电镀的前处理

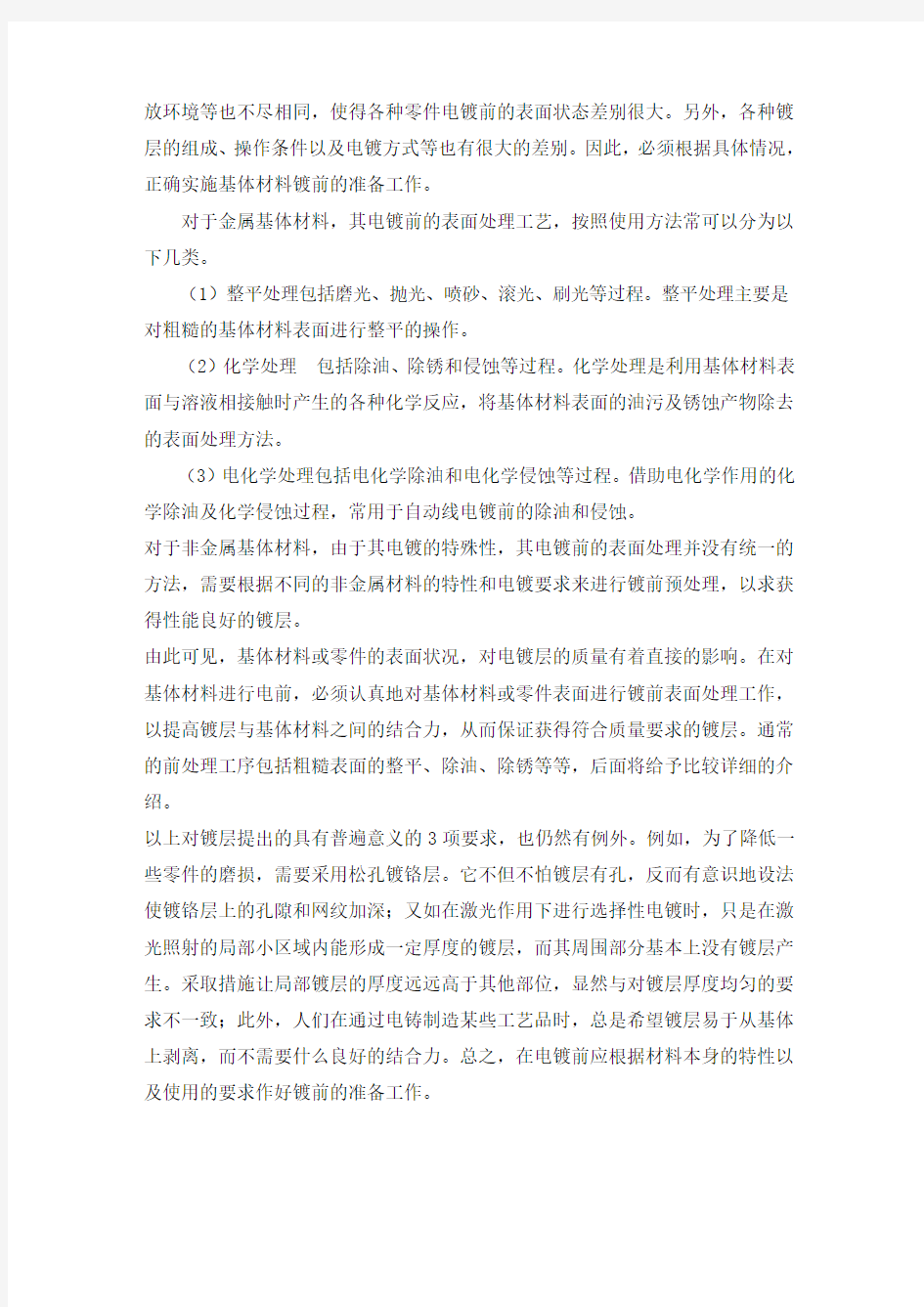
电镀的前处理
电镀的前处理是电镀工艺中非常关键的一步,基体材料表面处理的好坏直接影响到镀层的质量,所以应给予电镀前处理相当的重视。本章分析了表面状态影响镀层质量的各种因素,详细阐述了电镀前处理的各种基本方法,并针对不同的基体材料和不同的电镀层,列举了一系列电镀前处理的工艺条件。
概述
1.电镀前处理的意义
对于通过电镀形成的金属镀层,不管品种和性质如何,人们对它们都有一些共同的要求,这些要求大致有以下几方面。
(1)镀层应结构致密、表面光滑平整,有的甚至要求具有一定的光亮度。致密无孔的镀层,不仅有利于防护基体金属免遭腐蚀,有可能在较长的时间内保持着镀层的良好装饰性外观,而且可以更有效地发挥镀层所具有的各种功能。
(2)在基体的不同部位上,镀层厚度要均匀,或者是基体表面各部位镀层厚度的差异要尽可能地小。为了保护制品及零件的使用寿命,这一要求十分重要,否则,在遭受腐蚀或磨损时,镀层最薄的部位会首先露出基体材料,致使整个制品和零件提前报废。
(3)镀层与基体材料间的结合必须是牢固的,不允许出现镀层起皮、鼓泡等现象。与基体结合不牢固的镀层,根本没有任何的使用价值,即使镀层并没有从基体材料上脱落,在使用过程中这种镀层的性能也是很靠不住的。
为了满足镀层上述3层最主要的基本要求,必须对被镀的制品及零件表面的镀前处理工序给予足够的重视。
在电镀产品实际的质量检验中,常常会发现局部镀层脱落、鼓泡或花斑以及局部无镀层等现象,究其原因,大多数情况下都是由于基体材料镀前处理不良造成的。电镀是发生在被镀基体材料与镀液相接触的界面间的电化学反应。为了确保电镀层的质量,与镀液相接触的被镀零件表面必须是基体材料本身。也就是说被镀零件表面不能含任何油脂等污物,也不能有其他锈蚀产物膜层存在,同时零件表面应该力求平整光滑。这样,基体材料表面才能很好地被镀液所润湿,镀出的金属才能与平整光滑的基体材料表面牢固结合。可见,电镀前金属基体材料表面的前处理准备工作的重要性是毋庸置疑的。由于基体的材料各类繁多,加工过程及存
放环境等也不尽相同,使得各种零件电镀前的表面状态差别很大。另外,各种镀层的组成、操作条件以及电镀方式等也有很大的差别。因此,必须根据具体情况,正确实施基体材料镀前的准备工作。
对于金属基体材料,其电镀前的表面处理工艺,按照使用方法常可以分为以下几类。
(1)整平处理包括磨光、抛光、喷砂、滚光、刷光等过程。整平处理主要是对粗糙的基体材料表面进行整平的操作。
(2)化学处理包括除油、除锈和侵蚀等过程。化学处理是利用基体材料表面与溶液相接触时产生的各种化学反应,将基体材料表面的油污及锈蚀产物除去的表面处理方法。
(3)电化学处理包括电化学除油和电化学侵蚀等过程。借助电化学作用的化学除油及化学侵蚀过程,常用于自动线电镀前的除油和侵蚀。
对于非金属基体材料,由于其电镀的特殊性,其电镀前的表面处理并没有统一的方法,需要根据不同的非金属材料的特性和电镀要求来进行镀前预处理,以求获得性能良好的镀层。
由此可见,基体材料或零件的表面状况,对电镀层的质量有着直接的影响。在对基体材料进行电前,必须认真地对基体材料或零件表面进行镀前表面处理工作,以提高镀层与基体材料之间的结合力,从而保证获得符合质量要求的镀层。通常的前处理工序包括粗糙表面的整平、除油、除锈等等,后面将给予比较详细的介绍。
以上对镀层提出的具有普遍意义的3项要求,也仍然有例外。例如,为了降低一些零件的磨损,需要采用松孔镀铬层。它不但不怕镀层有孔,反而有意识地设法使镀铬层上的孔隙和网纹加深;又如在激光作用下进行选择性电镀时,只是在激光照射的局部小区域内能形成一定厚度的镀层,而其周围部分基本上没有镀层产生。采取措施让局部镀层的厚度远远高于其他部位,显然与对镀层厚度均匀的要求不一致;此外,人们在通过电铸制造某些工艺品时,总是希望镀层易于从基体上剥离,而不需要什么良好的结合力。总之,在电镀前应根据材料本身的特性以及使用的要求作好镀前的准备工作。
阳极氧化设备铝氧化设备https://www.360docs.net/doc/8610034175.html, skfjdjv
电镀前处理工艺
电镀前处理工艺的内容 镀前〔后)处理 镀前(后)处理工艺包括表面整理、除油、浸蚀。表面整理一般分为的磨光、抛光、滚光、刷光、喷砂处理等。 磨光是为了提高零件的表面平整度,除去零件的表面宏观缺陷、腐蚀痕、划痕、毛刺、焊缝、砂眼、气泡等,用以提高电镀质量。磨光适用于一切金属材料的镀前处理,磨光的效果取决于磨料、磨光轮的刚性和轮子的旋转速度。磨光前的零件、尤其是机械加工的零件应符合工艺规程要求,必要时可按标准样板检查,磨光前的酸浸蚀不允许有残留氧化皮、过腐蚀、变形、螺纹损伤等。 抛光一般用于镀后处理,也叫用于表面粗糙度要求较高的零件的镀前处理,使制品获得装饰性外观,提高制品的耐蚀性。抛光般在抛光机上进行。 滚光适用于大批量小零件的处理,可全部或部分替代镀前磨光、抛光、刷光工序,滚光效果与滚筒的形状、尺寸、转速、滚筒中磨料及溶液性质、零件种类及形状有关。 刷光是用金属丝轮或金属丝刷在刷光机上或用手工进行刷光的一种表面整理过程,它可全部或部分替代滚光处理。 喷砂是为除去零件表面的毛刺、氧化皮、铸件表面上的熔渣等杂质、焊渣等。喷砂的效果取决于砂粒的粒度和压缩空气的压力的大小。 除油工艺包括机械除油、溶剂除油、化学除油、电解除油、是为了除去零件表面的油污,以保证镀层与基体的附着强度。 