压铸工艺与压铸模具设计要点说明

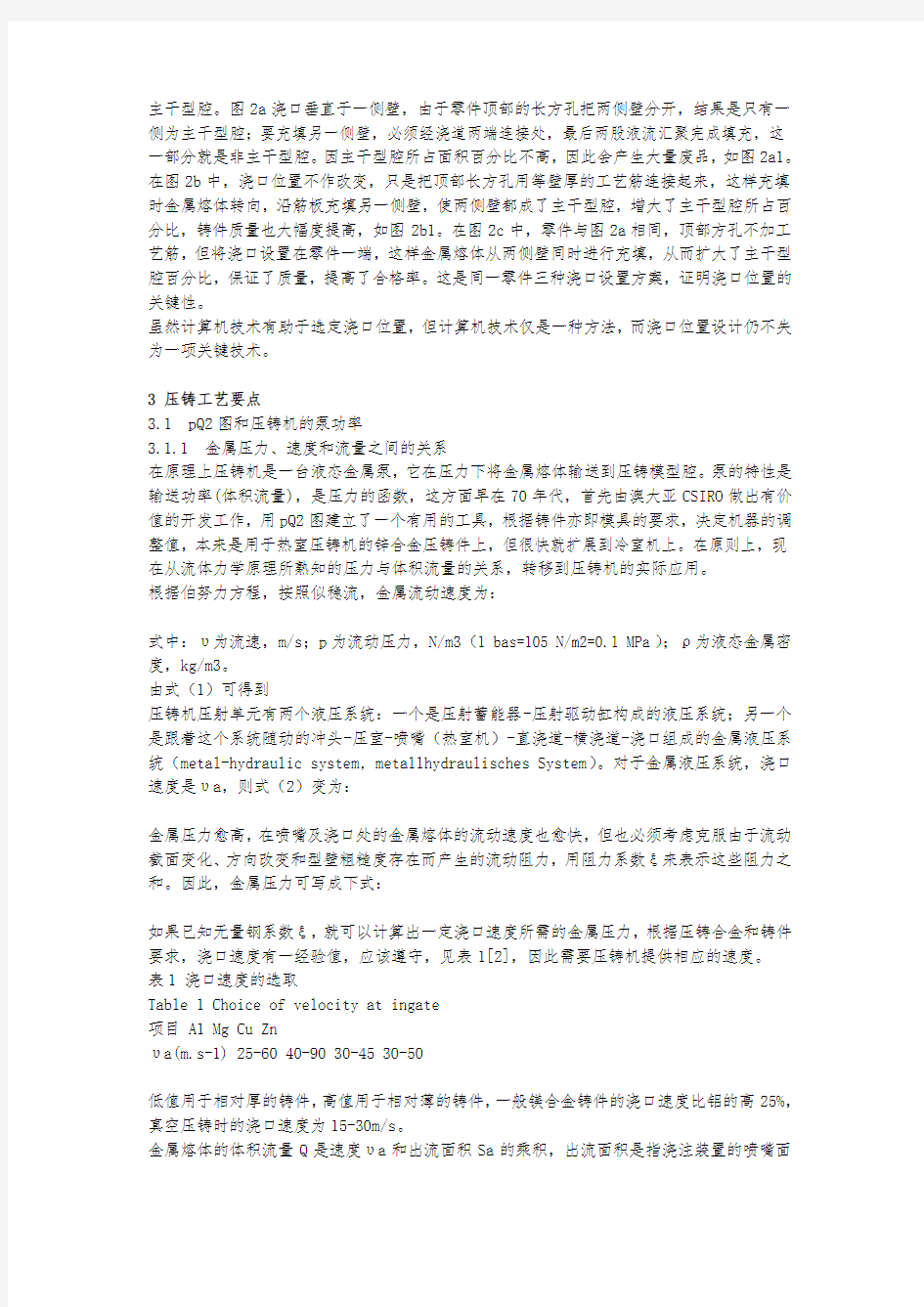
压铸工艺及压铸模具设计要点
摘要:压铸机、模具与合金三者,以压铸件为本,压铸工艺贯穿其中,有机地将它们整合为一个有效的系统,使压铸机与模具得到良好的匹配,起到优化压铸件结构,优选压铸机、优化压铸模设计、提高工艺工作点的灵活性的作用,从而为压铸生产提供可靠保证。所以,压铸工艺寓于模具中之说,涵之深不言而喻。
关键词:压铸机;模具;压铸工艺;模具设计
The Main Points of Die Casting Process and
Die Casting Die Design
PAN Xian-Zeng, LIU Xing-fu
Abstract: The die casting machine, die and alloy, the three on the basis of die castings, running through with the die casting process forms organically a whole and an effective system. Making the machines well to mate with dies, optimization of die casting construction, optimization of selecting die casting machine, optimization of die design and improving the flexibility of die casting process conveys in the die, this has a profound intension.
Key words: die casting machine; die; die casting process; die design
1 压铸机—模具—合金系统
压铸机、模具和合金这三个因素,在压铸件生产过程中,它们构成了一个系统,即压铸机-模具—合金系统,它是以压铸件为本,工艺贯穿其中,赋予系统活力与效率,而模具则是工艺进入系统的平台。压铸机、模具与合金三者关系形象地表示如图1所示。
压铸机-模具-合金系统主要表现为:
(1) 浇口的位置影响充填金属熔体的流动方向及状态,和充填型腔的质量,对模具结构和工艺产生决定性影响,这是关键所在。
(2) 选定最佳充型时间,这是非常重要的一步,影响到充型时的金属熔体的体积流量(Q),也就是充型功率,并据此计算浇口尺寸。
(3) 选择排气、溢流的位置和尺寸,除正常的排气、排污和温度平衡外,还可减少冲击压力,避免金属飞溅和产生毛刺。
(4) 加热与冷却,平衡模具温度,保持工作温度。
2 压铸工艺与模具设计的关键技术
压铸时浇口的位置影响压铸件的结构设计、质量和压铸模具设计,通过查询资料可得到正确设置浇口位置的提示。由于铸件结构的多样性,要选择浇口的正确位置是很困难的,但也有一些基本要求,如普遍认为设置浇口要使充型时的金属射流尽可能地以自由射流在型腔中流过较长距离,也就是正确的浇口位置、形状、尺寸(流向角)配合压铸参数可获得金属射流沿型壁不断有序扩展、转向,并连续不断地扩展至尽头。型腔的大部分(即主干型腔)由射流充填完成,只有一小部分型腔(即非主干型腔)由金属熔体支流补充完成或由金属熔体股流相碰撞完成充填,并通过排溢系统排除残余。图2为浇位置与主干型腔示意图[1]”。
同一个压铸件选择不同的浇口位置和流向角,可以得到不同的主干型腔、非主干型腔和各自占有的面积百分数,图2中的壳体压铸时,由于浇口的位置不同,得出不同的主干型腔和非
主干型腔。图2a浇口垂直于一侧壁,由于零件顶部的长方孔把两侧壁分开,结果是只有一侧为主干型腔;要充填另一侧壁,必须经浇道两端连接处,最后两股液流汇聚完成填充,这一部分就是非主干型腔。因主干型腔所占面积百分比不高,因此会产生大量废品,如图2a1。在图2b中,浇口位置不作改变,只是把顶部长方孔用等壁厚的工艺筋连接起来,这样充填时金属熔体转向,沿筋板充填另一侧壁,使两侧壁都成了主干型腔,增大了主干型腔所占百分比,铸件质量也大幅度提高,如图2b1。在图2c中,零件与图2a相同,顶部方孔不加工艺筋,但将浇口设置在零件一端,这样金属熔体从两侧壁同时进行充填,从而扩大了主干型腔百分比,保证了质量,提高了合格率。这是同一零件三种浇口设置方案,证明浇口位置的关键性。
虽然计算机技术有助于选定浇口位置,但计算机技术仅是一种方法,而浇口位置设计仍不失为一项关键技术。
3 压铸工艺要点
3.1 pQ2图和压铸机的泵功率
3.1.1 金属压力、速度和流量之间的关系
在原理上压铸机是一台液态金属泵,它在压力下将金属熔体输送到压铸模型腔。泵的特性是输送功率(体积流量),是压力的函数,这方面早在70年代,首先由澳大亚CSIRO做出有价值的开发工作,用pQ2图建立了一个有用的工具,根据铸件亦即模具的要求,决定机器的调整值,本来是用于热室压铸机的锌合金压铸件上,但很快就扩展到冷室机上。在原则上,现在从流体力学原理所熟知的压力与体积流量的关系,转移到压铸机的实际应用。
根据伯努力方程,按照似稳流,金属流动速度为:
式中:υ为流速,m/s;p为流动压力,N/m3(1 bas=105 N/m2=0.1 MPa);ρ为液态金属密度,kg/m3。
由式(1)可得到
压铸机压射单元有两个液压系统:一个是压射蓄能器-压射驱动缸构成的液压系统;另一个是跟着这个系统随动的冲头-压室-喷嘴(热室机)-直浇道-横浇道-浇口组成的金属液压系统(metal-hydraulic system, metallhydraulisches System)。对于金属液压系统,浇口速度是υa,则式(2)变为:
金属压力愈高,在喷嘴及浇口处的金属熔体的流动速度也愈快,但也必须考虑克服由于流动截面变化、方向改变和型壁粗糙度存在而产生的流动阻力,用阻力系数ξ来表示这些阻力之和。因此,金属压力可写成下式:
如果已知无量钢系数ξ,就可以计算出一定浇口速度所需的金属压力,根据压铸合金和铸件要求,浇口速度有一经验值,应该遵守,见表1[2],因此需要压铸机提供相应的速度。
表1 浇口速度的选取
Table 1 Choice of velocity at ingate
项目 A1 Mg Cu Zn
υa(m.s-1) 25-60 40-90 30-45 30-50
低值用于相对厚的铸件,高值用于相对薄的铸件,一般镁合金铸件的浇口速度比铝的高25%,真空压铸时的浇口速度为15-30m/s。
金属熔体的体积流量Q是速度υa和出流面积Sa的乘积,出流面积是指浇注装置的喷嘴面
积或压铸模的浇口面积,其关系为
Q=υaSa
式中:Sa为出流面积,m2。将式(5)代入式(4)得到:
公式(6)指出了金属压力和金属流量的关系;充型时,如果体积流量Q不足或液流速度υa 达不到要求,就必须提高金属压力,p升高,Q、υa就会升高,即可达到充型要求。提高压力可通过提高压射阀前蓄能器压力,也可通过调节压射系统压力调节阀(即节流阀)的开度实现。
由式(6)可知,在金属密度ρ、出流面积Sa一定时,所需金属压力p与体积流量Q的平方成正比。为了描绘压力是体积流量的函数,在纵座标上p采用线性分度,Q在横座标上采用平方分度,从座标原点引出一条直线,表示相应的阻力系数ξ,并代表了相应出流面积Sa 时的压力的体积流量的关系,这是通常在pQ2图中的阻力线或模具线(DL),见图3[2]。在理想状态下,无流动阻力,则ξ=1,阻力线对横座标比较平坦即夹角小,阻力愈大,ξ值越小,阻力线对横座越徒,夹角也愈大,见图4[2]。
3.1.2 压铸机的泵功率和机器特性线(pQ2图)
一台已知压铸机它可供使用的金属压力是多高?对此存在两个简单的极限条件:
(1)如果活塞(冲头)速度为零(活塞停止),也就是充型结束时,能达到的最大金属压力(不接通增压器);
(2)如果压室中无金属压射时(所谓空压射)冲头所能达到最高的速度,此时可得到最大体积流量,金属压力等于零。
