离子镀膜法简述-10082953-李煊

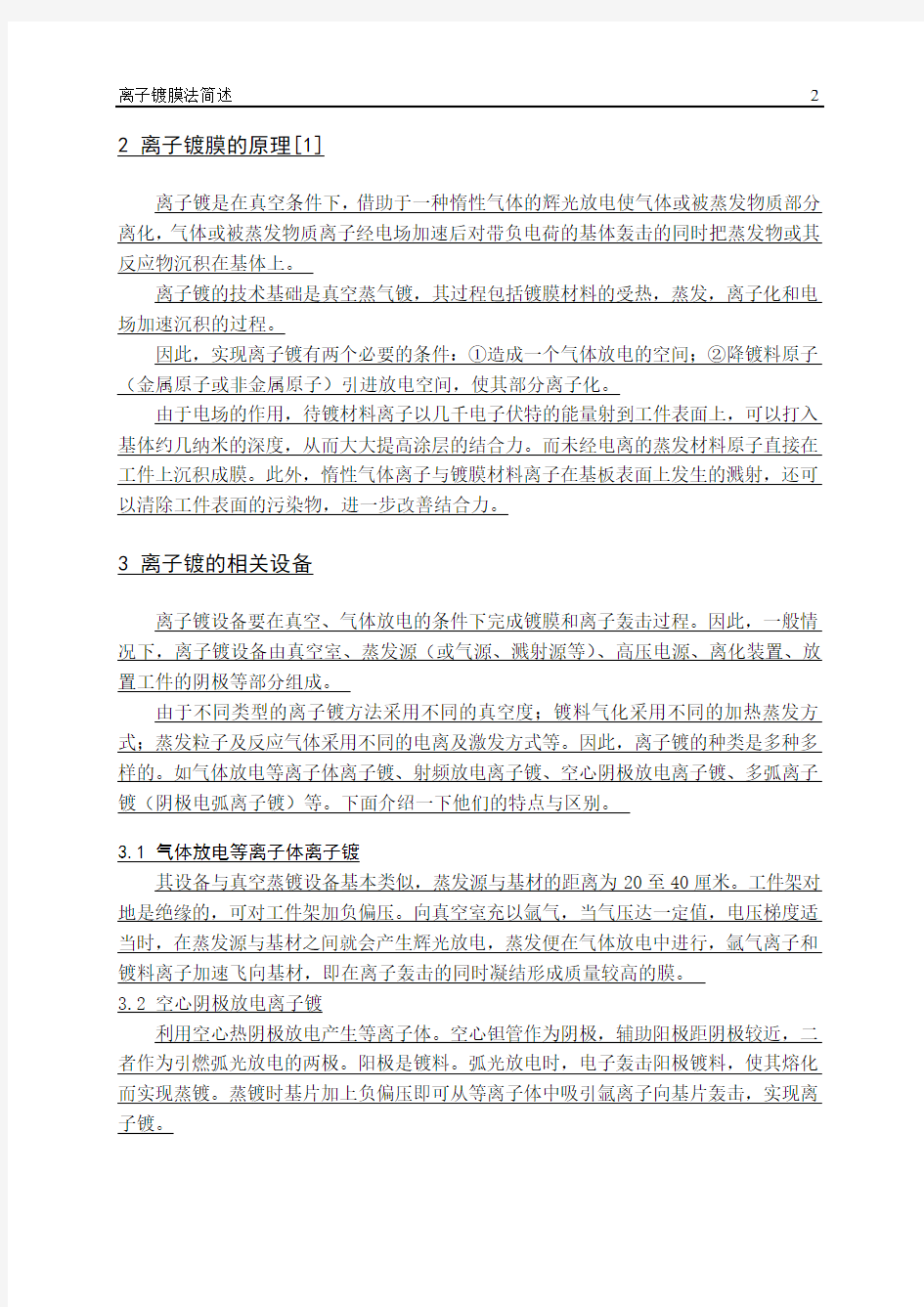
离子镀膜法简述
信材080(10082953)李煊
摘要:本文简述离子镀膜法的作用原理、相关使用的设备、与其余镀膜法相比较而言的特点与应用举例,在特点方面举出了附着性能好、绕镀能力强等优点特性并详细讨论,之后用详细的图表展示了在耐磨、耐热、耐腐蚀、润滑、装饰、电子工业集成电路等方面的应用,并且讨论了该方法现今的发展状况和未来的发展趋势
关键词:离子镀;放电;离子束;加热加工
1 前言
在现代生活中表面技术是非常重要的。通过机械结合、喷涂、化学镀、电镀或蒸镀等方法可以使材料与基体材料结合,然而这些方法存在很多缺陷,就比方说,膜层与基体结合强度低,膜层材料的纯度不高,膜层结构难以控制,膜层厚度不均匀等,导致失效现象广泛存在于材料的实际应用中。尤其是材料的表面处理,它是制约其发展的一大问题。
薄膜技术是表面工程三大技术之一,利用近代技术在零件或(衬底)表面上沉积厚度为100 nm至数微米薄膜的形成技术,称之为薄膜技术。薄膜的应用极为广泛,微电子工业中广泛采用铝合金作为布线膜层材料,金、银、铜、铂、镍等难熔金属作为导电薄膜在防电磁信息泄露材料中应用广泛。尤其是银和铜,将银与聚酯材料结合做成导电涂层通过涂敷的方式与基体结合,它的主要缺点是纯度低、结合强度低。在航空及航宇工业中,各种飞机、导弹、卫星、飞船的零部件经常在复杂而有害的条件下工作。以飞机为例,机翼、机身的蒙皮以及起落架等外表零部件,均受着大气、水份、灰尘以及燃料燃烧生成物中所含的化学活性气体的直接腐蚀。水上飞机的外表部分,特别是机体和浮筒,经常受到海水、湖水或河水的侵蚀;航空发动机的燃烧室、涡轮零件及气缸活塞零件,也经常受到高温和含酸及其他活性物质的燃气气流的氧化。还有诸如航空轴承、微型输电装置、精密齿轮、电位计等一类仪表元件,也经常受到不同程度的摩擦磨损。要使上述各种零部件能够适应耐温、防蚀、耐磨等苛刻要求,单纯从零件的结构或材料上想办法,往往是不够的。怎么办呢?当前使用最广的办法之一就是采用表面镀膜的方法来保护零部件的基体,使其满足上述要求。这正如人们根据不同环境条件穿上不同的衣衫一样,根据需要给零件镀上一层耐热、防腐或耐磨的镀层。
离子镀是在真空条件下,利用气体放电使气体或被蒸发物质部分电离,并在气体离子或被蒸发,物质离子的轰击下,将蒸发物质或其反应物沉积在基片上的方法。其中包括磁控溅射离子镀、反应离子镀、空心阴极放电离子镀(空心阴极蒸镀法)、多弧离子镀(阴极电弧离子镀)等。
2 离子镀膜的原理[1]
离子镀是在真空条件下,借助于一种惰性气体的辉光放电使气体或被蒸发物质部分离化,气体或被蒸发物质离子经电场加速后对带负电荷的基体轰击的同时把蒸发物或其反应物沉积在基体上。
离子镀的技术基础是真空蒸气镀,其过程包括镀膜材料的受热,蒸发,离子化和电场加速沉积的过程。
因此,实现离子镀有两个必要的条件:①造成一个气体放电的空间;②降镀料原子(金属原子或非金属原子)引进放电空间,使其部分离子化。
由于电场的作用,待镀材料离子以几千电子伏特的能量射到工件表面上,可以打入基体约几纳米的深度,从而大大提高涂层的结合力。而未经电离的蒸发材料原子直接在工件上沉积成膜。此外,惰性气体离子与镀膜材料离子在基板表面上发生的溅射,还可以清除工件表面的污染物,进一步改善结合力。
3 离子镀的相关设备
离子镀设备要在真空、气体放电的条件下完成镀膜和离子轰击过程。因此,一般情况下,离子镀设备由真空室、蒸发源(或气源、溅射源等)、高压电源、离化装置、放置工件的阴极等部分组成。
由于不同类型的离子镀方法采用不同的真空度;镀料气化采用不同的加热蒸发方式;蒸发粒子及反应气体采用不同的电离及激发方式等。因此,离子镀的种类是多种多样的。如气体放电等离子体离子镀、射频放电离子镀、空心阴极放电离子镀、多弧离子镀(阴极电弧离子镀)等。下面介绍一下他们的特点与区别。
3.1 气体放电等离子体离子镀
其设备与真空蒸镀设备基本类似,蒸发源与基材的距离为20至40厘米。工件架对地是绝缘的,可对工件架加负偏压。向真空室充以氩气,当气压达一定值,电压梯度适当时,在蒸发源与基材之间就会产生辉光放电,蒸发便在气体放电中进行,氩气离子和镀料离子加速飞向基材,即在离子轰击的同时凝结形成质量较高的膜。
3.2 空心阴极放电离子镀
利用空心热阴极放电产生等离子体。空心钽管作为阴极,辅助阳极距阴极较近,二者作为引燃弧光放电的两极。阳极是镀料。弧光放电时,电子轰击阳极镀料,使其熔化而实现蒸镀。蒸镀时基片加上负偏压即可从等离子体中吸引氩离子向基片轰击,实现离子镀。
4 离子镀特点
4.1 镀层附着性能好
