化工过程强化技术研究进展
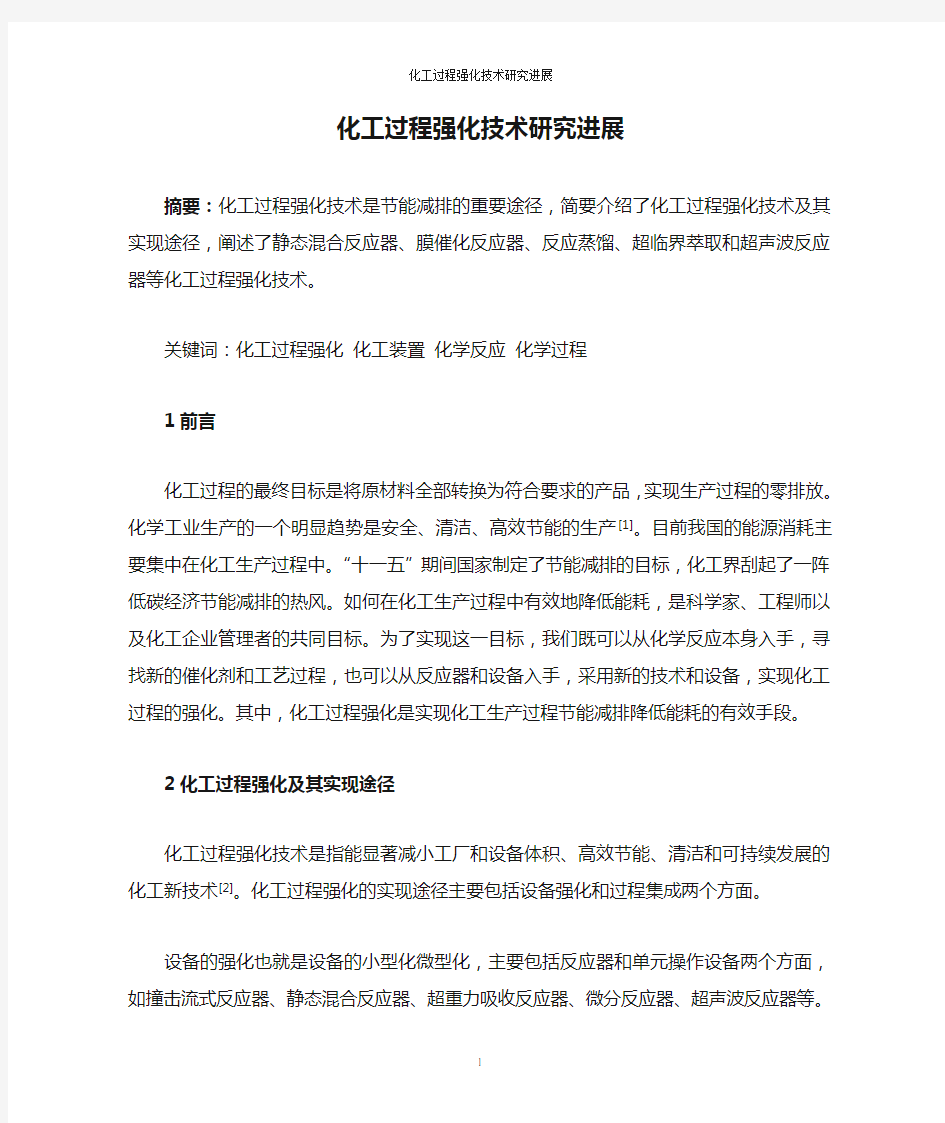

化工过程强化技术研究进展
摘要:化工过程强化技术是节能减排的重要途径,简要介绍了化工过程强化技术及其实现途径,阐述了静态混合反应器、膜催化反应器、反应蒸馏、超临界萃取和超声波反应器等化工过程强化技术。
关键词:化工过程强化化工装置化学反应化学过程
1前言
化工过程的最终目标是将原材料全部转换为符合要求的产品,实现生产过程的零排放。化学工业生产的一个明显趋势是安全、清洁、高效节能的生产[1]。目前我国的能源消耗主要集中在化工生产过程中。“十一五”期间国家制定了节能减排的目标,化工界刮起了一阵低碳经济节能减排的热风。如何在化工生产过程中有效地降低能耗,是科学家、工程师以及化工企业管理者的共同目标。为了实现这一目标,我们既可以从化学反应本身入手,寻找新的催化剂和工艺过程,也可以从反应器和设备入手,采用新的技术和设备,实现化工过程的强化。其中,化工过程强化是实现化工生产过程节能减排降低能耗的有效手段。
2化工过程强化及其实现途径
化工过程强化技术是指能显著减小工厂和设备体积、高效节能、清洁和可持续发展的化工新技术[2]。化工过程强化的实现途径主要包括设备强化和过程集成两个方面。
设备的强化也就是设备的小型化微型化,主要包括反应器和单元操作设备两个方面,如撞击流式反应器、静态混合反应器、超重力吸收反应器、微分反应器、超声波反应器等。随着科技的不断进步,近些年来开发了许多新型的反应器和单元操作设备,其中有不少应经应用于工业生产,并取得了显著的效果。这些新型的反应器被运用于合适的化工过程中,可以显著减小设备的体积,并能够显著增加设备的生产能力,从而强化了生产过程。
过程集成主要是指化工过程集成化,主要包括化学反应与分离、换热、物质相变的集成,组合分离,还有替代能源,超临界流体和离子液体,非定态操作等新技术。过程集成的技术实质是反应-分离多序的综合,质量交换网络、热量交换网络等多种综合优化,不仅要考虑稳态过程的综合,同时又考虑动态过程的特性,是一项系统的生产优化和设计优化技术[3]。
3化工生产中的过程强化技术
3.1静态混合反应器
静态混合反应器就是指在流体混合过程中,没有机械转动装置,是依靠流体自身的动力流过设置在管路中的静止插件实现的。如利用扭曲叶片或交错平板的组合等,流体流经这些结构单元后,受到混合元件的约束,产生分流、合流、旋转等行为,是流体达到有效的混合。设计高效的混合设备,实现有效混合,对于提高产品的质量、减少副产物的收率、优化整个生产过程具有重要的意义[4]。静态混合反应器作为一种新型高效的反应混合装置,可以有效地进行化工过程强化,在过程工业中应用越来越广泛,甚至在很多场合有取代传统的搅拌反应器的趋势[5]。静态混合反应器具有无须机械搅拌、可连续生产、无污染、占地面积小、分散混合效果好等优点,被广泛应用于混合、反应、分散、传质和传热等方面。郑州工业大学开发的SMGK型换热器[6]是由GK静态混合元件、换热束、折流杆构成的折流圈、壳体和带导流板的夹套组成,实践证明GK型静态混合元件强化了管内传热,提高了管内传热膜系数。方书起的研究发现[7],在同样的功率消耗条件下,GK型静态混合元件传热系数高于K型元件,大约是K型元件的1.35倍。孟中磊等[8]利用管式静态混合反应器制备生物柴油时,将管式混合反应器和共溶剂结合起来,提高了生物柴油的产率,使反应更快地进行。
3.2膜催化反应器
