锂电池梯次利用
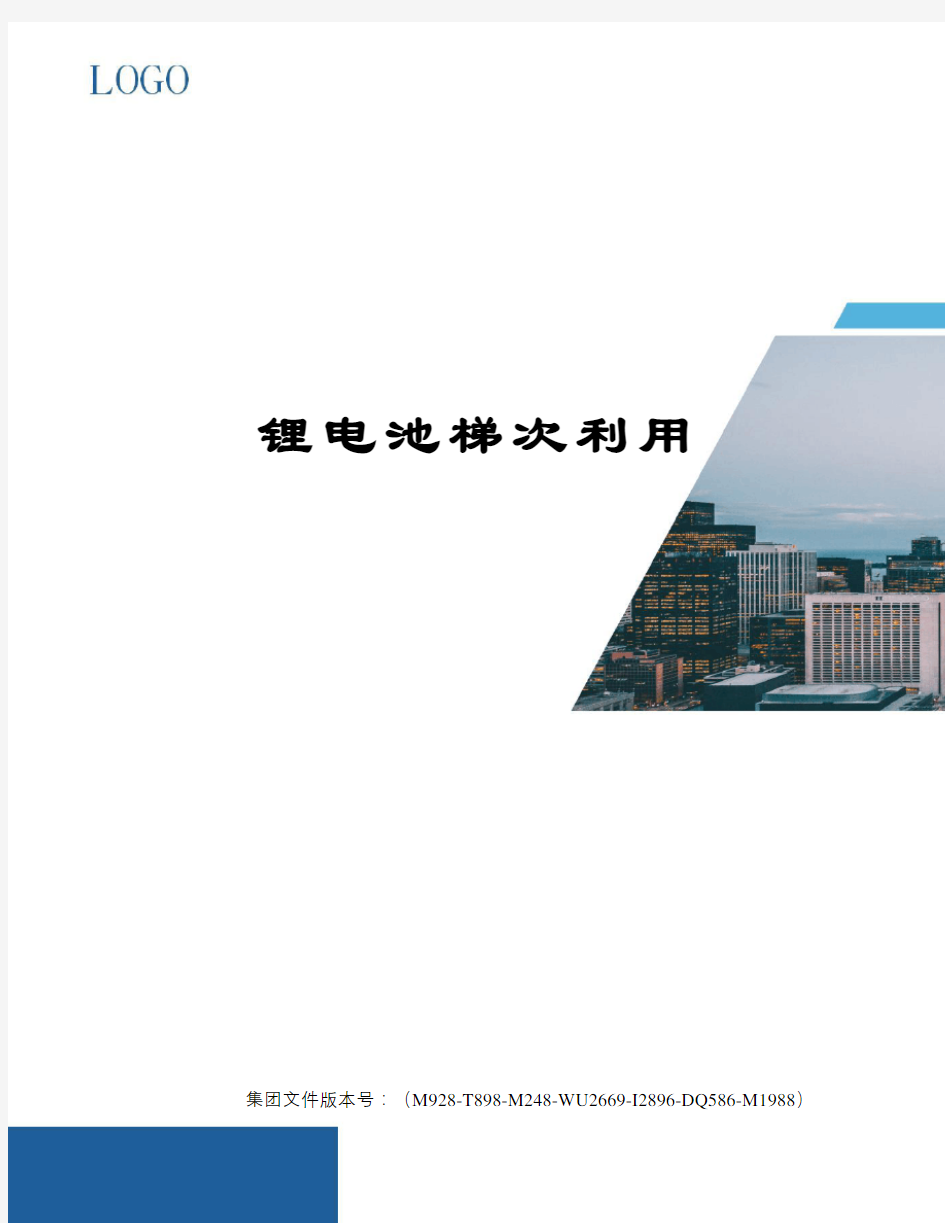

锂电池梯次利用
集团文件版本号:(M928-T898-M248-WU2669-I2896-DQ586-M1988)
背景
近年来,受益于政策、补贴,我国新能源汽车呈现快速增长,进而导致动力锂电池的需求量和报废量不断增长。统计数据显示,2015年中国锂电池总产量47.13Gwh,其中,动力电池产量16.9Gwh,占比36.07%;消费锂电池产量23.69Gwh,占比50.26%;储能锂电池产量1.73Gwh,占比3.67%。《报告》测算,到2020年动力锂电池的需求量将达到
125Gwh,报废量将达32.2Gwh,约50万吨;到2023年,报废量将达到101Gwh,约116万吨。
当前,电池金属材料资源的供需不平衡正逐渐显现。随着新能源车下游需求逐步明确,国内动力电池厂商2016-2017年纷纷扩大产能,尤其是三元电池的扩张,进一步提升了对钴的需求因此从废旧电池中回收再利用钴也越来越具有经济性。对企业而言,动力电池回收蕴藏着巨大的商机,经过回收处理,可以为电池生产商节约原材料成本。此外,动力电池回收还与政府建设低碳经济和环境友好型社会密切相关。
电动汽车的动力电池性能会随着充电次数的增加而衰减,当电池容量衰减至额定容量的80%以下时,动力电池就不适于应用在电动汽车上,这意味着其在电动汽车上的使用寿命终止。如果直接将电池淘汰,必将造成资源的严重浪费,同时也会导致环境污染。
国标GB/T34013-2017《电动汽车用动力蓄电池产品规格尺寸》明确规定了电动汽车用动力蓄电池的单体、模块和标准箱尺寸规格要求。这一标准可有效解决此前存在于动力电池梯次利用中,动力电池由于尺寸不一难以匹配储能电站或家用储能设备结构的难题,也降低了动力电池的梯次回收利用的门槛。
国标GB/T34014-2017《汽车动力蓄电池编码规则》规定了动力电池编码基本原则、编码对象、代码结构和数据载体。该标准发布,可在动力电池生产管理、维护和溯源、电动汽车关键参数监控,特别是在动力电池回收利用环节,凭借可追溯性和唯一性,更加准确地确定动力电池回收的责任主体。
国标GB/T34015-2017《车用动力电池回收利用余能检测》。则规范了动力电池外观检查、极性检测、电压判别、充放电电流判别、余能测试等检测流程,为车用动力电池的余能检测提供评价依据,有助于提高废旧动力蓄电池余能检测的安全性和科学性。
随着新能源汽车保有量的增长,动力锂电池的梯次利用和回收成为一个必须面对的问题。在动力锂电池梯次利用和回收尚未发展成熟的情况下,运营模式就显得尤为重要,这关乎成本和盈利等企业切身利益。目前国内已有企业在动力锂电池的梯次利用和回收方面展开布局,运营模式也各有不同。
动力电池梯次利用的意义在于从电池原材料—电池—电池系统—汽车应用—二次利用—资源回收—电池原材料的电池全生命周期使用角度考虑,可以降低电池成本,避免环境污染。
针对退役的动力电池,有两种可行的处理方法。一种是直接作为工业废品,进行报废和拆解,提炼其中的原材料,实现原材料的循环利用。另一种方式则是考虑退役的动力电池,虽然已经不满足汽车的使用条件,但仍然拥有一定的余能,其寿命并未完全终止,可以用在其他领域作为电能的载体使用,从而充分发挥其剩余价值。
退役电池单体之间存在差异,尤其是均匀性上,有时候能量的衰减是非线性、断崖式的,就如同木桶理论——最短的木板起决定作用,最差的电池则决定了整个储能系统的性能
目前我国动力电池回收处理技术发展较为成熟,但管理相对落后,阻碍了动力电池回收产业的发展。主要表现在:回收网络不健全,回收网络主要由中小回收公司组成,难以得到有效回收;回收企业规模较小,工艺水平不健全,较难保证资源回收效率;存在没有经营许可的企业非法从事废旧动力电池回收,带来安全和环保隐患。
据了解,目前国内外对废旧锂离子电池的回收过程是:首先彻底放电,然后对电池进行拆解分离出正极、负极、电解液和隔膜等各组成部分,再对电极材料进行碱浸出、酸浸出、除杂后进行萃取以实现有价金属的富集。
梯次利用
梯次利用的前提首先从全生命周期追溯。如果不解决电池使用过程中到底怎么使用的、使用状况是什么样的,梯次利用也无从谈起。
梯次利用技术难点一是探索最佳配组方案,标准模组直接梯次利用是最佳方案,单只问题电芯导致模组需要拆解并重新组合。难点二是集中式大型储能电站安全性。磷酸铁锂电芯的大规模储能梯次利用是可行的,退役的三元电芯的集中式储能方案不现实,适合直接资源化回收。难点三是BMS元器件老化,电子元器件的老化失效需要技术验证。
2009年日本东芝提出对SCIB电池进行二次利用。2013年之后,国内众多动力电池企业、电动汽车企业也都积极开展动力电池梯次利用基础研究。电动汽车市场化快速发展让动力电池的梯次利用有了“现实需求”,研发及应用逐渐增多。
电动汽车的梯次利用要考虑到电动汽车的复杂性,但技术上总体可行。在工程示范应用方面,国网建有30KW/1MWh梯次利用锰酸锂电池储能系统和250KW/1MWh梯次利用磷酸铁锂电池储能系统。
总体来讲,我们需要关注三个方面的问题:
①技术性可行性方面:包括老化程度、后期衰退、安全性、可靠性,涉及到老化、失效机理,后续寿命,安全性、可靠性检测、分级筛选技术、工况测试,重组与管理技术等方面,但相关标准目前仍缺失。
②经济可行性方面,包括旧电池成本计运输/检测、重组成本,新电池成本的快速降低,低成本的竞争性储能技术,再利用的收益,需要快速检测/分选/成本技术,电池系统组件综合再利用等。
③市场方面,所有权复杂、电池残值、风险责任、电力市场,这方面还需要政府支撑与扶持,产业界的积极响应和。
总体来说,随着动力电池技术进步和性能的提高,相关标准的逐步完善,都利于其梯次利用。而动力电池梯次利用的经济性随着储能市场的发展及电池梯次利用规模化的应用,也逐渐显现。
在回收工艺方面,我们实现了电池安全无污染的拆解,通过碱液中和去除电解液,对碱液也进行处理和再利用,同时也实现正负极、隔膜等所有材料的有效分离,对碱液实现全收集和净化处理。创新之处是碱液中和,无高温煅烧,无烟尘、尾气排放,实现100%分离,同时适用于LFP与三元电池回收处理。但同时也存在挑战,即设备自动化低和处理效率低。