两个极根条件是可确实的,参照图5[2]压铸机的压射装置示意图和下面的公式
式中:p1为压射(驱动)缸中的压力,bar;ps为蓄能器压力,bar;υ0为活塞速度,m/s;υ ot max为最大活塞速度(空压射速度),m/s。
由图5和式(7)可以看出:如果υ0=0(活塞停止),则p0=ps,就是说压射后在压射缸中建立起全蓄能器压力;如果相反,υ0=υ ot max(空压射速度),则p1=0,也就是压射活塞上无压力。
如果蓄能器压力和压射活塞面积已知,可以计算静金属压力pstat,它是压射终了冲头施加在金属上的压力。
(8)
式中:pstar为静金属压力,bar;pa为蓄能器压力,bar;A1为压射(驱动)活塞面积,m2;A0为冲头面积。
第二个极限条件(最大体积流量)可由空压射时活塞速度求得,见公式(9)。活塞速度和随动的冲头速度可由测量速度的传感哭(常用位置传感器)测得,见图6[3]。
式中:Qmax为空射时最大体积流量,m3/s;υ ot max为最大活塞(冲头)空压射速度,m/s;A0为冲头面积,m2。
把两个最大值pstat和Qmaxt在pQ2图的座标中用一直线相连,就得到所谓的机器特性线(ML),见图7[2];适于相应的压射活塞、冲头面积,及测量时所选调的蓄能器压力和压射阀开度。此特性线确定了为得到所需金属体积流量,可提供的金属压力。
为了检验,在充型阶段测量压力和活塞(冲头)速度以及充型时间,冲头速度乘以冲头面积求得体积流量Q,Q在充型阶段用所测得的金属压力(即所描绘的压力曲线)也可读取。
体积流量Q也可由铸件体积和充型时间之商(或由铸件重量除以金属熔体密度和充型时间之积)求得,这个与p和Q有关的工作点必须位于机器特性线上,机器特性线也可在不知道
Qmax时,从pstat经过用金属压射时的工作点连接直线,并延长至横座标,其交点就是Qmax。工作点也是阻力线与机器特性线的交点,流动阻力愈大,工作点的位置愈高,金属压力也愈高,相应的体积流量就愈小,随着浇口截面积变小,增加了流动阻力,阻力线走势更陡,因为对同等锁模力的机器,存在明显的压射功率的区别,对相同的压铸模也产生泵功率(也就是可供的体积流量)相应的区别(见图8[2])。相同锁模力的机器有很不同的泵功率,随着锁模力升高,泵功率不一定要跟着同样增大,锁模力对已知铸件投影面积是否足够,机器是否够大,必须检验,可藉助于pQ2图使已知的机器所能提供的需要的金属输达能力得到保证。因为压铸机特性上的工作点位置是通过机器的输出特性和已知的流动阻力确定的,为了创造生产铸件的最佳压铸条件,对此应进行优化,这种优化是基于提供冲头最大的压射功率。如G. L. Wilson所指,要满足用金属压铸的压射功率最大,则体积流量是:
也就是:
从这一点出发的机器特性与纵座相交于静压pstat。机器特性线上工作点,已知Q值,相对应金属压力p约为金属静压的2/3;如果选择式(10)(11)的条件,如图9所示[2],则
这是对已知铸件所需流量Q优化的原则,如何才能使机器特性与铸件所需相匹配,以此有三种可能:可选调的压射阀、可调的蓄能器压力、选择相配的冲头直径。表2是这三种调节对机器特性线的影响。
在pQ2图中机器特性线是很有涵的,如表2所述那样,可进行相应的变化、调节。如果将阻力线加入其中,那就更具指导意义。
3.2 铸件压铸所需的机器pQ2图
对已知铸件所需流量Q,根据公式(10)(11)和(12)的条件进行优化,而得到铸件压铸所需的机器特性线(pQ2图),见图10,并用来与所选压铸机的特性线进行比较。
优化计算过程和比较方法如下。
(1)已知铸件重量G(包括溢流槽),液态合金密度ρ(g/dm3),并根据铸件结构、壁厚和技术要求选取充型时间τ;按公式(13)求得金属流量Q0,并根据所优化原则公式(11)求得最大金属流Q0=Gτ/ρ
(2)按下式求得充型时所需的金属压力p0。
式中:υa=浇口速度(m/s)根据铸件要求(参照表1)选取;ξ为阻力系数;ρ为液态金属密度,g/cm3。根据优化原则,按公式(12)求最大金属压力p0’=2/3p0。
(3)在图10中,联接p0’与Q0’两点完成工艺所需的机器特性线(MLXU),并与所选机器的特性线(ML)进行比较,一般说来,只要工艺所需要的机器特性线MLXU位于所选机器的特性线ML的下方,就表明所选机器能满足压铸该零件的需要,至于供需之间的最佳匹配,则与模具特性(DL)有关。如果工艺所需要的机器特性线MLXU不能或不能完全位于机器的特性线ML的下方,则可以按照表2所述的改变浇口截面积(即改变DL的斜率)等方法,以使供需平衡如图10、11、12和13所示,否则应另选合适的压铸机。
3.3 以铸件为本,优化压铸机—模具—合金系统,提高工艺灵活性
在压铸机—模具—合金系统中,通过调整工艺参数,可以改善压铸件的质量和性能。这些工艺参数用一个工作窗口(OW)加以限定。这说明OW是这些工艺参数的极限图。在压铸工艺中,充型时间、浇口速度和最终金属静压用以限定OW,这些参数与充型现象有关,依赖于模具设计和压铸机性能。在模具设计时,OW的所有点被认为都是相等的,并无优先权,可以认为最佳工作点存在于OW的未知点上,在压铸模装在压铸机上试模之前是无法找到它
的。在模具设计阶段保证易于找到良好工作点是基于灵活性的考虑,灵活性是在OW通过调节获得的。
为此,将工艺参数分成软参数和硬参数两种,软参数是指通过操作或一个控制装置进行调节的参数,如功率水平、金属压力、熔体温度、模具温度和循环时间等参数。硬参数是指一种需修正的模具或同时需修正的压铸机,如冲头直径、浇口面积、排气槽等。软参数在试模时容易更改并获得成功,硬参数更改起来则既困难又费钱、费时,常常需要拆卸模具以便重新修正。因此,优化手段是基于软参数并扩大OW调整点的灵活性,从而为模具试验提供较大的围,避免费时费钱的模具更改。
3.3.1 压铸机包容线(MPE线)
压铸机包容线(MPE线)是一条与压铸机所有的特性线相切的双曲线,如图14所示。MPE线是压射用蓄能器压力pakk、最大空压射速度υot max和压射活塞面积A1的函数。
P=α/Q而式中:α为压射系统所能提供的压射功率,kW。
显然,MPE线与冲头直径无关,是压铸机压射终了的通用特性。它表示储存于充型蓄能器的能量在压射阶段通过液压系统施加于金属熔体上,位于MPE线下面的面积(图15)包括在机器的特性之。
3.3.2 优选浇口面积
充型时间和浇口速度的极限如图15所示,pQ2图中的OW区域用υa max、υa min、tf max 和tf min加以限定,tf max为充满铸型前只是部分凝固所需要的时间,tf min是充满型腔前能将型型腔的气体(空气+涂料蒸气)充分排出的时间。在增加模具排气能力或用真空时,tf min可以向更低值移动以增加OW的面积。υa min可以流动模型(雾化,层流)获得,υa min则考虑模具的侵蚀和磨损。
一般地,铝压铸件tf min≈30 ms,(铝压铸件表面镀层)不镀时为60 ms,A1合金为25~60 ms,锌压铸件tf min≈20 ms,(锌压铸件表面镀层)不镀时为40 ms,Zn合金30~50ms;镁优质压铸件tf min≈30 ms,一般不大于40ms,Mg合金40~90ms;Cu合金tf min为30~45ms。浇口面积由DL线的斜率来表示,DL线斜率随浇口面积增大而减少,DL线穿过OW右下角对应于最大浇口面积,反之穿过左上角则对应于最小浇口面积,如图15所示。
充型时间与浇口速度之间的关系是由所选择的特定的浇口面积所建立的,并描绘成一条DL 线。DL线通过OW并由其所截的线段是所有可能的充型的时间和浇口速度组合的区域,OW 并在MPE线之下DL线的长度是灵活性的图解,较长的线段表明调整点有较高的灵活性,DL 线下面的三角形面积A(图15所示)是可选择围,面积大则说明可调整的余地大。线段和面积两种方法表示灵活性都是允许的。如图16所示是最佳调定的pQ2图上的表示,DL线是OW的对角线,这样具有最大的灵活性,为了达到这一目的就要改变OW的极限并适当地调节MPE线和ML线。
3.4 从压射曲线说起
