毕业设计 高炉本体设计

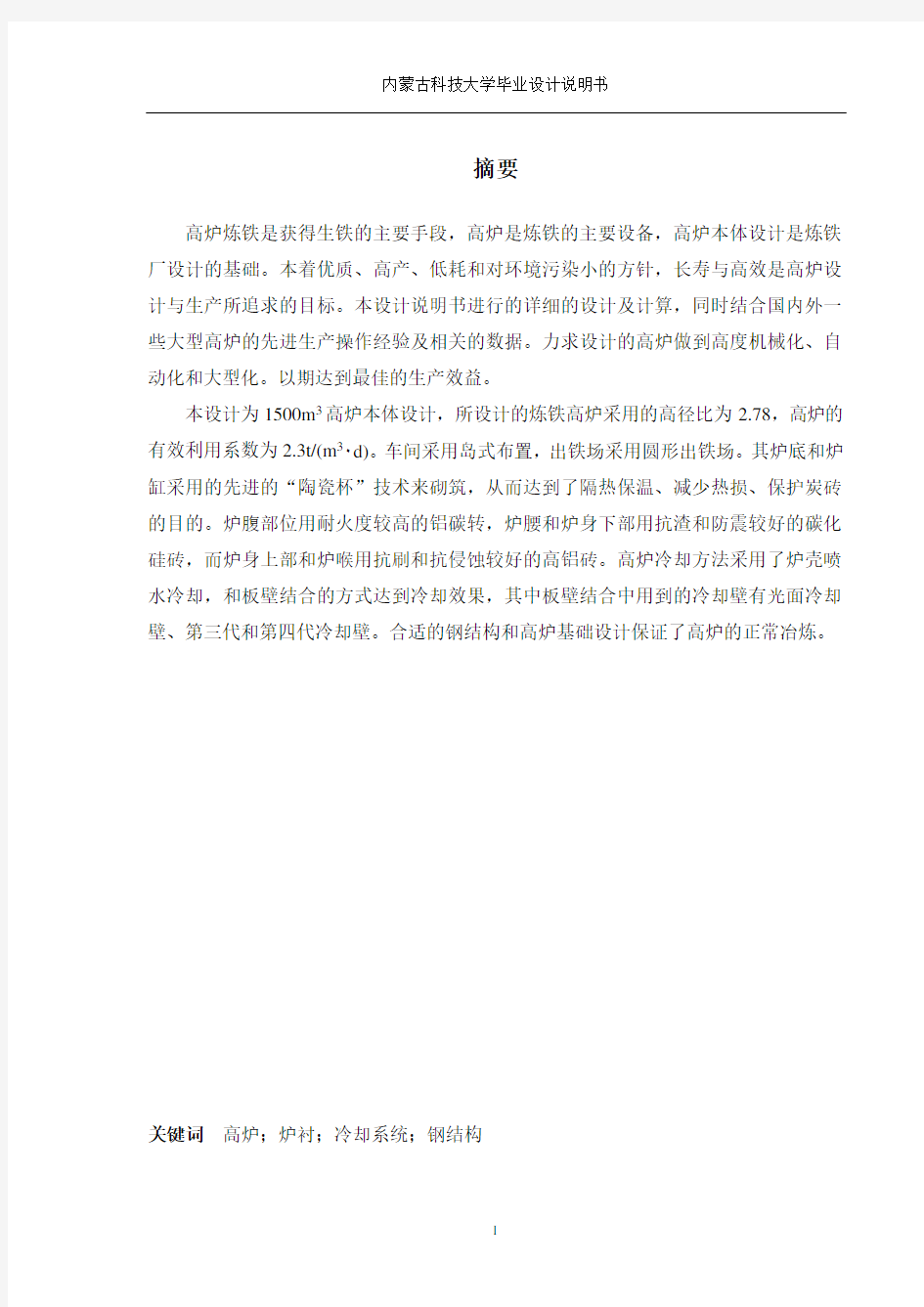
内蒙古科技大学毕业设计说明书
.
内蒙古科技大学
本科生毕业设计说明书
题目:包头地区原料条件下1500m3高炉
本体设计
学生姓名:
学号:
专业:冶金工程
班级:冶金09-1
指导教师:
摘要
高炉炼铁是获得生铁的主要手段,高炉是炼铁的主要设备,高炉本体设计是炼铁厂设计的基础。本着优质、高产、低耗和对环境污染小的方针,长寿与高效是高炉设计与生产所追求的目标。本设计说明书进行的详细的设计及计算,同时结合国内外一些大型高炉的先进生产操作经验及相关的数据。力求设计的高炉做到高度机械化、自动化和大型化。以期达到最佳的生产效益。
本设计为1500m3高炉本体设计,所设计的炼铁高炉采用的高径比为2.78,高炉的有效利用系数为2.3t/(m3?d)。车间采用岛式布置,出铁场采用圆形出铁场。其炉底和炉缸采用的先进的“陶瓷杯”技术来砌筑,从而达到了隔热保温、减少热损、保护炭砖的目的。炉腹部位用耐火度较高的铝碳转,炉腰和炉身下部用抗渣和防震较好的碳化硅砖,而炉身上部和炉喉用抗刷和抗侵蚀较好的高铝砖。高炉冷却方法采用了炉壳喷水冷却,和板壁结合的方式达到冷却效果,其中板壁结合中用到的冷却壁有光面冷却壁、第三代和第四代冷却壁。合适的钢结构和高炉基础设计保证了高炉的正常冶炼。
关键词高炉;炉衬;冷却系统;钢结构
Abstract
Blast furnace iron making is the main means for pig iron, the main equipment of iron making is blast furnace, blast furnace design of ontology is the foundation of the iron mill design. In line with high quality, high yield, low consumption and pollution to the environment policy of small, long life and high efficiency is the goal of the design and production of the blast furnace. This design manual for detailed design and calculation, at the same time, combined with some large blast furnace at home and abroad advanced production operation experience and related data. Strive to design blast furnace of high mechanization, automation and large. In order to achieve the best production efficiency.
This design for 1500 m3 blast furnace body design, The design of the blast furnace high aspect ratio of 2.78,the effective utilization of blast furnace coefficient of 2.3t/(m3?d).Workshop uses the island type layout cast house using circular cast house Blast furnace bottom and hearth uses advanced technology to building "ceramic cup", so as to achieve the heat insulation heat preservation, reduce heat loss and protect the carbon brick. Furnace belly with high refractoriness of aluminum carbon, bosh and furnace body with good slag resistance and shock-proof carborundum brick, The furnace body and brush with resistance and erosion resistance furnace throat good high alumina brick.Blast furnace cooling method USES a furnace shell water spray cooling, cooling effect and partition way, combined with the wooden partition used in cooling stave cooling wall has smooth surface, the third and fourth generation of cooling stave.Appropriate steel structure and foundation design guarantees the normal of the blast furnace smelting blast furnace.
Key word: blast furnace body;the lining;of blast furnace cooling system;steel structure
目录
摘要............................................................................................................................................ I Abstract .................................................................................................................................... II 目录....................................................................................................................................... III 第一章文献综述 (1)
1.1高炉炉型概述 (1)
1.1.1高炉炉型的发展 (1)
1.1.2高炉炉龄及其影响因素 (2)
1.2高炉炉衬的发展 (2)
1.2.1高炉各部分耐火材料的选择 (2)
1.2.2我国最新对耐火材料的选择 (4)
1.3高炉的冷却设备 (4)
1.3.1高炉冷却的必要性 (4)
1.3.2高炉冷却的目的 (5)
1.3.3高炉冷却的方式 (5)
1.3.4高炉各个冷却方式的发展以及优缺点 (6)
1.4高炉钢结构以及高炉基础的概述 (10)
1.4.1高炉的钢结构以及影响因素 (10)
1.4.2我国高炉钢结构设计的基本现状 (11)
1.4.3我国在高炉钢结构设计上的差距 (12)
1.4.4高炉基础的概述 (13)
1.5高炉设计方案 (15)
第二章炼铁工艺计算 (17)
2.1原料成分及参数选择 (17)
2.1.1原料成分 (17)
2.1.2参数选择 (18)
2.2原料成分的整理计算 (19)
2.2.1矿石成分补齐计算 (19)
2.2.2矿石成分的平衡计算 (20)
2.2.3燃料成分的整理计算 (22)
2.3配料计算 (23)
2.3.1吨铁矿石用量 (23)
2.3.2生铁成分计算 (23)
2.3.3熔剂用量计算 (24)
2.3.4炉料及炉渣成分计算 (24)
2.4物料平衡计算 (25)
2.5热平衡计算 (29)
2.5.1热收入 (29)
2.5.2热支出 (30)
2.6高温区热平衡计算 (34)
2.6.1高温区热收入 (34)
2.6.2高温区热支出 (34)
2.7炼铁焦比的计算 (36)
第三章高炉炉型设计 (38)
3.1炉型的计算 (38)
3.1.1铁口 (38)
3.1.2渣口 (39)
3.1.3风口 (39)
3.1.4日产铁量的计算 (40)
3.1.5炉缸尺寸计算 (40)
3.1.6死铁层厚度 (41)
3.1.7炉腰直径、炉腹角、炉腹高度的计算 (41)
3.1.8炉喉直径、炉喉高度、炉身高度、炉腰高度 (41)
3.2炉容的校核 (42)
3.3出铁场布置 (42)
第四章高炉炉衬设计 (44)
4.1各部位砖衬的选择 (44)
4.1.1炉底、炉缸部位的选择 (44)
4.1.2炉腹部位的选择 (44)
4.1.3炉身中下部及炉腰部位的选择 (44)
4.1.4炉身上部及炉喉部位的选择 (45)
4.2各部位砖量计算 (45)
4.2.1炉底、炉缸的砌筑 (46)
4.2.2炉腹的砌筑 (46)
4.2.3炉腰的砌筑 (47)
4.2.4炉身部位的砌筑 (48)
第五章高炉冷却系统设计 (52)
5.1高炉冷却设备 (52)
5.1.1高炉冷却目的及方法 (52)
5.1.2冷却设备 (52)
5.2冷却器的工作机制 (53)
5.3合理的冷却结构 (54)
5.4高炉冷却系统的维护 (57)
第六章高炉钢结构及基础 (60)
6.1高炉钢结构 (60)
6.1.1高炉本体钢结构 (60)
6.1.2炉壳 (61)
6.1.3炉体平台 (61)
6.1.4炉体框架 (61)
6.1.5热风围管 (62)
6.2高炉基础 (62)
参考文献 (63)
致谢 (65)
第一章文献综述
1.1高炉炉型概述
1.1.1高炉炉型的发展
高炉是一种竖炉型的冶炼炉,它由炉体内耐火材料砌成的工作空间、炉体设备、炉体冷却设备、炉体钢结构等组成。
高炉生产实践表明:合理的炉体结构,对高炉一代炉龄的高产、优质、低耗和长寿起到保证作用[1],由此可以看出高炉的炉型应该有炉型和炉龄两个方面阐述。
