烧结砖瓦生产技术问答(DOC 31)
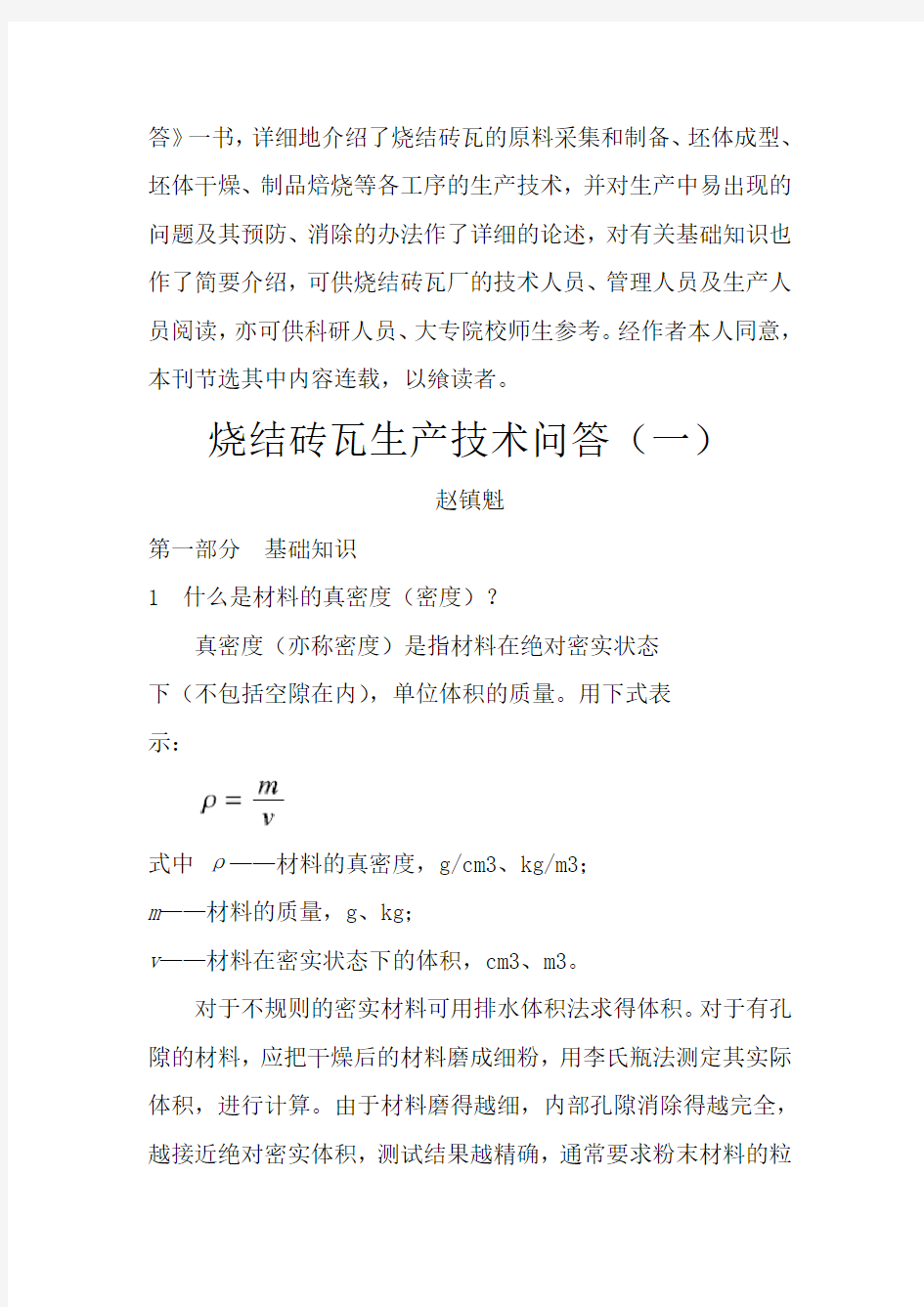

答》一书,详细地介绍了烧结砖瓦的原料采集和制备、坯体成型、坯体干燥、制品焙烧等各工序的生产技术,并对生产中易出现的问题及其预防、消除的办法作了详细的论述,对有关基础知识也作了简要介绍,可供烧结砖瓦厂的技术人员、管理人员及生产人员阅读,亦可供科研人员、大专院校师生参考。经作者本人同意,本刊节选其中内容连载,以飨读者。
烧结砖瓦生产技术问答(一)
赵镇魁
第一部分基础知识
1 什么是材料的真密度(密度)?
真密度(亦称密度)是指材料在绝对密实状态
下(不包括空隙在内),单位体积的质量。用下式表
示:
式中ρ——材料的真密度,g/cm3、kg/m3;
m——材料的质量,g、kg;
v——材料在密实状态下的体积,cm3、m3。
对于不规则的密实材料可用排水体积法求得体积。对于有孔隙的材料,应把干燥后的材料磨成细粉,用李氏瓶法测定其实际体积,进行计算。由于材料磨得越细,内部孔隙消除得越完全,越接近绝对密实体积,测试结果越精确,通常要求粉末材料的粒
径小于0.2mm。
烧结砖的真密度为2400~2800kg/m3。重庆叠叠砖厂生产的煤矸石砖的真密度为2500kg/m3。
2 什么是材料的表观密度(体积密度)?
表观密度(体积密度)是指材料在自然状态下(包括空隙在内),单位体积的质量,用下式表示:式中ρ0——材料的表观密度,g/cm3、kg/m3;
m——材料的质量,g、kg;
v0——材料在自然状态下的体积,cm3、m3。
对于烧结砖瓦等有孔隙的材料,如果是规则形状,可根据实际测量的尺寸求得自然体积;如果外形不规则,可用排液法求得,为了防止液体由孔隙渗入材料内部而影响测值,应在材料表面涂蜡。材料内常含有水分,材料的质量随材料的含水率而改变,因此表观密度应注明其含水程度。
一般用材料在气干状态下的表观密度,即干表观密度。材料的表观密度取决于材料的真密度、构造、孔隙率及含水情况。确定材料表观密度时,应考虑要有较小的导热系数、较高的机械强度和较高的抗震性能等因素。在一般情况下,材料的表观密度过大,则气孔率下降,导热系数增大,强度提高;材料的表观密度过小,虽然固相导热能力下降,但气孔中空气对流作用会增大传热损失,最终反而增大导热系数,同时机械强度会大幅度降低。故应选择一个“最佳表观密度”。“最佳表观密度”通常是用测试
方法确定的。
重庆叠叠砖厂生产的普通煤矸石砖的表观密
度为1705kg/m3。
3 什么是材料的堆积密度?
堆积密度是散粒材料(粉状、颗粒状)在堆积状
态下单位体积的质量,用下式表示:
式中ρ′0 ——材料的堆积密度,g/cm3、kg/m3;
m ——材料的质量,g、kg;
v′0 ——材料的堆积体积,cm3、m3。
材料的堆积体积包括所有颗粒的体积以及颗粒之间的空隙体积,它取决于材料颗粒的体积密度和堆积疏密程度。材料的含水状态也会影响堆积密度值。
重庆某电厂排出的干粉煤灰堆积密度为
560kg/m3。
4 什么是材料的密实度?
密实度是指材料体积内被固体物质充实的程度,即材料的密实体积与总体积之比。材料由固体物质和空隙两部分组成,固体物质的比例越高,材料就越密实,体积密度也就越大。计算式为:
×100%
或:×100%
式中D——材料的密实度,%
一般含孔隙的固体材料的密实度均小于1。
例:重庆二砖厂的普通页岩实心砖的
ρ=2500kg/m3,ρ0=1800kg/m3,求其密实度。
解:×100%=72%
即该厂普通页岩实心砖的密实度为72%。
5 什么是材料的孔隙率?
孔隙率是材料内孔隙体积所占的比例。孔隙率越大,材料的密实度和表观密度就越小。孔隙率P 为:
材料孔隙率和密实度有关,有孔隙的材料,两者之和D+P=1;完全密实的材料,孔隙率P=0,密实度D=100%。材料的许多性质,如强度、吸水性、抗渗性、抗冻性、导热性、吸声性都与孔隙有关。材料的孔隙率是指材料内部孔隙的比例。
材料的某些性质不但与材料的孔隙率有关,还与材料的孔隙特征有关。材料内部孔隙有连通与封闭之分,连通孔隙不仅贯通而且与外界相通,封闭孔隙不仅彼此不贯通,而且与外界隔绝。材料中的孔隙按其尺寸大小分为极微细孔隙、细小孔隙和较粗大孔隙,孔隙的大小及其分布对材料的性质影响也较大。
6 什么是材料的亲水性?
材料在空气中与水接触时,容易被水润湿的性质,称为材料的亲水在水、空气、材料三相交点沿水滴表面的切线与水和材料
接触面所成的夹角为润湿边角θ。
当水分子之间作用力(即表面张力)小于水分子与材料分子之间的相互作用力时,材料易被水润湿,润湿边角θ<90°,这种材料为亲水性材料。木材、混凝土、砂石等都属于亲水性材料。
7 什么是材料的憎水性?
材料不易被水润湿的性质,称为憎水性。
当水分子之间的作用力(即表面张力)大于水分子与材料分子之间的相互作用力时,材料不易被水润湿。润湿边角θ>90°,这种材料为憎水性材料。钢材、玻璃、塑料、沥青等为憎水性材料。
建筑上使用的防水材料一般为憎水性材料;大多数亲水性材料可通过表面处理而具有憎水性。
8 什么是材料的吸水性?
材料在水中吸收水分的性质称为吸水性。吸水性可用吸水率表示。吸水率为材料吸水饱和时,水的质量占材料干燥质量的百分率。即:
式中W m ——吸水率,%;
m1 ——材料吸水后的质量,g、kg;
m0 ——材料干燥时的质量,g、kg。
材料的吸水率与材料的孔隙率及孔隙特征有关。一般说密实的及具有封闭孔隙的材料是不吸水的;具有粗大孔隙的材料因水
分不易存留,其吸水率也不大;而孔隙率较大,且具有细小开口连通孔隙的亲水性材料往往有较大的吸水能力。
9 什么是材料的吸湿性?
