铸钢件探伤标准解析
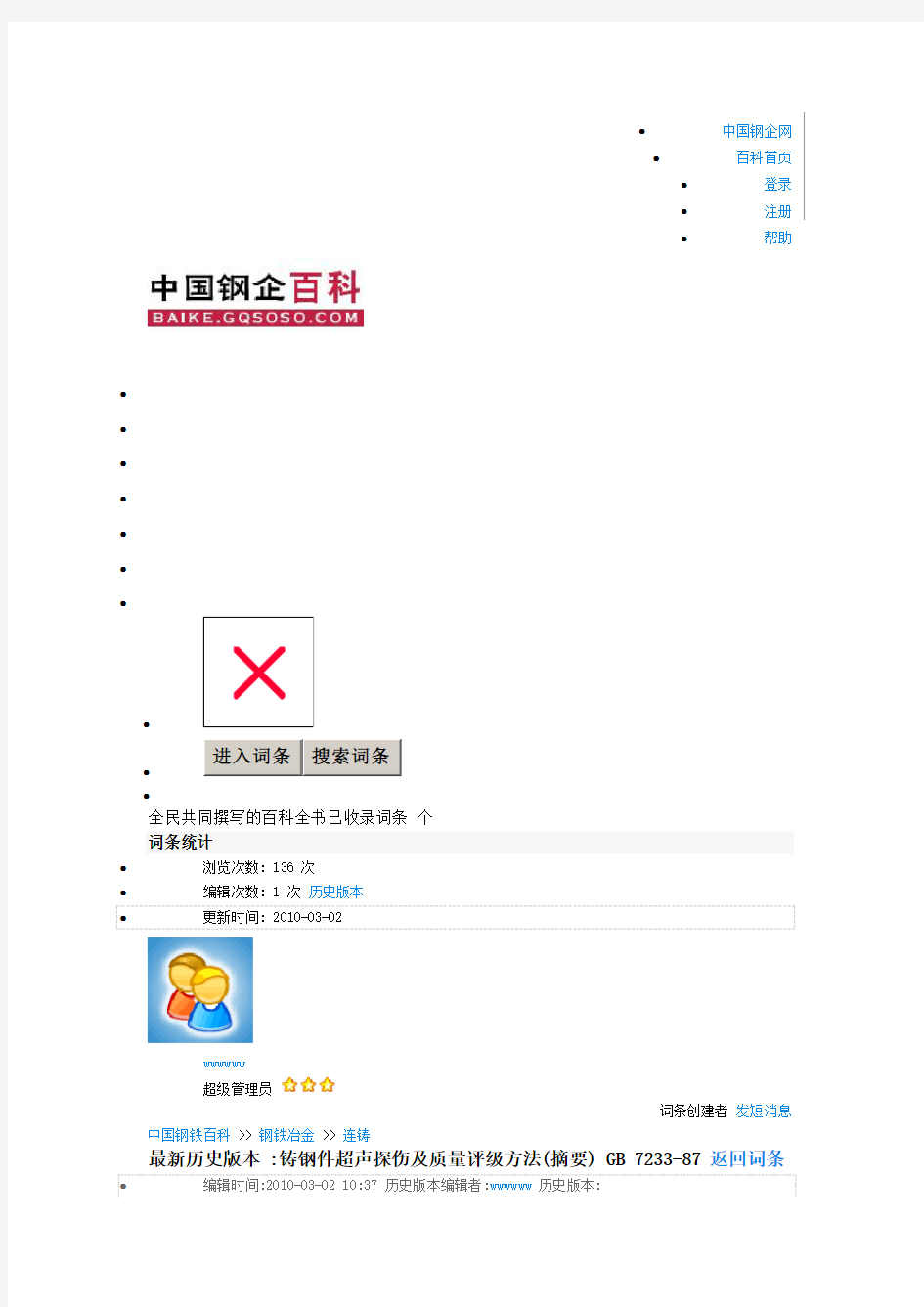

?中国钢企网
?百科首页
?登录
?注册
?帮助
?
?
?
?
?
?
?
?
进入词条搜索词条
?
?
全民共同撰写的百科全书已收录词条个
词条统计
?浏览次数: 136 次
?编辑次数: 1 次历史版本
?更新时间: 2010-03-02
wwwwww
超级管理员
词条创建者发短消息中国钢铁百科 >> 钢铁冶金>> 连铸
最新历史版本 :铸钢件超声探伤及质量评级方法(摘要) GB 7233-87 返回词条?编辑时间:2010-03-02 10:37 历史版本编辑者:wwwwww历史版本:
?内容长度:208130 图片数:0目录数:0
?修改原因:
铸钢件超声探伤及质量评级方法(摘要) GB 7233-87
本标准系铸钢件超声探伤的通用标准。
本标准规定了厚度等于或大于30mm的碳钢和低合金钢铸件的超声探伤方法;以及根据超声探伤的结果对铸件进行质量评级的方法。所用的超声探伤方法仅限于A型显示脉冲反射法。
在定货时,由供需双方商定铸钢件超声探伤的以下要求:
a.检测的区域及使用的探头;
b.纵波直探头探伤灵敏度;
c.铸钢件质量的合格等级,允许对平面型缺陷和非平面型缺陷提出不同的质量等级要求。
本标准不适用于奥氏体不锈钢铸件的检测。
1术语
1.1平面型缺陷(Planar discontinuity):用本标准规定的方法检测一个缺陷,如果只能测出它的两维尺寸,则称为平面型缺陷。属于这种类型的缺陷有裂纹、冷隔、未熔合等。
1.2非平面型缺陷(Nonplanar discontinuity):用本标准规定的方法检测一个缺陷,如果能够测出它的三维尺寸,则称为非平面型缺陷。属于这种类型的缺陷有气孔、缩松、缩孔、夹砂、夹渣等。
1.3透声性(Permeability to ultrasound):超声纵波垂直入射到测试面与其背面平行的无缺陷的铸钢材料中,超声波在其中往返传播一次所引起的声压降。单位为分贝(dB)。
通常用纵波直探头测试的第二次与第一次底面回波幅度所差的分贝数表示。
2仪器、试块、耦合剂
2.1仪器仪器应符合ZBy230—84 2.2探头 2.2.1纵波直探头的晶片直径在10~30mm的范围,当被检测铸钢件的探伤面较粗糙时,建议使用有软保护膜的纵波直探头。 2.2.2应使用在钢中的折射角为45。、60。、70。的横波斜探头,或使用K值为1.1.5、 2、2.5、3的横波斜探头。 2.2.3纵波双晶探头两晶片之间的声绝缘必须良好。 2.3仪器系统的性能仪器系统的灵敏度余量和分辨力的测试应符合ZBJ 04001.86的规定,并满足下列要求:a.使用2~2.5Mt的探伤频率,纵波直探头测试的灵敏度余量不得小于30dB,横波斜探头测试的灵敏度余量不得小于50dBc, b.在相应的探伤频率范围,纵波直探头和横波斜探头测试的分辨力应满足表1的规定。 表1仪器系统分辨力的下限值 2.4试块 2.4.1对比试块用铸造碳钢或低合金钢材料制做,其超声衰减系数应与被探伤铸钢件材料的衰减系数相同或相近。 制做对比试块的材料必须预先进行超声探伤,不允许存在等于或大于同声程562当量平底孔的缺陷。 对比试块侧面要标明试块的名称、编号、材质、透声性。 2.4.2供纵波直探头用的zGz系列对比试块见附录A(补充件)。当被探伤铸钢件的厚度大于250mm时,要制做最大探测距离等于铸钢件厚度的试块。 zGz系列对比试块仅在用试块调整纵波直探头探伤灵敏度时才使用。 2.4.3供纵波双晶探头用的ZGS对比试块见附录B(补充件)。 2.5耦合剂. 通常可选用机油、水溶性耦合剂、机油与黄甘油混合剂、水或浆糊作为耦合剂。 耦合剂不得在铸钢件成品上造成不允许的锈蚀。 调整仪器、校核仪器和检测铸钢件必须使用同种耦合剂。 3铸钢件 3.1探伤面 3.1.1铸钢件应在外观检查合格后进行超声探伤,铸钢件的探伤面及其背面所有影响超声检测的物质应予清除。 3.1.2铸钢件探伤面的表面粗糙度应满足以下要求: a.机械加工表面,Ra等于或小于10μm。 b.铸造表面,Ra等于或小于12.5μm. 3.1.3如机械加工之后铸钢件的形状妨碍超声探伤时,应在加工之前进行检测。 3.2铸钢件壁厚层次的划分 3.2.1按交货时铸钢件的外形,将铸钢件的截面厚度划分为三层:外层、内层、外层,铸钢件的厚度或截面尺寸小于90mm者,各层各占厚度或截面尺寸的三分之一。铸钢件的厚度或截面尺寸等于或大于90mm者,凡是距铸钢件某一表面30mm以内的范围为外层。其余部分为内层。 3.2.2经供需双方商定,允许对铸钢件检测区域规定专门的分层要求,也允许规定铸钢件的某一厚度范围或某些区域为质量严格要求区,并提出具体的质量要求。 3.3透声性 3.3.1测定铸钢件的透声性时,将纵波直探头与铸钢件上探伤面和背面平行而无缺陷的部位耦合接触,仪器的抑制置零。选用与纵波直探头探伤时相同的频率测试,调整仪器,使第一次底面回波的幅度达到垂直满刻度的50%,记录衰减器的读数。再调整衰减器,使第二次底面回波的幅度达到垂直满刻度的50%,记录衰减器的读数。两次衰减器读数之差即该测量点的透声性。 在铸钢件厚度相同的区域内,测量点不得少于三点。以各点透声性的平均值表示铸钢件该区域的透声性。 3.3.2如铸钢件没有背面与探伤面平行的足够大的探测部位,可以在铸钢件上适当位置预制一处这样的平面,也可以用与生产铸钢件相同的工艺制做平面试块,并以在其上测定的透声性代表铸钢件的透声性。 3.4铸钢件超声探伤适应性的判断仪器的“抑制”置零,使用2~2.5MF{z中的一种频率测试。在铸钢件的最大探测距离处,用纵波直探头测试。如选定为纵波直探头探伤灵敏度的参考平底孔的回波幅度比同声程噪声信号的幅度高8dB以上,则该铸钢件适合超声探伤。如果不能满足上述要求.可降低频率至1MHz测试,满足要求的,可以用这种频率探伤,并在探伤报告中说明。 如降低频率测试的结果仍不能满足超声探伤适应性的要求,则应采用热处理的方法改善铸钢件的透声性,并在满足超声探伤适应性的要求后进行超声探伤。 4检测 4.1仪器的调整 4.1.1一般调整“抑制”置零,探测深度取适当值。不论使用哪种探头,都要求调整零点,使时基线原点右边的示波屏时基线刻度与探测距离成正比。 4.1.2探伤灵敏度的调整和核查 4.1.2.1纵波直探头探伤灵敏度的调整纵波直探头探伤允许采用φ3、φ4、φ6当量平底孔三种灵敏度。供需双方应规定铸钢件每个区域的探伤灵敏度。用下述两种方法之一调整探伤灵敏度: a.用AVG曲线板调整。把与检测条件相符的AVG曲线板(设衰减系数为零而绘制的)嵌入示波屏,衰减器预置足够的储备量。将纵波直探头与铸钢件上探伤面和背面平行而无缺陷的部位耦合接触,调整仪器,使第一次底面回波的幅度达到AVG曲线板上“B一××dB"线标明的幅度,按“B一××dB”,减小衰减量××dB。利用曲线板上被选定作为探伤灵敏度的参考平底孑L的距离幅度曲线,进行透声性补偿,画出已经透声性补偿的距离幅度曲线。 透声性补偿方法见附录C(补充件)。 b.用对比试块调整。利用附录A中具有选定作为探伤灵敏度参考平底孔的一套试块调整。首先,将铸钢件与探测距离等于或最接近于铸钢件厚度的对比试块相比较,求出表面粗糙度补偿值与透声性补偿值的代数和,衰减器预置的储备量不得小于上述代数和的值。