化工分离过程中的节能新技术研究进展
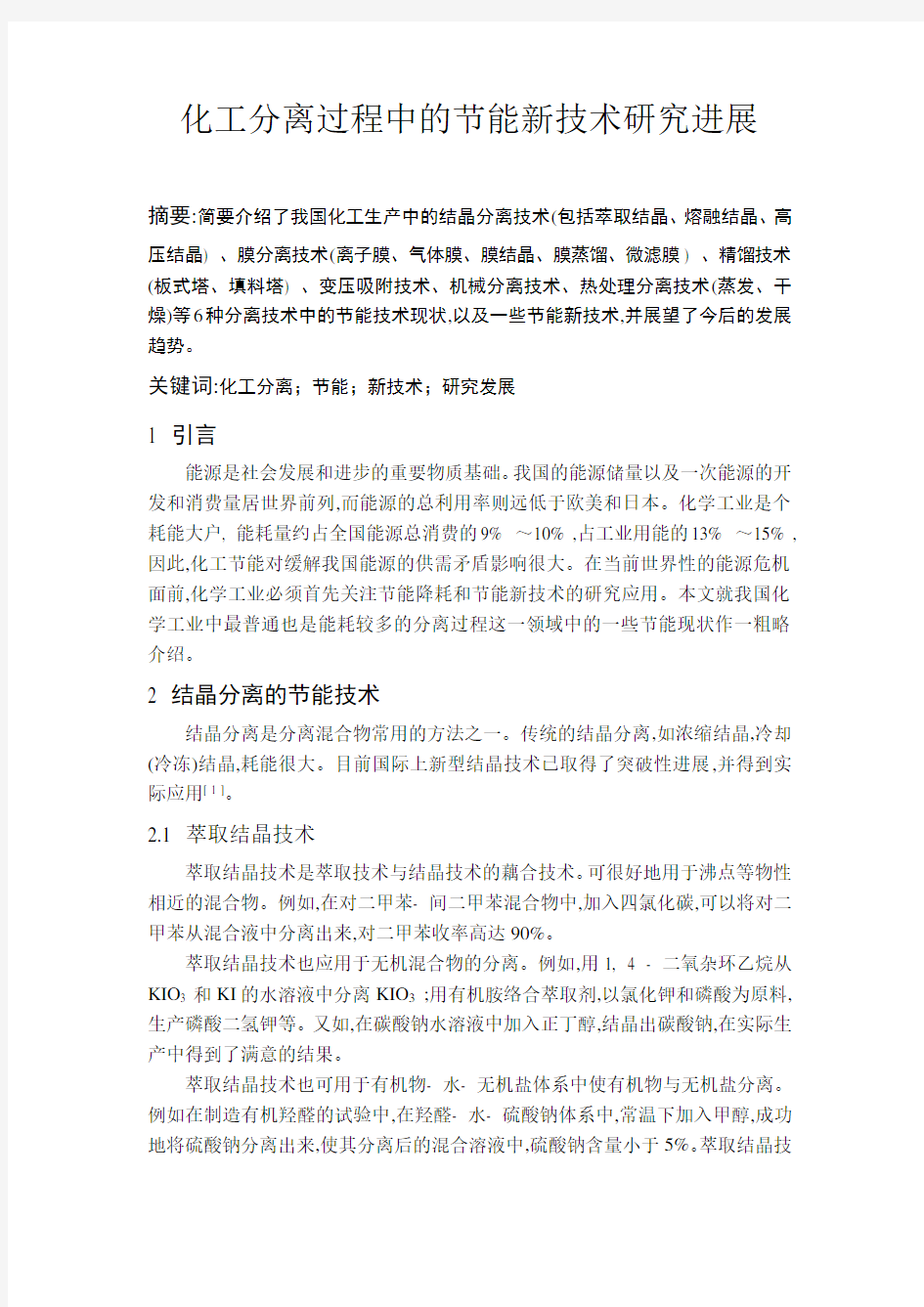

化工分离过程中的节能新技术研究进展
摘要:简要介绍了我国化工生产中的结晶分离技术(包括萃取结晶、熔融结晶、高压结晶) 、膜分离技术(离子膜、气体膜、膜结晶、膜蒸馏、微滤膜) 、精馏技术(板式塔、填料塔) 、变压吸附技术、机械分离技术、热处理分离技术(蒸发、干燥)等6种分离技术中的节能技术现状,以及一些节能新技术,并展望了今后的发展趋势。
关键词:化工分离;节能;新技术;研究发展
1 引言
能源是社会发展和进步的重要物质基础。我国的能源储量以及一次能源的开发和消费量居世界前列,而能源的总利用率则远低于欧美和日本。化学工业是个耗能大户, 能耗量约占全国能源总消费的9% ~10% ,占工业用能的13% ~15% ,因此,化工节能对缓解我国能源的供需矛盾影响很大。在当前世界性的能源危机面前,化学工业必须首先关注节能降耗和节能新技术的研究应用。本文就我国化学工业中最普通也是能耗较多的分离过程这一领域中的一些节能现状作一粗略介绍。
2 结晶分离的节能技术
结晶分离是分离混合物常用的方法之一。传统的结晶分离,如浓缩结晶,冷却(冷冻)结晶,耗能很大。目前国际上新型结晶技术已取得了突破性进展,并得到实际应用[ 1 ]。
2.1 萃取结晶技术
萃取结晶技术是萃取技术与结晶技术的藕合技术。可很好地用于沸点等物性相近的混合物。例如,在对二甲苯- 间二甲苯混合物中,加入四氯化碳,可以将对二甲苯从混合液中分离出来,对二甲苯收率高达90%。
萃取结晶技术也应用于无机混合物的分离。例如,用1, 4 - 二氧杂环乙烷从KIO3 和KI的水溶液中分离KIO3;用有机胺络合萃取剂,以氯化钾和磷酸为原料,生产磷酸二氢钾等。又如,在碳酸钠水溶液中加入正丁醇,结晶出碳酸钠,在实际生产中得到了满意的结果。
萃取结晶技术也可用于有机物- 水- 无机盐体系中使有机物与无机盐分离。例如在制造有机羟醛的试验中,在羟醛- 水- 硫酸钠体系中,常温下加入甲醇,成功地将硫酸钠分离出来,使其分离后的混合溶液中,硫酸钠含量小于5%。萃取结晶技
术关键是寻找到合适的萃取络合剂。
2.2 熔融结晶技术
由于近90%的有机化合物为低共熔型, 70%的化合物熔点在0~200 ℃,只有10%左右低于0 ℃,因此,用熔融结晶法更易分离。大多有机化合物的结晶,不需深冷分离,而且可利用废热、余热。新型熔融结晶技术特点: (1) 低能耗,结晶相变潜能仅是精馏的1 /3~1 /7; (2) 低操作温度; (3) 高选择性,可制取高纯或超纯( ≥99. 9%色谱纯)产品; ( 4) 环境污染较小。国际上熔融结晶装置目前有复合式悬浮结晶型和逐步冻凝型。天津大学已成功地开发了液膜结晶设备,并已成功地应用于4 200 t·a - 1邻位与对位二氯苯的分离。
2.3 高压结晶技术
高压结晶是利用加压下物系的液—固相变化的分离技术。其原理为:物系中包含的杂质使其熔点下降,对应相变压力上升,随着结晶过程的进行,固相份数增加,液相杂质浓度提高,相变压力不断上升,在共晶压力下,物系中就只有高纯目的物晶体和母液共存,排除母液经减压发汗,可分离得到更纯的目的物晶体。高压结晶尤其适应于有机物的提纯精制。
3 膜分离技术节能
膜分离技术是利用特定膜的渗透作用,在外界能量或化学位差的推动下,对气相或液相混合物进行分离、分级、提纯和富集,膜分离过程大多无相变,常温操作,高效、节能、工艺简便、污染小。20 世纪80 年代以来我国膜技术跨入应用阶段,同时也是新膜过程的开发阶段。在这一时期,膜技术在食品加工、海水淡化、纯水、超纯水制备、医药、生物、环保等领域得到了较大规模的开发和应用[ 2 ]。
3.1离子膜技术
离子膜烧碱不但能生产出高纯度烧碱和氢气,而且节能效果显著,比隔膜法节约能耗约30%。因此,离子膜法将逐步取代隔膜法生产烧碱。离子膜也开始应用于医疗、食品工业除去电解质,分离氨基酸及海水淡化等。
3.2 气体分离膜技术
膜分离氢气技术已成功地用在合成氨厂从驰放气中回收氢气,甲酸装置从合成气、水煤气脱氢气得到90%的一氧化碳, 炼厂从催化重整过剩气中分离出95%含量的氢气作为加氢裂解原料等。从空气中富集浓缩氧和氮,比深冷分离法要节能得多。
3.3 膜萃取技术
膜萃取是膜过程与液- 液萃取过程相结合的分离过程,特点是: (1) 萃取剂选
择范围宽; ( 2) 料液夹带损失小; (3) 过程不受“反混”的影响和“液泛”条件的限制;
(4) 可实现同级萃取和反萃取过程; ( 5) 可提高传质效率。膜萃取技术在分离生物化工产品和实现发酵耦合过程方面正成为研究工作的热点[ 3 ]。
3.4 膜蒸馏技术
膜蒸馏技术是膜技术与蒸发过程相结合的分离技术。过程是在常压和低于溶液沸点下进行,热侧溶液可以在较低的温度下操作,因而可利用废热或低温热源,达到节能效果。该技术弱点是单程效率较低,阻碍了其大规模应用。
3.5 微滤膜技术
微滤膜主要用于超纯水制取和除菌,微滤膜可制取电子工业用水,微滤膜除菌的水可以直接饮用。
4 精馏过程的节能降耗
精馏是化工、石化等行业中的重要组成部分,对整个流程的生产能力、产品质量、能源消耗与原料消耗、环境保护都有重大影响。石油和化学工业的能耗占工业总能耗的很大部分,其中约60%就用于精馏过程。精馏过程的节能主要有以下几种基本方式:提高塔的分离效率,降低能耗和提高产品回收率;采用多效精馏技术;采用热泵技术等。
4.1 板式塔
4.1.1高效导向筛板
高效导向筛板具有生产能力大、塔板效率高、塔压降低、结构简单、造价低廉、维修方便的特点,目前已广泛应用于化学工业、石油化工、精细化工、轻工化工、医药工业、香料工业、原子能工业等。
4.1.2板填复合塔板
板填复合塔板充分利用板式塔中塔板间距的空隙,设置高效填料,以降低雾沫夹带,提高气体在塔内的流速和塔的生产能力。同时气液在高效填料表面再次传质,进一步提高了塔板效率。由于负荷下限未变而上限大幅度提高,因此塔的操作弹性也大为提高。板填复合塔板已在石化、化工中的甲苯、氯乙烯等多种物系中得到成功应用。
4.1.3复杂精馏塔
传统的精馏塔及其精馏序列已不适应当前过程集成、设备集成的发展趋势。武昊宇等[ 4 ]进行了复杂精馏塔的研究,与传统精馏塔的一股进料二股产品的精馏塔比较,能够产生相当大的能量消耗及成本上的节约。复杂塔还适合更新设计,因为它经常可以通过对现有塔进行微小的改动来实行。在所有可能的多组分精馏过程新方案中,热偶精馏在能量和投资费用的节约上都非常有前途。他们采用
Underwood方程和Vmin分析了多组分热偶精馏的最小能耗;主要探讨了用详细的塔模型来进行多组分热偶精馏塔的设计,所建立的塔模型既能够描述传统塔又可以描述热偶精馏塔,并允许不同的选择结构互相比较:提出了以能量消耗最小为目标的,多组分混合物分离的热偶精馏序列的整体优化方法。他们以4 组分烷烃混合物的分离为例,根据详细的热偶精馏塔数学模型,计算了热偶精馏的能耗、年总费用,并比较了各种热偶方案的节能效果。以能量消耗最小为目标,对两种热偶精馏序列进行了整体优化。
4.2 填料塔
填料是填料塔最重要的传质内件,其性能主要取决于填料表面的湿润程度和气液两相流体分布的均匀程度。
4. 2. 1新型高效规整填料
新型高效规整填料主要包括金属板波纹填料和金属丝网波纹填料两大类,在将其进行物理的和化学的方法处理后,填料的分离效率大为提高。主要优点有: (1) 理论塔板数高,通量大,压力降低; ( 2) 低负荷性能好,理论板数随气体负荷的降低而增加,没有低负荷极限; (3) 放大效应不明显; ( 4) 适用于减压精馏,能够满足精密、大型、高真空精馏装置的要求,为难分离物系、热敏性物系及高纯度产品的精馏分离提供了有利的条件。
