射线照相底片评定
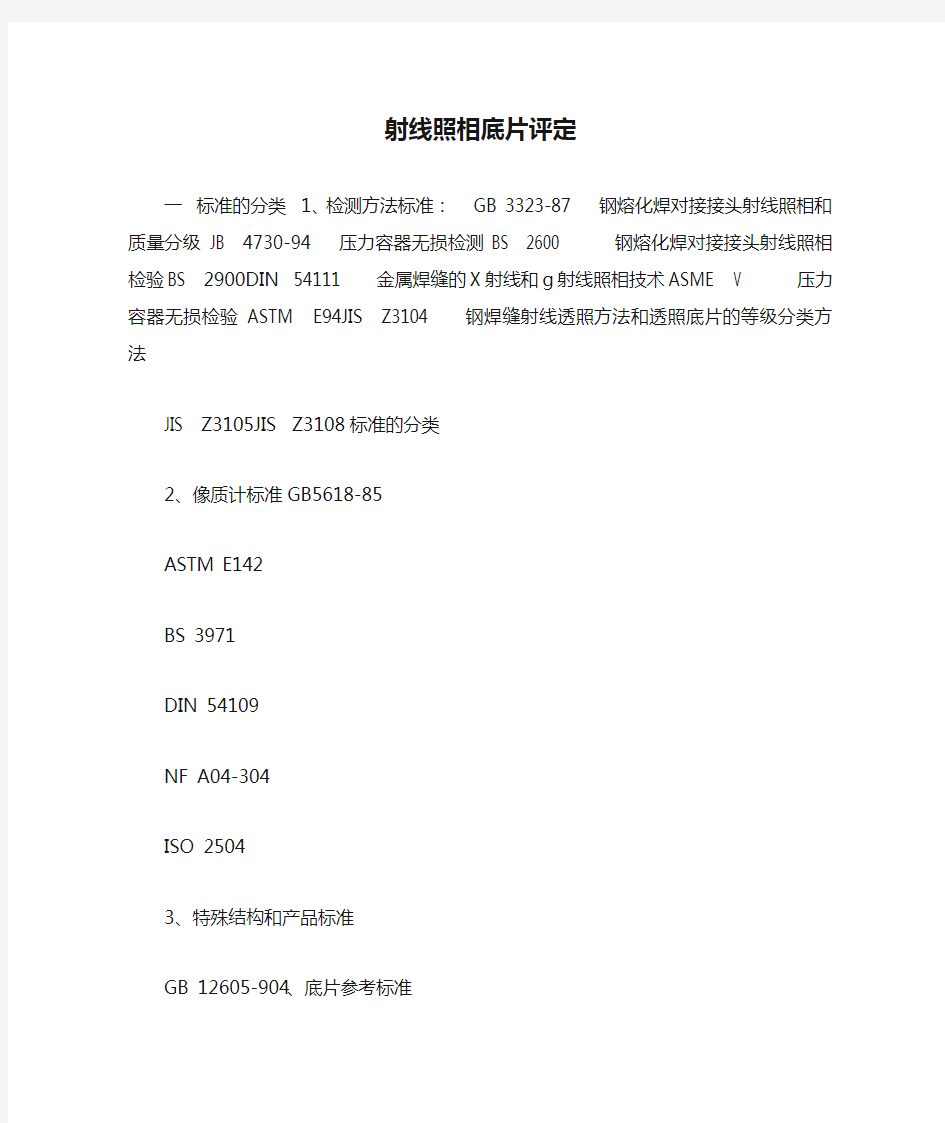

射线照相底片评定
一标准的分类1、检测方法标准:GB 3323-87 钢熔化焊对接接头射线照相和质量分级JB 4730-94 压力容器无损检测 BS 2600 钢熔化焊对接接头射线照相检验BS 2900DIN 54111 金属焊缝的X射线和g射线照相技术ASME V 压力容器无损检验ASTM E94JIS Z3104 钢焊缝射线透照方法和透照底片的等级分类方法JIS Z3105JIS Z3108标准的分类
2、像质计标准GB5618-85
ASTM E142
BS 3971
DIN 54109
NF A04-304
ISO 2504
3、特殊结构和产品标准
GB 12605-904、底片参考标准
IIW
ASTM E186,242
(中国无底片参考标准)二国内主要标准
1、GB3323--87 钢熔化焊对接接头射线照相和质量分级
与82标准相比将检测质量分为三级:A、AB、B。在标准的七处有体现:透照厚度;K 值;L2;L1;像质计;D;能量。
2、GB12605--90 钢管环缝熔化焊对接接头射线透照工艺和质量分级该标准的特点是
(1)分89、76mm二个台阶89≥ t ≥76用Ⅰ型专用像质计。t ≤76用Ⅱ型专用像质计。(2)对未焊透和内凹的分级更为详细:提出一套专用对比块。3、JB4730-94 压力容器无损检测(第二篇焊缝射线透照技术)保留了GB3323 和GB12605钢焊缝的相关部分,增加了铝、钛焊缝的透照工艺和质量分级。
国内主要标准
4、GB/T 5677-85 铸钢件射线照相及底片等级分类方法
适用于5-300mm厚的铸钢件;
铸造缺陷分五类:气孔、夹砂和夹渣、缩孔和缩松、内冷铁未熔合和泥芯撑未熔合。
评定方法:换算成点数
该标准目前正在修订
5、SD143-85 电力建设施工及验收技术规范
6、CB/T 3358-93 船舶钢焊缝射线照相工艺和质量分级
7、ZB J04 004-87 射线照相探伤方法(一般指导原则)
8、HB 5358.2-86 航空制件X射线照相检验质量控制标准
9、GB/T 5618-85 线型像质计
10、GB4792-84 放射卫生防护基本标准
三底片评定
1、焊缝评定方法:
(1)GB3323-87
16 焊缝质量分级
16.1 根据缺陷的性质和数量,焊缝质量分为四级。
16.1.1 Ⅰ级焊缝内应无有裂纹、未熔合、未焊透和条状夹渣。
16.1.2 Ⅱ级焊缝内应无有裂纹、未熔合、未焊透。
16.1.3 Ⅲ级焊缝内应无有裂纹、未熔合以及双面焊和加垫板的单面焊中的未焊透。不加垫扳的单面焊中的未焊透允许长度按表10条状长度的Ⅲ级评定。
16.1.4 焊缝缺陷超过Ⅲ级者为Ⅳ级。
16.2 圆形缺陷的分级
16.2.1 长宽比小于或等于3的缺陷定义为圆形缺陷。它们可以是圆形、椭圆形、锥形或带有尾巴(在测定尺寸时应包括尾部)等不规则的形状。包括气孔、夹渣和夹钨。
GB3323-87
16.2.2 圆形缺陷用评定区进行评定,评定区域的大小见表6。评定区应选缺陷最严重的部位。16.2.3 评定圆形缺陷时应将缺陷尺寸按表7换算成缺陷点数,见表7。
16.2.4 不计点数的缺陷尺寸见表8。
表6 缺陷评定
表7 缺陷点数换算表
返回例7GB3323-87
表8 不计点数的缺陷尺寸
16.2.5 当缺陷与评定区边界线相接时,应把它划分为该评定区内计算点数。返回例
16.2.6 当评定区附近缺陷较少,且认为只用该评定区大小划分级别不适当时,经供需双方协商,可将评定区沿焊缝方向扩大到3倍,求出缺陷总点数,用此值的1 / 3 进行评定。可扩大评定区的处理办法见附录D。
16.2.7 圆形缺陷的分级见表9。
GB3323-87
注:?表示评定区mm;
表示母材厚度mm;
表中的数字是允许缺陷点数的上限。
GB3323-87
16.2.8 圆形缺陷长径大于1 / 2 T时,评为Ⅳ级。
16.2.9 Ⅰ级焊缝和母材厚度等于或小于5mm的Ⅱ级焊缝内不计点数的圆形缺陷,在平定区内不得多于10个。
16.3 条形夹渣的分级
16.3.1 长宽比大于3的夹渣定义为条状夹渣。
16.3.2 条状夹渣的分级见表10。
16.4 综合评级
在圆形缺陷评定区内,同时存在圆形缺陷和条状夹渣或未焊透时应各自评级,将级别之和减1作为最终级别。
表10 条状夹渣的分级
质量等级单个条状夹渣长度条状夹渣总长
T £ 12:4 在任意直线上,相邻两夹渣间距均
Ⅱ12 T 3 60:20 长度在12T焊缝长度内不超过 T £ 9:6 在任意直线上,相邻两夹渣间距均 Ⅲ9 T 3 45:30 长度在6T焊缝长度内不超过T Ⅳ大于Ⅲ级者 注:(1)表中“L”为该组夹渣中最长者的长度。 (2)长宽比大于3的长气孔的评级与条状夹渣相同。 (3)当被检焊缝长度小于12T(Ⅱ级)或6T(Ⅲ级)时,可按比例折算。当折算的条状夹渣总长小于单个条状夹渣长度时,以单个条状夹渣长度为允许值。 JB4730-94 “6焊缝射线透照缺陷等级评定 6·1钢制压力容器对接沓缝透照缺陷等级评定 6·1·1本条适用于2~250mm板厚的碳素钢、低合金钢、不锈钢制 压力容器对接焊缝的X射线和射线透照和缺陷等级评定。 6·1·1·2透照底片质量等级、透照范围和焊缝的缺陷等级评定,应 按产品技术条件和GB150的规定选择,并应符合图样规定。 6·1·2底片质量应符合5·16条的规定。 6·1·3焊缝缺陷等级评定 6·1·3·1根据缺陷的性质和数量,将焊缝缺陷分为四个等级。 a·Ⅰ级焊缝内不允许裂纹、未熔合、未焊透和条状夹渣存在。 b·Ⅱ级焊缝内不允许裂纹、未熔合和未焊透存在。 c·Ⅲ级焊缝内不允许裂纹、未熔合以及双面焊或相当于双面焊的全焊透对接焊缝和加垫板单面焊中的未焊透存在。Ⅲ级焊缝中允 许存在的单面焊未焊透的长度,按表6-5级条状夹渣评定。 d·焊缝缺陷超过Ⅲ级者为Ⅳ级。 JB4730-94 6·1·3·2圆形缺陷的确定和分级 a·长度比小于或等于3的缺陷定义为圆形缺陷。它们可以是圆形、椭圆形、锥形或带有尾巴(在测定尺寸时应包括尾巴)等不规则的形状。包括气孔、夹渣和夹钨。 b·圆形缺陷用评定区进行评定,评定区域的大小见表6-1。评定区应选在缺陷最严重的部位。 c·评定圆形缺陷时,应将缺陷尺寸按表6-2换算成缺陷点数。如缺陷尺寸小于表6-3的,则该缺陷不需换算成点数参加缺陷评级。 d·当缺陷在评定区边界线上时,应反它划在该评定区内计算点数。 e·当评定区附近缺陷较少,且认为只用该评定区大小划分级别不适当时,经供需双方协商,可将评定区沿焊缝方向扩大三倍,求出缺陷总点数,用此值的1/3进行评定。可扩大评定区的处理办法见附录D(补充件)。 JB4730-94 表6-1 缺陷评定区 表6-2 缺陷点数换算表 表6-3 不计点数的缺陷尺寸 JB4730-94 f·圆形缺陷的分级见表6-4。 g·级焊缝和母材厚度等于或小于5mm的Ⅱ级焊缝内不计点数的圆形缺陷,在评定区风不得多于10个。 注:?表中的数字是允许缺陷点数的上限。 母材板厚不同时,取薄的厚度值。 返回例7 JB4730-94 6·1·3·3条状夹渣的确定和分级 a·长度比大于3的夹渣定义为条状夹渣。b·条状夹渣的分级见表6-5。 6·1·3·4综合评级 在圆形缺陷评定区内,同时存在圆形缺陷和条形夹渣或未焊透时,应各自评级,将级别之和减1作为最终级别。 