白车身柔性总拼焊接系统介绍
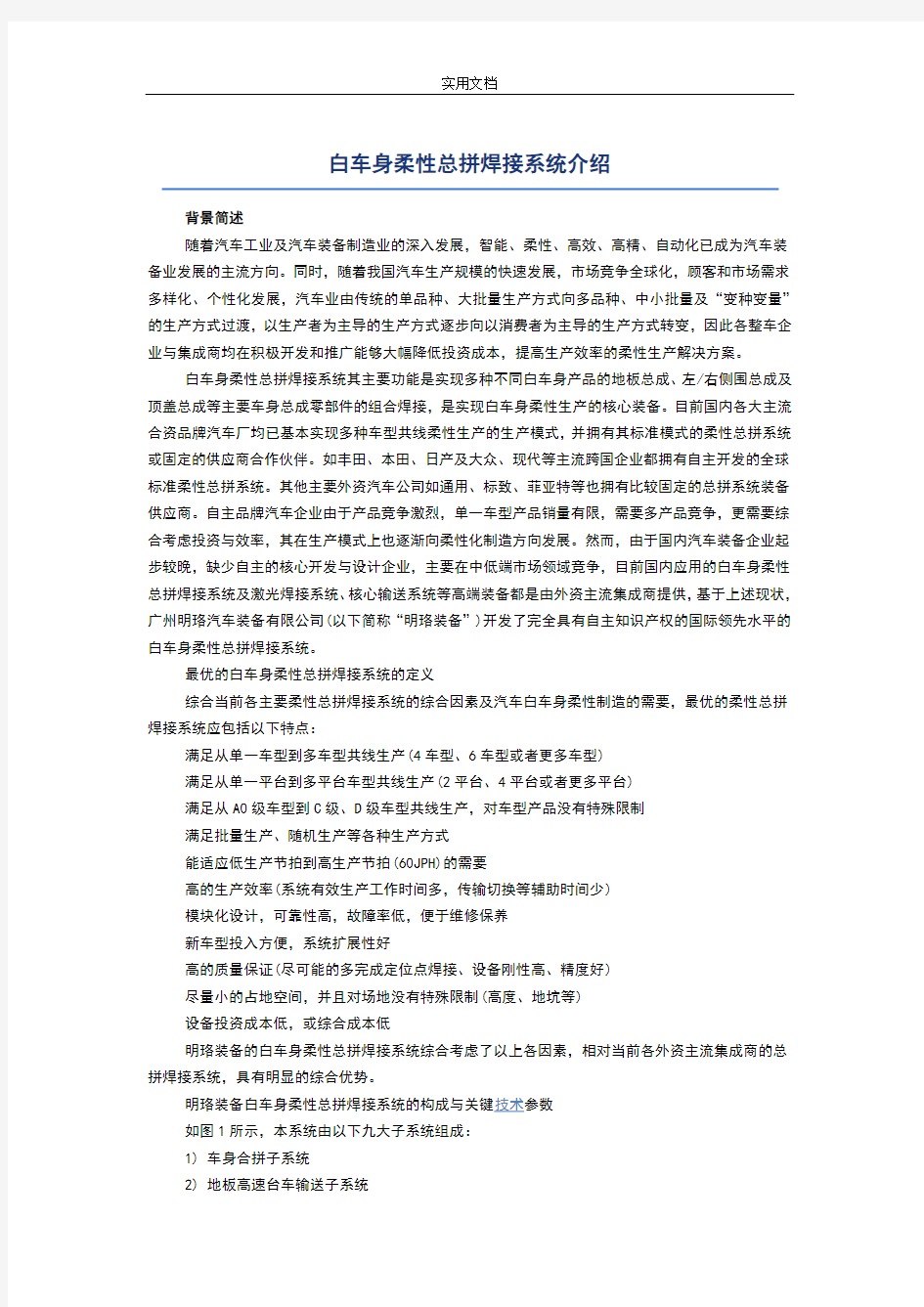

背景简述
随着汽车工业及汽车装备制造业的深入发展,智能、柔性、高效、高精、自动化已成为汽车装备业发展的主流方向。同时,随着我国汽车生产规模的快速发展,市场竞争全球化,顾客和市场需求多样化、个性化发展,汽车业由传统的单品种、大批量生产方式向多品种、中小批量及“变种变量”的生产方式过渡,以生产者为主导的生产方式逐步向以消费者为主导的生产方式转变,因此各整车企业与集成商均在积极开发和推广能够大幅降低投资成本,提高生产效率的柔性生产解决方案。
白车身柔性总拼焊接系统其主要功能是实现多种不同白车身产品的地板总成、左/右侧围总成及顶盖总成等主要车身总成零部件的组合焊接,是实现白车身柔性生产的核心装备。目前国内各大主流合资品牌汽车厂均已基本实现多种车型共线柔性生产的生产模式,并拥有其标准模式的柔性总拼系统或固定的供应商合作伙伴。如丰田、本田、日产及大众、现代等主流跨国企业都拥有自主开发的全球标准柔性总拼系统。其他主要外资汽车公司如通用、标致、菲亚特等也拥有比较固定的总拼系统装备供应商。自主品牌汽车企业由于产品竞争激烈,单一车型产品销量有限,需要多产品竞争,更需要综合考虑投资与效率,其在生产模式上也逐渐向柔性化制造方向发展。然而,由于国内汽车装备企业起步较晚,缺少自主的核心开发与设计企业,主要在中低端市场领域竞争,目前国内应用的白车身柔性总拼焊接系统及激光焊接系统、核心输送系统等高端装备都是由外资主流集成商提供,基于上述现状,广州明珞汽车装备有限公司(以下简称“明珞装备”)开发了完全具有自主知识产权的国际领先水平的白车身柔性总拼焊接系统。
最优的白车身柔性总拼焊接系统的定义
综合当前各主要柔性总拼焊接系统的综合因素及汽车白车身柔性制造的需要,最优的柔性总拼焊接系统应包括以下特点:
满足从单一车型到多车型共线生产(4车型、6车型或者更多车型)
满足从单一平台到多平台车型共线生产(2平台、4平台或者更多平台)
满足从A0级车型到C级、D级车型共线生产,对车型产品没有特殊限制
满足批量生产、随机生产等各种生产方式
能适应低生产节拍到高生产节拍(60JPH)的需要
高的生产效率(系统有效生产工作时间多,传输切换等辅助时间少)
模块化设计,可靠性高,故障率低,便于维修保养
新车型投入方便,系统扩展性好
高的质量保证(尽可能的多完成定位点焊接、设备刚性高、精度好)
尽量小的占地空间,并且对场地没有特殊限制(高度、地坑等)
设备投资成本低,或综合成本低
明珞装备的白车身柔性总拼焊接系统综合考虑了以上各因素,相对当前各外资主流集成商的总拼焊接系统,具有明显的综合优势。
明珞装备白车身柔性总拼焊接系统的构成与关键技术参数
如图1所示,本系统由以下九大子系统组成:
1) 车身合拼子系统
2) 地板高速台车输送子系统
9) 外围辅助设备
图1 MINO白车身柔性总拼焊接系统
阶段
随机生产方式批量生产方式
投入硬件设备名称数量投入硬件设备名称数量
第1车左/右合拼装置 1 左/右合拼装置 1
型
第2车
型
左/右车型切换装置 1 左/右车型切换装置1/2 第3车
型
左/右车型存储系统 2 左/右车型存储系统 1
第4车型左/右车型返回切换装
置
1 无需增加设备
第5车
型
无需增加设备左/右车型切换装置1/2 第6车
型
无需增加设备左/右车型存储系统 1 第7车
型
无需增加设备无需增加设备
第8车型无法实现
无需增加设备,可实现
更多车型
附表2 不同生产方式和车型数量条件下MINO柔性总拼焊接系统的设备投入情况
明珞装备白车身柔性总拼系统主要子系统介绍
1、车身合拼子系统
图2 车身合拼子系统示意图
图3 车身Frame合拼局部示意图
如右图2所示,车身合拼子系统由合拼滑台总成、FRAME总成、及FRAME定位总成3大总成构成。其中合拼滑台总成采用主流的解决方式设计,为满足FRAME合拼时的精度及动力性能,在传动方式上放弃了齿轮齿条传动形式,而改用曲柄滑块结构驱动,该方式的最显著特点是保证整个开合过程中FRAME的运动速度是正弦函数关系,加减速过程非常平稳,降低控制难度,同时该方式的控制精度比相同条件下齿轮齿条传动的精度高5到6倍。关于合拼方式,形式上与现有主流总拼焊接系统中一
种应用最广的柔性系统方式相似,但为了提高合拼精度及稳定性,在结构上做了较大的改进及创新。(图3为与主要竞争产品比较改进后的FRAME合拼局部示意图)
2、高速台车输送子系统(如图4所示)
高速台车系统是区别于传统往复杆输送系统及滚床输送系统的新技术,同传统输送方式一样,该子系统用于地板及车身的工位间传输,其传输速度直接影响生产线的效率和设备投资。在高节拍生产模式下,采用高速台车输送系统的地板或主焊接线,由于大大增加有效工作时间,整个生产线投资能较传统输送系统节省15%以上;
图4 MINO高速台车输送子系统示意图
明珞装备自主开发的高速台车输送系统结合了日本和欧洲先进的技术并融合创新,现已完成关键技术指标的权威测试,并成功获得国家科技部创新基金支持。
高速台车输送子系统关键技术参数如下:
1) 输送节拍:5.5S
2) 输送距离:6000mm
3) 负载能力:1300Kg
4) 电气定位:±0.4mm (应用于补焊工位)
5) 机械定位:±0.15mm(应用于定位焊工位)
6) 共线车型:4~8款
(明珞装备白车身柔性总拼焊接系统也可以根据客户要求开发或使用其他的输送方式)
3、地板柔性定位单元子系统
该子系统由8个NC Locator单元并列构成,用于地板定位、固定车身总成或地板总成,并实现多车型共线的生产解决方案。每个独立的NC Locator单元有3轴或5轴不同配置(根据实际生产情况需要进行配置)。
采用本系统的优点是:地板定位单元结构简单,理论上适用于任何车型的地板定位,新车型导入时,地板工位不需要增加新的设备,因此极大地降低了新车型导入的成本、缩短了新车型导入的设备周期,降低了新车型导入的难度。图5、图6分别是地板智能柔性定位系统的构成示意图及白车身定位示意图。
图5 地板智能柔性定位系统示意图
图6 白车身定位示意图
图7为明珞装备自主开发的柔性定位单元,其主要技术性能如下:
图7 测试中的MINO柔性定位单元
1) 能实现5自由度运动,其中2个直线自由度,3个旋转自由度,可根据不同使用工况,选择任意轴的组合,可实现单轴、2轴、3轴、4轴、5轴;
2) 行程范围: 450×300×300(可根据客户需求定制),3轴条件可满足相同定位孔径的几种不同车型的切换,5轴条件下可满足不同定位孔径的车型切换;
3) 全伺服控制,可通过PLC或示教器控制及定位,重复定位精度控制在±0.05mm;
