QCT27_2014汽车干摩擦式离合器总成台架试验方法
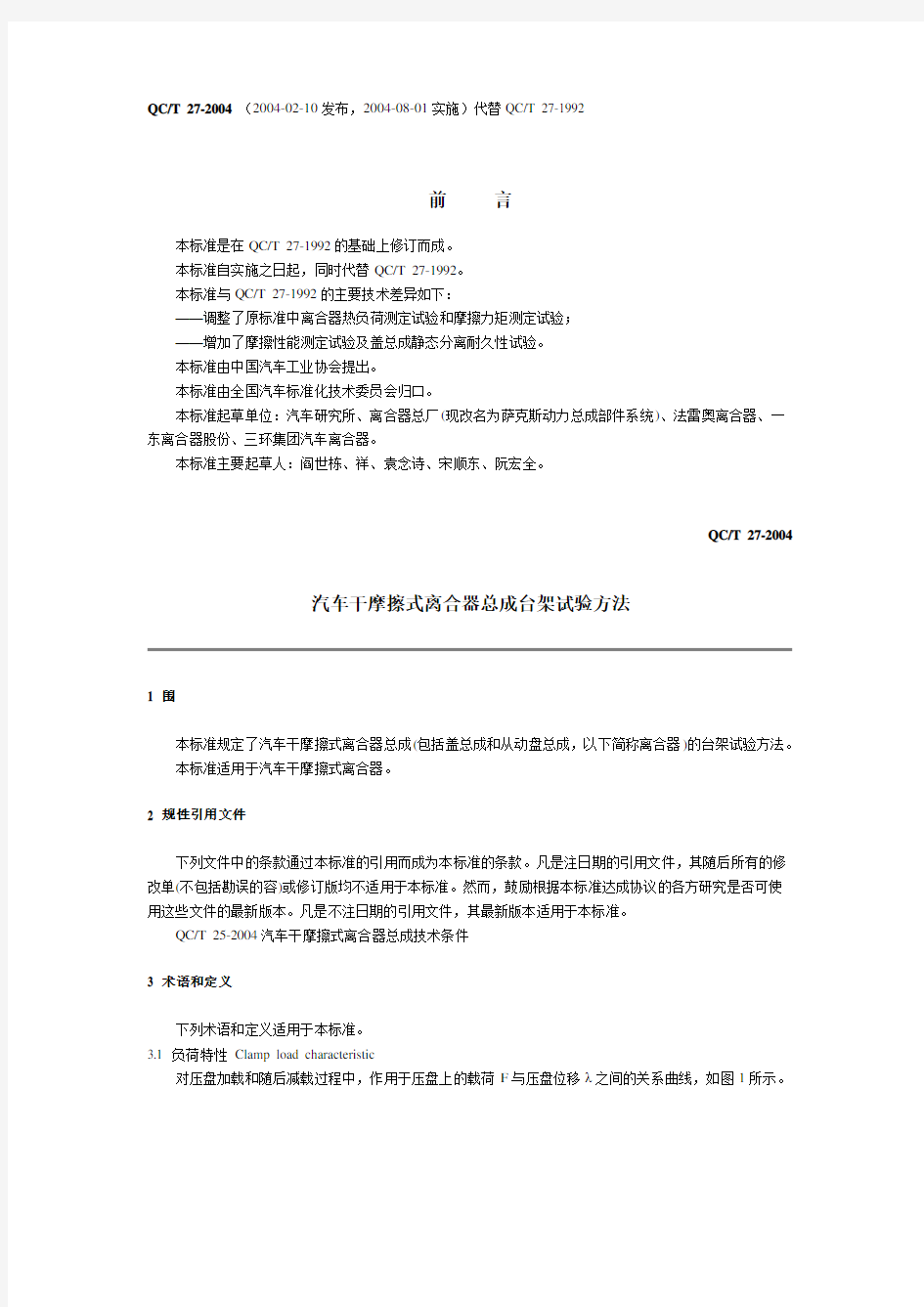

QC/T 27-2004(2004-02-10发布,2004-08-01实施)代替QC/T 27-1992
前言
本标准是在QC/T 27-1992的基础上修订而成。
本标准自实施之日起,同时代替QC/T 27-1992。
本标准与QC/T 27-1992的主要技术差异如下:
——调整了原标准中离合器热负荷测定试验和摩擦力矩测定试验;
——增加了摩擦性能测定试验及盖总成静态分离耐久性试验。
本标准由中国汽车工业协会提出。
本标准由全国汽车标准化技术委员会归口。
本标准起草单位:汽车研究所、离合器总厂(现改名为萨克斯动力总成部件系统)、法雷奥离合器、一东离合器股份、三环集团汽车离合器。
本标准主要起草人:阎世栋、祥、袁念诗、宋顺东、阮宏全。
QC/T 27-2004
汽车干摩擦式离合器总成台架试验方法
1 围
本标准规定了汽车干摩擦式离合器总成(包括盖总成和从动盘总成,以下简称离合器)的台架试验方法。
本标准适用于汽车干摩擦式离合器。
2 规性引用文件
下列文件中的条款通过本标准的引用而成为本标准的条款。凡是注日期的引用文件,其随后所有的修改单(不包括勘误的容)或修订版均不适用于本标准。然而,鼓励根据本标准达成协议的各方研究是否可使用这些文件的最新版本。凡是不注日期的引用文件,其最新版本适用于本标准。
QC/T 25-2004汽车干摩擦式离合器总成技术条件
3 术语和定义
下列术语和定义适用于本标准。
3.1 负荷特性Clamp load characteristic
对压盘加载和随后减载过程中,作用于压盘上的载荷F与压盘位移λ之间的关系曲线,如图1所示。
a) 螺旋弹簧离合器盖总成b) 膜片弹簧离合器盖总成
图1 负荷特性
3.2 工作点位置position at nominal disc thickness
安装状态下,从动盘总成夹紧名义厚度所对应的压盘位置。
3.3 工作压紧力clamp load at nominal disc thickness
安装状态下,压盘处于工作点位置时对从动盘总成施加的压紧力。如图1有F o为加载工作压紧力,F m 为平均工作压紧力,F u为卸载工作压紧力,其中
F m=(F u+F o)/2 (1)
3.4 磨损后工作点位置position after wear
安装状态下,从动盘总成具有允许磨损后的厚度时所对应的压盘位置。
3.5 磨损后工作压紧力clamp load after wear
安装状态下,压盘处于磨损后工作点位置时对从动盘总成施加的压紧力。如图1有F o1为磨损后加载工作压紧力,F m1为磨损后平均工作压紧力,F u1为磨损后卸载工作压紧力,其中
F m1=(F u1+F o1)/2 (2)
3.6 分离特性release load characteristic
用等于从动盘总成夹紧名义厚度(或允许磨损后的厚度)的垫块代替从动盘总成且使离合器盖总成处于模拟安装状态,在一定的预载荷作用下再分离和接合离合器,作用于分离指(杆)端的载荷F A及压盘位移h,随分离指(杆)端行程λA变化的关系,如图2。其中h a为压盘升程,△h a为压盘倾斜量。
图2分离特性
3.7 最大分离力F Amax max. release load
在规定的最小分离行程λc围,分离特性F A-λA曲线上的最大载荷值,如图2。
3.8分离点分离力F Ac release load at nominal release point
分离特性F A-λA曲线上,对应于规定的最小分离行程λc变的载荷值,如图2。
4 总则
4.1 试验项目
本标准包括如下台架试验项目:
4.1.1 盖总成功能特性试验
a) 盖总成分离指(杆)安装高度及分离指(杆)端面跳动量测定;
b) 盖总成分离特性测定;
c) 盖总成负荷特性测定;
d) 盖总成不平衡量测定。
4.1.2 从动盘总成功能特性试验
a) 从动盘总成轴向压缩特性、夹紧厚度、平行度测定;
b) 从动盘总成扭转特性测定;
c) 从动盘总成拖曳分离特性测定;
d) 从动盘总成不平衡量测定;
e) 离合器摩擦性能测定试验;
f) 防粘着试验。
4.1.3 离合器耐久性及可靠性试验
a) 盖总成静态分离耐久性试验;
b) 盖总成动态分离耐久性试验;
c) 盖总成耐高速试验;
d) 从动盘总成轴向压缩耐久性试验;
e) 从动盘总成扭转耐久性试验;
f) 从动盘总成耐高速试验。
4.2 对试验结果的评价
根据试验的性质、目的,将试验结果与QC/T 25-2004或产品图样技术要求或供需双方商定的技术要求等进行比较,确定试件是否满足要求。
4.3 试验报告.
