抛光工艺及技巧
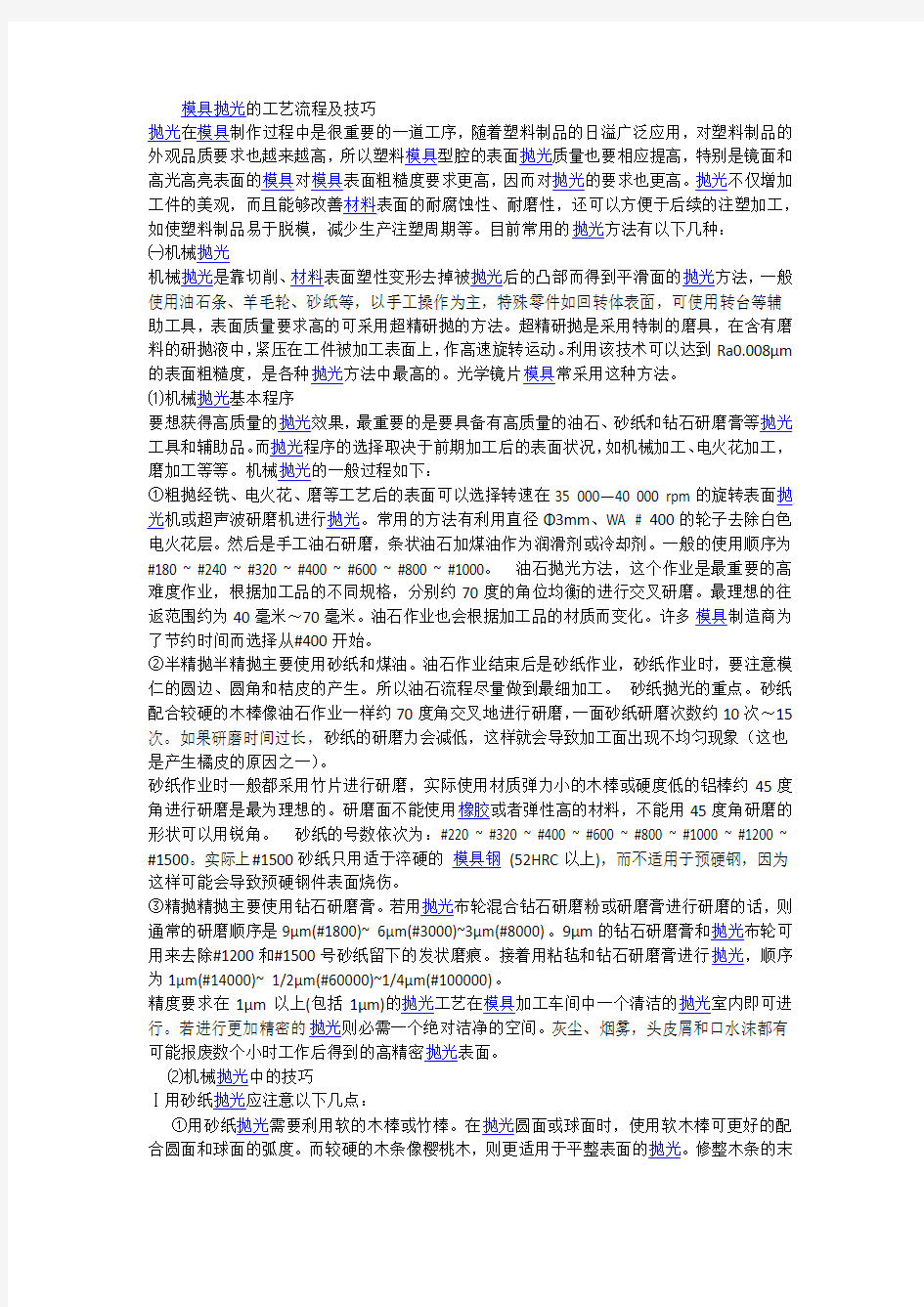

模具抛光的工艺流程及技巧
抛光在模具制作过程中是很重要的一道工序,随着塑料制品的日溢广泛应用,对塑料制品的外观品质要求也越来越高,所以塑料模具型腔的表面抛光质量也要相应提高,特别是镜面和高光高亮表面的模具对模具表面粗糙度要求更高,因而对抛光的要求也更高。抛光不仅增加工件的美观,而且能够改善材料表面的耐腐蚀性、耐磨性,还可以方便于后续的注塑加工,如使塑料制品易于脱模,减少生产注塑周期等。目前常用的抛光方法有以下几种:
㈠机械抛光
机械抛光是靠切削、材料表面塑性变形去掉被抛光后的凸部而得到平滑面的抛光方法,一般使用油石条、羊毛轮、砂纸等,以手工操作为主,特殊零件如回转体表面,可使用转台等辅助工具,表面质量要求高的可采用超精研抛的方法。超精研抛是采用特制的磨具,在含有磨料的研抛液中,紧压在工件被加工表面上,作高速旋转运动。利用该技术可以达到Ra0.008μm 的表面粗糙度,是各种抛光方法中最高的。光学镜片模具常采用这种方法。
⑴机械抛光基本程序
要想获得高质量的抛光效果,最重要的是要具备有高质量的油石、砂纸和钻石研磨膏等抛光工具和辅助品。而抛光程序的选择取决于前期加工后的表面状况,如机械加工、电火花加工,磨加工等等。机械抛光的一般过程如下:
①粗抛经铣、电火花、磨等工艺后的表面可以选择转速在35 000—40 000 rpm的旋转表面抛光机或超声波研磨机进行抛光。常用的方法有利用直径Φ3mm、WA # 400的轮子去除白色电火花层。然后是手工油石研磨,条状油石加煤油作为润滑剂或冷却剂。一般的使用顺序为#180 ~ #240 ~ #320 ~ #400 ~ #600 ~ #800 ~ #1000。油石抛光方法,这个作业是最重要的高难度作业,根据加工品的不同规格,分别约70度的角位均衡的进行交叉研磨。最理想的往返范围约为40毫米~70毫米。油石作业也会根据加工品的材质而变化。许多模具制造商为了节约时间而选择从#400开始。
②半精抛半精抛主要使用砂纸和煤油。油石作业结束后是砂纸作业,砂纸作业时,要注意模仁的圆边、圆角和桔皮的产生。所以油石流程尽量做到最细加工。砂纸抛光的重点。砂纸配合较硬的木棒像油石作业一样约70度角交叉地进行研磨,一面砂纸研磨次数约10次~15次。如果研磨时间过长,砂纸的研磨力会减低,这样就会导致加工面出现不均匀现象(这也是产生橘皮的原因之一)。
砂纸作业时一般都采用竹片进行研磨,实际使用材质弹力小的木棒或硬度低的铝棒约45度角进行研磨是最为理想的。研磨面不能使用橡胶或者弹性高的材料,不能用45度角研磨的形状可以用锐角。砂纸的号数依次为:#220 ~ #320 ~ #400 ~ #600 ~ #800 ~ #1000 ~ #1200 ~ #1500。实际上#1500砂纸只用适于淬硬的模具钢(52HRC以上),而不适用于预硬钢,因为这样可能会导致预硬钢件表面烧伤。
③精抛精抛主要使用钻石研磨膏。若用抛光布轮混合钻石研磨粉或研磨膏进行研磨的话,则通常的研磨顺序是9μm(#1800)~ 6μm(#3000)~3μm(#8000)。9μm的钻石研磨膏和抛光布轮可用来去除#1200和#1500号砂纸留下的发状磨痕。接着用粘毡和钻石研磨膏进行抛光,顺序为1μm(#14000)~ 1/2μm(#60000)~1/4μm(#100000)。
精度要求在1μm以上(包括1μm)的抛光工艺在模具加工车间中一个清洁的抛光室内即可进行。若进行更加精密的抛光则必需一个绝对洁净的空间。灰尘、烟雾,头皮屑和口水沫都有可能报废数个小时工作后得到的高精密抛光表面。
⑵机械抛光中的技巧
Ⅰ用砂纸抛光应注意以下几点:
①用砂纸抛光需要利用软的木棒或竹棒。在抛光圆面或球面时,使用软木棒可更好的配合圆面和球面的弧度。而较硬的木条像樱桃木,则更适用于平整表面的抛光。修整木条的末
端使其能与钢件表面形状保持吻合,这样可以避免木条(或竹条)的锐角接触钢件表面而造成较深的划痕。
②当换用不同型号的砂纸时,抛光方向应变换45°~ 90°,这样前一种型号砂纸抛光后留下的条纹阴影即可分辨出来。在换不同型号砂纸之前,必须用100%纯棉花沾取酒精之类的清洁液对抛光表面进行仔细的擦拭,因为一颗很小的沙砾留在表面都会毁坏接下去的整个抛光工作。从砂纸抛光换成钻石研磨膏抛光时,这个清洁过程同样重要。在抛光继续进行之前,所有颗粒和煤油都必须被完全清洁干净。
③为了避免擦伤和烧伤工件表面,在用#1200和#1500砂纸进行抛光时必须特别小心。因而有必要加载一个轻载荷以及采用两步抛光法对表面进行抛光。用每一种型号的砂纸进行抛光时都应沿两个不同方向进行两次抛光,两个方向之间每次转动45°~ 90°。
Ⅱ钻石研磨抛光应注意以下几点:
①这种抛光必须尽量在较轻的压力下进行特别是抛光预硬钢件和用细研磨膏抛光时。在用#8000研磨膏抛光时,常用载荷为100~200g/cm2,但要保持此载荷的精准度很难做到。为了更容易做到这一点,可以在木条上做一个薄且窄的手柄,比如加一铜片;或者在竹条上切去一部分而使其更加柔软。这样可以帮助控制抛光压力,以确保模具表面压力不会过高。
②当使用钻石研磨抛光时,不仅是工作表面要求洁净,工作者的双手也必须仔细清洁。
③每次抛光时间不应过长,时间越短,效果越好。如果抛光过程进行得过长将会造成“橘皮”和“点蚀”。
④为获得高质量的抛光效果,容易发热的抛光方法和工具都应避免。比如:抛光轮抛光,抛光轮产生的热量会很容易造成“橘皮”。
⑤当抛光过程停止时,保证工件表面洁净和仔细去除所有研磨剂和润滑剂非常重要,随后应在表面喷淋一层模具防锈涂层。
由于机械抛光主要还是靠人工完成,所以抛光技术目前还是影响抛光质量的主要原因。除此之外,还与模具材料、抛光前的表面状况、热处理工艺等有关。优质的钢材是获得良好抛光质量的前提条件,如果钢材表面硬度不均或特性上有差异,往往会产生抛光困难。钢材中的各种夹杂物和气孔都不利于抛光。
⑶不同硬度对抛光工艺的影响
硬度增高使研磨的困难增大,但抛光后的粗糙度减小。由于硬度的增高,要达到较低的粗糙度所需的抛光时间相应增长。同时硬度增高,抛光过度的可能性相应减少。
⑷工件表面状况对抛光工艺的影响
钢材在切削机械加工的破碎过程中,表层会因热量、内应力或其他因素而损坏,切削参数不当会影响抛光效果。电火花加工后的表面比普通机械加工或热处理后的表面更难研磨,因此电火花加工结束前应采用精规准电火花修整,否则表面会形成硬化薄层。如果电火花精修规准选择不当,热影响层的深度最大可达0.4mm。硬化薄层的硬度比基体硬度高,必须去除。因此最好增加一道粗磨加工,彻底清除损坏表面层,构成一片平均粗糙的金属面,为抛光加工提供一个良好基础。