机械除油一般采用滚简除油和擦拭除油。滚筒除油适用于小件大批量除油,擦拭除油适用于大型复杂件的除油。 溶剂除油是将零件浸于有机溶剂(或蒸汽)中,使油污溶于溶剂中。常用的有机溶剂有煤油、汽油、苯类、酮类及某些氯化烷烃、烯烃等。溶剂除油适应于所有金属零件的除油,特别适应于粉末冶金零件如轴瓦等。 化学除油是利用碱液的皂化作用和表面活性剂的乳化作用除去零件表面油污的过程,适用于所有零件.化学除油的效果取决于除油液的碱度和表面活性刘的乳化性能。 电化学除油是将零件挂在碱性电解液的阴极或阳极上,利用电化学极化作用及电极表面析出气体对油膜的撕裂作用和气泡的机械搅拌作用除去零件表面油污的过程。电化学除油的效果超过化学除油,是电镀前的最后除油工序.电化学除油适用于所有零件的除油。 浸蚀工艺包括弱浸蚀和强浸蚀,其目的是为了提高零件的表面活性。强浸蚀是为了除去零件
电镀工艺流程资料
电镀工艺流程资料(一) 一、名词定义: 1.1电镀:利用电解的方法使金属或合金沉积在工件表面,以形成 均匀、致密、结合力良好的金属层的过程叫电镀。 1.2镀液的分散能力: 能使镀层金属在工件凸凹不平的表面上均匀沉积的能力,叫做镀液的分散能力。换名话说,分散能力是指溶液所具有的使镀件表面镀层厚度均匀分布的能力,也叫均镀能力。 1.3镀液的覆盖能力:使镀件深凹处镀上镀层的能力叫覆盖能力, 或叫深镀能力,是用来说明电镀溶液使镀层在工件表面完整分布的一个概念。 1.4镀液的电力线:电镀溶液中正负离子在外电场作用下定向移动 的轨道,叫电力线。 1.5尖端效应:在工件或极板的边缘和尖端,往往聚集着较多的电 力线,这种现象叫尖端效应或边缘效应。 1.6电流密度:在电镀生产中,常把工件表面单位面积内通过的电 流叫电流密度,通常用安培/分米2作为度量单位 二.镀铜的作用及细步流程介绍: 2.1.1镀铜的基本作用: 2.1.1提供足够之电流负载能力; 2.1.2提供不同层线路间足够之电性导通; 2.1.3对零件提供足够稳定之附著(上锡)面; 2.1.4对SMOBC提供良好之外观。 2.1.2.镀铜的细步流程: 2.1.2.1ⅠCu流程:上料→酸浸(1)→酸浸(2)→镀铜→双水洗 →抗氧化→水洗→下料→剥挂架→双水洗→上料 2.1.2.2ⅡCu流程:上料→清洁剂→双水洗→微蚀→双水洗→酸浸 →镀铜→双水洗→(以下是镀锡流程) 2.1.3镀铜相关设备的介绍: 2.1. 3.1槽体:一般都使用工程塑胶槽,或包覆材料槽(Lined tank),但仍须注意应用之考虑。 a.材质的匹配性(耐温、耐酸碱状况等)。 b.机械结构:材料强度与补强设计,循环过滤之入/排口吸清理维 护设计等等。 c.阴、阳极间之距离空间(一般挂架镀铜最少6英寸以上)。 d.预行Leaching之操作步骤与条件。 2.1. 3.2温度控制与加热:镀槽之控制温度依添加特性/镀槽之性能 需求而异。一般而言操作温度与操作电流密度呈正向关系,但无论高温或低温操作,有机添加剂必定有分解问题。一般而言,不容许任何局部区域达60℃以上。在材质上,则须对耐腐蚀性进行了解,避免超出特性极限,对镀铜而言,石英及铁弗龙都是很适合的材料。
电镀车间废气处理工艺方案
电镀工艺废气处理工程设计方案二零一五年五月
目录 1、概述 (2) 1.1 项目概况 (2) 1.2 设计依据 (2) 1.3 设计指标 (2) 1.4 设计范围 (3) 2、处理工艺 (3) 3、治理工程内容 (5) 3.1 吸风系统 (5) 3.2 吸收系统 (5) 4、投资估算 (6) 5、废水排放量 (7)
1、概述 1.1 项目概况 电镀生产工艺过程中将产生含氰废气、含铬废气,以及酸洗过程中将产生酸雾。电镀槽为含氰废气:B×L×H=0.8×2×0.6m;含铬废气:B ×L×H=1×2×0.6m;酸洗废气拟放置于一个小房内B×L×H=2×4×4m,有酸洗和退镀工艺(硝酸、硫酸、盐酸)。这些废气的产生不仅影响生产车间的工作环境,还会污染周边的环境,因此,根据国家环保相关要求,需对这些污染物进行处理。 为此,我方经过现场实地考察并参考以往的成功工程经验,确定含氰废气采用次氯酸钠吸收;含铬废气采用焦亚硫酸钠吸收;酸洗废气采用氢氧化钠吸收,产生的废水均进入电镀废水处理工艺中。根据此工艺我方编制了以下处理方案,供环保部门审查和厂方选用。 1.2 设计依据 (1)厂方提供的有关技术资料; (2)GB16297-1996《大气污染物综合排放标准》。 1.3 设计指标 本工程设计指标参照GB16297-1996《大气污染物综合排放标准》中三级标准,设计污染物排放指标限值为: 铬酸雾最高允许排放浓度0.07mg/m3,20m高排气筒最高允许排放速率为0.20kg/h。
氰化氢最高允许排放浓度1.9mg/m3,25m高排气筒最高允许排放速率为0.24kg/h。 氯化氢最高允许排放浓度100mg/m3,20m高排气筒最高允许排放速率为0.65kg/h。 硫酸雾最高允许排放浓度:45mg/m3,20m高排气筒最高允许排放速率为3.9kg/h。 根据以上污染物排放浓度要求,确定本处理方案的处理效率为:1)酸洗废气:≥90%; 2)含氰废气:≥85%; 3)含铬废气:≥95%。 1.4 设计范围 本方案设计范围为自吸风罩至吸收塔出口之间的废气处理工艺及相应配套的设备选型。 2、处理工艺 根据各废气的主要特点,确定本次电镀废气处理方法为:含氰废气采用次氯酸钠吸收;含铬废气采用焦亚硫酸钠吸收;酸洗废气采用氢氧化钠吸收。其反应原理为: 2NaClO + CN-→CO2+ N2+ 2NaCl(1) 2NaOH + H2SO4→Na2SO4+ H2O(2) NaOH + HCl →NaCl + H2O(3) 2NaOH + NO2→2NaNO2+ H2O(4)