试验完成后,编写试验报告,基本容如下:
a) 试验名称;
b) 试验根据;
c) 试验目的;
d) 试验对象;
e) 试验方法和条件;
f) 试验结果与分析;
g) 试验结论。
5 盖总成功能特性试验
5.1 分离指(杆)安装高度及分离指(杆)端面跳动量测定
5.1.1 试验设备
5.1.1.1 能使载荷均匀作用于分离指(杆)端,并与压盘工作面垂直的测试台架。
5.1.1.2 试验夹具应能使盖总成模拟当从动盘总成具有夹紧名义厚度时的安装状态,如图3。
图3 盖总成功能特性试验示意图
5.1.2 试验步骤
5.1.2.1 将盖总成按技术要求固定于试验夹具上,使压盘处于工作点位置。
5.1.2.2 操纵加载装置,使代用分离轴承行程达到规定的分离行程,如此动作3~5次。
5.1.2.3 在安装状态下,测量各分离指(杆)端高度,其最大值与最小值之差即为分离指(杆)端面跳动量。5.1.2.4 对分离指(杆)端预加载荷100N,或按相应图纸技术要求规定。
5.1.2.5 测量分离指(杆)与分离轴承圆周接触点处至指定基准面的高度值,此高度值即为分离指(杆)安装高度值。
5.2 盖总成分离特性测定
5.2.1 试验设备
同5.1.1。
5.2.2 试验步骤
5.2.2.1 将盖总成按技术要求固定于试验夹具上,使压盘处于工作点位置。
5.2.2.2 对分离指(杆)端预加载荷100N,或按相应图纸技术要求规定。以此状态定义为位移零位。
5.2.2.3 操纵加载装置,使代用分离轴承行程达到规定的分离行程,如此动作3~5次。
5.2.2.4 操纵加载装置,使离合器分离,直到达到最大分离行程为止。再使离合器接合,恢复到位移零位;在此过程中测量并记录分离力和沿离合器平均直径圆周方向均布的三点处的压盘位移,绘制如图2的分离特性曲线。
5.2.2.5 按图2确定相应特征值:
a) 取3点位移测量值的最小值作为压盘升程h a;
b) 取3点位移测量值的最大值和最小值之差作为压盘倾斜量△h a;
c) 确定F Amax和F Ac。
5.3 盖总成负荷特性测定
5.3.1 试验设备
5.3.1.1 使载荷均匀作用于压盘表面,并与压盘工作表面垂直的试验台架。
5.3.1.2 试验夹具应能使盖总成模拟安装状态,如图4。
图4 盖总成负荷特性测定示意图
5.3.2 试验步骤
5.3.2.1 将盖总成固定于试验夹具上,使压盘处于自由状态,如图4。
5.3.2.2 对压盘加载。螺旋弹簧离合器,加载使压盘超过工作点位置2.5mm左右;膜片弹簧离合器,加载使压盘超过底谷点位移1mm左右。然后减载,直至卸掉全部载荷,记录压盘上载荷随压盘位移变化的数值。
5.3.2.3 用规定的试验垫块或其它方法确定特征点位置,以此来确定相应的载荷特征值。
5.3.2.4 如图1绘制负荷特性图。
5.4 盖总成不平衡量测定
5.4.1 试验设备
5.4.1.1 单面平衡机。
5.4.1.2 盖总成专用平衡夹具。
5.4.2 试验步骤
5.4.2.1 将盖总成安装于试验夹具上,使盖总成的定位方式与实际定位方式相同。
5.4.2.2 测量盖总成的不平衡量。
6 从动盘总成功能特性试验
6.1 从动盘总成轴向压缩特性、夹紧厚度、平行度测定
6.1.1 试验设备
保证载荷垂直而均匀地作用于从动盘总成摩擦表面的轴向压缩特性试验台及相应的仪器仪表装置,如图5。
1—主框架;2—位移传感器;3—预载盘;4—负载传感器;
5—球铰链;6—液压缸;7—上压板;8—从动盘总成;9—下压板
图5 从动盘总成轴向压缩特性测定示意图
6.1.2 试验步骤
6.1.2.1 将从动盘总成装于试验台上,装置状况如图5。
6.1.2.2 按规定工作压紧力压缩从动盘总成数次,直至轴向压缩量读数稳定。
6.1.2.3 施加规定的预载荷70N(或按技术文件规定的预载荷),然后开始测量。
6.1.2.4 对从动盘总成加载,直到从动盘总成上的载荷达到规定工作压紧力,记录轴向压缩量δ和所对应的垂直压力F。
6.1.2.5达到规定工作压紧力F b时,测量上下夹板间沿外圆周均布3点处的距离,其平均值为从动盘总成的夹紧厚度,最大值与最小值之差即为平行度。
6.1.2.6 绘制轴向压缩特性曲线,如图6。
图6 从动盘总成轴向压缩特性
6.2 从动盘总成扭转特性测定
6.2.1 试验设备
保证摩擦片部分完全固定,并对盘毂施加转矩的从动盘总成扭转特性试验台及相应的转角和转矩测量装置,如图7。
6.2.2 试验步骤
6.2.2.1 将从动盘总成安装到试验台的芯轴上,并将摩擦片部分夹紧。
6.2.2.2 装转角指针或角位移传感器,使之能随盘毂一起转动并处于零位。
6.2.2.3 对盘毂施加转矩,转动盘毂,直到规定转角极限。
1—拉压力传感器;2—支承板;3—夹紧盘;4—芯轴;
5—转角轴;6—角位移传感器;7—X-Y记录仪;8—扭转力臂
图7 从动盘总成扭转特性测定示意图
6.2.2.4 卸载至零。
6.2.2.5 反向施加转矩,转动盘毂,直到规定转角极限。
6.2.2.6 卸载至零。
6.2.2.7 重复6.2.2.3~6.2.2.6两次。
6.2.2.8 在中间位置检查并调整转角及转矩零位。
6.2.2.9 重复6.2.2.3~6.2.2.6,但需记录转角与转矩的对应数值。
6.2.2.10 绘出扭转特性曲线,如图8。
6.2.2.11 按图8所示确定减振器极限扭转角θmax,极限转矩M max,规定转角处的转矩滞后值M h(M h/2为摩擦阻尼力矩),规定转角围的扭转刚度Cα对应发动机最大转矩M emax时的转角θe。
图8 从动盘总成扭转特性
6.3 从动盘总成拖曳分离特性测定
6.3.1 试验设备
从动盘总成拖曳分离测试机。
6.3.2 试验步骤
6.3.2.1 将从动盘总成安装到从动盘总成拖曳分离测试机中垂直放置的两平行圆板之间的芯轴上。
6.3.2.2 通过加载圆板向从动盘总成摩擦面加载到规定工作压紧力。
6.3.2.3 卸载,圆板同时后移到技术条件中规定的位移量,并施加规定的拖曳分离转矩,或者在规定的拖曳分离转矩作用下,后移圆板到规定的位移量。
6.3.2.4 检测从动盘总成是否自由转动。
6.4 从动盘总成不平衡量测定
6.4.1 试验设备
6.4.1.1 单面平衡机。
6.4.1.2 从动盘总成平衡试验芯轴。
6.4.2 试验步骤
6.4.2.1 将从动盘总成安装于试验芯轴上。
6.4.2.2 测量从动盘总成的不平衡量。
6.5 离合器摩擦性能测定试验
6.5.1 试验条件
6.5.1.1 试件:新的从动盘总成及盖总成。
6.5.1.2 输入转速:730r/min。
6.5.1.3 惯性矩:5.25kg·m2。
6.5.1.4 离合周期:30s。
6.5.1.5 温度测量:压盘温度须在压盘表面中径,距工作表面下0.2mm处测得。
6.5.2 试验设备
满足6.5.1之试验条件,能作转矩、温度、转速之测定的离合器摩擦性能试验台,如图9。
1—电机;2—储能飞轮;3—被试离合器;4—惯量盘;5—制动器
图9 离合器摩擦性能试验台
6.5.3 试验步骤
6.5.3.1 测量盖总成的工作压紧力,称取从动盘总成质量。
6.5.3.2 将试件安装于试验台上。
6.5.3.3 按6.5.1规定的条件接合离合器,待试验台主、从动部分同步之后,分离离合器、制动试验台从动部分至停止,完成一个循环。如此循环60次。记录第20次、第40次和第60次过程中转矩随时间的变化曲线。
6.5.3.4 固定试验台从动部分,接合离合器使试验台主、从动部分之间产生滑摩直到压盘温度达到320℃,记录此时的转矩值。
6.5.3.5 冷却到室温。
6.5.3.6 按6.5.1规定的条件再循环1000次。记录第100次、第200次……及第1000次过程中转矩随时间的变化曲线。
6.5.3.7 称取从动盘总成质量。