4. 2. 2新型高效散堆填料
(1) 金属鲍尔环填料,它采用金属薄板冲轧制成,由于在环壁上开了许多窗孔,使得填料层内的气、液分布情况及传质性能比拉西环有较大的改善。(2) 金属阶梯环填料,这种填料降低了环的高度,并在环的2个侧端增加了锥形翻边,使其性能较鲍尔环填料有了较大的进步。在同样液体喷淋密度下,其泛点气速较鲍尔环提高了10% ~20%;在同样气速下,压力降较鲍尔环低30% ~40%。(3) 金属环矩鞍填料,国内简称为英特洛克斯填料。这种填料巧妙地把环形和鞍形两类填料的特点综合成为一体,使它既有环形填料通量大的特点,又有鞍形填料液体分布性能好的特点,从而成为当前散堆填料中的佼佼者[ 5 ]。
4. 3提高热的利用率
首先,增强再沸器和冷凝器中的传热面积可使传热温差下降。增强传热表面有两大类型: ( 1) 多孔相变化传热面:包括微孔沸腾表面及特殊处理的冷疑表面,均可使沸腾或冷凝给热系数较之光管提高10~30倍; (2) 扩展的传热面:包括翅片管或开槽沟扩大传热面,可以使传热系数提高不少。其次,采用空气冷却器或蒸发冷却器代替水冷凝器可以避免积垢,水电综合能耗也较低,而且节省用水。再次,如果塔釜液是无关重要的废液,则可以把它的显热变成潜热加以利用。另外,采用低品位热能也是节能的有效方法[ 6 ]。
4. 4新蒸馏过程的探索与开发
为提高分离效率,降低能耗,需要寻求一些特殊的蒸馏方法以分离一些特殊的物料,诸如热敏物料,共沸热料等。一般有下列几个方面: ( 1) 添加物蒸馏。在蒸馏过程中加入某些添加物以利用溶液的非理想性,增大某一组分的挥发性,使组分容易分离,达到高效、节能目的。(2) 耦合蒸馏。蒸馏过程与其它过程同时进行,以达到强化作用和简化过程的目的。( 3) 动态蒸馏。包括可控的不稳定蒸馏与分批蒸馏,能提高传质效率和缩短操作时间, 达到增产和节能的目的。(4) 场效应蒸馏。包括带电、磁、激光、重力、功能微粒等场效应的蒸馏,对传质过程有不同程度的促进[ 7 ]。
5 机械分离方法的节能问题
5.1 新型机械分离装置的开发
以沉降式离心分离机为例,这种机器多数为皮带驱动方式,但因为回转体大,所以选择适当的马达能产生相当大的节能效果,对于标准处理量为7 m3 ·h - 1的装置,当使用直接起动方式驱动时需要22 kW的马达,而使用液力变速器和离心离合器起动方式时,由于减少了起动负荷,所以只用15 kW的马达就足够了[ 8 ]。5. 2机械分离装置的小型化
在间歇操作中,由于能在很大程度上灵活地确定操作压力和分离时间,使之与被分离的物料相适应,因而对分离速度几乎不产生影响,故多数情况下能够实现小型化。在连续操作的情况下,被分离物质在小型装置中停留时间减少,分离时间变短,为了加以弥补,就必须改变操作条件:通过增加压力、改善物料预处理方法等提高分离速度;或者通过降低运转速度,使处理量做出某种程度的牺牲等。关于连续式离心过滤机的小型化问题,最近已有报道。
5. 3设备操作管理的优化
进行机械分离时,通过预处理来改善固液混合物的性质和通过几种机械分离方法的并用来提高工作效率,确定最佳的操作压力、分离时间等工艺条件。如最佳过滤时间的确定。这些必须根据合理的设计方针和可靠的实践经验来把握,重要的是要充分运用以达到节能的目的。
6热处理分离技术的节能问题
6. 1蒸发操作的节能问题
蒸发是从含有不挥发溶质的稀溶液中脱除大量溶剂的最有效的分离方法,但同时需要消耗大量的加热蒸汽,能耗较高。目前,蒸发操作采用的主要节能措施如
下[ 9 ] :
6. 1. 1采用多效蒸发
多效蒸发的采用是蒸发操作节能的有效手段。采用多个蒸发器可以提高加热蒸汽的利用率(加热蒸汽与蒸发水分量之比D /W) 。多效蒸发中,前一效的二次蒸汽(低压蒸汽)作为后一效的加热蒸汽使用,故提高了加热蒸汽的利用率,亦即提高了热能的经济性,降低了能耗。
6. 1. 2引出额外蒸汽
在多效蒸发流程中,有时将某一效的二次蒸汽引出一部分作为其他加热设备的热源,只要二次蒸汽的温位能满足于其他加热设备的需要,引出额外蒸汽总是有利的,而且,引出额外蒸汽的效数越往后移,生蒸汽的利用率越高,越有利于节能。
6. 1. 3利用冷凝水的热量
蒸发装置消耗大量的加热蒸汽,必产生大量的冷凝水。较高温位的冷凝水可用于预热原料液,或者采用热泵式冷凝水回收装置、汽压罐式冷凝水回收装置和密闭式高温冷凝水回收装置来回收热能。
6. 1. 4再压缩二次蒸汽
可利用机械压缩和蒸汽动力压缩的方法对二次蒸汽进行再压缩,使二次蒸汽温度升高后重新作为加热蒸汽使用,只需补充一定的能量,便可利用其大量潜热,十分有利于节能。
6. 2干燥操作的节能问题
干燥过程是各种工业过程广泛采用的单元操作,其能量消耗相当大,因此干燥过程的节能问题尤为重要。干燥过程的主要节能措施如下:
6. 2. 1选用合适的干燥流程及设备
干燥操作流程和设备有各种形式,适应于各种场合。如何选用合适的干燥流程与设备对于干燥过程的节能是相当重要的,这方面主要依据干燥物料的特性和干燥产品的要求以及生产的实际情况而定。
6. 2. 2降低干燥装置的热能供给量
首先应对原料进行预处理,尽量采用机械分离方法脱除一部分游离水分,因为机械分离方法比热处理分离方法消耗的能量要少得多;其次是改善干燥介质的热状态: (1) 尽可能提高干燥介质的进气温度,减少干燥过程中的干燥介质消耗量,则干燥废气带走的热能相应减少,热效率提高,针对物料的热敏性问题,可考虑采用中间加热的办法。(2) 降低干燥介质的出口温度,提高其湿度,同样可以减少干燥介质的消耗量,提高干燥操作的热效率,但为防止干燥产品返潮以及设备的堵塞和设备材料的腐蚀问题,气体离开干燥器的温度需高于进入干燥器时的绝热饱和温度20~50 ℃[ 10]。
6. 2. 3利用先进的节能技术
(1) 采用部分废气循环的干燥流程。将含有大量热量的部分废气返回预热室,与新鲜空气混合使用,可将废气中的余热重新利用,并降低了空气加热器的热负荷,能耗将下降10%。目前,一般的废气循环量控制在20%左右。(2) 采用热效率高的传热设备。为了提高传热系数,减少换热面积,降低设备投资费用,需采用高效的换热设备。如新型换热器———空心环管换热器,它采用空心环支承双面强化传热管管束的强化技术,与一般的管壳型换热器相比,在相同的传热条件下,总传热系数可提高80% ~100% ,换热面积可减少35% ~40%。(3) 采用热管技术。热管吸热段吸收废气热量,并通过管壁传给管内工质,工质吸热后蒸发成蒸汽,蒸汽在压差的作用下上升至放热段,与管外冷流体换热,蒸汽冷凝并向外放出汽化潜热,冷凝液在重力的作用下回到吸收段。热管技术具有传热效率高,流动阻力损失少等优点,广泛地应用于废气余热的回收[ 5 ]。(4) 采用热泵技术。热泵是利用液态工作介质(氨、氟里昂、水等)在蒸发器中减压蒸发,从较低温度的干燥废气中吸收余热,而气态工作介质经压缩机后进人冷凝器,在较高温度下冷凝放出潜热预热新鲜空气。热泵的流程可分为闭路循环式和开放式两种。利用闭路循环式热泵技术,空气可循环使用,而开放式热泵技术,废气经热量回收后排出干燥系统。
6. 2. 4加强设备操作管理和管路保温
加强设备和管路的保温隔热,以减少干燥系统的热损失。同时优化送风系统,减少因热气的漏出和冷气的渗人造成的能量损失。
7 结语
