10第十章渗透气化
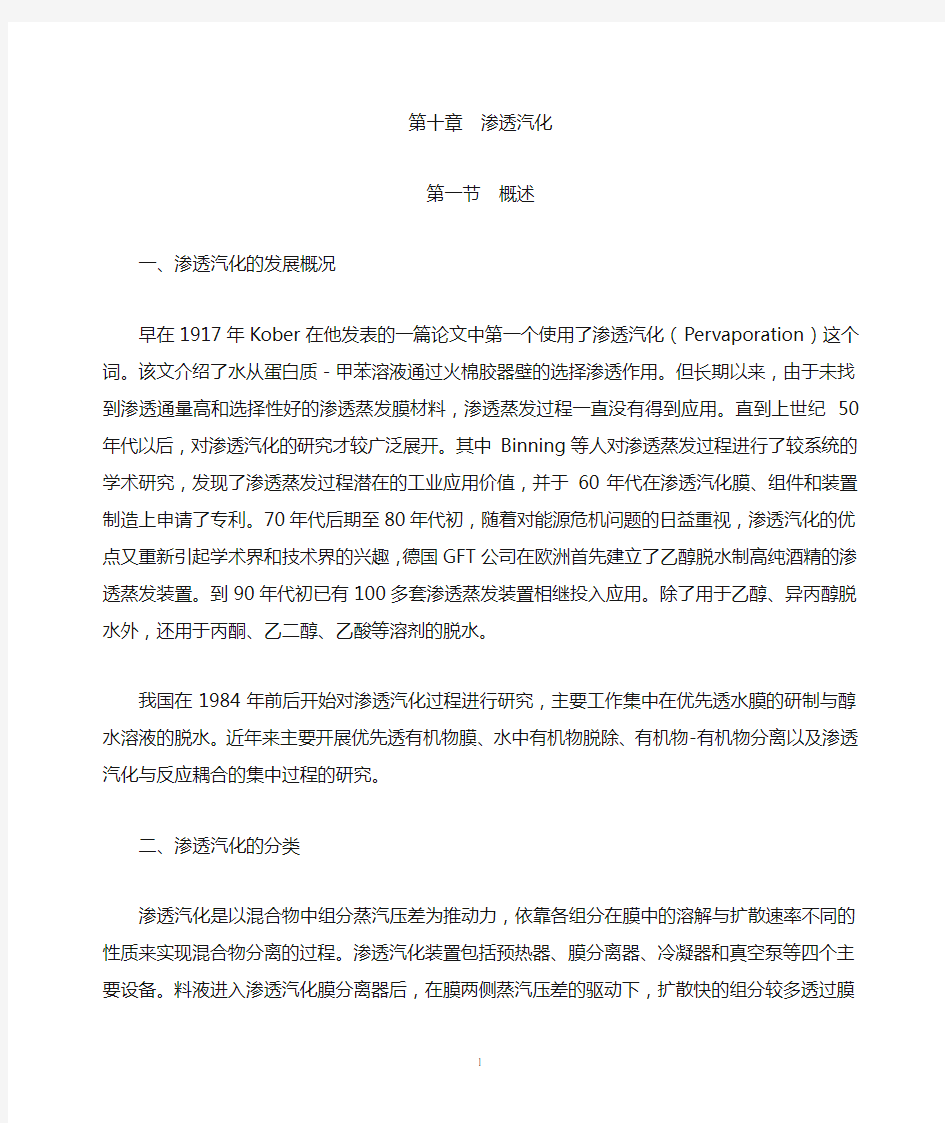

第十章渗透汽化
第一节概述
一、渗透汽化的发展概况
早在1917年Kober在他发表的一篇论文中第一个使用了渗透汽化(Pervaporation)这个词。该文介绍了水从蛋白质-甲苯溶液通过火棉胶器壁的选择渗透作用。但长期以来,由于未找到渗透通量高和选择性好的渗透蒸发膜材料,渗透蒸发过程一直没有得到应用。直到上世纪50年代以后,对渗透汽化的研究才较广泛展开。其中Binning等人对渗透蒸发过程进行了较系统的学术研究,发现了渗透蒸发过程潜在的工业应用价值,并于60年代在渗透汽化膜、组件和装置制造上申请了专利。70年代后期至80年代初,随着对能源危机问题的日益重视,渗透汽化的优点又重新引起学术界和技术界的兴趣,德国GFT公司在欧洲首先建立了乙醇脱水制高纯酒精的渗透蒸发装置。到90年代初已有100多套渗透蒸发装置相继投入应用。除了用于乙醇、异丙醇脱水外,还用于丙酮、乙二醇、乙酸等溶剂的脱水。
我国在1984年前后开始对渗透汽化过程进行研究,主要工作集中在优先透水膜的研制与醇水溶液的脱水。近年来主要开展优先透有机物膜、水中有机物脱除、有机物-有机物分离以及渗透汽化与反应耦合的集中过程的研究。
二、渗透汽化的分类
渗透汽化是以混合物中组分蒸汽压差为推动力,依靠各组分在膜中的溶解与扩散速率不同的性质来实现混合物分离的过程。渗透汽化装置包括预热器、膜分离器、冷凝器和真空泵等四个主要设备。料液进入渗透汽化膜分离器后,在膜两侧蒸汽压差的驱动下,扩散快的组分较多透过膜进入膜后侧,经冷凝后达到分离目的。
按照形成膜两侧蒸汽压差的方法,渗透汽化主要有以下几种形式:
1.减压渗透汽化:膜透过侧用真空泵抽真空,以造成膜两侧组分的蒸汽压差。在实验室中若不需收集透过侧物料,用该法最方便。
2.加热渗透汽化:通过料液加热和透过侧冷凝的方法,形成膜两侧组分的蒸汽压差。一般冷凝和加热费用远小于真空泵的费用,且操作也比较简单,但传质动力比第一类小。
3.吹扫渗透汽化:用载气吹扫膜的透过侧,以带走透过组分,吹扫气经冷却冷凝以回收透过组分,载气循环使用。
4.冷凝渗透汽化:当透过组分与水不互溶时,可以低压水蒸汽为吹扫载气,冷凝后水与透过组分分层后,水经蒸发器蒸发重新使用。
三、渗透汽化过程特点
渗透汽化与反渗透、超滤及气体分离等膜分离技术的最大区别在于物料透过膜时将产生相变。因此在操作过程中必须不断加入至少相当于透过物气化潜热的热量,才能维持一定的操作温度。
(一)渗透汽化特点:
1.分离系数大。针对不同物系的性质,选用适当的膜材料与制膜方法可以制得分离系数很大的膜,一般可达几十、几百、几千、甚至更高。因此只用单极即可达到很高的分离效果。
2.渗透汽化虽以组分的蒸汽压差为推动力,但其分离作用不受组分汽-液平衡的限制,而主要受组分在膜内渗透速率控制。各组分分子结构和极性等的不同,均可成为其分离依据。因此,渗透汽化适合于用精馏方法难以分离的近沸物和恒沸物的分离。
3.过程中不引入其它试剂,产品不会受到污染。
4.过程简单,附加的处理过程少,操作比较方便。
5.过程中透过物有相变,但因透过物量一般较少,汽化与随后的冷凝所需能量不大。
6.渗透通量小,一般小于1000g/m 2?h ,而选择性高的膜,其通量往往只有100g/m 2?h 左右,甚至更低。
7.膜后侧需抽真空,但通常采用冷凝加抽真空法,需要由真空泵抽出的主要是漏入系统的惰性气体,抽气量不大。
(二)渗透汽化适用的分离过程
1.具有一定挥发性的物质的分离,这是应用渗透汽化法进行分离的先决条件。
2.从混合液中分离出少量物质,例如有机物中少量水的脱除,可以充分利用渗透汽化分离系数大的优点,又可少受透过物汽化耗能与渗透通量小的不利影响。
3.恒沸物的分离,当恒沸液中一种组分的含量较小时,可以直接用渗透汽化法得到纯产品。当恒沸物中两组分含量接近时,可以用渗透汽化与精馏联合的集成过程。
4.精馏难以分离的近沸物的分离。
5.与反应过程结合。利用其分离系数高,单极分离效果好的特点,选择性的移走反应产物,促进化学反应的进行。
第二节 渗透汽化的基本理论
一、渗透汽化的基本原理
渗透汽化使用的是致密膜、有致密皮层的复合膜或非对称膜。原料液进入膜组件,流过膜面,在膜后侧保持低压。由于原液侧与膜后侧组分的化学位不同,原液侧组分的化学位高,膜后侧组分的化学位低,所以原液中各组分将通过膜向膜后侧渗透。因为膜后侧处于低压,组分通过膜后即汽化成蒸气,蒸气用真空泵抽走或用惰性气体吹扫等方法除去,使渗透过程不断进行。原液中各组分通过膜的速率不同,透过膜快的组分就可以从原液中分离出来,从膜组件中流出的渗余物可以是纯度较高的透过速率较慢的组分的产物。对于一定的混合液来说,渗透速率主要取决于膜的性质。采用适当的膜材料和制造方法可以制得对一种组分透过速率快,对另一组分得渗透速率相对很少,甚至接近零的膜,因此渗透汽化过程可以高效的分离液体混合物。
为了增大过程的推动力、提高组分的渗透通量,一方面要提高料液温度,通常在流程中设预热器将料液加热到适当的温度;另一方面要降低膜后侧组分的蒸气分压。
二、渗透汽化过程的分离性能
膜的渗透通量和分离因子是表征渗透汽化膜分离性能的主要参数,除与膜和被分离体系的物化性质、膜的几何结构有关外,还与温度和膜下游操作压力有关。渗透汽化膜过程的渗透速率主要用溶解扩散模型表示。对于二元混合物,渗透汽化膜的分离因子定义为:
α=j
i j i x x y y // 10-1 式中x i 、x j ――原液中组分i 与组分j 的摩尔分率;
y i 、y j ――透过物中组分i 与组分j 的摩尔分率。
通常式中i 表示透过速率快的组分,因此α的数值大于1。α大表示二组分的透过速率相差大,膜的选择性好。
单位时间内通过单位膜面积的组分的量称为该组分的渗透通量,其定义式如下:
J i =T
A Mi 10-2 式中Mi ——组分i 的透过量,g ;
A ——膜面积,m 2;
T ——操作时间,h ;
J i ——渗透通量,g/(m 2?h)。
对膜的要求是选择性好、渗透通量大。实际上膜的这两个性能指标常常是相互矛盾的。选择性好的膜,它的渗透通量往往比较小,而渗透通量大的膜,其分离系数通常较小。所以,在选膜与制膜时需要根据具体情况对这两项指标进行优化选择。
采用渗透汽化分离指数(PSI )可以综合表示渗透汽化分离性能,它等于分离因子α与渗透通量J 的乘积。
PSI=α·J 10-3
三、渗透汽化过程传递机理
渗透汽化过程的传递机理,由于涉及到渗透物和膜的结构和性质,渗透物组分之间、渗透物与膜之间复杂的相互作用,研究工作难度较大。目前已提出的机理模型,以溶解-扩散模型和孔流模型应用最多。
⒈溶解-扩散模型
这是描述渗透汽化传质机理使用最普遍的模型。按此模型,渗透蒸发中料液侧组分通过膜的传递可分成三步:①料液中组分吸收进入膜料液侧表面;②组分扩散透过膜;③从下游侧表面解吸进入气相。
当膜透过侧的压力足够低时,组分在透过侧的解吸一般极快,可认为是无选择性步骤,但是若透过侧压力接近透过组分的蒸汽分压时,渗透速率则明显下降。在通常操作中,透过侧的压力都很低,可不考虑解吸步骤对传质过程的影响。因此膜的选择性和渗透速率受料液中组分在聚合物膜中溶解度和扩散速率控制。前者是体系的热力学性质,后者是动力学性质。
组分通过膜的传递还受到料液中其他组分的影响,这种现象称为耦合现象,这也是渗透汽化与气体分离的区别之一。耦合作用也分热力学和动力学两部分。热力学部分表示组分在膜内的溶解度受另一组分影响,这种影响来自膜内渗透组分间的相互作用及每个组分与膜的相互作用。动力学耦合作用是由于渗透组分在聚合物中的扩散系数与浓度有关所致。低分子量组分溶解在聚合物中会促进聚合物链节的运动,在双组分混合物中,两个组分产生的这种塑化作用对所有组分的传递都有增强作用。
一般说,高溶解度会导致高扩散速率,原因是:①溶解使聚合物溶胀,促进链节的自由转动,减少扩散活化能;②聚合物中的自由体积更有利于组分扩散;③通过膜中溶解液体的扩散比通过固体聚合物快。
根据原始的溶解-扩散模型,组分i 通过膜的通量可用组分i 的浓度、活动率和推动力表示,即
J i =-c i B i dμi /dX 10-4
式中:B i ———组分的活动率;
μ——组分的化学位。
在常温下,上式可表示为:
J i =-c i B i (RT dx a d i ln +V i dx
dp )T 10-5 在渗透汽化中,上、下游压差在0.1MPa 左右,因此压力梯度远远小于活度梯度,上式简化为:
J i =-c i B i RT dx
a d i ln 10-6 定义Di =RTBi ,其为组分在膜内的扩散系数,则 J i =-c i D i RT
dx a d i ln 10-7 i 、j 二元混合物在高分子膜中的活度αi 可从Flory-Huggins 热力学关系得到
lnαi =lnφi +(1+φi )-(V i /V j )φj -(M
i V V )Φm +(Ψij (u j )φj + Ψim )(φi +φm )-(V i /V j ) ΨiM φi φm 10-8
式中:u j =φj/(φi+φj );φ为二元体系中组分的体积分率。组分与高分子膜的Flory 相互作用参数Ψim 可从纯组分i 或j 在高分子膜中的溶胀自由能求得,简化后为
Ψim =-[ln(1-φm )+ φm ]/φm 2 10-9
渗透组分在膜内的扩散速度与组分的大小、形状有很大关系,在同系物中分子量低的组分透过快、化学性质和分子量相同的组分,截面小的透过快。渗透组分的化学性质对组分在聚合物中的吸附和聚合物的塑化有很大影响,对组分在聚合物中的扩散同样也有很大影响,已有不少的模型描述溶质通过溶胀聚合物的扩散。
表示组分在膜内的扩散系数与浓度的关系式有三个。
⑴常数型扩散系数: D i =D i 0 10-10
⑵线形型扩散系数: D i =D i 0(A ii c i m +A ij c j m ) 10-11
在大多数情况下A ij =0时,A ii 取为1。这种关系用于非扩散。
⑶指数型扩散系数: D i =D i 0exp(A ii c i m +A ij c j m ) 10-12
这种表示式被许多研究者使用,也很有效,只是难以理论推导。
⒉ 孔流模型
