机械加工英语词汇
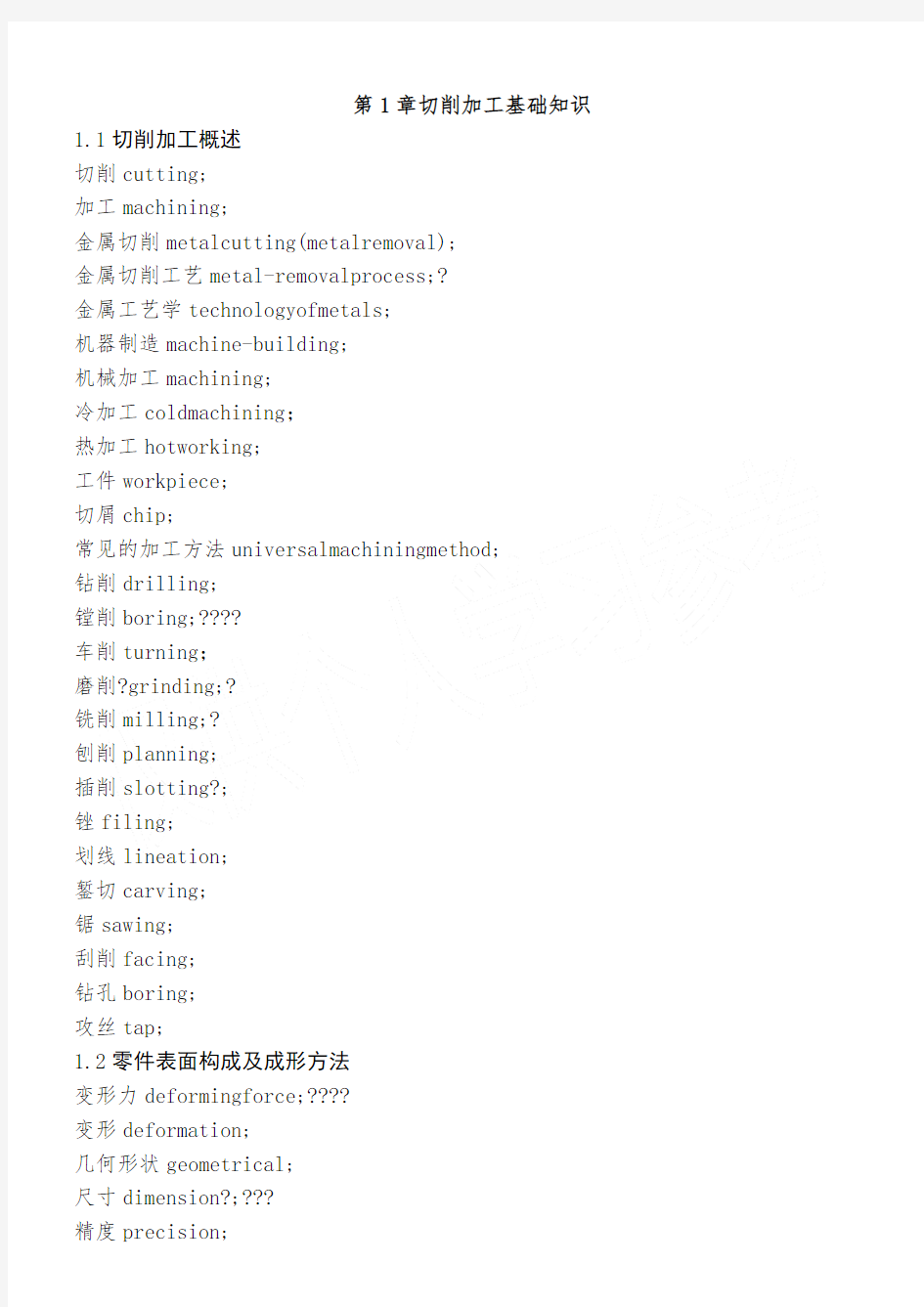

第1章切削加工基础知识1.1切削加工概述
切削cutting;
加工machining;
金属切削metalcutting(metalremoval);
金属切削工艺metal-removalprocess;?
金属工艺学technologyofmetals;
机器制造machine-building;
机械加工machining;
冷加工coldmachining;
热加工hotworking;
工件workpiece;
切屑chip;
常见的加工方法universalmachiningmethod;
钻削drilling;
镗削boring;????
车削turning;
磨削?grinding;?
铣削milling;?
刨削planning;
插削slotting?;
锉filing;
划线lineation;
錾切carving;
锯sawing;
刮削facing;
钻孔boring;
攻丝tap;
1.2零件表面构成及成形方法
变形力deformingforce;????
变形deformation;
几何形状geometrical;
尺寸dimension?;???
精度precision;
表面光洁度surfacefinish;
共轭曲线conjugatecurve;????
范成法generationmethod;?
轴shaft;
1.3机床的切削运动及切削要素
主运动mainmovement;????
主运动方向directionofmainmovement;
进给方向directionoffeed;????
进给运动feedmovement;
合成进给运动resultantmovementoffeed;?
合成切削运动resultantmovementofcutting;
合成切削运动方向directionofresultantmovementofcutting; 切削速度cuttingspeed;
传动drive/transmission;
切削用量cuttingparameters;
切削速度cuttingspeed;
切削深度depthofcut;
进给速度feedforce;
切削功率cuttingpower;
1.4金属切削刀具
合金工具钢alloytoolsteel;
高速钢high-speedsteel;
硬质合金hardalloy;
易加工easeofmanufacturing;
切削刀具cuttingtool;
刀具cutter;??
车刀lathetool;
主切削刃maincuttingedge;
副切削刃assistantcuttingedge;
刀体toolbody;
刀柄toolshank;
前刀面rakeface;
主后刀面majorflank;
刀尖noseoftool;
主剖面系toolorthogonalplanesystem;
切削平面toolcuttingedgeplane;
主剖面toolorthogonalplane;
切削宽度widthoftheuncutchip;
进给平面系assumedworkingplanesystem;
加工表面transientsurface;
前角rakeangle;
后角clearanceangle;
主偏角toolcuttingedgeangle;
刀尖角noseangle;
1.5刀具切削过程及磨削机理
塑性变形plasticdistortion;?
微观组织,显微结构microstructure;
切削力cuttingforce;???
切削温度cuttingtemperature;
积屑瘤built-upedge;
刀尖磨损nosewear;
月牙洼crater;
残留应力?residualstress;
应力stress;???
硬度rigidity;?
磨削grinding;
砂轮grindingwheel;
磨粒grain;?
剪切shear;
摩擦friction;
内力internalforce?;
1.6~1.8切削加工质量、材料的切削加工性、切削液的选择加工精度machiningaccuracy;
表面质量surfacefinish;
工艺性能technologicalperformance;
材料切削加工性指标machinabilityindexofmaterial;
切削液cuttingfluid;
切削油cuttingoil;
1.9件的装夹及夹具
定位梢dowel;
定位allocation;
?机床夹具jig;
组装线Assemblyline;
机械零件mechanicalparts;???
钳工locksmith;?
精加工finishmachining;???
粗加工roughmachining;??
气动夹紧pneuma-lock;
同心,同心度concentricity;
垂直度perpendicular;?
基准benchmark;
基准线referenceline;
夹具??fixture;
通用夹具universalfixture;
专用夹具Fixtureforspecialpurpose;
可调夹具adjustablefixture;
组合夹具modularfixture;
工序process;
设计基准designingdatum;
工艺基准datumfeaturesinprocess;
1.10金属切削机床
机床machinetool;
机床运动motionofmachine;
机床型号machinetoolmodel;
机床加工精度machiningaccuracyofmachinetool; 车床lathe;?
普通车床enginelathe;
卧式车床horizontallathe;
立式车床verticallathe;
钻床drillpress;
镗床boringmachine;
铣床millingmachine;
磨床grinder(grindingmachine);
牛头刨床shaper;
龙门刨床planer;
插床slottingmachine(slotter);
第2章常用加工方法综述及加工方案选择一、车削
车削turning;
车刀lathetool;????
