钼精矿氧化焙烧机理研究
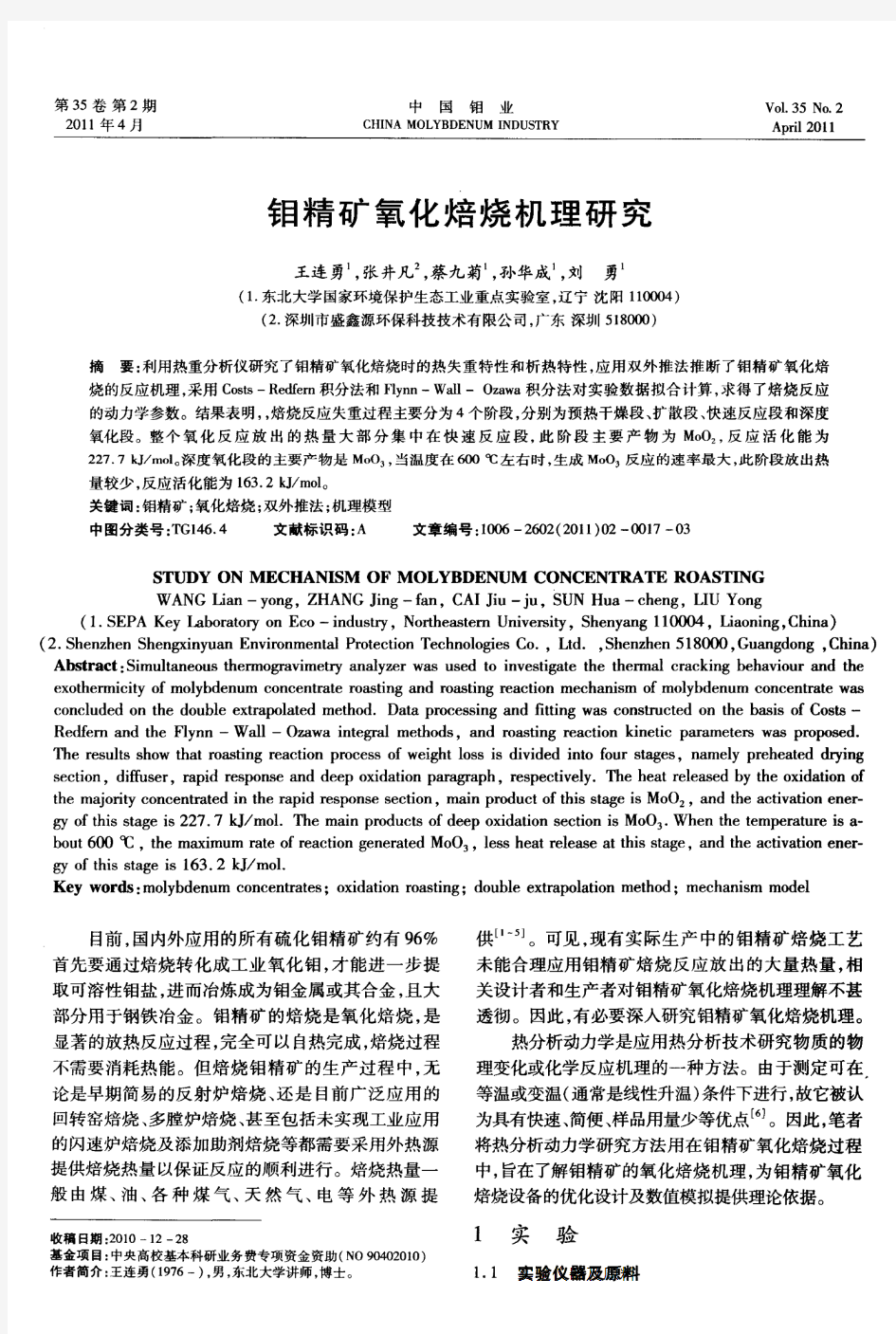

钼精矿焙烧回转窑热平衡测试与分析
钼精矿焙烧回转窑热平衡测试与分析 【摘要】本文以某公司钼精矿焙烧回转窑作为测试对象进行热工测试和热平衡计算,由此了解钼精矿焙烧回转窑的能量利用情况。通过分析结果提出了优化设计以及节能建议,以达到高产低耗的目的。 【关键词】钼精矿回转窑;热工测试;热平衡计算 0 引言 钼精矿回转窑内反应过程十分复杂,既有物料内部的物理化学反应,又有窑内气体流动、燃料燃烧和传热,且影响窑内热工过程的因素很多[1-3],若要改进回转窑设计,优化焙烧工艺操作,都必须借助回转窑的热量平衡和物料平衡来进行评估,因此需要对回转窑的热工过程进行综合测试。通过对回转窑的热工测定,我们可以了解回转窑的物料烧损和能量利用状况,编制相应的热平衡表,再对测试结果进行分析,结合回转窑的热工操作、窑体结构等具体情况,可以从中得到有价值的节能经验并提出节能措施。 1 热工测试 1.1 测定对象的确定 2 热平衡计算 本次热工测试中热平衡测定与计算方法以《中华人民共和国有色金属行业标准》YS/T124-1.1-94《回转窑热平衡测定与计算方法》为依据,并根据测试窑的特点进行了适当调整。 2.2.4 窑门溢气散热 2.2.5 其他热损失 3 热平衡测定结果分析与建议 由热平衡计算可知,此回转窑实际回收率为96%,燃料消耗量为93.75kg/h,单位产品燃料消耗耗为275kg/吨矿,绝大部分支出项热量由烟气及窑体散热带出,该回转窑在节能降耗方面上还有很大潜力可挖。 通过热平衡计算,揭示了钼精矿回转窑的热量分配情况,在热量支出项中: 3.1 出窑物料带走的热量 焙烧物料的出窑温度为776℃,这部分热量占到了总支出的3.2%,回收这部
焙烧工艺学
一、焙烧的概念和机理 1 焙烧的概念:焙烧是把压型后的生制品装在焙烧炉内、保护介质(填充料)中,在隔绝空气的条件下,按规定的升温速度进行间接加热,使生制品内的黏结剂焦化,并与骨料颗粒固结成一体的热处理过程。 2 焙烧的机理: 炭素生产用的黏结剂一般为煤沥青,是一种由多种多环和杂环芳香族化合物及少量高分子物质组成的混合物。生制品中的骨料已经过1300℃左右的高温煅烧,所以焙烧的过程主要就是黏结剂煤沥青焦化形成沥青焦的过程。 二、焙烧目的 焙烧的主要目的是使黏结剂成为沥青焦,把骨料颗粒结成一个整体,获得最大的残炭量,使制品具有良好的物理化学性能。具体物理化学性能主要有以下几个方面: 1、排除挥发分 2、降低比电阻,提高导电性能 3、固定几何形状 4、黏结剂焦化 5、提高各项物理化学性能 三、焙烧过程的四个不同阶段 1、低温预热阶段 明火温度350℃时,制品温度在200℃左右,黏结剂软化,制品成塑性状态,这段的升温速度要快一些。 2、挥发分大量排除,黏结剂焦化阶段 明火温度在350℃—800℃之间,制品本身温度在200℃—700℃之间,黏结剂开始分解,挥发分大量排除。450℃—500℃时黏结剂焦化成沥青焦。此阶段必须均匀缓慢的升温。 3、高温烧结阶段 明火温度达到800℃—1200℃,制品本身温度达到700℃以上,黏结焦化过程基本结束。此阶段升温速度可以适当加快一些,当达到最高温度后保温15—20小时,这是为了缩小焙烧炉内水平和垂直方向的温差。 4、冷却阶段 冷却过程温度下降太快,会引起产品内外收缩不均产生裂纹废品,也会对焙烧炉炉体带来不利影响,因此,冷却降温速度控制在50℃/h为宜,到800℃以下可使其自然冷却,一般到400℃以下方可出炉。 四、对焙烧过程产生影响主要有以下因素 (一)、升温速度的影响 (二)、压力的影响 (三)、制品收缩的影响 (四)、焙烧炉室温度场分布的影响 (五)、黏结剂迁移的影响 (详细论述省略) 一、填充料的主要作用 1、防止制品氧化 2、固定制品几何形状 3、传导热量 4、阻碍挥发分的顺利排除,同时导出挥发分
重金属冶金学第二套试卷及答案
重金属冶金学试卷 一、单项选择题(本大题共5小题,每小题2分,共10 分。在每小题给出的四个选项中,只有一项是符合题目要求的,把你所选的选项前的字母填在题后的括号内。) 1.在统计有色金属产量的10种主要有色金属中,重金属有几种?()A.6 B.7 C.8 D.9 2. 下列金属中不属于有色金属的是() A.铜 B.铅 C.锰 D.锌 3.下列不属于氧化镍矿湿法冶金的方法是() A.低压酸浸法 B.高压酸浸法 C.常压酸浸法 D.Caron法 4.下列哪种方法不属于锡精矿焙烧() A.氧化焙烧法 B.氯化焙烧法 C.氧化还原焙烧法 D.还原焙烧法 5.不属于造锍熔炼的主要化学反应的是:() A.硫化物氧化反应 B.氯化反应 C.造渣反应 D.高价硫化物分解反应 二、名词解释(本大题共5 小题,每小题3 分,共15 分。) 1.重金属2.火法冶金 3. 氯化焙烧4中性浸出 5 电冶金 三、填空题(本大题共4个小题,共14个空,每空1分,共14分。把答案填在题中横线上。) 1.火法炼铅方法可分为、和三类。 2. 湿法炼锌包括、、和四个主要过程 3. 硫化镍矿的提取方法有、和三种。 4. 现代炼锡法采用的火法流程包括、、和四个过程。
