功能量规(标准状态:现行)
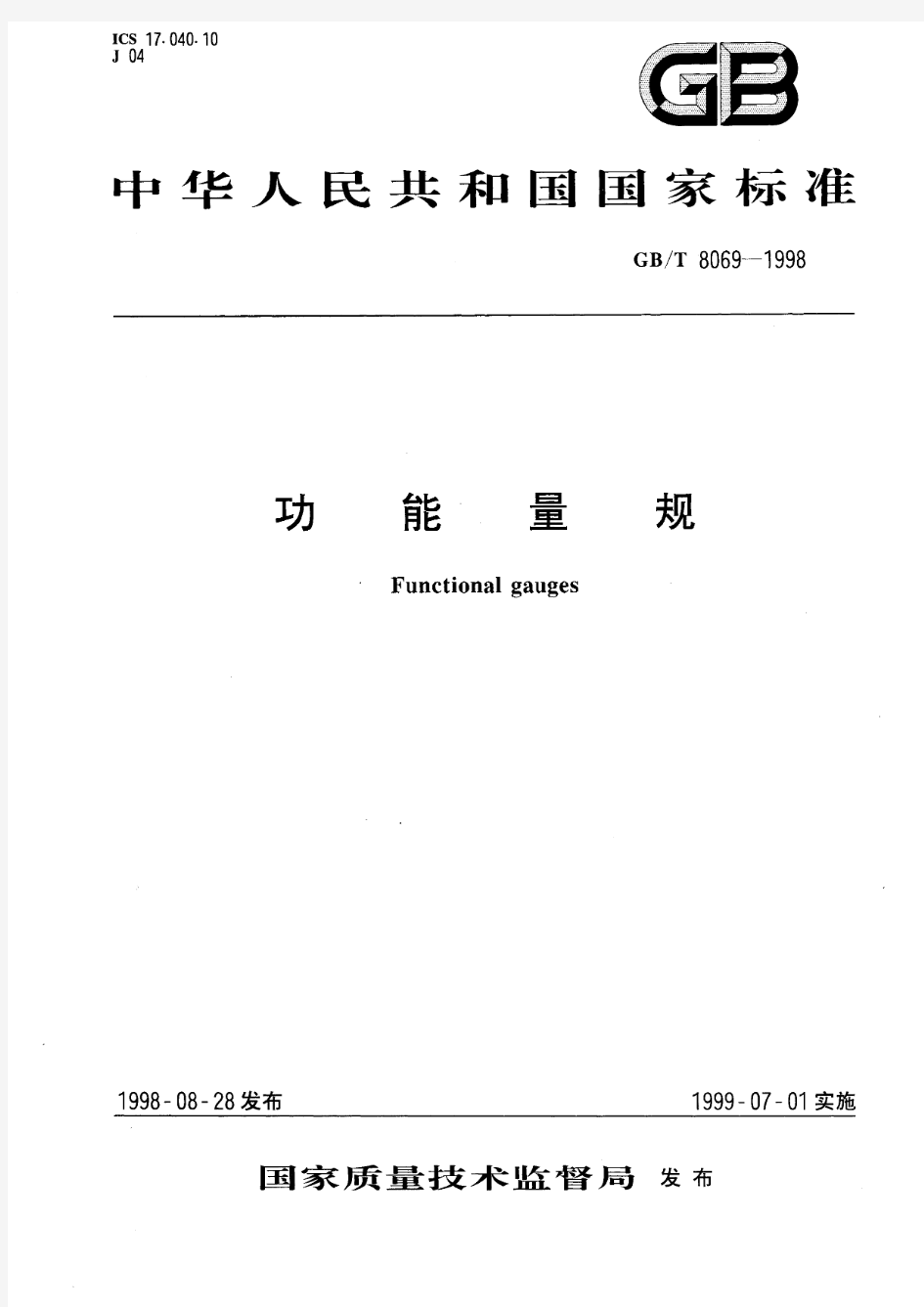

量规设计基础~
5.1 概述 光滑极限量规是一种没有刻度的专用检验工具,用光滑极限量规检验零件时,只能判断零件是否在规定的验收极限范围内,而不能测出零件实际尺寸和形位误差的数值。其特点是:结构简单,使用方便、可靠,验收效率高。 量规的形状与被检验工件的形状相反,其中检验孔的量规称为塞规,它由通规和止规组成,通规是按孔的最小极限尺寸设计的,作用是防止孔的作用尺寸小于其最小极限尺寸;止规是按孔的最大极限尺寸设计的,作用是防止孔的实际尺寸大于其最大极限尺寸,如图5-la)所示。检验轴的量规称为卡规,它的通规是按轴的最大极限尺寸设计的,其作用是防止轴的作用尺寸大于其最大极限尺寸;止规是按轴的最小极限尺寸设计的,其作用是防止轴的实际尺寸小于其最小极限尺寸,如图5-lb)所示。 用量规检验零件时,只有通规通过,止规不通过,被测件才合格。 图5-1光滑极限量规 量规按照用途分为: 1.工作量规 在零件制造过程中,生产工人检验工件时所使用的量规称为工作量规。通规用代号T表示,止规用代号Z表示。通常使用新的或者磨损较少的量规作为工作量规。 2.验收量规 检验人员或者用户代表验收工件时所用的量规称为验收量规。 验收量规不需要另行制造,一般选择磨损较多或者接近其磨损极限的工作量规作为验收量规。 3.校对量规 用于检验轴用工作量规的量规称为校对量规,由于孔用工作量规使用通用计量器具检验,所以不需要校对量规。校对量规有以下几种: 校通一通(TT)是检验轴用工作量规通规的校对量规。校对时,应该通过,否则通规不合格。 校止一通(ZT)是检验轴用工作量规止规的校对量规。校对时,应该通过,否则止规不合格。 校通一损(TS)是检验轴用工作量规通规是否达到磨损极限的校对量规。校对时,应该不通过轴用工作量规(通规),否则该通规已到或者超过磨损极限,不应该再使用。 5.2 量规尺寸及公差带 量规是专用量具,它的制造精度要求比被检验工件更高,但不能将量规工作尺寸正好加工到某一规定值,故对量规工作尺寸也要规定制造公差。 5.2.1 工作量规基本尺寸
量规设计
第6章光滑极限量规 6.1概述 检验光滑工件尺寸时,可用通用测量器具,也可使用极限量规。通用测量器具可以有具体的指示值,能直接测量出工件的尺寸,而光滑极限量规是一种没有刻线的专用量具,它不能确定工件的实际尺寸,只能判断工件合格与否。因量规结构简单,制造容易,使用方便,并且可以保证工件在生产中的互换性,因此广泛应用于成批大量生产中。光滑极限量规的标准是GB/T 1957-2006。 光滑极限量规有塞规和卡规之分,无论塞规和卡规都有通规和止规,且它们成对使用。塞规是孔用极限量规,它的通规是根据孔的最小极限尺寸确定的,作用是防止孔的作用尺寸小于孔的最小极限尺寸;止规是按孔的最大极限尺寸设计的,作用是防止孔的实际尺寸大于孔的最大极限尺寸,如图6.1所示。 卡规是轴用量规,它的通规是按轴的最大极限尺寸设计的,其作用是防止轴的作用尺寸大于轴的最大极限尺寸;止规是按轴的最小极限尺寸设计的,其作用是防止轴的实际尺寸小于轴的最小极限尺寸,如图6.2所示。 图6.1塞规检验孔 图6.2环规检验轴
