应力计算规定
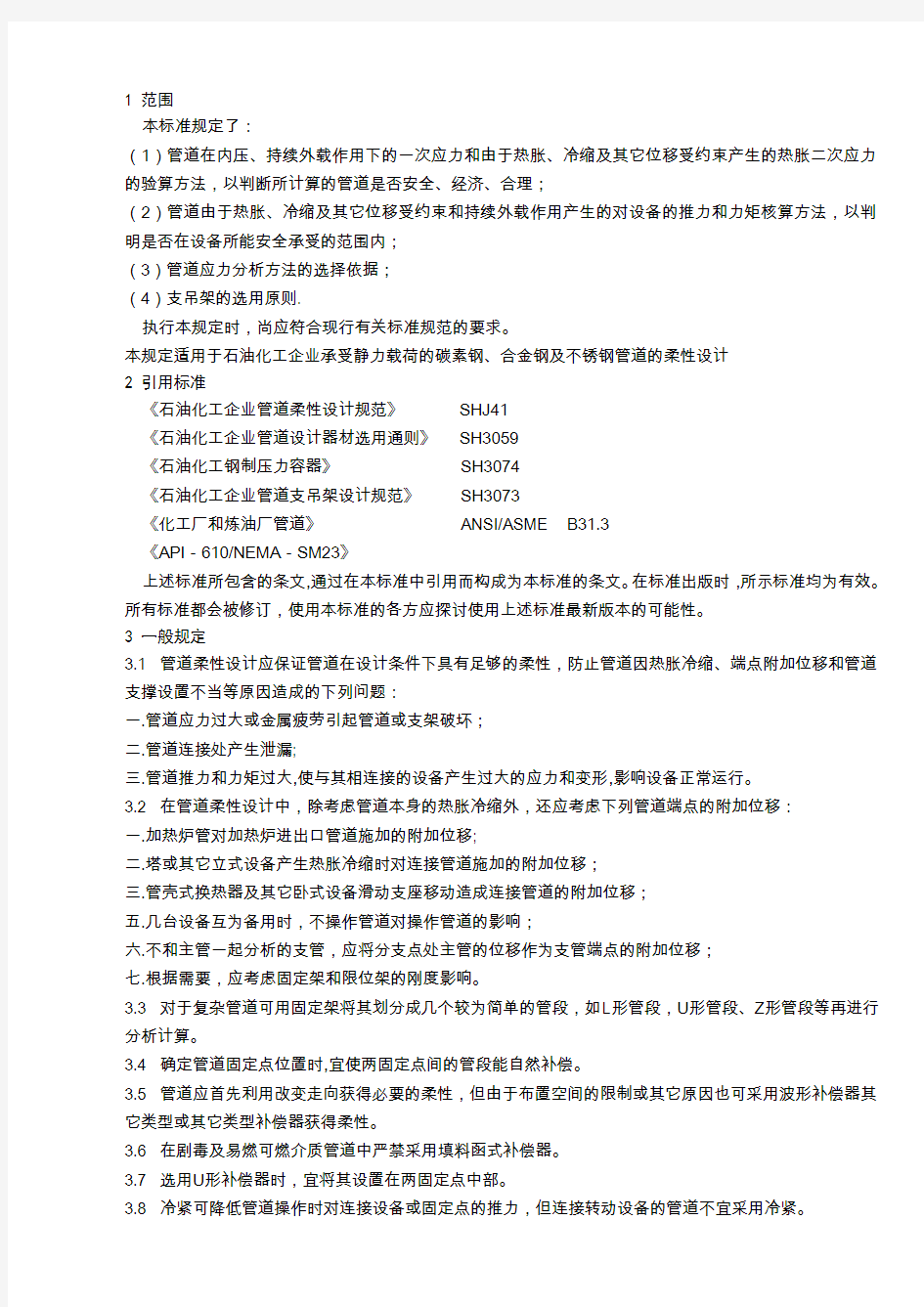

1 范围
本标准规定了:
(1)管道在内压、持续外载作用下的一次应力和由于热胀、冷缩及其它位移受约束产生的热胀二次应力的验算方法,以判断所计算的管道是否安全、经济、合理;
(2)管道由于热胀、冷缩及其它位移受约束和持续外载作用产生的对设备的推力和力矩核算方法,以判明是否在设备所能安全承受的范围内;
(3)管道应力分析方法的选择依据;
(4)支吊架的选用原则.
执行本规定时,尚应符合现行有关标准规范的要求。
本规定适用于石油化工企业承受静力载荷的碳素钢、合金钢及不锈钢管道的柔性设计
2 引用标准
《石油化工企业管道柔性设计规范》SHJ41
《石油化工企业管道设计器材选用通则》SH3059
《石油化工钢制压力容器》SH3074
《石油化工企业管道支吊架设计规范》SH3073
《化工厂和炼油厂管道》ANSI/ASME B31.3
《API-610/NEMA-SM23》
上述标准所包含的条文,通过在本标准中引用而构成为本标准的条文。在标准出版时,所示标准均为有效。所有标准都会被修订,使用本标准的各方应探讨使用上述标准最新版本的可能性。
3 一般规定
3.1 管道柔性设计应保证管道在设计条件下具有足够的柔性,防止管道因热胀冷缩、端点附加位移和管道支撑设置不当等原因造成的下列问题:
一.管道应力过大或金属疲劳引起管道或支架破坏;
二.管道连接处产生泄漏;
三.管道推力和力矩过大,使与其相连接的设备产生过大的应力和变形,影响设备正常运行。
3.2 在管道柔性设计中,除考虑管道本身的热胀冷缩外,还应考虑下列管道端点的附加位移:
一.加热炉管对加热炉进出口管道施加的附加位移;
二.塔或其它立式设备产生热胀冷缩时对连接管道施加的附加位移;
三.管壳式换热器及其它卧式设备滑动支座移动造成连接管道的附加位移;
五.几台设备互为备用时,不操作管道对操作管道的影响;
六.不和主管一起分析的支管,应将分支点处主管的位移作为支管端点的附加位移;
七.根据需要,应考虑固定架和限位架的刚度影响。
3.3 对于复杂管道可用固定架将其划分成几个较为简单的管段,如L形管段,U形管段、Z形管段等再进行分析计算。
3.4 确定管道固定点位置时,宜使两固定点间的管段能自然补偿。
3.5 管道应首先利用改变走向获得必要的柔性,但由于布置空间的限制或其它原因也可采用波形补偿器其它类型或其它类型补偿器获得柔性。
3.6 在剧毒及易燃可燃介质管道中严禁采用填料函式补偿器。
3.7 选用U形补偿器时,宜将其设置在两固定点中部。
3.8 冷紧可降低管道操作时对连接设备或固定点的推力,但连接转动设备的管道不宜采用冷紧。
3.9 对于材料在蠕变温度下(碳素钢380℃以上,低合金钢420℃以上)工作的管道,冷紧比(即冷紧值与全补偿值的比值)宜取0.7。对于材料在非蠕变温度下工作的管道,冷紧比宜取0.5。冷紧有效系数:热态取2/3,冷态取1。
3.10 作用于管道中间固定点和机泵上的载荷,应考虑滑动支架的摩擦力影响,摩擦系数应按表1选取。
3.11 当管道用吊杆或弹簧吊架支撑时,可不考虑摩擦力的影响。
3.12 对与汽轮机、离心压缩机等设备连接的管道,布置支吊架时应使设备接管承受的载荷为最小。
3.13 往复式压缩机和往复泵的进出口管道除应进行柔性设计外,还应考虑流体压力脉动的影响。
4 计算参数的确定
4.1 计算温度
管道柔性分析和应力计算时应根据不同的环境和工艺条件采用不同的计算温度:
4.1.1 安装温度(环境温度)应取20℃。
4.1.2 对一般工艺管道和公用工程管道应取管道表中的介质温度;
4.1.3 对蒸汽伴热管道应取工艺介质温度;
4.1.4 对管道夹套应取工艺介质和伴热介质中温度较高者;
4.1.5 对需要蒸汽吹扫的管道,当工艺介质温度低于吹扫蒸汽温度时,应取吹扫蒸汽温度;
4.1.6 对不保温管道,当介质温度低于38℃时应取介质温度;当介质温度等于或高于38℃时,应取介质温度的95%;
4.1.7 对衬里管道,壁温应取150℃。
4.1.8 对于低温操作但又需蒸汽吹扫的管道,应分别按低温和吹扫温度进行计算。
4.1.9 对于无介质管道(如备用泵的连接管道)的温度取值:
4.1.9.1 保温管道取50%的操作温度。
4.1.9.2 非保温管道取安装温度。
4.1.9.3 蒸汽伴热管道取设计温度的70%。
4.1.10 备用的泵暖管道取设计温度的70%。
4.2 计算压力
4.2.1 管道柔性计算压力应取管道设计压力。
4.2.2 当管道在不同操作条件下运行时,应取其最苛刻的压力温度组合。
4.3 许用应力
4.3.1 对临时(或短时)条件下的许用应力应按规定增加。例如,当由于压力、重量和其它持续载荷所产生的一次应力,加上风载或地震载荷所产生的应力之和,可以达到许用应力的1.33倍.
