化学镀镍废液的再生和处理方法
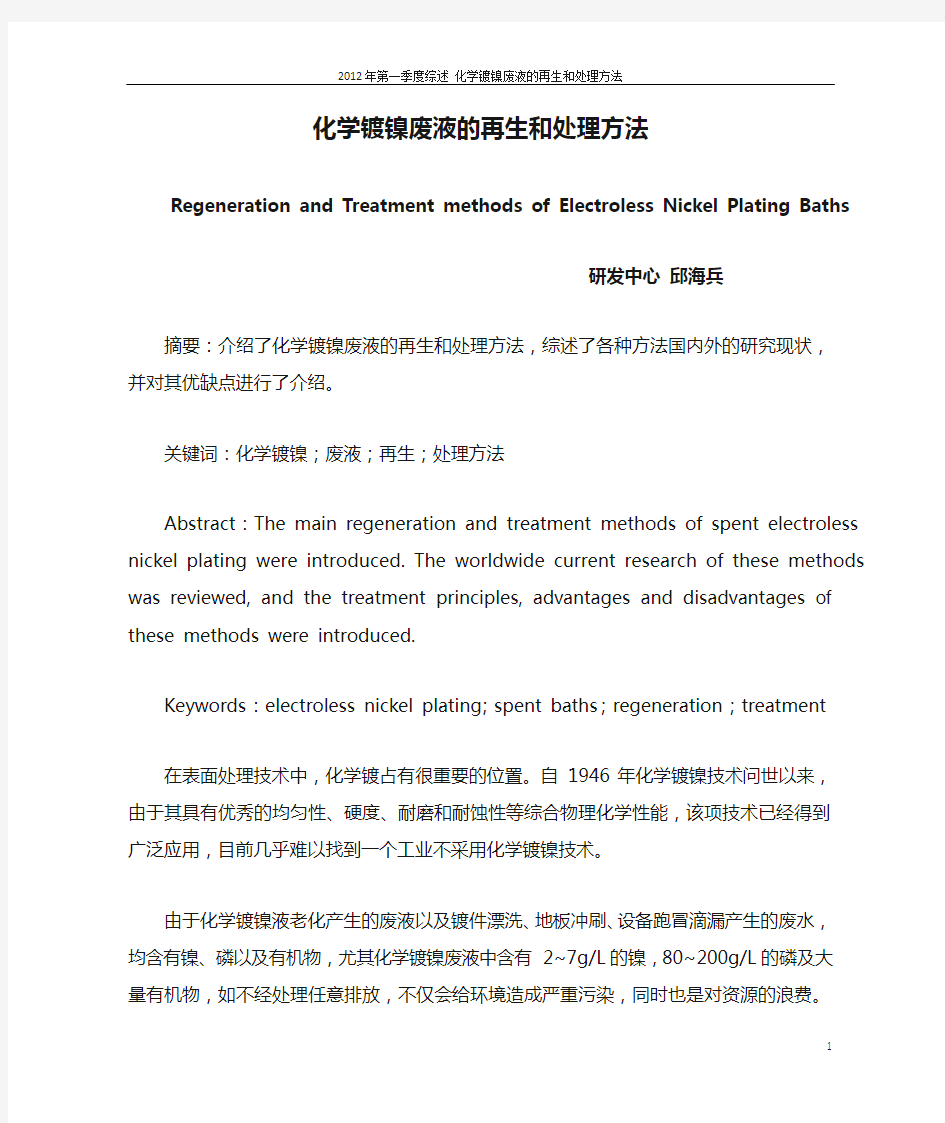

化学镀镍废液的再生和处理方法
Regeneration and Treatment methods of Electroless Nickel Plating
Baths
研发中心邱海兵
摘要:介绍了化学镀镍废液的再生和处理方法,综述了各种方法国内外的研究现状,并对其优缺点进行了介绍。
关键词:化学镀镍;废液;再生;处理方法
Abstract:The main regeneration and treatment methods of spent electroless nickel plating were introduced. The worldwide current research of these methods was reviewed, and the treatment principles, advantages and disadvantages of these methods were introduced.
Keywords:electroless nickel plating;spent baths;regeneration;treatment 在表面处理技术中,化学镀占有很重要的位置。自1946年化学镀镍技术问世以来,由于其具有优秀的均匀性、硬度、耐磨和耐蚀性等综合物理化学性能,该项技术已经得到广泛应用,目前几乎难以找到一个工业不采用化学镀镍技术。
由于化学镀镍液老化产生的废液以及镀件漂洗、地板冲刷、设备跑冒滴漏产生的废水,均含有镍、磷以及有机物,尤其化学镀镍废液中含有2~7g/L的镍,80~200g/L的磷及大量有机物,如不经处理任意排放,不仅会给环境造成严重污染,同时也是对资源的浪费。因此有效处理化学镀镍废液,使其中的环境污染物变废为宝,得到资源化利用,减少对环境污染、减少对生态的破坏,实现经济效益、环境效益和社会效益的协调统一,有着非常重要的意义。
1、化学镀镍废液
化学镀镍镀液主要由金属盐、还原剂、pH缓冲剂、稳定剂或络合剂等组成,镍盐用得最多的是硫酸盐,还有氯化物或者醋酸盐。还原剂主要是次亚磷酸盐、硼氢化物等。用次亚磷酸盐作还原剂的化学镀镍镀得的镀层是一种镍磷合金。以硼氢化物或胺基硼烷作还原剂得到的镀层是纯镍层,含镍量可
达99.5%以上。目前国内生产上大多采用次亚磷酸钠作还原剂,硼氢化钠和二甲基胺硼烷因价格较贵,只有少量使用。
用次亚磷酸钠作还原剂获得的镀层依含磷量不同可分为低磷(1%~4%)、中磷(4%~10%)和高磷(10%~12%)。镀层中磷含量主要决定于溶液的pH值,在弱酸性液(pH=4~5)中可获得中磷和高磷合金,在弱碱性(pH=8~10)中可获得低磷和中磷合金。
在酸性环境里,可以用只含镍离子和次亚磷酸盐的溶液化学镀镍,但是为了使工艺稳定,必须加入缓冲剂和络合剂。常用的有醋酸盐缓冲体系,也有用柠檬酸盐、羟基乙酸盐、乳酸盐等。络合物可以在镀液pH值增高时也保持其还原能力。酸性体系里的络合剂多数采用的是乳酸、柠檬酸、羟基乙酸及其盐。有机添加剂对镍的还原速度有很大影响,其中许多都是反应的加速剂,如丙二酸、丁二酸、氨基乙酸、丙酸以及氟离子。
在碱性化学镀镍溶液里,镍离子配位体是必需的成分,以防止氢氧化物和亚磷酸盐沉淀。一般用柠檬酸盐或铵盐的混合物作为络合剂。也有用磺酸盐、焦磷酸盐、乙二胺盐的镀液。
化学镀镍溶液在工作一段时间以后会逐渐老化,不能继续使用,成为化学镀镍废液。此时废液中除了含有镍离子、次磷酸根离子以及大量的亚磷酸根离子、钠离子、硫酸根离子外,还含有很多的络合剂、缓冲剂、稳定剂等有机物,使得废液成分非常复杂,增加了废液治理的难度。
2、化学镀镍废液的再生利用
化学镀镍液报废的主要原因是由于亚磷酸钠、硫酸钠反应产物的积累。若是能清楚这些副产物,保留其中的有效成分,如镍、络合剂等用于二次化学镀镍,不但能节省大量的费用,也减少了污染物的排放。
有关方面的研究报道文献和专利不少。美国田纳西州Doe Dak Ridge 实验室研究的化学镀镍无废工艺流程,包括离子交换、沉淀、蒸发等处理单元【1】。老化液经热交换器后先后进入3个氢型阳离子树脂交换柱,经离子交换树脂处理后,镀液中的钠离子和镍离子几乎全部被置换。流出液进入
沉淀反应池,用CaOhe CaCO
3调pH值,由于钙盐的引入而生成CaSO
4
沉淀,
从而去除了硫酸根。滤出液进入第二个沉淀池,调整pH值,加入MgO或沉淀剂,以出去亚磷酸根离子,冲洗后的沉淀可用作肥料。过滤液Mg(OH)
2
用硫酸调节pH值,蒸发去除多余水分,进入第二个离子交换柱。溶液中的钙、镁离子交换树脂上结合的镍离子,流出液经有效成分补充后可加热施镀。此装置有效去除了老化液中的亚磷酸根离子、钠离子和硫酸根离子,基本实现了化学镀镍的闭路循环。但此系统设备复杂,操作繁琐,费用高,且有可能将钙、镁离子引入镀液,影响施镀。刘贵昌等【2】采用可溶性钙盐去除化学镀镍废液中的亚磷酸根,再用可溶性氟化物去除残余的钙离子进行了研究,一定条件下,亚磷酸根及硫酸根的去除率分别为83%和50~70%,镍的损失率约为14%,经补充成分后,由再生液中获得的镀层较相同工艺条件下新镀液所得镀层在含磷量及耐蚀性上有所下降,镀速和镀层硬度稍有提高。
专利CN102094192[3]采用了氧化钙和乙酸钙除去亚磷酸根的方法,再加入碳酸铵除去过量的钙离子,使用抽滤的方法除去微溶物。最后补加镀镍过程中损失的镍盐和次磷酸钠,再生后镀液可继续投入生产。专利CN1818133[4]通过冷却废液的方法使硫酸钠和亚磷酸钠结晶析出。专利jp2002371368[5]利用水滑石沉淀去除化学镀镍老化液中亚磷酸和磷酸根离子,冷却结晶去除硫酸钠,再生化学镀镍废液;专利jp7267616[6]通过冷却溶液分离硫酸钠,再添加钙盐去除亚磷酸和磷酸根的方法再生化学镀镍废液。
3、化学镀镍废液的处理
化学镀镍废液的处理方法很多,目前报道的主要有化学沉淀法、还原法、电解法、离子交换法、电渗析法、溶剂萃取法等。
3.1化学沉淀法
化学沉淀法是一种传统而实用的方法,它是通过向废液中投加适宜的沉淀剂,在一定的pH值条件下,沉淀剂与废液中有害物质反应生成不溶性物质,凝聚、沉降、液固分离,从而出去废液中有害污染物。经典的化学沉淀工艺是向废液中投入石灰乳或苛性钠,使镀液pH值升至12.0,此时废液中绝大部分镍离子及重金属污染物沉淀析出。此外,石灰乳还能同废液中亚磷酸根形成钙盐沉淀,去除大部分的磷。
针对含有络合剂的废液,根据我们目前的实践,直接加氢氧化钠调节pH值至12.0以上也很难沉淀废液中镍离子。针对酸性化学镀镍废液一般可首先利用CaO调节废液的pH值在8左右,除去大部分的有机酸络合剂,然后在废液中加入CaO或NaOH,调至废液的pH值12.0以上,使废液中的大部分镍离子和其他重金属离子发生沉淀反应,再加入适量的高分子絮凝剂,加速不溶物的沉降。但是针对含铵盐作络合剂的碱性化学镀镍废液,废液中含有[NH4+],碱性条件下会形成镍氨络合物,以上方法很难奏效。
