寸(轴和花键规格、油口口径、底座、安装面或腔孔等)。
5.5 密封件和密封装置
5.5.1 材料
密封件和密封装置的材料应与所用的液压油液、邻近的材料及其工作条件和环境条件相容。
5.5.2 更换
零、部件设计应便于密封件和密封装置的检修和更换。
5.6 维修和操作资料
系统供方应提供必要的维修和操作资料,该资料清楚地:
a)说明起动和停机的程序;
b)给出所有需要的减压规程,并且标出系统中靠通常的排放装置不能减压的那些部分;
c)说明调整程序;
d)指出外部润滑点、所需的润滑剂类型和观察、加注的时间间隔;
e)标明需要安排维护的液位指示器、注油点、放油点、过滤器、测试点、滤网、磁性体等的位置;
f)规定容许的液压油液最差污染等级;
g)给出液压油液保养的规程;
h)提供对液压油液和润滑剂安全使用和处理的建议;
i)规定充分冷却需要的冷却介质的流量、最高温度和容许压力范围:
j)说明特殊组件的维修程序;
k)进一步给出市场上能买到的或是按国家标准统一编号制造的液压元件内零件的标识;该标识应是元件制造商的零件号或是由采用的国家标准所规定的编号;
1)列出推荐的备件。
5.7 操作和维修手册
系统供方应提供描述系统操作和维修的手册,其中包括在5.6中描述的要求以及关于元件和管路的说明和(或)维修资料。
5.8 油口
所有油口连接宜符合:
——ISO 6149—1(适用于螺纹油口和螺纹端头),或
——ISO 6162或ISO 6164(适用于四螺钉法兰油口连接)。
5.9 系统温度
5.9.1 发热
液压系统设计应使不必要的发热减至最低。
5.9.2 工作温度
应规定系统的工作温度范围。液压油液的温度不应超过它能可靠地使用的范围,并且应在系统中所有元件所规定的工作温度范围内。
6 能量转换元件
6.1 液压泵和马达
6.1.1 保护措施
液压泵和马达应安装在对可预见的损害有防护的地方,或适当地安装防护装置。
应对所有驱动轴和联轴器采取适当的保护。
6.1.2 机械安装
a)维修时易于接近;
b)不因负载循环变化、温度变化或所施加的压力载荷的结果,而产生轴线错位;
c)引起的轴向和径向的载荷在泵或马达的供应商规定的范围内;
d)传动联轴器和机座具有反复经受住所有工况下产生的最大转矩的能力:
e)利用具有充分阻尼作用的联轴器,限制扭转振动的传递和扩大。
6.1.3 转速的考虑
转速不应超过供方的文件中规定的最高转速。
6.1.4 泄油口、放气口和辅助油口
液压泵和马达泄油口的口径和封堵应符合元件供应商的规定。
泄油口、放气口和辅助油口的设置应不允许空气进入系统,并且它们的尺寸和设置应保证不会产生过高的背压。应使高压放气口的设置对人员的危害性最小。
6.1.5 壳体的预先注油
当液压泵和马达的壳体需要在起动之前预先注油时,应设置好注油点的位置和提供一种容易采用的预先注油的手段,以保证空气不会被封闭在壳体内。
6.1.6 工作压力范围
如果对泵和马达正常使用时的工作压力范围有限制,则应在供方提供的技术资料中做出规定。
6.1.7 液压安装
a)管路接口的连接应防止外泄漏;不应使用锥管螺纹或需要密封填料的连接结构;
b)在不工作时,应防止丧失吸油口的油液或壳体的润滑;
c)泵进口压力不应低于该泵供应商针对工况和系统用液压油液规定的最低值。
6.2 液压缸
6.2.1 适用性
液压缸应按下列特性设计和(或)选择:
6.2.1.1 抗纵弯性
为避免液压缸的活塞杆在任一位置产生弯曲或纵弯,应注意行程长度、载荷和液压缸的安装。
6.2.1.2 负载和超载
在会遇到超载或其他外部负载的应用场合,液压缸的设计和安装应考虑最大的预期负载或压力峰值。
6.2.1.3 安装额定值
所有负载额定值应考虑安装型式。
注:液压缸的压力额定值仅能反映缸体的承压能力,而不能反映安装结构的力传递能力。有关安装结构的额定值应询问供应商或制造商。
6.2.1.4 结构负载
当液压缸被用作为实际的限位器时,如果由其限制的机件引起的负载大于液压缸正常工作循环期间承受的负载,则液压缸应根据其承受的最大负载确定尺寸并选择机座。6.2.1.5 抗冲击和振动
任何安装在液压缸上或与液压缸连接的元件都应牢固,以防由冲击和振动引起松动。6.2.1.6 增压
在液压系统中应采取一种措施,防止由于活塞面积差引起的增压超过额定压力极限。6.2.2 安装和找正
液压缸宜采取的最佳安装方式,是使负载反作用沿液压缸的中心线发生。安装应尽量减少(小)下列情况:
a)由于推或拉载荷引起的液压缸结构的过度变形;
b)引起侧向或弯曲载荷;
c)轴销安装型式的旋转速度,该速度可能使这种安装型式需要连续的外部润滑。6.2.2.1 安装布置
安装面不应使液压缸变形,并应留出热膨胀的余量。液压缸应安装得易于接近,以便维修、调整缓冲装置和更换全套装置。
6.2.2.2 安装紧固件
用于液压缸及其附件的安装紧固件的设计和安装,应能承受所有可预见的力。紧固件宜
尽量避免承受剪切力。脚架安装的液压缸应具有承受剪切载荷的机构,而不能依靠安装紧固件承受。安装紧固件应足以承受倾覆力矩。
6.2.2.3 找正
安装面的设计应能防止安装时液压缸变形。应以可避免工作期间的意外横向载荷的方式安装液压缸。
6.2.3 缓冲装置和减速装置
当使用内置缓冲器时,液压缸末端挡块的设计应考虑负载减速的影响。
6.2.4 行程末端挡块
如果行程长度由外部行程末端挡块确定,应提供锁定该可调末端挡块的手段。6.2.5 活塞行程
活塞的行程应始终大于或等于它的标称行程。
6.2.6 活塞杆
应选择活塞杆的材料和表面处理,使磨损、腐蚀和可预见的冲击损坏减至最低程度。
应保护活塞杆免受压凹、刮伤和腐蚀等可预见的损坏。可以设置防护罩。
为了装配,带有外螺纹或内螺纹端头的活塞杆上,应设置适合标准扳手的平面。当活塞杆太小以致无法设置规定平面的情况下,可以省去。
6.2.7 维修
活塞杆密封件、密封组件和其他减磨件应易于更换。
6.2.8 单作用液压缸
单作用活塞式液压缸应设计放气口,并设置在适当的位置,以避免排出的油液喷射对人员造成危险。
6.2.9 更换
整体式液压缸是不合需要的,但当其被采用时,可能磨损的部件宜是可更换的。6.2.10 排气
6.2.10.1 油口设置
只要可能,安装液压缸时应使油口位于最高位置。
6.2.10.2 放气阀
安装液压缸应使它们能自动放气,或设置易于接近的外部放气阀。
6.3 充气式蓄能器
6.3.1 标识
除5.2.1的要求之外,下列标识应永久地标记在蓄能器上:
a)制造年份;
b)壳体总容积,以升(1)为单位;
c)制造商的系列号或批号;
d)允许的温度范围,以摄氏度(℃)为单位。
在蓄能器上或在蓄能器的标牌上应给出下列标识:
——“警告一压力容器,拆卸前排出油液”;
——额定充气压力;
——“仅用……作为充气介质”(例如氮气)。
6.3.2 对带有充气式蓄能器的液压系统的要求
带有充气式蓄能器的液压系统在关机时,应自动卸掉蓄能器的油液压力或可靠地隔离蓄能器。
在机器关机后仍需要压力的特殊情况下,上述要求不必满足。
充气式蓄能器和任何配套的受压部件,应在压力、温度和环境条件的额定范围内使用。在特殊情况下,可能需要防止在气体侧超压的保护装置。
带有充气蓄能器的液压系统应有警告标签,标明“警告一系统包含蓄能器。维修前,要使系统减压”。同样的内容应标注在回路图上。
如果设计要求充气式蓄能器在系统关机时隔离油压,那么应在蓄能器上或其附近的明显之处,注明安全保养的完整资料。
6.3.3 安装
6.3.3.1 安装位置
如果在充气式蓄能器系统中的元件或管接头损坏会引起危险,那么应对其采取适当的防护措施。
充气式蓄能器应依据蓄能器供应商的说明书安装,并应便于接近和维修。6.3.3.2 支撑
充气式蓄能器和任何配套的受压元件,应依据该蓄能器供应商的说明书加以支撑。6.3.3.3 未经认可的改动
禁止利用加工、焊接或任何其他手段改动充气式蓄能器。
6.3.4 维修
6.3.4.1 充气
充气式蓄能器很可能需要的主要日常保养,是检查或调整充气压力。蓄能器充气应仅使用供应商推荐的装置和程序。充气气体应是氮气或其他适用的气体。
压力检查应采用该蓄能器供应商推荐的方法进行,并应注意不能超过该蓄能器的额定压力。在任何检查或调整之后,不应有气体泄漏。
6.3.4.2 从系统中拆除
为了维修而拆下蓄能器之前,该蓄能器中的油压应被降低至零(减压状态)。6.3.4.3 充气式蓄能器的维修资料
维修、大修和(或)更换零部件,仅应由适当的专业人员按照书面的维修程序并使用被证明是按现行的设计规范制造的零件和材料来进行。在开始拆开充气式蓄能器之前,液体侧和气体侧应完全释压。
6.3.5 输出流量
充气式蓄能器的输出流量应与其预期的工作要求有关,但不应超过制造商规定的额定值。
7 液压阀
7.1 选择
液压阀的类型选择,应考虑正确的功能、密封性和抗御可预见的机械和环境影响的能力。推荐尽量采用板式安装阀和(或)插装阀。
7.2 安装
7.2.1 一般要求
安装阀时应考虑以下几点:
a)独立于配套的液压管路或接头;
b)拆卸、修理或调整用的通道;
c)重力、冲击和振动对阀的影响;
d)操作扳手和(或)接近螺栓及连接电气所需的足够空间;
e)确保阀不致错误安装的措施;
f)位置尽量接近其控制的执行器;
g)安装时不会被操作装置损坏。
7.2.2 管式安装阀
管式安装阀的连接应采用,符合ISO 6149—1的油口或符合ISO 6162或ISO 6164的四螺栓法兰接头。
7.2.3 板式安装阀
对板式安装阀宜采取措施,以保证:
a)对渗漏的阀或阀操作装置的检测;
b)消除背压有害影响;
c)为了使用防护导管,在相邻的阀之间留适当的间隔;
d)油路块或底板的安装面符合GB/T 2514、GB/T 8098、GB/T 8100、GB/T 8101、GB/T 17487和ISO 7790。
7.2.4 插装阀
插装阀宜使用具有符合GB/T 2877和JB/T 5963规定的插装孔的油路块。
7.3 油路块
7.3.1 表面平面度和表面粗糙度
油路块安装面的平面度和粗糙度,应符合阀制造商的推荐值。
7.3.2 变形
油路块在工作压力和工作温度下,不应产生会引起元件故障的变形。
7.3.3 安装
油路块应牢固地安装。
7.3.4 内部通道
内部通道的通流截面积,宜至少等于相关元件的通流面积。
