注塑机抱闸式锁模机构
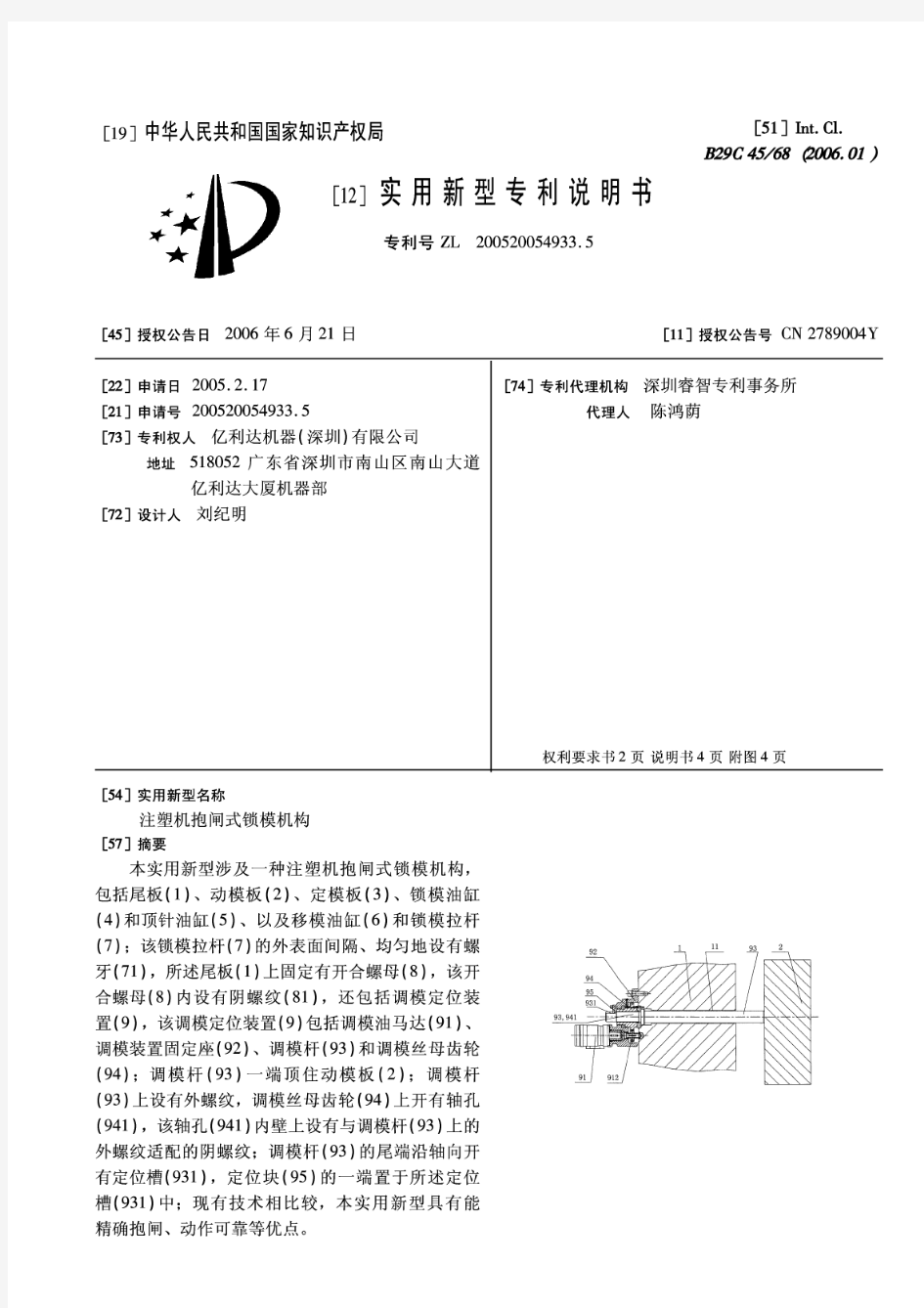

注塑模具锁模力计算
塑料零件锁模力计算方法 一、经验法:锁模力=制品投影面积×面积常数 缺点:过于粗略、随意性大、准确度差;必需建立在丰富的经验基础上,才懂判断如何选择比较合适的常数。 二、常数法:锁模力=投影面积×常数×1.2 合理; 缺点:对于同一原料不同零件结构时,此方法的应用仍然存在随意性。 三、工艺合模法: 投影面积S×模腔压力P≤工艺合模力P≤(0.8~0.9)额定合模力P 模腔压力与壁厚、流长比曲线图如下: 优点:该方法也增加了一个安全系数,按照制品类别区分,考虑了零件结构的复杂因素; 缺点:没有考虑不同塑料之间的差异,应用的准确性也不高。
四、考虑塑料黏度的锁模力计算方法: 锁模力=投影面积×模腔压力×黏度系数K÷安全系数K1 此方法既考虑了材料间的差异,又考虑了不同制品结构复杂程度的差异,同时考虑了模具设计这一因素。应该说是比较科学、准确的。 以上各种方法中,各常数的选择、设定,都是建立在大理实际案例所收集的数据基础之上。但实际应用中,当事人不一定具备如此广泛的理论与实践经验,因此计算中出现误差是在所难免的。 总之,实际应用时,必须考虑以下几点:材料、模具结构、模具浇口形式、零件结构、工艺条件(包括模温、料温等)。 以上只是一些确定锁模力的方法,在实际选择注塑机时,还应考虑如注射量、容模量等其它条件。 例一:零件描述:圆柱体,中间多片薄片;零件直径:10 cm;高度=80mm壁厚=0.8mm原料:普通PP;扇形浇口;一模四腔;总重量180克;尺寸如图1所示。 1)、投影面积计算: S=零件主体面积(3.14×52×4)+流道面积(21+24+6×2+9×2)×0.8=314+60=374 cm2 2)、流长比计算: L/B=(120+30)/8+80/0.8=18.75+100=118.57 3)、模腔压力的确定:根据制品壁厚和流长比,确定模腔压力P=320 kg/cm2 4)、材料黏度系数:K=1 5)、安全系数:K1=80% 锁模力计算: F=P×S×K/K1=320×374×1/80%=149600 kg/cm2=149.6吨 例二:薄壁制品 零件描述:塑料杯子。材料:普通PP;一模八腔;壁厚=0.48~0.52mm;总重量约80克;
注塑机操作说明
注塑机操作流程 四川理工学院机械学院材控系胡勇编制 第一部分参数设置 1.注塑成型机的工作循环周期图 2.注塑机结构
3.注塑机控制面板
1.状态显示画面 2.开关模参数设置显示画面
4.熔胶抽胶参数设置显示画面 5.脱模参数设置显示画面
7.温度参数设置显示画面 8.时间参数设置显示画面
第二部分操作流程 1.注塑机的动作程序: 喷嘴前进→注射→保压→预塑→倒缩→喷嘴后退→冷却→开模→顶出→退针→开门→关门→合模→喷嘴前进 2.注塑机操作项目: 注塑机操作项目包括控制键盘操作、电器控制柜操作和液压系统操作三个方面。分别进行注射过程动作、加料动作、注射压力、注射速度、顶出型式的选择,料筒各段温度及电流、电压的监控,注射压力和背压压力的调节等。 3.注射过程动作选择: 一般注塑机既可手动操作,也可以半自动和全自动操作。 (1)调整操作: ①工作特点:各部位的工作运动,是在按住相应的按钮开关时才能慢速动作,手离开按钮,动作即停止。此动作方式也可叫点动。 ②应用原则。应用在模具的安装调整工作,试验检查某一部位的工作运动时及维修拆卸螺杆时应用。 (2)手动操作: ①工作特点。手指按动某一按钮,其相应控制的某一零部件开始运动。直至完成动作停止。不再按动此按钮,也就不再有重复动作。 ②应用原则。在模具装好后试生产时应用,检查模具装配质量及模具锁紧力的大小调试。对某些制品生产时的特殊情况,也可用手动操作。 (3)半自动操作: ①工作特点。关闭安全门后,注塑制品的各个生产动作时间继电器和限位开关连通控制,按事先调好的动作顺序进行至制品成型,打开安全门,取出制件为止。 机器自动完成一个工作周期,但每一个生产周期完毕后操作者必须拉开安全门,取下工件,再关上安全门,机器方可以继续下一个周期的生产; ②应用原则。注塑机的各部位工作零部件,质量完好,能够准确完成各自
2011注塑机锁模装置设计
注塑机锁模装置设计 学院:机械工程学院专业班级:塑料机械0301班 姓名:邱华指导教师:刘俊萍 摘要:锁模装置可保证成型模具可靠的闭合和开启及顶出制品。作者重点分析和计算了 双肘杆机构的特性并进行了结构设计,采用AutoCAD作图解决了较为复杂的计算问题。 最后设计了调模装置。 关键词:注塑机;双肘杆锁模机构;图解法 The Design of Closed-mold Device for the Injection Molding Machine Abstract The closed-mold device is used to ensure the process of closing and opening of the mould and to eject the products. The author mainly analyzed and calculated the character of double-toggle mechanism and designed the structure .By means of AutoCAD, the author mapped and solved more complex calculation problems. Finally, the device to adjust mould is designed. Key words injection molding machine;double-toggle clamping mechanism; graphical method 1锁模机构的类型与选则 锁模装置的种类较多,按工作原理分,主要有液压式(直压式)和肘杆式(机械式)两大类型。