零件检定承认作业程序
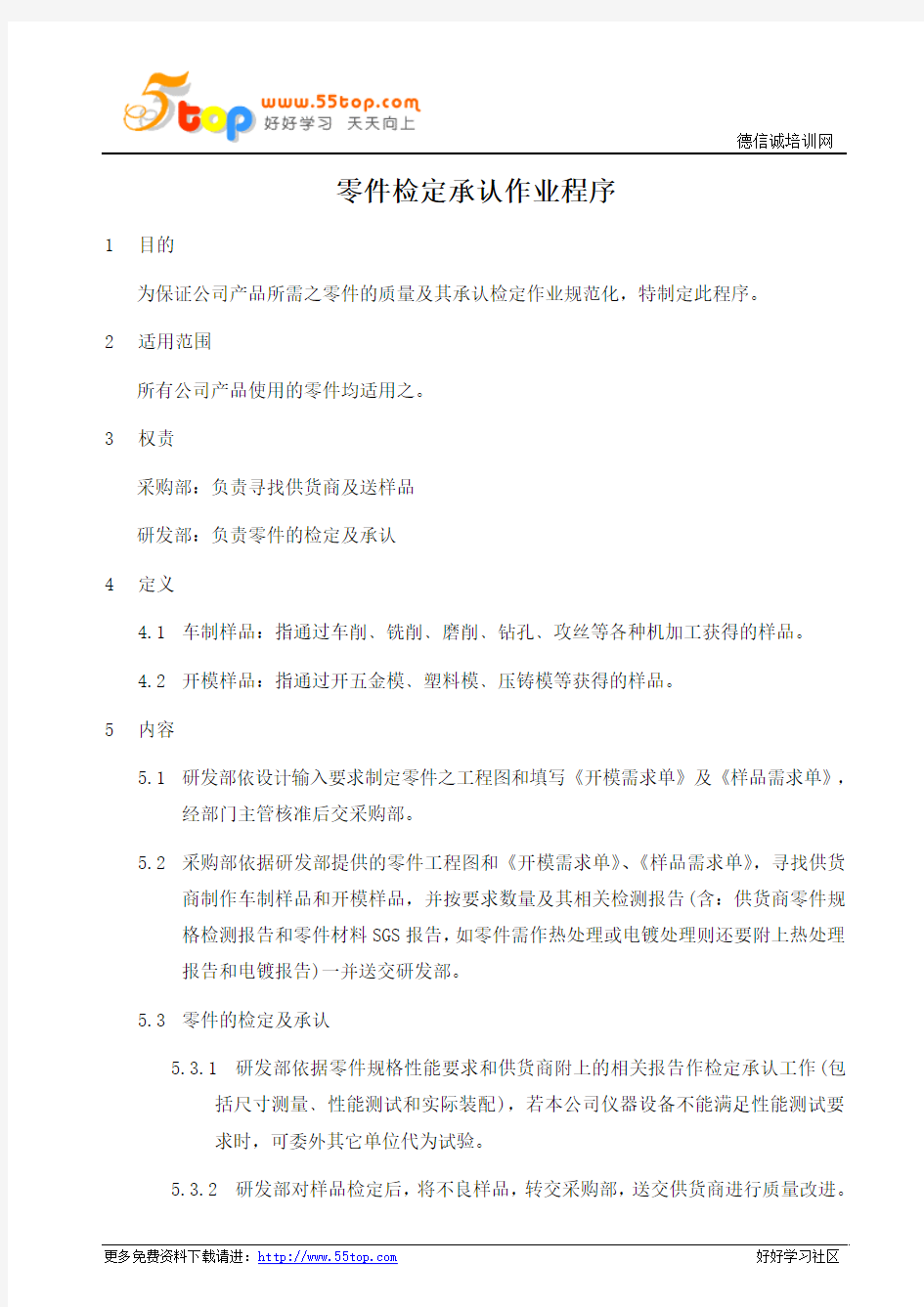
德信诚培训网
更多免费资料下载请进:https://www.360docs.net/doc/6a12965704.html, 好好学习社区 零件检定承认作业程序
1 目的
为保证公司产品所需之零件的质量及其承认检定作业规范化,特制定此程序。
2 适用范围
所有公司产品使用的零件均适用之。
3 权责
采购部:负责寻找供货商及送样品
研发部:负责零件的检定及承认
4 定义
4.1 车制样品:指通过车削﹑铣削﹑磨削﹑钻孔﹑攻丝等各种机加工获得的样品。
4.2 开模样品:指通过开五金模﹑塑料模﹑压铸模等获得的样品。
5 内容
5.1 研发部依设计输入要求制定零件之工程图和填写《开模需求单》及《样品需求单》,
经部门主管核准后交采购部。
5.2 采购部依据研发部提供的零件工程图和《开模需求单》、《样品需求单》,寻找供货
商制作车制样品和开模样品,并按要求数量及其相关检测报告(含:供货商零件规格检测报告和零件材料SGS 报告,如零件需作热处理或电镀处理则还要附上热处理报告和电镀报告)一并送交研发部。
5.3 零件的检定及承认
5.3.1 研发部依据零件规格性能要求和供货商附上的相关报告作检定承认工作(包
括尺寸测量﹑性能测试和实际装配),若本公司仪器设备不能满足性能测试要
求时,可委外其它单位代为试验。
5.3.2 研发部对样品检定后,将不良样品,转交采购部,送交供货商进行质量改进。
产品可靠性测试操作步骤
产品可靠性测试操作规范 为保证产品在各种使用过程、在不同的使用环境、受到不同的环境影响而确保其能正常工作,保证其在较长时间内无故障工作,同时也满足客户的要求。现要求按以下步骤进行可靠性测试,并将测试结果以《可靠性测试报表》的形式体现。 本试验由品质部进行,产品部协助。 一、来料阶段须进行的可靠性测试项目: 1.附着力测试 目的:提供产品表面涂层(喷油、丝印、移印、电镀)粘附强度及试验标准 适用范围:所有含表面涂层的产品 样品数量:3PCS 试验条件:界刀、3M810胶纸 试验程序:A.用界刀在表面涂层划相距1/16英寸11条平行直线,再划11条与其垂直的平行线(每一条应深至油漆的底层) B.用胶带贴于上面,并用手指压平,保证充分接触90+-30秒,然后以45度角往反方向均匀 迅速拉起 C.同一位置执行上述操作10次 D.测试完毕后检查,涂层脱落面积应小于规定范围 E.将测试结果记录于《可靠性测试报表》 2.耐磨性测试 目的:提供产品表面涂层的耐磨擦性能及试验标准 适用范围:所有含表面涂层的产品 样品数量:3PCS 试验条件:专用橡皮、负载 试验程序:A.用专用的日本砂质橡皮(橡皮型号:LER902K),施加500g的载荷,以40至60次每分钟的速度,以20mm左右的行程,在样品表面来回磨擦100个循环 B.测试完毕后检查,产品表面涂层应不露底 C.将测试结果记录于《可靠性测试报表》 3.耐醇性测试
目的:提供产品表面涂层的耐磨性及抵抗酒精性能及试验标准 适用范围;所有含表面涂层的产品 样品数量:3PCS 试验条件:纯棉布、酒精浓度>99%的酒精、砝码 试验程序:A.用纯棉布蘸满无水酒精,包在专用的500g砝码头上(包上棉布后的砝码测试头面积约为1CM 平方),以40至60次每分钟的速度,20mm左右的行程,在样品表面来回擦试100次 B.测试完毕后检查,产品表面涂层应不露底 C.将测试结果记录于《可靠性测试报表》 4.硬度测试 目的:提供产品表面涂层在正常使用、贮存或运输过程中抵抗外界物品刮伤的试验标准 适用范围:适用于含表面涂层的产品 样品数量:3PCS 试验条件:专用三菱牌2H铅笔、硬度测试仪 试验程序:A. 用2H铅笔(三菱牌),将笔芯削成圆柱形并在400目砂纸上磨平后,装在专用的铅笔硬度测试仪上( 施加在笔尖上的载荷为1Kg,铅笔与水平面的夹角为45°),推动铅笔向 前滑动约5mm长,共划5条,再用橡皮擦将铅笔痕擦拭干净。 B.测试完毕后检查,应无划痕 C.将测试结果记录于《可靠性测试报表》 二、半成品阶段须进行的可靠性测试项目: 老化寿命测试: 目的:提供产品在正常使用过程中的稳定性能及试验标准 适用范围:半成品 样品数量:20PCS以上 试验条件:常温常湿条件下,连续工作48小时 试验程序:A.于测试前先对产品的外观、功能进行检查并记录 B-1.音乐播放测试: B-1-1. 选取5台进行音乐播放:将样品在开机正常工作状态下,且音量调最大带负载情况下 连续工作48小时
零件承认管理办法
1 目的 规范公司新材料、新供应商导入,确定零件申请、承认及使用的作业流程,以保障后期量产物料品质和交货顺畅。 2 适用范围 新零件、新供应商的零件承认。 3 参考文件 3.1 《供应商管理作业程序》 3.2 《采购管理作业控制程序》 3.3 《项目管理作业程序》 4 术语及定义 First source:第一资源开发承认,简称首供 Second source:第二资源开发承认,简称二供 5 职责 4.1 研发:负责First source首次材料承认验证设计要求及设计意图的符合性,部分零件的电气性能的确认。 4.2工程:负责主导验证确认材料在生产中的量产制造可行性。 4.3品控:负责依据图纸和相关规范的要求对零件进行检验以及供应商报告的审核确认。 4.4 项目:负责主导量产前零件承认规格问题的确认工作,下达零件承认启动指令。 4.5 采购:负责主导零件承认,启动Second source第二供应商零件承认。 6程序说明 6.1 First source零件承认 6.1.1项目在与客户确认新项目送样经客户认可封样后,PM通知采购启动零件承认作业。