在塑料模具加工中所说的抛光与其他行业中所要求的表面抛光有很大的不同,严格来说,模具的抛光应该称为镜面加工。它不仅对抛光本身有很高的要求并且对表面平整度、光滑度以及几何精确度也有很高的标准。表面抛光一般只要求获得光亮的表面即可。镜面加工的标准分为四级:AO=Ra0.008μm,A1=Ra0.016μm,A3=Ra0.032μm,A4=Ra0.063μm,由于电解抛光、流体抛光等方法很难精确控制零件的几何精确度,而化学抛光、超声波抛光、磁研磨抛光等方法的表面质量又达不到要求,所以精密模具的镜面加工还是以机械抛光为主。
镜面抛光的要点
超镜面抛光时最重要的一点是抛光的尺寸,油石研磨到镜面抛光的距离是10μ。(最理想是#1500(#1000)油石开始进行研磨。砂纸的号数依次为:(#320 ~ )#400 ~ #600 ~ #800 ~ #1000 ~ #1200 ~ #1500~ #01~ #02~ #03~ #04~ #05~ #06~ #015)最基本的原则,在进行下一步作业之前,一定要将模仁彻底清洗干净,才会达到好效果。要非常慎重不要重复修改(反复修改会影响品质问题)。
纳期的期限、时间上的压力、过度疲劳、集中力下降,这些因素都容易影响工作,这一点要非常注意。
抛光操作是一项耗费时间和费用昂贵的工序,遵照一定的守则可以降低抛光操作的成本。抛光的每一个步骤都必须要保持清洁,这一点最重要。
抛光注意事项:
1、抛光必须在清洁无尘的室内进行。因为硬尘粒会污染研磨材料,损害已接近完成的模具表面。
2、每个抛光工具只使用一个级别的抛光钻石膏,并存放在防尘或密封的容器内。
3、当要转换更细一级的砂号时,要注意该级砂号是否完全覆盖上一级(较粗)砂纹,必须清洗双手和工件。
4、开始抛光时要先处理角落、边角和圆角等较难抛光的地方。
5、处理尖角及边角时应特别小心,注意不要形成圆角或圆边,应尽量采用较硬的抛光工具进行模具的研磨和油石打磨。
影响表面抛光性的因素
采用研磨的方法可使模具表面光洁,光洁的程度与下列因素有关:
1、钢材品质(钢材表面硬度不均匀或特性上有差异往往会增大抛光难度)。
2、热处理工艺(热处理在很多方面会影响到抛光性能)。
3、抛光技术(抛光工艺与抛光耗材的采用直接影响到抛光效果)。
通常认为抛光技术是最重要的影响因素,恰当的抛光技术、采用良好的抛光耗材、配合品质优良的工具钢材及正确的热处理工艺才能达到满意的光洁度。反之,抛光技术与耗材使用不当,即使采用最优质的钢材也不会达到高度镜面的效果。
工件表面光洁度标准
#01钻石膏(光学要求)
#03钻石膏抛光(镜面)
#06钻石膏抛光(镜面)
#15钻石膏抛光(镜面)
1200 沙纸(光面)
1000 沙纸(光面)
800 沙纸(光面)
600 沙纸(光面)
400 沙纸(光面)
320 沙纸(光面)
1000 油石(哑面,镜面时用) 800 油石(哑面)
600 油石(哑面)
400 油石(哑面)
320 油石(哑面)
喷#11粗玻璃珠
喷#240沙
喷#24沙
汽车抛光技术工艺流程
汽车抛光技术工艺流程 抛光操作方法及流程: 如果说洗车是车体护理的基础,研磨时漆面翻新的关键,那么抛光应是漆面护理的艺术创作。 汽车漆面抛光有三个步骤即研磨、抛光、还原。抛光之所以能产生无比光亮的效果主要是靠研磨,即靠摩擦材料把细微划痕去除,其次是靠车蜡,抛光剂里大多含有增亮成分,可以依靠抛光剂的光泽来弥补漆面的缺陷。 抛光原理: 1、表面粗糙,不平:任何一点光线的射入角和折射角不一样,造成表面亮度降低。 2、表面平滑:镜面反射,射入角和反射角一致,可得到最高反射亮度。所以,美容施工一定首先要将漆面整平,才有最佳的表面亮度和保护层。 操作方法:用于研磨作业的研磨剂是在随着抛光机和研磨剂摩擦作业进行,由于磨擦起热,使研磨剂中所含的"水","溶剂"成分减少,最后研磨剂变成干燥的粉状。研磨的初期阶段,研磨剂起着润滑剂的作用,几乎没有研磨力,研磨剂薄薄地随这着抛光机的转动向外涂抹;研磨溶剂中所含的水分和溶剂为了保护研磨粒子会慢慢的干燥,研磨粒子因为有了水和溶剂保护研磨粒子就会使研磨的时间比较长;水,溶剂由于磨擦发热而被蒸发,含量也减
少,变的不能保护研磨粒子,不能受到保护的研磨粒子渐渐开始破碎,研磨力下降,但是光泽呈现出来了。为了有效的使用这种时间带,为了不让发热而进行作业,如果用过大的力进行研磨就容易起热,研磨剂很就快会完全干燥,不仅研磨剂变的失去作用,而且还会因研磨剂颗粒留下出现伤痕。抛光研磨作业不是用力和快速进行的,而是为了有效的使用研磨剂的切削性来进行。 抛光的基础使用方法 1、盘面带有角度的情况 抛光机倾斜度比较的大的情况下会使漆面起热快,而且抛光盘的边的部位摩擦力加大,容易研磨坏车漆,也会使抛光盘面的接触漆面面积会变狭窄。 2、移动抛光机的基本方法 研磨作业是为了把漆面均匀地进行研磨做为基础,为此,需要想办法"在一定程度上控制抛光所承受的压力"。 (1)按动的压力--以抛光机自身的重量为基础,把在平面上的抛光机的自身重量作为基础,不要不需要使用太大的压力,即使在侧面进行抛光作业,也是需要使用与平面同等压力。不要增加或减少压力,这样就不容易因为压力不均匀产生有的部分抛的严重有的部位较轻而产生的光圈或是划痕没有清除。 (2)盘面与抛光的角度--避免在局部增加压力 抛光是根据盘面的形状使用压力。如果过度地抛光会形成"研磨面不均匀","抛光分界线","抛光伤痕"等原因,由于局部发热,会
打磨工安全操作规程
打磨工是、加工业、业、木业、皮革业等打磨工艺的工人。其工作目的是去除产品工件表面的毛刺、使之光滑,易于继续加工或达到成品。 使用的工具是主要是、磨机等。较小的手工作坊也有用角磨机,用砂纸手工操作。[1] 打磨工安全操作规程 一、工作时必须戴好防护口罩(或防护面罩)及眼镜。 二、工作前,应检查砂轮有无损坏,安全防护装置是否完好,通风除尘装置是否有效。 三、安装砂轮前,必须核对砂轮允许的最高速度是否与主轴速度相适 应,大于200毫米的砂轮应进行静平衡,不准使用有裂纹或缺损的砂轮。 四、砂轮卡盘直径不得小于砂轮直径的 1/3,卡盘与砂轮间应垫上1—2毫米的软寸垫,其外直径应比卡盘压紧面的直径大2毫米。 五、安装时,应注意螺母的压紧程度,应压紧到砂轮运动时不产生滑 动为易,有多个压紧螺丝钉时,应按对角顺序逐步均匀旋紧。 六、砂轮装好后,必须将防护罩重新装好,再进行试转。直的砂轮,
