欧派嘉板式家具生产过程质量检验标准

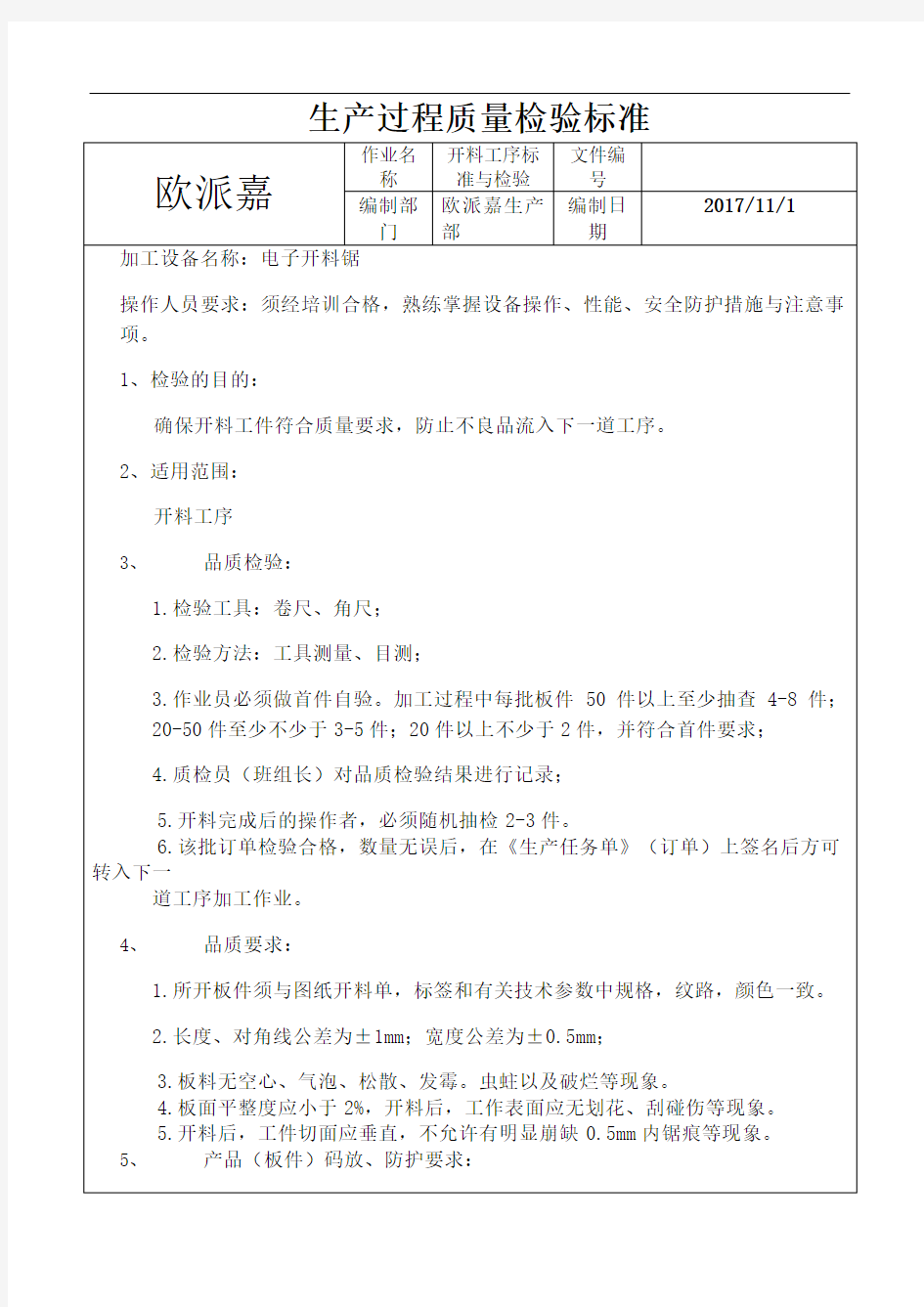
欧派嘉板式家具生产过程质量检验标准
集团文件版本号:(M928-T898-M248-WU2669-I2896-DQ586-M1988)
生产过程质量检验标准
生产过程质量检验标准
生产过程质量检验标准
生产过程质量检验标准
生产过程质量检验标准
板式家具加工工艺及检验标准
板式家具加工工艺及检验标准 一、基材 板式家具的基本材料是刨花板和中密度纤维板,这两种板是可以用工业化生产方式进行大规模生产的工程材料。从材料来源、幅面尺寸和加工性能方面来说,它们不象实木和其它材料,对家具的设计和制造约束很少,因此家具设计师和制造商可以不受材料的限制,而完全根据用户不同品味的需要,设计和制作功能实用、风格各异的家具. 刨花板:将木材加工剩余物或小径材、枝桠材加工成一定形状尺寸刨花,施加一定量胶粘剂,经铺装成型热压而成。按结构分为普通板和定向板两类,而普通型刨花板又可分为单层、三层、渐变三种结构。家具用板以渐变和三层结构为主。通常用平压法制造。 刨花板主要优点是可按需加工成不同厚度大幅面的板材;可直接使用;不需干燥;易加工。利于机械化生产;运输保存方便;价格便宜。其缺点是边部毛糙,易吸湿变形,吸水厚度膨胀率较大;握螺钉力较低,紧固件不宜多次拆卸;容积重通常高于木材,刨花板家具较重,横向构件易产生下垂变形等。 我国刨花板产品质量差异较大,一般来讲引进国外先进设备,生产管理较好的企业产品质量较好,各项指标均能达到国家标准,但中、小企业刨花板产品质量均较差,表现在刨花形态差、施胶量高、刨花板吸水厚度膨胀率超过10%、厚度尺寸偏差大于土1.2mm、扭曲度大于10mm、刨花板饰面性能(砂不光、不能贴面)、封边性能均较差。刨花板产品质量低劣,在我国刨花板生产中普遍存在的问题。而它恰恰正是发展板式家具的一个最大障碍。 用于家具的刨花板应适合于家具的生产特点。西方发达国家虽然对刨花板按其用途不同而规定若干种具有不同性质的刨花板,而实际上还根据用户定货或用途的不同要求,提供特制的满足某些性能指标要求的刨花板。我国各地发展刨花板的
家具主要生产工序的质量标准及技术措施
家具主要生产工序的质量标准及技术措施 提高家具产品的质量就是要使家具产品的功能、外观、规格、安全性达到相应的标准。家具产品的质量是在生产过程中形成的,必须在家具主要生产工序中运用设备、材料、工艺、管理、人员、环境等各种技术措施预防和消除不符合质量标准的产品出现。 1、生产准备 产品批量生产前应做“产前样”,经整体组装合格后才可进行批量生产;批量生产中应定时做抽样检查进行跟踪。 生产前对设备、刀具、模具、夹具进行检查,使这处于完好状态。 2、材料的质量标准 2.1对损害制品外观和结构的材料(端裂、蜂窝裂、表面裂、腐蚀、变色等),不得使用。 2.2拼板用材的含水率要在6%~8%之间,其他加工材料一般木材含水率在8%~12%。 2.3节疤在材面宽度方向上小于宽度的25%,并要进行适当的修补及处理。 2.4要根据涂饰要求选用不同等级的木材:浅色透明涂饰类用A级木材;深色半透明涂饰类 用B类木材;不透明及贴纸类用C级木材。雕刻产品不得用软质木材。浅色涂装的木材不允许有污渍,深色涂装要以能遮盖为原则。 2.5明处用料不得用腐朽材,暗处轻微腐材面积不得超过15%,深度不得超过材厚的25%。 不得有贯通的裂纹。虫蛀材须经杀虫处理。产品中,受力部件用材的斜纹角度不得超过20°。 2.6木材干燥质量检验标准 含水率及应力质量标准(表1) 干燥后外观质量标准(表2) 3、毛料加工的质量标准 3.1拼板 原料上不可有缺陷,厚度、宽度、长度误差在允许范围内。木材必须经过干燥处理,木材的含水率为8~10%。相邻拼件含水率差≤2%。 锯切面平整光洁,并保持锯切面之间的平行,工件之间的长度误差不超过工件长度 1.0%~1.5%。 木材正反纹理搭配拼合,材质颜色力求统一。拼缝<0.2㎜。涂胶应厚薄均匀一致,不缺胶和溢胶,严格按预定的涂胶工艺操作。 拼板时工作要以基准和基准边固定并夹紧。一个装夹工们上不可同进装夹2个拼合部件,以免压力不均。 3.2四面刨 检查形刀具是否正确、刀刃的钝化程度。组合型刀具保持完好状态。不应有缝隙及接刀痕迹。 根据零部件要求选好材质,调整设备。使加工产品尺寸、形状准确,无跳刀和加工缺陷。 3.3指接 指接不允许有死节、朽木、虫眼、树心等缺陷。长度余量为10mm~50mm。 指榫与指榫显露面必须确保垂直。指接部位无缝隙。 3.4带锯成型 曲线锯截时模具应准确。严格按照模板划线,划线与模板间隙1mm。
32mm系统板式家具设计准则及生产工艺