(一般在第二次试产前) 6.1.2采购接到通知后,依据《零件承认资料表》要求,通知供应商提供零件承认书样品和资料,资料必须涵盖下列内容: 材质证明、Rohs、尺寸测试报告、包装规范等基础资料(需一式三份)。供应商提供的样品与测试报告需编号一一对 应(及测试样品编号与记录一致)。 6.1.3供应商依要求提供《零件承认书》及样品交给采购窗口,由采购窗口确认资本资料是否齐全,不全则要求供应 商立即补全;齐全则转交给SQE工程师。(如果供应商受限测试设备能力,可通过委外或事先委托我司进行) 6.1.4SQE依《零件承认资料表》要求,确认报告是否齐全,测试报告内容是否真实一致,以及安排对应的可靠性测试 6.1.5所有相关测试完成,SQE进行汇总确认。将审核意见注明在《零件承认书》转交技术工程确认 6.1.6技术工程人员接到承认书后,对承认样品及报告进行审核,并与前期打样阶段样品进行比对。确认尺寸、结构、 装配、治具配合、测试验证。必要时将报告附在承认书后。转交设计研发。 6.1.7研发部接到《零件承认书》后,根据图纸、品控、工程报告确认样品材质要求、结构性能是否满足原定设计要求。 6.1.8各流程部门确认会签OK后,转交到文控受控发行(一份采购、一份IQC、一份文控留底) 6.1.9采购收到零件承认封样后,封样样品移交给供应商后,才可以正式下订单给供应商,供应商依据封样样品以及确认 的检验标准生产出货 6.2 Second source零件承认 6.2.1采购根据销售订单及采购风险,提出二供供应商,由采购自行决定启动零件承认。 6.2.2启动零件承认后,依据6.1.2到6.1.8执行(Second source 跳过第6.1.7 ) 6.3 零件测试结果与设计规格不符,无法完成承认作业时,由项目召集RD/SQE/工程确认零件规格,评估供应商能力及风险
样品试作管理办法
一. 目的 保证提供给客户的样品通过规定的检验及试验,符合客户的要求。 二. 范围 样品试作留样与技术数据管理. 三. 权责 3.1 销售:负责将客户需求、客供资料提供给技术部项目组,出现异常时与客户的沟通 3.2 技术:负责对样品的制作主导、评估、异常处理、技术变更及承认书的制作 3.2.1项目组:负责将客户资料及品质要求转换成内部检验标准给至试制组 3.2.2试制组:负责根据项目提供的客户标准试制符合客户需求的成品 3.3 采购:负责新产品的物料购买及物料相关资料的收集 3.3 制造:负责协助制作样品 3.4 质量:负责对样品的出货检验 3.5 文管:负责对文件的发行、管控及存档 四. 定义项 4.1产品样品:产品的标准样件,为生产时的检查标准 4.2物料样品:原材料的标准样件,为原料验收的检验标准。 4.3规格品:以往生产过的产品 4.4非规格品:指新产品 五.作业内容 5.1产品样品 5.1.1下申请单 销售接获客户索样需求时, 销售根据相关样品需求项填写《样品申请单》,经部门主管核准. 5.1.2可行性评估 销售将《样品申请单》和客供资料一起交技术部项目组,由项目组判定样品制作的可行性,初步就判定不可行的项目,项目则将申请单退回销售,并说明原因。 5.1.3现状审查 5.1.3.1签定样品属规格品、非规格品。规格品库存有时,则依《出货控制程序》领出;质量人
员依《产品监视与测量控制程序》检验合格后送交客户。 5.1.3.2非规格及规格品库存无时,按下述流程作业。 5.1.3.3签定有无模具及所需材料。模具若无,则依《工装管理办法》要求采购。 5.1.3.4所需材料若无,技术部项目组则需负责申请,由采购依《采购管理控制程序》执行采购 作业。 5.1.4转换图纸及客户图面存档 5.1.4.1技术部项目组审查客户图纸,如是常规图面则直接转换成我司图面。图面有异常时, 反馈给销售,由销售联系客户。有需要时技术部项目组可直接与客户技术沟通。 5.1.4.2硅橡胶产品图面编号原则:直接根据客户图纸之编号。 5.1.4.3模切图面编号之定义: 客户序号版本号 友隆编号部件编号 (二三项为001-999;四项为01-99) 5.2.4.3技术部项目组将客户图面写上我司的图号,然后按图号顺序整理存档 5.1.5物料申购,技术部项目组根据试制数量申购物料请购。技术试制人员填写《领料单》向仓库 领取所需材料. 5.1.6样品制作 5.1. 6.1由技术部项目组收集客户资料及质量标准后交至是指技术部技术改善组,技术改善组 根据客户标准主导样品的制作,生产协助执行打样。打样完成由项目组对试制组做出的 样品进行确认及签核。打样过程中的异常状况由技术改善组主导解决,若技改组经过改 善仍无法改善则由项目组连同营销部重新和客户确认质量标准。 5.1.7 样品的确认 5.1.7.1技术改善组试制人员做好样品,根据项目组提供客户品质标准自检合格后,交由试制 鉴定人员再次对产品进行加工和外观鉴定若是在试制过程中遇到客户标准中没有涉及到的的异常状况试制人员需立即反馈至项目处,由项目负责人对其进行最终的判定,确认OK后,贴上样品标签,送至量测室对样品进行全尺寸的量测,若尺寸NG,则将产品直接退至试制人员,若尺寸量测
可靠性测试规范