4) 高刚性设计,最大负载180Kg;
5) 全密封式结构,防尘效果好,所有驱动部件均隐藏于机构当中,占用空间小。
(除上述独立式柔性定位单元外,明珞装备白车身柔性总拼焊接系统也可以根据客户要求开发或使用其他的柔性定位方式,图8为明珞装备为某日系整车客户开发的一体式柔性定位单元)
图8 MINO一体式柔性定位单元
4、车型切换子系统
图9 车型切换子系统示意图
多车型随机生产方式下,车型切换子系统是由4个夹具切换小车和若干条轨道组成的封闭轨道系统构成。其主要功能是根据不同的车型进行夹具切换,系统采用双轨道切换设计,包括夹具切换输送轨道和夹具返回轨道,当需要切换车型时,本系统将当前工作位的车型夹具切换到四面体存储单元中,同时从另一个四面体存储单元中将即将生产的车型夹具切换到当前工作位。夹具切换完成后,系统可通过夹具返回轨道适时调整两个存储单元的夹具数量,保证每次切换时都能做到实时的切换,不占用生产时间(如图9所示)。
5、工装存储系统
传统柔性总拼系统工装存储方式均是采用平面阵列式布置存储方式,这种方式优点是结
图10 工装存储子系统结构示意图
构简单,实现容易,缺点是设备较多,占地面积比较大。针对这种情况,本系统采用的方式是立体式空间阵列存储,这样大大减小了工装存储的空间,尤其车型越多时,优势越明显。本系统主体结构是一个回转半径2000mm的大型四面体翻转台,该翻转台可承载15吨负载,共有4个存储位,单边存储系统有2个翻转台,有8个存储位,最多可存储7种不同车型的夹具,通过该夹具存储系统,可以实现多达7种不同平台车型的柔性共线生产。具体结构形式如图10所示。
结语
明珞装备产品研发团队在充分分析和总结了现有各种白车身柔性总拼焊接系统优缺点,发现现有各种柔性总拼系统均存在一定的不足和局限性,通过多年的研究和分析,在先后完成多个方案的基础上,最终开发出了适用性更广泛、国际领先水平的具有完全自主知识产权白车身柔性总拼焊接系统,我们相信通过后续持续研发和不断完善,明珞装备研发成功的创新总拼系统一定能打破外资集成商在这一高端智能装备领域的垄断!
白车身焊装焊接工艺处理
车身焊接工艺 一、车身装焊工艺的特点 汽车车身壳体是一个复杂的结构件,它是由百余种、甚至数百种薄板冲压件经焊接、铆接、机械联结及粘接等方法联结而成的。由于车身冲压件的材料大都是具有良好焊接性能的低碳钢,所以焊接是现代车身制造中应用最广泛的联结方式。表1列举了车身制造中常用的焊接方法: 车身制造中应用最多的是电阻焊,一般占整个焊接工作量的60%以上,有的车身几乎全部采用电阻焊。除此之外就是二氧化碳碳气体保护焊,它主要用于车身骨架和车身总成的焊接中。 由于车身零件大都是薄壁板件或薄壁杆件,其刚性很差,所以在装焊过程中必须使用多点定位夹紧的专用装焊夹具,以保证各零件或合件在焊接处的贴合和相互位置,特别是门窗等孔洞的尺寸等。这也是车身装焊工艺的特点之一。 为便于制造,车身设计时,通常将车身划分为若干个分总成,各分总成又划分为若干个合件,合件由若干个零件组成。车身装焊的顺序则是上述过程的逆过程,即先将
若干个零件装焊成合件,再将若干个合件和零件装焊成分总成,最后将分总成和合件、零件装焊成车身总成。轿车白车身装焊大致的程序图为如图1所示:
电阻焊 1.电阻焊及其特点 将置于两电极之间的工件加压,并在焊接处通以电流,利用电流通过工件本身产的的热量来加热而形成局部熔化,断电冷却时,在压力继续作用下而形成牢固接头。这种工艺过程称为电阻焊。电阻焊的种类很多,按接头形式可分为搭接电阻焊和对接电阻焊两种。结合工艺方法,搭接电阻焊又可分为点焊、缝焊和凸焊三种,对接电阻焊一般有电阻对焊和闪光对焊两种。 特点: (1)利用电流通过工件焊接处的电阻而产生的热量对工件加热。即热量不是来源于工件之外,而是内部热源。 (2)整个焊接过程都是在压力作用校完成的,即必须施加压力。 (3)在焊接处不需加任何填充材料,也不需任何保护剂。 形成电阻焊接头的基本条件只有电极压力和焊接电流。 2.点焊 点焊是利用在焊件间形成的一个个焊点来联接焊件的。两焊件被压紧于两柱形电极之间并通以强大的电流,利用电阻热将工件焊接区加热到形成应有尺寸的熔化核心为止。然后切断电流,熔核在压力作用下冷却结晶形成焊点。点焊在车身制造中应用最广。点焊的形式很多,但按供电方向来分只有单面点焊和双面点焊两种。在这两种点焊中按同时完成的焊点数又可分为单点、双点和多点焊。 点焊是车身制造中应用最广的焊接方法,一辆轿车的车身上有3500~5000个焊点,可以说,汽车车身是一个典型的点焊结构件。 (1)点焊的机械性质 A.与铆接和螺栓紧固相比,点焊无松动且刚性高,但滑动系数小,在设计时必须注意可能会出现的应力集中。
白车身焊装焊接工艺
白车身焊装焊接工艺 车身焊接工艺 一、车身装焊工艺的特点 汽车车身壳体是一个复杂的结构件,它是由百余种、甚至数百种薄板冲压件经焊接、铆接、机械联结及粘接等方法联结而成的。由于车身冲压件的材料大都是具有良好焊接性能的低 碳钢,所以焊接是现代车身制造中应用最广泛的联结方式。表1列举了车身制造中常用的 焊接方法: 表1 车身制造中常用的焊接方法及典型应用实例 车身制造中应用最多的是电阻焊,一般占整个焊接工作量的60%以上,有的车身几乎全部 采用电阻焊。除此之外就是二氧化碳碳气体保护焊,它主要用于车身骨架和车身总成的焊 接中。 由于车身零件大都是薄壁板件或薄壁杆件,其刚性很差,所以在装焊过程中 必须使用多点定位夹紧的专用装焊夹具,以保证各零件或合件在焊接处的贴合和相互位置,特别是门窗等孔洞的尺寸等。这也是车身装焊工艺的特点之一。 为便于制造,车身设计时,通常将车身划分为若干个分总成,各分总成又划分为若干个合件,合件由若干个零件组成。车身装焊的顺序则是上述过程的逆过程,即先将 若干个零件装焊成合件,再将若干个合件和零件装焊成分总成,最后将分总成和合件、零 件装焊成车身总成。轿车白车身装焊大致的程序图为如图1所示: 电阻焊 1.电阻焊及其特点 将置于两电极之间的工件加压,并在焊接处通以电流,利用电流通过工件本身产的的热量 来加热而形成局部熔化,断电冷却时,在压力继续作用下而形成牢固接头。这种工艺过程 称为电阻焊。电阻焊的种类很多,按接头形式可分为搭接电阻焊和对接电阻焊两种。结合 工艺方法,搭接电阻焊又可分为点焊、缝焊和凸焊三种,对接电阻焊一般有电阻对焊和闪 光对焊两种。 特点: (1)利用电流通过工件焊接处的电阻而产生的热量对工件加热。即热量不是来源于工件 之外,而是内部热源。 (2)整个焊接过程都是在压力作用校完成的,即必须施加压力。 (3)在焊接处不需加任何填充材料,也不需任何保护剂。 形成电阻焊接头的基本条件只有电极压力和焊接电流。 2.点焊 点焊是利用在焊件间形成的一个个焊点来联接焊件的。两焊件被压紧于两柱形电极之间并 通以强大的电流,利用电阻热将工件焊接区加热到形成应有尺寸的熔化核心为止。然后切 断电流,熔核在压力作用下冷却结晶形成焊点。 点焊在车身制造中应用最广。点焊的形式很多,但按供电方向来分只有单面 点焊和双面点焊两种。在这两种点焊中按同时完成的焊点数又可分为单点、双点和多点焊。
