物料平衡

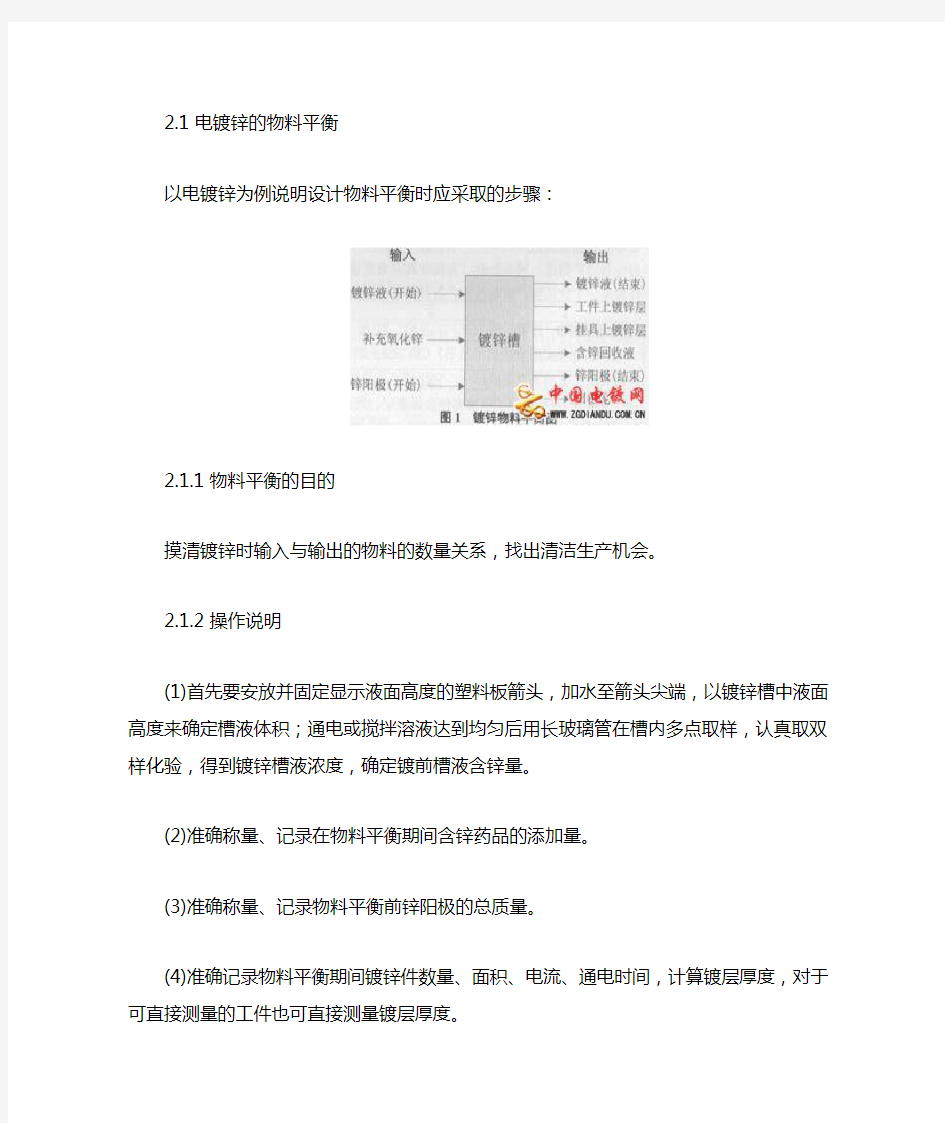
电镀清洁生产—物料平衡
摘要:根据多年的清洁生产审核实践,总结了电镀、热浸镀、磷化、电泳、酸洗、阳极氧化等表面处理工艺的物料平衡图。以电镀锌为例,介绍了建立物料平衡的操作方法。以某厂的镀铬槽为例,通过实际计算,讲解了如何根据物料平衡分析来提出清洁生产方案。
关建词;表面处理;清洁生产;审核;物料平衡
1前言
我国正处在难得的经济高速发展的机遇期,取得了世界瞩目的成就。如一切高速发展的国家一样,我国也遇到“资源短缺、环境污染加重”的压力。决策者们头脑清醒,深刻认识到这两个问题。在不久前,全国人大常委员会作出了修改《中华人民共和国清洁生产促进法》的决定,进一步加强清洁生产工作。清洁生产倡导的新理念是把过去“出了污染,事后处理”改变为“源削减”的环境保护方针。贯彻清洁生产工作的最好方法是实施清洁生产审核。在清洁生产审核程序中的审核阶段要求做“物料平衡”,通过实测审核重点的输入、输出值,经过计算、分析就可以发现问题,从而找到“节能、降耗、减污、增效”的清洁生产方案(或称清洁生产机会)。因此,设计好、做好“物料平衡”是清洁生产审核中很重要的一项工作。
从2006年以来,大连市表面工程协会先后完成了70余个企业的清洁生产审核的咨询工作。从各种电镀到热镀、磷化、酸洗、阳极氧化、电泳涂漆等工艺,都设计了相应的“物料平衡”方案,现将具体做法介绍如下,供同行参考和指正。
2一般电镀的物料平衡
2.1 电镀锌的物料平衡
以电镀锌为例说明设计物料平衡时应采取的步骤:
2.1.1 物料平衡的目的
摸清镀锌时输入与输出的物料的数量关系,找出清洁生产机会。
2.1.2 操作说明
(1)首先要安放并固定显示液面高度的塑料板箭头,加水至箭头尖端,以镀锌槽中液面高度来确定槽液体积;通电或搅拌溶液达到均匀后用长玻璃管在槽内多点取样,认真取双样化验,得到镀锌槽液浓度,确定镀前槽液含锌量。
(2)准确称量、记录在物料平衡期间含锌药品的添加量。
(3)准确称量、记录物料平衡前锌阳极的总质量。
(4)准确记录物料平衡期间镀锌件数量、面积、电流、通电时间,计算镀层厚度,对于可直接测量的工件也可直接测量镀层厚度。
(5)挂具吸收了电流,也应估算镀层面积和厚度。
(6)物料平衡结束时要调整镀锌溶液的液面高度,加水至箭头尖端;通电或搅拌溶液达到均匀;用长玻璃管多点取样;认真取双样化验,确定镀后槽液的含锌量。
(7)物料平衡期间准备一个镀锌后工件清洗、回收槽,清洗全部物料平衡期间的镀锌后工件,物料平衡结束时取样化验其含锌量,作为回收锌量。
(8)准确称量、记录物料平衡后锌阳极的总质量。
(9)物料平衡结束后要搜集阳极袋里的阳极泥,烘干后称量、记录。
(10)物料平衡结束后要收集过滤机滤芯上的阳极泥,烘干后称量、记录。
(11)统计物料平衡期间的总用水量。
2.1.3 计算与分析
(1)误差率(%)=(输入一输出)/输入×100%。
(2)金属利用率(%)=镀层总重÷纯输入×100%。
(3)新鲜水用量(t/m2)=物料平衡期间总用水量÷镀件总面积。
(4)镀件带出液污染物产生指标(g/m2)=回收槽浓度×回收槽体积÷镀件总面积。
2.2其他电镀工艺的物料平衡
图2~5列出其他镀种的物料平衡图,操作和计算可参照镀锌的有关内容。
2.3以大连某厂镀铬为例看物料平衡的意义2.
