硅片生产工艺技术流程1

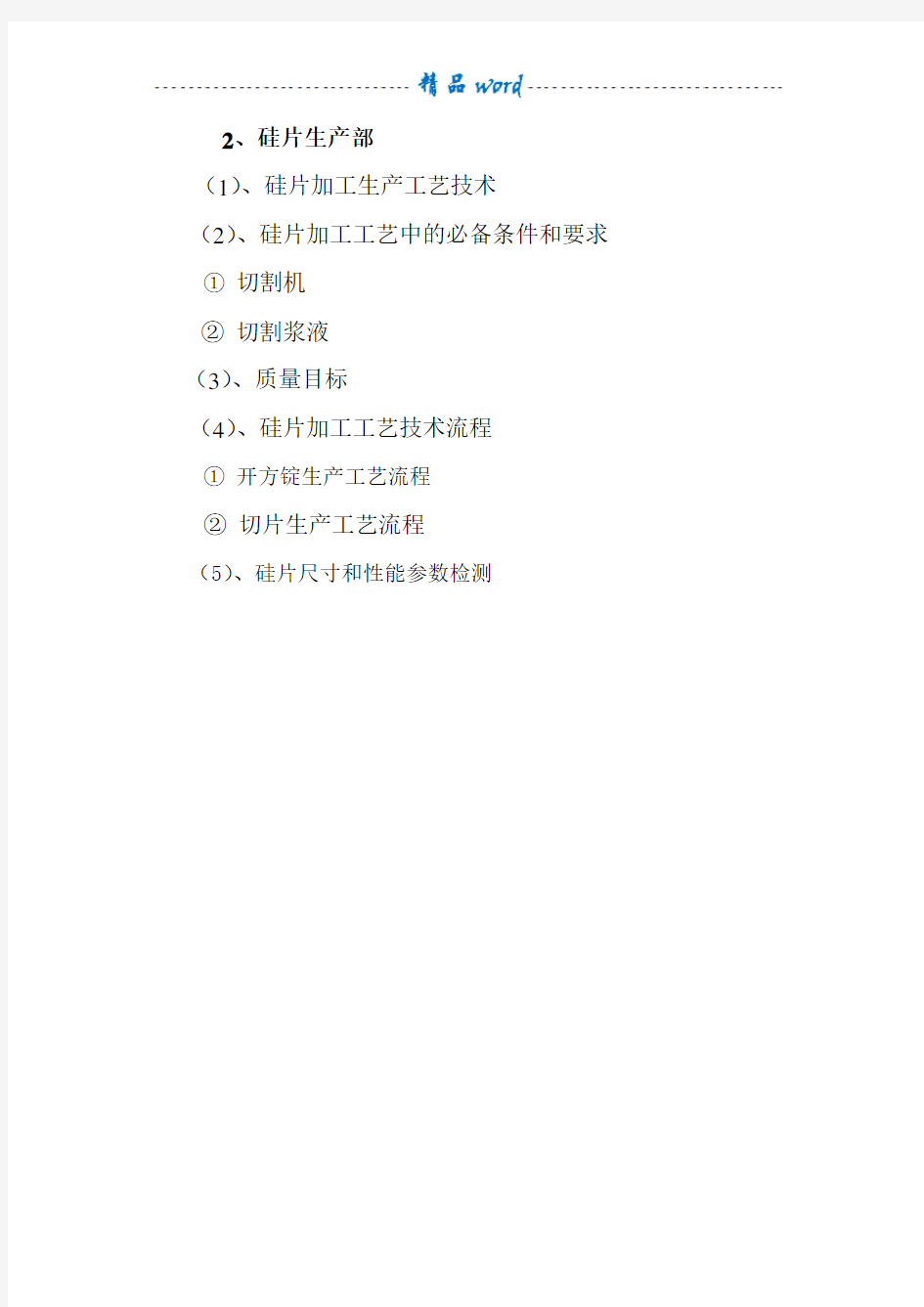
顺大半导体发展有限公司太阳能用
硅单晶片生产技术
目录
一、硅片生产工艺中使用的主要原辅材料
1、拉制单晶用的原辅材料,设备和部件:
2、供硅片生产用的原辅材料,设备和部件:
二、硅片生产工艺技术
1、硅单晶生产部
(1)、腐蚀清洗工序生产工艺技术
对处理后原材料质量要求
(2)、腐蚀清洗生产工艺流程
①多晶硅块料,复拉料和头,尾料处理工艺流程
②边皮料酸碱清洗处理工艺流程
③埚底料酸清洗处理工艺流程
④废片的清洗处理工艺流程
(3)、硅单晶生长工艺技术
(4)、单晶生长中的必备条件和要求
①单晶炉
②配料与掺杂
(5),单晶生长工艺参数选择
(6)、质量目标:
(7)、硅单晶生长工艺流程
2、硅片生产部
(1)、硅片加工生产工艺技术
(2)、硅片加工工艺中的必备条件和要求
①切割机
②切割浆液
(3)、质量目标
(4)、硅片加工工艺技术流程
①开方锭生产工艺流程
②切片生产工艺流程
(5)、硅片尺寸和性能参数检测
前言
江苏顺大半导体发展有限公司座落于美丽的高邮湖畔。公司始创生产太阳能电池用各种尺寸的单晶和多晶硅片。拥有国内先进的拉制单晶设备104台,全自动单晶炉112台。年产量可达到××××吨。拥有大型先进的线切割设备×××台。并且和无锡尚德形成了合作联盟(伙伴),每×可以向尚德提供×××硅单晶片。同时河北晶于2004年,占地面积××××。公司现在有×××名员工,从事澳、南京等光伏组件公司都和顺大形成了长年的合作关系。为了公司的进一步发展,扩大产业链,解决硅单晶的上下游产品的供需关系,2006年在扬州投资多晶硅项目,投资规模达到××亿。工程分两期建设,总规模年产多晶硅6000吨。2008年底首期工程已经正式投入批量生产,年产多晶硅×××吨。
太阳能用硅片生产工艺十分复杂,要通过几十道工序才能完成,只有发挥团队精神才能保证硅片的最终质量。编写该篇壮大资料的目的:首先让大家了解整个硅片生产过程,更重要的是让各生产工序中的每一位操作人员明确自己的职责,更自觉地按操作规程和规范做好本职工作,为顺大半导体发展有限公司的发展,尽自己的一份力量。
一、硅片生产工艺中使用的主要原辅材料和设备
1 、拉制单晶硅生产部
(1)、供单晶生产用的原辅材料质量要求和验收:
1)原料:多晶硅,边皮料,锅底料,复拉料(包括头尾料)以及废硅片料等组成。
拉直太阳能电池硅单晶用的原材料纯度,质量以及决定太阳能电池的性能和转换效率。为此,对多晶硅等原材料来源,纯度,外观形貌和后处理工序中物料洁净处理质量等因应具有严格的要求并制定出相应的厂内标准。
原料,特别是多晶硅进厂时应按下列程序进行验收:产品厂家,产品分析单,包装袋有无破损。
自家公司采用西门子法生产的多晶硅,经实际应用证明,具有比较高的纯度,质量可靠。
边皮料,锅底料,复拉料,头尾料以及废片料等均来自本单晶和硅片各生产工序。进洗料库时,应按如下所列要求进行检查和验收。
表1 对原材料质量要求
检查原料
质量要求来源内在质量外观
多晶硅电阻率:N型≧ 50Ω.cm
P型:≧50Ω.cm 银灰色,表面无氮化硅
膜,硅芯与晶体生长成
一体
顺大公司
边皮料质量与单晶相似是否会有粘胶存在开方整形的下脚
料
锅底料按电阻率分档有无石英渣及夹杂物单晶生产工艺复拉料头
尾料
质量与单晶相似表面有无污物单晶生产工艺废片料质量与单晶相似有无砂浆表面夹杂物切片工艺
·辅助材料:
用于腐蚀清洗硅原料和单晶棒料的化学试剂以及掺杂剂(杂质元素)等质量要求如表2所示:
表 2 化学试剂的质量要求
要求
名称
质量要求状态备注
HF(氢氟酸)分析纯液态安全存放
HNO3(硝酸)分析纯浓度
>55%
液态安全存放
KOH(氢氧化钾)分析纯液态或固态安全存放
NAOH(氢氧化钠)分析纯液态或固态安全存放
无水乙醇分析纯液态安全存放
(2)、供单晶生产需要的主要部件:
·籽晶与籽晶夹头:由两种材料制成。
表3 籽晶与籽晶夹头的材质和尺寸
部件名称材料尺寸(mm。)来源
籽晶无位错硅单晶100χ100χ130外协加工
自加工
φ170.5χ150
籽晶夹头
金属钼根据籽晶尺寸定外协加工
高纯高强度石
墨
根据籽晶尺寸定外协加工
籽晶在使用前需要经过5;1HF和HNO3混合液轻腐蚀,
清洗,烘干后用塑料袋装好备用。籽晶需要延续用多次时,表面有污物,需要腐蚀时,只能腐蚀籽晶下部,以免改变固定夹头部的尺寸。
·对石墨,碳毡等材料的主要部件:
对石墨,碳毡等材料的质量要求:
石墨和碳毡主要是用作加热,隔热,保温等部件材料。根据部件的用途,对其质量要求也有所不同。
用于制备加热器,反射板,导流筒,坩埚,坩埚轴等部件的石墨材质应具备致密度好,机械强度高,纯度高,灰分少等特点的等静压石墨材料,在工作期间性能稳定。如果材料经高温氯化煅烧,质量就更好了。
用于制备保温筒,保温盖,炉盘等部件应具有纯度比较高和灰分比较少的中粗石墨材料。
·主要部件用石墨材料质量参数:
表4 对石墨材质的要求
参数要求名称质量要求
来源
加热器致密度好,机械强度高,纯度高,灰分
少,性能稳定
外协
导流筒致密度好,机械强度高,纯度高,灰分
少,性能稳定
外协
坩埚托致密度好,机械强度高,纯度高,灰分
少,性能稳定
外协
坩埚轴致密度好,机械强度高,纯度高,灰分
少
外协
反射板致密度好,机械强度高,纯度高,灰分
少,性能稳定,
外协
保温筒中粗结构,机械强度比较高,纯度高,
灰分比较少,性能稳定
外协
加热器:根据单晶炉的炉型,设计了并且目前正在采用和运行的有三种尺寸的全部由高机械强度,纯度比较高的石墨材质加工的:17英寸加热器,拉制6英寸单晶,
18英寸加热器,拉制6英寸单晶,
20英寸加热器,拉制6或8英寸单晶,
主要部件结构如下:
反射板:双层石墨夹碳毡层结构,
导流筒:双层石墨夹碳毡层结构,
坩埚:三瓣结构,
坩埚轴,与金属坩埚轴直径尺寸相同,长度根据要求而定。上述部件全部由高机械强度,纯度比较高,灰分少的石墨材质加工而成的。
·石英坩埚:
石英坩埚直接与多晶硅料接触,并伴随单晶生长过程在高温下经受长时间的烘烤并与硅熔体发生反应和溶解,因此,应具有耐高温,坯料(二氧化硅)纯度高,和外形尺寸标准,无气泡,无黑点等质量特点。根据大装料量单晶生长工艺要求,在石英坩埚内壁还要求涂有均匀的耐高温氧化钡膜。
根据本炉型配置了17,18和20英寸三种标准尺寸的石英坩埚。
验收时特别注意检察:外形尺寸是否标准,是否存在气泡,黑点,破损,边缘损伤等缺陷。
·掺杂剂(杂质元素)和液氩:
用于单晶生长工艺中的化学试剂,掺杂剂(杂质元素)和液氩(Ar)等质量要求如表5所示;
表5 掺杂剂(杂质元素)和液氩等质量要求
要求
名称
质量要求状态备注
硼(B)≥ 99.999 % 晶体状或粉末状注意保存镓(Ga)≥ 99.999 % 常温下为液态冰厢内保存母合金(P型)电阻率≥10-3Ω.cm固态注意保存无水乙醇分析纯液态安全存放液氩(Ar)≥ 99.99 % 液态液氩罐存放
(3)、供单晶生产需要的设备:
·供腐蚀清洗工序需要的设备
表6 腐蚀清洗硅原料和单晶棒料的设备
超声清洗槽SGT28--3600 清洗硅原料3台备注
超声清洗槽HTA 清洗硅原料2台
烘箱DY—08--16 烘干硅原料1台自制8台离心热风脱
水机
功率3000W 烘干硅原料4台
通风橱二工位酸腐蚀料2台
硷腐蚀槽可加热≥1200C 腐蚀边皮料2台
酸腐蚀罐非标准酸腐埚底料若干
(4)、供硅单晶生产需要的主要设备:
表7 生产单晶用设备
参数名称型号和参数功能数量
(台)
备注
单晶炉可配置18和20英寸热场拉制单晶112 汉宏公司生产
单晶炉可配置18和20英寸热场拉制单晶86 晶运通公司生
产
单晶炉配置17英寸热场拉制单晶22 晶运通公司生
产
单晶炉可配置18和20英寸热场拉制单晶 4 天龙公司
带锯锯片厚度0.7㎜,刀速3㎜/
分截断单晶
棒
2 外购
红外测试