车床lathe?;
普通车床enginelathe;
卧式车床horizontallathe;
立式车床verticallathe;
仿形车床duplicatinglathe(copylathe);
转塔车床turretlathe;
细长轴longslendershaft
纵向车削straightturning;
锥体车削taperturning;
仿形车削contourturning;
端面车削facing;
回转表面surfaceofrevolution;
平面flatsurface;
圆面roundsurface;
仿形表面contouredsurface;
退刀槽recess;
卡盘chuck;
尾架tailstock;
床头箱,主轴箱headstock;
销pin;
卡箍barclasp;
花盘faceplate;
主轴spindle;
二、钻削
钻削drilling;
钻床drillpress;
钻头drill;
锪孔counterboring;
内表面internalsurface;
铰孔、扩孔reaming;
攻丝tapping;
孔加工spotfacingmachining;
铰ream;
铰刀reamer;
盲孔blindhole;
麻花钻twistdrill;
埋头孔countersink;
锥柄tapershank;
三、镗削
镗削bore;
镗床boringmachine;
镗杆boringbar;
纵向镗削straightboring;
表面光洁度surfacefinish;
卧式镗孔机horizontalboringmachine;
四、铣削
铣削mill;
铣床millingmachine;
铣刀millingcutter;
缝Slot;
槽groove;
平面flatsurface;
圆面roundsurface;
仿形表面contouredsurface;
周铣Peripheralmilling;
端铣facemilling;multimodelmiller;
靠模铣床;copymillingmachine;
仿形铣床;contouringmachine;
五、磨削
磨削grinding;
磨床grinder(grindingmachine);
外圆磨削externalgrinding;
内圆磨削internalgrinding(cylindricalgrinding); 平面磨削planegrindingabrasive;
外圆磨床cylindricalgrindingmachine;
平面磨床surfacegrinder;
外圆磨床cylindricalgrindingmachine;
内圆磨床internalcylindricalmachine;
成形磨床formgrindingmachine;
仿形磨床copygrindingmachine;
万能工具磨床universaltoolgrindingmachine;
六、拉削
拉削broaching;
拉床broachingmachine;
拉刀broachingtool;
外表面拉削externalsurfacebroaching;
内表面拉削internalsurfacebroaching;
多功能机床multifunctionmachine;
多齿刀具multitoothtool;
切屑槽chipgullet;
七、刨削
刨削planning;
牛头刨床shaper;
龙门刨床planer;
龙门刨削planning;
旋臂刨床radialdrillingmachine;
仿形刨床copyshapingmachine;
八、齿轮加工
齿轮加工gearmachining;
齿轮gear;
滚齿gearhobbing;
滚齿刀hobbingcutter;
直齿圆柱齿轮straighttoothedspurgear; 斜齿圆柱齿轮helical-spurgear;
直齿锥齿轮straightbevelgear;
齿轮齿条pinionandrack;
蜗杆蜗轮wormandwormgear;
九、螺纹加工
螺纹加工threadmachining;
螺纹切削threadcutting;
攻丝tapping;
丝锥tap;
板牙die;
螺钉screw;
标准件standardcomponent;
位移displacement;
截面section;
十、光整加工
光整加工microfinishing;
研磨mull(lapping);
研磨剂lappingcompound;
研磨膏paste;
研磨机床lappingmachine
抛光polishing;
抛光膏buffingcream;
抛光轮polishingwheel;
抛光机polisher;
珩磨honing;
珩磨轮honingwheel;
珩磨机床honingmachine;
超精加工机床superfinishingmachine;
超精加工superfinish;
第3章机械加工工艺过程
机械加工工艺过程machiningprocess;
工步stepofanoperation;
工位workstation;
工序process;
工艺文件manufacturingprocessdocument;
工艺卡片technologicalcard;
工艺规程processplan;
机械加工工艺卡machiningprocesssheet;
工艺设计technologicaldesign;
设计基准designingdatum;
工艺基准datumfeaturesinprocess;
基准重合consistencyofdatumfeature;
基面统一原则unifieddatumprinciple;
机械加工工序卡machiningoperationsheet;
工艺过程设计processplanning;;
工艺路线processroute;
工艺过程卡processsheet;
产品规格productspecification;
产品用途productuse;
产品责任productliability;
生产线productionline;
生产进度计划productionschedule;
生产率productivity;
批量生产batchproduction;
第4章切削加工零件结构工艺性切削cutting;
加工machining;
工件workpiece;
零件part;
毛坯rough;
工艺性能processingproperty;
装配结构的合理性rationalityofassemblystructure;
零件结构合理性rationalityofdetailstructure;
标准化standardization;
第5章先进制造技术
先进制造技术AdvancedManufacturingTechnology;
信息技术informationTechnology;
产品product;
设计design;
加工machining;
检测check;
管理manage;
销售sell;
使用use;
服务serve;
回收reclaim;
计算机集成制造系统ComputerIntegratedManufacturingSystem(CIMS); 智能制造系统IntelligentManufacturingSystem(IMS);
精密工程preciseengineering;
成组技术grouptechnology;
方式(法)methodology;
柔性制造系统FlexibleManufacturingSystem(FMS);
数控机床numericallycontrolledmachinetool;
加工中心MachiningCenter(MC);
计算机数字控制computerizednumericalcontrol(CNC);
