快速凝固铝合金的组织与性能
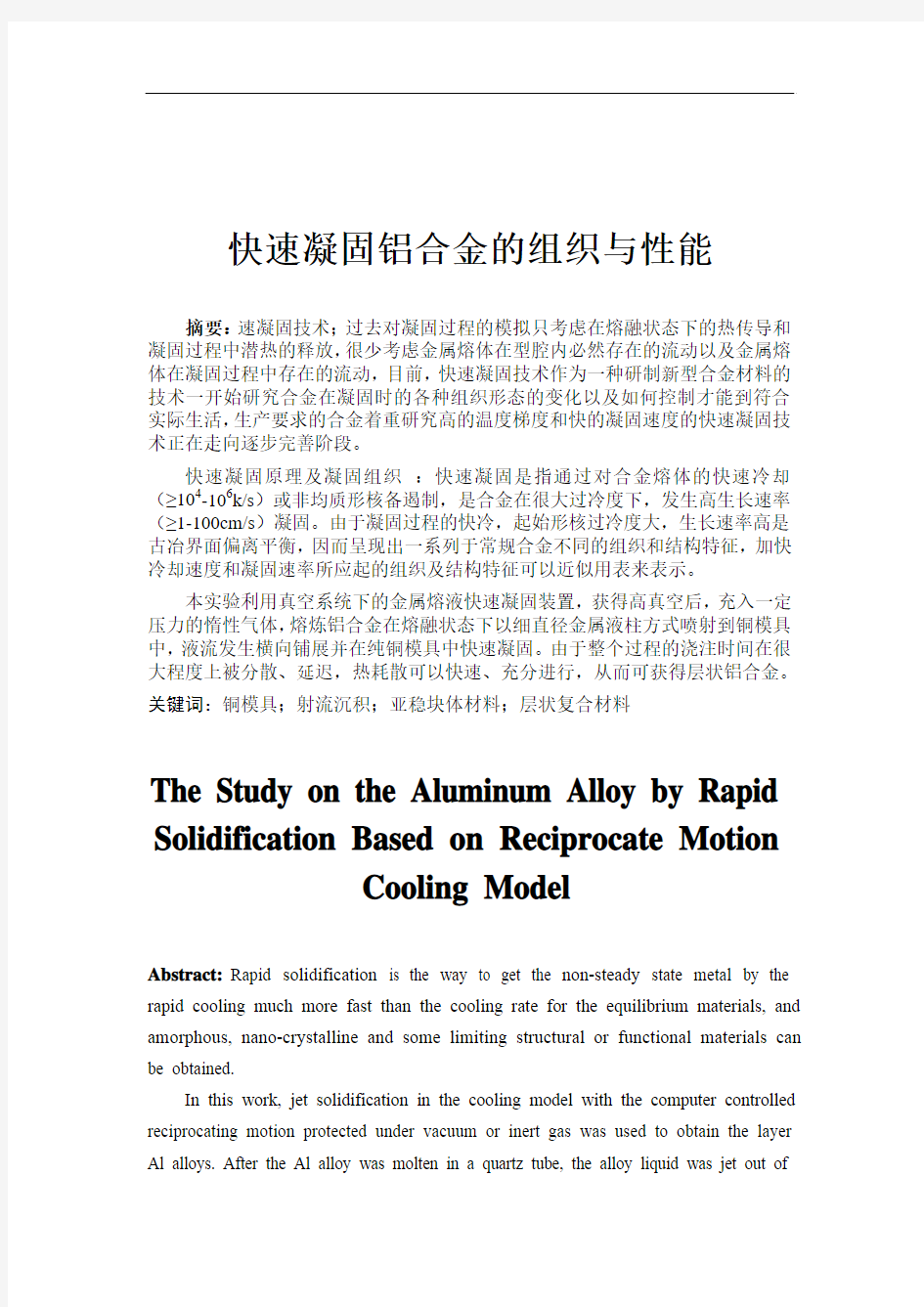

快速凝固铝合金的组织与性能摘要:速凝固技术;过去对凝固过程的模拟只考虑在熔融状态下的热传导和凝固过程中潜热的释放,很少考虑金属熔体在型腔内必然存在的流动以及金属熔
体在凝固过程中存在的流动,目前,快速凝固技术作为一种研制新型合金材料的
技术一开始研究合金在凝固时的各种组织形态的变化以及如何控制才能到符合
实际生活,生产要求的合金着重研究高的温度梯度和快的凝固速度的快速凝固技术正在走向逐步完善阶段。
快速凝固原理及凝固组织:快速凝固是指通过对合金熔体的快速冷却(≥104-106k/s)或非均质形核备遏制,是合金在很大过冷度下,发生高生长速率(≥1-100cm/s)凝固。由于凝固过程的快冷,起始形核过冷度大,生长速率高是古冶界面偏离平衡,因而呈现出一系列于常规合金不同的组织和结构特征,加快冷却速度和凝固速率所应起的组织及结构特征可以近似用表来表示。
本实验利用真空系统下的金属熔液快速凝固装置,获得高真空后,充入一定压力的惰性气体,熔炼铝合金在熔融状态下以细直径金属液柱方式喷射到铜模具中,液流发生横向铺展并在纯铜模具中快速凝固。由于整个过程的浇注时间在很大程度上被分散、延迟,热耗散可以快速、充分进行,从而可获得层状铝合金。关键词:铜模具;射流沉积;亚稳块体材料;层状复合材料
The Study on the Aluminum Alloy by Rapid Solidification Based on Reciprocate Motion
Cooling Model
Abstract:Rapid solidification is the way to get the non-steady state metal by the rapid cooling much more fast than the cooling rate for the equilibrium materials, and amorphous, nano-crystalline and some limiting structural or functional materials can be obtained.
In this work, jet solidification in the cooling model with the computer controlled reciprocating motion protected under vacuum or inert gas was used to obtain the layer Al alloys. After the Al alloy was molten in a quartz tube, the alloy liquid was jet out of
a little hole under the tube inside a copper die by high pressure Ar gas, and alloy liquid lateral spread and solidify in the model. The process were repeated foe many times, and accumulation like a wall growing up. Since the pouring time of the entire process was delay and dispersed, heat was quickly and fully dissipated, so the bulk layer Al alloy was obtained. The alloy be with the high density and fine structure.Microstructure observation, hardness testing, tensile test were carried out for the alloy. The aluminum alloy
By precise control of the working parameter, the test was adjust to obtained the needed materials. The interface of multi-layer homogeneous composite was studied, such as superheat of the molten metal, the relationship between the liquid jetting parameters and solidification process, metallurgical complex process, heat dissipation process and control of the materials deposition growth process were also analyzed. The experiences was obtained for the fabrication of multi-layer deposition composites of high melting point metals and alloys.