4.3.2 对许用应力超过屈服强度2/3的管道材料(如奥氏体不锈钢18-8和某些镍合金)、铸铁或其它无延展性的管道材料,则不能增加许用应力。
常用的许用应力值见附录A。
4.4 弹性模量
4.4.1 常用材料的弹性模量按附录C选取;
4.5 线膨胀系数
常用材料的线膨胀系数按附录B 选取。 4.6 基本许用应力修正系数
常用材料的焊缝系数按附录F 选取; 4.7 管道单位长度重量 4.7.1 管子重量按附录E 选取;
4.7.2 管内输送介质重量在未提供数据的情况下,可按下述原则选用: 一.对液体管道,按充满管道容积的介质重量计算。
二.对气体管道,应考虑气体凝结在管道中的填充量,计算方法如下: DN100以下的管道,按充满管道截面的20%计算; DN100~500范围内,按充满管道截面的15%计算; DN500以上的管道,按充满管道截面的10%计算。 4.8 集中载荷 4.8.1 安全阀反力。 4.8.2 调节阀推力. 4.8.3 风载荷. 4.8.4 地震载荷. 5 柔性分析方法的确定 5.1 柔性分析方法的选择原则
在确定柔性分析方法以前,应对所分析的管道进行分级,以便确定相应的分析方法。按照管道的操作条件和管径,进行柔性分析时一般分为三级: A 级:凭工程经验进行判断。
B 级:用简化方法进行判断,简化方法确定为ANSI B31.3 第319.4.1条式(19)的判断式。
C 级: 用计算机进行详细分析,计算软件确定为CAESAR -II 4.0 下列管道宜进行详细分析:
一.进出加热炉及蒸汽发生器的高温管道; 二.进出汽轮机的蒸汽管道;
三.进出离心压缩机、透平鼓风机的工艺管道; 四.进出高温反应器的管道; 五.温度超过400℃的管道;
六.贵重金属管道(如钛合金和哈氏合金等); 七.含有波纹管膨胀节的管道; 八.夹套管。
5.2 管道热胀及其补偿 5.2.1 管道热胀量的计算
设有一直管段,由常温20℃升到T ℃时,该管段将沿轴向膨胀,其热胀量可按式(1)或式(2)进行计算: ??t t L T =?α (1)
?t t L e =? (2) 式中 ?t —管段的热胀量,mm 。
L —管段的长度,mm 。
αt —管材的线膨胀系数,由20℃升至T ℃的每mm 温升1℃的平均线膨胀量,mm/mm ?℃ e t — 单位线膨胀量,由20℃升至T ℃的每mm 线膨胀量,mm/mm 。(见附录B)
?T —管段的温升,℃。
当管道为空间任意走向时,管道受热膨胀后将沿着两固定点的连线方向膨胀,其计算公式为: ?t =U ?αt ??T =U ? e t (3) 式中 U 为两固定点间的距离。
当计入两固定点的附加位移时,膨胀量计算公式为: ?t =()()()???X Y Z t t t 222++ (4) 式中?X t =∑L X ?e t +∑(?X GA +?X GB ) ?Y t =∑L Y ?e t +∑(?Y GA +?Y GB ) ?Z t =∑L Z ?e t +∑(?Z GA +?Z GB )
?X GA 、?Y GA 、?Z GA —A 固定点的附加位移,mm 。 ?X GB 、?Y GB 、?Z GB —B 固定点的附加位移,mm 。 5.2.2 管道的热补偿 5.2.2.1自然补偿
自然补偿是利用管道自然的弯曲形状所具有的柔性来补偿自身的热胀和端点位移,例如π型补偿器等。管系的弹性与管系的形状有密切管系,尤其与管系的展开长度增加成正比。下面从平面和空间典型管系布置说明自然补偿的原则: 一.平面管系
若要增加平面管系的弹性,必须增加远离固定点连线的管道长度,并且不能布置成锯齿型。现以L 型管系为例说明平面管系的布置与柔性的关系:
图1
图中,假定(a)管系不能自然补偿,则:
(b)、(c)两管系均能自然补偿。这是因为这两个管系增加了远离固定点连线的管子长度,且用增加?Y 的长度来吸收?X 的热胀量;
(d)、(e)两管系也可能满足自然补偿,但效果不如(b)、(c)两管系。这是因为它们未明显满足远离固定点连线的原则;
(f)、(g)两管系的柔性相对(a)管系来说没有增加远离固定点的长度,所以补偿能力没有改变;
(h)、(i)两管系补偿能力比(a)管系更差。这是因为虽然增加了一些远离固定点连线的长度,但管系在X、Y 管段坐标方向上的投影长度差值较大,因而管系自然补偿能力下降较大。
二。空间管系
增加管系的柔性,应增加L/d的值(L为固定点之间的展开长度,d为固定点之间的距离),并且不能布置成锯齿型. 一般是在远离端点连线的方向增加管子长度, 并使图形接近正方体, 如下图所示:
图2
图中,假设(a)管系不能满足自然补偿,则:
(b)管系由于增加了远离固定点连线的距离,自然补偿能力有所增加;
(c)管系由于增加了远离固定点连线的距离,并且比(b)管系更接近正方形,所以补偿能力更强;
(e)管系由于在长轴方向增加了长度,补偿能力有所加强,但效果不如(b)、(c)两管系理想;
(d)管系由于没有增加远离固定点连线的距离,并且管系沿各坐标轴方向的管段长度的差值更大,所以补偿能力比(a)管系还差。
5.2.2.2波纹管补偿器
利这种补偿方式是用波纹管补偿器的柔性来吸收管系的线位移和角位移. 常见的波纹管补偿器有单式、复式、铰链型和压力平衡型等。当自然补偿不能满足要求时,需采用这种补偿方法,其具体的布置方案和计算方法详见《波纹管补偿器的结构形式及计算方法》。
5.2.2.3冷紧
冷紧也是自然补偿的方法之一。冷紧(预拉伸)是指在安装时使管系产生一个初始位移和初应力的一种方法,其目的是改善和平衡冷热态时管道的受力状况,降低管道对设备嘴子和支架的推力.冷紧一般用冷紧量与全位移量的百分比来表示(也称为冷紧比),如100%冷紧,50%冷紧等.由于安装时预拉伸不易与设计量完全一致,故规定有效预拉伸量只考虑实际拉伸量的2/3. 冷紧后虽然应力降低了,但是应力范围并没有改变.
冷紧口的位置选择应注意冷紧后的效果,使热胀的应力和推力都降低。最终闭合口应选择在便于施工的地方,以及管系弯矩较小处。闭合口的就位不得使接口产生额外的扭转或偏移。
对于多分支管道,各分支管道的冷紧值,应根据节点的位移和各分支的柔度而定。冷紧口可以分散各分支管内,也可以集中在部分分支管段内。
对于垂直管段上的冷紧口,在管道设计时应按照管系柔性计算的结果,分别在图上注明向上、向下和左右前后的方向及冷紧值,以免在施工中造成方向性的错误。对于向下的冷紧值,可采用放长支吊架拉杆的办法。为此,支吊架拉杆的长度和丝扣的加工长度,都应考虑冷紧位移的可调幅度。
对于水平管段上的冷紧口,由于局部水平位移比较大,设计、安装时应使支吊架拉杆长度在冷热态的偏斜度均不超过允许值,以免对管系造成过大的水平分力。 在任何情况下,都应该是在冷紧之后才能使弹簧支吊架受力。
对于中间无约束的两固定端的管道,考虑冷紧后产生的推力计算式为:
(5)
式中 R m —在最高或最低设计温度下的瞬时最大推力; R —按全补偿值及 E a 为计算基础的推力;
C —冷紧比。无冷紧时C =0,100%冷紧时C =1; E m —最高或最低设计温度下的管材弹性模量,MPa; E a —安装温度下管材的弹性模量。 5.3 ANSI 简单判断法
在装置设计过程中,所有的应力问题若都用计算机处理是很不经济的,实际上装置中大部分的一般管道已具有较好的柔性,同时在现场施工时未必有良好的计算机环境。因此,用简化方法迅速对一些管道进行安全性判断就显得非常重要了。简化方法虽然不精确,但对于有经验的设计师来说,借助它来对整个管系进行判断一般也可以满足要求。
所谓简化方法是相对于基于严格数学力学的详细分析方法而言的,而在简化方法中省略掉的因素(如自重等),在实际情况中都是相当重要。而且简化方法所能应用的管系几何形状也有所限制,一般只适用于无分支的管系的二次应力验算。
管系的走向千差万别,用简化方法计算的结果产生的误差无法用简单的数学方法进行估计。 由于简化方法的局限性,一般在下列情况下不宜采用: ⑴与要求苛刻的设备(如高速旋转的动设备)相连的管道; ⑵在高温下输送危险介质的管道; ⑶大管径薄壁管道; ⑷价格昂贵的合金钢管道; ⑸停工频繁的管道。
上述的限制是原则性的,对于具体的问题,尚应根据具体情况从强度要求、推力要求、介质情况和经济性等方面做出判断,因为有些问题是相对的。例如对于输送危险介质的管道,其重要程序既与介质本身性质有关,也与操作条件、管道的位置有关。同样的一种烃类介质,在操作温度接近和超过其闪点时就认为该管道是重要管道,需进行详细分析,而当操作温度远低于介质闪点时,该管道就可以当做一般管道对待,管系的布置方式也影响简化方法的选择。当管系中主要的直管段距离过固定点的推力线太近时,不宜采用简化方法。应注意的是,简化方法一般不给出端点反力。如果某些简化方法的结果中含有反力时,此反力均未包括自重 摩擦力等对反力的影响,应人工加以修正。
当管道分级为B 时应用ANSI B31.3的简单判断式进行判断,满足该判断式的规定则说明管系有足够
R R C E E m m
a =-()123
的柔性,热膨胀和端点位移所产生的应力在许用范围内,可不再进行详细计算。这种判断结果是偏安全的。对价格昂贵的合金钢管系可能还需进行详细计算,使在确保安全的前提下设计出最经济的管系。
在使用简化方法时,一定要注意简化方法的使用条件。应用ANSI 这一判断式的管系必须满足如下假定:
⑴管系两端为固定点;
⑵管系内的管径、壁厚、材质均一致; ⑶管系无支管和支吊架;
⑷管系使用寿命期间的冷热循环次数少于7000次。 ANSI 的判断公式为:
(6)
式中 DN ——公称直径,mm; Δ——管系总变型量,mm;
L ——管系在两端固定端之间的展开长度,m; U ——管系两端固定点之间的直线距离,m 。 此式不适用于下列管道:
(1)循环次数大于7000次,有疲劳危险的管道; (2)端点附加位移量占总位移量大部分的管道;
(3)L/U > 2.5的不等腿U 型弯管管道,或近似直线的锯齿型管道。
5.4 CAESAR 的应用
当管道分级为C 或符合第5.1条规定时,应使用CAESAR 4.0进行详细应力解析。使用CAESAR 时的输入和输出要求详见LW-4023-1997。
6.管子壁厚的确定
6.1总则
6.1.1 直管段压力设计的最小壁厚根据式(7)确定: t m =t+c (7) 式中:
t m = 最小要求厚度,包括加工、腐蚀侵蚀余量。 t = 压力设计厚度,对内压按式(8)计算。 c = 加工余量(螺纹或沟槽深度)加腐蚀侵蚀余量。
对有较大集中载荷或管道支撑跨度较大时,直管段定货厚度应通过详细应力分析确定。 6.1.2 直管段压力设计厚度计算公式使用以下术语: d = 管道的内径。
D L U N ?-≤?