以上仅对化工生产中混合物分离这一领域的节能技术作了一个粗略的介绍,化工生产中其它领域节能技术、新工艺正在不断地涌现,如新型催化剂的研究应用、新设备的研制应用、新材料的研究应用等。笔者认为,任何新技术开发成功,关键在于工业化应用。因此,应加强化工工程、设备的开发研究,使新技术能迅速转化为生产力,节约能源,增加效益。在生产上的应用,应根据本企业的实际情况,对各种新技术,进行详细分析比较。
参考文献:
[ 1 ] 于彦. 混合物分离的节能新技术概述[ J ]. 安徽化工,1999 (4) : 7 - 9.
[ 2 ] 高以,叶凌碧. 膜分离技术基础[M ]. 北京:科学出版社, 1989: 2 - 4.
[ 3 ] 袁惠新,冯斌,陆振曦. 混合物分离技术的选择[ J ].化工装备技术, 2009 (3) : 7 - 13.
[ 4 ] 武昊宇. 多组分热偶精馏的节能设计与优化[ R&D ].青岛:青岛科技大学, 2007.
[ 5 ] 李群生. 精馏过程的节能降耗及新型高效分离技术的应用[ J ]. 化肥工业, 2008 (1) : 3 - 8.
[ 6 ] 曹正芳. 干燥过程的节能途径[ J ]. 节能技术, 2009(1) : 21 - 22.
[ 7 ] 罗宁,廖洁明. 技改出硕果降耗出效益[ J ]. 广东节能, 1995 (4) : 36 - 37.
[ 8 ] 王汝武. 凝结水回收方式的选择[ J ]. 节能, 2008 (3) :41 - 42.
[ 9 ] 冯霄,李勤凌. 化工节能原理与技术[M ]. 北京:化学工业出版社, 1998: 67 -
80.
[ 10 ] 党洁修,涂敏端. 化工节能基础过程热力学分析[M ].成都:成都科技大学出版社, 1987: 318 - 320.
传质分离过程
传质分离过程 1.分离过程可以定义为借助于物理、化学、电学推动力实现从混合物中选择性的分离某 些成分的过程。 2.分离过程可分为机械分离和传质分离两大类。机械分离的对象是两相以上的混合物。 传质分离过程用于各种均相混合物的分离。特点是有能量传递现象发生。 3.传质分离过程分为平衡分离过程和速率分离过程。 4.相平衡的准则为各相的温度、压力相同,各组分的逸度也相等。 5.相平衡的表示方法有相图、相平衡常数、分离因子。 6.维里方程用来计算气相逸度系数。 7.闪蒸是连续单级蒸馏过程。 8.指定浓度的组分成为关键组分,其中易挥发的成为轻关键组分,难挥发的成为重关键 组分。 9.若溜出液中除了重关键组分外没有其他重组分,而釜液重除了轻关键组分外没有其他 轻组分,这种情况称为清晰分割。 10.多组分精馏与二组分精馏在浓度分布上的区别可以归纳为:在多组分精馏中,关键组 分的浓度分布有极大值;非关键组分通常是非分配的,即重组分通常仅出现在釜液中,轻组分仅出现在溜出液中;重、轻非关键组分分别在进料板下、上形成接近恒浓的区域;全部组分均存在于进料板上,但进料板浓度不等于进料浓度。塔内各组分的浓度分布曲线在进料板处是不连续的。 11.最小回流比是在无穷多塔板数的条件下达到关键组分预期分离所需要的回流比。 12.特殊精馏分为萃取精馏(加入的组分称为溶剂)、共沸精馏、加盐精馏。 13.气体吸收是气体混合物一种或多种溶质组分从气相转移到液相的过程。解吸为吸收的 逆过程,即溶质从液相中分离出来转移到气相的过程。 14.吸收过程按溶质数可以分为单组分吸收和多组分吸收;按溶质与液体之间的作用性质 可以分为物理吸收和化学吸收;按吸收温度状况可以分为等温吸收和非等温吸收。 15.吸收的推动力是气相中溶质的实际分压与溶液中溶质的平衡蒸气压力之差。 16.难溶组分即轻组分一般只在靠近塔顶的几级被吸收,而在其余级上变化很小。易溶组 分即重组分主要在塔底附近的若干级上被吸收,而关键组分才在全塔范围内被吸收。 17.吸收塔的操作压力、操作温度和液气比是影响吸收过程的主要参数。操作压力越大吸 收率越大,操作温度越低吸收率越大。液气比越大吸收率越大。 18.超临界流体萃取是一种以超临界流体作为萃取剂,从固体或液体中提取出待分离的高 沸点或热敏性物质的新型萃取技术。超临界流体是状态处于高于临界温度、压力条件下的流体,它具有低粘度、高密度、扩散系数大、超强的溶解能力等特性。与传统的溶液萃取的优势:超临界流体具有极强的溶解能力,能实现从固体中提取有效成分; 可通过温度、压力的调节改变超临界流体的溶解能力的大小,因而超临界流体萃取具有较好的选择性;超临界流体传质系数大,可大大缩短分离时间;萃取剂的分离回收容易。 19.二氧化碳是最理想的超临界流体。 20.超临界流体的典型萃取流程:等温法、等压法、吸附法。 21.反胶团萃取有效的解决了溶剂萃取过程中蛋白质不溶于有机溶剂和易变性、失活的问 题。 22.吸附是指流体与固体多孔物质接触时,流体中的一种或多种组分传递并附着在固体 内、外表面形成单分子层或多分子层的过程。
分离过程习题答案
第一章绪论 1.列出5种使用ESA和5种使用MSA的分离操作。 答:属于ESA分离操作的有精馏、萃取精馏、吸收蒸出、再沸蒸出、共沸精馏。 属于MSA分离操作的有萃取精馏、液-液萃取、液-液萃取(双溶剂)、吸收、 吸附。 2.比较使用ESA与MSA分离方法的优缺点。 答:当被分离组分间相对挥发度很小,必须采用具有大量塔板数的精馏塔才能分 离时,就要考虑采用萃取精馏(MSA),但萃取精馏需要加入大量萃取剂, 萃取剂的分离比较困难,需要消耗较多能量,因此,分离混合物优先选择能 量媒介(ESA)方法。 3.气体分离与渗透蒸发这两种膜分离过程有何区别? 答:气体分离与渗透蒸发式两种正在开发应用中的膜技术。气体分离更成熟些, 渗透蒸发是有相变的膜分离过程,利用混合液体中不同组分在膜中溶解与扩 散性能的差别而实现分离。 5.海水的渗透压由下式近似计算: π=RTC/M, 式中C为溶解盐的浓度,g/cm3;M为离子状态的各种溶剂的平均分子量。若从含盐0.035 g/cm3的海水中制取纯水,M=31.5,操作温度为298K。问反渗透膜两侧的最小压差应为多少kPa? 答:渗透压π=RTC/M=8.314×298×0.035/31.5=2.753kPa。 所以反渗透膜两侧的最小压差应为2.753kPa。 9. 假定有一绝热平衡闪蒸过程,所有变量表示在所附简图中。求: (1)总变更量数Nv; (2)有关变更量的独立方程数Nc; (3)设计变量数Ni; (4)固定和可调设计变量数Nx , Na; (5)对典型的绝热闪蒸过程,你 将推荐规定哪些变量? 思路1: 3股物流均视为单相物流, 总变量数Nv=3(C+2)=3c+6 独立方程数Nc F zi T F P F V , yi ,Tv , Pv L , x i , T L , P L 习题5附图
化工分离过程重点