内部通道(包括铸造孔和钻孔)应无有害的杂质(如氧化皮、毛刺、切屑等),这些杂质会限制流动或被冲刷出来引起任何元件(其中包括密封件和填料)失灵和(或)损坏。
7.4 电控阀
7.4.1 电气连接
与电源的电气连接应符合适当的标准,例如:GB/T 5226.1。对于危险的工作条件,应采用适当的电保护等级(例如防爆、防水)。与阀的电气连接宜采用符合ISO 4400或ISO 6952的可拆的、不漏油的插入式接头。
7.4.2 接线盒
指定接线盒在阀上时,它们应按下列要求制做:
a)符合GB 4208的适当保护等级;
b)为永久设置的端子和端子电缆,其中包括附加的电缆长度,留有足够的空间;
c)防止电气检修盖丢失的拴系紧固件,例如带锁紧垫片的螺钉;
d)对于电气检修盖的适当的固定装置,例如链条;
e)带有张力解除功能的电缆接头。
7.4.3 电磁铁
应选择符合JB/T 5244规定的,能够可靠地操作阀的电磁铁。电磁铁应按照GB 4208的规定,防止外部流体和污垢进入。
7.4.4 手动越权控制
当电控不能用时,如果为了安全或其他原因需要操作电控阀,那么它应配备手动越权装置。该装置的设计和选择,应使其不会无意中被操作,并且当手动控制解除时应自动复位,除非另有规定。
7.5 符号标牌
在阀上应附有符号标牌,其表示的位置和控制方式与操作装置的运动方向一致。
7.6 调整*
允许调整一个或多个受控参数的阀宜具有下列特性:
a)保证阀调整安全的措施;
b)当需方与供方商定时,锁定调整以防止未经认可的改变的措施;
c)监控正在调整的参数的措施。
7.7 拆卸
无论阀采用何种连接方式,阀的拆卸不应要求拆卸任何关联的管路或管接头,但可松开关联的管路或管接头,以便让出拆卸间隙。
8 液压油液和调节元件
8.1 液压油液
8.1.1 技术条件
被推荐用于液压系统的液压油液应按其类型和特性来规定,而不能仅靠商品名称来规定。
液压油液宜按现行的国家标准来描述。存在起火危险之处,应考虑使用难燃液压液。8.1.2 相容性
8.1.2.1 所有液压油液
使用的液压油液应与用于系统的所有元件、辅件、合成橡胶和滤芯相容,并符合系统或元件供应商的推荐。
8.1.2.2 难燃液压液
应采取附加的预防措施,防止由于难燃液压液与下列物质不相容而产生的问题:
a)与系统配套的防护涂料和其他油液,例如油漆、加工和(或)保养液;
b)能与溢出或泄漏的难燃液压液接触的结构或安装材料,例如电缆、其他维修供应品和产品;
c)其他液压油液;
d)密封件或填料。
8.1.2.3 处理措施
液压油液或液压系统的供应商,应提供有关打算使用的液压油液的材料安全数据资料。如果需要保证以下几点,应提供补充资料:
a)对于人工处理液压油液的保健要求;
b)毒性;
c)万一起火,可能出现的中毒或窒息的危险;
d)关于液压油液处理和废弃的建议资料;
e)具有生物降解能力。
8.1.3 液压系统和润滑系统*
除非在供方与需方之间另有规定,液压系统和润滑系统宜分开。所有液压油液和润滑剂的注入孔应做出清晰和永久的标记。
8.1.4 保养
为了保持系统液压油液的性质,供方应提供对于系统液压油液取样和监测的手段及规程。
宜特别注意难燃液压液。
8.1.5 注油和保持液位*
用于注油和保持液位所使用的液压油液应经过过滤。在灌注时,可通过系统内设的过滤器或用需方自己的移动式过滤器来过滤,移动式过滤器的过滤精度应等于或优于系统所用过滤器的过滤精度。
8.2 油箱
8.2.1 设计
a)当系统中没有安装热交换器时,油箱应能充分散发正常工况下液压油液的热量;
b)在正常工作或维修条件下,油箱宜容纳所有来自于系统的油液;
c)油箱应保持液位在安全的工作高度,并且在所有工作循环和工况期间有足够的油液通向供油管
路,以及留有足够的空间用于热膨胀和空气分离;
d)油箱宜提供缓慢的再循环速度,便于夹带的气体释放和重的污染物沉淀;
e)油箱宜利用隔板或其他手段,将回流油液与泵吸人口分隔开;如果使用隔板,则它们不应妨碍油箱的彻底清理。
如果油箱是加压密闭式的,那么应考虑这种型式的特殊要求。
8.2.2 结构
8.2.2.1 一般要求
油箱宜与机器结构是分离的和可拆装的。
8.2.2.2 溢出
应采取预防措施,阻止溢出的油液直接返回油箱。
8.2.2.3 支撑结构
a)支撑结构宜将油箱的底部提高到距地基平面150mn以上的高度,以便于搬运、排放和改善散热条件;
b)支撑结构宜有足够面积的支座,便于在装配和安装期间用垫片、斜楔等调整。8.2.2.4 振动和噪声
应注意防止过度的结构振动和空气噪声,尤其当元件被安装在油箱内或直接装在油箱上时。
8.2.2.5 油箱顶
a)油箱顶应牢固地固定在油箱体上;
b)如果油箱顶是可拆卸的,应设计成能防止污染物侵入;
c)油箱顶宜设计和制造成能避免形成聚集和存留外部固体、油液污染物及废弃物的区
域。
8.2.2.6 油箱配置要求
a)确定吸油管尺寸时,应使泵的吸油性能符合制造商的推荐;
b)吸油管的布置应做到,在处于最低工作液位时能保持足够的供油,并且能避免空气吸人和油液中漩涡的形成;
c)进入油箱的回油管,宜在最低工作液位以下排油;
d)进入油箱的回油管,应以最低的可行速度排油,并可促进油箱内形成所希望的油液循环方式;油箱内的油液循环不应引起空气的混入;
e)进入油箱内的任何管路都应有效地密封;
f)设计上宜考虑尽量减少系统液压油液中沉淀污染物的重新悬浮;
g)宜采用“盲孔”(不通的孔)紧固方法,把油箱顶以及检修孔盖和任何商定的元件固定在箱体上。
8.2.2.7 维修措施
a)应设置检修孔,可供维修人员接近油箱内部各处进行清洗和检查;检修孔盖应可由一人拆下或装回;
b)吸油粗滤器、回油扩散器和其他可更换的油箱内部元件应便于拆卸或清理;
c)油箱应设置允许放油的装置;
d)油箱的形状宜能使油液完全排空。
8.2.2.8 完整性
油箱设计应能在下列条件下提供足够的结构完整性:
a)用系统的液压油液灌注至最大容量;
b)承受以系统在任何可预见的条件下所需的速度吸油或回油所引起的正、负压力。8.2.2.9 表面处理
a)所有内部表面应彻底清理,并且清除所有潮气、污垢、切屑、焊剂、氧化皮、熔渣、纤维状材料和任何其他的污染物;
b)任何内部的涂层要与用于系统的液压油液和大气环境相容,并且应按涂层供应商的推荐来涂敷。当未采用这样的涂层时,铁质内部表面宜涂上与液压油液相容的防锈剂;
c)外部涂层也应与液压油液相容。
8.2.2.10 搬运
油箱的结构宜适于叉车或吊具和起重机搬运,且不致引起永久的变形。起吊点宜做出标记。
8.2.3 附件
8.2.3.1 液位指示器
a)液位指示器对系统允许的“最高”和“最低”液位应做出永久地标记;
b)液位指示器对特定系统宜做适当的附加标记;
c)液位指示器应配备在每个注油点,以便注袖时可以清楚地看见液位。
8.2.3.2 注油点
注油点应配备带密封的和被栓住的盖子,以防止关闭后污染物侵入。
8.2.3.3 空气过滤器
考虑到系统设置地点的环境条件,开式油箱宜设置空气过滤器,以过滤进入油箱的空气达到与该系统要求相适应的清洁度等级。
8.3 过滤和液压油液调节
8.3.1 过滤
应提供过滤,以便将使用中的颗粒污染度限定在适合于所选择的元件和预期应用所要求的等级内。污染等级应按照GB/T 14039表示。
宜适当考虑应用独立的过滤系统。
8,3.2 过滤器的布置和规格确定
8.3.2.1 布置
过滤器应根据需要布置在压力管路、回油管路和(或)辅助循环管路中,以达到系统要求的清洁度等级。
8.3.2.2 维修
所有过滤组件都应配备指示器,当过滤器需要保养时,该指示器会发出指示。指示器应易于让操作人员或维修人员看见。
8.3.2.3 压差
对于其滤芯不能经受住系统全压差而不损坏的过滤器组件,应装设旁通阀。8.3.2.4 压降
通过滤芯的最大压降应限制在制造商规定的范围内。
8.3.2.5 脉动
当过滤器被布置在受到压力和流量脉动的管路中时,可能会影响其过滤效率,应引起对滤芯流动疲劳特性的重视。在严重的情况下,宜安装阻尼装置。
8.3.2.6 可接近性
过滤器应安装在易于接近的地方,并应留出足够的空间更换滤芯。
8.3.2.7 标识
滤芯的编号和所需数量应永久地标注在过滤器的壳体上。
8.3.2.8 更换
当可行时,应提供在系统不关机的情况下更换滤芯的手段。
8.3.3 吸油粗滤器或过滤器*
除非需方和供方商定,在泵吸油管路上不应使用过滤器。但容许用吸油口滤网或粗滤器。
如果使用,吸油过滤装置应装设内部旁通阀来限定在额定系统流量下的最大压降,以满足6.1.7c)的要求。推荐使用电气装置来指示不能接受的泵进口压力或实现系统自动关机。8.3.3.1 可接近性
在使用吸油粗滤器或过滤器的地方,它们应易于接近,并可在不排空油箱的情况下进行维修。
8.3.3.2 选择
选择和安装吸油粗滤器或过滤器时,应使泵的进口条件在制造商规定的范围内。在冷起动的条件下,宜特别注意这一点。
8.3.4 磁铁
如果使用磁铁收集铁磁性物质,宜做到在不排空油箱的条件下进行保养。
8.4 热交换器
当自然冷却不能控制系统液压油液的温度时,或要求精确控制液压油液的温度时,应使用热交换器。
8.4.1 液体对液体的热交换器
使用液体对液体的热交换器时,应使液体的循环路线和速度在制造商推荐的范围内。8.4.1.1 温度控制
为保持所要求的液压油液温度和使所需的冷却介质流量减到最少,在热交换器的冷却介质一侧应采用自动温度控制。
冷却介质控制阀宜设置在输入管路上。为了维修,在冷却介质管路中应设置截止阀。8.4.1.2 冷却介质*
如果使用特殊的冷却介质或供给的冷却介质很可能是脏的、腐蚀性的或有限定的,需方应告诉供方。
应防止热交换器被冷却介质腐蚀。
8.4.1.3 排放
应采取措施排空热交换器两侧的液体。
8.4.1.4 测量点
对于液压油液和冷却介质,宜设置温度测量点。测量点宜保证可永久地安装传感器和在不损失液压油液的情况下检修。
8.4.2 液体对空气的热交换器
使用液体对空气的热交换器时,应使两者的流速在制造商推荐的范围内。8.4.2.1 空气供给
应提供充足的清洁空气。
8.4.2.2 空气排放
空气排放不应引起危险。
8.4.3 加热器
当使用加热器时,其耗散功率密度不应超过液压油液制造商推荐的范围。
应采用自动温度控制,以保持希望的液压油液温度。
9 管路系统
9.1 一般要求
9.1.1 液压油液流动
通过管路、管接头和油路块的液压油液流速不宜超过:
a)吸油管路:1.2 m/s;
b)压力管路:5 m/s;
c)回油管路:4m/s;
9.1.2 管接头的应用
在管路系统中,可分离的管接头数量应保持最少(例如:利用弯管代替弯头)。9.1.3 布局设计
管路设计宜避免它被当作踏板或梯子使用。外部载荷不宜加在管路上。
管路不应用来支承元件,造成过度的载荷强加在管路上。这种过度载荷可能由元件质量、冲击、振动和冲击压力引起。
管路的任何连接,宜便于接近来拧紧而不致扰乱邻近管路或装置,尤其是在管路端接于一组管接头之处。
9.1.4 管路布置
管路的标记或布置方式,宜使它不会出现引起危险或故障的错误连接。
管路(硬管或软管)安装时,应使安装应力减到最小;其布置应能防止可预见的危险,并且不妨碍对元件调整、修理和更换或正在进行的工作。
9.1.5 硬管和软管的接头
推荐使用弹性密封件的硬管和软管接头。当适用时,所有金属管接头均应符合ISO 8434的第1、2、3或4部分和ISO 6162或ISO 6164。所有软管接头应符合ISO 12151的第1、2、3、4或5部分。
9.1.6 管接头的额定压力
管接头的额定压力应不低于其所在系统部位的最高工作压力。
9.2 硬管的要求*
硬管应符合9.2.1和9.2.2中给出的要求。
9.2.1 钢管
钢管应符合ISO 10763中规定的技术规格。
9.2.2 其他管子
使用除钢材以外的其他管材,应由需方与供方书面商定。
9.3 管路的支承
9.3.1 间隔
如果需要,管路应利用正确设计的支承件,在其端部和沿其长度相隔一定距离牢固地支承。
表1给出了管路支承件之间最大距离的推荐值。
表1 管路支承件之间的最大距离
管子外径mm 支承件之间的最大距离m
≤10 1
>10和≤25 1.5
>25和≤50 2
>50 3
9.3.2 安装
支承件应不损害管件。
9.4 杂质
管路,包括成形孔和钻削孔,应排除如氧化皮、毛刺、切屑等有害的杂质。这些杂质可能妨碍流动,或被冲刷出来引起包含密封件和填料的任何元件发生故障和(或)损坏。
9.5 软管总成
9.5.1 要求
a)软管总成应用未经装配使用过的,并且满足在适当标准中给出的所有性能和标明要求的新软管构成;
b)应标明软管和软管总成的生产日期(例如:季度和年份);
c)应提供由软管制造商推荐的最长储存时间;
d)应提供由系统供方推荐的使用寿命;
e)软管总成不能在超过制造商推荐的额定压力下使用;
f)软管总成不能受到超过制造商推荐的冲击或冲击压力。
9.5.2 安装
软管总成的安装应:
a)具有必要的最小长度,以避免在元件工作期间软管急剧地折曲和拉紧;软管的弯曲半径不宜小于推荐的最小值;
b)在安装和使用期间,尽量减小软管的扭曲度,例如,旋转管接头卡住的情况;
c)被布置或保护,使软管外皮的摩擦损伤减到最少;
d)加以支承,假如软管总成的重量可能引起过度变形时。
9.5.3 失效的保护措施
如果软管总成的失效构成击打的危险,该软管总成应被固定或遮挡。
如果软管总成的失效构成油液喷射或燃烧的危险,则应被遮护。
9.6 快换接头
选择快换(快速拆解)接头应做到,当其被拆开时可自动地密封上游端和下游端的油液压力,以防止危险。
10 控制系统
10.1 无指令的动作
控制系统的设计应能防止执行器无指令的动作和不正确的顺序。
10.2 系统保护
10.2.1 意外的起动
系统的设计应能使其容易与能源可靠脱离,并且容易释放该系统中的有压油液,以防止意外的起动。对此,液压系统可以通过以下方式来实现:
——隔离阀机械锁定在关闭位置及卸除液压系统的压力;
——隔离电源(见GB/T 5226.1)。
10.2.2 控制或动力源失效
选择和应用电控、气控和(或)液控的液压元件应做到,当控制动力源失效时不会引起危险。
无论所用的控制能源或动力的类型如何(例如:电的、液压的等),下列作用或偶发事件(意外的或故意的)应不致产生危险;
——打开或关闭能源;
——能源下降;
——切断或重新建立能源;
当恢复控制动力源时(意外地或故意地),不应发生危险情况。
10.2.3 外部载荷
应提供一种措施,以防止在外部高载荷作用于执行器之处产生不能接受的压力。10.2.4 油液损失
当系统关机时,如果泄油会引起危险,应提供防止系统液压油液流回油箱的措施。当液压油液溢出会构成起火危险时,系统宜设计成假如管路或其他元件破裂时能自动关机。10.3 元件
10.3.1 可调整的控制机构
可调整的控制机构应保持其设定值在指定的范围内,直到重新设定。
10.3.2 稳定性
选择压力和流量控制阀时,应保证工作压力、工作温度和负载的变化不会引起失灵或危险。
10.3.3 防止违章调节
在未经授权改变压力或流量可能引起危险或失灵之处,压力和流量控制装置或其外壳应安装安全防护装置,以防止未经授权的变动。
如果改变或调整可能引起危险或失灵,应提供锁定可调节元件的设定值或锁住其外壳的措施。
10.3.4 操纵手柄
手柄的运动方向不应混淆。例如:上推手柄不应降下被控装置。
10.3.5 越权手动控制
为便于设定,应为每个执行器设置安全手动控制。
10.3.6 双手控制
控制不应使操作者暴露于机器运动引起的危险之中,并应遵守相应的国家标准。10.3.7 弹簧偏置或带定位的阀
在控制系统失效时,要求保持其位置或采取规定的安全位置的任何执行器,应靠一个具有弹簧偏置或带定位到安全位置的阀来控制。
10.4 带伺服阀和比例阀的控制系统
10.4.1 越权控制系统
在执行器被伺服阀或比例阀控制,并且控制系统的失灵可以导致执行器引起危险的场合,应提供保持或恢复这些执行器的控制手段。
10.4.2 过滤器
如果由污染引起的阀失灵会产生危险,那么宜在供油路内接近伺服阀或比例阀之处,安装无旁通的并带有明显易见的滤芯状态指示器的全流量过滤器。该滤芯的压溃强度应超过该系统最高工作压力。通过无旁通过滤器的液流阻塞不应产生危险。
10.4.3 系统清洁度
在安装伺服阀和(或)比例阀之前,该系统和液压油液宜被净化,达到制造商规定范围内的稳定的污染等级。
10.4.4 附加装置
如果无指令的动作可能引起危险,那么靠伺服阀或比例阀控制速度(转速)的执行器应具有保持或移动到安全位置的手段。
10.5 其他设计考虑
10.5.1 系统参量的监控
在系统工作参量的变化可能构成危险处,应提供该系统工作参量的清晰指示。10.5.2 测试点
推荐在整个系统上采用适当数量的测试点,不拘尺寸和复杂性。
为检测压力,设置在液压系统中的测试点应:
a)易于接近;
b)永久地固定;
c)具有永久连接的安全盖,使污染物的侵入减到最少;
d)设计成能保证该测试点在最高工作压力下安全和快速地接合。
10.5.3 系统相互作用
在一个系统内或系统一部分的工况,不应对别的系统或部分产生有害的影响,尤其当需要精确控制时。
10.5.4 复合装置控制
在系统有一个以上相互联系的自动和(或)手动控制装置,并且其中任何一个的失效会造成危险的场合,应提供保护联锁装置或其他安全手段。在适用的场合,这些联锁装置宜中断所有工作,只要这种中断本身不会引起危险或损害。
10.5.5 顺序控制
10.5.5.1 按位置定序
在任何适用之处,应使用按位置检测定序,并且当压力控制或时间控制定序本身失灵会引起危险时,应始终使用位置检测定序。
10.5.5.2 位置检测装置的布置
如果在运动顺序或循环时间已被规定之后,位置检测装置的布置发生变化,该装置应返回到他们最初的位置或应重新调整成其他的运动顺序或循环定时。
10.6 控制的布置
10.6.1 保护
控制应以提供适当保护的方式来设计或设置,以防:
a)失灵和可预测的损坏;
b)高温;
c)腐蚀性环境。
10.6.2 可接近性
控制装置应易于接近以便调整和维修,它们应位于工作地板以上最低0.6 m或最高1.8m 处,除非尺寸、功能或配管方式要求另选位置。
10.6.3 手动控制
手动控制的布置和安装应:
a)将控制设置在操作人员正常工作位置能及的范围内;
b)不要求操作者越过正在旋转或运动的机构操作控制装置;
c)不妨碍操作者所需的工作运动。
10.7 应急控制
液压系统设计应使紧急停止或紧急返回控制的操作不会导致危险。
当危险(例如起火危险)存在时,应设置液压系统紧急停止控制。至少一个紧急停止按钮应被布置成遥控的。
10.7.1 应急控制的特征
当紧急停止和紧急返回控制被应用于液压系统时,它们应:
a)易被识别;
b)设置在每个工作人员的操作位置和在所有工作状态下都易于接近;为满足这些要求,可能需要附加的控制;
c)直接操作;
d)是独立的,并且不受其他控制或节流的调节影响;
e)对于所有应急功能不需要一个以上手动控制的操作。
10.7.2 系统重新起动
在紧急停止或紧急返回之后重新起动系统不应引起危险或损坏。
11 诊断和监控*
为了使预计的维修和检修故障容易,宜采取诊断测试和状态监控的措施。设置在系统中的诊断产品及其规格应由需方与供方商定。
11.1 压力测量
永久安装的压力表,应利用压力限制器或表隔离开关来保护。
压力表量程的上限宜超过最高工作压力至少25%。
压力阻尼装置不宜与压力传感器组成一体。
11.2 油液取样
考虑到检查液压油液清洁度等级状态,应提供符合GB/T 17489的提取具有代表性油样的手段。如果在高压管路中设置取样阀,应安放提示高压喷射危险的警告标签,并应遮护取样阀。
11.3 温度检测
温度检测装置应安装在油箱内。
12 清理和涂漆
在装置的外部清理和涂漆时,敏感材料应被保护以避免不相容的液体。
在涂漆时,所有铭牌、数据标记和不宜涂漆的区域(例如:活塞杆、指示灯等)应覆盖住,
涂漆后应除去覆盖物。
13 运输准备
13.1 管路的标识
每当为了运输,系统必须拆卸时,管路和管接头应做出清晰的标识。该标识应与任何相应图样上的资料一致。
13.2 包装
在运输期间,所有装置都应以能防止其损坏、变形、污染和腐蚀及保护其标识的方式包装。
13.3 孔口的密封
仅应使用那种直到它们被除去才能重新装配的密封盖。在运输期间,在液压系统或元件上暴露的孔口应予密封,并且外螺纹应予保护。应在重新装配时,再除去该保护。
13.4 搬运设施*
运输尺寸和质量应与需方厂房可用的搬运设施(铁轨连接、起吊滑轮、通道、地面承载)一致。如果需要,液压系统应按需方与供方的商定拆成部件搬运。
14 试运行
14.1 检验试验
为确定与可适用的要求的一致性,应进行下列试验:
a)检验该系统和所有安全装置的正确操作的试验;
b)压力试验,即在所有预定应用的条件下,在可能持续的最高压力下,试验系统的各部分。
14.2 噪声*
安装的液压系统应符合供方与需方在签订合同时商定的噪声等级。
14.3 液压油液泄漏
除不足以形成油滴的微量的渗湿之外,不应允许有能测到的意外泄漏。
14.4 应提供的最终资料*
在不迟于系统交付的时间或需方与供方商定的其他时间,系统供方应向需方提供下列最终资料:
a)符合ISO 1219—2(见5.1)的最终回路图;
b)零件清单;
c)总布置图样;
d)管路和管接头的布置图;
e)时间和(或)顺序及功能的说明;
f)适用的夹具或调整工具的图样;
g)平面布置图;
h)安装图(见4.5.2)和说明;
i)必要的其他图样;
j)维修和操作的数据和手册(见5.6和5.7);
k)性能试验结果;
l)液压油液调节要求。
应提供打算使用的液压油液的材料安全数据资料及对该液压油液的处置和废弃的建议资料。其中包括,对全体人员在处理液压油液时,万一发生火灾有中毒或窒息危险时的保健要求。
当最后验收时,所有项目应与该系统相符。
14.5 更改
每当供方做出给需方带来影响的更改时,都应记录这些更改并通知需方。
14.6 检验
应通过对照系统的技术规格检验它们的同一性来验证系统及其元件。另外,应检验该系统上元件的连接,以验证其与回路图的一致性。
15 标注说明(引用本标准时)
当决定遵守本标准时,在需方与供方之间的合同中和最终资料袋内,以及适当时在目录、销售文件和报价单中应采用下列说明:
“该液压系统符合GB/T 3766—2001《液压系统通用技术条件》,其中包括需方与供方之间的补充协议。”
附录 A
(提示的附录)
需要供方与需方商定的条款
以下所列是需要供方与需方商定要求和(或)责任的本标准的条款和分条款,在正文中用星号(*)标记。
条款或分条款编号标题
4.1.2 语言
4.2 危险
4.4 系统要求
4.5 现场条件
7.6 调整
8.1.3 液压系统和润滑系统
8.1.5 注油和保持液位
8.3.3 吸油粗滤器或过滤器
8.4.1.2 冷却介质
9.2 硬管的要求
11 诊断和监控
13.4 搬运设施
14.2 噪声
14.4 应提供的最终资料
附录 B
(提示的附录)
与液压传动应用相关的危险情况
表B1中给出了可能发生的与在机器中的液压传动应用有关的危险。
表B1 危险情况一览表
危险类型相应条款在本标准中的相关条款,或其他
相关标准
ISO/TR 12100—1:1992
ISO/TR
12100—2:
1992
ISO/TR
12100—2:1992
的附录A
机械的危险
——形状,
——相关位置;
——质量和稳定性(元件的势能);
——质量和速度(元件的动能);
——机械强度不足;4.2 1.3;1.4
1.3.7
4.3.2;4.3.3
4.3.4;4.3.6
4.5.1;5.2.1;5.3.1;5.3.2;
5.6
6.1;6.2;6.3;6.3.4.3;
7;8.2;9.1.3'9.1.4;9.1.5;
9.3.1;9.3.2;9.4;9.5;
9.5.1;
静液压传动工程机械的制动系统
静液压传动工程机械的制动系统 摘要国内外研制和应用静液压传动的工程机械越来越多,本文简要介绍了其制动系统的特点、类型,分析了不同工况下制动系统的作用以及不同制动系统的应用范围。 关键词:静液压传动工程机械制动系统 根据技术要求及通行安全,采用静液压传动的工程机械与常规机械一样,需要具备行走制动、停车制动和应急制动等3套制动系统。它们的操纵装置必须是彼此独立的。 1 行车制动系统 行车制动系统应能在所以运行状态下发挥作用。它首先用以使运动中的车辆减速,继而在必要时使车辆完全停止运动处于静止状态。对行走制动系统的要求是:第一,在车辆运动的整个速度范围内均能产生足够的制动阻力,使车辆减速直至停车;第二,具有足够的耗能或贮能容量来吸收车辆的动能;第三,行走制动装置的作用必须是渐进的;第四,行走制动系统的操纵功能必须是独立的,不应受其它正常操纵机构的影响,不能在离合器分离或变速器空档时丧失制动能力。从原则上说,凡是能完全满足上述要求的装置,均可用于行走制动系统。行走制动是使用最频繁的制动装置,一般称为主制动系统。 现代工程机械行走制动系统除普遍采用带有较大容量的制动盘、鼓等摩擦式机械制动器作为主执行元件外,也越来越多地利用发动机排气节流、电涡流、液涡流等作为辅助的吸能装置。后几种装置的优点是本身没有产生磨损的元件,能更好地控制减速力(矩),从而减少主制动元件(刹车盘、片等)的磨损和延长其使用寿命。但它们的制动力都与行走速度有关,一般无法独立使车辆完全停止,只能作为辅助制动装置(缓速装置)来使用。 静液压传动系统由连接在一个闭式回路中的液压泵和液压马达构成。对这种传动装置所选用的泵和马达,除了有与一般液压元件相同的高功率密度、高效率、长寿命等性能要求外,还要求两者均能在逆向工况下运行,即在必要时马达可作为泵运行,泵可成为马达运行,使整个系统具备双向传输功率或能量的能力。这样当泵的输出流量大于马达在某一转速下需要的流量时,多余的流量就使马达驱动车辆加速,而加速力的反作用力通过马达使入口压力升高,液压能转化为车辆的动能增量;反之,如调节变量泵的排量使其通过流量不敷于马达的需求时,马达出口阻力增大,在马达轴上建立起反向扭矩阻止车辆行驶,车辆动能将通过车轮反过来的驱动马达使其在泵的工况下运行,并在马达出油口建立起压力,迫使泵按马达工况拖动发动机运转,车辆的动能将转化为热能由发动机和液压系统中的冷却器吸收并耗散掉。由于静液压传动系统产生的阻力(矩)原则上只取决于系统压力和马达排量而与行走速度无关,所以这种系统既能象上述“缓速器”那样使车辆减速,又能使其完全停止运动,不仅能满足行走制动全部功能要求,而且在制动过程中没有元件磨损且可控性良好。因此,静液压传动系统本身完全可以作为行走制动装置使用。装有静液压传动系统的车辆一般无须另行配置机械制动器,但系统中不能有驾驶员可随意操纵的使功率流中断的装置(如液压系统中的短路阀、马达与驱动之间的离合器或机械换
委托开发合同协议书(官方版)
编号:QJ-HT-0653 委托开发合同协议书(官方 版) In order to clarify their rights and obligations, sign contracts to ensure that their legitimate rights and interests are not harmed. 甲方:_____________________ 乙方:_____________________ 日期:_____________________ --- 专业合同范本系列下载即可用---
委托开发合同协议书(官方版) 说明:该合同书适用于甲乙双方为明确各自的权利和义务,经友好协商签署合同,在合同期限内按照合同规定或者依照法律规定履行义务,保证权利双方合法权益不受损害,文档可下载收藏或打印使用(使用时请先阅读条款是否适用)。 表达委托开发合同协议书 本合同由双方与年月日在签署: 甲方: 联系人: 联系电话: 地址: 邮编: 乙方: 联系人: 联系电话: 地址:
邮编: 电话: 银行帐号: 开户银行: 现甲方将X系统将软件委托乙方开发,为明确双方责任,本着相互合作、互惠互利的原则,共同协商达成如下协议: 一、开发内容 1.标的名称:X系统开发 2.标的开发内容: 3.标的开发周期: 自本合同签署之日2个月,完成项目开发。 二、交付 乙方完成标的开发后,交付内容应包括如下: 1) 数据库设计文档 2) SourceCode 3) 系统部署操作手册
三、验收 1.甲方按照功能需求和验收标准,对乙方的开发成果及时进行验收; 2.验收期限:自开发成果全部交付之日起5个工作日内,甲方进行软件最终验收,如验收合格,甲方应出具工程验收确认单证明验收通过;如验收不合格,甲方有权要求乙方修改,乙方应立即进行修改并再次提交甲方验收直至验收合格。如果因此延迟完成开发工作的,乙方承担违约责任。 四、开发费与付款 1.总标的开发费:人民币伍万伍仟伍佰(55,500)元整; 2.付款进度: 1) 在本合同签署之日起5个工作日内,甲方支付乙方总标的开发费的60%,即人民币叁万叁仟叁佰(33,300)元整; 2) 系统开发结束,乙方向甲方申请验收,验收通过后10个工作日内,甲方向乙方支付开发费总额的40%,即人民币贰万贰仟贰佰(22,200)元整,乙方提交所有资料; 3. 项目开发和维护期间如需乙方前往异地城市(非上海市)提供技术服务,技术培训或系统调试,差旅费用由甲方承担。
液压操作系统技术协议
大功率无极绳连续牵引车的液压操作控制系统研制项目 技术协议 甲方:上海大屯能源股份有限公司拓特机械制造厂 乙方:山东科技大学 甲方就自主研发项目—大功率无极绳连续牵引车的液压操作控制系统,委托乙方设计、制造。经双方充分论证和友好协商,达成技术协议如下: 1、系统应具有防爆功能,适合煤矿井下工作环境。 2、系统应包括液压站、操作台、油缸和管线路接口四部分。其中液压站安装备用电机和油泵;操作台通过油管和电线与液压站和牵引车主机连接,一实现有线遥控;油缸包括张紧油缸 1套、安全制动油缸 1 套、离合和工作制动油缸各 1套;安装在牵引车主机上的管线路接口应设计成阀块形式。 3、系统主要参数 张紧油缸:D?160/d ?80/S1800 安全制动油缸:D?160/d ?80/S50 离合器油缸:D?125/d ?63/S30 工作制动油缸:D?125/d ?63/S30 (同离合器油缸) 溢流阀调定压力:7.5MPa 电磁阀动作电压:36V 绞车电机电压:660/1140V 蓄能器充气压力:5MPa 工作介质:46号液压油 4、系统所有电气元件如电磁阀、按钮等必须具有有效的MA证。 5、操作台主视面板上安 2 块压力表,预留行程表安装位置。俯视图面板上左侧装 2 个手动换向阀;靠右侧为油泵电机的起动、停止按钮和指示灯;装有无极绳连续牵引车主机双速电机的启动、停止按钮和指示灯;中间布置电磁阀 YA1 的通电、断电按钮。
6、所有油口采用公称内径为 10 的 KJ 系列快速接头。