孔流模型假定膜中存在大量贯穿膜的圆柱小管,所有的孔处在室温操作条件下,渗透物组分通过三个过程完成传质:①液体组分通过孔道传输到膜内某处的液-气相界面,此为Poiseuille 流动;②组分在液-气相界面处蒸发;③气体从界面处沿孔道传输出去,此为表面流动。可见,孔流模型的典型特征在于膜内存在着液-气相界面,渗透汽化过程是液体传递和气体传递的串联耦合过程。孔流模型预言,渗透汽化过程在稳定状态下,膜中可能存在浓差极化。
实际上孔流模型中的孔为高聚物网络结构中链间未相互缠绕的空间,其大小为分子尺寸。但其和溶解-扩散模型有本质上的不同,孔流模型定义的“通道”是固定的,而溶解-扩散模型定义的“通道”是高分子链段随机热运动的结果。卷曲高分子链段的随机运动是真实存在的,因而“固定通道”是孔流模型的不足之处。
⒊ 虚拟相变溶解扩散模型
尽管溶解-扩散模型得到了普遍认可,但它不能清晰的解释渗透汽化过程中的“溶胀耦合”效应和相变的发生。为此,有些学者提出了虚拟相变溶解-扩散模型。该模型假定渗透汽化过程是液体渗透和蒸汽渗透过程的串联耦合过程,渗透物通过下述过程完成传质:渗透物在进料侧膜面溶解,在活度梯度作用下以蒸汽渗透方式到达膜透过侧;在膜透过侧解吸。与传统的溶解-扩散模型相比,该模型的主要特点在于膜内存在压力梯度和虚拟相变。实际上,虚拟相变溶解-扩散模型可以看作是传统溶解-扩散模型和孔流模型的综合。
四、影响渗透汽化过程的因素
影响渗透汽化过程的分离性能的因素主要有以下几方面:
1.膜材料和结构以及被分离组分的性质
这是影响渗透汽化分离效果的最基本的因素。对于一定的料液和分离要求而言,最重要的问题
是要选择一种适宜的膜材料和膜的结构。对于同一种物料体系,如果它的组成不同,分离要求不同,也往往需要采用不同的膜。例如有机物/水体系,有机物中少量水的除去,应采用优先透水的PVA/PAN 复合膜,而水中少量有机物的除去,则应采用优先透有机物的有机硅复合膜。
2.温度
温度影响混合液组分在膜中的溶解度与扩散系数,所以它影响渗透汽化的渗透通量与分离系数。温度升高,聚合物链节的活动度增加,渗透物分子的活动度也增加,因此渗透物分子在聚合物膜中的扩散系数随温度的升高而增大。在多数情况下都可以用Arrhenius关系式表示。因为渗透系数等于扩散系数和溶解度系数的乘积,而扩散系数及溶解度系数随温度的变化都能满足Arrhenius关系,所以温度对渗透通量的影响可以由Arrhenius关系来表征。由此还可以计算处表观渗透活化能。
温度对分离系数的影响较为复杂,无一定规律可循。多数情况下,分离系数随着温度的上升而有所下降,即非优先渗透组分随着温度的上升,膜的渗透通量相对于优先渗透组分上升较快。
3.料液组成
料液组成的变化直接影响组分在膜面上的溶解度,而组分在膜内的扩散系数与其浓度有关,所以渗透汽化分离性能与料液组成有密切的关系。因为在膜内组分与聚合物以及组分间的相互作用力的影响,使得另一组分的存在对组分的扩散产生复杂的伴生效应,所以不能根据纯组分的渗透性能简单的按一般的理想情况(即组分的渗透通量与组分的组成成正比)来预测溶液渗透汽化的分离结果,必须通过实验确定。很多实验指出,实际渗透通量比按理想情况的估算值大,分离系数比理想估算值小,但也有文献报道,实际渗透通量比理想估算值效小。
通常,随着料液中优先渗透组分浓度的提高,总渗透通量增大,但组成对分离系数的影响往往出现比较复杂的情况。
4.上、下游压力的影响
膜两侧压力的影响主要体现为对渗透汽化推动力的影响。料液侧压力增加对料液的蒸汽压影响不大,对料液在膜中的溶解度影响不大,所以对渗透汽化的分离性能影响不大。但是提高料液压力却有一系列不利的因素,所以一般料液侧只保持为克服料液流过膜组件的阻力所必需的压头。但对易挥发液体,为了提高料液温度,可以适当提高压力。
渗透汽化过程受上游侧压力的影响不大,只有当上游侧压力超过1MPa时才有明显的影响。所以,上游侧通常维持常压。下游侧压力的变化对分离过程有明显的影响。通常,随着下游侧压力的增加渗透通量下降,而料液中易挥发组分在渗透物中的浓度增加,即当优先渗透组分为易挥发组分时,分离系数上升;当优先渗透组分为难挥发组分时,分离系数下降。
5.浓差极化及温度梯度的影响
在渗透汽化过程中,由于传质速率较低,浓差极化较小,所以它的影响可以忽略不计。在料液蒸发过程中,膜内将产生温差。
6.膜厚度的影响
随着膜厚度的影响,传质阻力加大,因此渗透通量将降低。但渗透通量的数值与膜厚度的数值并不是正好成反比。在实际渗透过程中,膜厚度增加一倍,渗透通量降低不到50%。这是因为膜的一部分处于干区,其厚度的增加不影响传质;只有增加处于溶胀区的膜的厚度才会增加传质阻力,因而引起渗透通量下降。分离系数与膜厚度无关。这是因为整个膜厚度改变时,起分离作用的活性致密层保持不变的缘故。
第三节渗透汽化膜
原则上,渗透汽化和气体分离可选用同一类膜或膜材料。然而,液体与聚合物的亲和力远高于气体,所以其溶解度也要高得多。这种情况可以从有机蒸气比永久性气体如N2的渗透系数大得多看出来。对气体分离,选择性可由纯组分得渗透系数之比来估算。然而对于液体混合物而言,由于热力学相互作用,其分离特征与纯液体有很大不同。气体在聚合物中溶解度较低时,可用Henry定律
描述。液体的溶解度要高得多,因此Henry定律不再适用。为更好地描述液体混合物、聚合物及纯液体在聚合物材料中的溶解度,通常要采用Flory-Huggins理论。
一、渗透汽化膜材料的选择理论
1.Flory-Huggins相互作用参数Ψ
Flory-Huggins相互作用参数Ψ表征了一个分子的纯溶剂放入高分子纯溶液中所需的能量值。Ψ值越大,溶剂与聚合物越不易互溶。通过实验可测出溶剂与聚合物之间的Ψ值,以判断该体系的互溶情况。
对渗透汽化过程,也可根据待分离混和液的各组分与膜材料之间的Ψ值来判断各组分溶解透过的情况。此法与极性相似和溶剂化原则相比,选择膜材料的准确性较高,但参数测定复杂,且混合液中各组分与高分子膜之间的相互作用随温度、混合液的浓度而变。
2.溶解度参数理论
Mulder等提出用组分与聚合物的溶解度参数的矢量差Δ作为组分与聚合物之间的亲和力大小的量度。Δ小,组分与聚合物间的亲和力大,组分在聚合物中的溶解量大,组分易于通过。两种物质的溶解度参数越接近,则互溶性越好。对组分A、组分B与膜组成的三元体系,希望优先渗透的组分在膜中应有较大的溶解性能,它和聚合物分子的溶解度参数应较为接近。
应该指出,以溶解度参数原则推测高分子膜对组分的选择透过性有很多不完善的地方。由于该原则仅考虑了组分在聚合物中的溶解,未涉及扩散因素;仅考虑组分与膜的相互作用,未考虑组分A、组分B与膜之间三元相互作用及伴生效应。
3.极性相似和溶剂化原则
极性相似和溶剂化原则即通常所说的极性聚合物与极性溶剂互溶,非极性聚合物与非极性溶剂互溶。极性聚合物和极性溶剂混合时,由于聚合物的极性基团和极性溶剂间产生相互作用而发生溶剂化作用,使聚合物链节松弛而被溶解。
对于渗透汽化膜,可根据被分离组分的极性选择膜材料。若极性组分为优先通过组分,则应选用极性聚合物为膜材料;相反,若非极性组分为优先透过组分,则应选用非极性聚合物为膜材料。
4.定性的亲憎水平衡理论
要使某组分优先渗透,必需选用与该组分有较强亲和力的膜。但膜材料与组分间的亲和力过强,有可能因溶胀过度而造成膜机械强度的减弱和丧失,也有可能因聚合物对组分的吸引力太强而使组分的扩散系数降低。因此,膜材料与优先渗透组分间应保持适当的亲和作用力。就聚合物而言,这种亲和作用力的大小取决于其所含的官能团的特性。基于这种设想,针对有机水溶液的分离,Huang 等提出用定性的亲憎水平衡理论来选择和制取适当的膜材料。Huang等指出对于一定的有机物水溶液,如果希望得到最佳的渗透汽化分离效果,则膜材料中的亲、憎水官能团比例与被分离的混合液应达到某种平衡状态。影响这种平衡状态的因素首先是膜材料中不同类型官能团的比例,其次是被分离的混合物组分的性质和组成。因此,为了获得最佳的分离效果,对于一定的分离效果,对于一定的分离对象,所用的膜材料需要保持一个适当的亲憎水平衡。
应该指出,尽管已有各种选取膜材料的理论与方法,但它们还不成熟,一般说,它们还只能指出选材料的方向,膜材料的最终确定还得通过直接的实验。另一方面,借助前人经验,从文献资料查找已研究过的适当材料仍然是首先应当考虑的途径。此外还应强调,在选择膜材料时必需考虑膜的造价和使用寿命等实际经济因素。
二、膜材料选择性的预测
根据溶解扩散模型,渗透汽化膜的选择性决定于组分在聚合物膜内的溶解(吸附)和扩散。大量的渗透汽化实验数据表明,在聚合物中优先吸附的组分在渗透汽化中大多是优先透过的。亦即由体系的热力学性质决定的优先吸附是决定聚合物材料选择性的主要因素。组分在聚合物中的平衡吸附可以用Flory-Huggins热力学关系描述。作为初步评估,溶解度参数理论还是非常有效的,对有
机物与水的分离,聚合物的亲、疏水性和弹性体性质也是评估膜选择性的有效方法。
1.溶解度参数
聚合物在溶剂中的溶解,实质上是拆散聚合物分子间的作用,并将其拉入溶剂的过程。因此溶剂分子间、聚合物分子间及溶剂与聚合物分子间的作用力及其相对大小是影响溶解过程的内在因素。各种聚集态物质分子间相互作用力的强弱可用单位体积内聚能-内聚能密度来度量,内聚能密度的平方根定义为溶解度参数δ。
根据热力学第二定律,溶解过程自发进行的必要条件是:
对于晶体高分子ΔG M=ΔH M-TΔS M+ΔH f<0 10-13
对无定形高分子ΔG M=ΔH M-TΔS M <0 10-14
式中ΔG M为Gibbs混和自由焓,ΔH M为混和热,ΔS M为混和熵;ΔH f为溶解热。在高分子-溶剂体系中混和熵ΔS M>0, ΔG M取决于ΔH M的值,由于ΔH M实际为正值,ΔH M愈小才能使ΔG M为负值,溶解可自发进行。对于二元体系用Scatchard和Hildebrand提出的方法表示为
ΔG M=(x A V A+x B V B)(δA-δB)2φAφB 10-15
φA=x A V A /V T 10-16
式中φ为体积分率;V A、V B为偏摩尔体积;溶解度参数之差(δA-δB)愈小,ΔH M值愈小,愈容易溶解。
2.聚合物的亲、疏水性
对亲水性聚合物,若聚合物链上有某些亲水基团可通过氢键,偶极-偶极作用与水分子相互作用,而呈现很大亲水性,这种聚合物即为亲水性聚合物。亲水性聚合物能优先透过水,因而是脱水膜最好的候选材料。