1、相平衡:指混合物或溶液形成若干相,这些相保持着物理平衡而共存的状态,从热力学上看,整个物系的自由焓处于最小的状态;从动力学看,相间表观传递速率为零。 2、区域熔炼:是根据液体混合物在冷凝结晶过程中组分重新分布的原理,通过多次熔融和凝固,制备高纯度的金属、半导体材料和有机化合物的一种提纯方法。 3、独立变量数:一个量改变不会引起除因变量以外的其他量改变的量。 4、反渗透:是利用反渗透膜选择性地只透过溶剂(通常是水)的性质,对溶液施加压力克服溶液的渗透压,使溶剂从溶液中透过反渗透膜而分离出来的过程。 5、相对挥发度:溶液中的易挥发组分的挥发度与难挥发组分的挥发度之比。 6、理论板:是一个气、液两相皆充分混合而且传质与传热过程的阻力皆为零的理想化塔板。 7、清晰分割:若馏出液中除了重关键组分外没有其他的重组分,而釜液中除了轻关键组分外没有其他轻组分,这种情况为清晰分割。 8、全塔效率:完成给定任务所需要的的理论塔板数与实际塔板数之比。默弗里板效率:实际板上的浓度变化与平衡时应达到的浓度变化之比。 9、泡点:在一定压力下,混合液体开始沸腾,即开始有气泡产生时的温度。露点:在一定压力下,混合气体开始冷凝,即开始出现第一个液滴时的温度。10、设计变量:设计分离装置中需要确定的各个物理量的数值,如进料流率,浓度、压力、温度、热负荷、机械工的输入(或输出)量、传热面大小以及理论塔板数等。这些物理量都是互相关联、互相制约的,因此,设计者只能规定其中若干个变量的数值,这些变量称设计变量。 简答题: 1、分离操作的重要意义 答:分离操作一方面为化学反应提供符合质量要求的原料,清除对反应或者催化剂有害的杂质,减少副反应和提高收率;另一方面对反应产物起着分离提纯的作用,已得到合格的产品,并使未反应的反应物得以循环利用。此外,分离操作在环境保护和充分利用资源方面起着特别重要的作用。2、精馏塔的分离顺序答:确定分离顺序的经验法:1)按相对挥发度递减的顺序逐个从塔顶分离出各组分;2)最困难的分离应放在塔序的最后;3)应使各个塔的溜出液的摩尔数与釜液的摩尔数尽量接近;4)分离很高回收率的组分的塔应放在塔序的最后;5)进料中含量高的组分尽量提前分出。 3、精馏过程的不可逆答:精馏过程热力学不可逆性主要由以下原因引起:1、通过一定浓度梯度的动量传递;2、通过一定温度梯度的热量传递或不同温度物流的直接混合;3、通过一定温度梯度的质量传递或者不同化学位物流的直接混合。 4、填料塔的选择板式塔与填料塔的选择应从下述几方面考虑1)系统的物性:A当被处理的介质具有腐蚀性时,通常选用填料塔;B对于易发泡的物系,填料塔更适合;C对热敏性物质或真空下操作的物系宜采用填料塔;D进行高粘度物料的分离宜用填料塔;E 分离有明显吸热或放热效应的物系以采用板式塔为宜;2)塔的操作条件;3)塔的操作方式。 5、填料种类的选择:A填料的传质效率要高;B填料的通量要大,在同样的液体负荷条件下,填料的泛点气速要高;C具有同样的传质效能的填料层压降要低;D单位体积填料的表面积要大,传质的表面利用率要高;E填料应具有较大的操作弹性;F 填料的单位重量强度要高;G填料要便于塔的拆装、检修,并能重复利用。(简述)6.进料板位置的选择:答:从上往下计算时,如果 S j HK j LK R j HK j LK y y y y ? ? ? ? ? ? < ? ? ? ? ? ? + + + + 1 , 1 , 1 , 1 , ,式中下标R和S分别表示用精馏段和提馏段操作线计算的结果,则第j级不是进料级,继续做精馏段的逐级计算; 如果S j HK j LK R j HK j LK y y y y ? ? ? ? ? ? > ? ? ? ? ? ? + + + + 1 , 1 , 1 , 1 , ,则第j级是进料级。由精馏段操作线确定yi,j,再由平衡关系求出xi,j,而下一级的yi,j+1应由提馏段操作线计算; 当从下往上逐级计算时,进料位置的确定方法是: 如果S j HK j LK R j HK j LK x x x x ? ? ? ? ? ? < ? ? ? ? ? ? , , , , 和S j HK j LK R j HK j LK x x x x ? ? ? ? ? ? > ? ? ? ? ? ? + + + + 1 , 1 , 1 , 1 , 则第j级是适宜进料位置,xi,j+1应换成平恒精馏段操作线计算。第一章2、分离过程可以分为机械分离和传质分离两大类,传质分离又可分为平衡分离过程和速率分离过程。3、分离媒介可以是能量媒介(ESA)或物质媒介(MSA)。4、当分离组分间隔相对挥发度很小,必须采用具有大量塔板数的精馏塔才能分离时,就要考虑萃取精馏。5、如果由精馏塔顶引出的气体不能完全冷凝,可从塔顶加入吸收剂作为回流,这种单元操作叫做吸收蒸出(或精馏吸收)。6、能形成最低共沸物的系统,采用一般精馏是不合适的,常常采用共沸精馏。7、离子交换也是一种重要的单元操作,采用离子交换树脂,有选择性的除去某组分,而树脂本身能够再生。第二章1、相平衡热力学是建立在化学位概念基础上的,lewis提出了等价于化学位的物理量——逸度。3、Φi s为校正处于饱和蒸汽压下的蒸汽对理想气体的偏离,指数校正项也称普瓦廷因子,是校正压力偏离饱和蒸汽压的影响。4、若按照所设温度T和求得∑K i X i>1,标明K i值偏大,所设温度偏高。根据差值大小降低温度重算;若∑K i X i<1,则重设较高温度。 第三章 1、设计分离装置就是要求确定各个物理量的数值,如进料流率、浓度、压力、温度、热负荷、机械功的输入量、传热面大小、理论塔板数等。2、N v是描述系统的独立变量数,N c是约束关系数,设计变量数N i,则有N i=N v-N c。3、约束关系式包括:1)、能量平衡式;2)、物料平衡式;3)、相平衡关系式;4)、化学平衡关系式;5)、内在关系式。 4、设计变量数N i可进一步区分为固定设计变量数N x e和可调设计变量数N a e。 5、不同装置的变量数尽管不同,其中固定设计变量的确定原则是共同的,只与进料物流数和系统内压力等级数有关。 6、轻关键组分:关键组分中相易挥发的那个组分;重关键组分:不易挥发的关键组分。 7、多组分精馏与二组分精馏在浓度分布上的区别可归纳为:a、在多组分精馏中,关键组分的浓度分布有极大值;b、非关键组分通常是非分配的,因此重组分仅出现在釜液中,轻组分仅出现在流出液中;c、重、轻非关键组分分别在进料板上下形成几乎恒浓的区域;d、全部组分均存在于进料板上,但进料板浓度不等于进料浓度,塔内各组分的浓度分布曲线在进料板是不连续的。 8、由于分离作用主要取决于液汽比L/V,流量相当大的变化对液汽比的影响不大,而对分离效果影响也小。级间饿两流量越接近于相等,即操作越接近于全回流,则流量变化对分离的影响也越小。
传质分离课后习题
第一章 绪论 1. 列出5种使用ESA 和5种使用MSA 的分离操作。 答:属于ESA 分离操作的有精馏、萃取精馏、吸收蒸出、再沸蒸出、共沸精馏。 属于MSA 分离操作的有萃取精馏、液-液萃取、液-液萃取(双溶剂)、吸收、吸附。 2. 比较使用ESA 与MSA 分离方法的优缺点。 答:当被分离组分间相对挥发度很小,必须采用具有大量塔板数的精馏塔才能分离时,就要考虑采用萃取精馏(MSA ),但萃取精馏需要加入大量萃取剂,萃取剂的分离比较困难,需要消耗较多能量,因此,分离混合物优先选择能量媒介(ESA)方法。 3. 气体分离与渗透蒸发这两种膜分离过程有何区别? 答:气体分离与渗透蒸发式两种正在开发应用中的膜技术。气体分离更成熟些,渗透蒸发是有相变的膜分离过程,利用混合液体中不同组分在膜中溶解与扩散性能的差别而实现分离。 4. 海水的渗透压由下式近似计算:π=RTC/M ,式中C 为溶解盐的浓度,g/cm 3;M 为离子状态的各种溶剂的平均分子量。若从含盐0.035 g/cm 3的海水中制取纯水,M=31.5,操作温度为298K 。问反渗透膜两侧的最小压差应为多少kPa? 答:渗透压π=RTC/M =8.314×298×0.035/31.5=2.753kPa 。 所以反渗透膜两侧的最小压差应为2.753kPa 。 5. 假定有一绝热平衡闪蒸过程,所有变量表示在所附简图中。求: (1) 总变更量数Nv; (2) 有关变更量的独立方程数Nc ; (3) 设计变量数Ni; (4) 固定和可调设计变量数Nx , Na ; (5) 对典型的绝热闪蒸过程,你 将推荐规定哪些变量? 思路1: 3股物流均视为单相物流, 总变量数Nv=3(C+2)=3c+6 独立方程数Nc 物料衡算式 C 个 热量衡算式1个 ;相平衡组成关 系式C 个;1个平衡温度等式;1个平衡压力等式 共2C+3个;故设计变量 F zi T F P F V , yi ,Tv , Pv L , x i , T L , P L 习题5附图