3.1数据
实测物料平衡的各种数据见表1。
2.3.2计算
(1)镀铬溶液输入(开始):开始金属盐浓度Pi×镀槽体积y÷单位换算系数。将铬酸酐换算成金属铬的系数为0.52。
东槽输入:
246.46 g/L×5 820L÷1 000=1434.4 kg铬酸酐;
1 434.4 kg×0.52=745.9 kg金属铬。
西槽输入:
227.30g/Lx6720L÷1000=1527.5kg铬酸酐;
1 527.5 kg×0.52=794.3 kg金属铬。
溶液总输入:745.9 kg+ 794.3 kg=1 540.2 kg金属铬。
(2)补充铬酸酐:铬酸酐重×换算系数。
20 kg×0.52=10.4 kg金属铬。
(3)镀铬溶液输出(结束):结束金属盐浓度P2×镀槽体积矿÷单位换算系数。东槽输出:
244.66g/L×5 820L-1000=1423.9kg铬酸酐;
1 423.9 kg×0.52=740.4 kg金属铬。
西槽输出:
224.06 g/L×6 720 L÷1 000=1505.7 kg铬酸酐;
1 505.7 kg×0.52= 783.0 kg金属铬。
溶液总输出:740.4 kg+ 783.0 kg=1 523.4 kg金属铬。
(4)工件上镀铬层:镀层体积×金属铬密度。
1 801 cm3×0.71 g/cm3÷1 000=1.28 kg金属铬。
(5)含铬回收液:回收槽金属盐浓度Pi×回收槽体积V÷单位换算系数。
0.16 g/L×360 L÷1 000×0.52=0.03 kg金属铬。
(6)铬雾回收液:铬雾回收液金属盐浓度ρl×铬雾回收液体积矿÷单位换算系数。
553 g/L×72.81 L÷1 000×0.52= 20.9 kg金属铬。
(7)挂具上镀层总重≈1 k g。
(8)铬雾逸出总重≈2kg。
(9)误差:(总输入一总输出)÷总输入×100%。
[(1 540.2+10.4) -(1 523.4+1.28+ 0.03+20.9 +1+2)]÷(1 540.2 +10.4)×100%= 1.99÷1 550.6×100%= 0.13%
(10)金属利用率。
不考虑回收:工件上镀铬层重÷纯输入。
1.28÷(1 540.2 -1 523.4 +10.4)×100%= 4.7%.
考虑回收:(工件上镀铬层重+含铬回收液+铬雾回收液)÷纯输入。
1.28+0.03+20.9)÷(1 540.2 -1 523.4+10.4)×100%=81.7%。
(11)镀件带出液污染物:回收液含金属盐÷镀层总面积÷单位换算系数。
0.03 kg÷(5 603.7 dm2/100)= 0.54 g/m2。
(12)新鲜水用量:全过程总用水量÷镀层总面积÷单位换算系数。
2.027÷(5 60
3.7 dm2/100)=0.036 t/m2. .
2.3.3 评价
与HJ/T 314-2006《清洁生产标准电镀行业》对照,评价该镀铬工艺的先进性,如表2所示。
2.3.4 绘制物料平衡图
根据上述计算绘制的物料平衡图如图6所示。
2.3.5 提出清洁生产方案
从实测结果及计算汇总来看,镀硬铬时真正消耗在镀层上的铬才1.28 kg,而铬雾回收液中却含相当于20.9 kg金属铬的铬酸酐。回收的铬酸酐质量浓度达到553 g/L,黏度很大,像酱油膏一样。可见必须做好铬雾回收工作。这就是清洁生产机会,也是一个好的清洁生产方案。
对于没有安装“铬雾回收器”的企业,要求尽快实现铬雾回收;对于“铬雾回收器”管理不善的企业,要求做好“防漏、及时回用”工作,因为跑掉的“铬雾”不仅仅是污染,失去的还有“利润”。
3热镀锌的物料平衡
热镀锌的物料平衡图见图7。国际锌协会CFC项目经理Rob White介绍的典型消耗数据见表3。
以大连某生产铁塔件和普通件的热镀锌厂物料平衡图为例,如图8所示。
总输出为11 350.9 +4 984+3 185+ 80= 19 599.9 (kg)。
锌灰占4 984÷19 599.9×100%= 25.4%;
锌渣占3 185÷19 599.9×100%=16.3%。
以上两项都大大超过典型消耗数据,生产中产生的锌灰和锌渣过多。寻找原因时发现,溶剂化槽里亚铁离子含量都高于国际和国内较好企业的标准(欧洲为0.5~3.0 g/L,台湾为5 g/L,大陆为5~10 g/L,而推荐值为l g/L)。
因为1kg铁离子可以和锌生成锌铁化合物,产生25 kg的锌渣,该厂原溶剂化槽里的助镀剂中含亚铁离子多达17 g/L,所以产生的锌渣特别多。笔者建议他们建立化验室,经常检测亚铁离子浓度,并采用加双氧水、提高pH沉淀铁的办法,使锌渣量大大降低,厂方非常满意。
4其他表面处理工艺的物料平衡
随着清洁生产审核工作的开展,陆续又遇到各种新的表面处理工艺,由于篇幅所限,不能详细介绍,现给出物料平衡图,恳请批评指正。
常温磷化物料平衡图见图9。
电泳涂漆物料平衡图见图10。
镀铁的物料平衡图见图lla,其中二价铁、三价铁平衡图见图llb。钢材酸洗的物料平衡图见图12。
新型的代磷化膜产品——皮膜剂处理工艺的物料平衡见图13。
铝硫酸阳极氧化的物料平衡图见图14,而能量平衡图见图15。
阳极氧化着色物料平衡图见图16。
5结语
在清洁生产审核中做“物料平衡”工作非常有意义,它可以定量反映审核重点的输入、输出各种物料、废弃物、能源等所占比例的关系,有利于直观地找到清洁生产机会,产生清洁生产方案。
物料平衡管理办法-13页文档资料
文件编号:Ⅲ-1.2〔2011〕138号批准人:王 竹民 物料平衡管理办法 1 目的 建立物料平衡管理规程,保证生产过程各种物料处于受控状态,确保投入与产出的平衡。 2 适用范围 本办法适用于公司所属各单位、部室、中心和销售总公司承钢分公司、采购总公司承钢分公司、国贸公司承德分公司。 3 定义 3.1 物料 指炼铁、炼钢、轧钢、钒产品等生产系统的主要原料、燃料、成品、半成品以及对生产成本具有较大影响的物品。包括:大宗原燃料、合金、辅料、备品备件、低值易耗品、机物料;成品、半成品、回收品、废料、废渣;来料加工物料及产品、外委加工物料及产品等。 3.2 物料平衡管理 运用平衡原理,从物资采购、验收入库,生产消耗,成品检化验、入库、销售出库、物料盘库等全程实施管控,保证实物流与信息流同步、账与物相符;做到进耗存平衡、投入产出实物流与金属平衡、产销存平衡。 通过物料平衡管理,对企业每个工序环节的物料进行投入产出的运行状态分析、评价、监督、调整,真实客观的反映物流状态。剔除人为的虚假因素,揭露物料转化、衔接过程中所产生的问题、矛盾,分析原因,为生产经营管理提供可靠的信息条件和核算基础,推动企业管理由粗放型向集约型转化,促使各项物料消耗的降低和经济效益的提高。 4 职责