近代高炉,由于鼓风机能力进一步提高,原料燃料处理更加精细,高炉炉型向着“大型横向”发展[2]。对于炉型而言,从20世纪60年代开始,高炉逐步大型化,大型高炉的容积由当时的1000~1500m3逐步发展到现在的4000~5500m3。随着炉容的扩大,炉型的变化出现以下特征:高炉的H U/D即高径比缩小,大型高炉的比值已降到2.0,1000m3级高炉降到2.5,300m3级高炉也降到3.0左右。和大小同步的还有高炉矮胖炉型发展,矮胖高炉的特征是炉子下部容积扩大,在适当的配合条件下利于增加产量,提高利用系数.但如矮胖得过分,易导致上部煤气利用差,使燃料比升高.此外,从全国节能要求出发,在高炉建设和炼铁生产经营管理中,应既抓产量,又抓消耗、质量和寿命的优秀实例进行总结推广,提倡全面贯彻“高产、优质、低耗、长寿,”八字方针[3]。与盛高炉型相比,矮胖炉型的主要优点是:与炉料性能相适应,料柱阻力减小;风口增多,利于接受风量;高护更易顺行稳定。这些优点,给高炉带来了多产生铁,改进生铁质量,降低燃料消耗和延长寿命的综合效果。通过研究发现,当今用于炼铁的高炉炉喉直径均偏小,其炉喉直径与炉缸直径的比值均小于0.785。通过研究发现,炉喉直径偏小影响炉身的间接还原效率,致使高炉能耗较高,影响高炉经济效益,因此,为了提高高炉炉身的间接还原效率,改善高炉产生技术指标和进行节能减排,特别推出一种扩大炉喉直径的新炉型高炉。采用的技术方案是:它包含炉缸、炉腹、炉腰、炉身、炉喉五部分,其中炉缸在炉腹的下面,炉缸上面连接炉腹,炉腹上面连接炉腰,炉腰上面连接炉身,炉身上面连接炉喉;由上述5部分组成的高炉内型,5个部分的横截面均呈圆形,其中炉缸直径用d表示,炉腰直径用D表示,炉喉直径用d表示,炉喉直径d1与炉缸直径d之比在0.785~1.0之间。从而炉型能够充分发挥炉身的间接还
原作用,使高炉节约焦炭,降低消耗,减少二氧化碳排放,能够使钢铁企业降低生产成本[4]。
1.1.2高炉炉龄及其影响因素
实现高炉长寿是高炉生产的主要目标之一。高炉炉龄主要取决于炉缸、炉腹、炉腰、炉身各层冷却系统以及高炉本体结构的实际使用情况。较长的高炉炉龄,无疑在经济上是合理的。高炉长寿是从设计、施工、操作状况等诸多环节统一管理的一项系统工程。一代高炉寿命的长短,直接反映高炉技术装备、操作管理水平和经济效益。若将一代高炉寿命延长几年,其经济效益是显而易见的。在目前高产、低耗的生产条件下,实现长寿具有十分重要的意义。高炉操作炉型是否合理,炉衬的完好率及其及时维护,冷却设备及冷却制度的选择,炉壳结构的稳定性的监护等都是直接影响高炉一代寿命的因素。特别是整个高炉生产期的稳定顺行,积极维护和管理是实现高炉长寿的重要环节,必须给予高度重视。国内高炉炉缸、炉底自采用高导热率的碳质耐火材料和加强冷却以后,寿命显著延长,影响高炉一代寿命的薄弱环节现已转到炉身下部。因此,提高炉身下部的寿命,使之与炉缸、炉底寿命相适应,已成为当前迫切需要解决的课题.影响高炉炉体寿命的因素很多,而且互相制约,问题比较复杂,但在其他诸因素相同,尤其是在稳定操作的情况下,对于由耐火砖衬、冷却器、炉壳组成的现代高炉炉体来说,高炉冷却确实是决定炉体能否长寿的重要原因。
1.2高炉炉衬的发展
1.2.1高炉各部分耐火材料的选择
对于炉衬而言,现代技术的发展,大大地促进了我国高炉技术的进步,高炉炉衬的侵蚀是影响高炉长寿的关键因素之一,随着计算机硬件技术的进步和计算流体动力学的发展,利用数值模拟技术开展有关高炉炉衬侵蚀的研究已成为主要的研究方法,高炉一代寿命大大提高。这除了应归于高炉炉体结构参数趋于合理、操作参数的进一步优化外,还应归功于高炉炉衬耐火材料与施工技术的进步[5]。而高炉各个部分的耐火材料的选择是不同的,粗略的有以下的几个方面分布:
⑴炉身上部和中部
炉身的上部主要受固体炉料的机械磨顺和高速煤气流的冲刷作用、碳素沉淀、碱
金属和锌的腐蚀,同时受到温度变化的影响。一般选用机械强度好的、气孔率低和热稳定性能好的粘土砖或高铝砖。
⑵炉身下部、炉腰和炉腹
从炉身下部到炉腹的砖衬,既受到下降炉料和上升高温高压煤气的磨损,又受到高FeO和高碱度初渣的化学侵蚀,此外,还有碱金属和锌与CO的化学作用,造成砖衬疏松剥落;特别是因高温波动而引起的热冲击破损危害更大,例如在炉况失常、或开炉、或休风期时,由于煤气流分布失常,砖衬内温度场发生剧烈波动,导致砖衬内部产生裂纹。同时,裂纹内伴随有化学产物的膨胀,其结果必然导致内衬很快破损。这些部位应选用机械强度高、热稳定性好、导热性良好和抗化学侵蚀性能的耐火材料。
⑶炉缸部和炉底部
炉缸部主要受高温液态渣铁的冲刷、渗透和碱金属熔蚀,故要求选用气孔率低、孔径小、导热性高、抗渣性和抗碱性好的耐火材料。目前,国内外高炉炉底炉缸采用的内衬结构型式大致分为两大类,一是全炭质材料炉底炉缸结构,二是炭质材料—陶瓷材料复合炉底炉缸结构。这两种结构的炉衬都能实现长寿目标,不同之处主要是砖的导热系数相差很大,碳砖在200℃时的导热系数为8~21W/(m K),陶瓷砖的导热系数≤0.2W/(m K),是碳砖导热系数的1/40~1/105,因而陶瓷杯复合炉衬具有良好的保温性能[6]。炉缸外环一般采用微孔炭砖、超微孔炭砖、自焙碳砖;炉缸内环采用高铝砖、刚玉转。
⑷风口
风口是炉内最高温度区域炉衬经常承受1800~2000℃的高温作用,同时也受到渣铁的冲刷和碱金属的侵蚀。由于高温高压气体从此送入炉内,对炉衬的振动也很严重,因此要求此处砌体具有良好的稳定性。风口带一般采用大块的组合砖砌体,材质为高铝砖、硅线石砖、刚玉砖、碳化硅砖等。
⑸铁口
铁口附近的砖衬经常受到渣铁的冲刷和侵蚀,在开铁口和堵铁口时,承受开铁口机的冲击力和泥炮的巨大作用力,而使耐火砖松动造成煤气泄漏;当炉缸冻结或铁口打不开时,有使用氧气烧铁口。因此,在设计铁口砌体时,必须考虑耐渣铁侵蚀和砌体的稳定性和密封性、耐火材料的抗剥落性和抗氧化性能。一般采用大块的组合砖砌体。材质为高铝砖、刚玉砖、碳化硅砖和铝—碳—碳化硅砖等。
1.2.2我国最新对耐火材料的选择
我国大中型高炉的炉缸炉底自50年代末采用碳砖综合炉底以来,在相当一段时期内,其寿命都在10年以上。但随着高炉冶炼强度的不断提高,炉缸寿命依然存在这问题。炉缸炉底上传而导致高炉停炉的现象在国内屡见不鲜。如邯钢1260m,高炉,1992年7月投产,1995年4月炉缸烧穿[7]。
我们就国内目前高炉炉衬耐火材料的应用情况,优选了三套比较有代表性的方案。其中,方案一选择了高导热石墨炭和半石墨化烧成炭砖砌筑炉底:炉缸采用高导热的微孔炭砖;并采用陶瓷杯技术;炉腹、炉腰、炉身下部选用Si3N4结合SiC砖。这种结构选择的材料等级较高,造价较贵。方案二以国产烧炭块代替方案一中的烧成炭砖,并以国内自行研制的与Si3N4结合SiC砖性能接近,而价格便宜得多的铝碳砖部分代替Si3N4结合SiC砖,以达到降低造价的目的。方案三采用了与方案二相同的炉底结构,但在炉腹、炉腰、炉身下部直至中部大量采用烧成铝碳砖代替Si3N4结合SiC砖,进一步降低高炉造价。综合的说其发展途径为:高炉碳砖应开发超微孔碳砖,主要是提高热导率达到20W/m·K以上。降低平均孔径达到<0.05um、<1um孔容积达到>85%,透气度达到0m。还要提高抗氧化性和抗铁水溶蚀性。这样的碳砖将可以完全防止铁水和有害气体的渗透侵蚀。高炉用的半石墨碳砖主要是提高热导率达到20w/m·K以上,还要提高抗氧化性和抗铁水溶蚀性[8]。
1.3高炉的冷却设备
1.3.1高炉冷却的必要性
在高炉炼铁界,为了提高炼铁综合经济效益,国内外炼铁工作者都把延长高炉寿命作为一个非常重要的课题进行研究,高炉寿命与炉体冷却结构,生产操作有着非常密切的关系,高炉后期的修补等技术也起到了重要的作用。高炉炉体冷却结构是高炉长寿的最重要的基础条件,各国对高炉炉体冷却结构作了很多调查及研究工作,以尽量提高高炉一代炉役寿命[9]。
所以继炉衬以后另一个高炉的重要体系不得不被提起那就是高炉的冷却系统。进入21世纪以来,随着国民经济的迅速增长,基础建设的步伐也在不断加快,同时带动了钢铁产业的飞速发展。全国各地的炼铁高炉如雨后春笋蓬勃发展,增长势头十分强劲。
说到炼铁高炉众所周知,对于一座高炉来说成熟高效的冶炼技术固然重要,但是如果没有理想的炉体冷却系统与之配套,炉体将会在很短的时间内受到损坏,从而导致高炉一代炉龄时间缩短,使高炉的大修时间提前,加大基建投资成本,直接影响钢铁企业的经济效益。很显然这样的后果大家都不愿看到,所以对一座高炉来说选择一种行之有效的高炉冷却方式就显得非常必要。
1.3.2高炉冷却的目的
高炉冷却的目的在于增大炉衬内的温度梯度,致使1150℃等温面远离高炉炉壳,从而保护某些金属结构和混凝土构件,使之不失去强度。使炉衬凝成渣皮,保护甚至代替炉衬工作,从而获得合理炉型,延长炉衬工作能力和高炉使用寿命。高炉冷却是形成保护性渣皮、铁壳、石墨层的重要条件。高炉常用的冷却介质有:水、风、汽水混合物。
根据高炉各部位工作条件,炉缸、炉底的冷却目的主要是使铁水凝固的1150℃等温面远离高炉壳,防止炉底、炉缸被渣铁水烧漏。而炉身冷却的目的是为了保持合理的操作炉型和保护炉壳。
1.3.3高炉冷却的方式
冷却系统包括:⑴对质量要求低水;⑵设备简单;⑶较低的资本成本;⑷低流量和直接用于冷却水压力[10]。
冷却的方式就目前而言国内高炉采用的冷却方式有三种:工业水开路循环冷却系统;汽化冷却系统;软水密闭循环冷却系统
冷却原理如下:冷却水通过被冷却的部件空腔,并从其表面将热量带走,从而使冷却水的自身温度提高。
①工业水开路循环冷却工作原理:由动力泵站将凉水池中的水输送到冷却设备后,自然流回凉水池或冷却塔,把从冷却设备中带出的热量散发于大气。系统压力由水泵供水能力大小控制。
②自然循环汽化冷却工作原理:利用下降管中的水和上升管中的汽水混合物的比重不同所形成的压头,克服整个循环过程中的阻力,从而产生连续循环,汽化吸热而达到冷却目的。
③软水密闭循环冷却工作原理:它是一个完全封闭的系统,用软水(采用低压锅
炉软水即可)作为冷却介质,其工作温度50~60℃(实践经验40~45℃)由循环泵带动循环,以冷却设备中带出来的热量经过热交换器散发于大气。系统中设有膨胀罐,目的在于吸收水在密闭系统中由于温度升高而引起的膨胀。系统工作压力由膨胀罐内的N2压力控制,使得冷却介质具有较大的热度而控制水在冷却设备中的汽化。
1.3.4高炉各个冷却方式的发展以及优缺点
⑴工业水冷却是使用最广泛的,因为它一次投资低,运行稳定。该系统由泵站、管道、冷却器、喷水池等组成。首先当采用工业净水开式循环方法冷却时,由于工业净水对水质要求较低,可直接在循环泵房的吸水池中加入药剂经沉淀及