6.5.3.8 按6.5.1规定的条件再循环3000次。记录第100次、第200次……及第3000次过程中转矩随时间的变化曲线。
6.5.3.9 称取从动盘总成质量。
6.5.3.10 测量盖总成的工作压紧力。
6.5.4 计算
6.5.4.1 各个试验阶段的摩擦系数按下式计算:
(3)
(4)
式中:
μ——摩擦系数;
M d——转矩值;
r m——摩擦片作用半径;
r a——摩擦片外半径;
r i——摩擦片半径;
F A——盖总成试验前和试验后工作压紧力的平均值。
6.5.4.2 转矩M d的确定
60次、1000次及4000次三个阶段中的转矩值,取每个阶段中记录值的平均值和最小值。
6.5.4.3 磨损量的计算
试验前后从动盘总成的质量差即为磨损量。
6.6 防粘着试验
6.6.1 试验条件
6.6.1.1 压盘和飞轮或代用飞轮摩擦面须事先用丙酮或其他清洗剂清洗干净。
6.6.1.2 将装配完整的离合器(包括盖总成、从动盘总成、飞轮)放置于特定的气候箱中并使其放置位置防止摩擦面积水。
6.6.1.3 须经过3个周期的冷凝水气候交变(共24×3h)。其交变气候条件如下:
第一阶段:温度(40±3)℃、相对湿度100%状态下保持8h(包括升温时间,但升温时间不超过1.5h)。
第二阶段:温度(23±5)℃、相对湿度小于100%状态下保持16h。
6.6.2 试验设备
6.6.2.1 温度、湿度可调整、控制的恒温、恒湿气候箱,如图10。
6.6.2.2 分离转矩测量装置,如图11。
1—盛水槽;2—温度测量装置;3—过压阀;4—网板
图10 恒温、恒湿气候箱示意图
图11 分离转矩测量装置示意图
6.6.3 试验步骤
6.6.3.1在满足6.6.1的条件下,经72h冷凝水交变气候试验后,即将离合器总成固定于分离转矩测量装置,使试件水平放置(如图11)且使飞轮固定。
6.6.3.2 如图11所示分离离合器,分离行程S为技术文件规定的最小分离行程或按照其他相关技术条件规定。
6.6.3.3 对从动盘毂施加转矩,使从动盘总成相对于压盘和飞轮表面开始转动时的转矩,即为分离转矩。
7 离合器耐久性及可靠性试验
7.1 盖总成静态分离耐久性试验
7.1.1 试验条件
a) 分离行程应符合以下规定(一般耐久试验和强化耐久试验等效):
b) 分离频率:不大于3Hz。
c) 试验温度:室温。
7.1.2 试验设备
往复行程可调,并满足7.1.1规定的往复试验台,如图12。
1—飞轮(或平板);2—盖总成;3—代用分离轴承;4—滑动轴;
5—连杆;6—曲柄销;7—从动盘总成(或标准块)
图12 往复试验台示意图
7.1.3 试验步骤
7.1.3.1 按5。2、5.3测定盖总成的分离特性及负荷特性,确定盖总成的工作压紧力、分离力和压盘升程。
7.1.3.2 如图12将盖总成及从动盘总成装于试验台中,也可用相当于从动盘总成夹紧名义厚度的垫块代替从动盘总成。
7.1.3.3 按规定分离行程分离接合一次,为一次循环。
7.1.3.4 往复循环至规定的循环次数或试件发生损坏。
7.1.3.5 从装置上取出盖总成,直观检查有无裂纹、松动或破裂零件。
7.1.3.6 按5.2、5.3测定盖总成的分离特性及负荷特性,确定试验后盖总成的工作压紧力、分离力和压盘升程。
7.2 盖总成动态分离耐久性试验
7.2.1 试验条件
a) 盖总成转速:应不低于以下规定转速:
1) 微型车和轿车:3000 r/min。
2) 轻型车:2000 r/min。
3) 中型车:1500 r/min。
4) 重型车:商定。
b) 分离频率:不大于2Hz。
c) 分离行程:按技术文件规定。
d) 分离轴承:与离合器相配套使用的轴承。
e) 分离轴承对离合器回转中心偏心量:0.40mm。
f) 环境温度:室温或(100±5)℃。
7.2.2 试验设备
满足7.2.1试验条件的盖总成动态分离耐久性试验台,如图13。
1—代用飞轮;2—盖总成;3—电机;4—外罩;5—分离轴承;
6—连杆;7—偏心轴;8—风扇;9—加热器
图13 动态分离耐久性试验台示意图
7.2.3 试验步骤
7.2.3.1 按5.2、5.3测定盖总成的分离特性及负荷特性,确定盖总成的工作压紧力、分离力和压盘升程。
7.2.3.2 如图13将盖总成、从动盘总成或相当于从动盘总成夹紧名义厚度的垫块安装到试验台上。
7.2.3.3 按规定分离行程分离、接合一次,为一次循环。
7.2.3.4 往复循环至规定的循环次数。
7.2.3.5 从装置上取出盖总成,直观检查有无裂纹、松动或破裂零件。
7.2.3.6 按5.2、5.3测定盖总成的分离特性及负荷特性,确定试验后盖总成的工作压紧力、分离力和压盘升程。
7.2.3.7 测定分离指(杆)端的磨损量。
7.3 盖总成耐高速试验
7.3.1 试验条件
a) 不平衡量:盖总成不平衡量应满足技术文件规定,盖总成与夹具装配后的不平衡量应满足试验机的要求。
b) 加速度:10.47 rad/s2~31.42 rad/s2(每秒加速度控制在100 r/min~300 r/min)。
c) 试验温度:室温。
7.3.2 试验设备
最高转速可达15000r/min以上,加速度可控制的离合器高速试验台,如图14。
1—电机;2—皮带轮;3—传动皮带;4—被试件;5—破坏舱
图14 高速试验台示意图
7.3.3 试验步骤
7.3.3.1 在平衡机上检验盖总成的不平衡量。
7.3.3.2 将盖总成按规定装于代用飞轮上,使之处于接合状态,装于试验台上。
7.3.3.3 启动并加速试件至规定转速,在该转速下连续运转至按技术文件规定的时间,或者直至发生爆破为止,记录爆破时的转速。
7.4 从动盘总成轴向压缩耐久性试验
本试验可与7.1同时进行。
7.4.1 试验条件
a) 轴向载荷:零至规定载荷往复循环。规定载荷等于与被试从动盘总成配用的盖总成压紧
力。
b) 分离频率:不大于4Hz。
c) 试验温度:室温。
7.4.2 试验设备
同7.1.2。
7.4.3 试验步骤
7.4.3.1 按5.3确定盖总成的工作压紧力是否符合要求。
7.4.3.2 按6.1测量从动盘总成轴向压缩特性,确定试验前轴向压缩量。
7.4.3.3 将被试从动盘总成和盖总成装于试验台上。
7.4.3.4 调整试验台,使之满足7.4.1的规定。
7.4.3.5 按规定分离行程分离、接合一次,为一次循环。
7.4.3.6 往复循环至规定的循环次数。
7.4.3.7 从装置上取出从动盘总成,直观检查有无裂纹、松动或破裂零件。
7.4.3.8 按6.1测量从动盘总成轴向压缩特性,确定试验后的轴向压缩量。
7.5 从动盘总成扭转耐久性试验
7.5.1 试验条件
a) 加载方式:
1) 单向加载时,0~1.2 M emax;或双向加载时,正向1.0 M emax,反向0.5M emax(M emax为发动机最大转矩)。
2) 或按对应上述载荷的相应扭转角加载。
b) 扭转频率:6Hz~25Hz。
7.5.2 试验设备
满足7.5.1试验条件的机械式或液压式扭转试验台,如图15。
1—从动盘总成;2—芯轴;3—垫板;4—夹紧盘;5—摇杆;6—连杆;7—偏心轴
图15 扭转耐久性试验台示意图
7.5.3 试验步骤
7.5.3.1 按6.2测定从动盘总成扭转特性。
7.5.3.2 将从动盘总成装于试验台的花键轴上,将摩擦片固定。
7.5.3.3 按7.5.1扭转从动盘总成至规定的次数或试件发生损坏。
7.5.3.4 按6.2测定试验后从动盘总成扭转特性,并检查有无损坏、松动及磨损情况。
7.6 从动盘总成耐高速试验
7.6.1 试验条件
a) 温度:200℃。
b) 保温时间:20 min。
c) 加速度:10.47 rad/s2~31.42 rad/s2(每秒加速度控制在100 r/min~300 r/min)。
7.6.2 试验设备
最高转速可达15000 r/min以上,加速度可控制的离合器高速试验台和用以加热保温试件的恒温箱。