从整个投入来看,回收处理1吨废旧电池的花费约在5575元,回收处理1吨废旧三元电池的收益为5900元。三元电池回收可实现预期经济效益,LFP电池回收,须通过提高回收处理效率以期实现经济效益平衡。
总而言之,要实现铁锂电池回收,回收效率是一个关键。
我国正处于电池梯次利用的起步阶段,技术难点还有重组技术、寿命预测和离散整合技术等。寿命预测是整个梯次利用产品技术的关键点,如果不掌握产品的使用寿命,试问如何为客户提供质量保证呢?所以从电池企业的角度出发,攻克寿命预测技术是梯次利用项目的重中之重。
当然,寿命预测技术之所以难,是由于很多关键技术集中体现,如衰减机理、检测、消耗量等。
还有一个难点,在不同的情况、不同的地区环境和工况下,电池的消耗速率并不一样,同一时间退役的一批电池,将出现不同的衰减速率,而将分布不均匀的电池重新应用于一个产品中,对于整个行业来讲,这是一个难点。离散整合技术的关键点就是在管理系统里如何让系统更有效地应用剩余的能量,目前业内都在集中力量攻克这个难点,重点解决不同的离散程度的电池包如何在一个系统里高效运行。
电池材料回收方面,宁德时代与具备材料回收资质的企业合作。从操作流程来讲,主要包括电池包分类、拆解及材料回收三步骤。
目前,针对材料回收的拆解环境、运输条件,企业都在制定标准,今年可推出材料回收和包装运输的标准,计划在2017年推行一系列梯次利用标准。
具体而言,电池拆解是通过破碎变成电极粉,再将相关金属进行回收;材料回收主要是通过电极粉、经过酸碱、萃取,然后变成三元材料,最终呈现的产物是硫酸镍、硫酸锰、硫酸钴等。对此,确保回收过程也是环保回收是衡量梯次利用的一个重要标准,因此过程监控显得非常重要。
基于此,国家对场地、拆解环境、拆解设备、拆解人员做出相应的要求,企业在制定标准时也涉及到设备、人员资质、拆解环境、油水分离等问题。总而言之,材料回收在保证环保的同时,要达到较高的回收率。
最后,电池材料回收是通过“物理+化学”的方法,整车企业无须过多考虑后端处理的问题。
相对而言,梯次利用更能够发挥产品的最大价值,实现循环经济的利益最大化,是更为绿色和环保的做法。但梯次利用所面临的难题和挑战也非常的多,如果不能有效解决,就不能实现真正的产业化。
1. 电池拆解
动力电池退役时,是整个pack从车上拆解下来的。不同的车型有不同的电池pack设计,其内外部结构设计,模组连接方式,工艺技术各不相同,意味着不可能用一套拆解流水线适合所有的电池pack和内部模组。那么,在电池拆解方面,就需要进行柔性化的配置,将拆解流水线进行分段细化,针对不同的电池pack,在制定拆解操作流程时,要尽可能复用现有流水线的工段和工序,以提高作业效率,降低重复投资。
在拆解作业时,不可能完全实现自动化,必然存在大量的人工作业,而pack本身是高能量载体,如果操作不当,可能会发生短路、漏液等各种安全问题,进而可能造成起火或爆炸,导致人员伤亡和财产损失。因此,采取什么样的措施和方法,确保电池拆解过程中的安全作业,是梯次利用的一个重点。
2. 剩余寿命预测
这里分两种情况考虑,一种是动力电池在服役期间,其相关运行数据有完整记录,那么当梯次利用的厂家拿到这些数据之后,结合电池的出厂数据,可以建立电池模组的简单寿命模型,能够大致估算出,在特定运行条件下电池模组的剩余寿命(根据所设定的终止条件)。
另一种情况就恶劣的多了,动力电池的使用情况并无数据记录,仅有出厂时的原始数据(如标称容量、电压、额定循环寿命等),使用过程未知,当前状态未知。当梯次利用的厂家拿到电池后,如何判断其健康状态和剩余寿命呢?这就需要对每个模组进行测试,先明确其当前的健康状态,然后要根据测试数据和出厂时的原始数据,建立一个对应关系,根据不同的材料体系,大致估算其潜藏的剩余价值。
第二种情况,梯次利用的成本会提高很多,测试设备、测试费用、测试时间、分析建模等,都会增加不少的成本,导致梯次利用的经济价值降低。基于有限的数据,对剩余寿命的预测也是不准确的,这无疑又会增加梯次利用产品的品质风险,使得产品的生命周期成本较高。所以,如何做到快速无损的检测,是该种情况下梯次利用的关键所在。
3. 系统集成技术
梯次利用,最合理的应该是拆解到模组级,而不是电芯级,因为电芯之间的连接通常都是激光焊接或其他刚性连接工艺,要做到无损拆解,难度极大,考虑成本和收益,得不偿失。
不同批次的电池模组,甚至来自不同厂家的电池模组,如何在同一系统中混用?这里面有几个系统集成技术必须着重考虑并解决:
1) 分组技术
需要对不同的电池模组建立数据库,根据材料体系、容量、内阻、剩余循环寿命等参数重新分组。分组参数设定要合理,过大不好,模组离散性大,成组为系统后,对系统性能和寿命影响很大;过小也不行,分组过于严格,会导致可匹配的模组少,系统集成困难,产品成本很高。
2) 成组技术
什么类型的电池模组可以成组为系统,这需要结合产品定位和目标市场(高端?中端?低端?),现有电池模组等级和类型,以及产品开发具体目标(性能,寿命等),建立一个系统级模型,推算出相关的匹配系数,确定产品的总体方案。
3) 系统柔性设计
这里有两个方面需要考虑:系统结构方面,需要充分考虑不同模组可能具有不同的尺寸,重量和串并联数,那么系统内部的结构设计应该是在X,Y,Z轴方向都有很大的弹性,以兼容不同的模组,固定方式既要考虑紧固性和可靠性,又要考虑弹性和便于快速装卸;模组的线束连接方面,多柔性化考虑,做到可快插和快换。
4. 电池管理系统的鲁棒性
(锂)电池管理系统的设计,一直是个世界级的难题,直到目前为止,也没有哪个公司在这个领域做到相当的成熟,最多实现了产业化而已。针对电池组的优化管理,尚无非常有效的解决方案,因为电芯并不是一个特性比较明确的物理系统,而是一个在不断变化的化学系统,其各项参数都与运行工况、外部环境、内部劣化速度相关,随时间在不断的变化。国外在算法和理论研究方面走的比较早,在工程方面也有深厚积累,所以产业相对成熟。国内在BMS软硬件研发方面,起步较晚(最近几年的事情),理论研究不足,工程应用是小步快跑,整体资源投入不足,各家企业都还没有非常稳定可靠的解决方案。
在梯次利用领域,BMS所要面对的情况,比汽车领域更为复杂。面对各种化学体系、各种规格和批次、各个生产厂家、各种健康状态的电池模组,如何进行有效的管理,确保他们在今后的岁月中健康工作,安度晚年?