表6-5 条状夹渣的分级GB3323 返回例2 质量等级单个条状夹渣长度条状夹渣总长 1/3T,最小可为4,在任意直线上,相邻两夹渣间距均 Ⅱ最大不超过20 不超过6L的任何一组夹渣,其累计 长度在12T焊缝长度内不超过T 2/3T,最小可为6,在任意直线上,相邻两夹渣间距均 Ⅲ最大不超过20 不超过3L的任何一组夹渣,其累计 长度在6T焊缝长度内不超过T Ⅳ大于Ⅲ级者 注:(1)表中“L”为该组夹渣中最长者的长度,“T”为母材厚度。 (2)长宽比大于3的长气孔的评级与条状夹渣相同。 (3)当被检焊缝长度不足12T(Ⅱ级)或6T(Ⅲ级)时,可按 比例折算。当折算的条状夹渣总长小于单个条状夹渣长 度时,以单个条状夹渣长度为允许值。 (4)当两个或两个以上条状夹渣在一条直线上且相邻间距小于或等于较小夹渣尺寸时,应作为单个连续夹渣处理,其间距也应计入夹渣长度,否则应分别评定。 (5)母材板厚不同时,取薄的厚度值。” 四底片评定实例(GB 3323-87) 例1 如图,评定圆形缺陷的级别,工件厚度T=25mm。 解:①T=25mm. 评定框为10×10 ②φ3:3点;φ2:2点;φ1:1点。共6点。 ③根据表6-4,应为Ⅱ级 底片评定实例 例2 如图,评定条形缺陷的级别,工件厚度T=8 mm。 4 4 2 3 40 解:①单条:T≤ 12 容许4,三个条渣均符合Ⅱ级; ②总长:∵4 - 4 间距3<6L(L=4) 又∵4 - 2 间距40>6L ∴4+4=8 符合12T内不超过T,为Ⅱ级。 底片评定实例 例3 如图,评定圆形、条形缺陷的级别,工件厚度T=25 mm。 ①圆形:2 + 2 = 4点;T=25mm, Ⅱ级。 ②条形:T /3 =8.3mm, L=10>8.3mm,不符合Ⅱ级; ∵2T /3 =16.6mm, L=10<16.6mm,20 <3L(30) ∴总长10+5=15,15 <25,符合Ⅲ级; ③综合评级:Ⅱ+Ⅲ-1=Ⅳ级 底片评定实例 例4:底片6272 T=25mm; 有φ1和φ3气孔二个,按GB3323-87定级。 解:T=25mm,评定区为10×10,φ1和φ3在同一评定区内。 根据换算表:φ1和φ3分别为:1点和3点,总共4点 根据定级表:4点为Ⅱ级。 底片评定实例 例5:底片B2-4 T=10mm,有长为9mm的夹渣一条,按GB3323-87定级。解:T=10mm,根据条形缺陷定级表 Ⅱ级容许4mm,9>4,所以降为Ⅲ级。 Ⅲ级容许(2/3)T=6.6mm,9>6.6,所以为Ⅳ级。 底片评定实例 例6:底片6-1 T=25mm; 有φ0.6mm和φ2mm气孔二个,有长为14mm、6mm的夹渣二条按GB3323-87定级。 底片评定实例 解:据图,夹渣和气孔在同一个评定区内,作综合评定。 先评气孔:φ0.6mm ----1点;φ2mm----2点。 共3点,应为Ⅰ级; 再评夹渣:14+6=20 (2/3)T=16.6mm ;20 >16.6mm,应为Ⅳ级。 综合评定:Ⅰ+ Ⅳ- 1= Ⅳ级 底片评定实例 例7、母材厚度T = 25mm的焊缝底片上发现如图缺陷,按GB3323标准评级。 解:气孔与评定区边界相接应把它划分为该评定区内计算点数。 底片上有φ2、φ2、φ1、φ1四个圆形缺陷。点数为:2、2、1、1。总点数为:6点。评为:Ⅱ级。分级表 底片评定实例 例8、长度为96mm、母材厚度T = 8mm的焊缝底片上发现三条夹渣,其长度和间距如图所示,分别按GB3323和JB4730标准评级。 解:按GB3323评级:先按Ⅱ级试评: 先看:单条(T≤12,容许4):4、4、2 符合Ⅱ级→看总长 再看:总长(累计间距:6 × 4 =24):3<24,40>24 总长=4+4=8 ≯8(T)符合Ⅱ级 ∴按GB3323评级:应为Ⅱ级。 底片评定实例 按JB4730评级: 先按Ⅱ级试评: 先看:单条(T/3=2.6,容许4):4、4、2 符合Ⅱ级→看总长 再看:总长(累计间距:3 × 4 =12):3<12,40>12 总长=4+3+4=11>8(T)不符合Ⅱ级 按Ⅲ级试评: 单条(2T/3=5.2,容许6):4、4、2 符合Ⅱ级→看总长 总长(累计间距: 3 × 4 =12):3<12,40>12 总长=4+3+4=11>8(T)不符合Ⅲ级 ∴按JB4730评级:应为Ⅳ级。 底片评定实例 (2)条形缺陷评级GB3323 先按Ⅱ级试评: 先看:单条(∵T>12,∴容许T/3=8.3):10>8.3。不符合Ⅱ 级→转向Ⅲ级试评 按Ⅲ级试评: 先看:单条(9 <T <45 ,容许2T/3=16.6):10 <16.6。符合 Ⅲ级。 再看:总长(间距20 <3L),总长=10+5=15<25(T)符合Ⅲ级。 (3)综合评定:Ⅱ+ Ⅲ-1=Ⅳ级 ∴按GBGB3323评级:应为Ⅳ级。 按JB4730评定,∵间距20 >10和5,∴总长中不加间距,其结果与GB3323一样。 第七章射线检测工艺规程 一射线检测工艺规程基本概念及编制程序 1、概念:根据现行标准和相关要求制定的正确完成无损检测工作的程序文件称为工艺规程(Procedure)。本单位检测人员必须按照工艺规程实施检测工作。 2、工艺规程文件通常可分为三种类型: (1)通用工艺规程:在某种检测方法或某类产品范围内通用的程序文件称为通用工艺规程。 (2)专用工艺规程(Instruction):根据通用工艺规程制定的适用于某一具体检测对象的技术文件称为专用工艺规程。 (3)技术指导书:为使用方便常以表格形式编制,因此也可称为工艺卡。 3、工艺规程编制程序: (1)资料准备a.与被检工件有关的技术文件或图纸; b.检测依据的标准、规程;工艺规程编制程序 c.设备、器材有效的技术资料(曝光曲线、胶片特性曲线) (2)确定工艺参数 (3)实验验证 (4)填写工艺卡 (5)审核批准 (6)实施、意见反馈和修订 二射线检测工艺规程主要内容 1、主题内容与适用范围 (应明确适用于何种材料、规格、结构、检测方法等) 2、引用标准 (凡引用的标准或规程都应在有效期内,标出其代号) 3 、检测人员资格 (参照相关标准中的规定,应列出条款内容) 射线检测工艺规程内容 4 、设备、器材和材料 (参照相关标准中对设备、器材和材料的规定,应列出条款内容。通常应包括:射线源、象质计、胶片、增感屏、标记、暗室要求等方面。) 5、检测技术 (1)透照方法 (确定采用单壁单影、双壁单影、双壁双影等方法。对所确定的方法应明确射线源-工件-胶片的相对位置;各种标记的摆放;一次透照长度和透照次数;散射线屏蔽等。)(2)曝光参数 (通过理论计算或查询实验曲线,确定焦距、管电压、管电 流、曝光时间等。) 6 、暗室处理 (确定胶片切装、保管要求,胶片冲洗规程,室内照明规定。) 射线检测工艺规程内容 7、防护 (防护措施) 8、表面要求 (去除表面可能形成伪缺陷的毛刺、焊渣等) 9、底片质量 (提出底片质量的具体要求:黑度、象质指数、伪缺陷、底片清洁度等。) 10、验收标准及焊缝质量分级 (引用相关标准) 11、记录、报告和资料保存 (将上述内容简要填入工艺卡内) 三射线检测工艺规程实例 下面文件是无损检测培训中心编写的《焊缝射线检测工艺规程》实例,包括三个部分: 1、射线检测通用工艺规程 2、某部件对接焊缝专用工艺规程 3、工艺卡 四工艺卡实例 如图冷凝器内套筒一件,1、2、3为环缝。4、5为纵缝。制订环缝和纵缝的射线检测工艺规程,并将有关参数填入工艺卡内。 