7.6.3 试验步骤
7.6.3.1 将待测的新从动盘总成按7.6.1中的a)和b)放置于恒温箱中加热保温。
7.6.3.2 将从动盘总成从恒温箱中取出后立即将它置于试验台芯轴上,并以规定加速度使试件加速到规定的转速。
7.6.3.3 在规定转速下,连续运转至规定的时间或者一直加速到发生爆破,记录下破坏时的转速。
汽车性能台架实
实验1 整车性能台架实验 1.1 实验目的与要求 1.1.1 实验目的 通过该实验的动手操作,要求学生掌握汽车整车台架实验的主要内容,熟悉汽车 台架测量部分评价指标的方法,并加深对汽车评价参数的理解。 1.1.2 实验要求 1)掌握汽车台架实验的方法和原理; 2)掌握相关设备的操作,了解其主要功用及构造; 3)对所得测数据进行分析,判断; 4) 撰写实验报告。 1.2 实验场地与设备: 1.2.1 场地 测量实验室一间 1.2.2 设备: 1)底盘测功机; 2)实验车一辆; 3)冷却风扇。 1.3 测功机构造与工作原理 1.3.1 构造 汽车底盘测功机主要由道路模拟系统、数据采集与控制系统、安全保障系统及引 导系统等构成。普通型道路模拟系统如图 l所示。 1.3.2 工作原理 由电涡流测功机结构图可知,感应子主要由旋转部分和摆动部分(电枢和励磁线圈)组成。转子轴上的感应子形状犹如齿轮,与转子同轴装有一个直流励磁线圈。当励磁线圈组通以直流电流时,其周围便有磁场存在,那么围绕励磁组就产生一闭合磁通。很明显,位于绕组左侧的感应子具有一个极性,右侧具有相反的极性。旋转时,由于磁密值
的周期性变化而产生涡流,此涡流产生的磁场同产生它的磁场相互作用,从而产生与被试机反向的制动力矩,使电枢摆动,通过电枢上的力臂,将制动力传给测量装置。 转速测量采用非接触式磁电转速传感器和装于主轴的60齿牙盘,将转速信号转换成电信号输出。 1.4.1 实验内容与步骤 1.4.1 实验条件 环境温度:0-40°C;环境相对湿度小于85%;大气压力80-10kpa 1.4.2 实验车辆载荷 除有特殊规定外,轿车为规定乘员数的一半(取整数) 1.4.3 试验车辆应预热至正常工作温度,轮胎气压应符合汽车制造厂规定,左右轮胎 花纹应一致; 1.4.4 底盘测功机应进行预热; 1.4.5 记录环境温度等相关数据; 1.4.6 测量汽车各档位中车速和驱动力。 1.4.7 测量汽车各档位中车速与功率的数值 1.4.8 测量汽车某档位的外特性与部分负荷特性中功率与转矩的数值。 1.5 实验注意事项 1.5.1 每次实验前必须详细预习实验指导书,明了实验目的、原理方法及操作步骤;
汽车发动机原理复习题
1、汽油机实际循环与下列()理论循环相似。 A、混合加热循环 B、定容加热循环 C、定压加热循环 D、卡诺循环 2、汽油机常用的压缩比在()范围内。 A、4 ~7 B、7 ~11 C、11 ~15 D、15 ~22 3、车用柴油机实际循环与下列()理论循环相似。 A、混合加热循环 B、定容加热循环 C、定压加热循环 D、卡诺循环 4、非增压发动机在一个工作循环中,缸内压力最低出现在() A、膨胀结束 B、排气终了 C、压缩初期 D、进气中期 5、发动机实际换气过程完善程度的评价参数有() A、机械效率 B、热效率 C、进气马赫数 D、充气效率 6、四冲程发动机换气过程中存在气门叠开现象的原因是() A、进气门早开和排气门早开 B、进气门晚关和排气门早开 C、进气门早开和排气门晚关 D、进气门晚关和排气门晚关 7、汽油机的火焰速度是() A、燃烧速度 B、火焰锋面移动速度 C、扩散速度 D、气流运动速度 8、提高压缩比使汽油机的爆震倾向加大,为此,可采取()的措施。 A、减小喷油提前角 B、减小点火提前角 C、加大喷油提前角 D、加大点火提前角 9、评价速燃期的重要指标中有() A、温度升高率 B、最大压力出现时刻 C、最高温度 D、压力升高时刻 10、下列措施中,不能够消除汽油机爆震的是() A、增大点火提前角 B、推迟点火提前角 C、加强冷却 D、选用高牌号的汽油 11、下面列出的()属于柴油机燃烧特点。 A、缺氧 B、空气过量 C、扩散燃烧 D、混合气预先形成 12、柴油机混合气形成过程中,存在燃料燃烧、燃料()、燃料与空气之间的扩散同步进行现象。 A、燃烧 B、凝结 C、蒸发 D、混合 13、球形油膜燃烧室属于柴油机()燃烧室。 A、涡流式 B、预燃室 C、间接喷射式 D、直接喷射式 14、下列四种燃烧室对喷射系统要求最高的是() A、开式燃烧室 B、半开式燃烧室 C、涡流室燃烧室 D、预燃室燃烧室 15、在发动机试验装置中,()是发动机试验台架的基本设备。 A、发动机 B、试验台 C、测功机 D、测量系统 17、万有特性图中,最内层的区域是() A、功率最高区域 B、油耗最小区域 C、转矩最大区域 D、转速最小区域 18、发动机的有效燃油消耗率和下面哪个参数成反比() A、机械效率 B、指示热效率 C、两个都是 D、两个都不是 19、三元催化转换器要求的空燃比范围是()理论空燃比。 A、小于 B、小于并接近 C、大于 D、大于并接近
发动机台架试验 -可靠性试验
学生实验报告实验课程名称:发动机试验技术
目录 一、试验目的 二、试验内容 1.试验依据 2.试验条件 3.试验仪器设备 4.试验样机 5.试验内容与方案 (1)交变负荷试验 (2)混合负荷试验 (3)全速负荷试验 (4)冷热冲击试验 (5)活塞机械疲劳试验 (6)活塞热疲劳试验 三、试验进度安排 四、试验结果的提供
摘要 国外在可靠性试验方面己做了许多有益的研究工作,但到目前为止尚未形成统一的试验方法,而且考虑到该试验的非普遍性及技术保密性,将来也不可能形成统一的试验规范。相对于热疲劳研究状况来讲,国内对机械疲劳的研究还比较少。为适应发动机比功率和排放法规日益提高的苛刻要求,发动机面临着更高机械负荷和热负荷的严峻考验。国内高强化发动机最大爆发压力已超过22 Mpa。活塞的机械疲劳损伤主要体现在销孔、环岸等部位。活塞环岸、销座及燃烧室等部位由于在较高的工作温度下承受着高频冲击作用的爆发压力,润滑状况较差,摩擦磨损,其他破坏可靠性的腐蚀磨损(缸套一环换向区、排气门/排气门座锥面等)、疲劳磨损(挺杆、轴瓦、齿轮表面等)、微动磨蚀(轴瓦钢背、飞轮压紧处、飞轮壳压紧处、湿缸套止口处等)、电蚀(火花塞电极等)和穴蚀(水泵叶轮等)这些都是可靠性试验的主要目标,也是实施可靠性设计、试验研究的重点部位。 众所周知,在内燃机整机上进行零部件可靠性试验成本昂贵。本文将参照原有的可靠性试验方法,通过看一些关于可靠性的零部件加速寿命实验技术制定一种评价内燃机可靠性的考核规范,包括活塞机械疲劳试验和活塞热疲劳试验,可迅速做出其可靠性恰当的评价,可以降低研发成本、缩短研发时间。 一、试验目的 1通过理解内燃机可靠性评估,评定发动机的可靠性。 1.1了解评估的多种理论方法,如数学模型法、上下限法、相似设备法、蒙特卡洛法、故障分析( 包括故障模式影响分析和故障树分析) 等。并掌握故障分析法。 1.2学会可靠性试验评估,为进行可靠性设计奠定基础理论,为发动机及相关零部件提供测试、验证以及改进的技术支持。 2掌握可靠性试验方法 2.1掌握内燃机可靠性综合性试验及专项试验。综合性试验的考核对象是零件的可靠性、零件表面性状的变化和发动机性能的保持性;专项试验是超水温( 耐热性) 、超负荷、混合负荷、交变负荷循环、超爆发压力、超速等试验。 二、试验内容 1试验依据 参考的试验标准: GB /T 19055-2003 汽车发动机可靠性试验方法 GB /T 18297-2001 汽车发动机性能试验方法 JB/T 5112-1999 中小功率柴油机产品可靠性考核 2试验条件 一般试验条件: 2.1燃料及机油:采用制造厂所规定的牌号,柴油中不得有消烟添加剂。