膜分离技术自上世纪60年代问世以来,由于具有无相变、设备简单、操作容易、能耗低和无污染等传统分离过程没有的优点而受到广泛关注。目前膜技术已包括反渗透、超过滤、微滤、渗析、电渗析、气体分离、液膜、渗透蒸发、膜反应、膜传感、控制释放及膜蒸馏等多个分支,广泛应用于化工、气体分离和生物工程等方面,强化了化工生产中的分离工程,较传统的萃取、蒸馏等分离技术有很大的技术优势。例如膜萃取技术可以避免液滴分散在另一液相中引起的夹带现象和随之产生的溶剂损失等问题,同时,由于膜萃取相中两相分开流动,互不影响,因而使萃取剂的选择余地大大放宽,而且还可避免逆流萃取中的返混现象。随着新膜研制的进展,其与化学反应过程的进一步耦合,以强化化工过程,设计新型反应器将成为膜技术应用于化工强化的发展方向。
膜催化反应是催化转化和产品分离组合起来的过程,它在催化反应发生的同时,选择性地脱除产物,以加速反应且突破反应平衡的限制,提高反应的产率、转化率和选择性[9]。采用膜催化反应器能够显著的提高反应能力,具有广泛的应用。彭少洪等[10]用多孔钛片为支撑体,将杂多化合物和具有氧溢流效应的氧化物Sb2O4制成催化膜,在特制的膜催化反应器中进行异丁烯选择氧化反应,结果表明杂多化合物-Sb2O4催化膜具有较高的催化活性。刘庆林等[11]考察了PV A-Zr(Ⅳ)膜催化乙酸和丁醇酯化反应的宏观反应动力学,认为膜催化酯化反应为扩散-反应联合控制。膜催化技术还广泛的应用于加氢领域,膜催化能有效的改善气液固三相的接触效率,因此越来越受到国内外加氢研究者的重视[12]。虽
然膜催化技术具有广阔的应用前景,研究开发也取得了一定进展,但在向工业化发展的过程中,尚有很多困难必须克服。首先是膜的制备问题,工业膜必须是大面积,要求成本低,制膜重复性好。其二是高温下设备的密封问题。其三是膜的污染和稳定问题,尤其是高温结碳对膜的污染特别严重。四是膜催化反应过程的模拟,虽然有一些学者开始进行这方面的研究,但建立较全面的膜反应器模拟方法尚是一个极富挑战性的任务[13]。
3.3反应蒸馏
反应蒸馏是将反应和蒸馏集成在一个蒸馏塔内完成。它的特点是反应和分离同时进行。因此,反应蒸馏可以及时地将一个或几个反应产物移走,提高反应选择性,减少副反应。对受化学平衡限制的反应,可以打破平衡的限制,提高原料的利用率。对放热反应,将反应放出的热量用于蒸馏分离,既可以使反应器温度分布均匀,又可以节约能量。将反应器和分离器集成在一起还减少了设备数,降低了投资。反应蒸馏已应用于生产乙酸乙酯的生产工艺,具有工艺流程简单、设备投资和操作费用低等优点[14]。刘晓欣等[15]将反应蒸馏应用于植物油酯交换制备生物柴油的研究中,结果表明此工艺具有反应速度快、平衡转化率和选择性高、甘油沉降速度快等特点。
3.4超临界萃取
超临界流体(supercritcal fluid,简称SCF)是指处于超过物质本身的临界温度和临界压力状态时的流体。超临界流体既具有液体对溶质有较大溶解度的特点,又具有气体易于扩散和运动的特点。更重要的是,超临界流体的许多性质,如黏度、密度、扩散系数、溶剂化能力等,随温度和压力变化很大,因此对选择性的分离非常敏感。超临界流体萃取(supercritical fluidextraction. 简称SFE)是利用超临界流体具有特异增加的溶解能力而发展出来的化工分离新方法。它作为一种独特、高效和清洁的新型提取、分离手段,在食品工业、精细化工、医药工业,以及环境等领域已展现出良好的应用前景,成为取代传统化学方法的首选。用正戊烷溶剂,在超临界状态下,于220℃和5MPa~15MPa循序升压条件下,将高温煤焦油萃取分馏为10个液相窄馏分和1个同相沥青产物;切割深度达78.36%,萃余沥青收率为21.64%,明显低于常规蒸馏沥青收率[16]。