对疏水性聚合物,在疏水性聚合物中不含与水分子亲和的基团,如聚乙烯、聚丙烯、聚偏氟乙烯、聚四氟乙烯等。但这些聚合物对水、有机物体系及有机物-有机物体系的选择性都很低,因为这些聚合物不象亲水性聚合物,它们与透过组分(有机物)之间并没有很强的相互作用,渗透和分离仅在这种半结晶聚合物的无定形部分发生,而且分离主要基于分子的大小和形状。但是这些疏水性聚合物都有很好的化学稳定性和热稳定性,且不溶于一般溶剂。
膜材料的亲、疏水性也可通过交联、共混、共聚等方法加以控制和调整
3.弹性体聚合物与玻璃态聚合物
弹性体材料通常优先吸附有机溶剂,是从水中脱除有机溶剂渗透汽化膜最好的候选材料。
弹性体聚合物的玻璃态转化温度低于室温,大多数弹性体聚合物都需要通过交联(或硫化)以得到足够的机械强度,由于在其柔性的链上缺乏极性基团,因此对水与有机物的混合物,它优先吸附有机组分。弹性体链的柔软性又使它具有相当高的渗透率,相应的,选择性就较低。各种橡胶类聚合物,如硅橡胶、丁二烯橡胶都可作为从水中脱除有机物的渗透汽化膜材料。
与弹性体相对的另一种聚合物为玻璃体聚合物,它又分晶态、半晶态和无定形聚合物三种。高结晶态聚合物很难与溶剂相溶,甚至不相溶。渗透汽化中的溶解扩散过程只发生在聚合物中的无定形部分。已在渗透汽化中用的膜材料,无定形的有CA、PSF、PP、PS和PVC,半晶态的有PVA、nylon-60、PVDF、PPO、PE。
三、渗透汽化膜
1.优先透水膜
优先透水膜的活性层都是含亲水性基团的聚合物,主要有以下几类。
⑴非离子型聚合物膜例如聚乙烯醇(PVA)、聚羟基甲撑(PHM)、甲氧基甲基化尼龙-3、交联聚甲基丙烯酸制成的膜属于这一类。它们分别含-OH、-NHCO、-OCH3、-OCOCH3等非离子性亲水基团。
目前在有机脱水中广泛应用的GFT膜就是由聚乙烯醇为活性层制成的复合膜,它由三层构成,底层是增强用的聚酯无纺布,中层为聚丙烯腈支撑膜,表层是经过马来酸交联的聚乙烯醇皮层。这种膜具有良好的分离性能和耐久性。
⑵离子型聚合物膜根据固定基团的属性区分,离子型聚合物可分为阳离子聚合物与阴离子聚合物两类。
⑶将亲水基团引入疏水膜中的透水膜通常采用共聚、共混、接枝等方法
⑷聚电解质透水膜由于离子基团对水的强烈水合作用和对有机物的盐析效应,膜材料中具有离子基团可以有效地提高膜对水的选择透过性与渗透通量。
2.优先透有机物膜
优先透有机物的膜材料通常是极性低、表面能低、溶解度参数小的聚合物。迄今研究较多的有硅橡胶、含氟聚合物、纤维素衍生物和聚苯醚等。
⑴有机硅聚合物这类聚合物憎水、耐热、具有很高的机械强度和化学稳定性,对醇、酯、酚、酮、卤代烃、芳香族烃、吡啶等有机物有良好的吸附选择性,是迄今研究最多的一类有机物膜材料。
⑵含氟聚合物目前已研究的聚四氟乙烯(PTFE)、聚偏氟乙烯(PVDF)、聚六氟丙烯(PHEP)、聚磺化氟乙烯基醚与聚四氟乙烯共聚物(Naifon)、聚四氟乙烯与聚六氟丙烯的等离子共聚物等。这些材料除了PVDF外均难溶于一般溶剂,通常用熔融挤压法或在聚合期间成膜。聚偏氟乙烯化学性质稳定、耐热性能好、疏水性强、抗污染性较好,可溶于常用的溶剂,成膜性能好,对卤代烃、乙醇、丙酮及芳香烃等有良好的选择性。
⑶纤维素衍生物纤维素类材料易于酯化、醚化、接枝、共聚、交联等,并且与许多聚合物都有良好的共混性。纤维素衍生物是非常好的成膜材料。纤维素可以通过各种改性手段调节其中亲憎水官能团的比例,控制其渗透汽化的分离性能。用于分离水中有机物的是憎水性的膜材料。
3.有机物分离膜
工业上有效的分离有机混合物渗透汽化膜的尚处于开发阶段。这种膜必需根据不同的分离体系特殊设计,不象前面的有机物/水体系的分离,膜材料的选择有较明确的规律可循。在有机混合物的分离中,膜材料的选择与开发必需针对具体体系的物理化学性质,如根据混合物组分的分子形状及尺寸以及所含基团的差异来选择与设计膜材料。
⑴醇/醚分离膜醇醚体系有重要意义的例子是甲醇/甲基叔丁基醚(MeOH/MTBE)和乙醇/乙基叔丁基醚(EtOH/MTBE)的分离。用于MeOH/MTBE体系分离的膜材料主要有乙酸纤维素、聚酰亚胺、Naifon、聚苯醚等。
⑵芳烃/烷烃分离膜例如苯/环己烷、甲苯/正辛烷或异辛烷的分离
⑶同分异构体的分离膜如混合二甲苯、丁醇异构体等。
⑷芳烃/醇类分离膜主要对象是苯、甲苯、与乙醇、甲醇组成的混合液,属非极性与极性体系,利用其极性和分子尺寸的差别选用和设计膜材料,优先渗透组分可以是醇,也可以是芳烃。
第四节膜组件及过程设计
一、概述
与反渗透、超滤、气体膜等分离过程一样,渗透汽化过程也使用板框式、螺旋卷式、圆管式和中空纤维式等型式的膜组件。但是由于渗透汽化过程的特点,膜组件结构上有一定的特点:
⑴渗透汽化过程是有相变的过程,其膜后侧为气体,如过程中不同时供热,料液温度将下降。
⑵渗透汽化过程的推动力为膜两侧的蒸气压差,膜后侧为真空,一般其绝对压力为几百帕,膜后侧压力大小对过程有重要的影响。所以组件中膜后侧气体的流动阻力对膜组件的分离效果影响很大,要求膜组件的膜后侧的流动阻力尽可能小,因此在组件的构造上要求膜后侧有较大的流动空间。
⑶渗透汽化过程通常在较高的温度(60~100℃)下操作,同时很多情况要接触到浓度很高的有机液体,这对膜组件的材料,特别是密封材料提出了较高的要求。
⑷渗透汽化的通量小,一般在2000g/(m2·h)以下。因此,在渗透汽化膜组件中料液流量几乎保持不变。
目前用渗透汽化方法进行有机物脱水时主要应用板框式膜组件。因为板框式膜组件可以使用耐溶剂的密封垫片(如弹性石墨、乙丙二聚物、PTFE等垫片),便于器内或级间加热,也利于减小膜后侧气体的流动阻力。
二、渗透汽化膜组件
目前渗透汽化组件大多为板框式,为降低成本,近年来也在进行卷式组件、管式组件的开发。
GFT公司认为渗透汽化过程对组件的材质和结构都有特殊要求:①料液为有机溶剂,且需在60~100℃操作,对组件和密封材料要求都比较苛刻;②必须尽量减少透过侧的压力降,以得到大的传质推动力。从这两方面看,板框式与卷式、中空纤维相比有其优势:首先卷式和中空纤维中用的粘结剂大多难以在这样的操作条件下保持其长期稳定性,而板框式中用的密封材料的选择相对就较容易,象石墨或乙烯、丙烯二聚物就可很好用于有机溶剂脱水组件的密封。再则板框式组件的透过侧空间比较大,可占组件体积的90%,这对降低透过侧的压力降极有利。若卷式组件要保证透过侧空间适用于渗透汽化过程,其填充密度将大大降低,约为100~120m2/m3,这与板框式组件的填充密度相当接近了。中空纤维组件也有类似的问题。GFT公司的板框式组件采用了不锈钢材料,开始的设备费投资较大,但以后膜的更换费每年只占5%~10%。
在板框式组件的设计中,除要保证透过侧有足够的汽化空间外,料液侧必须要形成良好的流体流动条件,在渗透汽化低进量情况下尤其要注意料液的均匀分布,避免死角和短路,保证膜面有一定流速,尽量造成湍动,以改进传质条件。
三、渗透汽化过程设计
(一)流程与工艺条件的确定
1.膜组件的流程
渗透汽化膜分离器组件的流程原则上与其他膜分离过程一样,也可以分为单级与多级操作。一般说单级操作不能将二组分混合液完全分离得到二个纯组分大产品,为了将二组分完全分开,必须采用具有回流的多级操作流程(级联)。但是由于渗透汽化的每一级都包括渗透物的冷凝器、冷凝液送入下一级的泵以及冷凝液加热器等设备,因而渗透汽化级联的流程比较复杂,所需膜面积大、能耗大;另一方面,渗透汽化具有分离系数大的特点,采用单级操作除去易渗透组分,可以直接得到纯的难渗透组分,所以渗透汽化一般采用单级操作。
单级操作时,渗透物中一般均含有一定浓度的难渗透物,通常需进一步回收处理。所以渗透汽化主要使用于从混合物中分离出少量物质。当混合液中二组分的含量均较大时,一般采用渗透汽化与其他方法(如精馏)的联合分离流程。
对于单级操作,当分离任务需要多个膜组件时,组件可以采用串联、并联和并、串联三种流程。具体采用哪种流程取决于料液流量、每个膜组件的适宜流量与膜组件数(即分离所需的总膜面积)。
渗透汽化过程中有物质的相变,渗透物通过膜后汽化成蒸气,汽化需要汽化热,通常由料液的显热供给。所以,渗透汽化过程中,料液的温度会下降。根据料液温度下降的多少,渗透汽化膜分离器的流程可分为无中间加热和有中间加热两种情况。
2.主要工艺条件
渗透汽化的主要工艺条件是料液在膜器内的温度、料液流速和压力降、料液的预处理、膜的清洗。在工艺条件确定中应考虑以下问题。
⑴料液在膜器内的温度
料液温度高、渗透汽化过程的推动力大、渗透物在膜中的扩散系数大、过程渗透通量大、为完成一定分离任务所需膜面积小、膜分离器的造价低;另一方面料液温度高、膜后侧压力可以较高,冷凝所需费用少。但是,提高料液温度受膜的耐温性和耐溶剂性的限制,过高的温度将严重降低膜
的使用寿命,增加更换膜所需的费用。所以料液温度需根据料液的性质、分离要求和所用膜的性质而定
⑵料液流速和压力降的控制。
在渗透汽化中因膜的渗透速率小,在连续操作中,单位面积膜处理的物料量通常很小,虽然浓差极化对渗透汽化的影响不象对超滤、反渗透那样严重,但对渗透汽化的传质过程仍有一定的影响。为了保持膜面料液有一定的流速,以利于膜面传质。在工业生产中又必须考虑大量膜面积多级串联会造成料液侧阻力过大;因此膜装置内的物料应采用串、并联结合的方式,既保证膜料液侧物料有一定流速,又不至压力降过大,必要时可采用中间加压泵。
⑶料液的预处理
料液必须脱除悬浮固体和金属粒子以免损伤膜表面。通常进行渗透汽化分离的物料都比较干净,并不需对物料进行特殊的预处理,在某些含盐有机溶剂脱水中,应注意由于水脱除使盐溶解度下降而析出沉积于膜面上。
⑷膜的清洗
渗透汽化膜不像多孔膜容易污染,但在工业生产中也需定期清洗以去除膜面污染物。一般可采用“在位”清洗。在有机溶剂脱水中可用组件体积1到3倍的清洗剂(如异丙醇)在加温下(50~80℃)循环即可。
通常渗透汽化膜可使用2~4年,在这段时间内膜的渗透速率和选择性变化都很小。
此外膜组件内膜的朝向对其分离性能有很大影响,应使膜的致密分离层朝向料液,若多孔支撑层朝向料液将使膜的分离因子大大下降。
3.操作方式
渗透汽化也可以有连续操作和间歇操作两种操作方式。连续操作工艺流程:料液连续送入膜分离器,从膜分离器出来的渗余液即为产品,连续送出。间歇操作工艺流程:一批料液加入料液罐,开始操作,用泵将料液经加热送至膜分离器,分离出部分组分返回料液罐,再由泵送至膜分离器。如此循环,直至料液组成达到要求值为止。将产品从料液罐放出后,进行下一批操作。
(二)膜面积的计算