4.1 组织机构和职责 4.1.1 成立物料平衡领导小组,负责公司物料平衡管理工作。 组长:公司主管领导 副组长:企业管理部部长 成员单位:企业管理部、财务部、生产计划部、能源环保部、设备管理部、物流管控中心、质量计量管控中心。 物料平衡办公室设在企业管理部。 4.1.2 物料平衡领导小组的职责 负责组织全公司物料管理工作,确定管理职责,起草、修订管理制度。审核确认各单位物料管理相关制度及实施细则;研究制定并动态维护相关物料损耗定额及预提与分摊方案;裁决争议,组织异常数据调查,提出处理意见。 4.2 物料平衡管理基本原则 按照“实物库存管理单位负责管理实物”组织物料平衡管理工作;实物库存管理单位,做好日常管理,动态跟踪进耗(出)存,核查实物量与ERP系统存货信息,确保帐物相符。一个工序环节的产出(发出),必须受到下道工序环节的承认;各有关部室、生产单位,明确一名主管领导负责此项工作,制定本单位仓储、盘点、物料平衡等物料管理实施细则,并报企业管理部审核备案。 4.3 各相关职能部门的职责 4.3.1 企业管理部:牵头组织相关单位,履行物料平衡领导小组职责,做好公司物料日常管理与平衡工作;负责对各物料管理责任单位进行物料管理与平衡工作业务指导,并组织按月检查、核实;组织各相关单位做好分工序产品的投入产出物料实物平衡、金属平衡月度报表工作;每季度(或根据公司特别要求)组织一次公司范围统一的存货盘点工作。
物料平衡计算公式
物料平衡计算公式 This model paper was revised by the Standardization Office on December 10, 2020
物料平衡计算公式: 每片主药含量 理论片重= 测得颗粒主药百分含量 1.原辅料粉碎、过筛的物料平衡 物料平衡范围: %~100 % 物料平衡= %100?+a c b a-粉筛前重量(kg) b-粉筛后重量(kg) c-不可利用物料量(kg) 2.制粒工序的物料平衡 物料平衡范围: %~ % 制粒工序的物料平衡= a d c b ++×100% 制粒工序的收率=a b ×100% a-制粒前所有原辅料总重(kg) b-干颗粒总重(kg) c-尾料总重(kg) d-取样量(kg) 3.压片工序的物料平衡范围: %~ % 压片工序的物料平衡=a d c b ++×100% 压片工序的收率=a b ×100%
a-接收颗粒重量(kg) b-片子重量(kg) c-取样重量(kg) d-尾料重量(kg) 4.包衣工序的物料平衡 包衣工序的物料平衡范围: %~ % 包衣工序的物料平衡 = b a e d c +++ 包衣工序的收率 = b a c + a-素片重量(kg) b-包衣剂重量(kg) c- 糖衣片重量(kg) d-尾料重量(kg) e-取样量(kg) 5.内包装工序物料平衡 内包装工序物料平衡范围: %~ % 包材物料平衡=%100?++++A a d c b B a- PTP 领用量(kg) b- PTP 剩余量(kg) A- PVC 领用量(kg) B- PVC 剩余量(kg) c-使用量(kg) d- 废料量(kg) 片剂物料平衡=%100?++a d c b a :领用量(Kg) b :产出量(Kg) c :取样量(Kg) d :废料量(Kg) 6.外包装工序的物料平衡
高炉冶炼物料平衡计算
高炉冶炼综合计算 1.1概述 组建炼铁车间(厂)或新建高炉,都必须依据产量以及原料和燃料条件作为高炉冶炼综合计算包括配料计算、物料平衡计算和热平衡计算。从计算中得到原料、燃料消耗量及鼓风消耗量等,得到冶炼主要产品(除生铁以外)煤气及炉渣产生量等基本参数。以这些参数为基础作炼铁车间(厂)或高炉设计。 计算之前,首先必须确定主要工艺技术参数。对于一种新的工业生产装置,应通过实验室研究、半工业性试验、以致于工业性试验等一系列研究来确定基本工艺技术参数。高炉炼铁工艺已有200余年的历史,技术基本成熟,计算用基本工艺技术参数的确定,除特殊矿源应作冶炼基础研究外,一般情况下都是结合地区条件、地区高炉冶炼情况予以分析确定。例如冶炼强度、焦比、有效容积利用系数等。 计算用的各种原料、燃料以及辅助材料等必须作工业全分析,而且将各种成分之总和换算成100%,元素含量和化合物含量要相吻合。 将依据确定的工艺技术参数、原燃料成分计算出单位产品的原料、燃料以及辅助材料的消耗量,以及主、副产品成分和产量等,供车间设计使用。配料计算也是物料平衡和热平衡计算的基础。 依据质量守恒定律,投入高炉物料的质量总和应等于高炉排出物料的质量总和。物料平衡计算可以验证配料计算是否准确无误,也是热平衡计算的基础。物料平衡计算结果的相对误差不应大于0.25%。 常用的热平衡计算方法有两种。第一种是根据热化学的盖斯定律,即按入炉物料的初态和出炉物料的终态计算,而不考虑炉内实际反应过程。此法又称总热平衡法。它的不足是没有反应出高炉冶炼过程中放热反应和吸热反应所发生的具体空间位置,这种方法比较简便,计算结果可以判断高炉冶炼热工效果,检查配料计算各工艺技术参数选取是否合理,它是经常采用的一种计算方法。 第二种是区域热平衡法。这种方法以高炉局部区域为研究对象,常将高炉下部直接还原区域进行热平衡计算,计算其中热量的产生和消耗项目,这比较准确地反应高炉下部实际情况,可判断炉内下部热量利用情况,以便采取相应的技术措施。该计算比较复杂。要从冶炼现场测取大量工艺数据方可进行。 1.2配料计算 一.设定原料条件 1、矿石成分: 表 1-1原料成分,%
物料平衡的管理规程
物料平衡的管理规程 1 目的 建立物料平衡的管理规程。建立物料平衡的审核标准,掌握生产过程中物料收率变化,防止差错和混药。 2 范围 适用于每个批次产品生产过程的关键工序都要进行物料平衡的计算及偏差处理。 3 职责 生产技术部部长、生产车间主任、工艺员、操作工,QA监控员。 岗位操作人员负责本岗位平衡的计算,并对计算结果进行判断; 生产车间主任负责批平衡收率的计算,工艺员负责各岗位平衡收率的审核及对出现偏差进行分析和说明; QA负责批生产平衡的审核。 4 内容 物料平衡是产品或物料实际产量或实际用量及收集到的损耗之和与理论产量或理论用量之间的比较,并考虑可允许的偏差范围。 物料平衡的计算是为了防止物料误用和非正常流失 每个品种各关键生产工序的批生产记录(批包装记录)都必须明确规定平衡的计算方法,以及根据验证结果和生产实际确定的平衡限度范围。 物料平衡计算: 产出量+废品量+剩余量 物料平衡=×100%(99-100%) 投入量 投入量:领料的净量。 产出量:为生产过程中实际产出量,包括合格产品和不合格产品。 废品量:过程抛撒受污染后收集的扫地料及检测后不能再使用的产品或料粉。 物料平衡计算单位: 4.5.1 中间产品、成品:中间体采用重量单位(kg);说明书、包装袋、包装盒、包装箱等,