吸湿性是材料在空气中吸收水分的性质。材料中水分的多少可用含水率表示,它等于材料吸入水分质量占干燥时质量的百分率。一般地说,开口、孔隙率较大的亲水性材料具有较强的吸
湿性。
材料的含水率为:
式中W含——材料的含水率,%;
m湿——材料含水时的质量,g、kg;
m干——材料干燥时的质量,g、kg。
材料的含水率受环境条件的影响,它随温度和湿度的变化而变化。材料含水后,不但质量增加,而且强度降低,抗冻性变差,有时还会发生明显的体积膨胀,使材料变形。材料中含水对材料的性质往往是不利的。
10 材料的吸水率和孔隙构造是什么关系?
如果材料具有细微而与外界连通的孔隙,则其吸水率较大。若是封闭孔隙,水分不容易渗入。粗大而与外界连通的孔隙水分虽然容易渗入,但仅能润湿孔壁表面,而不易在孔内存留。故封闭或粗大而与外界连通的孔隙材料,其吸水率较低。
11 什么是材料的耐水性?
材料在水的作用下不破坏、其强度也不显著降低的性质称为材料的耐水性。材料含有水分时,由于内部微粒间结合力减弱而强度有所降低,即使致密的材料也会受到影响。若材料中含某些易被水软化的物质(如黏土等),遇水后强度降低就更严重。
材料的耐水性可用软化系数K 表示:
式中K ——材料的软化系数;
f w ——材料在吸水饱和状态下的抗压强度,
MPa;
f ——材料在干燥状态下的抗压强度,MPa。
软化系数的范围在0~1 之间,软化系数小,材料吸水饱和后强度降低多,耐水性差。经常处于潮湿环境中的重要建筑物或部位,必须选用软化系数不低于0.85~0.90 的材料。用于受潮较轻或次要的建筑物,其材料的软化系数也不宜小于0.7~0.85。
12 什么是导热系数?
导热系数(亦称热导率)是指厚度为1m 的材料,当其两侧温度差为1℃时,单位时间内在单位面积上所传递的热量。导热系数可用下式表示:
式中λ——导热系数,W/(m·K);
Q——通过材料的热量,J;
δ——材料的厚度,m;
t1,t2——材料两侧的表面温度,℃,t1>t2;
A——材料的表面积,m2;
τ——热量通过材料的时间,h。
导热系数的单位是:W/(m·K)
符号含义:W——热负荷(瓦特),m——长度(米),K——温度(开尔文)。
导热系数小于0.23W/(m·K)的材料称为绝热材料。
几种材料的导热系数如表1 所示。
表1 几种材料的导热系数表1
可见,水和冰的导热系数分别约为空气的25 倍和100 倍,而冰的导热系数约为水的4 倍。烧结砖、砌块的特点是内部具有较多的孔隙,热量通过材料实体和孔隙两部分进行传递。通过实体的部分是靠固体的传导,而通过孔隙的部分是以辐射和其中介质的传导、对流的复杂方式进行。因此各种材料的导热系数相差很大,而同一种材料还受结构、湿度、温度等因素的影响。
结构对材料的导热系数影响很大,若结构疏松多孔,则孔隙被气体所充满,气体导热系数远较固体为小,从而降低了导热系数。但是必须注意,细小且封闭的孔隙,才不会引起明显的对流作用,而粗大且连通的孔隙,会因介质对流作用增强,反而使材料的导热能力提高。
材料潮湿其导热系数将会提高,这不仅是因为孔隙中水的导热系数比空气导热系数大,而且因为当水分由高温向低温迁移时也要携带热量,因此湿材料的导热系数比干材料和水的导热系数
都要大。例如干实心砖的λ=0.81 W/(m·K),水的λ=0.58
W/(m·K),而湿实心砖的λ=1.0W/(m·K)。在空气相对湿度为80% 时,砖的体积吸水量约为0.5%,导热系数约增加5%。西欧著名的“波罗顿”砖,最先进的导热系数仅为0.08~0.12 W/(m·K)。应该说明的是,由于受成型方法的局限,烧结制品是不匀质的,是各向异性的,这种各向异性表现为多种性能的差异。拿抗压强度来讲,垂直于挤出方向仅为挤出方向的70% 左右。各向异性对其导热系数也产生了一定的影响。
如在烧结多孔(空心)制品中,既有微观的空隙又有宏观的孔洞,比实心制品复杂。为了简化起见,采用了“当量导热系数”这个名词,当量导热系数除考虑孔隙和孔洞类型的影响外,是将热流方向上的材料视作完全匀质的。因为烧结多孔砖或空心砖
的各向异性,在测定其导热系数时,首先测定出平行热流方向的导热系数,再测定出垂直热流方向的导热系数,最后取其平均值作为多孔砖或空心砖的当量导热系数。在计算或测量制品的热阻时,使用的是当量导热系数。
13 什么是热阻?
所谓热阻是将导热系数的公式改写成下式:
由该式可以看出,λ/δ决定了材料在一定的表面温差下,单位时间内通过单位面积热量的大小,于是我们将λ/δ的倒数
δ/λ称为该材料的热阻,用R来表示。
于是热阻:
式中λ——墙体材料的导热系数,W/(m·K);
δ——墙体的厚度,m。
其物理意义是:当墙体两侧的温差为1℃,在1m2 的墙体面积上,传出4.18kJ(1kCal)的热量所需的时间(h),热阻又称热绝缘系数,单位是(m2·K)/W。热阻是墙体保温性能的特征值,是衡量其保温性能的主要指标,是传热阻力的一种体现,热阻越大,传出墙体相同热量所需要的时间就越长,当然保温的效果就越好。
热阻的倒数λ/δ称为传热系数,用符号K 表示,
即:(W/m2·K)。
14 常用的隔热保温材料主要性能有哪些?
常用的隔热保温材料主要性能如表2 所示。
表2 常用的隔热保温材料主要性能
15 什么是材料的热容量?
材料在加热温度升高时吸收热量,冷却温度降低时放出热量。材料温度升高1K 所需的热量或温式中摩尔气体恒量R=8.31J/(mol·K),M 是气体的摩尔质量。只要温度不太低,压强不太大,这个方程对一切气体都适用。若气体的摩尔数为n,克拉珀龙方程还可写成PV=nRT。
24 什么是绝对压力?什么是表压力?
以绝对真空作为零点的压力,称绝对压力。绝对压力= 大气压+ 表压力;或绝对压力= 大气压﹣真空度。
表压力又称相对压力。是以大气压作为零点的压力。通常测压表的零点为大气压力,因此测压表所读得的压力为表压力。当流体的压力大于大气压时,称流体的压力为正压;当压力小于大气压时,称负压或真空度。
25 什么是真空度?
有些真空泵把标准状态的大气压当0MPa,而绝对真空为
-0.1MPa。实际负压值与绝对真空的比值即为真空度,如实际负压值为-0.092MPa,而绝对真空相对于标准状态下的大气压为-0.1MPa,则:
真空度= = = 92%
26 什么是热力学第一定律?
以能量守恒和转换定律为基础的热力学基本定律。它有许多种表达方式,例如:“外界传递给一个物质系统的热量等于系统的内能的增量和系统对外所作功的总和”。“一个系统在一定状态下有一定的能值,如果这个系统的状态发生变化,系统中能量的变化完全由始态和终态决定,与中间过程无关”。应用第一定律可作各种物理、化学变化中能量平衡的计算。
27 什么是热力学第二定律?
是关于热量或内能转变为机械能或电磁能,或者是机械能或电磁能转变为热量或内能的特殊规律。它有许多表述方式,其中之一是:“不可能把热从低温物体传到高温物体而不引起其它变化”。此外还有很多说法,但本质上都是一致的。热不能自发地从低温流向高温,但能自发地从高温流向低温,也就是说自发过程是有方向性的,通过第二定律的研究,可以判断在给定条件下过程进行的方向和限度,即在什么情况下变化到达平衡。
28 什么是稳定传热?什么是不稳定传热?
当物体处于传热过程中,物体内部各点的温度不随时间而变
化,这种传热称稳定传热。此时各点的得热和失热相等。如隧道窑生产时,其窑壁可视为稳定传热。当物体内部各点的温度随时间而变化,这种传热称不稳定传热。此时各点的得热和失热不相等。如隧道窑的窑车和轮窑的窑壁可视为不稳定传热。
29 什么是矿物?
何为矿物?在地壳中由于各种地质作用所形成的天然化合物或单质称之为矿物(mineral),例如石英(是俗称砂子中的主要成分)就是一种固体矿物。它们具有相对固定的内部构造、化学组成和物理性质,在一定物理化学条件下稳定,是组成岩石、矿石和土壤的基本单位。
自然界矿物以三种形态存在:固态、液态和气态。绝大多数为固态,如方解石(CaCO3);其次为液态(如自然汞)和气态(如氦)。目前世界上已知矿物有三千多种,工业上现利用的矿物约二百多种,其中绝大部分为地壳中所有。少数来自其他天体的单质或化合物称为宇宙矿物。由人工合成的矿物称为人造矿物。按照成因条件可分为原生矿物(primary mineral)和次生矿物(secondarymineral)。原生矿物是在内生成条件下,成岩或成矿作用过程中,从岩浆熔融体或热水溶液中结晶或沉淀出来的矿物,如花岗岩中的长石、石英;次生矿物即在原生矿物形成以后,由于经受化学变化而产生的新矿物,如正长石经风化分解所形成的高岭石。次生矿物是相对原生矿物而言。
按其性质又分为金属矿物、非金属矿物、硅酸盐矿物、盐类
矿物等。对烧结砖瓦产品而言,所涉及到的矿物种类较多,其
中最重要的矿物是硅酸盐矿物(silicate mineral)和盐类矿物(saline mineral)。
30 什么是硅酸盐矿物?什么是硅酸盐工业?