32mm系统板式家具设计准则及生产工艺 一、“32mm"系列自装配家具 板式家具摒弃了框式家具中复杂的榫卯结构,而寻求新的更为简便接合方式,就是采用现代家具五金件与圆(棒)榫连接。而安装五金件与圆榫所必需的圆孔由钻头间距为32mm的排钻加工完成的。为获得良好的连接,“32mm系统”就此在实践中诞生,并成为世界板式家具的通用体系,现代板式家具结构设计被要求按“32mm系统”规范执行。 所谓“32mm系统”是指一种新型结构形式与制造体系。简单来讲,“32mm”一词是指板件上前后、上下两孔之间的距离是32mm或32mm的整数倍。在欧洲也被称为“EURO”系统,其中E-Essential knogledge,基本知识;U-Unique tooling ,专用设备的性能特点;R-Required hardware,五金件的性能与技术参数;O-Ongoing Obility,不断掌握关键技术。 32mm系列自装配家具,也称拆装家具(Knock Down Furniture,KD),并进一步发展成为待装家具(Ready To Assemble,RTA)及DIY(Do It Yourself)家具。 32mm系列自装配家具,其最大的特点是产品就是板件,可以通过购买不同的板件,而自行组装成不同款式的家具,用户不仅仅是销费者,同时也参与设计。因此,板件的标准化、系列化、互换性应是板式家具结构设计的重点。 另外,32mm系列自装配家具,在生产上,因采用标准化生产,便于质量控制,且提高了加工精度及生产率;在包装贮运上,采用板件包装堆放,有效地利用了贮运空间,减少了破损、难以搬运等麻烦。 二、 32mm系统的设计准则 “32mm系统”以旁板的设计为核心。旁板是家具中最主要的骨架部件,顶板(面板)、底板、层板以及抽屉道轨都必须与旁板接合。因此,旁板的设计在32mm系列家具设计中至关重要。在设计中,旁板上主要有两类不同概念的孔:结构孔、系统孔。前者是形成柜类家具框架体所必须的结合孔;后者用于装配搁板、抽屉、门板等零部件必须的孔,两类孔的布局是否合理,是32mm系统成败的关键。 ㈠系统孔 系统孔一般设在垂直坐标上,分别位于旁板前沿和后沿。若采用盖门,前轴线到旁板前沿的距离(K)为37(28)mm;若采用嵌门或嵌抽屉,则应为37(或28)mm加上门板
板式家具通用检验标准
一、各项检验通用标准规定 说明:①、各封边带加工后尺寸标准 a、PVC胶边:加工后厚度为1.3mm/两边(即0.65mm/边) b、纸边:加工后厚度为0.8mm/两边(即0.4mm/边) c、科技木皮:加工后厚度为1.5mm/两边(即0.75mm/边) d、天然木皮:加工后厚度为1.5mm/两边(即0.75mm/边)
e、木皮封边带厚度均以采购厚度0.6mm为准 ②、所有零部件图规格尺寸均不含封边带厚度尺寸。 3、产品外观检验规定(特殊设计除外)单位:mm
二、产品外观等级要求 A级要求 1、表面平整,表面缺陷点要求每0.5平方米不超过一处,缺陷点直径≤0.5mm。 2、表面崩边处连续修补长度不超过封边长度的约3%。 3、表面不能有划痕、碰伤、爆裂。 4、封边胶合紧密平直,不能有松脱、缺损现象。 5、站在0.5-0.8米远处,不可见修补痕。正常规定视力≥1.0。 6、表面颜色均匀,无明显色差。 7、修补后,单个的瑕疵要求直径小于0.5mm。 B级要求 1、表面平整,表面缺陷点要求每0.5平方米不超过三处,缺陷点直径≤0.5mm。 2、表面崩边处连续修补长度不超过封边长度的约5%。 3、表面不能有划痕、碰伤、爆裂。 4、封边胶合紧密平直,不能有松脱、缺损现象。 5、站在0.5-0.8米远处,不可见修补痕。正常规定视力≥1.0。 6、表面颜色均匀,无明显色差。 7、修补后,单个的瑕疵要求直径小于0.5mm。 C级要求 1、表面平整,表面缺陷点要求每0.5平方米不超过四处,缺陷点直径≤0.5mm。 2、表面崩边处连续修补长度不超过封边长度的约10%。 3、表面允许有轻微划痕、但不允许有碰伤、爆裂现象。 4、封边胶合紧密平直,不能有松脱、缺损现象。 D级要求 1、表面平整,不允许有碰伤、爆裂现象。 2、边缘平齐,不能有崩裂现象。 三、产品检验区域(通常分为A、B、C三区)
家具车间生产工艺标准
家具车间生产工艺标准 家具生产主要有材料配料、零件加工、产品组装、砂磨涂装、成品包装五个工艺过程,这五个工艺流程也称为家具生产的基础流程。 一、备料 概述:就是运用家具备料所需要的机械设备和工具,在备料车间对家具毛料或素材进行一系列的加工操作,用来供应生产所需。备料是家具生产的第 一道工序,俗话说“万丈高,从地起”,备料工艺水平的高低,直接影响 整个家具产品的质量。 工艺流程:备料包括选料、断料、开料(裁板/压板/贴皮/封边)、平刨、压刨、拼板、弯矩成型等工序。 质量要求: 1、拼板时尽量将颜色相近的材料拼在一条拼缝上,保持板面颜色基本一致。 2、备料规格不能太大,更不能缩小,长度保持在1-1.5厘米,宽厚度保持在 0.5-0.8厘米左右的砂光或精切余量。 3、所有材料必须保持方正、平直,杜绝拼缝空隙出现。上胶水时必须将胶水 均匀涂布在木材表面,不能过多或过少,以拼实后表面有芝麻大小胶粒溢 出为宜,拼板必须保持一面平整,一头整齐,确保材料利用率。 4、锯裁后的板件必须与实际尺寸要求相符,大小头之差应小于2mm。当板件 长度L为:1000mm<L<2500mm时,允许公差为2mm(极限偏差为土lmm)。 当板件长度L<1000mm时,允许加工公差为lmm(极限偏差为士0.5mm)。 5、截面应平整、与邻边垂直,不允许有波浪、发黑、毛刺、锯痕、崩边等现 象。