过滤处理后去掉水中的悬浮杂质,便可投入运行。由于高炉采用普通工业净化水作为冷却介质时,溶解于水中的可溶性杂质并未得到处理,所以在使用一段时间后,输送介质的管道及炉内冷却设备的通道上容易产生沉积物及水垢,从而导致传热效率降低,使得炉体内的冷却设备因过热而烧损。当冷却设备烧损后需及时更换否则会烧穿炉壁,所以要更换冷却设备,高炉就需要休风,影响生产秩序。另外采用开式循环方式时集水槽内的回水容易受到外界因素干扰,导致水质变差,且回水回流到热水井后需用扬水泵将其输送至晾水塔进行降温冷却后回流至冷水吸水井。由于开式循环过程中要蒸发掉一定量的水,需要定期定量补水。采用开式循环冷却方式的主要优点是:在风口平台上及高炉各层平台的集水槽前可以直观地看到每一块水冷壁和每一个风渣口冷却水运行情况,同时也便于炉前工测量水温,从而直观地观察每一个冷却设备的运行工况。在检修时能及时找出被烧损或堵塞的设备,以利更换。采用开式循环系统时需要引起注意的是当供水流速及流量太大时,由于回水系统靠重力回水流速较低,风口平台上的集水槽容易发生回水溢流(俗称吐水)事故。故为防止此事故发生,建议尽量降低循环水泵房及吸水池的标高,使其与风口平台的集水槽保证一定高差,充分利用回水系统的静压头保持系统平稳运行;另外一条是回水管径宜大不宜小。另外由于密闭循环可以充分利用系统管路的静压头,减少管路系统的水头损失,便于调节控制系统的工作压力,使系统运行可靠,降低动力消耗,据测算可节电耗30%左右。冷却水循环使用,靠喷水池蒸发冷却回水。总之,高炉采用工业水作冷却介质时,无论是直流式还是敞环式,都存在冷却水质差、水质不易稳定、水的循环损失大、允许水温升小、循环水量大等缺点。而最致命的弱点则是容易在冷却器通道壁上结垢。水垢积物通常是指水中成垢盐类结晶或沉淀所产生的沉淀物,对于水质而言(南方是悬浮物,
北方是水硬度),会在冷却器内结垢而影响冷却(5mm的水垢在200000kJ/(m2?h)的热流下能使冷却器表面温度比无垢时提高500),这是造成冷却器烧坏的重要原因。为改善水质一般都用加药处理和定期清洗冷却器来降低水垢的危害;同时还要控制进出水的温度,特别是出水温度不宜高于45°C[11]。
⑵汽化冷却。在20世纪50年代,前苏联的冶金热工专家将加热炉上成功的汽化冷却移到高炉冷却系统,高炉汽化冷却技术在苏联试验和应用之后,西欧、日本、北美等国也相继引进在一些高炉上采用,我国在60~70年代也曾有10余座大中小型高炉使用过。现在世界上缺水地区还有些高炉使用汽化冷却,气冷的极限值是多少,日本曾在福山5号高炉冷却系统确定之前,对水冷和气冷作了模拟实验比较,结果发现气冷所能承担的最大烧毁热流强度为841千瓦/m2,而在水冷条件下能抵抗的最大烧毁热流强度为1163千瓦/m2(如图1.1)[12]。大部分高炉(包括前苏联的高炉和我国的高炉)的汽化冷却方式已被软水闭路循环冷却或工业水冷却所替代。汽化冷却是将接近沸点(称做欠热度低)的软水作为冷却介质通入冷却器,在冷却器内受热而部分水达到沸点而汽化蒸发,冷却介质变成汽-水混合物,水在汽化时吸收汽化潜热,从而冷却了冷却器,而且节约了大量的冷却水。汽-水混合物的密度比软化水的小,因此在密度差的驱动下,汽-水混合物上升进入汽包。在汽包内汽-水混合物分离为蒸汽和水,蒸汽或回收利用或放散;分离出的水作为冷却介质继续循环使用。完全靠水与汽-水混合物密度差运行的系统叫自然循环汽化冷却;在循环系统中加有热水泵以帮助冷却介质克服运行阻力的叫强迫循环汽化冷却。
图1.1 水冷和汽冷的热承载能力比较
1-热水冷却区;2-过渡区;3-稳定泡核过渡区;4-烧毁区;Q C-烧毁热流
采用汽化冷却作为高炉的冷却方式时具有以下优点:
⑴由于汽化冷却介质为软化水或纯水,水质指标较高,可有效防止系统内的水垢形成,延长了冷却设备的使用寿命。
⑵可以节约大量的工业用水,据测算可节水60%~90%。如采用自然循环方式时因用水量少,可将大水泵改为小水泵,大管道改为小管道,节省基建投资。
⑶运行安全可靠、流量小,换热能力大,不必设立事故水塔。当发生停电事故时,在汽包中还贮备有约1h的循环水量可以维持正常的系统自然循环,故仍可安全运行。
⑷汽化冷却产生的大量低压蒸汽可作为厂区的二次能源加以利用,从经济角度考虑也是非常可观的。它是将欠热度大的软水(水温在45~55°C)利用循环泵在高炉冷却系统内运行,软水在冷却器内吸收冷却器传过来的热达到冷却的目的。一般在冷却器内软水的温升为8~10°C,循环水离开高炉后,用专门的冷却设施将循环软水降温10℃左右,北方地区一般采用大风扇吹(只在夏天高温季节使用,其他各季靠自然通风冷却),南方地区则用工业水热交换器。系统内设有脱气罐。此种冷却方式的优点是采用软水或纯水解决水质对冷却的影响;由于水的欠热度大而且闭路不产生蒸汽,所以运行耗水量少,仅在热水泵轴承密封处有少量渗漏;闭路循环可充分利用静压头,而且可用膨胀罐充来调节、控制系统的压力,系统运行可靠[13]。
汽化的缺点是对高炉热流大波动的适应性差,在突发性尖峰热流时,容易在冷却器水管中形成汽塞,阻碍循环,甚至造成停止循环而将冷却器烧坏。这是汽化冷却没能得到推广和已用过的高炉退回到工业水冷却或改用更稳妥可靠的软水闭路循环冷却的主要原因。
软水闭路循环冷却。软水密闭循环冷却系统的热量是通过热交换器蒸发到大气中的,开式循环系统回水至吸水井再加压上冷却塔时水在冷却塔中蒸发将热量散失出去,在冷却塔周围形成水雾,容易污染环境,而采用软水密闭循环冷却可以节约占地面积50%左右。软水密闭强制循环冷却方式的缺点是:对每一个冷却设备的运行工况不能通过直观的观察来判断是否运行正常,检修时比较困难,需逐一排查。当系统内水流速度加快时,系统阻力也随之加大,所以必须选择一个合适的水流速度才能达到节约能耗的目的。另外它的工程造价相对于开式循环系统来说要大许多,所以选择时要全面地权衡利弊得失,谨慎选用。
综合的说软水闭路循环冷却系统的优点可以简要的做以下的分析说明:
⑴消除管壁结垢,延长冷却器寿命[14]
该系统使用经过化学处理即除去水中硬度和部分盐类的软水,这就从根本上解决了冷却水管内壁结垢的问题,克服了工业水冷却的致命弱点。尽管热的软环系统介质温度比工业水冷却时高30~40℃,但由于后者冷却管内不可避免地要结垢,使冷却壁体的工作温度可能比汽冷条件下还高。因此,无论是与工业水系统还是汽冷系统相比,软环系统内的冷却器壁体工作温度是最低的.这无疑有利于延长冷却器寿命。
⑵运行稳定,灵活可靠
首先在本系统中设置了氮气充压容器,可以控制冷却部件内的水温远低于相应压力下水的沸腾温度,即具有较高的欠热度,使系统中的水不汽化,不存在两相流。即使在高热负荷区,汽泡的生成频率也极低,能很快地消失在过冷液中,从而避免了液态沸腾的产生。这就从根本上消除了系统不稳定运行的潜在因素,并具有足够的冷却后备能力,保证冷却部件不致因局部过热而烧毁。其次在全部采用冷却壁冷却的高炉上。一旦事故停电,本系统可以在短期内转为无压汽化冷却,为高炉冷却系统的安全运行创造了条件。系统压力由膨胀罐内充入的氮气压力来控制,不仅提高了系统的密封性,而且亦提高了水的汽化温度,使水具有一定的欠热度,减少了水的汽化量。特别是各循环系统回水进入膨胀罐之前通过了脱气罐,及时脱去了水中气泡,避免产生两相流和膜态沸腾、消除汽塞,使循环水流稳定运行。这里需要指出,脱气罐在整个冷却系统中起着重要作用。因为高炉各部位特别是中部热流强度极不稳定,一旦某处热流强度超过允许值,水温骤然升高,产汽量增多,极易造成局部汽塞,即使时间不长,亦会造成冷却件局部过热而烧损。系统中设置了脱气罐,可以及时排去冷却水中气体,避免水中气体过多造成汽塞[15]。
⑶补充水量低
工业水敞环系统的补水量包括:蒸发损失、排污损失和水泵密封处的泄漏量,大约占循环水量的4~5%。汽冷补水量大约为产汽量的1.2倍左右。软环系统由于完全密闭,没有蒸发损失,补充水量仅用以补偿水泵密封处的泄漏量或因检修而排放的水量,故其补充水量极小。例如西德狄林根4号高炉(内容积2065m3)软环系统的实际补水量每周仅1.5m3[16],相当于循环水量的百分之四。现在这种冷却方式已广泛应用于大中型高炉。
1.4高炉钢结构以及高炉基础的概述
1.4.1高炉的钢结构以及影响因素
设计高炉本体钢结构,主要是解决炉顶载荷、炉身载荷传递到炉基的方式方法,并且要解决炉壳密封等。多年实践的结果,目前高炉本体钢结构主要有以下几种形式。
⑴大框架和炉缸支柱式:炉顶载荷由四根支柱组成的炉体框架传至基础;炉身载荷由炉腰托圈、炉缸支柱传至基础。炉顶法兰与炉顶平台刚性连接,载荷由炉体框架传递,炉喉处设膨胀缝缓冲炉顶和炉身之间热的和机械的变形量。这种结构的特点是炉壳不承受载荷,工作可靠,但高炉风口平台拥剂,操作不方便。这种结构适用于小型高炉。
⑵炉缸支柱式:炉顶载荷由炉身炉壳传至炉腰托圈和炉缸支柱再传至基础。其特点是节省钢材,但大修时更换炉壳不方便,冶炼中应注意炉身部分冷却,特别是炉龄后期,短时间停水也会造成重大事故;风口平台拥挤,炉前操作不方便。我国中小型高炉曾采用这种结构。
⑶炉缸、炉身支柱式:炉顶装料设备和煤气导出管、上升管载荷由炉身炉壳传递至炉腰托圈;炉顶框架,大小钟载荷由炉身支柱传递至炉腰托圈;所有载荷通过炉腰托圈传递至炉缸支柱再至基础。煤气上升管和炉顶平台分别装设有座圈和托座,大修更换炉壳时炉顶煤气导出管和装料设备等载荷可作用在平台上。我国50年代大型高炉(V1053m2、V u l513m3)多采用这种结构。
⑷炉体框架式:炉顶框架、大小钟载荷、作用在炉体框架上,传递至基础;装料设备和煤气上升管等载荷,由炉壳传递至基础。煤气上升管和炉顶平台亦装有座圈和托座。由于取消了炉缸支柱,风口平台宽敞,炉前操作方便。目前大型高炉多采用这种结构。
⑸自主式:全部载荷由炉壳承受并传递至基础。结构简单,操作方便,耗钢材少。设计时应尽量减少炉壳折点,制造时折点要平缓过渡,其他结构应不约束炉壳受热膨胀,减少热应力;冶炼时加强炉壳冷却。我国中小型高炉曾采用这种结构[17]。
高炉设备大多数处于腐蚀介质环境中,一些设备和钢结构处于80~200℃高温环境,有较强的腐蚀作用,是钢铁厂腐蚀严重的区域。因此,加强高炉设备及钢结构的防腐蚀措施,是相当重要的。
高炉:炼铁一般是在高炉里连续进行的。高炉又叫鼓风炉,这是因为要把热空气吹入炉中使原料不断加热而得名的。这些原料是铁矿石、石灰石及焦炭。因为碳比铁的性质活泼,所以它能从铁矿石中把氧夺走,而把金属铁留下。
高炉结构荷载认识的深入高炉综合体结构承受多种作用,荷载相当复杂,但不外乎两类:一类决定结构强度,另一类与结构耐久性相关。正是结构强度和耐久性综合决定了高炉结构的寿命。
⑴煤气压力、炉衬和冷却系统的热膨胀(力)、炉料和铁水压力,决定了正常操作条件下炉壳的结构强度。