汽车制造实用工艺——焊装
编辑此次参观了第二工厂的焊装车间、总装车间、试车场,以及襄樊动力总成厂的发动机生产车间。值得一提的是,后续我们还探访了位于襄樊的国家汽车质量监督检验中心,这里是国众多汽车厂商对车辆性能进行试验、路试的重要基地,在后续报道中我们会为大家带来该检验中心的详细信息。 『在后续的报道中我们还将带来总成车间和襄樊工厂的更多容』 汽车制造基本工艺: 介绍焊装工厂之前,我们先来简单叙述一下汽车的基本制造流程。汽车制造流程中主要有四大工艺,即车身冲压、车身焊装、车身涂装、整车总装。这四大工艺流程一般都是在整车厂完成,但发动机、变速器、车桥、车身附件、饰件等部件一般都是在整车厂外完成制造,然后运输到整车厂与车身一起组装成整车。 『此图为神龙公司第一冲压车间,东风雪铁龙C5的冲压在这里完成』
需要说明的是,在神龙第二工厂没有冲压车间,东风雪铁龙C5的钢板的冲压是在第一工厂完成后运送到第二工厂来的,在第二工厂东风雪铁龙C5要进行的第一个步骤就是焊接工艺。通过了解,从目前的生产状况来看,第二工厂焊装车间的柔性化成型技术、在线激光三座标检测是较为先进的技术,不过在机器人的使用率等方面并没有明显的优势。话不多说了,我们来看看东风雪铁龙C5的焊接工艺吧。 ●神龙公司第二工厂焊装分厂介绍: 焊装分厂厂房面积4.66万平米,有ALW航空激光焊接、柔性化车身成型工艺、激光在线三座标测量等焊接和检测工艺,目的是为了打造东风雪铁龙C5的“救生舱式高强度车身”。其供应商与欧洲新雪铁龙C5相同,属于PSA集团下的设备供应商CFER。
在神龙第二工厂的焊装车间,基本的工艺流程是先将各个冲压好的零部件分别焊装,其中包括了车身前后端等部件;然后是地板线的焊装,这里完成了车身前后侧围等部分的焊装过程;地板部分焊装好后,就进入了车身成型线的焊装,经过这个工序之后,我们可以看
白车身焊装焊接工艺
白车身焊装焊接工艺Last revision on 21 December 2020
车身焊接工艺 一、车身装焊工艺的特点 汽车车身壳体是一个复杂的结构件,它是由百余种、甚至数百种薄板冲压件经焊接、铆接、机械联结及粘接等方法联结而成的。由于车身冲压件的材料大都是具有良好焊接性能的低碳钢,所以焊接是现代车身制造中应用最广泛的联结方式。表1列举了车身制造中常用的焊接方法: 表1 车身制造中常用的焊接方法及典型应用实例 车身制造中应用最多的是电阻焊,一般占整个焊接工作量的60%以上,有的车身几乎全部采用电阻焊。除此之外就是二氧化碳碳气体保护焊,它主要用于车身骨架和车身总成的焊接中。 由于车身零件大都是薄壁板件或薄壁杆件,其刚性很差,所以在装焊过程中必须使用多点定位夹紧的专用装焊夹具,以保证各零件或合件在焊接处的贴合和相互位置,特别是门窗等孔洞的尺寸等。这也是车身装焊工艺的特点之一。
为便于制造,车身设计时,通常将车身划分为若干个分总成,各分总成又划分为若干个合件,合件由若干个零件组成。车身装焊的顺序则是上述过程的逆过程,即先将 若干个零件装焊成合件,再将若干个合件和零件装焊成分总成,最后将分总成和合件、零件装焊成车身总成。轿车白车身装焊大致的程序图为如图1所示:
电阻焊 1.电阻焊及其特点 将置于两电极之间的工件加压,并在焊接处通以电流,利用电流通过工件本身产的的热量来加热而形成局部熔化,断电冷却时,在压力继续作用下而形成牢固接头。这种工艺过程称为电阻焊。电阻焊的种类很多,按接头形式可分为搭接电阻焊和对接电阻焊两种。结合工艺方法,搭接电阻焊又可分为点焊、缝焊和凸焊三种,对接电阻焊一般有电阻对焊和闪光对焊两种。 特点: (1)利用电流通过工件焊接处的电阻而产生的热量对工件加热。即热量不是来源于工件之外,而是内部热源。 (2)整个焊接过程都是在压力作用校完成的,即必须施加压力。 (3)在焊接处不需加任何填充材料,也不需任何保护剂。 形成电阻焊接头的基本条件只有电极压力和焊接电流。 2.点焊 点焊是利用在焊件间形成的一个个焊点来联接焊件的。两焊件被压紧于两柱形电极之间并通以强大的电流,利用电阻热将工件焊接区加热到形成应有尺寸的熔化核心为止。然后切断电流,熔核在压力作用下冷却结晶形成焊点。点焊在车身制造中应用最广。点焊的形式很多,但按供电方向来分只有单面点焊和双面点焊两种。在这两种点焊中按同时完成的焊点数又可分为单点、双点和多点焊。 点焊是车身制造中应用最广的焊接方法,一辆轿车的车身上有3500~5000个焊点,可以说,汽车车身是一个典型的点焊结构件。
白车身焊装工位结构介绍
车身焊装工位结构 1、焊装夹具基本构造 1.1、焊装夹具的用途(图1-1) 焊装夹具在车身生产中的作用是:通过夹具上的定位销(基准销)、S 面型块(基准面)、夹紧臂等组件的协调作用,将工件(冲压件或总成件)安装到工艺设定的位置上并夹紧,不让工件活动位移,保证车身焊接精度的一致性和稳定性。 1.2、焊装夹具基本构造(图1-2) 夹具的基本构造:如图1-2所示,由台板、支座、L 板、基准销、基准面、夹紧机构(气缸、夹紧臂、U 型限位块等)等组成。 1.2.1、台板(图1-2-1) a 、用途 用于安装夹具组件,上表面加工有坐标刻度线,用于夹具基准状况的检测。 b 、安装要求
台面应处于水平状态(工艺设计要求倾斜放置的除外),安装时用测量仪、水平仪或透明胶管灌水检查校水平。多台连线安装的夹具(特别是采用举升自动搬送的装置),同轴度和水平度、节距应符合设计要求。 1.2.2、支座(图1-2-2) a 、用途 用于支撑夹具台板、夹具高度调节和安放水平调整,使夹具按工艺布置要求定置安放。 b 、安装要求 连接螺栓紧固可靠,调节螺杆应有垫板支撑,夹具定置调整符合要求后,要将调节螺杆螺母拧紧,若是大型夹具或连线夹具垫板应和基础预埋件可靠连接(焊接)。 图1-2-1 支座
1.2.3、L 板(图1-2-3) a 、用途 用于安装夹具型块(S 面元件)、基准销组件、夹紧机构、导向装置等夹具组件。 b 、安装要求 采用高强螺栓与台板连接,并配定位销定位,同夹具组件的连接也应采用高强螺栓连接,并配定位销定位。 1.2.4、基准面(S 面型块图1-2-4) a 、用途 将零件支承在正确的位置上,并支撑夹具夹紧机构的夹紧力。 b 、安装要求 基准面型块采用高强螺栓安装在L 板(或连接板)上,并用定位销定位,表面应经过调质处理,硬度在HRC48以上,一般会在基准面端部约10mm 宽的部位涂红色标记,基准面应与数模相符(用三坐标仪测量)。 图1-2-3