Keywords:reciprocating motion; jetting sediment; metestable bulk materials;
composite materials
目录
第1章绪论 (1)
1.1 引言 (1)
1.2 铝合金及其主要分类 (1)
1.2.1 铝合金的分类 (1)
1.2.2 变形铝合金 (2)
1.2.3 铸造铝合金 (2)
第2章实验方法 (2)
2.1实验原理 (2)
2.2实验设备 (3)
2.3实验过程 (4)
第3章实验结果与讨论 (5)
3.1铝合金试样的制备 (5)
3.2层状铝合金的组织 (6)
3.3硬度测试实验结果 (6)
3.4快速凝固的冷速 (6)
第4章结论 (7)
第1章绪论
1.1非晶材料简介
非晶合金具有长程无序、短程有序的结构,与晶态合金相比,具备许多特有的性能,如高硬度、高强度、高电阻、耐蚀及耐磨等,为材料科研工作者开发高性能的功能材料和结构材料提供了巨大的潜力。
块体非晶合金形成的成分和结构条件影响非晶形成能力的因素有:合金中原子的键合特征、电子结构、原子尺寸的相对大小、各组元的相对含量、合金的热力学性质以及相应的晶态结构等。一般情况,如果某种物质对应的晶体结构很复杂,原子之间的键合较强,并且有特定的指向,其形成非晶结构在动力学上要容易一些。对非晶形成的可能性Inoue总结了3条实验规律:(1)合金由3种以上组元构成;(2)各组元原子尺寸差别较大,一般大于12%;(3) 3个组元具有负的混合热。从液态到形成非晶态,原子结构几乎不发生变化,各组成元素之间一般具有大于12%的原子尺寸差异和负的混合热,这样能够形成紧密随机堆垛结构,能够增大固液界面能,抑制结晶形核,也增大了长程范围内原子的重排困难性,抑制了晶体的生长,从而形成非晶态结构。
块体非晶合金材料的制备方法在早期,非晶材料的制备,首先采用快速凝固法制备非晶粉末,然后用粉末冶金方法将粉末压制或粘结成型。20世纪90年代初发现了具有极低临界冷却速率的合金系列,可以直接从液相获得块体非晶固体。目前,块体非晶合金的制备方法基本可划分为直接凝固法和粉末固结成形法。形成能力和宽的过冷液相区ΔTx,并且形成一种与传统非晶合金不同的新型非晶态组织,其特点为:原子呈高度密堆排列;产生新的区域原子组构;存在相互吸引的长程均匀性。Takeuchi等计算了351种三元非晶态合金系及其二元子系统的混合焓(ΔH)和错配熵(ΔS/KB),进一步完善了Inoue准则。Inoue准则被普遍接受,并依据它发现了许多能形成大块非晶的合金系,如Mg基、Al基、Fe基、Zr基、La基、Ti基、Cu基等。直接凝固法具体包括:水淬法,铜模铸造法,吸入铸造法,高压铸造,磁悬浮熔炼,单向熔化法等。粉末固结成形法该方法是利用非晶合金特有的在过冷液相区间的超塑成形能力,将非晶粉末加压固结成形。粉末固结成形法只需制备低维形状的非晶粉末,因此可以在一定程度上突破块体非晶合金尺寸上的限制,是一种极有前途的块体非晶合金的制备方法[6]。进行非晶粉末
固结成形的粉末冶金技术通常有热压烧结(HP)、热等静压烧结(HIP)等。除传统的粉末冶金技术外,最近有报道利用放电等离子烧结(Spark Plasma Sintering, SPS)技术将非晶粉末致密化制备块体非晶合金材料。SPS技术是利用外加脉冲强电流形成的电场清洁粉末颗粒表面氧化物和吸附的气体,并活化粉末颗粒表面,提高颗粒表面的扩散能力,再在外加压力下利用强电流短时加热粉体进行快速烧结致密化。其消耗的电能仅为传统烧结工艺的1/5~1/3。SPS技术具有如下优点:烧结温度低(比HP和HIP低200~300 ℃)、烧结时间短(只需3~10 min),而HP和HIP需要120~300 min)、单件能耗低;烧结机理特殊,赋予材料新的结构与性能;烧结体密度高,显微组织均匀,是一种近净成形技术;操作简单。SPS技术作为一种近年来迅速发展的新兴快速烧结技术,是一种很有前途的非晶粉末固结技术。由于其具有烧结温度低、烧结时间短、能够快速固结粉末制备致密的块体材料,因此,SPS技术可以应用于制备需要抑制晶化形核的非晶块体材料。其烧结机理是在极短的时间内,粉末间放电,快速熔化,在压力作用下非晶粉末还没来得及晶化就已经发生烧结,而后通过很快的冷却速度,非晶态结构被保存下来,从而得到致密的块体非晶态合金。Shen和Inoue利用SPS技术制备出了直径为20 mm、厚度为5mm Fe65Co10Ga5P12C4B4大块铁基非晶合金,其相对密度高达99.7%,且具有良好的软磁性能。韩国的Taek-SooKim利用SPS技术制备出了Cu54Ni6Zr22Ti18铜基非晶合金,玻璃转变温度为712 K,过冷温区(ΔT = Tx-Tg)为55 K,相对密度98%以上。韩国的Choi等利用SPS技术烧结制备出了Al-La-Ni-Fe非晶合金,其相对密度为96%,ΔT高达74 K。
块体非晶合金材料的性能应用,与晶态合金相比,非晶态合金在物理性能(力、热、电、磁)和化学性能等方面都发生了显著的变化。
非晶合金的力学性能及应用。非晶合金与普通钢铁材料相比,有相当突出的高强度、高韧性和高耐磨性。根据这些特点利用非晶态材料和其它材料可以制备成优良的复合材料,也可以单独制成高强度耐磨器件。非晶合金材料已广泛用于轻、重工业、军工和航空航天业,在材料表面、特殊部件和结构零件等方面也都得较广泛的应用。
非晶金属的电学性能及应用。一般非晶态金属的电阻率较同种的普通金属材料要高,在变压器铁芯材料中利用这一特点可降低铁损。在某些特定的温度环境下,非晶的电阻率会急剧的下降,利用这一特点可设计特殊用途的功能开关。还可利用其低温超导现象开发非晶超导材料。目前,人们对非晶态合金电学性能及其应用方面的了解相对较少,尚有待进一步研发。
非晶合金还具有优异的化学性能。研究表明,非晶态合金对某些化学反应具有明显的催化作用,可以用作化工催化剂。某些非晶态合金通过化学反应可以吸
收和释放出氢,可以用作储氢材料。由于没有晶粒和晶界,非晶态合金比晶态合金更加耐腐蚀,因此,它可以成为化工、海洋等一些易腐蚀的环境中应用设备的首选材料。
1.2 层状金属复合材料
层状金属复合材料;层状金属复合材料是利用股和技术是两种或两种以上物理、化学、力学性能不同的金属在界面上实现牢固冶金结合而制备的一种新型复合材料,层状金属符合材料在保持木材金属特性的同时具有“相补效应”可以弥补各自的不足,经过恰当的组合易于形成有益的综合性能,被广泛的应用。
层状金属复合材料的生产方法有多种,传统上可以分为两类:固-固相复合法和液-固相复合法,前者报多:爆炸复合法,轧制复合法,挤压复合法,扩散焊接法,后者包括铸造复合法,钎焊法。复合方式的不同也决定了复合材料的结构、功能特性和应用领域,也各有其优缺点。例如,利用复合轧制、挤出等压力加工方法可以获得有限层数的同质或异质层状金属复合材料,但所选用材料必须具有很好的延展性,对于延展性不好的材料则不能应用;利用金属粉末喷射激光烧结技术可以制备多层金属复合材料,但由于存在金属粉末表面氧化层、烧结过程的氧化,以及烧结技术本身存在致密度差的缺点而导致大量冶金缺陷的存在;金属粉末喷射成型技术是将现代塑料喷射成形技术引入粉末冶金领域而形成的一门新型粉末冶金近净形成形技术。但其制备过程需要加入有机粘结剂,从而使得制备和使用温度受到限制而不能用于制备全金属复合材料,且其复合界面并非冶金结合。
1.3 铝合金及其主要分类
根据铝合金的成分与生产工艺特点,可以将铝合金分为变形铝合金和铸造铝合金。这两组合金可用铝合金的二元平衡图作概略的说明(见图1.1)。
变形铝合金
共晶温度时的饱和溶解度D点是这两类合金成分的分界线。在D点右边的为铸造铝合金,这样,就保证铸造铝合金中有较多的共晶体,在液态时有较好的流动性,对铸型能充分填充使铸件致密,但铸造铝合金的塑性低,不适于压力加工。D点以左变形铝合金,这组合金的化学成分不高,合金有较高的塑性,适于压力加工。可获得均匀的单相固溶体组织,这种组织的变形能力较好,适于锻造及压延。
图1.1 铝合金的二元相图
变形合金需要有良好的塑性变形能力,合金的主要组成相位固溶体,为了提高强度,合金中需要包含少量的第二相,变形铝合金中主要包括硬铝和锻铝。
2024铝合金是硬铝中常用合金,属Al-Cu-Mg系合金,主要强化相由θ
(CuAl
2),S(Al
2
CuMg),MnAl
6
相,当Cu/Mg逐渐减小时,主要强化相由θ相过度到
S相。S相具有很高的室温强度,且耐热性也较高,因此耐热硬铝皆保持较低的铜镁比,以获得(α+S)的组织。该合金主要作用150℃以下工作的零件,如用作飞机蒙皮,骨架,肋梁,隔框等高强度结构件。常用作高温下工作的零件,如航空发动机压气机的叶片等。
铸造铝合金
铸造铝合金的优点是比重小,比强度较高,并有良好的抗蚀性和铸造工艺性,可进行各种成型铸造,而且由于铝合金的熔点较低,熔炼工艺和设备都比较简单,因此铝合金铸件在航空,一般机械制造及仪表等工业部门都得到了相当广泛的应用。
铸造铝合金按其主要成分可以分为五类:
(1)Al-Si系及Al-Si-Mg系合金,即著名的硅铝明。这类合金具有优良的铸造工艺性和气密性,中等强度,适合在常温下使用,可生产形状复杂的铸件,应用很普遍。
(2)Al-Cu系合金。特点是有较高的热强性,适合在较高温度工作,但这类合金的铸造工艺性和抗蚀性较低。
(3)Al-Mg系合金。属于高强和搞抗蚀性合金,并有良好的切削加工和光制性
能,在造船工业和食品,化工部门应用较多。缺点是耐热性和铸造工艺性较差。
(4)Al-RE(稀土)系合金。这类合金具有良好的耐热性和铸造工艺性,最高使用温度可达400℃,缺点是室温强度低,合金成分复杂,生产管理不方便。(5)Al-Zn系合金。这类合金的特点是具有自淬火效应,铸造成型后即可直接进行人工时效,因而省去了淬火工序,铸件的内应力大为减小。适于制造要求尺寸稳定性高的铸件。其缺点是比重较大,耐热性也很低。
第2章实验方法
2.1实验原理
本实验利用真空系统下的具有的金属熔液快速凝固装置,获得高真空后充入一定压力的惰性气体熔炼铝金属及合金为熔融状态以细直径金属液柱方式射流到安置一定宽度的纯铜模具上,液流发生横向铺展并在纯铜模具中快速凝固。由于整个过程的浇注时间在很大程度上被分散、延迟,热耗散可以快速、充分进行,从而可获得层状金属材料。并对于获得的层状金属进行金相观察组织分析,力学性能等研究。真空高频感应熔炼实验装置如图2.1。
图2.1 真空高频感应熔炼实验装置示意图
图2.2 沉积金属过程示意图
2.2实验设备
带有往真空感应熔炼炉(图2.3),MP-2B型号的研磨抛光机,GX71金相显微镜,显微硬度计,电子拉伸试验机,101-2A型电热鼓风干燥箱,SX1-5-10箱式电阻炉。
图2.3 带有往复运动机构的真空感应熔炼炉
图2.4 纯铜快速凝固模具
2.3实验过程
在自行设计的装置,在高真空及惰性气体保护条件下,利用纯铜基板的机构,
将熔炼金属为熔融状态后,喷射到纯铜模基板上并铺展快速凝固,反复堆积生长,各层之间避免了氧化膜的产生,具有冶金结合,往复运动金属液射流喷射到具中沉积,得到层状铝合金。每个合金重量约为15g。
第三章实验结果与讨论
3.1铝合金试样的制备
图3.1为真快速凝固过程示意图。将熔炼炉抽高真空,真空度达到0.1Pa以下,充入少量高纯度氩气后再次抽高真空,…
制备工艺参数为:…。
图3.1 快速凝固过程示意图
在铜模具中刚制备出来的铝合金,如图3.2和图3.3所示,
图3.2 快速凝固铝合金
图3.3为其正视图。可以看出合金样品的侧面并不是平整。其原因可能与射流过程中的工艺参数有关,例如瞬间喷射量、喷射速度、往复运动铜模具冷却能力发生变化等。
3.2 层状铝合金的组织
标尺???