应空转5分钟。砂轮转动时,不允许有明显震动。 七、调整砂轮防护罩及工件托架时,必须在砂轮停转后,放准进行。 经常保持工件托架与砂轮的距离小于3毫米。 八、打磨时,应先启动吸尘装置,握牢工件,用力不得过猛,不准用 杠杆推压元件,严禁站在砂轮正面操作,以防砂轮破裂伤人。 九、不是专门用于端面磨削的砂轮,禁止用端面进行打磨。 十、使用手持电动砂轮机打磨时,必须有牢固的防护罩和加设保护接零线,或配用漏电保护器,并遵守以下电动手砂轮安全操作规程。 1、如电源线在工作中受损或断裂,勿触摸导线,应马上拔出插头。 2、工作时防止触碰机器的后端。 3、作业中如果砂轮片被卡住,此时必须马上关闭机器。 4、勿将手持电动砂轮机固定在虎钳上。 十一、两人以上同时施工,不准同时在同一方向相对作业,防止发生意外。
喷漆工艺操作规范
精心整理 喷漆工艺流程 喷漆工艺标准流程 1. 检查钣金修复的平整度: 首先对要喷漆的部位进行检查是否平整,擦干净没有钣金的喷漆部份,检查是否有凹陷。 2. 打磨处理需要补土的部份: 用砂轮机将钣金边缘进行处理,用砂纸将钣金周围磨出羽状边,再用砂纸打磨旧漆面,扩大补土的范围。 3. 清洁涂油 打磨完成后,清洗干净打磨位置及喷漆位置。 4,中涂5, 6. 7. 8. 9完成打 1011. 12. 13. 漆面抛光是汽车美容技术中最重要的组成部分。抛光技术水平的高低直接关系到汽车美容的最终效果。因此,抛光技术是汽车美容服务的基础。车身漆面彻底清洁后,就可根据漆面损伤的程度进行抛光处理。 一、材料选用及抛光方法 以英国特使系列产品为例,特使系列C3全能抛光剂含有研磨剂、去污剂、还原剂、光亮剂等多种成分,专为车身镜面抛光而设计,已被越来越多的欧美汽车厂指定使用。这种产品抛光速度快,可快速去除交通膜及中度划痕,不伤漆面,不留光环,节省工时,1小时可抛光、翻新一辆旧车漆面。抛光后残留物少,容易擦净,克服了其他同类产品抛光后残窖物到处飞溅,不易清除的缺点。可有效解决漆面划痕、哑光、褪色、氧化、粗糙等漆面缺陷,尤其适用于旧车漆面、划痕较深的漆面和桔皮、流挂等,若配合镜面釉使用,瞬间即可达到超亮镜面效果,是护车“三宝”中的重点用品。
抛光方法:将抛光机调整好转速,海绵轮用水充分润湿后,甩去多余水分。先取少量C3抛光剂涂于漆面(每一小块作一次处理,不可大范围涂抹),从车顶篷开始抛光。抛光机的海绵轮应保持与漆面相切,力度适中,速度保持一定。抛光时按一定的顺序抛光,不可随意进行。用过C3抛光剂后,再换用增艳剂按以上步骤操作一次。 二、镜面釉处理 当整车漆面处理完毕后,漆面会很平滑、光亮,但有时也还会有一些极其细小的划痕和花痕或光环,为了保持漆面的光滑和光亮,则需上特使系列镜面釉。这种镜面釉以高分子釉剂等聚合物为主要原材料,不含蜡、硅及硝基合成氨,可在任何车型的漆面上做出釉质镜面效果,在汽车漆面上形成具有光滑、明亮、密封的釉质镜面保护膜,专车身时刻保持光亮如镜。同时具有防酸雨、抗氧化、防紫外线、防褪色等多项显著功能,还可抵御硬物轻度刮伤,不怕火和油污等,并具有一年以上的保持功效。 1 2 3 4 不 以下 1 2接下来是涂原子灰,晾干后打磨。这个工序最费时也很重要,一般需要重复涂抹打磨几次,需要用到 120#240#360#600#水砂纸, 3涂抹添眼灰。作用是掩盖原子灰上的砂纸痕和气孔。然后用1000#或1200#水砂纸打磨。 4洗车,用气枪将喷涂部位吹干。然后用报纸遮挡不需要喷涂的部位。 5喷漆, 喷塑 将塑料粉末喷涂在零件上的种表面处理方法。 静电喷涂工艺(静电喷塑)具有的优势: 不需稀料,施工对环境无污染,对人体无毒害;涂层外观质量优异,附着力及机械强度强;喷涂施工固化时间短;涂层耐腐耐磨能力高出很多;不需底漆;施工简便,对工人技术要求低;成本低于喷漆工艺;有些施工场合已经明确提出必须使用静电喷塑工艺处理;静电喷粉喷涂过程中不会出现喷漆工艺中常见的流淌现象。
喷漆工艺流程
喷漆工艺标准流程 1、检查钣金修复的平整度: 首先对要喷漆的部位进行检查是否平整,擦干净没有钣金的喷漆部份,检查是否有凹陷。 2、打磨处理需要补土的部份: 用砂轮机将钣金边缘进行处理,用砂纸将钣金周围磨出羽状边,再用砂纸打磨旧漆面,扩大补土的范围。 3、清洁涂油 打磨完成后,清洗干净打磨位置及喷漆位置。 4、中涂 尽量控制中涂底漆在较小的范围,并注意边缘位置要渐进,不要成台阶状。 5、打磨中涂 待中涂底漆干燥固化后,用砂纸打磨中涂底漆,并准备补土。 6、补土 将低凹处的汽车表面用原子灰将其补平,待干打磨。 7、研磨 根据不同的表面形状选择不同的打磨方式后将原子灰的边缘与原车旧漆平稳过渡至原车的流水线要求。 8、喷底漆或刮填眼灰 对补土处进行喷涂底漆或刮填眼灰并平整原子灰的一些小孔和涂物损坏处。 9、底漆打磨 对底漆或填眼灰进行打磨,平整后用砂纸扩大打磨范围,增强新漆面在旧漆膜上的附着力,完成打磨后便可进入喷漆前的准备。 10、吹水遮蔽 对要喷漆的范围内所有的边缘接口,用压缩空气的方式将边缝内的水吹干,对不喷漆的部位进行遮蔽。 11、涂油,涂尘 用除油剂清洁整个需要喷涂的工作,用粘尘布进行喷涂前涂尘工作。 12、喷漆面漆 喷漆面漆可分三个工序:A,单工序——单工序针对纯色漆。B,双工序——双工序针对金属漆。 C,三工序——三工序针对白珍珠,变色龙。(注:针对不同色漆~所喷涂面漆的施工工艺流程不同。) 13、打磨抛光 用水磨砂纸,打磨漆面上面的尘点及橘皮纹后用腊抛光
漆面抛光是汽车美容技术中最重要的组成部分。抛光技术水平的高低直接关系到汽车美容的最终效果。因此,抛光技术是汽车美容服务的基础。车身漆面彻底清洁后,就可根据漆面损伤的程度进行抛光处理。 一、材料选用及抛光方法 以英国特使系列产品为例,特使系列C3全能抛光剂含有研磨剂、去污剂、还原剂、光亮剂等多种成分,专为车身镜面抛光而设计,已被越来越多的欧美汽车厂指定使用。这种产品抛光速度快,可快速去除交通膜及中度划痕,不伤漆面,不留光环,节省工时,1小时可抛光、翻新一辆旧车漆面。抛光后残留物少,容易擦净,克服了其他同类产品抛光后残窖物到处飞溅,不易清除的缺点。可有效解决漆面划痕、哑光、褪色、氧化、粗糙等漆面缺陷,尤其适用于旧车漆面、划痕较深的漆面和桔皮、流挂等,若配合镜面釉使用,瞬间即可达到超亮镜面效果,是护车“三宝”中的重点用品。 抛光方法:将抛光机调整好转速,海绵轮用水充分润湿后,甩去多余水分。先取少量C3抛光剂涂于漆面(每一小块作一次处理,不可大范围涂抹),从车顶篷开始抛光。