在硬件方面,应确保BMS的硬件归一化设计,兼容各种不同的模组,而不必针对不同的模组和产品,开发多种规格的硬件产品。这样可以简化BMS的硬件开发、升级和维护,降低产品的成本。在软件方面,需要做到底层软件模块化、标准化和固定化,应用层软件做到模块化、标准化和智能化,能够自适应各种类型的模组,并能够自我学习,在运行过程中为模组和电芯建立模型,做到智能化的监控、预测、诊断、报警和各类在线服务。软件的升级可在线进行,并可远程升级。
5. 成本控制
毫无疑问,成本是梯次利用的最大优势,也是梯次利用经济效益的来源。那么如何做到良好的成本控制,将系统成本做到新电池产品的三分之一,甚至五分之一,将直接决定梯次利用是否能够发展成为一个庞大的产业。
在原材料环节,如何以较低的成本拿到电池pack,如何降低pack和模组拆解的难度,如何针对不同pack复用流水线和工艺,如何简化测试,如何建立电池模型等,都会影响后续的产品成本。
在产品开发环节,如上面所讲,系统集成是关键,电池模组混用、系统柔性化设计、BMS鲁棒性设计等,都能有效降低产品物料成本。
在产品的运维环节,如何确定合理的质保年限,做到智能化的管理,远程诊断和维护等,都会影响产品的生命周期成本。
6. 产业链整合
动力电池的梯次利用产业链,涉及到用户(车主或商业运营单位)、车企、动力电池企业、梯次利用企业,如何创造一个共生共赢的产业链生态圈,是必须要考虑的。
如果仅仅是后端的梯次利用企业获利,那么用户、车企、以及动力电池企业,就没有足够的动力去参与和推动动力电池的梯次利用,产业规模就难以起来。
这既需要政府层面建立相关规范和标准,也需要产业链各环节的企业,一起紧密合作,尝试成立电动汽车后市场的产业联盟,大家一起来参与,才能推动产业健康发展。
7. 商业模式创新
对于动力电池的梯次利用衍生产品,客户在知情的情况下,会对产品的性能、寿命、可靠性、安全性等心存疑虑,产品的推广会存在一定的阻碍。在产品的推广和应用方面,要充分考虑客户的现状和诉求,多种商业运作方式相结合,在充分帮助客户获利的基础上,获得自己的利益。可充分借鉴其他行业的一些成功经验,如分期付款、分时租赁、盈利后结算、托管运营、甚至免费供货(靠后续增值服务)等,探索梯次利用方面的有效商业模式。
二、可靠性与安全性难题
1. 电芯的容量和内阻离散性
即使经过严格筛选的退役电池模组,在重新配对成组为系统之后,由于大多数电芯都已进入生命周期的中后期,其老化(劣化)速度不一,并且情况较刚出厂的电池要恶劣的多,突出表现为容量和内阻的差异越来越大,导致系统在可用容量和充放电功率方面越来越弱,可靠性问题严重。
这种老化速度的离散性变化趋势,严重时会使得产品的性能和寿命远低于预期,增加产品的售后风险。那么在技术研究上面,除了上述已经谈到了的分组和成组技术,还需要结合BMS的智能化管理和电力电子的功率变换技术,通过BMS在运行过程中去“感知”这种变化趋势,并找出系统的短板,再通过电力电子技术去平衡或弥补“缺陷”,一定程度而言,可以延缓这种加速老化的趋势,延长使用寿命。
2. 潜在的安全隐患
针对拆借后的电池模组,仅通过目视检查,是无法发现一些安全缺陷的,如轻微胀气、漏液、内短路、外壳破损、绝缘失效、极柱腐蚀等。
如果这些安全缺陷不被检查出来,相关模组用到新产品中,那么会导致新产品存在较为严重的安全隐患。采取简单、快速而有效的检查措施为拆解后的电池模组进行安全“体检”,这是非常重要的测试工序。
在新产品运行过程中,BMS仍然承担着电池“家庭医生”的角色,必须时刻对安全状态进行监控,排查隐患,及时采取措施。在梯次利用市场,BMS的安全检测功能显得尤为重要,如同人到中年,身体自然不如年轻人那么健康,及时体检,能够发现大多数疾病的前兆。
三、梯次利用的市场和商业前景
电动汽车动力电池的梯次利用,必须找到适合的市场,并能够产生良好的经济效益,这样才能推动产业化的发展,实现真正的变废为宝,最大限度的挖掘剩余价值。
这个市场,不能是远期的市场,而应该是当前存在的市场,且退役的动力电池在该市场中具备一定的产品竞争优势,使得该市场中的相关企业有足够的利益驱动,采用梯次利用的动力电池组作为部件。
经过初步的分析,我们找到了动力电池梯次利用的3个潜在市场,这些市场既有足够大的规模,也与电池产业息息相关(其主要部件就是电池组),动力电池的梯次利用技术可以与这些市场实现无缝对接,快速实现产业化。
锂电池的回收过程中面临的一些问题,就是隔膜和电解液难以回收,负极回收价值也不是特别高,正极的回收价值比较高。现在国家路线是提升电池高比能量,使得目前整个电池材料的发展是朝着一个高镍材料的方向发展,相比与钴元素,我们未来整个电池回收在元素方面的回收积极性或价值会逐渐的降低。
电池回收可以分为梯级利用和再生利用。梯级利用是我司重点考虑的问题,我希望电池包可以实现整包级别或者模组级别的梯级利用。对于单体级别梯级利用是不看好的,如果单体拆解一整套的流程走下来,一方面成本比较高,另一方面在整个电芯拆解的过程中,势必会用到各种切割或则打磨,可能会产生察觉不到的各种各样的问题,可能对电池的性能会产生巨大的影响。
虽然我们倾向于电池包级别,进行梯级利用,但面对的问题是比较多的,其中最主要的问题,是否有这样的市场可以匹配我们的电池系统级别的运用。目前来看,电池包经过简单的拆解得到电池模组,我们目前是比较看好这块的,因为模块层级扩展性比较好,可以适用于不同的市场。
在梯次利用方面,我们需要解决一些比较大的科学技术问题:第一个是梯级电池的分选技术问题,对于专业的电池汽车来说,我司可以把分选技术做的很好。一方面,我们比较了解我们的电芯,另一方面我们有相应的检测设备,保证我们的电芯可以得到比较好的分选,从而保证梯级利用的寿命和较低的成本;第二个需要关注的问题是梯级目标市场的匹配性,如何找到匹配的市场来使用我们梯级的电池包或者电池模组,而不需要拆解到电芯才能得到应用。第三是梯级电池成组的技术,我们
已有相应的新电池产线,可以适用于梯级电池成组,因此,这方面不是一个问题。第四面临的另一重大问题是电池管理系统的可重复利用性,现有的BMS都是针对某一个电动汽车而进行的设计,大部分采用一些主从式或集中式的电池管理系统模块,而这又不适用于储能应用。后期我们的规划分布式的电池管理系统,模组梯级利用时,匹配一个相对来说扩展性比较好的主板,就可以实现对整个的储能应用系统的的管理。
在再生利用方面,目前来说,我们在这一块的研究处于起步阶段。通过长时间的调研,我们倾向于通过比较“简单粗暴”方法,来实现我们电池的元素回收。现有的湿法工艺虽然可以实现元素比较好的分离,但整个工艺的复杂性还是比较大的,我们现在比较看好火法工艺。对于磷酸铁锂的再生利用,材料的修复的方法需要进一步的研究,这是比较适合磷酸铁锂的方法。
下面简要介绍下我们公司的产品:包括三类电芯:方形铝壳磷酸铁锂和18650圆柱三元和软包三元,我们的目标到是在2017年形成9GWH产能。我们通过技术创新和智能制造两种手段,提高我国的电池技术水平和生产智能化,保证电芯技术先进性和质量性能的一致性。谢谢!