图3.4 铝合金金相组织
3.3 硬度测试实验结果
显微硬度测量参数:加载5kg,时间10s。
表3.1 实验前后显微硬度值(HV)变化
实验点 平均值 1
2 3 原始铝合金
28.3 29.7 30.2 29.4 层状铝合金 97.8 103 98.4 99.7
3.4 快速凝固的冷速
为了讨论快速凝固过程对制备出来的材料的金相组织的影响,以下进行了对
冷速的讨论。
熔炼温度约为680?C ,在高压氩气的作用下合金熔液以液柱状喷射到铜模具
上,。。。
。液柱与沉积表面接触后,开始发生横向铺展。由于纯铜具有极强的导热能
力,合金熔液横向铺展到铜模具侧壁,就应完成凝固过程。
假设速度为行走速度的1/10,则
s v d t Croos 1.0302/62/===
(3.1) s K t T T t T v R cooling /70001
.0306801=-=-=?= (3.2) 温差650C ,0.1s ,大约7000K/s ,在如此大的冷速下获得的Al 合金的晶粒远
远小于普通铸造,
第4章结论
1.在真空及惰性气体保护条件下,在急冷铜模中喷射沉积制备了层状铝合金从宏观上观察沉积铝合金,其侧表面虽然可以看出层状状态,但金相显微分析表明,内部组织没有明显的分层。
2.理论计算表明,冷速约为2000?C/s,铝合金中的晶粒尺寸约为10μm,远小于正常铸态的晶粒尺寸,这与熔融Al合金射流到基板上后,以及合金熔液横向铺展过程,侧壁大量散热,从而加速合金溶液的冷却和凝固过程有关。
3.力学实验表明,其真空往复运动沉积射流硬度高于正常铸态的铝合金。
参考文献
[1]刘春林,金属粉末喷射成型技术与应用[J],宁波高等专科学校学报,
V ol24,2,(2004).1
[2] 2024铝合金薄板的热处理工艺与性能的研究西北工业大学
2007.03
[3] 万群. 中国冶金百科全书金属材料卷,[M],北京:冶金工业出版社,2001
[4] 李月珠.快速凝固剂技术和材料M北京:国法工业出版社,1993
[5] 张驰,杨长辉,陈元芳,金属(陶瓷)粉末注射成型技术及应用[J],现代制造
工程,(2003)
[6] 陈振华,严红革,陈刚,等.多层喷射沉积的装置和原理[J].湖南大学学
报.2001,5(28) p21.
[7] 陈振华,蒋向阳,杨伏良,等.喷射沉积设备[P].中国专利:ZL 95110862.x,
1995-07.
[8] 林肇琦等,有色金属材料学[M],沈阳:东北工学院出版社,1986.
[9] 林肇琦等,有色金属材料学[M],沈阳:东北工学院出版社,1986.
[10] 林肇琦等,有色金属材料学[M],沈阳:东北工学院出版社,1986.
[11] 林肇琦等,有色金属材料学[M],沈阳:东北工学院出版社,1986.
[12] 林肇琦等,有色金属材料学[M],沈阳:东北工学院出版社,1986.
热处理对7075铝合金组织和性能的影响
热处理对7075铝合金组织和性能的影响 摘要:对7075铝合金进行了固溶和单级时效处理,研究了单级时效对铝合金组织和性能的影响,结果表明铝合金经单级时效后纤维组织消失,在晶界处生成第二相粒子。铝合金显微硬度的峰值时效温度为120℃,时间为16h,硬度为220HV。120℃/24h时效后合金的峰值强度为680.5MPa。本研究中主要阐述热处理对7075铝合金组织和性能的影响。 关键词:热处理;7075铝合金;组织性能 引言 近些年来,铝合金的发展历程先后经历了由单一的追求高强度到追求高强耐腐蚀,再到追求高强高韧耐腐蚀性能,又到高强高韧耐腐蚀抗疲劳,最终到现在的追求高淬透性高综合性能五个发展阶段。然后发展方向却集中在以满足高强高韧铝合金的航空航天领域以及适用于各种使用条件的民用铝合金领域。当前对于铝合金强韧化以及耐蚀性的研究已经成为了重中之重,相信随着综合性能的提高,铝合金在国民经济发展中的运用将更加广泛。 1、7xxx系铝合金概述 7xxx铝合金是以Al-Zn-Mg和Al-Zn-Mg-Cu合金为主的一种超高强度铝合金,它是超高系列铝合金的最主要代表,Fe和Si是7xxx铝合金的主要有害杂质。较2xxx高强度铝合金在强度和硬度方面高出许多。属于热处理可强化的合金。该系铝合金具有强度高、密度小、易加工、焊接性能良好等优良特点,并且一般耐蚀性较好,因此在航空航天工业、车辆、建筑、桥梁、工兵装备及大型压力容器方面得到了广泛的应用。现阶段7xxx铝合金的研究主要集中在通过调节合金化元素和优化热处理工艺来得到高强高韧耐腐蚀的综合性能[1]。这也是本文的研究方向的出发点。该系代表合金如7005、7050、7075等。 2、试验材料与方法 试验材料为7075铝合金,将铝合金(尺寸为20mmX20mmX160mm)在盐浴中进行固溶处理,处理工艺为480℃/2h铝合金固溶处理后在试验箱中进行单级时效处理,时效温度分别为100,120,150℃,时效时间为0-48h。 将试样按国标GB/T228-2010用线切割加工成拉伸试样,用酒精超声清洗去除表面油污,在MT810万能试验机上进行拉伸强度测试,取5个试样的平均值;采用
快速凝固技术
快速凝固技术的研究进展 摘要:快速凝固技术是当材料科学与工程中研究比较活跃的领域之一,目前已成为一种金属材料潜在性能与开发新材料的重要手段。快速凝固技术得到的合金与常规合金有着不同的组织和结构特征,对材料科学和其它学科的理论研究以及开展实际生产应用起了重要的作用。介绍了快速凝固技术的原理和特点、主要方法和在实际中的应用和存在的问题。 关键词:快速凝固技术;合金;应用;存在问题
1 引言 随着对金属凝固技术的重视和深入研究,形成了许多种控制凝固组织的方法,其中快速凝固已成为一种具有挖掘金属材料潜在性能与发展前景的开发新材料的重要手段,同时也成了凝固过程研究的一个特殊领域[1]。过去常规铸造合金之所以会出现晶粒粗大,偏析严重、铸造性能差等缺陷的主要原因是合金凝固时的过冷度和凝固速度很小,这是由于它们凝固时的冷速很小而引起的。要消除铸造合金存在的这些缺陷,突破研制新型合金的障碍,核心是要提高熔体凝固时的过冷度,从而提高凝固速度,因此出现了快速凝固技术。 目前,快速凝固技术作为一种研制新型合金材料的技术已开始研究了合金在凝固时的各种组织形态的变化以及如何控制才能得到符合实际生活、生产要求的合金。着重于大的温度梯度和快的凝固速度的快速凝固技术,正在走向逐步完善的阶段。 2 快速凝固技术 1960年美国的Duwez等用铜辊快淬法,首次使液态合金在大于107K/S的冷却速度下凝固,在Cu—Si合金中发现了无限固溶的连续固溶体;在Ag—Ge合金中出现新的亚稳相;在Au—Si合金中形成非晶结构。在快速冷却所形成的亚稳结晶组织中,出现了一系列前所未见的重要的结构特征,表现出各种各样比常规合金优异的使用性能[2]。此后,快速凝固技术和理论得到迅速发展,成为材料科学与工程研究的一个热点。 快速凝固是指通过对合金熔体的快速冷却(≥104~106 K/s)或非均质形核被遏制,使合金在很大过冷度下,发生高生长速率(≥1~100 cm/s)凝固[3]。通过快速凝固技术获取的粉末和材料会具有特殊的性能和用途。由于它是一种非平衡的凝固过程[4],详细的说就是凝固过程中的快冷、起始形核过冷度大,生长速率高,促使固液界面偏离平衡,生成亚稳相(非晶、准晶、微晶和纳米晶),从
铝合金及热处理