抛光机的海绵轮应保持与漆面相切,力度适中,速度保持一定。抛光时按一定的顺序抛光,不可随意进行。用过C3抛光剂后,再换用增艳剂按以上步骤操作一次。 二、镜面釉处理 当整车漆面处理完毕后,漆面会很平滑、光亮,但有时也还会有一些极其细小的划痕和花痕或光环,为了保持漆面的光滑和光亮,则需上特使系列镜面釉。这种镜面釉以高分子釉剂等聚合物为主要原材料,不含蜡、硅及硝基合成氨,可在任何车型的漆面上做出釉质镜面效果,在汽车漆面上形成具有光滑、明亮、密封的釉质镜面保护膜,专车身时刻保持光亮如镜。同时具有防酸雨、抗氧化、防紫外线、防褪色等多项显著功能,还可抵御硬物轻度刮伤,不怕火和油污等,并具有一年以上的保持功效。 使用方法:使用时先用干净软布将抛光残留物清除干净,摇匀镜面釉,用软布或海绵将其涂在漆面上,停留60s后用手工或机器抛光。机器抛光保持转速在1000r/min以下,最后用干净软布擦去残留物。手工处理时,直线抛光、抛亮即可。 注意事项: 控制抛光机的转速,不可超过选定的速度范围; 保持抛光方向的一致性,应有一定的次序; 更换抛光剂的同时更换海绵轮,不可混用海绵轮; 严禁使用羊毛轮进行镜面釉处理。 三、漆面护理 抛光后并做过镜面釉处理的漆面,必须再上蜡层才能完成最后的保护,这样才会更加充分地达到保护汽车的目的。因为漆面长期与外界接触,受外部影响很大,紫外线、雨水、树枝、石块等均可对漆面造成伤害。为了保持汽车的整体美,必须注意随时上蜡保护,一般每2个月左右一次,根据气候等外部条件随时调整。
模具抛光的工艺流程及技巧
模具抛光的工艺流程及技巧 抛光在模具制作过程中是很重要的一道工序,也是收官之作,随着塑料制品的日溢广泛应用,对塑料制品的外观品质要求也越来越高,所以塑料模具型腔的表面抛光质量也要相应提高,特别是镜面和高光高亮表面的模具对模具表面粗糙度要求更高,因而对抛光的要求也更高。抛光不仅增加工件的美观,而且能够改善材料表面的耐腐蚀性、耐磨性,还可以方便于后续的注塑加工,如使塑料制品易于脱模,减少生产注塑周期等。 目前常用的抛光方法有以下几种: ㈠机械抛光机械抛光是靠切削、材料表面塑性变形去掉被抛光后的凸部而得到平滑面的抛光方法,一般使用油石条、羊毛轮、砂纸等,以手工操作为主,特殊零件如回转体表面,可使用转台等辅助工具,表面质量要求高的可采用超精研抛的方法。超精研抛是采用特制的磨具,在含有磨料的研抛液中,紧压在工件被加工表面上,作高速旋转运动。利用该技术可以达到Ra0.008μm的表面粗糙度,是各种抛光方法中最高的。光学镜片模具常采用这种方法。 ⑴机械抛光基本程序要想获得高质量的抛光效果,最重要的是要具备有高质量的油石、砂纸和钻石研磨膏等抛光工具和辅助品。而抛光程序的选择取决于前期加工后的表面状况,如机械加工、电火花加工,磨加工等等。 机械抛光的一般过程如下:①粗抛经铣、电火花、磨等工艺后的表面可以选择转速在35 000—40 000 rpm 的旋转表面抛光机或超声波研磨机进行抛光。常用的方法有利用直径Φ3mm、WA # 400的轮子去除白色电火花层。然后是手工油石研磨,条状油石加煤油作为润滑剂或冷却剂。一般的使用顺序为#180 ~ #240 ~ #320 ~ #400 ~ #600 ~ #800 ~ #1000。许多模具制造商为了节约时间而选择从#400开始。 ②半精抛半精抛主要使用砂纸和煤油。砂纸的号数依次为:#400 ~ #600 ~ #800 ~ #1000 ~ #1200 ~ #1500。实际上#1500砂纸只用适于淬硬的模具钢(52HRC以上),而不适用于预硬钢,因为这样可能会导致预硬钢件表面烧伤。 ③精抛精抛主要使用钻石研磨膏。若用抛光布轮混合钻石研磨粉或研磨膏进行研磨的话,则通常的研磨顺序是9μm(#1800)~ 6μm(#3000)~3μm(#8000)。9μm的钻石研磨膏和抛光布轮可用来去除#1200和#1500号砂纸留下的发状磨痕。接着用粘毡和钻石研磨膏进行抛光,顺序为1μm(#14000)~ 1/2μm(#60000)~1/4μm(#100000)。 精度要求在1μm以上(包括1μm)的抛光工艺在模具加工车间中一个清洁的抛光室内即可进行。若进行更加精密的抛光则必需一个绝对洁净的空间。灰尘、烟雾,头皮屑和口水沫都有可能报废数个小时工作后得到的高精密抛光表面。 ⑵机械抛光中的技巧 Ⅰ用砂纸抛光应注意以下几点: ①用砂纸抛光需要利用软的木棒或竹棒。在抛光圆面或球面时,使用软木棒可更好的配合圆面和球面的弧 度。而较硬的木条像樱桃木,则更适用于平整表面的抛光。修整木条的末端使其能与钢件表面形状保持吻合,这样可以避免木条(或竹条)的锐角接触钢件表面而造成较深的划痕。 ②当换用不同型号的砂纸时,抛光方向应变换45°~ 90°,这样前一种型号砂纸抛光后留下的条纹阴影即 可分辨出来。在换不同型号砂纸之前,必须用100%纯棉花沾取酒精之类的清洁液对抛光表面进行仔细的擦拭,因为一颗很小的沙砾留在表面都会毁坏接下去的整个抛光工作。从砂纸抛光换成钻石研磨膏抛光时,这个清洁过程同样重要。在抛光继续进行之前,所有颗粒和煤油都必须被完全清洁干净。 ③为了避免擦伤和烧伤工件表面,在用#1200和#1500砂纸进行抛光时必须特别小心。因而有必要加载一个 轻载荷以及采用两步抛光法对表面进行抛光。用每一种型号的砂纸进行抛光时都应沿两个不同方向进行两次抛光,两个方向之间每次转动45°~ 90°。
不锈钢镜面抛光工艺及方法和要求
不锈钢镜面抛光工艺及方法和要求 不锈钢抛光工艺可以分为打磨和出光两部分。现将该两部分工艺和方法总结如下: Ⅰ.打磨 不锈钢焊接件打磨主要目标是去掉焊点,达到表面粗糙度为R10um的工件,为出光做准备! 打磨部分概括来说有: 三个工序:粗磨,半精磨,精磨 三个面:两个侧面一个棱边 九个抛光机 二十七个调节机构, 详细说明如下: 1、对上道转入抛光工序的工件进行目测检验,如焊缝是否有漏焊,焊穿,焊点深浅不均匀,偏离接缝太远,局部凹陷,对接不齐,是否有较深划痕,碰伤,严重变形等在本工序无法补救的缺陷,如果有上述缺陷应返回上道工序修整。如果无上述缺陷,进入本抛光工序。 2、粗磨,用600#的砂带在三面上往返磨削工件,本工序要达到的目标是去掉工件焊接留下的焊点,以及在上步工序出现的碰伤,达到焊口圆角初步成型,水平面和垂直面基本无大划痕,无碰伤,经此步工序后工件表面的粗糙度应能达到R0.8mm。注意在抛光过程中注意砂带机的倾斜角度和控制好砂带机对工件的压力。一般来说以与被抛面成一条直线比较适中!