他们都是由模板、拉杆、锁模机构、顶出机构及其它附属装置组成。肘杆式又分单曲肘和双曲肘式,双曲肘机构按组成曲肘的铰链数可分为四孔型和五孔型;如按曲肘排列位置又分为斜排式和直排式。目前最多采用的是五孔斜排形式,由于这种双曲肘式结构对称,结构紧凑,增力作用大,运动特性好,所以选择双肘杆式锁模装置。机构简图如图1。 图1五孔斜排式双曲肘机构简图图2 运动行程与各参数的图解图 2 肘杆机构的结构设计和特性分析 2.1 肘杆机构的参数确定 当动模板的行程S m给定后,综合考虑使机构具有较小的轴向尺寸、较大的增力作用、较高的
关于国产注塑机型号及主要技术参数
国产注塑机型号及主要技术参数都怎样标注? 目前,国内生产注塑机的厂家有多个,表3-5仅列出部分注塑 机生产厂的注塑机型号及主要技术参数。表3-6是大连华大机械有限公司生产注塑机型号及主要技术参数。表3-7是江苏无锡市格兰机械有限公司生产注塑机型号及主要技术参数。 表3-5国产注塑机型号及主要技术性能参 型号 XS-Z-3 0 XS-Z60 SZA-Y Y60 XS-ZY125 XS-ZY 125(A ) X&-ZY250 XS-ZY25 0(A) XS-ZY350(G5 4-S200/400) 理论注射量 (最大)/cm3 30 60 62 125 192 250 450 200?400 螺杆(柱塞) 直径/mm -28 -38 35 42 42 50 50 55 注射压力 /MPa 119 122 138.5 119 150 130 130 109 注射行程 /mm 130 170 80 115 160 160 160 160 注射时间/s 0.7 0.85 1.6 1.8 2 1.7 摞杆转速(r/min) 25? 160 29、43、56、 69,83,101 10? 140 25、31、39、 58,32,89 13?304 16,28,48 注射方式柱塞式柱塞式 螺杆 式螺杆式 螺杆 式 螺杆式螺杆式蜾杆式 锁模力/kN 250 500 440 900 900 1800 1650 2540 最大成型面 积/cm2 90 130 160 320 360 500 645 160 180 270 300 300 500 350 260 模具髙度 (最大)/mm 180 200 250 300 300 350 400 406 (最小)/mm 60 70 150 200 200 200 200 165 模版尺寸、mm 250×2 80 330×4 40 598× 520532×634 拉杆间距 /mm 235 190× 300 330× 300 260×290 360× 360 295×373 370×37 290×368 合模方式肘杆肘杆液压肘杆肘杆液压肘杆肘杆油泵流量 /(L/min) 50 70、12 48 100J2 180J2 129、74、 26 170J2 压力/MPa 6.5 6.5 14 6.5 7.0、 14.0 6.5
中型注塑机锁模装置结构设计
中型注塑机锁模装置结构设计 摘要 本篇设计是中型注塑机锁模装置结构设计,注塑机锁模装置可保证成型模具可靠的闭合和开启及顶出制品,文章主要介绍了注塑机锁模装置的类型以及结构和液压缸的选型计算等等。随时时代的发展和工业的进步,液压工业对其提出了新的要求。中型注塑机锁模装置液压控制系统在注塑模具的工作中起着重要的作用,它直接影响着塑件的成型与模具的性能,因此中型注塑机锁模装置液压控制系统的设计是当今液压工业发展的必然趋势,在以后的若干年里,也会起到越来越重要的作用。 本次设计是关于中型注塑机锁模装置结构的设计,通过对新式的中型注塑机锁模装置的结构和液压方面进行设计,使得此种类型的中型注塑机锁模装置的使用范围更广泛,在塑料模具领域也会起到越来越重要的作用。 关键词:中型注塑机锁模装置、液压缸、控制、作用。
Structure Design Of Locking Device For Medium Sized Injection Molding Machine Abstract This design is a medium-sized injection machine mould locking device structure design, injection molding machine lock mould device can ensure reliable mold closing and opening and ejection products. This article mainly introduces the injection molding machine lock mould device type