⑵炉内高温的周期作用或突然作用,能使结构产生热疲劳或冲击应力,降低钢材塑性并导致脆性破坏。服役后期,内衬及冷却器的损伤,可导致局部过热或大面积烧红,将产生很大热应力,加速炉壳开裂、美国内陆公司证明,沿炉壳厚度的温度梯度是大应力的主要原因,当最大热应力超过屈服应力,炉壳就会开裂。
⑶低周疲劳是影响高炉寿命的主要因素。据前苏联对高炉实际工作状态的研究,炉壳是在不同循环特征和不同变化幅度的周期荷载作用下工作的,炉壳10年中荷载变化的循环次数为2×104,荷载不对称系数0.6~0.9。在这种周期荷载作用下,炉壳的应力集中区和焊缝缺陷处出现局部塑性变形,从而产生低周疲劳破坏。
所以,高炉结构的最终寿命,就是正常条件下的结构强度,抵御低周疲劳脆断的时限。大量的实验、分析、实践证实炉壳损坏有两种原因:一是由于疲劳,特别是局部过热引起的疲劳损伤;另一种是突然的脆性断裂。因此,炉壳设计的应力控制标准应以断裂韧性和疲劳强度为据。以断裂韧性为结构抗裂性指标,K=K lC作为防止脆断的依据,K≦K1C时结构安全;反之亦然[18]。
1.4.2我国高炉钢结构设计的基本现状
高炉就目前已投产的,划分为五种类型⑴带炉身支柱、托圈和炉缸支柱的⑵设在塔式大框架内的自立式高炉⑶全自立式高炉⑷带托圈和炉缸支柱的⑸其它类型高炉[19]我国高炉钢结构设计技术的水平很不平衡,大致分为3个层次:
⑴北京钢铁设计研究总院、重庆钢铁设计研究院是我国高炉结构设计进入电算阶段的代表,示我国相关技术的先进水准。他们凭借大量的工程实践,先进的计算设备和手段,对高炉钢结构系统包括上料、除尘、炉体框架、上开管、下降管和炉体的综合系统或各部分进行静力或动力分析,炉壳整体或局部进行弹塑性分析。在计算中,将综
合系统用空间杆系模型代替,高炉本体简化为空间多质点悬壁杆,整体分析后,再将悬壁杆还原为壳体,用有限元分析。
⑵一些专业大院,虽然其中也有少数做过大型高炉设计,但基本停留在:a=K D,验算边缘效应及手工计算的水准。按60年代《高炉结构设计技术规定》指导设计,并参考已有经验。一些较新的理论和成果,未被采用。
⑶中小冶金设计单位基本属于第三层次,主要停留在小型高炉设计上,在未搞清结构受力特点和传力顺序的条件下,沿用已有的经验或图纸,较少考虑设计的技术性和经济性。
1.4.3我国在高炉钢结构设计上的差距
⑴我国高炉结构设计,还处在以经验为主、计算分析为辅的阶段。设计新建高炉时,技术人员往往参照已建的高炉或已往的经验,确定炉壳厚度和用钢量,决定炉壳的主体结构,计算分析只是参考。其根本原因,就在于没有明确掌握高炉内三项材料的运动规律、炉内化学变化对炉皮的真实压力,以及高温作用、低周荷载对炉壳疲劳与脆断的影响,不得不把经验作为主要依据。
⑵我国高炉结构设计,已经进入电算时代,已有较为完备、符合高炉工况的计算软件和细部分析能力,能够在弹性薄膜理论和板壳有矩理论指导下,对整体进行分析,也可对局部进行弹塑性分析。但我国高炉结构的设计精度还不高,落后于日本、前苏联等国家。由于我们缺乏对高炉,特别是炉体内部的实验和研究,很难对荷载做进一步的准确统计。因此,不管拥有多么先进的计算设备和手段,校核的数据与使用总有一定距离。而且,在实际设计中,我们只考虑了炉役前期,统计正常操作下的荷载,尽管我们已经考虑内衬膨胀对炉壳的压力,但对热疲劳,低周荷载在炉役后期,对高炉寿命减少的影响没有考虑。断裂力学对结构寿命的估计,还未应用于设计。
⑶我国还没有统一的高炉设计概念,没有编制自己的设计规范和计算程序,缺乏明确的炉壳设计控制标准。目前国内没有一本有关的专著,基本沿用苏联理论和规范,以及日本的一些做法,加上各设计单位缺乏相互交流,在市场利益机制的驱使下,必然大部分沿袭旧有设计经验。所以,结构设计进步迟缓。此外,高炉结构设计在技术人员队伍上的断档,也应重视[20]。
1.4.4高炉基础的概述
高炉炉壳:现代化高炉广泛使用焊接的钢板炉壳,只有极少数最小的土高炉才用钢箍加固的砖壳。炉壳的作用是固定冷却设备,保证高炉砌体牢固,密封炉体,有的还承受炉顶载荷。炉壳除承受巨大的重力外,还要承受热应力和内部的煤气压力,有时要抵抗崩料、坐料甚至可能发生的煤气爆炸的突然冲击,因此要有足够的强度。炉壳外形尺寸应与高炉内型、炉体各部厚度、冷却设备结构形式相应。
高炉炉型,高炉炉型指的是高炉工作空间的形状。现代高炉的炉型为五段式炉型,自上而下由以下五部分组成:炉喉、炉身、炉腰、炉腹和炉缸。在炉喉上部还有炉顶平台和炉顶钢圈[21]。
炉喉:高炉本体的最上部分,呈圆筒形。炉喉既是炉料的加入口,也是煤气的导出口。它对炉料和煤气的上部分布起控制和调节作用。炉喉直径应和炉缸直径、炉腰直径及大钟直径比例适当。炉喉高度要允许装一批以上的料,以能起到控制炉料和煤气流分布为限。
炉身:高炉铁矿石间接还原的主要区域,呈圆锥台简称圆台形,由上向下逐渐扩大,用以使炉料在遇热发生体积膨胀后不致形成料拱,并减小炉料下降阻力。炉身角的大小对炉料下降和煤气流分布有很大影响。
炉腰:高炉直径最大的部位。它使炉身和炉腹得以合理过渡。由于在炉腰部位有炉渣形成,并且粘稠的初成渣会使炉料透气性恶化,为减小煤气流的阻力,在渣量大时可适当扩大炉腰直径,但仍要使它和其他部位尺寸保持合适的比例关系,比值以取上限为宜。炉腰高度对高炉冶炼过程影响不很显著,一般只在很小的范围内变动范。
炉腹:高炉熔化和造渣的主要区段,呈倒锥台形。为适应炉料熔化后体积收缩的特点,其直径至上而下逐渐减小,形成一定的炉腹角。炉腹的存在,使燃烧带处于合适的位置,有利于气流均匀分布。炉腹高度随高炉容积大小而定,但不能过高或过低,一般为3.0~3.6m。炉腹角一般为79°~82°;过大,不利于煤气分布;过小,则不利于炉料顺行。
炉缸:高炉燃料燃烧、渣铁反应和贮存及排放区域,呈圆筒形。出铁口、渣口和风口都设在炉缸部位,因此它也是承受高温煤气及渣铁物理和化学侵蚀最剧烈的部位,对高炉煤气的初始分布、热制度、生铁质量和品种都有极重要的影响。炉缸高度的确定包括渣口的高度﹑风口高度的确定以及风口安装尺寸的确定。高炉炉型是炉体系统
的基础,炉型的好坏不但关系到高炉是否高产稳产,也关系到高炉煤气利用的好坏和燃料比的大小,同时,也对高炉寿命的长短起着重要作用。
高炉炉型应该根据炉容大小、矿石品种、品位、熟料率、球团率、焦炭质量以及内衬和冷却壁的形式等多种因素共同确定。一般而言,炉容越大、品位越高、熟料率越高、球团比越大、内衬越薄、炉型相对越矮胖,反之炉型越瘦长。在我国,随着各钢铁企业大力提高矿石品位、提高熟料率及球团比以及薄壁内衬的盛行,高炉有逐渐矮胖的趋势[22]。
炉底:高炉炉底砌体不仅要承受炉料、渣液及铁水的静压力,而且受到1400~4600℃的高温、机械和化学侵蚀、其侵蚀程度决定着高炉的一代寿命。只有砌体表面温度降低到它所接触的渣铁凝固温度,并且表面生成渣皮(或铁壳),才能阻止其进一步受到侵蚀,所以必需对炉底进行冷却。通常采用风冷或水冷。目前我国大中型高炉大都采用全碳砖炉底或碳砖和高铝砖综合炉底,大大改善了炉底的散热能力。
炉基:它的作用是将所集中承担的重量按照地层承载能力均匀地传给地层,因而其形状都是向下扩大的。高炉和炉基的总重量常为高炉容积的10~18倍(吨)。炉基不许有不均匀的下沉,一般炉基的倾斜值不大于0.1%~0.5%。高炉炉基应有足够的强度和耐热能力,使其在各种应力作用下不致产生裂缝。炉基常做成圆形或多边形,以减少热应力的不均匀分布。炉基表面受热不均是基础产生裂缝和混凝土遭到破坏的主要原因。由于基础长期在高温作用下,不仅产生了相当大的内应力和变形,并改变了材料的物理学性能,使钢筋混凝土失去了它的承载能力。普通混凝土温度超过400℃时,由于石灰的水化作用,混凝土即在空气中自行破坏[23]。
实践证明采用在炉底耐火层与炉基钢筋之间的素垫层内钻孔布设水放射状的双层冷却管,向内管注入冷水、经外管和内管之间的环状间隙流出并带出热量的循环水冷却方案,对降低高炉炉基及炉底温度并将其控制在一个确保高炉正常工作的允许温度范围、维持炉基安全并减缓炉底熔蚀、延长一代炉龄、节省巨额的高炉翻修费用切实可行,技术经济效果显著。
炉衬:高炉炉衬组成高炉的工作空间,并起到减少高炉热损失、保护炉壳和其它金属结构免受热应力和化学侵蚀的作用。炉衬是用能够抵抗高温作用的耐火材料砌筑而成的。炉衬的损坏受多种因素的影响,各部位工作条件不同,受损坏的机理也不同,因此必须根据部位、冷却和高炉操作等因素,选用不同的耐火材料。
高炉本体设计
高炉炼铁综合计算及高炉本体设计
目录 前言3 摘要错误!未定义书签。 第一章高炉炼铁综合计算4 原始条件4 工艺计算6 配料计算6 物料平衡10 热平衡计算15 热平衡表18 m的高炉本体设计 19第二章有效容积12753 技术经济指标确定19 高炉内型尺寸计算19 炉衬材质及厚度22 炉底衬砖的设计22 炉腹、炉腰及炉身下部的砌筑22 炉身上部和炉喉砌筑23 高炉冷却 23 冷却的目的和意义24 高炉冷却介质 24 冷却设备 24 炉体钢结构25 炉体钢结构25 炉壳25 高炉基础25 结论错误!未定义书签。 谢辞26 参考文献 27
前言 高炉炼铁是以铁矿石(天然富矿、烧结矿、球团矿)为原料,以焦炭、煤粉、重油、天然气等为燃料和还原剂,以石灰石等为熔剂,在高炉内通过燃料燃烧、氧化物中铁元素的还原以及非铁氧化物造渣等一系列复杂的物理化学过程获得生铁。其主要副产品有高炉炉渣和高炉煤气。 为实现优质、低耗、高产和延长炉龄,高炉本体结构和辅助系统必须满足耐高温,耐高压,耐腐蚀,密封性好,工作可靠,寿命长,产品优质,产量高,消耗低等要求。现代化高炉已成为高度机械化、自动化和大型化的一种综合生产装置。高炉车间的设计也必须满足高炉生产的经济技术指标,以期达到最佳的生产效果。 摘要: 高炉炼铁的历史悠久,炼铁技术日臻成熟,是当今主要的炼铁方式。高炉作为炼铁工艺的主体设备,其结构的合理性对炼铁的工艺操作、生产技术指标以及自身的寿命都有十分重要的影响。根据攀枝花钒钛磁铁矿的高炉冶炼特点,通过进行配料计算和物料平衡计算,设计了1700m3高炉本体。设计过程除考虑通常的高炉设计方案外,还考虑了攀枝花钒钛磁铁矿多年高炉冶炼的一些生产实践经验。采用碳砖加高铝砖综合炉底、全碳砖炉缸;冷却设备的设计为水冷炉底、炉缸和炉底采用三段光面冷却壁、炉身采用镶砖冷却壁;高炉钢结构采用炉体框架式结构,最后采用CAD绘制出高炉本体图。 关键词: 高炉炼铁;综合计算,高炉本体设计
毕设任务书_车间设计