自动换刀装置automatictoolchanger(ATC);
直接数字控制Directnumericalcontrol(DNC);
分布式数字控制Distributednumericalcontrol(DNC);
群控DNC;
单机自动化stand-aloneautomatization;
自动机床Automaticmachine;
组合机床combinationmachine;
专用机床specialmachine;
NC钻床NCdrillingmachine;
NC磨床NCgrindingmachine;
NC车床NClathe;
卧式加工制造中心horizontalmachinecenter;
立式加工制造中心verticalmachinecenter;
车间shopfloor;
库存inventory;
工艺process;
分类classification;
编码系统codingsystem;
零件外型partconfiguration;
工艺规划processplanning;
单元式制造cellularmanufacturing;
小车维修站Cartmaintenancestation;
零件清洗站Partswashstation;
装卸站Unloadstation;
回收系统Recoverysystem;
小车转弯站Cartturnaroundstation;
集成化integration;
协调tradeoff;
成族零件family-of-part;
换刀装置Toolchanger;
机床控制装置machinecontrolunit;
组装线Assemblyline;
第6章先进制造运行模式
先进制造运行模式AdvancedManufacturingOperationModel;
计算机集成制造系统ComputerIntegratedManufacturingSystems(CIMS); 精益生产(LP亦称精良生产)LeanProduction;
敏捷制造AgileManufacturing(AM);
绿色制造GreenManufacturing;
计算机辅助设计ComputerAidedDesign(CAD);
计算机辅助制造ComputerAidedManufacturing(CAM);
计算机辅助工艺过程设计ComputerAidedprocessplanning(CAPP); 物料需求计划MaterialRequirementsPlanning(MRP);
计算机辅助教育ComputerAidedEducation(CAE);
虚拟制造VirtualManufacturing(VM);
并行工程ConcurrentEngineering(CE);
面向装配的设计DesignForAssembly(DFA);
面向制造的设计DesignForManufacturing(DFM);
第7章特种加工
特种加工(NTM)NontraditionalManufacturing;
一、电火花加工
电火花加工spark-erosionmachining;
电火花线切割加工electricaldischargewire–cutting;
电火花穿孔spark-erosiondrilling;
电火花雕刻spark-erosioncarving;
二、电解加工
电解加工Electrolyticmachining;
三、超声波加工
超声波加工Ultrasonicmachining;
变幅杆Transducernose;
铜垫圈Copperwasher;
放大刀具夹持器Amplifyingtoolholder;
超声波振动Ultrasonicvibration;
银钎焊Sliverbraze;
仿形刀具Shapedtool;
蜡焊缝Waxweld;
支持材料Backupmaterial;
磨料悬浮液Abrasiveslurry;
吸入管Suctionline;
四、激光加工
激光加工Laserprocessing;
激光束加工Laserbeammachining;
激光切割lasercutting; 激光打孔laserdrilling; 激光焊接laserwelding;
机械加工中的刀具管理系统
机械加工中的刀具管理系统 随着加工系统的高速化、无人化及智能化发展,为了提高加工产品的品质,刀具管理的必要性尤为重要。因此,各企业为了提高生产效率,减少成本,都竞相引入刀具管理系统或建立刀具数据库。 1 刀具管理系统 机械加工中刀具管理系统是对N C 设备所需的刀具(铣刀和板料等1的基本信息、在库及购买的管理。 其主要职能有:1 ) 刀具管理:一般N C 用刀具的入库、检收、补充及报废管理; 2 ) S ( 自动化)刀具管理:对FM s 设备所需的刀柄和主轴管理; 3 ) 库房/购买管理:刀具的异体、预算、购买、订货及来历等的管理。 2 刀具室 刀具室的建立,不单单是作为一个库房来存在,它要完成的任务在制作过程中应该起到很大的作用,工作做的如何直接影响到产品质量,生产周期以及加工成本。 刀具室要记录各个设备的月消耗,通过对比分析来确定刀具使用情况,以便于更好的做出成本分析。 刀具室除了基础的刀具配送外,还应承担其他的任务。 1 ) 一般信息——刀具编号、材质、规格、刀具长度、直径及形状等。刀具室应该对刀具进行统一编号,以便于日后管理,并将刀具相关信息录入电脑记录,例如:F 1 2 —1 ( 编号为“l ”的直径中1 2 m l T l 平刀) ;B 1 0 —2 ( 编号为“2 ”的直径①1 0 m m球刀) 。当然可根据适合自己习惯的方法进行编号,录入刀具的一些基本参数, 以方便库管员根据加工程序单所示的的参数找到相应的刀具。 2 ) 加工信息——刀具寿命、刀具磨损量及切削条件。库管员根据现场反馈情况和日常统计明确刀具的使用寿命,以此来确定刀具的更换周期,及时地更新刀具磨损量,根据实际加工情况合理的配备合适的刀具,切勿大材小用。 3 ) 库房分析——刀具选取、品质水准、刀具修理及研磨、特殊刀具制作、供应商考核、 月消耗及设备考核。刀具管理可以说是~个很复杂的工作,不单单是把刀具送到现场,进行账目统计,以及刀具维修这么简单。在此过程中还要根据本部门所处的水准和加工类型来合理选用刀具。例如:对于大型汽车覆盖件,在做精加工时要使用品质有保证的机床 和刀具。我们公司是采用日本东芝高速龙门铣配黛杰高精度球刀来完成作业,若是做E 类 件就不必使用这类设备和刀具,国产刀具完全能够满足精度和面品需要。 选用刀具的时候,是用价高的还是价低的,要考虑刀具的性价比,例如,在建厂初期,
机械制造公司车间管理制度
机械加工车间管理规定 1、劳动纪律: ⑴员工必须遵守厂规厂纪,违反者按《违反厂规厂纪处罚条例》处理。 ⑵员工上班应做到不迟到、早退,严格按照两班制的作息时间进入工作岗位,不到岗者作迟到处理,下班时间未到擅自离岗者按早退处理,迟到一次罚款5.00元,早退一次10元。没到下班时间不允许离开自己的岗位,更不允许站在门口喧哗,聊天,擅离岗者10元/次。 ⑶上班时间不得串岗闲聊,不允许大声唱歌喧哗,打闹嬉笑,更不得擅自出厂或回宿舍,有事离岗必须向组长或车间主任请示,得到批准后方可离开,如擅自离岗被发现一次罚款20.00元。 ⑷不得在工作时间内看报纸、杂志,打游戏,吃零食,如发现一次罚款20.00元。 ⑸有事须写请假条,经班组长签字后交车间主任批准,原则上每个班组请假不得多于2人,不请假按旷工处理,每天罚款50.00-100.00元。 ⑹下班或吃饭时,须将自己机床上的日光灯与电风扇关闭,不执行者一次罚款10.00元。 ⑺服从指挥,听从安排,下级服从上级,个人服从组织,对车间、班组的安排如认为不合理,可以越级反映,但不得顶着不办或消极怠工,不得赌博或打架斗殴,违者罚款50-100元,情节严重者建议厂部给予行政处罚直至开除。 2、现场管理制度 ⑴保持现场良好的工作秩序,创造亮丽、舒适的工作环境。 ⑵保持车间内的整齐、整洁。工作台必须定位摆放,不得放置与生产无关的物料,废品应放置在规定位置,合格品与不合格品不得混放。 ⑶所有在加工的在制品、合格品、不合格品等均须分别放置。 ⑷下班时每位员工必须按照“数控机床保养内容”进行清扫与保养机床。 ⑸爱护公司财产,严禁在机床设备上人为刻画,留下痕迹,一经查实将给予50.00元的处罚。 3、生产工艺管理制度 ⑴生产工艺是确保产品质量的基础,所有员工应遵守操作规程严禁违章作业。 ⑵严格按照图纸施工,生产的半成品必须经检验员确认后方可连续生产,生产过程中必须经