手机可靠性测试规范 1. 目的 此可靠性测试检验规范的目的是尽可能地挖掘由设计,制造或机构部件所引发的机构部分潜在性问题,在正式生产之前寻找改善方法并解决上述问题点,为正式生产在产品质量上做必要的报证。 2. 范围 本规范仅适用于CECT通信科技有限责任公司手机电气特性测试。 3. 定义 UUT (Unit Under Test) 被测试手机 EVT (Engineering Verification Test) 工程验证测试 DVT (Design Verification Test) 设计验证测试 PVT (Product Verification Test) 生产验证测试 4. 引用文件 GB/T2423.17-2001 盐雾测试方法 GB/T 2423.1-2001 电工电子产品环境试验(试验Ab:低温) GB/T 2423.2-1995 电工电子产品环境试验(试验Bb:高温) GB/T 2423.3-1993 电工电子产品环境试验(试验Ca:恒定湿热) GB/T 2423.8-1995 电工电子产品环境试验(自由跌落) GB/T 2423.11-1997 电工电子产品环境试验(试验Fd: 宽频带随机振动) GB 3873-83 通信设备产品包装通用技术条件 《手机成品检验标准》XXX公司作业指导书 5. 测试样品需求数 总的样品需求为12pcs。 6. 测试项目及要求 6.1 初始化测试 在实验前都首先需要进行初始化测试,以保证UUT没有存在外观上的不良。如果碰到功能上的不良则需要先记录然后开始试验。在实验后也要进行初始化测试,检验经过实验是否造成不良。具体测试请参见《手机成品检验标准》。 6.2 机械应力测试 6.2.1 正弦振动测试 测试样品: 2 台
材料零部件控制程序
1.目的 根据《特种设备制造、安装、改造、维修质量保证体系基本要求》、公司《压力管道安装、改造、维修质量保证手册》的要求,建立材料、零部件质量控制系统,通过对材料、零部件的采购、验收、标识、存放与保管、领用和使用、材料代用等环节的管理和控制,以确压力管道安装、改造、维修用的材料、零部件的质量和正确使用。 2.适用范围 适用于公司压力管道安装、改造、维修工程所用材料、零部件的全过程控制。 3. 职责 3.1 工程技术部 a).工程室 ①.物资采购组:负责收集合格分供方的评审的输入资料和材料、零部件的采购。 ②.库房:负责材料、零部件的标识、保管、发放和回收。 b).技术室:负责编制订货技术条件和参与合格分供方评审,并对分供方的技术能力提 出合理意见。 c).项目组:负责材料、零部件的使用和参与合格分供方评审,并对分供方的综合服务 能力提出合理意见。 3.2 质量安全部 a).质量室:参与合格分供方评审,并对分供方的质量保证能力提出合理意见。
b).检验试验组:负责材料、零部件的验收。 3.3 运营管理部 财务室:参与合格分供方评审,并对分供方的经济保证能力提出合理意见。 4. 程序 4.1 合格分供方评价 4.1.1 评价范围 为公司压力管道安装、改造、维修工程提供设备、材料、零部件的所有制造商、生产商、贸易商和外协加工商。 4.1.2评价类型 合格分供方评价分为准入评价和重新评价两种类型。 4.1.3 准入评价 4.1.3.1准入评价时机 a).材料、零部件分供方拟为公司供货前。 b).拟在合格分供方名录外分供方采购时。 4.1.3.2 准入评价内容 a).分供方合法性评价 ①.分供方必须是依法成立的企业、个体工商户或其他组织。
样品承认流程
样品承认流程 WI-DD-003 文件编号 样品承认流程 页号第1页共2页 1、目的 通过实施样品承认程序,确保样品的质量,并作为采购订货及进料检验的依 据。 2、范围 适用于本公司所有样品承认。 3、职责 3.1采购部负责提供样品及相关资料; 3.2研发部对样品的功能及性能进行首次承认和样品封样及样品分发。 4、程 序 4.1引入新的元器件、更换生产厂家、材质变更时必须对该物料进行承认; 4.2 样品承认联络单的发出 采购部发出《内部工作联络单》,准确注明待承认物料的名称,规格型号、数量、供应商名称、使用机型、希望完成时间等,此单由采购部经理批准后连同样品、供应商提供的样品承认书、相关资料,提交研发部,并在<样品承认一览表>上予以注明;研发部自行获取的样品,经确认合格后,应填写《内部工作联络单》 4.3样品承认 4.3.1专用物料,由研发部按照设计部门的技术标准及相关设计资料,对其测 试和承认,交部门经理批准,承认完毕后,样品须提交原设计部门审核,厂长批准; 4.3.2一般物料,由研发部按照技术标准及相关资料,对其进行测试和承认,交部 门审核批准,最终提交厂长批准;
4.3.3如有需要,研发部可提出申请交品管部测试、承认,但需提供相关资料交品管部作为承认依据;《内部工作联络单》经设计部门签署意见后由厂长批准后方可生效; 4.3.4分送部门 对承认合格之《内部工作联络单》由物料承认部门制作三份:一份由研发部存档;一份由质量部IQC存档,作来料检验之依据;一份由采购部留存并可复印转供应商作为生产依据。 4.4封样与分发 4.4.1样品承认完成后,研发部门进行样品封样,并将封样样品及承认资料分发给采购部、品管部IQC,并自行存档,同时,由研发部在<样品承认一览表>上,作好签收记录; WI-DD-003 文件编号 样品承认流程 页号第2页共2页 4.4.2对新物料做完样品承认后,研发部应对未做编码的物料进行编码; 4.5时间要求 样品承认原则上在3日内应给出承认结果;若属急单,要求在规定时间内完成;对于需要做较多实验的特殊元器件,时间可放宽至5天,对于新产品开发用的新物料,可由研发部自行确认,但必须在完成开发设计之后的小批量试产前完成。 4.6对于系列的通用元器件,根据实际情况,对该系列部份品种承认合格后,承认部门可在《内部工作联络单》上提出申请,经厂长批示后可作为整个系列已承认合格之依据。 4.7质量稳定且对产品品质影响较小的常规元器件承认合格,不用小批量试产,可大批量使用。 4.8由设计部门同意的风险采购订单成批量订购到货后,仍需采购部先发出<样品承认联络单>,按此作业流程操作,然后IQC才对批量订购货品进行来料检验。
可靠性测试规范之盐雾试验作业指导书