汽车发动机可靠性试验方法 GBT 19055-2003
GB/T 19055-2003 前言 本标准与GB/T 18297-2001《汽车发动机性能试验方法》属于同一系列标准,系汽车发动机试验方法的重要组成部分。 本标准自实施之日起,代替QC/T 525-1999。 本标准的附录A为规范性附录。 本标准由中国汽车工业协会提出。 本标准由全国汽车标准化技术委员会归口。 本标准起草单位:东风汽车工程研究院。 本标准主要起草人:方达淳、吴新潮、饶如麟、鲍东辉、周明彪。 引言 本标准系在JBn 3744-84即QC/T 525-1999《汽车发动机可靠性试验方法》长期使用经验的基础上参考国外的先进技术,制定了本标准。 本标准对QC/T 525-1999的重大技术修改如下: ——拓展了标准适用范围,不仅适用于燃用汽、柴油的发动机,还适用于燃用天然气、液化石油气和醇类等燃料的发动机; ——修改了可靠性试验规范,对最大总质量小于3.5t的汽车用发动机采用更接近使用工况的交变负荷试验规范;对最大总质量在3.5t~12t之间的汽车用发动机采用混合负荷试验规范,以改进润滑状态;冷热冲击试验过去仅在压燃机上进行,现扩展到点燃机,并增加了“停车”工况,使零部件承受的温度变化率加大; ——修改了全负荷时最大活塞漏气量的限值,首次推出适用于不同转速范围的非增压机、增压机、增压中冷机的限值计算公式,使评定更为合理; ——为使汽车发动机满足国家排放标准对颗粒排放物限值的要求,修改了额定转速全负荷时机油/燃料消耗比的限值(由原来1.8%改为0.3%); ——增加“试验结果的整理”的内容,并单独列为一事,要求对整机性能稳定性、零部件损坏和磨损等进行更为规范和详尽的评定; ——增加“试验报告”的内容,并单独列为一章,明确试验报告主要内容,使试验报告更为规范。 ——增加了附录A《汽车发动机可靠性评定方法》,使评定更为准确和全面, ——鉴于汽车发动机排放污染物必须满足国家排放标准的要求,在认证时按排放标准进行专项考核,故本标准不再涉及。 汽车发动机可靠性试验方法 1 范围 本标准规定厂汽车发动机在台架上整机的一般可靠性试验方法,具中包括负荷试验规范(如交变负荷、混合负荷和全速全负荷)、冷热冲击试验规范及可靠性评定方法。 本标准适用于乘用车、商用车的水冷发动机,不适用于摩托车及拖拉机用发动机。该类发动机属往复式、转子式,不含自由活塞式。其中包括点燃机及压燃机;二冲程机及四冲程机;非增压机及增压机(机械
汽车简式减振器台架试验方法
减振器台架试验及评定方法 主题和范围:本方法规定了PLD 汽车悬架用筒式减振器的台架试验和试验件评定方法。 本方法包含筒式减振器的示功试验、速度特性试验、温度特性试验、耐久性试验。 1 示功试验 目的:测取试件的示功图和速度图。 设备:PLD 系列微机控制电液伺服汽车减振器试验台。 条件: 1.3.1 试件温度:20士2℃。 1.3.2 试件试验行程S :(100±1)mm 。 1.3.3 试件频率n :(100±2) c 、p 、m 。 1.3.4 速度ν根据和并由下式决定的减振器活塞速度。 (m/s)520106 4.n S π=???=-ν 1.3.5 方向:铅垂方向。 1.3.6 位置:将减振器拉伸至最大行程并测定其行程中间位置A m ,并纪录。 试验方法 1.4.1 按加振,待f P 、y P 微机显示值稳定后,停止试验并记录相应得数值。 f P …………复原阻力,N ; y P …………压缩阻力,N ; 评定 1.5.1 示功图应丰满、圆滑,不得有空程、畸形等。 1.5.2 减振器在示功试验中,不得有漏油和明显的噪声等异常现象。 1.5.3 复原阻力和压缩阻力应符合附录A 要求,复原阻力和压缩阻力的允差值应符合下式规定: 复原阻力的允许差值为±(14%f P +40)N ,f P —额定复原阻力; 压缩阻力的允许差值为±(14%y P +40)N ,y P —额定压缩阻力; 2 速度特性试验 目的:检测减振器在不同活塞速度下的阻力,取得试件的速度特性。 设备:PLD 系列微机控制电液伺服汽车减振器试验台。 温度条件: 试件温度:20±2℃ 试件试验行程S :20~100 mm ,速度)/(.s m 520=ν;最高速度须高于1.5 m /s 。 方向:铅垂方向。 位置:A m 。 试验方法:本方法采用多工况合成法测试速度特性P 一v 曲线 每个测点工况皆按本标准实施; 最后如图4所示取得试验速度特性:
发动机台架试验
昆明理工大学交通工程学院学生实验报告实验课程名称:发动机试验技术
目录 一、试验目的 二、试验内容 1.试验依据 2.试验条件 3.试验仪器设备 4.试验样机 5.试验内容与方案 (1)交变负荷试验 (2)混合负荷试验 (3)全速负荷试验 (4)冷热冲击试验 (5)活塞机械疲劳试验 (6)活塞热疲劳试验 三、试验进度安排 四、试验结果的提供 摘要 国外在可靠性试验方面己做了许多有益的研究工作,但到目前为止尚未形成统一的试验方法,而且考虑到该试验的非普遍性及技术保密性,将来也不可能形成统一的试验规范。相对于热疲劳研究状况来讲,国内对机械疲劳的研究还比较少。为适应发动机比功率和排放法规日益提高的苛刻要求,发动机面临着更高机械负荷和热负荷的严峻考验。国内高强化发动机最大爆发压力已超过22 Mpa。活塞的机械疲劳损伤主要体现在销孔、环岸等部位。活塞环岸、销座及燃烧室等部位由于在较高的工作温度下承受着高频冲击作用的爆发压力,润滑状况较差,摩擦磨损,其他破坏可靠性的腐蚀磨损(缸套一环换向区、排气门/排气门座锥面等)、疲劳磨损(挺杆、轴瓦、齿轮表面等)、微动磨蚀(轴瓦钢背、飞轮压紧处、飞轮壳压紧处、湿缸套止口处等)、电蚀(火花塞电极等)和穴蚀(水泵叶轮等)这些
都是可靠性试验的主要目标,也是实施可靠性设计、试验研究的重点部位。 众所周知,在内燃机整机上进行零部件可靠性试验成本昂贵。本文将参照原有的可靠性试验方法,通过看一些关于可靠性的零部件加速寿命实验技术制定一种评价内燃机可靠性的考核规范,包括活塞机械疲劳试验和活塞热疲劳试验,可迅速做出其可靠性恰当的评价,可以降低研发成本、缩短研发时间。 一、试验目的 1通过理解内燃机可靠性评估,评定发动机的可靠性。 1.1了解评估的多种理论方法,如数学模型法、上下限法、相似设备法、蒙特卡洛法、故障分析( 包括故障模式影响分析和故障树分析) 等。并掌握故障分析法。 1.2学会可靠性试验评估,为进行可靠性设计奠定基础理论,为发动机及相关零部件提供测试、验证以及改进的技术支持。 2掌握可靠性试验方法 2.1掌握内燃机可靠性综合性试验及专项试验。综合性试验的考核对象是零件的可靠性、零件表面性状的变化和发动机性能的保持性;专项试验是超水温( 耐热性) 、超负荷、混合负荷、交变负荷循环、超爆发压力、超速等试验。 二、试验内容 1试验依据 参考的试验标准: GB /T 19055-2003 汽车发动机可靠性试验方法 GB /T 18297-2001 汽车发动机性能试验方法 JB/T 5112-1999 中小功率柴油机产品可靠性考核 2试验条件 一般试验条件: 2.1燃料及机油:采用制造厂所规定的牌号,柴油中不得有消烟添加剂。 2.2磨合:按制造厂规定的磨合规范进行。 2.3冷却系温度:水冷机的冷却液的出口温度控制在361 K±5K,必要时可减少温度允差。 2.4机油温度:按制造厂的规定或控制在368 K±5K,必要时可减少温度允差。2.5燃料温度:柴油温度控制在311 K±5K;汽油温度控制在298 K±5K。 2.6排气背压:按制造厂的规定或低于6.7 k Pa。 2.7发动机标准进气状态
汽车试验学总结