白车身焊装强度的质量控制
白车身焊装质量控制 汽车白车身的焊装质量控制受焊装后尺寸精度、焊装强度及外观质量等多种因素影响。为了强化白车身的焊装质量控制,从技术和管理两个方面加强努力,将现有生产存在的问题进行分类不断完善,从而提高产品质量,以有效提高车辆生产的“质投比”。白车身的焊装质量控制主要体现在4个方面:焊装后尺寸精度、焊装强度、外观质量以及减震抗噪密封性。用户对质量的要求,决定了生产厂商对质量。 用户对质量的要求,决定了生产厂商对质量的重视程度和投入程度。因尺寸精度影响后序零件的装配,不仅是用户的要求,生产厂商也必须给予足够的重视;减振抗噪密封性会影响用户的驾驶或乘座的舒适度,对此生产厂商也会重视;外观质量影响车身的美观,甚至直接影响生产企业的销售状况,生产厂商更会对其引起重视。然而,用户在购买车辆时唯独对焊装强度无法评判,总不能把新车撞一撞来试验其结实程度。由于用户在购买汽车时对车身强度的意识比较淡化,导致了生产厂商对焊装强度这个指标重视不够。 为了强化白车身的焊装质量控制,长安汽车公司目前正从技术和管理两个方面加强努力。 技术方面 一、技术管控 1.白车身精度的管控
众所周知,在汽车制造行业中,白车身的制造工艺是重中之重,其中白车身尺寸精度是保证整车零部件装配精度的基础。白车身焊接精度关系着整车装配的匹配性、整车的安全性,所以有效的控制、提高白车身的焊接精度,是整车质量的重要保证,也是产品能否具有市场竞争力的重要基础之一。车间车身精度的管控从工装夹具的管控开始,夹具的管控从日常 点检抓起,而且车间对夹具进行分类并定期进行精度检测。车间的装配工艺也是一项重要内容,编制了操作者进行生产时使用的作业指导书指导操作。对于白车身的监控车间每日开展开口检具检测,定期对车间部件开展PCF检测,以便及时发现生产过程中的尺寸问题。 2.车身强度的管控 车身强度关系到汽车的安全性能,目前焊装车间主要采用破坏性和非破坏性两种方式对车身进行严格控制。非破坏实验主要有撕裂实验和撬检。撕裂实验是开班前对焊接设备进行检测的一种方式,通过模拟真实的焊接环境,观察焊点质量是否合格,对开班时的焊枪进行监控。撬检是在生产过程中对焊点进行规定的焊点进行撬暂,是一种对焊接过程监控的方式,通过对焊点质量的观察来判定焊点是否合格。另外,车间每季度对生产线所有的焊钳参数检测一次,及时对不符合工艺要求的设备进行调整,防止因参数造成焊点质量问题。破坏性手段主要有撕裂,车间定期对白车身进行撕裂实验,主要白车身和外协件的对虚焊进行监控,随着公司对质量的严格要求,目前车间增加了对分总成的撕裂。 3.车身外观的管控
白车身焊装工艺设计概述.doc
汽车车身焊装工艺概述第一节焊装工艺分析 工艺性好坏的客观评价标准就是在一定的生产条件和规模下,能否保证以最少的原材料和加工劳动量,最经济地获得高质量的产品。影响车身焊装工艺性的主要因素有生产批量、车身产品分块、焊接结构、焊点布置等。 一.生产批量 车身的焊装工艺主要由生产批量的大小确定的。一般来说,批量越小,夹具的数量越少,自动化程度越低,每台夹具上所焊的车身产品件数量越多;反之,批量越大,焊装工位越多,夹具数量越多,自动化程度越高,每台夹具上所焊的车身产品件数量越少。 1.生产节拍的计算 2.时序图设计 时序图(TIME CHART)是指一个工位从零部件上料到焊好后合件取料的整个过程中所有动作顺序、时间分配以及相互间互锁关系,这些动作包括上下料(手动或自动),夹具夹紧松开,自动焊枪到位、焊接、退回以及传送装置的运动等。 由于每个车身装焊的零部件数量一定,焊点数量一定,焊接时
间一定,要达到一定生产节拍内完成所有焊接,就必须将工序分开,分工位上料、焊接。 二.车身产品分块 分块是将车身外壳体分成若干块便于冲压和焊装的零部件、组合件、分总成和总成。合理的分块不仅有利于形成良好的装配质量,并可有效地简化和优化制造工艺。 汽车白车身是一个尺寸很大的复杂的焊接结构件,设计制造时常常是将车身总成合理地划分为若干个部件和组合件,分别进行装配焊接成分总成件,然后再装配焊接成总成结构,这样化复杂为简单,化大为小,可以大大提高劳动生产率,改善结构的焊接工艺性。 1.结构分离面 将白车身总成分解为若干个分总成,相邻两个分总成的结合面称为分离面。分离面可以分为两类: (1)设计分离面 根据使用上和构造上的特点,将汽车车身分成为可以单独进行装配的分总成,如发动机罩、行李厢盖、车门、车身本体等,这些分总成之间的结合面,称 为设计分离面。 设计分离面一般采用可拆卸的连接,如铰链连接,以便在使用和维修过程中迅速拆卸和重新安装,而不损坏整体结构。(2)工艺分离面
汽车车身焊装工艺技术(DOCX 51页)
汽车车身焊装工艺技术(DOCX 51页)
汽车车身焊装工艺 汽车车身装配主要采用焊接方式,在汽车车身结构设计时就必须考虑零部件的装配工艺性。焊装工艺设计与车身产品设计及冲压工艺设计是互相联系、互相制约的,必须进行综合考虑,它是影响车身制造质量的重要因素。 第一节焊装工艺分析 工艺性好坏的客观评价标准就是在一定的生产条件和规模下,能否保证以最少的原材料和加工劳动量,最经济地获得高质量的产品。影响车身焊装工艺性的主要因素有生产批量、车身产品分块、焊接结构、焊点布置等。 一.生产批量 车身的焊装工艺主要由生产批量的大小确定的。一般来说,批量越小,夹具的数量越少,自动化程度越低,每台夹具上所焊的车身产品件数量越多;反之,批量越大,焊装工位越多,夹具数量越多,自动化程度越高,每台夹具上所焊的车身产品件数量越少。 1.生产节拍的计算 生产节拍是指设备正常运行过程中,单位产品生产所需要的时间。 假设某车年生产纲领是30000辆份 / 年 工作制:双班,250个工作日,每个工作日时间为8小时
设备开工率:85% 则生产节拍的计算为: 2.时序图设计 时序图(TIME CHART)是指一个工位从零部件上料到焊好后合件取料的整个过程中所有动作顺序、时间分配以及相互间互锁关系,这些动作包括上下料(手动或自动),夹具夹紧松开,自动焊枪到位、焊接、退回以及传送装置的运动等。生产线上每个工位的时序图设计总时间以满足生产节拍为依据,同时时序图也是焊装线电气控制设计的技术文件和依据,是机电的交互接口。 如图4-1所示为一张时序图,它的内容包括: (1)设备名称,它是以完成动作的单元来划分。例如移动装置,夹具单元1,焊接,车身零部件名称等。其中车身零件名称表示上料动作,组件名称表示取料动作。 2)相应设备的动作名称,它是以动力源的动作来划分的。例如移动装置是由气缸驱动上下运动和电机驱动工位间前后运动组成,它的动作名称分别为上升,下降,前进,后退;再例如夹具是由夹紧气缸驱动夹紧,它的动作名称分为夹紧,打开等。 (3)各动作顺序及时间分配,动作时间表分配是以坐标网格的形式标记,每格单位为5秒,一个循环总时间为生产节拍,各动作之间的前后顺序关系图用箭头线标识。一般气缸