普通真空镀膜时,蒸发料粒子大约只以一个电子伏特的能量向工件表面蒸镀,在工件表面与镀层之间,形成的界面扩散深度通常仅为几百个埃(10000埃=1微米=0.0001厘米)。也就是说比一根头发丝的百分之一还要小。两者间可以说几乎没有连接的过渡层,好似截然分开。而离子镀时,蒸发料粒子电离后具有三千到五千电子伏特的动能。如果说普通真空镀膜的粒子相当于一个气喘吁吁的长跑运动员,那么离子镀的粒子则好似乘坐了高速火箭的乘客,当其高速轰击工件时,不但沉积速度快,而且能够穿透工件表面,形成一种注入基体很深的扩散层,离子镀的界面扩散深度可达四至五微米,也就是说比普通真空镀膜的扩散深度要深几十倍,甚至上百倍,因而彼此粘附得特别牢。对离子镀后的试件作拉伸试验表明,一直拉到快要断裂时,镀层仍随基体金属一起塑性延伸,无起皮或剥落现象发生。可见附着得多么牢固。
4.2 绕镀能力强
离子镀时,蒸发料粒子是以带电离子的形式在电场中沿着电力线方向运动,因而凡是有电场存在的部位,均能获得良好镀层,这比普通真空镀膜只能在直射方向上获得镀层优越得多。因此,这种方法非常适合于镀复零件上的内孔、凹槽和窄缝。等其他方法难镀的部位。用普通真空镀膜只能镀直射表面,蒸发料粒子尤如攀登云梯一样,只能顺梯而上;而离子镀则能均匀地绕镀到零件的背面和内孔中,带电离子则好比坐上了直升飞机,能够沿着规定的航线飞抵其活动半径范围内的任何地方。
4.3 镀层质量好
离子镀的镀层组织致密、无针孔、无气泡、厚度均匀。甚至棱面和凹槽都可均匀镀复,不致形成金属瘤。象螺纹一类的零件也能镀复,由于这种工艺方法还能修补工件表面的微小裂纹和麻点等缺陷,故可有效地改善被镀零件的表面质量和物理机械性能。疲劳试验表明,如果处理得当,工件疲劳寿命可比镀前高百分之二、三十。
4.4 清洗过程简化
现有镀膜工艺,多数均要求事先对工件进行严格清洗,既复杂又费事。然而,离子镀工艺自身就有一种离子轰击清洗作用,并且这一作用还一直延续于整个镀膜过程。清洗效果极好,能使镀层直接贴近基体,有效地增强了附着力,简化了大量的镀前清洗工作。
4.5 可镀材料广泛
等离子镀由于是利用高能离子轰击工件表面,使大量的电能在工件表面转换成热能,从而促进了表层组织的扩散作用和化学反应。然而,整个工件,特别是工件心部并未受到高温的影响。因此这种镀膜工艺的应用范围较广,受到的局限性则较小。通常,各种金属、合金以及某些合成材料、绝缘材料、热敏材料和高熔点材料等均可镀复。即可在金属工件上镀非金属或金属,也可在非金属上镀金属或非金属,甚至可镀塑料、橡胶、石英、陶瓷等。
5 离子镀膜的应用[2]
离子镀的一些典型应用如表所示
离子镀膜的应用举例
应用镀膜基体(或组
合)
应用举例
耐磨
T i C,T i N,A l
2
O
3
H f N,W C,C r
高速钢、硬
质合金、模
具钢、碳钢
刀具、模具、
超硬工具、
机械零件
T i O
2
,S i O
2
,S i
3
N
4
钢、塑料、
半导体
表面保护强
化
耐热Al,W,Ti,Ta,Mo,Co-Cr-Al系
合金
钢、不锈钢、耐热
合金、Co-Cr-Al-Y
系合金
排气管、耐火材料、
发动机材料、航空
航天器件
耐蚀Al,Zn,Cd,Ta,Ti 普通钢、结构钢、
不锈钢
飞机、船舶、汽车、
管材、一般结构件
润滑Au,Ag,Pb,Cu-Au,Pb-Sn,MoS
2高温合金、轴承钢
喷气发动机轴承、
航空航天及高温旋
转器件
装饰Au,Ag,Ti,Al,TiN,TiC,CrC 钢、黄铜、铝、铜、
不锈钢、玻璃、塑
料
首饰、徽章、钟表、
眼镜、彩色画、光
泽、着色
电子工业集成电路Re,Ta-N,Ta-Al,Ta-Si,Ni-Cr 陶瓷、塑料、玻璃薄膜电阻、电阻器Au,Al,Cu,Ni Au,Al,Ni/Si片电极
SiO
2
,Al
2
O
3
SiO
2
,Al
2
O
3
/金属电容、二极管Nb,氧化物氧化物,Ag/石英透镜
6 离子镀膜的方式
根据不同膜材的气化方式和离化方式,可构成不同类型的离子镀膜方式。膜材的气化方式有:电阻加热、电子束加热、等离子电子束加热、高频感应加热、阴极弧光放电加热等。气体分子或原子的离化和激活方式有:辉光放电型、电子束型、热电子型、等离子电子束型、多弧型及高真空电弧放电型,以及各种形式的离子源等。不同的蒸发源与不同的电离或激发方式可以有多种不同的组合。
7 总结
总之,表面和薄膜科学、微电子器件及纳米技术等的迅速发展,将使仪器开发和监测方法体系研究成为离子镀膜技术中的发展重点;而电子束蒸发源将是镀膜技术中的一种重要的加热方法和发展方向。随着科技的发展,离子镀膜技术会在新科技与新设备的推进下取得更加飞速的发展。
参考文献
[1]离子镀膜原理介绍,2009,2009(3):9-13.