其次,在这块对比试块上测试,调整仪器,使平底孔的回波幅度达到垂直满刻度的10%~20%。不改变仪器的参数,对探测距离较小的一系列试块逐一测试,建立距离幅度曲线。在这条曲线上,对透声性予以补偿,得到已经透声性补偿的距离幅度曲线。最后,调整衰减器,进行表面粗糙度和透声性补偿。 透声性补偿方法见附录C。 4.1.2.2纵波双晶探头探伤灵敏度的调整。衰减器预置的储备量不得小于表面粗糙度补偿量。测试不同探测距离的平底孔,调整仪器,使其中最高的回波幅度达到垂直满刻度的80%。不改变仪器的参数,对探测距离不同的平底孔逐一测试,建立距离幅度曲线。调整衰减器,补偿表面粗糙度损失。 4.1.2.3横波斜探头探伤灵敏度的调整将横波斜探头与铸钢件探伤面耦合接触,调整仪器,使噪声信号的幅度达到1~3mm。如果仪器在最高灵敏度时,噪声信号幅度仍不足1mm,则以最高灵敏度探伤。 4.1.2.4探伤灵敏度的核查探伤中,应定期核查探伤灵敏度。发现探伤灵敏度改变时,要重新调整,并对前次核查以来完成的探伤工作重新进行探伤。探伤工作结束时,应核查探伤灵敏度。 4.2扫查探伤人员要选择有规律的扫查路径进行探伤,相邻两次扫查应相互重叠约为探头晶片尺寸的15%。扫查时,探头移动的速度不得大于150mm/s。横波斜探头探伤至少要在探伤面上相互垂直的两个方向扫查,在扫查的同时,应不断偏转探头,偏转角度不得小于15。因铸钢件几何形状的限制而扫查不到的部位,必须在探伤报告中注明。 4.3缺陷的检测采用供需双方规定的探头对铸钢件检测区域进行扫查。 纵波直探头或纵波双晶探头扫查时。采甩比4.1.2.1或4.1.2.2项确定的探伤灵敏度高6dB的扫查灵敏度。凡出现下列任何一种显示情况的位置,都要做上标记:a.缺陷回波幅度等于或大于距离幅度曲线的位置; b.底面回波幅度降低12dB或12dB以上的位置; c.不论缺陷回波幅度的大小,凡出现线状和片状特征缺陷显示的位置。 4.4缺陷尺寸的测定按 4.1.2款确定的探伤灵敏度,测定4.3条标记的缺陷尺寸。 4.4.1平面型缺陷尺寸的测定对于具有线状和片状特征的缺陷显示,有6dB法画出缺陷的范围。按几何原理,确定缺陷的位置、大小和缺陷在铸钢件厚度方向的尺寸,按表2的规定,计算缺陷的面积。 4.4.2非平面型缺陷尺寸的测定 4.4.2.1缺陷回波幅度等于或大于距离幅度曲线者,用6dB法在探伤面上画出缺陷的范围。按表3的规定,计算缺陷的面积。当使用纵波检测时,缺陷近探伤面一侧的边界和深度,由缺陷回波脉冲前沿的幅度上升到比距离幅度曲线低6dB的位置来确定。当使用横波斜探头检测时,缺陷的边界,由缺陷回波脉冲前沿幅度上升到比同时显示的最大缺陷回波幅度低6dB的位置来确定。缺陷在铸钢件厚度方向的尺寸,由不同方向检测所确定的缺陷上部和下部边界而得到。由于铸钢件几何形状的限制,不能从不同方向检测的缺陷,必须在探伤报告中说明。 4.4.2.2对于底面回波降低12dB或12dB以上的位置,应核查底面是否倾斜或不平整、耦合接触是否良好。凡是因存在缺陷而使底面回波降低12dB或12dB以上者,以底面回波降低12dB为条件,在探伤面上画出缺陷的范围,按表3注②计算缺陷的面积。缺陷的深度,由一处连续缺陷回波中最左边的波峰的位置来确定。缺陷在铸钢件厚度方向的尺寸,由一处连续缺陷回波中最左边的与最右边的两个波峰之间的宽度来确定。即无底面回波,又无缺陷回波的位置,应提高探伤灵敏度检测,观察是否存在反射面与入射声束倾斜的缺陷。 4.4.3缺陷范围的修正.探伤面为曲面时,在探伤面上画出的缺陷范围应予修正。修正的方法可用计算法或作图法。 4,4.4存在疑问的缺陷对于存在疑问的缺陷显示,允许采用经过验证而行之有效的其它无损检测方法来检验。 5质量等级的评定 铸钢件的质量等级,分别按平面型缺陷和非平面型缺陷来划分。根据平面型缺陷和非平面型缺陷的尺寸,将铸钢件质量等级各分为五级。对于同一类型的缺陷,在相同的探伤条 件下,一级质量最好,二、三、四、五级质量依次降低。评定质量等级时,缺陷尺寸中有一项或几项大于某级的要求,则参加下一级的评定,凡不满足四级要求的评为五级。 评定时,采用317×317mm2(面积约100000mm2)的评定框。位于评定框边界线上的缺陷,计算缺陷的尺寸时,只计入该缺陷框内部分的尺寸。 5.1按平面型缺陷评定质量等级时,把评定框置于铸钢件上平面型缺陷最严重的位置。根据评定框内平面型缺陷的尺寸,按表2评定铸钢件的质量等级。 表2平面型缺陷质量等级的划分 注:一个缺陷的面积,等于该缺陷的最大尺寸和与其垂直方向的最大尺寸之积。 5.1.1凡检测区域内存在裂纹的铸钢件,评为五级。 5.2按非平面型缺陷评定质量等级时,把评定框置于铸钢件上非平面型缺陷最严重的位置。根据评定框内非平面型缺陷的尺寸和深度,按表3评定铸钢件的质量等级。 表3非平面型缺陷质量等级的划分 注:①一个缺陷的最大尺寸大于320mm,则评为五级。 ②一个缺陷的面积,等于该缺陷的最大尺寸和与其垂直方向的最大尺寸之积。 ⑧位于外层的间距小于25mmt的两个或多个缺陷,在计算一个缺陷的面积时,视为一个缺陷。其“一个缺陷的面积”等于这些缺陷面积之和。 5.3位于外层和内层界面上的非平面型缺陷,如其大部分在外层,则计入外层。否则,则计入内层。 5.4如评定框的面积大于一个检测区域的面积,该区域各级别允许的平面型缺陷和非平面型缺陷的总面积,按检测面积与评定框面积之比,以正比例予以折算。但是,缺陷在铸钢件厚度方向的尺寸和一个缺陷的面积仍按表2和表3的规定。 如一个检测区域的某一边小于317mm,而其面积等于或大于评定框的面积,则以一个矩形评定框来评定。矩形框的一边的长度为上述检测区域的边长,另一边长度的确定方法是使这个矩形的面积等于100000mm2。 5.5某级铸钢件,系指铸钢件中平面型缺陷和非平面型缺陷均分别满足该级的规定。 5.6评定探伤面为曲面的铸钢件质量等级时,在缺陷最严重的位置放置评定框。在垂直于评定框平面的方向,对处于评定框投影范围内的缺陷予以评定。缺陷的尺寸按4.4.3款进行修正。注意:不得在同一评定框内对同一缺陷重复计入其尺寸。 5.7铸钢件焊补部位也可以应用本标准进行探伤和评定。 6人员资格(略) 7探伤报告(略) 附录A铸钢件超声纵波直探头探伤用系列对比试块(补充件) A:1名称和编号名称为ZGZ系列对比试块,编号见表。 A.2材料试块材料应符合本标准2.4.1款的规定。 A.3形状和尺寸形状和尺寸见下图和表。 ZGZ系列对试块 注:d:平底孔直径;l:探测距离;L:试块全长;D:试块直径;T:铸钢件厚度(T 大于250mm)。 附录B铸钢件超声纵波双晶探头探伤用对比试块(补充件) B.1名称和编号名称为ZGS对比试块,编号为3。 B.2材料试块材料应符合本标准2.4.1款的规定。 B.3形状和尺寸形状和尺寸见下图和表。 对比试块9个平底孔的探测距离L明细表 附录C透声性补偿方法(补充件) 用试块调整纵波直探头探伤灵敏度时,如果铸钢件的透声性与探测距离等于或最接近于铸件厚度的对比试块的透声性之差的绝对值大于2dB,或者,用AVG曲线板调整时,如果铸钢件的透声性大于8dB,必须对透声性予以补偿。 c.1按纵波直探头探伤灵敏度调整方法,求出铸钢件的透声性与对比物的透声性之差P: a.