铝合金的热处理 铸造铝合金的金相组织比变形铝合金的金相组织粗大,因而在热处理时也有所不同。前者保温时间长,一般都在2h以上,而后者保温时间短,只要几十分钟。因为金属型铸件、低压铸造件 铸造铝合金的金相组织比变形铝合金的金相组织粗大,因而在热处理时也有所不同。前者保温时间长,一般都在2h以上,而后者保温时间短,只要几十分钟。因为金属型铸件、低压铸造件、差压铸造件是在比较大的冷却速度和压力下结晶凝固的,其结晶组织比石膏型、砂型铸造的铸件细很多,故其在热处理时的保温也短很多。铸造铝合金与变形铝合金的另一不同点是壁厚不均匀,有异形面或内通道等复杂结构外形,为保证热处理时不变形或开裂,有时还要设计专用夹具予以保护,并且淬火介质的温度也比变形铝合金高,故一般多采用人工时效来缩短热处理周期和提高铸件的性能。 一、热处理的目的 铝合金铸件热处理的目的是提高力学性能和耐腐蚀性能,稳定尺寸,改善切削加工和焊接等加工性能。因为许多铸态铝合金的机械性能不能满足使用要求,除Al-Si系的ZL102,Al-Mg系的ZL302和Al-Zn系的ZL401合金外,其余的铸造铝合金都要通过热处理来进一步提高铸件的机械性能和其它使用性能,具体有以下几个方面:1)消除由于铸件结构(如璧厚不均匀、转接处厚大)等原因使铸件在结晶凝固时因冷却速度不均匀所造成的内应力;2)提高合金的机械强度和硬度,改善金相组织,保证合金有一定的塑性和切削加工性能、焊接性能;3)稳定铸件的组织和尺寸,防止和消除高温相变而使体积发生变化;4)消除晶间和成分偏析,使组织均匀化。
二、热处理方法1、退火处理 退火处理的作用是消除铸件的铸造应力和机械加工引起的内应力,稳定加工件的外形和尺寸,并使Al-Si系合金的部分Si结晶球状化,改善合金的塑性。其工艺是:将铝合金铸件加热到280-300℃,保温2-3h,随炉冷却到室温,使固溶体慢慢发生分解,析出的第二质点聚集,从而消除铸件的内应力,达到稳定尺寸、提高塑性、减少变形、翘曲的目的。 2、淬火 淬火是把铝合金铸件加热到较高的温度(一般在接近于共晶体的熔点,多在500℃以上),保温2h以上,使合金内的可溶相充分溶解。然后,急速淬入60-100℃的水中,使铸件急冷,使强化组元在合金中得到最大限度的溶解并固定保存到室温。这种过程叫做淬火,也叫固溶处理或冷处理。 3、时效处理 时效处理,又称低温回火,是把经过淬火的铝合金铸件加热到某个温度,保温一定时间出炉空冷直至室温,使过饱和的固溶体分解,让合金基体组织稳定的工艺过程。 合金在时效处理过程中,随温度的上升和时间的延长,约经过过饱和固溶体点阵内原子的重新组合,生成溶质原子富集区(称为G-PⅠ区)和G-PⅠ区消失,第二相原子按一定规律偏聚并生成G-PⅡ区,之后生成亚稳定的第二相(过渡相),大量的G-PⅡ区和少量的亚稳定相结合以及亚稳定相转变为稳定相、第二相质点聚集几个阶段。 时效处理又分为自然时效和人工时效两大类。自然时效是指时效强化在室温下进行的时效。人工时效又分为不完全人工时效、完全人工时效、过时效3
铝合金铸造技术篇
国兴金属制品有限公司教育训练教材 铝合金铸造技术篇 一、前言: 铝合金为目前使用极为广泛的一种金属。在铸造上而言,不论重力铸造,砂模铸造、压铸精密铸造┄等各种铸造方法均可见到大量的铝合金铸件,由于这些方法铸造,其原因乃在于铝合金具有质量轻、机械质优良、耐腐蚀、美观以及机械加工容易等优点。因而不仅大量使用于一般生活用品,例如:运输工具、通信器材、运动器材料、家庭五金┄等商业用途上,亦大量使用于航空太空载具及武器系统等军事装备。 铝合金铸造技术的发展时间,已有数十年历史,由于机械设计及加工观念的改变与要求以及机械设计的日趋复杂,加上新的合金不断的被发展出来,部份的铸造用铝合金机械强度甚至超过一些锻造用铝合金,如A201、A206等,因而铸造的重要性再度被肯定,在铸造一般生活用品时,铝合金的铸造并非一困难工作,但要铸造高品质的铸件时,则铝合金的铸造就非想象中的容易。 影响铸件品质的要素有八点,例如:铸造方案的设计,材料的选择以及铝水的品 质等,其中铝水的品质,则系熔炼的工作。 二、熔炼设备 熔炉: 铝合金熔炼用的炉子,以热源区分,可分为两个主要的种类:燃料及电力。 在使用燃料的熔炉中,则又分为油炉及瓦斯两种。 而电力炉则可区分为反应炉及电阻炉。 在选择炉子时,值得考虑的因素甚多,例如:熔解量的多寡;能源的价格;原始设备的成本,安装的价格,设备维护的难易,厂房设施配合;以及产品的种类。就一般铝合金铸造的:由于铝件的重量有限,为求操作上的方便,以及成本的考虑,绝大部份均系采用坩锅炉(目前已大量改用连续炉)。 以不同加热方式的炉子而言,使用油炉或气炉,或可降低成本。但是,不论油炉或电炉,均有机会增加铝水中的氢气量。一般而言,在使用油炉时,所使用的燃油中带含有10-20%的水气,对气炉而言,例如瓦斯不包含空气之中,因温度而含的水分,而仅计算燃烧所产生水蒸气,至少在消耗气体量的两倍以上。而不论使用燃油或瓦斯气体为热源时,燃烧后产生的水气,必然是包围着熔解炉。因此,可想而知的是氢气 的来源必然可观。 三、铝汤处理之目的: 在铝汤有由原材料在熔解过程中发生的氢气或氧化物等非金属介在物之外,尚含钠碱
金属凝固原理复习资料
金属凝固原理复习题部分参考答案 (杨连锋2009年1月) 2004年 二 写出界面稳定性动力学理论的判别式,并结合该式说明界面能,温度梯度,浓度梯度对界面稳定性的影响。 答:判别式, 2 01()()2 (1)m c v D s g m v D g G T k ωωωω * *??- ??? =-Γ- ++?? -- ??? ,()s ω的正负决定 着干扰振幅是增长还是衰减,从而决定固液界面稳定性。第一项是由界面能决定的,界面能不可能是负值,所以第一项始终为负值,界面能的增加有利于固液界面的稳定。第二项是由温度梯度决定的,温度梯度为正,界面稳定,温度梯度为负,界面不稳定。第三项恒为正,表明该项总使界面不稳定,固液界面前沿形成的浓度梯度不利于界面稳定,溶质沿界面扩散也不利于界面稳定。 三 写出溶质有效分配系数E k 的表达式,并说明液相中的对流及晶体生长速度对E k 的影 响。若不考虑初始过渡区,什么样的条件下才可能有0s C C * = 答:0 00 (1)N L s v E D C k k C k k e δ*- = = +- 可以看出,搅拌对流愈强时,扩散层厚度N δ愈小, 故s C * 愈小。生长速度愈大时,s C * 愈向0C 接近。(1)慢的生长速度和最大的对流时,N L v D δ《1,0E k k = ;(2)大的生长速度或者液相中没有任何对流而只有扩散时,N L v D δ》1,E k =1 (3)液相中有对流,但属于部分混合情况时,0 1E k k <<。1E k =时,0 s C C * = ,即在 大的生长速度或者液相中没有任何对流而只有扩散时。 四 写出宏观偏析的判别式,指出产生正偏析,负偏析,和不产生偏析的生长条件。 答:0 1s q q C k C k = -+,s C 是溶质的平均浓度,0C 是液相的原始成分,q 是枝晶 内溶质分布的决定因素,它是合金凝固收缩率β,凝固速度u 和流动速度v 的函数, (1)(1)v q u β=-- 。0s C C =,即 1p u v β β =- -时,q=1,无宏观偏析。0s C C >时,对于01k <的合金来说,为正偏析,此时 1p u v β β >- -。0s C C <时,对于01k <的合金来 说,为负偏析,此时 1p u v β β <- -。 五 解:用2m m m m r m m k r T V T V T H H σσ?=- ?=- ? ??计算
均匀化退火对6056铝合金组织与性能的影响