().2
2083
D = 管道的外径。 P = 内设计压力(表压)。
E = 焊缝系数。
S = 材料在设计温度下的许用应力。
Y = 由表2查出的系数,当t
d = 管道的内径。 D = 管道的外径。
表2 系数Y 取值(t 6.2 内压作用下的直管段 6.2.1当t t = (8 ) 也可用式(9)、(10)、(11)替代式(8): (9) (10) (11) 6.2.2 当t>=D/6或P/(SE )>0.385时,直管段压力设计的壁厚计算要求特殊考虑,如强度理论、失效影响及热应力。 7.应力验算 7.1一次应力验算 一次应力验算通常包括两个部分: 内压产生的折算应力验算 PD SE PY 2() + t PD SE = 2 t D SE P SE P = --+(()/()) 12 t P d c SE P Y = +--() (() 221 管道在承受内压时,管壁上的三个主应力为内压周向应力、内压轴向应力和内压径向应力。其中内压周向应力σzx 最大,内压径向应力σjx 最小。根据第三强度理论,其当量强度为 σzx -σjx ≤[σ]t j (12) 即 P[D w -(S-C)] 2η(S-C) 式中: P=设计压力,MPa ;Dw=管子外径,mm ;η=基本许用应力修正系数;C=壁厚附加量,mm ;S=管子的计算壁厚,mm ;[σ]t j =设计温度下材料的基本许用应力,Mpa. 这个公式与内压壁厚公式是一致的。实际上,只要采用的管子壁厚不小于管子的计算壁厚,自然就能满足这个验算条件的要求。 内压轴向应力和持续外载应力的验算 这是管道在工作条件下的应力状况,这时管壁上的三个主应力仍为周向应力、轴向应力和内压径向应力。其中,轴向应力包括内压轴向应力σzhp 、持续外载轴向应力σzhw 和持续外载当量应力σw 。用公式表达为 (σzhp +σzhw +σw )- σjx ≤[σ]t j (13) 即 P(D w -S) 4S 由于一次应力没有自限性,所以上式必须满足,才能保证管道最基本的安全。 7.2二次应力验算 二次应力产生的破坏,是在反复交变应力作用下引起的疲劳破坏(属于高应力低周期的疲劳),而其初应力往往超过屈服极限σS ,从而引起塑性应变。所以对于二次应力的限定,是采用许用应力范围和控制一定的交变循环次数,而许用应力范围的目的就是限制发生过量的塑性变形。 如果热胀和其它位移受约束而产生的应变还没有达到材料的屈服极限,并且管道又没有进行冷紧,此应变在全热态;若管道进行了100%的有效全冷紧,则此应变又全在冷态;若进行了50%的有效冷紧,则此应变一半在热态,一半在冷态。如果热胀产生的初应力相当大时,在热态就会由于屈服、蠕变和应力松弛而使应力降低下来,但是降低的量很难确定。热应力降低的地方,就会产生反方向的应力,这种现象称为自拉,其效应与冷紧相类似。但不管热应力如何变化,热胀应力范围是基本不变的。所以冷紧不会影响应力范围。因为管系在热态或在冷态的实际应力的大小很难通过计算得出,所以二次应力的判定也就难以用一个应力水平来进行。 管道材料在热态和冷态所能维持的安全应力水平(包括一次和二次),可分别由材料在热态和冷态下的强度条件和疲劳条件来确定: 冷态:取疲劳强度 0.5σb ; 热态:取高温强度 因此,一次应力S 1和二次应力S 2在冷态和热态的最大应力范围为: 0.5σb + σ s t ≤ [σ]t j +σzhw +σw ≤[σ]t j σs t 也可写成 1.5([σ]j+[σ]t j) 在考虑一定的安全裕量后为: 1.25([σ]j+[σ]t j) 即安全条件为 S1+ S2 ≤1.25([σ]j+[σ]t j) (14) 由于一次应力不得大于[σ]t j,所以仅考虑二次应力时的安全条件为: S2 ≤1.25[σ]j+0.25[σ]t j(15) 从以上的公式推导可以看出,当一次应力未用满,而二次应力超过许用范围时,可以使用式(14)进行判断。 8.设备的嘴子受力限制 8.1总则 8.1.1静设备接管的允许推力和力矩应由该设备的设计单位提出。 8.1.2转动设备的允许推力和力矩由该设备的制造厂提出,或由管道设计人员提出后请制造厂确认。当制造厂未能提出数据时,应按以下标准核算: (a)离心泵 离心泵的嘴子受力不应超过API-610中有关嘴子受力的规定。这是管嘴允许受力的最严格的标准,制造厂可以根据其经验,允许较大的受力。 (b)蒸汽轮机 蒸汽轮机的嘴子受力不应超过NEMA/SM23中有关嘴子受力的规定。制造厂可根据其经验数据,允许较大的受力。 8.1.3离心泵的允许受力、矩 8.1.3.1钢或合金钢制卧式泵及垂直支起的泵嘴子受力、矩由表3查得。 8.1.3.2垂直同心泵的侧面嘴子允许力、矩取表3中值的两倍。 8.1.3.3对非钢或合金钢制泵或当泵嘴尺寸大于DN400时,制造厂应提供对应于表3的允许载荷。 8.1.3.4图3至图7的座标系统适用于表3的允许力、矩。 表3 嘴子荷载(SI单位制) 法兰公称直径(in) 力/力矩 2 3 4 6 8 10 12 14 16 顶部嘴子 FX 710 1070 1420 2490 3780 5340 6670 7120 8450 FY 580 890 1160 2050 3110 4450 5340 5780 6670 FZ 890 1330 1780 3110 4890 6670 8000 8900 10230 FR 1280 1930 2560 4480 6920 9630 11700 12780 14850 侧面嘴子 FX 710 1070 1420 2490 3780 5340 6670 7120 8450 FY 890 1330 1780 3110 4890 6670 8000 8900 10230 FZ 580 890 1160 2050 3110 4450 5340 5780 6670 FR 1280 1930 2560 4480 6920 9630 11700 12780 14850 端部嘴子 FX 890 1330 1780 3110 4890 6670 8000 8900 10230 FY 710 1070 1420 2490 3780 5340 6670 7120 8450 FZ 580 890 1160 2050 3110 4450 5340 5780 6670 FR 1280 1930 2560 4480 6920 9630 11700 12780 14850 每一嘴子 MX 460 950 1330 2300 3530 5020 6100 6370 7320 MY 230 470 680 1180 1760 2440 2980 3120 3660 MZ 350 720 1000 1760 2580 3800 4610 4750 5420 MR 620 1280 1800 3130 4710 6750 8210 8540 9820 注: F=力,N;M=矩,N.M;R=合成。X、Y、Z方向见图3至7. 8.1.3.5管道设计者确定管道对泵嘴的作用力、矩的方法 8.1.3.5.1卧式泵 (1)泵进出口管道作用于泵嘴上力、矩不应造成泵和电机轴线的过量偏斜(不对齐)。表3中允许力、矩保证泵体变形在制造厂设计标准的一半之内,泵轴线位移小于0.25mm。 (2)只要满足(a)、(b)、(c)指定的条件,管道作用于泵嘴力、矩可允许超出表3的允许值,而勿需与泵制造厂协商。满足这些条件可以保证泵体变形在制造厂设计允许的范围内,且泵轴线的位移小于0.38mm 。注:该标准仅适用于管道设计。 (a)作用于每一泵嘴法兰处的每一分力、分力矩不应超过表3中允许值的两倍。 (b)作用于每一泵嘴法兰处合力(FRS A、FRD A)、合力矩(MRS A、MRD A)应满足式(3)、(17)限制。 (FRS A/1.5 FRS T2)+ (MRS A/1.5 MRS T2)<=2 (16) (FRD A/1.5 FRD T2)+ (MRD A/1.5 MRD T2)<=2 (17) (c)作用于每一泵嘴法兰处的分力、分力矩必须移到泵中心线上。合力(FRC A)的大小和合力矩(MRC A)的大小应满足式(18)、(19)、(20)的限制。(下式中图3、至图7的符号习惯及右手法则适用)。 FRC A<1.5( FRS T2+ FRD T2) (18) MYC A<2.0( MYS T2+ MYD T2) 0.5(19) MRC A<1.5( MRS T2+ MRD T2) (20) 式中: FRC A=[( FXC A)2+( FYC A)2+ ( FZC A)2] 0.5 FXC A=FXS A+FXD A FYC A=FYS A+FYD A FZC A=FZS A+FZD A MRC A=[( MXC A)2+( MYC A)2+ ( MZC A)2] 0.5 MXC A=MXS A+MXD A-[(FYS A)(zS)+(FYD A)(zD)-(FZS A)(yS)-(FZD A)(yD)]/1000 MYC A=MYS A+MYD A+[(FXS A)(zS)+(FXD A)(zD)-(FZS A)(xS)-(FZD A)(xD)]/1000 MZC A=MZS A+MZD A-[(FXS A)(yS)+(FXD A)(yD)-(FYS A)(xS)-(FYD A)(xD)]/1000 C----泵中心 F----力,N。 MR----合力矩。 D----出口管嘴。 S----入口管嘴。 x、y、z----管嘴法兰处相对于泵中心的座标。 X、Y、Z----荷载方向。 下标A----作用荷载。 下标T2----表3查得值。 注:常数1000适用国际单位制。 (3)若管道对泵产生的作用力、力矩超出上述(2)的允许值,应经供、买双方共同认可。 8.1.3.5.2垂直同心泵 仅靠连接管道支撑的垂直同心泵,只要每一管嘴处产生的主应力力不大于41MPa,各分力、分力矩可大于表3中允许值的两倍。计算时,泵嘴的截面特性应基于SCH40管子,公称直径为泵嘴的公称直径。管嘴处的主应力、纵向应力、剪切应力可分别由式(21)、(22)、(23)确定。 P=(σ/2)+( σ2/4+τ2)0.5<41 (21) σ =[1.27FY/(Do2-D I2)]+[1.02x104D O(MX2+MZ2)0.5]/(D O4-D I4) (22) τ =[1.27(FX2+FZ2)0.5]/(D O2-D I2)+[0.51x104Do(MY)]/(D O4-D I4) (23) 式中: P----主应力,MPa. σ----纵向应力,Mpa. τ----剪切应力,Mpa. Do----SCH40、公称直径为嘴子公称直径的管子的外径,mm。 D I----SCH40、公称直径为嘴子公称直径的管子的内径,mm。 注:FX、FY、FZ、MX、MY、MZ表示作用于出、入口嘴子上的荷载,前缀S A和D A省略。作用嘴子上为拉伸力时,FY 取正号;为压缩力时取负号。必须参考泵图形决定荷载为拉伸或压缩。式(23)中MY为绝对值。 