[2]王银川.真空镀膜技术的现状与发展,2000(6):43-52.
SiO 2陶瓷等
金属、印刷板、集成电路 表面绝缘保护膜 磁光记录 Gd-Co,Mn-Bi,Mn-Cu-Bi 合金膜/塑料 光盘 光导通讯 TiO 2,ZnO,BaTiO 3,SnO 2,In 2O 3 塑料、玻璃、陶瓷
保护膜、反射膜、特殊透明膜等 塑料
Ni,Cu,Cr 塑料 汽车零件、电气零件 声学 ZnO,PZT,BaTiO 3,LiNbO 3
ZnO/石英、红宝石、金膜 压电膜、声表面波器件 能源 Si,GaAs,黑Cr
太阳能收集器 太阳能电池、太阳能房 Al,Au
Al/铀,Au/Cu 套 反应堆、加速器 TiC,Au,Mo 聚变反应容器内壁 聚变反应容器
真空镀膜技术
真空镀膜技术 磁控溅射膜即物理气相沉积(PVD) 金属镀膜不一定用磁控溅射,可以根据成本&工艺需求选择合理的沉积方法,具体有: 物理气相沉积(PVD)技术 第一节概述 物理气相沉积技术早在20世纪初已有些应用,但在最近30年迅速发展,成为一门极具广阔应用前景的新技术。,并向着环保型、清洁型趋势发展。20世纪90年代初至今,在钟表行业,尤其是高档手表金属外观件的表面处理方面达到越来越为广泛的应用。 物理气相沉积(Physical Vapor Deposition,PVD)技术表示在真空条件下,采用物理方法,将材料源——固体或液体表面气化成气态原子、分子或部分电离成离子,并通过低压气体(或等离子体)过程,在基体表面沉积具有某种特殊功能的薄膜的技术。物理气相沉积的主要方法有,真空蒸镀、溅射镀膜、电弧等离子体镀、离子镀膜,及分子束外延等。发展到目前,物理气相沉积技术不仅可沉积金属膜、合金膜、还可以沉积化合物、陶瓷、半导体、聚合物膜等。 真空蒸镀基本原理是在真空条件下,使金属、金属合金或化合物蒸发,然后沉积在基体表面上,蒸发的方法常用电阻加热,高频感应加热,电子柬、激光束、离子束高能轰击镀料,使蒸发成气相,然后沉积在基体表面,历史上,真空蒸镀是PVD法中使用最早的技术。 溅射镀膜基本原理是充氩(Ar)气的真空条件下,使氩气进行辉光放电,这时氩(Ar)原子电离成氩离子(Ar+),氩离子在电场力的作用下,加速轰击以镀料制作的阴极靶材,靶材会被溅射出来而沉积到工件表面。如果采用直流辉光放电,称直流(Qc)溅射,射频(RF)辉光放电引起的称射频溅射。磁控(M)辉光放电引起的称磁控溅射。电弧等离子体镀膜基本原理是在真空条件下,用引弧针引弧,使真空金壁(阳极)和镀材(阴极)之间进行弧光放电,阴极表面快速移动着多个阴极弧斑,不断迅速蒸发甚至“异华”镀料,使之电离成以镀料为主要成分的电弧等离子体,并能迅速将镀料沉积于基体。因为有多弧斑,所以也称多弧蒸发离化过程。 离子镀基本原理是在真空条件下,采用某种等离子体电离技术,使镀料原子部分电离成离子,同时产生许多高能量的中性原子,在被镀基体上加负偏压。这样在深度负偏压的作用下,离子沉积于基体表面形成薄膜。 物理气相沉积技术基本原理可分三个工艺步骤: (1)镀料的气化:即使镀料蒸发,异华或被溅射,也就是通过镀料的气化源。 (2)镀料原子、分子或离子的迁移:由气化源供出原子、分子或离子经过碰撞后,产生多种反应。 (3)镀料原子、分子或离子在基体上沉积。 物理气相沉积技术工艺过程简单,对环境改善,无污染,耗材少,成膜均匀致密,与基体的结合力强。该技术广泛应用于航空航天、电子、光学、机械、建筑、轻工、冶金、材料等领域,可制备具有耐磨、耐腐饰、装饰、导电、绝缘、光导、压电、磁性、润滑、超导等特性的膜层。
溶液法制硫化镉薄膜
上海大学2012~2013学年春季学期材料科学导论C课程论文 课程名称:材料科学导论C 课程编号: 10415074 论文题目: CdS薄膜及其制备 姓名: 邢凯健 学号: 09120157 论文评语: 论文成绩: 任课教师: 评阅日期:
CdS薄膜及其制备 摘要: CdS薄膜在异质结太阳能电池中是十分重要的n型窗口材料,它的制备可以通过真空镀膜,分子束外延,磁控溅射及化学沉积的方法来实现,而化学沉积方法中,最为常用的就是水浴法是十分重要的。 关键词:CdS薄膜化学水浴法反应速率 一、CdS的基本性质 CdS薄膜的禁带宽度为2.42eV,能透过绝大部分阳光,是十分优秀的窗口材料,其薄膜质量的好坏会直接影响在此基础上制备的吸收层CdTe薄膜质量的好坏,对电池的效率和寿命是十分重要的。因此如何制备出高质量的CdS薄膜成为了一个十分关键的课题。 二、水浴法制备CdS薄膜 如今有许多物理方法可以去制备CdS薄膜,例如真空镀膜法、磁控溅射法等等,这些物理方法制备的CdS薄膜的厚度均匀,测试的结果也十分理想,那么我们为什么还要使用化学方法去制备CdS薄膜呢?其中最为重要的因素就是化学方法,例如水浴法,所需要的成本十分低廉,特别是与前面所提到的几种物理方法相比,前期所投出的经费是微乎其微。并且后期也不会遇到仪器维修等问题。 但是水浴法制备CdS薄膜的质量从许多文献中可以发现,并不是非常的理想,生长所得到的薄膜的厚度不均匀,并且会有气孔、裂纹等等。这是因为化学方法制备CdS薄膜的不可控因素太多(例如当天的湿度,温度,所使用的仪器,药品的纯度及实验误差等等)。那么我就在上海大学电子楼对于该CdS薄膜的生长作了一定的研究,也得出了一些结论。 2.1 实验原理