6、冷压后部件表面应干净、平整,不可有明显的骨架印痕,弯曲变形,划痕 及多余涂胶现象。 7、板芯条要紧密,表面平整,过渡自然无胶水污染。 8、热压贴皮拼花必须保证木纹走向与要求相符,粘贴必须牢固、平滑,不允 许脱胶、离层、气泡、划花、折皱、烂纸、压痕及其它杂物等现象。 9、封边要保证严密、平整、胶合牢固、无脱胶、溢胶、漏封、叠封、撕裂和 跑边现象;表面无划花、刮伤、碰伤、压痕、胶痕等缺陷;接口部位平顺,不能在显眼位置。 注意事项: 1、备料过程中的选料事关重大,要严格按设计要求使用相关材料,不得随意 更改任何配件之材质。材料的毛边,以及有撕裂、凹陷、压痕、虫孔、腐朽、斑点、节杷、变形等现象的尽量不予使用。 2、严格按订单要求成套生产(包括小配件)。 3、下料前必须弄清楚材料长短宽窄(规格)和它所在的位置,尽量将正规材 料用在表面上。 4、裁板:①、板材进锯时,应平起平落,每次开料最好不得超过两层。 ②、冷压件布胶必须均匀,胶水必须适量、木纹方向必须一致、压力必须适当、加压时间适宜,板件胶合应牢固,不允许有脱胶现象,板件辅入时,必须与骨架相邻两边取齐,冷压后上、下板位置偏差小于1.5cm。 5、热压贴皮拼花必须注意材料含水率、木皮薄片质量、板材质量、木皮拼缝 间隙、木纹走向、热压温度、热压时间、胶水用量及施布等。 6、封边:封边包括喷防粘剂,齐边铣削,工件预热,涂胶,施压封边,封边
板式家具生产工艺流程
板式家具生产工艺流程 一个完整意义上的板式家具生产工艺流程要从原材料的准备,经过木工制作、油漆涂饰到最后产品包装入库等诸多环节和步骤组成。因为油漆工序在上两期《深圳家具》上已有一些专业人士详尽论述过,所以本次板式生产工艺重点针对木工工序。提到板式家具生产工艺在很多人看来十分简单,三步一体的开料、封边、打孔,所用的设备也无外乎开料锯、封边机、排钻。结构要点无非是32系列拆装连接件等,其实实际上的板式家具生产工艺要远比这些复杂得多,同样是一块板件,有些只要一两道工序就可以完成,而有些则十数道甚至数十道工序才能够完成。如抽屉底板,只要开料就可以,而如一块较复杂的地柜面板其结构是蜂窝空心,面木皮,边实木封边且有边型,上面还要镶嵌玻璃。单一面板的加工就要二十几道工序才能完成,所以说板式工艺的复杂程度同产品的外观设计、产品结构、用料以及生产线上产品品种的种类数量等诸多因素息息相关,涉及的要素越多就越复杂。板式生产工艺的主要构成要素:原材料、工艺文件、机器设备、操作工人以及相应的品质和生产管理系统。其中原材料准时到位是整个工艺流程的前提和基础,而工艺文件则是整个加工流程和管理活动的行动依据,工艺文件要全面细致。板式家具工艺文件大概有:效果图、三视图、零部件分解图、零部件加工图、五金配件清单、包装方案、安装示意图、原材料明细表(BOM)、零部件加工工艺流程表、产品使用说明书。其中零部件加工图要与零部件加工工艺流程表结合使用并与生产线上的零部件产品同步运行效果最佳。零部件加工流程表里面的主要内容要涵盖名称、规格、数量、用料、批次、加工注意事项、特殊检验标准、工时、工序及序列号等基本内容。
家具质量标准
江苏炜赋集团公司富豪家具分公司 文件编号:FH-W 01 二OO二年九月
目录 第一章产品加工要求(除涂装)………………………第二章涂装加工要求……………………………………第三章产品结构标准……………………………………第四章产品品质及检验标准……………………………
制订、变更及执行程序 一、目的:针对本公司及外协产品制订本加工要求及品质标准, 指导生产和测量、检查、监控。 二、执行范围:本公司及外协所有的产品加工。包含所有产品的 产品设计、生产制造以及品质检验的全过程。外协加工单位(组织)的生产制造、品质检验也按此标准执行。 三、制订、变更程序 1、本《产品加工要求及品质标准》由生产技术部、品 质管理部联合制订。 2、涉及到运作过程中的变更、修改和充实,必须由班 组逐级上报经审核后阶段性修改变更和充实,审核者为生产技术部和品质管理部。 3、变更后的标准应有变更记录,并送达各有关部门。 四、执行程序 本《产品加工要求及品质标准》由生技部、品管部共同制订后报总经理室审批执行。
第一章产品加工要求 一、原木加工及干燥要求 1、原木应小头进锯,锯解板材厚度公差为+1MM~-0.5MM; 2、排板隔条厚度要求均匀,容许厚度误差为1MM;两端隔条距板端100MM; 3、隔条在材堆中放置间隔合理,上下保持垂直,垂直度公差5MM; 4、木材干燥应无内裂,无明显端裂、无过度弯曲、翘曲,含水率均匀; 5、木材出窑含水率为6-8%。 二、配料加工要求 1、实木面框拼接料宽度≤80MM,长度超过1米的拉档和玻璃门框不允许使用独根材料; 2、拼板应无明显色差,无明显胶线; 3、刨光后无跳痕、无焦黑痕、无蓝斑、无横茬;平整光滑; 4、板材厚度公差+0.2MM,不得有大头小身; 5、有虫孔的木料不可使用; 6、面框配料加工厚度尺寸+0.5~+0.2MM;组框后需铣型边的面框料宽度尺寸放3MM加工余量,面框深度尺寸+0.5~0.2MM; 7、人造板封边的配料厚度尺寸为人造板厚度尺寸+0.6~0.2MM; 8、直边牙板厚度、宽度尺寸为+0.4MM,曲边牙板宽度放2MM 加工余量,与脚耳相配的牙板宽度为+0.2MM; 9、需铣型、仿型、车型无方身的脚配料放3MM加工余量; 10、零件必须方、正、平、直; 11、显木纹油漆产品胶拼部件颜色必须相近,木纹必须对称; 12、显木纹油漆产品所有零件不许有明显木材缺陷,外表部件无腐朽、变色、死节、开裂、过大黑线等缺陷,内部零件可允许存在不影响外观的轻微缺陷,但必须修补合格后下发;
板式家具质量检测标准书