7、甲方提供液压站用防爆电机 2 台,提供所有连接高压油管和电线、电缆 8、甲方提供所有油缸草图(包括油缸连接尺寸、缸径、杆径尺寸和安全制动油缸内部碟簧规格数量和装配方式),乙方按图设计图纸、制造,甲方按草图技术要求验收。 9、乙方根据甲方要求设计系统图,经甲方确认签字后设计工作图。 10、在乙方制造完成后,甲方前往合作商家现场验收,验收合格后运送到甲方装配现场装配到主机上,乙方与甲方进行整机调试,及时改进完善设计。 11、乙方想甲方提供该系统的设计计算书和整套图纸。 12、质量及服务承诺按相关工业产品标准执行。 13、未尽事宜,双方协商解决。 14、本协议作为合同书内容,具有合同法律效力。 甲方:上海大屯能源股份有限公司拓特机械制造厂 代表(签字): 日期:乙方:山东科技大学代表(签字): 日期:
液压传动系统的设计和计算word文档
10 液压传动系统的设计和计算 本章提要:本章介绍设计液压传动系统的基本步骤和方法,对于一般的液压系统,在设计过程中应遵循以下几个步骤:①明确设计要求,进行工况分析;②拟定液压系统原理图;③计算和选择液压元件;④发热及系统压力损失的验算;⑤绘制工作图,编写技术文件。上述工作大部分情况下要穿插、交叉进行,对于比较复杂的系统,需经过多次反复才能最后确定;在设计简单系统时,有些步骤可以合并或省略。通过本章学习,要求对液压系统设计的内容、步骤、方法有一个基本的了解。 教学内容: 本章介绍了液压传动系统设计的内容、基本步骤和方法。 教学重点: 1.液压元件的计算和选择; 2.液压系统技术性能的验算。 教学难点: 1.泵和阀以及辅件的计算和选择; 2.液压系统技术性能的验算。 教学方法: 课堂教学为主,充分利用网络课程中的多媒体素材来表示设计的步骤及方法。 教学要求: 初步掌握液压传动系统设计的内容、基本步骤和方法。
10.1 液压传动系统的设计步骤 液压传动系统的设计是整机设计的一部分,它除了应符合主机动作循环和静、动态性能等方面的要求外,还应当满足结构简单,工作安全可靠,效率高,经济性好,使用维护方便等条件。液压系统的设计,根据系统的繁简、借鉴的资料多少和设计人员经验的不同,在做法上有所差异。各部分的设计有时还要交替进行,甚至要经过多次反复才能完成。下面对液压系统的设计步骤予以介绍。 10.1.1 明确设计要求、工作环境,进行工况分析 10.1.1.1 明确设计要求及工作环境 液压系统的动作和性能要求主要有:运动方式、行程、速度范围、负载条件、运动平稳性、精度、工作循环和动作周期、同步或联锁等。就工作环境而言,有环境温度、湿度、尘埃、防火要求及安装空间的大小等。要使所设计的系统不仅能满足一般的性能要求,还应具有较高的可靠性、良好的空间布局及造型。 10.1.1.2 执行元件的工况分析 对执行元件的工况进行分析,就是查明每个执行元件在各自工作过程中的速度和负载的变化规律,通常是求出一个工作循环内各阶段的速度和负载值。必要时还应作出速度、负载随时间或位移变化的曲线图。下面以液压缸为例,液压马达可作类似处理。 就液压缸而言,承受的负载主要由六部分组成,即工作负载,导向摩擦负载,惯性负载,重力负载,密封负载和背压负载,现简述如下。 (1)工作负载w F 不同的机器有不同的工作负载,对于起重设备来说,为起吊重物的重量;对液压机来说,压制工件的轴向变形力为工作负载。工作负载与液压缸运动方向相反时为正值,方向相同时为负值。工作负载既可以为定值,也可以为变量,其大小及性质要根据具体情况加以分析。
工程机械液压系统的基本构成及元件介绍
工程机械液压系统的基本构成及元件介绍 工程机械的液压系统,是工程机械很重要的一个组成部分。它不仅关系到设备动臂和铲斗等的使用,还关系到设备的转向等问题。对工程机械的液压系统的构成有一个初步的了解,能够让工程机械的使用者更好的使用设备,减少故障和事故发生的可能性。今天,小编将带您初步地了解工程机械的液压系统的基本构成和元件情况,希望这篇文章会对您有所帮助。 所谓的液压系统就是使用有连续流动性的油液(即所谓液压油),通过液压泵把驱动液压泵的电动机或发动机的机械能转换成油液的压力能,经过各种控制阀(压力控制阀、流量控制阀、方向控制阀等),送到作为执行器的液压缸或液压马达中,再转换成机械动力去驱动负载。 一、工程机械液压系统各组成部分及功能: 1原动机(电动机、发动机):向液压系统提供机械能 2液压泵(齿轮泵、叶片泵、柱塞泵):把原动机所提供的机械能转变成油液的压力能,输出高压油液 3执行器(液压缸、液压马达、摆动马达):把油液的压力能转变成机械能去驱动负载作功,实现往复直线运动、连续转动或摆动 4控制阀(压力控制阀、流量控制阀、方向控制阀):控制从液压泵到执行器的油液的压力、流量和流动方向,从而控制执行器的力、速度和方向 5油箱:盛放液压油,向液压泵供应液压油,回收来自执行器的完成了能量传递任务之后的低压油液 6管路:输送油液 7过滤器:滤除油液中的杂质,保持系统正常工作所需的油液清洁度 8密封:在固定连接或运动连接处防止油液泄漏,以保证工作压力的建立 9蓄能器:储存高压油液,并在需要时释放之 10热交换器(散热器):控制油液温度 11液压油:是传递能量的工作介质,也起润滑和冷却作用一个系统中不一定包含以上所有的组成部分,但是液压泵、执行器、控制阀、液压油是必须有的。 二、液压系统的分类: 1、开式系统和闭式系统: 按照液压回路的基本构成可以把液压系统划分为开式系统和闭式系统。 开式系统: 泵所输出的压力油在完成做功任务后从执行驶器返回油箱。应用普遍,但油箱要足够的大。有油缸的系统肯定是开式系统
液压机机技术协议
HJS32-315四柱油压机 技术协议 一、基本参数 二、特点和性能 1、机械部份:
1)机身采用三梁四柱式结构,上梁、工作台通过立柱和紧固螺母、调整螺母结合成一个固定机架,机架精度靠调节螺母调整,具有良好的强度、刚度和精度保持性,上梁、工作台、滑块等大件为钢板焊接件,材料为 Q235-B,经计算机优化设计,采用二氧化碳气体保护焊,焊后消除应力,焊缝经打磨,无焊渣和流疤现象,机身外观平整,无明显凹凸现象。 2)滑块采用四柱导向方式,具有良好的导向性能和精度保持性,滑块下方布有 T 形槽,用于安装模具,立柱为 45#钢,导向表面热处理硬度为 HRC45-50。 3)上梁为箱形结构件,经计算机优化设计,上梁内装有主工作油缸,上面装有充液油箱。4)工作台为箱形结构件,经计算机优化设计,工作台面上方布有T 形槽。 5)主油缸为一只活塞缸,布置在上横梁孔内,油缸体的材料为45号锻钢。 2、液压系统: 1)液压动力机构安装在机身右方,由泵、电机、阀集成块,油箱等组成,动力机构中包 括油液过滤,油温油位显示等多种装置,主油泵为恒功率轴向柱塞泵,输出流量可随压力 的变化而变化。 2)液压系统采用二通插装阀,具有体积小、结构紧凑、流阻小、流量大、动作灵敏、工作可靠、密封性能好等特点。主缸下腔有二级支承系统,确保在某一元件突然失灵的情况下滑块不会下落。主缸和顶出缸压力可在 5MPa~25MPa 间调节,系统中设有安全阀,以限制液 压系统的最高压力。 3)油箱为钢板焊接结构,油箱侧面开有清洗窗口,设有油标。空气滤清器、阀集成块等在 油箱盖板上方有序排列。 4)主要液压管路设有布局合理的抗震管夹,以防止高压管道的震动和泄漏,管道安装前进行酸洗和钝化处理,以保证油液的清洁度。 3、电气系统: 1)设有独立的电气控制柜,按钮集中控制。本机电源为 AC380V,50HZ;控制电源为 AC220V;先导阀电磁铁电源为 DC24V。 2)采用 PLC 可编程序控制器。在 PLC 输出点与电磁阀之间,通过中间继电器连接 3)提供湖机液压机运行控制软件 V1.0。 4、操作系统: 1)可实现调整、手动和半自动三种操作方式。 调整(点动):操作相应的功能按钮完成相应的动作,每按一次按钮完成相应动作的一次点
液压合同范本
*******有限公司 技 术 协 议 甲方: 乙方: 二零一九年一月十七日
目录 1、供货内容及范围 (3) 2、技术要求 (3) 3、主要设备性能参数 (4) 4、产品制造、监制、安装验收标准及安装调试 (4) 5、技术资料、文件的提供及交付进度 (4) 6、伴随服务内容、方案及承诺 (4) 7、设备交货期、质保期及售后服务承诺 (4) 8、涂装、包装和运输 (5) 9、质量保证与售后服务 (5) 10、联系人及联系电话 (5) 11、其他 (5)
集团股份有限公司(以下简称甲方)****(以下简称乙方)就****液压件备件产品的供应、服务等事宜,经协商达成如下技术协议: 1、供货内容及范围(合同编号:) 2、技术要求 2.1液压元件的基本参数、安装连接尺寸,应符GB/T2346、 GB/T2347、GB/T2348、GB/T2349、GB/T2350、GB/T2353、 GB/T2514、GB/T2877、GB/T2878、GB/T8098、GB/T8100、 GB/T8101、GB/T14036的规定。 2.2对液压元件的承压通道应进行耐压试验,试验方法应按各元件相关标准的规定。 3、主要设备性能参数 详见产品说明及装箱单 4、产品制造、监制、安装验收标准及安装调试 4.1液压元件制造符合通用技术标准GB/T 7935-2005 4.2乙方在为甲方提供的配套件出厂之前应由富有经验的检验人员进行严格的出厂检验并随同配套件提供产品合格证书。 5、技术资料、文件的提供及交付进度 5.1乙方按其产品系列为甲方提供的配套件应能充分满足和达到甲方所要求的技术性能、参数指标和质量要求。
技术开发合同(详细版)
编号:QJ-HT-0348技术开发合同(详细版) Both parties shall perform their obligations as agreed in the contract or in accordance with the law within the term of the contract. 甲方:_____________________ 乙方:_____________________ 日期:_____________________ --- 专业合同范本系列下载即可用---