量规按用途可分为以下三类: 1)工作量规工作量规是工人在生产过程中检验工件用的量规,它的通规和止规分别用代号“T”和“Z”表示。 2)验收量规验收量规量是检验部门或用户代表验收产品时使用的量规。 3)校对量规校对量规是校对轴用工作量规的量规,以检验其是否符合制造公差和在使用中是否达到磨损极限。 6.2量规设计 6.2.1极限尺寸判断原则(泰勒原则) 单一要素的孔和轴遵守包容要求时,要求其被测要素的实体处处不得超越最大实体边界,而实际要素局部实际尺寸不得超越最小实体尺寸,从检验角度出发,在国家标准“极限与配合”中规定了极限尺寸判断原则,它是光滑极限量规设计的重要依据,阐述如下:孔或轴的体外作用尺寸不允许超过最大实体尺寸。即对于孔,其体外作用尺寸应不小于最小极限尺寸;对于轴,其体外作用尺寸不大于最大极限尺寸。 任何位置上的实际尺寸不允许超过最小实体尺寸。即对于孔,其实际尺寸不大于最大极限尺寸;对于轴,其实际尺寸不小于最小极限尺寸。 显而易见,作用尺寸由最大实体尺寸控制,而实际尺寸由最小实体尺寸控制,光滑极限量规的设计应遵循这一原则。 6.2.2量规公差带设计 1. 工作量规 1)量规制造公差 量规的制造精度比工件高得多,但量规 在制造过程中,不可避免会产生误差,因而 对量规规定了制造公差。通规在检验零件 时,要经常通过被检验零件,其工作表面会 逐渐磨损以至报废。为了使通规有一个合理 的使用寿命,还必须留有适当的磨损量。因 此通规公差由制造公差(T)和磨损公差两 部分组成。 止规由于不经常通过零件,磨损极少, 所以只规定了制造公差。 量规设计时,以被检验零件的极限尺寸作为量规的基本尺寸。 图6.3光滑极限量规公差带图图6.3所示为光滑极限量规公差带图。标准规定量规的公差带不得超越工件的公差带。 通规尺寸公差带的中心到工件最大实体尺寸之间的距离Z(称为公差带位置要素)体
位置度量规设计计算过程
检具计算说明 要求测量M8螺纹空位置度①0.4。 M8螺纹孔在位宜度检测时根据最大时效尺寸可当做①6.647誉心,° = 6.647〃〃" 采用台阶式插入型功能量规 D、、w = D、、厂t ?)=6. 647-0. 4=6. 247mm T, = T 】)+ T、、产°?265 + 0.4 = 0.665mm 由表一可査得 T 产W| = 0.012mm 7; = W= 0.008mm S 二0.005mm —mm (=0. 02mm 11 = 0.006mm 由表二可得 p(=0.063mm 对检验部位有 dm = Dm =6.247mm d. = (%+”)〉(6.247+0?063)二=6.31 爲呷 diw = (d IB+Fl)一(Ti+W|)=(6247+0.063) -(0.012+0.012) = 6.286mm 对导向部位 取d G B = DGB=8inin D( ;W = D GB +(T G + W(;)= 8 + (0.008 + 0.008) = &016mm
d G=(d GB-S min)l T( = (8—0.005):驱=7.995爲呷d GW =(d GB-S n,n)-(TG+Tw)=(8-0.005)-(0.008+0.008)=7.979mm 对加位部位 (|>28.8± 0.2mm dkB = D M = 28.6mm T, = 0.4mm 由表一 T] =Wi. = 0.012mm =28.6 -0.012 dk=dLB_Ti duv = di.B 一(Ti+W J = 28.6 - (0.012+0.0 ⑵=28.576mm
位置度量规设计计算过程