四、简答题(本大题共7个小题,每小题6分,共42分。) 1. 为何铜锍品味越高,渣中铜含量越高? 2. 为什么说硫化锌是较难焙烧的硫化物? 3. 沸腾焙烧的强化措施有哪些? 4. 在湿法炼锌过程中,锌焙砂中性浸出的pH值为什么要控制在 5.2左右?工业上常加入氧化剂(MnO2)的作用是什么? 5. 湿法炼锌浸出搅拌为什么采用空气搅拌,而静液过程为什么采用机械搅拌? 6. 锌焙砂中性浸出净化时,锌粉置换铜镉的原理是什么?影响锌粉置换反应的因素有哪些? 7. 锡精矿的焙烧方法有那几种?分析各自的优缺点。 五、论述题(本大题共1 个小题,每小题9分,共9分。) 1.说明硫化锌溶液精矿氧压浸出的原理及其特点。 六、计算题(本大题共1个小题,每小题10分,共10 分) 1.在锌电积过程中,槽电压和电流效率均随电流密度变化,根据下表 D/A.m-2E/V ηi/% 100 2.5 80 200 2.7 90 500 3.0 94 1000 3.5 96 (1)根据表中的电流密度,分别计算锌电积德电能消耗。(锌的电电化学当量值q为1.2195g/(A.h)) (2)为了使锌电积的成本最低,应如何选择电积过程的电流密度? B卷 一.选择题 BCADB 二、名词解释 1.重金属 重金属是指铜、铅、锌、镍、钴、锡、锑、汞、镉和铋等金属,他们的共同点是密度均在6g/cm3左
湿法炼锌中沸腾焙烧过程的研究现状与进展
湿法炼锌中沸腾焙烧过程的研究现状与进展 现代炼锌方法分为火法和湿法两大类,世界上大部分的锌都是从硫化锌精矿 中提取出来的。无论火法还是湿法,一般都需预先焙烧或烧结,脱除大部分硫和其他杂质,以满足下道工序的要求。目前,在国内应用较成熟的焙烧技术是硫化锌精矿的粉状沸腾焙烧技术。 沸腾焙烧又称流态化焙烧,是众多焙烧方法中的一种。所谓的沸腾焙烧是指将所要处理的固体破碎,研磨成细粉,增加固体与气体的接触面积,缩短颗粒内部的传递和反应距离。自下而上流经这些粉料的气体,在达到一定速度时,会将固体颗粒悬浮起来,使之不断运动,犹如沸腾的水,故称沸腾焙烧。沸腾焙烧的基础是固体流态化,用沸腾焙烧炉焙烧锌精矿,炉内热容量大且均匀,温差小,料粒与空气接触表面积大,反应速度快,强度高,传热传质效率高,使焙烧过程大大强化,产品质量稳定生产率高。下面主要叙述在湿法炼锌中沸腾焙烧过程的发展和应用现状。 1 湿法炼锌中沸腾焙烧过程的发展和应用现状 1.1 在制粒焙烧方面的研究情况 李芳、张建彬,张起梅等[1]在锌精矿制粒沸腾焙烧中指出随着原料供应日趋紧张、精矿质量下降,发展沸腾焙烧技术,对提高锌冶炼金属回收率具有重要的意义。他们进行了锌精矿制粒焙烧的试验研究,重点分析了制粒粘合剂的选择和制粒焙砂质量控制。在沸腾焙烧试验中,针对焙砂质量及其影响因素诸如焙烧温度、原料粒度、过剩空气系数和物料在炉内的停留时间等进行了研究;另外通过适当减少加料量,使相应提高过剩空气系数,延长停留时间,Pb的脱除有所降低,同时s脱除效果亦有明显提高。最后他们得出结论:制粒沸腾焙烧提高了炉子的处理能力,床处理能力达到30.4 t/m2·d,炉温控制得当,风量均匀,焙砂质量可以达到Pb<1.0%,Cd<0.05%,S<1%的控制要求。沸腾炉操作温度可控制在1140~1180℃,比现有粉状物料焙烧操作温度提高60~80℃。 靳澍清、刘丽珍、吉正元等[2]在锌精矿造粒、焙烧试验研究中采用几种粘结剂进行造粒试验,对成粒矿进行静态焙烧试验,提出造粒和焙烧试验工艺条件及参数,粒矿进行静态焙烧试验,为大规模的生产奠定了一定的基础。 张瑜、李志勇、吴志平等[3]在锌精矿制粒沸腾焙烧新工艺的应用与改进中介绍了锌精矿制粒沸腾焙烧新工艺的工业化生产应用与技术改进情况,同时阐述了所取得的成果及存
冶金原理实验报告硫化锌精矿氧化过程动力学
冶 金 原 理 实 验 报 告 专业班级: 冶金0905 学号: 0503090629 姓名:吴海艳 实验日期: 2011 年 11 月 日 室温: 20C ? 大气压:Pa 1001.15? 实验名称:硫化锌精矿氧化过程动力学 一.实验目的 (1) 采用固定床进行硫化锌精矿氧化焙烧,分析各段时间硫的产出率,来测定氧 化速度与时间曲线。 (2) 学会氧化动力学的研究方法。 (3) 了解硫化锌精矿氧化过程机理。 (4) 学会硫的分析方法。 二.实验原理 在冶炼过程中,为了得到所要求的化学组分,硫化锌精矿必须进行焙烧,硫化锌的氧化是焙烧过程最主要的反应:ZnS+3/2O 2=ZnO+SO 2 反应过程的机理: ZnS+1/2O 2(气)——ZnS …[O]吸附——ZnO+[S]吸附 ZnO+[S]吸附+O 2——ZnO+SO 2解吸 这个反应是有气相与固相反应物和生成的多相反应,包括向反应界面和从反应界面的传热与传质过程。可以认为反应按如下步骤进行 (1) 氧通过颗粒周围的气体膜向其表面扩散; (2) 氧通过颗粒表面氧化生成物向反应界面扩散; (3) 在反应界面上进行化学反应; (4) 反应生成的气体SO 2向着氧相反的方向扩散,即反应从颗粒表面向其中心部 位逐层进行,硫化物颗粒及其附近气体成分的浓度可用未反应核模型表示。 提高硫化物氧化速度,可以通过以下方式: 提高氧分压,加速SO 2吸收,减小矿石粒度,降低氧化层厚度,提高温度 本实验采用固定床焙烧,来测定硫化锌氧化速度。分析氧化过程某一时刻产生的SO 2 的量,来计算硫化锌硫的脱出率;即单位时间硫的脱出率。为了便于比较不同硫化物和不同条件下硫化物的氧化速度,引入以下公式:总 S S S i R = 式中R S ——精矿中硫的氧化分数;S i ——硫化锌精矿氧化过程中某一时间内失去的硫量;S 总——精矿中所有的含硫量。 利用氧化分数和时间关系作出,可以得出不同温度、不同粒度、不同气相组成对硫化锌焙烧过程的影响。 实验利用卧式管状炉,通空气在温度低于硫化锌的熔点下进行。通过秒表计时,控制吸收液的吸收时间,利用滴定来分析SO 2得到S 的脱出率。