薄膜物理与技术复习大全 (西电版)
1.薄膜定义:按照一定需要,利用特殊的制备技术,在基体表面形成厚度为亚微米至微米级的膜层。这种二维伸展的薄膜具有特殊的成分、结构和尺寸效应而使其获得三维材料所没有的特性,同时又很节约材料,所以非常重要。通常是把膜层无基片而能独立成形的厚度作为薄膜厚度的一个大致的标准,规定其厚度约在1μm左右。 2.一些表面定义: 1)理想表面:沿着三维晶体相互平行的两个面切开,得到的表面,除了原子平 移对称性破坏,与体内相同。 2)清洁表面:没有外界杂质。 3)弛豫表面:表面原子因受力不均向内收缩或向外膨胀。 4)重构表面:表面原子在与表面平行的方向上的周期也发生变化,不同于晶体 内部原子排列的二维对称性(再构)。 5)实际表面:存在外来原子或分子。 3. 薄膜的形成的物理过程 驰豫 重构驰豫+重构? ? ? ? ? 驰豫:表面向下收缩,表面层原子与内层原子 结构缺陷间距比内层原子相互之间有所减小。 重构:在平行表面方向上原子重排。
①小岛阶段——成核和核长大,透射电镜观察到大小一致(2-3nm)的核突然出现.平行基片平面的两维大于垂直方向的第三维。说明:核生长以吸附单体在基片表面的扩散,不是由于气相原子的直接接触。 ②结合阶段——两个圆形核结合时间小于0.1s,并且结合后增大了高度,减少了在基片所占的总面积。而新出现的基片面积上会发生二次成核,复结合后的复合岛若有足够时间,可形成晶体形状,多为六角形。核结合时的传质机理是体扩散和表面扩散(以表面扩散为主)以便表面能降低。 ③沟道阶段——圆形的岛在进一步结合处,才继续发生大的变形→岛被拉长,从而连接成网状结构的薄膜,在这种结构中遍布不规则的窄长沟道,其宽度约为5-20nm,沟道内发生三次成核,其结合效应是消除表面曲率区,以使生成的总表面能为最小。 ④连续薄膜——小岛结合,岛的取向会发生显著的变化,并有些再结晶的现象。沟道内二次或三次成核并结合,以及网状结构生长→连续薄膜。 4. 薄膜的附着类型及影响薄膜附着力的工艺因素 薄膜的附着类型 ①简单附着:薄膜和基片间形成一个很清楚的分界面,薄膜与基片间的结合力为范 德华力 ②扩散附着—由两个固体间相互扩散或溶解而导致在薄膜和基片间形成一个渐变界 面。实现扩散方法:基片加热法、离子注入法、离子轰击法、电场吸引法。 ③通过中间层附着—在薄膜与基片之间形成一个化合物而附着,该化合物多为薄膜材料与基片材料
离子镀膜 (PVD ) 技术和设备常见问题解答
离子镀膜(PVD ) 技术和设备常见问题解答 Q1: 请问什么是PVD? A1: PVD是英文Physical Vapor Deposition的缩写,中文意思是“物理气相沉积”,是指在真空条件下,用物理的方法使材料沉积在被镀工件上的薄膜制备技术。 Q2: 请问什么是PVD镀膜?什么是PVD镀膜机? A2: PVD(物理气相沉积)技术主要分为三类,真空蒸发镀膜、真空溅射镀膜和真空离子镀膜。相对于PVD技术的三个分类,相应的真空镀膜设备也就有真空蒸发镀膜机、真空溅射镀膜机和真空离子镀膜机。 近十多年来,真空离子镀技术的发展是最快的,它已经成为了当代最先进的表面处理方法之一。我们通常所说的PVD镀膜,指的就是真空离子镀膜;通常所说的PVD镀膜机,指的也就是真空离子镀膜机。 Q3: 请问PVD镀膜的具体原理是什么? A3: 离子镀膜(PVD镀膜)技术,其原理是在真空条件下,采用低电压、大电流的电弧放电技术,利用气体放电使靶材蒸发并使被蒸发物质电离,在电场的作用下,使被蒸发物质或其反应产物沉积在工件上。 Q4: 请问PVD镀膜与传统的化学电镀(水电镀)相比有何优点? A4: PVD镀膜与传统的化学电镀的相同点是,两者都属于表面处理的范畴,都是通过一定的方式使一种材料覆盖在另一种材料的表面。 两者的不同点是:PVD镀膜膜层与工件表面的结合力更大,膜层的硬度更高,耐磨性和耐腐蚀性更好,膜层的性能也更稳定;PVD镀膜可以镀的膜层的种类更为广泛,可以镀出的各种膜层的颜色也更多更漂亮;PVD镀膜不会产生有毒或有污染的物质。 Q5: 请问PVD镀膜能否代替化学电镀? A5: 在现阶段,PVD镀膜是不能取代化学电镀的,并且除了在不锈钢材料表面可直接进行PVD镀膜外,在很多其他材料(如锌合金、铜、铁等)的工件上进行PVD镀膜前,都需要先对它们进行化学电镀Cr(铬)。PVD镀膜主要应用在一些比较高档的五金制品上,对那些价格较低的五金制品通常也只是进行化学电镀而不做PVD镀膜。 Q6: 请问采用PVD镀膜技术镀出的膜层有什么特点? A6: 采用PVD镀膜技术镀出的膜层,具有高硬度、高耐磨性(低摩擦系数)、很好的耐腐蚀性和化学稳定性等特点,膜层的寿命更长;同时膜层能够大幅度提高工件的外观装饰性能。 Q7: 请问PVD能在镀在什么基材上? A7: PVD膜层能直接镀在不锈钢以及硬质合金上,对锌合金、铜、铁等压铸件应先进行化学电镀铬,然后才适合镀PVD。 Q8: 请问PVD镀膜能够镀出的膜层种类有那些? A8: PVD镀膜技术是一种能够真正获得微米级镀层且无污染的环保型表面处理方法,它能够
化学镀膜