锌合金电镀及退镀工艺
锌合金电镀及退镀工艺 锌合金前处理的一般工序,包括研磨/抛光、除油、超声波除蜡等。介绍了常见的锌合金电镀铜–镍–铬及镀金的工艺,以及某公司在锌合金件上电镀仿金、铬、古铜、黄古铜、红古铜、珍珠镍等工艺的流程及镀液配方。给出了锌合金上铜、镍、铬镀层的退除方法。 1·前言 锌铝压铸件是一种以锌为主要成分的压铸零件。这种零件表面有一层很致密的表层,里面则是疏散多孔结构,又是活泼的两性金属。所以,只有采用适当的前处理方法和电镀工艺,才能确保锌合金上的电镀层有良好的附着力,达到合格品的要求。 2·电镀用锌合金材料[1] 电镀常用的锌合金材料为ZA4–1,其主要成分为:铝3。5%~4。5%,铜0.75%~1。25%,镁0。03%~0.08%,余量为锌,杂质总和≤0。2%。而925牌号的锌合金含铜量高,也易于电镀.通常,锌合金的密度为6.4~6.5g/cm3,若密度〈6.4g/cm3,电镀后易发生起泡和麻点.总之,选材时务必严格把关。另外,压铸时模具必须设计合理,避免给电镀带来难以克服的缺陷(如麻点)。 3·镀前处理 3。1研磨、抛光 切勿破坏致密表层,若暴露出内层多孔疏松结构,则无法获得结合力良好的镀层。 3。2除油 锌合金对酸、碱敏感,选择去油剂时应有所要求。常用E88锌合金电解除油粉或SS浸洗除油粉(安美特公司产品)。 3。3超声波除蜡 高档产品常选用“开宁”公司的锌合金除蜡水。 3.4阴极电解除油 自配的除油剂必须加入适量的金属配位剂,防止金属沉积到零件表面,从而避免发花。阴极电解除油时要采用循环过滤。 3。5工艺流程 化学除油─超声波除油─电解除油─浸蚀活化(硫酸5~10mL/L+氢氟酸10~20mL/L, pH控制在0。5~1。5,视工件外形复杂性而定;室温,10~30s至刚开始全面反应产生气泡后立即取出零件,然后彻底清洗干净)。 3.6热浓硫酸除蜡除油 为减少工序和时间,在投资少、见效快,操作方便、稳定的条件下,锌铸件经磨抛光后(零件必须干燥!)采用浓硫酸加热脱水除油;而锌合金铸件在热的浓硫酸中除油快,又不会受腐蚀。热浓硫酸除蜡除油配方及其操作条件为:80~90℃,3~5min。 4·某电镀公司锌合金汽配件电镀工艺流程 锌合金电镀半自动线上的前处理部分(保证工件表面清洁)分为上挂、除蜡、阴阳极电解除油、水洗等9个工序,电镀部分包括弱浸蚀、水洗、预浸、碱铜、焦铜、酸铜、水洗、半亮镍、亮镍、镍封、珍珠镍、镀铬、回收等37个工序,电镀后处理部分为还原去Cr(VI)、水洗、热水洗、下挂和烘干这5个工序。 5·锌合金电镀铜–镍–铬的工艺流程 超声波除蜡─热水洗(75℃)─化学除油─热水洗─三级逆流清洗─阴极电解除油─热水洗─三级逆流清洗─酸浸蚀(体积分数为2%的硫酸+体积分数为2%的氢氟酸,室温,析出气泡后停留2s)─三级逆流清洗─预浸(氰化钠50g/L,室温,10s)─氰化镀铜(氰化亚铜30 g/L、氰化钠45g/L、酒石酸钾钠20g/L,50℃,3min,Jk=1。0A/dm2)─回收─三级逆流清洗─酸活化(体积分数为10%的硫酸,室温,0.5min;下同)─三级逆流清洗─焦磷酸盐镀铜(焦磷酸铜65g/L、焦磷酸钾300g/L、氨水3mL/L、光亮剂适量,56℃,15min,Jk= 2A/dm2,pH=8.8)─回收─三级逆流清洗─酸活化─三级逆流清洗─硫酸盐镀铜(硫酸铜200g/L、硫酸60g/L、氯离子60mg/L、光亮剂适量,23℃,15min,Jk=3。5A/dm2)─回收─三级逆流清洗─酸活化─三级逆流清洗─硫酸盐镀镍(硫酸镍200g/L、氯化镍60g/L、硼酸50g/L、光亮剂适量,50℃,10min,pH=4。6,Jk=4A/dm2)─回收─三级逆
塑料制品电镀前的表面处理工艺介绍
https://www.360docs.net/doc/8610034175.html,/ https://www.360docs.net/doc/8610034175.html,/ 塑料制品电镀前的表面处理工艺介绍 塑料制品的表面处理主要包括涂层被覆处理和镀层被覆处理。一般塑料的结晶度较大,极性较小或无极性,表面能低,这会影响涂层被覆的附着力。由于塑料是一种不导电的绝缘体,因此不能按一股电镀工艺规范直接在塑料表面进行镀层被覆,所以在表面处理之前,应进行必要的前处理,以提高涂层被覆的结合力和为镀层被覆提供具有良好结合力的导电底层。 1.涂层被覆的前处理前处理包括塑料表面的除油处理,即清洗表面的油污和脱模剂,以及塑料表面的活化处理,目的是提高涂层被覆的附着力。 (1)塑料制品的除油。与金属制品表面除油类似,塑料制品除油可用有机溶剂清洗或用含表面活性剂的碱性水溶液除油。有机溶剂除油适用于从塑料表面清洗石蜡、蜂蜡、脂肪和其他有机性污垢,所用的有机溶剂应对塑料不溶解、不溶胀、不龟裂,其本身沸点低,易挥发,无毒且不燃。 碱性水溶液适用于耐碱塑料的除油。该溶液中含有苛性钠、碱性盐以及各种表面活性物质。最常用的表面活性物质为OP系列,即烷基苯酚聚氧乙烯醚,它不会形成泡沫,也不残留在塑料表面上。 (2)塑料制品表面的活化。