石红【7】提出采用化学氧化-沉淀法处理化学镀镍废液,先将化学镀镍废液中的络合剂用合适的氧化剂氧化破解掉,使镍离子呈游离状态,然后用氢氧化物沉淀,废液中的次磷酸根同时被氧化成亚磷酸根、正磷酸根离子,一并沉淀处理,所使用的氧化剂包括次氯酸钠、次氯酸钙、双氧水、高锰酸钾等。
化学沉淀法的优点是工艺比较简单,操作费用低。缺陷是产生大量废渣,必须妥善处理或综合利用,否则易造成二次污染,同时造成大量高价值金属镍的浪费。
3.2 还原法
在化学镀镍废液中,趁热加入适量氯化钯溶液或认为改变某些工作条件,诱导化学镀镍废液自发分解,使废液中镍离子还原析出生成黑色镍微粒,沉降分离后,约60~90%的镍可回收利用,处理后废液中镍离子浓度降低了数十倍。后续的化学沉淀和废渣处理就较容易,但此法费用较高,尤其是氯化钯价格高且不易回收。
类似的诱导自发分解镀液的方法还有升高废液pH值和温度,滴加还原剂硼氢化钠等,以触发镀液的分解反应。刘娟等【8】研究采用硼氢化钠还原法从化学镀镍废液中回收镍,最佳回收工艺硼氢化钠140mL/L,分散剂KH5703g/L,温度40℃,pH值5.0条件下,废液中镍离子浓度从6.717g/L 降至低于1mg/L,所回收的产物含有镍、硼和磷等元素,由非静态硼化镍和非晶态镍-磷合金组成。专利CN102351351[9]中提到采用金属(铁、钢条)置换报废液中镍。专利CN101817607[10]和CN101805831[11]采用催化还原剂、镍金属提取载体分别在酸性和碱性化学镀镍废液中直接提取镍。专利
CN102071410[12]在化学镀镍废液中加入镍磷颗粒或含镍磷颗粒的液体作诱导剂,引发化学镀镍废液中化学还原析出镍磷颗粒,以析出的镍磷颗粒为原料制备镍盐、氢氧化镍或金属镍。
还原法的优点是能有效回收镍资源,使废液中镍离子浓度大大降低,有利于后续的达标处理,减少废渣排放,但存在药剂成本高,尤其采用氯化钯为催化剂进行催化还原回收,同时形成的镍沉积物不易分离提纯。3.3 电解法
电解法是采用不溶性材料为阳极,对废液进行电解处理。阳极上发生有机物的破解氧化反应及[OH-]放电反应,而阴极上则析出镍,从而达到回收利用。
闫雷等【13】以泡沫镍做阴极,钛基二氧化钌涂层电极作阳极对化学镀镍废液进行电解研究,pH控制7~8,表观电流迁都0.45~0.5A,废液温度80℃,电解2h,可以使废液中镍的浓度从2018mg/L降至53.7mg/L,同时废液中总有机碳去除率达到97.3%,阴极回收镍纯度在88.5%以上。专利CN102212842[14]采用不锈钢为阴极,镀二氧化铱钛合金网状板为阳极电解化学镀镍老化液进行金属镍回收。专利us5730856[15]采用电解氧化法处理化学镀镍废液,镍离子通过电解回收,电解后废液作为含磷废料溶液。
电解法具有处理效率高,操作方便等优点,在欧美一些国家使用比较普遍,但当电解过程中镍的浓度降低到一定程度时,会导致电流效率降低,能耗升高,因此若要将镍的含量降低至排放标准就不能只采用此法,需进一步用其他方法处理达标。
3.4 离子交换法
利用离子交换法处理化学镀镍废液是一种深度处理方法,但由于化学镀镍废液中含有大量的络合物和钠离子,给处理带来了较多困难,关键在于树脂的选择、工艺的设计及操作管理上。
东江环保股份有限公司黄德贤,陈曙生在<污染防治技术与发展>专题报告中提到用D403树脂处理化学镀镍废液【16】,经树脂吸附再生后再生液中镍含量在80g/L以上。专利CN102329030[17]采用一系列步骤处理化学镀镍废水,包括:1、强碱性阴离子树脂破络处理;2、强酸性阳离子树脂吸附镍离
子;3、强氧化剂氧化亚磷酸根和次亚磷酸根以及有机酸络合剂;4、铁板为阴阳极,脉冲电凝处理,形成磷酸铁沉淀,同时沉淀剩余的镍离子;5、调节废水pH 值沉淀铁离子,最终出水镍离子<0.1mg/L。
离子交换法处理化学镀镍废液,自动化程度高,回收镍质量高,可以明显提高镀液的使用周期;缺点是投资费用大,处理能力较小,工艺操作复杂,树脂易被氧化和污染。目前,欧美主要将其应用于镀镍废液的再生。
3.5 电渗析法
电渗析法的原理是在电场力作用下,溶液中的阴、阳离子分别透过阴、样离子交换膜,达到溶液脱盐目的,可大量去除有害的亚磷酸根离子和无用的钠离子、硫酸根离子,并尽可能保留镀液中的镍离子、次磷酸根离子和有机酸,使镀液得到再生。
上世纪90年代以来,日本等国家在化学镀镍液再生的研究和开发方面,比较引人注目。矢俊正幸的研究表明,经电渗析处理,镀液使用20个周期后,各项指标仍完全正常;同时还发现,电渗析处理后镀液使用寿命的延长与磷酸根的去除有关,镍盐、次磷酸盐的补加也是关键因素。
何湘柱等【18】采用电渗析法处理化学镀镍废液,室温下,当J=65ma/cm2,
2-,在补加有效成分后,pH=4.5,v=1L/45s时,可以较好的去除有害成分HPO
3
再生液可以回用。
专利CN101962764[19]介绍了通过电渗析、化学沉淀、反渗透工艺实现化学镀镍老化液的再生。
电渗析法可到达延长镀液使用寿命,节省镍、磷资源,降低化学镀镍成本,具有显著的经济效益和环境效益。不足之处是一次投资成本高,操作费用高,能耗大。
3.6 溶剂萃取法
江丽、刘辉【20】用P204作为萃取剂对酸性化学镀镍废液进行镍的萃取。最佳工艺条件为:pH值6.1,P204含量2.0mol/L,皂化率为25%,相比2:1,温度15~30℃,平衡时间1min,按此条件用P204-煤油3级逆流萃取,镍萃取率达到96%以上。用硫酸反萃取,经适当处理可制得优于工业级的硫酸镍的产品。
4、化学镀镍废液的综合治理
由于化学镀镍废液成分复杂,单一的处理方法很难满足环保要求,组合使用几种处理技术对废液进行综合处理,才能得到良好的效果。
于秀娟、周定等【21】人对化学镀镍废液进行镍离子电解回收后,再以15%的石灰乳作沉淀剂,进一步将废液中的残余镍离子浓度处理至1.0mg/L以下,最后以Ca(ClO)
作为氧化沉淀剂处理废液中的磷,在pH值为9.0、反应温度为80℃、
2
投加比为1:5.2的情况下、连续搅拌5小时,可使废液中的总磷含量<2.0mg/L,达标排放。
美国田纳西洲Doe Dak Ridge实验室研究的化学镀镍无废工艺流程包括离子交换-沉淀-蒸发等处理单元.该系统能有效地去除废液中的亚磷酸根离子、钠离子和硫酸根离子,基本实现了化学镀镍的闭路循环。但设备复杂、操作繁琐、费用高,还可能会将钙、镁离子带入镀液,影响施镀[1]。
5、小结
综上,虽然国内外针对化学镀镍废液的处理进行了诸多研究,也取得了不菲的成就,但目前还没有形成一套成熟的、行之有效的、低费用、低能耗、简单易行的处理方法,尤其是对镍和磷的联合处理。
因此研究低费用、无二次污染,尽最大可能回收镍、磷资源的处理方法,是我们目前迫切需要解决的问题。
参考文献:
1、Anderson R W. Rejuvenating Electroless Solution:Electroless
Nickel Bath Recoverry by Cation Exchange and Precipition[J].plating and Surface Finishing,1992,79(3):18-20.