硅酸盐矿物是由金属阳离子与硅酸结合形成的矿物。“硅酸盐”按严格的化学概念,是指二氧化硅(SiO2)和金属氧化物(MxOy,M=Na、K、Ca、Mg、Al、Fe 等)所形成的盐类。这类矿物在自然界分布极广,种类在800 种以上,占已知矿物总数的1/4 左右,是构成地壳岩石、土壤和许多物质的主要成分。它是火成岩、变质岩及许多沉积岩的主要造岩矿物,构成地壳总重量的75% 左右。其组成的主要元素有:O、Si、Al、Fe、Ca、Mg、Na、K,有时为Mn、Ti、B、Be、Zr、Li、H、F 等。以这类矿石为主要原材料,经高温处理制成的制品或材料称为硅酸盐制品(silicate products)或硅酸盐材料(silicate materials);制造这类制品或材料的工艺过程称为硅酸盐工艺(ceramicprocess);生产这类制品或材料的工业称为硅酸盐工业(silicate industry)。传统的硅酸盐制品有陶瓷、砖瓦、玻璃、耐火材料、水泥、搪瓷等。在硅酸盐矿物中包括对烧结砖瓦产品生产和性能起决定性作用的黏土矿物(clay mineral)。对烧结砖瓦产品来说,影响最大的盐类矿物是硫酸盐和碳酸盐。
31 什么是pH 值?
用于表示溶液的酸碱度。pH 值一般在0~14之间,pH=7 时是
中性溶液,pH<7 时是酸性溶液,pH>7 时是碱性溶液。pH 值越低,则溶液的酸性越强;pH 值越高,则溶液的碱性越强。用酸碱指示剂可粗略地测定溶液的pH 值,用pH 计可以进行精确测定。
32 什么是矢量?
科学中的测量分为两大类。一类就是简单地测量数量的多少。如某窑的内拱高度为160mm,或顶车机的推力为30t,或某个角是45°。……这些都是“标量”。“标量”仅仅是计数而已。
但有时,只是计数还不够,人们不仅要问有多少,还要问方向如何。例如,顶车机的30t 推力推向何方。换言之,这个推力不是标量,而是“矢量”。“矢量”一词源自拉丁词“携带”的意思。“携带”的含义是:在任何矢量中都隐含着将某物从此处带至彼处的意义。
33 什么是摩尔(mol)?
摩尔(mol)是用来表示物质量的国际制基本单位。1 摩尔的任何物质都是含有6.02×1023 个分子数(等于12g12C 中含有的原子数),这个数叫做阿佛加德罗常数。在标准状态下,1 摩尔的任何气体所占的体积都是22.4L,这个体积叫做气体的摩尔体积。
1 摩尔的硫原子含有6.02×1023 个硫原子,质量是32g;1 摩尔的氧分子含有6.02×1023 个氧分子,质量是32g;1摩尔的氢氧根离子含有6.02×1023个氢氧根离子,质量是17g;1 摩尔
的水分子含有6.02×1023 个水分子,质量是18g,水的摩尔质量为18g。54g 的水是3 个摩尔的水,所以54g 水的摩尔数是3。
摩尔数= 。
但国际制规定的基本单位:质量为kg、长度为m,导出的体积应是m3。因此,物质的质量单位和气体的体积单位都要作换算。可得出:水蒸气的千摩尔质量为18kg,干空气的千摩尔质量为28.96kg,它们的千摩尔在标准状态下的体积都是22.4m3。可算得在标准状态下水蒸气和干空气的体积密度:
ρ水蒸气= =0.8036(kg/m3)
ρ干空气= =1.293(kg/m3)
通过物质的质量、气体在标准状态下的体积,
可以计算出该气体的千摩尔数:
千摩尔数(kmol)=。
34 什么是晶体和非晶体?
晶体是固体的一类。它又分为单晶体和多晶体两种。单晶体具有规则的几何外形,物理性质上具有各向异性,在某一确定的压力下都有一个确定的熔解温度——熔点。多晶体既表现不出外
部的几何特征,在物理性质上也表现不出各向异性,相反在宏观上表现为各向同性。但它和单晶体一样具有晶体的本质特征:具有一定的熔点。
非晶体是固体的另一类。它具有一定得体积和形状,但不具有规则的几何形状、物理性质表现为各向异性,没有一定的熔点。从本质上说,非晶体是粘滞性很大的液体。
35 什么是温室效应?
温室效应就是由于大气中CO2 等气体含量增加,使全球气温升高的现象。
(1)大气中的CO2 有80% 来自人和动、植物的呼吸,20% 来自燃料的燃烧。散布在大气中的CO2有75% 被海洋、湖泊、河流等地面的水及空中降水吸收溶解于水中,还有5% 的CO2 通过植物光合作用,转化为有机物质贮藏起来,这就是多年来CO2占空气成分0.03%(体积分数)始终保持不变的原因。
(2)但近几十年来,由于人口急剧增加,工业迅猛发展,呼吸产生的CO2 及煤炭、石油、天然气燃烧产生的CO2,远远超过了过去的水平。而另一方面,由于对森林的乱砍乱伐、大量农田建成了城市和工厂,破坏了植被,减少了将CO2 转化为有机物的条件。再加上地表水域逐渐缩小,降水量大大降低,减少了吸收溶解CO2 的条件,破坏了CO2 生成与转化的动态平衡,就使大气中的CO2 含量逐渐增加。
3)如果CO2 含量比现在增加一倍,全球气温将升高3~5℃。
两极地区可能升高10℃,气候将明显变暖。气温升高,将导致某些地区雨量增加,某些地区出现干旱,飓风力量增强,出现频率也将提高,自然灾害加剧。更令人担忧的是,由于气温升高,将使两极地区冰川融化,海平面升高,许多沿海城市、岛屿或低洼地区将面临海水上涨的威胁,甚至被海水吞没。
36 什么是弹性形变?什么是塑性形变?
所谓弹性形变是除去外力后能够恢复原状的形变。
物体的形变过大,超过一定限度,这时候即使
除去外力,物体也不能完全恢复原状,这个限度叫
做弹性限度,超过了这个限度,物体发生的形变叫
做塑性形变。
37 什么是放射性?
(1)人们对于原子核运动变化的认识,是从发现某些元素的原子核具有天然放射性开始的。所谓放射性,是某些元素的原子核不断地自发地放射出某种看不见的射线,这种现象叫做天然放射性。天然的放射性元素约50 种。
(2)放射性元素在变化时(称为放射性衰变),从原子核中放出的射线常见的三种:α射线(甲种射线)、β射线(乙种射线)和γ射线(丙种射线)。α射线是带正电的高速粒子,就是氦原子核He,有很强的电离作用,易被物质吸收,穿透本领小;β射线是带负电的高速粒子流,就是电子,电离作用小,穿透本领很大;γ射线是不带电的,是一种电磁辐射,电离作用小,
穿透本领很大。原子核在衰变时,并不是同时放出这三种射线,通常只放出α射线或β射线,而γ射线往往是伴随α射线或β射线同时一起发射的。
(3)放射性原子核的衰变:有α衰变、β衰变和γ衰变等三种不同类型。
(4)放射性强度以I 表示。
(5)把放射性强度I 对时间t 作图,可看到放射性强度随时间而逐渐减小。
(6)λ是个常数,称为衰变系数。它表征着放射性衰减速度的快慢,各个放射性同位素有不同的λ值,λ值是各个放射性同位素的特征常数。λ值不会随着外界条件的变化而改变的。无论是加热、冷却、高压、加磁场以及化学状态的变化等等,都不能改变放射性衰变的速率。
(7)放射出来的粒子数N 的数值会随时间的增长而减少。
(8)放射性核素是随时间按指数比例而衰变,这一关系是对任何放射性核素的衰变都适用的普遍规律,通常称此式为放射性衰变定律。
(9)衰变常数λ数值大的放射性核素衰变得快,小的则衰变得慢。
(10)放射性原子核的数目衰变掉一半所需要的时间称为放射性核素的半衰期。
(11)寿命短的同位素很快就衰变完(几十分钟或几天)。
烧结砖厂生产整个过程及原理