这种活化是为了提高塑料的表面能,也即在塑料表面生成一些极性基或加以粗化,以使涂料更易润湿和吸附于制件表面。表面活化处理的方法很多,如化学品氧化法、火焰氧化法、溶剂蒸气浸蚀法和电晕放电氧化法等。其中最广泛使用的是化学晶氧化处理法,此法常用的是铬酸处理液,其典型配方为重铬酸钾4.5%,水8.0%,浓硫酸(96%以上)87.5%。 有的塑料制品,如聚苯乙烯及ABS塑料等,未进行化学品氧化处理时也可直接进行涂层被覆。为了获得高质量的涂层被覆,也有用化学品氧化处理的,如ABS塑料在脱脂后,可采用较稀的铬酸处理液浸蚀,其典型的处理配方为铬酸420g/L,硫酸(比重1.83)200ml/L。典型的处理工艺为65℃70℃/5min10min,水洗净,干燥。 https://www.360docs.net/doc/8610034175.html,/ https://www.360docs.net/doc/8610034175.html,/ https://www.360docs.net/doc/8610034175.html,/
现代电镀后处理中的清洗操作工艺环节介绍
现代电镀后处理中的清洗操作工艺环节介绍 从电镀槽中镀出的合格产品,若不清洗掉零件夹带的镀液,有时会使镀层泛色或出现锈点、白点,最后仍不能得到满意的产品。特别是镀锌、镀镉及它们的合金,若镀后清洗不彻底,不把渗入基体或镀层中的溶液洗净,那么在产品贮存期间会产生泛点(或渗点)。如果加强镀后清洗,用冷水、热水交替处理,就可以防止产生这类故障。 一、常用的几种清洗方法①清洗有单级浸洗和多级浸洗,按浸洗的组织方法有多级逆流漂洗和间歇逆流漂洗。为了强化浸洗效果,浸洗时加有零件摆动、空气搅拌、泵强制循环,还有超声波强化浸洗。②与浸洗相对应的是喷淋,喷淋有连续喷淋和间歇喷淋,有定式喷淋和扫描式喷淋,有全喷和顶喷。③浸洗加顶喷也是常用的方法,也有先浸洗后喷淋或先喷淋后浸洗的。 二、清洗操作要求①镀件与清洗水要加强接触。镀件进入水槽之后要上下、左右抖动,使镀件与清洗水充分接触,.以达到清洗的应有效果。②不要忽视挂钩的清洗。当清洗槽深度较浅(逆流清洗槽的前几个槽深度更浅),带挂具清洗时挂具上部浸不到水面以下,在卸挂、干燥时,挂具上的溶液会污染镀件,引起镀层发花,出现斑点。此时可用水龙头冲洗,或用水勺浇一下未清洗到的挂具上部,以避免这种故障。③镀件清洗时速度不宜太快,最好在挂具提出清洗槽后能在槽上方暂停片刻。以减少被带入下
一个清洗槽的镀件表面所黏附的酸、碱污水。④清洗时要防止镀(涂)层遭到机械损伤,否则会严重影响镀(涂)层的完整性,失去了镀(涂)层应有的防护和装饰功能。为此,操作时一次数量不宜过多,且要轻拿、轻放。⑤对于盲孔、狭缝中镀液的辅助除去,一是甩除法,即把难出水工件猛甩,积聚在这些部位的溶液即会甩出来,经清洗后再甩效果更好。 二是注水交换法,即采用医用注射器向盲孔、狭缝内注入清水,把隐藏在里面的污水驱逐出来,从而达到洁净的目的。 三、清洗对水质的要求①清洗水中不能含过多的钙镁离子,否则带入镀液后容易产生沉淀。②清洗水中不能含过多的铁离子,否则带人镀液后会使镀层发脆、发雾、起条纹或产生针孔。 ③清洗水中不能含过多的有机物,否则带入镀液会产生针孔或使镀层发脆、发雾、起条纹。④即使合格的清洗水,也要加入新水,否则越洗越脏,无法达到清洗目的。这时可用清洗水的污染极限来表述对清洗水的要求。一般,前处理后(脱脂和酸洗)的清洗水的污染极限是75010-4%,光亮电镀后的清洗水的污染极限是4010-4%,一般电镀后的清洗水的污染极限是(100~150)10—4%。⑤有不少工件的清洗水的要求是很高的。如航空工业中,铝阳极氧化要求用纯水清水才能人氧化槽,贵金属电镀前要用纯水洗,烘干前要用纯水洗。
汇祥电镀废气治理方案设计
标准文案 ——高要市金利汇祥金属表面处理 高要市金利汇祥金属表面处理 电镀废气处理工程 技术方案 市海珠羊城环保 市思创环保工程 2011 年05 月 设计单位:市海珠羊城环保
施工单位:市思创环保工程 审定:杜皓明 审核:荣中国 项目负责人:任桂平 设计人:何觉安 目录 1、概述 (2)
1.2 设计依据 (5) 1.3 设计指标 (5) 1.4 设计围 (5) 2、处理工艺 (5) 3、治理工程容 (8) 3.2 吸收系统 (9) 4、设备选型 (9) 5、动力设计 (10) 6、总图设计 (11) 7、工程投资预算 (12) 8、付款方式 (19) 9、售后服务 (19) 1、概述 1.1 项目概况 高要市金利汇祥金属表面处理位于市金利镇金盛工业区,是铝制品、化工等产
品专业生产加工的私营独资企业,公司拥有完整、科学的质量管理体系。诚信、实力和产品质量获得业界的认可。 通过现场勘查,工业园各车间废气处理各车间具体现状如下:
综合上述,各车间主要存在如下问题: 1、贵厂部分车间在电镀生产工艺过程中将产生大部分铬酸雾及氰化镀铜 的氰化氢废气只进行收集,没有单独回收处理; 2、车间的喷漆废气未进行处理直排(F车间已有设备,估计6月份投产); 3、部分车间酸雾收集系统效果不良、导致车间空气状况差; 4、由于厂区里面的各个车间买的酸雾塔基本都在在周边的商铺买的,没 有经过具体设计,导致了大风机配小塔、抽风效果不理想,处理效率 低下、处理工艺错误等后果;经过该塔处理后的废气极有可能不能达 标排放。 5、我公司所设计的酸雾塔及铬酸回收装置都是经过严格计算,并且经过 环保部门检测达标的合格产品,具有压力损失小,处理效率高,使用 寿命长等特点。 6、我公司所选用的设备及管道材质均为高于同类别,采用使用寿命长的 高等级板材。 这些废气的产生不仅影响生产车间的工作环境,还会污染周边的环境,因此,根据国家环保相关要求,需对这些污染物进行处理,处理后的电镀废气达到《电镀污染物排放标准》(GB21900-2008)。 为此,我方经过现场实地考察并参考以往的成功工程经验,确定氰化氢废气采用低阻力的高效离心净化塔配备硫酸亚铁溶液吸收处理;含铬酸雾废气采用微孔式铬酸回收器回收;氰化氢废气处理产生的废水排入电镀废水管网后,交由污水站统一处理。根据此工艺我方编制了以下处理方案,供厂方选用。