均匀化退火对6056铝合金组织与性能的影响 宁波科诺铝业有限责任公司,董培纯邱建平李博 摘要:采用热分析技术、扫描电子显微镜、拉伸试验研究均匀化退火处理对于6056铝合金微观组织和力学性能的影响。结果表明:6056铝合金铸态组织存在严重的枝晶偏析及明显的非平衡共晶组织,经过540℃×12 h 均匀化退火处理后,枝晶偏析和非平衡共晶组织明显消除,其强度降低、塑性大幅度提高。 关键词:均匀化退火;微观组织;力学性能 The effect of homogenizing annealing on microstructure and properties of 6056 aluminum alloy (Ningbo KENO Aluminum Co.,Ltd,Ningbo 315033,China) Abstract:The influence of homogenizing annealing on microstructure and properties of 6056 aluminum alloy is investigated by heat analysis technology,scan electrical microscope and tensile test. The results show that severe dendritic-segregation and unequilibrium phases exist in its as-cast structure,After 540℃×12h homogenizing annealing treatment,dendrite segregation and unequilibrium eutectic phases eliminate . The strength decrease and the ductility increase obviously. Keywords:Homogenization annealing;Microstructure;Mechanical properties 引言 6056铝合金是广泛应用于汽车和航空领域的一种Al-Mg-Si-Cu合金,其强度比6061铝合金高15%,可焊性、耐腐蚀性能和切削加工性能均优于7075和2024铝合金[1,2]。6056铝合金成分复杂,在半连续铸造过程中,铸锭组织会不同程度地偏离平衡状态,产生严重的枝晶偏析,形成大量的非平衡凝固共晶组织,因此,6056铝合金铸锭必须进行均匀化退火处理,以消除枝晶偏析,同时使合金中非平衡凝固共晶组织溶入基体,最大限度地减少基体中残留的结晶相,提高合金的塑性[3,4]。 均匀化退火处理是6056铝合金获得理想工艺性能和力学性能的关键环节之一。目前国内对于6065铝合金的均匀化退火处理的研究还不充分,本文通过研究均匀化退火对6065铝合金微观组织和性能的影响,为6056铝合金的生产提供试验指导。 试验材料与试验方法 按照表1所示的6056铝合金成分进行配料,使用中频感应炉熔炼,精炼后采用半连续铸造的方法铸成Φ85 mm的铸棒。在铸棒上取样,采用DSC进行热分析试验,得到铸棒中低熔点共晶组织的熔化温度,以确定均匀化退火温度,DSC试验的升温速率5 ℃/min,从室温加热到600 ℃。截取Φ85×100 mm的铸棒进行均匀化退火,均匀化退火温度为540 ℃,保温时间分别是6 h、12 h。从铸态和均匀化退火后的铸棒上切取金相试样,经机械研磨和抛光后,在2 ml HF、3 ml HCl、5 mlHNO3、250 mlH2O 腐蚀液中腐蚀10 s,用清水冲洗干净,然后用酒精擦净吹干,制得的试样采用扫描电子显微镜观察微观组织形貌。将铸态及均
铝合金
铝合金铸件气孔与预防 引言:在纯铝中加入一些金属或非金属元素所熔制的铝合金是一种新型的合金材料,由于其比重小,比强度高,具有良好的综合性能,因此被广泛用于航空工业、汽车制造业、动力仪表、工具及民用器具制造等方面。随着国民经济的发展以及经济一体化进程的推进,其生产量和耗用量大有超过钢铁之势。加强对铝合金材料性能的研究,保证铝合金铸件具有优良品质,既是我们每一个科技工作者义不容辞的责任,也是同我们的日常生活息息相关的头等大事。本文结合作者铝合金铸件生产实践经验谈谈铝合金铸件气孔与预防问题。 1.气孔类别 由于铝合金具有严重的氧化和吸气倾向,熔炼过程中又直接与炉气或外界大气相接触,因此,如熔炼过程中控制稍许不当,铝合金就很容易吸收气体而形成气孔,最常见的是针孔。针孔(gas porosity/pin-hole),通常是指铸件中小于1mm的析出性气孔,多呈圆形,不均匀分布在铸件整个断面上,特别是在铸件的厚大断面和冷却速度较小的部位。根据铝合金析出性气孔的分布和形状特征,针孔又可以分为三类①,即: (1) 点状针孔:在低倍组织中针孔呈圆点状,针孔轮廓清晰且互不连续,能数出每平方厘米面积上针孔的数目,并能测得出其直径。这种针孔容易与缩孔、缩松等予以区别开来。 (2) 网状针孔:在低倍组织中针孔密集相连成网状,有少数较大的孔
洞,不便清查单位面积上针孔的数目,也难以测出针孔的直径大小。 (3) 综合性气孔:它是点状针孔和网状针孔的中间型,从低倍组织上看,大针孔较多,但不是圆点状,而呈多角形。 铝合金生产实践证明,铝合金因吸气而形成气孔的主要气体成分是氢气,并且其出现无一定的规律可循,往往是一个炉次的全部或多数铸件均存在有针孔现象;材料也不例外,各种成分的铝合金都容易产生针孔。 2.针孔的形成 铝合金在熔炼和浇注时,能吸收大量的氢气,冷却时则因溶解度的下降而不断析出。有的资料介绍②,铝合金中溶解的较多的氢,其溶解度随合金液温度的升高而增大,随温度的下降而减少,由液态转变成固态时,氢在铝合金中的溶解度下降19倍。(氢在纯铝中的溶解度与温度的关系见图1③)。因此铝合金液在冷却的凝固过程中,氢的某一时刻,氢的含量超过了其溶解度即以气泡的形式析出。因过饱和的氢析出而形成的氢气泡,来不及上浮排出的,就在凝固过程中形成细小、分散的气孔,即平常我们所说的针孔(gas porosity)。在氢气泡形成前达到的过饱和度是氢气泡形核的数目的函数,而氧化物和其他夹杂物则在起气泡核心的作用 在一般生产条件下,特别是在厚大的砂型铸件中很难避免针孔的产生。在相对湿度大的气氛中溶炼和浇注铝合金,铸件中的针孔尤其严重。这就是我们在生产中常常有人纳闷干燥的季节总比多雨潮湿的时节铝合金铸件针
快速凝固
什么是快速凝固?请说明实现快速凝固的基本条件、满足快速凝固条件的途径以及快速凝固的特点。 答:快速凝固,是指在比常规工艺过程快得多的冷却速率下,合金以极快的速率从液态转变为固态的过程。快速凝固的实质是使受冷合金在一个方向上传热迅速,因而用这些方法做出的材料,均是薄片或细粉。 金属材料快速凝固技术主要包括用于试验研究的液态金属快速冷淬技术和连续生产用的工业快速凝固技术。 实现快速凝固的两个基本条件是: (1)金属熔液必须被分散成液流或液滴,而且至少在一个方向上的尺寸极小,以便散热; (2)必须有能带走热量的冷却介质。 满足上述条件的途径各有三条:熔液可分散成细小液滴、接近圆形断面的细流或极薄的矩形断面液流;散热冷却可借助于气体、液体或固体表面。几乎所有实际的快速凝固工艺都遵循这些途径。图2给出了它们之间的组合,以构成快速凝固生产工艺。其中七种组合是切实可行的工艺。只有薄带状液流与液体和气体冷却介质的组合没有成功,因为在快速流动的流体中要使液流保持矩形断面是极其困难的。
图2快速凝固基本工艺中金属液流和冷却介质间的组合 快速凝固工艺:1.雾化快凝固速度法(RSR);旋转电极法(REP)。 2.水雾化快速旋转杯法(RSC)。 3.杜瓦兹枪、柱塞/铁砧、鼓喷溅、 电子束喷溅淬冷、控制喷雾沉积(CSD)、喷雾沉积、奥斯普雷(Osprey)。 4.泰勒丝、自由飞行熔液自旋(FFMS)。 5.FFMS、旋转水纺丝。 6.熔液提取、 垂直滴落熔液提取。7.熔液自旋、平面流铸、熔液拖拽、熔液溢流从快速凝固的原理来讲,实现快速凝固的大致有三种基本途径。 1、凝固前施以深度过冷 这种途径是在液态金属凝固以前,温度就下降到低于固相线较多的水平,然后才发生金属的凝固过程。在金属凝固的过程中,要放出潜热,该潜热又要加热凝固中的金属,凝固中金属的温度上升,但不会超过固相线的水平。也可以这么说,凝固潜热完全为凝固中的金属所吸收,不向外界传播,而凝固也快速完成。为达到这种途径快速凝固的目的,开始必须把金属过冷到足够的程度,以致使凝固放热能得到抵消。原则上过冷和凝固金属的体积并没有多大关系,然而实际上,体积大了,冷却工艺进行得就较慢。实践中最大的限制问题是很难做到大型凝固件中没有杂质存在。杂质能起到晶核的作用,从而使过冷的程度受到限制。 2、高拉速连续凝固
快速凝固铝合金的组织与性能