核准: 审核: 作成:袁媛 盐雾试验作业指导书 版 本 B0 制订部门 品质部 页次 1/7 生效日期 2020.05.11 1. 0目的 指导作业,规范操作,提升试验结果的客观性及可信赖性。 2. 0范围: 所有需要盐雾测试的产品。 3. 0定义: 盐雾试验:利用盐水喷雾腐蚀来检验和鉴定电镀层封孔性之好坏,以及对镀层耐腐蚀性和对基 体保护性能的测试;或试样无表面处理时本身耐腐蚀的能力。 4. 0权责 品管部负责取样、测试、判定。 5.0设备、药品及操作条件 5.1盐水喷雾试验机 5.2氯化钠(分析纯)溶液(5%)、溶液使用纯水配制,紧急时可使用纯净水替代。 5.3操作条件 项 目 试 验 中 备 注 盐水质量百分比浓度(%) 5±0.1 盐水不得重复使用 盐水PH 值 6.5-7.2 测定收集的盐雾溶液 压缩空气压力(kgf/cm 2) 1.00±0.1 经过现场校验和认证 喷雾量(ml/80cm 2/hr) 1.5+0.5 连续不得中断,至少8H 以上 压力桶温度 47±20C 试验室温度和湿度 35±20C,90% RH 以上 样品放置角度 15°-25° 附角度参照图 试验时间(hr) 参考本文件7.0条款 6.0 试验 6.1试样准备: 在试样准备以及试验结束取样观察全过程中,不可裸手接触试样,应全程戴一次性手套或 手指套,以保护试件电镀面不被汗渍及其它外来物污染。在用手套或手指套防护下,将镍片用双面胶粘在治具上,单个产品间距不少于20mm 。 6.2试样摆放: (1)试样不应摆放在盐雾直接喷射到的位置。
核准: 审核: 作成:袁媛 盐雾试验作业指导书 版 本 B0 制订部门 品质部 页次 2/7 生效日期 2020.05.11 (2)在盐雾试验箱中被试面与垂直方向成15°~ 25°,并尽可能成20°,对于不规则的试样, 例如整个工件都是被试面,也应尽可能接近上述规定。 -带材测试:带材对折30°~50°之间,垂直放置在盐雾箱内。 20° 40° -镍片测试:借助辅助治具,确保试样被试面与垂直方向成15°~ 25° (3)试样可以摆放在试验箱不同水平面上,但不能接触箱体,也不能相互接触,单个试 样件间距不得小于20mm 。试样或其支架上的滴液不得落在其他试样上。 6.3 试验后试样的处理: (1)试验结束后取出试样,用温度不高于40℃的清洁流动水轻轻清洗以除去试样表面残留 的盐雾溶液,接着在距离试样约300mm 处用气压不超过300kPa 的空气立即吹干.或者 清洗后用无尘布轻轻吸干试件表面水份. 电镀面 错误摆放方式试件表面水渍印 试件不可纵向放 置上下间会滴液 L 型电镀面 电镀面
材料承认程序
材料承认程序 (QC080000-2017) 1.0目的: 通过适切的样品承认作业,确保供应原材料、零组件等其品质特性能符合规格使用要求。 2.0范围: 2.1本程序适用于新规格的物料或者旧规格新供应商提供的物料的承认。 2.2所有生产用原材料、零组件等,采购部在发出采购订单前,均须经由本程序认可。 3.0定义:无。 4.0职责: 4.1开发部(含模块开发):负责主导材料的承认过程及材料是否可用的判定。 4.2品管部、工艺部、生产部:负责协助材料承认过程的测试及实验。 4.3 采购部:负责依申请单位需求提供原材料、零组件等样品,经开发部承认合格后作为采购必要条件。 4.4 文控中心:负责材料承认书及承认样品的保管及发行。 5.0内容: 5.1物料样品品质承认流程:
5.2物料样品品质承认内容: 5.2.1索样: A.开发第二供应商或者新供应商时,由采购直接跟供应商索取样品交开发部承认。 B.新产品或者工程变更的样品需求,由开发部填写[请购单]经部门主管审核,交采购部索取样品以供承认。(注:1、样品需求如果是免费直接由需求部门主管审核;2、样品涉及到费用,由需求部门呈分管副总批准)。 C.索取样品的数量必须满足试验及留样的要求,留样的要求如下: a.共3个,开发部:1个(留存)、采购部:1个(发送供应商)、IQC:1个(进料检验验证需要) 5.2.2送样: 供应商送样时,需附上该产品的承认书(含规格、图纸、ROHS测试报告、全尺寸或全功能测试报告),承认书内容不齐全,开发部应拒绝承认。 5.2.3验证: A.开发部收到样品后,应针对客户的要求或者材料的主要特质特性进行相关验证(测试和可靠性试验),以确认是否满足规格要求后,填写[样品验证记录],并在承认书上注明是否合格,经开发部经理(或授权人)审批后生效。 5.2.4样品不合格:
软件测试作业及答案
第一章 1.选择题 (1)软件本身的特点和目前软件开发模式使隐蔽在软件内部的质量缺陷不可能完全避免,在下列关于导致软件质量缺陷的原因的描述中,不正确的是(C) A.软件需求模糊以及需求的变更,从根本上影响着软件产品的质量 B.目前广为采用的手工开发方式难以避免出现差错 C.程序员编码水平低下是导致软件缺陷的最主要原因 D.软件测试技术具有缺陷 (2)缺陷产生的原因是(D) A.交流不充分及沟通不畅、软件需求的变更、软件开发工具的缺陷 B.软件的复杂性、软件项目的时间压力 C.程序开发人员的错误、软件项目文档的缺乏 D.以上都是 2.判断题 (1)缺乏有力的方法学指导和有效的开发工具的支持,往往是产生软件危机的原因之一。(√) (2)目前的绝大多数软件都不适和于快速原型技术。(√) (3)在程序运行之前没法评估其质量。(×) (4)下列哪些活动是项目 探索火星生命迹象(√) 向部门经理进行月工作汇报(×) 开发新版本的操作系统。(√) 每天的卫生保洁。(×) 组织超级女声决赛。(√) 一次集体婚礼。(√) 3.简答题 (1)什么是软件软件经历了哪几个发展阶段 答:软件是一系列按照特定顺序组织的计算机数据和指令的集合。一般来讲软件北划分为系统软件,应用软件和介于着两者之间的中间件。其中系统软件为计算机使用提供最基本的功能,但是并不是针对某一特定领域,而应用软件则恰好相反,不同的应用软件更根据用户和所服务的领域提供不同的功能。 20世纪50年代初期至60年代中期是软件发展的第一阶段(又称程序设计阶段); 第二阶段从20世纪60年代中期到70年代末期是程序系统阶段。 第三阶段称为软件工程阶段,从20世纪70年代中期到80年代中期,由于微处理器的出现,分布式系统广泛应用,以软件的产品化,系列化,工程化和标准化为特征的软件产业发展起来,软件开发有了可以遵循的软件工程化的设计原则,方法和标准。 第四阶段是从20世纪80年代中期至今,客户端/度武器(C/S)体系结构,特别是Web技术和网络分布式对象技术法飞速发展,导致软件体系结构向更加