当今压铸机常配以三级压铸系统:第一级为冲头慢速渐进,将金属熔体推至浇口,即所谓慢压射阶段;第二级是冲头以高速将金属熔体通过浇口,在规定的时间充满型腔,即充型阶段;第三级为尚未完全凝固的铸件在高压下(启动增压器)进行凝固和被压实,即压实阶段。图17所示为典型的三级压射曲线示意图,图中曲线分成一级慢压射、二级充型和三级增压压实三个阶段。有些压射系统将第一级压射又分成两个小部分,第一部分是冲头先封住浇料口(图18所示X1线),第二部分为慢压射阶段,然后再进行光型和压实,这就成了四级压射系统,这样除了可避免熔体溅出浇料口,更可以提高压室初始充满度。
3.4.1 慢压射阶段
慢压射阶段在工艺上主要是选控慢压射速度,目的是在金属熔体涌至浇口时,压室中的气体能完全从浇口进入型腔,而不被金属熔体包裹,避免在铸件中形成气孔;为此,需要选择一个临界冲头速度,可以是等加速度,也可以是恒速,一般说,等加速度效果好。国外压铸机多配以“Parashot'’或“SIMUI”的等加速度的慢压射的速度选控系统,图19、图20[2]可作为选控慢压射速度之参考。
3.4.2 充型阶段
此阶段在工艺上最应关注的是:充型时间、压射速度、浇口速度和空压射速度的相互关系,及主要要参数的选择。
3.4.2.1 最佳充型时间
充型时间就是金属熔体流过浇口,以高的浇口速度,在金属熔体停止流动前充满型腔的时间。这一时间很短,是一个非常关键的参数,是选用压铸机,进行工艺设计和模具设计的基础。
充型时间要短,目的是充型时在铸件最小的部位或液流远端不产生早期凝固,避免铸件出现缺肉、冷隔等缺陷。充型时间越短,充型速度就越高,会加大型腔磨损,还可能因胀型而金属飞溅和产生飞边;充型速度高,会使型腔中气体没有足够时间从型腔中逸出。充型时间的正确选择只有综合考虑才能得到,表3给出了选择充型时间和浇口速度的相关因素[4]。
金属熔体从工作温度到凝固温度释放的热量决定了其在相同导热率下保持可铸性的时间,因此这种热量便作为判定其最大可充型时间的尺度。释放热量与充型时间成正比,根据热量比可以得到几种合金的充型时间的关系。Mg合金、Zn合金、A1合金和Cu合金在相同凝固条件下,从工作温度到凝固温度释放的热量分别为261、329、509、918kCal/dm3,则它们的型时间比为τMg:τZn:τAI:τCu ≈0.51:0.65:1:1.8。也就是说τMg=:0.51τAI,τZn=0.65τAI,τCu=1.8τAI。
表4给出了充型时间与壁厚有关的推荐值,更确切地说与凝固模数有关。一些世界著名的公司如瑞士Buehler也以此作为选择充型时间的依据。早先的资料中是按铸件平均壁厚计算的,而后来资料也有按最小壁厚计算的。
注:最大值用于铝合金,中间值用于锌合金,最小值用于镁合金。
B.Nogowizin基于材料的热性质和他人经验,从试验出发,得到最佳充型时间关系式[3]:
式中:τ为充型时间,s为铸件平均壁厚;ρ为固、液相间合金密度平均值;HSW为合金熔化热;C为固、液相间合金平均化热容;tL为合金液相线温度;f为固相率;?t为液相线温度与固相率为f时温度之间隔;tF为模具温度;λF为模具材料的导热率;CF为模具材料的比热容;ρF为模具材料的密度。
此时,浇注温度tg=tL+ (60~120)(℃)
压铸时显然金属液在型腔中无过热,人们观察到熔体流中具有一定数量的固相,当固相率达到30%~80%时,在型腔中熔体运动只能通过高的流入速度,当最佳充型时间按式(17)计算时,相当于f值为70%~80%。
图21中可以确定液相线温度和形式70%~80固相时的温度间隔,即?t=38℃,表5[3]和表6中列举模具钢1.234 4(X40CrMoV51)和压铸合金的物理性质,也可用于1.234 3(X38CrM051)、1.236 5(X32CrMoV33)和1.236 7(X38CrMov53)[3]。铝合金和铜合金的熔化热的经验值不详,所以用理论值。试验指出,镁合金的熔化热等于纯镁的熔化热。表7[3]是按式(17)和按f=70%计算的最佳充型时间,如f=80%时,则表中数据要扩大1.3倍。由表5可知A1-Si和AISiCu合金最佳充型时间要比Al-Mg合金长1.2~1.6倍,这归因于Si高溶化热,使含硅的
《压铸工艺及模具设计》复习题1-答案教学内容
压铸模具设计复习题 一、名词解释 1、压力铸造:压力铸造是将熔融状态或者半熔融状态的金属浇入压铸机的压室,在高压力的作用下,以极高的速度充填在压铸模(压铸型)的型腔内,并在高压下使熔融或者半熔融的金属冷却凝固成形而获得铸件的高效益、高效率的精密铸造方法。 2、压射压力:压射压力Fy是压射机构(压射缸内压射活塞)推动压室冲头运动的力,即压射冲头作用于压室中金属液面上的力。 3、压射速度:即压室内压射冲头推动金属液的移动速度(又称冲头速度) 4、内浇口速度:是指金属液通过内浇口时的线速度(又称充填速度) 5、合金浇注温度:是指金属液从压室进入型腔的平均温度,因测量不便,通常以保温炉内的温度表示。一般高于合金液相线20~30℃ 6、模具的工作温度:模具的工作温度是连续工作时模具需要保持的温度。 7、充填时间:金属液自开始进入模具型腔直至充满型腔所需的时间称为充填时间。 8、增压建压时间:是指金属液在充模的增压阶段,从充满型腔的瞬时开始,至达到预定增压压力所需的时间,也就是比压由压射比压上升到增压比压所需的时间。 9、压室充满度:浇入压室的金属液量占压室容量的百分数称压室充满度。 10、压铸机的压射机构:是将金属液推送进模具型腔填充成型为压铸件的机构。 二、填空题(每空1分,共计20分) 1、金属液充填理论主要有:喷射充填理论、全壁厚充填理论、三阶段充填理论 2、压铸按压铸机分类:热室压铸、冷室压铸 3、液态金属成型新技术有:真空密封造型、气压铸造、冷冻造型 4、压铸用低熔点类合金主要有:锌、锡、铅。 5、压铸生产中,要获得表面光滑及轮廓清晰的压铸件,下列因素起重要作用:(1)压射速度 (冲头速度);(2)压射比压;(3)充填速度(内浇口速度)。 6、压铸铁合金种类:压铸灰铸铁、可锻铸铁、球墨铸铁、低碳钢、不锈钢、合金钢和工具钢等。 7、铸造方法有砂型铸造、特种铸造。压铸工艺属于特种铸造工艺范畴。 8、常见压铸的分类方法:按压铸材料分类、按压铸机分类、按合金状态分类 9、压铸按压铸材料分类:单金属压铸、合金压铸 10、压铸用高熔点类合金主要有:铝、镁、铜。 11、压铸合金、压铸模和压铸机是压铸生产的三大要素。 12、压铸新技术有真空压铸、加氧压铸和定向抽气加氧压铸、精速密压铸、半固态压铸、挤 压压铸、铁合金压铸。 三、判断题(每小题1分,共计10分) 1、全壁厚充填理论所提出的充填形态是最理想的。 2、充填过程主要有以下3种现象:(1)压入(2)金属液流动(3)冷却凝固。 3、压力铸造属于特种铸造中金属型(即压铸模)在压力机上进行生产的一种精密铸造,其最终产品为压铸件。
压铸模具设计开题报告
辽宁工程技术大学 本科毕业设计(论文)开题报告 题目螺杆套压铸模铸造______________ 指导教师付大军 ______________________ 院(系、部)材料学院 ______________ 专业班级成型08—4 _____________ 学号0808020409 ___________________ 姓名刘冠男__________________________ 日期2012-3-2 _______________ 教务处印制