超临界萃取技术是近二三十年发展起来的一种新型分离技术,它综合了溶剂萃取和蒸馏的两种功能特点。其过程是在超临界状态下使超临界流体与待分离的物质在萃取罐中接触,通过改变体系的压力和温度,使其选择性地萃取其中某一组分,经过一段时间以后,将萃取罐中的超临界流体通过减压阀进入分离罐,通过温度或压力的变化,降低超临界流体的密度,使所萃取的物质与超临界流体进行分离,而超临界流体又可循环使用。
与一般液体相比,SFE 的萃取速率和范围更为扩大,具有以下特点:
(1)通过调节温度和压力可提取纯度较高的有效成分或脱出有害成分;
(2)选择适宜的溶剂(如CO2),可在较低温度或无氧环境下操作,分离、精制热敏性物质和易氧化物质;
(3)SFE 具有良好的渗透性和溶解性,能从固体或黏稠的原料中快速提取有效成分;
(4)通过降低超临界流体的密度,容易使溶剂从产品中分离,无溶剂污染,且回收溶剂无相变过程,能耗低;
(5)兼有萃取和蒸馏的双重功效,可用于有相物的分离和精制;
(6)同类物质(如有机同系物)按沸点升高顺序进入超临界相。
我国从20 世纪70 年代末80 年代初即开展了对超临界流体技术的研究。国家对此项技术的研究也给予了较大的支持。但与世界先进水平相比,我国在这一方面尚存一定差距。虽然超临界CO2萃取技术在我国食品工业的研究开发起步较晚,但随着高新技术的发展和人们研究的不断深入,超临界CO2萃取技术必将推动功能食品的研究开发向更高层次发展。超临界流体尤其是超临界CO2,具有高溶解性和高选择性,临界温度在室温附近,安全无毒、价廉、产品纯度高,能保持产品原有的品质等优点,在食品工业特别是对高附加值天然产物和生理活性物质的提取和分离等有着广阔的应用前景。
3.5超声波反应器
超声波是一种频率高于20kHz的弹性波,由于其频率极高,因而具有一般声波所不具备的特殊效应,如机械效应、空化效应、热效应、微扰效应等。广泛应用于化工、冶金、材料、食品环境等[17-20]各行业。对化工过程,超声波的特殊效应可强化制粒过程、提取过程、化学反应过程、流体力学过程、质量传递过程和热量传递过程[21]等,它不仅加快了化工过程的反应速度,而且可以改变化学反应方向,因此超声波技术是一门很有潜力的学科。超声波的控粒作用不仅可以使大颗粒被粉碎成为高度均匀的微细颗粒,还可以使小颗粒聚集成大颗粒,以便于去除。超声波可以强化萃取、超滤等提取过程,Mauro Mecozzi[22]等以乙酸作为萃取剂利用超声波辅助萃取海底淤泥中的碳氢化合物,使萃取时间从原来的48h缩短到5h并且收率超过80%。因此,利用开发超声波的特殊效应将会使许多化工生产过程得到强化。
超声波在液体中可以产生微小的空穴。空穴在迸裂的瞬间产生高温和高压而形成特殊的环境,并由此引起流体剧烈图案东,使超声波反应器可以显著加快某些化学反应,反应速率的提高可达到几倍到几百倍。
4结语
近些年来,化工过程强化越来越受到人们的重视。展望未来,会有更多的工艺过程通过化工强化来大幅度减少设备体积、节省投资、降低能耗和减少环境污染。这样才符合节能减排、低碳环保的科学理念,才能满足生态经济和可持续发展的要求。
参考文献:
[1]Keller II G E, Bryan P F. Process Engineering Moving in New Directions. Chemical Engineering Progress . 2000(1):41—50.