已知:内套筒壁厚T=25mm,余高2mm,双面焊,外径φ=960mm。 解: (1)确定检测方法: 环缝:如图所示,环缝1、2、3的最佳检测方法为:源内中心法。 纵缝:如图所示,纵缝4、5的最佳检测方法为:环缝外透法。 (2)确定环缝透照工艺 管电压:根据曝光曲线:T=25mm,余高2mm。TA=29mm ∵300kV不容许(达到最大管电压); 240、260、280kV也不容许(曝光量必须>15mA·min)∴选择220kV 曝光量:根据曝光曲线确定,曝光量30 mA·min,焦距600mm,黑度1.5。由于实际焦距为960/2=480mm,所以需要修正曝光量,在同一黑度下: E1 E2 f1=600 E1=30mA·min f12 f22 f2=480mm E2=? ∴E2=20mA·min ,则选取:电流5mA 时间4min。 透照次数:1次 (3)确定纵缝透照工艺: 管电压: 根据曝光曲线:T=25mm,余高2mm。确定管电压220kV。 曝光量:根据曝光曲线确定:曝光量30 mA·min,焦距600mm,黑度1.5。选择实际焦距为600mm,不需要修正曝光量。 ∴E=30mA·min ,则选取:电流5mA 时间6min。 透照次数:纵缝不需计算透照次数,只需确定L3 按GB3323标准:L3≤0.5L1 即可。 (4)确定像质计及像质指数:TA=29mm查得像质指数=9 像质计为Ⅱ号 射线照相底片的评定 《射线检测》补充教材 编写:王学冠 中国锅炉压力容器检验协会教育工作委员会 二○○四年六月 网络借鉴 第六章射线照相底片的评定 6.1评定的基本要求 -底片质量要求 -评定环境、设备的要求 -评定人员条件要求. 6.1.1底片质量要求 ⑴灵敏度:从定量方面而言,是指在射线底片可以观察到的最小缺陷尺寸或最小细节尺寸;从定性方面而言,是指发现和识别细小影像的难易程度。在射线底片上所能发现的沿射线穿透方向上的最小尺寸,称为绝对灵敏度,此最小缺陷尺寸与透照厚度的百分比称为相对灵敏度。用人工孔槽,金属丝尺寸(像质计)作为底片影像质量的监测工具而得到的灵敏度又称为像质计灵敏度。 要求:底片上可识别的像质计影像、型号、规格、摆放位置,可观察的像质指数(Z)是否达到标准规定要求等,满足标准规定为合格。 ⑵黑度:为保证底片具有足够的对比度,黑度不能太小,但因受到观片灯亮度的限制,底片黑度不 能过大。根据JB4730标准规定,国内观片灯亮度必须满足观察底片黑度Dmin≥2.0。底片黑度测定要求:按标准规定,其下限黑度是指底片两端焊缝余高中心位置的黑度,其上限黑度是指底片中部焊缝两侧热影响区(母材)位置的黑度。只有当有效评定区内各点的黑度均在规定的范围内方为合格。底片评定范围内的黑度应符合下列规定:A级:≥1.5;AB级:≥2.0;B级:≥2.3;经合同各方同意,AB级最低黑度可降低至1.7,B级最低黑度可降低至2.0。透照小径管或其它截面厚度变化大的工件时,AB级最低黑度允许降低至1.5。采用多胶片技术时,单片观察时单片的黑度应符合以上要求,多片迭加观察时单片黑度应不低于1.3。 ⑶标记:底片上标记的种类和数量应符合有关标准和工艺规定,标记影像应显示完整、位置正确。 常用标记分为识别标记:如工件编号、焊缝编号、及部位片号、透照日期;定位标记:如中心定位标记、搭接标记和标距带等;返修标记:如R1…N。上述标记应放置距焊趾不少于5mm。 ⑷伪缺陷:因透照操作或暗室操作不当,或由于胶片,增感屏质量不好,在底片上留下的缺陷影像, 如划痕、折痕、水迹、斑纹、静电感光、指纹、霉点、药膜脱落、污染等。上述伪缺陷均会影响评片的正确性,造成漏判和误判,所以底片上有效评定区域内不许有伪缺陷影像。 ⑸散射:照相时,暗袋背面应贴附一个“B”铅字标记,评片时若发现在较黑背景上出现“B”字较 淡影像(浅白色),则说明背散射较严重,应采用防护措施重新拍照,若未见“B”字,或在较淡背景出现较黑的“B”字,则表示合格。 6.1.2评片环境、设备等要求: ⑴环境:要求评片室应独立、通风和卫生,室温不易过高(应备有空调),室内光线应柔和偏暗, 室内亮度应在30cd/m2为宜。室内噪音应控制在<40dB为佳。在评片前,从阳光下进入评片室应适应评片室内亮度至少为5~10min;从暗室进入评片室应适应评片室内亮度至少为30s。 ⑵设备 ①.观片灯:应有足够的光强度,确保透过黑度为≤2.5的底片后可见光度应为30cd/m2,即透照前照度 至少应≥3,000 cd/m2;透过黑度为>2.5的底片后可见光度应为10cd/m2,即透照前照度至少应≥网络借鉴 射线评片技巧目录 (一):气孔、夹渣、夹钨射线底片影像特点 (二):条形缺陷评片步骤与技巧、条形缺陷综合评级 (三):焊缝未熔合射线底片影像特点 (四):焊缝未焊透射线底片影像特点 (五):裂纹射线底片影像特点 (一):气孔、夹渣、夹钨射线底片影像特点 按照JB/T4730-2005《承压设备无损检测》第2部分射线检测篇介绍,焊接接头中的缺陷按性质区分为裂纹、未熔合、未焊透、条形缺陷和圆形缺陷五类。在《射线检测评片》栏目中将介绍该五类性质的缺陷成因、缺陷评片技巧、评级方法,分享在工作中遇见的射线检测案例。本文介绍圆形缺陷(气孔、密集气孔、夹渣、夹钨)评片技巧和缺陷定量评级。 一、圆形缺陷的评片 缺陷长宽之比小于等于3(L/N<=3),且非裂纹、未焊透和未熔合危害性缺陷。对接接头焊缝常见的圆形缺陷包括圆形气孔、非金属夹渣、夹钨等性质缺陷。 圆形缺陷示意图 1、气孔 (1)气孔成因 在《焊缝气孔形成机理及超声检测波形特性》文中详细介绍了焊缝气孔形成的原因。气孔分为单个气孔和密集性气孔。气孔降低了焊缝的金属致密性,降低焊接接头的强度、韧性等力学性能。 (2)气孔射线成像特点 气孔内部充满气体,射线穿过气孔几乎不会形成材质衰减。在射线底片上气孔呈暗色斑点,中心黑度较大。单个气孔边缘较浅平滑过渡,轮廓规则较清晰,密集气孔成团状。气孔大多是球形的,也可以有其它形状,气体的形状与焊接条件密切有关。 单个气孔缺陷 密集性气孔 2、非金属夹渣 (1)夹渣成因 焊缝夹渣形成原因主要有以下几点: ?在焊接每层焊道层间清渣不干净; ?焊接电流过小、焊接速度过快; ?焊接操作过程不当; ?母材坡口设计加工不当; ?液态金属冷却速度过快等; 第一条是焊缝产生夹渣的直接原因,第二到第五条原因是由于焊渣在液态金属中浮渣不及时而残留在焊缝中。焊缝中存在非金属夹渣,当焊缝承受应力过程中在夹渣周围会形成裂纹扩展,裂纹发展到一定程度焊缝开裂。夹渣严重降低了焊接件强度、韧性等力学性能。 (2)夹渣射线成像特点 焊缝金属包裹着非金属夹杂物形成夹渣、射线穿过夹渣有一定的衰减,但远远小于焊缝金属对射线的衰减。射线底片上夹渣呈暗色斑点,黑度分布无规律,轮廓不圆滑不规则,小点状夹渣轮廓较不清晰。 非金属夹渣 《射线检测》补充教材页脚 第六章射线照相底片的评定 6.1评定的基本要求 -底片质量要求 -评定环境、设备的要求 -评定人员条件要求. 6.1.1底片质量要求 ⑴灵敏度:从定量方面而言,是指在射线底片可以观察到的最小缺陷 尺寸或最小细节尺寸;从定性方面而言,是指发现和识别细小影像的难易程度。在射线底片上所能发现的沿射线穿透方向上的最小尺寸,称为绝对灵敏度,此最小缺陷尺寸与透照厚度的百分比称为相对灵敏度。用人工孔槽,金属丝尺寸(像质计)作为底片影像质量的监测工具而得到的灵敏度又称为像质计灵敏度。 