《化工分离工程》试卷及答案教学内容
《化工分离工程》试 卷及答案
收集于网络,如有侵权请联系管理员删除 一、填空(每空2分,共20分) 1. 如果设计中给定数值的物理量的数目等于 设计变量 ,设计才有结果。 2. 在最小回流比条件下,若只有重组分是非分配组分,轻组分为分配组分,存在着两个恒浓 区,出现在 精镏段和进料板 位置。 3. 在萃取精镏中,当原溶液非理想性不大时,加入溶剂后,溶剂与组分1形成具有较强 正 偏差的非理想溶液,与组分2形成 负偏差或理想 溶液 ,可提高组分1对2的相对挥发度。 4. 化学吸收中用增强因子表示化学反应对传质速率的增强程度,增强因子E 的定义是 化学吸收的液相分传质系数(k L )/无化学吸收的液相分传质系数(k 0L ) 。 5. 对普通的N 级逆流装置进行变量分析,若组分数为C 个,建立的MESH 方程在全塔有 NC+NC+2N+N=N(2C+3) 个。 6. 热力学效率定义为=η ; 实际的分离过程是不可逆的,所以热力学效率 必定 于1。 7. 反渗透是利用反渗透膜选择性的只透过 溶剂 的性质,对溶液施加压力,克服 溶剂的渗透 压 ,是一种用来浓缩溶液的膜分离过程。 二、推导(20分) 1. 由物料衡算,相平衡关系式推导图1单级分离基本关系式。 1(1) 0(1) 1c i i i i z K K ψ=-=-+∑ 式中: K i ——相平衡常数; ψ ——气相分率(气体量/进料量)。 2. 精馏塔第j 级进出物料如图1,建立MESH 方程。
三、简答(每题5分,共25分) 1.什么叫相平衡?相平衡常数的定义是什么? 由混合物或溶液形成若干相,这些相保持物理平衡而共存状态。热力学上看物系的自由焓最小;动力学上看相间表观传递速率为零。 K i=y i/x i。 2.关键组分的定义是什么;在精馏操作中,一般关键组分与非关键组分在顶、釜的分配 情况如何? 由设计者指定浓度或提出回收率的组分。 LK绝大多数在塔顶出现,在釜中量严格控制; HK绝大多数在塔釜出现,在顶中量严格控制; LNK全部或接近全部在塔顶出现; HNK全部或接近全部在塔釜出现。 3.在吸收过程中,塔中每级汽、液流量为什么不能视为恒摩尔流? 吸收为单相传质过程,吸收剂吸收了气体中的溶质而流量在下降过程中不断增加,气体的流量相应的减少,因此气液相流量在塔内都不能视为恒定。 4.在精馏塔中设中间换热器为什么会提高热力学效率? 在中间再沸器所加入的热量其温度低于塔底加入热量的温度,在中间冷凝器所引出的热量其温度高于塔顶引出热量的温度,相对于无中间换热器的精馏塔传热温差小,热力学效率高。 5.反应精馏的主要优点有那些? (1)产物一旦生成立即移出反应区;(2)反应区反应物浓度高,生产能力大;(3)反应热可由精馏过程利用;(4)节省设备投资费用;(5)对于难分离物系通过反应分离成较纯产品。 四、计算(1、2题10分,3题15分,共35分) 1. 将含苯0.6(mol分数)的苯(1)—甲苯(2)混合物在101.3kPa下绝热闪蒸,若闪蒸温度为94℃,用计算结果说明该温度能否满足闪蒸要求? 已知:94℃时P10=152.56kPa P20=61.59kPa 2. 已知甲醇(1)和醋酸甲酯(2)在常压、54℃下形成共沸物,共沸组成X2=0.65(mol分率), 在此条件下:kPa P kPa p98 . 65 , 24 . 9002 1 = =求该系统的活度系数。 3. 气体混合物含乙烷0.50、丙烷0.4、丁烷0.1(均为摩尔分数),用不挥发的烃类进行吸收,已知吸收后丙烷的吸收率为81%,取丙烷在全塔的平均吸收因子A=1.26,求所需理论板数;若其它条件不变,提高平均液汽比到原来的2倍,此时丙烷的吸收率可达到多少。 收集于网络,如有侵权请联系管理员删除
分离工程试卷及答案
分离工程 一、单项选择题(共27空,每空2分,共54分) 1. 按所依据的物理化学原理,传质分离过程可以分为________________分离过程和________________ 分离过程,常见的平衡分离过程有__________________、__________________、_________________。 2. 表征表征能量被利用的程度有两类效率:________________和_________________。要降低分离过程的能耗,提高其___________________效率,就应该采取措施减小过程的有效能损失。有效能损失是由_________________引起的。 3. 泡露点计算是分离过程设计中最基本的汽液平衡计算,按规定哪些变量和计算哪些变量可分为如下四种类型:________________________、________________________、________________________和________________________。 4. 影响气液传质设备处理能力的主要因素有______________、______________、_______________和________________。 5. 多组分多级分离过程严格计算中围绕非平衡级所建立的MERQ 方程分别是指________________________、________________________、________________________和________________________。 6. 常见的精馏过程节能途径有________________________________________、________________________________________、 ________________________________________。 7. 理想气体和理想溶液混合物传热速率________________最小分离功,非理想溶液混和物传热速率________________最小分离功,最小分离功的大小标志着_______________。 二、不定项选择题(共15小题,每题2分,共计30分) 1. 当把一个气相冷凝时,开始产生液滴的点叫作() A.露点 B.临界点 C.泡点 D.熔点 . 2. 闪蒸是单级蒸馏过程,所能达到的分离程度() A.很高 B.较低 C.只是冷凝过程,无分离作用 D.只是气化过程,无分离作用 3. 设计变量数就是() A.设计时所涉及的变量数 B.约束数 C.独立变量数与约束数的和 D.独立变量数与约束数的差 4. 在多组分混合物的吸收过程中,不同组分和不同塔段的吸收程度是不同的。()一般主要在靠近塔顶的几级被吸收,在其余级变化很小。 A.轻关键组分 B.重关键组分 C.轻非关键组分 D.重非关键组分 5. 多组分精馏与多组分吸收过程均不能对所有组分规定分离要求,而只能对分离操作中起关键作用的组分即关键组分规定分离要求,其中多组分精馏过程最多只能有( )个关键组分,多组分吸收过程最多只能有( )个关键组分。() A.1 B.2 C.3 D.4 6. 下列各单元中,( )单元的可调设计变量数为 0,( )单元的可调设计变量数为 1。() A.混合器 B.分相器 C.分配器 D.再沸器 7. 对一个恒沸精馏过程,从塔内分出的最低温度的恒沸物() A.一定是做为塔底产品得到 B.一定是为塔顶产品得到 C.可能是塔项产品,也可能是塔底产品 D.视具体情况而变 8. 如果二元物系有最低压力恒沸物存在,则此二元物系所形成的溶液一定是() A.正偏差溶液 B.理想溶液 C.负偏差溶液 D.不一定 9. 下列哪一个是机械分离过程() A.蒸馏 B.吸收 C.膜分离 D.离心分离 10. 气液两相处于平衡时()