电热膜可靠性试验作业指导书
电热膜可靠性试验作业指导书 修订日期修订 单号 修订内容摘要页次版次修订审核批准 2011/03/30 / 系统文件新制定 4 A/0 / / / 批准:审核:编制:
电热膜可靠性试验作业指导书 序号检验项目技术要求检验方法 1 功率试验开始时记录好功率,测试完成后与开始 功率对比。不能超出+5/-10的标准。 功率测试仪 2 绝缘强度耐压连接线线芯表面镀锡,剥线时切口整齐。芯 线于金属膜之间施加交流电1500V,5mA, 50HZ,历时3S不击穿。 用耐压测试仪测试 2 浸水耐压测试将发热组件一半浸入水中,铆接处露出水 面,用交流1500V,50HZ,整定电流5mA, 历时3S不击穿。 用耐压测试仪测试 3 泄漏电流 1.06倍额定电压下,其泄漏电流≤0.25mA。用泄漏电流测试仪测试 4 铆接力端子与连线铆接牢固,30N拉力1min不得 松动。 用推拉力计测试 5 可靠性试验装机额定电压下长期工作,正常使用寿命不 低于3000小时。 按规定要求通电测试 备注: 1在产品的额定电压通电前按上述的检验方法检查,在3000小时运转后再按上述方法检查。 2产品可靠试验基本上按上述顺序进行,如果某些试验项的结果与进行该项试验的先后顺序无关,试验顺序可以变动; 3试验应在无强制对流空气且环境温度为20℃±45℃的场所进行; 4首样检验、试制新产品、产品在设计、工艺、材料有重大改变时,上述每项都必须检验。 其余则可以根据客户或送检部门要求检验其中一项、几项或全部项目; 5可靠性试验时如有任一试验条款中任一试品不合格,则判该批为不合格,要求改进后重新送样,并对不合格项目进行复试; 6可靠性试的样本数量不少于10只; 7本作业指导书引用标准有(标准如有修订或换版则以最新版为准), 试验中不完善的项
可靠性试验程序
可靠性试验程序 1.目的 1.1 运用可靠性试验,以验证本公司产品,是否符合预期质量要求。 1.2 找出潜在的质量问题,作为改善产品及制程的依据。 2.范围 2.1 新开发的产品,在DVT或DMT或PR阶段时,执行可靠性试验; 2.2 已量产的产品,其零组件或制程有变更时,视情况需要,执行可靠性试验; 2.3 量产阶段的产品,执行可靠性试验。 3.定义 3.1 DVT:设计确认试验。(Desing Verilication Test); 3.2 DMT:设计完成试验。(Desing Maturity Test); 3.3 PR:量试,即新产品开发完成后的大量生产(Pilot Run) 3.4 MP:大量生产,即产品量试完成后的大量生产(Mass Production)。4.权责 4.1 品管部负责可靠性试验执行单位; 4.2 维修单位负责对不合格的修理,品管部作初步分析,再依4.3纠正措施进行。 4.3 纠正措施:设计问题由研发部负责; 制程问题由生技部负责;作业问题由制造部负责。 5.流程图
6.内容及要求 6.1成品取样: 6.1.1 全新产品,于DVT或DMT或PR阶段时,依DVT/DMT测试规范执行可靠性试验。 6.1.2 已量产的产品,其零组件或制程有变更时,依“产品可靠性试验项目”,由品管部决定应执行的可靠性试验项目; 6.1.3 量产阶段的产品(OQC检验的合格品),质量工程课应于每年年初拟定“年度量产产品可靠度测试计划”,按产品分类取样。每六个月随机抽验执行环境试验,每九个月执行寿命试验。 6.2可靠性试验内容: 6.2.1 可靠性试验一般在公司内执行,若公司能力不足时,则送外试验,必须说明试验名称、负责人员,试验起始时间及异常状况联络人。 6.2.2 可靠性试验执行项目:参照“产品可靠性试验项目” 6.2.3 试验完后,质量工程课人员对所得的相关资料和产品本身进行查验,判断是否符合公司规格或客户要求,并由主管审核后发出可靠性试验结果报告。6.3纠正措施: 6.3.1 可靠性试验结果不合格时,由质量工程课发出可靠性试验纠正措施单,并由研发相关单位或生技部,填写发生原因与纠正措施; 6.3.2 经纠正措施改善后的产品,应重复执行原失败的可靠性试验项目,直到合格为止。 6.4合格的处理: 6.4.1 试验合格的产品,由质量工程课人员,依入库程序,办理入库; 6.4.2 质量工程课须发出有质量工程课主管审核的可靠性试验结果报告至相关单位。 7.相关文件(无) 8.应用表单 8.1可靠性试验结果报告(QRP041-01) 8.2可靠性试验纠正措施单(QRP041-02) 8.3年度量产产品可靠性测试项目(QRP041-03)
建筑可靠性鉴定检测作业指导书
建筑可靠性鉴定检测作业指导书文件编号: 版本号: 分发号: 编制: 批准: 生效日期:
建筑可靠性鉴定检测作业指导书 1.检测范围 1.1 厂房、仓库、综合楼及其他生产建(构)筑物。 1.2 住宅楼、办公楼、宾馆、酒店等民用建筑物。 2.检测依据 2.1有关标准和规程 2.1.1《民用建筑可靠性鉴定标准》GB/T 50292-1999; 2.1.2《工业建筑可靠性鉴定标准》GB 50144-2008; 2.1.3《危险房屋鉴定标准》JGJ 125-1999(2004年版); 2.1.4《建筑抗震鉴定标准》GB 50023-2009; 2.1.5《火灾后建筑结构鉴定标准》CECS 252:2009; 2.1.6《建筑结构检测技术标准》GB/T 50344-2004; 2.1.7《回弹法检测砼抗压强度技术规程》JGJ/T 23-2011; 2.1.8《钻芯法检测混凝土强度技术规程》CECS 03:2007; 2.1.9《混凝土结构工程施工质量验收规范》GB 50204-2015; 2.1.10《工程测量规范》GB 50026-2007; 2.1.11《建筑变形测量规程》JGJ/T8-2007; 2.1.12《砌体工程现场验收检测技术标准》GB/T 50315-2011; 2.1.13《钢结构工程施工质量验收规范》GB 50205-2001; 2.1.14《超声回弹综合法检测砼强度技术规范》CECS 02:2005; 2.1.15《建筑地基基础设计规范》GB50007-2011; 2.1.16 现行有关规程、规范。 2.2 各变电站建(构)筑物竣工验收资料。 2.3 各变电站历年加固、改造及维修记录。 3.检测鉴定实施程序 检测步骤为:初步调查——确定检测鉴定目的、范围和内容——详细调查——补充调查(必要时)——各项检测鉴定结果评定——检测鉴定报告。 4.检测内容 4.1初步调查:(全部) 4.1.1 收集图纸资料;调查建筑物使用历史。 4.1.2 建(构)筑物实物与现有资料进行初步核对;调查建筑物实际使用条件和内外环
物料承认控制程序
物料承认控制程序 1.目的 通过物料承认作业,确保公司生产使用物料、部品符合规定要求。 2.适用范围 公司物料(包括自制和外购)及来料不良物料之承认作业. 3.定义 3.1新物料:产品开发或工程变更时产生的新物料、新供应商/外协商的物洋及供应商生产场地或工艺变更后的物料。 4.职责 4.1采购、PMC及生产等部门负责提供需承认之物料样品及资料。 4.2开发、市场等部门负责物料承认作业。 4.3生产、品管部门必要时协助物料承认活动。 5.流程图 6作业流程 6.1物料承认时机
6.1.1公司生产所需部品、物料在以下情况下,必须经开发部测试验证合格后,方可予以后续作业。 ①新产品开发或工程变更阶段出现新增物料时; ②量产阶段因品质、价格或交期等原因需找新供应商/外协商,或原认可供应商/外协商生产技术场地发生重大变更时; ③来料不良而生产急需使用时。 6.1.2客户对产品包装有指定要求时,所有包装物料(如彩盒、标签等)必须由市场交客户认可后方可批量采购。 6.2样品需求 6.2.1新增物料如属外购时,则由开发、市场等部门提供图纸、规格等资料,并注明样品数量及时间交采购部寻找供应商送样承认。 6.2.2如为开发新供应商/外购商时,则由采购部或PMC部要求合适供应商/外协商送样承认. 6.2.3如属自制零部件(含模具外加工但本公司生产),由开发部提供图纸规格,并注明需求样品数量及时间交生产部门制作. 6.2.4其他部门联络厂商送样时须告相关采购员,同时厂商应明确告知采购员制作样品所需资料(如图纸、样品、菲林等)。如制作过程中有不明之处或涉及技术问题,采购应联络相关人员对其解释。 6.3取样作业 6.3.1厂商依要求时间提供是足数样品(至少10PCS),并随样品提供1套相关的技术资料(产品规格、检验报告等)及承认书。 ①所有对产品品质及工艺有重要影响的关键元器件,如继电器、机芯、PCB等必须要求供应商提供质量合格证书。 ②针对安全性物料,必须要求供应提供第三方认证机构认可的安全证书复印件。 ③每一款新样品送样时必须附上报价单,如样品数量过多须付款时,厂商应事先与采购协商并要求按规定下订单。 6.3.2自制部件由生产部门依要求时间生产足数样品,并经品管部初步检验认可后附上检验记录. 6.4物料承认作业
可靠性测试作业程序
7.4.2试验对象:所有线材成品均适用之 7.4.3試驗依據: EIA-364-17 7.4.4試驗方法: a 溫度 85±2℃條件下 , 持續時間 96H. b 放置 1H 後確認外觀無損傷 , 功能無 open 或 short 。 7.4.5 成品此項測試按客戶在新產品打樣時規定要求執行;品質出現異常時執行及客戶有要求時執行 ; 每三個月執行一次 . 7.5ROSH 测试 7.5.1試驗目的 :评估连接器产品是否满足 ROSH 要求。 7.5.2试验对象 :所有连接器产品及原料均适用之。 7.5.3试验依据 :参照 DS-RP21《环境管理物质技术标准》。 7.5.4試驗方法:DS-QW0703-QE 《荧光光谱仪作业指导书》。 7.5.5成品此項測試按客戶在新產品打樣時規定要求執行;品質出現異常時執 行及客戶有要求時執行 . 7.6產品可靠性測試處理方式: 7.6.1 當可靠性測試失敗時,由測試人員發出《品質異常處理單》 , 通知工程部進行分析以及改善,改善後由品保測試人員重新進行測試確認 , 當重新測試 Ok, 並追蹤後續二批生產使用情況 , 確認無不良則進行結案處理 ; 若測試還是失敗 , 則需要重新提供改善對策。
7.6.2 可靠性測試失敗的產品及物料 , 則參照 DS-QP0805《不合格品管制作業程序》行處理與執行 , 若產品有出货到客户端 , 品保告知業務 , 由業務連絡客戶進行確認 , 依照協商的方式進行處理 . 7.7針對以上可靠性測試應作好試作記錄。 7.8如客戶有特殊要求另訂之。 八、作業流程 : 見附頁 九、參考文件: 不合格品管制作業程序 矯正及預防措施作業程序 十、使用表單: 10.1 可靠性測試計劃 10.2 老化测试报告 10.3 耐插拔测试报告 10.4 摇摆测试报告 10.5 盐雾测试报告 10.6可靠性测试报告