白车身焊接工艺
白车身焊接工艺 目前公司运用的焊接方法有:点焊,凸焊,螺柱焊,二氧化碳保护焊,手工电弧焊。 点焊: 电弧焊:将被焊工件压紧于两电极之间,并通以电流,利用电流流经工件接触面及领近区域产生的电阻热将其加热到熔化或塑性状态,使之形成金属结合的一种方法。包括点焊,缝焊,凸焊,对焊。 优点:1.熔核形成时,始终被塑性环包围,融化金属与空气隔绝,冶金过程简单。 2.加热时间短,热量集中,故热影响区小,变形应力小。 3.焊接成本低 缺点:无可靠无损检测方法,点,缝焊的搭接头不仅增加了构件的质量,且因在两板间熔核周围形成夹角,使接头处的抗拉强度和疲劳强度均较低。 金属电阻焊时的焊接性(主要指标): 1.材料的导电性和导热性 2.材料的高温强度(越高焊接性越差) 3.材料对热循环的敏感性 熔点高,线膨胀系数大,易形成致密的氧化膜的金属,其焊接性能差。 点焊:工件只在有限的接触面上,即所谓“点”上被焊接起来,并形成扁球形的熔核。 焊接电极:是保证电焊质量的重要零件,其主要功能:向工件传导电流,向工件传递压力,迅速到山焊接区的热量。主要构成:端部,主体,尾部和冷却水孔。 电焊方法:双面焊和单面焊 双面焊时,电极由工件的两侧向焊接处溃点。 单面焊时,电极由工件的一侧向焊接处溃点。不形成焊点的电极采用大直径和大接触面积以减少电流密度。 点焊工艺参数:焊接电流,焊接压力,焊接时间 当进行不等厚度或不同材料电焊时,熔核将不对称于其交界面,而是向厚板或导电,导热性差的一边偏倚,结果使薄件或导电,导热性好的工件焊透率低,焊接强度小。熔核偏移的原因是有两工减产热和散热条件不相同引起的。 焊接接头:通常采用搭接街头和折边接头。接头可以由两个或两个以上等厚或不等厚度的工件组成。设计点焊结构时,必须考虑电极的可达性。同时,还应考虑如边距(取决被焊金属种类,厚度和焊接条件),搭边量(是边距的两倍),点距(最小值考虑分流),装配间隙(尽量小)和焊点强度(以正拉强度和抗剪强度之比作为判断接头延性的指标。值越大越好)等因数。 凸焊:凸焊是电焊的变型,在一个工件上有预制的凸点,凸焊时,一次在接头处形成一个或多个熔核。 应用场合:低碳钢和低合金钢,板件,螺帽,螺钉类零件等,厚度一般为0.5-4mm。 焊接模具是用于保持和夹紧工件于适当位置,同时也可用于电极。 夹具是不导电的辅助装置。对于小的工件,电极和夹具通常是合为一体。 凸焊工艺特点:由于电流集中,克服点焊时熔核偏移的缺点。凸焊时,电极必须随凸点被压溃而快速下降,否则会应失压而产生飞溅。 凸焊工艺参数:电极压力,焊接时间,焊接电流。
整车焊装工艺认识(1)
整车焊装工艺认识 汽车制造中的焊接工艺汽车制造四大工艺中,焊装尤其重要,而在焊装的前期规划中,车身焊接夹具的设计又是关键环节。工装夹具的设计是一门经验性很强的综合性技术,在设计时首先应考虑的是生产纲领,同时还必须熟悉产品结构,了解钣金件变形特点,把握零部件装配精度及容差分配,通晓工艺要求。只有做到这些,才能对焊接夹具进行全方位的设计,满足生产制造要求。汽车焊接生产线也是是汽车制造中的关键,焊接生产线中的各种工装夹具又是焊装线的重中之重,焊接夹具的设计则是前提和基础。设计工装夹具时,不仅要考虑生产纲领,还必须要熟悉产品结构,了解钣金件变形特点,通晓工艺要求等诸多内容。 生产纲领即合格产品的年产量,它决定了焊接夹具的自动化水平及焊接工位的配置,是通过生产节拍体现的,是焊接夹具设计首先应考虑的问题。生产节拍由夹具动作时间、装配时间、焊接时间、搬运时间等组成。夹具动作时间主要取决于夹具的自动化程度;装配时间主要取决于冲压件精度、工序件精度、操作者的熟练程度;焊接时间主要取决于焊接工艺水平、焊接设备的自动化程度、焊钳选型的合理化程度等;搬运时间主要取决于搬运的自动化程度、物流的合理化程度及生产现场管理水平等。只要把握以上几点,就能合理地解决焊接夹具的自动化水平与制造成本的矛盾。 汽车车身的结构特点与焊接的关系汽车车身一般由外覆盖件、内覆盖件和骨架件组成,覆盖件的钢板厚度一般为0.8~1.2mm,有的车型外覆盖件钣金厚度仅有0.6mm、0.7mm,骨架件的钢板厚度多为1.2~2.5mm,也就是说它们大都为薄板件。 对焊接夹具设计来说,应考虑如下特点: 1. 刚性差、易变形经过成型的薄板冲压件有一定的刚性,但与机械加工件相比,刚性要差得多,而且单个大型冲压件容易变形,只有焊接成车身壳体后,才具有较强的刚性。以轿车车身大侧围外板为例,一般材料厚度为0.7~0.8mm,绝大多数是0.8mm,拉延形成空腔后,刚性非常差,当和内板件焊接形成侧围焊接总成后才具有较强的刚性。 2. 结构形状复杂汽车车身都是由薄板冲压件装焊而成的空间壳体,为了造型美观,并使壳体具有一定的刚性,组成车身的零件通常是经过拉延成型的空间曲面体,结构形状较为复杂。特别是随着现代汽车技术的发展和消费者对汽车品质和外观时尚的要求越来越高,车身结构设计也越来越复杂。 3. 以空间三维坐标标注尺寸汽车车身产品图以空间三维坐标来标注尺寸。为了表示覆盖件在汽车上的位置和便于标注尺寸,汽车车身一般每隔200mm或400mm划一坐标网线,而整车坐标系各有不同,这里举轿车为例,一般定义整车坐标系坐标原点是:X轴:车身的对称平面与主地板的下平面之间的交线,向车身后方为正,前方为负。Y轴:过前轮的中心连线且垂直于车身地板下平面的平面与车身对称平面之间的交线,向车身右侧为正,左侧为负。Z轴:过两前轮中心且与主地板平面垂直的直线,向上为正,向下为负。装配精度装配精度包括两方面:外观精度与骨架精度,外观精度指门盖等开闭件装配后的间隙面差;骨架精度指三维坐标值。货车车身的装配精度一般控制在2mm内,轿车控制在1mm内。焊接夹具的设计既要保证工序件之间的焊装要求,又要保证总体的焊接精度,通过调整工序件之间的匹配状态及容差分配来满足整体的装配要求。车身焊装夹具设计方法6点定则是汽车车身焊装夹具设计的主要方法,其含义是指限制6 个方向运动的自由度。在设计车身焊装夹具时,常有两种误解:一是认为6点定位原则对薄板焊装夹具不适用;二是看到薄板焊装夹具上有超定位现象。产生这种误解的原因是,把限制6个方向运动的自由度理解为限制6个方向的自由度。焊接夹具设计的宗旨是限制6个方向运动的自由度,这种限制不仅依靠夹具的定位夹紧装置,而且依靠制件之间的相互制约关系。只有正确认识了薄板冲压件焊装生产的特点,同时又正确理解了6点定则,才能正确应用这个原则。 1. 保证门洞的装配尺寸门洞的装配尺寸是整车外观间隙阶差的基础,当总成焊接无