矿物原料焙烧原理及方法
https://www.360docs.net/doc/626441785.html, 矿物原料焙烧原理及方法 矿物原料焙烧是化学选矿的预处理作业或独立的化学选矿作业。即在适当的焙烧气氛和低于矿物原料熔点温度等相应条件下,通过加热升温焙烧使矿物原料中的目的矿物发生物理和化学变化的工艺过程。通过焙烧可使目的矿物转变为易于通过浸出或易于用物理选矿分选分离的矿物形态。焙烧使矿物发生化学变化的同时,也使物料(焙砂)的物理形态变得疏松、多孔,为后续作业处理创造了必要条件。焙烧还可除去(回收)易挥发的组分(杂质)。 根据矿物焙烧发生化学反应的条件和工艺参数,焙烧可以分为氧化焙烧、还原焙烧、氯化焙烧、钠化焙烧合硫化焙烧等。 在选矿中采用焙烧法处理的物料常为难选原矿以及物理选矿所得粗精矿和难选的中矿等。焙烧产品有焙砂、干烟尘剂湿法收尘集气产品等。并可相应使用适宜的方法分别处理,回收其中的有用组分。影响焙烧的主要因素有焙烧温度、反应氛围和时间、反应气氛的浓度、气流运动的絮流度以及物料的物理、化学性质,如物料粒度、孔隙率、化学组成及矿物组成等。焙烧法的不利因素是能耗较高,操作控制条件严格,环境污染与治理务必采取相应措施。 矿物热分解是将矿石或人造化合物加热到一定物度,使之分解为组成较为简单的化合物(含气体),或者是使原矿物晶型发生转变的工艺过程。矿物热分解液称款物的煅烧。碳酸盐的热分解有称为焙解,名称不同,实质一样。不论是金属矿还是非金属矿采用煅烧分解矿物都非常普遍。像碳酸盐、磷酸盐、硫酸盐、氢氧化物、硅铝酸盐等矿物往往都少不了通过煅烧分解矿物、改变晶型、构造与形态。高岭土等黏土矿物的煅烧生加工,在近20年来发展迅速。 化合物热分解的平衡常数等于该化合物的热分解压,此分解压可作为该化合物热稳定性的度量。化合物热分解压愈大,热稳定性愈小;反之,热分解压愈小,热稳定性愈大,愈难发生热分解。有些化合物加热至一定温度时,虽其组成未发生变化,但其晶型已产生了变化,物理化学性质液产生了相应的变化,氧化矿物、硫化矿物、硫酸盐、氢氧化物和各种含氧酸盐等各种不同化合物(矿物)的分解压不同,通过控制煅烧温度、气相组成,可选择性地使某些化合物产生热分解,或发生晶型转变,继而采用不同方法进行分选。 通过控制焙解温度和气相组成,即可选择性地分解、改变碳酸盐组成,然后用化学或物理方法选别,达到富集有价组分和去除杂质的目的。
硫化锌精矿的加压酸浸(一)
书山有路勤为径,学海无涯苦作舟 硫化锌精矿的加压酸浸(一) A 加压酸浸的机理加压氧化酸浸是液、固、气多相反应,浸出中氧对硫 化锌精矿有氧化作用和金属氧化物的酸溶作用,实质上是将传统湿法炼锌的焙 烧、浸出两个过程合为一个过程进行。硫化锌精矿加压氧化酸浸的机理基本上 可分为两种类型,即电化腐蚀机理和吸附配合物机理。 a 电化腐蚀机理硫化 物的溶解类似于金属腐蚀的电化反应。阴极反应:O2+2H++2e ==== H2O2 H2O2+2H++2e ==== 2H2O 阳极反应:MeS ==== Me2++S+2e MeS+4H2O ==== Me2++SO42-+8H++8e 总反应:1MeS+ ——O2+2H+ ==== Me2++H2O+S 2 MeS+2O2 ==== MeSO4 硫化物中的S2-在矿粒阳极部位氧化放出电子,通过矿粒本身转送到阴极部位,使氧还原,完成一个闭路微电池。 氧的还原通过一个H2O2 中间物进行转移。硫化锌在100℃下进行氧化酸溶试验,其动力学曲线如下图所示。溶液中的氧压与所需酸量的关系是:氧压愈 高,要求的酸浓度愈高;氧压一定时,酸超过极限含量,反应速率则不再增 大,保持一个恒定值。在130℃时硫化锌进行氧化酸溶也可得到类似的曲线, 证实属于电化学腐蚀机理。 [next] b 吸附配合物机理假设在固相S 与液相B 之间的反应中途形成吸附配合物S·B,其反应机理可用下式表示。S 固+B 液==== S·B—→产物 吸附配合物的形成是过程的最缓慢阶段,为过程速率的控制步骤。过程的 反应动力学可以推导如下:设Q 为形成吸附配合物过程中参与反应的部分, 1 - Q = 没有参与反应的游离部分设形成配合物的速率ξ1为ξ1= K1(1-Q) [B]n 设配合物分解(成组分)的速率ξ2为ξ2= K2Q 设配合物分解(成产物)的速率ξ3为ξ3= K3Q 式中,K1,K2,K3 均为速率常数。当n=1 反应
硫化锌精矿氧化焙烧
实验二硫化锌精矿氧化焙烧 一、目的 (1)用固定床进行硫化锌精矿氧化焙烧,分析各段时间硫的产出率,来测定氧化速度与反应时间的关系曲线。 (2)学会氧化动力学的研究方法。 (3)了解硫化锌精矿氧化过程机理。 (4)学会硫的分析方法。 二、原理 在冶炼过程中,为了得到所要求的化学组分,硫化锌精矿必须进行焙烧,硫化锌的氧化是焙烧过程最主要的反应: ZnS+3/2O2=ZnO+SO2 反应过程的机理: ZnS+1/2O2(气)——ZnS+[O]吸附——ZnO+[S]吸附 ZnO+[S]吸附+O2——ZnO+SO2解吸 这个反应是气相与固相的化学反应,包括反应界面的传热与传质过程。 硫化锌颗粒开始氧化的初期。化学反应速度本身控制着焙烧反应速度。但当反应进行到某种程度时,颗粒表面便为氧化生成物所覆盖,参与反应的氧通过这一氧化物层向反应界面的扩散速度,或反应生成物SO2通过扩散从反应界面离去的速度等,便成为总氧化速度的控制步骤。 因此,可以认为反应按如下步骤进行: (1)通过颗粒周围的气体膜向其表面扩散; (2)氧通过颗粒表面氧化生成物向反应界面扩散; (3)在反应界面上进行化学反应; (4)反应生成的气体SO2向着氧相反的方向扩散,即反应从颗粒表面向其 中心部位逐层进行,硫化物颗粒及其附近气体成分的浓度可用未反应核模型表示。 提高硫化物氧化速度,可以通过以下方式:提高氧分压,加速SO2吸收,减小矿石粒度,降低氧化层厚度,提高温度等措施。 本实验采用固定床焙烧,来测定硫化锌氧化速度。分析氧化过程某一时刻产生的SO2的量,来计算硫化锌硫的脱出率;即单位时间硫的脱出率。为了便于比较不同硫化物和不同条件下硫化物的氧化速度,引入以下公式:
高铁硫化锌精矿加压浸出工艺
高铁硫化锌精矿加压浸出新工艺 瞿仁静王晓曼鲁艳梅 (云南省冶金研究设计院,云南昆明650031) 摘要:高铁硫化锌精矿加压浸出冶炼工艺与传统工艺不同,锌精矿焙烧过程发生的氧化反应和锌焙砂浸出过程发生的酸溶反应合并在一起进行,主体设备为高压釜。该技术较传统工艺节能30%,锌浸出率≥95%,铁浸出率≤30%,浸出指标好,有广阔的发展前景。本文介绍了这种工艺的原理、流程、特点以及该新兴工艺在工业上的具体应用。 关键词:高铁硫化锌精矿;加压浸出;节能;环保;锌浸出率;铁浸出率。 New Process of Pressure Leaching on High-iron Zinc-sulphide Concentrate Qu Renjing Wang Xiaoman Lu Yanmei (Yunnan Metallurgical Research and Design Institute, Kunming, Yunnan 650031, China) ABSTRACT:Different with the traditional process, pressure leaching on high-iron zinc-sulphide concentrate combines the oxidation reaction occurs zinc concentrate roasting process and the acid-soluble reaction occurs zinc calcine leaching process together, and the main equipment is autoclave. The process saves 30% energy compared with traditional technology, and with the high rate of zinc leaching processes. Zinc leaching rate is greater than or equal to 95%, iron leaching rate is less than or equal to 30%, leaching index was better, and has broad prospects for development. The principles, processes, characteristics and the industrial applications of this new technology were described. KEYWORDS:high-iron zinc sulphide concentrate;pressure leaching;energy saving;environmental protection;zinc leaching rate;iron leaching rate 1 前言 在现代经济建设中,锌已成为不可缺少且用量大的基础有色金属。我国锌储量居世界第一位,云南锌资源十分丰富,锌探明储量超过2000万t,其中高铁锌资源储量700万t,占云南锌资源储量的三分之一。 高铁硫化锌精矿中,铁以类质同相替代矿物晶格中的锌,通过机械磨矿和选矿的物理方法难以使铁分离,产出的锌精矿含锌低(40~45%),含铁高(14~20%),其化学成分低于铁精矿质量四级品标准要求。采用传统湿法炼锌工艺,焙烧时铁大量生成铁酸锌,锌浸出率低,浸出渣含锌高。采用高温高酸浸
锌精矿焙烧
设计任务书 电锌厂焙烧车间工艺设计及计算一.原始数据 二.技术条件选择 1.沸腾层高度 2.空气过剩系数 3.沸腾层温度 4.炉顶温度 5.炉顶负压 6.直线速度 7.出炉烟气量 三.技术经济指标 1.焙烧矿产出率(包括烟尘和焙砂) 2.烟尘含锌量 3.焙砂含锌量 4.焙烧料含锌量 5.脱硫率 6.焙烧锌直收率 7.出炉烟气含尘量 8.出炉烟气SO2量 9.烟尘含S S量 10.焙砂含S S量 11.烟尘含S so42-量 12.焙砂含S so42-量 四.冶金计算 (1)选取计算的有关主要指标(各种成分进入烟气的比例)(2)锌精矿的物相组成计算 (3)烟气产出率及其化学成分和五项组成计算
(4)焙砂产出率及其化学成分和五项组成计算 (5)焙烧需要的空气量及产出烟尘量与组成计算 (6)沸腾炉焙烧物料平衡计算 (7)热平衡计算 五.参考书目 1.铜铅锌设计参考资料铜铅锌冶炼设计参考资料编写组1978 2.有色冶金工厂设计基础陈枫1989 3.重金属冶金学赵天从编1987 第二版 4.锌冶金学冶金工业出版社 5.冶金原理冶金工业出版社 6.锌冶金彭荣秋中南大学出版社 7.湿法炼锌学梅光贵等中南大学出版社