化学镀膜 2007-01-18 20:55:04 (已经被浏览304次) 化学镀膜 化学镀膜最早用于在光学元件表面制备保护膜。随后,1817年,Fraunhofe在德国用浓硫酸或硝酸侵蚀玻璃,偶然第一次获得减反射膜,1835年以前有人用化学湿选法淀积了银镜膜它们是最先在世界上制备的光学薄膜。后来,人们在化学溶液和蒸气中镀制各种光学薄膜。50年代,除大快窗玻璃增透膜的一些应用外,化学溶液镀膜法逐步被真空镀膜取代。 真空蒸发和溅射这两种真空物理镀膜工艺,是迄今在工业领域能够制备光学薄膜的两种最主要的工艺。它们大规模地应用,实际上是在1930年出现了油扩散泵---机械泵抽气系统之后。 1935年,有人研制出真空蒸发淀积的单层减反射膜。但它的最先应用是1945年以后镀制在眼镜片上。 1938年,美国和欧洲研制出双层减反射膜,但到1949年才制造出优质的产品。1965年,研制出宽带三层减反射系统。在反射膜方面,美国通用电气公司1937年制造出第一盏镀铝灯。德国同年制成第一面医学上用的抗磨蚀硬铑膜。在滤光片方面,德国1939年试验淀积出金属—介质薄膜Fabry---Perot型干涉滤光片。在溅射镀膜领域,大约于1858年,英国和德国的研究者先后于实验室中发现了溅射现象。该技术经历了缓慢的发展过程。 1955年,Wehner提出高频溅射技术后,溅射镀膜发展迅速,成为了一种重要的光学薄膜工艺。现有两极溅射、三极溅射、反应溅射、磁控溅射和双离子溅射等淀积工艺。 自50年代以来,光学薄膜主要在镀膜工艺和计算机辅助设计两个方面发展迅速。在镀膜方面,研究和应用了一系列离子基新技术。 1953年,德国的Auwarter申请了用反应蒸发镀光学薄膜的专利,并提出用离子化的气体增加化学反应性的建议。 1964年,Mattox在前人研究工作的基础上推出离子镀系统。那时的离子系统在10Pa压力和2KV的放电电压下工作,用于在金属上镀耐磨和装饰等用途的镀层,不适合镀光学薄膜。后来,研究采用了高频离子镀在玻璃等绝缘材料上淀积光学薄膜。70年代以来,研究和应用了离子辅助淀积、反应离子镀和等离子化学气相等一系列新技术。它们由于使用了带能离子,而提供了充分的活化能,增加了表面的反应速度。提高了吸附原子的迁移性,避免形成柱状显微结构,从而不同程度地改善了光学薄膜的性能,是光学薄膜制造工艺的研究和发展方向。 实际上,真空镀膜的发展历程要远远复杂的多。我们来看一个这个有两百年历史的科技历程: 19世纪 真空镀膜已有200年的历史。在19世纪可以说一直是处于探索和预研阶段。探索者的艰辛在此期间得到充分体现。 1805年, 开始研究接触角与表面能的关系(Young)。 1817年, 透镜上形成减反射膜(Fraunhofer)。 1839年, 开始研究电弧蒸发(Hare)。
离子镀膜法简述-10082953-李煊
离子镀膜法简述 信材080(10082953)李煊 摘要:本文简述离子镀膜法的作用原理、相关使用的设备、与其余镀膜法相比较而言的特点与应用举例,在特点方面举出了附着性能好、绕镀能力强等优点特性并详细讨论,之后用详细的图表展示了在耐磨、耐热、耐腐蚀、润滑、装饰、电子工业集成电路等方面的应用,并且讨论了该方法现今的发展状况和未来的发展趋势 关键词:离子镀;放电;离子束;加热加工 1 前言 在现代生活中表面技术是非常重要的。通过机械结合、喷涂、化学镀、电镀或蒸镀等方法可以使材料与基体材料结合,然而这些方法存在很多缺陷,就比方说,膜层与基体结合强度低,膜层材料的纯度不高,膜层结构难以控制,膜层厚度不均匀等,导致失效现象广泛存在于材料的实际应用中。尤其是材料的表面处理,它是制约其发展的一大问题。 薄膜技术是表面工程三大技术之一,利用近代技术在零件或(衬底)表面上沉积厚度为100 nm至数微米薄膜的形成技术,称之为薄膜技术。薄膜的应用极为广泛,微电子工业中广泛采用铝合金作为布线膜层材料,金、银、铜、铂、镍等难熔金属作为导电薄膜在防电磁信息泄露材料中应用广泛。尤其是银和铜,将银与聚酯材料结合做成导电涂层通过涂敷的方式与基体结合,它的主要缺点是纯度低、结合强度低。在航空及航宇工业中,各种飞机、导弹、卫星、飞船的零部件经常在复杂而有害的条件下工作。以飞机为例,机翼、机身的蒙皮以及起落架等外表零部件,均受着大气、水份、灰尘以及燃料燃烧生成物中所含的化学活性气体的直接腐蚀。水上飞机的外表部分,特别是机体和浮筒,经常受到海水、湖水或河水的侵蚀;航空发动机的燃烧室、涡轮零件及气缸活塞零件,也经常受到高温和含酸及其他活性物质的燃气气流的氧化。还有诸如航空轴承、微型输电装置、精密齿轮、电位计等一类仪表元件,也经常受到不同程度的摩擦磨损。要使上述各种零部件能够适应耐温、防蚀、耐磨等苛刻要求,单纯从零件的结构或材料上想办法,往往是不够的。怎么办呢?当前使用最广的办法之一就是采用表面镀膜的方法来保护零部件的基体,使其满足上述要求。这正如人们根据不同环境条件穿上不同的衣衫一样,根据需要给零件镀上一层耐热、防腐或耐磨的镀层。 离子镀是在真空条件下,利用气体放电使气体或被蒸发物质部分电离,并在气体离子或被蒸发,物质离子的轰击下,将蒸发物质或其反应物沉积在基片上的方法。其中包括磁控溅射离子镀、反应离子镀、空心阴极放电离子镀(空心阴极蒸镀法)、多弧离子镀(阴极电弧离子镀)等。
磁控溅射镀膜原理及工艺