3、半精磨,用800#的砂带按照前面往返磨削工件的方法中磨工件的三面,主要是对前面工序出现的接缝进行修正以及对粗磨后产生的印痕进行进一步的细磨,对前面工序留下的印痕要反复磨削,达到工件表面无划痕,基本变亮。本工序表面粗糙度应能达到R0.4mm。(注意本工序不要产生新的划痕及碰伤,因为在后面的工序无法修补此类缺陷。) 4、精磨,用1000#的砂带主要是对前步工序出现的细小纹线的修正磨削,磨削方法与上同。本工序要达到的目标是磨削部分与工件未磨削部分的接缝基本消失,工件表面进一步光亮,通过本工序磨削后的工件要基本接近镜面效果,工件表面粗糙度应能达到R0.1mm 5、关于更换砂带的说明:一般来说,600#的砂带可以抛磨1500mm长的工件6-8根,800#的砂带可以抛磨工件4-6根,1000#的砂带可以抛磨工件1-2根,具体情况还需以工件焊接焊点情况,抛光使用的压力,以及打磨的方式方法有很大的关系。另外还需注意更换砂带必须保证砂带在海绵轮上能平稳转动,以达到均匀磨削工件的目的。 打磨三个面说明:焊接件需要打磨以焊接棱边为分界线的水平和竖直的两面,具体来说一共需打磨三面,其打磨示意图如下图所示:
模具抛光的工艺流程及技巧
模具抛光的工艺流程及技巧 模具抛光的工艺流程及技巧 抛光在模具制作过程中是很重要的一道工序,也是收官之作,随着塑料制品的日溢广泛应用,对塑料制品的外观品质要求也越来越高,所以塑料模具型腔的表面抛光质量也要相应提高,特别是镜面和高光高亮表面的模具对模具表面粗糙度要求更高,因而对抛光的要求也更高。抛光不仅增加工件的美观,而且能够改善材料表面的耐腐蚀性、耐磨性,还可以方便于后续的注塑加工,如使塑料制品易于脱模,减少生产注塑周期等。目前常用的抛光方法有以下几种: ㈠机械抛光 机械抛光是靠切削、材料表面塑性变形去掉被抛光后的凸部而得到平滑面的抛光方法,一般使用油石条、羊毛轮、砂纸等,以手工操作为主,特殊零件如回转体表面,可使用转台等辅助工具,表面质量要求高的可采用超精研抛的方法。超精研抛是采用特制的磨具,在含有磨料的研抛液中,紧压在工件被加工表面上,作高速旋转运动。利用该技术可以达到Ra0.008μm的表面粗糙度,是各种抛光方法中最高的。光学镜片模具常采用这种方法。 ⑴机械抛光基本程序 要想获得高质量的抛光效果,最重要的是要具备有高质量的油石、砂纸和钻石研磨膏等抛光工具和辅助品。而抛光程序的选择取决于前期加工后的表面状况,如机械加工、电火花加工,磨加工等等。机械抛光的一般过程如下: ①粗抛经铣、电火花、磨等工艺后的表面可以选择转速在35 000—40 000 rpm的旋转表面抛光机或超声波研磨机进行抛光。常用的方法有利用直径Φ3mm、WA # 400的轮子去除白色电火花层。然后是手工油石研磨,条状油石加煤油作为润滑剂或冷却剂。一般的使用顺序为#180 ~ #240 ~ #320 ~ #400 ~ #600 ~ #800 ~ #1000。许多模具制造商为了节约时间而选择从#400开始。 ②半精抛半精抛主要使用砂纸和煤油。砂纸的号数依次为:#400 ~ #600 ~ #800 ~ #1000 ~ #1200 ~ #1500。实际上#1500砂纸只用适于淬硬的模具钢(52HRC以上),而不适用于预硬钢,因为这样可能会导致预硬钢件表面烧伤。 ③精抛精抛主要使用钻石研磨膏。若用抛光布轮混合钻石研磨粉或研磨膏进行研磨的话,则通常的研磨顺序是9μm(#1800)~ 6μ m(#3000)~3μm(#8000)。9μm的钻石研磨膏和抛光布轮可用来去除#1200和#1500号砂纸留下的发状磨痕。接着用粘毡和钻石研磨膏进行抛光,顺序为1μm(#14000)~ 1/2μm(#60000)~1/4μm(#100000)。 精度要求在1μm以上(包括1μm)的抛光工艺在模具加工车间中一个清洁的抛光室内即可进行。若进行更加精密的抛光则必需一个绝对洁净的空间。灰尘、烟雾,头皮屑和口水沫都有可能报废数个小时工作后得到的高精密抛光表面。 ⑵机械抛光中的技巧 Ⅰ用砂纸抛光应注意以下几点: ①用砂纸抛光需要利用软的木棒或竹棒。在抛光圆面或球面时,使用软木棒可更好的配合圆面和球面的弧度。而较硬的木条像樱桃木,则更适用于平整表面的抛光。修整木条的末端使其能与钢件表面形状保持吻合,这样可以避免木条(或竹条)的锐角接触钢件表面而造成较深的划痕。 ②当换用不同型号的砂纸时,抛光方向应变换45°~ 90°,这样前一种型号砂纸抛光后留下的条纹阴影即可分辨出来。在换不同型号砂纸之前,必须用100%纯棉花沾取酒精之类的清洁液对抛光表面进行仔细的擦拭,因为一颗很小的沙砾留在表面都会毁坏接下去的整个抛光工作。从砂纸抛光换成钻石研磨膏抛光时,这个清洁过程同样重要。在抛光继续进行之前,所有颗粒和煤油都必须被完全清洁干净。 ③为了避免擦伤和烧伤工件表面,在用#1200和#1500砂纸进行抛光时必须特别小心。因而有必要加载一个轻载荷以及采用两步抛光法对表面进行抛光。用每一种型号的砂纸进行抛光时都应沿两个不同方向进行两次抛光,两个方向之间每次转动45°~ 90°。 Ⅱ钻石研磨抛光应注意以下几点: ①这种抛光必须尽量在较轻的压力下进行特别是抛光预硬钢件和用细研磨膏抛光时。在用#8000研磨膏抛光时,常用载荷为100~200g/cm2,但要保持此载荷的精准度很难做到。为了更容易做到这一点,可以在木条上做一个薄且窄的手柄,比如加一铜片;或者在竹条上切去一部分而使其更加柔软。这样可以帮助控制抛光压力,以确保模具表面压力不会过高。 ②当使用钻石研磨抛光时,不仅是工作表面要求洁净,工作者的双手也必须仔细清洁。 ③每次抛光时间不应过长,时间越短,效果越好。如果抛光过程进行得过长将会造成“橘皮”和“点蚀”。 ④为获得高质量的抛光效果,容易发热的抛光方法和工具都应避免。比如:抛光轮抛光,抛光轮产生的热量会很容易造成“橘皮”。 ⑤当抛光过程停止时,保证工件表面洁净和仔细去除所有研磨剂和润滑剂非常重要,随后应在表面喷淋一层模具防锈涂层。 由于机械抛光主要还是靠人工完成,所以抛光技术目前还是影响抛光质量的主要原因。除此之外,还与模具材料、抛光前的表面状况、
打磨工艺规范
打磨工艺规范 Last revision date: 13 December 2020.