8.1.4蒸汽轮机的允许力、矩 8.1.4.1在任何接口处施加在汽轮机上的总的合力和合力矩不得超过下列数值(按图8): FR+MR/3=167De 式中: FR=合力,磅。除了垂直方向的排气口外,凡在接口处采用无约束的膨胀节处的压力所产生的力都包括在内。允许垂直向下的排气法兰上所受全部真空的负载,但它不计作管道负载的一部分。 Fr=Fx2+Fy2+Fz2(24) MR=合力矩,磅-英尺. Mr=Mx2+My2+Mz2(25) D=直径为8英寸以下的接口的公称管径,英寸。 大于上述尺寸的管道,则采用数值 De=(16+D)/3 (6) 图8 8.1.4.2在进汽、抽汽和排汽接口的力和力矩分解到排汽接口各中心线上的总合成力和力矩必须不得超过下列两种条件: (a)这些合力不应超过: Fc=(250Dc-Mc)/2 (27) 式中: Fc= 进汽口、抽汽口和排汽口的总合成力,磅。 Mc=进汽口、抽汽口和排汽口的力矩以及由力所造成的力矩的总合成力矩,磅-英尺。 Dc=其面积等于进汽口、抽汽口和排汽口的总面积的圆形开孔的直径(英尺),其直径在9英寸一下。对于直径超过9英寸者: Dc=(18+当量直径)/3 英寸 (b)合力和合力矩的分量不应超过下列数据: Fy=125Dc My=125Dc Fz=100Dc Mz=125Dc Fx=50Dc Mx=250Dc 各分量表示如下: Fy=Fr的垂直分量。 Fz=Fr在垂直于汽轮机主轴的水平分量。 Fx=Fr沿汽轮机主轴的垂直平面内的分量。 My=Mr在水平平面内的分量。 Mz=Mr在平行于汽轮机主轴的垂直平面内的分量。 Mx=Mr沿汽轮机主轴的垂直平面内的分量。 8.1.4.3对具有垂直排汽口并在排汽口上装设无约束膨胀节的汽轮机装置,允许其由压力负荷产生的附加力。(这个附加力是垂直于排汽法兰的表面和中心线的。)对这种应用场合,计算排汽口接口处力的垂直分量时不包括压力负荷,然后将这个力与排汽口上压力负荷的六分之一值相比。在进行8.1.4.1、8.1.4.2项所列计算中,取此两数值中较大一项做为在排汽口上力的垂直分量。 在排汽口上由于压力负荷所引起的力是允许的,但除了前面所规定的数值外,还不得超过排汽口上(包 括压力负荷)垂直力(磅)的最大值,即排汽面积(平方英寸)的15.5倍。 8.1.4.4这些许用力和力矩的数值仅适用于汽轮机结构而不适用于连接管道、法兰和法兰螺栓,它们所允 许的力和力矩应遵照相应的规范。 9.支吊架的选用 9.1总则 依据对管系应力分布状况的分析,恰当的设置管架,达到如下目的: 9.1.1支承管系重量,防止出现过量挠度。 9.1.2控制和抵御某些对管系的不利影响(如振动、地震、风载)。 9.1.3改善管系的应力分布状况,保护某些特术或敏感设备。 9.2管架设置的原则 9.2.1配管设计中,首先根据管道的设计条件,参阅附录H(管道跨距表),按各管段的配置型式和载荷条件(包括静载荷和热载荷),确定支吊架的设置位置及型式,必要时可用应力分析专用程序进行校核; 9.2.2管道支吊架的设置应首先满足管道跨距的要求,保证管系不应在轻微外介扰力作用下发生明显的振动,规定装置内管段的自振频率不低于4Hz,装置外管段的自振频率不低于2.55Hz,相应的管道允许挠度,装置内为16mm,装置外为38mm,管道的跨距计算如下: L=0.212(EtI/q0)0.25(28) L*=0.265(EtI/q0)0.25(29) 式中:L---装置内管道由刚度条件决定的跨距,m; L*---装置外管道由刚度条件决定的跨距,m; I---管子扣除腐蚀裕量后的惯性矩,cm4; Et---管材在设计温度下的弹性模量,MPa; q0---每米管道的质量,Kg/m。 9.2.3管架应尽量设置在直管段部分,避免在小半径弯头、支管连接点等局部应力较高的部位设置支撑点,以防管系中局部应力超标; 9.2.4刚性支吊架应设置在沿支撑方向上管道位移为零或要求为零的位置上; 9.2.5支吊架应尽可能靠近阀门、法兰、及其它小型设备或管件,但不能以它们作直接支撑,以免因局部荷载作用引起连接面泄漏,或阀体因受力变形导致阀瓣卡住、关闭不严等不良后果; 9.2.6除经过详细应力分析外,导向架不宜过分靠近弯头和支管连接部位,否则可能额外地增加管系应力和支撑系统的荷载; 9.2.7对因清理、维修等要求而需经常拆卸的管段,不宜设置永久性管架; 9.2.8为便于工厂成批生产,加快建设速度,设计时应尽可能选用标准支吊架; 9.2.9为防止管道过大的横向位移和可能承受的冲击荷载,一般在下列场合设置导向管托,以保证管道只沿轴向位移; (a)安全阀出口的高速放空管道和可能产生两相流的管道; (b)横向位移过大可能影响临近管道时,固定支架之间的距离过长,可能产生横向不稳定时; (c)为防止法兰和活接头泄漏要求管道不宜有过大横向位移时; (d)为防止振动管道出现过大的横向位移时; 9.2.10当架空敷设的管道热胀量超过100mm时,应选用加长管托,以免管托滑到管架梁下; 9.2.11支架生根焊在钢制设备上时,所用垫板应按设备外形成型。当碳钢设备壁厚大于38mm时,应取 的设备专业的同意。当生根在合金设备上时,垫板材料应与设备材料相同,并应取得设备专业的同意;9.2.12对于荷载较大的支架位置要事先与有关专业联系,提出支架位置、标高和荷载情况,荷载应充分考虑各种工况(包括非正常工况); 9.2.13下列情况应选用可变弹簧支吊架: (a)由于管道在支撑点处有向上的垂直位移,致使支架托空,荷载转移; (b)由于管道在支撑点处有向下的垂直位移,选用刚性支架将阻挡管道的位移时; (c)选用的弹簧其荷载变化率应不大于25%, 荷载变化率=(工作荷载--安装荷载)/工作荷载X 100% (d)当选用的弹簧不能满足上述荷载变化率时,可选用两个弹簧串连安装,对同型号多弹簧串联,串联弹簧的总刚度为单个弹簧刚度除以串联弹簧总个数,总荷载为单个弹簧的荷载; (e)当实际荷载超过选用表中最大允许的荷载或大直径管道设置弹簧时,可选用多个弹簧并联,并联弹簧的总刚度为各弹簧刚度的总和,总荷载为各弹簧的荷载总和; 9.2.14当管道在支撑点有垂直位移,且要求支撑力的变化范围必需限制在8%以内时,管系应采用恒力架; 9.2.15确定弹簧的位移范围时,应充分考虑其它因素(如安装偏差、水平位移的影响、管子塑性变形等) 以防弹簧被压死或拉死。 10.特殊管道的柔性设计 10.1烟气轮机管道的柔性设计 10.1.1一般要求 (a)烟机进出口管道在冷态或热态作用于进出口管嘴上的力和力矩均应小于烟机所允许承受的力和力矩。 (b)在设备布置和管道设计中,应尽量使管道图形简单,同时使管道作用于烟机的力和力矩较小。 10.1.2入口管道的设计 (a)由于烟气温度高(600~700℃),且烟气流速高(27m/s),不得有异物进入烟机,以免损坏烟机,烟机入口管道不得采用冷壁设计,应采用耐热不锈钢钢板卷管。 (b)不锈钢在高温下热膨胀量较大,大口径管道柔性差,烟机允许受力、矩苛刻,一般采用单式铰链型波纹管补偿器,成三铰链布置型式,用以吸收水平管及竖直管的热膨胀。 当管系成L形时,可采用一组三铰链,当竖直管较长或管系成空间Z型时,可采用两组三铰链。 (c)考虑安装偏差、机组找正、支架及下沉、梁的挠曲、管道塑性变形等因素可能引起烟机嘴子法兰口的张口和错位,在烟机入口水平段设复式万向型膨胀节。 (d)跨过高温闸阀高温蝶阀的暖机旁路及预热线需与主管一起进行应力分析,且考虑两种操作工况。 (e)由于烟机入口管在冷热态均需保持水平,且要求磨擦反力较小,主要承重架一般采用刚性中心支撑,即摆式支架。 (f)高温闸阀、高温蝶阀较重,为防止管道在高温下下挠,支撑应尽量靠近阀门,建议用三摆式支架支撑。 (g)为防止支架基础下沉及梁的下挠,并考虑非正常条件的不利影响(如调整摆式支架时可能造成荷载转移,关闭高温闸阀时产生的短时间锤击力)。委托土建专业时,支架的垂直荷重应考虑相邻支架托 空时分配给该支架的荷载,对三摆式支架,建议每个支架荷重(委托土建专业)取分配给三个摆式支架实际荷载的总和。 (h)入口管宜采用冷紧,考虑管道高温下会发生蠕变,建议水平管和竖直管均采用100%冷紧。 10.1.2出口管道的设计 (a)烟机出口应采用柔性连接,即出口管上设普通型或压力平衡型膨胀节,出口至水封罐设复式铰链型膨胀节。 (b)为防止出口管施加烟机出口嘴过大水平推力及垂直荷重,出口管竖管设固定支架,水平管上设弹簧吊。 (c)出口管道应采取分段补偿的方式,一般分为两段,出口立管上的普通型或压力平衡型膨胀节作为补偿出口管嘴及立管膨胀量的独立系统,三通或弯头之后至水封罐入口为另一系统,采用设复式铰链型或三铰链式膨胀节的补偿方式。 (d)为防止异物落入烟机内,出口立管应采用热壁设计,即采用耐热不锈钢管加外保温。立管之后的水平管段可采用冷壁设计,即碳钢管内衬有龟甲网双层隔热衬里或无龟甲网双层隔热衬里。 (e)如果出口立管上设置普通型膨胀节,为减少热态时膨胀节变形产生的反力,宜采用冷态对膨胀节的预拉,预拉值一般为垂直热胀量的一半。为减少膨胀节产生的盲板力,立管上弹簧吊荷载除考虑膨胀节下管件重量外,还应考虑盲板力,一般取盲板力的一半。 10.1.3支架的设计原则 10.1.3.1进口管道支架 (a)由于烟机的机壳为中心支撑,为保证其转子在热态时的水平度,烟机进口管道上的支架应采用中心支撑。 (b)为减少热胀位移情况下支架磨擦反力,支架的设计应考虑磨擦系数小的结构。 如采用摆式支架。也可采用弹簧吊架,为减少磨擦力,吊杆应有一定长度。考虑管系的稳定性,入口水平管道上的支架不宜全采用弹簧吊架,应采用弹簧吊架与摆式支架结合的方式。 (c)支架的设置位置应靠近入口管道上的集中荷载处,即在高温闸阀、高温蝶阀的两侧及中间设支架。当高温蝶阀后的支架距入口法兰较远时,在靠近入口法兰处的管道上应设置一弹簧吊架,以减少作用于法兰处的垂直荷重。 (d)入口管道上高温蝶阀后复式万向铰链型膨胀节中间筒节处加弹簧支架。 (e)高温状态下高速运转的烟机难以承受较大的侧向力和力矩,且考虑入口管在风载或其它动载作用下的稳定性,入口水平管道上应设置不少于两个的导向支架,尤其当入口管为空间Z形时。 10.1.3.2出口管道支架 (a)对上排气的烟机,出口管道上的支架至关重要,一般采用框架式支架,用以承受出口管道的重量及出口水平管的热位移反力。支架梁应有一定刚度,其梁中心部位的挠曲度应不大于2‰。为减少出口立管对烟机垂直荷载,出口立管膨胀节下应设弹簧吊。 (b)对于下排气的烟机,如出口法兰直接一普通型膨胀节,其承重支架可设置在机组基础底板上; 10.2蒸汽轮机的柔性设计 10.2.1蒸汽轮机为高速旋转的转动设备,管道设计应使进出口管道对蒸汽轮机的作用力、矩尽可能小,使其不超过制造厂提供的允许值或NEMA/SM23中有关嘴子受力的规定。 10.2.2蒸汽轮机的进出口管系须应用应力分析专用程序进行分析,不能用简化方法。 10.2.3蒸汽轮机的进出口管系热补偿应尽量采用自然补偿,但当管径较大或场地条件 限制,自然补偿不能满足嘴子受力要求时,亦可采用膨胀节吸受热位移。 10.2.4当管系热胀采用自然补偿时,不宜采用冷紧。 