用对比试块调整时,P等于铸钢件的透声性与选定的对比试块的透声性之差,若铸钢件透声性劣于试块的透声性,P为正值,否则,P为负值。 b.用AVG曲线板调整时,P等于铸钢件的透声性减6dB,P恒为正值。 c.2按P的绝对值所在的范围,查表c1,得到P、3/4P、1/2P、1/4P的绝对值,其代数值的符号与p的符号相同。 表C1 c.3查表C2,得到代数值P、号P、丢P、百1P分勇0对应的幅度比。 表C2 c.4按采用调整灵敏度的方法,利用AVG曲线板上被选定作为纵波直探头探伤灵敏度的参考平底孔的距离幅度曲线,或者,利用ZGZ系列对比试块测绘的距离幅度曲线,找出对应于0、1/4、1/2、3/4倍铸钢件厚度的回波幅度值,分别乘以p、3/4P、1/2P、1/4P对应的幅度比。底面回波幅度不变,在透明板上分别画出以上五点,平滑地连接这五点而成的曲线,即经过透声性补偿的距离幅度曲线 铸钢件的制作方案 一. 概述 xxX主体育场并非简单构筑物,其中的铸钢件要求尺寸精度高且加工制作难度大,其既为一件精密的机械零件,又是一件精美的艺术品。 在xxX主体育场铸钢件的设计、模型制造、铸造、加工及质检等过程中,始终贯彻下述原则:我们在设计、生产制作过程中,认真执行相关国家、行业及特定验收标准。严格控制每一生产过程,确保提供外型尺寸符合图纸要求;化学成分、机械性能达到设计要求;铸钢件内外质量满足检测要求的高品质铸钢件。 xxX主体育场铸钢件是集计算机辅助设计(CAD)、计算机辅助制造(CAM)、计算机辅助测量(CAM)及先进的铸造凝固模拟分析技术(CAE)为一体的高科技产品。 本内容详细介绍xxX主体育场铸钢件在设计、制作过程各个环节:难点及解决方案;铸钢件主要结构形式;制作工艺流程;铸钢件制作;质量控制;检验标准。 二. 关键点、难点及解决方案 (一)铸钢件的关键点 关键点:xxX主体育场铸钢件结构形式需要满足下列要求: 首先:铸钢件保证原设计的外部造型及整体受力要求。 其次:铸钢件保证尺寸精度及表面粗制度的设计要求。 最后:铸钢件内部结构符合铸造工艺的要求。 解决方案:针对以上铸钢件的关键点,利用三维造型软件、有限元受力分析软件、计算机凝固模拟分析软件相互协调,在原设计的基础上深化设计满足上述要求的铸钢件结构形式(铸钢件三维实体模型)。 (二)铸钢件的难点 难点:由于xxX主体育场铸钢件的特点种类多、数量多、分枝多,导致大量的模型制作工作量。如何解决模型制作在满足设计的结构形式的前提下保证工期的要求是本工程的难点。 解决方案:针对以上铸钢件的难点。利用三维造型软件。 (包括封面,共 16 页) 1.0目的 为保证我司钣金件产品的质量,又减少图纸对通用要求的描述,特制订本通用检验标准。 2.0范围 本标准适用于我司标准以及非标准的钣金产品,本标准侧重范围,规定了钣金件在质量形成过程中各个工序的检验标准,主要从外观、尺寸控制、力度、组装要求作出规定;对钣金件产品的功能、结构特别性能不作规定,我司主要产品要求须参照相关检验标准,特别产品之特殊要求需另外说明。 3.0职责 3.1工程部 3.1.1设计时应支持本标准,对特别要求应特别说明。 3.1.2与本标准有关的不符合项之特纳。 3.2销售部 3.2.1客户特别要求的收集 3.2.2与本标准有关的不符合项之特纳 3.3生产部 按本标准做货及自检。 3.4品管部 按本标准检验。 4.0作业内容 4.1剪床开料 4.1.1外观保证 4.1.1.1剪床开料必须用经IQC检验合格之板材,大料平直度、外表面状态必 须符合IQC检验标准。 4.1.1.2未经确认不得采用已生锈之SECC和SPCC板料,以及表面严重划伤之 SUS板料。 4.1.1.3对胶沙不锈钢应注意开料之纹向要求,不可在不确定情况下作出纹向 任意开料,并严格保护表面,以避免刮伤。 4.1.1.4剪床开料之批锋应小于料厚之3%,手摸应无明显刮手现象。 4.1.2尺寸控制 4.1.2.1为保证钣金成形尺寸,减少过程累积误差对工件尺寸的影响,剪床开 料尺寸允差按下表检验: 4.1.2.2对一开几过多的开料件,如单一方向开料数量超过六件(一般应为偶 数),应先将料对开,然后再开成单件,以减少误差累积。 4.1.2.3对长度超过1500-2500之开料切边直线度应小于0.3mm/m,宽度大小端 误差小于0.5mm。 4.1.2.4开料件之长短边90。角度允差±3′。 4.2 CNC冲孔 4.2.1外观保证 4.2.1.1 CNC冲孔应先检查板材是否有划伤,对经剪床放行而有少许划伤之板 料,冲孔时应将划伤面尽量放于批锋面,以减少对外观的影响。 4.2.1.2 CNC冲孔应留意批锋在工件成形后的位置影响,应尽量保证批锋在工 件成形后的内面方向:(对重要表面,工程绘图应将外表面放在正视方 向,以方便编程)对重要表面又分左右之工件,CNC冲孔需在冲孔时分 左右(即正反),以保证成形后批锋都朝内面。 4.2.1.3对胶沙不锈钢,CNC冲孔应保证批锋位于胶沙之反面。(工程绘图,应 留意将外表面放在胶沙面且于图之正视方向,并作出相应之标注,如在 打弯图上标明胶沙面位置)。 4.2.1.4冲孔应保证最小的模具接合缝以及批锋高度,直边接合缝不可出现大 于0.1~0.15之阶梯现象。孔边批锋高度一般应小于料厚的3%,最大不 可超过0.1mm(对T≦3mm厚板材言) 4.2.1.5为保证折弯后钣金件的拼角外观以及折弯尺寸,CNC冲应留意工艺孔不 可漏冲。一般T=0.8或1.0板,工艺孔取Φ2.0;T=1.0/1.5/2.0板,工艺孔取Φ2.6;T=3.0板,工艺孔取Φ3.2。 4.2.2尺寸保证 4.2.2.1孔距 关于印发《钢轨探伤管理规则》的通知 各铁路局: 1995年铁道部发布的《钢轨探伤管理规则》(铁工务〔1995〕144号)对指导工务钢轨探伤工作,保证线路质量,确保铁路运输安全生产起到了重要作用。近年来,随着铁路提速和重载的不断发展,对钢轨探伤工作提出了更高的要求。随着大型钢轨探伤车的不断投入使用,全路已形成了钢轨探伤车和探伤仪的两级钢轨探伤网络。现行《钢轨探伤管理规则》已不适应铁路运输的发展,需进行修改完善。现将修改后的《钢轨探伤管理规则》予以发布,自2006年10月1日起施行。铁道部原发《钢轨探伤管理规则》(铁工务〔1995〕144号)同时废止。《钢轨探伤管理规则》由铁道部运输局负责解释。 二○○六年十一月十日 钢轨探伤管理规则 第一章总则 第一条为适应铁路运输的发展,加强钢轨探伤管理,提高钢轨探伤作业质量,根据《铁路技术管理规程》,特制定本规则。 第二条钢轨探伤工作具有流动性和技术性强、安全责任重等特点,是工务部门钢轨防断、确保行车安全的关键工作。钢轨探伤作业应安排在白天进行。各有关部门要为探伤人员提供必要的工作、生活和业务学习条件,要对探伤设备的转运、存放、上道作业等给予积极支持和配合。 第三条各级管理部门要重视探伤工作,探伤从业人员应固定,探伤队伍应稳定。铁路局要积极改善工务系统培训基地的探伤培训条件,加强探伤技术人员的培训工作。工务段(桥工段)应建立探伤人员演练场所。探伤管理组应建立探伤人员技术档案。 第四条铁路局应加强两级探伤网络建设,实现钢轨探伤车与钢轨探伤仪之间检测数据资源共享、相互补充;定期组织钢轨探伤车操作人员与工务段探伤人员进行技术交流,根据检测结果进行技术总结,以防漏检或误判。 