一、选题的目的、意义和研究现状 根据对螺杆套压铸模的设计,了解和熟悉压力铸造的工艺设计过程和模具的设计过程。对压力铸造过程,模具的设计过程中以及实际应用过程中出现的缺陷问题,根据压铸模具工艺设计的理论与实践的结合,在外套的工艺结构不影响其性能和使用的情况下进行相应合理的设计,从而达到避免缺陷,提高外套工作性能的目的 社会需要是促进科学技术发展的主要原因。当一种生产工艺不能满足社会需要时,就会有新的更好的工艺产生,压铸技术的出现就是如此。压铸最早用来铸造印刷用的铅字,当时需要生产大量清晰光洁以及可互换的铸造铅字,压铸法随之产生。1885年奥默根瑟勒(Mergenthaler)发明了铅字压铸机。最初压铸的合金是常见的铅和锡合金。随着对压铸件需求量的增加,要求采用压铸发生产熔点和强度都更高的合金零件,这样,相应的压铸技术,压铸模具和压铸设备就不断地改进发展。1905年多勒(Doehler)研究成功用于工业生产的压铸机,压铸锌,锡,铅合金铸件。1907年瓦格纳(Wagne)首先制成启动活塞压铸机,用于生产铝合金铸件。1927年捷克工程师约瑟夫。波拉克(Joset Polak设计了冷压室压铸机,克服了热压室压铸机的不足之处,从而使压铸生产技术前进了一大步,铝,镁,锌,铜等合金零件开始广泛采用压铸工艺进行生产。压铸生产是所有压铸工艺中生产速度最快的一种,也是最富有竞争力的工艺之一,使得它在短短的160 多年里的时间内发展成为航空航天,交通运输,仪器仪表,通信等领域内有色金属铸件的重要生产工艺。[6]-[8] 20 世纪60 年代至70 年代是压铸工艺与设备逐步完善的时期。而70 年代到 现在,则是电子技术和计算机技术加速用于压铸工艺与设备的大发展阶段。数控压铸机,计算机控制压铸柔性单元及系统和压铸工艺与设备计算机辅助设计的出现,标志着压铸生产开始从经验操作转变到科学控制新阶段,从而使压铸件的质量,自动化程度及劳动生产旅都得到了极大的提高。[9] 在压铸生产中,正确采用各种压铸工艺参数是获得优质压铸件的重要措施,而金属压铸模则是提供正确选择和调整有关工艺参数的基础。所以说,能否顺利进行压铸生产,压铸件质量的优劣,压铸成型效率以及综合成本等,在很大程度上取决于金属压铸模结构的合理性和技术的先进性以及模具的制造质量。[4] 由于金属压铸成型有着不可比拟的突出优点,在工业技术快速发展的年代,必将得到越来越广泛的应用。特别是在大批量的生产中,虽然模具成本高一些,但总的说来,其生产的综合成本得到大幅度降低。在这个讲求微利的竞争时代,采用金属压铸成型技术,更有其积极和明显的经济价值。 近年来,汽车工业的飞速发展给压铸成型的生产带来了机遇。由于可持续发展和环境保护的需要,汽车轻量化是实现环保,节能,节才,告诉的最佳途径。 因此,用压铸合金件代替传统的铸铁件,可使汽车质量减轻30%以上。同时,压铸合金件还有一个显著地特点是传导性能良好,热量散失快,提高了汽车行车安全性。因此,金属压铸行业正面临着发展的机遇,其应用前景十分广阔。[2] 中国的压铸业经历了50多年的锤炼,已经成为具有相当规模的产业,并以每年8%~12%的速度增长,但是由于企业综合素质还有待提高,技术开发滞后于生产规模的扩大,经营方式滞后于市场竞争的需要。从总体看,我国是压铸大国之一,但不是强国,压铸业的水平还比较落后,我国的压铸工业与国际上先进国家相比还有差距,而这些差距正为我国压铸业发展提供了过阔的空间。[3]
常见的压铸模具结构及设计
压铸模具材料与结构设计 压铸模具材料与结构设计目录 1 压铸模具的结构 压铸模具一般的结构如图 1.导柱 2.固定外模(母模) 3分流子镶套 4.分流子5固定内模6角销7滑块挡片 8滑块9.可动内模10.可动外模(公模) 11.模脚12.顶出板13.顶出销承板14.回位销 15.导套 2.压铸模具结构设计应注意事项 (1)模具应有足够的刚性,在承受压铸机锁模力的情况下不会变形。 (2)模具不宜过于笨重,以方便装卸修理和搬运,并减轻压铸机负荷。 (3)模穴的压力中心应尽可能接近压铸机合模力的中心,以防压铸机受力不均,造成锁模不密,铸件产生毛边。 (4)模具的外形要考虑到与压铸机的规格的配合: (a)模具的长度不要与系杆干涉。 (b)模具的总厚度不要太厚或太薄,超出压铸机可夹持的范围。 (c)注意与料管(冷室机)或喷嘴(热室机)之配合。 (d)当使用拉回杆拉回顶出出机构时,注意拉回杆之尺寸与位置之配合。 (5)为便于模具的搬运和装配,在固定模和可动模上方及两侧应钻螺孔,以便可旋入环首螺栓。 3 内模(母模模仁) (1)内模壁厚 内模壁厚基本上不必计算其强度,起壁厚大小决定于是否可容纳冷却水管通过,安排溢流井,及是否有足够的深度可攻螺纹,以便将内模固定于外模。由于冷却水管一般直径约10mm,距离模穴约25mm,因此内模壁厚至少要50mm。内模壁厚的参考值如下表。 内模的高度应该比外模高出0.05-0.1mm,以便模面可确实密合,并使空气可顺利排出。其与外模的配合精度可用H8配h7,如下图所示。 (3)内模与分流子的配合 分流子的功用是将熔汤由压铸机导至模穴内,因此其高度视固定模的厚度而定。分流子的底部与内模相接,使流道不会接触外模,如下图,内模与分流子的配合可用H7配h6。 4外模 (1)固定外模
压铸模具滑块设计
倒勾处理(滑块) 一?斜撑销块的动作原理及设计要点 是利用成型的开模动作用,使斜撑梢与滑块产生相对运动趋势,使滑块沿开模方向及水平方向的两种运动形式,使之脱离倒勾。如下图所示: 上图中: β=α+2°~3°(防止合模产生干涉以及开模减少磨擦) α≦25°(α为斜撑销倾斜角度) L=1.5D (L为配合长度) S=T+2~3mm(S为滑块需要水平运动距离;T为成品倒勾) S=(L1xsina-δ)/cosα(δ为斜撑梢与滑块间的间隙,一般为0.5MM; L1为斜撑梢在滑块内的垂直距离)
二?斜撑梢锁紧方式及使用场合
三?拔块动作原理及设计要点 是利用成型机的开模动作,使拔块与滑块产生相对运动趋势,拨动面B拨动滑块使滑块沿开模方向及水平方向的两种运动形式,使之脱离倒勾。 如下图所示: 上图中: β=α≦25°(α为拔块倾斜角度) H1≧1.5W (H1为配合长度)
S=T+2~3mm(S为滑块需要水平运动距离;T为成品倒勾) S=H*sinα-δ/cosα (δ为斜撑梢与滑块间的间隙,一般为0.5MM; H为拔块在滑块内的垂直距离) C为止动面,所以拨块形式一般不须装止动块。(不能有间隙) 四?滑块的锁紧及定位方式 由于制品在成型机注射时产生很大的压力,为防止滑块与活动芯在受到压力而位移,从而会影响成品的尺寸及外观(如跑毛边),因此滑块应采用锁紧定位,通常称此机构为止动块或后跟块。 常见的锁紧方式如下图:
五.滑块的定位方式 滑块在开模过程中要运动一定距离,因此,要使滑块能够安全回位,必须给滑块安装定位装置,且定位装置必须灵活可靠,保证滑块在原位不动,但特殊情况下可不采用定位装置,如左右侧跑滑块,但为了安全起见,仍然要装定位装置.常见
上盖压铸成型工艺及模具设计设计说明书
压铸工艺及模具 设计说明书 起止日期: 2014 年 12 月 29 日 至 2015 年 01 月 09 日 学生姓名 班级 学号 成 绩 指导教师(签字) 机械工程学院 2015年 01 月 07 日 上盖压铸成型工艺及模具设计
摘要 本课题主要是针对上盖压铸件的模具设计,通过对铸件进行工艺的分析和比较, 最终设计出一副压铸模。该课题从产品结构工艺性,具体模具结构出发,对模具的浇注系统、模具成型部分的结构、顶出系统、冷却系统、压铸机的选择及有关参数的校核、都有详细的设计,同时并简单的编制了模具的加工工艺。通过整个设计过程表明该模具能够达到此铸件所要求的加工工艺。根据题目设计的主要任务是上盖压铸模具的设计,也就是设计一副压铸模具来生产上盖铸件产品,以实现自动化提高产量。通过模具设计表明该模具能达到上盖的质量和加工工艺要求。本文主要运用Pro/ENGINEER wildfire5.0及其AutoCAD2007来完成整个设计工作。从中学习到了许多的模具设计的知识和对在校所学知识的深化。 关键词:上盖压铸件;压铸模具设计;斜销侧抽芯;一模一腔。
目录 第1章压铸件分析 (5) 1.1 压铸件结构分析 (6) 1.1.1 压铸件特点和基本结构 (6) 1.1.2 压铸件精度分析 (6) 1.2 压铸件材料分析 (6) 第2章分型面及浇注系统 (7) 2.1确定分型面 (7) 2.1.1 分型面选择 (7) 2.1.2 分型面方案对比 (7) 2.2 初选压铸机 (7) 2.2.1 型腔数量及布局 (7) 2.2.2 锁模力计算 (7) 2.2.3 初选压铸机 (8) 2.3 浇注系统设计 (9) 2.3.1 直浇道设计 (9) 2.3.2 横浇道设计 (9) 2.3.3 内浇道设计 (10) 2.3.4 溢流槽设计 (10) 2.4 排气系统设计 (11) 第3章成型零件设计 (12) 3.1 成型零件尺寸计算 (12) 3.1.1 型腔尺寸计算 (12) 3.1.2 型芯尺寸计算 (13) 3.1.3 位置尺寸计算 (13) 3.2 成型零件结构设计 (13) 3.2.1 型腔结构设计 (13) 3.2.2 型芯结构设计 (13) 第4章模架选择及设计 (14)