机械加工质量管理规定
质量管理 为使产品质量检验和质量事故处理、扣罚管理有所依循,提高产品制造质量,特制定本规定。 1、质量检验规定 1.1外购件检验:所有外购件(包括原材料、标准件(主要指材质和外观)、带图外购件)都必须交检,外购件到厂后由仓库管理员向检验人员报检,检验合格后方可办理入库,并做好文件依据存档(按日期、批次编码),不合格件不能入库,由检验员开具不合格单报采购部及时处理。 1.2加工件检验 ①凡一次性投产大件2件(单件重量20公斤以上)以上及小件5件以上的零件称为批量加工件,批量加工件必须进行首检,首检合格(质检员必须在生产质量卡上签首检合格意见)后方可批量生产。同时,操作者在随后的批量生产中,还必须随时自检加工出的产品以避免报废。 ②自检:a) 各道工序(包括搬运)都要自检经手零件有无表面划伤、摔坏、压烂等外表质量问题;b)操作者在加工前检测与本工序直接关系的尺寸是否符合图纸要求;c)操作者对自己所加工的工件必须严格进行检验,自检合格后方可送检验员检验。 ③巡检:在生产过程中的产品,检验员应按照工艺文件对关键加工件、关键工序或岗位每天不定期的巡回检查,并做好记录。发现异常状况及时通知操作人员停止操作,同时通报工艺主管和有关领导,并采取有效措施纠正,直到正常运行为止。同时,施工组、生产车间主管也应加强对操作者的技术交底,预防报废品跟踪及采取保证产品质量的措施等工作。 详见《产品质量奖罚细则》的有关规定。 1.3主机检验:要求产品报检前必须所有配置齐全,经班组自检合格后方可报检,否则不予检验。报检产品由检验人员按照企业标准和合格证各项目进行检验,并做好详细记录,操作者根据检验记录对不合格项进行细致整改,班组自检合格后再由检验员进行复检直至合格后方可出厂。详见《产品质量奖罚细则》的有关规定。三次以上交检不合格再报检的给予该班组每次罚款100元。
机械加工行业MES系统解决方案
机械加工行业MES系统解决方案导读:现在机械加工业,遍地开花,透明度越来越高,利润部分越来越低,外贸现在的获利也是更低,一切都需要跑量,而年各类附料暴涨,机械加工也越来越受到强大的压力,那么如何在生产过程中挖掘更多的利润呢? 机械加工行业特点 大型机械装备类型生产模式主要依客户订单进行生产组织,属于典型的少量多样的订单形态,产品定制化特点强,产品的原材料品种较多,物料准备与生产周期较长,生产工艺复杂,经常采用手工填报流程卡的方式来进行简单的数据归档,大型部件在工艺间周转主要通过大型行车吊运以及轨道车搬运,中小部件由叉车或人工搬运,物料部品需要齐套并且进行JIT配送,由于客户需求的变化,产品工艺路线经常调整,生产现场需要对ECN工程变更需要及时下达。 机械加工行业现状 机械加工行业属于离散型的生产,客户个性化需求多,产品品种日趋多样性,市场需求变化快,预测难度增大,企业很难合理的安排生产。 由于产品加工要经过不同的工序,各个工序的生产能力不平衡,生产上容易出现木桶效应,生产
被关键的瓶颈资源所制约,造成交期的延误。 产品结构复杂,零部件多且外协自制兼有,工艺过程经常变更,生产计划的计算和安排非常复杂,临时插单现象多,生产计划往往变的不实用。 外协厂家,外协件多,对外协产品的质量、交货期的跟踪控制困难。数据采集点多,数据收集维护工作量大,而且数据往往分布于不同的部门。 机械加工行业MES系统需求 机械加工行业的主要原材料占整个生产物料成本的95%~99%,以挖掘机为例,原材料有各种规格的钢板、焊丝、焊条、油漆以及各种气体等,其中主要原材料是钢板,占原材料比率的98%以上,因此机械加工MES的原材料管理是机械加工行业信息化建设的重中之重,通过MES系统实现对原材料用量需求、采购、仓储领用、废料回收等的精确管控,从而降低成本,对于机械加工企业有重要意义。 机械加工行业MES系统解决方案 OrBit-MES针对大型机械装备生产行业提供了完整的解决方案,其重点主要集中在:工时管理、
机械制造企业环保管理制度
机械制造企业环保管理制度 1 总则 1.1 认真贯彻执行《中华人民国环境保护法》(以下简称《环保法》)、《省环境保护条例》等一系列国家颁布的环境法律、法规和标准。 1.2 遵循保护和改善生活环境与生态环境,防治污染和其他公害,保障人体健康,促进社会主义现代化建设的发展方针,结合公司具体情况,组织实施公司的环境保护管理工作。 2 管理要求 2.1 公司下水道严格实行雨污分流制,雨水单独排放,特殊工业废水须特殊处理后方可进入下水道,与生活污水一并汇入综合污水处理站,由专人处理达标后方可安全排放,或经过深度处理制成中水回用于生产。 2.2 对生产过程中产生的“三废”必须大力开展综合利用工作,做到化害为利,变废为宝;不能利用的,应积极采取措施,搞好综合治理,严格按照标准组织排放,防止污染。 2.3 必须按照设备完好标准搞好设备管理和维修工作(包括三废治理设施),杜绝跑、冒、滴、漏,减少或减轻“三废”污染。 2.4 凡有“三废”排放的分厂(分公司)、部门,必须把环境保护工作纳入方针计划,建立环境保护责任制度;采取有效措施,防止在生产建设中产生的废气、废水、废渣、粉尘、恶臭气体、有害物质,以及噪声、振动、电磁波辐射、热辐射等对环境的污染和危害。 2.5 认真贯彻“三同时”方针,新建、改建、扩建项目中防治污染的设施,必须与主体工程同时设计,同时施工,同时投产使用。防治污染的建设项目必须提前经有关部门验收合格后,主体工程方可投入生产使用。 2.6 公司归属的生产界区围,应当统一规划种植树木和花草,并加强绿化管理,净化辖区空气;对非生产区的空地亦应规划绿化,落实管理及保护措施。 3 组织领导体制和应尽职责 3.1 加强对环境保护工作的领导和管理。公司确定一名副总经理主管环境保护管理工作,并成立公司环境保护委员会。日常工作由工程部门归口管理,其主要职责是:行使公司环保工作的计划、组织、指挥、协调、检查和考核管理职能,日常一切工作须对公司负责,并由职工代表大会予以监督。
车床传动轴机械加工工艺过程设计
车床传动轴机械加工工艺过程设计 院系名称 班级 学生姓名 学号 指导老师
1.问题提出: 零件的几何精度直接影响零件的使用性能,而机械加工工艺过程制定的是否合理将直接影响零件的加工精度。针对车床传动轴,应用所学的机械制造基础知识进行一次加机械工工艺过程设计的综合性工程应用训练。 2.专题研究的目的: 1、掌握零件主要部分技术要求的分析方法; 2、掌握零件材料的选择方法和确定毛坯的制备方法及工艺; 3、掌握工艺分析方法; 4、掌握定位基准的选择方法; 5、掌握制定出合理的零件加工顺序的原则和方法; 7、掌握制定出合理的零件加工路线的方法。 3.研究内容: 图1所示为车床的传动轴,轴上开有键槽用来安装齿轮以传递运动和动力,两端是安装滚动轴承的支承轴颈。完成该传动轴零件的机械加工工艺过程设计。工艺设计的具体内容包括: 一、进行零件主要部分的技术要求分析研究; 1、本零件是传动轴,传动过程中只传递转矩而不承受弯矩,可以通过热处理方法提高轴的耐磨性和抗疲劳强度。 2、此传动轴的形状简单,属于对称零件,同时阶梯轴很少,而且各段直径相差不太大。 3、轴上需磨削的轴段都设计出了砂轮越程槽,而且砂轮越程槽都是统一大小的。 4、传动轴上的各个键槽开在同一母线的位置上,便于加工。键槽和齿轮通过与键配合,实现动力的传递。 5、轴端设有倒角,以便于装配,并且轴肩高度不妨碍零件的拆卸。 6、此传动轴设计成两端小中间大的形状,便于零件从两端装拆。