技术开发合同(详细版) 说明:该合同书适用于甲乙双方为明确各自的权利和义务,经友好协商双方同意签署合同,在合同期限内按照合同约定或者依照法律规定履行义务,可下载收藏或打印使用(使用时请先阅读条款是否适用)。 合同编号:____________________ 项目名称:_____________________ 签订时间:_____________________ 签订地点:_____________________ 有效期限:_____________________ 甲方:_________________________ 乙方:_________________________ 丙方:_________________________ 本合同甲方委托乙方研究开发______________项目,并支付研究开发经费和报酬,乙方接受委托并进行此项研究开发工作。双方经过平等协商,在真
实、充分地表达各自意愿的基础上,根据中华人民共和国合同法》的规定,达成如下协议,并由双方共同恪守。 第一条本合同研究开发项目的要求如下: 1.技术目标:___________________________________________________________ 2.技术内容:___________________________________________________________ 3.技术方法和路线_______________________________________________________ 第二条乙方应在本合同生效后_____日内向甲方提交研究开发计划。研究开发计划应包括以下主要内容: 1.______________________________________________________ 2.______________________________________________________ 3.______________________________________________________ 第三条乙方应按下列进度完成研究开发工作: 1._____________________________________________________
(完整版)液压常用计算公式
液压常用计算公式 1、齿轮泵流量(min /L ): 1000Vn q o =,1000 o Vn q η= 说明:V 为泵排量 (r ml /);n 为转速(min /r );o q 为理论流量(min /L );q 为实际流量(min /L ) 2、齿轮泵输入功率(kW ): 60000 2Tn P i π= 说明:T 为扭矩(m N .);n 为转速(min /r ) 3、齿轮泵输出功率(kW ): 612 60'q p pq P o == 说明:p 为输出压力(a MP );'p 为输出压力(2 /cm kgf );q 为实际流量(min /L ) 4、齿轮泵容积效率(%): 100V ?=o q q η 说明:q 为实际流量(min /L );o q 为理论流量(min /L ) 5、齿轮泵机械效率(%): 10021000?=Tn pq m πη 说明:p 为输出压力(a MP ); q 为实际流量(min /L );T 为扭矩(m N .); n 为转速(min /r )
6、齿轮泵总效率(%): m ηηη?=V 说明:V η为齿轮泵容积效率(%);m η为齿轮泵机械效率(%) 7、齿轮马达扭矩(m N .): π 2q P T t ??=,m t T T η?= 说明:P ?为马达的输入压力与输出压力差 (a MP ); q 为马达排量(r ml /);t T 为马达的理论扭矩(m N .) ;T 为马达的实际输出扭矩(m N .);m η为马达的机械效率(%) 8、齿轮马达的转速(min /r ): V q Q n η?= 说明:Q 为马达的输入流量(min /ml ); q 为马达排量(r ml /); V η为 马达的容积效率(%) 9、齿轮马达的输出功率(kW ): 310 602?=nT P π 说明:n 为马达的实际转速(min /r ); T 为马达的实际输出扭矩(m N .) 10、液压缸面积(2cm ): 42 D A π= 说明:D 为液压缸有效活塞直径(cm ) 11、液压缸速度(min m ): A Q V 10=
液压系统设计步骤
第九章液压传动系统设计与计算 液压系统设计的步骤大致如下: 1.明确设计要求,进行工况分析。 2.初定液压系统的主要参数。 3.拟定液压系统原理图。 4.计算和选择液压元件。 5.估算液压系统性能。 6.绘制工作图和编写技术文件。 根据液压系统的具体内容,上述设计步骤可能会有所不同,下面对各步骤的具体内容进行介绍。 第一节明确设计要求进行工况分析 在设计液压系统时,首先应明确以下问题,并将其作为设计依据。 1.主机的用途、工艺过程、总体布局以及对液压传动装置的位置和空间尺寸的要求。 2.主机对液压系统的性能要求,如自动化程度、调速范围、运动平稳性、换向定位精度以及对系统的效率、温升等的要求。 3.液压系统的工作环境,如温度、湿度、振动冲击以及是否有腐蚀性和易燃物质存在等情况。 图9-1位移循环图 在上述工作的基础上,应对主机进行工况分析,工况分析包括运动分析和动力分析,对复杂的系统还需编制负载和动作循环图,由此了解液压缸或液压马达的负载和速度随时间变化的规律,以下对工况分析的内容作具体介绍。 一、运动分析 主机的执行元件按工艺要求的运动情况,可以用位移循环图(L—t),速度循环图(v—t),或速度与位移循环图表示,由此对运动规律进行分析。 1.位移循环图L—t 图9-1为液压机的液压缸位移循环图,纵坐标L表示活塞位移,横坐标t表示从活塞启动到返回原位的时间,曲线斜率表示活塞移动速度。该图清楚地表明液压机的工作循环分别由快速下行、减速下行、压制、保压、泄压慢回和快速回程六个阶段组成。 2.速度循环图v—t(或v—L) 工程中液压缸的运动特点可归纳为三种类型。图9-2为三种类型液压缸的v—t图,第一种如图9-2中实线所示,液压缸开始作匀加速运动,然后匀速运动,
技术开发合同协议书
技术开发合同协议书文件编号TT-00-PPS-GGB-USP-UYY-0089
合同登记编号: 技术开发合同 项目名称:多功能应急救援装备开发 甲方(委托方):山东鲁班智能装备有限公司 乙方(受托方):山东大学 签订地点:山东省济南市 签订日期:2015 年01月09日 有效日期: 2015年01月09日至 2018年01月08日 国家科学技术部监制
依据《中华人民共和国合同法》的规定,合同双方就多功能应急救援设备开发项目,经协商一致,签订本合同。 一、标的内容、形式和要求: 本合同研究开发项目的要求如下: 1、技术目标 乙方完成多功能应急救援设备中电控系统设计开发、机械机构有限元分析及动画模拟,协助甲方完成总体策划、结构设计和液压系统设计。通过合作开发,在甲方处试制第一台样机,使其具有多功能、轻量化和智能化的特点。 2、技术内容 (1)、电控系统的开发;利用C/C++等编程语言编写控制系统程序,采用CAN总线作为控制局域网总线,结合传感器、操作手杆和液压系统等硬件,实现叁臂的控制、支脚等位置的检测和生命探测等; (2)、机械结构有限元分析及动画模拟;根据甲方设计的机械机构建立三维模型,利用ANSYS、ADAMS等软件对模型展开有限元分析、优化及动画模拟; (3)、协助甲方完成总体策划、结构设计和液压系统设计。
3、技术方法和路线 通过对多功能应急救援设备的功能分析,协助甲方完成结构设计和液压设计,开发电控系统并进行有限元分析及动画模拟。 4、双方指定项目负责人: 甲方:赵修林(总经理、高级工程师) 乙方:万熠(副院长、副教授) 二、履行的期限、地点和方式: 本合同履行期限为叁年,地点为济南市。 三、工作进度 乙方应按下列进度完成研究开发工作 1、2015.1-2015.2完成对现有工程机械(如挖掘机等)电控系统调研,并将调研情况提交给甲方,完成电控系统硬件选型,细化研究计划和任务分解。(第一阶段) 2、2015.3-2015.7完成电控系统设计编程等,结合液压等硬件进行一系列实验,提供相关测试资料给甲方。完成机械结构有限元仿真及动画模拟。(第二阶段)
液压油缸设计计算公式
液压油缸的主要设计技术参数 一、液压油缸的主要技术参数: 1.油缸直径;油缸缸径,内径尺寸。 2. 进出口直径及螺纹参数 3.活塞杆直径; 4.油缸压力;油缸工作压力,计算的时候经常是用试验压力,低于16MPa乘以1.5,高于16乘以1.25 5.油缸行程; 6.是否有缓冲;根据工况情况定,活塞杆伸出收缩如果冲击大一般都要缓冲的。 7.油缸的安装方式; 达到要求性能的油缸即为好,频繁出现故障的油缸即为坏。应该说是合格与不合格吧?好和合格还是有区别的。 二、液压油缸结构性能参数包括:1.液压缸的直径;2.活塞杆的直径;3.速
度及速比;4.工作压力等。 液压缸产品种类很多,衡量一个油缸的性能好坏主要出厂前做的各项试验指标,油缸的工作性能主要表现在以下几个方面: 1.最低启动压力:是指液压缸在无负载状态下的最低工作压力,它是反映液压缸零件制造和装配精度以及密封摩擦力大小的综合指标; 2.最低稳定速度:是指液压缸在满负荷运动时没有爬行现象的最低运动速度,它没有统一指标,承担不同工作的液压缸,对最低稳定速度要求也不相同。 3.内部泄漏:液压缸内部泄漏会降低容积效率,加剧油液的温升,影响液压缸的定位精度,使液压缸不能准确地、稳定地停在缸的某一位置,也因此它是液压缸的主要指标之。 液压油缸常用计算公式 液压油缸常用计算公式
项目公式符号意义 液压油缸面积(cm 2 ) A =πD 2 /4 D :液压缸有效活塞直径(cm) 液压油缸速度(m/min) V = Q / A Q :流量(l / min) 液压油缸需要的流量(l/min) Q=V×A/10=A×S/10t V :速度(m/min) S :液压缸行程(m) t :时间(min) 液压油缸出力(kgf) F = p × A F = (p × A) -(p×A) ( 有背压存在时) p :压力(kgf /cm 2 ) 泵或马达流量(l/min) Q = q × n / 1000 q :泵或马达的几何排量(cc/rev) n :转速(rpm ) 泵或马达转速(rpm) n = Q / q ×1000 Q :流量(l / min) 泵或马达扭矩(N.m) T = q × p / 20π 液压所需功率(kw) P = Q × p / 612 管内流速(m/s) v = Q ×21.22 / d 2 d :管内径(mm) 管内压力降(kgf/cm 2 ) △ P=0.000698×USLQ/d 4 U :油的黏度(cst) S :油的比重 L :管的长度(m) Q :流量(l/min) d :管的内径(cm) 液压常用计算公式