2014届应用化学制药方向《毕业设计任务书》 设计人: 设计题目: 设计目的:设计的目的是把选定的实验室的的小试工艺放大到规模化大生产的相应条件,在选择中设计出最合理、最经济的生产工艺流程,做出物料和能量衡算;根据产品的档次,筛选出合适的设备;按GMP规范要求设计车间工艺平面图;估算生产成本,最终使该制药企业得以按预定的设计期望顺利投入生产。 设计规范:《中华人民共和国药典(2010版)》、《药品注册管理办法(局令第28号)》、《医药工业洁净厂房设计规范(GB50457--2008)》、《药品生产质量管理规范(2010年版)》等。 设计内容: 1.处方设计 (1)查阅文献,详细列出药物的临床用途、理化性质、稳定性和生物学特性(天然药物罗列指标性成分的生物学特性)等信息(天然药物提取物还需列药物浸膏的性状信息)。说明这些信息对选择剂型的指导意义。 药物的理化性质信息至少包括:溶解度和pKa、粒径(天然药物浸膏的过筛目数)、晶型、吸湿性、脂水分配系数(天然药物浸膏列指标性成分的脂水分配系数)、pH-稳定性关系。 稳定性包括:药物(或天然药物的指标性成分)对光、湿、热的稳定性。 生物学特性包括:药物(或天然药物的指标性成分)在人体内的吸收、分布、代谢、排泄等。 (2)处方的筛选与优化 列出选定处方的处方全部组成及各原辅料的用量。处方组成应包括:原料药、全部辅料、包装材料或容器。 原料药、全部辅料、包装材料或容器应通过对比分析,选择固定的供应商。 说明处方筛选过程,并结合药物的临床用途、理化性质、稳定性和生物学特性及辅料的理化性质、稳定性和生物学特性等信息,说明所选定处方的合理性及存在的问题。 说明处方优化的过程及理由。 处方的筛选与优化的原则:根据临床用途及给药途径慎重选择,尽量优化处方,做到处方与生产工艺为最佳匹配、有利于设备选型与生产工艺验证。
年产量500万吨高炉炼铁车间设计毕业论文
年产量500万吨高炉炼铁车间设计毕业论文 目录 1 绪论 1.1 高炉炼铁的任务及工艺流程 (8) 1.2 高炉生产的特点及优点 (9) 1.3 设计原则和指导思想 (9) 2炼铁工艺计算 2.1 配料计算 (10) 2.2 物料平衡计算 (12) 2.3 热平衡计算 (15) 3高炉本体 3.1 高炉炉型 (19) 3.2 高炉炉衬 (20) 3.3 炉体冷却方式 (21) 3.4 冷却系统 (24) 3.5 高炉钢结构及高炉基础 (25) 4 炉顶装料制度 4.1 并罐式无钟炉顶装料设备 (29) 4.2 均压装置 (31) 4.3 探料尺 (32) 5 供料系统 5.1 矿槽、焦槽容积与数量的确定 (33) 5.2 筛分 (33) 5.3上料系统 (33) 5.4 贮矿槽下运输称量 (34)
6送风系统 6.1 鼓风机的选择 (35) 6.2 热风炉的结构 (35) 6.3 热风炉常用耐火材料 (37) 6.4 燃烧器及送风制度的选择 (37) 6.5 热风炉主要管道直径的选定 (37) 7.渣铁处理系统 7.1 风口平台及出铁场 (39) 7.2 炉前设备 (39) 7.3 炉渣处理 (41) 8 煤气除尘系统 8.1 除尘设备及原理 (44) 8.2 有关设备 (45) 8.3 重力除尘器 (45) 9 喷吹设备 9.1 设计为喷吹煤粉 (47) 9.2 高炉喷煤设备 (48) 10车间布置形式 10.1 车间布置 (50) 10.2 本设计车间平面布置形式 (50) 结束语 (52) 参考文献 (53)
1 绪论 1.1 高炉炼铁的任务及工艺流程 高炉炼铁的任务是用还原剂(焦炭、煤粉)在高温条件下将铁矿石或含铁原料还原成液态生铁的过程。高炉生产要求以最小的投入获得最大的产出,即做到高产、优质、低耗、有良好的经济效益。 高炉生产时借助高炉本体和其辅助设备来完成的。高炉本体是冶炼生铁的主体设备,它是由耐火材料砌筑的竖立式圆筒形炉体,最外层是由钢板制成的炉壳,在炉壳和耐火材料之间有冷却设备。要完成高炉炼铁生产,除高炉本体外,还必须有其他附属系统的配合,其生产工艺流程如图1-1所示。 图1-1 高炉炼铁生产工艺流程 1—矿石输送皮带机;2—称量漏斗;3—贮矿槽;4—焦炭输送皮带机;5—给料机; 6—焦粉输带机;7—焦粉仓;8—贮焦槽;9—电除尘器;10—调节阀;11—文氏管除尘器;12—净煤气放散管;13—下降管;14—重力除尘器;15—上料皮带机;16—焦炭称量漏斗;17—矿石称量漏斗;18—冷风管;19—烟道;20—蓄热室;21—热风主管;22—燃烧室; 23—煤气主管;24—混风管;25—烟筒。 (1)供料系统。包括贮矿槽、贮焦、称量与筛分等一系列设备,其任务是将
毕业设计平台使用方法
毕业实践综合系统学生操作文档系统域名:https://www.360docs.net/doc/a68178859.html, 用户名:学号 密码:身份证号 1.修改个人信息 学生输入学号和自己的身份证号码登陆进入系统出现个人信息维护的界面, 这个界面分成两部分,第一部分是个人信息,可以修改,第二部分是系统自动产生的统计信息,不用修改。界面如下所示: 图1.1:登陆后第一个页面 第一部分个人信息请完整填入,特别是不要忘记QQ和邮箱,老师想同你交流的时候的会把信息发到你的邮箱里。第二部分可以反映出你的毕业设计和实习的完成进程。 2.组建毕业设计小组 注:有的系毕业设计任务由分小组完成,则可以操作这个模块,,有的系的毕业设计任务由每个学生独立完成则不用操作这个模块。 在图 1.1所示的网页中上部分主菜单项,左边出现系统管理的各子菜单项,选择其中的子菜单,就在网页中间右半部分出现如下的页面:
图2.1组建毕业设计小组模块浏览界面 从图中可以看出,系,专业,班级下拉列表默认值为登录的学生所在系,所在专业,所在班级,且不能作修改,也就是说一个学生只能查看自己班级的毕业设计分组情况。 2.1新建一个毕业设计小组 点击,网页中间右半部分就出现如下界面: 图2.2 添加毕业设计小组界面 图中可以看出:系部,专业,班级,小组负责人等下拉列表框的内容已自动填写,分别是登录学生所在系部,专业,班级及其姓名,且不能修改。 在小组名称文本框中输入一个小组名称,建议最好在名称中包含小组负责人的信息,字数不要超过10个中文字。点击保存按钮,毕业设计小组就能添加成功,但如果登录的学生已经是某个小组成员,或者已经以个人名义选择了毕业设计课题,或已给其分配毕业设计课题(有的系毕业设计课题不用学生网上选择,由老师分配),则不能新建毕业设计小组。 毕业设计小组创建成功后,就出现如下界面:
年产40000吨苯酐的车间工艺设计_毕业设计
第一章文献综述 1.1苯酐简述 苯酐,全称为邻苯二甲酸酐(Phthalic Anhydride),常温下为一种白色针状结晶(工业苯酐为白色片状晶体),易燃,在沸点以下易升华,有特殊轻微的刺激性气味。苯酐能引起人们呼吸器官的过敏性症状,苯酐的粉尘或蒸汽对皮肤、眼睛及呼吸道有刺激作用,特别对潮湿的组织刺激更大。苯酐主要用于生产PVC 增塑剂、不饱和聚酯、醇酸树脂以及染料、涂料、农药、医药和仪器添加剂、食用糖精等,是一种重要的有机化工原料。在PVC 生产中,增塑剂最大用量已超过50%,随着塑料工业的快速发展,使苯酐的需求随之增长,推动了国内外苯酐生产的快速发展。 最早的苯酐生产始于1872 年,当时德国BASF 公司以萘为原料,铬酸氧化生产苯酐,后又改用发烟硫酸氧化生产苯酐,但收率极低,仅有15%。自1917 年世界开始以氧化钒为催化剂,用萘生产苯酐后,苯酐的生产逐步走向工业化、规模化,并先后形成了萘法、邻法两种比较成熟的工艺[1]。 1.2苯酐的性质[2] 苯酐,常温下为一种白色针状结晶(工业苯酐为白色片状晶体),易燃,在沸点以下易升华,有特殊轻微的刺激性气味。 分子式C8H4O3,相对密度1.527(4.0℃),熔点131.6℃,沸点295℃(升华),闪点(开杯)151.7℃,燃点584℃。 微溶于热水和乙醚,溶于乙醇、苯和吡啶。 1.3苯酐的合成方法比较及选取 1.3.1合成苯酐的主要工艺路线 1.3.1.1 萘法[1] 1.3.1.1.1反应原理 萘与空气在催化剂作用下气相氧化生成苯酐。
+O O O 2 V 2O 5 CO 2O H 29/2++2 2 1.3.1.1.2 工艺流程 空气经净化、压缩预热后进入流化床反应器底部,喷入液体萘,萘汽化后与空气混合,通过流化状态的催化剂层,发生放热反应生成苯酐。反应器内装有列管冷却器,用水为热载体移出反应热。反应气体经三级旋风分离器,把气体携带的催化剂分离下来后,进入液体冷凝器,有40%-60%的粗苯酐以液态冷凝下来,气体再进入切换冷凝器( 又称热融箱)进一步分离粗苯酐,粗苯酐经预分解后进行精馏得到苯酐成品。尾气经洗涤后排放,洗涤液用水稀释后排放或送去进行催化焚烧。 1.3.1.2邻法 1.3.1.2.1 反应原理[1] 邻二甲苯与空气在催化剂作用下气相氧化生成苯酐。 CH 3 CH 3 +3O 2 3O O O H 225 + 1.3.1. 2.2 工艺流程 过滤、净化后的空气经过压缩,预热后与汽化的邻二甲苯混合进入固定床反应器进行放热反应,反应管外用循环的熔盐移出反应热并维持反应温度,熔盐所
2012年高炉炼铁毕业设计
(2012届) 专科毕业设计(论文)资料 湖南工业大学教务处
本次设计是根据娄底地区设计年产量为480万吨的高炉炼铁车间,该地区矿藏丰富,水资源充沛,交通发达,设计炼铁车间比较合理。炼铁方法主要有高炉法、直接还原法、熔融还原法等,其原理是矿石在特定的气氛中(还原物质CO、、C;适宜温度等)通过物化反应获取还原后的生铁。生铁除了少部分用于铸H 2 造外,绝大部分是作为炼钢原料。虽然现在高炉并不是以后炼钢的发展趋势,但高炉冶金是获得生铁的重要手段。它是以铁矿石是为原料,焦炭煤粉作为燃料和还原剂,在高炉内通过燃料燃烧,氧化物中铁元素的还原以及非铁氧化物造渣等一系列复杂的物理化学过程。随着冶金技术的不断发展,对其冶炼的关键设备——“高炉”。也有了越来越严格的要求。高效率、高质量、高寿命、低能耗、低污染——是本次设计所追求的目标。 在本次设计中翻阅了大量的参考文献,相当于又系统的学习了一遍高炉的有关知识,是对高炉发展的新的具体认识和总结,是本人三年专业知识学习的一个促进过程。本次设计中得到了王建丽老师的悉心指导和帮助,本人表示非常的感谢。然而,由于本人水平有限,设计中难免有不足和纰漏之处。望各位给予指正。
第一章绪论 (1) 1.1 高炉炼铁任务及工艺流程 (1) 1.2 高炉生产的特点及优点 (2) 1.3 设计原则和指导思想 (2) 1.4 厂址及建厂条件论证 (3) 第二章炼铁工艺计算 (4) 2.1 配料计算 (4) 2.2 根据铁平衡求铁矿石需要量 (6) 2.3 渣量及炉渣成分计算 (6) 2.4 物料平衡计算 (7) 2.5 热平衡计算 (8) 第三章高炉本体 (14) 3.1 高炉炉型 (14) 3.2 高炉炉衬 (16) 3.3 炉体冷却方式 (16) 3.4 冷却系统 (19) 3.5 高炉钢结构及高炉基础 (20) 第四章炉顶装料系统 (23) 4.1 串罐式无钟炉顶装料设备 (23) 4.2 串罐式无钟炉顶的特点 (25) 第五章供料系统 (26) 5.1 高炉供料系统 (26) 5.2 储矿(焦)槽及其主要设备 (27)