打磨工艺规范 一、打磨设备 1.角磨机 2.直磨机 二、操作规程 1. 打磨前准备: 1.1工作前应检查砂轮有无损坏,防护装置是否完好;试机,并进行调整,确保砂轮无抖动现 象。 1.2 戴好口罩和护目镜,穿好工作防护服。 1.3 打磨前必须确保工件表面无其他杂物,发现有表面缺陷等应先补焊后再打磨。 1.4 进行首件打磨,检查是否符合打磨要求,并经质检或主管确认无误,方可开始批量作业。 2.操作规范 2.1 安装砂轮时,必须核对砂轮允许的最高转速是否与主轴转速相适应。 2.2 需打磨的产品应放置平稳,小件需加以固定,以免在打磨过程中产品位移而导致加工缺陷。 2.3 正确使用打磨工具,及时检查和更换磨损严重的砂轮磨片。 2.4 打磨时应紧握打磨工具,砂轮片与工作面保持5-15°,循序渐进(A→B),不得用力过 猛而导致表面凹陷。 2.5 在打磨过程中发现产品表面有气孔,夹渣,裂纹等现象时应及时通知电焊工补焊。 2.6 打磨结束后需进行自检,打磨区域应无明显的磨纹和凹陷,周边无焊接飞溅物,符合产品 设计和工艺要求。产品应归类存放,堆放整齐有序。 三、打磨工艺规范及技术要求 1. 焊前打磨 打磨范围:全部焊缝两侧20~50mm 操作方法:打磨焊缝时用安装了不锈钢刷的直柄打磨机沿焊缝方向进行打磨;多层焊接时,每 焊完一层需打磨去除不规则的焊缝、飞溅、氧化层,保证焊接平滑过渡
技术要求:打磨出金属光泽,保证焊接区域无氧化膜,打磨纹路与焊缝方向平行且均匀、打磨 深度不超过母材厚度的5%为标准。 2. 焊缝余高的打磨 打磨范围:焊缝两侧各20-50mm的区域。 操作方法:角磨机工作时要与被打磨面平行,使焊缝余高被去除;当焊缝有凹陷时以不伤母材 为标准,严禁用千叶片端部斜铲被打磨面、不得用力过猛而导致表面凹陷。 技术要求:被打磨表面要求平滑;不伤母材,以母材的被去除量不超过5%为标准;被打磨部分表面纹路要求一致,沿焊缝方向,严禁无规律打磨。 3 去除表面划伤 打磨范围:划伤区域 操作方法:使用打磨工具沿一定的方向打磨 技术要求:被打磨表面要求平滑;不伤母材,以母材的被去除量不超过5%为标准;被打磨部分表面纹路要求一致,严禁无规律打磨。 4. 去除焊接飞溅 打磨范围:焊缝两侧各40-50mm,超过此范围的飞溅参照表面划伤打磨方法进行打磨 操作方法:使用打磨工具沿焊缝方向打磨 技术要求:打磨出金属光泽、保证焊接区域没有飞溅物;打磨纹路与焊缝方向平行;打磨深度 不超过母材厚度的5%为标准。 5. 焊缝接头的打磨 打磨范围:对焊缝接头及段焊起弧点收弧点使用直磨机进行打磨 操作方法:使用安装了合金旋转锉的直磨机对焊缝接头及段焊起弧点、收狐点进行打磨 技术要求:焊缝接头的打磨要求外形与焊缝余高一致;段狐起弧点收狐点的打磨要求在去除焊 接缺陷的情况下表面没有尖锐的棱角;不伤母材,以母材的被去除量不超过母材厚 度的5%为标准。 6. 焊缝磨平 打磨范围:焊缝及焊缝两侧各15~25mm。
省模抛光步骤
随着塑料制品日溢广泛的应用,如日化用品和饮料包装容器等,外观的需要往往要求塑料模具型腔的表面达到镜面抛光的程度。而生产光学镜片、镭射唱片等模具对表面粗糙度要求极高,因而对抛光性的要求也极高。抛光不仅增加工件的美观,而且能够改善材料表面的耐腐蚀性、耐磨性,还可以使模具拥有其它优点,如使塑料制品易于脱模,减少生产注塑周期等。因而抛光在塑料模具制作过程中很重要的一道工序。 1 抛光方法 目前常用的抛光方法有以下几种: 1.1 机械抛光 机械抛光是靠切削、材料表面塑性变形去掉被抛光后的凸部而得到平滑面的抛光方法,一般使用油石条、羊毛轮、砂纸等,以手工操作为主,特殊零件如回转体表面,可使用转台等辅助工具,表面质量要求高的可采用超精研抛的方法。超精研抛是采用特制的磨具,在含有磨料的研抛液中,紧压在工件被加工表面上,作高速旋转运动。利用该技术可以达到Ra0.008μm的表面粗糙度,是各种抛光方法中最高的。光学镜片模具常采用种方法。 1.2 化学抛光 化学抛光是让材料在化学介质中表面微观凸出的部分较凹部分优先溶解,从而得到平滑面。这种方法的主要优点是不需复杂设备,可以抛光形状复杂的工件,可以同时抛光很多工件,效率高。化学抛光的核心问题是抛光液的配制。化学抛光得到的表面粗糙度一般为数10μm。 1.3 电解抛光 电解抛光基本原理与化学抛光相同,即靠选择性的溶解材料表面微小凸出部分,使表面光滑。与化学抛光相比,可以消除阴极反应的影响,效果较好。电化学抛光过程分为两步: (1)宏观整平溶解产物向电解液中扩散,材料表面几何粗糙下降,Ra>1μm。 (2)微光平整阳极极化,表面光亮度提高,Ra<1μm。 1.4 超声波抛光
打磨工艺规范
打磨工艺规范及技术要求 一、打磨设备 1.角磨机 2.直磨机 3直砂轮机
4拉丝机 二操作规程 1. 打磨前准备: 1.1工作前应检查砂轮有无损坏,防护装置是否完好;试机,并进行调整,确保砂轮无抖动现 象。 1.2 戴好口罩和护目镜,穿好工作防护服。 1.3 打磨前必须确保工件表面无其他杂物,发现有表面缺陷等应先补焊后再打磨。 1.4 进行首件打磨,检查是否符合打磨要求,并经质检或主管确认无误,方可开始批量作业。 2.操作规范 2.1 安装砂轮时,必须核对砂轮允许的最高转速是否与主轴转速相适应。 2.2 需打磨的产品应放置平稳,小件需加以固定,以免在打磨过程中产品位导致加工缺陷。 2.3 正确使用打磨工具,及时检查和更换磨损严重的砂轮磨片。 2.4 打磨时应紧握打磨工具,砂轮片与工作面保持一定合理的角度循序渐进不得用力过猛而表 面凹陷。 2.5 在打磨过程中发现产品表面有气孔,夹渣,裂纹等现象时应及时通知金工车间进行补焊。 2.6 打磨结束后需进行自检,打磨区域应无明显的磨纹和凹陷,周边无焊接飞溅物,符合产品 设计和工艺要求。产品应归类存放,堆放整齐有序。 三打磨工艺规范及技术要求 1. 焊前打磨 1.1打磨范围:全部焊缝两侧 1.2操作方法:打磨焊缝时用安装了不锈钢刷的直柄打磨机沿焊缝方向进行打磨;多层焊接时, 每焊完一层需打磨去除不规则的焊缝飞溅、氧化层,保证焊接平滑过渡 1.3技术要求:打磨出金属光泽,保证焊接区域无氧化膜,打磨纹路与焊缝方向平行且均匀、
打磨深度不超过母材厚度的5%为标准。 2. 焊缝余高的打磨 2.1打磨范围:焊缝两侧 2.2操作方法:角磨机工作时要与被打磨面平行,使焊缝余高被去除;当焊缝有凹陷时以不伤 母材为标准,严禁用千叶片端部斜铲被打磨面、不得用力过猛而导致表面凹陷。 2.3技术要求:被打磨表面要求平滑;不伤母材,以母材的被去除量不超过5%为标准;被打 磨部分表面纹路要求一致,沿焊缝方向,严禁无规律打磨。 3去除表面划伤 3.1打磨范围:划伤区域 3.2操作方法:使用打磨工具沿一定的方向打磨 3.3技术要求:被打磨表面要求平滑;不伤母材,以母材的被去除量不超过5%为标准;被打磨 部度的5%为标准。分表面纹路要求一致,严禁无规律打磨。 4. 去除焊接飞溅 4.1打磨范围:焊缝两侧各40-50mm,超过此范围的飞溅参照表面划伤打磨方法进行打磨 4.2操作方法:使用打磨工具沿焊缝方向打磨 4.3技术要求:打磨出金属光泽、保证焊接区域没有飞溅物;打磨纹路与焊缝方向平行;打磨 深度不超过母材厚度的5%为标准。 5.