烧结砖厂生产工艺流程及原理 烧结砖生产工艺过程总的来讲有原料的制备、坯体成型、湿坯干燥和成品培烧四部分组成。各部分的重要性总的概括起来说,原料是根本,成型是基础,干燥是保证,焙烧是关键。这四部分是互相依存关系。 页岩→皮带机配内燃料→锤式破碎机破碎→笼筛筛分→双轴搅拌机搅拌→陈化库陈化→双轴搅拌机搅拌(两级)→真空挤砖机挤出成型→切条→切坯→分坯→机械码窑车→回车线自然干燥→隧道窑干燥焙烧→成品出窑→成品堆场。 一、原材料 (一) 原料化学成份 评价某种物料是否能生产出烧结砖,其主要取决于它的物理性能,而化学成份对制品的性能具有间接的影响。在判断原料性能时,化学的成份分析可以作为判断的参考依据。化学分析通常测定二氧化硅、三氧化二铝、三氧化二铁、氧化 (二氧化硅)是烧结砖原料中的主要成份,钙、氧化镁、硫矸和烧失量等。SiO 2 含量在55~70%之间,超过此含量时,原料的塑性大为降低制品的强度极限。Al O3(三氧化二铝)在制品原料中的含量以10~20%为宜,低于10%时制品的2 力学强度降低,高于20%时,虽然制品强度较高,但烧成温度也高,耗煤量加大,并使制品的颜色变淡。Fe2O3(三氧化二铁)是制砖原料中的着色剂,一般含量为3~10%为宜,含量过高时会降低制品的耐火度。CaO(氧化钙)在原料中的石灰石(CaCO3)的形成出现,是一种有害物质,含量不宜超过10%,如含量过高时将缩小烧结温度的范围。当氧化钙含量大于15%时,烧结范围将缩小25℃,给焙烧操作造成困难,其颗粒较大于2mm时更易形成酥砖或引起制品爆裂,可导致坯体严重变形,如吸潮、松解、粉化等。MgO(氧化镁)原料中的含量不超过3%,越少越好,其化合物如硫酸镁在制品中会产生一种白色的泛霜,影响产品的质量。SO3(硫矸)在原料中的含量一般不超过1%,越少越好。硫矸在焙烧过程中的逸出,使制品发生膨胀和产生气泡的原因。其它的含硫物也对制品有害,如硫酸钙引起制品泛白和起霜,硫酸镁能引起制品泛霜和膨胀。 (二)原料物理性能 原料物理性能测试时,通常测定颗粒组成、可塑性、收缩率、干燥敏感性,烧结性等项目名称。 1、颗粒组成:原料的颗粒组成就是不同角度的颗粒在制砖原料中含量的数量化。原料颗粒的组成直接影响制砖的可塑性、收缩率和烧结性等性能影响很大,
煤矸石烧结砖
煤矸石烧结砖 煤矸石烧结砖是以煤矸石为结合剂的烧结砖工艺所生产的建筑材料。 生产工艺 生产工艺的主要环节有:将煤矸石装入料斗经皮带机送至原料加工厂房,经锤式粉碎机粉碎、滚筒筛或振动筛筛选加工成合格物料,然后送入一级搅拌加水后送入化仓进行化。把经过化的物料用皮带机送入二级搅拌及真空制砖机制成砖坯,然后用液压自动码坯机将砖坯码到窑车上送入烘干洞进行烘干,将烘干的砖坯用摆渡车送到隧道窑口后顶入窑烧结而成为成品砖。 制作方法 a.利用锤式破碎机对煤矸石原料进行破碎,然后用滚筒筛进行颗粒筛分处理,使得到的原料颗粒大小在2mm以下,其中2mm-50μm的占25%,50μm-5μm的占55%,小于5μm的占20%,然后所得原料经搅拌机加水搅拌;b.把搅拌好的原料输入化库化;c.经化完的原料输入真空挤出机挤出成型;d.把成型得到的坯体码放入干燥窑中干燥;e.将干燥好的坯体放入焙烧窑中焙烧。本发明由于采用高细破碎和化技术,提高坯料塑性;制坯采用高压真空挤出成型,提高砖坯密实度,优化空心砖的孔型和孔洞排布,进一步提高孔洞率,降低了砖部传热,提高了砖的保温性能。 优点 煤矸石制砖,从耐压、抗折、耐酸以及耐碱性能都高于粘土砖;从建筑用砖的成本方面来看,砌墙及粉刷前不用浇水,可节省用水费及人工费,同时,由于硬度高,产品在运输中的损耗比粘土砖低。 煤矸石烧结多孔砖。煤矸石烧结多孔砖。煤矸石烧结多孔砖。煤矸石烧 性能项目 规格mm 抗压强度MPa 抗折荷重KN 孔洞率% 吸水率% 泛霜实验石灰爆裂试验冻融试验单块% 强度等级当量导热系数w/mk 平均值最小值平均值最小值 190*190*90 22.5 19.2 13.0 10.0 28.8 13 轻微泛霜符合一等品指标<0.4 MU20 λ≤0.55
烧结砖生产工艺流程教案资料
烧结砖生产工艺流程
烧结砖生产工艺流程 煤矸石、页岩、粘土、粉煤灰、江河淤泥、工业尾矿等新型制砖原料经汽车运输至原料场防雨堆存,根据原料的软硬程度及含水率不同,将以上制砖原料公为软质原料和硬质原料。为使生产工艺科学合理。不同制砖原料采用不同的原料破碎处理工艺,以达到最佳的破碎效果。 软质原料由装载机送入箱式给(ji)料机均匀定量配比,经皮带输送机送入齿辊或对辊机粗碎,然后进入对辊机主碎,最后进入细碎对辊机细碎,以达到制砖原料工艺要求。软质原料因质地软、塑性好、含水率偏高,通常采用三道对辊破碎的处理工艺,该破碎方式适用于粘土、软质页岩及泥质煤矸石等原料处理。硬质原料由装载机经颚式破碎机粗碎,进入链板式给料机均匀定量配比,由皮带输送机送入锤式破碎机进行细碎,再进入圆滚筛或振动筛进行筛选,筛下料直接进入下道工序,未达到工艺要求的筛上料再返回锤式破碎机破碎。硬质原料通常采用破碎机加筛选的处理工艺。该破碎方式适用于含水率及塑性偏低、质地较硬的原料处理。根据投资情况和制品要求,也可以采用粗碎加细碎两道对辊机或轮碾机取代筛选工序的方式进行破碎处理,比较先进的生产线大多采取此种方式。无论采用哪一种破碎处理工艺,都要与原料的特性相
吻合,确保工艺设备的科学配套,以达到原料优化处理的目的,使原料在整个破碎处理过程中达到预期的工艺粒度要求。 通过细碎处理后的制砖原料掺配定量的原煤或煤矸石等内燃料进入双轴搅拌机适量加水混合搅拌后,经由皮带输送机送到陈化库的可逆皮带机上均匀对陈化库进行布料,使原料中的水份有足够的时间进行渗透交换,并软化原料,进一步提高原料的均匀性和液塑性等综合性能指标,更利于原料挤出成型,减少设备磨损,降低能耗等。同时陈化库也起着中转储存的作用,将原料处理系统和砖坯成型系统分离,减少挤出机的频繁停机,提高设备工作性能及生产能力,延长设备使用寿命。陈化库环境是个相对封闭的空间,避免了原料与室外空气长时间接触而受气压、气温、风速、湿度等因素的影响失去了原料陈化的作用及目的。经过陈化处理的原料经过多斗挖土机均匀取料经皮带输送机进入箱式给料机均匀定量供料进入下一道工序。陈化库采用可逆皮带机均匀布料、多斗挖土机均匀取料、箱式给料机均匀供料的三均匀工艺,投资合理,机械化程度高,原料的匀化处理好,经陈化后的原料其综合性能指数会得到较大提高,更适用于各种原料烧结制砖的生产需要,保证了产品质量,可根据生产要求灵活处理,为生产各种新型墙材烧结制品创造了必要条件。
烧结砖瓦生产技术问答一样本
答》一书, 详细地介绍了烧结砖瓦的原料采集和制备、坯体成型、坯体干燥、制品焙烧等各工序的生产技术, 并对生产中易出现的问题及其预防、消除的办法作了详细的论述, 对有关基础知识也作了简要介绍, 可供烧结砖瓦厂的技术人员、管理人员及生产人员阅读, 亦可供科研人员、大专院校师生参考。经作者本人同意, 本刊节选其中内容连载, 以飨读者。 烧结砖瓦生产技术问答( 一) 赵镇魁 第一部分基础知识 1 什么是材料的真密度( 密度) ? 真密度( 亦称密度) 是指材料在绝对密实状态 下( 不包括空隙在内) , 单位体积的质量。用下式表 示: 式中ρ——材料的真密度, g/cm3、 kg/m3; m——材料的质量, g、 kg; v——材料在密实状态下的体积, cm3、 m3。 对于不规则的密实材料可用排水体积法求得体积。对于有孔隙的材料, 应把干燥后的材料磨成细粉, 用李氏瓶法测定其实际体积, 进行计算。由于材料磨得越细, 内部孔隙消除得越完全, 越接近绝对密实体积, 测试结果越精确, 一般要求粉末材料的粒径小于0.2mm。 烧结砖的真密度为2400~2800kg/m3。重庆叠叠砖厂生产的煤矸石砖的真密度为2500kg/m3。 2 什么是材料的表观密度( 体积密度) ? 表观密度( 体积密度) 是指材料在自然状态下( 包括空隙在内) , 单位体积的质量, 用下式表示: 式中ρ0——材料的表观密度, g/cm3、 kg/m3; m——材料的质量, g、 kg;