计算二组分混合液用渗透汽化法分离所需的膜面积。已知料液流量F(kg/h),其中欲分离出的组分(设为优先渗透组分)的组成x i(质量分率),加热到温度Ti进入膜组件,要求除去优先渗透组分使其组分降为x R,选用已知性能的膜和膜组件,选定料液流动条件与膜后侧压力。在这种条件下可以用经验关系式法计算所需的膜面积和渗余液的温度T R。
现分析膜组件中膜面积为d A的一段微元段中的情况:
总物料衡算:
F=(F+d F)+J d A 10-17
优先渗透组分的物料衡算:
F x=(F+ d F)(x+dx)+J d A y 10-18
热量衡算:假设无热量损失,渗透物在T0℃下汽化并离开膜组件。
FTC F=(F+d F)(T+d T)C F+JdA(T0C p+ΔH V) 10-19
式中C F与C p分别为料液与渗透物液体的平均比热容;为渗透物的汽化潜热(T0℃时);J为总渗透通量,为二组分渗透通量之和。
整理以上三式,可得到下列微分方程组
d F=-J d A 10-20
dx/d A={J(x-y)}/F 10-21
d T/d A=(J/F)[(T- T0C p / C F)-ΔH V / C F] 10-22
根据由实际体系试验求得的渗透通量与温度和浓度的关系式,用数值法求解上述微分方程组可以求得料液中欲除去组分的组成降至x R所需的膜面积A,膜组件出口渗余液的量和温度T R以及渗
透液的量和组成。
(三)过程的优化
过程设计应在保证产品质量的前提下使单位产品的总费用最低。通常总费用包括设备费和操作费两部分。
1.渗透汽化的操作温度
温度是影响渗透通量的主要因素,在其他条件一定的情况下,渗透通量与温度的关系遵循Arrihenius 公式。温度高,渗透通量大,所需膜面积小,膜组件投资少,更换一次膜的费用省。但是提高温度受膜的耐温性的限制。温度高,膜的使用寿命短,更换膜的费用高。因此需要根据膜的耐温性与温度对渗透通量影响的大小来确定适宜的温度。此外,操作温度高,预热料液的设备费用和操作费用高也是一个应该考虑的问题。为了节省能耗,在系统设计中用渗余液预热部分料液。
2.中间加热
在渗透汽化过程中,料液温度下降,渗透通量减小,必须进行中间加热,提高料液温度,使过程的渗透通量始终保持在较高水平,以减少所需总膜面积,减少设备投资。但是中间加热次数的增加,也有使膜组件和中间加热器设备费用增加的一面。因此,必须以膜组件与中间加热器的设备费用最小为目标来确定每一个膜组件适宜的温度降和中间加热的次数。
3.膜组件设计
首先要根据料液及膜的性质确定适当的膜组件形式。目前用的最多的是板框式膜组件。用于渗透汽化的膜组件,其特点是膜后侧流道大。料液侧流道的设计首先应保证料液均匀分布,避免流动死角与短路,充分发挥膜的作用。其次应当保持适当的流速,减少浓差极化与温度极化的影响;第三,在组件设计中应尽可能减少料液流动的摩擦损失,组件中摩擦损失主要是进出膜框的局部损失。在框内流速选择上应在减轻极化现象影响与降低能耗间找出适当的折中方案。
膜后侧支撑板的设计通常应使其具有较大的流通截面。减少渗透汽流动的摩擦损失,降低流动压力降,有利于提高渗透通量,减少所需膜面积。流通截面大小的确定与多方面因素有关,渗透通量大、膜后压力低、膜框与支撑板的尺寸大,应采用更大的流通截面。但是流道大,需增大支撑板的厚度,使单位体积内膜面积减少,因此流通截面也有最优的值。
4.膜后侧压力
膜后侧压力是影响渗透通量的另一个重要因素。膜后侧压力大小取决于料液性能与分离的要求。要求渗余液中优先渗透组分的含量低,其蒸气压愈低,膜后侧压力愈低。对于一定的料液与分离要求,膜后侧压力愈低,过程的推动力愈大,渗透通量愈大,所需膜面积愈小,膜组件的费用低。但是压力愈低,真空泵的负荷大,要求渗透汽的冷凝温度低,冷凝器大,能耗大。因此,膜后侧压力需在膜组件与真空泵和冷凝器的费用之间找出最佳的折中值。
5.渗透汽的冷凝温度
冷凝温度取决于压力和渗透汽的性质。对于一定的渗透汽,冷凝温度低,渗透汽排出量少,真空泵投资少,能耗低,但是冷凝器本身的费用高。求出最佳的冷凝温度可以使真空泵与冷凝器的费用之和最少。
第五节渗透汽化的应用
一、有机溶剂脱水
目前有机物水溶液的分离主要采用精馏、萃取和吸附等方法。这些方法都有自身的特点与局限性,在某些情况下使用会出现种种问题,采用渗透汽化有可能克服这些问题,取得很好的效果。
适用于渗透汽化法进行有机物脱水的具体对象很多,可分以下几个方面介绍。
1.恒沸物的分离
恒沸物分离是渗透汽化最能发挥其优势的领域。用渗透汽化进行恒沸液的分离可以分为两种情况。一种是用渗透汽化法分离,直接制得产品,主要用于含水量较少得恒沸液。例如工业乙醇脱水
制备无水乙醇。另一种情况是使用渗透汽化法将恒沸液分离为两个偏离恒沸组成的产物,然后再用一般精馏或其他方法进行分离,这种方法可称为恒沸液的分割。
2.非恒沸液的分离
可以把有机物与水的混合物分为互溶与部分互溶二类。一般说,对于部分互溶体系,水在有机物种的溶解度小,化学位高,与互溶体系比较,在水含量相同的条件下,渗透汽化的推动力大,水的渗透通量高。所以,有机物中水的溶解度愈小,则该有机物脱水后其中的含量可以更小。
通常用渗透汽化法脱水,根据有机物脱水中水的溶解度的大小,其中水含量可降至几十到几百mg/L。对于水在其中溶解度很小的有机物,水含量可降至几个mg/L,但需要很低的压力、较大的真空泵和较大的膜面积。
使用渗透汽化脱水的经济性与原料中的水含量有关,一般说料液中水含量在0.1%~10%时,采用渗透汽化比较经济,水含量高,采用精馏或萃取可能比较经济,而含水量很低时,可能吸附更具有竞争力。使用渗透汽化脱水的经济性还与水和有机物的沸点高低有关。如果有机物的沸点比水低,相对说用渗透汽化比用精馏更有利。因为用粗馏法分离有机物中少量水时,大量低沸点的有机物需从精馏塔顶蒸出,而渗透汽化过程中是把少量沸点较高的水直接从有机物中分离出来。
二、水中有机物的脱除
用渗透汽化法脱除水中有机物的技术开发比较晚一些。到目前为止,对各种有机物的除去,包括醇、酸、酯、芳香族化合物、氯化碳氢化合物等已经进行了广泛研究,试验过各种材料,其中最常用的膜材料是硅橡胶。
用渗透汽化法脱除水中有机物的经济性与水中有机物的含量和有机物本身的情况有关。一般说,与其他各种分离与处理方法比较,水中有机物含量在0.1%~5%之间时用渗透汽化法比较好。浓度更高时,目前常用的蒸馏、蒸汽汽提等方法可能在经济上更有利。有机物浓度过低,渗透汽化的推动力小,渗透通量小,膜面积大,膜组件的投资大。此时,一般把它作为废液处理,采用吸附或生物处理法可能在经济上更合理。
用渗透汽化法从水中分离有机物主要可以分为以下四种情况:①从发酵液中提取有机物②酒类饮料中除去乙醇③废水处理和污染的地下水处理④溶剂回收。
三、有机/有机混合物的分离
由于分离过程的条件比较苛刻,这是目前渗透汽化技术应用开发最少的领域。如果膜和组件的稳定性得以解决,它将成为21世纪重要的膜应用技术。
用渗透汽化法进行有机物混合液分离主要是近沸物与恒沸物的分离。因为对于这些体系采用常用的精馏法,需要庞大的设备,很大的能耗,或者需要应用外加的恒沸剂或萃取剂,过程复杂,且易致产品与环境污染。如果近沸物与恒沸液中二种组分的含量相差较大时,应用渗透汽化,采用优先透过少量组分的膜,一级分离即可达到较完全的分离效果,这时渗透汽化具有明显的竞争力。当恒沸物中二组分的含量接近时,采用渗透汽化与精馏的联合过程是很经济的。对于近沸物,当二组分含量相当时,要将二组分完全分开,必须采用有回流的多级操作,这时应用渗透汽化通常是不经济的。因为渗透汽化通量小,多级操作所需膜面积大,透过物需在低压和较低温度下多次冷凝,冷凝系统投资与操作费用大。所以这种情况下只有在膜分离系数和渗透通量都很大时,渗透汽化才可能有竞争力。
迄今已研究的有重要工业意义的体系主要有以下几类:⑴醇/醚混合物的分离⑵芳烃与脂肪烃的分离⑶同分异构物的分离⑷环己酮、环己醇与环己烷的分离⑸脂肪烃/脂肪烃的分离(指烯烃/烷烃,正烷烃与异烷烃以及卤代烃混合物等的分离)
第六节渗透汽化膜的展望
渗透汽化膜分离是一种正在发展中的新技术,要使其在工业上广泛应用,在膜与膜组件的研制等方面还需进行大量的研究与开发工作。首先是高效膜的研制,要针对分离物系的物理化学特性,采用适当的膜材料与制膜方法,制取渗透系数高、渗透通量大的膜。膜的耐热与耐溶剂的稳定性是另一个重要的研究目标,提高膜的耐热性,使其能在较高的温度下操作是提高膜的渗透通量的重要途径,也是渗透汽化用膜的一个主要研究方向。降低膜的造价,对于渗透汽化的实际应用具有重要意义。目前渗透汽化主要使用不锈钢制的板框式膜组件,造价高,投资大。这是影响渗透汽化推广使用的一个不利因素。改进板框结构,采用廉价的材料和开发紧凑、高效的卷式与中空纤维式膜组件,降低膜组件的造价,将促进渗透汽化过程的工业应用。
渗透汽化的突出优点是分离系数高和不受汽—液平衡的限制,因而它在用精馏方法难以分离的恒沸物与近沸物的分离中将具有广阔的应用前景。就分离对象而言,用渗透汽化法分离有机混合液将是很有发展前途的方面。渗透汽化的缺点是渗透通量小和渗透物在低压下冷凝,因而它一般适用于从混合液中分离出少量物质,不宜采用多级操作。所以它通常要与其他分离过程联合使用才能获得最好的经济效果。
渗透汽化技术
渗透汽化技术(PV)的应用 杨丽琴、阴秋萍 摘要:综述了渗透汽化膜传递理论研究的现状,叙述了渗透汽化膜分离技术的基本原理及传质过程的机理,叙述了渗透汽化过程的进展,叙述了渗透汽化分离水中微量有机物及其在化工生产上的应用进行了介绍. 关键词:渗透汽化;传递理论;原理;膜组件;脱水膜;应用 1 引言 渗透汽化(pervaporation,简称PV)是一种新型膜分离技术。该技术用于液体混合物的分离,其突出的优点是能够以低的能耗实现蒸馏、萃取、吸收等传统方法难以完成的分离任务。它特别适用于蒸馏法难以分离或不能分离的近沸点、恒沸点混合物以及同分异构体的分离;对有机溶剂及混合溶剂中微量水的脱除及废水中少量有机污染物的分离具有明显的技术上和经济上的优势;还可以同生物及化学反应耦合,将反应生成物不断脱除,使反应转化率明显提高。所以,渗透汽化技术在石油化工、医药、食品、环保等工业领域中具有广阔的应用前景及市场。它是目前处于开发期和发展期的技术,国际学术界的专家们称之为21世纪最有前途的高技术之一。 2 渗透汽化膜分离技术 2. 1 基本原理 渗透汽化是利用致密高聚物膜对液体混合物中组分的溶解扩散性能的不同实现组分分离的一种膜过程(如图1-1所示)。液体混合物原料经加热器加热到一定温度后,在常压下送入膜分离器与膜接触,在膜的下游侧用抽真空或载气吹扫的方法维持低压。渗透物组分在膜两侧的蒸汽分压差(或化学位梯度)的作用下透过膜,并在膜的下游侧汽化,被冷凝成液体而除去。不能透过膜的截留物流出膜分离器。 2. 2 PV膜过程的特点 (1) PV最突出的特点是分离系数大,单级即可达到很高的分离效果; (2) PV分离过程不受组分汽.液平衡的限制,适用于精馏等传统方法难以分离的近沸物和恒沸物的分离;