汽车车身的焊接工艺及其措施
龙源期刊网 https://www.360docs.net/doc/7b18905981.html, 汽车车身的焊接工艺及其措施 作者:孙海 来源:《西部论丛》2017年第04期 摘要:汽车结构中的壳体是属于一种繁杂的组合体,其基本是由百余样薄板冲压式工件 利用粘合、铆钉、焊制、机械式紧固等连接方式进行组合和构置而成。一般情况下,由于汽车车体冲压件本身所用的材料都是一些低碳型钢材,此类钢材具备很好的焊接品质。故此,在实施车体焊制活动时其时常显示出操作方便、节省钢料、密封性强等品质特点。同时又因为汽车本身壳体具有很强的结构复杂性,故针对车体焊制程序的设计内容彰显出了其自身独有的重要性,其是实现汽车制造品质改进的必要性条件,故本文在此针对汽车车体焊制程序设计做出粗浅分析。 关键词:汽车车身焊接工艺措施 1汽车车身焊接工艺概况 汽车制造中必须高度重视焊接工艺,关乎到汽车整体性能的发挥,也是汽车在制造的过程中必须经历的环节之一。汽车车身的焊接是复杂的过程,由于车身壳体是经过百余种及数百种薄板冲压而成,需要将其通过焊接、铆接、机械联结及粘接等工艺方法,联合成一个有机的统一体,是艰巨而复杂的过程,期间针对车身的材料焊接需要选取技术含量高的技术。这样即可以节省材料又便于操作,特别是焊接技术的选取,其密封性较好,具有众多的优势性能,是现代汽车制造中运用最为广泛的方法。 2焊接工艺技术在汽车行业的应用现状分析 如今我国处于交通行业迅猛发展的时代,人均汽车占有量猛增,汽车成为很多中国家庭必备的出行工具,而汽车生产工艺也在不断进行升级,与之相关的汽车维修与保养行业地位也有着提升,可以说,汽车使用率的增长给汽车服务业带来了发展的春天。汽车焊接工艺在汽车生产行业发展前期主要应用在汽车车身的焊接与调整方面,但在汽车生产工艺技术不断发展的当下,汽车车身制造已经不再需要焊接工艺的参与,而是采用了模具制造的技术方式,这样可以提高汽车车身生产的标准性,而当前汽车行业对于焊接工艺的应用主要是在汽车车身细节配件的安装焊接和汽车后期维修与改 装中。 1)在汽车维修领域,汽车焊接工艺的应用主要是解决一些由于汽车碰撞而产生的损伤,是保证汽车车身与其相应配件使用性能的一种方式,汽车维修工作人员利用汽车焊接工艺技术来调整发生位移的车身配件等,使车身与其配件的位置更加精准,连接更加牢固。
白车身焊装焊接工艺
白车身焊装焊接工艺文件排版存档编号:[UYTR-OUPT28-KBNTL98-UYNN208]
车身焊接工艺 一、车身装焊工艺的特点 汽车车身壳体是一个复杂的结构件,它是由百余种、甚至数百种薄板冲压件经焊接、铆接、机械联结及粘接等方法联结而成的。由于车身冲压件的材料大都是具有良好焊接性能的低碳钢,所以焊接是现代车身制造中应用最广泛的联结方式。表1列举了车身制造中常用的焊接方法: 表1 车身制造中常用的焊接方法及典型应用实例
车身制造中应用最多的是电阻焊,一般占整个焊接工作量的60%以上,有的车身几乎全部采用电阻焊。除此之外就是二氧化碳碳气体保护焊,它主要用于车身骨架和车身总成的焊接中。
由于车身零件大都是薄壁板件或薄壁杆件,其刚性很差,所以在装焊过程中必须使用多点定位夹紧的专用装焊夹具,以保证各零件或合件在焊接处的贴合和相互位置,特别是门窗等孔洞的尺寸等。这也是车身装焊工艺的特点之一。 为便于制造,车身设计时,通常将车身划分为若干个分总成,各分总成又划分为若干个合件,合件由若干个零件组成。车身装焊的顺序则是上述过程的逆过程,即先将 若干个零件装焊成合件,再将若干个合件和零件装焊成分总成,最后将分总成和合件、零件装焊成车身总成。轿车白车身装焊大致的程序图为如图1所示:
电阻焊 1.电阻焊及其特点 将置于两电极之间的工件加压,并在焊接处通以电流,利用电流通过工件本身产的的热量来加热而形成局部熔化,断电冷却时,在压力继续作用下而形成牢固接头。这种工艺过程称为电阻焊。电阻焊的种类很多,按接头形式可分为搭接电阻焊和对接电阻焊两种。结合工艺方法,搭接电阻焊又可分为点焊、缝焊和凸焊三种,对接电阻焊一般有电阻对焊和闪光对焊两种。 特点: (1)利用电流通过工件焊接处的电阻而产生的热量对工件加热。即热量不是来源于工件之外,而是内部热源。 (2)整个焊接过程都是在压力作用校完成的,即必须施加压力。 (3)在焊接处不需加任何填充材料,也不需任何保护剂。 形成电阻焊接头的基本条件只有电极压力和焊接电流。 2.点焊 点焊是利用在焊件间形成的一个个焊点来联接焊件的。两焊件被压紧于两柱形电极之间并通以强大的电流,利用电阻热将工件焊接区加热到形成应有尺寸的熔化核心为止。然后切断电流,熔核在压力作用下冷却结晶形成焊点。点焊在车身制造中应用最广。点焊的形式很多,但按供电方向来分
白车身焊装工艺设计概述
汽车车身焊装工艺概述 第一节焊装工艺分析 工艺性好坏的客观评价标准就是在一定的生产条件和规模下,能否保证以最少的原材料和加工劳动量,最经济地获得高质量的产品。影响车身焊装工艺性的主要因素有生产批量、车身产品分块、焊接结构、焊点布置等。 一.生产批量 车身的焊装工艺主要由生产批量的大小确定的。一般来说,批量越小,夹具的数量越少,自动化程度越低,每台夹具上所焊的车身产品件数量越多;反之,批量越大,焊装工位越多,夹具数量越多,自动化程度越高,每台夹具上所焊的车身产品件数量越少。 1.生产节拍的计算 2.时序图设计 时序图(TIME CHART)是指一个工位从零部件上料到焊好后合件取料的整个过程中所有动作顺序、时间分配以及相互间互锁关系,这些动作包括上下料(手动或自动),夹具夹紧松开,自动焊枪到位、焊接、退回以及传送装置的运动等。 由于每个车身装焊的零部件数量一定,焊点数量一定,焊接时间一定,要达到一定生产节拍内完成所有焊接,就必须将工序分开,分工位上料、焊接。二.车身产品分块 分块是将车身外壳体分成若干块便于冲压和焊装的零部件、组合件、分总成和总成。合理的分块不仅有利于形成良好的装配质量,并可有效地简化和优化制造工艺。 汽车白车身是一个尺寸很大的复杂的焊接结构件,设计制造时常常是将车身总成合理地划分为若干个部件和组合件,分别进行装配焊接成分总成件,然后再装配焊接成总成结构,这样化复杂为简单,化大为小,可以大大提高劳动生产率,改善结构的焊接工艺性。 1.结构分离面 将白车身总成分解为若干个分总成,相邻两个分总成的结合面称为分离面。分离面可以分为两类: (1)设计分离面 根据使用上和构造上的特点,将汽车车身分成为可以单独进行装配的分总成,如发动机罩、行李厢盖、车门、车身本体等,这些分总成之间的结合面,称