压铸模具设计制造及使用的注意-事项
压铸模具设计制造及使用的注意-事项
压铸模具设计制造及使用的注意事项 一、压铸模设计 除正常设计的基本要求外,还应特别考虑: 1、采用合理先进的简单结构,使动作准确可靠,结构件的刚性良好,即模具具有足够的厚度,以确保其有足够的刚度,以防止模具变形及开裂。易损件拆换方便,有利于延长模具的使用寿命; 2、模具上的零件应满足机械加工工艺和热处理工艺的要求。尽量避免或减少尖角和薄壁,以利于热处理后使用,防止应力集中。 3、大型压铸模具(分型面投影面积大于1平方米),应采用方导柱导向系统,以避免动定模因热膨胀差异较大,造成导向精度下降; 4、对于设计大型复杂压铸模具的浇注系统及排气系统和冷却系统,最好能做流动分析及热平衡分析。这样布置流道系统(直浇道、横浇道、内浇口)和冷却系统及恒温预热系统的位置、管道大小、数量等就会做到合理布局;众所周知,浇注系统是把金属液从压室导入型腔内,它与金属液进入型腔的部位、方向、流
动状态等密切相关,并能调节填充速度、充填时间、型腔温度等充型条件。在压铸生产中,浇注系统对压铸件质量、压铸操作效率、模具寿命(高温、高压、高速的金属液对模具型腔壁的冲刷、腐蚀等),压铸件的切边和清理等都有重大影响,可见浇注系统的设计极其重要; 5、内浇口设计注意事项: ○1从内浇口进入型腔的高温金属液、不宜正面进入冲击动定模型壁及型芯,以防止型腔早期出现严重的冲蚀、粘模和龟裂现象; ○2采用多股内浇口时,要考虑防止出现金属液进入型腔后从几路汇合,相互冲击产生涡流,裹气和氧化夹渣等缺陷; ○3内浇口厚度的选择,一般是按照经验数据制定,建议在满足充型的条件下,尽量选择大些,避免因过大的压射速度冲击,引起模具早期出现侵蚀、粘模、麻点和龟裂; 6、溢流槽和排气槽的设计: ○1溢流槽的作用是积聚首先进入型腔的冷污金属液和裹有气体的金属液,以及调节模具多部分的温度,改善模具热平衡,有利于延长模
压铸模具设计简介
一、压铸简介压力铸造简称压铸,是一种将熔融合金液倒入压室内,以高速充填钢制模具的型腔,并使合金液在压力下凝固而形成铸件的铸造方法。压铸区别于其它铸造方法的主要特点是高压和高速。①金属液是在压力下填充型腔的,并在更高的压力下结晶凝固,常见的压力为15—100MPa。②金属液以高速充填型腔,通常在10—50米/秒,有的还可超过80米/秒,(通过内浇口导入型腔的线速度—内浇口速度),因此金属液的充型时间极短,约0.01—0.2秒(须视铸件的大小而不同)内即可填满型腔。压铸机、压铸合金与压铸模具是压铸生产的三大要素,缺一不可。所谓压铸工艺就是将这三大要素有机地加以综合运用,使能稳定地有节奏地和高效地生产出外观、内在质量好的、尺寸符合图样或协议规定要求的合格铸件,甚至优质铸件。1、压铸机(1)压铸机的分类压铸机按压室的受热条件可分为热压室与冷压室两大类。而按压室和模具安放位置的不同,冷室压铸机又可分为立式、卧式和全立式三种形式的压铸机。热室压铸机立式冷室卧室全立式(2)压铸机的主要参数a合型力(锁模力)(千牛)————————KN b压射力(千牛)—————————————KN c动、定型板间的最大开距——————————mm d动、定型板间的最小开距——————————mm e动型板的行程———————————————mm f大杠内间距(水平×垂直)—————————mm g大杠直径—————————————————mm h顶出力——————————————————KN i顶出行程—————————————————mm j压射位置(中心、偏心)——————————mm k一次金属浇入量(Zn、Al、Cu)———————Kg l压室内径(Ф)——————————————mm m空循环周期————————————————s n铸件在分型面上的各种比压条件下的投影面积注:还应有动型板、定型板的安装尺寸图等。2、压铸合金压铸件所采用的合金主要是有色合金,至于黑色金属(钢、铁等)由于模具材料等问题,目前较少使用。而有色合金压铸件中又以铝合金使用较广泛,锌合金次之。下面简单介绍一下压铸有色金属的情况。(1)、压铸有色合金的分类受阻收缩混合收缩自由收缩 铅合金-----0.2-0.3% 0.3-0.4% 0.4-0.5% 低熔点合金锡合金锌合金--------0.3-0.4% 0.4-0.6% 0.6-0.8% 铝硅系--0.3-0.5% 0.5-0.7% 0.7-0.9% 压铸有色合金铝合金铝铜系 铝镁系---0.5-0.7% 0.7-0.9% 0.9-1.1% 高熔点合金铝 锌系镁合金----------0.5-0.7% 0.7-0.9% 0.9-1.1%
压铸设计说明书)
课程名称:压铸工艺及模具设计课程设计 学院:机械工程专业:材料成形及控制工程姓名:吴远发学号:080803110033 年级:成形082 任课教师: 丁旭
目录 第一章零件的工艺分析 (2) 第二章选用分型面及浇注系统 (3) 第三章压铸机的选用 (4) 第四章计算压铸模成型部分尺寸 (6) 第五章设计零件图 (8)
第一章零件的工艺分析 图1所示为管接头零件图,材料为YL102,按卧式冷室压铸机设计压铸模。 图1 管接头零件图 该零件结构简单,但是两端存在凸台,不利于分型,因此在压铸模具设计时需要设计抽芯机构抽芯。零件表面大部分为圆柱曲面和平面,用一般的机械加工模具即可得到。铸件壁厚基本均匀,铸造难度适中。零件未标注尺寸公差,按要求公差取IT12级,用压铸方法生产该零件能达到相应的尺寸要求。压铸材料为ZL102,为压铸铝合金,可以作为该零件的材料,查手册可知道,其平均收缩率为0.7%。
第二章选用分型面及浇注系统 该零件形状为一圆筒两端带凸台,考虑各方面的因素,采用如图所示的分型面。该零件在卧式冷室压铸机上成型,零件的两端不利于脱模,采用抽芯机构,如图所示。 图2 分型面的确定
图3 浇注系统的确定 第三章 压铸机的选用 计算主胀型力F 主= 10 AP ,查表取该零件的压射比压P 为90Mpa 。面积A 为铸件及浇注系统在分型面上的投影面积,经估算,A 约为40cm 2。所以F 主=90×1÷10=360KN 。 计算分胀型力F 分=∑( 10 P 芯A tan α),F 分=2×(50×90÷10)tan1o=15.7KN; α为楔紧块的楔紧角。 计算锁模力F 锁≥K (F 主+F 分)=1.25×(360+15.7)=470KN 。 现在预选用J1118H 型压铸机,其主要参数:锁模力为1800KN 最大压射力Fmax 为200000N ,现在去压室直径为40mm ,则其对应的最大压射比P: P=4Fmax ×10-6/πD=6 210 4014.3200000 4-???×10-6=159Mpa 。 校核锁模力:F 主=159×40÷10=636KN F 分=159×50÷10=795KN
压铸工艺及压铸模具设计重点
压铸工艺及压铸模具设计要点 摘要:压铸机、模具与合金三者,以压铸件为本,压铸工艺贯穿其中,有机地将它们整合为一个有效的系统,使压铸机与模具得到良好的匹配,起到优化压铸件结构,优选压铸机、优化压铸模设计、提高工艺工作点的灵活性的作用,从而为压铸生产提供可靠保证。因此,压铸工艺寓于模具中之讲,内涵之深不言而喻。关键词:压铸机;模具;压铸工艺;模具设计 The Main Points of Die Casting Process and Die Casting Die Design PAN Xian-Zeng, LIU Xing-fu Abstract: The die casting machine, die and alloy, the three