渗透汽化膜分离技术
蒸汽渗透膜分离技术 清华大学膜技术工程研究中心北京清源洁华膜技术有限公司 2015年10月
1. ,概要 北京清源洁华膜技术有限公司成立于2013年,公司以清华大学膜技术工程研究中心渗透汽化膜等专利技术为基础,从事渗透汽化、汽体渗透、透醇膜、超滤膜、纳滤膜等的研发生产。 北京清源洁华膜技术有限公司主要发起人全部毕业于清华大学,分别具有几十年的膜性能研发生产、化工工艺开发设计、化工设备加工制造、化工装置及企业生产管理经验,对国家环境保护工作的紧迫性及膜分离技术的先进性共同认知促成大家走到了一起。 汽体渗透和渗透汽化膜分离技术是近二十年来发展起来的一种高新技术,依据溶解扩散分离原理,依靠有机汽体和空气各组分在膜中的溶解与扩散速度不同的性质来实现分离的新型膜分离技术,以混合物中组分分压差为分离推动力,有机汽体透过膜、空气不能透过膜。该技术具有高效、低能耗、操作安全等优点,与传统油汽回收技术相比,具有明显的技术上和经济上的优势。 北京清源洁华膜技术有限公司作为清华大学膜技术工程中心生产、实验基地,拥有三项国家发明专利,分别是:一种渗透汽化优先透醇沸石填充硅橡胶复合膜的制备方法(专利号:ZL 2008 1 0105405.6;专利有效期:2008年4月30日至2028年4月29日)、一种渗透汽化汽油脱硫用互穿网络膜的制备方法(专利号:ZL 2010 1 0282031.2;专利有效期:2010年9月14日至2030年9月13日)、二氮杂萘聚醚砜酮类聚合物平板超滤膜及其制备方法(专利证书号:ZL 2007 1 0177247.0;专利有效期:2007年11月13日至2027年11月12日)。 2.项目背景 清华大学膜技术工程研究中心深知国际竞争的残酷性和中国人拥有该先进技术自主产权的重要性,是国内最早开展渗透汽化和汽体渗透膜技术研究单位。在国家的支持下,本研究中心先后承担了国家自然科学基金“七五”重大项目“膜分离与分离膜”、“八五”重点项目“新型膜分离过程的应用基础研究”、“九五”国家重点科技攻关“渗透汽化透水膜及其过程关键技术开发”研究以及国家“十五”“863”项目“渗透汽化膜材料及其应用”研究,取得了醇、酯、酮脱水等16项小试研究成果和苯脱水、碳六油脱水两项工业中试研究成果,建立了年生产能力10万平方米的渗透汽化膜生产线,在广东、山东、江苏、浙江、四川等地相继建成了30
渗透汽化膜分离项目简介
膜法有机气体回收项目 XXX技术工程中心 2015年11月
1. ,概要 北京清源洁华膜技术有限公司(以下简称清源洁华)成立于2013年,公司以清华大学膜技术工程研究中心渗透汽化膜等专利技术为基础,从事渗透汽化、汽体渗透、透醇膜、超滤膜、纳滤膜等的研发生产。 清源洁华主要发起人全部毕业于清华大学,分别具有几十年的膜性能研发生产、化工工艺开发设计、化工设备加工制造、化工装置及企业生产管理经验,对国家环境保护工作的紧迫性及膜分离技术的先进性共同认知促成大家走到了一起。 汽体渗透和渗透汽化膜分离技术是近二十年来发展起来的一种高新技术,依据溶解扩散分离原理,依靠有机汽体和空气各组分在膜中的溶解与扩散速度不同的性质来实现分离的新型膜分离技术。其中膜法有机气体回收是以混合物中组分分压差为分离推动力,有机汽体透过膜、空气不能透过膜。该技术具有高效、低能耗、操作安全等优点,与传统油汽回收技术相比,具有明显的技术上和经济上的优势。 清源洁华作为清华大学膜技术工程中心生产、实验基地,拥有三项国家发明专利,分别是:一种渗透汽化优先透醇沸石填充硅橡胶复合膜的制备方法;一种渗透汽化汽油脱硫用互穿网络膜的制备方法;二氮杂萘聚醚砜酮类聚合物平板超滤膜及其制备方法等。 2.项目背景 清华大学膜技术工程研究中心深知国际竞争的残酷性和中国人拥有该先进技术自主产权的重要性,是国内最早开展渗透汽化和汽体渗透膜技术研究单位。在国家的支持下,本研究中心先后承担了国家自然科学基金“七五”重大项目“膜分离与分离膜”、“八五”重点项目“新型膜分离过程的应用基础研究”、“九五”国家重点科技攻关“渗透汽化透水膜及其过程关键技术开发”研究以及国家“十五”“863”项目“渗透汽化膜材料及其应用”研究,取得了醇、酯、酮脱水等16项小试研究成果和苯脱水、碳六油脱水两项工业中试研究成果。在渗透汽化膜制备、膜组件设计、膜工艺等方面申请专利10多项,形成了完整的具有我国自主知识产权的专有技术,代表着我国渗透汽化和汽体渗透膜技术的先进水平。
渗透汽化论文(渗透汽化膜分离技术的进展及应用)
渗透汽化膜分离技术的进展及应用 摘要: 综述了渗透汽化膜传递理论研究的现状, 分析了各种模型的特点, 并就渗透汽化膜传递理论的研究方向提出了建议。叙述了渗透汽化过程的新进展,并着重介绍了它在石化中的四方面应用,即(1) 有机溶剂及混合溶剂的脱水;(2) 废水处理及溶剂回收;(3) 有机混合物的分离;(4) 化学反应过程中溶剂的脱水。 关键词:渗透汽化;传递理论;模型;膜组件;脱水膜 前言 渗透汽化(Pervaporation, 简称PV ) 是用于液体混合物分离的一种新型膜技术。自80年代以来, 渗透汽化技术得到了很大的发展, 目前世界范围内有100 多套工业装置。然而, 渗透汽化膜分离的机理由于涉及到渗透物和膜的结构和性质, 渗透物组分之间、渗透物与膜之间复杂的相互作用, 涉及到化学、化工、材料、非晶态物理、统计学等学科的交叉, 研究工作的难度较大, 认识也不够深入。也提出了几种描述渗透汽化膜传递机理的模型, 其中主要有溶解扩散膜型和孔流模型[1]。膜技术作为一种高新技术,近30 多年来获得了极为迅速的发展,已在石油化工、海运、冶金、电子、轻工、纺织、食品、医疗卫生、生化制药、环保、航天等领域内广泛应用,形成了独立的新兴技术产业。据专家断言:“今后,谁掌握了膜技术,谁就掌握了石油化工技术的未来”。 1 渗透汽化过程传递机理 1.1溶解扩散模型 溶解扩散模型认为PV 传质过程分为三步: 渗透物小分子在进料侧膜面溶解(吸 附) ; 在活度梯度的作用下扩散过膜; 在透过侧膜面解吸(汽化)。 在PV 的典型操作条件下, 第三步速度很快, 对整个传质过程影响不大。而第一步的溶解过程和第二步的扩散过程不仅取决于高聚物膜的性质和状态, 还和渗透物分子的性质、渗透物分子之间及渗透物分子和高聚物材料之间的相互作用密切相关。因而溶解扩散模型最终归结到对第一步和第二步, 即渗透物小分子在膜中的溶解过程和扩散过程的描述。一般研究者都认为PV 过程的溶解过程达到了平衡[2]。对于这种考虑, 可以通过Henry 定律(对渗透物小分子和膜材料之间无相互作用力的理想情形) 或双方吸收模型(对渗透物小分子和膜材料之间存在较弱相互作用力的情形)或Flory-Huggins 模型(对渗透物小分子和膜材料之间存在较强相互作用力的情形) 计算得到渗透物小分子在膜表面的溶解度。近年来,Doong 等考虑到组分在膜中混合焓变、自由体积焓变、相互作用焓变和弹性焓变对总溶解焓变的影响, 提出了一个更为复杂的计算进料侧膜面组份活度的方法。 但实验发现, PV 过程的溶解过程并非总能达到平衡, 而是取决于溶解速度和扩散速度的相对大小[3]。余立新等通过实验发现了非平衡溶解过程的存在, 并提出了非平衡溶解扩散
渗透汽化技术简介及在水处理中的应用
渗透汽化技术简介及在水处理中的应用 渗透汽化(pervaporation,即 permeation vaporation,简称 PV),最先由Kober于20世纪初提出,是近年来发展比较迅速的一种膜技术,它是利用膜对液体混合物中各组分的溶解性不同及各组分在膜中的扩散速度不同从而得以达到分离目的。原则上适用于一切液体混合物的分离,具有一次性分离度高、设备简单、无污染、低能耗等优点,尤其是对于共沸或近沸的混合体系的分离、纯化具有特别的优势,是最有希望取代精馅过程的膜分离技术。 我国在1984年前后开始对渗透汽化过程进行研究,主要工作集中在优先透水膜的研制与醇水溶液的脱水。近年来主要开展优先透有机物膜、水中有机物脱除、有机物一有机物分离以及渗透汽化与反应耦合集中过程的研究。 一、渗透汽化的主要形式 按照形成膜两侧蒸汽压差的方法,渗透汽化主要有以下几种形式。 (1)减压渗透汽化 膜透过侧用真空泵抽真空,以造成膜两侧组分的蒸汽压差。在实验室中若不需收集透过侧物料,用该法最方便。 (2)加热渗透汽化 通过料液加热和透过侧冷凝的方法,形成膜两侧组分的蒸汽压差。一般冷凝和加热费用远小于真空泵的费用,且操作也比较简单,但传质动力比第一类小。 (3)吹扫渗透汽化 用载气吹扫膜的透过侧,以带走透过组分,吹扫气需经冷却冷凝,以回收透过组分,载气循环使用。
(4)冷凝渗透汽化 当透过组分与水不互溶时,可用低压水蒸气作为吹扫载气,冷凝后水与透过组分分层后,水经蒸发器蒸发重新使用。渗透汽化与反渗透、超滤及气体分离等膜分离技术的最大区别在于物料透过膜时将产生相变。因此在操作过程中必须不断加入至少相当于盘过物汽化潜热的热量,才能维持一定的操作温度。 二、渗透汽化的特点 (1)分离系数大。针对不同物系的性质,选用适当的膜材料与制膜方法可以制得分离系数很大的膜,一般可达几十、几百、几千,甚至更高。因此只用单极即可达到很高的分离效果。 (2)渗透汽化虽以组分的蒸汽压差为推动力,但其分离作用不受组分汽一液平衡的限制,而主要受组分在膜内渗透速率控制。各组分分子结构和极性等的不同,均可成为其分离依据。因此,渗透汽化适合于用精馅方法难以分离的近沸物和恒沸物的分离。 (3)渗透汽化过程中不引入其他试剂,产品不会受到污染。 (4)过程简单,附加的处理过程少,操作比较方便。 (5)过程中透过物有相变,但因透过物量一般较少,汽化与随后的冷凝所需 能量不大。 (6)渗透通量小,一般小于1000g/(m2 - h),而选择性高的膜,其通量只有100g/(m2?h)左右,甚至更低。 (7)膜后侧需抽真空,但通常釆用冷凝加抽真空法,需要由真空泵抽出的主要是漏入系统的惰性气体,抽气量不大。 三、渗透汽化适用的分离过程 (1)具有一定挥发性的物质的分离,这是应用渗透汽化法进行分离的先决条件。 (2)从混合液中分离出少量物质,例如,有机物中少量水的脱除,可以充