关于动力电池梯次利用的思考
随着国家对电动汽车补贴政策中对关键指标的调整,比如能量密度小于 105wh/kg没有补贴,该值越大补贴力度越大;续航里程150公里以下没有补贴,续航里程越大补贴力度越大等(见下表1和2),磷酸铁锂被国内车企纷纷弃用,带来磷酸铁锂电池产能过剩,六氟磷酸锂矿石大幅降价等现象,如果能把这些过剩的产能向储能产业转移,无疑对电池企业和储能电站建设业主是一种降本增效的双赢局面。因为目前来看,国内投入建设(示范项目居多)的大多数储能电站都是采用磷酸铁锂锂电池,少数采用铅炭电池、钠硫电池、液流电池、超级电容等储能形式,但只要上锂电池系统,基本都采用磷酸铁锂,采用三元等其它形式的,往往也是示范性地做个几十千瓦,用以对比收集数据。 表1 国家对电动车依据能量密度的补贴表 表2 国家对电动车依据续航里程的补贴表 那么动力电池退役后往储能电站方向的梯次利用是否存在一定问题呢? 下面我们对于相关问题逐步进行下梳理。 一、用于乘用车及储能电站电池的诸多不同点:
1、电池数量相差比较大:一般乘用车动力型电池,数量也就是几千块,比如特斯拉model-S基本是7600多块电池,国内的比亚迪等磷酸铁锂电池因为功率比特斯拉小(特斯拉一般是85KW,而国内车辆一般不超过60KW,所以两者的续航里程数相差很多),而兆瓦级的储能电站一般都达到几万块或几十万块电池(取决于系统容量和电池封装类别)。这么多的电池要经过串并联组合,从而输出符合要求的电压和电流,那么对电池管理系统和能量管理系统(即通常所说的BMS和EMS)要求陡然上升; 2、运行过程大不一样:车辆用动力型电池要求瞬间出力要足够大,比如启动和起步的时候要求能够有足够大的功率达到足够的扭矩驱动车辆迅速提速,反映在电池指标上就是要求电池的放电倍率要足够大,一般要求2C以上的电流,甚至要达到10C。而对于储能电站用的能量型电池,根据不同的使用场景,对电流倍率会有不同要求,比如对于削峰填谷,一般要在峰时段均匀放出夜间随存电力,时间往往是2~4个小时,此时的电流倍率为0.5~0.25C。也就是说此场景下对电池的倍率要求比较宽松,对电池的循环寿命有好处。另外一个应用场景就是储能电站参与电网辅助调节,比如深度调峰和AGC辅助调频。深度调峰对于时间也不是要求很短,以1小时前后为多,也就是1C左右的电流倍率为多,而参与AGC辅助调频就不一样了:AGC调频要求快速反应,Kp值要尽可能地大(最大为10),电池系统往往被要求在几分钟到几十分钟时间内放出所有电力(控制在一定放电深度DOD内),那么此时的电流倍率将达到5C~1C范围,对电池放电倍率特性要求很高,也严重考验电池质量和严重影响电池寿命; 3、应用环境不一样:电动车应用在道路场景,可能是市区也可能是高速,可能是夏季也可能是冬季,可能是南方也可能是北方,车辆行驶过程有可能产生颠簸,碰撞,温度的骤然变化,有可能造成电池或电路损坏,进而引发事故。而储能电站的运行环境相对友好,温度恒定,工作环境安静,运行平稳; 4、对能量密度要求不尽相同:由于乘用车内部空间有限,且对行驶质量要求尽量轻便,故对能量密度要求尽可能高,这也是国内外乘用车电池目前几乎全部采用三元
中国废旧电池的回收与再利用技术现状
US-China Electric Vehicles and Battery Technology Workshop, China 2011
中国废旧电池的回收与再利用技术现状
Current situation of recycling and reusing for spent batteries in China 李 丽 北京理工大学
Li Li Beijing Institute of Technology
E-mail: lily863@https://www.360docs.net/doc/ca13852328.html,
US-China Electric Vehicles and Battery Technology Workshop, China 2011
内容提要 Outline
1
我国目前的废旧电池回收现状
The current status of spent battery recycling in China
2
废旧电池综合回收利用技术
Recycle and recovery technologies of spent batteries
3
国内典型电池回收企业
Typical battery recycling companies in China
Beijing Institute of Technology
US-China Electric Vehicles and Battery Technology Workshop, China 2011
Challenge and Opportunites of Power Battery 1.Performance and Safety 2.Cost Reduction 3.Battery Recycling
From the viewpoints of environmental preservation, recovery of major components or valuable resources, and provision of raw materials, the battery recycling is highly desirable inInstitute ofpresent time or the future. Beijing either the Technology
废旧锂离子电池回收工艺研究
废旧锂离子电池回收工艺研究 摘要:锂离子电池回收处理技术随着锂离子电池的大量使用变得越来越重要,早期的锂电池回收主要采用湿法冶金技术,主要回收负极材料中的Co。随着处理技术的发展,锂离子电池里的多种金属都成为了回收目标,机械粉碎、热处理等新方法不断被引入到锂离子电池的回收过程中,锂离子电池的回收技术不断走向成熟。 关键词:锂离子电池回收预处理湿法冶金粉碎 1引言 从20世纪50年代开始,锂电池逐渐从研发实现了大规模的应用。从最初的锂原电池到可反复充电的锂金属二次电池,到现在广泛应用于笔记本电脑、智能手机、各种数码产品的二次锂离子电池(锂电池的发展历史见图1[1])。锂电池主要由正负极和电解质构成,正负电极和电解质之间有隔膜隔开;直接用金属Li作负极的称为锂电池,由能“储存”Li+的材料构成负极的称为锂离子电池。 大量的应用需求刺激了工业生产,松下、索尼、三洋、富士等公司都生产着大量的各种型号的锂离子电池[1]。随着各种电子产品的更新换代,大量的废旧电子产品变成了电子垃圾,但是电子垃圾的处理速度却远远没有跟上。各种简单粗暴的处理方式,如焚烧、酸淋、填埋等对环境和人类造成了不可挽回的伤害[2]。目前针对大多数电子垃圾的回收多是回收其中的贵金属、铁、铝和一些较容易回收的塑料,对结构组成复杂的部件则弃之不理。锂电池结构复杂,为了保证电池的安全性、高效性,锂电池封装紧密、结构紧凑,这导致锂电池的拆解回收就变得很困难,也增加了锂电池的回收成本[3]。 图1锂电池发展历程[1]
2早期锂离子电池处理技术 锂原电池在锂电池的发展过程中逐渐被淘汰,因为用金属Li直接做负极的缺陷在于不能实现重复充电使用,这显然不能符合将锂电池作为一种便捷的能源储备装置来使用。因此现今已实现商业化生产的锂电池都是锂离子电池,它们的不同之处主要是负极材料不同。各种负极材料的使用比例见表1[4]。 表1锂离子电池中各种负极材料的使用比例(体积)[4] LiNi0.33Mn0.33Co0.33O2LiCoO2LiNiO2LiMn2O4LiFePO4 29.00%37.20%7.20%21.40% 5.20% 废旧锂离子电池回收利用的研究开始于20世纪90年代中后期,相比于锂电池的历史要短的多,主要集中在使用最多的以石墨为正极、LiCoO2为负极的锂离子电池上。早期的锂离子电池处理大都采用了湿法冶金的处理技术[5,6]。采矿工业中的湿法冶金工艺成熟,借鉴这种技术使得处理废旧锂离子电池在设备和工艺上都有很好的基础条件。直到现在还有很多人在不断优化这种处理技术[7,8]。 在1999年,M.Contestabile就看到了锂离子电池的市场份额在快速增长,并预感到了处理这些使用过的电池将会变成一个棘手的问题[6]。为了解决这个问题,他设计了一个实验室规模的多步处理过程处理阴极材料为LiCoO2的锂离子电池(图2)。 图2回收过程流程图[6] 该处理方法首先把锂离子电池的外壳剥离,然后使用破碎和分离的设备把锂离子电池切碎,利于进一步的处理。在切碎的过程中由于电池正负极的短接会产生强烈的放热,需要一定的冷却处理,以防止有害物质的挥发和可能发生的爆炸。考虑到锂离子电池中的正负极材