要求:底片上可识别的像质计影像、型号、规格、摆放位置,可观察的像质指数(Z)是否达到标准规定要求等,满足标准规定为合格。 ⑵黑度:为保证底片具有足够的对比度,黑度不能太小,但因受到观 片灯亮度的限制,底片黑度不能过大。根据JB4730标准规定,国观片灯亮度必须满足观察底片黑度Dmin≥2.0。底片黑度测定要求:按标准规定,其下限黑度是指底片两端焊缝余高中心位置的黑度,其上限黑度是指底片中部焊缝两侧热影响区(母材)位置的黑度。只有当有效评定区各点的黑度均在规定的围方为合格。底片评定围的黑度应符合下列规定:A级:≥1.5;AB级:≥2.0;B级:≥2.3;经合同各方同意,AB级最低黑度可降低至1.7,B级最低黑度可降低至2.0。透照小径管或其它截面厚度变化大的工件时,AB级最低黑度允许降低至1.5。 采用多胶片技术时,单片观察时单片的黑度应符合以上要求,多片迭加观察时单片黑度应不低于1.3。 ⑶标记:底片上标记的种类和数量应符合有关标准和工艺规定,标记 影像应显示完整、位置正确。常用标记分为识别标记:如工件编号、焊缝编号、及部位片号、透照日期;定位标记:如中心定位标记、搭接标记和标距带等;返修标记:如R1…N。上述标记应放置距焊趾不少于5mm。 ⑷伪缺陷:因透照操作或暗室操作不当,或由于胶片,增感屏质量不 好,在底片上留下的缺陷影像,如划痕、折痕、水迹、斑纹、静电感光、指纹、霉点、药膜脱落、污染等。上述伪缺陷均会影响评片的正确性,造成漏判和误判,所以底片上有效评定区域不许有伪缺陷影像。 页脚 射线底片评定操作培训 1评定的基本要求 -底片质量要求 -评定环境、设备的要求 -评定人员条件要求. 1.1底片质量要求 ?灵敏度:从定量方面而言,是指在射线底片可以观察到的最小缺陷尺寸或最小细节尺寸;从定性方面而言,是指发现和识别细小影像的难易程度。在射线底片上所能发现的沿射线穿透方向上的最小尺寸,称为绝对灵敏度,此最小缺陷尺寸与透照厚度的百分比称为相对灵敏度。用人工孔槽,金属丝尺寸(像质计)作为底片影像质量的监测工具而得到的灵敏度又称为像质计灵敏度。 要求:底片上可识别的像质计影像、型号、规格、摆放位置,可观察的像质指数(Z)是否达到标准规定要求等,满足标准规定为合格。 ?黑度:为保证底片具有足够的对比度,黑度不能太小,但因受到观片灯亮度的限制,底片黑度不能过大。根据JB/T4730标准规定,国内观片灯亮度必须满足观察底片黑度Dmin≥2.0。底片黑度测定要求:按标准规定,其下限黑度是指底片两端焊缝余高中心位置的黑度,其上限黑度是指底片中部焊缝两侧热影响区(母材)位置的黑度。只有当有效评定区内各点的黑度均在规定的范围内方为合格。底片评定范围内的黑度应符合下列规定:A级:≥1.5;AB级:≥2.0;B级:≥2.3;经合同各方同意,AB级最低黑度可降低至1.7,B级最低黑度可降低至2.0。透照小径管或其它截面厚度变化大的工件时,AB级最低黑度允许降低至1.5。 采用多胶片技术时,单片观察时单片的黑度应符合以上要求,多片迭加观察时单片黑度应不低于1.3。 ?标记:底片上标记的种类和数量应符合有关标准和工艺规定,标记影像应显示完整、位置正确。常用标记分为识别标记:如工件编号、焊缝编号、及部位片号、透照日期; 定位标记:如中心定位标记、搭接标记和标距带等;返修标记:如R1…N。上述标记应放置距焊趾不少于5mm。 ?伪缺陷:因透照操作或暗室操作不当,或由于胶片,增感屏质量不好,在底片上留下的缺陷影像,如划痕、折痕、水迹、斑纹、静电感光、指纹、霉点、药膜脱落、污染等。上述伪缺陷均会影响评片的正确性,造成漏判和误判,所以底片上有效评定区域内不许有伪缺陷影像。 ?散射:照相时,暗袋背面应贴附一个“B”铅字标记,评片时若发现在较黑背景上出现“B”字较淡影像(浅白色),则说明背散射较严重,应采用防护措施重新拍照,若未见“B”字,或在较淡背景出现较黑的“B”字,则表示合格。 1.2评片环境、设备等要求: ?环境:要求评片室应独立、通风和卫生,室温不易过高(应备有空调),室内光线应柔和偏暗,室内亮度应在30cd/m2为宜。室内噪音应控制在<40dB为佳。在评片前,从 焊接接头射线检测底片评定记录 NO.05-06 报告编号:12212BGRT01 共11页第1页 产品名称2#粗甲醇水冷器产品编号12212 检测标准JB/T4730.2-2005 序号焊接 接头 编号 底 片 编 号 底片 黑度 透照 厚度 mm 象 质 计 灵 敏 度 缺陷性质、数 量及位置 评 定 级 别 评 定 结 果 一次 透照 长度 mm 备 注 1 A1 1- 2 2.3-3.0 70 7 / I 合格280 2 2- 3 2.4-3.0 70 7 / I 合格280 3 3- 4 2.6-3.1 70 7 / I 合格280 4 4- 5 3.0-3.2 70 7 / I 合格280 5 5- 6 3.0-3.3 70 7 / I 合格280 6 6- 7 2.9-3.1 70 7 / I 合格280 7 7-8 2.8-3.2 70 7 / I 合格280 8 8-9 2.8-2.9 70 7 / I 合格280 9 9-10 3.1-3.3 70 7 / I 合格280 10 10-11 2.9-3.4 70 7 / I 合格280T 11 11-12 2.9-3.3 70 7 / I 合格280 12 12-13 2.8-3.0 70 7 / I 合格280 13 13-14 2.8-3.0 70 7 / I 合格280 14 14-15 2.7-3.0 70 7 / I 合格280 15 15-16 2.8-3.1 70 7 / I 合格280 16 16-17 2.7-3.0 70 7 / I 合格280 17 17-18 2.5-2.8 70 7 / I 合格280 18 18-19 2.8-3.0 70 7 / I 合格280T 19 19-20 2.8-3.0 70 7 / I 合格280 20 20-21 2.8-3.0 70 7 / I 合格280 初评人(资格): 2013年6月16日复评人(资格): 2013年6月16日 第六章射线照相底片的评定 大连开发区质量技术监督稽查队陈伟 6.1 评片工作的基本要求通过射线照相,使缺陷在底片留下足以识别的影像。评片时,要考虑三要素: 第一要考虑的是底片质量必须符合标准要求; 第二应考虑与观片有关的设备和环境条件; 第三为评片人员对观察到的影像应能作出正确的分析与判断,这些都取决于评片人员的知识、经验、技术水平以及责任心。 6.1.1 底片质量要求 大家都知道,不同的检测标准对底片质量的要求有所不同,本部分按特种设备使用的《承压设备无损检测》JB∕T 4730·2—2005射线检测来评述底片质量。 1. 底片灵敏度 底片灵敏度又称像质计灵敏度,它是底片质量的最重要的指标,也是影像射线照相质量诸多因素的综合结果。底片灵敏度通常是用丝型像质计测定的,评片底片灵敏度的指标是像质计上应识别丝号,它等于底片上能识别的最细金属丝的编号。显然,给定透照厚度的底片上显示的金属丝直径越小,识别丝号越大,底片灵敏度就越高。对底片的灵敏度检 查内容包括:底片上是否有像质计影像,像质计型号、像质计规格、摆放位臵是否正确,能够观察到的金属丝识别丝号是否到达到相应技术等级规定等要求。 *有关像质计灵敏度的识别,请见JB∕T 4730·2—2005标准中的有关章节和附录A中的表A.1、表A.2和表A.3的要求和规定。 