板式家具质量检测标准书 检验名称板材料质量检验文件阶层三阶文件 编制部门门柜文件编号 SP-WI-P-001 编制日期 2010-3-26 版本/版次 V1.0 页码 1 of 12 检验的内容:人造板质量检验 检验的意义: (1)确保进厂材料、物品符合标准。 (2)防止生产过程中出现各种材料问题异动。 序号检验项目质量检验标准(技术要求)检验方法 1 材质质量检验 1、基材为中密度纤维板符合GB/T11718.1供应商提供国家技术监督局的相应——1999中的室内型板物理学性能指产品检测报告。 标要求; 2、基材为刨花板符合GB/T 4897.1~ 4897.7- 2003室内型板物理学性能指 标要求; 3、甲醛释放量达到国家室内用材的标准 其释放量?1.5mg/升。 2 外观质量检验 1、一面无明显划伤、凹坑、鼓包、鼓泡、目测。 黑色斑点、污渍等缺陷,另一面允许不 大于30?长的划伤2处,直径不大于 3mm的黑色斑点两处; 2、表面木纹纹路一致,凹凸部分匀称,纹
理清晰,色泽一致。 3、每批到货颜色一致,不同批允许不明显 色差。 3 外观尺寸厚度误差??0.3?,长度、宽度误用精度为0.1?的游标卡尺测量 差??3? 厚度,误差不大于?0.6?的3 米卷尺测量长度、宽度。 4 翘曲度翘曲度值?2?;用每米误差不大于?0.6?的刚尺 测量将产品凹面向上放置在水平台 面上,用线绳连接两对角,用钢直尺 量取最大弦高,最大弦高与对角线之 比即为翘曲度 5 邻边垂直度用钢卷尺测量两对角线,其差值用每米误差不大于?0.6?的3 即为邻边垂直度偏差要求?2? 米卷尺测量。 更改记录更改日期编制审核审批 检验名称衣柜功能件质量检验文件阶层三阶文件 编制部门门柜文件编号 SP-WI-P-002 编制日期 2010-3-26 版本/版次 V1.0 页码 2 of 12 检验的内容:衣柜功能件质量检验 检验的意义: (1)确保进厂材料、物品符合标准。 (2)防止产品安装过程中出现各种材料问题异动。 1、拉篮、鞋架、领带架的检验 1) 对照标准色板的颜色比较颜色是否相同,整批货颜色是否一致;
浅谈家具生产工艺流程与质量要求及注意事项
浅谈家具生产工艺流程与质量要求及 注意事项 1
2
浅谈家具生产工艺流程与质量要求及注意事项 家具生产主要有备(配)料、机加工(细作)、安(组)装、涂装、包装五个工艺过程,这五个工艺流程也称为家具生产的基础流程。 家具生产工艺在很多人看来十分简单,比如现代板式家具,三步一体的开料、封边、打孔,所用的设备也无外乎开料锯、封边机、排钻。结构要点无非是32系列拆装连接件等,其实实际上的板式家具生产工艺要远比这些复杂得多,同样是一块板件,有些只要一两道工序就能够完成,而有些则十数道甚至数十道工序才能够完成。如抽屉底板,只要开料就能够,而如一块较复杂的地柜面板其结构是蜂窝空心,面木皮,边实木封边且有边N型,上面还要镶嵌玻璃。单一面板的加工就要二十几道工序才能完成,因此说家具工艺的复杂程度同产品的外观设计、产品结构、用料以及种类、数量等诸多因素息息相关,涉及的要素越多就越复杂。 家具生产工艺的主要构成要素:原材料、工艺文件、机器设备、操作工人以及相应的品质和生产管理系统。其中原材料准时到位是整个工艺流程的前提和基础,而工艺文件则是整个加工流程和管理活动的行动依据,工艺文件要全面细致。家具工艺文件大概有:效果图、三视图、零部件分解图、零部件加工图、五金配件清单、包装方案、安装示意图、原材料明细表、零部件加工工艺流程表、产品使用说明书。其中零部件加工图要与零部件加工工艺 3
流程表结合使用,并与生产线上的零部件产品同步运行效果最佳。零部件加工流程表里面的主要内容要涵盖名称、规格、数量、用料、批次、加工注意事项、特殊检验标准、工时、工序及序列号等基本内容。机器设备和操作工人则是加工保障。 家具的主要生产工艺流程,因其类别、款式、装饰效果的不同也有不尽相同的工艺流程,比如家具从材质上分有板式家具、实木家具、五金家具、软体家具、混合家具等;从类别上分有酒店家具、民用家具、学校家具、公共家具、儿童家具等等;从款式上分有美式家具、欧式家具、中式家具、明清家具、仿古家具等等;从结构上分有整装家具、拆装家具等告示。因此,在实际操作过程中,因为受类别、款式、结构与成本等因素的影响,工艺流程与质量要求也尽不相同。 在这里,由于受版面限制,我们只从一般常见木家具来简单谈谈家具生产工艺流程与质量要求及注意事项的基本原则。 一、备(配)料 概述:就是运用家具备料所需要的机械设备和工具,在备料车间对家具毛料或素材进行一系列的加工操作,用来供应生产 所需。备料是家具生产的第一道工序,俗话说”万丈高,从 地起”,备料工艺水平的高低,直接影响整个家具产品的质 量。 工艺流程:备料包括选料、断料、开料(裁板/压板/贴皮/封边)、 4
家具生产品质检验标准文件
家具生产品质检验标准文件 第一节来料检验标准文件 来料检验,是品质检验工作的第一关,优质材料是制造优质产品的基础和保障1、来料检验的内容。 (1) 原材料检验:如木材、板材、木皮等。 (2) 辅助材料检验:如油漆、胶水、补土等。 (3) 耗材检验:如砂布、砂纸、砂轮片、碎布等。 (4) 配件检验:如螺丝、拉手、轨道、合页、饰条、玻璃、大理石等。 (5) 包装材料检验:如内箱、外箱、珍珠棉、标签等。 (6) 刀具、工具检验:如各种锯刀、电动工具、气动工具、手动工具等。 (7) 外协产品检验:如外协电镀零部件、贴面板、椅子白坯等。 2、来料检验的意义 (1) 确保进厂材料、物品符合标准。 (2) 防止生产过程中出现各种材料问题异动。 (3) 防止采购过程中出现舞弊行为。 1 一、木材来料质量检验标准书 1、木材品质控制目的 为备料、白身、油漆提供符合效率原则、品质要求的材料保证。 2、配合部门 为了有效地控制材料品质,在以品管部为主要归品管理部门之下,需要物控部,生产部、财务部、仓库以及备料车间予以积极配合,协力控制好材料的进厂检验和综合利用工作。 3、订货要求