7、Φ17圆柱表面为支撑轴颈与滚动轴承相配合,对其要求圆柱度公差则可控制横剖面和轴剖面内的各种形状误差。 8、Φ24圆柱面要与齿轮配合,为保证其平稳性和减少噪音,对其表面有径向全跳动的要求。 9、Φ24和Φ32轴段处的轴肩用于定位,防止其端面圆跳动产生偏心。 10、轴上键槽有对称度要求,一般来说键槽都有对成度公差。 二、确定传动轴的材料、毛坯的制备方法及工艺、热处理工艺; 1、选用材料为45钢,由于此车床传动轴是一般的阶梯轴,并且各阶梯的直径相差小,则可以直接以热轧圆柱棒料做毛坯。 2、选用调质和表面淬火的热处理工艺。 三、进行加工工艺分析; 1、传动轴大多是回转表面,主要是采用车削和外圆磨削。由于该轴主要 2、该传动轴加工划分为三个加工阶段,粗车,半精车,粗精磨各处外圆。各加工阶段大致以热处理和铣键槽为界。 四、确定定位基准; 此传动轴是精度要求高的轴类零件,因此先以毛坯外圆为粗基准,加工两端面及中心孔,再以中心孔定位完成各表面的粗加工;精加工开始先再修整中心孔,以提高轴在精加工时的定位精度,再以中心孔为精基准加工外圆。 五、制定传动轴的加工顺序; 1、外圆表面加工顺序应为,先加工大直径外圆,然后再加工小直径外圆,以 2、轴上的键槽等表面的加工应在外圆精车或粗磨之后,精磨外圆之前。 3、为了改善工件材料的力学性质而进行的热处理工艺调质、表面淬火通常安排在粗加工之后、加工之前进行。 六、制定传动轴的加工路线; 车端面和钻中心孔—粗车—半精车—调质—表面淬火—粗磨—铣键槽—精磨外圆—去毛刺 车床传动轴的机械加工工艺路线
机械加工车间管理制度
机械加工车间管理制度 一、机加班相关岗位的岗位描述以及各设备、各工种的安全操作规程 二、操作指导书(包括设备的基本操作规程以及工艺的基本操作指导等) 三、设备点检表及设备维修维护保养计划 四、现场管理制度 1、“5S”------ 1)现场实行“5S”管理制度,保持整洁的生产环境。设备、工装、工具、物料等按照定置进 行摆放,标识清晰; 2)合格品与不合格品要进行区分放置,废品应置于废品箱中; 3)生产加工过程中的废料、垃圾等及时清理。 2、工艺管理------ 1)严格按照《设备操作规程》和《工艺操作指导》进行零件加工操作; 2)批量加工的零部件开班生产的首件要经过检查确认合格后方可连续生产,且生产过程根 据工艺要求进行自检; 3)非指定人员不允许对设备参数、程序等进行更改; 4)原材料、在制品、成品件严格按照定置进行摆放。 3、质量管理------ 1)加工零件必须严格按照图纸进行加工,同时进行本道工序的自检和工序间的互检,确保 零件合格率; 2)在加工过程中发现不合格品立即进行处理,避免发生批量质量问题。 4、考勤管理------ 1)按时上下班,不迟到、不早退;
2)午饭时间为??-??,上午休息时间为??-??,下午休息时间为??-??; 3)各种病假、事假、带薪假等相关假期按照公司的假期管理制度执行。 5、安全管理------ 1)严谨在现场及非指定吸烟区域吸烟; 2)劳保用品穿戴整齐; 3)严格按照设备操作规程进行操作,如发现设备异常,应该停机检查请专业维修人员进行 处理,严谨擅自进行修理工作; 4)各工种按照相关安全操作规程进行操作; 5)防火器材要摆放在明显位置,做到保管好、会使用;(是否需要制定单独的安全防火制 度?) 6)易燃易爆、化学品等危险品要单独进行存放,且存放条件满足安全规定(此处是否需要 有单独的规定?) 五、绩效考核细则
机械加工行业生产十大管理方案
机械加工行业生产十大管理方案 1、基础数据管理 机械加工行业解决方案的产品数据管理子系统帮助用户建立和维护企业生产使用的主要基础数据。对产品的结构及零件、使用的材料、单件的材料用量,以及产品的质量要求等数据进行维护,具备替换件处理功能。提供工作中心及工艺路线的基本数据,进行产品分车间分工作中心的工时定额,汇总产品材料消耗定额,以及各种工程数据的复制和版本维护。 2、生产管理 [主生产计划] 主生产计划(MPS)主要说明企业计划生产什么,什么时候生产,生产多少,由它来驱动物料需求计划和能力需求计划。主生产计划的排产对象是具体的产品或通用部件,一般细到产品的型号、规格,时间周期一般细到月或旬。它与销售、预测系统有着灵活的接口,系统可以自动读取确认的销售合同和预测的数量。亦可由本系统手工录入。可按批量准则和库存情况自动生成计划。提供将通用部件列入主生产计划的两级处理,完成最终计划编制。 [物料需求计划] 依据产品结构数据(BOM)和预计库存状况,自动编制物料需求计划---生产计划、采购计划,可采用不同的批量政策。通过任务跟踪,指导其他工作中心,物料采购部门在适当的时间加工或采购适当数量的材料和零部件,有助于避免物料短缺、降低库存、提高企业的生产效率。 [能力需求计划] 根据MPS任务生成粗能力需求计划,对关键工作中心的设备、人力进行核算。可按日期、按工作中心查询粗能力需求。对关键资源进行核算。可生成工序进度计划,日能力需求计划和细能力需求计划,并进行细能力核算,提供细能力需求计划报表。 [车间现场管理] 根据相关数据编制车间作业计划,支持顺序、平行、交叉、分批作业,保证生产加工过程顺利畅通,缩短产品生产周期,提高交货的准确度。及时输入车间现场数据,如:产量、设备运转情况、原材料消耗情况等。保证车间管理人员能及时了解车间的生产情况。并提供生产进度日报、车间产品产量报告、生产工时的统计报告、车间在制品数量统计。自动计件工资系统与工资管理系统实现集成,保证计件工资的准确性,充分体现企业按劳分配的管理制度,提高企业员工的积极性。按班组的管理模式,使责任更清楚、更细化。 3、销售管理 建立完整的客户档案,集中管理各类单据,如:客户信息-报价-接单-排产-备货-出库-开票-送货-装箱-汇总,原来属于不同部门的业务实现了无缝的链接,缩短交货周期,提高交货准时性。并实现了订单的交货模拟和库存配套情况查询,可随机查询合同发货情况,办理发货/退货手续,自动开票,将
机械加工厂规章制度范本 最新
合同编号: 机械加工厂规章制度范本2018最新 签订地点: 签订日期:年月日
机械加工厂规章制度范本2018最新 一、目的 为规范工作秩序,提高工作效率,保证车间生产正常进行,让员工做好本职工作,特制订本制度。 二、适用范围:本厂全体工作人员。 三、具体制度 (一)考勤管理:标准考勤时间:办公室人员:上午07︰30-11︰15,下午12︰00-17︰00;生产人员:上午07︰30-19︰30,晚上19︰30-07︰30。 1、严禁迟到或早退、不打卡或代人打卡。如果出现代人打卡者,双方违反当事人扣除当月全勤奖。 2、如果出现因考勤机故障或员工卡不能正常打卡的,则由本人到车间进行登记,并由直接上级签字认可,否则按旷工处理。 3、上班时间超过半小时到达车间均属于迟到,30分钟以上未到岗位也未请假视为旷工一天,每迟到或早退一次,10分钟以内罚款10元。迟到10-30分钟(含30分钟)的每次均罚款50元。一个月内累计迟到的次数达3次者(含3次),记旷工一天。 4.若一个月内累计迟到的次数达10次以上(含10次),或半年内