绪论 锌精矿来源较广,成分复杂,为了使焙烧有一个相对稳定的工艺条件,必须对锌精矿进行配料以使精矿成分控制在焙烧操作允许的范围内,这关系到整个锌冶金过程中的稳定性。 本次设计的主要内容是锌精矿的沸腾焙烧,沸腾焙烧是现代焙烧昨业的新技术,也是强化焙烧的一种新方法。其实质是:使空气自下而上地吹过固体料层,吹风速度达到使固体粒子相互分离,并做不停地复杂运动,运动的粒子处于悬浮状态,其外状如同水的沸腾翻动不已。由于粒子可以较长时间处于悬浮状态,就构成了氧化各个矿粒最有利的条件,故使焙烧大大强化。 沸腾焙烧的基本原理是利用流态化技术,使参与反应或热、质传递的气体和固体充分接触,实现它们之间最快的传质,传热和动量传递速度,获得最大设备的生产能力。 在此次设计中,我们充分运用了现有的专业知识,加上自己大量查阅资料。让我们更深入的熟悉和了解锌沸腾焙烧的工艺流程,设备的计算方法,学会分析各类经济指标及各种技术参数,使我们在各方面的能力都有了提高。 此次设计包括锌沸腾焙烧工艺过程的论述,焙砂、烟尘、烟气成分,物料平衡与热平衡计算。在设计过程中我们在查阅大量资料的前提下,经过专业课老师的细心指导,对工艺过程进行了详细、科学、有针对性的计算,这在我们完成了学习任务的同时也对相关方面的知识有了更深入的认知。 2011年5月30日
铅锌硫化精矿的焙烧与烧结
3铅锌硫化精矿的焙烧与烧结 现在世界上的铅锌冶炼厂所处理的矿物原料,90%以上是铅锌硫化精矿,其化学成分参见表1.23与1.24,处理这些精矿的目的是提取铅、锌、硫与其它有价元素。由于这种硫化精矿中的铅与锌主要是以硫化物的形态存在,即为方铅矿(PbS)与闪锌矿(ZnS),因此要把PbS与ZnS还原得到金属,在目前的生产技术条件下很难找到一种能满足技术与经济要求的还原剂;当采用湿法炼锌时,也很难找到一种在常规浸出条件下能很好溶解ZnS并进一步顺利地从溶液中提取金属锌的溶剂。因此,世界上大多数铅锌冶炼厂所采用的冶炼方法,是将这种硫化精矿首先进行焙烧或烧结焙烧,以转变精矿中PbS与ZnS以便下一步处理,这就是焙烧或烧结焙烧的主要目的。在金属硫化物的氧化过程中,精矿中的硫会氧化为SO2,随烟气带走并与氧化后的金属氧化物分离。这种含SO2的烟气可以送去生产硫酸,所以铅锌冶炼厂也是生产硫酸的化工厂。 铅锌硫化精矿在氧化焙烧过程中得到的铅锌氧化物,目前在火法冶金中都是选用炭质还原剂在高温下使PbS与ZnS还原为金属。实现这一过程可以在各种冶金炉中进行,并且大多数铅锌冶炼厂都是采用鼓风炉进行还原熔炼。而鼓风炉还原熔炼过程中只能处理块状物料,因此细小的硫化精矿在焙烧时应利用硫化物氧化放出的热量来升高温度,使粉状的氧化物料在高温下熔结成块;这就是在硫化物氧化过程中同时进行的烧结过程,即所谓的烧结焙烧。因此,烧结是一个冶金过程,达到了硫化物氧化与粉状物料熔结成块两个目的。 铅锌冶炼厂为了实现硫化精矿的焙烧或烧结焙烧的目的,可以在不同的技术条件(如温度、气氛等)下与各种冶金设备(如流态化焙烧炉、烧结机等)中进行;在同等条件下及同样的设备中进行时,还可以采取不同的技术措施(如富氧鼓风、吸风与鼓风烧结等)来强化生产过程,提高产品质量,改善劳动条件与环境保护,从而获得更好的经济效益与社会效益。 3.1铅锌硫化精矿焙烧与烧结理论基础 硫化铅精矿中的主要金属硫化物是方铅矿PbS,另外ZnS、FeS2、FeAsS、Sb2S3、CdS、CuFeS2、Bi2S3等。硫化锌精矿中主要金属硫化物是闪锌矿ZnS,
硫化锌焙烧
1焙烧方法分类 从硫化锌精矿中提炼锌,无论采用火法或湿法,都必须先将硫化锌精矿进行焙烧。焙烧的实质就是在一定的气氛中加热锌精矿,使其发生物理化学变化,改变其成分以适应下一步冶金过程的要求,但精矿一般不熔化,或者说焙烧一般是固相与气相之间进行的化学过程而不出现液相。 依据焙烧过程的本质不同,一般把焙烧分为:煅烧、还原焙烧、氧化焙烧、硫酸化焙烧、氯化焙烧和烧结焙烧等几类。视矿石或精矿的成分和下一步冶金处理方法的不同,选用其中适当的焙烧方法。 1.1 煅烧 煅烧主要是处理碳酸盐、硫酸盐等氧化矿的一种预备过程,其目的是在高温条件下使碳酸盐或硫酸盐分解为氧化物以及除去其中的水分。 1.2 还原焙烧 还原焙烧应用于处理氧化矿石,在还原气氛中使矿石中自山状态的或结合状态的氧化物还原成低价氧化物或金属。在锌冶金中还原焙烧应用于处理锌的氧化矿或含锌废料(如浸出渣、蒸馏渣等)。当含锌物料与碳混合,在还原气氛下加热(800-1200℃)焙烧时,ZnO被还原为锌蒸气,然后又被炉气中O?、CO?等氧化成ZnO收集于布袋中。 1.3 氧化焙烧 氧化焙烧在氧化气氛中使硫化矿中的硫全部或大部除去,使硫化物全部或大部变成氧化物。 氧化焙烧分为两种,一种是把硫化矿石中的硫全部烧去,所得焙烧矿仅由氧化物组成,称作“死烧”,火法蒸馏炼锌所采用的焙烧就是“死烧”;另一种焙烧只是部分地烧去硫,如铜、镍硫化矿的焙烧,称作部分氧化焙烧。 1.4 硫酸化焙烧 硫酸化焙烧应用于有色金属湿法冶金。目的是在氧化气氛中把待提取的金属变成水溶性的硫酸盐。 硫酸化焙烧也可分为两种:一种是把矿石中的硫化物全部变成为水溶性的硫酸盐,称全硫酸化焙烧,简称酸化焙烧,另一种则是部分地将矿石中的硫化物转变为水溶性的硫酸盐,其余则氧化成氧化物,叫做部分硫酸化焙烧,有时也称酸化焙烧。湿法炼锌的焙烧就是部分硫酸化焙烧。 1.5 氯化焙烧 氯化焙烧应用于使不溶于水的金属化合物变成可溶于水氯化物。若将某些金属化合物变为易挥发的氯化物而与其他成分分离,这种氯化焙烧又称氯化挥发焙烧。因此氯化焙烧可以处理硫化物与氧化物两种物料。 氯化作用是依靠向焙烧物料中加食盐或氯化钙与氯化钾的混合物等完成的,有时也用氯气氯化。 1.6 烧结焙烧