第五条本规则适用于铁路线路钢轨探伤。 第二章组织管理 第一节机构和人员 第六条铁道部钢轨探伤主管部门负责全路钢轨探伤管理工作。 《铸钢件检验规范》执行情况会议纪要 2009年09月24日下午1点在福建海源公司四楼会议室,我司有关技术人员与三重技术人员就《检验规范》进行探讨,并针对近期铸钢件质量下滑等问题进行讨论。现将会议主要内容纪要如下: 一、关于《检验规范》使用:我司王总工程师提出,《检验规范》的制订是根据我司二十年压机制造过程中,结合实际情况,参照国家铸造标准范围内的,外协铸造厂家完全能做到的。三重张总工程师也同意了以上观点,双方同意以《检验规范》为产品检验判定标准。 二、会议就近期铸钢件质量下滑提出暂时解决方案,要求三重铸锻公司在一个月之内(过渡时间为一个月),需达到我司《检验规范》的质量要求。出厂的产品因铸造缺陷而进行焊补,导致我司上下架超出两次,第二次及以上由此引起的经济损失(如机加工费)由铸造厂家负责,并按最后成品的时间来考核交货时间,超出时间,按合同规定执行。因尺寸缺陷而进行焊补的,由此引起的延误工期,按合同规定的超出时间,给予扣款执行。 三、会议就因质量问题判定退回厂家进行返工的,如大面焊补,较大裂纹等,请厂家按合同规定,返工送达我司时,需提供缺料报告,焊补与修复工艺,退火纪录,探伤报告,与质量承诺书。 四、关于判定废品的程序。在我司检验部门按公司规定程序执行,不合格品判定,按规定销毁,不得重复交付废品的铸件。 五、对现场四件HF1100上梁返工回我司,要求三重铸锻公司派探伤人员现场与我司质检人员共同探伤复检,9月26日之前人员到位。 六、关于新产品图纸进行技术交流问题,要求铸造厂接到新产品图纸时,因铸造工艺需要,需与我司技术中心沟通,并以文字形式备案。 参加人员 三重公司:张总工程师与高伟峰经理 海源公司:王总、曹工、管代、郑祥光、唐建新、林森清、蒋荣辉、何建新 铸钢件生产工艺要求及质量标准 一、混砂工艺标准 (一)材料要求: 1、造型砂:符合GB9442-88 、JB435-63细粒砂要求,一般选用二氧化硅含量较高的天然砂或石英砂,原砂粒度根据铸件大小及壁厚确定,原砂的含泥质量分数应小于2%,原砂中的水份必须严格控制,且一般应进行烘干。 2、水玻璃:水玻璃模应根据铸件大小来确定。 (1)小砂型(芯)为加速硬化采用选用M=2.7—3.2的高模数水玻璃。 (2)中型砂型(芯)可选用M=2.3—2.6的水玻璃。 (3)生产周期长的大型砂型(芯)选用M=2.0—2.2的低模数水玻璃。 (二)混制比例(质量分数%) 造型砂/水玻璃=100:6~8 (三)混制时间:一般情况下混制5分钟,室温或水玻璃密度较大时可适当延长混砂时间。 (四)混制后要求:混制好的造型砂要求无块状或团状,流动性较好。 二、造型工艺要点: (一)基本原则: 1、质量要求高的面或主要加工面应放在下面。 2、大平面应放在下面。 3、薄壁部分应放在下面。 4、厚大部分应放在上面。 5、应尽量减少砂芯的数量。 6、应尽量采用平直的分型面。 (二)基本要求: 1、木模:要求轮廓完整,无裂纹、无破损、无残缺,表面光洁,尺寸符合铸造工艺图纸要求,并经常进行尺寸校验。 2、砂箱:砂箱的尺寸大小应根据木模规格确定,大、中型砂箱应焊接箱筋。 3、浇注系统:根据铸件的结构特点的工艺要求,选择适宜的浇注系统,通常采用顶注式、底注式。 (1)浇注系统设置基本原则:浇口、冒口安放位置合理,大小适宜不妨碍铸件收缩,便于排气、落砂和清理,应使铸型尺寸尽量减少,简化造型操作,节省型砂用量和降低劳动强度。 (2)内浇道位置的注意事项。 1)内浇道不应设在铸件重要部位。 2)应使金属液流至型腔各部位的距离最短。 3)应不使金属液正面冲击铸型和砂芯。 4)应使金属液能均匀分散,快速地充满型腔。 5)不要正对铸型中的冷铁和芯撑。 4、冒口 (1)冒口设置基本原则: 钣金件检验标准 一、适用范围: 公司产品钣金件的尺寸、外观检验。 二、检验项目及验收标准: A. 尺寸验收标准:尺寸按图纸要求及钣金加工公差表执行,特殊情况以实际装配并提交研发部工程师协同解决。 B. 表面处理验收标准: a. 表面烤漆检验标准: 1. 颜色及纹路:由承制方按要求制作样板,双方确认。验收按样板,不得有明显色差(不得大于3度),纹路符合样板。 2. 密着检验:用百格刀划一面100方格到底材后,用3M胶布贴上,60度方向瞬间用力拉开,不得脱落40/100格。 3. 溶剂检验:酒精擦拭后,不能有变色、掉色、无光泽等现象。 4. 硬度检验:以H铅笔将笔芯前端切齐,铅笔与待测物成45度推出,表面无划伤。 5. 钣金件表面烤漆前须作前道电着处理,达到双重保护的目的。根据实际的使用效果,允许厂商使用双面镀锌材质加工,以替代电着工艺。 6. 厂商在每次送货时须提供材质报告,有表面处理要求的须提供表面处理检验合格报告 7. 外观判定标准,如下表: 判定标准 外观 1. 表面不得有任何碰伤、开裂、刮伤等严重表面缺陷。如加工过程中有此缺陷,喷涂前须补腻子处理。表面各边、角、焊接部位毛刺均须去除。 2. 表面污点、颗粒、气泡检验: A面: 整个表面内允许3点,每点直径1mm以下,点与点距离20mm以上。 B面: 整个表面内允许5点,每点直径1mm以下,点与点距离20mm以上。 C面: 整个表面内允许7点,每点直径1mm以下,点与点距离20mm以上 3. 箱体内表面检验: 各面允许8点气泡或污点, 每点直径1mm以下,点与点距离20mm以上。 4. 烤漆厚度30μm-60μm。 5. 表面处理后,各螺柱及螺孔表面不允许有漆层覆盖,影响装配。 包装: 1. 每箱数量固定。 2. 包装袋内不得有残留毛屑及杂物。 3. 包装箱不得有破损现象。 4. 每箱须标明料号、品名、数量等资料。 b. 表面镀层检验标准: 镀层外观质量要求i. 镀层颜色检查 A、花锌:镀锌层经钝化后带有绿色、黄色和紫色的不亮或半光亮彩虹色; B、五彩:镀锌层经钝化后带有绿色、黄色和紫色光亮彩虹色; C、白锌:镀锌层经钝化后稍带有浅兰色调的银白色; D、镀铬:工程图无特别说明均为镀亮铬(3级—2级); E、镀镍:工程图无特别说明均为镀亮铬(3级—2级)。化学镀镍层应为稍带浅黄色的银白色或带黄色色彩的钢灰色,抛光后为光泽的钢灰色。ii. 镀层结晶 镀层结晶应是均匀、细致、光滑。iii. 允许缺陷镀层允许以下缺陷存在: A、轻微的水印(非主视面主要表面); 铸钢件超声探伤及质量评级方法(摘要) GB 7233-87 本标准系铸钢件超声探伤的通用标准。 本标准规定了厚度等于或大于30mm的碳钢和低合金钢铸件的超声探伤方法;以及根据超声探伤的结果对铸件进行质量评级的方法。所用的超声探伤方法仅限于A型显示脉冲反射法。 在定货时,由供需双方商定铸钢件超声探伤的以下要求: a.检测的区域及使用的探头; b.纵波直探头探伤灵敏度; c.铸钢件质量的合格等级,允许对平面型缺陷和非平面型缺陷提出不同的质量等级要求。 本标准不适用于奥氏体不锈钢铸件的检测。 1术语 1.1平面型缺陷(Planar discontinuity):用本标准规定的方法检测一个缺陷,如果只能测出它的两维尺寸,则称为平面型缺陷。属于这种类型的缺陷有裂纹、冷隔、未熔合等。 