动力电池梯次利用的难点与挑战
动力电池梯次利用的难点与挑战 针对退役的动力电池,有两种可行的处理方法,一种是直接作为工业废品,进行报废和拆解,提炼其中的原材料,实现原材料的循环利用,这方面已经有一些国内的企业进行商业化运作;另一种方式,则考虑退役的动力电池,虽然已经不满足汽车的使用条件,但仍然拥有一定的余能,其寿命并未完全终止,可以用在其他领域作为电能的载体使用,从而充分发挥其剩余价值。 相对而言,梯次利用更能够发挥产品的最大价值,实现循环经济的利益最大化,是更为绿色和环保的做法。但梯次利用所面临的难题和挑战也非常的多,如果不能有效解决,就不能实现真正的产业化。 1. 电池拆解 动力电池退役时,是整个pack从车上拆解下来的。不同的车型有不同的电池pack设计,其内外部结构设计,模组连接方式,工艺技术各不相同,意味着不可能用一套拆解流水线适合所有的电池pack和内部模组。那么,在电池拆解方面,就需要进行柔性化的配置,将拆解流水线进行分段细化,针对不同的电池pack,在制定拆解操作流程时,要尽可能复用现有流水线的工段和工序,以提高作业效率,降低重复投资。 在拆解作业时,不可能完全实现自动化,必然存在大量的人工作业,而pack本身是高能量载体,如果操作不当,可能会发生短路、漏液等各种安全问题,进而可能造成起火或爆炸,导致人员伤亡和财产损失。因此,采取什么样的措施和方法,确保电池拆解过程中的安全作业,是梯次利用的一个重点。 2. 剩余寿命预测 这里分两种情况考虑,一种是动力电池在服役期间,其相关运行数据有完整记录,那么当梯次利用的厂家拿到这些数据之后,结合电池的出厂数据,可以建立电池模组的简单寿命模型,能够大致估算出,在特定运行条件下电池模组的剩余寿命(根据所设定的终止条件)。 另一种情况就恶劣的多了,动力电池的使用情况并无数据记录,仅有出厂时的原始数据(如标称容量、电压、额定循环寿命等),使用过程未知,当前状态未知。当梯次利用的厂家拿到电池后,如何判断其健康状态和剩余寿命呢?这就需要对每个模组进行测试,先明确其当前的健康状态,然后要根据测试数据和出厂时的原始数据,建立一个对应关系,根据不同的材料体系,大致估算其潜藏的剩余价值。 第二种情况,梯次利用的成本会提高很多,测试设备、测试费用、测试时间、分析建模等,都会增加不少的成本,导致梯次利用的经济价值降低。基于有限的数据,对剩余寿命的预测也是不准确的,这无疑又会增加梯次利用产品的品质风险,使得产品的生命周期成本较高。所以,如何做到快速无损的检测,是该种情况下梯次利用的关键所在。 3. 系统集成技术
废旧锂离子电池回收利用的研究现状
废旧锂离子电池回收利用的研究现状 金玉健1Ξ ,梅光军,李树元 (武汉理工大学资源与环境工程学院,湖北武汉 430070) 摘 要:目前废旧锂离子电池的回收利用,重点是电极材料中有价金属的回收,主要是应用酸浸和溶剂萃取相联合的湿法冶金技术,其次将电化学技术用于浸出液中金属的沉积和对失效电极材料的直接修复也有相关的研究报导。根据锂离子电池的发展和未来的环境要求,今后的回收利用将朝综合处理和多元化处理技术的方向发展。关键词:锂离子电池;回收;湿法冶金;修复 自1990年锂离子二次电池问世以来,凭借 其优异的性能迅速占领电池市场,得到广泛应用。国际电源商情的调查数据显示:2000年,全世界锂离子电池的产量为5.41亿只,预计2005年将达到9.5亿只;2000-2003年,中国锂离子电池产业迅速成长,平均增长速度超过140%,未来几年,中国的锂离子电池产业仍将保持年均30%以上的增长速度。在锂离子电池的应用方面,手机和笔记本电脑占据前两位。根据新材料在线的调查,2003年全球锂离子电池的应用,手机和笔记本的市场份额分别为61.2%和25.1%,在便携摄像机、数码相机和PDA 三者中的应用也超过了10%,而在中国90%以上的应用领域为手机市场。1 回收利用现状目前,锂离子二次电池中使用的负极材料多为石墨,正极材料则为嵌锂过渡金属氧化物,如LiC oO 2、LiNiO 2、LiVO 2及LiMn 2O 4等,其中使用最多的是LiC oO 2,它也是最早商品化的锂离子二次 电池正极材料。此外,随着对锂离子电池正极材 料研究的深入,人们在LiC oO 2中掺入少量的镍,以它们的混合氧化物(LiC oxNi 1-x O 2,0 退役动力锂电池回收技术概览 据统计,2000年全世界锂离子电池的消费量是5亿只,2015年达到了70亿只。由于锂离子电池的使用寿命是有限,大量的废旧锂离子电池也随之产生。以中国为例,2020年我国废弃的锂电池将超过250亿只,总重超过50万吨。三元材料电池为例,其正极含有大量贵金属,其中钴占5~20%,镍占5~12%,锰占7~10%,锂占2~5%和7%塑料,所含金属大多是稀有金属,应该被合理的回收再利用。例如,钴作为一种战略资源,被广泛运用于各个领域,除了锂电池还有高温合金等。可以推算,贵金属的回收量是巨大的。 一份动力电池出货量数据如下图所示,按照商用车服役3三年,乘用车服役5年的时间推算,2018年将经历一个动力锂电池的退役小高潮。这些退役下来的电芯,典型的后续路径有两类,梯次利用或者直接材料回收。 动力电池出货量统计 1 梯次利用与原料回收 退役动力锂电池,走梯次利用道路的,是梯次利用之后再进行材料回收;直接材料回收的是批量过小的,无历史可查的,安全监测不合格的等等。 追求经济效益是企业和社会行为的动力。按道理,梯次利用,到电池的可利用价值降低到维护成本以下,再做原料回收,才是电池价值最大化。但实际的情况是,早期动力电池可追溯性差,质量、型号参差不齐。早期电池的梯次利用风险大,剔除风险的成本高,因而可以说,在动力电池回收的前期,电池的去处大概率以原料回收为主。 废旧电池回收产业链 2 正极材料有价金属提取方法 当前说的动力锂电池回收,其实并没有做到整个电池上各类材料的全面回收再利用。正极材料的种类主要包括:钴酸锂,锰酸锂,三元锂,磷酸铁锂等。 电池正极材料成本占据单体电池成本1/3以上,而由于负极目前采用石墨等碳材料较多,钛酸锂Li4Ti5O12和硅碳负极S i/C应用较少,所以目前电池的回收技术主要针对的是电池正极材料回收。 废旧锂电池的回收方法主要有物理法、化学法和生物法三大类。与其他方法相比,湿法冶金 因其能耗低、回收效率高及产品纯度高等优点被认为是一种较理想的回收方法。 2.1 物理法 1、电动汽车行业状况 新能源(电动)汽车作为我国七大战略性新兴产业之一,是基于驱动技术的重大转型,是针对能源安全、持续发展和和产业结构升级问题的重要突破口,因此,大力发展电动汽车对我国具有重要的战略意义。 目前,中国已经初步建立了电动汽车的法规、标准及管理体系,为电动汽车的产业化、商业化发展奠定了基础。2009年1月,国务院通过《汽车产业调整和振兴规划》,明确实施新能源汽车战略,推动纯电动汽车、充电式混合动力汽车及其关键零部件的产业化,提出“三年内形成50万辆纯电动、充电式混合动力和普通型混合动力等新能源汽车产能,新能源汽车销量占乘用车销售总量的5%左右”的目标。电动汽车作为新一轮的经济增长的突破口和实现交通能源转型的根本途径,已经成为世界各主要国家和汽车制造厂商的共同的战略选择,也是各国汽车市场的战略选择。在各国政府的大力推动下,世界汽车产业进入了全面的交通能源转型的时期,电动汽车进入了加速发展的新阶段。现在,更多的专家和更多的企业已经自觉地把发展新能源汽车、节能环保的汽车、电动汽车作为今后发展的目标。 根据中汽协数据,2015年我国电动汽车销售33.11万辆,其中纯电动汽车24.75万辆,同比增长4.5倍,插电混合动力汽车8.36万辆,同比增长1.8倍。 图1 中国新能源汽车销量(2011-2015)截至2015年底,全国汽车保有量达到1.72亿辆,其中电动汽车保有量达到58.32万辆,较2014年底的12万辆增长169.48%,但及汽车整体保有量相比差距仍然很明显。据中国产业调研网发布的中国电动汽车行业市场调查研究及发展趋势预测报告(2015年版)显示,未来几年是中国新能源汽车发展的战略机遇期,《节能及新能源汽车产业发展规划(2012-2020年)》明确指出,到2020年,纯电动汽车和插电式混合动力汽车生产能力达200万辆、累计产销量超过500万辆,燃料电池汽车、车用氢能源产业及国际同步发展。 2、动力电池状况 (1)动力电池技术状况 动力电池类型主要有铅酸电池、镍氢电池、镍镉电池、锂离子电池、钠硫电池、钠/氯化镍电池等。