分别采用“张”、“只”、“套”、“个”计算。 结果处理: 4.6.1 凡物料平衡在规定平衡限度范围之内,经质量部QA检查确认后,产品可以递交下工序。 4.6.2 凡物料平衡超出规定平衡限度范围的,应立即贴示“待验”标志,产品不得递交下工序,操作工应及时填写《偏差通知单》,通知生产车间主任及QA监控员按《生产过程偏差处理管理规程》中有关偏差处理程序进行调查,采取处理措施,并详细记录。 4.6.2.1 每个关键工序必须进行物料平衡计算,物料平衡计算是避免或及时发现差错的有效方法之一。因此每个品种各关键生产工序的批生产记录都必须明确规定物料平衡计算的方法,以及根据验证结果确定物料平衡合格范围。 4.6.2.2 物料平衡计算的基本要求: 4.6.2. 物料平衡计算: 实际值 物料平衡= ×100% 计划值 其中: 计划值:为批生产指令规定的各种物料投料量。 实际值:为生产过程中实际产出量, 包括:本工序产出量。 收集的废品量。 取样量。 丢弃的不合格物料(如捕尘系统、真空系统、管理系统中收集的残余物)。 4.6.2. 在生产过程中如有跑料现象,应及时通知生产车间主任及QA监控员,并详细记录跑料过程及数量。跑料数量也应计入物料平衡之中,加在实际值的范围之内。 5 饮片生产需进行物料平衡计算的主要工序。 净制、切烘、炒制、包装。 物料平衡的计算单位:以重量计算(饮片袋、纸箱等无法用重量计算的可用数量计)。 6 数据处理 凡物料平衡在合格范围之内,经QA监控员签字后,递交中间站或下工序。 凡物料平衡高于或低于合格范围,操作工应及时填写《偏差通知单》,通知生产车间主任及QA监控员按《生产过程偏差处理管理规程》中有关偏差处理程序进行调查,采取处理措施,并详细记录。
片剂中物料平衡计算
片剂物料平衡的计算 (1)整粒终混平衡的计算 A=总投料量(kg) B=合格颗粒量(kg) C=不合格颗粒量(kg) D=取样量(kg) B + C + D 平衡= --------------------×100% 应为95%~102% A (2)整粒终混得率的计算 得率=B/A×100% (3)压片平衡的计算 A=合格颗粒重量(kg) B=不合格品重量(kg) C=合格片重量(kg) D=取样量(kg) B + C + D 平衡=------------------×100% 应为95%~100% A (4)压片得率的计算 得率=C/A×100% (5)包装平衡的计算 A:领取素片重量(kg) B:包装数量(片) C:平均片重(kg) D:内包装不合格品量(kg) E:外包装不合格品量(kg)
平衡=(B×C÷1000+D+E)/A×100% 应为95%~102%(6)包装得率的计算 得率=(B×C÷1000)/A×100% (7)批平衡的计算 A:总投料量(kg) B:包装数量(片) C:制粒不合格品量(kg) D:制粒取样量(kg) E:压片不合格品量(kg) F:压片取样量(kg) G:内包装不合格品量(kg) H:外包装不合格品量(kg) B×平均片重÷1000+C+D+E+F+G+H 平衡=-------------------------------- ×100% (应为95%~102%) A (8)批得率的计算 得率=B×平均片重÷1000/A×100% (9)内包材平衡的计算 A:使用量(kg) B:合格药板数量(板) C:不合格药板数量(板) D:未冲裁报废铝箔(米) E:铝塑板的宽(米)
物料平衡计算公式:
物料平衡计算公式: 每片主药含量 理论片重= 测得颗粒主药百分含量 1.原辅料粉碎、过筛的物料平衡 物料平衡范围:97.0 %~100 % 物料平衡= %100?+a c b a-粉筛前重量(kg) b-粉筛后重量(kg) c-不可利用物料量(kg) 2.制粒工序的物料平衡 物料平衡范围:98.0 %~104.0 % 制粒工序的物料平衡= a d c b ++×100% 制粒工序的收率=a b ×100% a-制粒前所有原辅料总重(kg) b-干颗粒总重(kg) c-尾料总重(kg) d-取样量(kg) 3.压片工序的物料平衡范围:97.0 %~100.0 % 压片工序的物料平衡= a d c b ++×100% 压片工序的收率=a b ×100% a-接收颗粒重量(kg) b-片子重量(kg) c-取样重量(kg) d-尾料重量(kg) 4.包衣工序的物料平衡 包衣工序的物料平衡范围:98.0 %~100.0 % 包衣工序的物料平衡 = b a e d c +++ 包衣工序的收率 = b a c +
a-素片重量(kg) b-包衣剂重量(kg) c-糖衣片重量(kg) d-尾料重量(kg) e-取样量(kg) 5.内包装工序物料平衡 内包装工序物料平衡范围:99.5 %~100.0 % 包材物料平衡=%100?++++A a d c b B a- PTP 领用量(kg) b- PTP 剩余量(kg) A- PVC 领用量(kg) B- PVC 剩余量(kg) c-使用量(kg) d-废料量(kg) 片剂物料平衡=%100?++a d c b a :领用量(Kg) b :产出量(Kg) c :取样量(Kg) d :废料量(Kg) 6.外包装工序的物料平衡 包装材料的物料平衡范围:100% 包装材料物料平衡=%100?+++e a d c b e-上批结存 a-领用量 b-使用量 c-剩余量 d-残损量 7.生产成品率 成品率范围:90%~102% 片剂收率= %100?++a d c b a-计划产量 b-入库量 c-留样量 d-取样量
物料平衡管理制度
XXXX药业有限公司生产管理制度 1 目的:及时掌握各车间生产过程中收率的变动情况,以加强生产过程的管理。 2 范围:生产过程中物料平衡的监控 3 责任:车间技术主任、班组长、QA监督员 4 内容: 4.1 生产过程中的投料、配料计算、称量要有人复核;操作人和复核人均应填写姓名及日期,对于贵细、毒性药材或饮片应按规定双人监控投料,并有详细记录。 4.2 车间负责人或工艺员按物料平衡的计算规定对关键工序中间产品物料平衡收率进行计算。 4.3 平衡收率的计算方法必须按规定的计算方法计算,并核对是否符合规定范围,如确认符合规定,则签字转下道工序;如出现偏差,则按 5.9项规定进行。 4.4 在生产过程中如有跑料现象,应及时通知车间负责人,并详细记录跑料过程及数量,跑料数量应计入物料平衡收率的计算中。 4.5 在称量及复核过程中,每个数值都必须符合规定,如有差异,必须及时分析,上报,做出合理满意的解释后才能有车间负责人与QA监督员共同签字,递交下工序,同时记录,记录上应有参加分析处理人员的签字。