年产2000吨环氧树脂车间工艺设计毕业设计(论文)
目录 第1章绪论 (8) 1.1产品介绍 (8) 1.2、生产工艺 (8) 1.2.1一步法工艺 (11) 1.2.2二步法工艺 (11) 1.3、主要原材料 (12) 第2章初步工艺流程设计 (12) 2.1 工艺流程框图: (13) 2.2工艺流程: (14) 第3章物料衡算 (14) 3.1 计算条件与数据理: (15) 3.2 原料用量计算: (15) 3.3 缩合工段物料衡算: (16) 3.3.1 一次反应: (16) 3.3.3回收过量环氧氯丙烷: (18) 4.3.4 环氧树脂收集: (19) 第4章热量衡算 (19) 4.1对溶解釜进行热量衡算:............................ 错误!未定义书签。 4.2对反应釜进行热量衡算:............................ 错误!未定义书签。 4.2.1冷却阶段:.................................. 错误!未定义书签。 4.2.2反应阶段:.................................. 错误!未定义书签。 4.2.3.回流脱水阶段:.............................. 错误!未定义书签。 4.3对蒸发器进行热量衡算:........................ 错误!未定义书签。 4.3.1脱苯所需热量衡算:.......................... 错误!未定义书签。 4.3.2脱苯用冷凝器冷却水用量计算:................ 错误!未定义书签。 5.3 其它设备的选型................................... 错误!未定义书签。第5章设备选型....................................... 错误!未定义书签。 5.1溶解釜的设计...................................... 错误!未定义书签。 5.1.1选材:...................................... 错误!未定义书签。 5.1.2 确定参数:.................................. 错误!未定义书签。 5.1.3计算筒体厚度:.............................. 错误!未定义书签。 5.1.4计算封头厚度:.............................. 错误!未定义书签。 5.1.5校核筒体和封头的水压试验强度:.............. 错误!未定义书签。 5.1.6夹套的设计:................................ 错误!未定义书签。 5.1.7搅拌器的设计:.............................. 错误!未定义书签。 5.2反应釜的设计:................................ 错误!未定义书签。 5.2.1选材:...................................... 错误!未定义书签。 5.2.2确定参数:.................................. 错误!未定义书签。 5.2.3计算筒体厚度:.............................. 错误!未定义书签。
高炉炼铁(附彩图)
本次将高炉炼铁工艺流程分为以下几部分: 一、 高炉炼铁工艺流程详解 二、 高炉炼铁原理 三、高炉冶炼主要工艺设备简介 四、高炉炼铁用的原料 、高炉炼铁工艺流程详解 高炉炼铁工艺流程详图如下图所示: 附:高炉炉本体主要组成部分介绍以及高炉操作知识 料钾调控阙, -20 0V 炉身V -E001C ■ -14001C 炉腹, -leoor £ 小料牛 小料钟 出铁口 , 900-1000V " 京铁加利面 铁 炉 炉爆气首 工艺设备相见文库文档: 料风咀
注,各类校珀均产生暖声
:、高炉炼铁原理 炼铁过程实质上是将铁从其白然形态一一矿石等含铁化合物中还原出来的过程。 铁矿石、焦炭、石炎石炼铁方法主要有高炉法、直接 还原法、熔融还原法等,其原理是 矿石在特定的气氛中(还原物质 CO、H2、C;适宜温度等)通过物化 反应获取还原后的生铁。生铁除了 少部分用于铸造外,绝大部分是作 为炼钢原料。 高炉炼铁是现代炼铁的主要方 法,钢铁生产中的重要环节。这种 方法是由古代竖炉炼铁发展、展了 改进而成的。尽管世界各国研究发很多新的炼铁法,但由于高炉炼铁技 术经济指标良好,工艺简单, 生产量大,劳动生产率高,能耗低,这种方法生产的铁仍占世界铁总产量的95%以上。 炼铁工艺是是将含铁原料(烧结矿、球团矿或铁矿)、燃料(焦炭、煤粉等)及其它辅助原料(石灰石、白云石、锭矿等)按一定比例白高炉炉顶装入高炉,并由热风炉在高炉下部沿炉周的风口向高炉内鼓入热风助焦炭燃烧(有的高炉也喷吹煤粉、重油、天然气等辅助燃料),在高温下焦炭中的碳同鼓入空气中的氧燃烧生成的一氧化碳和氢气。原料、燃料随着炉内熔炼等过程的进行而下降,在炉料下降
高炉设计的基础概念
高炉炉型概述 高炉炉型的发展 高炉是一种竖炉型的冶炼炉,它由炉体内耐火材料砌成的工作空间、炉体设备、炉体冷却设备、炉体钢结构等组成。 高炉生产实践表明:合理的炉体结构,对高炉一代炉龄的高产、优质、低耗和长寿起到保证作用,由此可以看出高炉的炉型应该有炉型和炉龄两个方面阐述。 近代高炉,由于鼓风机能力进一步提高,原料燃料处理更加精细,高炉炉型向着“大型横向”发展。对于炉型而言,从20世纪60年代开始,高炉逐步大型化,大型高炉的容积由当时的1000~1500m3逐步发展到现在的4000~5500m3。 /D即高径比缩小,大型随着炉容的扩大,炉型的变化出现以下特征:高炉的H U 高炉的比值已降到,1000m3级高炉降到,300m3级高炉也降到左右。和大小同步的还有高炉矮胖炉型发展,矮胖高炉的特征是炉子下部容积扩大,在适当的配合条件下利于增加产量,提高利用系数.但如矮胖得过分,易导致上部煤气利用差,使燃料比升高.此外,从全国节能要求出发,在高炉建设和炼铁生产经营管理中,应既抓产量,又抓消耗、质量和寿命的优秀实例进行总结推广,提倡全面贯彻“高产、优质、低耗、长寿,”八字方针。与盛高炉型相比,矮胖炉型的主要优点是:与炉料性能相适应,料柱阻力减小;风口增多,利于接受风量;高护更易顺行稳定。这些优点,给高炉带来了多产生铁,改进生铁质量,降低燃料消耗和延长寿命的综合效果。通过研究发现,当今用于炼铁的高炉炉喉直径均偏小,其炉喉直径与炉缸直径的比值均小于。通过研究发现,炉喉直径偏小影响炉身的间接还原效率,致使高炉能耗较高,影响高炉经济效益,因此,为了提高高炉炉身的间接还原效率,改善高炉产生技术指标和进行节能减排,特别推出一种扩大炉喉直径的新炉型高炉。采用的技术方案是:它包含炉缸、炉腹、炉腰、炉身、炉喉五部分,其中炉缸在炉腹的下面,炉缸上面连接炉腹,炉腹上面连接炉腰,炉腰上面连接炉身,炉身上面连接炉喉;由上述5部分组成的高炉内型,5个部分的横截面均呈圆形,其中炉缸直径用d表示,炉腰直径用D表示,炉喉直径用d表示,
固体制剂车间工艺设计毕业论文
固体制剂车间工艺设计毕业论文 1设计依据及设计围 1.1设计依据 1.1.1设计任务 课题名称:布洛芬剂车间工艺设计 生产规模:年产片剂(奥美沙坦酯)6.5亿片 1.1.2设计规和标准 1.药品生产质量管理规(2010年修订,国家食品药品监督管理局颁发) 2.药品生产质量管理规实施指南(2010年版,中国化学制药工业协会) 3.医药工业厂房洁净设计规,GB50457-2008 4.洁净厂房设计规,GB 50073-2001 5.建筑设计防火规,GB/T50016-2006(2006年版) 6.设计规和标准建筑设计防火规,GB/T50016-2006(2006年版) 7.爆炸和火灾危险环境电力装置设计规,GB50058-1992 8.工业企业设计卫生标准,GBZ 1-2010 1.2设计围 本设计参照《医药建筑项目初步设计容及深度的规定》、《车间装置设计》;及校本科生毕业小设计总体要求。 此次设计的围限于片剂车间围的工艺设计及对辅助设施、公用工程等提出设计条件,包括相关的生产设备、车间布置设计、带控制点的工艺流程设计,同时对空调通风、
照明、洁净设施、生产制度、生产方式、土建、环保等在的一些非工艺工程提出要求。
2设计原则及指导思想 2.1设计原则 2.1.1医药工业洁净厂房设计规 1.工艺布局应按生产流程的要求,做到布置合理,紧凑,有利生产操作,并能保证对生产过程进行有效的管理。 2.工艺布局要防止人流、物流之间的混杂和交叉污染,并符合下列基本要求: a分别设置人员和物料进出生产区的通道,极易造成污染的物料(如部分原辅料,生产中废弃物等),必要时可设置专用入口,洁净厂房的物料传递路线尽量要短。 b人员和物料进入洁净生产区应有各自的净化用室和设施。净化用室的设置要求与生产区的空气洁净度级别相适应。 c生产操作区应只设置必要的工艺设备和设施。用于生产、贮存的区域不得用作非本区域工作人员的通道。 3.在满足工艺条件的前提下,为了提高净化效果,节约能源,有空气洁净度要求按下列要求布置: a空气洁净度高的房间或区域宜布置在人员最少达到的地方,并宜靠近空调机房。 b不同空气洁净度级别的房间或区域宜按空气洁净度级别高低有及外布置。 c空气洁净度相同的房间或区域宜相对集中。 d不同空气洁净度房间之间相互联系应有防止污染措施,如气闸室或传递窗(柜)等。 4.洁净厂房应设置与生产规模相适应的原辅材料、半成品、成品存放区域,且尽可能靠近与其相联系的生产区域,减少运输过程中的混杂与污染。存放区域应安排试验区,
年产200万吨炼铁高炉车间设计
年产200万吨炼铁高炉车间设计