仪470FT-IR 测氧碳含
量
1 进口
电阻率测试仪4探针测单晶电
阻率
1 广洲生产
型号测试仪测晶体导
电型号
2 广洲生产
2、硅片生产部
(1)、供硅片生产需要的辅助材料;
表8 供硅片生产需要的原辅材料
要求
名称
质量要求功能备注无水已醇分析纯清洁处理KOH(氢氧化钾)分析纯腐蚀晶锭安全存放NAOH(氢氧化钠)分析纯腐蚀晶锭安全存放切削液(聚本醇)含水量<5%,导电率<0.5 Ω
-1.㎝-1.
配磨砂浆液
清洗液硅片清洗专用清洗切割片
热溶胶软化温度>4000C 沾开方锭
A,B 胶WALTECH公司生产沾线切割锭
磨砂1500井(8μm)配磨砂浆料
切割金属线线径120μm 切割
砂轮片厚度0.22㎜8英寸锭开方
滚磨砂轮配有三种粒径:
150井,270井,300井
滚磨开方锭
切削液配制切削液∶磨砂=1.17∶1 线切割用加工部配制
(2)、供硅片生产用的主要设备:
表9 生产硅片需要的设备
参数设备名称型号和参数功能数量
(台)
备注
粘棒机带加热>4000C装置粘接开方锭 3
线切割机HCT-Shaping 切割开方锭 6 6台瑞士产
滚磨机SINUMERK-802C 滚磨开方锭 3
开方机外圆切割8英寸锭开方 2
线切割机NTC-nippei Toyama 切割硅片70 日产
超声清洗机TCH-7 , 8共位清洗切割硅片 4
网式电阻炉WL-1型烘干硅片10
马弗炉热,处理消除热施主 2
硅片厚度测试仪MS 203 测硅片厚度
电阻率测试仪MS 203 测硅片电阻率
弯曲度测试仪测硅片弯曲度
硅单晶生产部
二、硅片生产工艺技术
(1)、腐蚀清洗工序生产工艺技术
?对腐蚀清洗工序要求
物料来源不同,摆放有序,以免出现混料事故,
洗料间严禁采用金属制品用具,
洗料间经常清扫,随时保持清洁。
·安全防护:
在处理工艺中会使用大量强酸(HF,HNO3)和强硷(KOH,NaOH)等物质。这些物质对人身具有很大伤害作用,一定要有安全防护意识,严防与强酸和强硷与人体皮肤和指甲接触。进行硅料酸腐蚀时,操作人员一定在通风橱内操作。操作人员在进入操作间前必须穿好工作服和工作鞋(胶胶),带好工作冒,胶皮手套和眼镜等防护等。一旦出现事故,应及时用水冲洗等进行初步处理,同时通报相关领导。
提供给拉制硅单晶用的原材料来源不同,计有本公司采用西门子
水冲洗两遍
法生产的多晶硅,硅片生产过程中切下的边皮料,复拉料,单晶棒的头尾料以及埚底料等。由于在运输,加工等过程中,其表面沾污或沾接一些其它物质,对硅单晶正常生长会造成极为不利的影响。为此作为制备硅单晶用的原材料,在进入单晶生长工序后,对其表面需要进行严格的去污处理(用去离子水冲洗或丙酮和无水乙醇擦)。 根据原材料来源不同,表面状态和污染情况皆不相同,故对来源不同的原料应采用分别单独处理工艺。
? 对处理后原材料质量要求:
表面光亮, 无斑点(包括酸斑),无印迹(包括手印), 无黄色酸斑,无夹杂物等。
(2)、腐蚀清洗生产工艺流程
①、
多晶硅块料,复拉料和头,尾料处理工艺流程多晶硅块料
复拉料,头尾料 多晶硅块料
打 磨
腐蚀过程物料表面 酸腐蚀 HF +HNO 3(1﹕5) 不能与空气接触
电阻≥15兆Ω 酸液环保处理 去离子水
频率为3600Hz 低频超声 电阻≥15兆Ω 两遍清洗 去离子水
复拉,头尾料 多晶硅块料
包 装 水冲洗两遍
水温600C 高频超声 电阻≥15兆Ω
三遍清洗 去离子水,600C
在相对洁净 烘 干 烘箱温度700C ,≥5小时 间内进行
在相对洁净间 采用双层塑料密封包装
内进行
②、边皮料酸碱清洗处理工艺流程
边皮料
去 胶 600C 温水泡
硷 洗 KOH (N a OH ),1200C
水冲洗 自来水
腐蚀过程物料表面 酸腐蚀 HF +HNO 3(1﹕5)
不能与空气接触
电阻≥10M Ω 酸液环保处理 去离子水
频率为3600Hz 低频超声 电阻≥10M Ω 两遍清洗 去离子水
水冲洗两遍
水温600C 高频超声 电阻≥10M Ω
三遍清洗 去离子水,600C
在相对洁净 离心热风烘干 烘干温度700C ,≥1小时
间内进行
包 装 采用双层塑料密封包装
③、埚底料酸清洗处理工艺流程
埚底料
电阻率分挡 选出PN 结料
打 磨 去除料表面石英渣
时间达50-60小时 酸 泡 HF 50%
进一步去除石英渣
水冲洗 中水(经过处理的废水)
腐蚀过程物料表面 酸腐蚀 HF +HNO 3(1﹕5) 不能与空气接触
电阻≥10兆Ω 酸液环保处理 去离子水
频率为3600Hz 低频超声两遍清洗 电阻≥10兆Ω 去离子水
水温60C 高频超声电阻≥10兆Ω
三遍清洗去离子水,600C
在相对洁净离心热风甩干700C,≥1小时
间内进行
包装采用双层塑料密封包装
建议:
●埚底料经过HF酸锓泡后不应采用气味很浓的中水冲洗,而应改为自来水,最好为去离子水。
④、废片的清洗处理工艺流程
废片
去污泥水冲洗
去氧化膜酸泡加HF,搅拌
水冲洗搅拌,自来水
在通风橱内操作酸腐蚀HF+HNO3(1﹕5),搅拌
冲洗电阻≥10兆Ω去离子水
酸液环保处理搅拌
硷腐蚀KOH,搅拌
水冲洗电阻≥10兆Ω去离子水
搅拌
离心热风甩干700C,≥1小时
包装双层塑料袋封装
建议:1 废片清洗相互沾接,难于清洗干净。建议清洗处理后的废片最好用作铸锭料或复拉后作为直拉单晶原料。
2 该种废片应在原地经过初步清洗处理。
(3)、硅单晶生长工艺技术
太阳能用硅单晶一般都采用的直拉法制备的。该方法也称有坩埚法,为波兰科学家J Czochralski于1918年发明的,故又称切克拉斯基法,简称为CZ法。于1950年美国科学家G. K. Teal和J. B. Little将该方法成功地移植到拉制锗单晶上。之后又被G. K.Teal 移植到拉制硅单晶上。1960年Dash采用缩径方法拉制出无位错硅单晶。
该方法的主要特点:
a、设备相对简单,便于操作和掺杂方便。
b、可拉制大直径单晶,Φ200 mm和Φ300 mm单晶已经商品化生
产,更大直径的单晶,如Φ400mm单晶的制备正在研究中。
c、由于单晶氧含量高,机械强度优异,适于制造半导体器件。
不足之处:由于物料与石英坩埚发生化学反应,使硅熔体受到污染,单晶的纯度受到影响。
(4)、供单晶生产中需要的条件和要求
①、单晶炉:单晶硅棒是在单晶炉内生长的,本公司现有不同型号和尺寸的,供拉制6英寸和供拉制8英寸单晶的单晶炉共计216台并全部配有带过滤网的70型真空机械泵。:
·加热系统(热场)
热场系统组成的部件:它是由石墨加热器,石墨坩埚,保温筒,保温盖板,石墨电极,梅花托以及导流筒(热屏)等部件配置而成。
根据现有炉型配置了17英寸,18英寸和20英寸三种不同尺寸的热系统,并全部配置了导流筒(热屏)。导流筒(热屏)有多层(两层石墨中间夹一层碳毡),单层二种。,在单层中结构上又分单节和两节的。
附有导流筒的热系统是近年来随着单晶直径不断增大,加料量不断增加而兴起的,并已被众多单晶厂家所接受的热场。其最大的特点:
⑴、减少热辐射和热量损失,可降低热功率25%左右。
⑵、由于热屏对炉热的屏蔽使热场的轴向温度梯度增大,为提高单晶生长速度创造条件。
⑶、减少热对流,加快蒸发气体从熔体表面挥发,对降低单晶氧含量十分有利。
·配置的热场应附和如下要求:
配置成功的热场不但要保持熔体和晶体生长所需要的,适宜的轴向温度梯度和径向温度梯度,而且又能得到比较低的所需要的加热功率和具有比较高的成晶率。同时还要考虑气流的合理走向,以
便减少杂质沾污和保证有一个良好的单晶生长环境。除此之外,还能够符合由生产实际经验得出的,对引晶和晶体生长十分重要的参考数据:
当加热达到化料功率时电压不能超过60伏。
加热器上开口与液面距离: 25~30㎜
导流筒下沿与熔体液面距离: 25~30㎜
导流筒内层与晶体外表面距离: 25~30㎜
·石英坩埚:配置了与热系统三种尺寸相对应的,内表面涂有高纯度,耐高温氧化钡的石英坩埚,其装料量分别如下:17英寸热系统,配置17英寸石英坩埚,装料量55 公斤,