and structure and the hydraulic cylinder selection calculation and so on. With the development of the times and the progress of industry, hydraulic industry put forward new requirements to it. Medium-sized injection molding machine lock mould device of hydraulic control system in injection mold work plays an important role. It has a direct impact on the plastic parts molding and mold performance. Therefore, medium-sized injection molding machine lock mould device of hydraulic control system design is the inevitable trend of the current hydraulic industrial development, in the next few years, play a more and more important role. This design is a mold device structure design of medium-sized injection molding machine lock, through the new medium injection molding machine lock mould device of the structure and hydraulic design, making this type medium-sized injection molding machine lock clamping apparatus using range more widely, in the field of plastic mold will play a more and more important role. Key words: medium-sized injection molding machine clamping device, hydraulic cylinder, control, effect.
注塑机介绍
注塑机介绍 就热塑性塑料(thermoplastics)而言,注塑机将塑料颗粒材料经由熔融、射出、保压、冷却等循环,转变成最终的塑件。热塑性塑料注塑机通常采用锁模吨数(clamping tonnage)或射出量(shot size)作为简易的机器规格辨识,可以使用的其它参数还包括射出速率、射出压力、螺杆设计、模具厚度和导杆间距等等。根据功能区分,注塑机的大致上有三个种类:(1)一般用途注塑机;(2)精密、紧配注塑机;和(3)高速、薄肉厚注塑机。注塑机的主要辅助设备包括树脂干燥机、材料处理及输送设备、粉碎机、模温控制机与冷凝器、塑件退模之机械手臂、以及塑件处理设备。 1.注塑机组件 典型的注塑机如图1所示,主要包括了射出系统(injection system)、模具系统(mold system)、油压系统(hydraulic system)、控制系统(comtrol system)、和锁模系统(clamping system)等五个单元。 图1 应用于热塑性塑料的单螺杆注塑机 1.1射出系统 射出系统包括了料斗(hooper)、回转螺杆与料筒(barrel)组合,和喷嘴(nozzle),如图2。射出系统的功能是存放及输送塑料,使塑料经历进料、压缩、排气、熔化、射出及保压阶段。 图2 热塑性塑料的单螺杆注塑机之塑化螺杆、料筒、 电热片、固定模板及移动模板。 (1) 料斗 热塑性塑料通常以小颗粒供应成形厂。注塑机的料斗可以存放塑料胶颗粒,藉由重力作用使塑料颗粒经过料斗颈部,进入料筒与螺杆组合内。 (2) 料筒 注塑机的料筒可以容纳回转式螺杆,并且使用电热片(electric heater bands))加热塑料。
注塑机参数及安全调试指引.docx
前言: 为了更规范、更合理、更快速地完成注塑工艺参数调试,提高注塑机和模具使用寿命、减少修 机和修模时间、减少机位人手、减少耗材,提升产品质量和提高生产效率,最终确保生产顺利和稳 定,特制定此份注塑机安全调试指引。 一:注塑生产流程图 生产流程图 二:上模 机台型号与模具大小是否匹配 上模前需要根据模具大小,与机台容模厚度是否匹配,不可出现小机台上大模或大机台上很 小的模。按以下要求执行: 1/2 容模宽度≤模具宽度≤容模宽度 上模前准备 根据模具长度,将注塑机容模厚度设定在合适位置(较模具长度稍长即可),并将机台调至开模状态,之后将安全门打开;根据模具宽度,对于机台固定板上因夹马定位螺丝挡住上模的,则需 要先将螺丝拧下来,往外移至合适位置。最后将机械手调至外端,并将机台马达关闭。 调整容模厚度要求如下: 将注塑机调到手动状态,合模,容模厚度是否与模具长度匹配,对于过短或过长,则需将注 塑机打到调试状态,将容模厚度调试到与模具长度匹配为止。