对于电动汽车来说,要想获得及传统汽油车相当的竞争力,持外,更重要的是要找到尽可能接近于理想条件的动力电池,电动汽车理想的动力电池要求 动力电池梯次利用简述 1.概述 从电动汽车上退役的动力电池通常具有初始容量60-80%的剩余容量,并且具有一定的使用寿命,目前主要有两种可行的处理方法:其一是梯次利用,即将退役的动力电池用在储能等其他领域作为电能的载体使用,从而充分发挥剩余价值;其二是拆解回收,即将退役电池进行放电和拆解,提炼原材料,从而实现循环利用。 经过几年的研究探索和试点示范,我国动力电池梯级利用应用领域已集中在电力系统储能、通信基站备用电源、低速电动车以及小型分布式家庭储能、风光互补路灯、移动充电车、电动叉车等其他相关领域。 2.政策 国家积极鼓励动力电池梯级利用,但是暂未建立起完善动力电池梯级利用政策体系。 《节能与新能源汽车产业发展规划(2012—2020年)》,提出建立动力电池梯级利用管理体系。2016年1月,《电动汽车动力蓄电池回收利用技术政策》发布,国家明确提出要鼓励先梯级利用后再生利用,并且支持企业开展梯级利用,不断技术开发和创新。2016年2月份,工信部发布新能源汽车废旧动力蓄电池梯级利用行业规范条件和名单管理暂行办法。 2018年1月出台的《新能源汽车动力蓄电池回收利用管理暂行办法》中明确国家鼓励开展动力电池梯级利用,综合利用企业应符合《新能源汽车废旧动力蓄电池综合利用行业规范条件》(工业和信息化部公告2016年第6号)的规模、装备和工艺等要求,鼓励采用先进适用的技术工艺及装备,开展梯次利用和再生利用。梯次利用企业应遵循国家有关政策及标准等要求,按照汽车生产企业提供的拆解技术信息,对废旧动力蓄电池进行分类重组利用,并对梯次利用电池产品进行编码。梯次利用企业应回收梯次利用电池产品生产、检测、使用等过程中产生的废旧动力蓄电池,集中贮存并移交至再生利用企业。再生利用企业应遵循国家有关政策及标准等要求,按照汽车生产企业提供的拆解技术信息规范拆解,开展再生利用。 2018年2月发布的《新能源汽车动力蓄电池回收利用试点实施方案》明确 废旧锂电池中有价金属回收 一、背景 锂离子二次电池具有重量轻、容量大、使用寿命长等优点, 已成为目前广泛使用的便携式电源。随着手机、手提电脑、数码相机等电器的普及, 锂电池的生产量和消费量直线飙升, 巨大的电池生产消费带来了数目惊人的废电池。然而由于技术和经济等方面的原因, 目前锂电池回收率很低,大量废旧锂电池被遗弃, 给环境造成巨大威胁和污染, 同时对资源也是一种浪费, 分析表明: 锂离子电池平均含钴12%~18% , 锂1. 2%~1. 8%, 铜8%~10% , 铝4%~8% , 壳体合金30%。因此,如何在治理“电池污染”的同时, 实现废旧电池有色金资源尤其是钴的综合循环回收, 已成为社会关注的热点难题。 二、方案的提出 研究表明使用H2SO4+ H2O2体系可以浸出80%的钴;使用机械切割、筛选除铁铝铜、研磨过筛, 后对筛过物采用H2SO4 + H2O2体系浸出, 钴的浸出率高于95%; 先用N2甲基吡咯烷酮溶解PVDF后过筛, 并使用高浓度HCl对钴酸锂进行浸出;使用两级热处理两级过筛后高温煅烧的方法预选粉料, 分别采用HNO3和HNO3+2H2O2体系对筛后粉料浸出,在极大的液固比下HNO3+2H2O2体系的浸出率可达95%; 通过碱煮除铝、盐酸溶钴的方法的处理钴锂膜使钴的浸出率高于99%。这些研究在浸出后的除杂过程都很相似, 均为使用湿法分离技术使钴以氢氧化物或草酸盐的形式从液相中析出已达到分离的目的。 本实验所使用样品由某废旧锂电池拆解厂提供, 该厂通过手工 拆壳、电池芯粉碎、筛分 , 得到各种锂电池芯的混合粉料。这些混合粉料来自于大规模的废旧锂电池的收购, 具有很强的代表性, 本研究的目的在于为该厂后续工业化综合回收废旧锂电池中多种有色金属提供依据。 三、工艺流程 本实验流程为碱浸除铝后使用稀酸液浸泡的方法有效地破坏有机物与铜箔的粘附, 再使用水力旋分达到金属铜、稀酸、电池活性物质的分离, 通过H2SO4 + H2O2的低液固比选择性浸出钴、锂, 所得浸液几乎不含铁, 使用水解沉淀的方法沉淀浸液中的铝、铜, 再萃取分离钴、锂, 直接使用稀草酸液反萃有机相的得草酸钴, 萃余相循环配酸以达到富集锂的目的, 当锂富集到一定程度下使用碳酸沉锂得碳酸锂。综上所述, 实验工艺流程见图1。 表1粉料分析( %, 质量分数) Co Li Al Cu Fe 17. 28 2. 18 5. 95 10. 75 1. 49 图1 废旧锂电池有价金属回收流程图 废物混合动力锂离子电池 碱溶还原AL 酸洗和涡流分类还原Cu 锂电池的梯次利用和回收主要基于环境保护、资源节省、有利可图三个方面: 环境保护:锂电池的正极材料里包含镍、钴、锰、锂等重金属元素,这些重金属元素会对环境、水等造成污染;负极材料里面的碳材、石墨等会造成粉尘污染;此外,锂电池的电解液中含有有毒的化学成分,也会造成氟污染。 资源节省:锂电池中含有大量的金属元素,镍、石墨等我国比较多,但是像钴之类的金属元素是我国稀缺的;中国的锂元素绝对含量很多,但是开采难度比较大,一般都分布在西藏、青海、四川等条件比较艰苦的矿山;盐湖锂里面镁离子含量比较高,提取锂的难度也很大。 有利可图:做锂电池的梯次利用及资源化回收还是能形成商业化的,因为最近几年汽车行业大量转入电动化,锂电池需量增加,导致上游的贵金属材料价格非常高,金属钴价格为60万/吨,镍10万/吨,碳酸锂17万/吨,金属锂90万/吨。 市场风口 1、政策支持 最早在2012年的时候,国务院发布的《节能与新能源汽车产业发展规划》中提到了“制定动力电池回收利用管理办法”; 2014年国务院办公厅发布了《关于加快新能源汽车推广应用的指导意见》,研究制定动力电池的回收利用政策; 2015年财政部、科技部、工信部、发改委在《关于2016-2020年新能源汽车推广应用财政支持政策的通知》中提到“要让电动汽车及动力电池企业承担废旧电池回收的主体”; 2016年,发改委、工信部、环保局、商务部及质检总局又相应的发布了一系列政策,到目前为止,专门针对锂电池回收的政策总共有20多项。 2018年3月,七部委联合发布了最新的《关于开展新能源汽车动力蓄电池回收利用试点工作的通知》。 梳理这些政策,可以归纳出以下四点: 国家各部委主张动力电池先进行梯级利用,再进行资源化回收; 落实生产者责任延伸,即“谁生产,谁负责”; 建立动力电池的回收利用体系,开展一些试点项目,建立回收化网络及信息监管; 行业规范不断完善,国家对企业的资质要求逐步清晰。 2、市场规模 锂电池整体可以分为三大类: 消费类电池:用在手机、IPAD、笔记本电脑等消费类电子产品上的电池,以钴酸锂电池为主; 动力电池:用在新能源汽车上的电池,乘用车上主要是三元电池,商用车主要是磷酸铁锂电池; 储能电池:用在充电站、火电站、商用储能等方面的电池,主要使用的是磷酸铁锂电池。 梯次利用是什么?举个例子,例如将电池用在新能源汽车上,电池充满电的时候是100%的能量,当电池使用一段时间后,电量会衰减,当电量衰减到80%的时候就不能使用在汽车 废旧锂离子电池回收利用技术 锂离子电池自商业化以来,因其具有比能量高、体积小、质量轻、应用温度范围广、循环寿命长、安全性能好等独特的优势,被广泛应用于民用及军用领域,如摄像机、移动电话、笔记本电脑及便携式测量仪器等,同时锂离子电池也是未来电动汽车首选的轻型高能动力电池之一。2012年中国锂离子电池总产量已达到35.5亿只。 锂离子电池经过500~1000次充放电循环之后,其活性物质就会失去活性,导致电池的容量下降而使电池报废。锂离子电池的广泛使用势必带来大量的废旧电池,如若对其随意丢弃不仅会对环境造成严重污染,更是对资源的浪费。锂离子电池中含有较多的钴(Co)、铜(Cu)、锂(Li)、铝(Al)、铁(Fe)等金属资源,其中钴、铜及锂的含量最高分别可达20%、7%和3%。如果能将废旧锂离子电池中的经济价值高的金属加以回收利用,无论从环保方面还是资源的循环利用方面来讲,都具有重大的意义。 1 废旧锂离子电池正极材料回收工艺 锂离子电池通常由电池盖、电池壳、正极、负极、电解质、隔膜等部件组成。目前可用的锂离子电池正极材料有LiCoO2、LiNiO2、LiMn2O4、LiFePO4和三元材料等,负极材料有石墨材料、锡基材料、硅基材料以及钛酸锂材料等。电解质溶液中的导电盐一般为LiPF6、LiBF4、LiCF3SO3等锂盐,常用的溶剂有碳酸乙烯脂(EC)、碳酸丙稀脂(PC)、碳酸二甲脂(DMC)、甲乙基碳酸酯(EMC)等。