4.6 每个产品都应明确规定各质量监控点的收率标准、合理的偏差范围及计算方法。当收率超出了合理范围,车间应会同质量管理人员对工艺过程、设备、原料及产品方面进行综合调查,得到合理解释并经质保部确认不影响产品质量后方可放行至下工序。包装材料应按批包装指令领用计数发放,核对,发料人、领料人及核对人均应签名。 4.7 车间每个产品批次生产结束后,必须计算出本工序的收率,使用物料与剩余物料数量之和要与物料实际领用量相符或在允许偏差范围内。 4.8 一个批号产品完成后,由车间操作负责人按照产品的不同物料平衡监控点,填写物料平衡表,交QA监督员复核签字后归批生产记录。 4.9 偏差处理 4.9.1 凡收率高于或低于规定范围,应在状态标识中注明“待查”,不能递交下工序。 4.9.2 由工艺员或工序班组长填写偏差处理单,写明品名、批次或批号、?规格、数量、工序偏差内容、发生的过程及原因、填表人签字、注明日期,将偏差处理单交车间管理人员,并报生产部和质保部。 4.9.3 车间负责人会同生产部和质保部进行调查,根据调查结果提出处理意见和措施。 4.9.3.1 确认不影响产品最终质量的情况下继续加工。 4.9.3.2 确认不影响产品质量的情况下进行返工,或采取补救措施。 4.9.3.3 确认不影响产品质量的情况下,采取再回收、再利用措施。 4.9.3.4 确认影响产品质量,按不合格产品处理程序进行处理。 4.9.4 车间管理人员将调查结果及需采取的措施,写出书面报告附偏差处理单之后,上报质保部,经质保部部长审核,签字批准后送车间。
GCr9物料平衡计算
一、物料平衡计算 (1) 1、计算所需原始数据 (1) 2、物料平衡基本项目 (2) 3、计算步骤 (2) 二、热平衡计算 (9) 1、计算热收入Q s (9) 2、计算热支出Q z (11) 三、电弧炉炉型及主要参数 (12) 参考文献 (15)
一、物料平衡计算 1、计算所需原始数据 基本原始数据:冶炼钢种及成分(见表1);原材料成分(见2);炉料中元素烧损率(见表3);其他数据(见表4) 表1 冶炼钢种及其成分 钢种 成分(%) 备注C Si Mn P S Cr Fe GCr9 1.00~ 1.10/1.05 0.15~ 0.35/0.25 0.20~0.40 ≤0.027 ≤0.020 0.90~ 1.20 余量氧化法 注:分母系计算时的设定值,取其成分中限。 表2 原材料成分(%) 名称C Si Mn P S Cr Al Fe H2O灰分挥发分碳素废钢0.18 0.25 0.55 0.030 0.030 余量 炼钢生铁 4.20 0.80 0.60 0.200 0.035 余量 焦炭81.50 0.58 12.40 5.52 电极99.00 1.00 名称CaO SiO2MgO Al2O3CaF2Fe2O3CO2H2O P2O5S 石灰88.00 2.50 2.60 1.50 0.50 4.64 0.10 0.10 0.06 铁矿石 1.30 5.75 0.30 1.45 89.77 1.20 0.15 0.08 火砖块0.55 60.80 0.60 36.80 1.25 高铝砖 1.25 6.40 0.12 91.35 0.88 镁砂 4.10 3.65 89.50 0.85 1.90 焦炭灰分 4.40 49.70 0.95 26.25 18.55 0.15 电极灰分8.90 57.80 0.10 33.10 表3 炉料中元素烧损率 成分C Si Mn P S 烧损率(%)熔化期25~40,取30 70~95,取 85 60~70,取 65 40~50,取 45 可以忽略 氧化期0.06①全部烧损20 0.015②25~30,取27 ①按末期含量比规格下限低0.03%~0.10%(取0.06%)确定(一般不低于0.03%的脱碳量); ②按末期含量0.015%来确定
物料平衡
题目:物料平衡管理制度 制定人:年月日编码:GLSC00500 审核人:年月日颁发部门:质量管理部 批准人:年月日执行时间:年月日 分发部门:生产管理部、前处理车间、制剂车间、档案室: 目的:加强物料平衡的管理,防止差错和混淆事故的发生。 范围:适用于每批产品生产过程中的物料平衡管理。 职责:生产管理部、各生产车间、QA员、生产操作工。 内容: 一、制剂生产必须按照批生产指令所要求的处方量的100%(标示量)投料。 二、进行物料平衡检查是避免或及时发现差错与混淆的有效方法之一,每批产品应按产量和数量平衡。 三、物料平衡是产品(或物料)的理论产量(或理论用量)与实际产量(或实际用量)之间的比较,并有可允许的正常偏差。 四、生产过程的关键工序进行物料平衡检查,检查结果必须符合物料平衡规定的限度。 需要进行物料平衡检查的工序: 固体制剂:制粒、总混、压片(块)、分装、包衣、贴签、包装后成品。 液体制剂:配制、灌装、灭菌、灯检、包装。 提取:净制、浓缩。 五、物料平衡规定限度是根据生产实际情况、产品工艺验证、生产消耗定额等确定的一个适当的百分比值范围。 六、每批产品生产作业完成后进行物料平衡检查,若超过规定限度,必须进行偏差分析,查明原因,在得出合理解释确认无潜在质量事故后,方可按正常产品处理。 七、物料平衡计算公式: 实际值 ×100% 理论值 实际值:为生产过程中实际产出量(包括本工序产出量、收集废品量、取样量、留样量及丢弃的不合格物量);
理论值:为按照所用的原料(或包装材料)在生产中无任何损失或差错情况下得出的最大数量; 八、物料平衡的计算单位 (1)固体制剂进行物料平衡计算时以重量计算。 (2)液体制剂: 第1 页共2 页 ①包装前以体积计算 ②包装后以“万支”计算 ③分装过程: 分装药液体积(ml) = 支 平均装量(ml) (3)中药前处理、提取: ①固体以重量计算 ②液体以体积计算。 九、物料平衡计算结果经QA员复核,确认结果符合规定的限度范围,方可移交下工序。 十、各工序物料平衡检查种类及正常的偏差限度要求遵照工艺规程。
全厂物料平衡表
经典语录 1、最疼的疼是原谅,最黑的黑是背叛。 2、我有没有跟你说过爱是我不变的信仰,我有没有告诉过你爱就是永远把一个人放在心上。 3、我们生活在同一个温暖的水域,也许偶尔会被水草缠绕,但因为彼此温暖的呼吸,相信都不会是死结。如果我说我爱你,我一直爱你,不知道你会不会相信? 4、恋爱就是这么突如其来的一件事,从开始到慢慢进行,每一个细节都不可思议百转千回。 5、爱情只是宿命摆下的一个局。 6、幸福是什么。幸福,是照射在脸上的温暖阳光,瞬间就成了阴影。
7、我独自守候着岁月的轮回,等待那千年的梦。蓦然回首,青春的花,在那烟雨蒙蒙中遗失了心,却在这和煦阳光下找到了魂。终于了悟了那埋藏已久的心。于是,我轻轻的笑了。 8、人犹如深海里浮浮沉沉,一波一波的海水带着压力冲过来,要将自己深深地淹没,再淹没。 9、爱情如果只剩下同情,就算回到身边,又有何意义? 10、友情其实和爱情一样,很多的时候,距离才可以让彼此懂得。 11、爱一个人不是要拥有他,只要在远方默默地注视他,也就心满意足。 12、有一种隐忍其实是蕴藏着的一种力量,有一种静默其实是惊天的告白。 13、孤单不是与生俱来,而是由你爱上一个人的那一刻开始。 14、结婚时,会说“我愿意”。愿意什么呢?不是愿意爱你,而是愿意只爱你。不是愿意和你在一起,而是愿意只和你一起。不是愿意得到你,而是愿意为你而放弃别人。不是愿意接受幸福,而是愿意给你幸福。这句“我愿意”,是个天大的承诺,代表唯一、忠诚和责任……你愿意么? 15、希望的未来那么遥远,不想面对的将来总是不期而遇,对未来抱有不切实际幻想,以及对未来残酷认识不足,使人产生上面判断,对影响未来主要因素的变化判断准确,就能把握事物未来结果,采取行动应对,能使未来向好,既便困难到来,也会有所准备使损害最小,应对未来有效手段是立足当下,采取行动。 16、一句我等你,不知道需要多大的勇气。它远比我爱你三个字,更需要勇气。不是每个人你都愿意等待,也不是所有人都值得你去等待。一句我等你,包含了很多的无奈,心酸,苦涩。或许是爱不到,或许是不能爱,无论怎样,我等你这个承诺,远比我爱你更动听。可是有多少的爱情经得起等待。