但应注意以下三点: ⑴、标准是用透照厚度W来确定应识别丝号的,即单壁透照W=T,双壁透照W=2T。 ⑵、既不是焊缝或热影响区上的丝号,也不是加垫板单面焊焊缝相邻的母材和垫板上金属区的丝号,而应识别的是焊缝相邻的母材金属区的丝号,且能够清晰地看到长度不少于10mm的连续金属丝,专用像质计至少应能识别两根金属丝。 ⑶、单壁透照,像质计若放于胶片侧时,应做对比试验,使灵敏度满足标准要求,并在像质计适当位臵加F标记。 ⑷、像质计的摆放应符合要求。 2、底片的黑度 底片的黑度是射线照相底片质量的又一重要指标,为保证底片具有足够的对比度,黑度不能太小。受观片灯亮度的限制,底片黑度又不能过大。标准规定,不同检测技术等级的底片评定范围内黑度D应符合下列规定: 射线评片技巧焊缝未熔合射线底片影像特点修 订版 IBMT standardization office【IBMT5AB-IBMT08-IBMT2C-ZZT18】 射线评片技巧(三):焊缝未熔合射线底片影像特点2015-04-19?分类:解决方案?阅读(1933)?评论(0)? 根据GB6417-1986《金属熔化焊焊缝缺陷分类及说明》定义未熔合,在焊接过程中由于焊缝金属与母材金属未完全熔化结合,或者焊道金属与焊道金属之间未完全熔化结合产生的缺陷称为未熔合。本文讲述未熔合缺陷的分类、焊缝未熔合危害、焊缝未熔合的产生原因、焊缝未熔合在射线底片影像上的特征缺陷,以及讲解工作中射线检测的焊缝未熔合缺陷底片。 一、未熔合分类 焊缝未熔合可分为层间未熔合、坡口未熔合(侧壁未熔合)、根部未熔合,如下图所示为三类焊缝未熔合的示意图。未熔合常出现在焊缝根部形成根部未熔合、在焊道间层形成层间未熔合、在焊道和母材坡口之间形成坡口未熔合,以及在焊缝和母材溢流或焊瘤之间等位置。 坡口未融合示意图 层间未融合示意图 根部未融合示意图 二、未熔合危害 未熔合是一种面积型缺陷,坡口侧未熔合和根部未熔合明显减小了承载截面积,应力集中比较严重,其危害性仅次于裂纹。 三、未熔合的产生原因 (1)焊道清理不干净,存在油污或铁锈; (2)坡口设计加工不合理,液态金属流动有死角; (3)焊接电流过小,焊丝未完全熔化; (4)焊枪没有充分摆动,焊接位置存在死角; (5)焊工为了加快焊接速度,擅自提高电流等。 四、未熔合射线底片影像特征 (1)根部未熔合:典型影像是连续或断续的黑线,靠近母材侧影像轮廓整齐呈直线状且黑度较大,为坡口或钝边的机械加工痕迹。靠近焊缝中心测未熔合影像的轮廓可能较规则,也可能不规则,呈曲齿状的块状缺陷。 根部未熔合在底片上的位置就是焊缝根部的投影位置,若射线垂直焊缝透照,则缺陷一般在焊缝影像的中间。若斜角度透照或者母材坡口形状不对称(开单边坡口)可能偏向一边。 (2)坡口未熔合:典型影像是连续或断续的黑线,宽度不一,黑度不均匀,一侧轮廓较齐,黑度较大,另一侧轮廓不规则,黑度较小,在底片上的位置一般在中心至边缘的1/2处,沿焊缝纵向延伸。 坡口未熔合示意图和底片影像 第六章射线照相底片的评定 6.1 评片工作的基本要求 缺陷是否能够通过射线照相而被检出,取决于若干环节。首先,必须使缺陷在底片上留下足以识别的影象,这涉及到照相质量方面的问题。其次,底片上的影象应在适当条件下得以充分显示,以利于评片人员观察和识别,这与观片设备和环境条件有关。第三,评片人员对观察到的影象应能作出正确的分析与判断,这取决于评片人员的知识、经验、技术水平和责任心, 按以上所述,对评片工作的基本要求可归纳为三个方面,即底片质量要求,设备环境条件要求和人员条件要求。 6.1.1 底片质量要求 通常对底片的质量检查包括以下项目 1.灵敏度检查 灵敏度是射线照相质量诸多影响因素的综合结果。底片灵敏度用象质计测定,即根据底片上象质计的影象的可识别程度来定量评价灵敏度高低。目前国内广泛使用的是丝型象质计,评价底片灵敏度的指标是象质指数Z,它等于底片上能识别出的最细金属丝的编号。显然,透照给定厚度的工件时,底片上显示的金属丝直径越小,其象质指数z越大,底片的灵敏度也就越高。 灵敏度是射线照相底片质量的最重要指标之一,必须符合有关标准的要求。我国国家标准GB3323—87根据不同透照厚度和不同照相质量等级,规定了必须达到的象质指数Z(表6.1)。 对底片的灵敏度检查内容包括:底片上是否有象质计影象,象质计型号、规格、摆放位置是否正确,能够观察到的金属丝象质指数是多少,是否达到了标准规定的要求等。 2.黑度检查 黑度是射线照相底片质量的又一重要指标,各个射线探伤标准对底片的黑度范围都有规定。GB3323—87标准规定的底片黑度范围如表6.2。 由胶片特性曲线可知,胶片梯度随黑度的增加而增大,为保证底片具有足够的对比度,黑度不能太小,所以标准规定了黑度的下限值,另一方面,受观片灯亮度的限制,底片黑度又不能过大,黑度过大将造成透过光强不足,导致人眼观察识别能力下降,所以标准又规定了底片黑度的上限值。 底片黑度用光学密度计测定。测定时应注意,最大黑度一般在底片中部焊接接头热影响区位置,最小黑度一般在底片两端焊缝余高中心位置,只有当有效评定区内各点的黑度均在规定的范围内,才能认为该底片黑度符合要求。 《射线检测》补充教材 编写:王学冠 第六章射线照相底片的评定 6.1评定的基本要求 -底片质量要求 -评定环境、设备的要求 -评定人员条件要求. 6.1.1底片质量要求 ?灵敏度:从定量方面而言,是指在射线底片可以观察到的最小缺陷尺寸或最小细节尺寸;从定性方面而言,是指发现和识别细小影像的难易程度。在射线底片上所能发现的沿射线穿透方向上的最小尺寸,称为绝对灵敏度,此最小缺陷尺寸与透照厚度的百分比称为相对灵敏度。用人工孔槽,金属丝尺寸(像质计)作为底片影像质量的监测工具而得到的灵敏度又称为像质计灵敏度。 要求:底片上可识别的像质计影像、型号、规格、摆放位置,可观察的像质指数(Z)是否达到标准规定要求等,满足标准规定为合格。 ?黑度:为保证底片具有足够的对比度,黑度不能太小,但因受到观片灯亮度的限制,底片黑度不能过大。根据JB4730标准规定,国内观片灯亮度必须满足观察底片黑度Dmin≥2.0。底片黑度测定要求:按标准规定,其下限黑度是指底片两端焊缝余高中心位置的黑度,其上限黑度是指底片中部焊缝两侧热影响区(母材)位置的黑度。只有当有效评定区内各点的黑度均在规定的范围内方为合格。底片评定范围内的黑度应符合下列规定:A级:≥1.5;AB级:≥2.0;B级:≥2.3;经合同各方同意,AB级最低黑度可降低至1.7,B级最低黑度可降低至2.0。透照小径管或其它截面厚度变化大的工件时,AB级最低黑度允许降低至1.5。 采用多胶片技术时,单片观察时单片的黑度应符合以上要求,多片迭加观察时单片黑度应不低于1.3。 ?标记:底片上标记的种类和数量应符合有关标准和工艺规定,标记影像应显示完整、位置正确。常用标记分为识别标记:如工件编号、焊缝编号、及部位片号、透照日期;定位标记:如中心定位标记、搭接标记和标距带等;返修标记:如R1…N。上述标记应放置距焊趾不少于5mm。 ?伪缺陷:因透照操作或暗室操作不当,或由于胶片,增感屏质量不好,在底片上留下的缺陷影像,如划痕、折痕、水迹、斑纹、静电感光、指纹、霉点、药膜脱落、污染等。上述伪缺陷均会影响评片的正确性,造成漏判和误判,所以底片上有效评定区域内不许有伪缺陷影像。 1 射线无损检测底片评定制度 1.射线无损检测评片按JB4730-94《压力容器无损检测》标准,焊缝射线透照检测中相关要求执行。 