18英寸热系统,配置18英寸石英坩埚,装料量60 公斤,
20英寸热系统,配置20英寸石英坩埚, 装料量95 公斤,
②、配料与掺杂
·配料:
供拉制硅单晶用的有多晶硅料,复拉料,埚底料头,尾
料等四种。上述几种原料的配置根据公司要求和客户需要而定。
·掺杂:
掺杂剂(掺杂元素)的选择
根据客户需要,目前本公司生产的均为P型导电的硅单晶材料。适宜的掺杂元素为硼(B和镓(Ga)。
硼(B)的分凝系数为0.8,制得的单晶轴向和径向电阻率分布均比较均匀,因此,硼是最为理想的掺杂元素。但用掺硼硅片制备的太阳能电池转换效率有比较明显的衰减现象。
镓(Ga)的分凝系数为0.008,由于分凝系数非常小,其在晶体中分布的均匀性很差,单晶头尾电阻率差别比较大,作为掺杂剂而言是十分不理想的。但用掺镓硅片制备的太阳能电池转换效率衰减现象很小,因此器件厂家(尚德公司)要求提供掺镓硅片。故选择镓作为掺杂剂。
·掺杂方法和掺杂量计算
掺杂方法:
硼(B)的分凝系数为0.8,需要的掺入量比较少。为保证称量的精确性,多采用硼和硅母合金的形式掺入。镓(Ga)的分凝系数为0.008,,需要的掺入量多,故采用元素形式掺入。
掺杂量计算:
?硼(B)的掺入量计算:
按公式:m = M .N/κ.n
式中: m —掺入量(克)
M —装料量(克)
N —目标电阻率对应的杂质浓度(cm-3)
κ—硼的分凝系数
n —母合金的杂质浓度(cm-3)
?镓(Ga)的掺入量计算:
按公式: W/d.C L0= M/A.N0
式中:W -- 装料量(克)
C L0-- 硅熔体的初始杂质浓度(cm-3)
A -- 掺杂元素的原子量
D -- 硅的比重
M -- 掺杂元素的重量(克)
N0-- 阿佛伽得罗常数(6.023x1023 cm-3)
?另有根据尚德公司提供的如下计算数据系统和曲线图进行计算,采用数据和图表计算,在实际应用中比较简便,在车间生产中目前均采用该计算方法。显介绍如下:
需要掺入纯Ga质量
0.853486707
母合金的情况
杂质元素摩尔质量母合金的电阻率P型B10.8110 3.0000
Ga69.7230 0.5000 N型P30.9738 0.0020 原料表
掺杂元素电阻率重量体积
原料1B 1.0000 0.0000 0.0000 原料2B 1.0000 0.0000 0.0000 原料3B 1.0000 0.0000 0.0000 原料4B 1.0000 0.0000 0.0000 原料5B 1.0000 0.0000 0.0000 汇总0.00E+000.00 原料1Ga 1.0000 0.0000 0.0000 原料2Ga10.0000 0.0000 0.0000 原料3Ga10.0000 0.0000 0.0000 原料4原料510.0000 0.0000 0.0000
10.0000 0.0000 0.0000
汇总0.00E+000.00E+00原料1P100.0000 12.0000 5150.2146 原料2P100.0000 12.0000 5150.2146 原料3P100.0000 12.0000 5150.2146 原料4P100.0000 12.0000 5150.2146 原料5P100.0000 12.0000 5150.2146 汇总0.00E+00 2.58E+04总汇总0.0000 25751.0730
x
硅片生产工艺流程及注意要点
硅片生产工艺流程及注意要点 简介 硅片的准备过程从硅单晶棒开始,到清洁的抛光片结束,以能够在绝好的环境中使用。期间,从一单晶硅棒到加工成数片能满足特殊要求的硅片要经过很多流程和清洗步骤。除了有许多工艺步骤之外,整个过程几乎都要在无尘的环境中进行。硅片的加工从一相对较脏的环境开始,最终在10级净空房内完成。 工艺过程综述 硅片加工过程包括许多步骤。所有的步骤概括为三个主要种类:能修正物理性能如尺寸、形状、平整度、或一些体材料的性能;能减少不期望的表面损伤的数量;或能消除表面沾污和颗粒。硅片加工的主要的步骤如表1.1的典型流程所示。工艺步骤的顺序是很重要的,因为这些步骤的决定能使硅片受到尽可能少的损伤并且可以减少硅片的沾污。在以下的章节中,每一步骤都会得到详细介绍。 表1.1 硅片加工过程步骤 1.切片 2.激光标识 3.倒角 4.磨片 5.腐蚀 6.背损伤 7.边缘镜面抛光 8.预热清洗 9.抵抗稳定——退火 10.背封 11.粘片 12.抛光 13.检查前清洗 14.外观检查
15.金属清洗 16.擦片 17.激光检查 18.包装/货运 切片(class 500k) 硅片加工的介绍中,从单晶硅棒开始的第一个步骤就是切片。这一步骤的关键是如何在将单晶硅棒加工成硅片时尽可能地降低损耗,也就是要求将单晶棒尽可能多地加工成有用的硅片。为了尽量得到最好的硅片,硅片要求有最小量的翘曲和最少量的刀缝损耗。切片过程定义了平整度可以基本上适合器件的制备。 切片过程中有两种主要方式——内圆切割和线切割。这两种形式的切割方式被应用的原因是它们能将材料损失减少到最小,对硅片的损伤也最小,并且允许硅片的翘曲也是最小。 切片是一个相对较脏的过程,可以描述为一个研磨的过程,这一过程会产生大量的颗粒和大量的很浅表面损伤。 硅片切割完成后,所粘的碳板和用来粘碳板的粘结剂必须从硅片上清除。在这清除和清洗过程中,很重要的一点就是保持硅片的顺序,因为这时它们还没有被标识区分。 激光标识(Class 500k) 在晶棒被切割成一片片硅片之后,硅片会被用激光刻上标识。一台高功率的激光打印机用来在硅片表面刻上标识。硅片按从晶棒切割下的相同顺序进行编码,因而能知道硅片的正确位置。这一编码应是统一的,用来识别硅片并知道它的来源。编码能表明该硅片从哪一单晶棒的什么位置切割下来的。保持这样的追溯是很重要的,因为单晶的整体特性会随着晶棒的一头到另一头而变化。编号需刻的足够深,从而到最终硅片抛光完毕后仍能保持。在硅片上刻下编码后,即使硅片有遗漏,也能追溯到原来位置,而且如果趋向明了,那么就可以采取正确的措施。激光标识可以在硅片的正面也可在背面,尽管正面通常会被用到。
晶体硅太阳能电池的制造工艺流程
晶体硅太阳能电池的制造 工艺流程 This model paper was revised by the Standardization Office on December 10, 2020
提高太阳能电池的转换效率和降低成本是太阳能电池技术发展的主流。 晶体硅太阳能电池的制造工艺流程说明如下: (1)切片:采用多线切割,将硅棒切割成正方形的硅片。 (2)清洗:用常规的硅片清洗方法清洗,然后用酸(或碱)溶液将硅片表面切割损伤层除去30-50um。 (3)制备绒面:用碱溶液对硅片进行各向异性腐蚀在硅片表面制备绒面。 (4)磷扩散:采用涂布源(或液态源,或固态氮化磷片状源)进行扩散,制成PN+结,结深一般为-。 (5)周边刻蚀:扩散时在硅片周边表面形成的扩散层,会使电池上下电极短路,用掩蔽湿法腐蚀或等离子干法腐蚀去除周边扩散层。 (6)去除背面PN+结。常用湿法腐蚀或磨片法除去背面PN+结。 (7)制作上下电极:用真空蒸镀、化学镀镍或铝浆印刷烧结等工艺。先制作下电极,然后制作上电极。铝浆印刷是大量采用的工艺方法。 (8)制作减反射膜:为了减少入反射损失,要在硅片表面上覆盖一层减反射膜。制作减反射膜的材料有MgF2 ,SiO2 ,Al2O3,SiO ,Si3N4 ,TiO2 ,Ta2O5等。工艺方法可用真空镀膜法、离子镀膜法,溅射法、印刷法、PECVD法或喷涂法等。 (9)烧结:将电池芯片烧结于镍或铜的底板上。 (10)测试分档:按规定参数规范,测试分类。
由此可见,太阳能电池芯片的制造采用的工艺方法与半导体器件基本相同,生产的工艺设备也基本相同,但工艺加工精度远低于集成电路芯片的制造要求,这为太阳能电池的规模生产提供了有利条件。
半导体工艺流程