车身焊接工艺
车身焊接工艺 1. X围本标准规定了本公司车辆产品车身装焊应遵守的基本规则;本标准适用于本公司车辆产品自制结构件的装焊作业。 2. 引用标准下列文件的条款通过本标准的引用而成为本标准的条款,凡是注日期的引用文件,其随后所有的修改单(不包刮勘误的内容)或修订版均不适用于本标准,然而,鼓励根据本标准达成协议的各方研究是否可使用这些文件的最新版本。/T 9186 二氧化碳气体报护焊工艺规程《焊接手册》机械工业NES M 0109-1985 焊接接头试验方法通则NES M 0112-1993 焊接接头拉伸剪切试验方法NES M 0115-1993 焊接接头显微镜试验方法 3. 公司应用的焊接方法公司应用的焊接方法见表1表1 公司应用的焊接方法焊接方法应用X围电阻焊点焊悬挂式点焊车身分总成机器人点焊车身分总成固定点焊车身小型零部件凸焊螺母板、小分装件(板厚比超过1:3)螺柱焊分总成植钉焊分总成电弧焊CO2气保焊(弧焊机器人)仪表骨架总成、车身分总成CO2气体保护焊(半自动) 补焊车、身分总成 4. 焊接用辅料选用原则焊接用辅料选用原则见表2表2 焊接用辅料选用原则焊接方法辅料名称牌号及纯度点焊上下电极头铬锆铜等凸焊电极头焊接模具和夹具/ 定位销绝缘体或外层渡上绝缘材料CO2气体保护焊焊丝H08MnSiA等CO2气体CO2纯度大于99.5%,水分含量小于1~9g/m3 5. 焊接工艺参数及要点焊接工艺参数及要点见表3表3 焊接工艺参数及要点序号焊接方法工艺参数工艺要点1 电阻焊搭接宽度见表42 装配间隙务必控制在(0~1)mmX围内3 焊点间距不能小于表4中的最小间距,以免产生分流,对于多层焊,焊点距增大(20~25)%4 预压时间在达到压紧状态的情况下尽可能缩预压时间,提高生产效率。5 焊接时间见8项初选工艺规X表6 焊接压力焊接压力的大小影响接触电阻、电流密度、电极散热效果及焊接区的塑性变形,压力不足会起压痕过深、表面径向裂纹,影响焊接强度,压力大小具体见初选工艺规X表。7 焊接电流焊接电流影响熔核直径和焊透率,电流增大时,其熔核直径、焊透率也会增大;但电流过大,易产生飞溅,焊点强度降低,电流过小,易产生焊不透,熔核直径小等缺陷,具体见初选工艺规X表。8 预热电流预热时间对于淬透性较大,电导率、热导率较高的钢材,可通过调整电流缓升或缓降以达到预热或缓冷的目的9 冷却时间对于1~8mm的钢板,其冷却结晶时间一般为(0.1~2.5)s 5-125CYCLE (50HZ)10 休止时间休止时间为电极开始提起到电极第二次开始下降的时间,休止时间的长短影响连续打点的速度。11 电极直径电极直径的大小影响电流密度、熔核直径、散热效果,因此应根据不同的板厚选择合适的电极直径,具体见初选工艺规X表。12 连续打点次数电极使用寿命连续打点次数试验后确定,电极的使用寿命见电极更换基准。13 熔核直径熔核率压痕深度拉剪负荷(熔核直径、熔核率、压痕深度、拉剪负荷是质量特性)熔核直径的计算和判定见表5,熔核率计算:η=h/(δ-c)100%,一般熔透率为20~80%, h(熔核最大高度) ,δ(板厚),c(压痕深度)。压痕深度:不超过15%,特殊情况可增大到20~25%。14 CO2气保焊焊接电流(送丝速度)、对于不同的焊丝直径,焊接电流是不一样的,电流过大,易产生组织粗大、烧穿;电流过小,易产生焊不透、咬边。15 焊接电压对于一定的焊丝直径与焊接电流,必须选用合适的焊接电压匹配才能获得稳定短路过渡效果,具体匹配见表1116 空载电压一般电弧电源的空载电压为(50~80)V17 收弧电流收弧电压控制收弧接头的质量和外观。18 气体流量焊接过程中,CO2气体保护焊气体流量与焊丝直径、焊接电流、焊接速度、焊接周围环境、焊接位置有关,室外或仰焊时流量适当增大;气体流量过大和过小都会产生保护不良,具体见表11。19 气瓶使用气压
焊装工艺
4.4.3 焊装 本车间主要承担CS11车型车身总成及分总成的焊装、打磨、调整等任务,同时承担白车身总成及分总成的检测、白车身总成储存及焊接设备和夹具的日常维修任务。 4.4.3.1 设计原则 车间布置1条主焊线和1条调整线(分为装配区和打磨区); 主焊线、下部线、侧围、后地板、机舱、顶盖总成线等关键工位采用机器人焊接; 门盖区采用机器人涂胶滚边。 4.4.3.2 生产组织 车身总成和大型分总成按均衡流水方式组织生产,小总成集中轮番生产。4.4.3.3 设备及夹具 白车身总成及分总成以点焊为主,并有少量弧焊补焊。主焊线、下部线、侧围、后地板、机舱、顶盖总成线等采用机器人焊接方式,其它分总成线为人工中频点焊。四门两盖区采用机器人涂胶,内外板包边选用机器人滚边。 其它工序采用CMT冷金属过度CO2气体保护焊机、固定点焊机、螺柱焊机、涂胶泵等通用设备。 夹具多数为气动夹具。 4.4.3.4 车间运输 设置1条主焊线和下部线。主焊线和下部线均采用辊床滑橇或台车输送方式;车身下部总成和左、右侧围总成上主焊线采用EMS自行小车或FDS输送系统自动搬运;顶盖总成人工输送,机器人抓取上主焊线;前后地板总成、机舱总成上下部线也采用EMS自行小车输送系统自动搬运;侧围、后地板、机舱总成线间采用机器人自动搬运。 其余分总成工位间采用气动平衡吊输送,小总成采用人工搬运。 车身总成从主焊线到调整线采用辊床滑橇输送,调整线采用地板链输送。送往涂装车间的输送方式也为辊床滑橇,并在空中设置白车身存储平台,漆前存储量约60台,白车身送至涂装车间后,空橇返回焊装车间,构成滑橇循环线。 大型冲压件零件用叉车或专用运输车由冲压件库送至各总成焊接工位。
车身焊接工艺
车身焊接工艺 1. 范围 本标准规定了本公司车辆产品车身装焊应遵守的基本规则; 本标准适用于本公司车辆产品自制结构件的装焊作业。 2. 引用标准 下列文件的条款通过本标准的引用而成为本标准的条款,凡是注日期的引用文件,其随后所有的修改单(不包刮勘误的内容)或修订版均不适用于本标准,然而,鼓励根据本标准达成协议的各方研究是否可使用这些文件的最新版本。 JB/T 9186 二氧化碳气体报护焊工艺规程 《焊接手册》机械工业出版社 NES M 0109-1985 焊接接头试验方法通则 NES M 0112-1993 焊接接头拉伸剪切试验方法 NES M 0115-1993 焊接接头显微镜试验方法 3. 公司应用的焊接方法 公司应用的焊接方法见表1 表1 公司应用的焊接方法 焊接方法应用范围 电阻焊点焊悬挂式点焊车身分总成 机器人点焊车身分总成 固定点焊车身小型零部件 凸焊螺母板、小分装件(板厚比超过1:3) 螺柱焊分总成 植钉焊分总成 电弧焊CO2气保焊(弧焊机器人)仪表骨架总成、车身分总成 CO2气体保护焊(半自动) 补焊车、身分总成 4. 焊接用辅料选用原则 焊接用辅料选用原则见表2 表2 焊接用辅料选用原则 焊接方法辅料名称牌号及纯度 点焊上下电极头铬锆铜等 凸焊电极头 焊接模具和夹具/ 定位销绝缘体或外层渡上绝缘材料 CO2气体保护焊焊丝H08MnSiA等 CO2气体CO2纯度大于99.5%,水分含量小于1~9g/m3 5. 焊接工艺参数及要点 焊接工艺参数及要点见表3 表3 焊接工艺参数及要点 序号焊接方法工艺参数工艺要点 1 电阻焊搭接宽度见表4 2 装配间隙务必控制在(0~1)mm范围内 3 焊点间距不能小于表4中的最小间距,以免产生分流,对于多层焊,焊点距增大(20~25)%