在产品订货来到时,按标准通知供应商准备好标准品木材,以不同供应商已供货产品进行质量跟踪,对不同时期供应材料的质量进行客观评分,建立供应高质量表,经常联系供应商将质量评分的结果反馈给对方,把本厂的质量验收标准贯彻到对材料供应商的具体要求上,对于长期供尖优良品质材料的供应商予以一定的优先,以鼓励供应商按本厂材料质量标准供应合格的材料。 4、具体操作 (1) 在订货时向供应商下达具体要求。 (2) 严格按来料检验结果对供应商进行甄别。 (3) 严格按来料检验结果进行退货和扣款处理。 5、质量标准 检验方法参照美国阔叶材协会制定的《阔叶材分等标准》的要求。制定验收和检验标准如下: 木材供应标准要求分三等:第一等、第二等可混合为一个等级,但对桦木、椴木一等材所占比例不得小于20%,如长期达到此要求则检验可以适当放松或在付款期上给予优惠。第一等、第二等材的标准是符合备料车间加工效率最高要求的标准,达到此等标准的木材可以减小选料时间,三等材为次品,供应商不得长期提供此等材,等外材为不能达到标准等级,且综合利用率较低的材料,应作退货处理。 (1) 尺寸公差 长度:标准在1M以上,可以有150MM以下的余数长度。 宽度:所有品等制材记载最小宽度者,同一品等为90%须具足过宽度,其余10%可以容许5MM以下的宽度不足。 厚度:厚度应就板材最薄处测定,最厚处与最薄处(除弧边外)的级差限定如下; 厚度在25MM以下,限度为3MM。 厚度在25~50MM限度为4MM。
板式家具通用工艺标准
优越板式家具通用工艺标准 拟制: ______________ 校对:______________ 批准:_______________ ________________________________________________________________ 本标准由鹤山工艺部编制 1、本标准最终解释权归鹤山工艺部 2、任何部门与个人未经工艺部许可不得擅自复印或带出厂,违者严惩。 前言 随着公司规模的日益壮大,分厂不断的增多.,原来工艺技术标准已越来越不适应公司快速发展的步伐。加之由于标准的不统一,给各厂的生产带来了许多不便。甚至引起了技术标准上的混乱。为了避免这种不良现象,保证工艺标准上的唯一性,标准性。准确性,促使公司的工艺标准准确有序的流通。现鹤山工艺部拟制一套工艺技术标准来规范工艺技术标准的实施。 本标准对公司板式家具的基本生产工艺进行了透彻的分析,特别是对优越板式的工序工艺环节剖析深入、内容详尽。介绍了优越板式家具术语与工艺、常用材料、工序工艺标准,优越板式家具综合标准等。 由于水平有限、加之时间仓促。对公司的工艺技术深知甚少,还有许多工艺内容没能写进去,板式家具的工艺是一个在实践中不断摸索革新和完善的过程,只有更好没有最好。标准中如有错误与不妥与之处,敬请各位同仁批评、指正并衷心希望您提出宝贵的意见,以便修改。 目录 第一章:板式家具常用术语 第一节:工艺与工序 第二节:术语 第二章:优越家具常用材料 第一节:板材介绍 第二节:常用蜂窝纸与封边带 第三节:常用五金原材料及规格 第四节:常用小五金及排钻参数 第五节:常用玻璃及工艺要求
第六节:常用铝材及工艺要求 第七节:油漆的配比与工艺要求 第八节:纸箱与工艺要求 第九节:常用刀具 第三章:优越家具工序工艺标准 第一节:板式家具工艺概述 第二节:开料 第三节:压板 第四节:精切 第五节:封边 第六节:排钻 第七节:木工 第八节:批灰 第九节:油漆 第十节:装配 第十一节:包装 第十二节:五金 第四章优越板式家具综合标准 第一节:制图规范 第二节:图纸的种类 第三节:生产表格 第四节:优越板式家具工艺流程 第五节: 第六节: 第七节: 第八节: 第九节: 第十节: 第一章优越家具工艺与术语 第一节:工艺与工序 1、工艺的定义 通过各种加工设备改变原材料的形状、尺寸或物理性质,将原材料加工成符合技术要求的产品时,所进行的一系列工作的总和称为工艺过程,简称工艺。 2、工序 一个(或一组)工人在一个工作位置上对一个或几个工件连续完成的工艺过程的某一部分操作称为工序 3、优越家具生产工艺分为板式家具工艺、实木家具工艺、软体家具工艺、金属家具工艺等 第二节:术语
家具涂膜质量标准
家具涂膜质量标准 轻工业部为促进全国木家具涂饰质量的提高和统一全国木家具徐沛质量标准,特制定木家具涂饰标准(SG279-83),现将基本内容介绍如下。 (一)涂饰分级 按产品的材料和加工工艺不同,将涂饰分为普、中、高三级。 I 普级涂膜表面为原光(即不磨水砂、不抛光)。 2.中级正视面涂膜表面须磨水砂、抛光或为亚光,制品侧面涂膜为原光。 3.高级徐膜表面为全抛光或填孔亚光。 (二)涂饰材料 1.普级普级产品使用的涂料有酚醛、醉酸、酯胶等质地较差的树脂涂料。 2.中级中级产品正视面使用的涂料同高级产品,侧视面同普级产品。 3.高级高级产品使用涂料有聚氨酯、聚酯、丙烯酸、硝基、光敏、天然漆等性能较好的涂 料。 (三)技术要求 1.涂饰前产品表面处理步骤 第一产品的涂饰部位应清除油脂(松脂、矿物油)、腊质、盐分、碱质及其它污染残迹。 第二涂饰前的产品表面应平整、光滑、无刨痕和砂痕、线条、棱角等部位应完整无缺 第三高级产品涂饰前应去处木毛。 2.涂层外观要求