快速凝固铝合金的组织与性能摘要:速凝固技术;过去对凝固过程的模拟只考虑在熔融状态下的热传导和凝固过程中潜热的释放,很少考虑金属熔体在型腔内必然存在的流动以及金属熔 体在凝固过程中存在的流动,目前,快速凝固技术作为一种研制新型合金材料的 技术一开始研究合金在凝固时的各种组织形态的变化以及如何控制才能到符合 实际生活,生产要求的合金着重研究高的温度梯度和快的凝固速度的快速凝固技术正在走向逐步完善阶段。 快速凝固原理及凝固组织:快速凝固是指通过对合金熔体的快速冷却(≥104-106k/s)或非均质形核备遏制,是合金在很大过冷度下,发生高生长速率(≥1-100cm/s)凝固。由于凝固过程的快冷,起始形核过冷度大,生长速率高是古冶界面偏离平衡,因而呈现出一系列于常规合金不同的组织和结构特征,加快冷却速度和凝固速率所应起的组织及结构特征可以近似用表来表示。 本实验利用真空系统下的金属熔液快速凝固装置,获得高真空后,充入一定压力的惰性气体,熔炼铝合金在熔融状态下以细直径金属液柱方式喷射到铜模具中,液流发生横向铺展并在纯铜模具中快速凝固。由于整个过程的浇注时间在很大程度上被分散、延迟,热耗散可以快速、充分进行,从而可获得层状铝合金。关键词:铜模具;射流沉积;亚稳块体材料;层状复合材料 The Study on the Aluminum Alloy by Rapid Solidification Based on Reciprocate Motion Cooling Model Abstract:Rapid solidification is the way to get the non-steady state metal by the rapid cooling much more fast than the cooling rate for the equilibrium materials, and amorphous, nano-crystalline and some limiting structural or functional materials can be obtained. In this work, jet solidification in the cooling model with the computer controlled reciprocating motion protected under vacuum or inert gas was used to obtain the layer Al alloys. After the Al alloy was molten in a quartz tube, the alloy liquid was jet out of
快速凝固技术概述
快速凝固技术国内外发展及其应用 1.快速凝固技术国内外发展 随着对金属凝固技术的重视和深入研究,形成了许多种控制凝固组织的方法,其中快速凝固已成为一种具有挖掘金属材料潜在性能与发展前景的开发新材料的重要手段,同时也成了凝固过程研究的一个特殊领域。 快速凝固的概念和技术源于20世纪60年代初Duwez等人的研究,他们发现某些共晶合金在平衡条件下本应生成双相混合物,但当液态合金以足够快的冷却速度凝固合金液滴被气体喷向冷却板时,则可能生成过饱和固溶体、非平衡晶体,更进一步生成非晶体。上述结果稍后被许多研究结果所证实,而且由此发现一些材料具有超常的性能,如电磁、电热、强度和塑性等方面的性能,出现了用于电工、电子等方面的非晶材料。20世纪70年代出现了用快速凝固技术处理的晶态材料,80年代人们逐渐把注意力转向各种常规金属材料的快速凝固制备上,90年代大块非晶合金材料的开发与应用取得重大进展。快速凝固技术是目前冶金工艺和金属材料专业的重要领域,也是研究开发新材料手段。 快速凝固一般指以大于 5 10 ~ 6 10 K/s的冷却速率进行液相凝固成固相,是一种非平衡的 凝固过程,通常生成亚稳相(非晶、准晶、微晶和纳米晶),使粉末和材料具有特殊的性能和用途。由于凝固过程的快冷、起始形核过冷度大,生长速率高,使固液界面偏离平衡,因而呈现出一系列与常规合金不同的组织和结构特征。加快冷却速度和凝固速率所起的组织及结构特征可以近似地用图1来表示。从上图我们不难看出,随着冷却速度的加快,材料的组织及结构发生着显著的变化,可以肯定地说,它也将带来性能上的显著变化[1]。 快速凝固技术得到的合金具有超细的晶粒度,无偏析或少偏析的微晶组织,形成新的亚稳相和高的点缺陷密度等与常规合金不同的组织和结构特征。实现快速凝固的三种途径包括:动力学急冷法;热力学深过冷法;快速定向凝固法。由于凝固过程的快冷,起始形核过冷度大,生长速率高,使固液界面偏离平衡,因而呈现出一系列与常规合金不同的组织和结构特征。 1.1快速凝固技术的主要方法 (1)动力学急冷快速凝固技术 动力学急冷快速凝固技术简称熔体急冷技术,其原理可以概括为:设法减小同一时刻凝固的熔体体积与其散热表面积之比,并设法减小熔体与热传导性能很好的冷却介质的界面热阻以
铝合金的凝固和组织中的晶粒
铝合金的凝固和组织中的晶粒 一、熔体的凝固过程: 在半连续铸造过程中,熔体的浇铸和凝固是同时连续地进行的。对铸锭而言,冷却是分两次实现的。一次冷却是在结晶器内完成的,熔体进入结晶器后靠结晶器导热,在结晶器内形成一定厚度的凝固壳。此后随着铸造机下降,被拉出结晶器,遇到结晶器底部浇出的冷却水(称之为二次冷却)从此完成凝固的全部过程。这个凝固过程在金属学中称为金属结晶。 二、铸锭的正常晶粒组织 从理论上讲,在工业生产条件下,铸锭的晶粒组织由三个区域组成:即外层表面的细等轴晶区,由此往里的柱状晶区和中心等轴晶区。但在实际铝合金生产中铸锭在强度大的冷却条件下,经过Al-Ti-B的细化处理,铝合金铸锭的组织往往全部是等轴晶。铸锭晶粒的大小将直接影响铝加工制品的力学性能和加工性能,所以它被作为衡量铸锭质量的一个主要指标。 三、影响铸锭晶粒的因素 1、熔体结晶的条件:熔体结晶有两个条件是必不可少的,其一是结晶必需要先形成晶核,熔体中的晶核分两种。自发晶核是在低于结晶温度时,熔体由于能量起伏或液相起伏形成的晶核。非自发晶核是外来粒子进入熔体后而形成的晶核。其二是要有过冷度才可能发生结晶,所谓过冷度就是熔体的温度只有在冷却到低于熔点的温度下才能结晶,温度越低过冷度越大。 2、晶粒的细化:控制过冷度;一般情况下增大过冷度,熔体中的生核率和晶粒的长大速度都增加,但生核速度大于晶粒的增长速度,所以一般情况下金属结晶时过冷度越大,所得到晶粒越细小。在半连续铸造生产中增加过冷度的主要途径是有降低铸造速度使
单位时间内铸锭冷却量增加;降低冷却水的温度使单位时间内铸锭的温降增加;加大冷却水的水压使单位时间内浇到铸锭上的水量增加使铸锭的温降增加;降低铸造温度使铸锭的结晶过程缩短。 3、动态细化晶粒:对熔体采用机械搅拌、电磁搅拌、超声波振动等,这样一方面可以靠输入的能量使晶核提前生成,另一方面可以使成长中的树枝状晶破碎增加晶核的数目(在这里就要讲一下晶粒的形成,晶粒是先有一个晶核、晶核按多个方向晶轴成长,象树枝一样称之为枝晶,当众多的枝晶共同生长到一定程度互相顶撞,此时熔体添补到枝晶中,围绕它形成了一个枝晶粒) 4、变质处理细化晶粒:向熔体中加入少量的活性物质,促进熔体内部生成晶核或改变晶粒的成长过程,在变形铝合金中一般选用Ti、Zr、B、C等作为晶粒细化剂,我公司铸造时加入Al-Ti-B 丝就属于变质处理的方法。 四、粗大晶粒 在宏观组织中出现的均匀或不均匀的大晶粒均称为粗大晶粒。 1、粗大晶粒的宏观组织:粗大晶粒在铸锭的低倍试片检查时很容易发现,为了便于区别根据其直线尺寸,分别为五个级别:一级晶粒 1.17mm、 二级晶粒1.59mm、三级晶粒2.16mm、四级晶粒2.78mm、五级晶粒3.76mm。正常情况下铸锭的晶粒度一般控制在二级以上。有时由于工艺控制不当,铸锭中可出现超大晶粒,其尺寸有时可以超过正常晶粒的几倍,乃至几十倍。 2、粗大晶粒产生的原因:主要原因是,当铸造冷却速度慢时过冷度小,生成晶核的数量小,晶粒成长速度快则会产生均匀的粗大晶粒。其次是熔铸工艺的影响,如熔体过烧或局部过热使熔体中的非自发晶核急剧熔解,结晶核减少;熔体在炉内停留时间过长,