焊缝接头的打磨 5.1打磨范围:对焊缝接头及段焊起弧点收弧点 5.2操作方法:使用安装了合金旋转锉的直磨机对焊缝接头及段焊起弧点、收弧点进行打磨5.3技术要求:焊缝接头的打磨要求外形与焊缝余高一致;段弧起弧点收狐点的打磨要求在去 除焊接缺陷的情况下表面没有尖锐的棱角;不伤母材,以母材的被去除量不超过母材厚度的5%为标准,打磨后整体应无毛刺、凹坑和焊接不良处。 6.焊缝磨平 6.1打磨范围:焊缝及焊缝两侧各15~25mm。 6.2操作方法:先用角磨机和百叶片沿焊缝方向进行打磨,百叶片与工作面保持5~15°夹角, 循序渐进,使焊缝磨平,母材的被去除量不超过0.2mm为标准;当焊缝有凹陷时应补焊后再打磨,不得用力过猛导致表面凹陷。 6.3技术要求:焊缝高度与母材在同一水平面上,被打磨表面要求平滑(或平滑过渡)不伤母 材,母材的被去除量不超过母材厚度5%为标准。打磨后整体应无毛刺、凹坑和焊接不良处。 7.不锈钢表面拉丝处理 7.1处理范围:产品全部表面 7.2操作方法:焊缝位置用直砂机依次用120#240#320#千叶轮进行打磨,直砂机与工件表面平 行千叶轮垂直于工件表面做往复动作。拉丝机做表面和焊缝拉丝效果处理。 7.3技术要求:打磨后部件表面无凹凸不平现象,不允许出现毛刺或者凹孔、沙眼现象;打磨 后整体表面需光滑,不锈钢产品表面或焊接部位以XX目拉丝处理,拉丝后产品表面丝向方向一致,且粗细一致。不能存在明显分层、发黑、发黄现象。拉丝后整体应无毛刺、凹坑和焊接不良处
抛光要求标准
不锈钢抛光要求标准 1范围 本标准规定了产品的表面分区、抛光后的表面质量要求、降级接收要求和检验方法。 本标准适用于黄铜材、锌合金、铝合金和不锈钢抛光产品表面质量检验。 2表面分区 产品在安装之后,按照人们观察产品的习惯,是否容易观察到产品的表面来区分产品的主要外露面、次要外露面和不易看见的面。见表1 3表面质量要求。 3.1不锈钢抛光产品 3.1.1不锈钢镜光产品 按磨光抛光工艺抛磨完工后,不锈钢镜光产品合格的表面质量按表1执行;降级接收按表2执行。
注:1、缺陷点所在的表面积是指A面、B面和C面的表面积。 2、表中限定了A面和B面缺陷点的个数,A面和B面缺陷点的个数之和,为产品表面的 缺陷点总个数。 3、表面缺陷点大于2时,两缺陷点间距大于10-20毫米。 3.1.2不锈钢拉丝产品 按磨光抛光工艺抛磨完工后,不锈钢拉丝产品表面质量按表11执行,降级接收标准按表12执行。
注:1、缺陷点所在的表面积是指A面、B面和C面的表面积。 2、表中限定了A面和B面缺陷点的个数,A面和B面缺陷点的个数之和,为产品表面的 缺陷点总个数。 3、表面缺陷点大于2时,两缺陷点间距大于10-20毫米。 4检验方法 4.1.1目力测试,视力大于1.2,在220V50HZ18/40W萤光灯和220V50HZ40W的日光灯下,目测 距离为45±5cm。 4.1.2双手带作业手套握持抛光件。 产品水平放置,目测该面,检查完后,以两手为轴旋转到相邻的一面,的角度目测,逐步检查每一面。 上一方向目测完工后,旋转90度,变为南北方向,先上下旋转一定的角度目测,逐步检查每一面。
大理石抛光工艺流程
大理石抛光工艺流程 随着时间的推移,大理石表面经过长期使用后失去了原来的色泽,那么,怎么样让大理石恢复光亮如新的色泽呢?这就需要对大理石进行翻新和抛光处理。大理石抛光是石材护理晶面处理的前一道工艺流程或石材光板加工的最后一道程序,下面,让我们看一下大理石抛光工艺流程。 一、石材抛光工序 石材抛光的工序:石材抛光是养护石材的一道重要工序,有的石材可以直接抛光,抛光主要是为了增加石材表面的亮度。石材抛光一般按照粗磨→半细磨→细磨→精磨→抛光的程序进行,也有的可以省去其中的粗磨步骤,主要是看原来石材的表面是否经过初步处理。 准备工具和材料:齐峰大理石抛光粉F-11、石材晶面机等。
二、大理石抛光流程 大理石抛光工艺流程如下: 1粗磨:要求打磨片吃刀量深,磨削效率高,磨削的纹路粗,磨出的表面较粗糙,主要清除石材在前道工序中留有的锯片痕迹并将石材的平整度,造型面磨削到位; 2半细磨:将粗磨痕迹清除,形成新的较细的纹路,使石材表面平整、顺滑; 3细磨:细磨后的石材表面花纹、颗粒、颜色已清楚地显示出来,表面细腻、光滑,开始有微弱的光泽度; 4精磨:精磨后的石材表面,无肉眼察觉的痕迹。表面越来越光
滑,光泽度最高可达到55度以上; 5抛光:使用专用的花岗岩抛光机,从50号-3000号的石材水磨片由粗到细对石材进行研磨,致使地面光亮平整如新。经抛光后的石材表面明亮如镜,其光泽度可达到85度以上。 (大理石抛光处理前后对比图) 三、大理石抛光注意事项 根据石材不同的类型,采用不同的打磨抛光流程。 1、平面板的打磨抛光流程:检查材料的状况—胶补—开机前检查—上板—切边—依次启动各磨头—观察打磨抛光的情况—调整打磨参数—烘干—打蜡、清洁—检验—下板—包装。 2、弧面板的打磨抛光流程:检查材料状况—胶补—人工粗磨—检验—上板—开机前检查—粗磨—检查粗磨情况—细磨—抛光—检查抛光情况—下板。 3、异型线条的打磨抛光流程:检查材料的状况—检查造型的形状是否合格—按标准模板画轮廓线—粗磨两端面—从两端往中间粗磨—细磨—拼接—水磨刀400#后拆开—打磨抛光—检验。 本文编辑:奇峰石材护理 时间:2014年12月14日,转载请注明出处
(完整版)打磨工通用工艺规范
打磨工通用工艺规范 编制/日期: 审核/日期: 批准/日期: 打磨工通用工艺规范
1 适用范围 本守则规定了本公司打磨工艺要求。 本守则适用于本公司下料打磨清渣,焊接件打磨工艺 2 术语 2.1打磨:通过使用手提工具操作除去工件表层材料从而使工件获得所 需要的形状或表面粗糙度 2.2 打磨修整:将焊缝局部不规则处打磨消除 2.3 全部打磨:从一侧(或两侧)打磨整个焊缝表面但不改变整个焊缝形状 2.4 磨平:从一侧(或两侧)打磨整个焊缝,使其厚度同周围表面相同 3 打磨设备 3.1 角向磨光机,直磨机 3.2 砂轮磨片 钹型砂轮型号:125X6X22.2(MM) 百叶蝶 不锈钢碗刷 4操作规程 4.1操作前准备工作 4.1.1将机台及作业场所清理干净。 4.1.2准备好待加工工件,并放置于方便作业的位置,准备好加工完成品 放置备用的托架。 4.1.3检查是否有螺丝松动、漏电,安全装置、关机按钮、事故急停装置 是否正常工作。 4.1.4检查待加工工件是否已经过品检员检验并批准放行的合格零部件。 4.1.5按照所要加工的零部件的具体要求,选择合适的砂轮。 4.1.6戴好口罩及护目镜,穿好工作服。 4.1.7安装并紧固砂轮,。 4.1.8试机,并进行调整。确保砂轮无抖动现象; 4.1.9进行首件打磨,检查是否符合打磨要求,并经质检或主管确认无误,
方可开始批量作业。 4.2操作规范 4.2.1工作前,应检查砂轮有无损坏,防护装置是否完好,通风除尘装置 是否有效。 4.2.2安装砂轮时,必须核对砂轮允许的最高转速是否与主轴转速相适应。 4.2.3需打磨的产品应放置平稳,小件需加以固定,以免在打磨过程中产 品位移而导致加工缺陷。 4.2.4正确使用打磨工具,及时检查和更换磨损严重的砂轮磨片。 4.2.5打磨时应紧握打磨工具,砂轮片与工作面保持15-30°,循序渐进 (A→B),不得用力过猛而导致表面凹陷。 4.2.6在打磨过程中发现产品表面有气孔,夹渣,裂纹等现象时应及时通 知电焊工补焊。 4.2.7打磨结束后需进行自检,打磨区域应无明显的磨纹和凹陷,周边无 焊接飞溅物,符合产品设计和工艺要求。产品应归类存放,堆放整齐有 序。 5 打磨工艺规范 5.1打磨参数 打磨电压打磨电流打磨转速砂轮直径范围