on the basis of die castings, running through with the die casting process forms organically a whole and an effective system. Making the machines well to mate with dies, optimization of die casting construction, optimization of selecting die casting machine, optimization of die design and improving the flexibility of die casting process conveys in the die, this has a profound intension. Key words: die casting machine; die; die casting process; die design 1 压铸机—模具—合金系统 压铸机、模具和合金这三个因素,在压铸件生产过程中,它们构成了一个系统,即压铸机-模具—合金系统,它是以压铸件为本,工艺贯穿其中,给予系统活力与效率,而模具则是工艺进入系统的平台。压铸机、模具与合金三者关系形象地表示如图1所示。压铸机-模具-合金系统要紧表现为: (1) 内浇口的位置阻碍充填金属熔体的流淌方向及状态,和充填型腔的质量,对模具结构和工艺产生决定性阻碍,这是关键所在。
压铸模具设计开题汇报.doc
压铸模具设计开题报告 压铸是一种金属铸造工艺,其特点是利用模具内腔对融化的金属施加高压。模具通常是用强度更高的合金加工而成的,这个过程有些类似注塑成型。 一、选题的目的、意义和研究现状 根据对螺杆套压铸模的设计,了解和熟悉压力铸造的工艺设计过程和模具的设计过程。对压力铸造过程,模具的设计过程中以及实际应用过程中出现的缺陷问题,根据压铸模具工艺设计的理论与实践的结合,在外套的工艺结构不影响其性能和使用的情况下进行相应合理的设计,从而达到避免缺陷,提高外套工作性能的目的社会需要是促进科学技术发展的主要原因。当一种生产工艺不能满足社会需要时,就会有新的更好的工艺产生,压铸技术的出现就是如此。压铸最早用来铸造印刷用的铅字,当时需要生产大量清晰光洁以及可互换的铸造铅字,压铸法随之产生。根瑟勒Mergenthaler)发明了铅字压铸机。最初压铸的合金是常见的铅和锡合金。随着对压铸件需求量的增加,要求采用压铸发生产熔点和强度都更高的合金零件,这样,相应的压铸技术,压铸模具和压铸设备就不断地改进发展。Doehler)研究成功用于工业生产的压铸机,压铸锌,锡,铅合金铸件。agner)首先制成启动活塞压铸机,用于生产铝合金铸件。约瑟夫。波拉克Joset Polak)设计了冷压室压铸机,克服了热压室压铸机的不足之处,从而使压铸生产技术前进了一大步,铝,镁,锌,铜等合金零件开始广泛采用压铸工艺进行生产。压铸生产是所有压铸工艺中生产速度最快的一种,也是最富有竞争力的工艺之一,使得它在短短的年里的时间内发展成为航空航天,交通运输,仪器仪表,通
信等领域内有色金属铸件的重要生产工艺。 铸工艺与设备逐步完善的时期。而代到现在,则是电子技术和计算机技术加速用于压铸工艺与设备的大发展阶段。数控压铸机,计算机控制压铸柔性单元及系统和压铸工艺与设备计算机辅助设计的出现,标志着压铸生产开始从经验操作转变到科学控制新阶段,从而使压铸件的质量,自动化程度及劳动生产旅都得到了极大的提高。 在压铸生产中,正确采用各种压铸工艺参数是获得优质压铸件的重要措施,而金属压铸模则是提供正确选择和调整有关工艺参数的基础。所以说,能否顺利进行压铸生产,压铸件质量的优劣,压铸成型效率以及综合成本等,在很大程度上取决于金属压铸模结构的合理性和技术的先进性以及模具的制造质量。由于金属压铸成型有着不可比拟的突出优点,在工业技术快速发展的年代,必将得到越来越广泛的应用。特别是在大批量的生产中,虽然模具成本高一些,但总的说来,其生产的综合成本得到大幅度降低。在这个讲求微利的竞争时代,采用金属压铸成型技术,更有其积极和明显的经济价值。 近年来,汽车工业的飞速发展给压铸成型的生产带来了机遇。由于可持续发展和环境保护的需要,汽车轻量化是实现环保,节能,节才,告诉的最佳途径。因此,用压铸合金件代替传统的铸铁件,可使汽车质量减轻,压铸合金件还有一个显著地特点是传导性能良好,热量散失快,提高了汽车行车安全性。因此,金属压铸行业正面临着发展的机遇,其应用前景十分广阔。中国的压铸业经历了,已经成为具有相当规模的产业,并以每年速度增长,但是由于企业综合素质还有待提高,技术开发滞后于生产规模的扩大,经营方式滞后于市场竞争的需要。从总体看,我国
压铸模具制作说明
模具制作标准 目的:为使模具制作及维修作业能降低成本,缩短模具制作周期,确保模具寿命,保证产品品质。 一、制作模具编号: 1、必须在模具外恻上方雕刻或锻打模具编号,字体要求整套 模具字高统一。 2、每块模板均须用字码打上模具编号,且方向统一。 3、模具所有螺丝、吊圈孔及模具部件都必须是公制规格,而 附加模具配件必须是标准规格,禁止自行土制。 二、基准位: 1、每套模具必须在B板和动模板(以动模板为参照)俯视图 视角的右下方做上记号以示基准,以便模具后续维修。 三、码模槽: 1、非工字模胚均需在前后模铣出码模槽,具体尺寸根据模具 大小设计而定。 四、顶柱孔: 1、动模必须开有足够大的顶柱孔,根据模具配比的机台,比 实际顶柱的尺寸大直径10-20MM(除真空模具)。 2、小型且中心进浇模具只需中间开一个顶柱孔,中型模具必 须开三个以上顶柱孔以保持顶出平衡。 五、复位机构装置: 当顶针(丝筒)与行位顶出装置干涉时,必须在模具上设
有先复位装置,不谨靠弹簧使顶针板复位,以免弹簧日后失效,行位(抽芯)与顶针(丝筒)相碰撞。 六、顶针动作: 1、应考虑模具在任何场合顶针都能可靠的顶出产品,并在合 模前顶针不与模具的任何配件相干涉地复位。 2、顶出时产品不能有任何超出产品要求的变形,迅速顶出痕 迹不影响产品表面质量。 3、顶出应平衡很顺,不可出现顶出倾斜现象及顶出有杂音的 产生。 七、行位动作: 1、滑块行位动作应顺滑,保证产品不得有拉变形现象,不可 出现卡死动作,不均匀松动等现象。 2、大滑块滑动部位应开油槽 3、在表面要求较高和壁厚较厚的铸件且有强度要求的产品, 滑块上应设有冷却水路。 4、当滑块滑动行程过长时,必须在模座上增长导向,通常滑 动部位做到宽度的1.5倍左右为宜,抽芯时滑块在导向槽的部分,要有滑块滑动部位的2/3在导向滑槽内。 5、斜导柱与导柱孔的配合间隙必须留有0.2MM以上,禁止 非间隙配合。 6、斜导柱的角度小于滑块锲紧面2度,大滑块的锲尽紧块须 伸入下模15-20MM以斜度面互锁反压。
压铸模具设计简介(doc 8页)
压铸模具设计简介(doc 8页)