1清洗 集成电路芯片生产的清洗包括硅片的清洗和工器具的清洗。由 于半导体生产污染要求非常严格,清洗工艺需要消耗大量的高纯水; 且为进行特殊过滤和纯化广泛使用化学试剂和有机溶剂。 在硅片的加工工艺中,硅片先按各自的要求放入各种药液槽进行表面化学处理,再送入清洗槽,将其表面粘附的药液清洗干净后进入下一道工序。常用的清洗方式是将硅片沉浸在液体槽内或使用液体喷雾清洗,同时为有更好的清洗效果,通常使用超声波激励和擦片措施,一般在有机溶剂清洗后立即米用无机酸将其氧化去除,最后用超纯水进行清洗,如图1-6所示。 图1-6硅片清洗工艺示意图 工具的清洗基本米用硅片清洗同样的方法。 2、热氧化 热氧化是在800~1250C高温的氧气氛围和惰性携带气体(N2)下使硅片表面的硅氧化生成二氧化硅膜的过程,产生的二氧化硅用以作为扩散、离子注入的阻挡层,或介质隔离层。典型的热氧化化学反应为: Si + O2 T SiO2
3、扩散 扩散是在硅表面掺入纯杂质原子的过程。通常是使用乙硼烷(B2H6)作为N —源和磷烷(PH3)作为P+源。工艺生产过程中通常 分为沉积源和驱赶两步,典型的化学反应为: 2PH3 —2P+3H2 4、离子注入 离子注入也是一种给硅片掺杂的过程。它的基本原理是把掺杂物质(原子)离子化后,在数千到数百万伏特电压的电场下得到加速,以较高的能量注入到硅片表面或其它薄膜中。经高温退火后,注入离子活化,起施主或受主的作用。 5、光刻 光刻包括涂胶、曝光、显影等过程。涂胶是通过硅片高速旋转在硅片表面均匀涂上光刻胶的过程;曝光是使用光刻机,并透过光掩膜版对涂胶的硅片进行光照,使部分光刻胶得到光照,另外,部分光刻胶得不到光照,从而改变光刻胶性质;显影是对曝光后的光刻胶进行去除,由于光照后的光刻胶 和未被光照的光刻胶将分别溶于显影液和不溶于显影液,这样就使光刻胶上 形成了沟槽。 6、湿法腐蚀和等离子刻蚀 通过光刻显影后,光刻胶下面的材料要被选择性地去除,使用的方法就
硅片生产工艺技术流程
顺大半导体发展有限公司太阳能用 硅单晶片生产技术 目录 一、硅片生产工艺中使用的主要原辅材料 1、拉制单晶用的原辅材料,设备和部件: 2、供硅片生产用的原辅材料,设备和部件: 二、硅片生产工艺技术 1、硅单晶生产部 (1)、腐蚀清洗工序生产工艺技术 对处理后原材料质量要求 (2)、腐蚀清洗生产工艺流程 ①多晶硅块料,复拉料和头,尾料处理工艺流程 ②边皮料酸碱清洗处理工艺流程 ③埚底料酸清洗处理工艺流程 ④废片的清洗处理工艺流程 (3)、硅单晶生长工艺技术 (4)、单晶生长中的必备条件和要求 ①单晶炉 ②配料与掺杂 (5),单晶生长工艺参数选择 (6)、质量目标: (7)、硅单晶生长工艺流程
2、硅片生产部 (1)、硅片加工生产工艺技术 (2)、硅片加工工艺中的必备条件和要求 ①切割机 ②切割浆液 (3)、质量目标 (4)、硅片加工工艺技术流程 ①开方锭生产工艺流程 ②切片生产工艺流程 (5)、硅片尺寸和性能参数检测
前言 江苏顺大半导体发展有限公司座落于美丽的高邮湖畔。公司始创生产太阳能电池用各种尺寸的单晶和多晶硅片。拥有国内先进的拉制单晶设备104台,全自动单晶炉112台。年产量可达到××××吨。拥有大型先进的线切割设备×××台。并且和无锡尚德形成了合作联盟(伙伴),每×可以向尚德提供×××硅单晶片。同时河北晶于2004年,占地面积××××。公司现在有×××名员工,从事澳、南京等光伏组件公司都和顺大形成了长年的合作关系。为了公司的进一步发展,扩大产业链,解决硅单晶的上下游产品的供需关系,2006年在扬州投资多晶硅项目,投资规模达到××亿。工程分两期建设,总规模年产多晶硅6000吨。2008年底首期工程已经正式投入批量生产,年产多晶硅×××吨。 太阳能用硅片生产工艺十分复杂,要通过几十道工序才能完成,只有发挥团队精神才能保证硅片的最终质量。编写该篇壮大资料的目的:首先让大家了解整个硅片生产过程,更重要的是让各生产工序中的每一位操作人员明确自己的职责,更自觉地按操作规程和规范做好本职工作,为顺大半导体发展有限公司的发展,尽自己的一份力量。
单晶硅生产工艺
什么是单晶硅 单晶硅可以用于二极管级、整流器件级、电路级以及太阳能电池级单晶产品的生产和深加工制造,其后续产品集成电路和半导体分离器件已广泛应用于各个领域,在军事电子设备中也占有重要地位。 在光伏技术和微小型半导体逆变器技术飞速发展的今天,利用硅单晶所生产的太阳能电池可以直接把太阳能转化为光能,实现了迈向绿色能源革命的开始。北京2008年奥运会将把“绿色奥运”做为重要展示面向全世界展现,单晶硅的利用在其中将是非常重要的一环。现在,国外的太阳能光伏电站已经到了理论成熟阶段,正在向实际应用阶段过渡,太阳能硅单晶的利用将是普及到全世界范围,市场需求量不言而喻。 单晶硅产品包括φ3”----φ6”单晶硅圆形棒、片及方形棒、片,适合各种半导体、电子类产品的生产需要,其产品质量经过当前世界上最先进的检测仪器进行检验,达到世界先进水平。 相对多晶硅是在单籽晶为生长核,生长的而得的。单晶硅原子以三维空间模式周期形成的长程有序的晶体。多晶硅是很多具有不同晶向的小单晶体单独形成的,不能用来做半导体电路。多晶硅必须融化成单晶体,才能加工成半导体应用中使用的晶圆片 加工工艺: 加料—→熔化—→缩颈生长—→放肩生长—→等径生长—→尾部生长 (1)加料:将多晶硅原料及杂质放入石英坩埚内,杂质的种类依电阻的N或P型而定。杂质种类有硼,磷,锑,砷。 (2)熔化:加完多晶硅原料于石英埚内后,长晶炉必须关闭并抽成真空后充入高纯氩气使之维持一定压力范围内,然后打开石墨加热器电源,加热至熔化温度(1420℃)以上,将多晶硅原料熔化。 (3)缩颈生长:当硅熔体的温度稳定之后,将籽晶慢慢浸入硅熔体中。由于籽晶与硅熔体场接触时的热应力,会使籽晶产生位错,这些位错必须利用缩颈生长使之消失掉。缩颈生长是将籽晶快速向上提升,使长出的籽晶的直径缩小到一定大小(4-6mm)由于位错线与生长轴成一个交角,只要缩颈够长,位错便能长出晶体表面,产生零位错的晶体。 (4)放肩生长:长完细颈之后,须降低温度与拉速,使得晶体的直径渐渐增大到所需的大小。 (5)等径生长:长完细颈和肩部之后,借着拉速与温度的不断调整,可使晶棒直径维持在正负2mm之间,这段直径固定的部分即称为等径部分。单晶硅片取自于等径部分。 (6)尾部生长:在长完等径部分之后,如果立刻将晶棒与液面分开,那么热应力
电池片生产工艺流程汇总
电池片生产工艺流程 一、制绒 a.目的 在硅片的表面形成坑凹状表面,减少电池片的反射的太阳光,增加二次反射的面积。一般情况下,用碱处理是为了得到金字塔状绒面; 用酸处理是为了得到虫孔状绒面。不管是哪种绒面,都可以提高硅片的陷光作用。 b.流程 1.常规条件下,硅与单纯的HF、HNO3(硅表面会被钝化,二氧化硅与HNO3不反应)认为是不反应的。但在两种混合酸的体系中,硅则可以与溶液进行持续的反应。 硅的氧化 硝酸/亚硝酸(HNO2)将硅氧化成二氧化硅(主要是亚硝酸将硅氧化) Si+4HNO3=SiO2+4NO2+2H2O (慢反应 3Si+4HNO3=3SiO2+4NO+2H2O (慢反应 二氧化氮、一氧化氮与水反应,生成亚硝酸,亚硝酸很快地将硅氧化成二氧化硅。 2NO2+H2O=HNO2+HNO3 (快反应 Si+4HNO2=SiO2+4NO+2H2O (快反应(第一步的主反应)
4HNO3+NO+H2O=6HNO2(快反应 只要有少量的二氧化氮生成,就会和水反应变成亚硝酸,只要少量的一氧化氮生成,就会和硝酸、水反应很快地生成亚硝酸,亚硝酸会很快的将硅氧化,生成一氧化氮,一氧化氮又与硝酸、水反应,这样一系列化学反应最终的结果是造成硅的表面被快速氧化,硝酸被还原成氮氧化物。 二氧化硅的溶解 SiO2+4HF=SiF4+2H2O(四氟化硅是气体 SiF4+2HF=H2SiF6 总反应 SiO2+6HF=H2SiF6+2H2O 最终反应掉的硅以氟硅酸的形式进入溶液。 2.清水冲洗 3.硅片经过碱液腐蚀(氢氧化钠/氢氧化钾),腐蚀掉硅片经酸液腐蚀后的多孔硅 4.硅片经HF、HCl冲洗,中和碱液,如不清洗硅片表面残留的碱液,在烘干后硅片的表面会有结晶 5.水冲洗表面,洗掉酸液 c.注意