v0——材料在自然状态下的体积, cm3、 m3。 对于烧结砖瓦等有孔隙的材料, 如果是规则形状, 可根据实际测量的尺寸求得自然体积; 如果外形不规则, 可用排液法求得, 为了防止液体由孔隙渗入材料内部而影响测值, 应在材料表面涂蜡。材料内常含有水分, 材料的质量随材料的含水率而改变, 因此表观密度应注明其含水程度。 一般用材料在气干状态下的表观密度, 即干表观密度。材料的表观密度取决于材料的真密度、构造、孔隙率及含水情况。确定材料表观密度时, 应考虑要有较小的导热系数、较高的机械强度和较高的抗震性能等因素。在一般情况下, 材料的表观密度过大, 则气孔率下降, 导热系数增大, 强度提高; 材料的表观密度过小, 虽然固相导热能力下降, 但气孔中空气对流作用会增大传热损失, 最终反而增大导热系数, 同时机械强度会大幅度降低。故应选择一个”最佳表观密度”。”最佳表观密度”一般是用测试方法确定的。 重庆叠叠砖厂生产的普通煤矸石砖的表观密 度为1705kg/m3。 3 什么是材料的堆积密度? 堆积密度是散粒材料( 粉状、颗粒状) 在堆积状 态下单位体积的质量, 用下式表示: 式中ρ′0 ——材料的堆积密度, g/cm3、 kg/m3; m ——材料的质量, g、 kg; v′0 ——材料的堆积体积, cm3、 m3。 材料的堆积体积包括所有颗粒的体积以及颗粒之间的空隙体积, 它取决于材料颗粒的体积密度和堆积疏密程度。材料的含水状态也会影响堆积密度值。 重庆某电厂排出的干粉煤灰堆积密度为 560kg/m3。
砖厂生产工艺技术说明
生产工艺技术说明 生产的产品是煤矸石、黏土烧结多孔砖,利用制成坯体的煤矸石内残留碳的燃烧产生的热量,来供给坯体烧结所需的热量。为了保证生产线产品质量和产量,根据原料性能特点,本项目采用半硬塑挤出成型,一次码烧工艺,机械化自动码坯,隧道式干燥与焙烧,有利于提高了产品的成品率。原料处理采用混合料(煤矸石和页岩)集中处理,经过粗碎、细碎、高频振动筛筛选,筛上料再次细碎,筛下料加水搅拌进入陈化,陈化后的原料经搅拌搅拌挤出后,综合性能得到提高,可生产承重、非承重的空心砖或高档砖。干燥室采用二条内宽4.60m隧道式干燥室,焙烧窑采用二条内宽4.60m隧道窑。制品的干燥、焙烧过程实现微机监控,焙烧产生的余热用风机送进干燥室供坯体干燥脱水。在冬季,同时又可以将热风经换热器把冷水加热后用于取暖。为确保生产高质量的制品和各项工艺性能的可靠,主机及关键设备选用国内最先进的设备,主机选用能适应低塑性原料半硬塑挤出成型的高挤出压力、高真空度的双级真空挤砖机,全自动切条、切坯系统、自动码坯系统、窑车运转系统等。所有风机选型充分考虑即保证生产需要,又考虑节能环保的要求,主要风机加有变频装置。 表3-1 工作制度 序号工段名称年工作日日工作日班工作日备注 1 原料制备240 2 7.5 有效 工作日 2 成型车间240 2 7.5 3 干燥、焙烧240 3 8.0 4 配电240 3 8.0 生产工艺流程 3.3.1 工艺流程图(如下图)
3.3.2 工艺流程说明(1)原料制备
生产中选用煤矸石全部从周边煤矿运来,煤矸石中若含有大块砂岩、石灰石岩等杂质可人工捡出,以确保产品质量。可由装载机将煤矸石装入自卸车中,将煤矸石运到原料棚储存。页岩是委托社会车辆从附近的页岩山运输到厂内原料棚内。然后由装载机将两种原料按一定比例混合均匀并铲运到板式给料机中,板式给料机按工艺要求定量给料到胶带输送机上,输送到复摆型细碎颚式破碎机处进行破碎,破碎后的原料通过刮板给料机、圆盘给料机均匀喂料,再经反击锤式破碎机进行细碎,粉碎后物经过高频振动筛筛选,筛上料再次回到反击锤式破碎机进行细碎,筛下料输送到搅拌机中加水搅拌、混合,达到陈化的需要。 (2)原料陈化处理 混合料经双轴搅拌机加水搅拌处理后,通过胶带输送机运送到陈化库顶部的可逆移动配仓布料机上,将物料按一定班次规律均匀的堆存到陈化库中,物料的陈化时间应不少于3天。陈化的作用是使原料中水分均化程度提高,原料颗粒表面和内部性能更加均匀,更趋一致,颗粒变得容易疏解,物料的成型性能得到提高。 (3)挤出成型 经过陈化的混合料,由液压多斗取料机连续装运到胶带输送机上,运到成型车间的箱式给料机处,定量向双轴搅拌挤出机给料。原料通过再次加水搅拌,其水份控制在16~18%,输送到双级真空挤砖机;挤出成型采用高挤出压力的JKY60/60—40型双级真空挤出机,挤出压力达到4.0MPa,真空度达到≤-0.092MPa。挤出的泥条经自动切条机、自动切坯机切割成需要规格的砖坯,经翻坯机组进行翻坯、编组后,经砖坯输送机输送到机械码坯处,自动化码坯机将砖坯码放到窑车上,以备干燥。(4)干燥、焙烧 干燥与焙烧采用一次码烧工艺。
烧结砖生产工艺流程
烧结砖生产工艺流程 煤矸石、页岩、粘土、粉煤灰、江河淤泥、工业尾矿等新型制砖原料经汽车运输至原料场防雨堆存,根据原料的软硬程度及含水率不同,将以上制砖原料公为软质原料和硬质原料。为使生产工艺科学合理。不同制砖原料采用不同的原料破碎处理工艺,以达到最佳的破碎效果。 软质原料由装载机送入箱式给(ji)料机均匀定量配比,经皮带输送机送入齿辊或对辊机粗碎,然后进入对辊机主碎,最后进入细碎对辊机细碎,以达到制砖原料工艺要求。软质原料因质地软、塑性好、含水率偏高,通常采用三道对辊破碎的处理工艺,该破碎方式适用于粘土、软质页岩及泥质煤矸石等原料处理。硬质原料由装载机经颚式破碎机粗碎,进入链板式给料机均匀定量配比,由皮带输送机送入锤式破碎机进行细碎,再进入圆滚筛或振动筛进行筛选,筛下料直接进入下道工序,未达到工艺要求的筛上料再返回锤式破碎机破碎。硬质原料通常采用破碎机加筛选的处理工艺。该破碎方式适用于含水率及塑性偏低、质地较硬的原料处理。根据投资情况和制品要求,也可以采用粗碎加细碎两道对辊机或轮碾机取代筛选工序的方式进行破碎处理,比较先进的生产线大多采取此种方式。无论采用哪一种破碎处理工艺,都要与原料的特性相吻合,确保工艺设备的科学配套,
以达到原料优化处理的目的,使原料在整个破碎处理过程中达到预期的工艺粒度要求。 通过细碎处理后的制砖原料掺配定量的原煤或煤矸石等内燃料进入双轴搅拌机适量加水混合搅拌后,经由皮带输送机送到陈化库的可逆皮带机上均匀对陈化库进行布料,使原料中的水份有足够的时间进行渗透交换,并软化原料,进一步提高原料的均匀性和液塑性等综合性能指标,更利于原料挤出成型,减少设备磨损,降低能耗等。同时陈化库也起着中转储存的作用,将原料处理系统和砖坯成型系统分离,减少挤出机的频繁停机,提高设备工作性能及生产能力,延长设备使用寿命。陈化库环境是个相对封闭的空间,避免了原料与室外空气长时间接触而受气压、气温、风速、湿度等因素的影响失去了原料陈化的作用及目的。经过陈化处理的原料经过多斗挖土机均匀取料经皮带输送机进入箱式给料机均匀定量供料进入下一道工序。陈化库采用可逆皮带机均匀布料、多斗挖土机均匀取料、箱式给料机均匀供料的三均匀工艺,投资合理,机械化程度高,原料的匀化处理好,经陈化后的原料其综合性能指数会得到较大提高,更适用于各种原料烧结制砖的生产需要,保证了产品质量,可根据生产要求灵活处理,为生产各种新型墙材烧结制品创造了必要条件。 陈化后的原料再次进入辊式细碎机碾练把关,进入双轴
烧结工艺流程
烧结工艺流程 烧结是钢铁生产工艺中的一个重要环节,它是将铁矿粉、粉(无烟煤)和石灰按一定配比混匀。经烧结而成的有足够强度和粒度的烧结矿可作为炼铁的熟料。利用烧结熟料炼铁对于提高高炉利用系数、降低焦比、提高高炉透气性保证高炉运行均有一定意义。 由于烧结技术具体的作用和应用太广泛了, 以下介绍一下烧结生产在钢铁工业粉矿造块的意义和作用 我国的铁矿石大部分都是贫矿,贫矿直接入炉炼铁是很不合算b,因此必须将贫矿进行破碎、选出高品位的精矿后,再将精矿粉造块成为人造富矿才能入高炉冶炼。所以,粉矿造块是充分合理利用贫矿的不可缺少的关控环节。 富矿的开采过程中要产生粉矿,为了满足高炉的粒度要兔在整较过程中也会产生粉矿,粉矿直接入炉会51起高炉不顺。恶化高炉技术经济指标,因此粉矿也必须经过造块才能入炉。 粉矿经过迭决后,可以进一步控制相改善合铁原料的性肠获得气孔串高、还原性好、强度合适、软熔温度较高、成份稳定的优质冶金原料,有助于炉况的稳定和技术经济指标的改