2、刘贵昌,万众,杨长青,于同敏.化学镀镍废液再生[J].电镀与环
保,1997,17(4):11-14.
3、北京交通大学.铝合金表面化学镀镍镀液的制备方法及废镀液的再生方法:
中国,102094192[P].20110907.
4、华南理工大学.化学镀镍液的再生处理方法:中国,1818133[P].20081210.
5、nippon kagaku sangyo kk. Method for treating aged electroless nickel plating
liquid:Japan,2002371368.
6、nippon chemical ind. Method for treating aged electroless nickel plating liquid:
Japan.7267616.
7、石红.化学镀镍的废液回收处理技术研究.化学工程与装备,
2009,5:163-165.
8、刘娟,张振忠,赵芳霞,张帆.硼氢化钠还原法从化学镀镍废液中回收
镍.电镀与环保,2010,30(1):37-40.
9、江门市瑞期精细化工工程有限公司.一种化学镀镍报废液的处理工艺:中国,
102351351[P].20120215.
10、埃梯星(厦门)电子科技有限公司. 一种在酸性化学镀镍废液中直接提取镍的
方法:中国,101817607[P].20110810.
11、埃梯星(厦门)电子科技有限公司. 一种在碱性化学镀镍废液中直接提取镍的
方法:中国,101805831[P].20110720.
12、深圳市瑞世兴科技有限公司;深圳清华大学研究院. 一种从化学镀镍废液中
回收镍资源的方法:中国,102071410[P].20110525.
13、闫雷,于秀娟,李淑芹.电解法处理化学镀镍废液.沈阳建筑大学学报(自
然科学版),2009,25(4):762-766.
14、无锡中天固废处置有限公司. 化学镀镍老化液中镍的回收方法:中国,
102212842[P].20111130.
15、n ihon techno kabushiki kaisha [jp]. Method for treating waste liquid with
electrolytic oxidation and apparatus for carrying out the same: USA,5730856[P].
16、黄德贤,陈曙生.D403树脂处理化学镀镍液的应用研究.<污染防治技术
与发展>专题报告.
17、冯云香.化学镀镍废水处理方法:中国,102329030[P].20120314.
18、何湘柱,赵雨,赵国鹏.电渗析法再生化学镀镍废液工艺.电镀与涂饰,
2010,30(5):39-42.
19、大连理工大学. 膜法与电化学法综合再生化学镀镍老化液的方法:中国,
101962764[P].20120104.
20、江丽,刘辉.化学镀镍废液中镍的萃取及综合利用[J].广西化学,1999,
28(3):61-62.
21、于秀娟,周定,闫雷,李淑芹.化学镀镍老化液资源化处理工艺的研究[J].
环境保护学,2003,29:5-8.
化学镀工艺流程
化学镀所需仪器:电热恒温水浴锅;8522型恒温磁力搅拌器控温搅拌;增力电动搅拌机。 化学镀工艺流程:机械粗化→化学除油→水洗→化学粗化→水洗→敏化→水洗→活化→水洗→解胶→水洗→化学镀→水洗→干燥→镀层后处理。 1化学镀预处理 机械粗化:用机械法或化学方法对工件表面进行处理(机械磨损或化学腐蚀),从而在工件表面得到一种微观粗糙的结构,使之由憎水性变为亲水性,以提高镀层与制件表面之间结合力的一种非导电材料化学镀前处理工艺。 1.1 化学除油 镀件材料在存放、运输过程中难免沾有油污,为保证预处理效果,必须首先进行除油处理,去除其表面污物,增加基体表面的亲水性,以确保基体表面能均匀的进行金属表面活化。化学除油试剂分有机除油剂和碱性除油剂两种;有机除油剂为丙酮(或乙醇)等有机溶剂,一般用于无机基体如鳞片状石墨、膨胀石墨、碳纤维等除油;碱性除油剂的配方为:NaOH:80g/l,Na2CO3(无水):15g/l,Na3PO4:30g/l,洗洁精:5ml/l,用于有机基体如聚乙烯、聚氯乙烯、聚苯乙烯等除油;无论使用哪种除油试剂,作用时都需要进行充分搅拌。 1.2 化学粗化 化学粗化的目的是利用强氧化性试剂的氧化侵蚀作用改变基体表面微观形状,使基体表面形成微孔或刻蚀沟槽,并除去表面其它杂质,提高基体表面的亲水性和形成适当的粗糙度,以增强基体和镀层金属的结合力,以保证镀层有良好的附着力。粗化是影响镀层附着力大小的很关键的工序,若粗化效果不好,就会直接影响后序的活化和化学镀效果。化学粗化试剂的配方为:CrO3:40g/l,浓H2SO4:35g/l,浓H3PO4(85%):5g/l。化学粗化的本质是对基体表面的轻度腐蚀作用;因此,有机基体采用此处理过程,无机基体因不能被粗化液腐蚀而不需此处理。 1.3 敏化 敏化处理是使粗化后的有机基体(或除油后的无机基体)表面吸附一层具有还原性的二价锡离子Sn2+,以便在随后的活化处理时,将银或钯离子由金属离子还原为具有催化性能的银或钯原子。敏化液配方为:SnCl2·2H2O:20g/l,浓HCl:40ml/l,少量锡粒;加入锡粒的目的是防止二价锡离子的氧化。 1.4 活化 活化处理是化学镀预处理工艺中最关键的步骤, 活化程度的好坏,直接影响后序的施镀效果。化学镀镀前预处理的其它各个工序归根结底都是为了优化活化效果,以保证催化剂在镀件表面附着的均匀性和选择性,从而决定化学镀层与镀件基体的结合力以及镀层本身的连续性。活化处理的目的是使活化液中的钯离子Pd2+或银离子Ag+离子被镀件基体表面的Sn2+离子还原成金属钯或银微粒并紧附于基体表面,形成均匀催化结晶中心的贵金属层, 使化学镀能自发进行。目前,普遍采用的活化液有银氨活化液和胶体钯活化液两种;化学镀铜比较容易,用银即能催化;化学镀钴、化学镀镍较困难,用银不能催化,必须使用催
化学镀镍废液的再生和处理方法
化学镀镍废液的再生和处理方法 Regeneration and Treatment methods of Electroless Nickel Plating Baths 研发中心邱海兵 摘要:介绍了化学镀镍废液的再生和处理方法,综述了各种方法国内外的研究现状,并对其优缺点进行了介绍。 关键词:化学镀镍;废液;再生;处理方法 Abstract:The main regeneration and treatment methods of spent electroless nickel plating were introduced. The worldwide current research of these methods was reviewed, and the treatment principles, advantages and disadvantages of these methods were introduced. Keywords:electroless nickel plating;spent baths;regeneration;treatment 在表面处理技术中,化学镀占有很重要的位置。自1946年化学镀镍技术问世以来,由于其具有优秀的均匀性、硬度、耐磨和耐蚀性等综合物理化学性能,该项技术已经得到广泛应用,目前几乎难以找到一个工业不采用化学镀镍技术。 由于化学镀镍液老化产生的废液以及镀件漂洗、地板冲刷、设备跑冒滴漏产生的废水,均含有镍、磷以及有机物,尤其化学镀镍废液中含有2~7g/L的镍,80~200g/L的磷及大量有机物,如不经处理任意排放,不仅会给环境造成严重污染,同时也是对资源的浪费。因此有效处理化学镀镍废液,使其中的环境污染物变废为宝,得到资源化利用,减少对环境污染、减少对生态的破坏,实现经济效益、环境效益和社会效益的协调统一,有着非常重要的意义。 1、化学镀镍废液 化学镀镍镀液主要由金属盐、还原剂、pH缓冲剂、稳定剂或络合剂等组成,镍盐用得最多的是硫酸盐,还有氯化物或者醋酸盐。还原剂主要是次亚磷酸盐、硼氢化物等。用次亚磷酸盐作还原剂的化学镀镍镀得的镀层是一种镍磷合金。以硼氢化物或胺基硼烷作还原剂得到的