(需要设定调试的速度为最大速度的10%-15%,方可进行容模厚度的调试)。 吊模 将模具从地面或叉车上吊入机仓内,吊装前需检查模具吊装孔是否滑牙,起吊模具时需控制 起吊速度和运输速度。将模具吊起后(离地面高度 15 到 20 公分),平推至注塑机操作界面的对面,之后再将模具升高,至合适高度后,再平移至机台容模腔内,最后将模具降低,降低至进胶口与唧 嘴基本持平。需特别注意,吊环扭入深度必须在两倍直径以上。 对嘴 将模具吊入机仓内,模具进胶口位置与炮嘴基本在一条线上,打开马达进行对嘴。对炮嘴前, 应先合模锁模 ---- 模具处于低压状态(位置在 5MM-10MM),模具能够稍微活动即可。再启动射座以15%-20%的速度进行操作,防止射嘴和模具撞击或碰伤。且在微调模具上下时,唧嘴必须退后一 段距离,避免唧嘴或模具损坏。 打紧马仔,接油接水 1.. 对好嘴之后,马仔拧紧,将模具固定在机台之上。马仔拧紧是指:将螺丝拧紧,拧到手受 力突然增大时,再将螺丝拧 90 到 180 度即可。螺丝进入机板深度必须大于螺丝直径倍以上。 2.拧紧之后,需用扳手轻敲螺丝,发出清脆声音即表明螺丝拧紧。 3.接好油管、水管,并根据所用原料特性要求,调好油温机(或水温机)温度,并打开预热。 原料名称ABS ABS+PC PC PC+GF POM TPU 模温(℃)60--8080--10080--120110--13080--9050--70 4. 同时根据所用原料的特性,设定注塑机螺杆各段的温度,并将其打到保温状态----预热。设置温度的基本要求为:从进料口开始,往唧嘴方向,整个料筒温度依次升高,每段温度差值在
注塑机常见故障及处理(锁模部分)
注塑机常见故障及处理(锁模部分) (一):不锁模: 处理方法: 1):检查安全门前行程开关,并修复。 2):检查电箱内24V5A电源,换保险及电源盒。 3):检查阀芯是否卡住,清洗阀芯。 4):检查I/O板是否有输出,电磁阀是否带电。 5):检查液压安全开关是否压合,机械锁杆挡板是否打开。 (二):开合模机绞响: 处理方法: 1):检查润滑油管是否断开,若是的话,必须重新接好油管。 2):润滑油油量小,加大润滑油量,建议50模打油一次或用手动加足润滑油。 3):锁模力大,检查模具是否需大锁模力,调低锁模力。 4):放大板电流调乱,检查电流参数是否符合验收标准,重新调整电流值。 5):平行度超差,用百分表检查头二板平行度是否大于验收标准;调平行度。 (三):等几秒钟才开模: 处理方法: 1):起动速度慢,检查螺丝阻尼是否过大,调小螺丝阻尼孔。 2):阻尼螺丝钉中间孔太大,检查Y孔螺丝阻尼是否过大,换中心孔细的阻尼钉。(四):开锁模爬行: 处理方法: 1):二板导轨及哥林柱磨损大,检查二板导轨及哥林柱,更换二板铜套,哥林柱,加注润滑油。
2):开锁模速度压力调整不当,设定流量20,压力99时锁模二板不应爬行,调节流量比例阀孔,或先导阀孔,调整比例阀线性电流值。 3):管道及油缸中有空气,排气。 (五):开模开不动: 处理方法: 1):增加开锁模速度,压力流量过小未调好,检查开锁模速度,压力是否适当,加大开锁模压力,速度。 2):锁模电子尺零位变,检查锁模伸直机绞后是否终止在零位,重新调整电子尺零位。 3):检查是否反铰。 (六):自动生产中调模会越来越紧或越松: 处理方法: 1):调模电磁阀内漏,检查电磁阀是否为“O”型,型号4WE6E或0810092101,更换电磁阀或是否电磁阀不工作时带24V电。 2):手动打其它动作时是否有调模动作,并看阀是否卡死。 (七):锁模后其它动作工作时,全自动慢慢开模: 处理方法: 1):油制板泄漏,检查或更换特快锁模阀,更换油制板。 2):开模阀泄漏,开动油泵并锁模终止,按射台或射胶动作,二板是否后移,更换开模油阀。正常为开锁模不动。 (八):锁模时只有开模动作: 处理方法: 1):接错线,检查有否24VDC到阀,检查线路并接线。 2):卡阀或装错阀芯,检查阀芯是否装错,或堵塞,重新装阀芯或清洗。在正常情况下开锁模动作是不动的。 (九):锁模不畅:
注塑机合模参数设置参考说明
注塑机合模参数设置参考说明 锁模结构:双曲肘五铰链斜排内卷式,合模动作位置切换控制:电子尺 一.开始合模: 1、开始合模压力:初设置值参考为25,当此压力过小而导致速度过慢时,可尝试增加速度,此压 力过小,而使速度无法提高至需要时速度每次加+5尝试,注意,该压力设置较大时,会使动模板瞬间加高压改变静止状态变运动,至使动模板孔与拉杆产生巨大的摩擦力,久之加快了机器动模板孔与拉杆的磨损,影响到动模板运动的平稳性与精密度的下降,可能影响到个别对合模机构的精密要求较高模具的生产。 2、开始合模速度:看实际,不过要注意动作不宜过快,该速度要与下一段合模动作具有连贯性 的运动,而不是出现明显的停顿动作切换,最好是速度设置高,压力设置低,由压力控制速度。 二,低压合模:由低压低速推动模具,由需要安全保护的距离开始至模具完全闭合终止 1、低压合模速度:看实际,速度要慢,过快的速度,就算有设置了低压,惯性运动仍然有巨大的撞击破坏力。 滑快位置偏移、顶针断出.....等出现意外硬障碍物时,而进入合模动作,在有效的低压慢度的合模保护参数条件之下,大大减小撞击的损伤。其实可以这个速度为几十,然后不动它,再把压力开始调得很低比如5进行测试,以压力控制速度,再一步步加压至适合的合模保护速度。 