①第一阶段,从第一辆汽车的研制开始至福特公司建成的“汽车流水生产线”,汽车试验主要以研发性试验和道路试验为主,主要方法是操作体验和主观评价;②第二阶段,从福特公司建成全世界第一条汽车总装生产流水线至20世纪40年代,在此阶段,道路 试验得到了足够的重视,有实力的大公司开始建设汽车试验场,汽车试验由手工生产阶 段的操作体验、主观评价发展为仪器检测、客观评价;③第三阶段,从20世纪40年代至20世纪70年代,汽车试验技术进入一个新的发展时期,大量的基础性研究工作推动 了试验技术的发展,电子测量技术的应用在现代汽车试验中占有十分重要的作用,自20世纪60年代丰田公司创立精益生产方式开始,国际上有影响的大公司开始拥有自己 的汽车试验场;④第四阶段,20世纪70年代以后,汽车工业发展不仅保持了大规模、 多品种和高科技,而且出现了一些新的更科学、更合理的生产组织管理制度,汽车试验技术也得到了同步的提高和完善,电子计算机的应用对汽车试验起到了巨大的促进作用。 二、汽车试验的目的与分类: 1. 汽车试验的目的:是为了对产品的性能进行考核,使其缺陷和薄弱环节得到充分暴露, 以便进一步研究并提出改进弈剑,以提高汽车性能。 2. ①按实验目的分:研究型试验,新产品定型试验,品质检查试验; 3. ②按对象分:整车性能试验,总成试验,零部件试验; 4. ③按试验产所分:实验室台架试验,试验场试验,室外道路场地试验。 三、试验标准的分类 1. 国际标准:国际标准化组织ISO ( International Standards Organization )制定 2. 国际区域性标准:欧洲经济委员会ECE( Eco no mic Commissi on of Europe )和欧洲共同 体EEC ( European Economic Community) 3. 国家标准:我国国家标准简称GB;美国国家标准ANSI ( American National Standards Institute);日本国家标准简写JIS 4. 行业标准:我国汽车行业标准简写为QC,交通行业JT;美国汽车工程师学会SAE (Society of Automotive Engineer);美国《联邦机动车安全法规》FMVSS ( Federal Motor Vehicle Safety Sta ndards),是目前世界上最全面、最严格的汽车安全法规;日本汽车工程师协会JSAE ( Japanese Society of Automotive Engineer )制定的日本汽车工业通用标准JASO ( Japanese Automobile Standards Organization) 5. 企业标准:各汽车生产企业、汽车试验场,根据本身特点,参考相应国际、国家标准制定的,只限于本 企业内使用,通常企业标准严于国家标准和国际标准。 四、典型试验设备 1. 车速仪由第五轮、显示器、传感器、脚踏开关等组成;第五轮由轮子、齿圈、连接臂、安装盘组成。工 作原理:试验时,第五轮固定在试验车尾部或侧面,当第五轮随汽车运动而转动时,磁电传感器感受到齿圈的齿顶、齿谷的交替变化,并产生与齿数成一定比 例数量的电脉冲。脉冲数与汽车行驶距离成正比,脉冲频率与车速成正比。汽车行驶距 离与脉冲信号的比例关系是一常量,通常称之为“传递系数”。当显示器收到由传感器 传递过来的一定频率和数量的脉冲信号时,便自动与“传递系数”相乘得到相应的距离, 同时将距离与由晶体振荡器控制的时间相比得出车速,并显示、存储或打印出来;以上 过程,在试验中隔一定时间进行一次至试验结束,从而完成试验过程中车速、距离、时
汽车性能台架实
汽车性能台架实
————————————————————————————————作者:————————————————————————————————日期:
实验1 整车性能台架实验 1.1 实验目的与要求 1.1.1 实验目的 通过该实验的动手操作,要求学生掌握汽车整车台架实验的主要内容,熟悉汽车 台架测量部分评价指标的方法,并加深对汽车评价参数的理解。 1.1.2 实验要求 1)掌握汽车台架实验的方法和原理; 2)掌握相关设备的操作,了解其主要功用及构造; 3)对所得测数据进行分析,判断; 4) 撰写实验报告。 1.2 实验场地与设备: 1.2.1 场地 测量实验室一间 1.2.2 设备: 1)底盘测功机; 2)实验车一辆; 3)冷却风扇。 1.3 测功机构造与工作原理 1.3.1 构造 汽车底盘测功机主要由道路模拟系统、数据采集与控制系统、安全保障系统及引 导系统等构成。普通型道路模拟系统如图 l所示。 1.3.2 工作原理 由电涡流测功机结构图可知,感应子主要由旋转部分和摆动部分(电枢和励磁线圈)组成。转子轴上的感应子形状犹如齿轮,与转子同轴装有一个直流励磁线圈。 当励磁线圈组通以直流电流时,其周围便有磁场存在,那么围绕励磁组就产生一闭
合磁通。很明显,位于绕组左侧的感应子具有一个极性,右侧具有相反的极性。旋转时,由于磁密值的周期性变化而产生涡流,此涡流产生的磁场同产生它的磁场相互作用,从而产生与被试机反向的制动力矩,使电枢摆动,通过电枢上的力臂,将制动力传给测量装置。 转速测量采用非接触式磁电转速传感器和装于主轴的60齿牙盘,将转速信号转换成电信号输出。 1.4.1 实验内容与步骤 1.4.1 实验条件 环境温度:0-40°C;环境相对湿度小于85%;大气压力80-10kpa 1.4.2 实验车辆载荷 除有特殊规定外,轿车为规定乘员数的一半(取整数) 1.4.3 试验车辆应预热至正常工作温度,轮胎气压应符合汽车制造厂规定,左右轮胎 花纹应一致; 1.4.4 底盘测功机应进行预热; 1.4.5 记录环境温度等相关数据; 1.4.6 测量汽车各档位中车速和驱动力。 1.4.7 测量汽车各档位中车速与功率的数值 1.4.8 测量汽车某档位的外特性与部分负荷特性中功率与转矩的数值。
汽车球头销台架试验标准解读
前言 本标准以符合国家标准和行业标准为前提,在立足市场需求和产品性能的实际情况下指定的。同时在格式和内容编排上均符合GB/T1.1-2000和 GB/T1.2-2002规定。 本标准由XXXX机械有限公司提出 本标准由XXXX机械有限公司归口 本标准起草单位:XXXX机械有限公司 标准起草人:XXX
汽车球头销台架试验标准 1 范围 本标准规定了XX公司悬架使用的球销节(以下简称“球销总成”)的有关台架试验的方法和技术要求。 本标准适用于XX公司的所有汽车悬架球销总成。 2 规范性引用文件 下列文件中的条款通过标准的引用而成为本标准的条款。凡是注日期的引用文件,其随后的修改单(不包括勘误的内容)或修订版均不适合与本标准,然而,鼓励根据本标准达成协议的各方研究是否可以使用这些文件的最新版本,凡是不注日期的引用文件,其最新版本适用用本标准。 GB/T 7762-2003 硫化橡胶或热塑性橡胶耐臭氧龟裂静态拉伸试验 JIS K 6301 硫化橡胶的物理试验方法 3 目的 本标准的目的是使球销总成的性能、强度和耐久性试验的试验方法标准化,以便得到评定质量的统一方法。 4 试验种类 (1)摆角试验 (2)力矩试验 (3)刚度试验 (4)挤压和拉伸强度试验 (5)球头销静态强度试验 (6)疲劳强度试验
(7)工作温度下的耐磨持久性试验 (8)高温下的耐磨持久试验 (9)耐泥水持久性试验 (10)防尘罩耐臭氧试验 (11)防尘罩低温试验 (12)防尘罩耐热性试验 (13)防尘罩拉伸强度试验 5 试验的一般条件 试验条件一般适用于上面列举的所有试验,内容如下; (1)除非另有规定,试验应在常温常压下进行; (2)试验件应固定在刚度足够大的装置上,这样才不会消弱试验目的; (3)安装夹具的形状应不影响试验目的; 6 球销总成试验方法 6.1 摆角试验 这个试验是测量球销的工作摆角,按如下方法进行 6.1.1 试验装置 如图1所示,把销总成安装在试验夹具上 6.1.2 试验条件 测量方向:如图1所示,使球头销铅垂直立,沿A方向和A方向垂直的B方向进行测量。
(整理)发动机台架实验.