渗透汽化膜应用
有机汽体渗透分离膜 技术及工业应用 北京清源洁华膜技术有限公司 2015年9月
北京清源洁华膜技术有限公司座落在北京市平谷区兴谷开发区,是平谷区重点工业企业和北京市高新技术企业。公司以清华大学膜技术工程研究中心渗透汽化膜等专利技术为基础,从事渗透汽化、汽体渗透、透醇膜、超滤膜、纳滤膜等的研发生产。 北京清源洁华膜技术有限公司主要发起人全部毕业于清华大学,分别具有几十年的膜性能研发生产、化工工艺开发设计、化工设备加工制造、化工装置及企业生产管理经验,对国家环境保护工作的紧迫性及膜分离技术的先进性共同认知促成大家走到了一起。 膜分离技术被认为是21世纪最有发展前途的新技术之一,其中气体膜分离技术由于Prism 中空纤维氮氢分离器的问世,取得了空前的发展。气体膜分离技术与传统的吸附冷冻、冷凝分离相比,具有节能、高效、操作简单、使用方便、不产生二次污染并可回收有机溶剂的优点,已广泛用于空气分离富氧、富氮技术、天然气中脱碳、合成氨中的一氧化碳和氢气的比例调节等领域。 北京清源洁华膜技术有限公司作为清华大学膜技术工程中心生产、实验基地,拥有三项国家发明专利,分别是:一种渗透汽化优先透醇沸石填充硅橡胶复合膜的制备方法(专利号:ZL 2008 1 0105405.6;专利有效期:2008年4月30日至2028年4
月29日)、一种渗透汽化汽油脱硫用互穿网络膜的制备方法(专利号:ZL 2010 1 0282031.2;专利有效期:2010年9月14日至2030年9月13日)、二氮杂萘聚醚砜酮类聚合物平板超滤膜及其制备方法(专利证书号:ZL 2007 1 0177247.0;专利有效期:2007年11月13日至2027年11月12日)。 有机蒸汽膜法回收技术是上世纪八十年代兴起的新型膜分离技术,是气体分离膜应用的一个分支,依据溶解扩散分离原理,依靠有机汽体和空气各组分在膜中的溶解与扩散速度不同的性质来实现分离的新型膜分离技术,以混合物中组分分压差为分离推动力,有机汽体透过膜、空气不能透过膜。在化学、石化工业和医药工业中从废气中分离和回收有机蒸汽,炼油领域中分离有机蒸汽等应用越来越广泛。 有机蒸汽膜分离原理示意图: 用烷烃与空气混合气为介质测试有机蒸汽分离膜,分离膜对不同分子量的烃选择分离性能不同:
10第十章渗透气化
第十章渗透汽化 第一节概述 一、渗透汽化的发展概况 早在1917年Kober在他发表的一篇论文中第一个使用了渗透汽化(Pervaporation)这个词。该文介绍了水从蛋白质-甲苯溶液通过火棉胶器壁的选择渗透作用。但长期以来,由于未找到渗透通量高和选择性好的渗透蒸发膜材料,渗透蒸发过程一直没有得到应用。直到上世纪50年代以后,对渗透汽化的研究才较广泛展开。其中Binning等人对渗透蒸发过程进行了较系统的学术研究,发现了渗透蒸发过程潜在的工业应用价值,并于60年代在渗透汽化膜、组件和装置制造上申请了专利。70年代后期至80年代初,随着对能源危机问题的日益重视,渗透汽化的优点又重新引起学术界和技术界的兴趣,德国GFT公司在欧洲首先建立了乙醇脱水制高纯酒精的渗透蒸发装置。到90年代初已有100多套渗透蒸发装置相继投入应用。除了用于乙醇、异丙醇脱水外,还用于丙酮、乙二醇、乙酸等溶剂的脱水。 我国在1984年前后开始对渗透汽化过程进行研究,主要工作集中在优先透水膜的研制与醇水溶液的脱水。近年来主要开展优先透有机物膜、水中有机物脱除、有机物-有机物分离以及渗透汽化与反应耦合的集中过程的研究。 二、渗透汽化的分类 渗透汽化是以混合物中组分蒸汽压差为推动力,依靠各组分在膜中的溶解与扩散速率不同的性质来实现混合物分离的过程。渗透汽化装置包括预热器、膜分离器、冷凝器和真空泵等四个主要设备。料液进入渗透汽化膜分离器后,在膜两侧蒸汽压差的驱动下,扩散快的组分较多透过膜进入膜后侧,经冷凝后达到分离目的。 按照形成膜两侧蒸汽压差的方法,渗透汽化主要有以下几种形式: 1.减压渗透汽化:膜透过侧用真空泵抽真空,以造成膜两侧组分的蒸汽压差。在实验室中若不需收集透过侧物料,用该法最方便。 2.加热渗透汽化:通过料液加热和透过侧冷凝的方法,形成膜两侧组分的蒸汽压差。一般冷凝和加热费用远小于真空泵的费用,且操作也比较简单,但传质动力比第一类小。 3.吹扫渗透汽化:用载气吹扫膜的透过侧,以带走透过组分,吹扫气经冷却冷凝以回收透过组分,载气循环使用。 4.冷凝渗透汽化:当透过组分与水不互溶时,可以低压水蒸汽为吹扫载气,冷凝后水与透过组分分层后,水经蒸发器蒸发重新使用。 三、渗透汽化过程特点 渗透汽化与反渗透、超滤及气体分离等膜分离技术的最大区别在于物料透过膜时将产生相变。因此在操作过程中必须不断加入至少相当于透过物气化潜热的热量,才能维持一定的操作温度。 (一)渗透汽化特点: 1.分离系数大。针对不同物系的性质,选用适当的膜材料与制膜方法可以制得分离系数很大的膜,一般可达几十、几百、几千、甚至更高。因此只用单极即可达到很高的分离效果。 2.渗透汽化虽以组分的蒸汽压差为推动力,但其分离作用不受组分汽-液平衡的限制,而主要受组分在膜内渗透速率控制。各组分分子结构和极性等的不同,均可成为其分离依据。因此,渗透汽化适合于用精馏方法难以分离的近沸物和恒沸物的分离。 3.过程中不引入其它试剂,产品不会受到污染。
加热方式对渗透汽化过程的影响
文章编号:!""#$%&’((’""!)"($"""!$"(加热方式对渗透汽化过程的影响 韩宾兵陈翠仙!李继定 (清华大学化学工程系,北京!"""%( )摘要:利用渗透汽化平板膜浓度剖面和温度剖面的计算模型对乙醇脱水进行了模拟计算, 计算了外源不加热、恒温加热、恒功率加热、恒温差级间加热和恒膜面积级间加热)种加热方 式对水浓度剖面和温度剖面的影响,并比较了不同方式所需的单位面积加热功率*结果表明, 当料液中水含量较高时,外源加热是必须的;一般地讲,恒温加热和恒功率加热较级间加热所 需的膜面积小,但单位面积的加热功率相对较大* 关键词:渗透汽化;乙醇脱水;加热方式 中图分类号:+,"’%*%文献标识码:- 渗透汽化是用于液体混合物分离的一种新型膜技术[!!)]*渗透汽化过程中,渗透到膜后侧的渗透物组分需要吸收热量由液态变成汽态,这部分热量 由料液的显热即料液温度的降低提供*但料液温度 的降低将导致待分离组分的渗透通量下降,满足分 离要求所需的膜面积增加*因此当料液温度降低到 一定程度时,需用外源加热提高料液温度*本文研究 外源不加热、恒温操作、恒功率加热、恒温差级间加热和恒膜面积级间加热几种加热方式对渗透汽化过 程所需膜面积和单位面积加热功率的影响,以为工 业实际提供指导*!计算模型图!为描述渗透汽化平板膜过程的浓度剖面和温度剖面的计算模型示意图 * 图!渗透汽化过程平板膜计算模型示意图 假定待分离体系包括!个组分*温度为". (/,.代表进料)、体积流量为#.(0/1 )、第$组分的质量分数和热容分别为%.,$(2)、&’,.,$(3?4$!?/$!)的待分离体系进入分离膜,流经膜面后料液温收稿日期:’"""$"&$"% 基金项目:国家自然科学基金资助项目(’""’5!)作者简介:韩宾兵(!’!),男,山西省太谷县人,博士后,讲师*!通讯联系人第’!卷第(期 膜科学与技术 6.!*’! 7.*(’""!年%月898:;-79<=>97=9-7?+9=@7A 0A B C -4 """""""""""""""""""""""""""""""""""""""""""""""""""""""""""""""D *’""! 万方数据
渗透汽化膜分离法脱除汽油中有机硫化物的应用
渗透汽化膜分离法在脱除汽油中有机硫化物的应用 王雪1013207077 化学工艺13级博 渗透汽化技术又称渗透蒸发(Pervaporation,简称PV)技术作为一项新兴膜分离技术,以其高效、经济、安全、清洁等优点,在石油化工、医药、食品、环保等领域广泛应用,成为目前膜分离研究领域的热点之一。该技术用于液体混合物的分离,其突出的优点是能够以低的能耗实现蒸馏、萃取、吸附等传统方法难于完成的分离任务。它特别适用于蒸馏法难以分离或不能分离的近沸点、恒沸点混合物及同分异构体的分离;对有机溶剂及混合溶剂中微量水的脱除及废水中少量有机污染物的分离具有明显的技术和经济优势。 一、基本原理 渗透汽化是利用膜对液体混合物中各组分的溶解扩散性能的不同,实现组分分离的一种膜过程,见图1(a)。在渗透汽化过程中,料液侧(膜上游侧)通过加热提高待分离组分的分压,膜下游侧通常与真空泵相连,维持很低的组分分压,在膜两侧组分分压差的推动下,各组分选择性地通过膜表面进行扩散,并在膜下游侧汽化,最后通过冷凝的方式移出1。有机溶剂脱水渗透汽化分离的原理见图1(b)。 图1(a)Schematic diagram of pervaporation process2 图1 (b)有机溶剂脱水渗透汽化分离的原理
二、渗透汽化膜 1.有机膜 渗透汽化的主要作用元件是渗透汽化膜,膜的性能对渗透汽化过程有决定性的影响。渗透汽化膜按照功能可分为亲水膜、亲有机物膜和有机物分离膜3种。亲水膜又称为优先透水膜,其活性分离层又含有一定亲水性基团的高分子材料制成,具有一定的亲水性。目前应用最广泛的亲水性商品膜是GFT膜,其分离层是聚乙烯醇。在全球商业化的渗透汽化装置中,约90%的GFT膜都是由德国预案GFT公司及其相关单位开发的。目前已有相关学者开始研究亲水性膜在火箭燃料肼、不对称二甲肼和甲肼脱水过程中的应用3456。亲有机物膜又称优先透有机物膜,通常由低极性、地比表面积和溶解度参数小的聚合物(如聚乙烯、聚丙烯、有机硅聚合物、含氟聚合物、纤维素衍生物和聚苯醚等材料)制成。尽管亲有机物膜在渗透汽化膜分离过程中具有非常高的潜在应用价值,且世界范围内对该膜已有广泛研究,但目前能实现工业化应用的还很少。有机物分离膜可适用的分离体系多且性质差异大,膜材料的选择没有普遍规律,必须针对分离体系的物理化学性质进行选择和设计,主要有芳烃-烷烃分离膜、醇-醚分离膜以及同分异构体分离膜。 2.无机膜 相对于有机膜,无机膜具有优良的热稳定性、化学稳定性、机械稳定性、耐酸碱、微生物侵蚀和耐氧化性等优点。这些优点使无机膜的发展备受科技界的重视,具有非常广阔的应用前景7。无机膜按材料可分为陶瓷膜、合金膜、高分子金属配合物膜、分子筛膜和玻璃膜等。多孔无机膜的制备方法主要有:固态粒子烧结法、溶胶-凝胶(Sol-Gel)法、阳极氧化法、薄膜沉积法、分相法和水热合成法等。已经商品化的多孔膜主要是超滤和微滤膜,其制备方法以粒子烧结法和Sol-Gel法为主。粒子烧结法制备的膜孔径范围一般在0.1~10μm,适应于微孔过滤。目前已开发的商品化微滤膜主要有氧化铝膜、氧化钛膜和氧化锆膜。 Sol-Gel技术可以制备超滤范围的小孔径膜,目前采用该技术制备的已经商品化的超滤膜有氧化铝膜、氧化钛膜、氧化硅膜和氧化锆膜8。近年来,有关Sol-Gel 技术的研究主要集中在制备孔径小于2 nm的纳滤膜和气体分离膜。分子筛膜作为无机膜的一种,具有良好的热稳定性、化学稳定性和分离选择性。通过调节硅铝比可以调节分子筛膜的亲疏水性,如高硅铝比的MFI分子筛膜具有很强的疏水性,而低硅铝比的A分子筛膜具有很强的亲水性。另外,分子筛本身具有催化活性,通过分子筛膜可以从分子水平上实现分离和催化一体化;同时由于分子筛的孔径尺寸一定,所以在催化反应中具有择形性。这些优越性使得分子筛膜具有良好的应用前景。分子筛膜的种类很多,根据不同的应用目的选择不同的制备方法,其制备方法主要有原位水热合成法910、二次生长法1112131415、嵌入法1617和