半导体工艺及芯片制造技术问题答案(全)
常用术语翻译 active region 有源区 2.active component有源器件 3.Anneal退火 4.atmospheric pressure CVD (APCVD) 常压化学气相淀积 5.BEOL(生产线)后端工序 6.BiCMOS双极CMOS 7.bonding wire 焊线,引线 8.BPSG 硼磷硅玻璃 9.channel length沟道长度 10.chemical vapor deposition (CVD) 化学气相淀积 11.chemical mechanical planarization (CMP)化学机械平坦化 12.damascene 大马士革工艺 13.deposition淀积 14.diffusion 扩散 15.dopant concentration掺杂浓度 16.dry oxidation 干法氧化 17.epitaxial layer 外延层 18.etch rate 刻蚀速率 19.fabrication制造 20.gate oxide 栅氧化硅 21.IC reliability 集成电路可靠性
22.interlayer dielectric 层间介质(ILD) 23.ion implanter 离子注入机 24.magnetron sputtering 磁控溅射 25.metalorganic CVD(MOCVD)金属有机化学气相淀积 26.pc board 印刷电路板 27.plasma enhanced CVD(PECVD) 等离子体增强CVD 28.polish 抛光 29.RF sputtering 射频溅射 30.silicon on insulator绝缘体上硅(SOI) 第一章半导体产业介绍 1. 什么叫集成电路?写出集成电路发展的五个时代及晶体管的数量?(15分) 集成电路:将多个电子元件集成在一块衬底上,完成一定的电路或系统功能。集成电路芯片/元件数产业周期 无集成 1 1960年前 小规模(SSI) 2到50 20世纪60年代前期 中规模(MSI) 50到5000 20世纪60年代到70年代前期 大规模(LSI) 5000到10万 20世纪70年代前期到后期 超大规模(VLSI) 10万到100万 20世纪70年代后期到80年代后期甚大规模(ULSI) 大于100万 20世纪90年代后期到现在 2. 写出IC 制造的5个步骤?(15分)
单晶硅片制作工艺流程
单晶硅电磁片生产工艺流程 ?1、硅片切割,材料准备: ?工业制作硅电池所用的单晶硅材料,一般采用坩锅直拉法制的太阳级单晶硅棒,原始的形状为圆柱形,然后切割成方形硅片(或多晶方形硅片),硅片的边长一般为10~15cm,厚度约200~350um,电阻率约1Ω.cm的p型(掺硼)。 ?2、去除损伤层: ?硅片在切割过程会产生大量的表面缺陷,这就会产生两个问题,首先表面的质量较差,另外这些表面缺陷会在电池制造过程中导致碎片增多。因此要将切割损伤层去除,一般采用碱或酸腐蚀,腐蚀的厚度约10um。 ? ? 3、制绒: ?制绒,就是把相对光滑的原材料硅片的表面通过酸或碱腐蚀,使其凸凹不平,变得粗糙,形成漫反射,减少直射到硅片表面的太阳能的损失。对于单晶硅来说一般采用NaOH加醇的方法腐蚀,利用单晶硅的各向异性腐蚀,在表面形成无数的金字塔结构,碱液的温度约80度,浓度约1~2%,腐蚀时间约15分钟。对于多晶来说,一般采用酸法腐蚀。 ? 4、扩散制结:
?扩散的目的在于形成PN结。普遍采用磷做n型掺杂。由于固态扩散需要很高的温度,因此在扩散前硅片表面的洁净非常重要,要求硅片在制绒后要进行清洗,即用酸来中和硅片表面的碱残留和金属杂质。 ? 5、边缘刻蚀、清洗: ?扩散过程中,在硅片的周边表面也形成了扩散层。周边扩散层使电池的上下电极形成短路环,必须将它除去。周边上存在任何微小的局部短路都会使电池并联电阻下降,以至成为废品。 目前,工业化生产用等离子干法腐蚀,在辉光放电条件下通过氟和氧交替对硅作用,去除含有扩散层的周边。 扩散后清洗的目的是去除扩散过程中形成的磷硅玻璃。 ? 6、沉积减反射层: ?沉积减反射层的目的在于减少表面反射,增加折射率。广泛使用PECVD淀积SiN ,由于PECVD淀积SiN时,不光是生长SiN 作为减反射膜,同时生成了大量的原子氢,这些氢原子能对多晶硅片具有表面钝化和体钝化的双重作用,可用于大批量生产。 ? 7、丝网印刷上下电极: ?电极的制备是太阳电池制备过程中一个至关重要的步骤,它不仅决定了发射区的结构,而且也决定了电池的串联电阻和电
晶体硅的生产过程
一、单晶硅的制法通常是先制得多晶硅或无定形硅,然后用直拉法或悬浮区熔法从熔体中生长出棒状单晶硅。熔融的单质硅在凝固时硅原子以金刚石晶格排列成许多晶核,如果这些晶核长成晶面取向相同的晶粒,则这些晶粒平行结合起来便结晶成单晶硅。 单晶硅棒是生产单晶硅片的原材料,随着国内和国际市场对单晶硅片需求量的快速增加,单晶硅棒的市场需求也呈快速增长的趋势。 单晶硅圆片按其直径分为6英寸、8英寸、12英寸(300毫米)及18英寸(450毫米)等。直径越大的圆片,所能刻制的集成电路越多,芯片的成本也就越低。但大尺寸晶片对材料和技术的要求也越高。单晶硅按晶体生长方法的不同,分为直拉法(CZ)、区熔法(FZ)和外延法。直拉法、区熔法生长单晶硅棒材,外延法生长单晶硅薄膜。直拉法生长的单晶硅主要用于半导体集成电路、二极管、外延片衬底、太阳能电池。目前晶体直径可控制在Φ3~8英寸。区熔法单晶主要用于高压大功率可控整流器件领域,广泛用于大功率输变电、电力机车、整流、变频、机电一体化、节能灯、电视机等系列产品。目前晶体直径可控制在Φ3~6英寸。外延片主要用于集成电路领域。 由于成本和性能的原因,直拉法(CZ)单晶硅材料应用最广。在IC工业中所用的材料主要是CZ抛光片和外延片。存储器电路通常使用CZ抛光片,因成本较低。逻辑电路一般使用价格较高的外延片,因其在IC制造中有更好的适用性并具有消除Latch-up的能力。 单晶硅也称硅单晶,是电子信息材料中最基础性材料,属半导体材料类。单晶硅已渗透到国民经济和国防科技中各个领域,当今全球超过2000亿美元的电子通信半导体市场中95%以上的半导体器件及99%以上的集成电路用硅。 二、硅片直径越大,技术要求越高,越有市场前景,价值也就越高。 日本、美国和德国是主要的硅材料生产国。中国硅材料工业与日本同时起步,但总体而言,生产技术水平仍然相对较低,而且大部分为2.5、3、4、5英寸硅锭和小直径硅片。中国消耗的大部分集成电路及其硅片仍然依赖进口。但我国科技人员正迎头赶上,于1998年成功地制造出了12英寸单晶硅,标志着我国单晶硅生产进入了新的发展时期。 目前,全世界单晶硅的产能为1万吨/年,年消耗量约为6000吨~7000吨。未来几年中,
单晶硅生产工艺及单晶硅片生产工艺