发动机台架试验 一、试验目的及作用 目的:1、掌握发动机试验方法。 2、 3、 4、根据数据分析发动机的工作状况,判断发动机性能,寻求最佳工况。 作用:发动机各项性能指标、参数及各类特性曲线都是在发动机试验台架上按规定的试验方法进行测定的。 二、试验对象 本田125cc发动机(排量:1.5L;最大功率:4.8kW;最大扭矩:3.8N·M) 三、试验设备 1.试验台装置(图1); 2.辅助装置:a、可调水量冷却系统 b、专用油量测量装置 c、通风装置 d、消声地 坑; 3.制动测功装置—测功器 (1)水力测功器(2)平衡式电力测功器(3)电涡流测功器
四、试验方法-试验条件要求 试验方法要求 1 进气 尽可能使用原车用的进气系统,改变进气系统时,注意以下参数不能变动:(1)进气管直径 (2)原车用中冷器压力降△p或根据指定值 (3)增压器压气机前的进气真空度<5kPa (4)曲轴箱通风系统符合发动机技术要求 2 排气 尽可能使用原车用的排气系统,如果涡轮后的条件有变化,须保持指定的排气背压(通常要求涡轮后排气背压≤10kPa,有特殊要求的除外)。 3 燃油输送 在试验过程中,喷油泵进油管中不允许有气泡;过量的燃油根据技术要求回流,输油管中不能出现压力波动。 4 冷却系统 (1)节温器阀固定在全开位置(有特别要求的除外)。 (2)试验间的冷却系统要保证原车用冷却液的流量和系统的压力。 5 附件设备 不安装或全部脱开(有特别要求的除外)。 6 试验用油 按照技术要求选择,燃油的密度变化应小于参考值的±0.6% 。
测试条件要求 1 大气状况 从试验开始,至少每小时测量一次大气压力和进气湿度。 2 温度控制 (1)压气机前的进气温度25℃(国家标准的标准进气状态) (2)喷油泵进口的燃油温度38±2℃ (3)出水温度88±5℃(国家标准)。 (4)中冷后温度(全负荷工况): ?标定转速:49±2℃?最大扭矩转速:40±2℃ ?45%标定转速:37±2℃? 900r/min(或者低端转速):33±2℃ 3 在稳定状况下测量 在每个测量点,记录数据前,要保证所有的参数达到稳定。 五、试验时间及地点 时间:四月初(具体时间待定) 地点: 麓谷发动机台架试验室 六、试验人员 司明鑫、危红媛、季武威、赵吉瑞、夏涛 七、实验内容(GB/T 18297-2001 汽车发动机性能试验方法 1.规定了汽车用发动机性能台架试验方法,包括各种负荷下的动力性及经济性试验方法,无负荷下的起动、怠速、机械损失功率试验方法以 及有关气缸密封性的活塞漏气量及机油消耗量试验方法。 2.对主要测试仪表的精度要求 ?扭矩:误差不大于所测发动机最大扭矩的±1% ?转速:误差不大于所测值的±0.5% ?燃油消耗量:误差不大于所测值的±) 1.发动机负荷特性实验 1.实验目的: 1.掌握发动机负荷特性的试验方法 2.熟悉所用设备、仪表 3.学会数据采集整理以及绘制曲线 4.判断发动机性能,并应用 2.实验原理:保持发动机转速不变的情况,通过改变发动机负荷得到的发动机性能,包括油耗、功率、排气温度等参数。在规定的转速、不同的负荷下评定
汽车球头销台架试验标准
、尸■、■ 前言 本标准以符合国家标准和行业标准为前提,在立足市场需求和产品性能的实际情况下指定的。同时在格式和内容编排上均符合GB/T1.1-2000 和GB/T1.2-2002 规定。 本标准由XXXX 机械有限公司提出本标准由XXXX 机械有限公司归口本标准起草单位:XXXX 机械有限公司标准起草人:XXX
汽车球头销台架试验标准 1 范围 本标准规定了XX 公司悬架使用的球销节(以下简称“球销总成” )的有关台架试验的方法和技术要求。 本标准适用于XX 公司的所有汽车悬架球销总成。 2 规范性引用文件 下列文件中的条款通过标准的引用而成为本标准的条款。凡是注日期的引用文件,其随后 的修改单(不包括勘误的内容)或修订版均不适合与本标准,然而,鼓励根据本标准达成协议的各方研究是否可以使用这些文件的最新版本,凡是不注日期的引用文件,其最新版本适用用本标准。 GB/T 7762-2003 硫化橡胶或热塑性橡胶耐臭氧龟裂静态拉伸试验 JIS K 6301 硫化橡胶的物理试验方法 3 目的 本标准的目的是使球销总成的性能、强度和耐久性试验的试验方法标准化,以便得到评定 质量的统一方法。 4 试验种类 (1)摆角试验 (2)力矩试验 (3)刚度试验
(4)挤压和拉伸强度试验 (5)球头销静态强度试验 6)疲劳强度试验 7)工作温度下的耐磨持久性试验 (8)高温下的耐磨持久试验 (9)耐泥水持久性试验 (10 )防尘罩耐臭氧试验 (11 )防尘罩低温试验 (12 )防尘罩耐热性试验 (13 )防尘罩拉伸强度试验 5 试验的一般条件 试验条件一般适用于上面列举的所有试验,内容如下; (1)除非另有规定,试验应在常温常压下进行; (2)试验件应固定在刚度足够大的装置上,这样才不会消弱试验目的; (3)安装夹具的形状应不影响试验目的; 6 球销总成试验方法 6.1 摆角试验 这个试验是测量球销的工作摆角,按如下方法进行 6.1.1 试验装置 如图 1 所示,把销总成安装在试验夹具上 6.1.2 试验条件 测量方向:如图 1 所示,使球头销铅垂直立,沿 A 方向和 A 方向垂直的 B 方向进行测量
汽车试验第十章 汽车室内台架试验系统
第十章汽车室内台架试验系统 汽车室内台架试验的特点是精度高、试验不受室外环境条件的影响,因此实验效率高、实验结果的重复性好。室内台架试验系统不仅可以进行机构、总成及零部件试验,如发动机、变速器、悬架装置等的性能和它们的结构强度、刚度、疲劳寿命、耐久性等,还可进行整车性能试验,如动力性、经济件、制动性、操纵稳定性、平顺性等。 第一节汽车整车性能室内台架试验系统 汽车性能只有在运行的过程中才能体现出来,为此要想在室内进行整车性能试验,就必须让汽车运行起来。然而,将试验道路建在室内不太现实,为此常利用转鼓替代汽车行驶的路面,即转鼓试验台,又称汽车底盘测功机,是汽车在室内进行整车性能试验最基础的设备。 一、汽车底盘测功机的结构型式 汽车底盘测功机有单鼓、双鼓、二轮转鼓和四轮转鼓等多种不同的结构型式,如图10-1、图10-2图10-3和图10-4所示。双鼓式汽车底盘测功机其转鼓直径较小,大多在φ300mm~φ500mm之间;单转鼓式汽车底盘测功机的转鼓直径较大,目前转鼓直径最大的汽车底盘测功机,其转鼓直径达φ6300mm;转鼓直径最小的单鼓式汽车底盘测功机,其转鼓直径通常也在φ500mm以上。 图10-1 二轮单鼓图10-2 二轮双鼓 图10-3 四轮单鼓图10-4 四轮双鼓汽车底盘测功机的结构型式和转鼓直径的大小对实验精度有很大影响。要想获得高精度的测试结果,常采用大直径的单转鼓式汽车底盘测功机。其原因是:当转鼓直径D远大于汽车车轮直径d时,车轮在转鼓上行驶的动力学特征与在道路上行驶时的动力学特征十分接近,即转鼓曲率对测试精度的影响非常小。理论和实践都表明,当转鼓直径达到6m以上时,转鼓曲率对测试结果的影响几乎可以完全忽略不计;若继续增大转鼓的直径,对测试精度的贡献已微乎其微,但设备的制造成本却会大幅上升。正因为如此,在进行高精度汽车动力性和经济性试验时,多采用大直径单鼓式汽车底盘测功机,尤其是大直径四轮单鼓式汽车底盘测功机。即便是对于单轴驱动的汽车亦是如此,因为四轮转鼓能准确再现汽车行驶时的滚动阻力。由于大直径单鼓式汽车底盘测功机的体积庞大、制造成本因转鼓直径的增大而大幅提高,因此,对于滚动阻力的大小对测试结果不构成明显影响的试验项目,如汽车噪声、排放、行驶可靠性与耐久性等试验项目则通常采用体积小、制造成本较低的双鼓式或转鼓直径相对较小的单鼓式汽车底盘测功机。 对于双鼓式汽车底盘测功机,由于转鼓直径不可能做得很大,因此转鼓曲率对测试结
汽车发动机台架标定全程讲解
汽车发动机台架标定全程讲解 概述:发动机台架标定作为ECU标定的第一步,通过进气模式、扭矩模型、喷油点火等标定来最大程度的发挥发动机的性能,是整车标定的基础。 一.台架标定核心工作45天: ●VVT选择 ●点火角标定 ●温度模型标定 ●扭矩模型标定 ●VVT VE标定 ●爆震控制 ●外特性 ●万有特性 二:标定手段 ●控制油门:PUMA设备直接调节. ●控制发动机转速:PUMA设备直接调节. ●控制平均缸内压力:PUMA工具可设置油门开度为100%,即可通过调节标定 改变缸内压力. ●控制点火角:即可通过设置SprkAdvSlewValue改变点火提前角度数. ●控制空燃比:通过设置FUEL.SlewValue改变点火提前角度数. ●控制VVT开度:设置Intk_DsrdPstn.mode=1即可. 三.发动机改造及台架搭建:2天 ●4个进气歧管温度热电偶、4个排气歧管热电偶、1个催化器中心热电偶. ●进气压力传感器(发动机自带)、空滤前压力传感器、节气门前压力传感器、 排气背压传感器. ●油耗分析仪、空燃比检测仪(ES630).