样品试做程序
文件修订履历表 编号:版本:A/1
1 目的 新产品或新工艺开发时,为确保产品质量合格,满足客户要求,制定本程序。 2范围 适用于公司所有新产品,新工艺量产前所做的试验样品。 3职责 3.1生产部负责常规样件新产品的试做。(该新产品是指在试做时不需要更改原有的工艺流程。) 3.2工艺技术部开发工程师负责新工艺开发新产品样件试做的技术工作。(开发工程师一般由铸造工程师担当。) 3.3质量管理部负责试做样品的品质确认。 4程序 4.1市场部与客户沟通,充分了解客户的技术要求及客户产品质量标准,同时应充分考虑环境/职业健康安全等方面的因素,根据新产品的特性由工艺技术部组织产品开发,确定工艺方案,填写《产品开发任务书》交工艺技术部部负责人审核。 4.2 工艺技术部经理指定开发工程师接收任务,共同在《产品开发任务书》上签字后,反馈给市场部。 4.3 开发工程师编制项目〈开发计划表〉,〈控制计划〉;完成工艺设计草图 4.4 工艺评审工艺技术部组织技术,质量和生产有关人员对铸造工艺,机加工艺,检测工艺控制计划 等等进行评审。评审内容包括产品的技术和性能要求、工艺方案、适用的法律法规要求、所必需的其它要求等事项。开发工程师收集整理评审内容,填写〈工艺评审表〉。 4.5 工艺工装设计完成。与制造商签订〈模具制造技术协议〉;同时物流部与制造商签订《模具制造合同》。 4.6 工装模具验收质量部依据图纸和技术协议要求对所制作的模具和工装进行检验,并出具检验报告。 4. 7工装模具合格,由开发工程师通知生产部门下黄色样品跟踪单,生产信息由开发工程师填写。 4.8 铸造开发工程师下发从造型到样品客户确认各工序工艺卡,机加工开发工程师下发产品机加工艺卡。 试做过程中,开发工程师跟踪每一工序,修改完善工艺卡。样件完成,下发正式工艺卡。 4. 9样件品质确认
样品承认作业指导书
1. 目的: 確保供應商提供的樣品合乎本公司產品品質的需求。 2. 範圍: 適用於所有的供應商提供的樣品。 3. 定義: 無 4. 作業流程: 4.1流程圖:外購件樣品承認作業流程圖:
樣品承認流程
4.2作業說明: 4.2.1 樣品導入過程: 4.2.1.1 新機種導入時,專案PE需確認新增機種有無輔料; 4.2.1.1.1 如有輔料,輔料為鉚釘時,則依《鉚釘設計作業指導書》相關內容設計鉚釘,鉚 釘設計完成後交單位及部門主管簽核確認。 4.2.1.1.2 確認相關輔料後,開立《輔材樣品需求單》及提供圖紙,經單位及部門主管簽核 後,轉交採購單位。 4.2.1.2 採購單位元在接到工程單位元提供的《輔材樣品需求單》及相關技術資料、圖面後,即尋 找供應商打樣。 4.2.1.3 採購單位元依工程單位元提供產品圖紙及《供應商送樣資料作業指導書》給供應商,要求 供應商按照產品圖紙要求及《供應商送樣資料作業指導書》製作樣品及樣品承認書(一 式三份)。 4.2.2 樣品承認過程 4.2.2.1 採購單位收到供應商提供的樣品及樣品承認書後,轉交工程單位元專案PE對樣品進行 確認。 4.2.2.2 “樣品承認書”及“樣品”承認依《供應商送樣資料作業指導書》、《鉚釘類產品承認 驗證作業指導書》、《包材類產品承認驗證作業指導書》、《MYLAR類產品承認驗證作 業指導書》相關規定作業。 4.2.2.3 “樣品承認書”及“樣品”經工程單位元判定不合格後,工程單位元將此異常資訊及 相關要求在《樣品承認記錄》反映出來,知會給採購單位,並要求回復下次送樣時間。 4.2.2.4 “樣品承認書”及“樣品”經工程單位元確認合格後,工程單位元專案PE需製作《樣 品承認記錄》,專案PE需在供應商產品承認書上簽字確認,並呈單位及部門主管簽核。 4.2.2.5 “樣品承認書”經單位及部門主管簽核後,由工程單位元助理將樣品承認書一式三份交
可靠性试验(AEC-Q200-REV C )
1.范围 除另外说明外,本标准应用于AT切型晶体内部,仅限汽车客户的所有类型。 2.可靠性规格 2.1必要测试(AEC-Q200-REV C测试和HKA 测试) 进行表2中的AEC-Q200-REV C 测试加上表3中的HKA测试,并且 进行表2中(测试NO.14)和表3中(测试NO.110)的振动测试。 2.1.1AEC-Q200-REV C 测试
2.1.2HKA 表3
3.附录1 表2中的测试21 板弯曲实验的附录如下: 3.1范围 3.1.1描述 这个规格为评估挡板弯曲过程中贴装在PCB上时表面贴装组件的 终端强度确立了过程和标准 3.1.2参考文件 无可适用 3.2设备装置 3.3测试仪器 测试所用的设备应与图1所示相当。 3.3.1 样品数目 元器件的数目和实验的lot,AEC-Q200-REV C的表2中已被列出。 3.3.2测试环境 1.测试的组件贴装在一个由供应商提供的FR4板上,应符合以下 要求 2.平面模式是供应商为组件测试提供的标准 3.组件放置在一个100mm×40mm FR4 PCB板上,板的厚度 1.6mm×0.2mm,每层厚35μm±2μm,组件应在如下的回流曲线下 贴装: 预热温度:125℃±25℃,最长120秒。 183℃以上的时间:60秒-150秒 到达最高点的速率(183℃到最高点)≤3℃/秒 最高点温度:235℃+5℃ 到达最高点时间:10秒-20秒 坡道下降速率≤6℃/秒 4.安装100mm×40mm的板到一个类似于图2所示,器件面临下跌 的夹具上,设备应该能用机械手段,即可应用一个强力来弯曲 板(D)×=2mm 最小(或者定义在客户规格或者Q200)。应 用强力的持续时间应该是60(+)5秒。强力应用板上仅可一 次。