分离课后习题及答案
第一章绪论1.分离技术的三种分类方法各有什么特点? 答:(1)按被分离物质的性质分类分为物理分离法、化学分离法、物理化学分离法。 (2)按分离过程的本质分类分为平衡分离过程、速度差分离过程、反应分离过程。 (3)场流分类法 2.分离富集的目的? 答:①定量分析的试样通常是复杂物质,试样中其他组分的存在常常影响某些组分的定量测定,干扰严重时甚至使分析工作无法进行。这时必须根据试样的具体情况,采用适当的分离方法,把干扰组分分离除去,然后才能进行定量测定。②如果要进行试样的全分析,往往需要把各种组分适当的分离,而后分别加以鉴定或测定。③而对于试样中的某些痕量组分,进行分离的同时往往也就进行了必要的浓缩和富集,于是就便于测定。因此物质的化学分离和测定具有同样重要意义。 3.什么是直接分离和间接分离? 答:直接分离是将待测组分从复杂的干扰组分分离出来;间接分离是将干扰组分转入新相,而将待测组分留在原水相中。 4.阐述浓缩、富集和纯化三个概念的差异与联系? 答:富集:通过分离,使目标组分在某空间区域的浓度增大。浓缩:将溶剂部分分离,使溶质浓度 提高的过程。纯化:通过分离使某种物质的纯度提高的过程。 根据目标组分在原始溶液中的相对含量(摩尔分数)的不同进行区分:
(方法 被分离组分的摩尔分数)富集 <0.1;浓缩 0.1-0.9;纯化 >0.9。 5.回收因子、分离因子和富集倍数有什么区别和联系? 答:(1)被分离物质在分离过程中损失量的多少,某组分的回收程度,用回收率来表示。 待测组分A 的回收率,用RA 表示,QA °---为富集前待测物的量;QA---富集后待测物的量。%100?=οA A A Q Q R (2)分离因子:两组分的分离程度。用SA , B 表示。B A B A B A B ,//R R Q Q Q Q S A =??= A —待测组分; B —干扰组分。如果待测组分A 符合定量要求,即可认为QA ≈ Q oA ,SA,B ≈ Q oB/QB = 1/RB ,常量组分测定:SA,B ≈103;分离因子越大,分离效果越好。 (3)富集倍数:目标组分和基体组分的回收率之比,用F 表示,οο M M T T M T Q Q Q Q R R F //== RT 为组分的回收率;RM 为基体的回收率; QT °为富集前待测物的量; QT 为富集后待测物的量;QM °为富集前基体的量;QM 为富集后基体的量。 第二章 分离过程中的热力学 2.气体分子吸附在固体吸附剂表面时,某吸附等温线可以由朗格缪尔吸附方程得到。试分析吸附物质的吸附平衡常数K 与该气体物质在气相的分压p 需满足什么条件才能使朗格缪尔吸附等温线近似为直线。 答:溶质吸附量q 与溶质气体分压p 的关系可以用朗格缪尔吸附方程表示:p K p K q q A A +=1max ,式中qmax 为溶质在固相表面以单分子层覆盖的最大容量;KA 为溶质的吸附平衡常数。在低压时,p K q q p K A A max 1=,《。
化工分离工程考试答案
2013化工分离过程期中考试试题答案 一、填空题(每空1分,共20分) 1. 传质分离过程分为(平衡分离过程)和(速率分离过程)两大类。 2. 分离作用是由于加入(分离剂)而引起的,因为分离过程是(混合过程)的逆过程。 3. 汽液相平衡是处理(传质分离)过程的基础,相平衡的条件是(各相温度压力相等,各组分在每一相中的化学位相等)。 4. 当混合物在一定的温度、压力下,进料组成z i 和相平衡常数K i 满足 ( 1,1>>∑∑i i i i K z z K )条件即处于两相区,可通过(物料平衡和相平衡)计算求出其平衡汽液相组成。 5. 精馏塔计算中每块板由于(组成)改变而引起的温度变化,可用(泡露点方程)确定。 6. 多组分精馏根据指定设计变量不同可分为(设计)型计算和(操作)型计算。 7. 最低恒沸物,压力降低使恒沸组成中汽化潜热(小)的组分增加。 8. 萃取精馏中塔顶产品不合格时,经常采取(增加萃取剂用量)或(减小进料量)的措 施使产品达到分离要求。 9. 吸收有(1个)关键组分,这是因为(单向传质)的缘故。 10.吸收剂的再生常采用的是(用蒸汽或惰性气体的蒸出塔)、(用再沸器的蒸出塔)和(用 蒸馏塔)。 二、单项选择题(每小题1分,共10分) 1. 吸收属于(A ) A.平衡分离;B.速率分离;C.机械分离;D.膜分离。 2. 计算溶液泡点时,若∑=>-C i i i X K 101,则说明(C ) A. 温度偏低; B. 正好泡点; C. 温度偏高。 3. 如果体系的汽相为理想气体,液相为非理想溶液;则相平衡常数可以简化表示为( D ) A. L i i V i K φφ= B. s i i P K P = C. $$L i i V i K φφ= D. s i i i P K P γ= 4. 汽液相平衡K 值越大,说明该组分越(A ) A.易挥发; B.难挥发; C.沸点高; D.蒸汽压小。 5. 如果塔顶采用全凝器,计算塔顶第一级的温度可以利用方程( B ) A.泡点方程; B.露点方程; C. 闪蒸方程; D.相平衡方程。 6. 计算在一定温度下与已知液相组成成平衡的汽相组成和压力的问题是计算( B ) A.泡点温度; B.泡点压力; C.等温闪蒸; D.露点压力。 7. 精馏中用HNK 表示( C ) A. 轻关键组分; B. 重关键组分; C. 重非关键组分; D. 轻非关键组分。 8. 以下描述中,不属于萃取精馏中溶剂的作用的是( D ) A.稀释作用; B.对组分相互作用不同; C.与某组分形成正偏差溶液; D.与某组分形成共沸物。
化工分离过程过程性考核试卷 - 答案 (1)
化工分离过程过程性考核试卷(二) 一.填空题(每空1分,本大题共18分) 1.按照蒸馏方式划分,蒸馏可以分为简单蒸馏、平衡蒸馏、精馏和 特殊精馏。 2.相对挥发度等于1,说明物系不能用普通的蒸馏方法加以分离。 3.蒸馏中常用的相图为常压下的t-x-y相图和x-y相图。 4.连续精馏塔中,加料板以上的塔段称为精馏段,加料板以下的塔段称为提馏段。 5.精馏塔常见的进料热状况包括过冷液体、饱和液体、气液混合物、饱和蒸气 和过热蒸气。 6.间歇精馏的两种基本操作方式为恒回流比和恒回馏液组成。 7.精馏段的操作线方程为y=+,则回流比为3 ,塔顶馏出液组成为。 二、单项选择题:(每空1分,本大题共8分) 在每小题列出的四个备选项中选出一个正确答案的代号填写在题后的括号内。 8.操作中的精馏塔,若增加回流比,而其他操作条件不变,则下列结论正确的是(A ) 增加,x W降低增加,x W增加 降低,x W降低降低,x W增加 9.操作中的精馏塔,若保持F、x F、q、D不变,增加R,则提馏段下降液体量L (A ) A.增加 B.减少 C.不变 D.不确定 10.操作中的精馏塔,若将进料由饱和液体改为过冷液体,而其他操作条件不变,则下列结论正确的是(A ) 增加,x W降低增加,x W增加