[2]张永强,闵恩泽,杨克勇,杜泽学. 化工过程强化对未来化学工业的影响[J]. 石油炼制与化工,2001(6),32(6).
[3]方向晨,黎元生,刘全杰. 化工过程强化技术是节能降耗的有效手段[J]. 当代化工,2008(2),37(1).
[4]骆培成,程易,汪展文等. 液-液快速混合设备研究进展. 化工进展,2005,24(12):1319—1326.
[5]涂善东,王正东,顾伯勤等. 新世纪的化工机械技术展望. 化工进展,2003,23(3):258—266.
[6]]刘利平,马晓建,李洪亮. SMGK型换热器的应用[J]. 化工机械,2000,27(1).
[7]方书起. GK型静态混合元件的流体力学和强化传热性能研究[J]. 石油化工设备,2009(9), 38(5).
[8]孟中磊,蒋剑春,李翔宇,应浩,许玉. 管式静态混合反应器中加入共溶剂制备生物柴油[J]. 农业工程学报,2008(8), 24(8).
[9]吴雪妹.膜催化反应器及其应用研究[J]. 浙江化工,2002,4.
[10]彭少洪,毛萱,张渊明等. 杂多化合物膜催化异丁烯选择氧化反应[J]. 催化学报,2001(9), 22(5).
[11]刘庆林,肖剑,张志炳. PVA-Zr(Ⅳ)膜催化乙酸和丁醇酯化反应的特性[J]. 化工学报,2003,1.
[12]王建伟,米镇涛. 膜催化反应器及其在加氢领域的应用. 2005,第九届全国化学工艺年会.
[13]王芳,崔波,郑世清.膜催化技术的现状与展望[J]. 青岛化工学院学报,2002,2.
[14]胡松,陈清林,张冰剑. 反应蒸馏生产乙酸酯工艺研究进展[J]. 化工进展,2008,27(3).
[15]刘晓欣,胡见波,杜泽学.反应蒸馏用于植物油酯交换制备生物柴油的研究[J]. 石油炼制与化工,2007(10), 38(10).
[16]丁一慧,陈航,王东飞,马光伟等. 高温煤焦油的超临界萃取分馏研究[J]. 燃料化学学报,2010,38(2).
[17]杜永峰,苏亚凤. 超声波在化学工程中的应用[J]. 化学工程,2011,29(4).
[18]徐盛明,张传福,吴延军等. 超声波在有色冶金中的应用研究新进展[J]. 稀有金属与硬质合金,1995(6).
[19]左杜强,唐志坚,张平等. 超声波技术在环境保护领域中的应用[J].环境科学与技术,2003(6).