不同产品涂层外观要求分别列于表51、表5-2和表53。古铜色除图案要求不同外, 其余要求均同表5-3规定;填纹孔型亚光涂层除光泽要求不同外,其余要求均同表5-2、表5-3规定;不透明涂层除不显木纹外,其余要求均同表5-1、表5-2、表5-3规定。 表5-1普级产品涂层外观要求 表5-2 中级产品涂饰外观要求
3.涂饰样板更换须定期更换。 4.涂膜的理化性能按表5-4 规定。表5-4 涂膜的理化性能规定
注:①理化性能中耐温、耐水、耐酸、耐碱、耐磨系指家具面子部位的要求; ②轻微失光指光泽比试验前减少5~10%; ⑶硝基清漆的耐温度可比表中的规定降低10度 三、涂膜理化性能检测 涂膜理化性能主要取决于涂料的性能,同时跟涂层工艺也有一定的关系。对于质量相 的同类涂料,若涂饰工艺(即涂饰质量)不同, 则涂膜的理化性能(如附着力、光泽度、耐液性等)就会有所差异。涂料的种类和质量不同,即使涂饰工艺相同,涂膜的理化性能定会有较大的区别。如不饱和聚酯涂料涂膜的光泽度,耐磨性要优于聚氨酯涂料的,但涂膜的弹性却比聚氨酯涂料的低,所以涂膜的理化性能是涂料性能与涂饰工艺的综合性反应。涂膜的理化性能应根据产品的等级与用途合理确定,以确保产品使用功能的科学要求。 涂膜理化性能有各种各样,现国标GB4893.14893.885“家具表面漆膜测定法”规定了涂膜耐液、耐湿热、耐干热、耐温差、附着力、厚度及光泽度的测定方法;涂膜的弹性、硬度、透明度等性能的测定,涂料制造行业也有相应的检测方法与检测标准。在此仅简单介绍徐膜主要理化性能的测试方法。 (一)涂膜耐液测定法 1.试液家具涂膜接触的主要液体的性能及规格如表6-1所示。 表6-1 家具涂膜接触的主要液体
家具生产质量控制
家具生产质量控制 8093010 钟超 摘要:质量是企业的生命,就企业而言,要提高经济效益,从根本上讲必须提高产品质量。没有质量就没有数量,没有质量就没有经济效益,产品质量既是数量的基础,又是经济效益的基础。因此,加强生产过程质量控制不断提高产品质量从来都是企业发展,提升市场竞争力的最主要的手段之一。 关键词:家具、工艺、质量控制 1、生产质量控制 质量控制是为了达到质量要求所采取的作业技术和活动,其目的在于为了监视过程并排除质量环所有阶段中导致不满意的因素,以此来确保产品质量。从一个理想的产品设计由图样变成实物,是在生产制造过程中实现的。要保证家具的质量,必须加强对生产过程的质量进行控制。 家具生产过程质量控制的核心是使生产作业经常处于稳定受控状态,发挥工艺的保证作用,通过质量分析,找出可能产生质量缺陷的因索,采取既结合实际,又切实可行的预防措施,把废次品和返修品减少到最低限度。 将家具的整个制造过程进行分析,从产品角度来看,外部采购用以生产的原辅材料、半成品、成品应视为制造过程的输入环节,交付出厂或入库的成品、半成品应视为制造过程的输出环节,而内部所有生产制造工序将构成过程的中间要素活动(图1)。 在家具制造工业中,由于加工工艺过程是由较为复杂的工序组成的,在经过整个生产流水线的加工过程中,缺陷常会一个接一个地出现。因此,只检验最后的制成品是不够的.必须严格控制整个生产过程中每一道工序的加工质量,即从第一道工序起就进行控制。家具生产质量控制根据制造过程划分,主要分为:生产前的质量控制,生产过程中的质量控制,生产后质量控制。 针对不同的制造过程,各个家具公司应结合自身情况,根据各工序工艺参数的配置选择方面、设备管理方面应注意的细节和生产操作方面的一些生产实际经验,解决生产过程中的生产质量问题所用的一些方法,制定相应的质量控制计划,以便能够稳定地、持续地生产符
板式家具各项操作规范标准[详]
《板式家具标准操作规》 在板式家具生产过程中,选择和使用适合于各个家具厂具体情况的封边热熔胶, 不但能提升板式家具的品质和档次,而且可以提高生产效率,减少板件整修的难度,减轻工人劳动强度。 笔者长期从事木工和家具用胶粘剂的技术和市场工作, 下面就板式家具用封边热熔胶的选择和使用,提出一些心得和体会,希望能对我国板式家具生产水平的提升有所帮助。)目录: 1.封边热熔胶的选择 2.封边热熔胶的使用 3.排钻作业指导书 4.推台锯作业指导书 5.冷压订装作业指导书 6.安装作业指导书 7.包装作业指导书 8.封边作业指导书 9.排钻作业指导书
一.封边热熔胶的选择 封边热熔胶(Edgebanding Hot-MeltAdhesive)是一类专用于人造板材封边的胶粘剂,它是一种无溶剂的热塑性胶。热熔胶被加热到一定温度时,即由固态转变为熔融态户当涂布到人造板基材或封边材料表面后,冷却变成固态,将封边材料与基材粘接在一起。对封边热熔胶的选择和使用,必须注意下列几个方面: (1)封边热熔胶按基料的不同可分为三类: (1.1)EVA (乙烯-醋酸乙烯共聚树脂)基料热熔胶,这种热熔胶又可分为有填料和无填料两类。 (1.2)采用EVA 作为基料是最普通的封边热熔胶生产技术,它主要的局限是耐热性能较差。 (1.3)用EVA 热熔胶封边的板式家具的使用环境温度不能高于120C; (2)POL YAMIDE(聚酰胺)基料热熔胶,这种热熔胶具有很好的耐热性能和快速固化的特点,主要缺点是价格昂贵。 (3)HMPU(聚氨脂)基料热熔胶,它是性能最好的一类热熔胶,是高质量板材封边的保证。它价格昂贵,需要特殊的使用方法。 封边热熔胶的粘度封边热熔胶的粘度并不能直接反映胶的性能好坏。 一般情况下,封边热熔胶的粘度越高,它的初粘强度越好,但涂布性能越差。 低粘度热熔胶的涂胶量较小, 润湿性能更好。某些粘度低 固化速度很快的热熔胶,也有可能具有高的初粘强度。 对于质量差的刨花板,封边需要选用粘度较高的热熔胶,这是因为高粘度的热熔胶流动性差,涂胶时不像低粘度的热熔胶那样容易进入刨花板边部的孔隙中, 从而使热熔胶能充分涂在板材边缘。