不锈钢电镀前处理工序浅析
不锈钢电镀前处理工序 浅析 Company Document number:WTUT-WT88Y-W8BBGB-BWYTT-19998
不锈钢电镀前处理工序浅析 现代电镀网9月28日讯: 不锈钢在空气中容易钝化,生成一种致密的钝化膜,该钝化膜具有很好的耐蚀性。随着工业技术的发展,不锈钢的应用扩展迅速,从而导致不锈钢上功能性电镀的需求不断增加。 不锈钢的难点集中在不锈钢的底层电镀上,而底层电镀的难点在于不锈钢的前处理。如果前处理不当,往往会导致镀层分层、起皮、脱落等现象。 专注于高精密、高难度金属表面处理12年的杰昌电镀厂表示:不锈钢电镀前处理的难点在于如何消除不锈钢表面的钝化层使不锈钢基材表面完全活化。 以下介绍不锈钢电镀前处理的主要工序: (1)有机溶液浸泡除油 部分不锈钢零件不能用电化学除油的方法除油,因为有的不锈钢零件经过电化学除油后,表面发乌发黑,即使用酸洗也不能使其表面变得光亮。为了不破坏不锈钢表面的光亮状态,先用工业汽油刷洗其表面的油污,清洗后再转入化学除油工序。 (2)化学除油 将不锈钢零件放入装有工业清洗剂的槽体中(温度一般为50-70℃),可以配有超声波以彻底除去零件表面的油污;除油时间控制为将表面油污除尽为止。 (3)酸洗 在不锈钢电镀前处理过程中,酸洗是必不可少的工序。因为酸洗既可以去除不锈钢表面的锈蚀物和钝化膜,使其表面的基体裸露,提高镀层的结合力。 (4)活化 活化的目的是去除不锈钢表面的氧化膜,使其表面活化,保证镀层与不锈钢基体有足够的附着力。活化过程有浸渍活化和阴极活化。经过试验显示,对不锈钢进行浸渍活化,使其表面的钝化膜迅速去除,再进行电化学预镀处理,快速生成一层镀层,使镀层与不锈钢的附着力大大提升。 (5)预镀 零件进入预镀槽后,先不要通电,停放2~3分钟后,再通电进行预镀处理。不锈钢表面氧化层的生成速率非常快,化学活化后,有可能在其表面生长一层氧化膜。因此,预镀时零件先在溶液中浸泡,让溶液中的盐酸对其表面进行又一次活化及零件在溶液中对镍离子的化学吸附过程后,再通电发生反应,生成一层薄镍层。 (6)预镀镍 不锈钢零件预镀后,不清洗立即放进预镀镍槽中进行电镀处理,这样才能保证镀层有好的附着力。预镀镍后用流动水清洗两遍再进行后续电镀。 不锈钢零件电镀前处理过程中,活化与预镀工序非常重要。采用化学活化与预镀的前处理方法去除不锈钢零件上的钝化膜,使其表面生成一层附着力很好的镀层,从而实现不锈钢基材上电镀多种金属。
浅谈电镀后处理脱水常见问题及解决方法
浅谈电镀后处理脱水常见问题及解决方法 电镀后的最后一道工序是脱水干燥。这道工序相对于前面各个工序来讲没有那么复杂与技术含量,在一般的人看来也就是过几格水而已,不算什么技术。如果不重视它,也许出现问题往往就在这道工序上,也要给予重视,不能忽视。一般表现出来的现象是工件由上到下出现一道水迹。一些形状复杂的工件,在其螺丝孔里残留的电镀液烘烤后缓慢散发出来,表现轻微的就流出一道污痕,表现严重的是周围镀层都被腐蚀掉(比如镀青铜),这样的工件一般是不合格的,达不到客人要求,只能作返工处理,所以处理不好,既耽误货期,又浪费大量人力物力。对于这个问题的解决,我们一般采取的方法有一下几个方法: 一)采用超纯水电镀工件清洗干净与否,最重要的莫过于需要水质洁净,如果后处理水质不干净,水的硬度高、含有大量盐分、微生物等,清洗后的工件表面状况会非常糟糕,如出现工件颜色变色,大量污迹等。水质问题一般工厂都能做到,都是利用反渗透+离子交换装置解决,经过处理后水的电导率一般在5Ω/cm3-以下,有的甚至更低,电导率越低越好,使用一段时间后电导率升高则需要对离子交换进行再生处理。 二)增加辅助装置一些复杂的工件一般可以辅助一些吹、吸设备,利用压缩空气吹扫,可以轻松吹除一些挂得比较牢固的工件表面水珠,特别是光面比较大的工件效果特佳。对一些仅挂钩在挂具上的工件则只能采取吸取的方法。如果还采取吹扫则工件都被吹掉,弄
花。这种方法对一些有孔位工件尤为适用,比如讲吸尘器改装前面吸嘴,可以很好解决一些藏水工件。 三)加温对漂水过程中最后两槽水适当进行加温,一般讲温度控制在60度左右,但温度不宜过高,过高的温度会使水分蒸发越快,提取操作也不安全。温度提高水的表面张力降低,一方面加速水脱离工件表面,另外带着一定热量的工件在进入隧道炉干燥时有一定帮助作用,可以加快温度的提升,在热风的吹扫下水珠很容易脱离工件表面。 四)采取脱水油这个方法在以前使用得比较多,例如采取多级无水乙醇脱水,脱水防锈油等,这个方法对电镀后处理工件清洗不适用,在此不作讨论。 五)添加脱水剂采取以上方法可以对一些简单的电镀工件表面水珠轻松去除,但是对于一些复杂的工件则同样表现得不得力,上述方法增加很多的人力物力,如果在漂水槽中添加一点脱水剂,则对后面的清洗效果有很大的提升。脱水剂是由多种表面活性剂、缓蚀剂等复合而成的。它的最大特点就是能够快速在工件表面形成一层疏水膜,将大量水置换掉并起防变色作用,从而大大减轻后面吹、吸等方法的劳动量。使用脱水剂的最大弱项是:如果使用不当或使用劣质脱水剂,一些工件经过喷力架,力架与工件表面的结合力低,力架硬度大大降低,失去保护作用,稍经过摩擦、刮划,力架很容易脱掉,这也是不可取的。只有采取质量良好的脱水剂则可避免出现此类问题。