ch10组合变形
第十章 组合变形 10-2 图a 所示板件,b =20mm , =5mm ,载荷F = 12 kN ,许用应力[] = 100 MPa , 试求板边切口的允许深度x 。 题10-2图 解:在切口处切取左半段为研究对象(图b ),该处横截面上的轴力与弯矩分别为 F F =N )(a b F M -= (a) 显然, 2 22x b x b a -=-= (b) 将式(b)代入式(a),得 2 Fx M = 切口段处于弯拉组合受力状态,该处横截面上的最大拉应力为 2 2N max 432(2a)6 22a Fx a F Fx a F W M A F δδδδσ+ =+=+= 根据强度要求,在极限情况下, ][4322 σδδ=+a Fx a F 将式(b)与相关数据代入上式,得 01039.61277.042=?+--x x 由此得切口的允许深度为 m m 20.5=x
10-3 图示矩形截面钢杆,用应变片测得上、下表面的纵向正应变分别为a ε=×10 -3 与b ε=×10-3 ,材料的弹性模量E =210GPa 。试绘横截面上的正应力分布图,并求拉力F 及其偏心距e 的数值。 题10-3图 解:1.求a σ和b σ 截面的上、下边缘处均处于单向受力状态,故有 MPa 84Pa 104.010210 MPa 210Pa 100.1102103 9 39=???===???==--b b a a E εσE εσ 偏心拉伸问题,正应力沿截面高度线性变化,据此即可绘出横截面上的正应力分布图,如图10-3所示。 图10-3 2.求F 和e 将F 平移至杆轴线,得 Fe M F F ==,N 于是有 a z a E εW Fe A F σ=+= E εW Fe A F σz b =-= 代入相关数据后,上述方程分别成为 26250240=+Fe F 10500240=-Fe F
膜分离实验装置
实验十膜分离实验装置 一、实验目的 1.了解超滤膜分离的主要工艺设计参数。 2.了解液相膜分离技术的特点。 3.训练并掌握超滤膜分离的实验操作技术。 4.熟悉浓差极化、截流率、膜通量、膜污染等概念。 二、实验原理 膜分离是近数十年发展起来的一种新型分离技术。常规的膜分离是采用天然或人工合成的选择性透过膜作为分离介质,在浓度差、压力差或电位差等推动力的作用下,使原料中的溶质或溶剂选择性地透过膜而进行分离、分级、提纯或富集。通常原料一侧称为膜上游,透过一侧称为膜下游。膜分离法可以用于液-固(液体中的超细微粒)分离、液-液分离、气-气分离以及膜反应分离耦合和集成分离技术等方面。其中液-液分离包括水溶液体系、非水溶液体系、水溶胶体系以及含有微粒的液相体系的分离。不同的膜分离过程所使用的膜不同,而相应的推动力也不同。目前已经工业化的膜分离过程包括微滤(MF)、反渗透(RO)、纳滤(NF)、超滤(UF)、渗析(D)、电渗析(ED)、气体分离(GS)和渗透汽化(PV)等,而膜蒸馏(MD)、膜基萃取、膜基吸收、液膜、膜反应器和无机膜的应用等则是目前膜分离技术研究的热点。膜分离技术具有操作方便、设备紧凑、工作环境安全、节约能量和化学试剂等优点,因此在20世纪60年代,膜分离方法自出现后不久就很快在海水淡化工程中得到大规模的商业应用。目前除海水、苦咸水的大规模淡化以及纯水、超纯水的生产外,膜分离技术还在食品工业、医药工业、生物工程、石油、化学工业、环保工程等领域得到推广应用。 表10-1、各种膜分离方法的分离范围 膜分离类型分离粒径(μm) 近似分子量常见物质 过滤>1 砂粒、酵母、花粉、血红蛋白 微滤0.06-10 >500000 颜料、油漆、树脂、乳胶、细菌超滤0.005-0.1 6000-500000 凝胶、病毒、蛋白、碳黑 纳滤0.001-0.011 200-6000 染料、洗涤剂、维生素 反渗透<0.001 <200 水、金属离子
渗透汽化膜分离研究的新进展
综 述 渗透汽化膜分离研究的新进展 夏德万1,2,张 强1,2,施艳荞23,赵 芸1,矫庆泽1,陈观文2 (11北京理工大学化工与环境学院,北京 100081; 2.中国科学院化学研究所,北京 100080) 摘要:渗透汽化膜分离技术是当前分离膜研究领域的前沿课题之一。作为化学分离中的重要组成部分,近年来受到高度重视。本文按渗透汽化膜分离的三大类混合液体系有机液脱水、从水相中分离有机物和有机混合液的分离,综述了近几年渗透汽化膜分离技术研究的新进展。其中,又重点报道了有机混合液分离的最新研究成果,将其分为:极性Π非极性化合物、芳香烃Π脂肪烃体系、芳香烃Π脂环烃体系、同分异构体、多元体系和汽油脱硫等六部分进行了详细叙述。文章最后还对渗透汽化膜分离研究进行了展望。 关键词:渗透汽化;膜;分离 渗透汽化(Pervaporation,简称PV)是在液体混合物中组分蒸汽压差推动下,利用组分通过膜的溶解与扩散速率的不同来实现分离的过程。自上世纪八十年代渗透汽化实现产业化以来,在世界范围内,已有320套渗透汽化工业装置在运行,成为膜分离技术的前沿领域之一。 渗透汽化特别适于蒸馏法难以分离或不能分离的近沸或共沸混合液的分离;对有机溶剂中微量水的脱除或废水中少量有机物的分离,以及水溶液中高价值有机组分的回收,具有相变质量小、效率高、能耗低、设备简单、工艺放大效应小等优点。与蒸馏法相比,PV用于从工业酒精生产无水乙醇节能75%;用于从含水15%的异丙醇生产无水异丙醇节能65%;用于酯化反应生产乙酸乙酯节能58%。PV分离效果突出,已经显示出可喜的应用前景,被学术界认为是21世纪化工领域最有前途的高新技术之一。本文基于近几年来报道的最新研究结果,综述了渗透汽化膜分离技术的研究进展。 1 用于有机液脱水的渗透汽化膜 长期以来渗透汽化的研究工作基本集中在水Π醇体系的分离,特别是水Π乙醇体系的分离。原德国G FT公司(现属瑞士Sulzer Chemtech)以聚乙烯醇(PVA)为膜材质,对水优先透过渗透汽化膜首先进行了系列产业化。至今各国仍然有很多水Π乙醇体系分离方面的研究,研究者们希望获得性能更好的水Π乙醇体系分离膜。 水Π醇体系的分离中另一重要部分是水Π异丙醇的分离。Anjali等[1]用与2,42二异氰酸甲苯酯交联的脱乙酰度84%的壳聚糖膜PV分离异丙醇中的水,并对未交联的和交联的膜进行动态热力学分析,评价了其热力学稳定性。这种膜能很好地打破共沸平衡,膜厚为10μm时,水Π异丙醇选择分离系数达472,水渗透通量为0139kgΠ(m2h)。Vijaya等[2]将纳米尺度(30~100nm)的聚苯胺(PANI)粒子分散在PVA中,制得纳米复合膜,并用其在30℃下PV分离含水10%~50%的水Π异丙醇混合物,实验发现纳米复合膜的渗透通量低于均质PVA膜,而选择分离性则大大提高了。K ittur等[3]在壳聚糖中混入NaY沸石而制得一种有 基金项目:国家重点基础研究发展计划资助项目(2003C B615701); 作者简介:夏德万(19832),男,湖北省通山县人,硕士研究生,主要从事分离膜的研究。 3通信联系人:施艳荞,E2mail:g wchen@https://www.360docs.net/doc/741980423.html,
渗透蒸馏、渗透汽化、分子蒸馏的异同
渗透蒸馏、渗透汽化、分子蒸馏的异同 渗透蒸馏,又称为等温膜蒸馏,是基于渗透与蒸馏概念而开发的一种渗透过程与蒸馏过程耦合的新型膜分离技术,它具有一般膜分离技术投资省、能耗低的优点,同时又能在常温常压下使被处理物料实现高倍浓缩,克服常规分离技术所引起的被处理物料的热损失与机械损失,特别适合处理热敏性物料及对剪应力敏感性物料,从而使渗透蒸馏在食品、医药及生化领域展示出广阔的应用前景。 分子蒸馏亦称短程蒸馏,其应用能解决大量常规蒸馏技术所不能解决的问题。分子蒸馏是一种特殊的液—液分离技术,依据分子运动平均自由程的差别,能使液体在远低于其沸点的温度下将其分离,特别适用于高沸点、热敏性及易氧化物质的分离。分子蒸馏进行时,液体混合物被加热,能量足够的分子逸出液面,轻分子的平均自由程大,重分子的平均自由程较小,若在离液面小于轻分子平均自由程而大于重分子平均自由程处设置一冷凝面,轻分子达到冷凝面后被冷凝,从而使其不断逸出;重分子达不到冷凝面,很快趋于动态平衡,这样就将混合物分离了。分子蒸馏技术的主要特点是其操作是在远低于沸点温度和很低的压强下进行操作的。 渗透汽化是以混合物中组分蒸汽压差为推动力,依靠各组分在膜中的溶解与扩散速率不同的性质来实现混合物分离的过程。渗透汽化装置包括预热器、膜分离器、冷凝器和真空泵等四个主要设备。料液进入渗透汽化膜分离器后,在膜两侧蒸汽压差的驱动下,扩散快的组分较多透过膜进入膜后侧,经冷凝后达到分离目的。 从诞生时间上说,渗透蒸馏、渗透汽化、分子蒸馏这三种技术均是新型的蒸馏分离技术,其中的分子蒸馏技术甚至是一项较新的尚未广泛应用于工业化生产的分离技术。其基本原理都是将沸点不同的液体气化从而达到液-液分离的目的,并利用了表面化学的原理,利用膜分离技术,增大了蒸馏分离的效率和分离出物质的纯度,节约了能源,提高了生产效率。 但是,这三种蒸馏技术也是有其独特特点和适用范围的。 一、渗透蒸馏过程及其特点 渗透蒸馏是指被处理物料中易挥发性组分选择性的透过疏水性的膜,在膜的另一侧被脱除剂吸收的膜分离操作,在通常情况下,被处理物料与脱除剂均为水溶液,渗透蒸馏过程能够 顺利进行是由于被处理物料中的易挥发组分在疏水膜的两侧存在渗透活度差,被处理液中的易挥发组分在疏水膜两侧的渗透活度相等,即蒸汽压力差不再存在时,则渗透蒸馏过程将停止进行。渗透蒸馏包括三个连续的过程:被处理物料中易挥发组分的汽化;易挥发组分选择的通过疏水性膜;透过疏水性膜的易挥发性组分被脱除剂所吸收。渗透蒸馏除了一般膜分离技术所具有的投资省、能耗低的特点以外,还具有优良的导热性能、适宜高倍浓缩及良好的选择性等。 二、分子蒸馏技术的特点: 分子蒸馏技术作为一种与国际同步的高新分离技术,具有其它分离技术无法比拟的优点: 1、操作温度低(远低于沸点)、真空度高(空载≤1Pa)、受热时间短(以秒计)、分离效率高等,特别适宜于高沸点、热敏性、易氧化物质的分离; 2、可有效地脱除低分子物质(脱臭)、重分子物质(脱色)及脱除混合物中杂质; 3、其分离过程为物理分离过程,可很好地保护被分离物质不被污染,特别是可保持天然提取物的原来品质; 4 、分离程度高,高于传统蒸馏及普通的薄膜蒸发器。 三、渗透汽化过程特点。 渗透汽化与反渗透、超滤及气体分离等膜分离技术的最大区别在于物料透过膜时将产生