1.2非平面型缺陷(Nonplanar discontinuity):用本标准规定的方法检测一个缺陷,如果能够测出它的三维尺寸,则称为非平面型缺陷。属于这种类型的缺陷有气孔、缩松、缩孔、夹砂、夹渣等。 1.3透声性(Permeability to ultrasound):超声纵波垂直入射到测试面与其背面平行的无缺陷的铸钢材料中,超声波在其中往返传播一次所引起的声压降。单位为分贝(dB)。通常用纵波直探头测试的第二次与第一次底面回波幅度所差的分贝数表示。 2仪器、试块、耦合剂 2.1仪器仪器应符合ZBy230—84的规定,并满足下列要求: a.使用2~2.5Mt的探伤频率,纵波直探头测试的灵敏度余量不得小于30dB,横波斜探头测试的灵敏度余量不得小于50dBc, b.在相应的探伤频率范围,纵波直探头和横波斜探头测试的分辨力应满足表1的规定。 4.2.1外观:表面无绣迹、无毛刺批锋,整批来料外观一致性良好。 4.2.2尺寸:按图纸与国标要求,重要尺寸零缺陷。 4.2.2性能:试装配与使用性能符合产品要求。 5、工序质量检验标准 5.1冲裁检验标准 5.1.1 对有可能造成伤害的尖角、棱边、粗糙要做去除毛刺处理。 5.1.2 图纸中未明确标明之尖角(除特别注明外)均为R1.0。 5.1.3 冲压加工所产生的毛刺,对于门板、面板等外露可见面应无明显凸起、凹陷、粗糙不平、划伤、锈蚀等缺陷。 5.1.4毛刺:冲裁后毛刺高L≤5%t(t为板厚)。 5.1.5 划伤、刀痕:以用手触摸不刮手为合格,应≤0.1mm。 5.1.6平面度公差要求见表一。 附表一、未注平面度公差要求 5.2 折弯检验标准 5.2.1 毛刺:折弯后挤出毛刺高L≤10%t(t为板厚)。 5.2.2 压印:看得到有折痕,但用手触摸感觉不到。(有特殊表面要求和镜面除外) 5.2.3 折弯变形标准按照《表二》及《表三》。 【附表二:对角线公差要求】 5.2.4折弯方向、尺寸与图纸一致。 5.2.5钢板在弯、折、卷制作过程中出现的锤击痕迹应予以修复,不得有明显锤窝现象。 5.3 钣金加工件检验标准 5.3.1 尺寸:尺寸按图纸要求检验,尺寸公差见表三。 【附表三:未注尺寸公差要求】 5.3.2焊接 5.3.2.1焊缝应牢固、均匀,不得有虚焊、裂纹、未焊透、焊穿、豁口、咬边等缺陷。焊缝长度、高度均不允许超过图纸长度、高度要求的10%。 5.3.2.2 焊缝平滑,表面处理后不得出现堆起凸包、不均匀现象。 5.3.2.3工件焊接完毕后,不得存在焊渣、焊点、毛刺等,焊缝应光滑、平整。应保证工件的“边齐、面平”,包括工件上开口边缘的垂直平行度。 5.3.2.4焊接后,其它非焊接部位不允许有被焊渣、电弧损伤现象,表面焊渣、飞溅物需清除干净。 钢轨探伤管理规则 第一章总则 第一条为适应铁路运输的发展,加强钢轨探伤管理,提高钢轨探伤作业质量,根据《铁路技术管理规程》,特制定本规则。 第二条钢轨探伤工作具有流动性和技术性强、安全责任重等特点,是工务部门钢轨防断、确保行车安全的关键工作。钢轨探伤作业应 安排在白天进行。各有关部门要为探伤人员提供必要的工作、生活 和业务学习条件,要对探伤设备的转运、存放、上道作业等给予积 极支持和配合。 第三条各级管理部门要重视探伤工作,探伤从业人员应固定,探 伤队伍应稳定。铁路局要积极改善工务系统培训基地的探伤培训条件,加强探伤技术人员的培训工作。工务段(桥工段)应建立探伤人 员演练场所。探伤管理组应建立探伤人员技术档案。 第四条铁路局应加强两级探伤网络建设,实现钢轨探伤车与钢轨探伤仪之间检测数据资源共享、相互补充;定期组织钢轨探伤车操作 人员与工务段探伤人员进行技术交流,根据检测结果进行技术总结,以防漏检或误判。 第五条本规则适用于铁路线路钢轨探伤。 第二章组织管理 第一节机构和人员 第六条铁道部钢轨探伤主管部门负责全路钢轨探伤管理工作。 第七条铁路局工务处负责全局钢轨探伤的组织管理工作,负责钢轨探伤技术和设备的管理。 第八条铁路局工务检测所应设钢轨探伤管理组。 第九条工务段(桥工段)、工务机械段应根据工作任务设探伤生产机构。 第十条铁路局应设专业技术人员主管钢轨探伤工作。工务段(桥 工段)、工务机械段应设专人负责钢轨探伤工作。 第十一条要按照GB/T9445和《国家职业标准》的要求加强对探 伤人员的技能培训、鉴定和考核。执机人员必须具有I级或以上级 别的探伤人员技术资格;Ⅱ级探伤人员应不少于探伤人员总数的50%。 第十二条仪器检修人员应具备Ⅱ级或以上级别的探伤人员技术资格,具有必要的电子技术知识和技能。对仪器检修人员应实行考评 制度,不合格者不应担任检修工作。 第十三条探伤从业人员要加强业务学习、不断提高业务技能。工务段(桥工段)、工务机械段对不适应钢轨探伤工作的人员要及时调整。 第十四条探伤从业人员应具有高中及以上文化程度,能胜任探伤 工作。 第二节工作职责 第十五条工务处 ㈠制定铁路局钢轨探伤工作发展规划和各项规章制度,并组织实施。 ㈡制定探伤设备(包括钢轨探伤车、钢轨探伤仪、钢轨焊缝探伤仪、通用探伤仪以及相应的探伤器材等)和相应检修设备的配置计划,负责小型探伤设备的选型。建立健全钢轨探伤设备检修管理制度。 ㈢制定钢轨探伤作业标准,并督促、指导实施,做好钢轨伤损和断轨的分析、统计。 ㈣制定探伤人员的培训、技术交流和技术比武计划。 ㈤制定钢轨探伤车的运用管理办法及年度探伤计划。 第十六条钢轨探伤管理组 文章编号!"##$%’()*##’+#,%##(*%#* 铸钢件超声波探伤中应注意的几个问题 万升云 )华中科技大学-湖北武汉./0012+ 摘要!结合探伤实践-对铸钢件超声波探伤时探头频率选择和缺陷波形定性等几个相关的问题 作了详细的分析3 关键词!铸钢4超声波4探伤4频率 中图分类号!52607/.文献标识码!8 超声波检测是常规的无损检测方法之一-在探测铸钢件及其补焊区域时所应用的标准为98:2// ;<:=铸钢件超声波探伤及质量评级方法>3由于铸钢件存在着晶粒粗大-内部金属分布不均匀-其外形几何形状复杂-表面粗糙等原因-给超声波检测带来了许多困难3根据多年的探伤实践认为!目前铸钢件超声波探伤过程中存在以下几个值得注意的问题3 "探伤频率的选择原则 铸钢件探伤困难的根本原因是其晶粒粗大-内部组织分布极不均匀-加之外形复杂-表面粗糙等3在98:2//;<:中-对频率的选择规定也比较抽象-不易掌握-因而探伤时的探测频率的选择就显得非常重要3众所周知-一旦被探测的工件确定-则声波在其中的传播速度也一定-由关系式?@A B C 式中!?DD波长4 E DD波速4 C DD波的频率3 由上式可知-频率越高-波长越短-而脉冲反射法超声波探伤的最大检测能力为?B2-这是因为声波具有绕过障碍物传播的绕射现象-绕射现象的存在限制了脉冲反射法超声波探伤对最小缺陷的检测能力3当缺陷尺寸小于?B2时-绕射占主导地位-该缺陷就不具备产生反射回波的条件-反射法探伤就无法检测出此缺陷3所以-对于同一工件而言-采用高的探测频率-可以提高小缺陷的检测能力-防止漏检3但频率过高时-铸钢件本身存在着晶粒粗大的问题-这样一来-工件对声波的吸收衰减和散射 收稿日期4200/%0F%21 作者简介!万升云)1G66%+-男-1G 消失模铸钢件检验标准 1.