[20]宋永辉,兰新哲,张秋利等. 一种制备纳米银粉的新方法[J]. 西安建筑科技大学学报:自然科学版,2005,37(2)
[21]沈耀亚,赵德智,许凤军. 功率超声波在化工领域中的应用[J]. 现代化工,2000(10):14-18
[22]Mauro Mecozzi, Patrizia Dragone, Marina Amici, et al. Ultrasound assisted extraction and determination of the carbohydrate fraction in marine sediments[J]. Organic Geochemistry, 2000(31):1797-1803
1-费维扬-化工分离过程强化的若干新进展
化工分离过程强化的若干新进展 费维扬,罗淑娟,赵兴雷 (化学工程联合国家重点实验室(清华大学),北京100084)摘要: 介绍了化工分离过程的重要性、复杂性、多样性及面临的机遇和挑战。分析分离过程强化的新特点,并对它在过程工业可持续发展中的意义和作用进行讨论。 关键词:分离过程;过程强化;新分离技术;新特点 Recent advances on separation process intensification FEI Wei-yang, LUO Shu-juan, ZHAO Xing-lei (State Key Laboratory of Chemical Engineering(Tsinghua University), Beijing 100084, China) Abstract: The importance, diversity, complexity of chemical separation process and the challenge it faced are introduced in this paper. The new characteristics of separation process intensification are analyzed. Its significance and impact on sustainable development of process industry are also discussed Key words: separation process; process intensification; new separation technology; new characteristic 1概述 1.1 化工分离过程的重要性 化工分离过程是化学工程的1个重要分支,从原料的精制,中间产物的分离,产品的提纯和废水、废气的处理都有赖于化工分离技术[1-2]。绝大多数反应过程的原料和反应所得到的产物都是混合物,需要利用体系中各组分物性的差别或借助于分离剂使混合物得到分离提纯(见图1)。化工分离过程的应用遍及能源、资源、环保、生物、新材料等领域,无论是石油炼制、塑料化纤、湿法冶金、同位素分离,还是生物制品精制、纳米材料制备、烟道气脱硫和化肥生产等等都离不开化工分离过程。它往往是获得合格产品、充分利用资源和控制环境污染的关键步骤。 图1 化工分离过程的重要性 分离过程是耗能过程,设备数量众多,规模巨大。在1 000万t常、减压和100万t乙烯等特大型石化装置中,塔径10m以上的分离塔比比皆是。随着新产品的不断出现,对分离过程提出了越来越高的要求。例如医用的O18稳定同位素分离需要约2 000个理论级。化工分离过程通常占过程工业设备费和操作费的40%~70%[3],对过程的技术经济指标和产品的成本具有重要的影响。随着节能减排要求的提高
化工与装备导论课总结报告(化工过程强化)
化工与装备导论结课报告 ——对化工过程强化的初步了解化工61 刘佳明2161500015 2016年12月17日 目录 一、背景 (1) 二、过程强化的基本原理及意义 (1) 三、过程强化的基本思路及技术 (1) 1.新式设备的应用 (1) 2.物理场强化技术 (2) 3.微化工技术 (2) 4.数据集成计算 (3) 5.寻找替代能源 (4) 小结 (4) 四、现存问题及前景展望 (4) 参考文献 (5)
一、背景 化工工业是我国国民经济的重要支柱之一,多年来发展迅猛。但是它所带来的环境污染、能源消耗、安全事故频发等问题却逐渐凸显。化工工业的发展逐步进入瓶颈期,甚至有人说化工工业已成为夕阳产业。 过程强化概念的出现,及相关理论的研究和相关技术的实际应用为化工工业发展开辟了新的发展道路,让化工工业再次找到了光明的前景。过程强化技术的发展和进一步应用是化工工业迈向未来的必然要求,是化工工业发挥继续应有作用的基础与前提。它于对化学反应过程本身的研究一同成为使化工向能源节约型、环境友好型的绿色、安全化工发展的必然途径。 二、过程强化的基本原理及意义 化工过程强化技术是在实现生产目标的前提下,通过物理和化学手段,显著提升瓶颈过程速率,大幅度减少设备尺寸和数目,简化工艺流程,使工厂布局更加紧凑合理,单位能耗、废料、副产品显著减少的技术,即通过技术创新,改进工艺流程,提高设备效率,使工厂布局更紧凑,单位能耗更低,三废更少,实现化学工程的微型高效。