单晶硅生产工艺及单晶硅片生产工艺 单晶硅原子以三维空间模式周期形成的长程有序的晶体。多晶硅是很多具有不同晶向的小单晶体单独形成的,不能用来做半导体电路。多晶硅必须融化成单晶体,才能加工成半导体应用中使用的晶圆片。 加工工艺: 加料—→熔化—→缩颈生长—→放肩生长—→等径生长—→尾部生长(1)加料:将多晶硅原料及杂质放入石英坩埚内,杂质的种类依电阻的N或P型而定。杂质种类有硼,磷,锑,砷。 (2)熔化:加完多晶硅原料于石英埚内后,长晶炉必须关闭并抽成真空后充入高纯氩气使之维持一定压力范围内,然后打开石墨加热器电源,加热至熔化温度(1420℃)以上,将多晶硅原料熔化。 (3)缩颈生长:当硅熔体的温度稳定之后,将籽晶慢慢浸入硅熔体中。由于籽晶与硅熔体场接触时的热应力,会使籽晶产生位错,这些位错必须利用缩颈生长使之消失掉。缩颈生长是将籽晶快速向上提升,使长出的籽晶的直径缩小到一定大小(4-6mm)由于位错线与生长轴成一个交角,只要缩颈够长,位错便能长出晶体表面,产生零位错的晶体。 (4)放肩生长:长完细颈之后,须降低温度与拉速,使得晶体的直径渐渐增大到所需的大小。 (5)等径生长:长完细颈和肩部之后,借着拉速与温度的不断调整,可使晶棒直径维持在正负2mm之间,这段直径固定的部分即称为等径部分。单晶硅片取自于等径部分。 (6)尾部生长:在长完等径部分之后,如果立刻将晶棒与液面分开,那么热应力将使得晶棒出现位错与滑移线。于是为了避免此问题的发生,必须将晶棒的直径慢慢缩小,直到成一尖点而与液面分开。这一过程称之为尾部生长。长完的晶棒被升至上炉室冷却一段时间后取出,即完成一次生长周期。 单晶硅棒加工成单晶硅抛光硅片 加工流程: 单晶生长—→切断—→外径滚磨—→平边或V型槽处理—→切片 倒角—→研磨腐蚀—→抛光—→清洗—→包装
单晶多晶硅片生产工艺流程详解
在【技术应用】单晶、多晶硅片生产工艺流程详解(上)中,笔者介绍了单晶和多晶硅片工艺流程的前半部分,概述了一些工艺流程和概念,以及术语的相关知识。而本文则是从切片工艺开始了解,到磨片和吸杂,看硅片如何蜕变。 切片 切片综述 当单晶硅棒送至硅片生产区域时,晶棒已经过了头尾切除、滚磨、参考面磨制的过程,直接粘上碳板,再与切块粘接就能进行切片加工了。 为了能切割下单个的硅片,晶棒必须以某种方式进行切割。切片过程有一些要求:能按晶体的一特定的方向进行切割;切割面尽可能平整;引入硅片的损伤尽可能的少;材料的损失尽量少。 碳板 当硅片从晶棒上切割下来时,需要有某样东西能防止硅片松散地掉落下来。有代表性的是用碳板与晶棒通过环氧粘合在一起从而使硅片从晶棒上切割下来后,仍粘在碳板上。 碳板不是粘接板的唯一选择,任何种类的粘接板和环氧结合剂都必须有以下几个特性:能支持硅片,防止其在切片过程中掉落并能容易地从粘板和环氧上剥离;还能保护硅片不受污染。其它粘板材料还有陶瓷和环氧。 石墨 是一种用来支撑硅片的坚硬材料,它被做成与晶棒粘接部位一致的形状。大多数情况下,碳板应严格地沿着晶棒的参考面粘接,这样碳板就能加工成矩形长条。当然,碳板也可以和晶棒的其它部位粘接,但同样应与该部位形状一致。碳板的形状很重要,因为它要求能在碳板和晶棒间使用尽可能少的环氧和尽量短的距离。这个距离要求尽量短,因为环氧是一种相当软的材料而碳板和晶棒是很硬的材料。当刀片从硬的材料切到软的材料再到硬的材料,可能会引起硅片碎裂。 这里有一些选择环氧类型参考:强度、移动性和污染程度。粘接碳板与晶棒的环氧应有足够强的粘度,才能支持硅片直到整根晶棒切割完成,因此,它必须能很容易地从硅片上移走,只有最小量的污染。 刀片 当从晶棒上切割下硅片时,期望切面平整、损伤小、沿特定方向切割并且损失的材料尽量小。有一个速度快、安全可靠、经济的切割方法是很值得的。 在半导体企业,两种通常被应用的方法是环型切割和线切割。环型切割通常是指内圆切割,是将晶棒切割为硅片的最广泛采用的方法。
硅片生产流程
硅片生产流程 小组成员:吴国栋徐浩王汉杰王超 简介 硅片的准备过程从硅单晶棒开始,到清洁的抛光片结束,以能够在绝好的环境中使用。期间,从一单晶硅棒到加工成数片能满足特殊要求的硅片要经过很多流程和清洗步骤。除了有许多工艺步骤之外,整个过程几乎都要在无尘的环境中进行。硅片的加工从一相对较脏的环境开始,最终在10级净空房内完成。 工艺过程综述 硅片加工过程包括许多步骤。所有的步骤概括为三个主要种类:能修正物理性能如尺寸、形状、平整度、或一些体材料的性能;能减少不期望的表面损伤的数量;或能消除表面沾污和颗粒。硅片加工的主要的步骤如表1.1的典型流程所示。工艺步骤的顺序是很重要的,因为这些步骤的决定能使硅片受到尽可能少的损伤并且可以减少硅片的沾污。在以下的章节中,每一步骤都会得到详细介绍。 硅片加工过程步骤 1. 切片 2. 激光标识 3. 倒角 4. 磨片 5. 腐蚀 6. 背损伤 7. 边缘镜面抛光 8. 预热清洗 9. 抵抗稳定——退火 10. 背封 11. 粘片 12. 抛光 13. 检查前清洗 14. 外观检查 15. 金属清洗
16. 擦片 17. 激光检查 18. 包装/货运 切片(class 500k) 硅片加工的介绍中,从单晶硅棒开始的第一个步骤就是切片。这一步骤的关键是如何在将单晶硅棒加工成硅片时尽可能地降低损耗,也就是要求将单晶棒尽可能多地加工成有用的硅片。为了尽量得到最好的硅片,硅片要求有最小量的翘曲和最少量的刀缝损耗。切片过程定义了平整度可以基本上适合器件的制备。 切片过程中有两种主要方式——内圆切割和线切割。这两种形式的切割方式被应用的原因是它们能将材料损失减少到最小,对硅片的损伤也最小,并且允许硅片的翘曲也是最小。 切片是一个相对较脏的过程,可以描述为一个研磨的过程,这一过程会产生大量的颗粒和大量的很浅表面损伤。 硅片切割完成后,所粘的碳板和用来粘碳板的粘结剂必须从硅片上清除。在这清除和清洗过程中,很重要的一点就是保持硅片的顺序,因为这时它们还没有被标识区分。 激光标识(Class 500k) 在晶棒被切割成一片片硅片之后,硅片会被用激光刻上标识。一台高功率的激光打印机用来在硅片表面刻上标识。硅片按从晶棒切割下的相同顺序进行编码,因而能知道硅片的正确位置。这一编码应是统一的,用来识别硅片并知道它的来源。编码能表明该硅片从哪一单晶棒的什么位置切割下来的。保持这样的追溯是很重要的,因为单晶的整体特性会随着晶棒的一头到另一头而变化。编号需刻的足够深,从而到最终硅片抛光完毕后仍能保持。在硅片上刻下编码后,即使硅片有遗漏,也能追溯到原来位置,而且如果趋向明了,那么就可以采取正确的措施。激光标识可以在硅片的正面也可在背面,尽管正面通常会被用到。 倒角 当切片完成后,硅片有比较尖利的边缘,就需要进行倒角从而形成子弹式的光滑的边缘。倒角后的硅片边缘有低的中心应力,因而使之更牢固。这个硅片边缘的强化,能使之在以后的硅片加工过程中,降低硅片的碎裂程度。图1.1举例说明了切片、激光标识和倒角的过程。 磨片(Class 500k) 接下来的步骤是为了清除切片过程及激光标识时产生的不同损伤,这是磨片过程中要完成的。在磨片时,硅片被放置在载体上,并围绕放置在一些磨盘上。硅片的两侧都能与磨盘接触,从而使硅片的两侧能同时研磨到。磨盘是铸铁制的,边缘锯齿状。上磨盘上有一系列的洞,可让研磨砂分布在硅片上,并随磨片机运动。磨片可将切片造成的严重损伤清除,只留下一些均衡的浅显的伤痕;磨片的第二个好处是经磨片之后,硅片非常平整,因为磨盘是极其平整的。 磨片过程主要是一个机械过程,磨盘压迫硅片表面的研磨砂。研磨砂是由将氧化铝溶液延缓煅烧后形成的细小颗粒组成的,它能将硅的外层研磨去。被研磨去的外层深度要比切片造成的损伤深度更深。
硅片生产流程
硅片生产流程及主要设备 作为一种取之不尽的清洁能源,太阳能的开发利用正引起人类从未有过的极大关注。商业化太阳能电池采用的是无毒性的晶硅,单晶和多晶硅电池的特点是光电转换效率高、寿命长且稳定性好。硅片是晶体硅光伏电池加工成本中最昂贵的部分, 随着半导体制造技术的不断成熟完善,硅片制造成本不断降低。硅片切割是太阳能光伏电池制造工艺中的关键部分,太阳能电池所用硅片的切割成本一直居高不下,要占到太阳能电池总制造成本的30%以上。所以降低这部分的制造成本对于提高太阳能对传统能源的竞争力至关重要。目前硅片的切割方法都是围绕如何减小切缝损失、降低切割厚度、增大切片尺寸及提高切割效率方面进行的。 1.工艺流程:硅锭(硅棒)--切块(切方)--倒角抛光--粘胶--切片--脱胶清洗--分选检验、包装 2.工艺简介 切块/切方:将硅锭或者硅棒切成适合切片的尺寸,一般硅锭切成25 块(主流)。 倒角抛光:将晶柱的圆面棱角研磨成符合要求的尺寸,对表面进行抛光处理,从而获得高度平坦的晶片。 粘胶:用粘附剂把晶柱固定在由铝板和玻璃板组成的夹具上,自然硬化或用恒温炉使其硬化。 切片:把晶柱切割成硅片,切割的深度要达到夹具上的玻璃板,