降低,x W 降低 降低,x W 增加 11.在蒸馏所用的温度-组成相图中,位于泡点线和露点线之间的点所代表的状态为( C )。 A .饱和液体 B .饱和蒸气 C .气液两相混合物 D .过冷液体 12.精馏塔灵敏板的位置( C )。 A .一般靠近塔顶 B .一般靠近塔底 C . 一般靠近进料板 D .无确定的规律 13.饱和蒸气进料,进料热状况参数( D ) ﹤0 ﹤q ﹤1 C . q =1 D . q =0 14.操作中的精馏塔,若x F 减小,则( C ) 增加,x W 降低 增加,x W 增加 降低,x W 降低 降低,x W 增加 三、判断题:判断下列各题是否正确,正确的在题后括号内划√,错误的划×。(每小 题1分,本大题共8分) 15.精馏塔设计中,最小回流比对应的理论塔板数最少。( × ) 16.简单蒸馏和平衡蒸馏均为单级蒸馏操作。( √ ) 17.精馏塔设计中,全回流时所对应的理论塔板数最少。( √ ) 18.若板式塔内各塔板单板效率相同,则总板效率在数值上就等于单板效率。( × ) 19.对于高纯度分离时,一般可用测量塔顶温度来控制塔顶组成。( × ) 20.一般说来,同一层塔板的气相单板效率和液相单板效率在数值上并不相等。( √ ) 21.相对挥发度越大,说明混合液越易用蒸馏方法加以分离。( √ ) 22.理论板当量高度是指相当于一层理论板分离作用的填料层高度。( √ ) 四、名词解释题:(每小题3分,本大题共15分) 23.共沸精馏 若在两组分共沸液中加入第三组分(称为夹带剂),该组分能与原料液中的一个或两个组分形成新的共沸液,从而使原料液能用普通精馏方法予以分离,这种精馏操作称为共沸精馏。 24.萃取精馏 萃取精馏是向原料液中加入第三组分(称为萃取剂或溶剂),以改变原有组分间的相对挥发度而得以分离,萃取剂的沸点叫原料液中各组分的]沸点高很多,且不与组分形成恒沸液。 25. 恒摩尔流假定
节能新技术在化工分离工程中的应用
节能新技术在化工分离 工程中的应用 Document serial number【UU89WT-UU98YT-UU8CB-UUUT-UUT108】
论文题目节能新技术在化工分离工程中的应用
摘要 近年来,随着市场经济的快速发展,化工行业也迅速崛起。但是,由于化工行业巨大的污染性,而使其成为我国环境污染的源头之一,在当前追求低碳经济和绿色经济的大环境下,化工行业的发展受到了一定的限制。 关键词 化工分离节能新技术研究进展 引言 当前,随着社会的发展和进步,越来越多的人认识到节约资源、保护环境的重要性。国家的“十二五”规划纲要指出:“十二五”期间要大力开发和积极推广低碳技术,节能减排工作不断深入,“十二五”末高耗能产品单耗达到国际先进水平,能耗在“十一五”末的基础上再下降10%,主要产品实现清洁生产,主要污染物排放总量在“十一五”末的基础上再下降10%。进一步提高高耗能、高排放和产能过剩行业准入门槛。这就意味着当前高污染、高耗能的化工行业的节能减排进程必须加快。 正文 我国化工行业主要是从事化学工业生产和开发的能源工业以及基础原材料工业。化工行业是我国国民经济体系中的一个重要部门,它对经济发展、国防事业以及人们的社会生活都发挥着极其重要的作用。改革开放以来,我国的石油化工产业取得了巨大的成就。但是由于化学工业本身的缺点和局限,导致在生产过程中排放的污染物种类多、数量大、
毒性高,严重影响生态环境和人类的身体健康。当前,由于在节能减排技术开发上的滞后,导致我国化工行业节能减排和环保技术水平落后,也使得化工行业生产过程中的高耗能、高污染现状持续得不到缓解。从而导致我国化工行业的能耗量始终排在全国工业领域的前列。而化工行业的废水排放量甚至长期高居全国工业领域的第1位。 化工分离过程是将混合物分离成各组分组成各不相同的两种(或几种)产品的操作。一套标准的化工生产装置,应包括一个反应器和具有提纯原料、中间产物与产品以及后处理的多个分离设备构成。首先,分离过程必须能够去除原料杂质,为化学反应提供纯度达到工业生产要求的原料,减少杂质带来的影响(副反应增加,催化剂中毒等);再者,分离过程能够对反应产物进行处理,获得所需产品的同时分离出未完全反应的反应物,循环利用;此外,分离过程还需要在工业废水处理与环境保护方面发挥作用,减少工业三废的排放。因此,我们看到化工分离过程在化学工业生产中占据着非常重要的地位。 膜分离技术是利用特定膜的渗透作用,在外界能量或化学位差的推动下。对气相或液相混合物进行分离、分级、提纯和富集,膜分离过程大多尤相变,常温操作,高效、节能、工艺简便、污染小。20世纪80年代以来我国膜技术跨入应用阶段,同时也是新膜过程的开发阶段。在这一时期,膜技术在食品加工、海水淡化、纯水、超纯水制备、医药、生物、环保等领域得到了较大规模的开发和应用。 离子膜烧碱不但能生产出高纯度烧碱和氢气,而且节能效果显着,比隔膜法节约能耗约30%。因此,离子膜法将逐步取代隔膜法生产烧
化工分离过程试题库精选文档
化工分离过程试题库精 选文档 TTMS system office room 【TTMS16H-TTMS2A-TTMS8Q8-
化工分离过程试题库(复习重点) 第一部分填空题 1、分离作用是由于加入(分离剂)而引起的,因为分离过程是(混合过程)的逆过程。 2、固有分离因子是根据(气液相平衡)来计算的。它与实际分离因子的差别用(板效率)来表示。 3、汽液相平衡是处理(气液传质分离)过程的基础。相平衡的条件是(所有相中的温度压力相等、每一组分的逸度也相等)。 4、精馏塔计算中每块板由于(组成)改变而引起的温度变化,可用(泡露点方程)确定。 5、多组分精馏根据指定设计变量不同可分为(设计)型计算和(操作)型计算。 6、在塔顶和塔釜同时出现的组分为(分配组分)。 7、吸收有( 1个)关键组分,这是因为(单向传质)的缘故。 8、对多组分吸收,当吸收气体中关键组分为重组分时,可采用(吸收蒸出塔)的流程。 9、对宽沸程的精馏过程,其各板的温度变化由(进料热焓)决定,故可由(热量衡算)计算各板的温度。 10、对窄沸程的精馏过程,其各板的温度变化由(组成的改变)决定,故可由(相平衡方程)计算各板的温度。 11、为表示塔传质效率的大小,可用(级效率)表示。
12、对多组分物系的分离,应将(分离要求高)或(最困难)的组分最后分离。 13、泡沫分离技术是根据(表面吸附)原理来实现的,而膜分离是根据(膜的选择渗透作用)原理来实现的。 14、新型的节能分离过程有(膜分离)、(吸附分离)。 15、传质分离过程分为(平衡分离过程)和(速率分离过程)两大类。 16、分离剂可以是(能量)和(物质)。 17、Lewis 提出了等价于化学位的物理量(逸度)。 18、设计变量与独立量之间的关系可用下式来表示( Ni=N v-Nc ) 19、设计变量分为(固定设计变量)与(可调设计变量)。 20、温度越高对吸收越(不利) 21、萃取精馏塔在萃取剂加入口以上需设(萃取剂回收段)。 22、用于吸收过程的相平衡关系可表示为(L = AV)。 23、精馏有(2)个关键组分,这是由于(双向传质)的缘故。 24、精馏过程的不可逆性表现在三个方面,即(通过一定压力梯度的动量传递),(通过一定温度梯度的热量传递或不同温度物流的直接混合)和(通过一定浓度梯度的质量传递或者不同化学位物流的直接混合)。 25、通过精馏多级平衡过程的计算,可以决定完成一定分离任务所需的(理论板数),为表示塔实际传质效率的大小,则用(级效率)加以考虑。 26、超临界流体具有类似液体的(溶解能力)和类似气体的(扩散能力)。 27、常用吸附剂有(硅胶),(活性氧化铝),(活性炭)。 28、恒沸剂与组分形成最低温度的恒沸物时,恒沸剂从塔(顶)出来。