钴酸锂作为第 1 代商品化的锂电池正极材料是目前最成熟的正极材料,短时间内,特别是在通讯电池领域还有不可取代的优势。目前废锂离子电池的回收利用研究主要集中于电池中正极活性物质的回收利用方法。一般来说,根据所采用的主要关键技术,可以将废锂离子电池的资源化处理过程分为物理法、化学法和生物法这三类。 1. 1 物理法 物理法包括火法、机械破碎浮选法、机械研磨法及有机溶剂溶解法等。物理法往往需要后续化学处理才能进一步得到所需的目标产物。 1. 1. 1 火法 锂电池的回收利用技术简介 1.锂电池发展现状 (2) 2.锂电池的结构和组成 (2) 3.废旧锂电池的危害 (3) 4.锂电池的回收利用技术 (3) 4.1物理分选-化学浸出法 (3) 4.2沉淀分离法 (4) 4.3非晶型柠檬酸盐沉淀法 (4) 4.4电沉淀法 (4) 4.5离子交换法 (4) 4.6直接获取LiCoO2材料的回收技术 (5) 4.7生物浸出工艺 (6) 4.8萃取法 (6) 5.锂电池回收利用中二次污染的处理 (6) 5.1.沉淀分离法中二次污染物的处理 (7) 5.2直接获取LiCoO2材料的回收技术中二次污染的处理 (7) 6.总结 (7) 参考文献 (8) 1.锂电池发展现状 我国政府对锂电池的研究工作相当重视,早在“863”计划中便把研究开发锂离子电池列为重中之重的项目,“九五”期间又将锂离子电池列入国家重点科技攻关项目,在使之成为电子行业新的重大经济增长点的同时,带动整个行业的技术进步和经济发展。1999年中国实现了电池工业的一次飞跃) 固态电解质锂离子电池的开发投产,使我国在新能源领域赶上了世界最高水平。天津力神电池股份有限公司、厦门集美宝龙工业园、TCL集团、北京星恒电源有限公司都拥有具有自主知识产权的固态电解质锂电池生产线。 锂离子电池作为高科技、高产出、高利润、高创汇的绿色环保型能源产品,被国外专家称之为21世纪十大高科技之一或十大赚钱产业之一。另外随着电子产品消耗量日益增加,其消费量正以成倍的速度增长,另外,随着锂离子电池工业的不断发展,其成本会逐渐降低,锂电池有望占据全世界电池市场最大份额,得到广泛应用。在美国,可充电锂电池用锂量约占美国锂消费量的11%;日本可充电锂电池用锂量约占日本锂消费量的54%,在销售方面锂电池已经超过了镉镍电池和镍氢电池。 我国是世界上最大的电池生产国, 年产电池量占世界电池产量的1/ 3。在第九个五年发展计划中, 我国将高科技、高附加值的锂离子电池作为中国电池工业的发展重点并列入国务院发布的重点发展项目。从国内的消费市场看, 随着科技的发展和人民生活水平的不断提高, 家庭或个人用便携式电子产品、电器不断问世并迅速普及, 与之相配套的锂离子电池作为一种携带方便的化学能源, 市场发展潜力无疑是非常巨大的。 2.锂电池的结构和组成 目前,锂离子二次电池中使用的负极材料多为石墨,正极材料则为嵌锂过渡金属氧化物,如LiCoO2、LiNiO2、LiVO2、及LiMn2O4等。 锂离子电池的外壳材料为不锈钢、镀镍钢、铝等,形状有方型和圆柱型,正极与负极用隔膜隔开后卷绕而成。正极由约88%(质量分数)的正极活性物质、7%~8% (质量分数)的导电剂、3%~4% (质量分数)的有机粘合剂均匀混合后,涂布于厚约20μm的铝箔集流体上。负极由约90% (质量分数)的负极活性物质碳素材料、4%~5% (质量分数)的导电剂、6%~7% (质量分数)的有机粘合剂均匀混合后,涂布于厚约15μm的铜箔集流体上。电解液为1mol/L的LiPF6的有机溶液,有 锂电池梯次利用 集团文件版本号:(M928-T898-M248-WU2669-I2896-DQ586-M1988) 背景 近年来,受益于政策、补贴,我国新能源汽车呈现快速增长,进而导致动力锂电池的需求量和报废量不断增长。统计数据显示,2015年中国锂电池总产量47.13Gwh,其中,动力电池产量16.9Gwh,占比36.07%;消费锂电池产量23.69Gwh,占比50.26%;储能锂电池产量1.73Gwh,占比3.67%。《报告》测算,到2020年动力锂电池的需求量将达到 125Gwh,报废量将达32.2Gwh,约50万吨;到2023年,报废量将达到101Gwh,约116万吨。 当前,电池金属材料资源的供需不平衡正逐渐显现。随着新能源车下游需求逐步明确,国内动力电池厂商2016-2017年纷纷扩大产能,尤其是三元电池的扩张,进一步提升了对钴的需求因此从废旧电池中回收再利用钴也越来越具有经济性。对企业而言,动力电池回收蕴藏着巨大的商机,经过回收处理,可以为电池生产商节约原材料成本。此外,动力电池回收还与政府建设低碳经济和环境友好型社会密切相关。 电动汽车的动力电池性能会随着充电次数的增加而衰减,当电池容量衰减至额定容量的80%以下时,动力电池就不适于应用在电动汽车上,这意味着其在电动汽车上的使用寿命终止。如果直接将电池淘汰,必将造成资源的严重浪费,同时也会导致环境污染。 国标GB/T34013-2017《电动汽车用动力蓄电池产品规格尺寸》明确规定了电动汽车用动力蓄电池的单体、模块和标准箱尺寸规格要求。这一标准可有效解决此前存在于动力电池梯次利用中,动力电池由于尺寸不一难以匹配储能电站或家用储能设备结构的难题,也降低了动力电池的梯次回收利用的门槛。 国标GB/T34014-2017《汽车动力蓄电池编码规则》规定了动力电池编码基本原则、编码对象、代码结构和数据载体。该标准发布,可在动力电池生产管理、维护和溯源、电动汽车关键参数监控,特别是在动力电池回收利用环节,凭借可追溯性和唯一性,更加准确地确定动力电池回收的责任主体。 国标GB/T34015-2017《车用动力电池回收利用余能检测》。则规范了动力电池外观检查、极性检测、电压判别、充放电电流判别、余能测试等检测流程,为车用动力电池的余能检测提供评价依据,有助于提高废旧动力蓄电池余能检测的安全性和科学性。 随着新能源汽车保有量的增长,动力锂电池的梯次利用和回收成为一个必须面对的问题。在动力锂电池梯次利用和回收尚未发展成熟的情况下,运营模式就显得尤为重要,这关乎成本和盈利等企业切身利益。目前国内已有企业在动力锂电池的梯次利用和回收方面展开布局,运营模式也各有不同。 动力电池梯次利用的意义在于从电池原材料—电池—电池系统—汽车应用—二次利用—资源回收—电池原材料的电池全生命周期使用角度考虑,可以降低电池成本,避免环境污染。 背景 近年来,受益于政策、补贴,我国新能源汽车呈现快速增长,进而导致动力锂电池的需求量和报废量不断增长。统计数据显示,2015年中国锂电池总产量47.13Gwh,其中,动力电池产量16.9Gwh,占比36.07%;消费锂电池产量23.69Gwh,占比50.26%;储能锂电池产量1.73Gwh,占比3.67%。《报告》测算,到2020年动力锂电池的需求量将达到125Gwh,报废量将达32.2Gwh,约50万吨;到2023年,报废量将达到101Gwh,约116万吨。 当前,电池金属材料资源的供需不平衡正逐渐显现。随着新能源车下游需求逐步明确,国内动力电池厂商2016-2017年纷纷扩大产能,尤其是三元电池的扩张,进一步提升了对钴的需求因此从废旧电池中回收再利用钴也越来越具有经济性。对企业而言,动力电池回收蕴藏着巨大的商机,经过回收处理,可以为电池生产商节约原材料成本。此外,动力电池回收还与政府建设低碳经济和环境友好型社会密切相关。 电动汽车的动力电池性能会随着充电次数的增加而衰减,当电池容量衰减至额定容量的80%以下时,动力电池就不适于应用在电动汽车上,这意味着其在电动汽车上的使用寿命终止。如果直接将电池淘汰,必将造成资源的严重浪费,同时也会导致环境污染。 国标GB/T34013-2017《电动汽车用动力蓄电池产品规格尺寸》明确规定了电动汽车用动力蓄电池的单体、模块和标准箱尺寸规格要求。这一标准可有效解决此前存在于动力电池梯次利用中,动力电池由于尺寸不一难以匹配储能电站或家用储能设备结构的难题,也降低了动力电池的梯次回收利用的门槛。 国标GB/T34014-2017《汽车动力蓄电池编码规则》规定了动力电池编码基本原则、编码对象、代码结构和数据载体。该标准发布,可在动力电池生产管理、维护和溯源、电动汽车关键参数监控,特别是在动力电池回收利用环节,凭借可追溯性和唯一性,更加准确地确定动力电池回收的责任主体。 国标GB/T34015-2017《车用动力电池回收利用余能检测》。则规范了动力电池外观检查、极性检测、电压判别、充放电电流判别、余能测试等检测流程,为车用动力电池的余能检测提供评价依据,有助于提高废旧动力蓄电池余能检测的安全性和科学性。 