2.射线无损检测底片评定、审核工作必须由射线Ⅱ级资格人员担任。3.评片人员必须了解被检工件的焊接种类、焊接方法、坡口型式以及材料种类等,以提供评片时参考。 4.评片应在专用评片室内进行。评片室内的光线应暗淡,但不全暗,室内照明用光不得在底片表面产生反射。 5.评片时,底片应在干燥后观察,观察应在光线暗淡的评片室内进行,观片灯应有观察片最大黑度为3.5的最大亮度。 6.评片的底片质量应符合下列要求: 6.1底片上必须显示出与透明厚度相对应的要求达到的最小像质指数; 6.2底片有效评定区域内的黑度应满足1.2~3.5的要求。 6.3底片上象质计影象位置应正确,定位标记和识别标记齐全,且不掩盖被检焊缝影象。在焊缝影象上,能清晰地看到长度小于10mm的象质计金属丝影象; 6.4在底片评定区域内不应有以下妨碍底片评定的假缺陷;6.4.1灰雾 6.4.2处理时产生的条纹、水迹或化学污斑等缺陷; 6.4.3划痕、指纹、脏物、静电痕迹、黑点或撕裂等; 6.4.4由于增感屏不好造成的缺陷。 6.5对上述不符和底片质量要求的底片应拒绝评定,并要求重拍。6.6评片人员根据底片上全影象,按JB4730-94《压力容器无损检测》标准中,焊缝射线透照缺陷等级评定的规定进行评定,缺陷评定应坚持:定性(定缺陷特性);定量(定缺陷的大小尺寸和数量);定位(定缺陷所处位置);定级(按JB4730标准评定质量等级)的四定原则。 6.7焊缝无损检测底片评定合格,开出无损检测合格通知单,出具射线无损检测报告,不合格焊缝开出焊缝返修通知单,按相关规定要求返修后复拍再重新评定。 6.8报告及验收标记 6.8.1报告至少应包括以下内容: 6.8.1.1委托部门、被检工件名称、编号、被检工件材质、母材厚度; 6.8.1.2检测装置的名称、型号、透照方法及透照规范,透照部位及无损检测。 6.8.1.3检测结果、缺陷等级评定及检测标准名称;6.8.1.4返修情况; 6.8.1.5检验人员和责任人员签字及其技术资格、检测日期。6.8.2验收标记 6.8.2.1如果检测内容作为压力容器产品验收的项目,则检测合格的所有工件上都应作永久性或半永久性的标记,标记应醒目。产品上不适合打印标记时,应采取详细的检测示意图或其它有效方式标 主讲人:夏福勇 主讲人简介 夏福勇,教授级高级工程师。原杭州市特种设备检测研究院副总工程师,现任杭州市锅炉压力容器技术协会秘书长,全国特种设备无损检测人员资格考核委员会考评人员,中国无损检测学会教育培训和科普工作委员会委员。持具有特种设备行业RTIII、UTIII、MTIII、PTIII级资质以及锅炉、压力容器、压力管道检验师(原高级检验师)资质;完成省部级涉及无损检测、特种设备检验科研项目七项,参加起草国家总局安全技术规范四部,出版著作三部,获得实用新型专利四项,在国内外发表专业论文二十余篇。获得过国家质检总局科技兴检奖等。 主要内容 一、底片评定的基本要求 1.底片质量要求 2.评片环境、设备等要求: 3.评片人员要求 4.相关知识要求 一、底片评定的基本要求 评片工作一般包括下面的内容: 1)评定底片本身质量的合格性; 2)正确识别底片上的影像; 3)依据从已知的被检工件信息和底片上得到的影像信息,按照验收标准或技术条件对工件质量作出评定; 4)记录和资料。 1.底片质量要求 (1)灵敏度:从定量方面而言,是指在射线底片可以观察到的最小缺陷尺寸或最小细节尺寸;从定性方面而言,是指发现和识别细小影像的难易程度。在射线底片上所能发现的沿射线穿透方向上的最小尺寸,称为绝对灵敏度,此最小缺陷尺寸与透照厚度的百分比称为相对灵敏度。用人工孔槽,金属丝尺寸(像质计)作为底片影像质量的监测工具而得到的灵敏度又称为像质计灵敏度。 要求:底片上可识别的像质计影像、型号、规格、摆放位置,可观察的像质丝号是否达到标准规定要求等,满足标准规定为合格。 (2)黑度: 为保证底片具有足够的对比度,黑度不能太小,但因受到观片灯亮度的限制,底片黑度不能过大。 底片黑度测定要求:按标准规定,其下限黑度是指底片两端搭接标记处的焊缝余高中心位置的黑度,其上限黑度是指底片中部焊缝两侧热影响区(母材)位 射线照相底片的评定 1评定的基本要求 -底片质量要求 -评定环境、设备的要求 -评定人员条件要求. 1.1底片质量要求 ?灵敏度:从定量方面而言,是指在射线底片可以观察到的最小缺陷尺寸或最小细节尺寸;从定性方面而言,是指发现和识别细小影像的难易程度。在射线底片上所能发现的沿射线穿透方向上的最小尺寸,称为绝对灵敏度,此最小缺陷尺寸与透照厚度的百分比称为相对灵敏度。用人工孔槽,金属丝尺寸(像质计)作为底片影像质量的监测工具而得到的灵敏度又称为像质计灵敏度。 要求:底片上可识别的像质计影像、型号、规格、摆放位置,可观察的像质指数(Z)是否达到标准规定要求等,满足标准规定为合格。 ?黑度:为保证底片具有足够的对比度,黑度不能太小,但因受到观片灯亮度的限制,底片黑度不能过大。根据JB4730标准规定,国内观片灯亮度必须满足观察底片黑度Dmin≥2.0。底片黑度测定要求:按标准规定,其下限黑度是指底片两端焊缝余高中心位置的黑度,其上限黑度是指底片中部焊缝两侧热影响区(母材)位置的黑度。只有当有效评定区内各点的黑度均在规定的范围内方为合格。底片评定范围内的黑度应符合下列规定:A级:≥1.5;AB级:≥2.0;B级:≥2.3;经合同各方同意,AB级最低黑度可降低至1.7,B级最低黑度可降低至2.0。透照小径管或其它截面厚度变化大的工件时,AB级最低黑度允许降低至1.5。 采用多胶片技术时,单片观察时单片的黑度应符合以上要求,多片迭加观察时单片黑度应不低于1.3。 ?标记:底片上标记的种类和数量应符合有关标准和工艺规定,标记影像应显示完整、位置正确。常用标记分为识别标记:如工件编号、焊缝编号、及部位片号、透照日期;定位标记:如中心定位标记、搭接标记和标距带等;返修标记:如R1…N。上述标记应放置距焊趾不少于5mm。 ?伪缺陷:因透照操作或暗室操作不当,或由于胶片,增感屏质量不好,在底片上留下的缺陷影像,如划痕、折痕、水迹、斑纹、静电感光、指纹、霉点、药膜脱落、污染等。上述伪缺陷均会影响评片的正确性,造成漏判和误判,所以底片上有效评定区域内不许有伪缺陷影像。 ?散射:照相时,暗袋背面应贴附一个“B”铅字标记,评片时若发现在较黑背景上出现“B”字较淡影像(浅白色),则说明背散射较严重,应采用防护措施重新拍照,若未见“B”字,或在较淡背景出现较黑的“B” 字,则表示合格。 1.2评片环境、设备等要求: ?环境:要求评片室应独立、通风和卫生,室温不易过高(应备有空调),室内光线应柔和偏暗,室内亮度应在30cd/m2为宜。室内噪音应控制在<40dB为佳。在评片前,从阳光下进入评片室应适应评片室内亮度至少为5~10min;从暗室进入评片室应适应评片室内亮度至少为30s。 ?设备 射线照相工艺规程 本文源自:无损检测招聘网 https://www.360docs.net/doc/c215657412.html, 本规程适用于是我公司在制造压力容器和压力管道安装过程中必须遵循的射线探伤通用工艺. 