化学镀镍配方汇编
简述电镀槽液加料方法与溶液密度测定方法 1.电镀生产现场工艺管理的主要内容: 1)控制各槽液成分在工艺配方规范内。遵守规定的化学分析周期。 2)保持电镀生产的工艺条件。如温度、电流密度等。 3)保持阴极与阳极电接触良好。 4)严格的阴极与阳极悬挂位置。 5)保持镀液的清洁和控制镀液杂质。 6)保持电镀挂具的完好和挂钩、挂齿良好的电接触。 2.电镀槽液加料方法:加料要以“勤加”“少加”为原则。 2.1固体物料的补充,某些有机固体料先用有机溶剂溶解,再慢慢加入以提高增溶性。若直接加入往往会使镀液混浊。一般的固体物料,可用镀槽中的溶液来分批溶解。即取部分电镀液把要加的料在搅拌下慢慢加入,待静止澄清,把上层清液加入镀槽。未溶解的部分,再加入镀液,搅拌溶解。这样反复作业,直到全部加完。在不影响镀液总体积的情况下,也可以用去离子水或热的去离子水搅拌溶解后加入镀槽。有些固体料易形成团状,影响溶解过程。可以先用少量水调成稀浆糊状,逐步冲稀以避免团状物的形成。 2.2液体物料的补充,可以用去离子水适当稀释或用镀液稀释后在搅拌下慢慢加入。严禁将添加剂光亮剂的原液加入镀槽。 2.3补充料的时机,加料最好是在停镀时进行。加入后经过充分搅匀再投入生产。在生产中加料,要在工件刚出槽后的“暂休”时段加入。可在
循环泵的出液口一方加入,加入速度要慢,药料随着出液口的冲击力很快分散开来。 2.4加料方法不当可能造成的后果: 2.4 1)如果加入的是光亮剂,则易造成此槽工件色泽差异。 2.4.2)如果加入的是没有溶解的固体料,则易造成镀层毛刺或粗糙。 2.4.3)如果是加入酸调节pH,会造成槽液内部pH不均匀而局部造成针孔。 3.镀液及其它辅助溶液密度的测试方法: 3.1要经常测定溶液的密度,新配制的镀液或其它辅助液,都要测定它的密度并作为档案保存起来供以后对比。镀液的密度一般随着槽龄增加而增加。这是由于镀液中杂质离子、添加剂分解产物等积累的结果,因此可以把溶液密度与溶液成分化验数据一起综合进行分析,判断槽液故障原因以利排除。 3.2溶液密度测定方法,在电镀生产中,常用密度计或波美计测试溶液密度。密度与波美度可以通过下列公式转换。对重于水的液体密度 =145/(145-波美度),波美度=(145x145)/密度,在用波美计测试时,其量程要从小开始试测,若波美计量程选择不当,会损坏波美计。 测试密度不要在镀槽内进行,应取出部分镀液在槽外进行。在镀槽中测试,当比重计或波美计万一损坏,镀液会被铅粒污染。应将待测液取出1.5L左右(用2000mL烧杯),热的溶液可用水浴冷却。然后将样液转移至1000mL直形量筒中,装入量为距筒口约20mm处,就可用比重计测量。 脉冲电镀电源使用须知
化学镀镍与电镀镍工艺相互之间的区别
化学镀镍与电镀镍工艺及相互之间的区别 1 电镀镍 电镀是一种电化学过程,也是一种氧化还原过程。电镀镍是将零件浸入镍盐的溶液中作为阴极,金属镍板作为阳极,接通直流电源后,在零件上就会沉积出金属镍镀层。电镀镍的配方及工艺条件见表1。 电镀镍的工艺流程为:①清洗金属化瓷件;②稀盐酸浸泡;③冲净;④浸入镀液; ⑤调节电流进行电镀; ⑥自镀液中取出;⑦冲净;⑧煮;⑨烘干。 表1 电镀镍的配方及工艺条件 成分含量/g/L 温度 /0C PH值电流密度 /A/dm2 硫酸镍硫酸镁硼酸氯化钠 100-170 21-30 14-30 4-12 室温5-6 0.5 电镀镍的优点是镀层结晶细致,平滑光亮,内应力较小,与陶瓷金属化层结合力强。电镀镍的缺点是:①受金属化瓷件表面的清洁和镀液纯净程度的影响大,造成电镀后金属化瓷件的缺陷较多,例如起皮,起泡,麻点,黑点等;②极易受电镀挂具和在镀缸中位置不同的影响,造成均镀能力差,此外金属化瓷件之间的相互遮挡也会造成瓷件表面有阴阳面的现象;③对于形状复杂或有细小的深孔或盲孔的瓷件不能获得较好的电镀表面;④需要用镍丝捆绑金属化瓷件,对于形状复杂、尺寸较小、数量多的生产情况下,需耗费大量的人力。 2 化学镀镍 化学镀镍又称无电镀或自催化镀,它是一种不加外在电流的情况下,利用还原剂在活化零件表面上自催化还原沉积得到镍层,当镍层沉积到活化的零件表面后由于镍具有自催化能力,所以该过程将自动进行下去。一般化学镀镍得到的为合金镀层,常见的是Ni-P合金和Ni-B合金。相较Ni-P合金而言,Ni—B合金的熔焊能力更好,共晶温度高,内应力较小,是一种更为理想的化学镀镍方式。但本文着重讨论的是Ni-P合金镀层。 化学镀镍的配方及工艺条件见表2。 表2化学镀镍的配方及工艺条件 成分含量/g/L 温度 /0C PH值 硫酸镍次磷酸钠柠檬酸钠氯化铵 45-50 45-60 20-30 5-8 85 9.5 化学镀镍的工艺流程为:①清洗金属化瓷件;②冲洗;③活化液浸泡;④冲净; ⑤还原液浸泡;⑥浸入镀液并不时调节pH值;⑦自镀液中取出;⑧冲净;⑨煮;
酸性化学镀镍络合剂的研究
2008年8月襄樊学院学报 Aug.,2008第29卷第8期 Journal of Xiangfan University V ol.29No.8 酸性化学镀镍络合剂的研究 肖作安,占 丹 (襄樊学院化学与生物科学系,湖北襄樊441053) 摘要:通过考察乳酸,酒石酸,柠檬酸和有机酸Y 组成的复合络合剂对镀速的影响,确定了合适的复合络合剂,其中复合络合剂由柠檬酸与有机酸Y 组成,柠檬酸含量为10g/L ,有机酸Y 为20g/L.测定了该酸性化学镀镍的镀层的结合力以及孔隙率与耐蚀性,结果表明,该化学镀镍层光亮平整,结合力强,孔隙率分布较窄,耐硝酸点蚀120s ,具有优良的耐蚀性能. 关键词:化学镀镍;络合剂;耐蚀性 中图分类号:TQ153.1文献标志码:A 文章编号:1009-2854(2008)08-0031-04 随着科技的发展,人类对材料的性能要求越来越高,一些表面处理技术极大地拓宽了金属材料的应用范围,化学镀镍作为一项表面处理技术,以其工艺简便、镀层均匀及优异的耐蚀性、耐磨性等特殊性能而 日益受到人们的重视,得到迅速发展,广泛应用于航空、汽车、电子、计算机、石油、化工、机械等领域,有着非常广阔的发展前景[1-4]. 化学镀镍通常以次亚磷酸钠为还原剂,槽液分为酸性和碱性两种,应用较普遍的是酸性镀镍,其稳定性好,镀层光亮细致,本实验就选择在酸性体系进行化学镀镍.一般单一络合剂能得到光亮银白色、无针孔、表面光滑平整的镀层,但很难获得镀层美观、性能优良的整体效果.因此,本实验探索了一种新型的复合络合剂,能使镀液更稳定,使用寿命长,镀层美观,而且性能更优良. 1实验部分 1.1基体材料 基体材料为45#钢,其表面积均为4cm 2. 1.2工艺流程 化学除油-水清洗-除锈(盐酸洗液)–蒸馏水洗-施镀-水洗-干燥.1.3施镀工艺 其施镀工艺规范如下. 六水合氯化镍40g/L -100g/L ,次亚磷酸钠10g/L-30g/L ,乙酸钠10g/L-50g/L ,硼酸10g/L-50g/L ,稳定剂0.1m g/L ,pH 值3-6,温度75℃-95℃. 本实验主要研究常见的3种络合剂与合成的有机酸Y 形成的复合络合剂:乳酸+有机酸Y ;酒石酸+有机酸Y ;柠檬酸+有机酸Y .1.4镀层性能测试方法 1.4.1沉积速度 采用重量法,用电子天平准确称量试样在施镀前后的重量,按下述公式计算 4 0110)(t w w v ×Α××= ρ式中,V-沉积速率/(m/h);W 0和W 1为基体材料施镀前、施镀后试样的重量(g);ρ为镀层密度(g/cm 3);A 为试样表面积(cm 2);t 为施镀时间(h). 收稿日期:6作者简介:肖作安(),男,湖北应城人,襄樊学院化学与生物科学系讲师2008-0-12 1979-.