工艺参数对3003铝合金组织与 性能的影响
Material Sciences 材料科学, 2018, 8(5), 603-608 Published Online May 2018 in Hans. https://www.360docs.net/doc/7f12410053.html,/journal/ms https://https://www.360docs.net/doc/7f12410053.html,/10.12677/ms.2018.85071 Effect of Process Parameters on Microstructure and Properties of 3003 Aluminum Alloy Yitan Wang1, Qingsong Dai1,2, Ping Fu1, Mingwei Zhao1 1Guangxi Liuzhou Yinhai Aluminum Co., Ltd., Liuzhou Guangxi 2School of Materials Science and Engineering, Central South University, Changsha Hunan Received: May 4th, 2018; accepted: May 20th, 2018; published: May 29th, 2018 Abstract Taking 3003 aluminum alloy as the research object, the effects of cold rolling rate and annealing temperature on the microstructure and properties of the sheet were studied. The results show that the work hardening of 3003 alloy sheet is significant. With the increasing of cold rolling de-formation, the tensile strength and yield strength of alloy plates increase gradually, while the elongation decreases. And during the annealing of the finished product, recovery and recrystalli-zation occur within the alloy. As the annealing temperature increases, the tensile strength and yield strength gradually decrease, and the elongation gradually increases. Keywords 3003 Aluminum Alloy, Cold Rolling Deformation, Annealing Temperature, Microstructure and Properties 工艺参数对3003铝合金组织与 性能的影响 王绎潭1,戴青松1,2,付平1,赵明伟1 1广西柳州银海铝业股份有限公司,广西柳州 2中南大学材料科学与工程学院,湖南长沙 收稿日期:2018年5月4日;录用日期:2018年5月20日;发布日期:2018年5月29日
常见铝合金特性及其主要用途[指南]
常见铝合金特性及其主要用途[指南] 常见铝合金特性及其主要用途 一、1000系列,,纯铝系 1、 1060 作为导电材料IACS保证61%,需要强度时使用6061电线 2、 1085 1080 1070 1050 1N30 1085 1080 1070 1050? 成形性、 表面处理性良好,在铝合金中其耐蚀性最佳。因为是纯铝、其强度较低,纯度愈高其强度愈低。日用品、铝板、照明器具、反射板、装饰品、化学工业容器、散热片、溶接线、导电材 3、 1100 1200 1100 1200 AL纯度99.0%以上之一般用途铝材,阳极氧化处理后之外观略呈白色外与上记相同。一般器物、散热片、瓶盖、印刷板、建材、热交换器组件 1N00, 强度比1100略高,成形性良好,其化特性与1100相同。 二、日用品 2000系列,, AL x Cu系 1、 2011快削合金,切削性好强度也高。但耐蚀性不佳。要求耐蚀性时,使用6062系合金音量轴、光学组件、螺丝头 2、 2018 2218 2018 2218锻造用合金。锻造性良好且高温强度较高,因此使用於需要耐热性之锻造品。耐蚀性不佳。汽缸头、活塞、 VTR汽缸 3、 2618锻造用合金。高温强度优越但耐蚀性不佳。活塞、橡胶成形用模具、一般耐热用途组件 4、2219 强度高,低温及高温特性良好,溶接性也优越,但耐蚀性不佳。低温用容器、航太机器 5、2025 锻造用合金。锻造性良好且强度高,但耐蚀性不佳。螺旋桨、磁气桶 2N01, 锻造用合金。具耐热性,强度也高,但耐蚀性不佳。航空器引擎、油压组件
三、 3000系列,,AL x Mn系 1、3003 3203 3003 3203强度比1100约高10%,成形性、溶接性、耐蚀性均良好。一般器物、散热片、化?板、影印机滚筒、船舶用材 2、 3004 3104 3004 3104强度比3003高,成形性优越,耐蚀性也良好。铝罐、灯炮盖头、屋顶板、彩色铝板 3、3005强度比3003高约20%,耐蚀也比较好。建材、彩色铝板 4、3105 强度比3003略高,其他之特性与3003类似。建材、彩色铝板、瓶盖 四、4000系列,,AL x Si系 1、4032 耐热性、耐摩俄性良好,热膨胀?数小。活塞、汽缸头 2、4043 汤流良好,凝固收缩少,用硫酸阳极氧化处理呈灰色之自然发色。溶接线、建筑嵌板 五、5000系列,,AL x Mg系 1、 5005, 5005 5050强度与3003相同,加工性、溶接性、耐蚀性良好,阳极氧化后之修饰加工良好,与6063形材?色相称。建筑用内外装、车辆之内装、船舶之内装 2、5052 ?中程度强度之最具代表性合金,耐蚀性、溶接性及成形性良好,特别是疲劳强度高,耐海水性佳。一般怆金、船舶、车辆、建筑、瓶盖、蜂巢板 3、5652 限制5052之不纯物元素,并抑制过氧化氢分离之合金,其他特性与5052同过氧化氢容器 4、5154 强度比5052约高20%,其他特性与5052相同与5052同样、压力容器 5、5254 限制5154之不纯物元素,并抑制过氧化氢分解之合金,其他特性与5154相同。过氧化氢容器
铝合金铸造工艺
铝合金铸造工艺 一、铸造概论 铝合金铸造的种类如下: 由于铝合金各组元不同,从而表现出合金的物理、化学性能均有所不同,结晶过程也不尽相同。故必须针对铝合金特性,合理选择铸造方法,才能防止或在许可范围内减少铸造缺陷的产生,从而优化铸件。 1、铝合金铸造工艺性能 铝合金铸造工艺性能,通常理解为在充满铸型、结晶和冷却过程中表现最为突出的那些性 能的综合。流动性、收缩性、气密性、铸造应力、吸气性。铝合金这些特性取决于合金的成分,但也与铸造因素、合金加热温度、铸型的复杂程度、浇冒口系统、浇口形状等有关。 (1) 流动性 流动性是指合金液体充填铸型的能力。流动性的大小决定合金能否铸造复杂的铸件。在铝合金中共晶合金的流动性最好。 影响流动性的因素很多,主要是成分、温度以及合金液体中存在金属氧化物、金属化合物及其他污染物的固相颗粒,但外在的根本因素为浇注温度及浇注压力(俗称浇注压头)的高低。 (2) 收缩性 收缩性是铸造铝合金的主要特征之一。一般讲,合金从液体浇注到凝固,直至冷到室温,共分为三个阶段,分别为液态收缩、凝固收缩和固态收缩。合金的收缩性对铸件质量有决定性的影响,它影响着铸件的缩孔大小、应力的产生、裂纹的形成及尺寸的变化。通常铸件收缩又分为体收缩和线收缩,在实际生产中一般应用线收缩来衡量合金的收缩性。 