干燥过程的物料平衡与热平衡计算
干燥过程的物料与热平衡计算 1、湿物料的含水率 湿物料的含水率通常用两种方法表示。 (1)湿基含水率:水分质量占湿物料质量的百分数,用ω表示。 100%?= 湿物料的总质量 水分质量 ω (2)干基含水率:由于干燥过程中,绝干物料的质量不变,故常取绝干物料为基准定义水分含量。把水分质量与绝干物料的质量之比定义为干基含水率,用 χ表示。 100%?= 量 湿物料中绝干物料的质水分质量 χ (3)两种含水率的换算关系: χ χ ω+= 1 ω ω χ-= 1 2、湿物料的比热与焓 (1)湿物料的比热m C 湿物料的比热可用加和法写成如下形式: w s m C C C χ+= 式中:m C —湿物料的比热,()C kg J ?绝干物料/k ; s C —绝干物料的比热,()C kg J ?绝干物料/k ; w C —物料中所含水分的比热,取值4.186()C kg J ?水/k (2)湿物料的焓I ' 湿物料的焓I '包括单位质量绝干物料的焓和物料中所含水分的焓。(都是以0C 为基准)。 ()θθχθχθm s w s C C C C I =+=+='186.4 式中:θ为湿物料的温度,C 。
3、空气的焓I 空气中的焓值是指空气中含有的总热量。通常以干空气中的单位质量为基准称作比焓,工程中简称为焓。它是指1kg 干空气的焓和它相对应的水蒸汽的焓的总和。 空气的焓值计算公式为: ()χ1.88t 24901.01t I ++= 或()χχ2490t 1.881.01I ++= 式中;I —空气(含湿)的焓,绝干空气kg/kg ; χ—空气的干基含湿量,绝干空气kg/kg ; 1.01—干空气的平均定压比热,K ?kJ/kg ; 1.88—水蒸汽的定压比热,K ?kJ/kg ; 2490—0C 水的汽化潜热,kJ/kg 。 由上式可以看出,()t 1.881.01χ+是随温度变化的热量即显热。而χ2490则是0C 时kg χ水的汽化潜热。它是随含湿量而变化的,与温度无关,即“潜热”。 4、干燥系统的物料衡算 干燥系统的示意图如下: (1)水分蒸汽量W 按上述示意图作干燥过程中的0水量与物料平衡,假设干燥系统中无物料损失,则: 2211χχG LH G LH +=+ 水量平衡 G 1
MES系统中物料平衡的设计与实现.
MES 系统中物料平衡的设计与实现 石油炼制企业在不断的发展壮大,对信息技术和综合自动化系统的需求也在持续变化。本文通过以制造执行系统 (Manufacturing Execution System , MES 技术为代表的信息化整合优化集成,企业可以显著降低成本、提高竞争力和增强抗风险能力,因此, MES 技术的研究与应用成了整个流程工业综合自动化技术发展的关键之一。本文内容涵盖了物料平衡模块的各个关键技术点,主要包括物料平衡数据的归并与审核、平衡数据的校正,为全公司 MES 系统的实施奠定了坚实的基础。 1 绪论 目前, 以信息集成为核心的企业综合自动化系统在国内外的许多企业已经投用, 并且取得良好的使用效果。实践表明它能够将先进的、科学的管理方法更好地应用于化工企业, 将生产管理的经验和领域专家的知识结合起来, 协调并参与实时生产管理过程, 再结合产品的市场行情,搞好市场分析,形成最佳的生产结构,从而创造更大的经济效益。 20世纪 90年代,我国化工企业基础自动化建设与改造基本完成,部分企业还实施了 ERP(Enterpdse Resource Planning , 企业资源规划 , 但因缺乏将ERP 和控制系统集成连接在一起的中间层, ERP 的实施效果受到了极大的限制,信息化建设进程一度陷入窘境。 MES(Manufacturing Execution System,生产执行系统是支撑企业生产管理层业务运行和管理的信息系统,恰好能填补这一空白。 MES 是处于计划层和现场自动化系统之间的执行层, 主要负责车间生产管理和调度执行。一个设计良好的 MES 系统可以在统一平台中集成诸如生产调度、产品跟踪、质量控制、设备故障分析、网络报表等管理功能,使用统一的数据库和通过网络联接可以同时为生产部门、质检部门、工艺部门、物流部门等提供车间管理信息服务。系统通过强调制造过程的整体优化来帮助企业实施完整的闭环生产, 协助企业建立一体化和实时化的 ERP /MES /SFC 信息体系。 MES 直到 1990年, 才由美国的 AMR(Advanced Manufaeturing Research提出并使用。 20世纪 90年代初,工业界开始认识到需要一个可以将业务系统和控制系统集成在一起的中间层。制造执行系统 (MES从一开
物料平衡管理规定
物料平衡管理规定
受控状态: 1目的 建立物料平衡的管理办法,保证生产过程中物料衡算处于受控状态。防止差错和混淆。 2范围 生产中所有物料及主要工序的收率控制。 3责任 生产科、技术科、质监科、生产车间、质监员、工艺员、统计员。 4参考文件 GMP文件之物料平衡。 5内容
5.1 生产各环节应把建立物料平衡检查标准、物料消耗定额产成品的收率变化,并进行严格控制作为生产管理中防止差错和混淆的一项重要工作来做。 5.2 需要计算收率的主要工序: 5.2.1 配制: a、在含量保证的前提下,合理控制配液收率在97~101%之 间。 b、在物料称量、配液、料液管输等转移过程中,防止损失跑 料的漏液。 5.2.2 过滤: a、操作过程中检查管道、阀门的密封,防止损失。 b、贮罐、管道内药液尽可能抽尽。 c、提高灯检一次合格率。 5.2.3 灌封: a、控制装量差异在合格范围中线。 b、操作工应熟练操作,减少灌封过程的不合格品。 c、灌封不合格的应及时回收。 5.2.4 灭菌: a、熟练掌握对澄明度标准的正确判断,减少误判。 b、灌封不合格的应及时回收利用。 5.2.5 成品:应控制收率在95%以上。 5.3 凡收率在合格范围内,经持管部门检查签发”传递证”能够
递交下道工序。 5.4 凡收率高于或低于允许范围者,应立即贴上”待查”标志不能递交下道工序,通知车间管理人员及质管部门质管员”按偏差处理SOP”进行调查。采取处理措施,并详细记录。 6培训 6.1 培训对象:工艺员、质监员、洁净区班长、包装班长、配液岗位操作工。 6.2 培训时间:二小时。