传质分离过程ASPEN模拟全过程
传质分离过程ASPEN模拟全过程 姓名:王超班级:化工1301 学号:201309010114 【题目2-8】组成为60%苯,25%甲苯和15%对二甲苯(均为摩尔分数)的液体混合物100kmol,在101.3kPa和100℃下闪蒸。试计算液体和气体产物的数量和组成。假设该物系为理想溶液。用安托尼方程计算蒸汽压。 启动Aspen Plus选择模块General with Metric Units,文件保存为Example2.8。 建立如图所示的流程图,其中FLASH选用模块库中的Separators丨Flash丨V-DRUM1模块。
点击N→,出现FlowsheetComp;ete对话框,点击确定,进入Setup 丨Specifications丨Global页面,在名称(Title)框中输入2-8。
在左窗口选择Units-Sets,点击New,出现Create new ID对话框,选择默认的US-1,点击OK。 然后进行如图的单位设置。
在左窗口选择Report Options,进入Steam页面,勾选Fraction basis 栏目下的Mole。 点击N→,进入Components丨Specifications丨Selection页面,输入组分甲苯(C6H6)、甲苯(C7H8)、对二甲苯(C8H10-3)。
点击N→,进入Properties丨Specifications丨Global页面,选择物性方法PENG-ROB。然后点击N→,在点击OK,如图所示 进入Streams丨FEED丨Input丨Specifications页面,输入进料(FEED)温度25℃,压力101.3kPa,流量100kmol,以及苯、甲苯、对二甲苯的摩尔分数分别为0.6、0.25、0.15。
化工分离过程[1]
模拟考试试题 (1)卷 一、填空(每空2分,共20分) 1、气液传质分离过程的热力学基础是( )。如果所有相中的温度压力相等、每一组分的逸度也相等,则此时达到了 。 2、精馏塔计算中每块板温度变化是由于 改变,每块板上的温度利用 确定。 3、多组分精馏根据指定设计变量不同可分为 型计算和 型计算。 4、只在塔顶或塔釜出现的组分为 。 5、 超滤是以 为推动力,按( )选择分离溶液中所含的微粒和大分子的膜分离操作。 6、吸收操作在传质过程上的主要特征是 二、推导分析(20分) 1. 由物料衡算,相平衡关系式推导图1单级分离基本关系式。 1(1) 0(1)1c i i i i z K K ψ =-=-+∑ 式中: K i ——相平衡常数;ψ——气相分率(气体量/进料量)。 2. 一烃类混合物送入精馏装置进行分离,进料组成和相对挥发度a 值如下,现有A 、B 两种方案可供选择(见下图),你认为哪种方案合理?为什么? 异丁烷 正丁烷 戊烷 异丁烷 正丁烷 戊烷 摩尔% 25 30 45 相对挥发度:1.24 1.00 0.34
三、简答(每题5分,共25分) 1. 在萃取精馏中,萃取剂在何处加入?为何? 2. 从热力学角度和工艺角度简述萃取精馏中萃取剂选择原则? 3. 在吸收过程中,塔中每级汽、液流量为什么不能视为恒摩尔流? 4. 试分析吸附质被吸附剂吸附一脱附的机理? 5. 精馏过程全回流操作的特点? 四、计算(1、2题10分,3题15分,共35分) 1. 将含苯0.6(mol 分数)的苯(1)—甲苯(2)混合物在101.3kPa 下绝热闪蒸,若闪蒸温度为94℃,用计算结果说明该温度能否满足闪蒸要求? 已知:94℃时 P 10=15 2.56kPa P 20=61.59kPa 2. 已知某乙烷塔,塔操作压力为28.8标准大气压,塔顶采用全凝器,并经分析得塔顶产品组成为: 组 分 甲烷. 乙烷. 丙烷. 异丁烷. 总合 组成x iD 1.48 88 10.16 0.36 100%(摩尔) 相平衡常数: 5.4 1.2 0.37 0.18 (20℃) 5.6 1.24 0.38 0.19 (22℃) 试计算塔顶温度。 3. 气体混合物含乙烷0.50、丙烷0.4、丁烷0.1(均为摩尔分数),用不挥发的烃类进行吸收,已知吸收后丙烷的吸收率为81%,取丙烷在全塔的平均吸收因子A=1.26,求所需理论板数;若其它条件不变,提高平均液汽比到原来的2倍,此时丙烷的吸收率可达到多少。 (注:1lg 1lg ---= A A N ? ? )
化工分离过程课后答案刘家祺
分离工程习题 第一章 1. 列出5种使用ESA 和5种使用MSA 的分离操作。 答:属于ESA 分离操作的有精馏、萃取精馏、吸收蒸出、再沸蒸出、共沸精馏。 属于MSA 分离操作的有萃取精馏、液-液萃取、液-液萃取(双溶剂)、吸收、吸附。 5.海水的渗透压由下式近似计算:π=RTC/M,式中C 为溶解盐的浓度,g/cm 3;M 为离子状态的各种溶剂的平均分子量。若从含盐 g/cm 3的海水中制取纯水,M=,操作温度为298K 。问反渗透膜两侧的最小压差应为多少kPa 答:渗透压π=RTC/M=×298×=。 所以反渗透膜两侧的最小压差应为。 9.假定有一绝热平衡闪蒸过程,所有变量表示在所附简图中。求: (1) 总变更量数Nv; (2) 有关变更量的独立方程数Nc ; (3) 设计变量数Ni; (4) 固定和可调设计变量数Nx , Na ; (5) 对典型的绝热闪蒸过程,你 将推荐 规定哪些变量 思路1: 3股物流均视为单相物流, 总变量数Nv=3(C+2)=3c+6 独立方程数Nc 物料衡算式 C 个 热量衡算式1个 相平衡组成关系式C 个 1个平衡温度等式 1个平衡压力等式 共2C+3个 故设计变量Ni =Nv-Ni=3C+6-(2C+3)=C+3 固定设计变量Nx =C+2,加上节流后的压力,共C+3个 可调设计变量Na =0 解: (1) Nv = 3 ( c+2 ) (2) Nc 物 c F z i T F P F V , y i ,T v , P v L , x i , T L , P L 习题5附图
能 1 相 c 内在(P ,T) 2 Nc = 2c+3 (3) Ni = Nv – Nc = c+3 (4) Nxu = ( c+2 )+1 = c+3 (5) Nau = c+3 – ( c+3 ) = 0 思路2: 输出的两股物流看成是相平衡物流,所以总变量数Nv=2(C+2) 独立方程数Nc :物料衡算式 C 个 ,热量衡算式1个 ,共 C+1个 设计变量数 Ni=Nv-Ni=2C+4-(C+1)=C+3 固定设计变量Nx:有 C+2个加上节流后的压力共C+3个 可调设计变量Na :有0 11.满足下列要求而设计再沸汽提塔见附图,求: (1) 设计变更量数是多少 (2) 如果有,请指出哪些附加变 量需 要规定 解: N x u 进料 c+2 压力 9 c+11=7+11=18 N a u 串级单元 1 传热 1 合计 2 N V U = N x u +N a u = 20 附加变量:总理论板数。 16.采用单个精馏塔分离一个三组分混合物为三个产品(见附图),试问图中所注设计变量能否使问题有唯一解如果不,你认为还应规定哪个(些)设计变量 解: N X U 进料 c+2 压力 40+1+1 c+44 = 47 N a u 3+1+1+2 = 7 N v u = 54 设计变量:回流比,馏出液流率。 第二章 进料,顶产物 底产物 习题6附图