善。粒矿造块过程中,还可以除去部份有害杂质,如硫、氟、砷、锌等,有利于提高生铁的质量。因为人造富矿比天然富矿更具有优越性,成为了现代商炉原料的主要来源。 粉矿迭块还可综合利用含铁、合被、台钙的粉状工业废料,如高炉炉尘、钢迢、轧钢皮、均热炉渣、硫酸渣、染料铁红、电厂烟尘灰笔适当配入可以成为廉价的高炉好原料,又可以减少环境污染,取得良好的经济效益和社会效益。 粉矿造铁是现代高炉冶炼并获得优质高产的基础,对于高炉冶炼有君十分重要的意义,是钢铁工业生产必不可少的重要工序,对钢铁生产的发展起着重要作用。 1.2 粉矿造块的方法 粉矿造块方法很多,主要是烧结矿和球团矿。此外,还有压制方团矿、辊压团矿、蒸养球团t碳酸化球团,其成球方式和固结方法与球团矿不同,还有小球烧结,国外称为HPs球团化挠结矿,界于球团和烧结之间;还有铁焦生产,是炼焦和粉矿造块相结合。 球团矿的焙烧方法主要乞竖队带式焙烷仇链蓖机—回转窃。目前地方小铁厂还有平地堆烷的。 烧结方法主要有吹风烧结法和抽风烧结法两大类。吹风烧结有平地堆挠、饶结识、挠结盘,抽风烧结有路式侥结、艰面步进式烧绍机、带式烧结机、环形挠结机电即日本矢作式)。 国内外苫遍采用的是常式抽风烧结机,在我国地方小铁广还有相当一部分用平地吹风堆烧和箱式抽风烧结。比外,还有回转窑浇结法、悬浮烧结法。 所谓“烧结”就是指粉状物料加热到熔点以下而粘结成固体的现象. 烧结过程简单来说,就是把品位满足要求,但粒度却不满足的精矿与其他辅助原料混合后在烧结机上点火燃烧,重新造块,以满足高炉的要求。点火器就是使混合料在烧结机上燃烧的关键设备,控制好点火器的温度、负压等,混合料才能成为合格的烧结成品矿。 烧结的主要体系是,配料,混料,看火等。看火的经验:看火主要控制的三点温度是;点火温度,终点温度,和总管废气温度。一般来说把终点温度控制在倒数第2号风箱的温度。 铁矿粉造块 铁矿粉造块目前主要有两种方法:烧结法和球团法。两种方法所获得的块矿分别为烧结矿和球团矿。 铁矿粉造块的目的: ◆综合利用资源,扩大炼铁用的原料种类。 ◆去除有害杂质,回收有益元素,保护环境。 ◆改善矿石的冶金性能,适应高炉冶炼对铁矿石的质量要求。 一、铁矿粉烧结生产
烧结作业区工艺流程图
烧结作业区管理流程图 一、管理步骤 来料验收-----卸车储备-----混匀布料、混匀供料-----烧结生产 二、流程图 1、验收 2、储备 3、混匀布料、供料工艺 a、铁料
4、烧结工艺 白灰窑
现作业区以创建“书香型”作业区、全力打造视觉文化为目标,提出“科学管理、管理科学”的全新理念,统筹安排生产工作,坚持纵向贯通、横向协同的管理思路,加强生产协调的核心作用,控制好各生产工序的稳定,服务好其它作业区的保供、做到各工序间的无缝连接,保证产品质量,并与先进行业指标对标挖潜,寻找差距、降低成本、创新工艺、提升产品质量。打造烧结先进的指标,构建和谐顺畅的生产流程,使烧结机利用系数突破1.30 t/㎡·h已达1.482t/㎡·h,年产量163万吨,且各项指标都在接近全国最高指标水平,基本满足高炉正常生产。 先将各流程做一简单的介绍: 1、从PL-2皮带把混匀矿打到配料室1#、2#、3#、4#铁料仓;
2、从白灰窑把-3mm粒级大于85%以上的生石灰通过手动葫芦吊打入配 料室11#生石灰仓; 3、通过PL-6皮带将-3mm粒级大于85%的石灰石打入配料室9#、10#仓; 4、通过PL-3皮带将-3mm粒级在80%-85%的焦粉打入配料室7#、8#仓; 5、按正常配比将混匀矿、焦粉、石灰石、生石灰、烧结返矿通过PL-12、 Z4-1、H-1运输到一次混合机里面,在混合机加水、混匀通过ZL-1皮带运输到制粒机,在制粒机配加蒸汽以提高料温;物料(混合料)在制粒机里面混匀制粒6分钟通过Z5-1、S-1皮带,在通过梭布小车均匀布料到烧结小矿槽。 6、在烧结机上先布一层粒级10-20mm的烧结矿10mm作为底料,混合料 在通过圆辊及六辊布料到烧结机,料层布到650mm,在通过圧料器把料通过点火器点火烧结。 7、混合料在烧结机上烧结50分钟左右,通过单齿辊破碎到环冷机,在环冷 机冷却1个小时左右,通过Z6-1、LS-1在成品筛分室通过振动筛将-5mm烧结返矿通过Z2-1、PL-9、PL-10皮带运输到配料室5#、6#仓内;将10-20mm烧结矿通过Z5-2、Z7-1、S-2皮带打到底料仓;将大于20mm粒级烧结矿通过Z8-1输送到高炉 8、在烧结上料之前先开启机头、机尾电场及主抽风机。
烧结砖防泛碱措施
路面烧结砖防泛碱措施 烧结砖在烧制过程中因工艺等因素,砖中留有一定的孔隙,因而这种砖有一定的吸水率。基层中的可溶性盐随着水分转移到砖的表面,形成我们所说的白霜。防止砖面出现白霜也是一个迫切需要解决的问题。根据我们在全国各地的施工经验,为防止页岩砖出现白霜,我们建议在工程施工时,应该注意以下几个方面: 1、施工中所使用的水泥应使用正规厂家生产的低碱硅酸盐水泥,不应使用非正规厂家生产的矿渣水泥。我们发现,如果使用正规厂家生产的硅酸盐水泥,则砖面就基本不出现白霜,若使用的是矿渣水泥,则砖面的白霜就比较严重。(注:烧结砖本身不含碱,因烧结砖有很好的透气性,所以铺装后期垫层里面水泥灰中的碱会通过砖体返到表面,形成白霜。) 2、施工中使用的水应为河水,不能使用海水。在施工中若使用海水,海水中含有的盐分也将造成砖面上的白霜。施工中使用的砂子应为河砂,避免使用海砂。施工的过程中施工的工人一定要注意砖面的清洁,边铺装边撒细沙覆盖,这样就避免了园林施工过程中水泥灰等在砖体表面形成难以清除的污迹。 3、在烧结砖铺装之前,应尽量早的打好垫层。这样的好处在于铺装之前水泥垫层里面的碱会提前泛出来,这样铺装之后的烧结砖就不会有表面大量泛碱的现象出现。 如果工程上的砖面出现了白霜,目前常用的方法为 1、在烧结砖大面积泛碱后,用潮湿的河沙覆盖于铺装表面,在这个过程中碱会溶于湿沙,把湿沙扫走后碱也就与湿沙一起带走。这样反复几次,水泥灰中的碱基本会清理干净。 2、盐酸清除法。即用2%的盐酸来清除砖表面上的白霜。 3、此外,有机硅防水涂料(水溶性)清除法也是一种行之有效的方法。 有机硅防水涂料是以进口有机硅为主要原料经先进的工艺配制乳化而成。喷涂或涂刷在砖表面后就能渗入砖内数毫米,形成一层肉眼见不到的薄膜,这样,基层中即使有可溶性盐,也无法渗出到砖表面。而且施工方法也十分简单,先清理砖面,然后取有机硅防水涂料一份加6~9份自来水配制,经充分搅拌均匀后用喷雾器或漆刷直接喷刷,一般为两遍,在第一遍固化前再喷第二遍。 关于烧结砖的厚度和尺寸 1、在砖的厚度上,因烧结砖的强度要比水泥砖高很多,在铺装的时候可以考虑用40㎜铺人行步道,50㎜铺车行道及消防通道,60㎜铺重型车道。 2、因烧结砖在1100℃至1200℃高温的环境下烧结而成,所以烧结砖都存在自然地尺寸误差。烧结砖铺装过程中砖与砖应留2㎜左右的缝隙,这样铺装的效果要更理想。 中节能国环新型材料有限公司
砖瓦工业焙烧技术知识问答
砖瓦工业焙烧技术知识问答 1.砖、瓦生产岗位工应具备哪些相关知识和技能? 1. 原料制备生产工 (1)熟悉常用砖瓦原料性能及其技术要求; (2)掌握各种原料、内燃料的配料计算; (3)原料、内燃料制备方法及工艺流程; (4)常用设备的工作原理及操作规程; (5)原料制备工序的清洁生产、安全操作及劳动防护知识。 2. 坯体成型生产工 (1)熟悉成型工艺原理及操作技术规范; (2)掌握成型设备的操作方法; (3)各种空心模具的使用方法; (4)成型缺陷的分析与处理; (5)坯体成型工序的清洁生产、安全操作及劳动防护知识。 3. 坯体干燥生产工 (1)了解干燥原理; (2)常用的干燥方法和干燥制度; (3)会操作、维护干燥设备; (4)干燥缺陷的分析与处理; (5)坯体干燥工序的清洁生产、安全操作及劳动防护知识。 4. 制品焙烧生产工 (1)熟悉焙烧窑炉热工原理; (2)熟悉烧成工艺知识; (3)熟悉窑炉及附属设备的工作原理及操作; (4)知晓热工制度的制定方法; (5)熟悉常用热工仪表的原理及使用; (6)烧成缺陷的分析与处理; (7)制品焙烧工序的清洁生产、安全操作及劳动防护知识。 2.烧结砖瓦属于哪一类材料? 烧结砖瓦属于无机非金属陶瓷材料中的粗陶(或土器),有些(如清水墙装饰砖、陶板等)可归纳为陶瓷材料中的精陶或炻器。 按建筑材料的主要组成成分,可分为无机材料、有机材料和复合材料三大类。具体分类如图所示。 3.烧结砖瓦在陶瓷中的地位如何?