电镀废气的处理
电镀废气的处理 电镀的定义 利用电解的方式使金属或合金沉积在工件表面,以形成致密,均匀结合力良好的金属层的过程。 电镀工艺的用途 防腐蚀、防护装饰、抗磨损、电性能(根据零件要求,提供导电或绝缘性能的镀层)、工艺要求 电镀生产工艺过程中产生含氰废气,含铬废气。以及酸洗过程中将产生酸雾。这些废气不仅影响车间的工作环境,还污染周边的环境。需要对这些废气进行处理。 含氰废气采用次氯酸的吸收,含铬废气采用焦亚硫酸钠的吸收,酸洗废气采用氢氧化钠的吸收。 工艺流程 吸收处理工艺为:车间产生的废液经吸风罩吸收汇集到各自吸收塔中,与塔中吸收液逆流接触后,废气均被吸收袭来,净化后的气体在净塔中初五装置除雾排空,吸收液循环使用。 电镀废气的种类、产生及危害 含尘废气 由于喷砂、抛光等工序产生的,含有金属氧化物及纤维性粉尘等。污染空气及对从业者咽喉、肺造成伤害。 酸性废气 由于采用盐酸、硫酸等酸性物质进行酸洗过程中产生的。具有极
强的刺激性气味。腐蚀厂房设备,污染大气,严重的可能造成酸雨。 碱性废气 电镀过程中使用氢氧化钠、碳酸钠及磷酸钠等碱性物质,加热工艺过程中碱性气体。对工作者咽喉、气管、肺部很有很大的伤害。 含铬废气 有很强的毒性和腐蚀性,可引起鼻部严重病变,严重的可致癌。 含氰废气 氰化物与酸反应能够产生毒性更强的氰化氢气体,吸入微量可致人死亡。 氮氧化物废气 酸洗,抛光等工艺过程中所产生的酸性废气。对神经系统造成严重的损伤 电镀废气的抑制 酸雾的抑制,采用高效合理的酸洗工艺,添加酸雾抑制剂。 碱雾的抑制,采用低温化学除油工艺,添加碱雾抑制剂。 铬雾的抑制,采用低温低浓度镀铬新工艺,添加铬雾抑制剂。 蛋汤话务废气抑制,采用不加硝酸的化学处理新工艺,抑制氮氧化物气体的产生。 氮氧化物废气抑制 化学氧化法 在溶液中加入双氧水和高锰酸钾等强氧化剂,可将亚硝酸氧化成硝酸,抑制氮氧化物的产生。
电镀前处理主要环节作用和目的
电镀前处理主要环节作用和机理 一、脱脂 1、作用:除去素材表面脂肪类油漬和其他有机性污垢,以获得良好電镀效果,并防止 对后序工序的污染。 2、温度管控范围:40~60℃标准:50℃ 3、作用机理: 借助于溶液的皂化与乳化作用以达到去除油污的目的。 动植物油的去除主要是依据皂化反应。所谓皂化,就是油脂与脱脂液中的碱起化学反应生成肥皂的过程。使原来不溶于水的油脂,分解成了可溶于水的肥皂和甘油,从而被除去。 4.注意事項: 1).超音波振荡有作于增强脱脂效果。 2).除油粉浓度不足时,无法达到脱脂效果;浓度过高时,带出损耗较大,成本增高,需控制在合理范围内。 3).温度不足时,除油效果不佳,提高温度可以降低溶液与油脂的表面张力,加速除油效果;温度过高时,素材易发生形变。作业时需严格控制温度。 4).脱脂工序后,素材表面应完全润湿,如有明显之水珠与素材界面排斥现象说明此操作未达到要求,需重复操作,并及时调整各参数。 二、膨润※(了解即可) 作用机理: 通过膨润剂膨胀工件达到表面微蚀,同时软化材质本身,释放因注塑或材质原因产生的应力不均,以便后序粗化工序能够均匀良好的腐蚀。 电镀素材的内应力的检查,针对不同材料,方法也会有一定的区别。对于ABS类一般情况下都会采用冰醋酸浸渍法。具体做法如下: 将素材完全浸入25℃±3℃的冰醋酸溶液中4分钟,取出后立即用凉水清洗干净,然后晾干(若需吹干,也只能用冷风),检查表面,若有明显之亮雾不均或细小的裂纹,说明此处有应力存在。将产品于1米高处抛落,若产品表面出现明显裂纹,说明此处应力过大。
通常情况下于65℃--75℃温度下加热2—4H或以同样温度的热水中浸泡30min以消除素材应力,也可于25%(体积)的丙酮中浸泡3--5min以消除应力。 三、粗化 1、温度管控范围:63~69℃,标准:66℃ 2、ABS塑料是丙烯晴(A)、丁二烯(B)、苯乙烯(S)的三元共聚物,在粗过化程中,塑胶粒子被容去形成凹坑,使表面有憎水性变成亲水性,使镀层附着在胶件上面并牢固结合。 注意事项: 1).高铬型溶液,溶粗化速度快,镀层附着力好;但是铬酸与硫酸值大于800 g/L时,溶液会有沉淀产生,需保持气体搅拌。 2).浓度不足时,粗化效果差;浓度过高时,易粗化过度,损伤素材,且带出损耗较大,成本增高。 3).温度不足时,粗化效果不佳,温度过高过时,素材易发生形变。 4).时间过短时,无法满足粗化效果,时间过长时,易粗化过度,损伤素材。 5).粗化过程中会有Cr3+产生。Cr3+浓度越高,粗化效果越差,镀层的附着力也会随之下降,需定期做电解控制。 6).粗化湿润剂有利于工件良好润水,合理范围内,于搅拌情况下,液面会有一层黄色泡沫,如不足时,需及时补加。 7).粗化后,素材表面应当完全被水润湿,粗化程度的表面特征,可以从外观上作出判断: a. 粗化不足,表面平滑有光泽,对强光源反射好. b. 粗化适宜,表面微暗,平滑但不反光. c. 粗化稍过度,表面明显发暗,但仍平滑. d. 粗化过度,表面呈白绒状,疏松.