2、低压合模压力:可以先把速度调得很高,压力调得很低例如5进行合模测试,因为压力低,就算速度设置 很大,失去压力的支持,合模速度也不会很快的,以压力控制速度,在5的基础上,一点点往上加至理想的合模保护速度,以最低的压力合模。 3、低压合模开始位置:(即上一段合模终止位置)这个要根据模具大小与结构而设置大小差异较大的数值, 一般为模具闭合前的5-20厘米之间,这个位置大家看着办。很多人就是设置模具合得太近,就才开始用低压,应该提前得到低压保护的距离受到上一段较大压力速度冲击合模,滑快位置偏移、顶针断出......等出现意外硬障碍物时,快猛撞击,这时低压保护无效,来迟了,(重点核心)..... 4、低压合模终止位置(即高压锁模开始位置):此参数为模具刚好刚完全闭合的位置,即动模板前进已经 到尽头停止了,调试时先调好低压压力和速度,再将位置设置为0,关门手动合模测试得出一个低压合模完全闭合位置数值,比如这个数值是2.2,这个数值的大小受电子尺设置调整、调模松紧、合模压力大小影响,并且这个数值会受到机器精度和模具表面细小杂物的影响等原因影响,每次合模可能会有小小变动,所以要将终止位置设置稍大一点点比如加0.2设置为2.4(参考加0.1-0.3),以最低的位置,精确保护模具,如果不把低压合模测试获得的位置数值设置大一点点的话,直接就用2.2,可能经常会出现低压合模位置大于2.2,低压位置结束不了而无法转到高压锁模。不过更多人是设置模具还有数厘米距离或更长距离没有完全闭合就低压终止,开始用高压了,低压保护无效,经常见到一些模具被意外带已经顶出了的形成品合模,钢材质模腔被压得变形。(重点核心) 三、高压锁模----开始用高压推动机铰伸直将已经闭合了的模具锁压紧。很多人就是
注塑机锁模力调整
卧式注塑机锁模力调整方式 例一,震雄、震德等机铰式液压机捷霸CPC系列锁模力调整步骤 1,注塑机于手动模式 2,系统画面切换到调模页面 3,此时,调模页面显示的是当前机器的模厚位置,然后输入目标模厚移动位置; 4,启动自动调模 5,电脑画面显示按设定的模厚位置调模前进中/调模后退中,6,目标模厚移动位置达到后,调模完成; 7,手动按锁模键,模具完全接触时,按取消+锁模键,系统会自动计算生成低压关模结束位置(即高压锁模开始位置);8,按锁模健直到高压锁模完成。察看锁模压力表,表上压力是否满足当前模具所需要锁模力,否则在调模状态按“调模前进”/“调模后退键”再微调模厚,直至目标锁模力。9,最后,手动模式中打开模具,锁模力调整完成。 例二,直压液压式注塑机锁模力调整步骤 1,机器于安装模具/准备模式 2,按锁模键,直到闭模完即可,机器未启动高压锁模。 3,设置闭模完当前位置为高压锁模切换零点 4,设定高压锁模力
5,手动模式,按锁模键,直到高压锁模完成(高压启动到完成时间为1—2秒) 6,最后,手动打开模具,锁模力调整完成 例三,KEBA系统锁模力自动调整步骤 KEBA系统自动调模分为位置、锁模力、压力三种控制方式操作平台:注塑机于模具安装模式,切换系统于调模页面 1,位置调模方式步骤 ①设定调模动作压力,速度和监视时间 ②根据待安装的模具厚度设定模厚 ③启动自动调模,自动调模进行中 ④自动调模完成,机器当前模厚反馈值为输入的模厚, ⑤手动锁模,观察系统压力表的压力值是否适合当前模具锁模 力,否则需要重新设定模厚再次自动调模,直至适当的锁模力为止 ⑥手动开模,自动调模完成。 2,锁模力调模方式步骤 ①设定调模动作压力,速度和监视时间 ②设定锁模力 ③启动自动调模,自动调模进行中 ④自动调模完成,但系统画面无锁模力反馈值 ⑤手动锁模,观察系统压力表的压力值是否适合当前模具锁模 力,否则需要重新设定锁模力再次自动调模,直至适当的锁模
注塑机的参数设置基础概括
一、注塑机的参数设置一、注塑成型前准备:1.所用树脂的特性1)干燥条件:干燥温度和干燥时间2)成型温度范围:玻璃化转变温度;熔融温度(粘流温度);热变形温度;分解温度3)模温:无定型聚合物;结晶型... 一、注塑机的参数设置 一、注塑成型前准备: 1.所用树脂的特性 1)干燥条件:干燥温度和干燥时间 2)成型温度范围:玻璃化转变温度;熔融温度(粘流温度);热变形温度;分解温度 3)模温:无定型聚合物;结晶型聚合物。树脂的流动性。模具的复杂程度;结晶速度快慢。 4)流动性:树脂的牌号 2.所用模具的结构特点 1)模具型腔的薄厚,即成型制品的薄厚,流动阻力;模具流长比(离进胶口最远距离与制品壁厚之比) 2)是否容易脱模 3.模具的安装 1)确定模具的定模、动模,以及上下 2)确定顶杆的位置和数量是否合适 3)对角拧紧固定螺钉 4.清洗机筒 1)用热稳定性好的材料清洗 2)前后两种树脂熔融温度不同,用温度高的那种的熔融温度下限进行清洗机筒。 二、注塑成型加工参数的设定 1、先设定机筒和喷嘴各段温度 1)根据物料性质确定加工温度范围:高于熔融温度(或粘流温度),低于分解温度; 2)还要考虑物料的流动性,由树脂的熔体流动速率(MFR)确定:对于流动性差、高粘度,且黏度对温度敏感的材料,如PC,PMMA,PA66等,温度取较高; 3)与模具结构有关:复杂难充型的模具,温度取较高 4)对热敏性材料(PVC、POM等),温度必须严格控制低于其热分解温度,原则上能流动条件下,尽可能低温。 