板式家具企业标准
企业标准 木家具质量检验及质量评定
目次 前 言 (1) 引 言 (2) 1主题容与适用围 (1) 2 引用标准 (1) 3 术语 (2) 4 检验类 (3) 5 制程检验 (4)
6 最终检验 (5) 7 板式家具的整体外观检验 (6) 8 板式家具的原材料进料验 (7) 9 五金配件的检验 (8) 前言 本标准依据国家标准GB/2828-2000《木家具通用技术条件》和行业标准GB/2828《木家具质量检验及质量评定》并结合企业产品特点制订而成。
1 本标准部分技术条件要求在国家标准的基础上有所提高。 2 本标准的检验项目及容在国家标准的基础上所增加,主要的项目和容有: (1)产品外观要求 (2)各工序工艺要求 (3)外协件,外购件要求 (4)原材料要求 3 本标准检验项目及要求质量保证零部件的质量;用零部件的质量保证产品生产的全过程;用工艺要求的质量保证零部件的质量,用零部件的质量保证产品的整体实现. 4 本标准偏重于产品生产工艺过程的预防性控制检验,强调从原材料到生产过程中甚至成品要做到过程与结果统一. 本标准由企业厂部提出: 本标准起草部门: 本标准起草人: 标准审批: 引言
企业产品质量检验及质量评定标准,是企业产品质量检验及质量评定的依据,本标准规定了本企业产品一木家具检验分类,检验项目,检验规则,试验方法程序和检验结果的评定;特别是检验项目含盖了本企业产品生产工艺的全部过程,对于规本企业的质量检验工作,建立完善的质量检验体系将产生重要的作用,是企业质量保证体系的建立与实施的基础性文件. 木家具质量检验及质量评定 1 主题容及适用围 本标准规定了木家具的检验分类,检验项目,抽样规则,试验方法,
板式家具质量标准
菲莱公司板式家具质量标准 一:下料 1、确认产品颜色,下料尺寸与图纸吻合,尺寸误差±0.5mm。 2、副锯台≤0.2mm,不能出现明显崩茬。 3、当部件小于1000mm*500mm时对角线误差≤1mm,大于此尺寸的部件对角线误差控制在2mm以内,超过此误差极为不合格产品。 4、所有面板、门板、抽面、侧板及重要部件板材必须严格检查,保证正面无划伤、磕碰、杂质、蹦茬等各种质量问题。顶底、层板、背板等次要部分的板件质量标准可以相对放松一点,但必须保证没有明显磕碰、掉角、蹦茬及严重划伤! 5、严格按照料单纹理方向下料,料单上部件规格为〖长(纵向)*宽(横向)*厚度〗,任何人不得以任何理由擅自改动纹理方向。如特殊情况可以请示领导(不论哪位领导同意必须在下料单上签字)。但面板、门板、抽面以及所有在柜体组装好后可以看见的部件不得改变纹理方向。 6、码放整齐,每个产品的所有部件放在一起,每家客户的订货为一个批次 7、严格控制每家顾客所有产品的色差,要保证以家为单位用同一批次的板材。 二:铣型 1、检查下料组送过来的部件是否与料单一致,清点数量、规格、颜色。核对无误后再铣型。
2、所有需铣型产品图样必须保证与图纸一致。 3、,根据料单提供的轨道样式确定开槽位置。 4、所有模板的制作要保证与图纸一致,线条流畅、圆滑无明显弯曲现象,开槽宽度与深度必须与轨道吻合。 5、选用合适刀头,保持刀头锋利,不得出现蹦边现象。铣型时用力要均匀,完全按照模板形状。 6、所有铣型部件完成后需用砂纸磨平,防止封边不严,如因铣型不平造成的封边脱落现象由铣型组负全责。 三:封边 1、先看料单,与料单核对颜色与部件数量、尺寸。看下料组是否有多下、漏下、错下现象,尺寸是否与料单吻合。 2、所有面板、门板、抽面、侧板及重要部件板材必须严格检查,保证正面无划伤、磕碰、杂质、蹦茬等各种质量问题。顶底、层板、背板等次要部分的板件质量标准可以相对放松一点,但必须保证没有明显磕碰、掉角、蹦茬及严重划伤! 3、粘贴要牢固,胶量要适中。 4、胶线要控制在肉眼观察不明显的范围之内,不能出现明显白线或黑线。 5、压力要合适,保证封边长时间使用不脱落。 6、铣刀角度要正确,薄厚边要区分清楚,不得刮伤板面。 7、分清先后顺序,先封后面,再封两边,最后封前面。坚持先背后面,先纸后薄的原则,不得封错。
板式家具通用检验标准
一、各项检验通用标准规定 1、产品部件形状和位置公差的规定单位: mm 2、抽屉、门各边与框架的分缝(特殊设计分缝除外)的规定单位:mm
说明:①、各封边带加工后尺寸标准 a、PVC胶边:加工后厚度为1.3mm/两边(即0.65mm/边) b、纸边:加工后厚度为0.8mm/两边(即0.4mm/边) c、科技木皮:加工后厚度为1.5mm/两边(即0.75mm/边) d、天然木皮:加工后厚度为1.5mm/两边(即0.75mm/边) e、木皮封边带厚度均以采购厚度0.6mm为准 ②、所有零部件图规格尺寸均不含封边带厚度尺寸。 3、产品外观检验规定(特殊设计除外)单位:mm