磁控溅射镀膜原理及工艺 摘要:真空镀膜技术作为一种产生特定膜层的技术,在现实生产生活中有着广泛的应用。真空镀膜技术有三种形式,即蒸发镀膜、溅射镀膜和离子镀。这里主要讲一下由溅射镀 膜技术发展来的磁控溅射镀膜的原理及相应工艺的研究。 关键词:溅射;溅射变量;工作气压;沉积率。 绪论 溅射现象于1870年开始用于镀膜技术,1930年以后由于提高了沉积速率而逐渐用于工业生产。常用二极溅射设备如右图。 通常将欲沉积的材料制成板材-靶,固定在阴 极上。基片置于正对靶面的阳极上,距靶一定距离。 系统抽至高真空后充入(10~1)帕的气体(通常 为氩气),在阴极和阳极间加几千伏电压,两极间 即产生辉光放电。放电产生的正离子在电场作用下 飞向阴极,与靶表面原子碰撞,受碰撞从靶面逸出 的靶原子称为溅射原子,其能量在1至几十电子伏 范围内。溅射原子在基片表面沉积成膜。其中磁控 溅射可以被认为是镀膜技术中最突出的成就之一。 它以溅射率高、基片温升低、膜-基结合力好、装 置性能稳定、操作控制方便等优点,成为镀膜工业 应用领域(特别是建筑镀膜玻璃、透明导电膜玻璃、 柔性基材卷绕镀等对大面积的均匀性有特别苛刻 要求的连续镀膜场合)的首选方案。 1磁控溅射原理 溅射属于PDV(物理气相沉积)三种基本方法:真空蒸发、溅射、离子镀(空心阴极离子镀、热阴极离子镀、电弧离子镀、活性反应离子镀、射频离子镀、直流放电离子镀)中的一种。 磁控溅射的工作原理是指电子在电场E的作用下,在飞向基片过程中与氩原子发生碰撞,使其电离产生出Ar正离子和新的电子;新电子飞向基片,Ar正离子在电场作用下加速飞向阴极靶,并以高能量轰击靶表面,使靶材发生溅射。在溅射粒子中,中性的靶原子或分子沉积在基片上形成薄膜,而产生的二次电子会受到电场和磁场作用,产生E(电场)×B(磁场)所指的方向漂移,简称E×B漂移,其运动轨迹近似于一条摆线。若为环形磁场,则电子就以近似摆线形式在靶表面做圆周运动,它们的运动路径不仅很长,而且被束缚在靠近靶表面的等离子体区域内,并且在该区域中电离出大量的Ar正离子来轰击靶材,从而实现了高的沉积速率。随着碰
06 第六章 溶液镀膜法
第六章溶液镀膜法 溶液镀膜法是指在溶液中利用化学反应或电化学反应等化学方法在基板表面沉和只薄膜的一种技术。它包括化学反应沉积、溶胶—凝胶法、阳极氧化、电镀以及LB制膜法等。这是一类不需要真空环境的制膜技术,由于所需设备少,可在各种基体表面成膜、原材料容易解决,所以在电子元器件、表面涂要禾装饰等方面得到了广泛的应用。 §6-1 化学反应沉积 一、化学镀 化学镀实质上是在还原剂的作用下,使金属盐中的金属离子还原成原子状态并沉积在基板表面上,从而获得镀层的一种方法,又称为无电源电镀。它与化学沉积法同属于不通电而造化学反应沉和只金属的镀膜方法。两者的区别在于,化学镀的还原反应必须在催化剂的作用下才能进行,且沉积反应只发生在镀件的表面上,而化学沉积法的还原反应却是在整个溶液中均匀发生的,只有一部分金属镀在镀件上,大部分则成为金属粉末沉淀下来。所以,确切地说化学镀的过程是在有催化条件下发生在镀层上的氧化还原过程。即在这种镀覆的过程中,溶液中的金属离子被生长着的镀层表面所催化,并且不断还原而沉积在基体表面上。在此过程中基体材料表面的催化作用相当重要,周期表中的Ⅶ族金属元素都具有在化学镀过程中所需的催化效应。 所谓催化剂指的是敏化剂和活化剂,它可以促使化学镀过程发生在具有催化活性的镀件表面。如果被镀金属本身不能自动催化,则在镀件的活性表面被沉积金属全部覆盖之后,其沉积过程便自动终止;相反,像Ni、Co、Fe、Cu和Cr等金属,其本身对还原反应具有催化作用,可使镀覆反应得以继续进行,直到镀件取出,反应才自行停止。这种依靠被镀金属自身催化作用的化学镀又称为自催化化学镀。通常所谓的化学镀均指这类化学镀。 自催化化学镀有以下优点:(1)可在复杂的镀件表面形成均匀的镀层;(2)镀层的孔隙率比较低;(3)可直接在塑料、陶瓷、玻璃等非导体上进行沉积镀膜;(4)镀层具有特殊的物理、化学性质;(5)不需要电源,没有导电电极。化学镀在电子工业等部门中得到广泛应用。 在化学镀中,所用还原剂的电离电位必须比沉积金属的电极电位低,但二者电位差又不宜过大。常用的还原剂有次磷酸盐和甲醛,前者用来镀Ni,后者用来镀Cu。此外,还有用氢硼化物、阱、氨基硼氢化合物等,无论采用什么还原剂都必须能在自催化的条件下提供金属离子还原时所需要的电子,即 催化表面 M+n+ ne(来自还原剂)M0(6-1)这种反应只能在具有催化性质的镀件表面上进行,才能得到镀层,而且如前所述,一旦沉积开始,沉积出来的金属就必须继续这种催化功能,沉积过程才能继续进行,镀层才能加厚。所以,从这个意义讲,化学镀必然是一种受控的自催化的化学还原过程。目前广泛用于镀制镍、钴、钯、铂、银、金以及上述金属的合金薄膜。 例如,化学镀镍是利用镍盐溶液(硫酸镍或氯化镍)和钴盐(硫酸钴)溶液,在强还原剂次磷酸盐(次磷酸钠、次磷酸钾等)的作用下,使镍离子和钴离子还原成镍金属和钴金属,同时次磷酸盐分解析出磷,在具有催化表面的基体上,获得镍磷或镍钴磷合金的沉积膜。关于使用次磷酸盐作还原剂的化学镀镍的反应机理,多数学者认为镍的沉积反应是由于基体材
镀膜的发展历史