●开发电脑、ES590 592. ●燃烧分析仪,缸压信号. ●示波器采集58X,凸轮轴信号、喷油信号、点火信号、爆震传感器信号. ●测功机、油门踏板和PUMA设备. ●废气分析仪. ●台架搭建:线束改造、发动机安放. 四:数据准备:0.5天 ●Engine dyno disable function 因在台架上进行试验,缺少整车上的必要线束、 传感器等,为保证正常标定,需关闭ECU的部分诊断功能. ●关闭误报的各种EOBD故障码. ●关闭闭环控制长期自学习值. ●关闭碳罐控制. ●COT 关闭. ●PE关闭. ●DFCO关闭. ●关闭失火诊断. ●关闭Baro预测. ●设置VVT开度. 五:台架标定: 1.1第一次外特性和信号一致性检查 目的: ●检验原始发动机是否接近工程目标 ●检查4缸一致性 方法: ●根据扭矩特性,选择标定最佳VVT开度. ●根据扭矩特性,选择最佳空燃比. ●根据扭矩特性,选择最优点火角. ●节气门全开工况,从1200rpm开始,每隔400rpm,稳定一定时间(如15S)采 数,直到6000rpm. 数据处理: ●根据外特性数据,作出最大扭矩、最大功率、最小比油耗值曲线 1.2各缸排温一致性检查:
汽车检测实验报告
学生实验报告 (理工类) 课程名称:汽车检测诊断技术专业班级: 学生学号:学生姓名: 所属院部:指导教师:诸鑫瑞 20 14 ——20 15 学年第一学期 金陵科技学院教务处制
实验项目名称:发动机点火系次级电压波形检测实验学时: 2 实验地点:汽车电控技术实验室实验成绩: 一、实验目的和要求 1、了解金德K81,KT600汽车诊断仪的结构; 2、熟悉桑塔纳2000GSi发动机,别克君威2.5发动机,雪佛兰乐风1.4发 动机点火系统工作原理; 3、掌握利用K81, KT600汽车诊断仪检测发动机次级电压波形的方法。 二、实验仪器和设备 1、桑塔纳AJR发动机台架一套,别克君威2.5发动机台架一套,雪佛兰乐 风汽车一辆; 2、金德K81故障分析仪一套,KT600故障分析仪两套; 3、数字万用表三个; 4、常用工具三套。 三、实验原理 通过测试点火次级陈列波形,可以有效地检查车辆的行驶性能。 该波形主要是用来检查短路或开路的火花塞高压线以及由于积碳而引起的 点火不良的火花塞。 由于点火次级波形明显地受到各种不同发动机、燃油系统和点火条件的影响,所以它能够有效地检测出发动机机械部件和燃油系统部件以及点火系统部件 的故障。 并且,一个波形的不同部分还分别能够指明在发动机所有气缸中的哪个部件 或哪个系统存在故障。 桑塔纳2000GSi轿车点火系统的技术数据如表1所列。 表1 桑塔纳2000GSi点火系技术数据表
桑塔纳2000GSi 具有两个点火线圈的双火花点火系。 插头端子如图1所示: 图1 点火线圈4针插头 四、实验过程 以检测桑塔纳2000GSi 发动机次级点火波形为例,讲述实验步骤: 1、将K81或KT600诊断仪连接电感夹,桑塔纳2000GSi 轿车为两个点火线圈的双火花点火系,需两组电感夹,一组连接诊断仪CH1 端口,一组连接诊断仪CH2 端口,一个单独电感夹连接诊断仪CH3端口。 2、一组电感夹同时夹住1,3缸点火线圈与火花塞间高压线路,另一组电感夹同时夹住2,4缸点火线圈与火花塞间高压线路,单独的电感夹夹住1缸高压线作为判缸信号。 3、起动发动实验台架,预热到冷却水温C 80。 4、据车型,选择数据接口,选择国产电喷车系专用接插件(插头)与主机电缆相连接,并插入诊断座内。 5、K81或 KT600诊断仪接通电源,屏幕会依次自动显示欢迎菜单。 6、根据屏幕提示选择第二项波形分析。 7、根据屏幕提示选择点火系统波形分析,并选择次级电压波形分析。 8、根据屏幕提示进入设置选项,根据桑塔纳2000GSi 轿车点火系统的技
汽车发动机台架试验的研究
汽车发动机台架试验的研究 摘要: 发动机台架试验就是指对发动机进行一系列的试验, 对试验过程出现的问题进行系统分析, 不断优化处理, 从而不断提高发动机的性能与可靠性。本文阐述了发动机台架试验的目的及相关的试验类型, 并对试验中遇到的问题进行了分析, 并提出了解决的办法。 关键词: 发动机;台架;试验;研究; 1 进行发动机台架试验的目的 发动机台架试验对处于不同研发阶段的发动机进行相关测试, 并为其优化改进提供试验数据支持, 发动机台架试验的目的概括来说主要有以下是三个目的。 (1) 对新研发的试制样机进行测试。一款新研发的发动机, 当试制样机组装完成后, 会对发动机整体性能进行测试, 并对试验中出现的问题进行分析、解决, 该阶段的试验可以说是对发动机的整体性、系统性进行测试, 一些大的缺陷会在该阶段中暴露出来。 (2) 对发动机重要零部件进行性能及可靠性试验。发动机中不同机构的零部件的工作性能影响了发动机的整体可靠性, 在台架试验中需要对发动机重要零部件的材料、结构、工况情况进行长时间试验, 来验证相关重要零部件的性能及可靠性。 (3) 发动机的可靠性不是短时间的试验就能测试出来的, 试制样机研发经过初步的台 架试验对发动机进行完善后, 还需要对发动机在满负荷、长时间运行下的可靠性进行试验。 2 发动机台架试验连接方式 根据发动机动力输出方式的不同, 在发动机台架试验中分为硬连接和软连接两种试验方法。 2.1 硬连接 硬连接就是把发动机的飞轮经过连接盘、连接轴及缓冲胶直接与台架上的测功机相连接。硬连接的优点在于功率损失少, 试验所测得值更加接近发动机实际输出功率, 硬连接应用范围广, 几乎可以在所有发动机机型中应用;缺点在于不能真实反映出整车环境。 2.2 软连接 软连接就是首先在发动机上连接变速器, 再在变速器的输出端通过连接轴和测功机连接, 这种连接方式只在后驱发动机台架试验中用到。软连接因为发动机和测功机之间加装了变速箱, 变速箱在传递功率过程中不可避免的会造成能量的损失, 所以测功机测出的功率