电镀前处理工艺概述以及配方
电镀前处理工艺概述以及配方 1前处理的定义 一般前处理过程为,研磨预备洗净水洗电解脱酯水洗酸浸及活性化水中和水洗电镀。1.1前处理的目的 前处理的目的是为了得到良好的镀层,由于镀件在制造、加工搬运、保存期间会有油酯、氧化物锈皮、氢氧化物、灰尘等污物附着于镀件表面上,若不去除这些污物而进行电镀将得不到良好的镀层。镀?件品质,前处理占很重要的地位。 1.2前处理不良所造成之镀层缺陷 前处理不良所造成之镀层缺陷,有下列几项:(1)剥离,(2)气胀,(3)污点,(4)光泽不均,(5)凹凸不平,(7)小孔(8)降低耐蚀性,(9)脆化。电镀之不良,前处理占很大的原因。 1.3污物的种类 污物的种类,可分为有机物及无机物。有机物污物主要是动物性油酯,植物性油酯及矿物性油酯,无机物污物是金属氧化物、盐类、尘埃、及砂土。另外由有机物和无机物污物之物如研磨屑、研磨材料。动物性及植物性油酯可被化缄剂皂去除。矿物性油污无法被缄剂皂去除需用三菉乙烯、汽油、石油溶剂乳化剂等去除。无机物污物可被酸或缄溶解,利用酸、缄浸渍、化学或电解方法去除及机械研磨方法去除。无机、有机混合污物,去除较困难,除了利用化学方法,亦须用电解,机械研磨等方法联合应用去除。 1.4电镀前处理去除的典型污物(1)润滑油(6)淬火残留物(2)切削
油(7)热处理盐(3)研磨油(8)热处理盐(4)热斑(9)污迹 (5)锈及腐蚀物(10)油漆及油墨1.5表面清洁测定 表面清洁度测定,在工场最实用的方法是用水冲(water-beaktest),检查表面水是否均匀润湿,如果是均匀润湿则为清洁表面,反之则不清洁。其它方法有,Nielsonmethod,Atomizertest,Fluoresentmethod,weightofresidualsoil,wip-ingmethod,residualpatlernmethod及Radioisotopetracertechnique。 1.6选择清洁方法及清洁材料之影响因素其影响因素有:(1)被清洁表面之特性(9)清洁剂的温度(2)被去除污物之特性(10)应用时间(3)清洁要求程度(11)经验(4)应用的方法(12)搅拌次数(5)水质(13)污染的程度(6)手续、另件、设备人员的安全(14)下一步处理(7)成本(15)废物之处理(8)清洁剂的浓度4镀铬之影响因素(l)CrO3浓度与导电度关系(2)温度兴导电度之关系(3)CrO3浓度与电流效率之关系(4)硫酸浓度之影响:浓度低时,低电流密度下电流效率高,反之电流效率低‥(5)三价铬的影响 1.三价铬很少时,沉积速率减媛。 2.三价铬很高时,镀层变暗。 3.三价铬增加,则导电度降低,需较大电压 4.三价铬愈多,光泽范围愈小。 (6)电流密度及温度的影向1.镀浴温度升高,电流效率降低。2.电流密度愈高,电流效率愈高。 3.高电流密度,低温则镀层灰暗,硬度高脆性大,结晶粗大‥ 4.高温而低电流密度,镀层硬度小,呈乳白色,延性好,无网状裂纹,结晶细致,适合装饰性的镀件。 5.中等温度及中等电流密
电镀废气处理方法
电镀废气处理方法 电镀车间在电镀生产中产生的废气,必须有效地加以处理。才能更好地维护大气环境,具体处理工艺流程如下: 一、酸性气体→三级碱液喷淋 ⑴硫酸雾气:可用浓度为10%的苏打(Na2CO3)的碱性溶液(NaOH),(pH值必须大于10)进行中和处理。 ⑵盐酸雾气:可用2%-5%的NaOH低浓度溶液进行中和处理。 ⑶氢氟酸:可用5%苏打(Na2CO3)的碱性溶液(NaOH)进行中和处理。 二、铬雾→收集回收→二级喷淋处理→水气分离→排放。 采用5%-10%的焦亚硫酸钠作为喷淋液,如喷淋液出现淡黄色必须更换喷淋液或加料。喷淋液淡绿色为正常。 三、氮氧化物→三级还原吸附→活性炭吸附→排放。
采用还原性碱液吸附法,将NOx还原为N2,同时将挥发的硝酸中和。 1、8%的氢氧化钠与10%的硫化钠混合水溶液作为吸收液,或者用氢氧化钠溶液多级喷淋后再加一级硫化钠水溶液喷淋吸收,其吸收率达到90%以上。警告!使用硫化钠必须注意,不得与硝酸溶液接触,避免中毒。 2、弱酸性尿素10%处理,吸收率可达90%以上,无二次污染,但成本高。 四、氰化氢→三级喷淋分解处理→排放。 1、氰化氢废气可以用1.5%NaOH+1.5%NaClO喷淋吸收。次氯酸钠水溶液应用氢氧化钠将吸收液调pH值保持碱性状态,(PH值在10以上)用一般喷淋塔吸收,净化效率可达到90%以上。或可用2%-5%的次氯酸酸钠(重量)溶液作吸收液。 2、硫酸亚铁溶液作吸收液时,0.1-0.7%硫酸亚铁(重量)水溶液送入喷淋塔吸收3-4s,净化效率可以达到98%。 最后要注意:上述所有喷淋塔下来准备不再循环使用的淋喷废水必须按质分类,进入相应的电镀废水中,加以处理后达标排放。 杭州海州环保设备有限公司座落于“杭州市高新技术产业园”—钱江经济开发区,注册资本500万元,系浙江省环保产业协会会员单位,拥有总承包和设计资质,是一家以废气、废水处理设备科研、设计、生产、销售、工程安装为一体的科技型企业。现拥有各类专业技术人员30余人,企业建有综合性实验室,拥有各种先进的化验检测仪器及中、小实验设备。本公司主要产品:蓄热式燃烧、吸附脱附+催化燃烧、光氧催化废气处理设备、低温等离子体设备、活性炭吸附设备、喷淋塔设备、干式漆雾过滤器设备等。 海州环保致力于用更优质的产品、更专业的服务,构建双赢模式,已逐步在行业中树立起重合同守兴誉的良好形象! 公司自成立以来,本着“客户第一,诚信至上”的原则,先后已经陆续为全国500余家企业提供一体化环保解决方案,得到喷涂、食品、印染、化工等
尼龙电镀前处理工艺
摘要:介绍了适用于尼龙(PA)基材的新型前处理工艺。经过胯胀、调校、钯活化、还原、化学镍δ=0.3μm)、预镀镍或铜(δ=2~5μm)、酸铜(δ=20μm)、光亮镍δ=12μm)、装饰铬(δ=0.3μm)等工艺后,可在尼龙表面获得结合力良好的装饰性镪层。该工艺为开发尼龙塑料在电镀业的应用迈出了重要的一步。 关键词:尼龙;电镀;前处理;装饰性镀层 中图分类号:T Gl78;TQ l53.3文献标志码:A 文章编号:1004-227X(2009)09-0014-02 Pre tre at men t fo r el ect ro pla ti ng of pol ya mid e(PAl sub str at es//B RAN DE S M aj a-Mar io la,F ELS C arl C hri st ian K O D an ny* Abs tra c t:A rel ia ble pro ce ss f or t he p re tre at men t ol pol yam id es(PA)fo r me tal p lat in g was d es c ri be d.B)ap pl yin g sw ell in g,con dit io nin g,Pd a cti va tio n,red uc tio n.el ect ro les s ni ck el lay er(δ=0.3μm),Ni or C u st ri ke l aye r(δ=2-5μm),a ci d co pp er lay er(J=20μm),br igh t n ick el l ay el(δ=12μm)and bri gh t ch ro me lay er(δ=0.3μm),a d ec ora ti ve coa ti ng w it h g ood ad he sio n C an be obt ain ed o n s pe cif ic t ype o f PA su rf ace.Thi s is a si gni fi can t st ep for t he dev el opm en l an d ap pl ica ti on o f th e me ta l pl at ing of pol yam id es. Key wor ds:p ol yam id e; el ect ro pla ti ng;p ret re at men t;de cor at ive coa tin g lay er Fir st.a ut hor'S ad dre ss:Ato te ch Deu ts chl an d G mbH.Ber li n,Ge rm any 尼龙材料的特点 近年来,尼龙作为一种塑料基材已被广泛应用于工业。