化学镍金的工艺
化学镍金的工艺 Tags: 化学镍金,印制电路板, 积分Counts:907 次 本文在简单介绍印制板化学镀镍金工艺原理的基础上,对化学镍金之工艺流程、化学镍金之工艺控制、化学镍金之可焊性控制及工序常见问题分析进行了较为详细的论述。在一个印制电路板的制造工艺流程中,产品最终之表面可焊性处理,对最终产品的装配和使用起着至关重要的作用。综观当今国内外,针对印制电路板最终表面可焊性涂覆表面处理的方式,主要包括以下几种:Electroless Nickel and Immersion Gold形电镀铜的常见缺陷及故障排除。 1.前言 由于行业竞争的激烈,印制板的制造商不断降低成本提高产品质量,追求零缺陷,以质优价廉取胜。而客户对印制板的要求也没有单纯停留在对产品性能的可靠性上,同时对产品的外观也提出了更严格的要求。而图形电镀铜作为化学沉铜的加厚层或其它涂覆层的底层,其质量与成品的关系可谓休戚相关“一荣俱荣,一损俱损”。所以图形电镀铜上的任何缺陷如镀层粗糙、麻点针孔、凹坑、手印等的存在,严重影响成品的外观,透过涂覆其上的阻碍或铅锡镀层或是镍金层,都能清楚的显露出来。 本文主要叙述图形电镀铜常见的系列故障及缺陷,并针对这些缺陷进行跟踪调查、模拟实验,找出产生缺陷的成因,制定切实的纠正措施,保证生产的正常进行。 2.缺陷特点及成因 2.1 镀层麻点 图形电镀铜上出现麻点,在板中间较为突出,退完铅锡后铜面不平整,外观欠佳。 刷板清洁处理后表面麻点仍然存在,但已基本磨平不如退完锡后明显。此现象出现后首先想到电镀铜溶液问题,因为出现故障的前一天(4月2日)刚对溶液进行活性炭处理,步骤如下:1)在搅拌条下件下加入2升H2O2 2)充分搅拌后将溶液转至一个备用槽中,加入4kg活性碳细粉,并加入空气搅拌2小时,之后关闭搅拌,让溶液沉降。 从调查中发现,生产线考虑到次日有快板,当晚将溶液从备用槽中转回工作槽。未经过充分过滤沉降活性炭,而转移溶液时未经循环过滤泵(慢)直接从工作槽的输出管理返回(管道粗,快)。因为溶液转回工作槽后已过下班时间,电镀人员没有小电流密度空镀处理阳极。在4月3日按新开缸液加完光亮剂FDT-1就开始电镀。 问题已经清楚,电镀铜上有麻点,来源于电渡溶液里的活性炭颗粒或其它脏东西。因为调度安排工作急,电镀人员未按照工艺文件的程序进行操作,溶液没有充分循环过滤,导致溶液里的机械杂质影响镀层质量。另一个因素是磷铜阳极清洗后,未通过电解处理直接工作,没来得及在阳极表面生成一层黑色均匀的“磷膜”,导致Cu+大量积累,Cu+水解产生铜粉,致使镀层粗糙麻点。 金属铜的溶解受控制步骤制约,Cu+不能迅速氧化成Cu2+。而阳极膜未形成,Cu-e.Cu2+ 的反应不断以快的方式进行,造成Cu+的积累,而Cu+具有不稳定性,通过歧化反应:2Cu+.Cu2+Cu,所生成的会在电镀过程中以电泳的方式沉积于镀层,影响镀层的质量。阳极经过小电流电解处理后生成的阳极膜能有效控制Cu的溶解速度,使阳极电流效率接近阴极电流效率,镀液中的铜离子保持平衡,阻止Cu+的产生,
如东开元污水处理厂污水处理工艺说明废水分类水量表项目含镍
如东开元污水处理厂污水处理工艺说明
一、废水分类水量表
项目 总规划(t/h) 一期规划(t/h) 含镍废水 16 8 化学镍废水 8 4 含铬废水 18 9 含氰废水 2 1 综合废水 20 10 混排废水 8 4 前处理废水 26 13
除以上 7 类废水以外,对以下废液进行收集集中处理
序号 1 2 3 废液项目 高浓度重金属废液、清洗液 限量提升到相应处理系统进行 废酸槽液 处理 前处理碱性脱脂废液 系统无法承受过量的废液委外处理 处理方式 备注
二、工艺简介 1、化学镍废水处理系统
化学镍废水中镍离子通常与镀液中的柠檬酸和次、亚磷酸盐等物质形成络合镍,同时水中存在次、亚磷酸盐, 废水从车间排至废水池,均匀水质水量后,提升至 pH 值调节池,投加硫酸调至酸性,在投加强氧化剂次钠氧化络 合镍,同时氧化次、亚磷酸根转化为正磷酸根,预处理后进入收集池 2。
2、含镍废水处理系统
含镍废水中镍离子通常以离子态存在,与化学镍预处理后的废水混合并调整 pH 值后,进入混凝絮凝沉淀系统, 经过石英砂过滤器和保安过滤器,达到镍离子回收装置进水浊度要求后,进入回收系统,大部分镍被回收利用,出 水进入回调池,化学镍和含镍废水设立独立在线监测系统和排放口,水质达标进入回用工序,不达标回至除镍吸附 柱进行再处理。
3、含铬废水处理系统
含铬废水中含有六价铬和三价铬,先将废水用硫酸调 pH 值至 2~3,再加入还原剂焦亚硫酸钠,将六价铬还原 为三价铬,在下一个反应池中用 NaOH 或 Ca(OH)2 调 pH 值至 7~8,生成 Cr(OH)3 沉淀,再加混凝剂,使 Cr(OH)3 沉淀除去进入中间水池,因靠常规物化沉淀很难将总铬稳定降到排放标准,中间水池水先后进入石英砂过滤器、保 安过滤器和除铬吸附柱,确保废水稳定达标,废水排放设立独立在线监测系统和排放口,水质达标进入回用工序, 不达标回至除铬吸附柱进行再处理。
化学镀镍溶液的组成及其作用
化学镀镍溶液的组成及其作用 主盐: 化学镀镍溶液中的主盐就是镍盐,一般采用氯化镍或硫酸镍,有时也采用氨基磺酸镍、醋酸镍等无机盐。早期酸性镀镍液中多采用氯化镍,但氯化镍会增加镀层的应力,现大多采用硫酸镍。目前已有专利介绍采用次亚磷酸镍作为镍和次亚磷酸根的来源,一个优点是避免了硫酸根离子的存在,同时在补加镍盐时,能使碱金属离子的累积量达到最小值。但存在的问题是次亚磷酸镍的溶解度有限,饱和时仅为35g/L。次亚磷酸镍的制备也是一个问题,价格较高。如果次亚磷酸镍的制备方法成熟以及溶解度问题能够解决的话,这种镍盐将会有很好的前景。 还原剂: 化学镀镍的反应过程是一个自催化的氧化还原过程,镀液中可应用的还原剂有次亚磷酸钠、硼氢化钠、烷基胺硼烷及肼等。在这些还原剂中以次亚磷酸钠用的最多,这是因为其价格便宜,且镀液容易控制,镀层抗腐蚀性能好等优点。 络合剂: 化学镀镍溶液中的络合剂除了能控制可供反应的游离镍离子的浓度外,还能抑制亚磷酸镍的沉淀,提高镀液的稳定性,延长镀液的使用寿命。有的络合剂还能起到缓冲剂和促进剂的作用,提高镀液的沉积速度。化学镀镍的络合剂一般含有羟基、羧基、氨基等。 在镀液配方中,络合剂的量不仅取决于镍离子的浓度,而且也取决于自身的化学结构。在镀液中每一个镍离子可与6个水分子微弱结合,当它们被羟基,羟基,氨基取代时,则形成一个稳定的镍配位体。如果络合剂含有一个以上的官能团,则通过氧和氮配位键可以生成一个镍的闭环配合物。在含有的镍离子镀液中,为了络合所有的镍离子,则需要含量大约的双配位体的络合剂。当镀液中无络合剂
时,镀液使用几个周期后,由于亚磷酸根聚集,浓度增大,产生亚磷酸镍沉淀,镀液加热时呈现糊状,加络合剂后能够大幅度提高亚磷酸镍的沉淀点,即提高了镀液对亚磷酸镍的容忍量,延长了镀液的使用寿命。 不同络合剂对镀层沉积速率、表面形状、磷含量、耐腐蚀性等均有影响,因此选择络合剂不仅要使镀液沉积速率快,而且要使镀液稳定性好,使用寿命长,镀层质量好。 缓冲剂: 由于在化学镀镍反应过程中,副产物氢离子的产生,导致镀液pH值会下降。试验表明,每消耗1mol的Ni2+同时生成3mol的H+,即就是在1L镀液中,若消耗的硫酸镍就会生成的H+。所以为了稳定镀速和保证镀层质量,镀液必须具备缓冲能力。缓冲剂能有效的稳定镀液的pH值,使镀液的pH值维持在正常范围内。一般能够用作PH值缓冲剂的为强碱弱酸盐,如醋酸钠、硼砂、焦磷酸钾等。 稳定剂:化学镀镍液是一个热力学不稳定体系,常常在镀件表面以外的地方发生还原反应,当镀液中产生一些有催化效应的活性微粒——催化核心时,镀液容易产生激烈的自催化反应,即自分解反应而产生大量镍-磷黑色粉末,导致镀液寿命终止,造成经济损失。在镀液中加入一定量的吸附性强的无机或有机化合物,它们能优先吸附在微粒表面抑制催化反应从而稳定镀液,使镍离子的还原只发生在被镀表面上。 但必须注意的是,稳定剂是一种化学镀镍毒化剂,即负催化剂,稳定剂不能使用过量,过量后轻则降低镀速,重则不再起镀,因此使用必须慎重。所有稳定剂都具有一定的催化毒性作用,并且会因过量使用而阻止沉积反应,同时也会影响镀层的韧性和颜色,导致镀层变脆而降低其防腐蚀性能。试验证明,稀土也可以作为稳定剂,而且复合稀土的稳定性比单一稀土要好。
化学镀工艺流程详解.