可靠性技术与测试流程 试题及答案
可靠性技术与测试流程试题 一、选择题(单项选择) 1、可靠性试验是定量评估产品的可靠性,即产品在的条件下,规定时间内完成的概率。 2、环境试验考察的是产品对环境的;确定产品的是符合合同要求,为接收,拒收提供决策依据。 3、温度变化对产品在:;;等方面有很大的影响。 4、湿热对产品在:;等方面有很大的影响。 5、MTBF也称为:,是指相邻两次故障之间的平均工作时间。 二、选择题(不定项选择) 1、哪些试验项目对产品有影响?() A、高低温试验 B、湿热试验 C、太阳辐射试验 D、大气腐蚀试验 2、振动试验的类型主要有:() A、正弦扫频振动 B、正弦定频振动 C、随机振动 D、定频随机振动 3、冲击试验的波型主要有:() A、半正弦波 B、后峰锯齿波 C、梯形波 D、方波 4、以下标准号中,哪个是指“电工电子产品环境试验第2部分:试验方法,试验C ab:恒定湿热试验”() A、GB/T2423.1 2001 B、GB/T2423.2 2001 C、GB/T2423.3 2006 D、GB/T2423.4 1993 5、客户要求产品的MTBF值≥20000h;已知生产风险α= 0.2;客户接收风险β=0.2。鉴别比:Dm=4.3;产品的MTBF θ1≥20000h 失效数r≤1;品数量:n=80台;温度加速因子AF;工作最大上限温度为40℃的产品在45℃的环境温度下进行实验,根据温度加速因子的计算公式得AF=1.477,请计算出80台产品在45℃条件下,当失效次数≤1次时,产品的MTBF≥20000h;需要多少时间:() A、600h B、700h C、616h D、717h 6、可靠性预计常用的试验方法为:() A、元器件计数法 B、应力分析法 C、高温老化应力法 D、器件温升测试法 7、以下哪些测试项目是在HALT试验中必须确定的() A、低温破坏极限 B、低温工作极限 C、高温破坏极限 D、高温工作极限 8、已知加速度频谱密度值为:0.5(m/s2)2/Hz,则对应的功率频谱密度值为: ( ) A、0.005 B、0.01 C、0.05 D、0.001 9、在IPD流程中,可靠性测试介入的阶段点为()。 A、TR4 B、TR5 C、TR6 D、TR4及TR5 10、在影响产品的环境因素中,以下哪些为机械条件() A、冲击 B、振动 C、噪音 D、摇摆 三、是非题(每题2分,共10题计20分) 1、试样的表面最热点温度低于周围大气的环境温度5℃以上为散热样品;高于5℃为非散热样品( )。 2、欠试验条件中断:试验条件低于允许误差下限时,应将试验条件重新稳定后继续试验。试验时间应为重新稳定后时间()。 3、水试验的目的是考核防水产品的外壳、防护罩(盖)的密封防水能力,与产品性能无关()。 4、太阳辐射的热效应可用高温试验来评价,因其作用机理相同,从而其试验结果也相同()。 5、大气中经常含有不同浓度的二氧化硫和硫化氢等有害的气体,对产品金属零部件及材料有影响,但不影响产品的使用安全()。 6、砂尘是黏附在设备上,并且不断地积累,长期作用后形成导电桥、产生短路,从而影响产品的功能和性能()。 7、材料表面的霉菌可以产生酸和电解质,这些物质会腐蚀产品,使材料电解、老化,引起短路甚至电气失效()。
软件测试课程形成性考核作业及实践2
软件测试(本科)课程形成性考核册 中央广播电视大学工学院
使用说明 本形考册是中央广播电视大学软件工程(本科)专业软件测试课程形成性考核的依据,与《软件测试(本科)》教材(贺平编著,中央电大出版社出版,2011,1)配套使用。 本课程3学分,共54学时,在一个学期内开设。本课程的特点为综合性强,基本理论知识及基本技术方法的覆盖面宽、课程基本涵盖了软件测试全貌,同时实践性也较强。学习本课程,不仅要求同学们正确理解、掌握软件测试的基本知识和基础理论,更要求能够运用这些知识与技术方法,分析所面对的软件测试的(工程)问题,结合软件工程、软件设计、软件编程的相关知识与技术,通过实践运用,学会对软件测试问题的分析、技术方法运用策略及过程,完成实际测试任务。 本课程的形成性考核成绩占课程总成绩的30%(终结性考试成绩占课程总成绩的70%,课程总成绩按百分制记分,60分为合格。 形成性考核按百分制计分,每次形成性考核任务也按照百分制计分。形考任务的形式为综合性的,共有5次,其中作业形式3次,主要检查课程学习情况,检查对课程内容理解与掌握的程度;实践是完成本课程学习目标的重要组成部分,实践环节培养同学们运用软件测试技术方法解决实际测试程序(案例)的重要环节,主要培养和考核大家对这方面的掌握程度及工程应用的能力,实践形式2次。考核成绩由地方电大教师根据学生完成情况进行评定。两种形成性方式考核,每次均占20%。
软件测试作业1 (本作业覆盖教材中的第1至2章的内容) 一、单项选择题(每小题3分,共45分) 1.软件测试目的可以是:( B ) A.发现缺陷 B.确认软件能够正常运行 C.预防缺陷 D.直接提高产品的售价 E.减少整个产品开发周期时间 a)A, B b)A, B, C c)A, B, C 和 D d)所有选项 2.基本的测试过程主要由下面哪些活动组成:( B )计划和控制(control) B.分析和设计 C.实现和执行 D.评估准出准则和测试报告 E.测试结束活动 a)A, B 和 C b)A, B, C 和 D c)除 E 以外所有选项 a)所有选项 3.关于测试作用的描述,不正确的是:( A ) a)测试无法显示软件潜在的缺陷; b)测试能保证软件的缺陷和错误全部找到; c)测试只能证明软件存在错误而不能证明软件没有错误; d)所有的软件测试都应追溯到用户需求。 4.可维护性测试属于:() a)非功能测试