本守则依据标准: GB150-1998钢制压力容器、 GB151-1999 钢制换热器 TSG R0004-2009固定式压力容器安全技术规程 TSG D0001-2009 压力管道安全技术检测规程-工业管道 GB50235-1997 工业金属管道工程施工及验收规范 GB50148-1993 工业金属管道工程质量检验 JB/T 4730-005 承压设备无损检测 第一章(适用于压力容器) 1、对射线照相各项技术要求,针对压力容器的结构特点,提供保证射线 探伤工作质量所需遵循的通用工艺方法,本工艺射线探伤法符合 JBT4730.2-2005标准所规定的AB级照相法. 2、射线照相人员应经国家质量监督检验检疫总局培训、考核所颁发的特 种设备检验检测人员证后,RTⅠ或RTⅠ级以上资格人员担任. 3、射线照相须在全过程中严格按照射线照相工艺卡的各项参数进行操 作.“射线照相工艺卡”应由RTⅡ及其以上资格人员逐项填写编制,并经 无损检测责任人批准后使用. 4、射线胶片的使用与暗室处理按“管理制度汇编”暗室工作及制度执行. 5、摄片时机对一般材料,应在焊后12小时进行,对有延迟裂纹倾向的材料 应在焊后24小时进行. 6、委托探伤的压力容器焊缝必须有委托单位履行的无损探伤申请委托 单,申请单上必须有焊缝外观检验合格的见证和焊接检验员的签名. 7、射线照相前应对焊缝外观进行复验,焊缝表面的不规则状态在底片上 的图象应不掩盖焊缝中的缺陷与之混淆,否则应做适当的修整. 8、射线照相过程中的电离辐射防护应符合GB16357-1996《工业X射线 探伤放射性防护标准》GB18871-2002《电离辐射及辐射源安全基本标准》的有关规定. 9、射线照相的工艺要素和基本步骤: (1)透照方法的确定 (2)探伤编号方法 (3)几何条件的确定 (4)定位标记、识别标记、象质计的选用及摆放; (5)贴片及屏蔽散射线的措施 (6)射线窗口对焦 (7)曝光量的选择及操作 (8)底片质量自检 射线探伤操作规程 本文源自:无损检测招聘网 https://www.360docs.net/doc/c215657412.html, 1 2目的 该项操作规程,对压力容器产品的射线探伤实施有效控制。 2适用范围 本规程适用于对压力容器进行无损检测射线探伤前应做的准备工作和射线探伤中全过程的管理。 3选择的前提 对给定工件进行射线探伤时,应根据有关规程和标准要求选择适当的探伤条件。应以国标GB3323-87为选择条件的依据,焊缝透照按底片影像质量由低而高的要求分A级、AB级和B级三种检验等级。压力容器焊缝的射线探伤,至少应满足AB级的要求。 不同的象质等级对底片的黑度、灵敏度与不清晰度有不同的规定。要满足规定等级的象质要求,从探伤器材、方法、条件及程度等各个方面都要预先进行全面地部署。 4照相规范的确定 在照相过程中,除了合理地选择透照方法外,还必须选择好透照规范,使小缺陷能够在底片上明显地辨别出来,从而达到高灵敏度。有关规范的选择: 1)射线源的选择,应选择小尺寸的射线源; 2)透照距离的选择。在透照中,焦距选择大多在600~700mm间; 3)胶片与增感屏的选择。通常照相时将原度为0.01~0.13mm的铅箔增感屏与非增感形胶片一起使用。 5几何参数的选择 几何参数是影响射线照相灵敏度的重要因素,因此必须综合考虑与合理选择。 1)焦点或射线源尺寸:焦点大小对缺陷影响在射线底片上的显示对比度和清晰度都有很大影响; 2)焦点尺寸和几何布置会引起的影像模糊及放大; 3)焦点尺寸与射线底片对比度; 4)照射场内的X射线强度分布; 5)透照距离L1的选择——对Uy值和满足K值的有效长度要综合考虑。 6曝光条件的选择及修正 为得到满足射线透照应该具备的条件与象质良好的底片,通常要选择能够得到适当黑度和灵敏度的曝光条件进行透照。主要有以下几个因素: 1)曝光因子; 2)曝光条件的选择; 3)曝光条件的修正; 4)底片黑度达到确定的范围。 6透度计 为了评定底片的灵敏度,需要采用透度计,透度计是用来检查透照技术和胶片处理质量的。我国GB3323-87《钢熔化焊时对接头射线照相和质量分级》标准规定使用粗细不同的几根金属丝等距离排列做成的线型象质计,用底片上必须显示的最小钢丝直径与相应的象质指数来表示照相的灵敏度。 7焊缝透照方法 在透照方法中必须确定的几何参数是:焦距F(包括射源至工件表面的距离L1和工件表面至胶片的距离L2)、一次透照长度L3、环焊缝100%、透照时的最少曝光次数N;同时需要考虑的因素是:几何不清晰度Uy、透照厚度比K、横裂检出角θ、纵裂检出角θˊ、有效评定长度Leff以及100%透照时相邻两片的搭接长度ΔL、几何参数和相关因素在不同的透照方法中均有不同的技术要求。 8显影液的配制方法 为了使显影过程能正常进行,显影液的配制方法与程序必须合适。配制显影液时最好用蒸馏水或煮沸过的温水和有关的药品组成。 9定影液的调配 酸性定影液中含有互相分解的成分,要靠其它药品的作用才能共存,所以对药品的配制程序、温度和搅拌都要特别注意。 10水洗和干燥 1)胶片经定影后,应在流动的清水中冲洗20~30分钟。冲洗的目的是将胶片表面和内层吸附的硫代硫酸钠杂质及银的洛合物清除掉。 2)干燥可采用简易的晾片架,放在墙壁高处进行自然干燥或在清洁通风的空间晾干。11安全保护 为了保障我国从事放射工作人员和广大居民的的健康和安全,根据国际放射防护委员会所规定的限值,国家制定颁布了我国现行防护标准《放射卫生防护基本标准》,在GB4792-84中规定职业放射工作人员,其全身内外照射的终身累积剂量当量不得超过250 一、探伤人员要评片,四项指标放在先*,底片标记齐又正,铅字压缝为废片。 二、评片开始第一件,先找四条熔合线,小口径管照椭圆,根部都在圈里面。 三、气孔形象最明显,中心浓黑边缘浅,夹渣属于非金属,杂乱无章有棱边。 四、咬边成线亦成点,似断似续常相见,这个缺陷最好定,位置就在熔合线。 五、未焊透是大缺陷,典型图象成直线,间隙太小钝边厚,投影部位靠中间。 六、内凹只在仰焊面,间隙太大是关键,内凹未透要分清,内凹透度成弧线。 七、未熔合它斜又扁,常规透照难发现,它的位置有规律,都在坡口与层间。 八、横裂纵裂都危险,横裂多数在表面,纵裂分布范围广,中间稍宽两端尖。 九、还有一种冷裂纹,热影响区常发现,冷裂具有延迟性,焊完两天再拍片。 十、有了裂纹很危险,斩草除根保安全,裂纹不论长和短,全部都是Ⅳ级片。十一、未熔合也很危险,黑度有深亦有浅,一旦判定就是它,亦是全部Ⅳ级片。十二、危害缺陷未焊透,Ⅱ级焊缝不能有,管线根据深和长,容器跟着条渣走* 十三、夹渣评定莫着忙,分清圆形和条状,长宽相比3为界,大于3倍是条状。十四、气孔危害并不大,标准对它很宽大,长径折点套厚度,中间厚度插入法。十五、多种缺陷大会合,分门别类先评级,2类相加减去Ⅰ,3类相加减Ⅱ级。十六、评片要想快又准,下拜焊工当先生,要问诀窍有哪些,焊接工艺和投影。注:*四项指标系底片的黑度、灵敏度、清晰度、灰雾度必须符合标准的要求。**指单面焊的管线焊缝和双面焊的容器焊缝内未焊透的判定标准。 ★射线照相底片的评定★ 射线照相底片的评定 6.1评定的基本要求 -底片质量要求 -评定环境、设备的要求 -评定人员条件要求. 6.1.1底片质量要求 ?灵敏度:从定量方面而言,是指在射线底片可以观察到的最小缺陷尺寸或最小细节尺寸;从定性方面而言,是指发现和识别细小影像的难易程度。在射线底片上所能发现的沿射线穿透方向上的最小尺寸,称为绝对灵敏度,此最小缺陷尺寸与透照厚度的百分比称为相对灵敏度。