累计迟到的次数达20次以上(含20次)属于严重违反公司规章制度,将予以辞退。 (二)班前会、班后会 1、早晨07︰20及晚上19︰20召开交接班会议。 2、如果有事或其他原因造成不能参加会议者,必须提前给班长打电话说明原因。 3、交班班长在生产中遇到的问题,尽量在本班解决,为下一班的安全生产打下良好基础,如问题未能解决,做好详细交班记录,并上报车间主任,在交接班时与接班负责人解释清楚后方可下班。 4、交班时交班班长必须如实反映生产状况和设备运行情况,不得对存在的问题隐瞒,接班者要严肃认真,仔细检查,做到交班清,接班严。 5、如果交班者故意隐瞒事实真相或有意违反规定,虽然接班者已接班,但发生的后果视情节严重由双方共同承担。 6、交班人员应明确回复接班人员提出的问题,并和接班人员共同核实,检查设备运行情况。 7、交班人员在接班人员因故未到现场,或未完成接班检查工作前不得擅自离去。 8、接班人应按交接班内容逐一检查核对,符合实际情况即可交接班,不得无理刁难或无故不接,由于接班人检查核对不周而引起的后果,
轴的机械加工工艺设计
轴的机械加工工艺过程设 计学生作品 所属学院: 专业:机械工程及自动化 小组成员: 组长: 授课教师: 提交时间:
传动轴设计准备工作——明确问题的提出及研究目的1.问题提出: 零件的几何精度直接影响零件的使用性能,而机械加工工艺过程制定的是否合理将直接影响零件的加工精度。针对车床传动轴,应用所学的机械制造基础知识进行一次加机械工工艺过程设计的综合性工程应用训练。 2.专题研究的目的: (1)掌握零件主要部分技术要求的分析方法; (2)掌握零件材料的选择方法和确定毛坯的制备方法及工艺;(3)掌握工艺分析方法; (4)掌握定位基准的选择方法; (5)掌握制定出合理的零件加工顺序的原则和方法; (6)掌握制定出合理的零件加工路线的方法。 车床传动轴的几何设计要求——研究内容 图1所示为车床的传动轴,轴上开有键槽用来安装齿轮以传递运动和动力,两端是安装滚动轴承的支承轴颈。完成该传动轴零件的机械加工工艺过程设计。 工艺设计的具体内容包括: (1)进行零件主要部分的技术要求分析研究; (2)确定传动轴的材料、毛坯的制备方法及工艺、热处理工艺;(3)进行加工工艺分析;
(4)确定定位基准; (6)制定传动轴的加工顺序; (6)制定传动轴的加工路线。 图1 传动轴 工作安排 1.查阅资料了解传动轴各部位的作用; 2.根据相关资料及所学知识确定材料、毛坯及热处理工艺; 3.根据传动轴的结构特点,制定相应的加工工艺路线,并确定加工工序; 4.总结上述过程,完成研究报告。 组员分工 1.查阅资料—— 2.选材、毛坯及热处理工艺的选择—— 3工艺路线的确定—— E F M N P Q
机械加工质量管理规定
机械加工质量管理规定 Company Document number:WTUT-WT88Y-W8BBGB-BWYTT-19998
质量管理 为使产品质量检验和质量事故处理、扣罚管理有所依循,提高产品制造质量,特制定本规定。 1、质量检验规定 外购件检验:所有外购件(包括原材料、标准件(主要指材质和外观)、带图外购件)都必须交检,外购件到厂后由仓库管理员向检验人员报检,检验合格后方可办理入库,并做好文件依据存档(按日期、批次编码),不合格件不能入库,由检验员开具不合格单报采购部及时处理。 加工件检验 ①凡一次性投产大件2件(单件重量20公斤以上)以上及小件5件以上的零件称为批量加工件,批量加工件必须进行首检,首检合格(质检员必须在生产质量卡上签首检合格意见)后方可批量生产。同时,操作者在随后的批量生产中,还必须随时自检加工出的产品以避免报废。 ②自检:a) 各道工序(包括搬运)都要自检经手零件有无表面划伤、摔坏、压烂等外表质量问题;b)操作者在加工前检测与本工序直接关系的尺寸是否符合图纸要求;c)操作者对自己所加工的工件必须严格进行检验,自检合格后方可送检验员检验。 ③巡检:在生产过程中的产品,检验员应按照工艺文件对关键加工件、关键工序或岗位每天不定期的巡回检查,并做好记录。发现异常状况及时通知操作人员停止操作,同时通报工艺主管和有关领导,并采取有效措施纠正,直到正常运行为止。同时,施工组、生产车间主管也应加强对操作者的技术交底,预防报废品跟踪及采取保证产品质量的措施等工作。 详见《产品质量奖罚细则》的有关规定。 主机检验:要求产品报检前必须所有配置齐全,经班组自检合格后方可报检,否则不予检验。报检产品由检验人员按照企业标准和合格证各项目进行检验,并做好详细记录,操作者根据检验记录对不合格项进行细致整改,班组自检合格后再由检验员进行复检直至合格后方可出厂。详见《产品质量奖罚细则》的有关规定。三次以上交检不合格再报检的给予该班组每次罚款100元。
机加工自动线控制系统(DOC)
目录 第1章工程实践训练的目的与任务 (1) 1.1 目的 (1) 1.2 任务 (1) 第 2 章机加工自动线的用途、基本组成和工作原理 (3) 2.1 机加工自动线的用途 (3) 2.2 机加工自动线的基本组成和工作原理 (3) 2.2.1 机械部分的基本组成和工作原理 (3) 2.2.2 液压部分的基本组成和工作原理 (4) 2.2.2.1 机加工自动线输送带液压部分工作原理 (9) 2.2.2.2 定位、夹紧机构液压部分工作原理 (9) 2.2.2.3 铣端面动力头液压传动部分工作原理 (10) 第3章自动线控制系统的组成及其各电器元件的作用 (12) 第 4 章机加工自动线控制系统的操作训练 (15) 4.1 操作前的准备 (15) 4.2 全线全自动方式下的操作 (15) 4.3 全线半自动方式下的操作 (16) 4.4 手动方式下的操作 (17) 4.5 停止运行的操作 (17) 第5章机加工自动线控制系统的编程及其调试训练 (18) 5.1 编程训练 (18) 5.2 程序的调试训练 (23) 5.2.1 将程序写入PLC的内存中 (23) 5.2.2 程序的调试 (23) 第6章机加工自动线控制系统的故障诊断训练 (24) 第7章工艺图纸的设计 (26) 心得体会 (27)
第1章工程实践训练的目的与任务 1.1 目的 生产自动化是科学技术不断进步和生产高度发展的产物,是一种理想的生产形式。在大批量生产条件下,由于产品品种单一,产品结构稳定,而且产量大,一般都具备有工步、工序自动化和流水作业的基础,建立自动线使产品零件加工工艺过程自动化是少品种大批量生产实现自动化的一种良好方式。因此,在机械行业,机械加工生产自动线已成为一种常见的自动化生产形式。 自动线由基本工艺设备及工件传送系统、控制系统组成。其中,控制系统的设计、安装、调试和维护是电气化技术人员的岗位职责。 自从1969年DEC公司研制出PLC。并首次用于美国通用汽车公司的汽车自动装配线以来,PLC得到了迅速的发展,在工业控制方面得到了广泛的应用。PLC控制已基本取代了过时的继电~接触器控制。PLC应用技术也成为电气化专业学生必需掌握的技术之一。 本系统旨在为学生进行机加工自动线电气控制系统的运行、调试和维护提供一个实训环境。通过操作、调试、排障等工程实训,使学生熟悉机加工生产自动化的运行,掌握自动线PLC控制系统的布线工艺、调试和维护方法,增强PLC的工程应用能力,为将来从事PLC应用方面的技术工作打下基础。 1.2 任务 本项目的训练内容分为设计训练、操作训练和故障排除训练三个方面。本项目的设计训练内容包括机加工自动线控制台电气工艺图的设计训练,机加工自动线PLC控制程序的设计调试训练两个方面。 机加工自动线PLC控制程序的设计调试训练内容包括: (1)PLC控制系统程序的总体结构图的设计。 (2)PLC控制系统公用程序(只含一个工位)的设计调试。 (3)PLC控制系统手动程序(只含一个工位)的设计调试。 (4)PLC控制系统单机半自动程序(只含一个工位)的设计调试。
机械行业安全生产规章制度