随着新能源汽车保有量的增长,动力锂电池的梯次利用和回收成为一个必须面对的问题。在动力锂电池梯次利用和回收尚未发展成熟的情况下,运营模式就显得尤为重要,这关乎成本和盈利等企业切身利益。目前国内已有企业在动力锂电池的梯次利用和回收方面展开布局,运营模式也各有不同。 动力电池梯次利用的意义在于从电池原材料—电池—电池系统—汽车应用—二次利用—资源回收—电池原材料的电池全生命周期使用角度考虑,可以降低电池成本,避免环境污染。 针对退役的动力电池,有两种可行的处理方法。一种是直接作为工业废品,进行报废和拆解,提炼其中的原材料,实现原材料的循环利用。另一种方式则是考虑退役的动力电池,虽然已经不满足汽车的使用条件,但仍然拥有一定的余能,其寿命并未完全终止,可以用在其他领域作为电能的载体使用,从而充分发挥其剩余价值。 退役电池单体之间存在差异,尤其是均匀性上,有时候能量的衰减是非线性、断崖式的,就如同木桶理论——最短的木板起决定作用,最差的电池则决定了整 高考必考题锂离子电池习题汇总 材料:锂离子电池实际上是一种锂离子浓差二次电池(充电电池),正负电极由两种不同的锂离子嵌入化合物组成。它主要依靠锂离子在正极和负极之间移动来工作。在充放电过程中,Li+在两个电极之间往返嵌入和脱嵌:充电时,Li+从正极脱嵌,经过电解质嵌入负极,负极处于富锂状态,正极处于贫锂态;放电时则相反,Li+从负极脱嵌,经过电解质嵌入正极,正极处于富锂态 在充放电过程中,负极材料的化学结构基本不变。因此,从充放电反应的可逆性看,锂离子电池反应是一种理想的可逆反应。目前,用作锂离子电池的正极材料是过渡金属和锰的离子嵌入化合物,负极材料是锂离子嵌入碳化合物,常用的碳材料有石油焦和石墨等。国内外已商品化的锂电池正极是LiCoO2,LiNiO2,LiMn2O2,负极是层状石墨 锂离子电池:锂系电池分为锂电池和锂离子电池。手机和笔记本电脑使用的都是锂离子电池,通常人们俗称其为锂电池,而真正的锂电池由于危险性大,很少应用于日常电子产品1、某可充电的锂离子电池以LiMn2O4为正极,嵌入锂的碳材料为负极,含Li+导电固体为电解质。放电时的电池反应为:Li+LiMn2O4=Li2Mn2O4。下列说法正确的是() A.放电时,LiMn2O4发生氧化反应B.放电时,正极反应为:Li++LiMn2O4+e-=Li2Mn2O4 C.充电时,LiMn2O4发生氧化反应D.充电时,阳极反应为:Li++e-=Li 2、(2014天津6)已知:锂离子电池的总反应为:LixC+Li(1-x)CoO2=C+LiCoO2锂硫电池的总反应为:2Li+S=Li2S 有关上述两种电池说法正确的是( ) A.锂离子电池放电时,Li+向负极迁移 B.锂硫电池充电时,锂电极发生还原反应 C.理论上两种电池的比能量相同 D.右图表示用锂离子电池给锂硫电池充电 3、天津是我国研发和生产锂离子电池的重要基地。锂离子电池正极材料是含锂的二氧化钻(LiCoO2),充电时LiCoO2中Li被氧化,Li+迁移并以原子形式嵌入电池负极材料碳(C6)中,以LiC6表示。电池反应为,下列说法正确的是()A.充电时,电池的负极反应为LiC6-e-Li+C6 B.放电时,电池的正极反应为CoO2+Li++e-LiCoO2 C.羧酸、醇等含活泼氢气的有机物可用作锂离子电池的电解质 D.锂离子电池的比能量(单位质量释放的能量)低 动力电池梯次利用的难 点与挑战 Hessen was revised in January 2021 动力电池梯次利用的难点与挑战 针对退役的动力电池,有两种可行的处理方法,一种是直接作为工业废品,进行报废和拆解,提炼其中的原材料,实现原材料的循环利用,这方面已经有一些国内的企业进行商业化运作;另一种方式,则考虑退役的动力电池,虽然已经不满足汽车的使用条件,但仍然拥有一定的余能,其寿命并未完全终止,可以用在其他领域作为电能的载体使用,从而充分发挥其剩余价值。 相对而言,梯次利用更能够发挥产品的最大价值,实现循环经济的利益最大化,是更为绿色和环保的做法。但梯次利用所面临的难题和挑战也非常的多,如果不能有效解决,就不能实现真正的产业化。 1. 电池拆解 动力电池退役时,是整个pack从车上拆解下来的。不同的车型有不同的电池pack设计,其内外部结构设计,模组连接方式,工艺技术各不相同,意味着不可能用一套拆解流水线适合所有的电池pack和内部模组。那么,在电池拆解方面,就需要进行柔性化的配置,将拆解流水线进行分段细化,针对不同的电池pack,在制定拆解操作流程时,要尽可能复用现有流水线的工段和工序,以提高作业效率,降低重复投资。 在拆解作业时,不可能完全实现自动化,必然存在大量的人工作业,而pack本身是高能量载体,如果操作不当,可能会发生短路、漏液等各种安全问题,进而可能造成起火或爆炸,导致人员伤亡和财产损失。因此,采取什么样的措施和方法,确保电池拆解过程中的安全作业,是梯次利用的一个重点。 2. 剩余寿命预测 这里分两种情况考虑,一种是动力电池在服役期间,其相关运行数据有完整记录,那么当梯次利用的厂家拿到这些数据之后,结合电池的出厂数据,可以建立电池模组的简单寿命模型,能够大致估算出,在特定运行条件下电池模组的剩余寿命(根据所设定的终止条件)。 另一种情况就恶劣的多了,动力电池的使用情况并无数据记录,仅有出厂时的原始数据(如标称容量、电压、额定循环寿命等),使用过程未知,当前状态未知。当梯次利用的厂家拿到电池后,如何判断其健康状态和剩余寿命呢这就需要对每个模组进行测试,先明确其当前的健康状态,然后要根据测试数据和出厂时的原始数据,建立一个对应关系,根据不同的材料体系,大致估算其潜藏的剩余价值。 第二种情况,梯次利用的成本会提高很多,测试设备、测试费用、测试时间、分析建模等,都会增加不少的成本,导致梯次利用的经济价值降低。基于有限的数据,对剩余寿命的预测也是不准确的,这无疑又会增加梯次利用产品的品质风险,使得产品的生命周期成本较高。所以,如何做到快速无损的检测,是该种情况下梯次利用的关键所在。 3. 系统集成技术 梯次利用,最合理的应该是拆解到模组级,而不是电芯级,因为电芯之间的连接通常都是激光焊接或其他刚性连接工艺,要做到无损拆解,难度极大,考虑成本和收益,得不偿失。 动力电池梯次利用简述 1. 概述 从电动汽车上退役的动力电池通常具有初始容量60-80%的剩余容量,并且具有一定的使用寿命,目前主要有两种可行的处理方法:其一是梯次利用,即将退役的动力电池用在储能等其他领域作为电能的载体使用,从而充分发挥剩余价值;其二是拆解回收,即将退役电池进行放电和拆解,提炼原材料,从而实现循环利用。 经过几年的研究探索和试点示范,我国动力电池梯级利用应用领域已集中在电力系统储能、通信基站备用电源、低速电动车以及小型分布式家庭储能、风光互补路灯、移动充电车、电动叉车等其他相关领域。 2. 政策 国家积极鼓励动力电池梯级利用,但是暂未建立起完善动力电池梯级利用政策体系。 《节能与新能源汽车产业发展规划(2012 —2020 年) 》,提出建立动力电池梯级利用管理体系。2016 年1 月,《电动汽车动力蓄电池回收利用技术政策》发布,国家明确提出要鼓励先梯级利用后再生利用,并且支持企业开展梯级利用,不断技术开发和创新。2016年2 月份,工信部发布新能源汽车废旧动力蓄电池梯级利用行业规范条件和名单管理暂行办法。 2018年1 月出台的《新能源汽车动力蓄电池回收利用管理暂行办法》中明 确国家鼓励开展动力电池梯级利用,综合利用企业应符合《新能源汽车废旧动力 蓄电池综合利用行业规范条件》 (工业和信息化部公告2016 年第6 号)的规模、 装备和工艺等要求,鼓励采用先进适用的技术工艺及装备,开展梯次利用和再生 利用。梯次利用企业应遵循国家有关政策及标准等要求,按照汽车生产企业提供 的拆解技术信息,对废旧动力蓄电池进行分类重组利用,并对梯次利用电池产品 进行编码。梯次利用企业应回收梯次利用电池产品生产、检测、使用等过程中产 生的废旧动力蓄电池,集中贮存并移交至再生利用企业。再生利用企业应遵循国 家有关政策及标准等要求,按照汽车生产企业提供的拆解技术信息规范拆解,开 展再生利用。 2018年2 月发布的《新能源汽车动力蓄电池回收利用试点实施方案》明确退役动力锂电池回收技术概览
动力电池梯次利用报告
动力电池梯次利用简述
废旧锂电池中有价金属回收Word版
最全面分析:锂电池梯次利用及资源化回收2018.4
锂离子电池回收技术
锂电池的回收利用
锂电池梯次利用图文稿
(完整版)锂电池梯次利用
锂离子电池 习题汇总
动力电池梯次利用的难点与挑战
动力电池梯次利用简述