年产200万吨炼铁高炉车间设计 摘要 人类获得生铁重要手段是通过高炉炼铁,高炉炼铁是钢铁冶金中的基础环节,同时也是最重要的环节。本设计任务是设计一个年生产能力达200万吨炼铁高炉车间。 本次设计的高炉1100m3。高炉炉型为五段式,高炉炉衬设计依据各个部分的工作条件的不同以及炉衬破损的机理,选择相应的耐火材料。热风炉采用的传统改进型内燃式热风炉,燃烧室为复合型断面,热风炉数量为3座,关于热风炉的设计部分还包括热风炉的各种设备以及相应的技术参数。上料系统采用的是可不间断上料,原料破损率低的皮带运输上料,炉顶装料设备是并罐式无钟炉顶。煤气处理系统的功能是降低高炉煤气粉尘含量,一般分为三个阶段--粗除尘、半精细除尘、精细除尘。煤粉喷吹系统采用了单管路串罐式直接喷吹工艺,这种工艺大大提高了喷吹效率,改善冶炼条件。本设计中还包括了其他一些环节的设计,例如渣铁处理系统。在设计的同时,广泛参考借鉴前辈的研究数据和国内外同级别炉容的高炉的实际生产经验,从理论和实践并举的角度出发,努力使本设计的高炉在技术操作上实现自动化和机械化,并把对环境的损害降到最低。 关键词:高炉,冶金计算,热风炉,鼓风机,煤气处理,渣铁处理
目录 前言 (1) 第一章高炉炼铁概况 (2) §1.1 高炉炼铁的发展概况 (2) §1.2 高炉及其附属设备 (2) §1.3 高炉炼铁设计的基本原则 (2) 第二章高炉炼铁综合计算 (4) §2.1 原始资料 (4) §2.2 配料计算 (5) §2.3 物料平衡计算 (8) §2.4 热平衡计算 (12) 第三章高炉炼铁车间设计 (17) §3.1 高炉座数及容积设计 (17) 第四章高炉本体设计 (18) §4.1 炉型设计 (18) §4.2 炉衬设计 (20) §4.3 高炉冷却设备 (21) §4.4 高炉冷却系统 (23) §4.5 高炉送风管路 (23) §4.6 高炉钢结构 (23) §4.7 高炉基础 (24) 第五章附属设备系统 (25) §5.1 供料系统 (25) §5.2 炉顶装料系统 (26) §5.3 送风系统 (27) §5.4 煤气处理系统 (30) §5.5 煤粉喷吹系统 (33) §5.6 渣铁处理系统 (34) 第六章高炉炼铁车间平面布置 (37)
软件开发毕业设计范文
长春信息技术职业学院毕业论文 计算机软件毕业论文 系别: 专业班级: 指导老师: 学生姓名: 2013年5月18日
摘要: 在21世纪的今天,手机几乎是每个人的必备品,特别是在高校的学生,不管是吃饭、睡觉、还是上课,手机总是不离手。而且手机更新换代更是日新月异,然后在现在的手机市场中android系统的智能机成为主流。 我们这款画画小软件正是在android系统的平台上进行运行。在日常生活中,我们画画只能在纸上的时代已经过去,这款android小画家画画软件,可以进行简单的简笔画操作、上色。既节约了增加了我们平时的乐趣,也节约了资源。该软件具有改变画图的形状、改变画笔的颜色、改变画刷的宽度、改变画画的风格、以及保存、清除等功能。经过测试,这是一款能为我们生活增加乐趣的软件。 关键字:手机;android;画画软件
目录 第一章引言..................................................... - 1 - 1.1发展情况................................................. - 1 - 1.2研究现状................................................. - 1 - 1.3研究前景展望............................................. - 1 - 1.4选题的目的及意义......................................... - 2 - 第二章系统可行性分析........................................... - 3 - 2.1经济可行性分析........................................... - 3 - 2.2操作可行性分析........................................... - 3 - 2.3技术可行性分析........................................... - 3 - 2.3.1 eclipse概述....................................... - 3 - 2.3.2 ADT 概述........................................... - 4 - 2.3.3 android SDK概述................................... - 4 - 2.3.4 java概述.......................................... - 5 - 第三章需求分析................................................. - 6 - 3.1软件功能描述............................................. - 6 - 3.2系统功能分析............................................. - 7 - 3.3软件需求分析............................................. - 9 - 3.4软件概念结构设计......................................... - 9 - 第四章软件详细设计............................................ - 12 - 4.1软件设计原理............................................ - 12 - 4.2软件模块设计............................................ - 12 - 第五章软件测试................................................ - 30 - 总结...................................................... - 31 - 参考文献....................................................... - 32 - 致谢...................................................... - 33 -
高炉设计的基础概念
文献综述 高炉炉型概述 高炉炉型的发展 高炉是一种竖炉型的冶炼炉,它由炉体内耐火材料砌成的工作空间、炉体设备、炉体冷却设备、炉体钢结构等组成。 高炉生产实践表明:合理的炉体结构,对高炉一代炉龄的高产、优质、低耗和长寿起到保证作用,由此可以看出高炉的炉型应该有炉型和炉龄两个方面阐述。 近代高炉,由于鼓风机能力进一步提高,原料燃料处理更加精细,高炉炉型向着“大型横向”发展。对于炉型而言,从20世纪60年代开始,高炉逐步大型化,大型高炉的容积由当时的1000~1500m3逐步发展到现在的4000~5500m3。随着炉容的扩大,炉型的变化出现以下特征:高炉的H U/D即高径比缩小,大型高炉的比值已降到,1000m3级高炉降到,300m3级高炉也降到左右。和大小同步的还有高炉矮胖炉型发展,矮胖高炉的特征是炉子下部容积扩大,在适当的配合条件下利于增加产量,提高利用系数.但如矮胖得过分,易导致上部煤气利用差,使燃料比升高.此外,从全国节能要求出发,在高炉建设和炼铁生产经营管理中,应既抓产量,又抓消耗、质量和寿命的优秀实例进行总结推广,提倡全面贯彻“高产、优质、低耗、长寿,”八字方针。与盛高炉型相比,矮胖炉型的主要优点是:与炉料性能相适应,料柱阻力减小;风口增多,利于接受风量;高护更易顺行稳定。这些优点,给高炉带来了多产生铁,改进生铁质量,降低燃料消耗和延长寿命的综合效果。通过研究发现,当今用于炼铁的高炉炉喉直径均偏小,其炉喉直径与炉缸直径的比值均小于。通过研究发现,炉喉直径偏小影响炉身的间接还原效率,致使高炉能耗较高,影响高炉经济效益,因此,为了提高高炉炉身的间接还原效率,改善高炉产生技术指标和进行节能减排,特别推出一种扩大炉喉直径的新炉型高炉。采用的技术方案是:它包含炉缸、炉腹、炉腰、炉身、炉喉五部分,其中炉缸在炉腹的下面,炉缸上面连接炉腹,炉腹上面连接炉腰,炉腰上面连接炉身,炉身上面连接炉喉;由上述5部分组成的高炉内型,5个部分的横截面均呈圆形,其中炉缸直径用d表示,炉腰直径用D表示,炉喉直径用d表示,炉喉直径d1与炉缸直径d之比在~之间。从而炉型能够充分发挥炉身的间接还原作用,使高炉节约焦炭,降低消耗,减少二氧化碳排放,能够使钢铁企业降低生产成本。 高炉炉龄及其影响因素
日产2500吨白水泥熟料生产线原料粉磨车间工艺设计毕业设计说明书(可编辑)
日产2500吨白水泥熟料生产线原料粉磨车间工艺设计 毕业设计说明书 2500t/d特种水泥熟料生产线原料粉磨车间工艺设计 摘要:拟设计一条日产2500t干法白水泥生产线,设计部分重点是生料粉磨配套系统工艺设计。在设计中参考了很多国内外比较先进的大型水泥厂,用了很多理论上的经验数据。其中主要设计内容有:1.配料计算、物料平衡计算、储库计算;2.全厂主机及辅机的选型;3.全厂工艺布置;4.窑磨配套系统工艺布置;5.计算机CAD绘图;6.撰写设计说明书。 白水泥与普通硅酸盐水泥在成分上的主要区别是白水泥中铁含量只有普通水泥的十分之一左右。设计采用石灰石与叶腊石两种原料。物料平衡计算时考虑到需控制铁含量,按照经验公式(石灰石饱和系数、硅酸率、铝氧率)计算并参考其他白水泥厂,得出恰当的率值为:KH0.9、IM3.85、SM18。全厂布局由水泥生产的流程决定。设计中采用立磨粉磨系统。立磨设备工艺性能优越,单机产量大,操作简便,能粉磨料粒度大、水分高的原料,对成品质量控制快捷,可实行智能化、自动化控制等优点。设计采用窑尾废气烘干物料,节约能源。总之原则上最大限度地提高产量和质量,降低热耗,符合环保要求,做到技术经济指标先进合理。 关键词:白水泥;干法生产线;回转窑;立磨 2500t / d special cement clinker production line and supporting system for kiln grinding process design