2、设定开关模参数 开、合模原则上遵从慢快慢、快慢慢的顺序,即开模一慢(慢);开模快速(快);开模二慢(慢);关模快速(快)(可分快1、快2);关模低压(慢);关模高压(慢); 压力速度终止位置 快关模快速低压或中压,20-50快速,50-80总行程的70-80%,20 慢关模低压低压,15-30低速,15-253-5 慢关模高压高压,100-低速,15-30 慢开模一慢中或高压,80-低速,20-35行程较短,10-20 快开模快速中压,40-60高速,50-80总行程的70-80%,200 慢开模二慢低压,20-30低速,10-30较短,230 注:以上数值仅表达变化趋势(仅参考),不是一定这个范围,要根据实际注塑机的速度快慢调节。 3、设定储料参数和射出参数 先储料: 1)冷却时间: 考虑材料性能,Tg较高的无定型材料和结晶快的结晶型材料,冷却时间就短。 还要考虑模具结构和制品的结构,模具和制品很薄的,散热快,冷却时间短;厚模、厚制品,且较为封闭的,散热慢的,冷却时间长。 一般30-120秒。对于结构简单、薄壁、冷却快的,冷却时间短,一般10-15S。
注塑机常见故障及处理(锁模部分)
注塑机常见故障及处理(锁模部分) (一):不锁模: 处理方法: 1):检查安全门前行程开关,并修复。 2):检查电箱内24V5A电源,换保险及电源盒。3?):检查阀芯就是否卡住,清洗阀芯。?4):检查I/O板就是否有输出,电磁阀就是否带电。 5):检查液压安全开关就是否压合,机械锁杆挡板就是否打开。 (二):开合模机绞响: 处理方法: 1):检查润滑油管就是否断开,若就是得话,必须重新接好油管。2?):润滑油油量小,加大润滑油量,建议50模打油一次或用手动加足润滑油。3?):锁模力大,检查模具就是否需大锁模力,调低锁模力。4?):放大板电流调乱,检查电流参数就是否符合验收标准,重新调整电流值。?5):平行度超差,用百分表检查头二板平行度就是否大于验收标准;调平行度。 (三):等几秒钟才开模: 处理方法: 1):起动速度慢,检查螺丝阻尼就是否过大,调小螺丝阻尼孔。2?):阻尼螺丝钉中间孔太大,检查Y孔螺丝阻尼就是否过大,换中心孔细得阻尼钉。 (四):开锁模爬行: 处理方法: 1):二板导轨及哥林柱磨损大,检查二板导轨及哥林柱,更换二板铜套,哥林柱,加注润滑油。2?):开锁模速度压力调整不当,设定流量20,压力99时锁模二板不应爬行,调节流量比例阀孔,或先导阀孔,调整比例阀线性电流值。 3):管道及油缸中有空气,排气。 (五):开模开不动: 处理方法: 1):增加开锁模速度,压力流量过小未调好,检查开锁模速度,压力就是否适当,加大开锁模压力,速度。 2):锁模电子尺零位变,检查锁模伸直机绞后就是否终止在零位,重新调整电子尺零位。3):检查就是否反铰。 (六):自动生产中调模会越来越紧或越松: 处理方法:
注塑机的参数设置
注塑机的参数设置 一、注塑成型前准备: 1.所用树脂的特性 1)干燥条件:干燥温度和干燥时间 2)成型温度范围:玻璃化转变温度;熔融温度(粘流温度);热变形温度;分解温度 3)模温:无定型聚合物;结晶型聚合物。树脂的流动性。模具的复杂程度;结晶速度快慢。 4)流动性:树脂的牌号 2.所用模具的结构特点 1)模具型腔的薄厚,即成型制品的薄厚,流动阻力;模具流长比(离进胶口最远距离与制品壁厚之比)2)是否容易脱模 3.模具的安装 1)确定模具的定模、动模,以及上下 2)确定顶杆的位置和数量是否合适 3)对角拧紧固定螺钉 4.清洗机筒 1)用热稳定性好的材料清洗 2)前后两种树脂熔融温度不同,用温度高的那种的熔融温度下限进行清洗机筒。 二、注塑成型加工参数的设定 1、先设定机筒和喷嘴各段温度 1)根据物料性质确定加工温度范围:高于熔融温度(或粘流温度),低于分解温度; 2)还要考虑物料的流动性,由树脂的熔体流动速率(MFR)确定:对于流动性差、高粘度,且黏度对温度敏感的材料,如PC,PMMA,PA66等,温度取较高; 3)与模具结构有关:复杂难充型的模具,温度取较高 4)对热敏性材料(PVC、POM等),温度必须严格控制低于其热分解温度,原则上能流动条件下,尽可能低温。 2、设定开关模参数 开、合模原则上遵从慢快慢、快慢慢的顺序,即开模一慢(慢);开模快速(快);开模二慢(慢);关模快速(快)(可分快1、快2);关模低压(慢);关模高压(慢); 压力速度终止位置 快关模快速低压或中压,20-50 快速,50-80 总行程的70-80%,20 慢关模低压低压,15-30 低速,15-25 3-5 慢关模高压高压,100- 低速,15-30 慢开模一慢中或高压,80- 低速,20-35 行程较短,10-20 快开模快速中压,40-60 高速,50-80 总行程的70-80%,200 慢开模二慢低压,20-30 低速,10-30 较短,230 注:以上数值仅表达变化趋势(仅参考),不是一定这个范围,要根据实际注塑机的速度快慢调节。 3、设定储料参数和射出参数 先储料: 1)冷却时间: 考虑材料性能,Tg较高的无定型材料和结晶快的结晶型材料,冷却时间就短。 还要考虑模具结构和制品的结构,模具和制品很薄的,散热快,冷却时间短;厚模、厚制品,且较为封闭的,散热慢的,冷却时间长。 一般30-120秒。对于结构简单、薄壁、冷却快的,冷却时间短,一般10-15S。 2)储料1和储料2: 先要确定总储料量,根据制品和浇注系统凝料(水口料)的质量计算得到。由此确定储料2段的终止位置。