以便在之后的程序中把硅片和玻璃板分开。 脱胶清洗:用清水清洗切成的硅片,再用热水浸泡,使硅片与玻璃板分开。 分选检验包装:抽样检查厚度、尺寸、抗阻值等指标,全部检查破损、裂痕、边缘缺口,挑选出符合要求的硅片进行包装。3.太阳能硅片切割方法 太阳能硅片切割方法主要有: 外圆切割、内圆切割和磨料线切割和电火花切割(WEDM )等。80年代中期之前的硅片切割都是由外圆切割机床或者内圆切割机床完成的, 这两种切割方法在那时的研究已经达到了鼎盛时期, 相当多功能的全自动切片机相继商品化, 生产主要分布在瑞士、德国、日本、美国等地方。 90年中后期以来, 多线切割技术逐渐走向成熟,其切缝损失小、切割直径大、成片效率高、适合大批量硅片加工, 在国内外太阳 能电池的硅片切割上,得到广泛的应用。WEDM 经过近半个世纪的发展, 技术已经十分成熟, 达到了相当高的工艺水平, 是一种非接触、宏观加工力很小的加工方式, 理论上采用WEDM 切割, 硅片的厚度可以达到很薄。 3.1外圆切割 外圆切割机主要有卧式和立式两种, 由主轴系统、冷却循环系统、工业机控制系统、电磁旋转工作台等组成, 其中主轴系统是它的核心系统, 刀片安装在主轴上面, 一般是在钢质圆片基体外圆部分电镀一层金刚石磨粒, 可以单刀切割或者多刀切割。
硅片生产过程详解
培训目的: 1、确定硅片生产过程整个目标; 2、为工艺过程确定一典型流程; 3、描述每个工艺步骤的目的; 4、在硅片生产过程中,硅片性能的三个主要关系的确定。 简介 硅片的准备过程从硅单晶棒开始,到清洁的抛光片结束,以能够在绝好的环境中使用。期间,从一单晶硅棒到加工成数片能满足特殊要求的硅片要经过很多流程和清洗步骤。除了有许多工艺步骤之外,整个过程几乎都要在无尘的环境中进行。硅片的加工从一相对较脏的环境开始,最终在10级净空房内完成。 工艺过程综述 硅片加工过程包括许多步骤。所有的步骤概括为三个主要种类:能修正物理性能如尺寸、形状、平整度、或一些体材料的性能;能减少不期望的表面损伤的数量;或能消除表面沾污和颗粒。硅片加工的主要的步骤如表1.1的典型流程所示。工艺步骤的顺序是很重要的,因为这些步骤的决定能使硅片受到尽可能少的损伤并且可以减少硅片的沾污。在以下的章节中,每一步骤都会得到详细介绍。 表1.1 硅片加工过程步骤 1.切片 2.激光标识 3.倒角 4.磨片 5.腐蚀 6.背损伤 7.边缘镜面抛光 8.预热清洗 9.抵抗稳定——退火 10.背封 11.粘片 12.抛光 13.检查前清洗 14.外观检查 15.金属清洗 16.擦片 17.激光检查 18.包装/货运
切片(class 500k) 硅片加工的介绍中,从单晶硅棒开始的第一个步骤就是切片。这一步骤的关键是如何在将单晶硅棒加工成硅片时尽可能地降低损耗,也就是要求将单晶棒尽可能多地加工成有用的硅片。为了尽量得到最好的硅片,硅片要求有最小量的翘曲和最少量的刀缝损耗。切片过程定义了平整度可以基本上适合器件的制备。 切片过程中有两种主要方式——内圆切割和线切割。这两种形式的切割方式被应用的原因是它们能将材料损失减少到最小,对硅片的损伤也最小,并且允许硅片的翘曲也是最小。 切片是一个相对较脏的过程,可以描述为一个研磨的过程,这一过程会产生大量的颗粒和大量的很浅表面损伤。 硅片切割完成后,所粘的碳板和用来粘碳板的粘结剂必须从硅片上清除。在这清除和清洗过程中,很重要的一点就是保持硅片的顺序,因为这时它们还没有被标识区分。 激光标识(Class 500k) 在晶棒被切割成一片片硅片之后,硅片会被用激光刻上标识。一台高功率的激光打印机用来在硅片表面刻上标识。硅片按从晶棒切割下的相同顺序进行编码,因而能知道硅片的正确位置。这一编码应是统一的,用来识别硅片并知道它的来源。编码能表明该硅片从哪一单晶棒的什么位置切割下来的。保持这样的追溯是很重要的,因为单晶的整体特性会随着晶棒的一头到另一头而变化。编号需刻的足够深,从而到最终硅片抛光完毕后仍能保持。在硅片上刻下编码后,即使硅片有遗漏,也能追溯到原来位置,而且如果趋向明了,那么就可以采取正确的措施。激光标识可以在硅片的正面也可在背面,尽管正面通常会被用到。 倒角 当切片完成后,硅片有比较尖利的边缘,就需要进行倒角从而形成子弹式的光滑的边缘。倒角后的硅片边缘有低的中心应力,因而使之更牢固。这个硅片边缘的强化,能使之在以后的硅片加工过程中,降低硅片的碎裂程度。图1.1举例说明了切片、激光标识和倒角的过程。 图1.1 磨片(Class 500k) 接下来的步骤是为了清除切片过程及激光标识时产生的不同损伤,这是磨片过程中要完成的。在磨片时,硅片被放置在载体上,并围绕放置在一些磨盘上。硅片的两侧都能与磨盘接触,从而使硅片的两侧能同时研磨到。磨盘是铸铁制的,边缘锯齿状。上磨盘上有一系列的洞,可让研磨砂分布在硅片上,并随磨片机运动。磨片可将切片造成的严重损伤清除,只留下一些均衡的浅显的伤痕;磨片的第二个好处是经磨片之后,硅片非常平整,因为磨盘是极其平整的。 磨片过程主要是一个机械过程,磨盘压迫硅片表面的研磨砂。研磨砂是由将氧化铝溶液延缓煅烧后形成的细小颗粒组成的,它能将硅的外层研磨去。被研磨去的外层深度要比切片造成的损伤深度更深。
半导体工艺流程
集成电路芯片生产的清洗包括硅片的清洗和工器具的清洗。由于半导体生产污染要求非常严格,清洗工艺需要消耗大量的高纯水;且为进行特殊过滤和纯化广泛使用化学试剂和有机溶剂。 在硅片的加工工艺中,硅片先按各自的要求放入各种药液槽进行表面化学处理,再送入清洗槽,将其表面粘附的药液清洗干净后进入下一道工序。常用的清洗方式是将硅片沉浸在液体槽内或使用液体喷雾清洗,同时为有更好的清洗效果,通常使用超声波激励和擦片措施,一般在有机溶剂清洗后立即采用无机酸将其氧化去除,最后用超纯水进行清洗,如图1-6所示。 图1-6硅片清洗工艺示意图 工具的清洗基本采用硅片清洗同样的方法。 2、热氧化 热氧化是在800~1250℃高温的氧气氛围和惰性携带气体(N2)下使硅片表面的硅氧化生成二氧化硅膜的过程,产生的二氧化硅用以作为扩散、离子注入的阻挡层,或介质隔离层。典型的热氧化化学反应为: Si + O2→SiO2
扩散是在硅表面掺入纯杂质原子的过程。通常是使用乙硼烷(B 2H 6)作为N -源和磷烷(PH 3)作为P +源。工艺生产过程中通常分为沉积源和驱赶两步,典型的化学反应为: 2PH 3 → 2P + 3H 2 4、离子注入 离子注入也是一种给硅片掺杂的过程。它的基本原理是把掺杂物质(原子)离子化后,在数千到数百万伏特电压的电场下得到加速,以较高的能量注入到硅片表面或其它薄膜中。经高温退火后,注入离子活化,起施主或受主的作用。 5、光刻 光刻包括涂胶、曝光、显影等过程。涂胶是通过硅片高速旋转在硅片表面均匀涂上光刻胶的过程;曝光是使用光刻机,并透过光掩膜版对涂胶的硅片进行光照,使部分光刻胶得到光照,另外,部分光刻胶得不到光照,从而改变光刻胶性质;显影是对曝光后的光刻胶进行去除,由于光照后的光刻胶和未被光照的光刻胶将分别溶于显影液和不溶于显影液,这样就使光刻胶上形成了沟槽。 6、湿法腐蚀和等离子刻蚀 通过光刻显影后,光刻胶下面的材料要被选择性地去除,使用的基片 涂胶后基片 光刻胶 阻挡层
多晶硅太阳能电池生产工艺.docx