机械行业安全生产规章制度 第一条:根据《xxx劳动安全暂行条例》和交通建设 局的有关文件规定,实行行政负责,归口管理,纪律监察, 群众监督的安全生产管理体制,特制定本规定. 第二条:本规定适用于本单位各类人员,凡违反本规 定的均按照有关条款处理.安全工作考核作为单位评选先进、奖金效益工资发放的主要依据之一,具有一票否决权. 第三条:本处安全生产管理,实行层层责任制,施工队、作业班组(包括招聘的承建制施工队承建项目)向项目部 负责,项目部向处负责,分级签定安全生产责任书:同时各 级领导承担一定的责任,处主要领导负全面责任,项目经 理负主要责任,其他领导负综合管理责任. 第一章安全生产责任制 (1)安全生产责任制的概念:安全生产责任制是生产 单位岗位责任制的一个组成部分,是企业最基本的安全 制度,是安全规章制度的核心。安全生产责任制的实质 是安全生产,人人有责。安全生产责任制的核心是切实 加强安全生产的领导,建立起以政府部门、企业主要领 导为第一责任人的责任制。安全生产责任制要贯彻预防 为主的原则。安全生产责任制要求企业各级生产领导在 安全生产方面要对上级负责,对职工负责,对自己负责。
(2)企业安全生产责任制的要求: ①建立安全生产责任制体系:即建立起经营者(决策、管理、和监督责任)、管理者、技术人员及全体员工的安全责任制体系。 ②建立全生产责任制的步骤:首先要树立安全第一 的思想,对落实安全生产责任制要有专门的人员与机构 来保障,制定安全生产责任制的管理制度。 ③全生产责任制的落实:在以法人代表为核心的责 任体系下,通过检查、监督、奖惩等制度来保证安全生 产责任制得到落实。 (3)安全生产责任制的实现 责任制度就是明确企业一把手是安全减灾的第一责 任人;管生产必须管安全;全面综合管理,不同职能机构 有特定的安全职责。如一个企业,要落实安全责任制度,需要对各级领导和职能部门制定出具体的安全责任,并 通过检查、监督、考评、奖惩等实际工作得到落实。 第二章组织机构及职权 处设立安全生产委员会,设主任一人,副主任二至三人,成员由行政办公室、工程技术科、设备物资科、劳资科和各项目部(队)行政负责人组成.安全生产委员会(以 下简称安委会)在处行政领导下开展工作,贯彻执行国家 安全生产政策法规法令,贯彻落实上级主管部门的安全生
机械制造工艺过程设计
前言 通过机床工艺及夹具设计,汇总所学专业知识如一体( 如《公差于配合》、《机械零件设计》、《机械原理》、《机械制造工艺》等 ) 。让我们对所学的专业课得以巩固、复习及实用,在理论与实践上有机结合;使我们对各科的作用更加深刻的熟悉与理解,并为以后的实际工作奠定坚实的基础! 在这次设计中,我们主要设计 C6140拨叉的夹具。在设计中阅读大量的参考资料并且得到老师的指导由于能力有限在设计中难免有 不足之处,恳请各位老师、同学批评指正。
一.设计的目的: 机械制造工艺学课程设计, 是在学完机械制造工艺学及夹具设计 原理课程,经过生产实习取得感性知识后进行的一项教学环节;在老师的指导下,要求在设计中能初步学会综合运用以前所学过的全部课程,并且独立完成的一项工程基本训练。同时,也为以后搞好毕业设 计打下良好基础。通过课程设计达到以下目的: 1、通过对零件某道工序的夹具设计,学会工艺装备设计的一般 方法。通过学生亲手设计夹具(或量具)的训练,提高结构设计的能力。 2、能熟练的运用机械制造工艺学的基本理论和夹具设计原理的 知识,正确地解决一个零件在加工中的定位,夹紧以及合理制订工艺规程等问题的方法。 3、学会使用手册及图表资料。掌握与本设计有关的各种资料的 名称和出处,能够做到熟练运用。 4、通过课程设计也提高了自己的编写文件的能力 二.零件的分析 (一)、零件的作用:题目给定的零件是CA6140 拨叉(见附图 1)它位于车床变速机构中,主要起换档,使主轴回转运动按照工作者的要求进行工作。通过拨叉的拨动使车床滑移齿轮与不同的齿轮啮合从而达到要求 的主轴转速。宽度为 30+0.0120mm 的面寸精度要求很高,因为在拨叉拔动
机械加工质量控制
机械加工质量控制 机械零件的加工质量包括两个方面:加工精度和表面质量。 一、加工精度 (一)加工精度的概念 加工精度是指加工后的零件在形状、尺寸、表面相互位置等方面与理想零件的符合程度。它由尺寸精度、形状精度和位置精度组成。 尺寸精度:指加工后零件表面本身或表面之间的实际尺寸与理想尺寸之间的符合程度。 形状精度:指加工后零件表面本身的实际形状与理想零件表面形状之间的符合程度。 位置精度:指加工后零件各表面之间的实际位置与理想零件各表面之间的位置的符合程度。(二)机械加工精度获得的方法 1.尺寸精度的获得方法 1)试切法这是一种通过试切工件—测量—比较—调整刀具—再试切—……再调整,直至获得要求的尺寸的方法。 2)调整法是按试切好的工件尺寸、标准件或对刀块等调整确定刀具相对工件定位基准的准确位置,并在保持此准确位置不变的条件下,对一批工件进行加工的方法。 3)定尺寸刀具法在加工过程中采用具有一定尺寸的刀具或组合刀具,以保证被加工零件尺寸精度的一种方法。 4)自动控制法通过由测量装置、进给装置和切削机构以及控制系统组成的控制加工系统,把加工过程中的尺寸测量、刀具调整和切削加工等工作自动完成,从而获得所要求的尺寸精度的一种加工方法。 2.形状精度的获得方法 机械加工中获得一定形状表面的方法可以归纳为以下三种。 1)轨迹法此法利用刀具的运动轨迹形成要求的表面几何形状。刀尖的运动轨迹取决于刀具与工件的相对运动,即成形运动。 用这种方法获得的形状精度取决于机床的成形运动精度。 2)成形法此法利用成形刀具代替普通刀具来获得要求的几何形状的表面。机床的某些成形运动被成形刀具的刀刃所取代,从而简化了机床结构,提高了生产效率。 用这种方法获得的表面形状精度既取决于刀刃的形状精度,又有赖于机床成形运动的精度。3)范成法零件表面的几何形状是在刀具与工件的啮合运动中,由刀刃的包络面形成的。因而刀刃必须是被加工表面的共扼曲面,成形运动间必须保持确定的速比关系,加工齿轮常用此种方法。 3.位置精度的获得方法 在机械加工中,获得位置精度的方法主要有下述两种。 1)一次装夹法工件上几个加工表面是在一次装夹中加工出来的。 2)多次装夹法即零件有关表面间的位置精度是由刀具相对工件的成形运动与工件定位基准面(亦是工件在前几次装夹时的加工面)之间的位置关系保证的。在多次装夹法中,又可划分为: ①直接装夹法即通过在机床上直接装夹工件的方法。 ②找正装夹法即通过找正工件相对刀具切削成形运动之间的准确位置的方法。 ③夹具装夹法即通过夹具确定工件与刀具切削刃成形运动之间的准确位置的方法。 二、表面质量 (一)表面质量的概念 零件的机械加工质量不仅指加工精度,而且也包括加工表面质量。表面质量是指机械加工后零件表面层的几何结构,以及受加工的影响表面层金属与基体金属性质产生变化的情况。表面层一般只有0.05~0.15mm。
机械加工质量管理
机械加工质量管理 (林雪锋2017/4/27) 机械加工企业的质量管理是企业交货承诺的重要内容,目的是如何保证企业生产的零部件质量,机械加工企业小规模时由企业主直接管理,当企业发展到一定规模时,企业适宜采用事业部管理制,事业部承担了销售、生产、质量、成本等职能,以下我按事业部制的管理模式,谈谈质量管理。 质量管理的职责:1)事业部负责人承担事业部质量管理主要职责,2)事业部品质经理承担事业部质量管理的常务工作,3)各部门负责人承担质量管理的部门工作; 质量管理的主要工作包括:1)确定事业部质量管理的部门与岗位具体职责和分工,2)选定质量管理、控制的具体人员,包括生产人员和检验人员,3)制定质量管理的流程和管理细则,包括原材料、半成品、成品检验和验收规程,质量事故处理制度、常规项目质量控制指引、特殊项目质量控制指引,4)对重要项目进行质量控制,包括确定关键控制点及进行控制,过程重大问题的处理,质量事故的处理,顾客投诉的处理; 质量管理分工:1)品质部负责原材料、外购件、外协件和成品的检验,接收顾客的投诉和处理,质量事故的处理,过程半成品的抽检,2)生产部负责生产的过程质量控制,包括半成品检验,3)工程(工艺)部负责控制图纸的准确性,与生产部确定制作工艺,从设备和工艺上达到制作精度及避免质量问题,编写成《工序流程卡》,4)根据质量控制的实际情况推行自检、互检和专职检的方式; 常规产品的质量管理:1)事业部负责人会同品质部、采购部进行原材料质量管理,包括确定原材料的要求和检验标准,及进行检验,2)事业部负责人会同生产部和品质部进行过程的质量控制、半成品检验,3)事业部负责人会同品质部进行成品的检验,处理顾客的投诉,4)事业部负责人与品质经理会同工程部编写《检验卡》,内容包括:关键控制点、检验设备、量具、检验频次等内容,生产部根据《检验卡》进行检验,品质部根据《检验卡》进行抽检; 新产品的质量管理:1)事业部负责人和品质经理会同工程部、生产部、客户确定产品的质量要求,包括尺寸精度、形位公差、原材料要求等,有必要的会