流程框图和物料平衡标准框图
高铝粉煤灰预脱硅-碱石灰烧结法生产氧化铝 工艺流程标准化框图 (主产品)
高铝粉煤灰预脱硅-碱石灰烧结法生产氧化铝工艺流程标准化框图文字说明: (一)粉煤灰预处理 高铝粉煤灰与氢氧化钠溶液按照一定的比例混合形成粉煤灰浆液,进入预脱硅工序,在一定的反应温度、压力和反应时间下,粉煤灰浆液中高铝粉煤灰与NaOH溶液发生反应,生成含有硅酸钠溶液的脱硅粉煤灰浆液,通过泵输送进入分离与洗涤工序,在此工序内,通过分离设备完成固相(脱硅粉煤灰)和液相(硅酸钠溶液)的分离,固相(脱硅粉煤灰)送往生料浆制备工序,液相(硅酸钠溶液)送往活性硅酸钙制备工序,添加石灰乳进行反应生成副产品活性硅酸钙,并回收氢氧化钠溶液进入蒸发工序,蒸发后进入预脱硅工序使用。(二)熟料制备 将脱硅粉煤灰、石灰石、无烟煤及碳分蒸发来的碳分母液(Na2CO3)按照碱比、钙比、水分要求在生料浆制备工序制备成合格生料浆,由生料浆输送泵送入熟料烧结工序回转窑窑尾,通过在回转窑窑头喷入的煤粉燃烧形成的热量进行烧结,形成主要成为铝酸钠、硅酸二钙、钛酸钙等的熟料,熟料经过中碎系统送往熟料仓。 (三)铝酸钠溶液制取 来自熟料仓中熟料进入熟料溶出工序,通过与调整液混合溶出形成溶出浆液,溶出浆液经分离后形成固相(硅钙渣)和液相(铝酸钠粗液),固相(硅钙渣)送硅钙渣脱碱工序与电石渣进行反应,生成碱含量符合要求的副产品硅钙渣,液相(铝酸钠粗液)进入一段脱
硅工序,经过高温高压一段脱硅反应后,一部分铝酸钠溶液送往种分工序,另一部分铝酸钠溶液继续添加石灰乳进行深度脱硅反应,反应后的铝酸钠精液送往碳分工序。 (四)氧化铝的制取 送往碳分工序的铝酸钠精液在碳分槽中通入二氧化碳进行连续碳酸化分解,分解生成的氢氧化铝经种子过滤机进行过滤,滤饼送往种分工序作为晶种,滤液送蒸发工序进行回用。由一段脱硅工序送来的铝酸钠溶液与碳分工序送来的氢氧化铝晶种进行混合降温,形成高固含的氢氧化铝浆液送往成品过滤工序,通过过滤机进行分离与洗涤,液相送往蒸发,固相氢氧化铝送往焙烧工序,通过焙烧炉将氢氧化铝生产成冶金级的氧化铝(主产品)。
物料平衡管理规程
物料平衡管理规程 目的:建立物料平衡的工作标准,控制物料的误用或非正常流失,避免差错和混淆。 范围:每个批次产品生产过程的关键工序。 责任人:操作员、车间工艺员、车间主任、生产部部长、QA员。 内容: 1产品(或物料)的理论产量(或理论用量)与实际产量(或实际用量)之间的比值应有可允许的正常偏差。 1.1在每个关键工序进行物料平衡是避免或及时发现差错与混淆的有效方法之一。因此,每个品种各关键生产工序的批生产记录、批包装记录都必须明确规定物料平衡的计算方法,以及根据验证结果确定的物料平衡允许范围(控制指标详见各产品工艺规程)。 1.2 每批产品应在生产完成后,立刻做物料平衡检查。 2物料平衡检查的基本要求 2.1计算公式 实际值 ×100% 理论值 其中: 理论值:为按照所用的原料(包装材料)量,在生产中无任何损失或差错的情况下得出的最大数量。 实际值:为生产过程中实际产出量,包括:本工序产出量;收集的废品量;生产中取样量(检品); 2.2 在生产过程中如有跑料现象,应及时通知车间主任及QA员,按《生产过程偏差处理管理规程》(编号SMP-SC-SG-011)处理,并详细记录跑料过程及数量。跑料数量也应计入物料平衡之中,加在实际值的范围之内。 3各关键工序进行物料平衡的计算方法 3.1粉碎工序: 细粉总量 ----------------------------------- ×100% 净药材重量(或干膏重量) 3.2制粒工序: 颗粒总量+本批尾料量-上批尾料量 --------------------------------------------------------×100% 投料量 3.3批混工序: 批混后细粉重量+取样量 ------------------------------------------------------ ×100%
加氢裂化装置物料平衡
加氢裂化装置物料平衡 一、某石油化工科学研究院提供的物料平衡数据(w%)
第四节工艺流程说明 一、反应部分 (工艺流程图见-??) 原料油从蒸馏装置或罐区进入原料缓冲罐(D-101),经升压泵(P-101)升压后,再经过过滤(SR-101),进入滤后原料油缓冲罐(D-101)。原料油经反应进料泵(P-102)升压后与混合氢混和,混氢原料油与反应产物换热(E-101),然后进入反应进料加热炉(F-101)加热。混氢原料油在反应进料加热炉内加热至所需的温度后进入加氢精制反应器(R-101),然后进入加氢裂化反应器(R-102),在催化剂的作用下,进行加氢反应。催化剂床层间设有控制反应温度的急冷氢。反应产物经与混氢原料油换热后,进入热高压分离器(D-103)。 装置外来的补充氢由新氢压缩机(K-101)升压后与循环氢混和。混和氢先与热高分气进行换热,再和原料油混和。 从热高压分离器分离出的液体(热高分油)先经液力透平(HT-101)降压回收能量,或经调节阀降压,减压后进入热低压分离器进一步在低压将其溶解的气体闪蒸出来。气体(热高分气)与冷低分油和混合氢换热,最后由热高分气空冷器(A-101)冷却至55℃左右进入冷高压分离器,进行气、油、
水三相分离。为防止热高分气中NH3和H2S在低温下生成铵盐结晶析出,堵塞空冷器,在反应产物进入空冷器前注入除盐水。 从冷高压分离器分离出的气体(循环氢),经循环氢脱硫后进入循环氢压缩机分液罐缓冲(D-108),由循环氢压缩机(K-102)升压后,返回反应部分同补充氢混合。循环氢脱硫所用贫胺液来自渣油加氢。自循环氢脱硫塔底出来的富胺液去渣油加氢富胺液闪蒸罐闪蒸。从冷高压分离器分离出的液体(冷高分油)减压后进入冷低压分离器,继续进行气、油、水三相分离。冷高分底部的含硫污水减压后送出装置至污水汽提装置处理。从冷低压分离器分离出的气体(低分气)至脱硫部分;液体(冷低分油)经与热高分气换热后进入H2S汽提塔,含硫污水减压后送出装置至污水汽提装置处理。从热低压分离器分离出的气体(热低分气)经过水冷冷却后至冷低压分离器,液体(热低分油)直接进入H2S汽提塔。 二、分馏部分
物料平衡管理制度022—00