烧结砖瓦在陶瓷中的地位如图所示。 4.什么是烧结砖瓦工艺? 生产烧结砖瓦制品的工艺过程称为烧结砖瓦工艺。应根据砖瓦性能要求和原料特点选择适宜的生产设备并进行合理的工艺布置。 首先是原料处理,包括风化、破碎、粉碎、剔除杂质、粒度分级、配料、干燥和脱水、加水均化、热处理和真空处理、陈化等工序。通常把原料处理过程称为制备。 制备好的原料按既定要求,制成具有规定形状和尺寸的坯体,这一过程是成型。在生产有装饰功能的制品时,在坯体成型的同时,将制品表面施以纹面或涂刷装饰层。 已成型的坯体需经历一个干燥过程,其目的是脱除湿坯的水分,使坯体硬化,以便进入焙烧阶段。对于原料干燥敏感性系数偏高和产品形状较复杂的制品来说,干燥是一个困难的过程,如干燥制度不合理,极易使坯体变形、开裂。干燥过程还是一个消耗能量较多的环节。强化干燥过程,改善干燥工艺,不仅可以提高劳动生产率,而且还能有效地降低能耗。 烧成是生产砖瓦的最后一个也是最重要的一个工艺过程。通过焙烧使坯体变为具有相当强度的、耐久的制品。焙烧需在窑内进行,按焙烧过程中气氛环境的特点,可将它分为氧化气氛焙烧及还原气氛焙烧工艺;按燃料燃烧方式还可分为内燃及外燃焙烧工艺。 生产过程中的各工序产量应平衡,前一工序必须充分满足后一工序的要求,切忌中间有“卡”产量的“瓶颈”现象。 5.如何进行砖瓦原料消耗量计算? 1963年,我国尚未建设大型页岩砖瓦生产线时,就为阿尔巴尼亚沃拉页岩砖瓦厂作了设计方案,虽然这些方案与现代设计有较大差别,但其“工艺计算书”写得较详细,现特摘录其中的“页岩原料消耗量部分”作参考。 1,产品方案 1)产品规格、产量 2)六孔、四孔空心砖详细尺寸图(略)。 2.页岩原料平衡计算 1)工艺参数 (1)工作制度 工作制度如表2所示。 表2 工作制度
烧结生产工艺流程1(20200523204223)
烧结工艺流程 一、我厂烧结机概况: 我厂90M2带式抽风机是有鞍山冶金设计研究总院设计。设计利用系数为 1.57t/m·h。(设备能力为 2.0 t/m·h)作业率90.4%,年产烧结矿224万吨。产品 为冷烧结矿;温度小于120℃;粒度5—150mm;0—5mm粉末含量小于5%; TFe55%;FeO小于10%;碱度2.0倍。配料采用自动重量配料强化制粒烧结工艺。 厚料层烧结、环式鼓风冷却机冷却烧结矿。冷烧结矿经整粒筛分;分出冷返矿及 烧结机铺底料和成品烧结矿。选用了高效主抽风机等节能设备,电器控制及自动 化达到国内同类厂先进水平,采用以PLC为核心的EIC控制系统,构成仪电合一的计算机控制系统。仪表选用性能良好的电动单元组合仪表智能型数字显示仪表 等,对生产过程的参数进行指示;记录;控制;自动调节,对原料成品及能源进 行计量,在环境保护方面采用静电除尘器,排放浓度小于100mg/m3,生产水循环使用,实现全厂污水零排放。采取多项措施对薄弱环节设备采用加强型及便于检 修的设备,关键部位设电动桥式吊车,有储存时间8小时的成品矿槽以提高烧结机作业率,使烧结和高炉生产互不影响。 二、什么叫烧结工艺: 烧结工艺就是按高炉冶炼的要求把准备好的铁矿粉、熔剂、燃料及代用品,按一定比例经配料、混料、加水润滑湿。再制粒、布料点火、 借助风机的作用,使铁矿粉在一定的高温作用下,部分颗粒表面发生软 化和熔化,产生一定的液相,并与其他末熔矿石颗粒作用,冷却后,液相将矿粉颗粒粘成块这个过程为烧结工艺。 三.烧结的方法 按照烧结设备和供风方式的不同烧结方法可分为:1)鼓风烧结如:
烧结锅、平地吹;2)抽风烧结:①连续式如带式烧结机和环式烧结机 等;②间歇式如固定式烧结机有盘式烧结机和箱式烧结机,移动式烧结 机有步进式烧结机;3)在烟气中烧结如回转窑烧结和悬浮烧结。 四.烧结矿的种类: CaO/SiO2小于1为非自熔性烧结矿;碱度为1-1.5是自熔性烧结. 矿碱度为 1.5~2.5是高碱度烧结矿;大于 2.5是超高或熔剂性烧结矿。 五. 烧结的意义 通过烧结可为高炉提供化学成分稳定、粒度均匀、还原性好、冶金性能高的 优质烧结矿,为高炉优质、高产、低耗、长寿创造了良好的条件;可以去除有害杂 质如硫、锌等;可利用工业生产的废弃物,如高炉炉尘、轧钢皮、硫酸渣、钢渣等; 可回收有色金属和稀有稀土金属。 六.烧结工艺流程的组成 (1)含铁原料、燃料和熔剂的接受和贮存;(2)原料、燃料和熔剂的破碎 筛分;(3)烧结料的配料、混合、制粒、布料、点火和烧结;(4)烧结矿的破碎、筛分、冷却和整粒。 七.烧结原料 1.含铁原料主要有磁铁矿、赤铁矿、褐铁矿、菱铁矿,铁矿粉是烧结生产的 主要原料,它的物理化学性质对烧结矿质量的影响最大。要求铁矿粉品位高、成分 稳定、杂质少、脉石成分适于造渣,粒度适宜、精矿水分大于12%时影响配料准确性,不宜混合均匀。粉矿粒度要求控制在8mm以下便于烧结矿质量提高,褐铁矿、菱铁矿的精矿或粉矿烧结时要考虑结晶水、二氧化碳的烧损(一般褐铁矿烧损 9~15%,收缩8%左右,菱铁矿烧损17~36%,收缩10%。) 2.烧结熔剂按其性质可分为碱性熔剂、中性熔剂(Al2O3)和酸性熔剂(石英、蛇绞石等)三类,烧结常用碱性熔剂有石灰石(CaCO3)消石灰(Ca(OH)2)生石灰
烧结砖瓦企业质量管理规程
烧结砖瓦企业质量管理规程 (一九九一年一月十四日国家建筑材料工业发布) 【颁布单位】国家建筑材料工业局 【颁布日期】 19910114 【实施日期】 19911001 一九九一年一月十四日国家建筑材料工业发布 【章名】第一章总则 第一条为推动和加强烧结砖瓦(以下简称砖瓦)企业的质量管理,不断提高砖瓦质量,制定本规程。 第二条本规程适用于所有生产烧结砖瓦的企业。 第三条本规程由国家建筑材料工业局生产管理司和省、自治区、直辖市建材主管部门组织实施。 第四条企业领导和职工要不断强化质量意识,坚持“质量第一,用户至上的宗旨,积极推行全面质量管理,加强生产全过程的质量控制和质量检验,及时排除影响质量的因素,确保原燃材料、半成品、成品符合技术条件要求,出厂产品符合产品标准。 第五条企业要严格执行砖瓦产品国家标准、行业标准、企业标准和《工业产品质量责任条例》。 按照GB/T10300-88《质量管理和质量保证》及本规程的规定,结合企业实际情况,建立健全质量管理机构,制订企业质量管理实施细则和各项责任制,推行方针目标管理并认真组织实施。 第六条企业的产品质量由厂长全面负责。质量管理机构在厂长直接领导下行使质量管理职权。企业职工的收入分配必须体现“质量第一的方针”。把产品质量与职工的荣誉和物质利益结合起来,使质量指标具有否决权。 【章名】第二章质量管理机构人员及职责 第七条砖瓦企业要按其生产规模大小设立专职或兼职质量管理机构,大、中规模(注)企业应设立专职机构,小规模企业应设立专职或兼职机构。专职机构内应设检验室、生产质量控制组、质量管理组等。
检验室要符合《烧结砖瓦企业检验室基本条件》。 兼职机构也要具有必要的检测手段。 注:企业规模暂按年产量划分,设计能力年产砖6000万块或瓦500万片以上为大规模;年产砖3000-6000万专或瓦300-500万片为中规模;年产砖3000万块以下或瓦300万片以下为小规模。空心砖产量折算成普通砖计。 第八条质量管理机构的职责 (一)品质检验对原燃材料、半成品、成品进行检验,及时提供准确可靠的检验数据。 (二)质量管理根据产品标准的要求,制订原燃材料、半成品、成品的技术条件,并按质量管理规程或质量管理实施细则对生产过程的产品质量进行监督和管理,制止影响产品质量的违章行为,应用数理统计等科学方法掌握质量波动规律,不断提高预见性防范和能力。使生产全过程处于受控状态。 (三)产品监督严格按产品标准鉴定出厂产品质量,签发出厂产品质量合格证。防止混等及不合格出厂。 (四)参与制定质量责任制及考核办法,评价各工序的产品质量,为质量奖惩提供依据,行使质量否决议。 (五)及时组织有关部门检查、处理出厂产品不合格等重大质量事故。 (六)有权向上级有关部门反映企业质量情况,企业领导和各级主管部门要支持其行使职权,不得无理干预,更不得借故打击报复,否则追究其责任。 第九条质量管理机构人员配备 (一)质量控制、管理人员的数量不得低于全厂职工总数的1%(不满100人的企业配1名) 检验人员大规模企业不少于5-8名(其中外观质检员2名以上)。 中规模企业不少于3-5名(其中外观质检员2名以上)。 小规模企业不少于2名(其中外观质检员1名),各类规模企业检验人员要相对稳定。
烧结工艺流程图
烧结工艺流程图: 图片: 烧结工艺流程图: 烧结是钢铁生产工艺中的一个重要环节,它是将铁矿粉、粉(无烟煤)和石灰按一定配比混匀。经烧结而成的有足够强度和粒度的烧结矿可作为炼铁的熟料。利用