检具计算说明 要求测量M8螺纹空位置度Φ0.4。 M8螺纹孔在位置度检测时根据最大时效尺寸可当做Φ6.6470.2650+, 6.647M mm D = 采用台阶式插入型功能量规 D =-MVM tD○M =6.647-0.4=6.247mm 0.2650.40.665mm =+=+=t DMTTT 由表一可查得 11 0.012mm ==TW 0.008mm ==GGTW min =0.005mm S mm t 1 =0.02 G 0.006mm t'= 由表二可得 1 =0.063mm F 对检验部位有 MV IB =6.247mm d D = 1000I 0.0120.012-T =mm 1IB )(d (6.2470.063)F d 6.31--==++ 11IW IB 1()(+)(6.2470.063)(0.0120.012) 6.286mm d d W F T =+-=+-+= 对导向部位 取GB GB =8mm d D = T 0.008G 00=mm GB 8D d G ++= GW GB G G ()8(0.0080.008)8.016mm W D D T =++=++= G 000G 0.0080.006mm GB min T ()(80.005)d 7.995d S --===--- G W GW GB min ()()(80.005)(0.0080.008)7.979mm d d S T T =--+=--+=
对定位部位 28.80.2mm φ± M LB 28.6mm d D == t 0.4m m T = 由表一 L L 0.012mm W T == L 00L 0.012LB T d 28.6d -==- L LW LB L ()28.6(0.0120.012)28.576mm d d W T =-+=-+=
检测技术的基本概念
检测技术的基本概念 典型参数的检测技术 检测技术的练习 检测技术的基本概念 检测的意义 为了满足机械产品的功能要求,在正确合理地完成了可靠性、使用寿命、运动精度等方面的设计以后,还须进行加工和装配过程的制造工艺设计,即确定加工方法、加工设备、工艺参数、生产流程及检测手段。其中,特别重要的环节就是质量保证措施中的精度检验。 “检验”就是确定产品是否满足设计要求的过程,即判断产品合格性的过程。检验的方法可以分为两类:定性检验和定量检验。定性检验的方法只能得到被检验对象合格与否的结论,而不能得到其具体的量值。定量检验的方法是在对被检验对象进行测量后,得到其实际值并判断其是否合格的方法,简称为“检测”。检测的核心是测量技术。通过测量得到的数据,不仅能判断其合格性,还为分析产品制造过程中的质量状况提供了最直接而可靠的依据。 测量的基本要素 一个完整的测量过程应包含被测量、计量单位、测量方法(含测量器具)和测量误差等四个要素。 被测量在机械精度的检测中主要是有关几何精度方面的参数量,其基本对象是长度和角度。 计量单位是以定量表示同种量的量值而约定采用的特定量。我国规定采用以国际单位制(SI)为基础的“法定计量单位制”。常用的长度单位有“毫米(mm)”、“微米(μm)”和“纳米(n m)”,常用的角度单位有“度(°)”、“分(′)”、“秒(″)”和“弧度(rad)”、“球面度(sr)”。 测量方法是根据一定的测量原理,在实施测量过程中对测量原理的运用及其实际操作。广义地说,测量方法可以理解为测量原理、测量器具(计量器具)和测量条件(环境和操作者)的总和。 测量误差是被测量的测得值与其真值之差。由于测量会受到许多因素的影响,其过程总是不完善的,即任何测量都不可能没有误差。从测量的角度来讲,真值只是一个理想的概念。