它以设备计算软件为支持,数学模拟为重要手段,过程优化和工艺过程研究为主线。它通过物理场强化、微化工工艺、膜过程耦合、超临界流体、数据集成计算等技术,显著增强化工生产中传质、传热、传动效率,加快化学反应的速率并使其转化率充分提高;力求达到使生产原料全部转化为产品,实现零排放;同时又能够避免传统工艺中的诸多不安全因素,显著降低化工生产中的安全风险。 三、过程强化的基本思路及技术 1.新式设备的应用 过程强化设备包括静态混合反应器、微型反应器、规整结构催化反应器。 静态混合反应器即通过一定的特殊结构,使流体被迫发生性态的变化,以使流体充分快速混合的设备。它的结构紧凑,传质、传热、传动性能好,转化率高,全密闭无污染,安全性能好。解决了传统釜式反应器内部物料局部过热、设备笨重难以维修等问题。易于实现高效连续生产。 微型反应器的特征尺寸在数百微米内,能够实现微米尺度分散的单项或多项
典型有机化工过程的传递与反应协同机制及强化重大项目指引
附件2: “典型有机化工过程的传递与反应协同机制及强化” 重大项目指南 化学工业是我国国民经济支柱产业,而有机化工是化学工业的主导产业,包括基本有机化工、精细化工、三大高分子合成材料等,其有机产品的合成,约90%以上是以三烯(乙烯、丙烯、丁二烯)、三苯(苯、甲苯、二甲苯)、甲烷和乙炔等为基础原料,经氧化、磺化、卤化、硝化等有机分子官能化反应得到,因此“官能化”反应成为有机化工的关键过程。该关键过程涉及多相复杂体系内的快速反应,通常受分子混合、传递的限制,对反应速率与传递过程的匹配性有严格的要求。由于对反应与传递的协同机理的认识不够,特别是对微观尺度上的传递和混合机制缺乏深入的认识,难以选择合适的调控手段,造成目前工业反应过程的选择性低和收率低等问题,导致高能耗、高污染、高物耗,使有机化工成为化学工业“节能减排”的重点领域。 本项目针对氧化、磺化等典型有机化工“官能化”反应体系,围绕液相快速反应体系的分子混合机理及过程强化、多相反应体系的微纳尺度分散相形成机制与界面传递规律等关键科学问题,以提高反应选择性和收率、减少能耗和物耗并从源头上消除污染为目标,开展从宏观到微观的物质传递与反应过程协同性的科学规律及理论模型研究,采用非常规外场强化等手段,实现典型有机化工关键过程物质传递与反应过程的强化和耦合调控,形成超重力强化、等离子体强化、膜技术强化与调控的关键技术与新工艺,为具有原创性的“节能减排”重大工程应用奠定科学基础。 一、科学目标 针对磺化和氧化等典型“官能化”有机化工反应过程,采用理论分析、实验研究和计算机模拟相结合的方法,研究液相快速反应体系内的分子混合与传递机理、多相复杂反应体系的微纳尺度分散相的形成规律与界面传递现象、外场对化工过程传递与反应的强化机制和耦合协调规律,建立传递与反应协同作用新理论模型,应用超重力、等离子体、膜技术等强化手段,实现物质传递与反应过程的协调匹配和调控,解决反应选择性低和收率低的
化工过程强化的发展现状
化工过程强化的发展现状 目录 1.前言 (2) 2. 发展 (2) 2.1 起源和历史 (2) 2.2 以硬件为主的化工过程强化 (3) 2.3 强调硬件和软件结合的化工过程强化 (3) 2.4 耦合技术迅速发展 (3) 2.5 信息技术对化工过程强化发挥越来越大的作用 (3) 2.6 从实现可持续发展的高度来推动化工过程强化 (4) 3. 化工过程强化的作用 (4) 4. 化工过程强化手段分析 (4) 4.1 化工过程强化设备 (4) 4.1.1 多功能反应器 (4) 4.1.2 微反应器 (5) 4.1.3 旋转盘反应器和超重力反应器 (5) 4.1.4 新型催化反应器 (6) 4.1.5 超声波反应器 (6) 4.2 化工过程强化技术 (7) 4.2.1 膜技术 (7) 4.2.2 脉动燃烧干燥技术 (7) 4.2.3 超临界流体技术 (7) 4.2.4 离子液体 (7) 4.2.5 微化工技术 (8) 4.3 其它方法 (8) 5. 化工过程强化应用实例 (9) 5.1 超重力法合成纳米颗粒 (9) 5.2 悬浮床催化蒸馏的应用(SCD新工艺合成异丙苯) (10) 6. 问题与挑战 (11) 参考文献 (12)
1.前言 我们的生活与化学工业息息相关,医药、塑料、橡胶、汽油等都是化学工业制造的,这些工业是高利润的产业,是国民经济的支柱,但在这些产品的化工生产过程中所存在的高能耗、高污染等问题一直以来都是实现可持续发展首要解决的问题[1]。强化化工过程使之达到高效、节能和无污染,是解决过程工业带来的“发展-污染”的矛盾和实现可持续发展的有效手段。 化工过程强化就是通过技术创新,改进工艺流程,在实现既定生产目标的前提下,通过大幅度减小生产设备的尺寸、减少装置的数目等方法来使工厂布局更加紧凑合理,单位能耗更低,废料、副产品更少。广义上说,过程强化包括新装置和新工艺方法的发展:一是生产设备的强化,包括新型反应器、新型热交换器、高效填料、新型塔板等;二是生产过程的强化,如反应和分离的耦合(如反应精馏、膜反应、反应萃取等)、组合分离过程(如膜吸收、膜精馏、膜萃取、吸收精馏等)、外场作用(离心场、超声、太阳能等)以及其他新技术(如超临界流体、动态反应操作系统等)的应用等[2]。