物料平衡管理制度 文件编号:SC-ZD-022-00 1.在每个关键岗位进行物料平衡是避免或及时发现差错与混淆的有效方法之一。因此,每个品种各关键生产岗位的批生产、包装记录都必须明确规定物料平衡率的计算方法及合格范围,并根据验证结果确定收率(合格率)的范围。 2.物料平衡率的计算: 2.1计算公式: 物料平衡率= 实际值 ×100% 理论值 其中: 理论值:为投料量。 实际值:为生产过程中实际产出量。 实际产出量包括本岗位产出量(包括零头)、收集的废品量、生产中取的样品量、无法收集的不合格物料(如捕尘系统、真空系统、管道系统中的残余物等)。 2.2在生产过程中如有跑料现象,跑料数量也应计入物料平衡之中,加在实际值的范围之内。 2.3上工序移交下来的有效物料的数量,经复核后成为下工序计算收率的理论值。 3.需进行物料平衡的主要工序: 3.1前处理、提取:净料干燥、浓缩浸膏的干膏、粉碎。 3.2口服固体制剂: 3.2.1片剂:制粒、总混、压片、分装、包装。 3.2.2胶囊剂:总混、胶囊填充、分装、包装。 3.2.3散剂:分装、包装。 4.物料平衡的计算单位: 4.1前处理、提取:固体以重量计算,液体以体积或重量计算。 4.2固体制剂:以重量进行计算。 5.制订物料平衡限度与范围: 5.1常采用根据设备、设施情况估计一定范围,再积累一定批次生产产品物料平衡数据,计算结果进行统计计算,而得出平衡限度。
5.2限度范围: 5.2.1生产过程中因有如捕尘系统、真空系统、管道系统收集的无法收集的丢弃不合格物料,因此不能是100%,一般物料平衡范围96-100%。 5.2.2标签、说明书、中盒等外包装不得随意使用、丢弃。因此物料平衡范围为100%。 6.数据处理: 6.1凡物料平衡在限度范围之内,经质量监督员检查合格后,应在“物料卡”上签字,方可流入下工序。 6.2凡物料平衡高于或低于限度范围,质量监督员须立即贴示标记,不能流转至下工序,按《生产过程偏差处理管理制度》进行处理。 6.3质量保证部定期对各工序物料平衡及产品的收率(合格率)进行回顾性验证,为工艺改进、技术革新及技术标准文件的修订提供参考。 7.物料平衡检查: 7.1每批生产结束后由技术员根据理论投料量及实际产量计算各 工序成品率,按不同产品的出成率要求进行检查。 7.2出成率达到规定要求时,车间主任、质量监督员在批生产记录上审核签字,待该批成品检验合格后,方可出厂。 7.3成品率不在规定范围时,车间主任必须查明各工序影响因素,在得出合理解释、确认无潜在质量事故后,按正常产品处理。若存在质量事故,则应向生产技术部反映,书面提出处理申请,报送质量保证部将最终处理意见及处理记录归入批生产记录。
物料平衡管理规定
一、目的 1、建立物料平衡管理规定,明确检查标准,严格进行收率控制,防止生产过程中发生差错和混淆。 二、范围 1、适用于车间生产的各主要工序。 三、职责 1、生产管理人员、质量管理人员、工序负责人、生产操作人员。 四、内容 1、建立物料平衡检查标准,掌握生产过程中物料收率变化,进行严格的收率控制,使之在合理范围之内,这是防止差错和混淆的有效方法之一。 2、固体制剂车间制粒、整粒总混、压片、胶囊填充、颗粒内包工序以重量为单位计算物料平衡,其它工序以数量为单位计算物料平衡。 3、需要计算物料平衡的主要工序: 3.1 制粒; 3.2 整粒总混; 3.3 压片; 3.4 胶囊填充; 3.5 内包; 3.6 外包。 4、物料平衡计算的基本公式: 实际收得量 物料平衡率% = ———————×100% 理论产量 4.1 理论产量: 4.1.1 按照领用的原辅料量,在生产中无任何损失或差错的情况下得出的最大数量值; 4.1.2 领用的包装材料量。 4.2 实际收得量: 4.2.1 生产过程中实际产出量,包括:本工序产出量、收集的回制量(头子、细粉)、收集的废品量、生产中取样量、丢弃的不合格物料(如捕尘系统、真空系统、管道系统中收集的残余物) 4.2.2 包装材料的实用数、残损报废数、退库数的总和. 4.3 原则上上道工序移交下来的有效物料并经复核的数量,为下道工序计算物料
平衡率的理论产量;
4.4 产品(或物料)的理论产量(或理论用量)与实际产量之间的比值允许有正常范围的偏差; 4.5 每批产品应在生产作业完成后,做物料平衡检查。如有显著差异,必须查找原因,在得出合理解释、确认无潜在质量事故后,方可按正常产品处理; 4.6 在生产过程中若发生跑料、散料的现象,应及时通知工艺员及质量监督员,并详细记录损失数量及事故过程,损失数量应计入物料平衡中,加在实际收得量之内。 5、物料平衡标准: 5.1 固体制剂车间各工序中间产品、成品的物料平衡率范围参见各产品生产工艺规程; 5.2 包装材料的物料平衡率为100%。 6、注意事项: 6.1 凡物料平衡率在规定范围之内的,均属正常,经质量监督员检查签字后,方可递交下道工序或成品入库; 6.2 凡物料平衡率在规定范围之外的,不能递交下道工序,并报车间主任及质量监督员,采取处理措施,并详细记录。 .
物料平衡计算公式
物料平衡计算公式 Document serial number【KK89K-LLS98YT-SS8CB-SSUT-SST108】
物料平衡计算公式: 每片主药含量 理论片重= 测得颗粒主药百分含量 1.原辅料粉碎、过筛的物料平衡 物料平衡范围:97.0%~100% 物料平衡=%100?+a c b a-粉筛前重量(kg)b-粉筛后重量(kg)c-不可利用物料量(kg) 2.制粒工序的物料平衡 物料平衡范围:98.0%~104.0% 制粒工序的物料平衡= a d c b ++×100% 制粒工序的收率=a b ×100% a-制粒前所有原辅料总重(kg)b-干颗粒总重(kg) c-尾料总重(kg)d-取样量(kg) 3.压片工序的物料平衡范围:97.0%~100.0% 压片工序的物料平衡= a d c b ++×100% 压片工序的收率=a b ×100% a-接收颗粒重量(kg)b-片子重量(kg) c-取样重量(kg)d-尾料重量(kg) 4.包衣工序的物料平衡 包衣工序的物料平衡范围:98.0%~100.0% 包衣工序的物料平衡= b a e d c +++ 包衣工序的收率=b a c + a-素片重量(kg)b-包衣剂重量(kg)c-糖衣片重量(kg)d-尾料重量(kg)e-取样量(kg)
5.内包装工序物料平衡 内包装工序物料平衡范围:99.5%~100.0% 包材物料平衡=%100?++++A a d c b B a-PTP 领用量(kg)b-PTP 剩余量(kg)A-PVC 领用量(kg) B-PVC 剩余量(kg)c-使用量(kg)d-废料量(kg) 片剂物料平衡=%100?++a d c b a :领用量(Kg)b :产出量(Kg) c :取样量(Kg) d :废料量(Kg) 6.外包装工序的物料平衡 包装材料的物料平衡范围:100% 包装材料物料平衡=%100?+++e a d c b e-上批结存a-领用量b-使用量c-剩余量d-残损量 7.生产成品率 成品率范围:90%~102% 片剂收率=%100?++a d c b a-计划产量b-入库量c-留样量d-取样量 1.粉碎过筛和称配岗位物料平衡检查: 配料量 ╳100% 粉碎过筛后原辅料总重 (物料平衡范围应控制在99.8~100.2%) 2.制粒干燥、整粒总混岗位物料平衡检查: 总混后重量+不良品 ╳100% 干颗粒净重+润滑剂+崩解剂 (物料平衡范围应控制在99.0~100.0%)