10.2.5支吊架的设置 (a)为减少管道对蒸汽轮机的垂直荷载,同时考虑立管的热胀,靠近进出口立管处设弹簧吊架。 (b)为减少水平管道对蒸汽轮机产生过大水平推力,在靠近进出口嘴子处设止推支架。当止推支架由于嘴子附加位移产生脱空时,可设水平方向的弹簧。 (c)靠近嘴子的支架应考虑磨擦反力的作用,为减少管系的磨擦力对嘴子的不利影响,支架应采用磨擦系数小的型式,如加聚四氟乙烯垫板。 (d)为避免远离嘴子的管道对嘴子产生不利影响,应在适当位置设固定支架,将管系分段。 钢筋砼梁应力应变计算方法的探讨 摘要:对于钢筋砼梁应力应变的计算,分别用桥梁规范中弹性体假定的应力计算方法和以砼处于弹塑性阶段的应力计算方法进行分析,通过算例比较两者计算结果的差异,提出一些个人的见解。 关健词:桥梁工程;钢筋砼梁;应力应变值;计算方法;基本假定;弹性;弹塑性 0 前言 钢筋砼梁属于受弯构件。按《公路钢筋砼及预应力砼桥涵设计规范》(以下简称《桥规》)要求,对于钢筋砼受弯构件的设计,首先按承载能力极限状态对梁进行强度计算,从而确定构件的设计尺寸、材料、配筋量及钢筋布置,以保证截面承载能力要大于荷载效应;另外,尚需按正常使用极限状态对构件进行应力、变形、裂缝计算,验算其是否满足正常使用时的一些限值的规定。为检验钢筋砼梁的施工是否满足设计要求,均应对形成该梁的材料(钢筋及砼)进行强度检验,但由于砼的养护环境、工作条件及钢筋的加工、布置等方面,均存在试样与实际构件之间的差异,因而不能完全地说明该构件的工作性能。有时,按需要可对梁进行直接加载试验以量测荷载效应值,通过实测值与理论计算值的比较,以检验其工作性能是否能满足设计和规范的要求。通常情况下,我们不能直接测定梁体的应力值,只能通过实测梁体的应变值,进而求算其应力值。但钢筋砼结构属于非匀质材料,不能直接运用材料力学计算公式进行其应力及应变的计算,因此,本文按弹性阶段应力计算和弹塑性阶段应力计算2种方法进行分析比较。 1 按弹性阶段计算应力的方法 钢筋砼梁在使用阶段的工作状态可认为与施工阶段的工作状态相同,都处于带裂缝工作阶段,因此可按施工阶段的应力计算方法进行计算。 1.1 基本假定 《桥规》规定:钢筋砼受弯构件的施工阶段应力计算,可按弹性阶段进行,并作以下3项假定。 1.1.1 平截面假定 认为梁的正截面在梁受力并发生弯曲变形后,仍保持为平面,平行于梁中性轴的各纵向纤维的应变与其到中性轴的距离成正比,同时由于钢筋与砼之间的粘结力,钢筋与其同一水平线的砼应变相等。其表达式为: εh/x=εh′/(h0-x) εg=εh′ 式中:εh′-为与钢筋同一水平处砼受拉平均应变; εh-为砼受压平均应变; εg-为钢筋平均拉应变; x-为受压区高度; h0-为截面有效高度。 1.1.2 弹性体假定 假定受压区砼的法向应力图形为三角形。钢筋砼受变构件处在带裂缝工作阶段,砼受压区的应力分布图形是曲线形,但曲线并不丰满,与直线相差不大,可以近似地看作呈直线分布,即受压区砼的应力与应变成正比。 σh=εhEh 式中:σh-为砼应力; εh-为砼受压平均应变; E h-为砼弹性模量。 1.1.3 受拉区砼完全不能承受拉应力 在裂缝截面处,受拉区砼已大部分退出工作,但在靠近中和轴附近,仍有一部分砼承担着拉应力。由于其拉应力较小,内力偶臂也不大,因此,不考虑受拉区砼参加工作,拉应力全部由钢筋承担。 σg=εgEg 式中:σg-为钢筋应力; εg-为受拉区钢筋平均应变; E g-为钢筋弹性模量。 1.2采用换算截面计算应力 根据同一水平处钢筋应变与砼的应变相等,将钢筋应力换算为砼应力,则钢筋应力为砼应力的n g 倍(n g=E g/E h)。由上述假定得到的计算图式与材料力学中匀质梁计算图非常接近,主要区别是钢筋砼梁的受拉区不参予工作。因此,将钢筋假想为受拉的砼,形成一种拉压性能相同的假想材料组成的匀质截面,即为换算截面,再按材料力学公式进行应力计算。 1.2.1受压区边缘砼应力 第四节 温度应力计算 一、温度对结构的影响 1 温度影响 (1)年温差影响 指气温随季节发生周期性变化时对结构物所引起的作用。 假定温度沿结构截面高度方向以均值变化。则 12t t t -=? 12t t t -=?该温差对结构的影响表现为: 对无水平约束的结构,只引起结构纵向均匀伸缩; 对有水平约束的结构,不仅引起结构纵向均匀伸缩,还将引起结构内温度次内力; (2)局部温差影响 指日照温差或混凝土水化热等影响。 A :混凝土水化热主要在施工过程中发生的。 混凝土水化热处理不好,易导致混凝土早期裂缝。 在大体积混凝土施工时,混凝土水化热的问题很突出,必须采取措施控制过高的温度。如埋入水管散热等。 B :日照温差是在结构运营期间发生的。 日照温差是通过各种不同的传热方式在结构内部形成瞬时的温度场。 桥梁结构为空间结构,所以温度场是三维方向和时间的函数,即: ),,,(t z y x f T i = 该类三维温度场问题较为复杂。在桥梁分析计算中常采用简化近似方法解决。 假定桥梁沿长度方向的温度变化为一致,则简化为二维温度场,即: ),,(t z x f T i = 进一步假定截面沿横向或竖向的温度变化也为一致,则可简化为一维温度场。如只考虑竖向温度变化的一维温度场为: ),(t z f T i = 我国桥梁设计规范对结构沿梁高方向的温度场规定了有如下几种型式: 2 温度梯度f(z,t) (1)线性温度变化 梁截面变形服从平截面假定。 对静定结构,只引起结构变形,不产生温度次内力; 对超静定结构,不但引起结构变形,而且产生温度次内力; (2)非线性温度变化 梁在挠曲变形时,截面上的纵向纤维因温差的伸缩受到约束,从而产 。 生约束温度应力,称为温度自应力σ0 s 对静定结构,只产生截面的温度自应力; 对超静定结构,不但产生截面的温度自应力,而且产生温度次应力; 二、基本结构上温度自应力计算 1 计算简图 2 3 ε 和χ的计算 三、连续梁温度次内力及温度次应力计算 采用结构力学中的力法求解。 各种许用应力与抗拉强度、屈服强度的关系 我们在设计的时候常取许用剪切应力,在不同的情况下安全系数不同,许用剪切应力就不一样。校核各种许用应力常常与许用拉应力有联系,而许用材料的屈服强度(刚度)与各种应力关系如下: <一> 许用(拉伸)应力 钢材的许用拉应力[δ]与抗拉强度极限、屈服强度极限的关系: 1.对于塑性材料[δ]= δs /n 2.对于脆性材料[δ]= δb /n δb ---抗拉强度极限 δs ---屈服强度极限 n---安全系数 轧、锻件n=1.2-2.2 起重机械n=1.7 人力钢丝绳n=4.5 土建工程n=1.5 载人用的钢丝n=9 螺纹连接n=1.2-1.7 铸件n=1.6-2.5 一般钢材n=1.6-2.5 注:脆性材料:如淬硬的工具钢、陶瓷等。 塑性材料:如低碳钢、非淬硬中炭钢、退火球墨铸铁、铜和铝等。 <二> 剪切 许用剪应力与许用拉应力的关系: 1.对于塑性材料[τ]=0.6-0.8[δ] 2.对于脆性材料[τ]=0.8-1.0[δ] <三> 挤压 许用挤压应力与许用拉应力的关系 1.对于塑性材料[δj]=1.5- 2.5[δ] 2.对于脆性材料[δj]=0.9-1.5[δ] 注:[δj]=1.7-2[δ](部分教科书常用) <四> 扭转 许用扭转应力与许用拉应力的关系: 1.对于塑性材料[δn]=0.5-0.6[δ] 2.对于脆性材料[δn]=0.8-1.0[δ] 轴的扭转变形用每米长的扭转角来衡量。对于一般传动可取[φ]=0.5°--1°/m;对于精密件,可取[φ]=0.25°-0.5°/m;对于要求不严格的轴,可取[φ]大于1°/m计算。 <五> 弯曲 许用弯曲应力与许用拉应力的关系: 1.对于薄壁型钢一般采取用轴向拉伸应力的许用值 2.对于实心型钢可以略高一点,具体数值可参见有关规范。 ①叶片离心拉应力计算 1)对于涡轮增压器来说,等截面叶片根部截面上的拉应力公式为 20m 1=2u a σρσθ+ 2/N m 其中 ρ为叶片的材料密度(3 /kg m ); m u 为叶片中经处的圆周速度(m/s ); /m D l θ=为直径叶高比; m D 为叶片平均直径(m ); l 为叶片高度(m ); a σ为叶片附加应力,其表示式为: 2222p p t e a m m h m h D A D A u z D A D A πρσ????????=+ ? ????????? ,2/N m 其中 z 为叶轮叶片个数; t D 为叶冠中经(m ); p D 为叶片凸台或拉筋的中经(m ); h D 为叶根直径(m ); e A δ=?为叶冠截面面积(2m ); p A 为凸台或拉筋的截面积(2 m ); h A 为叶根截面面积(2m ); 如果叶片没有设置阻尼拉筋或凸台,则p A =0;如果叶片不带冠,则e A =0;当两者均不存在时,a σ=0. 2)叶片截面面积沿叶高按线性变化时的拉应力计算式: 212113m a u λλσρσθθ+-??=++ ??? 2/N m 式中,/t h A A λ=是叶顶叶根截面比。通常,对压气机叶片,λ=0.3~0.65 3)叶片截面面积沿叶高按某一任意规律变化时,任意一个截面上离心应力可 用数值积分法计算。对于第i 个几面,离心力i σ可按下式计算: 21i i ic i i V r A σρω?=∑ 2/N m 其中 ()112 i i i i im i V A A x A x -?=+?=?为叶片第i 个微段的体积(3m ); i A 和1i A -为叶片第i 个微段的内径与外径上的截面积(3m ); ic h i ic r r x x =++?为第i 个微段重心c 的半径(m ); ()1216i i ic i im A A x x A -+?=?为第i 个微段重心c 离第i 截面的间距(m ); ω为旋转角速度(rad/s ); ρ为材料密度(3/kg m ); ②叶片弯应力计算 1)由气体作用引起的弯矩 作用于叶片任意截面上的气体周向弯矩gu M 可以按下式计算: ()2gu i M B l x =- N m ? 而 ()122um um G B c c zl =+ N/m 式中 i x 为计算截面至叶根的距离(m ); z 为叶片个数; l 为叶片的高度(m ); 1um c ,2um c 为叶片中经处、出口气流周向分速(m/s ); G 为气体流量(kg/s )。 作用于叶片而难以截面上的气体周向弯矩ga M 的计算公式也表达为: ()2ga i M D l x =- N m ? 而 ()()12122m a a r G D c c p p zl z π=-+- N/m 式中 1a c ,2a c 为叶片进、出口中经截面上的周向分速(m/s ); 1p ,2p 为叶片进、出口中经截面上的气体压力(2 /N m ); 习题 10?1一工字型钢梁,在跨中作用集中力F,已知l=6m,F=20kN,工字钢的型号为20a,求梁中的最大正应力。 解:梁内的最大弯矩发生在跨中kN.m 30 max = M 查表知20a工字钢3 cm 237 = z W 则 MPa 6. 126 Pa 10 6. 