一、压铸简介压力铸造简称压铸,是一种将熔融合金液倒入压室内,以高速充填钢制模具的型腔,并使合金液在压力下凝固而形成铸件的铸造方法。压铸区别于其它铸造方法的主要特点是高压和高速。①金属液是在压力下填充型腔的,并在更高的压力下结晶凝固,常见的压力为15—100MPa。②金属液以高速充填型腔,通常在10—50米/秒,有的还可超过80米/秒,(通过内浇口导入型腔的线速度—内浇口速度),因此金属液的充型时间极短,约0.01—0.2秒(须视铸件的大小而不同)内即可填满型腔。压铸机、压铸合金与压铸模具是压铸生产的三大要素,缺一不可。所谓压铸工艺就是将这三大要素有机地加以综合运用,使能稳定地有节奏地和高效地生产出外观、内在质量好的、尺寸符合图样或协议规定要求的合格铸件,甚至优质铸件。1、压铸机(1) 压铸机的分类压铸机按压室的受热条件可分为热压室与冷压室两大类。而按压室和模具安放位置的不同,冷室压铸机又可分为立式、卧式和全立式三种形式的压铸机。热室压铸机立式冷室卧室 全立式(2)压铸机的主要参数a合型力(锁模力)(千牛)————————KN b压射力(千牛)—————————————KN c 动、定型板间的最大开距——————————mm d动、定型板间的最小开距——————————mm e动型板的行程———————————————mm f大杠内间距(水平×垂直)—————————mm g大杠直径—————————————————mm h顶出力——————————————————KN i顶出行程—————————————————mm j压射位置(中心、偏心)——————————mm k一次金属浇入量(Zn、Al、Cu)———————Kg l压室内径(Ф)——————————————mm m空循环周期————————————————s n铸件在分型面上的各种比压条件下的投影面积注:还应有动型板、定型板的安装尺寸图等。2、压铸合金压铸件所采用的合金主要是有色合金,至于黑色金属(钢、铁等)由于模具材料等问题,目前较少使用。而有色合金压铸件中又以铝合金使用较广泛,锌合金次之。下面简单介绍一下压铸有色金属的情况。(1)、压铸有色合金的分类受阻收缩混合收缩自由收缩 铅合金-----0.2-0.3% 0.3-0.4% 0.4-0.5% 低熔点合金锡合金锌合金--------0.3-0.4% 0.4-0.6% 0.6-0.8%
压铸工艺与模具设计复习题
《压铸工艺与模具设计》复习题 一、判断题 1、全立式冷压室压铸机压铸过程是先加料后合模。(√) 2、巴顿认为:充填过程的第一阶段是影响铸件的表面质量;第二阶段是影响铸件的强度;第三阶段是影响铸件的硬度。(×) 3、压铸压力有压射力和胀型力。(×) 4、硅在铝合金中能改善其高温时的流动性,但降低合金的抗拉强度和塑性。(×) 5、压铸件的尺寸精度一般按机械加工精度来选取,在满足使用要求的前提下,尽可能选用较高的精度等级。(×) 6、确定公差带时,待加工的尺寸,孔取正值,轴取负值。(×) 7、压铸件的表面粗糙度取决于压铸模成型零件型腔表面的粗糙度。(√) 8、压铸件表面有表面层,由于快速冷却而晶粒细小、组织致密。(√) 9、同一压铸件内最大壁厚与最小壁厚之比不要大于3:1。(√) 10、铸件上所有与模具运动方向平行的孔壁和外壁均需具有脱模斜度。(√) 11、要提高薄壁压铸件的强度和刚度,应该设置加强肋。(×) 12、肋厚度要均匀,方向应与料流方向一致。(√) 13、液压曲肘式合模机构在压铸模闭合时是利用“死点”进行锁紧的(√) 14、斜导柱抽芯机构中弹簧起限位作用。(√) 15、压铸生产过程中,压射的第一阶段是低速压射,第二、第三阶段是高速压射。(×) 16、常用的高熔点压铸合金有锌合金、铝合金和镁合金。(×) 17、选择浇注温度时,应尽可能选择较高的温度浇注。(×) 18、压铸完成后,开模时应尽可能使铸件留在定模中。(×) 19、排溢系统包括溢流槽和飞边槽。(×) 20、推出机构一般设置在定模中。(×) 21、巴顿提出的三阶段充填理论,勃兰特提出全壁厚理论。(√) 22、金属液充填端部为矩形的型腔时受到的阻力比端部为圆形的小。(×) 23、压铸生产中,胀模力应大于锁模力。(×) 24、排溢系统包括溢流槽和飞边槽。(×) 25、硅是大多数铝合金的主要元素。(√) 26、镶拼式结构分为整体镶块式和组合镶块式。(√) 27、压铸件的尺寸精度比模具的精度低三到四级左右。(√) 28、确定公差带时,不加工的配合尺寸,孔取负值,轴取正值。(×) 29、厚壁压铸件,其壁中心层的晶粒粗大,易产生缩孔、缩松等倾向。(√) 30、压铸件厚壁与薄壁连接处可以突扩或突缩。(×) 31、肋应该布置在铸件受力较小处,对称布置。(×) 32、斜导柱抽芯机构中弹簧起限位作用。(√) 33、选择浇注温度时,应尽可能选择较高的温度浇注。(×) 34、同一压铸件上嵌补的嵌件不得多于两个。(×) 35、压铸机合模后的模具总厚度应小于压铸机的最小合模距离。(×)
压铸模使用必须注意的几个要点 模具工作温度 润滑剂
压铸模使用必须注意的几个要点 一、压铸模的使用特点在压铸生产过程中,压铸模的零件成形条件极其恶劣,它们经受着机械的 磨蚀、化学的侵蚀和热疲劳的反复作用。 1) 金属液在高压、高速下进入模具型腔,对模具型腔的 表面产生激烈的摩擦和冲击,使模具表面产生侵蚀和磨损。 2) 金属液在浇注 一、压铸模的使用特点 在压铸生产过程中,压铸模的零件成形条件极其恶劣,它们经受着机械的磨蚀、化学的侵蚀和 热疲劳的反复作用。 1) 金属液在高压、高速下进入模具型腔,对模具型腔的表面产生激烈的摩擦和冲击,使模具表面产生侵蚀和磨损。 2) 金属液在浇注过程中难免有熔渣带入,熔渣对成形零件表面产生复杂的化学作用,铝和铁的 化合物像尖劈一样,加速了压铸模裂纹的形成和发展。 3) 热应力是模具成形零件表面产生裂纹的主要原因,在每一个压铸件生产过程中,成形件表面 除了受到金属液的高速、高压冲刷外,还存在着吸收金属在凝固过程中放出的热量,产生了热交换。此外由于模具材料热传导的关系,使成形件表面层温度急剧上升,与内部产生了很大的温差,从而产生了内应力。当金属液充填型腔时,型腔表层首先达到高温而膨胀,而内层模温较低,相 对的膨胀量小,使表层产生压应力。开模后,型腔表面与空气接触,受到压缩空气及涂料的激冷 而产生拉应力。这种交变应力随着生产的延续而增加,当超过模具材料的疲劳极限时,使模具表 面层产生塑性变形而产生裂纹。 为了保持型面的耐用,要求型面具有抗热疲劳性能、耐磨损、不粘模、易脱件。所以对成形零 件采用了目前应用较好的4Cr5MoSiV1(H13)材料制造。 二、合金熔液的温度 压铸模生产过程中为了能更好地填充到压铸模所有凹孔和深处,保证金属流动时彼此融和,在 使用压铸模时,应正确选择金属的浇注温度,合金压铸液体浇注温度如下: 材料名称压铸液体温度/℃ 锌合金 420-500 铝合金 620-690 镁合金 700-740 铜锌合金 850-960 压铸合金温度选用原则: 1) 浇入的金属温度越低,压铸模的寿命越长; 2) 用低温压铸,才有可能减少排气槽深度的增大,降低金属液溅出的危险;
压铸模具设计说明书
压铸模具设计说明书 专业:材料成型及控制技术班级: 学生姓名: 学号: 指导教师:
压铸模具设计说明书 一、设计内容 1、带浇铸系统的铸件图设计 2、模具型腔部分设计 二、压铸机的选择 铸件材料:铝合金冲头直径d=Ф40 铸件体积V1=3.14x120x28 -3.14x108x20=133387.2错误!未找到引用源。 压射力Fy=Py错误!未找到引用源。/4=错误!未找到引用源。=94200N 压射比p=错误!未找到引用源。=错误!未找到引用源。=75 L为压射室长度350 冲头直径d=Ф40 压射室合金溶液体积:V3=错误!未找到引用源。L/4=439600错误!未找到引用源。 充满度错误!未找到引用源。=错误!未找到引用源。=60.7% 铸件在分型面上的投影面积(浇注系统与溢流槽的面积取铸件的30%)A=A1(1+0.3)=18812错误!未找到引用源。 胀模力F=pA=75x18812=1410900N 合模力(锁模力)实际压铸时要率大于胀模力 三、浇铸系统的设计
铸件的平均壁厚b=7.6mm 填充时间t=0.2s (查铸造手册)填充速度v=30m/s(查铸造手册) 铝合金的密度取错误!未找到引用源。 浇注金属液的重量G=G1(铸件重量)+G2(浇注系统和溢流槽的重量) G1=ρV1=320.2g G2=10%G1=32g G=352.3g 1)内浇口的尺寸 内浇口的截面积Ag=K错误!未找到引用源。=4.0x错误!未找到引用源。=78.4错误!未找到引用源。 内浇口深度D=2mm 则宽度C=错误!未找到引用源。=39.5≈40mm(取整) 2)横浇道的尺寸 横浇道的截面积取Ar=3Ag(查铸造手册) 深度Dr=错误!未找到引用源。=9.7≈10mm(查铸造手册) 则宽度Cr=错误!未找到引用源。=24.3≈24mm(查铸造手册)横浇道长度L错误!未找到引用源。1xCr=40mm 取L=50mm(查铸造手册) 横浇道设计成扇形横浇道 3)直浇道的尺寸 冲头直径d=Ф50 浇口套尺寸如图(查铸造手册) 4)溢流槽的设计 参照铸造手册:全部的溢流槽的溢流口截面积的总和An应等于内浇口截面积Ag 的60%~70% 取An=0.7Ag=0.7x78.4≈55错误!未找到引用源。 设计3个弓形溢流槽每个溢流口的截面积为20错误!未找到引用源。