锁模力的计算及注塑机的选择
锁模力的计算及注塑机的选择 A.锁模力计算: 撑模力量=成品在开关模方向的投影面积(cm2)×模穴数×模内压力(kg/cm2); B.怎样选择合适的注塑机: 1、选对型: 由产品及塑料决定机种及系列。 由于注塑机有非常多的种类,因此一开始要先正确判断此产品应由哪一种注塑机,或是哪一个系列来生产,例如是一般热塑性塑胶或电木原料或PET原料等,是单色、双色、多色、夹层或混色等。此外,某些产品需要高稳定(闭回路)、高精密、超高射速、高射压或快速生产(多回路)等条件,也必须选择合适的系列来生产。 2、放得下:由模具尺寸判定机台的“大柱内距”、“模厚”、“模具最小尺寸”及“模盘尺寸”是否适当,以确认模具是否放得下。 模具的宽度及高度需小于或至少有一边小于大柱内距; 模具的宽度及高度最好在模盘尺寸范围内; 模具的厚度需介于注塑机的模厚之间; 模具的宽度及高度需符合该注塑机建议的最小模具尺寸,太小也不行。 3、拿得出:由模具及成品判定“开模行程”及“托模行程”是否足以让成品取出。 开模行程至少需大于成品在开关模方向的高度的两倍以上,且需含竖浇道(sprue)的长度; 托模行程需足够将成品顶出。 4、锁得住:由产品及塑料决定“锁模力”吨数。 当原料以高压注入模穴内时会产生一个撑模的力量,因此注塑机的锁模单元必须提供足够的“锁模力”使模具不至于被撑开。锁模力需求的计算如下: 由成品外观尺寸求出成品在开关模方向的投影面积; 撑模力量=成品在开关模方向的投影面积(cm2)×模穴数×模内压力(kg/cm2); 模内压力随原料而不同, 一般原料取350~400kg/cm2; 机器锁模力需大于撑模力量,且为了保险起见,机器锁模力通常需大于撑模力量的1.17倍以上。 至此已初步决定夹模单元的规格,并大致确定机种吨数,接着必须再进行下列步骤,以确认哪一个射出单元的螺杆直径比较符合所需。 5、射得饱: 由成品重量及模穴数判定所需“射出量”并选择合适的“螺杆直径”。 计算成品重量需考虑模穴数(一模几穴); 为了稳定性起见,射出量需为成品重量的1.35倍以上,亦即成品重量需为射出量的75%以内。 6、射得好:由塑料判定“螺杆压缩比”及“射出压力”等条件。 有些工程塑料需要较高的射出压力及合适的螺杆压缩比设计,才有较好的成型效果,因此为了使成品射得更好,在选择螺杆时亦需考虑射压的需求及压缩比的问题。 一般而言,直径较小的螺杆可提供较高的射出压力。
注塑参数设定
一、注塑成型前准备 1、所有树脂的特性 1、干燥的条件: 干燥的温度和干燥的时间 2、成型温度的范围: 玻璃化转变温度、熔融温度(粘流温度)、热变形温度、分解温度 3、模温: 无定型聚合物、结晶型聚合物、树脂的流动性、模具的复杂程度、结晶速度的快 慢 4、流动性 树脂的牌号 2、所有模具的结构特点 1、模具型腔的薄厚,即成型制品薄厚,流动阻力;模具流长比(离进浇口最远距离 与制品的壁厚之比) 2、是否容易脱模 3、模具的安装 1、确定模具的定模及动模以及上下 2、确定顶杆的位置和数量是否合适 3、对角拧紧固定螺钉 4、清洗机筒 1、用热稳定性好的材料清洗 2、前后两种树脂熔融温度不同,用温度高的那种的熔融温度下限进行机筒的清洗 二、注塑成型加工参数的设定 1、先设定机筒和喷嘴各段温度 1、根据物料性质确定加工温度范围:高于熔融温度(或粘流温度),低于分解温度 2、还要考虑物料的流动性,由树脂的熔体流动速率(MFR)确定:对于流动性差。
高粘度且黏度对温度敏感的材料,如PC,PMMA,PA66等,温度取较高 3、对热敏性材料(PVC、POM等),温度必须严格控制低于其热分解温度,原则上能流动的条件下,尽可能低温。 2、设定开关模参数 开、合模原则上遵从慢快慢、快慢慢的顺序,即开模一慢(慢);开模快速(快);开模二慢(慢)关模快速(快)(可分快1、快2);关模低压(慢);关模高压(慢); 3、设定储料参数和射出参数 先储料: 1、冷却时间 考虑材料性能,Tg较高的无定型材料和结晶快的结晶型材料,冷却时间就短还要考虑模具结构和制品的结构,模具和制品很薄的,散热快,冷却时间短(一般10~15S),模厚、厚制品,且较为封闭的,散热慢。冷却时间就长(一般30~120S) 2、储料1和储料2 先要确定总储料量,根据制品和浇注系统凝料(水口料)的质量计算得到,由此确定储量2段的终止位置 3、射退 储料达到设定值后,螺杆停止旋转(即不在向储料室输送熔体),只向后抽胶来调整储料室中熔体压力和密度,进而控制流延和影响制品的密度。一般3~10S后设置射出参数4、射出参数设置 1、根据总储料量开始设置射出参数 2、射出各参数设定原则 对于直浇口的产品,既可以采用单级注射的形式,也可以采用多级注射的形式。 对于结构简单、精度要求不高、断面规格的小型塑料制件,可采用低于三级注射的控制方法。 对于复杂和精度要求较高、大型的塑料制品,一定要选择四级或以上的多级注射工艺。 3、多级注射的设定原则是: 注:对于壁厚均匀、截面规则的制品,建议采用一级注射,即美国RGJ技术所倡导的那样,一级高压高速注射模腔的90%,剩余10%用保压通过调整保压时间注满。 A: 射出1段的设定:射出1段的终止位置是要将塑胶注到浇注系统的浇口处。除直浇口,其余的几乎都采用中压、中速或者中压、低速; B:射出2段的设定:射出2段是要将塑胶注入从浇口开始至整个型腔1/2~2/3的空间汇总,高压、高速,高压、中速或者中压、中速,看制品结构和使用的材料而定; C:接下的射出段,宜采用中压中速或中压低速,终止位置设置在时塑胶恰好充满剩余的型腔空间。这些注射过程都是属于充填相的范围。 D、射出最后一段属于增压相范围,保压切换点就是在这一段的注射终止位置(位置切换)或者是在第三段终止位置和零位置之间(时间切换) 5、保压设置 1.保压切换点的选择方法有:时间切换和位置切换两种方法。当射出开始时,同时射出计时,也同时计算各级射出终止位置,如果射出参数不变,流动性较佳的,则最后一段,终