126 10 237 10 306 6 3 max max = ? = ? ? = = - z W M σ 10?2一矩形截面简支梁,受均布荷载作用,梁的长度为l,截面高度为h,宽度为b,材料的弹性模量为E,试求梁下边缘的总伸长。 解:梁的弯矩方程为()2 2 1 2 1 qx qlx x M- = 则曲率方程为() () ? ? ? ? ? - = =2 2 1 2 1 1 1 qx qlx EI EI x M x z z ρ 梁下边缘的线应变()()? ? ? ? ? - = =2 2 1 2 1 2 2 qx qlx EI h x h x z ρ ε 下边缘伸长为() 2 3 2 02 2 1 2 1 2Ebh ql dx qx qlx EI h dx x l l z l = ? ? ? ? ? - = = ?? ?ε 10?3已知梁在外力作用下发生平面弯曲,当截面为下列形状时,试分别画出正应力沿横截面高度的分布规律。 解:各种截面梁横截面上的正应力都是沿高度线性分布的。中性轴侧产生拉应力,另一 b h 侧产生压应力。 10?4 一对称T 形截面的外伸梁,梁上作用均布荷载,梁的尺寸如图所示,已知l =1.5m ,q =8KN/m ,求梁中横截面上的最大拉应力和最大压应力。 解: 1、设截面的形心到下边缘距离为y 1 则有 cm 33.74 108410 4104841=?+???+??= y 则形心到上边缘距离 cm 67.433.7122=-=y 于是截面对中性轴的惯性距为 4 2323cm 0.86467.24101241033.3841284=??? ? ????+?+???? ????+?=z I 2、作梁的弯矩图 设最大正弯矩所在截面为D ,最大负弯矩所在截面为E ,则在D 截面 MPa 08.15Pa 1008.15100.8641033.710778.168 2 31max t,=?=????==--y I M z D σ MPa 61.9Pa 1061.910 0.8641067.410778.16 8 232max c,=?=????==--y I M z D σ 在E 截面上 MPa 40.5Pa 1040.5100.8641067.4100.168 2 32max t,=?=????==--y I M z E σ MPa 48.8Pa 1048.810 0.8641033.7100.16 8 231max c,=?=????==--y I M z E σ 所以梁内MPa 08.15max t,=σ,MPa 61.9max c,=σ C 课时授课计划 掌握弯曲应力基本概念; 掌握弯曲正应力及弯曲剪应力的计算;掌握弯曲正应力的强度计算; 掌握弯曲剪应力强度校核。 I D (d 根据[M],用平衡条件确定许用外载荷。 在进行上列各类计算时,为了保证既安全可靠又节约材料的原则,设计规范还规定梁内的最大正应力允许稍大于[σ],但以不超过[σ]的5%为限。即 3、进行强度计算时应遵循的步骤 (1)分析梁的受力,依据平衡条件确定约束力,分析梁的内力(画出弯矩图)。(2)依据弯矩图及截面沿梁轴线变化的情况,确定可能的危险截面:对等截面梁,弯矩最大截面即为危险截面。 (3)确定危险点 (4)依据强度条件,进行强度计算。 第三节梁的剪应力强度条件 一、概念 梁在横弯曲作用下,其横截面上不仅有正应力,还有剪应力。 对剪应力的分布作如下假设: (1)横截面上各点处剪应力均与剪力Q同向且平行; (2)横截面上距中性轴等距离各点处剪应力大小相。 根据以上假设,可推导出剪应力计算公式: 式中:τ—横截面上距中性轴z距离为y处各点的剪应力; Q—该截面上的剪力; b—需求剪应力作用点处的截面宽度; Iz—横截面对其中性轴的惯性矩; Sz*—所求剪应力作用点处的横线以下(或以上)的截面积A*对中性轴的面积矩。 剪应力的单位与正应力一样。剪应力的方向规定与剪力的符号规定一样。 二、矩形截面横梁截面上的剪应力 如图所示高度h大于宽度b的矩形截面梁。横截面上的剪力Q沿y轴方向作用。 将上式带入剪应力公式得: 上式表明矩形截面横梁截面上的剪应力,沿截面高度呈抛物线规律变化。 在截面上、下边缘处y=±h/2,则=0;在中性轴上,y=0,剪应力值最大, 坝体强度承载能力极限状态计算及坝体稳定承载能力极限状态计算 (一)、基本资料 坝顶高程:1107.0 m 校核洪水位(P = 0.5 %)上游:1105.67 m 下游:1095.18 m 正常蓄水位上游:1105.5 m 下游:1094.89 m 死水位:1100.0 m 混凝土容重:24 KN/m3 坝前淤沙高程:1098.3 m 泥沙浮容重:5 KN/m3 混凝土与基岩间抗剪断参数值:f `= 0.5 c `= 0.2 Mpa 坝基基岩承载力:[f]= 400 Kpa 坝基垫层混凝土:C15 坝体混凝土:C10 50年一遇最大风速:v 0 = 19.44 m/s 多年平均最大风速为:v 0 `= 12.9 m/s 吹程D = 1000 m (二)、坝体断面 1、非溢流坝段标准剖面 荷载作用的 标准值计算(以单宽计算) A 、正常蓄水位情况(上游水位1105.5m ,下游水位1094.89m ) ① 竖向力(自重) W 1 = 24×5×17 = 2040 KN W 2 = 24×10.75×8.6 /2 = 1109.4 KN W 3 = 9.81×(1094.5-1090)2×0.8 /2 = 79.46 KN ∑W = 3228.86 KN W 1作用点至O 点的力臂为: (13.6-5) /2 = 4.3 m W 2作用点至O 点的力臂为: m 067.16.83 2 26.13=?- W 3作用点至O 点的力臂为: m 6.58.0)10905.1094(3 1 26.13=?-?- 竖向力对O 点的弯矩(顺时针为“-”,逆时针为“+”): M OW1 = 2040×4.3 = 8772 KN ·m M OW2 = -1109.4×1.067 = -1183.7 KN ·m H 钢支架设计计算书 一、依据 1、 《通桥(2008)-2322-Ⅵ》 2、 《铁路桥梁钢结构设计规范》 钢Q235许用应力[]MPa 135=σ,[]MPa w 140=σ,剪应力[]MPa 80=τ 3、 《铁路桥涵地基与基础规范》 二、荷载标准值: 1、模板和装配式钢桥自重: 模板(千斤顶和贝雷梁上横梁重计入):m KN /3.616.322000= 模板和装配式钢桥自重设计值:61.3×1.2=73.6/KN m 1、查《通桥(2008)2221A -Ⅴ》31.1米梁图知: C50混凝土方量310.6m 3;混凝土容重25KN/ m 3 C50混凝土重:310.6×25=7765 KN 普通钢筋重:1.95+54.357=56.307t=563.57KN 预应力钢筋重:117.25KN 每孔梁重: m KN /1.2596.32/)25.11757.5637765(=++ 每孔梁重设计值:259.1×1.2=310.9KN/m 3、施工附加荷载: 施工人员和施工设备:1.0×1.4×13.4=7.7/KN m 振捣混凝土产生的竖向荷载:1.0×1.4×5.5=7.7/KN m 倾倒混凝土时产生的冲击荷载:1.0×1.4×5.5=7.7/KN m 施工附加荷载设计值:7.7×3=23.1/KN m 荷载总值:m KN q /6.4071.239.3106.73=++= 四、箱梁计算荷载模型划分 1、各部分面积计算: 1/2箱梁截面划分为第Ⅰ部分;第Ⅱ部分;第Ⅲ部分各部分面积如下: AⅠ=2.16m2 AⅡ=0.77 m2 AⅢ=1.12 m2 全截面总面积为:A总=8.76 m2 2、各部分沿梁长方向均部荷载计算: qⅠ=(2.16/8.76)×310.9=76.7KN/m qⅡ=(1.12/8.76)×310.9=39.7 KN/m qⅢ=(1.07/8.76)×310.9=38KN/m 二、纵梁检算 地应力计算公式 (一)、井中应力场的计算及其应用研究(秦绪英,陈有明,陆黄生 2003年6月) 主应力计算 根据泊松比μ、地层孔隙压力贡献系数V 、孔隙压力0P 及密度测井值b ρ可以计算三个主应力值: ()001H v A VP VP μσσμ??=+-+??-?? ()001h v B VP VP μσσμ??=+-+??-?? H v b dh σρ=?? 相关系数计算: 应用密度声波全波测井资料的纵波、横波时差(p t ?、s t ?)及测井的泥质含量sh V 可以计算泊松比μ、地层孔隙压力贡献系数V 、岩石弹性模量E 及岩石抗拉强度T S 。 ① 泊松比 22 2 20.52()s p s p t t t t μ?-?=?-? ② 地层孔隙压力贡献系数 22222(34)12() b s s p m ms mp t t t V t t ρρ??-?=-?-? ③ 岩石弹性模量 222 2234s p b s s p t t E t t t ρ?-?=???-? ④ 岩石抗拉强度 22 (34)[(1)]T b s p sh sh S a t t b E V c E V ρ=???-????-+?? 注:,,,m ms mp t t ρρ??分别为密度测井值,地层骨架密度,横波时差和纵波时差值。,,a b c 为地区试验常数。 其它参数 不同地区岩石抗压强度参数是参照岩石抗拉强度数值确定,一般是8~12倍,也可以通过岩心测试获得。岩石内摩擦系数及岩石内聚力是岩石本身固有特性参数,可以通过测试分析获得。地层孔隙压力由地层水密度针对深度积分求取,或者用重复地层测试器RFT 测量。也可以通过地层压裂测试获得,测试时,当井孔压力下降至不再变化时,为储层的孔隙压力。 材料力学常用公式 1.外力偶矩 计算公式(P功率,n转速)2.弯矩、剪力和荷载集度之间的关 系式 3.轴向拉压杆横截面上正应力的计 算公式(杆件横截面轴力 F N,横截面面积A,拉应力为正) 4.轴向拉压杆斜截面上的正应力与切应力计算公式(夹角a 从x轴 正方向逆时针转至外法线的方位 角为正) 5. 6.纵向变形和横向变形(拉伸前试 样标距l,拉伸后试样标距l1; 拉伸前试样直径d,拉伸后试样 直径d1) 7. 8.纵向线应变和横向线应变 9.10.泊松比 11.胡克定律 12.受多个力作用的杆件纵向变形计 算公式? 13.承受轴向分布力或变截面的杆 件,纵向变形计算公式 14.轴向拉压杆的强度计算公式 15.许用应力,脆性材 料,塑性材料 16.延伸率 17.截面收缩率 18.剪切胡克定律(切变模量G,切应变g ) 19.拉压弹性模量E、泊松比和切变 模量G之间关系式 20.圆截面对圆心的极惯性矩(a) 实心圆 21.(b)空心 圆 22.圆轴扭转时横截面上任一点切应力计算公式(扭矩T,所求点到 圆心距离r) 23.圆截面周边各点处最大切应力计 算公式 24.扭转截面系数,(a) 实心圆 25.(b)空心圆 26.薄壁圆管(壁厚δ≤ R0 /10 , R0为圆管的平均半径)扭转切应 力计算公式 27.圆轴扭转角与扭矩T、杆长l、 扭转刚度GH p的关系式 28.