磁化焙烧原理
C ihUQ beishQO一CIXU0n 磁化焙烧一磁选(magnetizing roasting- 磁化焙烧 megnetic separation)磁化焙烧与磁选的联合处理法。磁化焙烧是在一定温度和气氛下把弱磁性铁矿物(赤铁矿、褐铁矿、菱铁矿和黄铁矿等)变成 强磁性的磁铁矿或磁性赤铁矿(不Fe203)的过程。是弱磁性矿石在磁选前的准备作业,以便用弱磁场磁选机进行分选。磁化焙烧一磁选技术的分选指标优良,但成本较高。磁化焙烧按原理分为还原焙烧、中性焙烧和氧化焙烧。还原焙烧应用最广。它在500~800℃的还原气氛下进行,焙烧产物是强磁性的Fe30、;若产物在还原气氛下冷却到400℃,再在空气中冷却,则产物是井 Fe203。前者为还原焙烧,后者为还原一氧化焙烧。还原焙烧用的还原剂为固体或气体。固体还原剂如煤粉和焦炭粉;气体还原剂是各种煤气,如高炉煤气、焦炉煤气、发生炉煤气和天然气等。中性焙烧是在不加或少加空气的条件下,把菱铁矿加热到300~400℃,使其分解为磁铁矿。氧化焙烧是在氧化气氛下,将黄铁矿氧化为磁黄铁矿或磁铁矿。为判断磁化焙烧后弱磁性矿物转化为强磁性矿物的程度,采用还原度来度量。还原度是焙烧矿石中的氧化亚铁和全铁含量的百分数 (架只1。。写)。还原完全时还原度为42.8%,小于、TFe/、‘“”厂”沪。一,/J、/。一”“~j/J、浅/J了曰.LJ/。”J’“ 28%时,则表示还原程度不够。磁化焙烧炉有竖炉、回转窑和沸腾炉。中国多采用竖炉,炉子容积一般为50m“,处理能力 15t/h;容积较大的为70m3,处理能力为23t/h。竖炉给矿粒度为75~Zomm,小于Zomm的粉矿不能用竖炉焙烧。回转窑能处理粉矿,但有时容易结瘤。沸腾炉热效率高,还原性能好,能处理3一。mm 粉矿。但粉尘量大,对环境污染较严重。 磁化焙烧是矿石加热到一定温度后在相应的气氛中进行物理化学反应的过程。根据矿石不同,化学反应不同。磁化焙烧按其原理可分为还原焙烧、中性部烧和氧化焙烧等。 1、还原焙烧适用于赤铁矿和褐铁矿。常用的还原剂有C,CO和H2比等。
锌精矿焙烧课计
1、设计任务 设计一个年产10000吨电锌厂焙烧车间(初步设计)1.1、原始数据 电锌年产量:10000吨 锌精矿的化学成分(%) 1.2、技术条件选择 沸腾层高度:1.5m左右 空气过剩系数:1.25 沸腾层温度:850~900C 炉顶温度:820~870 炉顶负压:-10~30Pa 直线速度:0.5~0.6m/s 出炉烟气量、温度:900 1.3、技术经济指标 年处理锌精矿:1.3万吨/年 年工作日:300天 沸腾炉炉床面积:28m2 沸腾炉炉床能力:5.2t/(m2d)
焙烧矿产出率(包括烟尘和焙砂):88%(占锌精矿的)烟尘含锌量:54.89% 焙砂含锌量:56.91% 焙烧料含锌量:48% 脱硫率:93.6% 焙烧锌直收率:52% 冶炼总回收率:95% 出炉烟尘含量:35%(占焙烧矿的) 量:9365%(体积百分数) 出炉烟气SO 2 烟尘含Ss量:1.73% 焙砂含Ss量:0.4% 2-量:2.14% 烟尘含Sso 4 2-量:1.10% 焙砂含Sso 4
2、原始资料 2.1、锌矿的分布及品位 截至2002年,全世界查明锌储量为20000万吨,储量基础为45000万吨,现有储量和储量基础的静态保证年限为23年和51年。锌储量和储量基础占锌资源量的10.52%和3.68%。中国锌的储量和储量基础均居世界首位,已成为世界最大的铅锌资源国家。 根据统计资料,在我国铅锌储量中铅锌平均品位只有 4.66%,而根据目前铅锌价格水平和成本水平,只有铅锌(1:2.5)合计地质品位在7%~8%以上的地质储量才是能经济利用的储量,目前我国能经济利用的铅锌合计储量只有4513.86万吨,仅占总储量的 42.6%。 锌在自然界多以硫化物的状态存在,主要矿物是闪锌矿(ZnS),但这种硫化矿的形成过程中有FeS固溶体,成为铁闪锌矿(nZnSmFeS).含铁高的闪锌矿会使提取冶炼过程复杂化。流化床的地表部位还常有一部打分被氧化的 氧化矿,如菱锌矿(ZnCO 3)、硅锌矿(Zn 2 SiO 4 )、导极矿(H 2 Zn 2 SiO 5 )等。 我国铅锌储量较多的省(区)主要是云南、广东、甘肃、四川、广西、内蒙古、湖南和青海等八省(区),其铅锌储量占全国总储量的80.7%。大中型锌矿187处,探明资源总量7961万吨,储量1950万吨,其中大型锌矿区44处,探明资源总量5352万吨,储量 1553万吨,分别占全国的 58.1%和76.6%。 目前已探明的储量主要集中在云南、广东、内蒙古、江西、湖南和甘肃等六省。各大区储量见下表: 中国铅锌资源各大区分布比例(%)表 2.2、精矿的组成成分 铅锌矿的开采分露天开采和地下开采两种。由于金属品位不高,铅锌共生,并含有大量的脉石和其他杂质金属,矿石需先经过选矿。通过采用浮选法优先选出锌精矿,副产铅精矿和硫精矿。我国某些大型企业铅锌矿产出的锌精矿成分实例如下表。 硫化锌精矿是生产锌的主要原料,成分一般为:锌45%~46%,铁5%~15%,硫的含量变化不大,为30%~33%。可见,锌精矿的主要组分为Zn,Fe和S,三者占总重的90%左右。硫化锌精矿是生产锌的主要原料,成分一般为:
焙烧