用人工孔槽,金属丝尺寸(像质计)作 射线照相底片评定 一标准的分类1、检测方法标准:GB 3323-87 钢熔化焊对接接头射线照相和质量分级JB 4730-94 压力容器无损检测 BS 2600 钢熔化焊对接接头射线照相检验BS 2900DIN 54111 金属焊缝的X射线和g射线照相技术ASME V 压力容器无损检验ASTM E94JIS Z3104 钢焊缝射线透照方法和透照底片的等级分类方法JIS Z3105JIS Z3108标准的分类 2、像质计标准GB5618-85 ASTM E142 BS 3971 DIN 54109 NF A04-304 ISO 2504 3、特殊结构和产品标准 GB 12605-904、底片参考标准 IIW ASTM E186,242 (中国无底片参考标准)二国内主要标准 1、GB3323--87 钢熔化焊对接接头射线照相和质量分级 与82标准相比将检测质量分为三级:A、AB、B。在标准的七处有体现:透照厚度;K 值;L2;L1;像质计;D;能量。 2、GB12605--90 钢管环缝熔化焊对接接头射线透照工艺和质量分级该标准的特点是 (1)分89、76mm二个台阶89≥ t ≥76用Ⅰ型专用像质计。t ≤76用Ⅱ型专用像质计。(2)对未焊透和内凹的分级更为详细:提出一套专用对比块。3、JB4730-94 压力容器无损检测(第二篇焊缝射线透照技术)保留了GB3323 和GB12605钢焊缝的相关部分,增加了铝、钛焊缝的透照工艺和质量分级。 国内主要标准 4、GB/T 5677-85 铸钢件射线照相及底片等级分类方法 适用于5-300mm厚的铸钢件; 铸造缺陷分五类:气孔、夹砂和夹渣、缩孔和缩松、内冷铁未熔合和泥芯撑未熔合。 评定方法:换算成点数 该标准目前正在修订 5、SD143-85 电力建设施工及验收技术规范 6、CB/T 3358-93 船舶钢焊缝射线照相工艺和质量分级 7、ZB J04 004-87 射线照相探伤方法(一般指导原则) 8、HB 5358.2-86 航空制件X射线照相检验质量控制标准 9、GB/T 5618-85 线型像质计 10、GB4792-84 放射卫生防护基本标准 三底片评定 1、焊缝评定方法: (1)GB3323-87 16 焊缝质量分级 射线评片技巧三:焊缝未熔合射线底片影像特 点 HEN system office room 【HEN16H-HENS2AHENS8Q8-HENH1688】 2015-04-19?分类:?阅读(1933)?评论(0)? 根据GB6417-1986《金属熔化焊焊缝缺陷分类及说明》定义未熔合,在焊接过程中由于焊缝金属与母材金属未完全熔化结合,或者焊道金属与焊道金属之间未完全熔化结合产生的缺陷称为未熔合。本文讲述未熔合缺陷的分类、焊缝未熔合危害、焊缝未熔合的产生原因、焊缝未熔合在射线底片影像上的特征缺陷,以及讲解工作中射线检测的焊缝未熔合缺陷底片。 一、未熔合分类 焊缝未熔合可分为层间未熔合、坡口未熔合(侧壁未熔合)、根部未熔合,如下图所示为三类焊缝未熔合的示意图。未熔合常出现在焊缝根部形成根部未熔合、在焊道间层形成层间未熔合、在焊道和母材坡口之间形成坡口未熔合,以及在焊缝和母材溢流或焊瘤之间等位置。 坡口未融合示意图 层间未融合示意图 根部未融合示意图 二、未熔合危害 未熔合是一种面积型缺陷,坡口侧未熔合和根部未熔合明显减小了承载截面积,应力集中比较严重,其危害性仅次于裂纹。 三、未熔合的产生原因 (1)焊道清理不干净,存在油污或铁锈; (2)坡口设计加工不合理,液态金属流动有死角; (3)焊接电流过小,焊丝未完全熔化; (4)焊枪没有充分摆动,焊接位置存在死角; (5)焊工为了加快焊接速度,擅自提高电流等。 四、未熔合射线底片影像特征 (1)根部未熔合:典型影像是连续或断续的黑线,靠近母材侧影像轮廓整齐呈直线状且黑度较大,为坡口或钝边的机械加工痕迹。靠近焊缝中心测未熔合影像的轮廓可能较规则,也可能不规则,呈曲齿状的块状缺陷。 根部未熔合在底片上的位置就是焊缝根部的投影位置,若射线垂直焊缝透照,则缺陷一般在焊缝影像的中间。若斜角度透照或者母材坡口形状不对称(开单边坡口)可能偏向一边。 (2)坡口未熔合:典型影像是连续或断续的黑线,宽度不一,黑度不均匀,一侧轮廓较齐,黑度较大,另一侧轮廓不规则,黑度较小,在底片上的位置一般在中心至边缘的1/2处,沿焊缝纵向延伸。 坡口未熔合示意图和底片影像 钢焊缝射线照相底片缺陷影像的识别 1 底片上缺陷影像的分析 1.1底片上影像来源分类 底片上影像千变万化,形态各异,但按其来源大致可分为三类: 1. 由缺陷造成的缺陷影像; 2. 由试件外观形状造成表面几何影像; 3. 由于材料、工艺条件或操作不当造成的伪缺陷影像。 对于底片上的每一个影像,评片人员都应能够作出正确解释。影像分析和识别是评片工作的重要环节,也是评片人员的基本技能。 1.2焊接缺陷影像的显示特征 焊接缺陷的影像特征基本取决于焊缝中缺陷的形态、分布、走向和位置,因射线透照角变化而造成的影像畸变或影像模糊也应予以充分考虑;对缺陷特性和成因的充分了解和经验,有助于缺陷的正确判断。必要时,应改变射线检测方案重新拍片;也可对可疑影像进行解剖分析,这样可以减少误判和漏判。 缺陷影像的判定,应依据三个基本原则: 1.2.1影像的黑度(或亮度)分布规律。如气孔的黑度变化不大,属平滑过渡型;而夹渣的黑度变化不确定,属随机型。 1.2.2影像的形态和周界。如裂纹的影像为条状,且必有尖端;而未焊透或条状夹渣虽然也是条状的,但一般不可能有尖端。未焊透的两边周界往往是平直的,而夹渣的周围往往是弧形不规则的,而气孔的形态大多是规则的。 1.2.3影像所处的部位。如破口边沿未熔合往往产生于焊接坡口的熔合面上,因此大多出现在焊缝轴线的两侧;而未焊透则多出现在焊缝轴线上。 2 缺陷影像的识别 2.1气孔 2.1.1成像:呈暗色斑点,中心黑度较大,边缘较浅平滑过渡,轮廓较清晰。 2.1.2形状:圆形、椭圆形、长条形、虫形等。 2.1.3形态:单个、分散、密集、链状等。 2.1.4分布:焊缝中任意部位。 参见以下电子图片。 2.1.5两种特殊情况 ⑴针孔:直径较小,但影像黑度很大,一般发生在焊缝中心。 参见以下电子图片。 ⑵夹珠:它是由前一道焊接生成的气孔,被后一道焊接熔穿,铁水流进气孔的空间而形成的,在底片上的影像为黑色气孔中间包含着一个白色圆珠。 参见以下电子图片。 2.2非金属夹渣 2.2.1成像:呈暗色斑点,黑度分布无规律,轮廓不圆滑,小点状夹渣轮廓较不清晰。 2.2.2形状:形状较不规测,点状、长条形、块状,有时带尖角。 2.2.3分布:焊缝中任意部位。 2.2.4形态:单个或分散、密集(网状)、长条断续等。 参见以下电子图片。 2.3夹钨(金属夹渣) 2.3.1成像:呈亮点,轮廓清晰。 2.3.2形状:圆形、椭圆形、长条形或呈开花状。 2.3.3分布:氩弧焊打底电弧焊盖面的焊缝分布在根部;全氩焊焊缝在焊缝任意部位。射线底片评定(行业一类)
射线评片技巧.
射线照相底片的评定
射线底片评定操作培训
射线检测底片评定表
射线照相底片评定
射线评片技巧焊缝未熔合射线底片影像特点修订版
第六章射线照相底片的评定
工业X射线底片评定方法
射线无损检测底片评定制度
射线底片评定技术(评片基本要求部分)
射线照相底片的评定
某单位射线胶片照相检测RT工艺规程范本
某单位射线胶片照相检测操作规程(范本)
RT焊缝射线照相底片的评判规律
射线照相底片评定
射线评片技巧三:焊缝未熔合射线底片影像特点完整版
钢焊缝射线照相底片缺陷影像的识别