注塑机参数设置界面
动作监视画面 运转中 机器监视 侦测页 模号:PQRI 上模 0.0秒 总数 5 模 设定: 射200 一 220 二200 三﹡﹡﹡﹡ 四 0 油温 现在: ■198 □220 ■195 □﹡﹡﹡﹡ □ 0 16 温度设定画面 (可选项:加热 保温 自动保温 自动加热 不加热) 【温设】 射嘴 一段 二段 三段 四段 油温 现在 加热 保温 高温偏差(数值可自己填写) 冷间螺杆保护延迟(可选项 ON OFF ) 低温偏差(数值可自己填写) 【定时】加热 保温 【日期时间】 3/19/9 14:32:23 四
开合模设定画面 关模 /开模 /调模 动模:78.3mm 【锁模】 快速锁模 压力 速度 位置 (可选项ON OFF ) 噸 压力 Bar 速度 % (上限140) 位置 mm 开模限 270 mm 压力速度 射胶设定画面 射胶 /加料 /射前加料 【射胶】 螺杆 36.6mm 保三 保二 保一 射四 射三 射二 射一 Bar % mm 秒 冷却时间秒 (根据需要输入) 射出形态(可选项: 时+位 位置) 【加料】 加一 加二 后松退 【射前加料】 压力Bar 速 度 % 位置 秒 系统压 OFF (可选项为 ON OFF ) 系统压是否是背压呢?
顶出设定画面 【顶进】进一进二顶针﹡﹡﹡mm 压力 顶针形态 速度顶出延迟 位置顶出保持 次数 (顶出形态可选:震动不用重复)【顶退】退二退一 压力Bar 速度(%) 位置(mm) 【吹气】动模静模 时间秒吹气使用ON OFF)位置mm 功能设定画面 功能\ 时间设定 【功能选择】 取出机油温预热 冷却完加料预热温 度℃ 电眼侦测预热压力Bar 预热速 度 %(可选项为:ON OFF) 【时间设定】 周期保护秒复动时间秒 低压保护秒射出延迟秒 加料保护秒加料延迟秒 射出保护秒异常时间秒 开模保护秒中间警报秒 (以上时间根据需要设定,主要是起保护作用,出现异常会报警)
教你任何设置注塑机合模参数
教你任何设置注塑机合模参数 一,开始合模: 1、开始合模压力:初设置值参考为25,当此压力过小而导致速度过慢时,可尝试增加速度,此压力过小,而使速度无法提高至需要时速度每次加+5尝试,注意,该压力设置较大时,会使动模板瞬间加高压改变静止状态变运动,至使动模板孔与拉杆产生巨大的摩擦力,久之加快了机器动模板孔与拉杆的磨损,影响到动模板运动的平稳性与精密度的下降,可能影响到个别对合模机构的精密要求较高模具的生产。 2、开始合模速度:看实际,不过要注意动作不宜过快,该速度要与下一段合模动作具有连贯性的运动,而不是出现明显的停顿动作切换,最好是速度设置高,压力设置低,由压力控制速度。 二,低压合模: 由低压低速推动模具,由需要安全保护的距离开始至模具完全闭合终止 1、低压合模速度:看实际,速度要慢,过快的速度,就算有设置了低压,惯性运动仍然有巨大的撞击破坏力。滑快位置偏移、顶针断出、、、、等出现意外硬障碍物时,而进入合模动作,在有效的低压慢度的合模保护参数条件之下,大大减小撞击的损伤。其实可以这个速度为几十,然后不动它,再把压力开始调得很低比如5进行测试,以压力控制速度,再一步步加压至适合的合模保护速度。 2、低压合模压力:可以先把速度调得很高,压力调得很低例如5进行合模测试,因为压力低,就算速度设置很大,失去压力的支持,合模速度也不会很快的,以压力控制速度,在5的基础上,一点点往上加至理想的合 模保护速度,以最低的压力合模。 3、低压合模开始位置:(即上一段合模终止位置)这个要根据模具大小与结构而设置大小差异较大的数值,一般为模具闭合前的5-20厘米之间,这个位置大家看着办。很多人就是设置模具合得太近,就才开始用低压,应该提前得到低压保护的距离受到上一段较大压力速度冲击合模,滑快位置偏移、顶针断出、、、、等出现意外硬障碍物时,快猛撞击,这时低压保护无效,来迟了,(重点核心)、、、、 4、低压合模终止位置(即高压锁模开始位置):此参数为模具刚好刚完全闭合的位置,即动模板前进已经到尽头停止了,调试时先调好低压压力和速度,再将位置设置为0,关门手动合模测试得出一个低压合模完全闭合位置数值,比如这个数值是2.2,这个数值的大小受电子尺设置调整、调模松紧、合模压力大小影响, 并且这个数值会受到机器精度和模具表面细小杂物的影响等原因影响,每次合模可能会有小小变动,所以要将终止位置设置稍大一点点比如加0.2设置为2.4(参考加0.1-0.3),以最低的位置,精确保护模具,如果不把低压合模测试获得的位置数值设置大一点点的话,直接就用2.2,可能经常会出现低压合模位置大于2.2,低压位置结束不了而无法转到高压锁模。不过更多人是设置模具还有数厘米距离或更长距离没有完全闭合就低压