焙烧 焙烧是指成型后的碳素生坯制品在焙烧炉内,通过一定的介质保护,在隔绝空气的条件下,按一定的温度制度进行高温热处理,使生坯制品内的粘结剂结焦炭化,并将骨料颗粒固结成一体的工艺过程。 焙烧机理:碳素生产用粘结剂一般为煤沥青,是一种由多种多环和杂环芳香族化合物及少量高分子似碳黑的物质组成的混合物。在焙烧加热过程中,这些物质发生多种反应,主要包括:加热反应、分解反应、聚合反应等。由于这种连续的分解和聚合,连接牢固的分子在未挥发的残油中集积起来,连接不牢固的逐渐断掉而减少。这样就按化学键的强度进行淘汰,使分子更加紧密,稳定性更大,并产生由排成正六角碳原子网络组成的巨大平面分子,成为碳青质。碳青质形成时,在平面分子层面之间就产生所谓金属键,表现在分解物质经700℃以上温度处理后,其导电性逐渐增大。但碳青质只是二维的排列,与石墨晶体的三维排列有着本质的区别。当焙烧温度达到900℃以上时,碳青质进一步脱氧和收缩后变成了沥青焦。 焙烧的目的是将生坯制品中粘结剂通过高温热处理转变为焦炭,获得最大残炭量,使制品具有良好的物理化学性能。具体主要有以下几个方面。 1.排除挥发分 炭和石墨制品生产主要使用煤沥青作为粘结剂。煤沥青是炼焦工业副产品煤焦油蒸馏加工后的残留物,组分主要是甲苯不溶物、喹啉不溶物、α树脂、β树脂,这些物质在焙烧过程中发生蒸馏、分解、缩聚等物理化学反应,将生成的轻质碳氢化合物以挥发分的形式排除,从而使焙烧后的制品物理化学性能得到极大改善。 2.使制品中的粘结剂焦化 焙烧过程中粘结剂经过各种反应最后形成结构致密的焦炭,一方面将各种骨料颗粒牢固地连接未一体,同时制品内的空隙得到填充。 3.提高制品的导电性能 炭和石墨制品的导电性能与原料煅烧程度、制品的焙烧和石墨化热处理程度有直接的联系。由于焙烧过程中煤沥青焦化将骨料颗粒粘结为一体,挥发分大量排出,使制品电阻率大幅度降低,提高了制品导电性能。 4.固定制品形状 成型后的生坯制品虽然具有一定的形状,但由于粘结剂没有焦化,受热后生坯制品容易软化变形,对制品的加工和产品质量造成影响。通过焙烧过程中粘结剂的焦化,使骨料颗粒固结为一体,具有一定的机械强度,制品形状得到固定,同时制品的体积也得到一定的稳定性。 5.提高制品的各项物理化学性能 焙烧过程中,粘结剂焦化,制品体积收缩,真密度增加,机械强度、抗氧化性、导热性、耐腐蚀性能等都得到较大提高,使制品获得良好的物理化学性能。
铬铁矿无钙焙烧的反应机理
铬铁矿无钙焙烧的反应机理 纪柱 (天津化工研究院,天津300131) 摘要 研究了铬铁矿无钙焙烧反应机理,得出配碱量高低及有无填料对氧化速度、硅铝的副反应均有显著影响;少碱和足碱焙烧的活化能分别为50.3及73.2kJ/K.mo l。 关键词 铬铁矿 铬酸钠 固相反应 反应动力学 活化能 铬矿无钙(不用白云石、石灰石等钙质填料)焙 烧制取铬酸钠及其物相变化已有报导〔1、2〕,现将过程 的反应机理作如下探讨。 实验用含Cr2O349.31%的铬铁矿(M g,FeⅡ) (Cr、Al、FeⅢ)2O4(可简写成M g Cr2O4及FeCr2O4), 主要杂质为Mg、Fe、Si、Al。使用含Na2CO399.88% 的试剂纯碱。所用填料为M gO及Fe2O31200℃合成 的镁铁矿。 1 配碱率的影响 1.1 主要反应 铬铁矿无钙焙烧的主要反应有: M gCr2O4+2Na2CO3+3 2O22Na2C rO4+M gO+2C O2(1) … 2FeCr2O4+4Na2CO3+7 2 O24Na2C rO4+Fe2O3+4CO2…… (2) …………………………………………………………………SiO2+Na2CO3Na2S iO3+CO2(3) ……………………………… Al2O3+Na2C O32NaAlO2+C O2(4) …………………………… 生成的Na2SiO3、NaAlO2作为Na原料还将进一步反应(式11~16),M gO及Fe2O3则生成镁铁矿M gFe2O4。 式(1,2)表明,每kg铬(以Cr2O3计)所需纯碱理论量为1.395kg。实际配碱量与理论量之比称为配碱率,配碱率≤50%称少碱焙烧,>80%称足碱焙烧。生成铬酸钠的碱与实际配碱量之比称为碱利用率。 1.2 无填料焙烧 不用任何填料,铬矿仅与纯碱混合焙烧,其氧化率及碱利用率同配碱率的关系见图1。熟料水溶Al2O3及可熔盐(焙烧温度下的熔液)同配碱率关系见图2。氧化率曲线在配碱<50%时斜率大,>50%后斜率变小;碱利用率曲线在配碱(40~50)%处呈现极大值。以水溶Al2 O3表示的NaAlO2几乎随配碱量线性增大;以水溶SiO2表示的Na2SiO3亦同,其值比A l2O3小一个数量级。 图2 可熔盐同配碱率关系图 斜率变化及极大值出现的原因是炉料中可熔盐已达到铬矿正常焙烧的阈值30%。例如配碱40%,可熔盐为28.31%,配碱50%,可熔盐为32.58%超
硫化锌精矿焙烧的主要反应
锌湿法冶金流程实训指导书 编者:胡小龙
目录 1.锌精矿的焙烧 (1) 1.1湿法炼锌对锌精矿焙烧的目的与要求 (1) 1.2硫化锌精矿焙烧的主要反应 (1) 1.3锌精矿焙烧 (8) 2 浸出 (9) 2.1浸出的目的 (9) 2.2中性浸出 (9) 2.3酸性浸出 (11) 2.4沉矾 (12) 3 净化 (14) 3.1净化目的 (14) 3.2一段净化 (14) 3.3二段净化 (15) 3.4三段净化 (15) 3.5工序产品的质量要求 (16) 4 综合回收 (17) 4.1工艺原理 (17) 4.2原料、产品要求 (17) 4.3铜镉渣浸出 (18) 4.4铜渣酸洗及上清压滤 (18) 4.5铜镉渣浆化及过滤 (18) 4.6钴渣酸洗及压滤 (19) 4.7贫镉液沉钴 (19) 4.8Β-奈酚除钴 (19)