化学镀工艺流程 化学镀是一种在无电流通过的情况下,金属离子在同一溶液中还原剂的作用下通过可控制的氧化还原反应在具有催化表面(催化剂一般为钯、银等贵金属离子的镀件上还原成金属,从而在镀件表面上获得金属沉积层的过程,也称自催化镀或无电镀。化学镀最突出的优点是无论镀件多么复杂,只要溶液能深入的地方即可获得厚度均匀的镀层,且很容易控制镀层厚度。与电镀相比,化学镀具有镀层厚度均匀、针孔少、不需直流电源设备、能在非导体上沉积和具有某些特殊性能等特点;但化学镀镀层质量不很好,厚度上不去,且可镀的品种不多,故主要用于不适于电镀的特殊场合。 近年来, 化学镀技术得到了越来越广泛的应用,在各种非金属纤维、微球、微粉等粉体材料上施镀成为研究的热点之一;用化学镀方法可以在非金属纤维、微球、微粉镀件表面获得完整的非常薄而均匀的金属或合金层,而且镀层厚度可根据需要确定。这种金属化了的非金属纤维、微球、微粉镀件具有良好的导电性,作为填料混入塑料时能获得较好的防静电性能及电磁屏蔽性能,有可能部分取代金属粉用于电磁波吸收或电磁屏蔽材料。美国国际斯坦福研究所采用在高聚物基体上化学镀铜来研制红外吸收材料。毛倩瑾等采用化学镀的方法对空心微珠进行表面金属化改性研究,发现改性后的空心微珠具有较好的吸波性能,可用于微波吸收材料、轻质磁性材料等领域。 化学镀所需仪器:电热恒温水浴锅;8522型恒温磁力搅拌器控温搅拌;增力电动搅拌机。化学镀工艺流程:机械粗化→化学除油→水洗→化学粗化→水洗→敏化→水洗→活化→水洗→解胶→水洗→化学镀→水洗→干燥→镀层后处理。 1化学镀预处理 需进行化学镀的镀件一般不溶于水或者难溶于水。化学镀工艺的关键在于预处理,预处理的目的是使镀件表面生成具有显著催化活性效果的金属粒子,这样才能最终在基体表面沉积金属镀层。由于镀件微观表面凸凹不平,必须进行严格的镀前预处理,否则易造成镀层不均匀、密着性差,甚至难于施镀的后果。
碱性化学镀镍
碱性化学镀镍 碱性化学镀镍 减少污染后续酸性化学镀或其他电镀液1.工艺特点: NICHEM 2003碱性化学镀镍工艺特别适合于铝及铝合金预镀化学镍 减少污染后续酸性化学镀或其他电镀液 结合力优良 对复杂工件的处理更显其优越性 也可用于其他基体的电镀打底层 操作温度低 使用方法 本产品采用国际通用的A、B、C三种溶液,以A、B开缸,根据镍离子浓度进行分析补加工作液的消耗组分,以A、C 补加,极其方便: 2.镀液组成及操作条件:原料及操作 单位 范围
NICHEM 2003碱性化学镀镍A %(v/v) 70 NICHEM 2003碱性化学镀镍B %(v/v) 170 pH 9.0-9.5
温度 ℃ 室温-35℃ 装载量 dm2/L 0.32-0.96 时间 分钟 5-10分钟3.配制溶液:
开缸时,在槽中加入所配溶液1/2的水。 加入加入7%的A和17%的B,机械搅拌均匀,配备过滤机过滤。 加入纯水至所需近似体积。 用氨水调节pH值至9.2(大约用20毫升),补水至刻度线即可按工艺要求施镀。 4.设备需求 项目要求 槽体PP、PVC或高密度PE。 挂具PP、PVC或316型不锈钢。确保工件在槽液中垂直,相邻两块板间隔最小是10mm。 空气搅拌主副槽要有适度、均匀的打气搅拌。 循环每小时3-4个循环。 添加系统需要,加料泵材质为PVC、PP 或PE,可耐强碱。 过滤系统连续循环过滤,用10μm过滤棉芯或过滤袋。 抽风需要。
加热系统需要。 5.镀液的分析及补加 工作液的Ni2+标准浓度为6.0克/升,Ni2+浓度的分析方法:用移液管取5ml工作液置于250ml的锥形瓶中,加入50ml 去离子水,再加入10ml氨水(28%),摇匀,加入0.2克紫脲酸铵指示剂,摇匀,用0.05M的EDTA标准液进行滴定,终点为浅棕色变为浅紫色。以EDTA用量为准进行计算 计算方法为:补加A量=补加C量(ml)=(6-EDTA用量×0.59)×13×体积(L) 6.操作要点 确保镀槽在使用前用硝酸(1:1)浸泡,并用水冲洗干净 镀液温度保持在29-35度,温度太低则速度慢,温度太 高则镀液易分解 用氨水和硫酸(20%)调pH值,保持pH值在9.0-9.5间,以确保镀速,pH值太低则镀速慢,太高则镀液易分解,最好用pH计控制。 避免带入重金属杂质以及表面活性剂。
优秀的化学镀镍,这些步骤一个都不能少!