镀膜的发展历史 化学镀膜最早用于在光学元件表面制备保护膜。随后,1817年,Fraunhofe在德国用浓硫酸或硝酸侵蚀玻璃,偶然第一次获得减反射膜,1835年以前有人用化学湿选法淀积了银镜膜它们是最先在世界上制备的光学薄膜。后来,人们在化学溶液和蒸气中镀制各种光学薄膜。50年代,除大快窗玻璃增透膜的一些应用外,化学溶液镀膜法逐步被真空镀膜取代。 真空蒸发和溅射这两种真空物理镀膜工艺,是迄今在工业撒谎能够制备光学薄膜的两种最主要的工艺。它们大规模地应用,实际上是在1930年出现了油扩散泵---机械泵抽气系统之后。 1935年,有人研制出真空蒸发淀积的单层减反射膜。但它的最先应用是1945年以后镀制在眼镜片上。1938年,美国和欧洲研制出双层减反射膜,但到1949年才制造出优质的产品。1965年,研制出宽带三层减反射系统。在反射膜方面,美国通用电气公司1937年制造出第一盏镀铝灯。德国同年制成第一面医学上用的抗磨蚀硬铑膜。在滤光片方面,德国1939年试验淀积出金属—介质薄膜Fabry---Perot型干涉滤光片。 在溅射镀膜领域,大约于1858年,英国和德国的研究者先后于实验室中发现了溅射现象。该技术经历了缓慢的发展过程。1955年,Wehner提出高频溅射技术后,溅射镀膜发展迅速,成为了一种重要的光学薄膜工艺。现有两极溅射、三极溅射、反应溅射、磁控溅射和双离子溅射等淀积工艺。 自50年代以来,光学薄膜主要在镀膜工艺和计算机辅助设计两个方面发展迅速。在镀膜方面,研究和应用了一系列离子基新技术。1953年,德国的Auwarter申请了用反应蒸发镀光学薄膜的专利,并提出用离子化的气体增加化学反应性的建议。1964年,Mattox在前人研究工作的基础上推出离子镀系统。那时的离子系统在10Pa压力和2KV的放电电压下工作,用于在金属上镀耐磨和装饰等用途的镀层,不适合镀光学薄膜。后来,研究采用了高频离子镀在玻璃等绝缘材料上淀积光学薄膜。70年代以来,研究和应用了离子辅助淀积、反应离子镀和等离子化学气相等一系列新技术。它们由于使用了带能离子,而提供了充分的活化能,增加了表面的反应速度。提高了吸附原子的迁移性,避免形成柱状显微结构,从而不同程度地改善了光学薄膜的性能,是光学薄膜制造工艺的研究和发展方向。
多弧离子镀原理
多弧离子镀 离子镀膜 真空离子镀膜于1963年由D.M.Mattox提出,并开始实验。1971年Chamber等发表电子束离子镀技术,1972年B报告了反应蒸发镀(ARE)技术,并制作了TIN及TIC超硬膜。同年,MOLEY和SMITH将空心阴极技术应用于镀膜。20世纪八十年代,国内又相继出现了多弧离子镀及电弧放电高真空离子镀,至此离子镀达到工业应用水平。 离子镀膜原理及种类: 离子镀是真空室中,利用气体放电或被蒸发物质部分离化,在气体离子或被蒸发物质粒子轰击作用的同时,将蒸发物或反应物沉积在基片上。离子镀把辉光放电现象、等离子体技术和真空蒸发三者有机结合起来,不仅能明显地改进了膜质量,而且还扩大了薄膜的应用范围。其优点是薄膜附着力强,绕射性好,膜材广泛等。D.M.首次提出离子镀原理,起工作过程是: 先将真空室抽至4×10(-3)帕以上的真空度,再接通高压电源,在蒸发源与基片之间建立一个低压气体放电的低温等离子区。基片电极接上5KV 直流负高压,从而形成辉光放电阴极。辉光放电去产生的惰性气体离子进入阴极暗区被电场加速并轰击基片表面,对其进行清洗。然后计入镀膜过程,加热使镀料气化,起原子进入等离子区,与惰性气体离子及电子发生碰撞,少部分产生离化。离化后的例子及气体离子以较高能量轰击镀层表面,致使膜层质量得到改善。 离子镀种类很多,蒸发远加热方式有电阻加热、电子束加热、等离子电子束加热、高频感应加热等 然而多弧离子镀与一般的离子镀有着很大的区别。多弧离子镀采用的是弧光放电,而并不是传统离子镀的辉光放电进行沉积。简单的说,多弧离子镀的原理就是把阴极靶作为蒸发源,通过靶与阳极壳体之间的弧光放电,使靶材蒸发,从而在空间中形成等离子体,对基体进行沉积。
多弧离子镀膜技术有效运用分析
龙源期刊网 https://www.360docs.net/doc/7812501895.html, 多弧离子镀膜技术有效运用分析 作者:李洪亮 来源:《世界家苑·学术》2018年第09期 摘要:多弧离子镀技术实为一种基于离子镀技术而创新改进出的较新型技术,现阶段, 其已在多领域中得到广泛应用。本文首先简要分析了多弧离子镀的基本原理及主要特点,探讨了多弧离子镀在多领域中的实际应用。 关键词:多弧离子镀;镀膜;运用 离子镀技术是一种在上个世纪60年代基于真空溅射与真空蒸镀而发展起来的较新型薄膜制备技术,而对于多弧离子镀而言,其则为基于离子镀而不断发展与更新的改进方法,乃是整个离子镀技术架构当中的重要构成。到了上个世纪80年代,Multi-Arc公司(美国)首次将此技术应用于实践。本文就多弧离子镀膜技术的特点、原理及实际应用作一探讨。 1.