太阳能电池光电转换原理主要是利用太阳光射入太阳能电池后产生电子电洞对,利用P-N 接面的电场将电子电洞对分离,利用上下电极将这些电子电洞引出,从而产生电流。整个生产流程以多晶硅切片为原料,制成多晶硅太阳能电池芯片。处理工艺主要有多晶硅切片清洗、磷扩散、氧化层去除、抗反射膜沉积、电极网印、烧结、镭射切割、测试分类包装等。 生产工艺主要分为以下过程: ⑴ 表面处理(多晶硅片清洗、制绒) 与单晶硅绒面制备采用碱液和异丙醇腐蚀工艺不同,多晶硅绒面制备采用氢氟酸和硝酸配成的腐蚀液对多晶硅体表面进行腐蚀。一定浓度的强酸液对硅表面进行晶体的各相异性腐蚀,使得硅表面成为无数个小“金字塔”组成的凹凸表面,也就是所谓的“绒面”,以增加了光的反射吸收,提高电池的短路电流和转换效率。从电镜的检测结果看,小“金字塔”的底边平均约为10um 。主要反应式为: 32234HNO 4NO +3SiO +2H O Si +???→↑氢氟酸 2262SiO 62H O HF H SiF +→+ 这个过程在硅片表面形成一层均匀的反射层(制绒),作为制备P-N 结衬底。处理后对硅片进行碱洗、酸洗、纯水洗,此过程在封闭的酸蚀刻机中进行。碱洗是为了清洗掉硅片未完全反应的表面腐蚀层,因为混酸中HF 比例不能太高,否则腐蚀速度会比较慢,其反应式为:2232SiO +2KOH K SiO +H O →。之后再经过酸洗中和表面的碱液,使表面的杂质清理干净,形成纯净的绒面多晶硅片。 酸蚀刻机内设置了一定数量的清洗槽,各股废液及废水均能单独收集。此过程中的废酸液(L 1,主要成分为废硝酸、氢氟酸和H 2SiF 6)、废碱液(L 2,主要成分为废KOH 、K 2SiO 3)、废酸液(L 3,主要成分为废氢氟酸以及盐酸)均能单独收集,酸碱洗后均由少量纯水洗涤,纯水预洗废液(S 1、S 2、S 3)和两级纯水漂洗废水(W 1),收集后排入厂区污水预处理设施,处理达标后通过专管接入清流县市政污水管网。 此过程中使用的硝酸、氢氟酸均有一定的挥发性,产生的酸性废气(G 1-1、G 1-2),经设备出气口进管道收集系统,经厂房顶的碱水喷淋系统处理达标后排放。G 1-2与后序PECVD 工序产生的G 5(硅烃、氨气)合并收集后经过两级水吸收处理后经排气筒排放。
单晶硅片制作工艺流程
单晶硅片制作工艺流程 The Standardization Office was revised on the afternoon of December 13, 2020
单晶硅电磁片生产工艺流程 ?1、硅片切割,材料准备: ?工业制作硅电池所用的单晶硅材料,一般采用坩锅直拉法制的太阳级单晶硅棒,原始的形状为圆柱形,然后切割成方形硅片(或多晶方形硅片),硅片的边长一般为10~15cm,厚度约200~350um,电阻率约1Ω.cm的p型(掺硼)。 ?2、去除损伤层: ?硅片在切割过程会产生大量的表面缺陷,这就会产生两个问题,首先表面的质量较差,另外这些表面缺陷会在电池制造过程中导致碎片增多。因此要将切割损伤层去除,一般采用碱或酸腐蚀,腐蚀的厚度约10um。 ? ? ?3、制绒: ?制绒,就是把相对光滑的原材料硅片的表面通过酸或碱腐蚀,使其凸凹不平,变得粗糙,形成漫反射,减少直射到硅片表面的太阳能的损失。对于单晶硅来说一般采用NaOH加醇的方法腐蚀,利用单晶硅的各向异性腐蚀,在表面形成无数的金字塔结构,碱液的温度约80度,浓度约1~2%,腐蚀时间约15分钟。对于多晶来说,一般采用酸法腐蚀。 ? ?4、扩散制结:
?扩散的目的在于形成PN结。普遍采用磷做n型掺杂。由于固态扩散需要很高的温度,因此在扩散前硅片表面的洁净非常重要,要求硅片在制绒后要进行清洗,即用酸来中和硅片表面的碱残留和金属杂质。 ? ?5、边缘刻蚀、清洗: ?扩散过程中,在硅片的周边表面也形成了扩散层。周边扩散层使电池的上下电极形成短路环,必须将它除去。周边上存在任何微小的局部短路都会使电池并联电阻下降,以至成为废品。目前,工业化生产用等离子干法腐蚀,在辉光放电条件下通过氟和氧交替对硅作用,去除含有扩散层的周边。 ?扩散后清洗的目的是去除扩散过程中形成的磷硅玻璃。 ? ?6、沉积减反射层: ?沉积减反射层的目的在于减少表面反射,增加折射率。广泛使用PECVD淀积SiN ,由于PECVD淀积SiN时,不光是生长SiN作为减反射膜,同时生成了大量的原子氢,这些氢原子能对多晶硅片具有表面钝化和体钝化的双重作用,可用于大批量生产。 ? ?7、丝网印刷上下电极:
多晶硅硅片生产流程
多晶硅硅片生产流程 (1)洗料 为得到纯净的多晶硅原料,须将多晶硅原料清洗,去除杂质和油污。将多晶硅料放入氢氟酸和硝酸中浸泡,然后用高纯水多次清洗,清洗干净后进入下一道工序。 b、烘料 将清洗干净的多晶硅原料放入烘箱中烘干。 c、装袋 烘干后的多晶硅原料按型号、电阻率分别包装。 d 、配料 根据生产需要将不同电阻率的多晶硅料加入母合金配制成符合要求的原料。(2)多晶铸锭阶段 a、准备阶段 经减压、放气后打开炉盖,清洁炉壁及石墨件,将清洗好的石英坩埚装入炉内。 b、投料 将配制好的多晶硅料500 公斤装入石英坩埚中,合上炉盖。检查水和泵油情况,正常后进入下一工序。 c、抽真空 密封炉盖后启动真空泵,将炉体内抽成真空,然后充入氩气。 d、化料 将坩埚加热到1420℃以上将多晶料融化。 e、定向凝固 多晶料全部融化后开始凝固多晶,开始时多晶每分钟生长0.8 mm~1.0 mm,长晶速度由工作台下移速度及冷却水流量控制,长晶速度近于常速,硅锭长度受设备及坩埚高度限制,当硅锭达到工艺要求时,凝固结束。停机使多晶炉降,约四个小时后将多晶锭取出。 f、检验
检验多晶锭的电阻率、寿命及氧炭含量,合格的进入下一道工序,不合格的作标记切断,部分可以回收重新铸锭。 (3)切片 a.多晶硅锭 将铸锭生产工序检测的硅锭清洗干净 b.切方 将硅锭固定在切方机上,要完全水平。固定好后切成方棒(6 英寸125mm×125m m;8 英寸156mm×156mm)。 c.抛光 将切好的方棒在抛光机上抛光。 e.清洗粘胶 将切方抛光好的方棒用超声波清洗机清洗干净后,粘在工件板的玻璃板上。 f.切片 将粘好硅棒的工件板按在切片机上(4 根),将硅片切成180微米厚的硅片。 g.脱胶 将切割好的粘在玻璃板上的硅片用70 度的热水将硅片与玻璃板分离 h.清洗 将脱过胶的硅片插在硅片盒中在超声波清洗机中清洗。清洗时先在常清水中清洗,然后在放有清洗剂的70度热水中清洗,最后在常清水中清洗。 i.甩干 将经过清洗的硅片连盒插在甩干机的甩干工位上甩干。 j.检片 将甩干好的硅片检测硅片TV 和TTV 及表面洁净度,并将硅片按等级分类。k.包装 该工艺方案具有简单,易操作,产品成品率高等特点。
硅片生产技术工艺
硅片生产工艺 硅片的生产工艺可以分成两个阶段, 拉单晶硅棒和切片抛光 多晶硅材(天然的) 拉单晶硅棒(CZ法) (译者注:直拉法(CZ)培育硅单晶) 在(CZ法)拉棒的过程中,天然多晶硅被放置在晶体拉制炉里面的石英坩埚里面,该石英坩埚被放置在石墨加热器环绕的石墨坩埚的.这些天然多晶硅在惰性气体或者真空里面被加热融化,然后用种子晶慢慢的拉出来. 单晶硅棒 一个完整的单晶硅棒长成之后就是这样的形状,一个直径D=200mm的单晶硅棒的重量在60到100公斤. 硅棒的外径滚磨 硅棒被切成一定的长度,同时外围被磨制成达到技术要求的外径. 一个方向标记或者一个奥痕添加在外围来表示晶体的生长方向. (译者注:我见到的晶棒多数都是在顶端打个标记, 周围有四根棱线,晶向为100). 这就是一个磨制完成的硅棒,周围磨制的痕迹可以通过直径和左顶端(这个图显示硅棒上面有个凹槽)
硅棒放在石墨架上面,硅片一片一片用内园切割机旋转钻石刀片.线切割通常用于直径200mm或者以上硅棒的切片. 倒角 硅片的周围用钻石工具区磨制达到产品直径的要求,进一步磨制将切割成的晶片税利边修整成圆弧形。 研磨 硅片放在一个两边都有纤维的旋转盒体里面,硅片两侧表面都进行磨制. 腐蚀(双面化学抛光) 硅片放在一个化学腐蚀的盒子里面旋转,用酸化的方式去除来自上一道工序的表面缺陷。 热处理,去处不稳定因素 热处理在扩散炉中进行,使在拉棒过程中带来的氧得以扩散,从而达到想要得电阻率. 抛光(有一面为镜面抛光) 指单晶硅片表面需要改善微缺陷,从而获得高平坦度晶片的抛光。 清洗 在单晶硅片加工过程中很多步骤需要用到清洗,这里的清洗主要是抛光后的最终清洗。清洗的目的在于清除晶片表面所有的污染源。