优秀的化学镀镍,这些步骤一个都不能少! 化学镀镍不受镀件形状的影响,对于形状复杂怪异的仪器零件、管道或容器内壁,甚至是特殊条件下的阀和搅拌器等均能提供非常均匀的镀层。这些是其他电镀工艺难以实现的,而且化学镀镍生产设备比较简单、操作方便,因此化学镀镍被广泛应用于各种设备零件。 其次,化学镀镍有优异的耐磨性能和耐腐蚀性能,因此被用于制造手术刀和缝合器等医疗器械、航天航空器发动机的零件、轴和滚筒类的零件、大型模具或零件、高精密零件等。 第三,化学镀镍的均匀厚度和始终如一的电热性等物理性能,使其在电子工业上也大放异彩,经过化学镀镍能提高电子元件的可靠性,目前计算机生产中的硬盘、驱动器、软盘、光盘、打印机鼓等绝大部分都采用了化学镀镍。 化学镀镍的工艺流程包括前处理、化学镀镍和后处理3大部分,每一部分都对化学镀镍的最终效果起关键性作用。 化学镀镍前处理包括了研磨抛光、除油、除锈、活化等过程,与其他电镀加工的方法类似,其中研磨和机械抛光是对待镀件表面进行整平处理的机械加工过程;除油、除锈则是为了除去待镀件表面的油污和锈迹,以便镀层结合更牢固;活化是为了是待镀件获得充分活化的表面,以催化化学镀反应的进行。 化学镀镍的操作在这里就不详细叙述了,下面来了解一下经过化学镀镍操作后,如何做好最后一个步骤:化学镀镍后处理,来提升其效果性能或为后续的二次电镀做好准备。
零件在化学镀镍后必须采取清洗和干燥,目的在于除净零件表面残留的化学镀液、保持镀层具有良好的外观,并且防止在零件表面形成“腐蚀电池”条件,保证镀层的耐蚀性。除此之外,为了不同的目的和技术要求还可能进行如下后续处理。 1、烘烤除氢,提高镀层的结合强度,防止氢脆。 2、热处理,改变镀层组织结构和物理性质,如提高镀层硬度和耐磨性。 3、打磨抛光,提高镀层表面光亮度。 4、铬酸盐钝化,提高镀层耐蚀性。 5、活化和表面预备,为了涂覆其他金属或非金属涂层,提高镀层耐蚀性、耐磨性或者进行其他表面功能化处理。 我们可以看到,要做好化学镀镍的加工,前处理与后处理是极其重要的。其实不仅是化学镀镍,阳极氧化、电镀锌、镀硬铬、不锈钢表面处理等电镀加工都需注意前处理与后处理。因此拥有一套完善成熟的电镀处理流程对于电镀企业来说是重中之重。
化学镀镍废水处理工艺研究
化学镀镍废水处理工艺研究 化学镀镍是以镍盐和次磷酸盐等共同作用生成的非晶镀层,是一种前沿的表面处理技术,被广泛的用于电子、石油、计算机和汽车等领域。以次磷酸盐为还原剂的化学镀镍技术的机理是原子氢理论,该理论认为是H2PO2-催化脱氢产生原子氢并还原镍离子,其总反应式如式(1)所示: 随着化学镀时间的不断延长,溶液中的亚硫酸根离子等副产物达到一定浓度时,化学镀溶液会自发分解,金属一磷合金镀层的沉积受到影响,镀层的耐磨性等性能下降,导致废弃,形成化学镀废液。化学镀镍废液中含有大量难降解有机污染物和无机盐,其中的金属镍含量高达几克每升,镍离子与络合剂EDTA,NTA等结合形成稳定的高浓度难降解工业废液,很难通过传统的化学破络及沉淀方法彻底去除。同时,化学镀镍废液中含有含量较高的次磷酸根和亚磷酸根离子,不加处理会引起水体富营养化。目前,化学镀镍废水主要采用化学沉淀法、离子交换法、膜分离及吸附法进行处理。但离子交换法,膜分离及吸附法存在运行操作技术要求高,膜易受污染以及离子交换剂饱和再生等限制,不能大范围的推广应用。化学破络及沉淀法操作方便、设备简单,在含镍废水中应用较多。如施银燕等采用双氧水和NaOH沉淀去除废水中的镍离子,于泊集等使用氢氧化镁处理不同pH值得含镍废水均取得一定的去除效果。李蛟等用CaO破络合剂处理镀镍废水,结果表明镍离子的最高去除率只有32%,因此,单一的化学试剂处理并无法满足废水中金属离子、无机盐和有机物的同时去除。《污水综合排放标准》(CB 8978-1996)中明确限定磷酸盐的排放限值应低于0. 5 mg / L ,而化学镀废水中次/亚磷酸盐由于溶度积较高,直接投加Ca和Fe离子对其沉淀效果较差,必须将其氧化为正磷酸根再通过沉淀等手段去除。Fenton ( H2 O2 +Fe2+)氧化技术是高级氧化技术的一种,其产生轻基自由基(HO·)氧化电位高达2. 8 eV,可以氧化绝大多数的有机或无机物,具有试剂无毒、绿色、操作简单等特点。因此,通过Fenton氧化技术不仅可以去除化学镀废水中的高浓度有机物,还可以氧化次/亚磷酸盐,回收反应过程中正磷酸根和三价铁形成的高纯度磷酸铁,从而实现资源回收。 本文在化学沉淀的基础上,采用两段式处理工艺,即CaO破络除镍和Fenton氧化法去除有机物和磷,对反应过程中的各影响因索进行了研究。研究表明,该方法不仅能有效的去除废水中的金属镍,更可以回收反应过程中产生的磷酸铁。该工艺处理效率高,操作简单,实用性强,将具有一定的应用价值。 1 实验部分 1.1 实验水样 实验所用废水取自某化学镀镍车间,废水产量约1 t / d,呈浅绿色,该化学镀废水中主要包含硫酸镍、次磷酸氢钠、柠檬酸钠、乙酸和氨水等。该废水性质如表1所示。
化学镀镍工艺
化学镀镍工艺——镀前处理需知 化学镀镍的对象是具体的工件,进厂待镀的工件状况,包括工件材质、制造或维护方法,工件尺寸和最终使用情况是不同的;因此前处理方法应有所不同。在确定正确的前处理工艺流程时,必须对工件善有充分的了解。 合金类型为保证镀层足够的结合力以及镀层质量,必须鉴定基体材质。某些含有催化毒性合金成分的材料在镀前处理时加以表面调整,保证除去这些合金成分后才能进行化学镀镍。例如:铅(含铅钢)、硫(含硫钢)、过量的碳(高碳钢)、碳化物(渗碳钢)等。因为这些物质的残留会产生结合力差和起泡问题。而且,在未除净这些物质的表面、镀层会产生针孔和多孔现象。另一种处理方法是在镀前采用预镀的方法隔离基体才料中有害合金元素的影响。在不清楚待镀工件材质而且又不可能进行材料分析的情况下,必须进行预先试验,试合格后方可处理工作。 工件的制造历史钢件表面状况由于渗碳、渗氮、淬火硬化后提高表面硬度是重要的变化途径之一。通常化学镀镍在硬度范围HRC58-62的铁件表面上镀层的结合力是难以合格的。一方面,上述硬度范围的工件必须进行特别的清洗方法,即在含氰化物的溶液中周期换向电解活化或其它合适的电解清洗,以便溶解除去表面的无机物质诸如碳化物。另一方面,在施镀中产生的表面应力,诸如航天工业用的表面有较高张应力的工件,必须在镀前镀后进行去应力处理,以获得合格的结合力。在制造过程中工件表面大量通讯以除去的机械润滑油和抛光剂等也必须在镀前清除干净。 工件的维修历史工件维修时为除去表面的有机涂层、铁锈或氧化皮,采用喷砂处理,这种工件是化学镀前最难处理的。因为这些工件表面不仅嵌进了残留物质,而且腐蚀产物附着得很牢。在这种情况下,应先采用机械方法清洁表面,以保证后续化学清洗和活化工序的质量。为除去工件表面嵌进的油脂和化学脏污,有时预先烘工件十分有效,尽管这不是唯一的好用的清除方法。 工件的几何尺寸许多工件的几何赃妨碍了采用某前处理技术,如大尺寸的容器以及内表面积很大的管件就是如此。通常清洗和活化钢件应包括电解清洗和活化,在上述情况下,应采用机械清洗、化学清洗和活化更为可行。对于具有盲孔和形状复杂的零件,需要加强清洗工序以解决除去污垢、氢气泡逸出和溶液带出的问题。在工件吊挂和放置方法上也应考虑解决上述问题。 工件非镀面的阻镀问题许多工件要求局部化学镀镍,因此必须彩屏蔽材料将非镀部分保护起来。屏蔽材料可用压敏胶带、涂料、专用塑料夹具等。当然市场上现在有商品的阻镀涂料(或叫保护漆)出售,并且高级一点的,可以镀后轻松除去,用专用溶剂溶解后可以反复使用。 化学清洗浸洗是化学镀前处理的重要步骤之一,其重要的功能在于清除工件表面的污垢,为保证清洗效果,通常使用清洗剂、机械搅拌和加温。采用碱性清洗剂时必须加热至60-80℃,以便彻底清洗污垢,大多数碱性清洗采取浸洗并且强力搅拌,也可以采用喷淋清洗方式。市售的浸洗清洁剂的质量和去污能力差异很大,因此根据工件污染程度选用清洁剂是很重要的。 电解清洗电解清洗化学镀镍活化处理前的末道清洗方法,多适用于精密零件。直流电解清洗即阻极电解清洗的优点在于工件表面产生大量的氢气增加了洗涤效果;其缺点在于工件带负电,因而吸附清洗溶液中的铜、锌和其它金属离子、皂类和某些胶体物质,在工件上形成疏松的电极泥以致带去。电解清洗时采用周期换向电注,当工件为阳极时,迫使工件表面带正电荷的离子和污垢脱离。而且工件表面生成的氧气有利于有效地洗涤掉嵌牢在工件上的污垢,由清洗溶液中的清洁剂去润湿污垢,乳化转换掉污垢。
电镀废水处理 除镍剂 重金属捕集剂 重捕剂 化学镍废水