白车身的焊装工艺性检查的操作指导书
白车身的焊装工艺性检查的操作指导书 一、目的: 推进“面向制造的设计”工作,白车身的设计就必须达到一定的工艺性。其基本要求是可制造,其进一步的要求是易制造,进而尽可能的降低成本。本操作指导书是为工艺设计的同步工程人员而编制的。 二、性质:满足产品功能需要前提下的工艺优化 三、适应范围:车身所有的总装工艺性 四、操作:与产品设计部门配合 五、内容: 总体检查项目 1.1与同类车比较 ●此项为总体检查,其目的是与同类车相比较,此款车的简繁程度。 ●建立国际同类产品的标竿数据库。 ●如冲压件数目较标竿值多,反映有潜力可以合并冲压件来简化焊装。 ●焊点多则反映焊装过于繁琐或者有不必要地焊点。 ●电焊长度过长是反映车身结构或是装配顺序不合理,可以进一步优化。 ●夹紧点较多则反映焊装夹具的设计过于繁琐。 ●模块划分是否合理性 1.2 逐件检查每个另件 ●检查每个零件和每个组件的存在必要性。 ●检查每个零件上每个细节的存在必要性。 ●检查每个细节的工艺合理性,包括孔,夹点和焊点。 ●检查从冲压件到分总成到总成的参考定位系的一致性和合理性。 1.3 努力目标 ●车身结构和加工工序简单。 ●设计为其配备工夹具简单易行。 ●与其他工件接口容易。 1.4定位的柔性生产的考虑 ●下部定位是否符合柔性生产的要求(具有与现有车型相同的定位孔) ●不同车型吊具能混线生产(具有与现有车型相同的吊孔) 1.5 检查几个难点 ●骨架合成 ●发动机仓装配 ●后轮罩装配。
车身焊装工艺性的分类标准 2.1冲压件的可/易移性 ● A.大型组件要求形成框架结构,防止变形;如形状、,减少U型、X型及其它异型。 B.尽量避免设计易变形的大型组件(如地板面版), C.易变形的大型组件上设计增加刚度的小结构, D.单个零件要便于存放、拿取、放件时不易扭曲变形。 E.尽量避免设计需要两个人搬运或机械搬运的大型零件。 ●零件的形状对称,减少转动角度。 ●零件的形状或者完全对称,或者截然不同,易辨认不出错,尽可能实现零件在同一款车以至不同车上通用。 ●零件的取放,通道畅通,角度符合人机工程机理。 ●无零件与零件之间、零件与工具之间的干涉。 ●外观件的装配工序要尽可能的少,在节拍满足的情况下,压缩至最短,减少外观面磕碰伤。 2.2冲压件的焊装可/易夹性 ●尽量不夹在外表面上以及其反面,以减少损伤及打磨修理工作量。 ●夹紧面应该设计成平面,以利于简化夹具。最好是单一平面,(X平面,Y平面,和Z平面)以利于夹具设计和尺寸控制。 2.3焊装易定位性 ●以孔/销定位方式为首选,型面定位方式为次选,不得已情况下采用边缘定位方式。 A.定位孔尽可能在主平面上; B.各定位孔尽可能互相平行; C.定位型面尽可能要求在平面上,减少曲面定位,杜绝交接面定位。 ●定位点位置、数量及方向设计合理。 ●定位顺序设计合理,以保证定位的唯一性。 2.4焊装可/易焊性 ●所有焊点均可由公司的焊枪完成。(无焊点设在焊枪死角) A.有足够的焊钳进出零件的空间; B.能够实现点焊面与焊钳极臂垂直; C.有电极焊接时的运动空间; D.有足够的可视空间,至少能看见一个极臂与板件的接触点; E.零件不能与焊钳钳身、悬挂钢缆、焊钳转盘相干涉。 ●同一工位焊枪能达到所有预定焊点位置,不换或少换焊枪。 A.零件形状所构成的焊接面能适合普通X型、C型焊钳焊接; B.同一焊接工位焊接实现使用尽可能少的焊钳种类,以减少换焊枪的时间; C.能够使用同一型号焊钳焊接的焊点,焊接料厚尽可能接近,以便于参数统一,以减少切换焊接 参数的时间。 ●设计的工件无/少镀锌表面。 ●设计的工件无/少多层焊。 多使用两层板点焊,减少三层板焊接,杜绝三层以上板件搭接点焊。
汽车车身焊接工艺设计
浅析汽车车身的焊接工艺设计 在汽车厂中,焊接生产线相对于涂装线和总装线来说,刚性强,多品种车型的通用性差,每更新换代一种车型,均需要更新车间大量专用设备和生产工艺。焊接工艺设计可以称得上是焊接生产线的“灵魂”,涉及的专业知识较多,如机械化、电控、非标设备、建筑、结构、水道、暖通、动力、电气、计算机、环保和通讯等,从宏观上决定车间的工艺水平、物流、投资和预留发展,具体决定着生产线的工艺设备种类和数量、夹具形式、物流工位器具形式、机械化输送方式及控制模式等。因此,焊接工艺设计在焊接生产线的开发中占有举足轻重的地位,是产生高性价比焊接生产线 的关键。 1、车身焊接工艺设计的前提条件 1.1产品资料 a.产品的数学模型(简称数模)。在汽车制造行业中,一般情况下用 UG,Catia,ProE等三维软件均能打开数模(如图1),并在其中获取数据或进行深人的工作。在工艺设计过程中,将所有数模装配在一起就构成了一个整车数模,从数模中可以获得零部件的结构尺寸、位置关系。由数模还可以生成整车、分总成、冲压件的各种视图(包括轴测图),以及可以输出剖面图。 b.全套产品图纸。
c.样车、样件(包括整车车身总成、各大总成、分总成和冲压件)。 d.产品零部件明细表(包括各部件的名称、编号,冲压件的名称、编号、数量,标准件的规格、数量)。 工艺设计时,业主必须提供上述a、b、c中至少1项,d项可以从前3项中分析出来,正常状态下d项(如图2)早在汽车设计结束时就已经确定了。如果仅提供b 项,那么需要增加大量的车身拆解、分析工作。
1.2工厂设计的参数 工厂设计的参数包括以下几方面: a.生产纲领即年产量; b.年时基数即生产班次、生产线的利用率等; c.生产线的自动化程度(机器人+自动焊钳焊点数/全车身焊点数x 100%=自动化率); d.生产线的工艺水平要求(如主要设备选用原则、生产线的输送方式,电气控制水平等); e.各种材料、外购件的选用原则(如型材、控制元件、气动元件、电机、减速器); f.各种公用动力介质的供应方式、能力、品质等参数,建厂所在地的环境状况如温度、湿度等; g.当生产线布置在原有厂房内时,应收集原有房的土建、公用有关资料,如厂房柱顶标高、屋架承载能力、电力和动力介质的余富程度等。 2、工艺分析