作为一种热塑性塑料,尼龙很容易在液态下被加工,在-30~110 0C温度范围内具有良好的稳定性。此外,它还具有优异的耐热、高冲击强度,弹性变形小,耐摩擦和减震等性能,而低的熔融黏度使其易加工成型。总而言之,尼龙不但重量轻、制造成本低,而且还具有优异的物理性能。 各种各样的尼龙塑料如PA6、PAl l、P Al2和PA66等,可根据极性氨基的数量识别。此特性是区分尼龙塑料与A BS、A BS/P C塑料的依据。尼龙塑料电镀前处理如使用铬酸粗化,会对氨基有些影响,得不到预期的良好装饰性效果。因此,在尼龙电镀之前,需要考虑两个重要的影响因素:一是注塑不同特性的尼龙塑料时,会添加不同的填充料(如矿纤、玻璃纤维等),以增
【免费下载】电镀工艺和喷砂工艺简介
电镀工艺和喷砂工艺简介引 言制造一部C 辊的修磨工艺是首先将现有磨损C 辊的镀铬层磨掉,然后再在C 辊的表面进行镀硬铬,镀层厚度0.1-0.15mm ,辊面粗糙度:Ra0.2,在这里首先介绍一下电镀的工艺流程;在涂布机出炉膛纠偏处将原先的橡胶纠偏辊更换成金属表面喷砂的导辊,增加了导辊的耐热性和表面摩擦力,克服了原先橡胶辊高温老化摩擦力小,经常引起极片跑偏的问题,因此在这里也介绍一下喷砂的工艺。 关 键 词抗磨损 基体材料 注射塑件 金属镀层标识 镀覆方法高速喷射束 机械性能 清理与抛光 流平和装饰 喷砂处理铜、镍、铬三种金属沉积层 反光或亚光 高光亚光 真空镀一、电镀的工艺 1.电镀的定义和分类1-1.电镀的定义 随着工业化生产的不断细分,新工艺新材料的不断涌现,在实际产品中得到应用的设计效果也日新月异,电镀是我们在设计中经常要涉及到的一种工艺,而电镀效果是我们使用时间较长,工艺也较为成熟的一种效果,对于这种工艺的应用在我们的产品上已经非常多,我们希望通过总结我们已有的经验作一些设计的参考性文件,可以更好的将电镀效果应用在我们的设计上,也更合理的应用在我们的设计上,可以为以后的工作带来一些方便。通过这种工艺的处理我们通常可以得到一些金属色泽的效果,如高光,亚光等,搭配不同的效果构成产品的效果的差异性,通过这样的处理为产品的设计增加一个亮点。 1-1-1. 电镀的定义电镀就是利用电解的方式使金属或合金沉积在工件表面,以形成均匀、致密、结合力良好的金属层的过程,就叫电镀。简单的理解,是物理和化学的变化或通过管线敷设技术,不仅可以解决吊顶层配置不规范问题,而且可保障各类管路习题到位。在管路敷设过程中,要加强看护关于管路高中资料试卷连接管口处理高中资料试卷弯扁度固定盒位置保护层防腐跨接地线弯曲半径标高等,要求技术交底。管对全部高中资料试卷电气设备,在安装过程中以及安装结束后进行高中资料试卷调整试验;通电检查所有设备高中资料试卷相互作用与相互关系,根据生产工艺高中资料试卷要求,对电气设备进行空载与带负荷下高中资料试卷调控试验;对设备进行调整使其在正常工况下与过度工作下都可以正常工作;对于继电保护进行整核对定值,审核与校对图纸,编写复杂设备与装置高中资料试卷调试方案,编写重要设、电气设电力保护装置调试技术,电力保护高中资料试卷配置技术是指机组在进行继电保护高中资料试卷总体配置时,需要在最大限度内来确保机组高中资料试卷安全,并且尽可能地缩小故障高中资料试卷破坏范围,或者对某些异常高中资料试卷工况进行自动处理,尤其要避免错误高中资料试卷保护装
电镀不良的一些情况和解决方法分析
电镀不良的一些情况和解决方法 发布日期:2013-09-04 来源:中国电镀网浏览次数:2097 关注: 加关注 核心提示:电镀不良对策镀层品质不良的发生多半为电镀条件,电镀设备或电镀药水的异常,及人为疏忽所致.通常在现场发生不良时比较容易找出塬 电镀不良对策 镀层品质不良的发生多半为电镀条件,电镀设备或电镀药水的异常,及人为疏忽所致.通常在现场发生不良时比较容易找出塬因克服,但电镀后经过一段时间才发生不良就比较棘手.然而日后与环境中的酸气,氧气,水分等接触,加速氧化腐蚀作用也是必须注意的.以下本章将对电镀不良的发生塬因及改善的对策加以探讨说明. 1.表面粗糙:指不平整,不光亮的表面,通常成粗白状 (1)可能发生的塬因: (2)改善对策: 1.素材表面严重粗糙,镀层无法覆盖平整. 1.若为素材严重粗糙,立即停产并通知客户. 2.金属传动轮表面粗糙,且压合过紧,以至于压伤. 2.若传动轮粗糙,可换备用品使用并检查压合紧度. 3.电流密度稍微偏高,部分表面不亮粗糙(尚未烧焦) 3.计算电流密度是否操作过高,若是应降低电流 4.浴温过低,一般镀镍才会发生) 4.待清晰度回升再开机,或降低电流,并立即检查温控系统. 5.PH值过高或过低,一般镀镍或镀金(过低不会)皆会发生. 5.立即调整PH至标准范围. 6.前处理药液腐蚀底材. 6.查核前处理药剂,稀释药剂或更换药剂 2.沾附异物:指端子表面附着之污物. (1)可能发生的塬因: (2)改善对策: 1.水洗不干净或水质不良(如有微菌). 1.清洗水槽并更换新水.
2.占到收料系统之机械油污. 2.将有油污处做以遮蔽. 3.素材带有类似胶状物,于前处理流程无法去除. 3.须先以溶剂浸泡处理. 4.收料时落地沾到泥土污物. 4.避免落地,若已沾附泥土可用吹气清洁,浸透量很多时,建议重新清洗一次. 5.锡铅结晶物沾附5.立即去除结晶物. 6刷镀羊毛?纤维丝6.更换羊毛?并检查接触压力. 7.纸带溶解纤维丝. 7.清槽. 8.皮带脱落屑. 8.更换皮带. 3.密着性不良:指镀层有剥落.起皮,起泡等现象. (1)可能发生的塬因: (2).改善对策: 1.前处理不良,如剥镍. 1.加强前处理. 2.阴极接触不良放电,如剥镍,镍剥金,镍剥锡铅. 2.检查阴极是否接触不良,适时调整. 3.镀液受到严重污染. 3.更换药水 4.产速太慢,底层再次氧化,如镍层在金槽氧化(或金还塬),剥锡铅. 4,电镀前须再次活化. 5.水洗不干净. 5.更换新水,必要时清洗水槽. 6.素材氧化严重,如氧化斑,热处理后氧化膜. 6.必须先做除锈及去氧化膜处理,一般使用化学抛光或电解抛光. 7.停机化学置换反应造成. 7.必免停机或剪除不良品 8,操作电压太高,阴极导电头及镀件发热,造成镀层氧化. 8.降低操作电压或检查导线接触状况 9,底层电镀不良(如烧焦),造成下一层剥落. 9.改善底层电镀品质. 10.严重.烧焦所形成剥落10.参考NO12处理对策.