Abstract: Designing a 2500 t/d white cement production line, which was focused on the design part of the raw material grinding design supporting system. In the design, many more advanced large-scale cement home and abroad are referenced. Main content of the design were: 1. burden calculation, the material balance calculation, calculation of reservoir; 2. The whole plant selection of main and auxiliary machinery; 3. the entire plant process layout; 4. the system grinding process kiln Arrangement; 5. computer CAD drawing; 6.writing design specifications. The main difference in composition of white cement and ordinary Portland cement is the content of white cement in the iron was only one-tenth of the ordinary cement. Controlling the iron content was considered when calculated material balance. According to the experience formula KH, IM, SM and refer to other white cement plant, drawn the appropriate ratio value: KH 0.9, IM 3.85, SM 18. The layout of the entire plant was up to the cement production process.Vertical roller mill grinding system was used in key plant design. Vertical grinding process equipment performance was superiority, single output, easy to operate, grinding people particle size, moisture and high raw materials, finished product quality control fast and it can take advantages of intelligent and automated control.In principle, the aim of the design is increase production and quality, reduce heat consumption, be accord with environmental requirements. so, technical and economic indicators should
毕业设计文档模板
目录 第一章引言 (1) 第二章所用开发语言简介 (1) 2.1 Delphi 介绍 (1) 2.2 Delphi具有的优点 (1) 2.3模块中使用的Delphi系统预定义控件及其属性简介 (1) 第三章需求分析阶段 (2) 3.1登录模块和主界面模块需求分析 (2) 3.2登录模块和主界面模块设计系统性能要求: (2) 3.3负责模块中系统的功能分析: (2) 3.4功能模块 (2) 3.4.1功能的实现 (2) 3.4.2模块框架图 (2) 3.5模块数据分析 (3) 第四章设计阶段 (3) 4.1概要设计 (3) 4.1.1数据库概论及SQL SERVER 2000简介 (3) 4.1.2模块数据库设计 (3) 4.2详细设计 (5) 4.2.1数据信息准备 (5) 4.2.2程序数据流图 (6) 第五章软件设计说明 (6) 5.1界面模块设计 (6) 5.2主界面模块设计 (9) 第六章结束语 (10) 第七章参考文献 (10) 第八章致谢 (11)
第一章引言 随着我国教育事业的不断推进,一直以来许多高校对在校师生的基本资料维护、班级信息、选课情况、选修课程信息及学生选课成绩管理的半手工管理方式已不在适应社会,主要表现为工作效率低,容易由于人为的疏忽造成一些不必要的麻烦。最典型的就是学校手工记录些信息,经常由于不知道放哪或者丢失而无从下手。 以上所描述的手工过程的不足之处显而易见,整个管理环节都有可能由于人为因数而发生意想不到的后果。所以利用计算机来处理这些流程无疑会极大程度地提高效率和处理能力。我们将会看到学校管理人员不用象以前那样辛苦,工作人员出错的概率也会减少,工作效率就会提高。 为方便对在校师生的个人资料、选课情况、班级管理等进行高效的管理,特编写该程序以提高学校信息的管理效率。使用该程序之后,管理层可以及时查询在校师生的基本情况、班级管理,学生可以进行选课管理、成绩查询等一些功能,教师也可以进行适应的操作,如查看学生的基本信息、学生的选课成绩等。 第二章所用开发语言简介 2.1 Delphi 介绍 Delphi7.0是美国Borland公司出品的一种强大的可视化软件快速开发工具,是目前最好的Windows 应用程序开发工具! 它能支持面向对象、可视化的开发风格、具有强大的数据库管理功能,它所提供的强大的数据库编程工具,如ADO组件、IBX组件和数据模块设计窗口。 2.2 Delphi具有的优点 Delphi7.0提供一个快速的编译器,优化的编译模式在很大程度上提高了代码质量;提供统一集成开发环境(Integrated Development Environment 即IDE);集成了许多可视化辅助工具,实现了直观、可视的程序设计风格,方便地编写和管理各种类,维护程序的源代码;大大简化了应用程序的开发,提高编程效率;其封装了Windows的API函数、DATA等函数,简化了编程时创建、维护窗口的许多复杂的工作。 2.3模块中使用的Delphi系统预定义控件及其属性简介 (1)Button (按钮控件):产生某些命令或改变某些选项设置。 (2)Panel (面板控件):用于布局,美观设计,也可作为放置组件的
高炉钢结构设计
高炉钢结构设计 (steel structure design of blast furnace) 炼铁高炉专用钢结构的设计。高炉钢结构设计主要内容包括高炉本体和炉顶、上料系统、热风炉系统、粗煤气除尘系统、出铁场和辅助设施钢结构的设计,做好系统间整体配合联系、进行结构的材料选择和采取安全防护措施。高炉系统钢结构见图1。 设计时要进行结构形式的选择,构件强度稳定性、变形的计算和合理的构造处理,以保证结构安全使用与经济合理。设计应按《钢结构设计规范》及其它有关规范规定进行。对于地震区的高炉钢结构,其抗震设计要求还要符合抗震设计规范规定。 高炉钢结构的大部分是高炉生产设备的主要组成部分,其特点是:(1)种类繁多,形式特殊。有多层空间框架的炉体框架、多折点壳体的炉壳、异形壳体组成的热风炉壳、圆或椭圆形筒壳的通廊等。(2)结构尺寸及构件断面较大。如:5000m3 左右高炉全高可达120m,炉壳直径为20m,炉壳厚度可达90~120mm,炉体框架箱形柱的断面尺寸达2.0m×4.0m。(3)钢材用量多,如5000m3 高炉,包括运输、动力、管线在内钢结构用量近9万t。(4)工作条件较苛刻。如:炉体及周围结构受高温影响及水气锈蚀作用,热风炉外壳上部有时受晶间应力腐蚀开裂作用,上料料车卷扬机的作业率高达80%,壳体构件还要承受煤气爆炸等事故性内压力和砖衬被侵蚀后高炉外壳局部温度过热的作用。(5)各系统间结构穿插交错,荷载辗转传递。要控制其变形,使其相互协调。 高炉本体和炉顶钢结构高炉本体结构形式主要有自立式和非自立式两种(图2),也有介于两者之间的过渡形式。自立式高炉包括高炉外壳、炉体框架和炉顶刚架。炉壳独自承受炉内有关全部竖向荷载,而在炉周设炉体框架支承上部设备及平台。大中型高炉多用此种形式。非自立式高炉在炉壳下部设托圈和炉缸支柱,以支持炉内荷载,且多不设炉体框架,而将炉身平台及炉顶刚架支承在炉壳上,小型高炉多用此种形式。
年产150万吨中厚板车间工艺设计.docx
.................大学 本科生毕业设计开题报告 题目:年产150万吨中厚板车间工艺设计 学院:冶金与能源学院 专业:材料成型及控制工程 班级: 姓名: 学号: 指导教师: 2015年11 月15 日 一.选题背景 1.1题目来源 冶金行业经过了近8年的高速发展,行业的钢材产能已经达到近6亿吨/年。已有和在建的中厚板生产线近70条,中厚板生产能力达到接近7000万吨/年。但是国际金融危机的影响和国内经济周期的调整,钢铁产品市场成了典型的买方市场。冶金企业如何在这一轮经济调整中,实现技术和产品的转型成了决定企业生存的关键。各中厚板生产厂纷纷根据自身的技术装备特点、技术研发能力、市场客户需求确定自己的产品战略定位。综合实力强的企业,全力体现出产品的差异化战略,坚持不懈地开发生产其他企业无法生产或难于生产的市场短线、高档产品。高档次产品开发离不开性能控制技术,性能控制的新技术不仅提高钢板的性能,还可以带来生产成本的降低。 1.2项目概述: 经过对国内外中厚板市场现状的分析以及前景预测,综合对当地各种物料供应、能源等其它资源的分析,我们选择区域与资源优势居一体的唐山曹妃甸地区作为建厂厂址,设计一座年产量150万吨4300热轧中厚板车间,并且能够生产规格齐全、性能优良,能满足市场需求的产品。 1.3中厚板简介 中厚钢板:厚度大于4mm的钢板属于中厚钢板。其中,厚度4.0-20.0mm的钢板称为中厚板,厚度20.0-60.0mm的称为厚板,厚度超过60.0mm的为特厚板。 中厚板的用途: 中厚板主要用于建筑工程、机械制造、容器制造、造船、桥梁等行业,并且随着国民经济建设其需求量非常之大,范围也十分广。 (1)造船钢板:用于制造海洋及内河船舶船体。要求强度高、塑性、韧性、冷弯性能、焊接性能、耐蚀性能都好。 (2)桥梁用钢板用于大型铁路桥梁。要求承受动载荷、冲击、震动、耐蚀等。 (3)锅炉钢板:用于制造各种锅炉及重要附件,由于锅炉钢板处于中温(350℃以下)高压状态下工作,除承受较高压力外,还受到冲击,疲劳载荷及水和气腐蚀,要求保证一定强度,还要有良好的焊接及冷弯性能。 (4)压力容器用钢板:主要用于制造石油、化工气体分离和气体储运的压力容器或其