第2章 机械加工工艺系统
形成发生线的方法: (1)轨迹法 (2)成形法 (3)展成法 (4)相切法 二、机械加工的运动 1、表面成形运动 从几何的角度来分析,为保证得到工件表面的形状所需的运动,称为成形运动。根据工件表面形状和成形方法的不同,成形运动有以下类型: (1)简单成形运动:一个成形运动是由单独的旋转运动或直线运动构成的。 (2)复合成形运动:一个成形运动,是由两个或两个以上旋转运动或直线运动,按照某种确定的运动关系组合而成。 从保证金属切削过程的实现和连续进行的角度看,成形运动可分为: (1)主运动:切除切屑所需的基本运动。 3个特点:速度最快;消耗功率最大;唯一性。(通常只有一个主运动)。 (2)进给运动:使金属层不断投入被切削的运动。 3个特点:速度较慢;消耗功率较小;可以为一个或多个。(可以是连续的,也可以是断续的。) 成形运动是机床最基本的运动。 2、辅助运动 除成形运动外,为完成机床工作循环,还需一些其它的辅助运动: (1)空行程运动刀架、工作台的快速接近与退出工件等,可节省辅运动。 (2)切入运动保证被加工面获得所需尺寸,刀具相对互动式件表面的深入运动。 (3)分度运动使工件或刀具回转到所需要的角度。 (4)操纵及控制运动包括变速、换向、起停及工件的装夹等。
常见机床的切削运动 三、切削用量和切削层参数 1、切削过程中工件上的表面 正在加工的工件表面,根据其所处的状态分为: (1)待加工表面:即将进入切削加工的表面。 (2)已加工表面:已经加工完成的表面。 (3)加工表面(过渡表面):切削刀具正在进行切削加工的表面。
2、切削用量 切削用量三要素: (1)切削速度v c:切削速度是主运动的线速度(m/s或m/min) 主运动为旋转运动v c =πd n/1000 往复运动v c = 2Lnr /1000 (2)进给量:刀具相对工件沿进给方向移动的距离。 1)进给速度v f(mm/min) 进给速度v f = n f = n f z z (mm/s 或mm/min) 2)进给量f(mm/r) 3)每齿进给量f z(mm/z) (3)背吃刀量(切削深度)a p(mm):已加工表面与待加工表面间的距离。 车削外圆时a p = (dw-dm)/2 钻孔时a p = dm/2
机加工车间规章制度
机加工车间规章制度 机加工车间规章制度 一、管理要求: 1.培养和营造车间全体员工的团队精神,做到“四个统一”即:观念统一、着装统一、行动统一、操作统一。 2.效率的提升,是靠激励、互助、协同、鼓动出来的。 3.根据产品的实际情况: a)合理安排,做到定岗、定置、定员工作。 b)生产所需的工具与物料配备要齐、不能缺东少西。 c)岗位异常时要提前发现,及时纠正。 d)关注产出,坚持每天公示产量。 4.机器保养与整理: a)每天保持工作范围清洁、干净无杂物,所有物料应统一靠黄线摆正,不准压线,确保物流(安全)通道畅通。 b)下班前,需整理工作范围,对机器、地面进行清扫、清洁,并确保一些死角无脏物,凳子需统一摆好,保持整齐。 c)员工对自己操作的机器设备进行日常保养与维护工作,每月的进行定期保养工作。 二、岗位作业要求: a)根据技术要求选择相对应的丝攻并夹紧。 b)攻丝前先固定紧工作台、夹具及摇臂,禁止用手握住工件直接攻丝。 c)夹具尽可能的固定在工作台的中心位置,防止夹不牢现象出现。
d)操作时禁止敞开衣服或戴手套,头部不要离攻丝机器太近,女员工头发要盘起来,男员工不得留长头发。 e)擦拭机器、更换丝攻、交换皮带或加油时均应先停机再处理。 f)使用长而细的丝攻时,应预先垫好支撑物。g)攻丝时应注意品质,不要现大螺、未攻丝或未攻透现象。 3.铆接工序要求(包括穿铆钉、铆接): a)穿铆钉工位要检查铆钉、刀柄、刀座、铆盖是否与生产的产品相符合,铜件颜色和亮度是否正确、各配件是否变形等。 b)铆接工位要检查铆盖是否与所生产的产品相符合,注意铆接上的松、紧调整等。 以上两个工位要求大家齐心协力,有团队理念。 三、环境卫生与秩序: 1.所属员工有义务和责任,保持车间内的环境卫生整洁有序、物品(料)摆放有秩序。 2.各人负责公共区域的清理、清扫工作。 3.车管人员负责本办公室的清理、清扫工作。 4.车间和车间办公室内严禁吸烟。 四、生产过程管控: 1.生产任务:车间负责人按生产任务单的要求,在规定时间内有计划的保质、保量完成生产任务,如完成不了,应即时向上级主管汇报,以便协调;同时切实安排好车间生产,保证各组的正常生产,避免衔接不良、产生误工。 2.产品质量:保证产品零配件符合质量要求和物料正确与齐备,尤其是确保产品首件质量的前提下,在生产过程中要时刻关注产品的质量,巡检人员应按
机加工车间安全管理制度最新完整版
. 天鹰缸套有限公司 机加工车间安全管理制度
. 总则 第一条为加强公司安全生产工作,促进公司全面健康发展,根据国家安全生产法律、法规、政策,结合公司的实际情况,特制定本制度。 第二条公司的安全生产工作必须贯彻“安全第一,预防为主”的方针,贯彻执行行政领导负责制,公司负责人和各部门负责人要坚持“管生产必须管安全”的原则,生产要服从安全的需要,实现安全生产和文明生产。 第三条对在安全生产方面有突出贡献的部门和个人要给予奖励,对违反安全生产制度和操作规程造成事故的责任者,要给予严肃处理,触及刑律的,交由司法机关处理。 第四条本制度适用于公司全体生产人员、生产管理员和与生产相关的其他人员。 第五条本制度经总经理签署后,自公布之日生效。 生产安全管理 安全生产教育制度 一.安全教育的规定 1.必须认真地对新工人进行安全生产的入厂教育、车间教育和现场教育,并且经过考试合格后,才能准许其进入操作岗位。 2.对于从事特种作业的工人必须进行专门的安全操作技术训练,经过考试合格后,才能准许他们持证上岗操作。 3.建立班前班后教育制度,对员工进行经常的安全教育。并且注意结合员工文化生活,进行各种安全生产的宣传活动。 二.安全生产教育的主要形式和方法 1.三级教育:在工业企业所有伤亡事故中,由于新工人缺乏安全知识而产生的事故发生率一般为50%左右,所以对新工来厂实习人员和调动工作的工人,要实行厂级、车间、班组三级教育。 A.厂级安全教育(行政部):①工厂的性质及其主要工艺流程;②我国安全生产的方针、政策法规和管理体制;③本企业劳动安全卫生规章制度及状况、劳动纪律和有关事故案例;④工厂内特别危险的地点和设备及其安全防护注意事; ⑤新工人的安全生产责任制等内容。 B.车间安全教育(部门主管):①本车间的生产性质和主要的工艺流程;②本车间预防工伤事故和职业病的主要措施; ③本车间的危险部位及其应注意事项;④本车间的安全生产的一般情况及其注意事项;⑤本车间的典型事故案例;⑥新工人的安全生产职责和遵章守纪的重要性。 C.班组安全教育(主管、班长):①班组的工作性质、工艺流程、安全生产的概况和安全生产职责范围;②新工人将要从事的生产性质、安全生产责任制、安全操作规程以及其它有关安全知识和各种安全防护、保险装置的作用③;工作地点的安全生产和文明生产的具体要求;④容易发生工伤事故的工作地点、操作步骤和典型事故案例介绍;⑤个人防护用品的正确使用和保管;⑥发生事故以后的紧急救护和自救常识;⑦遵章守纪的重要性和必要性。