所以过程强化是国内外化工界长期奋斗的目标,也是化学科学和工程研究的主要成果之一。 化工过程强化是国内外化工界长期奋斗的目标,近年来更加引起了人们的重视。在美国等许多发达国家,化工过程强化被列为当前化学工程优先发展的三大领域之一。英国将重点放在基础研究上,法国则重视理论模型的建立,德过侧重实验技术和工程研究等,日本在生物工程和新材料的研究方面投入了很大的力量,加拿大和澳大利亚则以资源利用为研究重点等。我国化学工程研究和应用也取得了重大的进展。例如石油工业的崛起大大推动了催化剂、反应工程和精馏技术的发展,核燃料后处理和湿法冶金的发展推动了溶剂萃取技术水平的提高等[1~2]。目前,化工过程强化技术已被列为“十一五”首批启动的国家“863”计划的中的项目之一,以实现节能减排。 2. 发展 随着现代过程工业的发展,产品不断更新,环保要求日益提高,建设生态经济和实现可持续发展的要求更为迫切。因此,人们力图灵活应用化学工程的原理和方法,致力于过程强化,即通过技术创新,改进工艺流程,提高设备效率,使工厂布局更紧凑,单位能耗更低,三废更少。应该说,过程强化是国内外化工界长期奋斗的目标,也是化学科学和工程研究的主要成果之一,化工过程强化被列为当前化学工程优先发展的领域之一。可以说,当前人们对化工过程强化认识达到了前所未有的高度。从最初对化工过程的认识到现在多种多样的化工过程强化技术的产生,化工过程强化经历了许多转变和发展。 2.1 起源和历史 过程强化的历史最早可追溯到上世纪70年代末。当时,英国化学工业公司首先将此概念用于生产过程,以减少投资。上世纪90年代中期,国际上出现的以节能、降耗、环保、集约化为目标的化工过程强化技术,是当前化学工程优先发展的三大领域之一。2005年7月,在英国召开的第七届世界化学工程学术会议上,过程强化是最热门的研究方向之一。自此,人们对化
化工过程强化技术研究进展
化工过程强化技术研究进展 摘要:化工过程强化技术是节能减排的重要途径,简要介绍了化工过程强化技术及其实现途径,阐述了静态混合反应器、膜催化反应器、反应蒸馏、超临界萃取和超声波反应器等化工过程强化技术。 关键词:化工过程强化化工装置化学反应化学过程 1前言 化工过程的最终目标是将原材料全部转换为符合要求的产品,实现生产过程的零排放。化学工业生产的一个明显趋势是安全、清洁、高效节能的生产[1]。目前我国的能源消耗主要集中在化工生产过程中。“十一五”期间国家制定了节能减排的目标,化工界刮起了一阵低碳经济节能减排的热风。如何在化工生产过程中有效地降低能耗,是科学家、工程师以及化工企业管理者的共同目标。为了实现这一目标,我们既可以从化学反应本身入手,寻找新的催化剂和工艺过程,也可以从反应器和设备入手,采用新的技术和设备,实现化工过程的强化。其中,化工过程强化是实现化工生产过程节能减排降低能耗的有效手段。 2化工过程强化及其实现途径 化工过程强化技术是指能显著减小工厂和设备体积、高效节能、清洁和可持续发展的化工新技术[2]。化工过程强化的实现途径主要包括设备强化和过程集成两个方面。 设备的强化也就是设备的小型化微型化,主要包括反应器和单元操作设备两个方面,如撞击流式反应器、静态混合反应器、超重力吸收反应器、微分反应器、超声波反应器等。随着科技的不断进步,近些年来开发了许多新型的反应器和单元操作设备,其中有不少应经应用于工业生产,并取得了显著的效果。这些新型的反应器被运用于合适的化工过程中,可以显著减小设备的体积,并能够显著增加设备的生产能力,从而强化了生产过程。 过程集成主要是指化工过程集成化,主要包括化学反应与分离、换热、物质相变的集成,组合分离,还有替代能源,超临界流体和离子液体,非定态操作等新技术。过程集成的技术实质是反应-分离多序的综合,质量交换网络、热量交换网络等多种综合优化,不仅要考虑稳态过程的综合,同时又考虑动态过程的特性,是一项系统的生产优化和设计优化技术[3]。 3化工生产中的过程强化技术 3.1静态混合反应器
过程强化的若干新进展_费维扬
过程强化的若干新进展 中国科学院院士 费维扬 (清华大学化学工程系,北京100084) 摘 要:本文从现代过程工业发展的需求出发,介绍了过程强化的历史和现状,分析了近年来过程强化的特点。本文还结合实例对化工过程强化的作用和存在的问题等进行了讨论。 