同一材料制成的圆轴各段内的扭 矩不同或各段的直径不同(如阶 梯轴)时或 29.等直圆轴强度条件 30.塑性材料;脆性 材料 31.扭转圆轴的刚度条件? 或 32.受内压圆筒形薄壁容器横截面和 纵截面上的应力计算公式 , 33.平面应力状态下斜截面应力的一 般公式 , 34.平面应力状态的三个主应力 , 常用力学计算公式统计 一、材料力学: 1.轴力(轴向拉压杆的强度条件) σmax=N max/A≤[σ] 其中,N为轴力,A为截面面积 2.胡克定律(应力与应变的关系) σ=Eε或△L=NL/EA 其中σ为应力,E为材料的弹性模量,ε为轴向应变, EA为杆件的刚度(表示杆件抵抗拉、压弹性变形的能力) 3.剪应力(假定剪应力沿剪切面是均匀分布的) τ=Q/A Q 其中,Q为剪力,A Q为剪切面面积 4.静矩(是对一定的轴而言,同一图形对不同的坐标轴 的静矩不同,如果参考轴通过图形的形心,则x c=0, y c=0,此时静矩等于零) 对Z轴的静矩S z=∫A ydA=y c A 其中:S为静矩,A为图形面积,y c为形心到坐标轴的 距离,单位为m3。 5.惯性矩 对y轴的惯性矩I y=∫A z2dA 其中:A为图形面积,z为形心到y轴的距离,单位为 m4 常用简单图形的惯性矩 矩形:I x=bh3/12,I y=hb3/12 圆形:I z=πd4/64 空心圆截面:I z=πD4(1-a4)/64,a=d/D (一)、求通过矩形形心的惯性矩 求矩形通过形心,的惯性矩I x=∫Ay2dA dA=b·dy,则I x=∫h/2-h/2y2(bdy)=[by3/3]h/2-h/2=bh3/12 (二)、求过三角形一条边的惯性矩 I x=∫Ay2dA,dA=b x·dy,b x=b·(h-y)/h 则I x=∫h0(y2b(h-y)/h)dy=∫h0(y2b –y3b/h)dy =[by3/3]h0-[by4/4h]h0=bh3/12 6.梁正应力强度条件(梁的强度通常由横截面上的正应 力控制) σmax=M max/W z≤[σ] 其中:M为弯矩,W为抗弯截面系数。 7.超静定问题及其解法 对一般超静定问题的解决办法是:(1)、根据静力学平衡条件列出应有的平衡方程;(2)、根据变形协调条件列出变形几何方程;(3)、根据力学与变形间的物理关系将变形几何方程改写成所需的补充方程。 8.抗弯截面模量 钢管许用应力 钢管壁厚表示方法有管子表号、钢管壁厚尺寸和管子重量三种方法 Sch10s、Sch40s、Sch80s四个等级; 2)以钢管壁厚尺寸表示? 中国、ISO、日本部分钢管标准采用 3)是以管子重量表示管壁厚度,它将管子壁厚分为三种: A.标准重量管,以STD表示 B.加厚管,以XS表示 C.特厚管,以XXS表示。 对于DN≤250mn的管子,Sch40相当于STD,DN<200mm的管子,Sch80相当于XS。补充: 1、以管子表号(Sch.)表示壁厚系列 这是1938年美国国家怔准协会ANSIB36.10(焊接和无缝钢管)标准所规定的。 管子表号(Sch.)是设计压力与设计温度下材料的许用应力的比值乘以1000,并经圆 整后的数值。即 ????? Sch .=P/[ó]t×1000??? (1-2-1) 式中? P—设计压力,MPa;?? ????????? [ó]t—设计温度下材料的许用应力,MPa。 无缝钢管与焊接钢管的管子表号可查资料确定。 ANSI B36.10和JIS标准中的管子表号为;Sch10、20、30、40、60、80、100、120、140、160。 ANSI B36.19中的不锈钢管管子表号为:5S、10S、40S、80S。 ??? 管表号(Sch.)并不是壁厚,是壁厚系列。实际的壁厚,同一管径,在不同的管子表 号中其厚度各异。不同管子表号的管壁厚度,在美国和日本是应用计算承受内压薄壁管厚度 的Barlow公式计算并考虑了腐蚀裕量和螺纹深度及壁厚负偏差-12.5%之后确定的,如公式 (1-2-2)和(1-2-3)所示。??? tB=D0P/2[ó]t??????? (1-2-2)??????????????? t=[D0/2(1-0.125)×P/[ó]t]+2.54??? (1-2-3) 式中? tB 、t——分别表示理论和计算壁厚,mm D0————管外径,mm P——设计压力,MPa [ó]t——在设计温度下材料的许用压力,MPa 计算壁厚径圆整后才是实际的壁厚。 如果已知钢管的管子表号,可根据式(1-2-1)计算出该钢管所能适应的设计压力,即 ????? P=Sch..× [ó]t/1000??????????????? (1-2-4) 例如,Sch40,碳素钢20无缝钢管,当设计温度为350oC时给钢管所能适应 设计压力为: P=40×92/1000①=3.68 MPa 中国石化总公司标准SHJ405规定了无缝钢管的壁厚系列并Sch.5S②,? Sch.10, Sch.10s,Sch.20,Sch.20s,Sch.30,Sch.40,Sch。40s,Sch.60,Sch.80,Sch.100, Sch.120,Sch.140,Sch。160,如表1-2-9所示。 2、以管子重量表示管壁厚度的壁厚系列 美国MSS和ANSI规定的以管子重量表示壁厚方法,将管子壁厚分为;种: ??? (1)标准重量管以STD表示; 脆断体(高、低周疲劳)的剩余寿命计 算 课程名称:机械结构强度与可靠性设计 专业:机械设计及理论 年级:2013级 完成时间:2014-05-02 文章是对脆断体(高周疲劳和低周疲劳)的剩余寿命计算的一个综述。对于机械零件的寿命计算,尤其是对于断裂件(含裂纹体)的剩余寿命计算,正确估算裂纹体的剩余疲劳寿命估算,能够有效的保证重要零件的合理检修要求,能够很好的创造好经济条件。一般对于高周疲劳,无裂纹寿命N1是主要的,它占了总寿命N(N=N1+N c)中的主要部分,而裂纹扩展寿命N c短,因此高周疲劳中往往只按初始裂纹尺寸来估算N e值。但对于低周疲劳中总寿命中N c占主要部分,N1 很小。与疲劳裂纹扩展速度相关的物理量有应力强度因子幅值ΔK I和其他量。疲劳裂纹的扩展速度:疲劳条件下的亚临界裂纹扩展速率是决定零部件疲劳破坏寿命的特性指标之一。 剩余寿命的时间是指初始裂纹a0到临界裂纹尺寸a c的时间。零件在变应力作用下,初始裂纹a0会缓慢产生亚临界扩展,当它达到临界裂纹尺寸a c 时,就会发生失稳破坏。裂纹体在变应力作用下的裂纹扩展速率与应力场裂纹尺寸和材料特性的关系。ΔK I—控制疲劳裂纹扩展速度的主要力学参量,实验指出控制盘疲劳裂纹扩展速度的主要力学参量是应力强度因子幅值ΔK I。da/dN与ΔK I的关系曲线表明了材料在无害环境中疲劳裂纹的扩展速度与应力强度因子幅值的关系。 ①区间I: da/dN=0处,有ΔKth,称为界限应力强度因子幅值。 当ΔK I≤ΔKth时,裂纹不扩展,稳定状态 当ΔK I ≥ΔKth 时,裂纹开始扩展,ΔKth 是判断构件是否会发生裂纹亚临界扩展的指标. ② 区间II 为裂纹的亚临界扩展区;由亚临界裂纹扩展速度da/dN 与ΔK I 存在的指数规律得出的Paris 公式 da/dN=c(ΔK I )m 。 da/dN —裂纹亚临界扩展速率,a 为裂纹半长,N 为循环次数;ΔK I —在每一循环中I 型应力强度因子变化幅值; c —与平均应力、应力变化、频率、材料机械性能G 有关的常数; m —与材料有关的常数 由max min max min (I K K K F F σσ?=-=-=? 得I I K F ?=? 式中Δσ为应力变化幅度,一般 max min σσσ?=- 实验数据:da/dN 主要决定于ΔK I ,而且与试件和裂纹的特征和加载方式无关。实验室数据可以直接用于实际零件的裂纹亚临界扩展速率和裂纹体剩余寿命的计算。 ③区间IIIda/dN 剧增,裂纹迅速作临界失稳扩展,引起断裂。 由于考虑到Paris 公式只适用于低应力、高疲劳强度问题,未考虑第二位因素的影响,如平均应力、介质条件、温度、过载峰、加载方式、加载频率等。 (1)对于平均应力的影响,对裂纹扩展速率由显著影响,平均应力越大,da/dN 越大。Forman 提出了修正公式,考虑了K Ⅰ趋近临界值K C 时裂纹的加速扩展效应和平均应力的影响: 10()m I C I c K da dN K K ??=?-? 其中: min max (1);; C c C K r K F r K F σσσ?=-=??==? 式中c 、m —材料常数; K C —平面应力断裂韧性;考虑到零件的表面残余压应力可以提高疲劳强度,其 05、基本知识 怎样推导梁的应力公式、变形公式(供参考) 同学们学习下面内容后,一定要向老师回信(849896803@https://www.360docs.net/doc/9d7654179.html, ),说出你对本资料的看法(收获、不懂的地方、资料有错的地方),以便考核你的平时成绩和改进我的工作。回信请注明班级和学号的后面三位数。 1 * 问题的提出 ........................................................................................................................... 1 2 下面就用统一的步骤,研究梁的应力公式和变形公式。 ................................................... 2 3 1.1梁的纯弯曲(纯弯曲:横截面上无剪力的粱段)应力公式推导 ................................. 2 4 1.2 梁弯曲的变形公式推导(仅研究纯弯曲) .................................................................... 5 5 1.3 弯曲应力公式和变形公式的简要推导 ............................................................................ 6 6 1.4 梁弯曲的正应力强度条件和刚度条件的建立 ................................................................ 7 7 2.1 梁剪切的应力公式推导 .................................................................................................... 8 8 2.2 梁弯曲的剪应力强度条件的建立 .................................................................................... 8 9 3. 轴向拉压、扭转、梁的弯曲剪切,应力公式和变形公式推导汇总表 .. (9) 1 * 问题的提出 在材料力学里,分析杆件的强度和刚度是十分重要的,它们是材料力学的核心内容。 