因此,对于每一个测量值都应给出相应的测量误差范围,说明其可信度。不考虑测量精度而得到的测量结果是没有任何意义的。 检测的一般步骤 通常情况下,检测应有以下几个步骤: 1、确定被检测项目认真审阅被测件图纸及有关的技术资料,了解被测件的用途,熟悉各项技术要求,明确需要检测的项目。 2、设计检测方案根据检测项目的性质、具体要求、结构特点、批量大小、检测设备状况、检测环境及检测人员的能力等多种因素,设计一个能满足检测精度要求,且具有低成本、高效率的检测预案。 3、选择检测器具按照规范要求选择适当的检测器具,设计、制作专用的检测器具和
量具的分类【大全】
量具的分类【全】 按其用途可分为三大类: 1、单值量具 只能体现一个单一量值的量具。可用来校对和调整其它测量器具或作为标准量与被测量直接进行比较,如量块、角度量块等。 2、多值量具 可体现一组同类量值的量具。同样能校对和调整其它测量器具或作为标准量与被测量直接进行比较,如线纹尺。 3、专用量具 专门用来检验某种特定参数的量具。常见的有:检验光滑圆柱孔或轴的光滑极限量规,判断内螺纹或外螺纹合格性的螺纹量规,判断复杂形状的表面轮廓合格性的检验样板,用模拟装配通过性来检验装配精度的功能量规等等。 4、通用量具 我国习惯上将结构比较简单的测量仪器称为通用量具。如游标卡尺、外径千分尺、百分表等。 量具是以固定形式复现量值的测量器具。它的特点如下: 1、本身直接复现了单位量值,即量具的标称值就是单位量值的实际大小,如量块本身就复现了长度量的单位。 2、在结构上一般没有测量机构,没有指示器或运动着的元部件。如量块只是复现单位量值的一个实物。 3、由于没有测量机构,如不依赖其他配用的量具,就不能直接测出被测量值。例如量块要配用干涉仪、光学计。因此它是一种被动式测量器具。 测量器具的技术性能指标 1、量具的标称值 标注在量具上用以标明其特性或指导其使用的量值。如标在量块上的尺寸,标在刻线尺上的尺寸,标在角度量块上的角度等。 2、分度值 测量器具的标尺上,相邻两刻线(最小单位量值)所代表的量值之差。如一外径千分尺的微分筒上相邻两刻线所代表的量值之差为0.01mm,则该测量器具的分度值为0.01mm。分度值是一种测量器具所能直接读出的最小单位量值,它反映
了读数精度的高低,也说明了该测量器具的测量精度高低。 3、测量范围 在允许不确定度内,测量器具所能测量的被测量值的下限值至上限值的范围。例如,外径千分尺的测量范围有0~25mm、25~50mm等,机械式比较仪的测量范围为0~180mm。 4、测量力 在接触式测量过程中,测量器具测头与被测量面间的接触压力。测量力太大会引起弹性变形,测量力太小会影响接触的稳定性。 5、示值误差 测量仪器的示值与被测量的真值之差。示值误差是测量仪器本身各种误差的综合反映。因此,仪器示值范围内的不同工作点,示值误差是不相同的。一般可用适当精度的量块或其它计量标准器,来检定测量器具的示值误差。 测量工具的选定 每次测量前,需要根据被测零件的特殊特性选择测量工具,比如,长、宽、高、深、外径、段差等可选用卡尺、高度尺、千分尺、深度尺;轴类直径可选用千分尺、卡尺;孔、槽类可选用塞规、块规、塞尺;测量零件的直角度选用直角尺;测量R值选用R规;测量配合公差小,精度要求高或要求计算形位公差时可选用三次元、二次元;测量钢材硬度选用硬度计。 1、卡尺的应用 卡尺可测量物体的内径、外径、长度、宽度、厚度、段差、高度、深度;卡尺是最常用、使用最方便的量具,在加工现场使用频率最高的量具。 