抛光技术规范
抛光技术规范 Company Document number:WTUT-WT88Y-W8BBGB-BWYTT-19998
模具抛光技术规范 一、抛光的意义 由于手机外壳外观质量要求不断提高,且多数要求为光面,而模具表面质量是注塑件表面质量的直接体现,所以抛光是一道必须认真对待的工序,马虎不得。一付抛光达到要求的模具更具有以下优点: 1、注塑产品时,产品较易脱模。 2、减轻模具受塑料气体腐蚀的程度。 3、降低由于尖角处瞬间压力过高或由于疲劳而引起模具崩裂的可能性。 二、抛光表面要求 1、定模仁抛光要求 A、表面无微型波浪形起伏不平、刮伤痕迹、细小麻点,砂纸痕迹须均匀精 细,无较深痕迹。 B、棱角、曲面过渡处等均须线条分明、干净利落,保持原来形状不变形走 样。 C、口部不反口翻边。 2、模仁及镶件抛光要求 动模仁筋条及镶件内部无倒扣,口部不翻边,最终的砂纸纹路必须沿脱模方向。 3、电极抛光要求 无毛刺、不变形、不塌角,定模精电极要求表面光滑无刀痕。 三、抛光工具 砂纸、油石、羊毛辘、毛扫、钻石膏、金刚锉、火石仔、金刚磨针、各式铜片、各式竹片、纤维油石、砂布靴、超声波抛光机、气动转动打磨机、气动前后振动抛光头。 1、砂纸:220#、320#、400#、600#、800#、1000#、1200#、1500# 2、金相砂纸:0#、2#、3#、4#、5#、6# 3、EDM油石:220#、320#、400#、600# 4、羊毛辘:圆柱形、圆椎形、方形尖咀 5、毛扫:大平面及弧面的镜面抛光用 6、钻石膏:1#(白)、3#(黄)、6#(橙)、9#(绿)、15#(蓝) 7、金刚锉:方、圆、扁、三角、弯锉及其它形状 8、火石仔:圆柱形、圆锥形、或用砂轮打成所需的形状及大小 9、金刚磨针:圆柱形、圆锥形、长圆柱形、长圆锥形 10、砂布靴:配合前后振动头及双面胶纸贴上砂纸用 11、铜片:打成扁形以方便贴上砂纸抛深筋或平面 12、竹片:各种形状适合操作及模具形状,作用是压着砂纸在模件上抛光
宝石加工工艺流程-图文详解
宝石加工工艺流程 1. 刻面型宝石加工工艺流程 开料工序主要是对大料而言,对于小料,可以直接进入冲坯工序。 亭部的研磨和抛光方法与冠部相同,因而上述的十道工序可以归纳为六道主要工序,即开料、冲坯、粘胶、圈形、研磨、抛光。 开料→ 冲坯→ 粘胶→ 圈形→ 研磨→ 抛光 1、开料 (1)劈裂法 锯劈法操作方式 将原料放在切割机上, 用锯片沿解理或裂隙方 向轻轻锯开一个小缺 口,这样原料大部分就 会自动裂开。若没有裂 开,可把原料再放在工 作台(或桌面)边缘轻 轻一磕,一般也会裂开。 ②楔劈法的操作方式,如下图所示:
楔劈法操作方式 用高硬度材料如合成刚 玉(Hm=9)的尖锐棱角, 在需要劈裂的宝石原料 表面沿解理或裂隙方向 刻划一个槽形缺口,然 后用劈楔刀刃放在缺口 上,用小锤敲击刀背, 使原料裂解开来。 (2)锯切法 ①大料的切割 A B ②小料的切割 毛坯高度适中毛坯高度过高毛坯高度过低
2、冲坯 3、粘胶 各种形状的粘杆一种常用的粘接架(顶平器)
预热宝石粘接宝石顶平校正4、圈形 手工圈形示意图 5、刻磨 用八角手加工刻面宝石的机械装置示意 6、抛光
抛光顺序:对宝石各部分刻面的抛光顺序与研磨顺序基本一样。 所以,在抛光宝石时,要适当控制抛光剂的供给量,抛光剂过多或过少都对抛光不利。 ? (标准圆钻式琢型的加工顺序和方法) 刻面型宝石的加工顺序和方法,因琢型的种类及 复杂程度不同而有所差别,但加工过程大同小 异。一般而言,刻面数量较少、对称性好的琢型 比较容易加工。 由于标准圆钻式琢型具刻面数量适中和对称性 好的特点,通常作为学习宝石加工入门的基本琢 型。 刻面宝石琢型的加工过程,一般可分为以下十个 步骤进行: (1)坯料制备 ?切割、冲坯。坯料的比例按成品琢型的比例估 计,各部分要留有充足的加工余料。
打磨工艺规范
打磨工艺规范 一、打磨设备 1.角磨机 2.直磨机 二、操作规程 1. 打磨前准备: 1.1工作前应检查砂轮有无损坏,防护装置是否完好;试机,并进行调整,确保砂轮无抖动现 象。 1.2 戴好口罩和护目镜,穿好工作防护服。 1.3 打磨前必须确保工件表面无其他杂物,发现有表面缺陷等应先补焊后再打磨。 1.4 进行首件打磨,检查是否符合打磨要求,并经质检或主管确认无误,方可开始批量作业。 2.操作规范 2.1 安装砂轮时,必须核对砂轮允许的最高转速是否与主轴转速相适应。 2.2 需打磨的产品应放置平稳,小件需加以固定,以免在打磨过程中产品位移而导致加工缺陷。 2.3 正确使用打磨工具,及时检查和更换磨损严重的砂轮磨片。 2.4 打磨时应紧握打磨工具,砂轮片与工作面保持5-15°,循序渐进(A→B),不得用力过 猛而导致表面凹陷。 2.5 在打磨过程中发现产品表面有气孔,夹渣,裂纹等现象时应及时通知电焊工补焊。? 2.6 打磨结束后需进行自检,打磨区域应无明显的磨纹和凹陷,周边无焊接飞溅物,符合产品 设计和工艺要求。产品应归类存放,堆放整齐有序。 三、打磨工艺规范及技术要求 1. 焊前打磨 打磨范围:全部焊缝两侧20~50mm 操作方法:打磨焊缝时用安装了不锈钢刷的直柄打磨机沿焊缝方向进行打磨;多层焊接时,每 焊完一层需打磨去除不规则的焊缝、飞溅、氧化层,保证焊接平滑过渡 技术要求:打磨出金属光泽,保证焊接区域无氧化膜,打磨纹路与焊缝方向平行且均匀、打磨 深度不超过母材厚度的5%为标准。 2. 焊缝余高的打磨
打磨范围:焊缝两侧各20-50mm的区域。 操作方法:角磨机工作时要与被打磨面平行,使焊缝余高被去除;当焊缝有凹陷时以不伤母材 为标准,严禁用千叶片端部斜铲被打磨面、不得用力过猛而导致表面凹陷。 技术要求:被打磨表面要求平滑;不伤母材,以母材的被去除量不超过5%为标准;被打磨部分表面纹路要求一致,沿焊缝方向,严禁无规律打磨。 3 去除表面划伤 打磨范围:划伤区域 操作方法:使用打磨工具沿一定的方向打磨 技术要求:被打磨表面要求平滑;不伤母材,以母材的被去除量不超过5%为标准;被打磨部分表面纹路要求一致,严禁无规律打磨。 4. 去除焊接飞溅 打磨范围:焊缝两侧各40-50mm,超过此范围的飞溅参照表面划伤打磨方法进行打磨 操作方法:使用打磨工具沿焊缝方向打磨 技术要求:打磨出金属光泽、保证焊接区域没有飞溅物;打磨纹路与焊缝方向平行;打磨深度 不超过母材厚度的5%为标准。 5. 焊缝接头的打磨 打磨范围:对焊缝接头及段焊起弧点收弧点使用直磨机进行打磨 操作方法:使用安装了合金旋转锉的直磨机对焊缝接头及段焊起弧点、收狐点进行打磨 技术要求:焊缝接头的打磨要求外形与焊缝余高一致;段狐起弧点收狐点的打磨要求在去除焊 接缺陷的情况下表面没有尖锐的棱角;不伤母材,以母材的被去除量不超过母材厚 度的5%为标准。 6. 焊缝磨平 打磨范围:焊缝及焊缝两侧各15~25mm。 操作方法:先用角磨机和千叶片沿焊缝方向进行打磨,千叶片与工作面保持5~15°夹角,循 序渐进,使焊缝磨平,母材的被去除量不超过0.2mm为标准;当焊缝有凹陷时应 补焊后再打磨,不得用力过猛导致表面凹陷。