二、产品外观等级要求 A级要求 1、表面平整,表面缺陷点要求每0.5平方米不超过一处,缺陷点直径≤0.5mm。 2、表面崩边处连续修补长度不超过封边长度的约3%。 3、表面不能有划痕、碰伤、爆裂。 4、封边胶合紧密平直,不能有松脱、缺损现象。 5、站在0.5-0.8米远处,不可见修补痕。正常规定视力≥1.0。 6、表面颜色均匀,无明显色差。 7、修补后,单个的瑕疵要求直径小于0.5mm。 B级要求 1、表面平整,表面缺陷点要求每0.5平方米不超过三处,缺陷点直径≤0.5mm。 2、表面崩边处连续修补长度不超过封边长度的约5%。 3、表面不能有划痕、碰伤、爆裂。 4、封边胶合紧密平直,不能有松脱、缺损现象。 5、站在0.5-0.8米远处,不可见修补痕。正常规定视力≥1.0。
6、表面颜色均匀,无明显色差。 7、修补后,单个的瑕疵要求直径小于0.5mm。 C级要求 1、表面平整,表面缺陷点要求每0.5平方米不超过四处,缺陷点直径 ≤0.5mm。 2、表面崩边处连续修补长度不超过封边长度的约10%。 3、表面允许有轻微划痕、但不允许有碰伤、爆裂现象。 4、封边胶合紧密平直,不能有松脱、缺损现象。 D级要求 1、表面平整,不允许有碰伤、爆裂现象。 2、边缘平齐,不能有崩裂现象。 三、产品检验区域(通常分为A、B、C三区) 1、 A区:通常指产品使用时常处于视野范围内前方,面对视野,容易看到的区域; 如:面板、门板、抽面板、高屏背板前面、低屏背板前面、各类脚类及层板、侧板、底板等部件的前面部位。 2、 B区:通常指产品使用时处于视野范围内的左或右方、前面底下方,可看到但不经常看到;
家具行业执行标准
家具行业执行标准 标准编号标准名称发布单位生效日期状态DB37/T 1726-2010 家具售后服务规范山东省质量技术监督局2011-02-01 现行DB44/T 1055-2012 家具五金自弹型和液压缓冲型杯状暗铰链广东省质量技术监督局2012-11-15 现行DB44/T 1082-2012 家具材料分类广东省质量技术监督局2013-02-28 现行DB44/T 1174-2013 橡木家具通用技术条件广东省质量技术监督局2013-11-24 现行DB44/T 1214-2013 板式家具售后安装服务要求广东省质量技术监督局2014-03-06 现行DB44/T 1223-2013 核桃木家具通用技术条件广东省质量技术监督局2014-03-06 现行DB44/T 823-2010 藤家具广东省质量技术监督局2011-03-01 现行DB44/T 824-2010 办公家具木制多媒体会议台广东省质量技术监督局2011-03-01 现行DB44/T 941-2011 家具配件万向脚轮广东省质量技术监督局2012-03-01 现行DB51/ 348-2011 软家具床垫安全技术条件四川省质量技术监督局2011-06-01 现行DB54/T 0031-2009 藏式家具通用技术规范西藏自治区质量技术监. 2009-08-14 现行DBl2/T 384-2008 家具产品标识标注规天津市质量技术监督2009-01-01 现行FZ/T 62011.3-2008 布艺类产品第3部分:家具用纺织品国家发展和改革委员会2008-10-01 现行GB/T 10357.1-2013 家具力学性能试验第1部分:桌类强度和耐久性国家质量监督检验检疫. 2014-05-01 现行
板式家具工序标准与要求内容
板式家具各工序工作围及流程要求 一、下料 a、工作围:所有从设计部所下料单,以及在生产过程中出现的部件损坏需补料的板件。 b、工作权利:监督设计部所有料单,对料单有疑问可以直接与设计部沟通,对不合理之处提出合理化建议。监督采购部所采购的板材,看板材是否有严重质量问题及色差,发现问题及时上报。如出现上述问题,有权利拒绝下料,汇报领导后造成无法按时出货的与下料人员无关,由直接负责人负责。 c、工作职责:轻拿轻放,按时完成所接受的生产任务,下料顺序根据料单上的交货时间按先后下料,同一天交货产品按先下大件后下小件的顺序下料。下料时,注意板件木纹方向,将板件分为两部分,正常的板件放在一起,需铣型(开槽,铣异型等特殊工艺)的部件放在一起。整件产品所有部件完成后,如果没有任何部件需铣型的直接交给封边组,由封边组签字验收。有铣型部件的将铣型部件交给木工部,由木工部签字验收,剩下的部件交给封边组,由封边组签字验收。 d、工作义务:详细记录每天个人的生产量,妥善保管领导交给的生产任务单,不得丢失。在将下完料的产品交给下一工序时,自己做好记录,记清签收人,防止出现纠纷时相互纠缠。每天经常清理工作台面,防止异物划伤板件,定期对机器进行保养,清理导轨,对重要部位打黄油。 下料加工标准和要求: 1.每批开料时,要每件检查,对照图纸工艺规格尺寸是否一致,所开料切割面是否垂直,光滑并与板面成直角,有无里边爆边现象。线板的木纹意向根据板件部位是否与设计要求相符。加工净尺寸1米以误差≦0.5㎜,对角线误差≦0.5㎜。 2.检查板面有无明显划伤、划痕、破损、空心松散、发霉现象。 3.加工过程中,每批板件50件以上至少抽查5-10件,20-50件至少不少于3-5件,20件以上不少于2件,并符合首件要求。 4.开斜配料3㎝的宽长尺寸公差不超过0.5㎜,两端裁锯时必须保持直角。 5.开出的板件锯口平整无破边、崩口、黑边,板面无划伤。 6.开出的配料无心衬、无严重开裂、腐朽,所有工件无明显的崩缺(0.3mm)、锯痕等现象。 7.开料完成后的操作者,必须随机抽检2-3件。 8.该批检查合格数量无误后,在《生产任务单》签名,方可转入下工序加工作业。