目的 规消失模铸钢件的检验标准,以使各工序过程的产品质量得以控制。 2.适用围 本标准适用于消失模铸钢件的检验,图纸和技术文件并同使用。如与国家标准和技术规冲突时,以国家标准和技术规为准。 3.引用标准 GB /T 26658 《消失模铸件质量评定方法》 GB /T 11352 《一般工程用铸造碳钢件》 GB /T 6414 《铸件尺寸公差与机械加工余量》 GB /T 11351 《铸件重量公差》 GB /T 5613《铸钢牌号表示方法》 GB /T 6060.1《铸件表面粗糙度比较样块》 GB /T 222《钢的成品化学成分允许偏差》 GB /T 223《钢铁及合金化学分析方法》 GB /T 228《金属拉伸试验方法》 GB /T 231.1《金属布氏硬度试验方法》 /T 5000.6《重型机械通用技术条件铸钢件》 /T 5000.7 《重型机械通用技术条件铸钢件补焊》 /T 5000.12 《重型机械通用技术条件涂装》 /T 5000.13 《重型机械通用技术条件包装》 /T 5000.14 《重型机械通用技术条件铸钢件无损探伤》 4.材料检验 铸件牌号,化学成分和力学性能 牌号: ZG230-450 化学成分(质量分数%)|C≤: 0.30 化学成分(质量分数%)|Si≤: 0.50 化学成分(质量分数%)|Mn≤: 0.90 化学成分(质量分数%)|S≤: 0.04 化学成分(质量分数%)|P≤: 0.04 残余元素: Cr≤0.35,Ni≤0.30,Mo≤0.20,Cu≤0.30,V≤0.05;但Cr+Ni+Mo+Cu+V ≤1.00 热处理|退火温度/℃: 890~910 屈服强度σ0.2/MPa: 230 抗拉强度σb/MPa: 450 伸长率δ5(%): 22 断面收缩率ψ(%): 23 5.外观检验 5.1 铸件形状外观 裸视目测。要求外观轮廓清,圆角尺寸正确且过渡平滑美观;可允许外观轮廓30%以下欠清晰,圆角过渡不够平滑。 5.2 铸件表面缺陷 在正常情况下铸件表面喷丸清理后进行检查,对照标准图谱裸视目测(取最坏部分面积100mm×60mm)。 5.2.1允许表面夹杂物(夹砂、夹渣等)缺陷5点以下,直径3mm深度≤1.5mm。 5.2.2允许表面气孔数少于8点,孔径≤φ1mm深度≤1mm。 5.2.3允许铸件表面有轻微皱皮。 5.2.4允许铸件表面有轻度冷隔(对火)。 5.2.5允许铸件表面龟纹大小、深度应控制在直径≤2mm,痕迹深度≤0.5mm。 5.2.6允许铸件表面轻度粘砂(可磨修)。 5.2.7允许铸件表面金属突出物:粘结线痕迹宽度≤1mm,高≤1mm,无针刺、结瘤。 5.2.8允许有高于铸件表面轻微的浇冒口切割痕迹。 5.2.9铸件表面缺陷允许轻度焊补,焊补面积≤20%。 5.3 铸件表面粗糙度 用80%以上的表面面积的粗糙度代表铸件的表面粗糙度,现场用比较样块进行对比评定,轮廓偏距绝对值的算术平均值Ra≤25μm。 5.4铸件挠曲,弯曲率见表1 5.5铸件尺寸偏差 用卡尺、卷尺或板尺测量,根据测量8件以上铸件的同一尺寸的最大偏差值对照表2确定。 5.6铸件重量偏差 用秤称量8个以上铸件重量,计算出重量平均值G0,铸件最大重量与最小重量的差值△G,计算出重量差的百分数K=△G/G0*100%,对照表3确定。 1.目的:规范钣金结构件的检验标准,以使各过程的产品质量得以控制。 2.适用范围: 本标准适用于各种钣金结构件的检验,图纸和技术文件同时使用。当有冲突时,以技术规范和客户要求为准。 3.引用标准: 本标准的尺寸未注单位皆为mm,未注公差按以下国标IT13级执行 GB/T1800.1-2009产品几何技术规范极限与配合第1部分:公差、偏差、和配合的基础 GB/T1800.2 -2009产品几何技术规范极限与配合第2部分:标准公差等级和孔、轴极限偏差表 GB/1804-2000 一般公差未注公差的线性和角度尺寸的公差 未注形位公差按GB/T1184 -1996 形状和位置公差未注公差值执行。 4。原材料检验标准 4.1金属材料: 4.1.1钣材厚度及质量应符合国标,采用钣材需出示性能测试报告及厂商证明。 4.1.2材料外观:平整无锈迹,无开裂与变形。 4.1.3 尺寸:按图纸或技术要求执行,本司未有的按现行国标执行。 4.2通用五金件、紧固件 4.2.1外观:表面无绣迹、无毛刺批锋,整批来料外观一致性良好。 4.2.2尺寸:按图纸与国标要求,重要尺寸零缺陷。 4.2.2性能:试装配与使用性能符合产品要求。 5、工序质量检验标准 5.1冲裁检验标准 5.1.1 对有可能造成伤害的尖角、棱边、粗糙要做去除毛刺处理。 5.1.2 图纸中未明确标明之尖角(除特别注明外)均为R1.0。 5.1.3 冲压加工所产生的毛刺,对于门板、面板等外露可见面应无明显凸起、凹陷、粗糙不平、划伤、锈蚀等缺陷。 5.1.4毛刺:冲裁后毛刺高L≤5%t(t为板厚)。 5.1.5 划伤、刀痕:以用手触摸不刮手为合格,应≤0.1mm。 5.1.6平面度公差要求见表一。 附表一、未注平面度公差要求 5.2 折弯检验标准 5.2.1 毛刺:折弯后挤出毛刺高L≤10%t(t为板厚)。 5.2.2 压印:看得到有折痕,但用手触摸感觉不到。(有特殊表面要求和镜面除外) 5.2.3 折弯变形标准按照《表二》及《表三》。 【附表二:对角线公差要求】 铁路工务技术比武题库,探伤组 铁路工务技术比武题库探伤组 钢轨探伤组题库(30题) 1、《钢轨探伤管理规则》第十一条对探伤人员资质有何要求? 要按照GB/T9445和《国家职业标准》的要求加强对探伤人员的技能培训、鉴定和考核。执机人员必须具有i级或以上级别的探伤人员技术资格;Ⅱ级探伤人员应不少于探伤人员总数的50%。 2、《钢轨探伤管理规则》第十二条对仪器检修人员有何要求? 仪器检修人员应具备Ⅱ级或以上级别的探伤人员技术资格,具有必要的电子技术知识和技能。对仪器检修人员应实行考评制度,不合格者不应担任检修工作。 3、《钢轨探伤管理规则》第三十二条钢轨探伤工作基本要求?1.探头配置和推行速度 ⑴探头配置:探头配置应能保证从钢轨踏面上扫查时,声束所能射及部位的危害性缺陷都能被有效探测。要加强对轨头(包括内侧、中部和外侧)和轨底横向裂纹(核伤)的探测。除使用70°探头的二次波外,可使用一次波探测轨头核伤。 ⑵推行速度:普通线路地段一般不大于2km/h;无缝线路地段一般不大于3km/h。 4.《钢轨探伤管理规则》第三十二条道岔部位探伤工作基本要求? ⑴.每年入冬前,应加强对正线道岔曲基本轨的探测。 ⑵.尖轨探伤时应注意仪器探测与手工检查相结合,仪器探测区域为轨面宽度大于50mm的部位。 ⑶.高锰钢整铸辙叉应采用手工检查,钢轨组合辙叉应采用仪器探测与手工检查相结合。 ⑷.要定期对可动心轨进行探伤检查。 5.《钢轨探伤管理规则》第三十二条重点处所钢轨探伤工作基本要求?在对接头、曲线、隧道、道口、桥梁等重点处所进行钢轨(焊缝)探伤时,要慢速推行,并注意观察波形显示,必要时要结合手工检查。 6.《钢轨探伤管理规则》第三十二条成段更换钢轨探伤工作基本要求?⑴.再用轨应先探伤、后上道。成段更换钢轨或再用轨,在线路验交时,必须进行探伤,并在三个月内加强检查和监视。 ⑵.新钢轨上道后()应及时进行探伤,发现伤损时,应及时上报技术(线路)科,并采取措施、加强防范、逐级上报。 