1.锌精矿的焙烧 1.1湿法炼锌对锌精矿焙烧的目的与要求 根据湿法炼锌的工艺原理,湿法炼锌焙烧硫化锌精矿的目的主要是使锌精矿中的ZnS绝大部分转变为ZnO,少量则为ZnSO4,同时尽可能完全地除去砷、锑等杂质。具体说来其要求有五点: (1)在湿法炼锌中,出于硫化锌在一般条件下不能直接用稀硫酸进行浸出,所以焙烧时,要尽可能完全地使ZnS转型,使其绝大部分氧化成为可溶于稀硫酸的ZnO。不过为了补偿冶金过程中H2SO4的机械损失和化学损失,仍要求焙烧矿中有适量的可溶于水的ZnSO4。生产实践证明,一般浸出流程,只要使焙烧矿中含有2.5~4%的ZnSO4形态的硫就可以补偿冶金过程中H2SO4的损失,并不希望过多,否则会导致冶金过程中硫酸根的过剩,影响正常生产的进行和增加原材料的消耗。 (2)使砷,锑氧化成挥发性的氧化物除去,同时除去部分铅,以减轻浸出、净化工序工作量。 (3)使炉气中的SO2浓度尽可能地高,以利制造硫酸。 (4)焙烧得到细小粒子状的焙烧矿,以利下一步浸出,即不希望有烧结现象发生。 (5)在焙烧时应尽可能地少产生铁酸锌和硅酸锌。因为铁酸锌不溶于稀硫酸,而导致锌的浸出率降低;硅酸锌虽然能溶于稀硫酸,但溶解后会产生胶体状的二氧化硅,影响浸出矿浆的澄清与过滤。 处理块状硫化矿的焙烧最早是采用堆式焙烧,后改为竖炉焙烧。随着原矿品位的降低和浮选的迅速发展,炼锌厂处理的原料,都是粉末状的锌精矿,这就迫使采用符合精矿焙的特点的焙烧炉。 1.2硫化锌精矿焙烧的主要反应 因为焙烧是在原料和产物熔点温度以下进行的一种化学反应,故工业上焙
重金属冶金学 复习题
重金属冶金学复习题 一、名词解释 1.重金属 重金属指铜、铅、锌、镍、钴、锡、锑、汞、镉和铋等金属,他们的共同点是密度均在6g/cm3左右。 2.氧化焙烧 氧化焙烧是在氧化气氛中,矿料中硫化物在高温度下与氧反应,使精矿中的硫、砷等转化为挥发性的氧化物,从精矿中除去。 3.中性浸出 由于锌矿物中不同程度的含有铁杂质,浸出过程中不可避免有铁的浸出,为了得到铁含量尽可能低的硫酸锌浸出液,可控制浸出的终点pH值在5.2~5.4之间,使进入溶液的铁水解进渣,因浸出终点溶液接近中性,故称为中性浸出。 4.电冶金 利用电能从矿石或其他原料中提取、回收和精炼金属的冶金过程。 二、填空题 1. 有色金属分为轻金属、重金属、贵金属和稀有金属四大类。 2. 火法练锌包括焙烧、还原蒸馏和精炼三个主要过程。 3. 根据还原蒸馏法炼锌或湿法炼锌对焙砂的要求不同,沸腾焙烧分别采用高温氧化焙烧和低温部分硫酸化焙烧两种不同的操作。 4.火法炼铅方法可分为氧化还原熔炼法、反应熔炼法和沉淀熔炼法三类。 5. 湿法炼锌包括焙烧、浸出、净化和电积四个主要过程 三、简答题 1.在造锍熔炼过程中,减少Fe3O4生成的措施有哪些? 答:在造锍熔炼过程中,保持低的炉渣成分a(FeO),高的铜锍品味a(FeS),适当高的温度和低的气氛P(SO2),可以消除或减少Fe3O4的影响。 2. 说明硫化锌精矿焙烧的目的。 答:因为FeS不能直接被H2、C、CO还原,也不溶解于冷的稀硫酸和稀盐酸,焙烧的根本目的在于将精矿中的硫化锌尽量氧化为氧化锌,同时尽量脱除对后续工艺有害的杂质。 3. 沸腾焙烧的强化措施有哪些?
答:高温沸腾焙烧,锌精矿富氧空气沸腾焙烧、多层沸腾焙烧、利用二次空气或贫SO2焙烧结烟气焙烧等。 4. 湿法炼锌浸出搅拌为什么采用空气搅拌,而静液过程为什么采用机械搅拌? 答:湿法炼锌浸出过程中为了使浸出液中Fe2+尽可能地全部氧化成Fe3+除去,采用空气鼓风的方法进行搅拌,而静液过程中为了除去Cu、Cd、Co等杂质加入锌粉,考虑到空气搅拌会使锌粉氧化损失,因此静液过程中采用的是机械搅拌。 5. 锌焙砂中性浸出净化时,锌粉置换铜镉的原理是什么?影响锌粉置换反应的因素有哪些? 答:锌粉置换除铜、镉采用多段锌粉置换法在锌粉表面上进行的多相反应过程,,影响锌粉置换除铜、镉的因素有:锌粉的质量和用量、搅拌速度、置换温度、中静液成分和添加剂。 6.为何铜锍品味越高,渣中铜含量越高? 答:传统的造锍熔炼法,体系氧势较低,所产铜锍品味不高,渣中铜含量较低,而现代的强化熔炼法,由于体系氧势高,铜锍品味高。 五、论述题 1.为什么瓦钮柯夫熔池熔炼炉的生产率很高?请与白银熔炼进行对比分析。 答:(1)备料简单,对炉料适应性强。 (2)由于处理湿料与块料,烟尘率低。 (3)鼓泡乳化强化了熔炼过程,炉子的处理能力很大,硫化物在渣层氧化,放出的热能得到充分利用。 (4)大型瓦钮柯夫炉炉膛中的隔墙将炉膛空间分隔为熔炼区和渣贫化区,熔炼产物铜锍与炉渣逆流从炉子两端放出,炉渣在同一台炉中得到贫化,无需设置炉外贫化工序。 (5)炉子在负压下操作,生产环境较好,作业简单。 2.说明硫化锌溶液精矿氧压浸出的原理及其特点。 答:硫化锌精矿氧压技术的特点是:锌精矿不经焙烧直接加入压力釜中,在一定的温度和氧分压条件下直接酸浸获得硫酸锌溶液,原料中的硫、铅、铁等则留在渣中,分离后的渣经浮选、热滤,回收元素硫、硫化物残渣及尾矿,进入硫酸锌溶液中的部分经铁中和沉铁后进入后续工序处理。 该工艺浸出效率高,对高铁闪锌矿和含铅的锌精矿适应性强,与常规湿法锌炼方法相比,物需建设配套的焙烧车间和酸厂,有利于环境的治理;尤其是对于成品硫酸外运交通困难地区的情况,