四柱液压机购销合同
液压机购销合同 合同编号: 20180801 买方:____________________________ (以下简称甲方) 卖方:____________________________ (以下简称乙方) 根—及国家有关法律法规的规定,甲、乙、双方经协商一致, 特此签订本合同,以资双方共同遵照执行。 一、产品品名、规格型号、数量、价格、生产厂商、交货期 二、付款方式 2.1 设备总价包括设备造价、运输费、保险费及安装调试费。 2.2 合同签订生效后,甲方预付款 30%即_____________ ,乙方安排生产。本合同项下货物全部 生产完成,乙方接到甲方的发货通知,甲方需支付乙方货款 60%即______________ 。乙方负责 运输到甲方指定地点,经甲方验收合格后,甲方需支付乙方剩余货款 10%即____________ 后, 乙方负责安装调试交付使用,乙方安装人员在没有经过甲方同意,安装人员不得撤离安装现场。 2.3 按以下第一种方式结算:_______________ ①银行电汇②现金③支票 三、交货及运输 3.1 运输费用由乙方承担,送货至甲方指定地点。请填写安装地点:____________________ 3.2 交货期:合同签订生效后,甲方基础施工完毕,乙方在接到甲方发货通知后____ 日内 发货,乙方负责安装调试。 四、货物验收 4.1 甲方收货后按照国家制造相关规定的出厂标准进行验收。 4.2乙方负责向甲方提供货物出厂给付用户的装箱单,原装产品合格证各一份,说明书 等常规资料各一份。 4.3交货后—个工作日内,甲方应及时安排上述货物的验收。 五、产品质量 5.1 设备保修期为设备验收合格后_______ 保修—个月,__________ 保修_个月;设备 ____________ 在质保期内免费进行保修,设备________ 保证期不少于自交货起______ 个月。 5.2 设备如使用非_____ 原装的耗件由此引起的设备故障不属于保修范围。
液压缸计算公式
1、液压缸内径和活塞杆直径的确定 液压缸的材料选为Q235无缝钢管,活塞杆的材料选为Q235 液压缸内径: p F D π4= =??14.34= F :负载力 (N ) A :无杆腔面积 (2m m ) P :供油压力 (MPa) D :缸筒内径 (mm) 1D :缸筒外径 (mm) 2、缸筒壁厚计算 π×/≤≥ηδσψμ 1)当δ/D ≤0.08时 p D p σδ2max 0> (mm ) 2)当δ/D=0.08~0.3时 max max 03-3.2p D p p σδ≥ (mm ) 3)当δ/D ≥0.3时 ??? ? ?? -+≥max max 03.14.02p p D p p σσδ(mm ) n b p σσ= δ:缸筒壁厚(mm ) 0δ:缸筒材料强度要求的最小值(mm )
max p :缸筒内最高工作压力(MPa ) p σ:缸筒材料的许用应力(MPa ) b σ:缸筒材料的抗拉强度(MPa ) s σ:缸筒材料屈服点(MPa ) n :安全系数 3 缸筒壁厚验算 2 1221s ) (35 .0D D D PN -≤σ(MPa) D D P s rL 1 lg 3.2σ≤ PN :额定压力 rL P :缸筒发生完全塑性变形的压力(MPa) r P :缸筒耐压试验压力(MPa) E :缸筒材料弹性模量(MPa) ν:缸筒材料泊松比 =0.3 同时额定压力也应该与完全塑性变形压力有一定的比例范围,以避免塑性变形的发生,即: ()rL P PN 42.0~35.0≤(MPa) 4 缸筒径向变形量 ??? ? ??+-+=?ν221221D D D D E DP D r (mm ) 变形量△D 不应超过密封圈允许范围 5 缸筒爆破压力 D D P E b 1 lg 3.2σ=(MPa)
液压泵站技术协议
DGTA20120038 正本成都科技有限公司 液压油站 技术文件 设备名称: 液压油站 二○一二年七月 1
1.1 设备名称:DGXT12020 液压泵站(卓尔能) 1.2 数量:1 套 2.设备用途 为试验设备提供液压动力源 3.设备使用条件 3.1 安装位置:室内 3.2 能源介质、气象条件: (1)气象资料 气温:月平均气温最高35 摄氏度, 极端最高气温38 摄氏度,月平均最低气温5 摄氏度,年平均气温:25 摄氏度。 (2)电源: 电机电压:380 V 电磁铁电压:DC24V。 频率:50 Hz。 4.设备组成及主要技术参数 4.1 设备组成 油箱.泵.电机.阀组.附件.执行元件.电控部分 4.2 设备技术参数及要求 (1) 液压站规格及性能要求
a.油泵:公称流量:Q= 7 L/min,工作压力:P= 10 MPa 电机参数:电机型号:M2QA-110L-4-B5,功率:2.2 Kw,转速:n=1450rpm 工作制度:间歇工作 3 b.下部油箱 容量:50 L 材料:Q235 (2) 系统工作介质 a.系统工作介质:VG46#抗磨液压油 b.工作介质粘度:46cst@40°C c.工作介质清洁度:NAS9 级(NAS1638 标准) d.系统正常工作油温范围:30℃≤t≤60℃ (3) 各用电元件电源参数: a.电磁换向阀:V=DC24 V b.电机:V=380 V 50Hz 5.技术要求 5.1 材料要求 钢结构构件材料应符合国家相关标准要求。
5.2 工作要求 1. 满足流量和压力要求。 2. 带有冷却器。 3. 按照原理图配置相应控制阀。 5.3 涂装要求 设备色标按卓尔能机电设备(上海)有限公司标准要求执行。6.设备供货范围及装备水平 6.1 供货范围 (1)液压站1 套。 (2) 液压站说明书和质量合格证。 4 6.2 交货状态 液压站应在制造厂整体装配好。 油循环前的清洗、除锈等工作均由设备制造厂负责,按相关标准执行。 6.3 检验 设备交货前5 天,供货方应提交检验大纲,并按检验大纲对设备进行检验。
四柱液压机购销合同
液压机购销合同 合同编号:20180801 买方:(以下简称甲方) 卖方:(以下简称乙方) 根据《中华人民共和国合同法》及国家有关法律法规的规定,甲、乙、双方经协商一致,特此签订本合同,以资双方共同遵照执行。 2.1设备总价包括设备造价、运输费、保险费及安装调试费。 2.2合同签订生效后,甲方预付款30%即,乙方安排生产。本合同项下货物全部生产完成, 乙方接到甲方的发货通知,甲方需支付乙方货款60%即。乙方负责运输到甲方指定地点,经甲方验收合格后,甲方需支付乙方剩余货款10%即后,乙方负责安装调试交付使用,乙方安装人员在没有经过甲方同意,安装人员不得撤离安装现场。 2.3按以下第一种方式结算: ①银行电汇②现金③支票 三、交货及运输 3.1运输费用由乙方承担,送货至甲方指定地点。请填写安装地点: 3.2交货期:合同签订生效后,甲方基础施工完毕,乙方在接到甲方发货通知后 日内发货,乙方负责安装调试。 四、货物验收 4.1甲方收货后按照国家制造相关规定的出厂标准进行验收。 4.2乙方负责向甲方提供货物出厂给付用户的装箱单,原装产品合格证各一份,说明书 等常规资料各一份。 4.3交货后个工作日内,甲方应及时安排上述货物的验收。 五、产品质量 5.1设备保修期为设备验收合格后保修个月,保修个月;设备 在质保期内免费进行保修,设备保证期不少于自交货起个月。 5.2设备如使用非原装的耗件由此引起的设备故障不属于保修范围。 六、售后服务 乙方须向甲方提供以下售后服务: 6.1无偿向甲方相关人员提供有关乙方所销售产品的正确安装、操作使用及日常维护保养的 培训。 6.2无偿向甲方相关人员提供使用乙方所销售产品时的现场技术指导。 6.3无偿协助甲方相关人员制定甲方内部有关乙方所销售产品的操作及保养规程。 6.4根据乙方相关的服务标准或双方共同约定的服务标准提供维修或保修。
液压常用计算公式
液压常用计算公式 1、齿轮泵流量(min /L ): 1000Vn q o =,1000 o Vn q η= 说明:V 为泵排量(r ml /);n 为转速(min /r );o q 为理论流量 (min /L );q 为实际流量(min /L ) 2、齿轮泵输入功率(kW ): 说明:T 为扭矩(m N .);n 为转速(min /r ) 3、齿轮泵输出功率(kW ): 说明:p 为输出压力(a MP );'p 为输出压力(2 /cm kgf );q 为实际流量(min /L ) 4、齿轮泵容积效率(%): 说明:q 为实际流量(min /L );o q 为理论流量(min /L ) 5、齿轮泵机械效率(%): 说明:p 为输出压力(a MP ); q 为实际流量(min /L );T 为扭矩 (m N .);n 为转速(min /r ) 6、齿轮泵总效率(%): 说明:V η为齿轮泵容积效率(%);m η为齿轮泵机械效率(%) 7、齿轮马达扭矩(m N .): π 2q P T t ??=,m t T T η?=
说明:P ?为马达的输入压力与输出压力差(a MP ); q 为马达排量 (r ml /);t T 为马达的理论扭矩(m N .);T 为马达的实际输出扭矩(m N .);m η为马达的机械效率(%) 8、齿轮马达的转速(min /r ): 说明:Q 为马达的输入流量(min /ml ); q 为马达排量(r ml /); V η为马达的容积效率(%) 9、齿轮马达的输出功率(kW ): 说明:n 为马达的实际转速(min /r ); T 为马达的实际输出扭矩(m N .) 10、液压缸面积(2 cm ): 说明:D 为液压缸有效活塞直径(cm ) 11、液压缸速度(min m ): 说明:Q 为流量(min L );A 为液压缸面积(2cm ) 12、液压缸需要的流量(min L ): 说明:V 为速度(min m );A 为液压缸面积(2 cm );S 为液压缸行程(m );t 为时间(min ) 13、液压缸的流速(s m /): 2114D Q A Q V V V πηη==,) (42222d D Q A Q V V V -==πηη 说明:Q 为供油量(s m /3 );V η为油缸的容积效率(%);D 为无杆腔活塞直径(m );d 为活塞杆直径(m ) 14、液压缸的推力(N ):