7.《钢轨探伤管理规则》第三十三条探伤灵敏度作业校对标准?0°探头通道:反射法5mm水平裂纹当量; 穿透法136mm处φ6mm通孔或6dB底波降低。 37°(或35°至45°之间的其他角度,下同)探头通道:3mm螺孔裂纹当量。 70°探头通道:φ4mm平底孔当量。 8.《钢轨探伤管理规则》第三十六条焊缝探伤基本要求有哪些? 基本要求 铸钢件冒口的设计规范 钢水从液态冷却到常温的过程中,体积发生收缩。在液态和凝固状态下,钢水的体积收缩可导致铸件产生缩孔、缩松。冒口的作用就是补缩铸件,消除缩孔、缩松缺陷。另外,冒口还具有出气和集渣的作用。 1、冒口设计的原则和位置 1.1冒口设计的原则 1.1.1、冒口的凝固时间要大于或等于铸件(或铸件被补缩部分)的凝固时间。 1.1.2、冒口所提供的补缩液量应大于铸件(或铸件被补缩部分)的液态收缩、凝固收缩和型腔扩大量之和。 1.1.3、冒口和铸件需要补缩部分在整个补缩的过程中应存在通道。 1.1.4、冒口体内要有足够的补缩压力,使补缩金属液能够定向流动到补缩对象区域,以克服流动阻力,保证铸件在凝固的过程中一直处于正压状态,既补缩过程终止时,冒口中还有一定的残余金属液高度。 1.1.5、在放置冒口时,尽量不要增大铸件的接触热节。 1.2、冒口位置的设置 1.2.1、冒口一般应设置在铸件的最厚、最高部位。 1.2.2、冒口不可设置在阻碍收缩以及铸造应力集中的地方。 1.2.3、要尽量把冒口设置在铸件的加工面或容易清除的部位。 1.2.4、对于厚大件一般采用大冒口集中补缩,对于薄壁件一般采用小冒口分散补缩。 1.2.5、应根据铸件的技术要求、结构和使用情况,合理的设置冒口。 1.2.6、对于清理冒口困难的钢种,如高锰钢、耐热钢铸件的冒口,要少放或不放,非放不可的,也尽量采用易割冒口或缩脖型冒口。 2、设置冒口的步骤与方法 冒口的大小、位置及数量对于铸钢件的质量至关重要。对于大型铸钢件来说,必须把握技术标准及使用情况,充分了解设计意图,分清主次部位,集中解决关键部位的补缩。以模数法为例,冒口设计的步骤如下:2.1、对于大、中型铸钢件,分型面确定之后,首先要根据铸件的结构划分补缩范围,并计算铸件的模数(或铸件被补缩部分的模数)M铸。 2.2、根据铸件(或铸件被补缩部分)的模数M铸,确定冒口模数M冒。 2.3、计算铸件的体收缩ε。 2.4、确定冒口的具体形状和尺寸。 2.5、根据冒口的补缩距离,校核冒口的数量。 2.6、根据铸件结构,为了提高补缩距离,减少冒口的数量,或者使冒口的补缩通道畅通,综合设置内外冷铁及冒口增肉。 2.7、校核冒口的补缩能力,要求ε(V冒+V件)≤V冒η。 3、设计冒口尺寸的方法 3.1、模数法 在铸件的材料、铸型的性质和浇注条件确定之后,铸件的凝固时间决定于铸件的模数。 模数M=V/A(厘米),V—体积(厘米3);A—散热面积(厘米2)。 随着办公条件的改善,计算机的普及,模数可以用计算机进行计算。方法是:用SolidWorks软件画出铸件(或铸件被补缩部分)的立体图,计 钣金件检验规范 集团标准化工作小组 #Q8QGGQT-GX8G08Q8-GNQGJ8-MHHGN# Q/XW Q/XW JXXXXX-2012 钣金件检验规范 (征求意见稿) 2012-XX-XX 发布 2012-XX-XX实施 发布 Q/XW JXXXXX-2012 1. 目的 本标准旨在明确制造过程中对各种钣金件质量的描述、检验方法、判定标准、及对钣金件固有缺陷记录和使用标准,为制造过程、入库的质量检验提供依据。 2. 适用范围 本标准适用于本公司范围内生产的冲压件半成品和成品的检验。 3. 引用标准 GB/T 2828 逐批检查计效抽样程序及抽样表 GB/T 13914-2002 冲压件尺寸公差 GB/T 700-2006 碳素结构钢 GB/—1998 标准公差数值 GB/T1031—1995 表面粗糙度参数及其数值 GB/T 质量管理和质量保证术语 GB/T 13915-92 冲压件角度公差 JB/T 8930-1999 冲压工艺质量控制规范 JB/T 4129-1999 冲压件毛刺高度 GB/T 15055-2007 冲压件未注公差尺寸极限偏差 GB/T 8923-2009 涂覆涂料前钢材表面处理表面清洁度的目视评定 GB/T 708-2006 冷轧钢板和钢带的尺寸、外形、重量及允许偏差 4.术语定义 关键钣金件 对整车的结构、装配、生产工艺、使用性能、安全等方面有重要影响的钣金件将这一类钣金件作为过程质量的关键环节去加以控制,列为关键钣金件。 固有缺陷 针对前期产品开发过程中,因技术、工装及设计等原因导致的钣金件存在一些工艺上无法彻底整改的缺陷,制造过程对这些缺陷进行固化和稳定。 钣金件分类 根据钣金件在车身上功能尺寸等作用 分为:关键件和非关键件。 根据钣金件在车身上的位置不同及客户的可视程度 Q/XW JXXXXX-2012分为:A 、B 、C、D 四个区域。 根据钣金件上孔在车身装配及工艺要求 分为:一般孔、定位孔、装配孔。 分为:一般料边、压合料边、焊接料边。 钣金件在整车上分区定义 钣金件质量缺陷类型 文件编号:RHD-QB-K2443 (管理制度范本系列) 编辑:XXXXXX 查核:XXXXXX 时间:XXXXXX 钢轨探伤管理办法标准 版本 钢轨探伤管理办法标准版本 操作指导:该管理制度文件为日常单位或公司为保证的工作、生产能够安全稳定地有效运转而制定的,并由相关人员在办理业务或操作时必须遵循的程序或步骤。,其中条款可根据自己现实基础上调整,请仔细浏览后进行编辑与保存。 第一章总则 第1条为适应公司重载、大轴重运输的需要,针对大型探伤车上线后,新形势下加强钢轨探伤管理,防止钢轨折断,确保列车安全畅达,特制订本办法。 第2条钢轨探伤是防止断轨事故、确保行车安全的关键工作,具有流动性大、专业性强、技术要求高、操作复杂、安全责任重等特点,分公司各部门要从科学角度高度重视,保证探伤人员和队伍相对稳定。 探伤工作考核奖惩制度依据分公司《安全奖罚实 施细则》执行。例如发现重伤钢轨(包括辙叉、尖轨和夹板)奖。对探伤人员责任心不强、探伤速度快、探伤态度不良造成的责任漏检要实行责任考核追究。 第3条实行公司钢轨探伤车和分公司钢轨探伤仪两级探伤网络管理,实现钢轨探伤车和钢轨探伤仪之间资源共享、技术交流、优势互补、共同提高的目的。 第4条加强探伤作业过程监控和分析,对探伤仪记录的数据、波形做到当日分析,发现可疑波形按要求在规定时间内完成复核。 第5条分公司要加强对探伤工作领导并做好探伤工作的巡查,建立管理人员跟班作业制度,运输生产部主管人员每月不少于1天,工队长每月不少于7天,副队长、技术主管每月不少于15天时间跟班作业,对现场探伤工作情况进行巡查指导,并做好记 钢轨探伤组题库(30题) 1、《钢轨探伤管理规则》第十一条对探伤人员资质有何要求? 要按照GB/T9445和《国家职业标准》的要求加强对探伤人员的技能培训、鉴定和考核。执机人员必须具有I级或以上级别的探伤人员技术资格;Ⅱ级探伤人员应不少于探伤人员总数的50%。 2、《钢轨探伤管理规则》第十二条对仪器检修人员有何要求? 仪器检修人员应具备Ⅱ级或以上级别的探伤人员技术资格,具有必要的电子技术知识和技能。