《压铸工艺及模具设计》复习题李晋
一、单选、填空和判断题:60% 1. 压铸的基本概念和常用的分类方法。答:压铸是将一种熔融状态或半熔融状态的金属浇入压铸机的压室,在高压力的作用下,以极高的速度充填在压铸模(压铸型)的型腔内,并在高压下使熔融或半熔融的金属冷却凝固成型而获得铸件的高效益、高效率的精密铸造方法。 2. 压铸的特点与应用范围。答:高压和高速是压铸时液态或半液态金属充填成型过程的两大特点。压铸已广泛应用在国民经济的各行各业中,如兵器、汽车与摩托车、航空航天产品的零部件及电器仪表、无线电通信、电视机、计算机、农业机具、医疗器械、洗衣机、电冰箱、钟表、照相机、建筑装饰以及日用五金等各种产品的零部件的生产方面。 3. 压铸的发展历史。答:1822年,威廉姆·乔奇制造了一台日产1.2万—2万铅字的铸造机,显示压铸工艺方法的生产潜力;1849年斯图吉斯设计并制造成第一台手动活塞式热室压铸机,并在美国获得专利;1855年默根瑟勒印字压铸机,开始生产低熔点的铅、锡合铸字,到19世纪60年代用锌合金压铸零件生产。1904年英国的法兰克林开始用压铸方法生产汽车的连杆轴承,开创压铸零件在汽车工业中的应用的先例1905年多勒成功研制了用于工业生产的压铸机,压铸锌、锡、铜合金铸件。随后瓦格纳设计了鹅颈式气压压铸机,用于生产铝合金铸件。1927年捷克工程师约瑟夫·波拉克设计了冷室压铸机,使压铸技术向前推进了一大步。20世纪50年代大型压铸机的发展开始,近10年压铸机开始向自动化智能化方向发展。 4. 压铸工艺中最重要的两个参数是什么?何谓压射力和压射压力?何谓压射速度和充填速度?答:压铸压力和压铸速度是压铸工艺中最重要的两个参数。压铸机压射缸内的工作液作用于压射头,使其推动金属液充填模具型腔的力称为压射力。压射压力是指压射过程中,压室内单位面积上金属液所受到的静压力。压射速度是指压铸机压射缸内的压力油推动压射冲头前进的线速度。充填速度是指金属液在压力作用下,通过内浇口进入型腔的线速度。 5. 何谓四级压射和三级压射?典型的金属充填理论有哪几种?其基本内容及发生的条件是什么?答; 四级压 射位于P4和P5.三级压射,是指现代压铸机压射机构为实现优质的填充效果所采用的慢压射、快压射、增压三个变压过程。典型的金属充填理论有喷射充填理论,全壁厚充填理论,三阶段充填理论;基本内容及发生的条件是P8和P9 6. 适合于压铸的合金取决于哪些因素?常用的压铸合金有哪些?其特点如何?答:压铸的合金取决于1> 密度小,导电和导热性好。2> 强度和硬度高,塑性好。3>性能稳定,耐磨和抗腐蚀性好。4>熔点低,不易吸气和氧化。5>收缩率小,产生热裂、冷裂和变形的倾向小。6>流动性好,结晶温度范围小,产生气孔、缩松的倾向小。常用的压铸合金有铝合金,锌合金,镁合金,铜合金。其特点见P14 7. 压铸时间的构成及其选择。压铸时间有充填、持压、及压铸件在压铸模中停留的时间。1充填时间的长短取决于铸件的的体积大小和复杂程度。对大而简单的铸件,充填时间要相对长些,对复杂和薄壁铸件充填时间要短些。2持压时间的长短取决于铸件的材质和壁厚。对熔点高、结晶温度范围大和厚壁的铸件,持压时间要长些,对结晶温度范围小而壁又薄的铸件,持压时间可短些。若持压时间不足,易造成缩松。但持压时间过长,起不到很大效果,且易造成立式压铸机的切除余料困难。3足够的开模时间可使铸件在模具内便有一定的强度,开模和顶出时不致产生变形或拉裂。若开模时间过短,则在铸件强度还较低时就脱模,铸件易变形,对强度低的合金还可能因为内部气孔的膨胀而产生表面气泡。但开模时间太长,则铸件温度过低,收缩大,对抽芯和顶出铸件的阻力变大,对热脆性大的合金还会引起铸件开裂,同时还会降低压铸的生产率。
电梯踏板的压铸模设计
本科生毕业设计 姓名:学号: 学院: 专业: 设计题目:电梯踏板的压铸模设计 专题: 指导教师:职称: 20** 年6月徐州
摘要 随着与国际接轨的脚步不断加快,市场竞争的日益加剧,人们已经越来越认识到产品质量、成本和新产品的开发能力的重要性。而模具制造是整个链条中最基础的要素之一,模具制造技术现已成为衡量一个国家制造业水平高低的重要标志,并在很大程度上决定企业的生存空间。 虽然中国模具工业在过去十多年中取得了令人瞩目的发展,但许多方面与工业发达国家相比仍有较大的差距。例如,CAD/CAE/CAM技术的普及率不高;许多先进的模具技术应用不够广泛等等,致使相当一部分大型、精密、复杂和长寿命模具依赖进口。 本说明书结合电梯踏板的模具设计系统地阐述了压铸与模锻技术的基本原理,分析了压铸与模锻工艺主要参数的确定方法,论述了压铸模与锻模主要零部件设计方法,并介绍了模具的加工制造及维修保养。 关键词:压铸模具加工制造维修保养
ABSTRACT With the nation of footstep join to the world continuously ,market competition is turning worse ,people is already known the important of quality ,cost ,and the ability of develop new product . but the manufacturing to the molding is one of the most basal factors in the whole chain ,the molding tool manufacturing technique has become to measure the important marking of a national manufacturing industry level now ,and decide the existence space of the business enterprise to a large extent . Although in the passed ten years of development ,the Chinese molding tool industry gain the harvest ,but compare to developed country we still have something to study .for example ,the universality rate of the technical of CAD/CAE/CAM is not high ;many of molding tool technique is not applied enough etc, caucus to import a larger number the complications and the longevity life molding tool . This manual systematically combined the molding tool to die-casting with the mold technical basic principle by introduce the design of the elevator pedal, analyze the method to make certain to the main parameter of die-casting and the mold craft, introduce the method to process and maintain . Keyword: Die-casting mould process maintain