数显卡尺:分辩力0.01mm,用于配合公差小(精度高)的尺寸测量。 卡尺使用前需先用干净的白纸将灰尘与脏污去除(用卡尺外测定面卡住白纸然后自然拉出,重复2-3次即可) 使用卡尺测量时,卡尺的测量面应尽量与被测物体的测量面平行或垂直; 使用深度测量时,如被测物体有R角时,需避开R角但紧靠R角,深度尺与被测高度尽量保持垂直; 卡尺测量圆柱时,需转动且分段测量取最大值; 因卡尺使用的频率高,保养工作需要做到最好,每天使用完后需擦拭干净后放入盒内,使用前需用量块检验卡尺的精度。 2、千分尺的应用 千分尺使用前需先用干净的白纸将灰尘与脏污去除(用千分尺测量接触面与螺杆面卡住白纸然后自然拉出,重复2-3次即可),然后扭动旋钮,测量接触面与螺杆面快接触时,改用微调,当两面完全接触后调零,即可进行测量。 千分尺测量五金件时,调动旋钮,快接触工件时,改用微调旋钮旋进,当听到咔、咔、咔三声响后停止,从显示屏或刻度上读出数据。 测量塑胶产品时,测量接触面与螺杆轻轻接触到产品即可。 千分尺测量轴类直径时,至少测量两个以上方向且分段测取最大值测量中的千分尺,两接触面应当随时保持清洁,减少测量误差。
同轴度量规的设计及误差分析
同轴度量规的设计及测量误差分析 摘要:阐述一种典型的功能量规——同轴度量规的设计步骤,并分析用同轴度量规测量时产生误差的原因及减小误差的方法。 关键词:同轴度量规误差 1、前言 功能量规是检验零件关联被测要素的实际轮廓是否超越规定边界(最大实体边界或实效边界)的量规。边界的方向由基准确定,位置由基准的理论正确尺寸确定。一般情况下,在被测要素和基准要表素的尺寸(如孔和轴的直径、槽和凸台的宽度等)检验合格后,再使用位置量规检验,若位置量规能自由通过,则表示被测的实际轮廓未超越规定边界。 GB/T8069-1998《功能量规》国家标准适用于按GB1182~1184《形状和位置公差》,GB4249《公差原则》所规定的被测要素遵守相关原则(最大实体原则、包容原则)的平行度、垂直度,倾斜度、同轴度、对称度和位置度的量规。 同轴度量规是实际生产中广泛使用的一种位置量规,具有设计加工简单,使用方便,成本低廉等优点。下面对同轴度量规的设计方法及使用同轴度量规测量时可能产生的误差作简单的阐述与分析。 2、同轴度量规的设计 同轴度误差是指被测实际轴线对基准轴线(或公共轴线)同轴度程度的定位误差。因此,同轴度误差是包容被测实际轴线,且与基准轴线(或公共基准轴线)同轴的定位最小包容区域的直径,即要素的实际轴线对基准轴线的允许变动量。公差带定义为直径为公差值t,且与基准轴线同轴(重合)的圆柱面内的区域。如图1所示: (图1) 同轴度误差可用圆度仪测量、坐标法测量,打表测量以及综合量规检验。 用综合量规测量时综合量规的直径分别为基准孔的最大实体尺寸和被测孔的实效尺寸。若综合量规能通过,表示被测零件的同轴度合格。 综合量规的工作部分尺寸则可以按照GB/T8069-1998《功能量规》的设计公式来计算,即: 定位部分: (1)基本尺寸d BP=D1MMC (2)极限尺寸d LP=D BP0 -TP (3)磨损极限尺寸d WP=D BP-(TP+WP) 测量部分: (1)基本尺寸d BM=D2MMC-t (2)极限尺寸d LM=(D BM+FM)0 -TP (3)磨损极限尺寸d WM=(D BM+FM)-(TM +WM) 其中TP、WP、TM、WM及FM可以从GB/T8069-1998中查出。 必须指出,上述所列量规设计公式只适用于分