精馏-渗透汽化膜技术回收乙腈的应用实例
头孢曲松钠是瑞士Roche 公司1982 年上市的广谱长效抗菌素,其使用剂量小、毒副作用小,具有很大市场份额,是第三代具有广谱抗菌活性的头孢菌素。在实际生产中,由原料7-ACA制取头孢曲松钠粗品时,乙腈作反应用溶剂,反应结束后,产生的乙腈母液经过分离得到一定质量指标的回收乙腈再次作为反应溶剂循环使用。 传统工艺:在生产过程中,乙腈不可避免地与水及其它杂质混在一起,产生乙腈废液。由于乙腈会与水会形成恒沸物(常压下乙腈-水恒沸物含水量约16 wt.%),采用常规精馏方法无法将乙腈废液直接分离精制成可再次使用的反应溶剂(溶剂乙腈含水量通常≤0.05wt.%)。而从此工艺路线来看,回收乙腈的质量对头孢曲松钠粗品的质量起着决定性的影响。 而采用精馏-渗透汽化膜技术可以有效解决以上问题。 新工艺:将头孢曲松钠合成中的乙腈废液进入提浓塔,采用精馏方式脱除部分水与重组分;提浓后得到乙腈馏液送入中和罐调节酸碱度;将中和后的乙腈馏液送入除杂塔进一步除杂,乙腈馏液在除杂塔中脱除杂质后,进入渗透汽化膜分离机组,釜残液返回前级提浓塔回收其中的乙腈;经渗透汽化膜分离机组分离后得到粗品乙腈,料液侧溶液中的水以及少量乙腈以蒸汽形式透过渗透汽化膜得到渗透液,渗透液冷凝后返回中和罐后再次回收其中的乙腈;
渗透汽化分离机组得到的粗品乙腈送入精制塔进行精制,得到成品乙腈,精制塔馏出的乙腈-水恒沸物返回至除杂塔回收其中的乙腈。 新工艺流程图: 1是预热器,2是提浓塔,3是中和罐,4是除杂塔,5是过热器,6是渗透汽化分离机组,7是渗透液冷凝器,8是真空泵,9是精制塔。 江苏九天高科技股份有限公司是集研发、生产、销售、服务于一体的国家高新技术企业,致力于提供溶剂分离整体解决方案和优质服务,可用于生物医药、石油化工、精细化工、新能源等领域的有机溶剂分离和提纯。公司自主开发出针对不同应用领域和应用体系的溶剂分离及脱水工艺,通过成套化、标准化的系统研究与开发,实现了预处理系统、分离及脱水系统、节能系统、加热制冷系统和控制系统的模块化集成和全自动化控制。公司提供从技术研发、工艺设计、设备制造、工程实施、项目运营在内的定制化溶剂分离整体解决方案,欢迎新老客户来电垂询,莅临考察。
渗透汽化膜分离技术及其在石油化工中的应用
科技论坛在当前我国石油化工行业发展的过程中,由于渗透汽化膜分离技术有着高效、经济等方面的特点,因此得到了人们的广泛应用。这不仅使得石油化工产品的生产质量的效率得到进一步的提高,还很好的满足了现代化石油化工行业经济发展的相关要求。而且随着社 会的不断发展,人们将一些先进的科学技术应用到其中,这就使得渗透汽化膜分离技术的各方面应用效果得到有效的提高。下面我们就对渗透汽化膜分离技术以及在石油化工中的实际应用进行简要的介绍。1渗透汽化膜分离技术的基本原理 所谓的渗透汽化膜也就是根据液体混合物中各个组成成分的溶解扩散性的不同,利用膜来对其进行分离的一种过程。而在此过程中,人们则是通过渗透汽化的方式,在对其溶液进行加入,使得组分中的分压提升,使其膜在分压的推动下,来将溶液中存在的物质进行有效的处理,这就使得溶液的汽化分离效果得到有效的提升。2渗透汽化膜 2.1有机膜。我们在对溶液进行渗透汽化的过程中,渗透汽化膜在其中有着十分重要的意义,它的质量问题直接对整个渗透汽化分离的效果有着严重的影响。因此我们对渗透汽化膜的选着有着十分重要的意义。目前我们在对容易进行渗透汽化时,所采用的膜有很多种,我们可以根据其功能的不同将其划分成亲水膜、亲有机膜以及有机分离膜这三种。这三种不同的渗透汽化膜在不同的环境下,其自身的应用效果也就存在着一定的差异,因此为了保障其自身的应用效果,我们就需要采用相应的技术手段来对其进行选取,从而 满足人们的相关要求。 目前在我国工业生产的过程中,主要是采用有机膜,这样不仅使得工业生产的质量得到了有效的保障,还节约了工程使得施工成本,从而使其经济效益得到了进一步的提高。而且随着科学技术的不断进步,人们也将许多先进的技术手段应用到其中,这就使得渗透汽化膜分离技术的应用效果得到进一步的提高。 2.2无机膜。在渗透汽化分离技术应用的过程中,无机膜由于有着量额稳定性和耐氧性,因此子啊当前我国工业生产的过程中,也得到了人们的广泛应用。其中我们可以根据使用的材料不同将其划分成陶瓷膜、合金膜以及玻璃膜等,这种不同材料的无机膜在实际应用的过程中,其效果也不一样,为此我们在对其进行施工的过程中,就要根据其实际情况,来对其进行选取,从而使其应用效果得到有效的保障。2.3有机-无机复合膜。有机-无机复合膜兼顾了有机膜和无机膜的优点,其制备方法通常为Sol-Gel 法。将有机-无机复合膜用于渗透蒸发还处于研究阶段,目前已商品化的有机-无机复合膜是一种交联的聚二甲基硅氧烷-硅酸盐/聚丙烯腈复合膜,可用于高度水溶性有机物的去除。3渗透汽化膜组件 渗透汽化过程使用的膜组件可根据不同的膜材料和膜形状进 行选择,膜组件可以分为板框式、螺旋卷式、圆管式和中空纤维式4种。有机膜主要采用板框式膜组件,便于分离器内物料的加热并减小渗透侧气体的流动阻力。而管状无机膜主要采用圆管式膜组件。为了降低温度极化和浓度极化效应导致膜分离性能降低的影响,阐述了一种新型恒温管式膜组件,原料液在由管状膜与加热腔形成的 环形夹层中进行换热和分离,原料液通过加热腔中的加热介质直接加热, 供给混合物分离所需的热量。该膜组件可用于渗透汽化和蒸汽渗透膜分离过程, 也可用于膜分离与催化反应相结合以强化酯化反应、 酯交换反应等的催化膜反应器。4渗透汽化在石化中的应用渗透汽化被开发为工业实用技术,至今已有20多年的历史。国际上相继建成了100多套工业装置,这不仅证明了这一新型膜分离技术的可靠性,而且表明其在技术上具有先进性,充分显示出作为“绿色节能工艺”的优势和竞争力。 4.1有机溶剂脱水。渗透汽化技术在有机溶剂脱水领域的工业化应用得到迅速发展, 广泛应用于醇类、酮类、醚类、酯类、胺类、酸类等有机溶剂的脱水。在膜材料方面, 除了应用范围最广的聚乙烯醇/聚丙烯腈复合膜外, 世界范围内对无机膜(如分子筛膜)的开发和应用也在迅速发展。它是一种在多孔氧化铝载体上制备NaA 分 子筛膜的方法, 所制备的NaA 分子筛膜在乙醇、异丙醇等有机溶剂的渗透汽化脱水过程中表现出优异的分离性能。在此基础上,实现了NaA 分子筛膜的工业化应。 目前,在日本正在运行的NaA 型分子筛膜渗透汽化分离装置已有60多套。 相关学者以液体硅酸钠、铝酸钠和氢氧化钠为原料,在一种流动体系中制备了工业应用规格的 NaA 分子筛膜, 并建立了年生产能力100t 无水乙醇的分子筛膜渗透汽化分离装置, 该装置也可用于乙醇、异丙醇、四氢呋喃等有机溶剂的渗透汽化脱水, 且分离性能优良。采用该装置对乙醇溶剂进行连续脱水100h 的考察, 实验结果表明,该装置具有良好的稳定性。4.2废水中有机物的脱除。工业废水中除含有易挥发性有机物外,往往还含有各种盐类,目前要处理该类工业废水非常困难。如果采用传统的直接燃烧法, 盐类会腐蚀燃烧炉;如果采用普通的废水处理法,其中的有机物又会破坏后续生化处理过程中的生物活性。 采用渗透汽化技术则可以实现盐溶液和有机物的分离, 然后再采用传统方法分别处理盐溶液和有机物。 4.3有机混合物的分离。在石油化工领域,常常有大量的有机混合物需要分离, 如从石脑油中回收甲苯、苯乙烯等芳香烃;降低燃料汽油中芳香烃的含量等。对于相当部分恒沸物、 近沸物或同分异构体且它们含量差别较大的体系, 采用渗透蒸发技术,利用膜的选择性进行该类有机混合物的分离, 相对于传统的精馏法具有明显的优势。在芳烃-脂肪烃混合物的分离中, 苯和环己烷的分离是最典型的 结束语 总而言之,在在我国是由化工行业发展的过程中,渗透汽化膜分离技术的实际应用,不仅使得石油化工技术的应用效果得到进一步的提升,还满足现代化石油化工行业发展的相关要求,从而使其生产质量得到有效的提高。而且随着科学技术的不断进步,人们也将许多先进的科学技术应用其中,这就使得渗透汽化膜分离技术的 应用效果得到进一步的提高。参考文献[1]张小明,吕高孟,雷骞,索继栓.流动体系中NaA 分子筛膜的制备及 渗透汽化分离性能研究[J].膜科学与技术, 2010(1).[2]张雄福,王金渠,刘长厚.ZSM-5型沸石膜的合成及应用于乙苯脱 氢反应研究进展[J].膜科学与技术, 2001(2).渗透汽化膜分离技术及其在石油化工中的应用 李健 (哈尔滨石油化工设计院,黑龙江哈尔滨150000) 摘要:在现代化社会经济发展的过程中,石油化工行业的发展有着十分重要的意义,这不仅有利于社会经济的发展,还有效的提高了人们的生活质量,满足了人们日常生活的进步要求。而且随着时代的不断进步,人们为了使得石油化工生产效率和质量得到有效的保障也将许多先进的科学技术应用到其中,这就很好的满足了现代化石油化工行业发展的相关要求。其中渗透汽化膜分离技术的应用,就使得石油化工技术的应用效果得到进一步的提升。通过对渗透汽化膜分离技术的工作原理进行简要的介绍,讨论了渗透汽化膜分离技术在石油化工生产当中的实际应用,以供参考。 关键词:渗透汽化膜分离技术;石油化工;应用分析 19··