强度条件就是工作应力不超过许用应力,即,[]σσ许用应力工作应力≤、[]ττ≤; 刚度条件就是工作变形不超过许用变形,即,[]y y 许用变形工作变形≤、[]θθ≤。 如,梁 弯曲强度条件:[]σσ≤=W M max max ;剪切强度条件:[]τρτρ≤?= b I S F z Q * max ,max 刚度条件:挠度 ?? ? ???≤l y l y max ;转角[]??≤max 这里带方括号的,是材料的某种许用值。由材料实验确定出破坏值,再除以安全系数, 即得。 显然,不等式左侧的工作应力和工作变形计算公式,是十分重要的。如果把各种应力公式和变形公式的来历搞明白,对于如何进行强度分析和刚度分析(这是材料力学的主要内容)就会得心应手。 杆件的基本变形一共四种:轴向拉压、扭转、剪切和弯曲变形。它们分别在轴向拉压杆、扭转轴、梁的各章讲授。 其对应的公式各异,但是,推导这些公式的方法却是一样的,都要从静力、几何、物理三个方面考虑,从而导出相应的《应力公式》,在导出应力公式之后,就可以十分方便地获得《变形公式》。 148 第6章 结构件及连接的疲劳强度 随着社会生产力的发展,起重机械的应用越来越频繁,对起重机械的工作级别要求越来越高。《起重机设计规范》GB/T 3811-2008规定,应计算构件及连接的抗疲劳强度。对于结构疲劳强度计算,常采用应力比法和应力幅法,本章仅介绍起重机械常用的应力比法。 6.1 循环作用的载荷和应力 起重机的作业是循环往复的,其钢结构或连接必然承受循环交变作用的载荷,在结构或连接中产生的应力是变幅循环应力,如图6-1所示。 起重机的一个工作循环中,结构或连接中某点的循环应力也是变幅循环应力。起重机工作过程中每个工作循环中应力的变化都是随机的,难以用实验的方法确定其构件或连接的抗疲劳强度。然而,其结构或连接在等应力比的变幅循环或等幅应力循环作用下的疲劳强度是可以用实验的方法确定的,对于起重机构件或连接的疲劳强度可以用循环记数法计算出整个 循环应力中的各应力循环参数,将其转化为等应力比的变幅循环应力或转化为等平均应力的等幅循环应力。最后,采用累积损伤理论来计算构件或连接的抗疲劳强度。 6.1.1 循环应力的特征参数 (1) 最大应力 一个循环中峰值和谷值两极值应力中绝对值最大的应力,用max σ表示。 (2) 最小应力 一个循环中峰值和谷值两极值应力中绝对值最小的应力,用min σ表示。 (3) 整个工作循环中最大应力值 构件或连接整个工作循环中最大应力的数值,用max ?σ 表示。 (4) 应力循环特性值 一个循环中最小应力与最大应力的比值,用min max r σσ=表示。 (5) 循环应力的应力幅 一个循环中最大的应力与最小的应力的差的绝对值,用σ?表示。 第四节 许用应力·安全系数·强度条件. 强度计算。三角函数 由脆性材料制成的构件,在拉力作用下,当变形很小时就会突然断裂,脆性材料断裂时的应力即强度极限σb ;塑性材料制成的构件,在拉断之前已出现塑性变形,在不考虑塑性变形力学设计方法的情况下,考虑到构件不能保持原有的形状和尺寸,故认为它已不能正常工作,塑性材料到达屈服时的应力即屈服极限σs 。脆性材料的强度极限σb 、塑性材料屈服极限σs 称为构件失效的极限应力。为保证构件具有足够的强度,构件在外力作用下的最大工作应力必须小于材料的极限应力。在强度计算中,把材料的极限应力除以一个大于1的系数n (称为安全系数),作为构件工作时所允许的最大应力,称为材料的许用应力,以[σ]表示。对于脆性材料,许用应力 (5-8) 对于塑性材料,许用应力 (5-9) 其中、分别为脆性材料、塑性材料对应的安全系数。 安全系数的确定除了要考虑载荷变化,构件加工精度不同,计算差异,工作环境的变化等因素外,还要考虑材料的性能差异(塑性材料或脆性材料)及材质的均匀性,以及构件在设备中的重要性,损坏后造成后果的严重程度。 安全系数的选取,必须体现既安全又经济的设计思想,通常由国家有关部门制订,公布在有关的规范中供设计时参考,一般在静载下,对塑性材料可取;脆性材料均匀性差,且断裂突然发生,有更大的危险性,所以取,甚至取到5~9。 为了保证构件在外力作用下安全可靠地工作,必须使构件的最大工作应力小于材料的许用应力,即 (5-10) 上式就是杆件受轴向拉伸或压缩时的强度条件。根据这一强度条件,可以进行杆件如下三方 面的计算。 1.强度校核 已知杆件的尺寸、所受载荷和材料的许用应力,直接应用(5-10)式,验算杆件是否满足强度条件。 2.截面设计 已知杆件所受载荷和材料的许用应力,将公式(5-10)改成 , 由强度条件确定杆件所需的横截面面积。 3.许用载荷的确定 已知杆件的横截面尺寸和材料的许用应力,由强度条件 确定杆件所能承受的最大轴力,最后通过静力学平衡方程算出杆件所能承担的 最大许可载荷。 例5-4 一结构包括钢杆1和铜杆2,如图5-21a 所示,A 、B 、C 处为铰链连接。在 b b n σσ= ][s s n σσ= ][b n s n 0.2~5.1=s n 0.5~0.2=b n ][max max σσ≤= A N ][σN A ≥ ][max σA N ≤ 1、钢受均布荷载 (1)工字钢力学正应力计算: 根据材料力学正应力计算公式: max M max W , 其中: 12#矿用工字钢的许用应力510 MPa 12#矿用工字钢抗弯截面W系数为 144.5 cm 3最大弯矩 M max0.125ql 2 q为顶板作用在工字钢上的压力 工字钢长度 l 按4米计算 得出: 5101060.125q 46 2 , 144.510 510106144.510 6 36847.5N q 0.12542 (2)工字钢最大弯曲下沉量计算: 根据工字钢挠度计算公式:max5ql 4 384EI 其中: q已计算得出为 工字钢长度 l 按4米计算弹性 模量 E=206GPa 12#工字钢惯 性矩为 867.1cm4 得出: max 536847.5440.068 206109867.110 8 384 2、工字钢受集中荷载 (1)工字钢力学正应力计算: 根据材料力学正应力计算公式: max M max W , 其中: 12#矿用工字钢的许用应力510 MPa 12#矿用工字钢抗弯截面W系数为 144.5 cm 3最大弯矩 M max0.25Fl 2 F为顶板作用在工字钢上的压力 工字钢长度 l 按4米计算 得出: 5101060.25F 46 2 , 144.510 510106144.5106 F 0.2542 18423 .75N (2)工字钢最大弯曲下沉量计算: 根据工字钢挠度计算公式:Fl 3 max 48EI 其中: q已计算得出为 工字钢长度 l 按4米计算弹性 模量 E=206GPa 12#工字钢惯 性矩为 867.1cm4 得出:max18423 .75430.0013 20610 9867.110 8 48 第一章绪论 【例1-1】钻床如图1-6a所示,在载荷P作用下,试确定截面m-m上的内力。 【解】(1)沿m-m 截面假想地将钻床分成两部分。取m-m 截面以上部分进行研究(图1-6b),并以截面的形心O为原点。选取坐标系如图所示。 (2)为保持上部的平衡,m-m 截面上必然有通过点O的内力N和绕点O的力偶矩M。 (3)由平衡条件 ∴ 【例1-2】图1-9a所示为一矩形截面薄板受均布力p作用,已知边长=400mm,受力后沿x方向均匀伸长Δ=0.05mm。试求板中a点沿x方向的正应变。 【解】由于矩形截面薄板沿x方向均匀受力,可认为板内各点沿x方向具有正应力与正 应变,且处处相同,所以平均应变即a 点沿x 方向的正应变。 x 方向 【例1-3】 图1-9b 所示为一嵌于四连杆机构内的薄方板,b=250mm 。若在p 力作用下CD 杆下移Δb=0.025,试求薄板中a 点的剪应变。 【解】由于薄方板变形受四连杆机构的制约,可认为板中各点均产生剪应变,且处处相同。 第二章 拉伸、压缩与剪切 【例题2.1】 一等直杆所受外力如图2. 1 (a)所示,试求各段截面上的轴力,并作杆的轴力图。 解:在AB 段范围内任一横截面处将杆截开,取左段为脱离体(如图2. 1 (b)所示),假定轴力N1F 为拉力(以后轴力都按拉力假设),由平衡方程 0x F =∑,N1300F -= 得 N130kN F = 结果为正值,故N1F 为拉力。 同理,可求得BC 段内任一横截面上的轴力(如图2. 1 (c)所示)为 N2304070(kN)F =+= 在求CD 段内的轴力时,将杆截开后取右段为脱离体(如图2. 1 (d)所示),因为右段杆上包含的外力较少。由平衡方程 0x F =∑,N330200F --+= 材料力学常用公式 1.外力偶矩计算公式(P功率,n转速) 2.弯矩、剪力和荷载集度之间的关系式 3.轴向拉压杆横截面上正应力的计算公式(杆件横截面轴力F N,横截面面积A,拉应力 为正) 4.轴向拉压杆斜截面上的正应力与切应力计算公式(夹角a 从x轴正方向逆时针转至外法线的方位 角为正) 5.纵向变形和横向变形(拉伸前试样标距l,拉伸后试样标距l1;拉伸前试样直径d,拉伸后试样 直径d1) 6.纵向线应变和横向线应变 7.泊松比 8.胡克定律 9.受多个力作用的杆件纵向变形计算公式? 10.承受轴向分布力或变截面的杆件,纵向变形计算公式 11.轴向拉压杆的强度计算公式 12.许用应力,脆性材料,塑性材料 13.延伸率 14.截面收缩率 15.剪切胡克定律(切变模量G,切应变g ) 16.拉压弹性模量E、泊松比和切变模量G之间关系式 17.圆截面对圆心的极惯性矩(a)实心圆 (b)空心圆 18.圆轴扭转时横截面上任一点切应力计算公式(扭矩T,所求点到圆心距离r) 19.圆截面周边各点处最大切应力计算公式 20.扭转截面系数,(a)实心圆 (b)空心圆 21.薄壁圆管(壁厚δ≤ R0 /10 ,R0为圆管的平均半径)扭转切应力计算公式 22.圆轴扭转角与扭矩T、杆长l、扭转刚度GH p的关系式 23.同一材料制成的圆轴各段内的扭矩不同或各段的直径不同(如阶梯轴)时 或 24.等直圆轴强度条件 25.塑性材料;脆性材料 26.扭转圆轴的刚度条件? 或 27.受内压圆筒形薄壁容器横截面和纵截面上的应力计算公式, 28.平面应力状态下斜截面应力的一般公式 , 29.平面应力状态的三个主应力, , 30.主平面方位的计算公式 31.面内最大切应力 32.受扭圆轴表面某点的三个主应力,, 33.三向应力状态最大与最小正应力 , 34.三向应力状态最大切应力应力应变计算方法
温度应力计算
各种许用应力与抗拉强度、屈服强度的关系
应力计算
第十章-梁的应力-习题答案
工程力学第九章梁的应力及强度计算
重力坝稳定及应力计算
工字钢、H型钢计算书
地应力计算公式解读
材料力学公式汇总
力学计算公式
钢管许用应力
机械可靠性结构度计算
05、基本知识 怎样推导梁的应力公式、变形公式(供参考)
第6章结构件及连接的疲劳强度计算原理
材料的许用应力和安全系数计算三角
工字钢受力计算.docx
材料力学计算题库
材料力学常用公式