对仪器检修人员应实行考评制度,不合格者不应担任检修工作。 3、《钢轨探伤管理规则》第三十二条钢轨探伤工作基本要求? 1.探头配置和推行速度 ⑴探头配置:探头配置应能保证从钢轨踏面上扫查时,声束所能射及部位的危害性缺陷都能被有效探测。要加强对轨头(包括内侧、中部和外侧)和轨底横向裂纹(核伤)的探测。除使用70°探头的二次波外,可使用一次波探测轨头核伤。 ⑵推行速度:普通线路地段一般不大于2km/h;无缝线路地段一般不大于3km/h。 4.《钢轨探伤管理规则》第三十二条道岔部位探伤工作基本要求? ⑴.每年入冬前,应加强对正线道岔曲基本轨的探测。 ⑵.尖轨探伤时应注意仪器探测与手工检查相结合,仪器探测区域为轨面宽度大于50mm的部位。 ⑶.高锰钢整铸辙叉应采用手工检查,钢轨组合辙叉应采用仪器探测与手工检查相结合。 ⑷.要定期对可动心轨进行探伤检查。 5.《钢轨探伤管理规则》第三十二条重点处所钢轨探伤工作基本要求? 在对接头、曲线、隧道、道口、桥梁等重点处所进行钢轨(焊缝)探伤时,要慢速推行,并注意观察波形显示,必要时要结合手工检查。 6.《钢轨探伤管理规则》第三十二条成段更换钢轨探伤工作基本要求? ⑴.再用轨应先探伤、后上道。成段更换钢轨或再用轨,在线路验交时,必须进行探伤,并在三个月内加强检查和监视。 ⑵.新钢轨上道后应及时进行探伤,发现伤损时,应及时上报技术(线路)科,并采取措施、加强防范、逐级上报。 7.《钢轨探伤管理规则》第三十三条探伤灵敏度作业校对标准? 0°探头通道:反射法5mm水平裂纹当量; 穿透法136mm处φ6mm通孔或6dB底波降低。 37°(或35°至45°之间的其他角度,下同)探头通道:3mm螺孔裂纹当量。 70°探头通道:φ4mm平底孔当量。 8.《钢轨探伤管理规则》第三十六条焊缝探伤基本要求有哪些? ?中国钢企网 ?百科首页 ?登录 ?注册 ?帮助 ? ? ? ? ? ? ? ? 进入词条搜索词条 ? ? 全民共同撰写的百科全书已收录词条个 词条统计 ?浏览次数: 136 次 ?编辑次数: 1 次历史版本 ?更新时间: 2010-03-02 wwwwww 超级管理员 词条创建者发短消息中国钢铁百科 >> 钢铁冶金>> 连铸 最新历史版本 :铸钢件超声探伤及质量评级方法(摘要) GB 7233-87 返回词条?编辑时间:2010-03-02 10:37 历史版本编辑者:wwwwww历史版本: ?内容长度:208130 图片数:0目录数:0 ?修改原因: 铸钢件超声探伤及质量评级方法(摘要) GB 7233-87 本标准系铸钢件超声探伤的通用标准。 本标准规定了厚度等于或大于30mm的碳钢和低合金钢铸件的超声探伤方法;以及根据超声探伤的结果对铸件进行质量评级的方法。所用的超声探伤方法仅限于A型显示脉冲反射法。 在定货时,由供需双方商定铸钢件超声探伤的以下要求: a.检测的区域及使用的探头; b.纵波直探头探伤灵敏度; c.铸钢件质量的合格等级,允许对平面型缺陷和非平面型缺陷提出不同的质量等级要求。 本标准不适用于奥氏体不锈钢铸件的检测。 1术语 1.1平面型缺陷(Planar discontinuity):用本标准规定的方法检测一个缺陷,如果只能测出它的两维尺寸,则称为平面型缺陷。属于这种类型的缺陷有裂纹、冷隔、未熔合等。 1.2非平面型缺陷(Nonplanar discontinuity):用本标准规定的方法检测一个缺陷,如果能够测出它的三维尺寸,则称为非平面型缺陷。属于这种类型的缺陷有气孔、缩松、缩孔、夹砂、夹渣等。 1.3透声性(Permeability to ultrasound):超声纵波垂直入射到测试面与其背面平行的无缺陷的铸钢材料中,超声波在其中往返传播一次所引起的声压降。单位为分贝(dB)。 通常用纵波直探头测试的第二次与第一次底面回波幅度所差的分贝数表示。 2仪器、试块、耦合剂 2.1仪器仪器应符合ZBy230—84 Q/XW Q/XW JXXXXX-2012 钣金件检验规 (征求意见稿) 2012-XX-XX 发布 2012-XX-XX实施 发布 Q/XW JXXXXX-2012 1. 目的 本标准旨在明确制造过程中对各种钣金件质量的描述、检验方法、判定标准、及对钣 金件固有缺陷记录和使用标准,为制造过程、入库的质量检验提供依据。 2. 适用围 本标准适用于本公司围生产的冲压件半成品和成品的检验。 3. 引用标准 GB/T 2828 逐批检查计效抽样程序及抽样表 GB/T 13914-2002 冲压件尺寸公差 GB/T 700-2006 碳素结构钢 GB/T1800.3—1998 标准公差数值 GB/T1031—1995 表面粗糙度参数及其数值 GB/T 6583.1 质量管理和质量保证术语 GB/T 13915-92 冲压件角度公差 /T 8930-1999 冲压工艺质量控制规 /T 4129-1999 冲压件毛刺高度 GB/T 15055-2007 冲压件未注公差尺寸极限偏差 GB/T 8923-2009 涂覆涂料前钢材表面处理表面清洁度的目视评定 GB/T 708-2006 冷轧钢板和钢带的尺寸、外形、重量及允许偏差 4.术语定义 4.1 关键钣金件 对整车的结构、装配、生产工艺、使用性能、安全等方面有重要影响的钣金件 将这一类钣金件作为过程质量的关键环节去加以控制,列为关键钣金件。 4.2 固有缺陷 针对前期产品开发过程中,因技术、工装及设计等原因导致的钣金件存在一些工 艺上无法彻底整改的缺陷,制造过程对这些缺陷进行固化和稳定。 4.3 钣金件分类 4.3.1 根据钣金件在车身上功能尺寸等作用 分为:关键件和非关键件。 4.3.2 根据钣金件在车身上的位置不同及客户的可视程度 Q/XW JXXXXX-2012分为:A 、B 、C、D 四个区域。 4.3.3 根据钣金件上孔在车身装配及工艺要求 分为:一般孔、定位孔、装配孔。 4.3.4根据钣金件上料边在车身焊接、压合等工艺要求 分为:一般料边、压合料边、焊接料边。 4.4 钣金件在整车上分区定义 4.5 钣金件质量缺陷类型 4.5.1 外观缺陷 包括:裂纹、缩颈、坑包、变形、麻点、锈蚀、材料缺陷、起皱、毛刺、拉、压痕、划伤、圆角不顺、叠料、及其他。 4.5.2 功能尺寸缺陷 包括:孔偏、少边、少孔、孔径不符、多料、型面尺寸不符、其他。 4.5.3 返修缺陷 包括:裂纹、孔穴、固体夹杂、未溶合和未焊透、形状缺陷、变形、坑包、刨痕、抛光影、板件变薄、及其他。 4.6 检验类型 4.6.1 首件检验 Q/XW JXXXXX-2012在以下情况,对第一个(或几个)钣金零件的检验,称为首件检验。 a.变换品种; b.变换材料; c.修、换模后; d.机器(或设备)调整后; e.操作者接班后。 4.6.2 巡回检验铸钢件的制作方案
钣金检验通用标准
钢轨探伤管理规定.doc
铸钢件检验规范
铸钢件生产工艺要求及质量标准
钣金件检验标准
铸钢件超声探伤及质量评级方法
钣金件检验规范(修订版)
钢轨探伤管理规则
铸钢件超声波探伤中应注意的几个问题
消失模铸钢件检验标准[详]
钣金件检验规程
铁路工务技术比武题库,探伤组
铸钢件冒口的设计规范.
钣金件检验规范
钢轨探伤管理办法标准版本
铁路工务技术比武题库 探伤组汇总
铸钢件探伤标准解析
钣金件检验规范标准