铝合金收缩大小,通常以百分数来表示,称为收缩率。 ①体收缩 体收缩包括液体收缩与凝固收缩。 铸造合金液从浇注到凝固,在最后凝固的地方会出现宏观或显微收缩,这种因收缩引起的宏观缩孔肉眼可见,并分为集中缩孔和分散性缩孔。集中缩孔的孔径大而集中,并分布在铸件顶部或截面厚大的热节处。分散性缩孔形貌分散而细小,大部分分布在铸件轴心和热节部位。显微缩孔肉眼难以看到,显微缩孔大部分分布在晶界下或树枝晶的枝晶间。 缩孔和疏松是铸件的主要缺陷之一,产生的原因是液态收缩大于固态收缩。生产中发现,铸造铝合金凝固范围越小,越易形成集中缩孔,凝固范围越宽,越易形成分散性缩孔,因此,在设计中必须使铸造铝合金符合顺序凝固原则,即铸件在液态到凝固期间的体收缩应得到合金液的补充,是缩孔和疏松集中在铸件外部冒口中。对易产生分散疏松的铝合金铸件,冒口设置数量比集中缩孔要多,并在易产生疏松处设置冷铁,加大局部冷却速度,使其同时或快速凝固。 ②线收缩 线收缩大小将直接影响铸件的质量。线收缩越大,铝铸件产生裂纹与应力的趋向也越大;冷却后铸件尺寸及形状变化也越大。 对于不同的铸造铝合金有不同的铸造收缩率,即使同一合金,铸件不同,收缩率也不同,在同一铸件上,其长、宽、高的收缩率也不同。应根据具体情况而定。
铝合金凝固组织的细化方法和机理概述
qiyekejiyufazhan 目前,铝型制品在工业中的需求量逐渐增加,因为铸造铝合金的密度比铸铁和铸钢小,比强度较高,熔点低,液态流动性能良好。在承受相同载荷条件下,采用铸造铝合金可以减轻设备重量,所以在现代航天航空工业及动力设备和交通运输设备制造中,铸造铝合金得到广泛应用。 人们在研究中发现,细化晶粒是改善金属材料性能最有效、最直接的方法,孕育是铸造金属晶粒细化的重要手段。传统的孕育处理方法是在液态金属中加入孕育剂或变质剂,通过试剂与金属液发生反应有的生成了异质形核的核心,这种反应增加了金属的形核率,同时部分试剂分布于晶界处,使晶核难以继续长大,以实现细化晶粒的目的。但这种传统的处理方法有一定缺陷:存在污染并且孕育处理时效产生。 细化晶粒是改善铝合金质量的重要方法,为了获得铸造金属最佳性能,需要把晶粒控制为细小均匀的等轴晶。对此,可以采用多种方法进行晶粒细化,包括机械物理细化晶粒法、物理场细化晶粒法、化学细化晶粒法。 1机械物理细化晶粒法 实验证明,金属的晶粒尺寸与晶粒成核速率和晶粒长大速率密切相关。为了获得细晶粒尺寸的金属,需要控制成核率大于晶粒尺寸,相反,将获得粗晶粒金属。相关实验还表明,过冷度会影响晶粒的成核速率和晶核的生长速率,成核速率和生长速率随过冷度的增加而增加。如果过冷度持续增大到一定程度,晶核的增长速度将小于晶粒的形核率,此时会出现明显的细化晶粒作用。 在铸造铝合金制备的浇注和结晶过程中,采用机械物理(如机械振动、机械搅拌)是一种细化晶粒的方法。机械物理(振动和搅拌)为液态铝合金提供了充足的能量,增加了成核能力和晶粒的成核速率。同时,结晶晶体受到机械物理(振动和搅拌)产生的对流冲击的影响。在这种作用下,晶体被破坏,破碎的晶体形成新的晶核。可见,晶粒细化是由成核速率 的增加而产生的。机械振动和机械搅拌是较为传统的两种方法,在工业生产中应用较广。但是,由于其操作控制具有一定难度,人为影响因素比较大,因此在铸造铝合金中,尤其是在制备高品质的铝材工业生产中存在很大缺陷。 2物理场细化晶粒法 对金属凝固组织施加物理场的科学研究在20世纪30年代首先被提及,但当时科学技术水平有限,无法支持物理场对晶粒细化作用的科学研究。直到20世纪末,全球科学技术水平得到飞速发展,使得人们可以有效地制备超声波、电磁场和大功率电流等物理场。就目前来看,物理场可以有效地控制晶粒的尺寸,达到细化晶粒的作用,使金属产品的质量得到明显改善。现阶段最主要的3种物理场细化晶粒的方法包括电流方向、磁场方向、超声波方向。 2.1电流方向 20世纪60年代初期,W.GPFANN 等首先研究了电场作用下的传输行为。1987年,MelTon.C.Fleming 研究发现,采用高压电场对液态金属进行大电流放电处理,金属的组织明显细化,得到具有光滑表面的准球状或球状的晶粒形貌。顾根达在实验中也发现,在电流小于750A 、电压小于10kV 的作用下,铸态金属组织得到细化。1996年,Li Hui 等人研究了Al-Si 亚共晶铝合金的组织结构。实验结果表明,亚共晶铝合金的伸长率和拉伸强度在电流处理后明显改善。初级a-Al 逐渐从粗树状枝上细化,最终形成粒状形态。 目前,在电场对铝及合金晶粒细化的影响领域,其细化机理有如下两种看法:1〇在铝熔体中存在着原子集团,对铝熔体施加电场后,迁移作用会产生,促使原子集团发生移动,在移动过程中原子集团势必会发生摩擦。此外,电场还削弱了原子团的电子云,从而有效地降低了电子云的屏蔽效应。因此,在这种电场力和摩擦力的交互影响下,原子集团破碎成一个个更 【作者简介】徐博聪,男,辽宁辽阳人,硕士,辽宁省机电工程学校讲师,研究方向:焊接技术与应用金、属熔炼技术与应用。 铝合金凝固组织的细化方法和机理概述 徐博聪 (辽宁省机电工程学校,辽宁辽阳111000) 【摘要】铸造铝合金比铸铁和铸钢密度小,具有比强度较高、熔点低、流动性能好的特 点。铝合金的需求随着工业生产的增加而增加。为了提高铝合金的应用范围,提高铝合金的强度是一个重要课题。目前,晶粒细化是提高工业省份铸造铝合金性能的最直接也是最经济的方式。文章介绍了3种铝合金凝固组织的细化方法和机理:机械物理细化晶粒法、物理场细化晶粒法、化学细化晶粒法。【关键词】铝合金;凝固组织;晶粒细化【中图分类号】TG11【文献标识码】A 【文章编号】1674-0688(2018)08-0077-02 77
快速凝固技术的应用
快速凝固技术的应用 机103班田玉之 1010012084 摘要:快速凝固指的是在比常规工艺过程中快得多的冷却速度下,金属或合金以极快的速度从液态转变为固态的过程。快速凝固技术得到的合金与常规合金有着不同的组织和结构特征,对材料科学和其它学科的理论研究以及开展实际生产应用起了重要的作用。 Rapid solidification refers to than conventional process much faster cooling rate, metal or alloy in order to speed the transition from the liquid state to the solid state process. Rapid solidification technology of alloy and the conventional alloy has different organization and structure features, materials science and other disciplines of theoretical research and practical application of production 关键词:快速凝固;镁合金;铝合金 引言:随着科学技术的发展,对金属凝固技术的重视和深入研究, 形成了许多种控制凝固组织的方法, 其中快速凝固已成为一种具有挖掘金属材料潜在性能与发展前景的开发新材料的重要手段, 同时也成了凝固过程研究的一个特殊领域。过去对凝固过程的模拟考虑了在熔融状态下的热传导和凝固过程潜热的释放, 不考虑金属在型腔内必然存在的流动以及金属在凝固过程中存在的流动。目前快速凝固技术作为一种研制新型合金材料的技术已开始研究了合金在凝固时的各种组织形态的变化以及如何控制才能得到符合实际生活、生产要求的合金。 各种应用: 一快速凝固技术在镁合金中的应用 镁合金是所有结构金属中最轻的一种, 具有比重小, 比强度、比刚度高,耐冲击等一系列优点, 在汽车、电子电器、航空航天等领域具有广阔的应用前景, 但镁合金的加工成形性能及耐蚀性能较差, 大大限制了其发展. 目前, 国内在 高性能镁合金的管、棒、板、型材及一些结构件方面基本上还是空白, 而传统的