关键词:过程工业 过程强化 化学科学与工程 信息技术 可持续发展 The Progress of Process Intensif ication Member of the CAS FEI Weiyang (Department of Chemical E ngineering,Tsinghu a U niversity,B eijing100084) Abstract:The history and recent advances of process i ntensif ication are i nt roduced.A nd the charac2 teristics of process i ntensif ication are analyzed.In this paper,it is discussed i n detail by i nstance that i nvolves the f unction and some problems of chem ical engi neeri ng process i ntensif ication. K ey w ords:process i ndust ry,process i ntensif ication,chem ical engi neeri ng,i nf orm ation technology, sustai nable development 1 概述 化工、炼油、制药等现代过程工业是大型化、高效率、高利润的产业,是国民经济的支柱。但是,它们在创造大量财富的同时,也往往存在高物耗、高能耗和高污染的问题,成为建设资源节约型和环境友好型经济瓶颈之一。 随着现代过程工业的发展,产品不断更新,环保要求日益提高,建设生态经济和实现可持续发展的要求更为迫切。因此,人们力图灵活应用化学工程的原理和方法,致力于过程强化(Process Intensifica2 tion),即通过技术创新,改进工艺流程,提高设备效率,使工厂布局更紧凑,单位能耗更低,三废更少。应该说,过程强化是国内外化工界长期奋斗的目标,也是化学科学和工程研究的主要成果之一[1,2]。 自1995年举行首次化工过程强化的国际会议以来[3],每三年举办一次化工过程强化的国际会议。在美国工程基金会(U EF)、美国科学基金会NSF)和美国化学工程师学会(AIChE)联合召开的名为化学工程新热点(Refocusing Chemical Engi2 neering)的研讨会上(2001,意大利),化工过程强化被列为当前化学工程优先发展的领域之一。此外,美国工程基金会等还于2002年9月在英国爱丁堡举行了过程发明和过程强化(Process Innovation and Process Intensification,即PI2)的专题研讨会,各国的专家和学者也组织了过程强化网(Process Intensi2 fication Network,即PIN),积极开展学术交流和科技合作。可以说,人们对化工过程强化认识达到了前所未有的高度,也发表了大量化工过程强化的论文[4~9]。
化学强化工艺知识
化学强化玻璃简介 2013.08.29 站别:事业二部化钢组 制作:陈俊飞
化学强化玻璃的基本特性 化学强化玻璃具有较好的热稳定性 热稳定性是玻璃能承受剧烈温度变化而不破坏的性能。 强化玻璃的热稳定性是用其所能承受的温度差来表示,一般玻璃所能承受的温度约70-100℃,而强化玻璃所能承受的温度差约150-200℃,热稳定性比一般玻璃提高了1.5-2倍。 康宁强化玻璃餐具摔不破玻璃奶瓶
化学强化离子交换原理 玻璃化学强化原理是将玻璃置于熔融的熔盐中,使玻璃表层半径较小的离子(Na +)与熔盐中半径较大的离子(K +)交换,最终在玻璃的两表面形成压应力层,在玻璃的內部形成张应力层,达到提高玻璃机械强度和抗温度冲击性能的目的。 K + K +K + K + Na +Na + Na + Na + K + K + 玻璃 钾离子 钾离子置换钠离子
●化学钢化玻璃定义: 利用玻璃表面离子的迁移和扩散特性,使玻璃的表面层区域(一般在数百微米以内的厚度)的成分发生变化。这一变化导致玻璃表面微裂纹消失或者体积变化在玻璃表面形成压应力层,从而使玻璃的强度得到提高。这一技术被称为玻璃的化学钢化。通过化学钢化获得的具有高强度玻璃产品即为化学钢化玻璃(或化学强化玻璃)。 ●化学钢化原理: 随着化学钢化理论研究的深入,化学钢化技术的种类在不断增强。根据玻璃的网络结构学说玻璃态的物质是以硅氧四面体(SiO 2)4-作为基本结构单元存在,构成玻璃的硅氧三维空间骨架。AL 2O 3因AL 3+配位数不固定,或4+或6+,一般以(ALO 4)4-存在,但在碱金属氧化物R 2O 或碱土金属氧化物RO 存在的情况下以(ALO 4)5-存在,并与(ALO 4)4-联成复杂的铝硅氧阴离子团。由于(ALO 4)5-体积约在41cm 3/mol ,而(ALO 4)4-则是27.24cm 3/mol ,从而导致因玻璃成分中AL 2O 3含量的提高(ALO 4)5-在玻璃中的含量相对增加(ALO 4)4-相对减少玻璃体结构网络空隙扩大有利于碱金属离子的扩散。此网络是由含氧的离子多面体构成的,其中心被Si 4+、AL 3+、或P 5+所占据,这些离子同氧离子一起构成网络,网络中填充碱金属离子(如Na +、K +等碱土金属离子)。其中碱金属离子较活跃,很容易从玻璃内部析出,化学钢化法就是基于离子自然扩散和相互扩散,以此改变玻璃表面的成分从而在玻璃表面形成压应力层。就目前发表的文献和实际应用技术进行归类,可分为表面脱碱;高膨胀玻璃表面涂覆低膨胀玻璃;碱金属离子交换三大类。碱金属离子交换类型和离子交换温度可分为低于转变点温度的离子交换法(简称低温法)和高于转变点温度的离子交换法(简称高温法)。