本文介绍含镍电镀废水处理方案,通过化学沉淀法,可以把镍处理至表三标准,镍浓度处理至0.1mg/L以下。 l 工具/原料 l 含镍电镀废水 l 化学镀镍废水 l 锌镍合金处理剂 l 重金属捕集剂 l 聚合氯化铝PAC、聚丙乙烯酰胺PAM、氢氧化钠 l 方法/步骤 1.含镍电镀废水介绍含镍电镀废水是指电镀镍时所产生的清洗水,一般分为电镀镍废水和化学镀镍废水,电镀镍废水是指通过电镀把金属镍镀在金属基底上,例如以铜为基底;化学镀镍 废水是指通过化学氧化还原的方法把镍镀在基底上,基底多为塑料等非导体。电镀镍废水的成分比较简单,一般多为镍离子以及硫酸根等,化学镀镍废水成分复杂, 除了镍离子外,废水中还含有大量的络合剂,比如柠檬酸、酒石酸、次磷酸钠等。 2.含镍电镀废水处理标准在电镀废水处理标准中,国家表一标准要求镍排放标准不高于1m g/L,国家表二标准要求不高于0.5mg/L,国家表三标准要求不高于0.1mg/L,《电镀废水治理工程规范》中要求含镍废水需要单独收集,并且镍需要处理至标准才能排放至综合池。 3.针对电镀含镍废水以及化学镀镍废水,可采用化学沉淀法进行处理,化学沉淀法不需要复杂的设备。其中,电镀含镍废水可以直接采用加碱至11,PAC混凝,PAM絮凝沉淀出水,镍即可达标,如果含镍废水中混有前处理废水,那么需要在加碱之后的出水加入少量重金属捕集剂重金属捕集剂进行螯合反应,重金属捕集剂重金属捕集剂可以把镍离子从低浓度处理至达标。 对于化学镀镍废水,由于废水中存在大量的络合剂,络合剂与镍离子形成络合小分子溶解于废水中,因此直接加碱不能沉淀,通过加入锌镍合金处理剂进行反应,可以破坏络合健的结构,通过螯合反应与镍离子结合,再通过混凝絮凝沉淀,把镍离子去除。 4.根据含镍电镀废水处理方案,设计相应的含镍废水处理工艺。对于电镀镍废水,采用两步法处理比较划算,即先用氢氧化钠进行沉淀一次以后,再加入 重金属捕集剂重金属捕集剂螯合沉淀。 5.对于化学镀镍废水,可以通过一步法直接加锌镍合金处理剂进行螯合沉淀,把镍离子去除。 l 注意事项 l 电镀镍废水与化学镀镍废水,镍的种类不一样,处理方法也不同 l 注意在破坏络合剂时,有时也可以采用氧化破络的办法
化学镀镍
化学镀镍/浸金的状况 ENIG Introduction 作为PCB的表面镀层,镍层的厚度要求>5um,而浸金层厚度在0.05-0.15um 之间。化学镀镍/浸金镀层的焊接性是由Ni层来体现的,因此Au层的厚度不能太高,否则会产生脆性和焊点不牢的故障。Au只起保护Ni层的作用,防止Ni 的氧化和渗析,所以又不能太薄。 As one of the surface finishing for PCB, the thickness of nickel layer shall be more than 5um, while the thickness of immersion gold shall be between 0.05-0.15 um. As the solderability of ENIG is reflected from Ni layer, so the au layer shall not be too thick. Or else there will be frangibility and solder pot unstable issue. Au is to protect the Ni layer and prevent from Ni oxidation and dialysis. So it shall not be too thin. 现在的Ni/Au生产线都采用Atotech公司的Atotech化学Ni/Au工艺。 Nowadays most Ni/Au production lines are adopting atotech chemical Ni/Au technology developed by Atotech company. 沉镍Electroless Nickel 1 沉镍原理概述Electroless Nickel Principle introduction 沉镍金工艺的沉镍的原理,实际上反而从“化镍浸金”一词中能够较容易地被我们所理解。即其中镍层的生成是自催化型的氧化-还原反应,在镀层的形成过程中,无需外加电流,只靠高(85-1000C左右)槽液中次磷酸钠(NaH2PO2)还原剂的作用,即可在已活化的铜表面反应析出镍镀层。而沉镍金工艺中金镀层的生成,则是典型的置换反应。当PCB板进入金槽时,由于镍的活性较金大,因而发生置换反应,镍镀层表面逐渐被金所覆盖。 ·The Principle of Electroless Nickel can be more easily understood from the word of “Electroless Nicke Immersion Gold”. That means the nickel layer is generated from the Autocatalytic redox reaction. During the coating forming process, impressed current is not needed. Under NaH2PO2 reductant in bath with high temperature between 85-1000C, nickel layer can be formed via activated copper surface reaction. But the gold layer is generated via typical replacement reaction. When PCB enters the gold bath, as the nickel is more active than gold, there will be replacement reaction. So the nickel layer will be covered by gold.
化学镀镍工艺
化学镀镍工艺 化学镀镍机理: 1)原子氢析出机理。原子氢析出机理是1946年提出的,核心是还原镍的物质是原子氢,其反应过程如下: H2P02-+H20→HP032-+H++2H Ni2++2H→Ni+2H+ H2P02-+H++H→2H20+P 2H→H2 水和次磷酸根反应产生了吸附在催化表面上的原子氢,吸附氢在催化表面上还原镍离子。同时,吸附氢在催化表面上也产生磷的还原过程。原子态的氢相互结合也析出氢气。2)电子还原机理(电化学理论)电子还原机理反应过程如下: H2P02-+H20→HP032-+H++2e Ni2++2e→Ni H2P02-+2H++e→2H20+P 2H++2e→H2 酸性溶液中,次磷酸根与水反应产生的电子使镍离子还原成金属镍。在此过程中电子也同时使少部分磷得到还原。 3)正负氢离子机理。该理论最大特点在于,次磷酸根离子与磷相连的氢离解产生还原性非常强的负氢离子,还原镍离子、次磷酸根后自身分解为氢气。 H2P02-+H20→HP032-+H++H- Ni2++2H-→Ni+H2 H2P02-+2H++H-→2H20+P +1/2H2 H-+H+→H2 分析上述机理,可以发现核心在于次磷酸根的P-H键。次磷酸根的空间结构是以磷为中心的空间四面体。空间四面体的4个角顶分别被氧原子和氢原子占据,其分子结构式为: 各种化学镀镍反应机理中共同点是P-H键的断裂。P-H键吸附在金属镍表面的活性点上,在镍的催化作用下,P-H键发生断裂。如果次磷酸根的两个P-H键同时被吸附在镍表面的活性点上,键的断裂难以发生,只会造成亚磷酸盐缓慢生成。对于P-H键断裂后,P-H间共用电子对的去向,各种理论具有不同的解释。如电子在磷、氢之间平均分配,这就是原子氢析出理论;如果电子都转移至氢,则属于正负氢理论;而电子还原机理则认为电子自由游离出来参与还原反应。因此,可以根据化学镀镍机理的核心对各种宏观工艺问题进行分析解释。 化学镀镍工艺过程 化学镀镍前处理工艺 一:除油:
化学镀镍配方成分,化学镀镍配方分析技术及生产工艺
化学镀镍配方成分分析,镀镍原理及工艺技术导读:本文详细介绍了化学镍的研究背景,分类,原理及工艺等,本文中的配方数据经过修改,如需更详细资料,可咨询我们的技术工程师。 禾川化学引进国外配方破译技术,专业从事化学镍成分分析、配方还原、研发外包服务,为化学镍相关企业提供一整套配方技术解决方案。 一、背景 化学镀镍也叫做无电解镀镍,是在含有特定金属盐和还原剂的溶液中进行自催化反应,析出金属并在基材表面沉积形成表面金属镀层的一种优良的成膜技术。化学镀镍工艺简便,成本低廉,镀层厚度均匀,可大面积涂覆,镀层可焊姓良好,若配合适当的前处理工艺,可以在高强铝合金和超细晶铝合金等材料上获得性能良好的镀层,因此在表面工程和精细加工领域得到了广泛应用。 禾川化学技术团队具有丰富的分析研发经验,经过多年的技术积累,可以运用尖端的科学仪器、完善的标准图谱库、强大原材料库,彻底解决众多化工企业生产研发过程中遇到的难题,利用其八大服务优势,最终实现企业产品性能改进及新产品研发。 样品分析检测流程:样品确认—物理表征前处理—大型仪器分析—工程师解谱—分析结果验证—后续技术服务。有任何配方技术难题,可即刻联系禾川化学技术团队,我们将为企业提供一站式配方技术解决方案! 二、化学镀工艺 化学镀工艺流程为:试样打磨-清洗-封孔-布轮抛光-化学除油-水洗-硝酸除锈-水洗-活化-化学镀-水洗-钝化-水洗-热水封闭-吹干。
图1 化学镀的工艺流程图 三、化学镀镍分类 化学镀镍的分类方法种类多种多样,采用不同的分类规则就有不同的分类法。 四、化学镀镍原理 目前以次亚磷酸盐为还原剂的化学镀镍的自催化沉积反应,已经提出的理论有羟基-镍离子配位理论、氢化物理论、电化学理论和原子氢态理论等,其中以原子氢态理论得到最为广泛的认同。 该理论认为还原镍的物质实质上就是原子氢。在以次亚磷酸盐为还原剂还原Ni2+时,可以以下式子表示其总反应: 3NaH2PO2+3H2O+NiSO4→3NaH2PO3+H2SO4+2H2+Ni(1) 也可表达为: Ni2++H2PO2-+H2O→H2PO3-+2H++Ni(2)