典型液压系统汇总
单元七典型液压系统 学习目标: 1.掌握读懂液压系统图的阅读和分析方法 2.掌握YT4543型液压动力滑台液压系统的组成、工作原理和特点 3.掌握YB32-200型压力机液压系统的组成、工作原理和特点 4.掌握Q2—8汽车起重机液压系统的组成、工作原理和特点 5.能绘制电磁铁动作循环表 重点与难点: 典型液压系统是对以前所学的液压件及液压基本回路的结构、工作原理、性能特点、应用,对液压元件基本知识的检验与综合,也是将上述知识在实际设备上的具体应用。本章的重点与难点均是对典型液压系统工作原理图的阅读和各系统特点的分析。对于任何液压系统,能否读懂系统原理图是正确分析系统特点的基础,只有在对系统原理图读懂的前提下,才能对系统在调速、调压、换向等方面的特点给以恰当的分析和评价,才能对系统的控制和调节采取正确的方案。因此,掌握分析液压系统原理图的步骤和方法是重中之重的内容。 1.分析液压系统工作原理图的步骤和方法 对于典型液压系统的分析,首先要了解设备的组成与功能,了解设备各部件的作用与运动方式,如有条件,应当实地考察所要分析的设备,在此基础上明确设备对液压系统的要求,以此作为液压系统分析的依据;其次要浏览液压系统图,了解所要分析系统的动力装置、执行元件、各种阀件的类型与功能,此后以执行元件为中心,将整个系统划分为若干个子系统油路;然后以执行元件动作要求为依据,逐一分析油路走向,每一油路均应按照先控制油路、后主油路,先进油、后回油的顺序分析;再后就是针对执行元件的动作要求,分析系统的方向控制、速度控制、压力控制的方法,弄清各控制回路的组成及各重要元件的作用;更后就是通过对各执行元件之间的顺序、同步、互锁、防干扰等要求,分析各子系统之间的联系;最后归纳与总结整个液压系统的特点,加深对系统的理解。 2.在此选用YT4543型组合机床动力滑台的液压系统,作为金属切削专用机床进给部件的典型代表。此系统是对单缸执行元件,以速度与负载的变换为主要特点。要求运动部件实现“快进一一工进一二工进一死挡铁停留一快退—原位停止”的工作循环。具有快进运动时速度高负载小与工进运动时速度低负载大的特点。系统采用限压式变量泵供油,调速阀调速的容积节流调速方式,该调速方式具有速度刚性好
液压系统的设计计算
液压系统的设计计算2 题目:一台加工铸铁变速箱箱体的多轴钻孔组合机床,动力滑台的动作顺序为快速趋进工件→Ⅰ工进→Ⅱ工进→加工结束块退→原位停止。滑台移动部件的总重量为5000N ,加减速时间为0.2S 。采用平导轨,静摩擦系数为0.2,动摩擦系数为0.1。快进行程为200MM ,快进与快退速度相等均为min /5.3m 。Ⅰ工进行程为100mm ,工进速度为min /100~80mm ,轴向工作负载为1400N 。Ⅱ工进行程为0.5mm ,工进速度为min /50~30mm ,轴向工作负载为800N 。工作性能要求运动平稳,试设计动力滑台的液压系统。 解: 一 工况分析 工作循环各阶段外载荷与运动时间的计算结果列于表1 液压缸的速度、负载循环图见图1
二 液压缸主要参数的确定 采用大、小腔活塞面积相差一倍(即A 1=2A 2)单杆式液压缸差动联接来达到快 速进退速度相等的目的。为了使工作运动平稳,采用回油路节流调速阀调速回路。液压缸主要参数的计算结果见表2。 按最低公进速度验算液压缸尺寸 故能达到所需低速 2 7.163 1005.06.253 min min 2 2cm v Q cm A =?=>= 三 液压缸压力与流量的确定
因为退时的管道压力损失比快进时大,故只需对工进与快退两个阶段进行计算。计算结果见表3 四液压系统原理图的拟定 (一)选择液压回路 1.调速回路与油压源 前已确定采用回油路节流调速阀调速回路。为了减少溢流损失与简化油路,故采用限压式变量叶片泵 2.快速运动回路 采用液压缸差动联接与变量泵输出最大流量来实现 3.速度换接回路 用两个调速阀串联来联接二次工进速度,以防止工作台前冲(二)组成液压系统图(见图2)
浅谈工程机械液压系统
浅谈工程机械液压系统 发表时间:2019-09-10T09:27:07.000Z 来源:《基层建设》2019年第17期作者:储小伟 [导读] 摘要:知识经济时代背景下的工业生产,必须对其中的技术手段进行升级。 身份证号码:32062119901119XXXX 摘要:知识经济时代背景下的工业生产,必须对其中的技术手段进行升级。作为机械化生产中的重要条件,工程机械液压系统必须要保证自身应用中的稳定性与连续性。液压系统的故障源能造成多个故障,而且同样的问题由于程度不同结构不同,与之配合的机械结构也不相同,这样也会造成故障的现象多种多样。所以对液压系统故障进行分析时,最主要的就是具体问题具体分析,只有全面把握液压系统的故障才能够提高液压系统故障检测的质量与水平。 关键词:工程机械;液压系统;故障特点 1引言 工程机械液压系统的故障具有一定的隐蔽性,如果仅仅依靠密闭管道内部,并且具有一定压力的油液进行传输,那么在表面就无法对系统的元件内部结构以及工作状况进行直接观察,所以导致故障的判断受到影响。液压装置自身的损坏与失效会发生在系统的内部,不容易被拆装,如果现场缺乏有效监测手段则无法对工程机械液压系统的故障进行全面的判断造成液压系统故障,分析非常困难。再次,引起故障的原因具有多样性的特点,通常情况下由于大多数液压系统的故障与原因会存在交叠的问题,一个故障可能因为多种原因而引起,这些原因也会经常共同出现,并且互相影响。本文从工程机械液压系统故障诊断的方法入手,对设备的维护措施展开分析,通过系统设定、环境管理、材料控制、操作优化这四个方面的内容,完成使用条件的改良。 2液压系统故障诊断方案 2.1对换式诊断法 当设备维修直接在现场进行,并存在诊断设备与仪器使用不便的问题,就可尝试采用对换式诊断法进行故障分析。在该技术条件中,首先要拆除待诊断元件,然后使用型号相同的元件进行替换,如果设备恢复使用,则说明被替换的元件存在故障。应用对换法进行诊断,虽在元件的拆卸上有一定的技术难度,但是由于大多数设备元件的体积都相对较小且便于拆装。所以,换式诊断具有较为突出的现场应用价值。注意,使用对换式诊断法,需保证技术人员拥有大量经验与扎实的知识,以此防止盲目拆卸对设备元件的耗损。 2.2常规检测方法 常规诊断方法下,需按照标准技术管理的顺序完成控制内容。首先,技术人员应凭借自身的技术经验,或是在专家的技术指导下,截取与故障的相关知识内容。然后,由分类化的方法,形成系统性管理框架,通过对现场情况的分析,使用不同层次的技术内容,分析元件产生故障的程度与范围。例如,在系统语言的输入与输出中,处理系统中存在的技术问题,完成常规检测方法下的系统故障处理。 2.3智能铁谱分析 智能铁谱是针对油液完成的计算内容,通过对润滑油液内,金属磨粒中铁谱、光谱、气相色谱等技术参数的分析。由此确定机械运行中的磨损状态,并分析产生故障的位置与原因。尤其在分离机械摩擦磨粒后,可以根据其尺寸参数、形成定量等数据,完成机械磨损情况的参数统计。 2.4仪表测量诊断 仪表测量法中,对整体系统中的各个仪表设备进行检查。将诸如温度、压力、流量等多个测量点的故障检测,可以简单的分析出设备中存在的故障内容。通常情况下,如液压系统存在问题,就会直接在压力表中显现出来。但如果使用流量检测,就很难精确的定位产生故障的控制点。所以,液压检测也是仪表诊断中的常见应用措施。 2.5模糊逻辑分析 模糊逻辑分析的方法下,将小波分析作为技术核心,通过变换下的小波参数,确定检测信号中存在的奇异点,以此完成故障的诊断。此种方法,常应用在突发性事件的诊断过程中。在技术优化上,可以通过噪声与尺度的反比例关系,实现随机去噪的效果,并将ANN信息进行输入,可强化诊断效果,提高方法合理性。 3工程液压系统的维护措施 (1)定期进行保养。由于大多数的工程机械液压系统都安装有智能监控设备,可以及时对液压系统的故障进行判断,但是也只能够起到警示的作用,如果不能够定期进行保养,也很容易造成设备故障,为此最主要的就是通过定期检测与智能设备监测进行有机结合。通过定期对滤清器滤网进行判断,如果滤网中金属粉末过多,则说明油泵可能出现磨损等问题。要对工程液压系统累计运行500h之后进行滤芯替换。还要对液压油箱滤清器进行彻底的清理,并且及时更换液压油。通过安排专业的检测人员对液压系统进行检测,并且结合适当的情况进行调整与维护。 (2)避免杂质、空气和水进入到液压系统内部。由于液压油对液压系统的运行效率具有非常明显的影响,而且大多数的液压系统精密元件构成非常多,一旦有固体杂质进入到液压系统内部必然会导致精密偶件受伤,甚至会导致油道阻塞等情况造成液压系统产生故障,而且液压油中通常含有7%的气体随着压力的升高,空气会从油中分离出来。如果气泡破裂时会导致液压元件产生汽蚀的现象引发噪音。在空气进入到油液之后,会造成气蚀问题加剧,而且液压油的压缩性也会存在不稳定性,导致液压系统的运行效率受到影响。当液压油中的水含量超标时,会导致液压元件产生锈蚀问题,严重的情况下甚至会影响溶液乳化,而导致机械设备出现严重磨损,所以在工程机械液压系统运行的过程中,最主要的就是避免水分进入到油液,加强对于储油罐的油盖密闭。避免油和水分进入到液压系统内部。 (3)液压油的合理。液压油对于工程液压系统至关重要。能够影响液压系统的润滑,而且也能对液压系统的压力传递,密闭和冷却等产生影响,所以一旦液压油选择不恰当,很容易造成工程机械液压系统的耐久性下降,为此最主要的就是根据工程液压系统的实际型号进行判断,按照使用说明书选择恰当的液压油。 (4)应用技术优势,设置专家系统液压系统的维护,必须建立在良好的技术基础上。只有这样,才能准确的分析出诱发故障的异常点位,并将技术条件作为指导内容,对系统进行针对性的维护与管理。在当前的技术条件下,这种方法不仅依赖设备运维人员丰富的经验,同时,也需要专家的技术指导。所以在维护中,建立专家管理系统,就显得十分必要。信息化的技术环境下,为建立专家系统构建了基础的技术条件。通过数字系统的设立,可以准确的为机械液压系统设定专业化技术指导,并利用数字化数据库模块,形成完整的技术空间,