多弧离子镀的基本原理 针对多弧离子镀而言,其主要由引弧电极、磁场线圈及水冷阴极等构成,所谓阴极材料,从根本上来讲,即为镀膜材料,当处于真空环境中,将电源接通,且使引弧电极瞬间接触于阴极,当引弧电极瞬间离开时,因导电面积瞬间变小,电阻随之增大,局部温度在短时间内会快速升高,造成阴极材料出现不同程度融化,最终造成液桥导电,形成金属蒸发;另外,还需要指出的是,基于阴极表面,通常会形成局部性的、区域性的高温区,此时,等离子体会不断产生,引燃电弧,电源维持弧光放电,在此影响下,阴极表面便会产生许多比较明亮的高电流密度,而且还呈现出高速变化状态;在此大背景下,阴极弧斑会有非常小的尺寸,通常处于1~100μm区间内;具有比较高的电流密度,通常达到105~107A/CM2。各弧斑有着并不长的存在时间,当其以一种爆发性的方式离化并发射电子与离子时,会大量蒸发阴极材料,而在此过程中,于阴极表面周围,金属离子受此影响与驱动,会形成比较典型的空间电荷,另外,还会根据实际情况及环境,构建弧斑生成所需条件,形成全新的弧斑,并持续生成,因而可以较好的保持电弧电流的基本稳定。针对阴极材料而言,通常情况下,其会以每个弧斑60~90%的离化率,在基片表面蒸发与沉积,最终形成膜层。磁场会控制阴极弧斑的速度与运动方向,而适宜的磁场强度会分散与细化弧斑,均匀刻蚀阴极表面。 2.多弧离子镀的基本特点 多弧离子镀主要有如下工艺特点:(1)阴极电弧的蒸发源不会有熔池出现,能在镀膜室中恰当位置随意设置,还可根据实际需要,选用多个电弧蒸发源,最大程度提高沉积速率,从中获得均匀的膜层厚度,除此之外,还能实现基片转动机构的相应简化。(2)较高的金属离化率,通常能够达到80%,所以,有着比较高的镀膜速率,这对膜层性能及膜基附着性的提高,有重要促进作用。(3)一弧多用。电弧不仅是离化源与蒸发源,而且还是离子源与加热
真空镀膜技术简述
真空镀膜技术简述 摘要:介绍了在真空条件下真空蒸发镀、溅射镀膜和离子镀等镀膜技术的概念和这几种真空镀膜技术的特点、应用及发展的前景。和传统的电镀法相比,真空镀膜具有低能耗无毒,无废液,污染小,成本低,装饰效果好,金属感强等优点,是一项很有发展前途的新技术。目前使用最广泛的镀膜方法,主要有热蒸发镀膜法和磁控溅射法。 关键词:真空蒸发镀膜溅射镀膜离子镀膜 1 前言 材料科学是国家发展的三大支柱之一,薄膜材料更是我国前沿科学和高新技术产品的重要基石。镀膜技术也叫薄膜技术,是在真空条件下采用物理或化学方法,使物体表面获得所需的膜体。目前已被广泛应用于耐酸、耐蚀、耐热、表面硬化、装饰、润滑、光电通讯、电子集成、能源等领域。 真空蒸发、溅射镀膜和离子镀等通常称为物理气相沉积法,是基本的薄膜制备技术。它们都要求淀积薄膜的空间要有一定的真空度。所以,真空技术是薄膜制作技术的基础,获得并保持所需的真空环境,是镀膜的必要条件。 2 真空蒸发镀膜技术 真空蒸发镀膜法(简称真空蒸镀)是在真空室中,加热蒸发容器中待形成薄膜的原材料,使其原子或分子从表面气化逸出,形成蒸气流,入射到固体(称为衬底或基片)表面,凝结形成固态薄膜的方法。蒸发源是蒸发装置的关键部件,根据蒸发源不同,真空蒸发镀膜法又可以分为下列几种。 2.1 电子束蒸发源蒸镀法 将蒸发材料放人水冷铜增祸中,直接利用电子束加热,使蒸发材料气化蒸发后凝结在基板表面成膜,是真空蒸发镀膜技术中的一种重要的加热方法和发展方向。电子束蒸发克服了一般电阻加热蒸发的许多缺点,特别适合制作熔点薄膜材料和高纯薄膜材料。
2.2 电阻蒸发源蒸镀法 采用担、铝、钨等高熔点金属,做成适当形状的蒸发源,其上装入待蒸发材料,让电流通过,对蒸发材料进行直接加热蒸发,或者把待蒸发材料放人A12马、Beo等增祸中进行间接加热蒸发,这就是电阻加热蒸发法。利用电阻加热器加热蒸发的镀膜机构造简单、造价便宜、使用可靠,可用于熔点不太高的材料的蒸发镀膜,尤其适用于对膜层质量要求不太高的大批量的生产中。迄今为止,在镀铝制镜的 生产中仍然大量使用着电阻加热蒸发的工艺。电阻加热方式的缺点是:加热所能达到的最高温度有限,加热器的寿命也较短。近年来,为了提高加热器的寿命,国内外已采用寿命较长的氮化硼合成的导电陶瓷材料作为加热器。据日本专利报道,可采用20%一30%的氮化硼和能与其相熔的耐火材料所组成的材料来制造增祸,并在表面涂上一层含62%一82%的错,其余为错硅合金材料。 3 磁控溅射镀膜技术 磁控溅射法又叫高速低温溅射法。目前磁控溅射法已在电学膜、光学膜和塑料金属化等领域得到广泛应用。磁控溅射法与蒸发法相比,具有镀膜层与基材的结合力强,镀膜层致密、均匀等优点。磁控溅射还有其它优点,如设备简单,操作方便,控制也不太难。在溅射镀膜过程中,只要保持工作气压和溅射功率恒定,基本上即可获得稳定的沉积速率。如果能精确地控制溅射镀膜时间,沉积特定厚度的膜层是比较容易实现的。 由于它具有高速、低温两大特点,因此在薄膜领域得到广泛应用。磁控溅射靶是磁控溅射镀膜设备的核心部件。常规的圆柱形磁控溅射靶是以圆环形永磁体在靶材表面建立环形磁场,在轴向等距离的环形表面形成刻蚀区,因而影响沉积薄膜厚度的均匀性,而且靶材利用率仅为20%~30%。年来随着大面积和连续镀膜技术的发展,对膜厚的均匀性、镀膜的重复性以及靶材利用率要求愈来愈高,因而目前国内外都在推广应用旋转圆柱磁控溅射靶。如图1其靶的二端是固定的,靶材是一个圆管,围绕固定的条状磁铁组件而旋转。这样靶面360°都均匀被刻蚀,靶材利用率高达80%。特别旋转磁控靶应用于反应溅射完全可以克服反应溅射而造成非刻蚀区的污染问题,这是由于360°表面的连续轰击刻蚀,提供了一个非常稳定的溅射沉积条件。