烧结熟料炼铁对于提高高炉利用系数、降低焦比、提高高炉透气性保证高炉运行均 有一定意义。 由于烧结技术具体的作用和应用太广泛了, 以下介绍一下烧结生产在钢铁工业 粉矿造块的意义和作用 我国的铁矿石大部分都是贫矿,贫矿直接入炉炼铁是很不合算b,因此必须将贫矿进行破碎、选出高品位的精矿后,再将精矿粉造块成为人造富矿才能入高炉冶炼。 所以,粉矿造块是充分合理利用贫矿的不可缺少的关控环节。 富矿的开采过程中要产生粉矿,为了满足高炉的粒度要兔在整较过程中也会产生粉矿,粉矿直接入炉会51起高炉不顺。恶化高炉技术经济指标,因此粉矿也必须经 过造块才能入炉。 粉矿经过迭决后,可以进一步控制相改善合铁原料的性肠获得气孔串高、还原性好、强度合适、软熔温度较高、成份稳定的优质冶金原料,有助于炉况的稳定和技术经济指标的改善。粒矿造块过程中,还可以除去部份有害杂质,如硫、氟、砷、锌等,有利于提高生铁的质量。因为人造富矿比天然富矿更具有优越性,成为了现 代商炉原料的主要来源。 粉矿迭块还可综合利用含铁、合被、台钙的粉状工业废料,如高炉炉尘、钢迢、轧钢皮、均热炉渣、硫酸渣、染料铁红、电厂烟尘灰笔适当配入可以成为廉价的高炉好原料,又可以减少环境污染,取得良好的经济效益和社会效益。 粉矿造铁是现代高炉冶炼并获得优质高产的基础,对于高炉冶炼有君十分重要的意义,是钢铁工业生产必不可少的重要工序,对钢铁生产的发展起着重要作用。
烧结砖生产工艺流程
烧结砖生产工艺流程-标准化文件发布号:(9556-EUATWK-MWUB-WUNN-INNUL-DDQTY-KII
烧结砖生产工艺流程煤矸石、页岩、粘土、粉煤灰、江河淤泥、工业尾矿等新型制砖原料经汽车运输至原料场防雨堆存,根据原料的软硬程度及含水率不同,将以上制砖原料公为软质原料和硬质原料。为使生产工艺科学合理。不同制砖原料采用不同的原料破碎处理工艺,以达到最佳的破碎效果。 软质原料由装载机送入箱式给(ji)料机均匀定量配比,经皮带输送机送入齿辊或对辊机粗碎,然后进入对辊机主碎,最后进入细碎对辊机细碎,以达到制砖原料工艺要求。软质原料因质地软、塑性好、含水率偏高,通常采用三道对辊破碎的处理工艺,该破碎方式适用于粘土、软质页岩及泥质煤矸石等原料处理。硬质原料由装载机经颚式破碎机粗碎,进入链板式给料机均匀定量配比,由皮带输送机送入锤式破碎机进行细碎,再进入圆滚筛或振动筛进行筛选,筛下料直接进入下道工序,未达到工艺要求的筛上料再返回锤式破碎机破碎。硬质原料通常采用破碎机加筛选的处理工艺。该破碎方式适用于含水率及塑性偏低、质地较硬的原料处理。根据投资情况和制品要求,也可以采用粗碎加细碎两道对辊机或轮碾机取代筛选工序的方式进行破碎处理,比较先进的生产线大多采取此种方式。无论采用哪一种破碎处理工艺,都要与原料的特性相
吻合,确保工艺设备的科学配套,以达到原料优化处理的目的,使原料在整个破碎处理过程中达到预期的工艺粒度要求。 通过细碎处理后的制砖原料掺配定量的原煤或煤矸石等内燃料进入双轴搅拌机适量加水混合搅拌后,经由皮带输送机送到陈化库的可逆皮带机上均匀对陈化库进行布料,使原料中的水份有足够的时间进行渗透交换,并软化原料,进一步提高原料的均匀性和液塑性等综合性能指标,更利于原料挤出成型,减少设备磨损,降低能耗等。同时陈化库也起着中转储存的作用,将原料处理系统和砖坯成型系统分离,减少挤出机的频繁停机,提高设备工作性能及生产能力,延长设备使用寿命。陈化库环境是个相对封闭的空间,避免了原料与室外空气长时间接触而受气压、气温、风速、湿度等因素的影响失去了原料陈化的作用及目的。经过陈化处理的原料经过多斗挖土机均匀取料经皮带输送机进入箱式给料机均匀定量供料进入下一道工序。陈化库采用可逆皮带机均匀布料、多斗挖土机均匀取料、箱式给料机均匀供料的三均匀工艺,投资合理,机械化程度高,原料的匀化处理好,经陈化后的原料其综合性能指数会得到较大提高,更适用于各种原料烧结制砖的生产需要,保证了产品质量,可根据生产要求灵活处理,为生产各种新型墙材烧结制品创造了必要条件。
年产3000万块烧结砖(红砖)生产线方案书
年产3000万块烧结砖生产线 计划书 一.设计依据和原则: 1.采用人工干燥烧成工艺,生产不受雨天影响,因此年工作时间按10个月,每月30天,即300天/年计。 2.年产量:250X120X65多孔砖或实心砖3000万块 3.本方案生产原料以软质粘土原料为主,采用燃煤为内燃料,加入量按原料比例加入5-12%(根据发热量确定)即可。 4.为了降低劳动强度和减少劳动人员,在整线方案上采用目前国际上最先进最的一次码烧工艺,挤出湿坯后用自动液压码砖机直接码到隧道窑窑车上,然后在隧道窑内干燥和烧成一次完成。 5. 要求自动化程度较高,劳动强度尽可能低,劳动人员尽量减少,同时还应保证所使用的技术工艺成熟可靠,在上述前提下本着勤俭办厂的原则,优化设计方案,采用投资成本较低,可靠实用的设备。 二.建设条件要求 1.拟建厂址要求: 为了节省工程投资,更有利于企业发展,该项目厂址应选在有丰富的原料,且原料的质量、储量能满足十五年设备折旧年限的生产需求,供电、供水、交通方便的厂址为最佳厂址。 2.原料来源: 原料要进行粉碎、搅拌加水、混匀、碾练,以满足工艺要求。 三.生产工艺流程 1. 工艺流程图 原料开采 ↓ 露天堆放风化→料库贮存雨天备用 ↓ 内燃粉煤渣链式给料机 ↓↓ 配煤机皮带输送机 ↓↓
皮带运输机对辊破碎机皮带运输机 ↓ 皮带运输机 ↓ 滚筒筛筛分筛上粗料 ↓ 筛下细料 ↓ 可逆移动皮带输送机 ↓ 陈化仓陈化 ↓ 多斗挖料机 ↓ 皮带输送机 ↓ 高速细碎对辊机 ↓ 皮带输送机 ↓ 链板式供料机 ↓ 皮带输送机 ↓ 强力搅拌机←加水 ↓ 真空挤出机 ↓
自动切条机切条 ↓ 自动切坯机 ↓ 全自动液压码砖机码窑 ↓ 钢丝绳回车机 ↓ 电动过渡托车 ↓ 液压顶车机 ↓ 入窑干燥烧成 ↓ 成品出窑码垛 ↓ 汽车装运 2.工艺流程说明: ⒈原料的供应及加工: 开采好的原料堆放陈化,再以铲车加入链板式供料机,以皮带输送机送入对辊机破碎,内燃粉煤渣用配煤机通过皮带也与泥料一起送入辊机混合破碎,破碎后经滚筒筛过筛,筛上粗料由皮带机反送回头重复破碎,过筛后的原料再通过皮带运输机送入贮料库备用。 ⒉成型及烧成: 将加工好的原料通过皮带输送机送入真空挤出机(该机挤出压力达到了3.5Mpa,能够保证原料在较高的压力下被挤出成型,使坯体的含水率较低,利于保证坯体的尺寸准确性和湿坯的强度,不至于在机械码坯时使坯体变形) 的上级,再次对原料进行绞练、挤压、切割,使原料颗粒更加密集,水分更加均匀。并在
砖瓦行业现状解决
为什么要转型? 市场环境变化: 建筑市场需求发生了很大变化。 建筑结构有了很大改变: 改革开发前,建筑结构以多层砖混结构为主,需要大量承重墙体材料。 改革开放后,发展了大量的钢筋混凝土高层建筑,如高层纯剪力墙结构、高层框架结构、高层框简结构。这类结构在一、二线城市已占60%、70%,三线城市也超过40%。这些结构都以混凝土为墙体,只有填充墙部分可用其他材料,对材料要求能自承重即可。 广大农村、小城镇、县城等还是以一到六层砖混结构为主。经济发达的沿海地区和多地地震地区,多层框架结构有一定发展。 目前,年轻人外出打工,农村建筑市场在萎缩,新型城镇化在发展。 墙体功能要求增加: 不仅要求有承重维护功能,而且要具备保温、隔热、隔音、降噪、抗震等功能。 墙体材料品种多样化: 墙体材料市场上已不再是烧结砖一统天下了,蒸压加气混凝土、混凝土空心砌块、蒸压砖、石膏砌块、石膏空心条板、陶粒空心板、纸面石膏板、纤维水泥复合板等新型墙体材料在各地拥有不同程度的发展。对烧结砖市场形成严重挑战,挤压了烧结砖市场,在填充领域尤其明显。 生产条件的变化: 原材料来源的变化; 燃料结构的变化; 环境保护指标的提高; 劳动力价格的上升。 中国经济发展进入新常态: 当前对中国经济最严重的挑战是产能严重过剩,而需求萎缩或者不足。在未来若干年内,中国经济发展将处在增长速度换挡期、结构调整阵痛期,前期刺激消化期“三期重叠”的时期。 与烧结砖行业关联度的房地产行业,疯狂膨胀的黄金时期已经过去,现在走到了转折点。供应超过需求、地产疲软、房产量价齐跌。从2014年全国市场表现看,房地产行业境况显不如前。全国商品房销售额全年同比降幅8%,销售价格同比跌5%。未来10年对房地产商来说是残酷的、削泡沫、去库存、挤压过剩产能的时代。 以上情况要求并迫使烧结砖工业调整结构、转型发展。 中国烧结砖工业的结构现状 中国烧结砖工业结构包括: 原材料结构; 产品结构; 生产技术结构; 生产线和企业规模结构; 原材料结构 中国用于烧结砖的原材料有: 农田粘土、荒山荒坡粘土、黄土高原粘土、城市建筑基坑土; 江河湖淤泥;
烧结砖生产工艺过程
烧结砖生产工艺过程 摘要:烧结砖生产工艺过程总的来讲有原料的制备、坯体成型、湿坯干燥和成品培烧四部分组成。制砖原料经采掘之后,有的原料经加水搅拌和碾炼设备处理就可以了,有的原料就不行。如山土、煤矸石和页岩等原料,还要经过破碎和细碎之后再加水搅拌和碾炼才行。原料选择和制备的好坏直接影响到成品砖的质量好坏。所以常言说原料是制烧结砖的根本。这说明原料与原料制备的重要性。 烧结砖生产工艺过程总的来讲有原料的制备、坯体成型、湿坯干燥和成品培烧四部分组成。制砖原料经采掘之后,有的原料经加水搅拌和碾炼设备处理就可以了,有的原料就不行。如山土、煤矸石和页岩等原料,还要经过破碎和细碎之后再加水搅拌和碾炼才行。原料选择和制备的好坏直接影响到成品砖的质量好坏。所以常言说原料是制烧结砖的根本。这说明原料与原料制备的重要性。 选用的制砖原料通过制备处理之后,进入成型车间进行成型。我国的绕结砖的坯体成型方法基本上都采用塑挤出成型。塑挤出成型又有三种方法。即塑性挤出成型;半硬塑挤出成型和硬塑挤出成型。 这三种挤出成型方法是依据成型含水率的不同来区分的。当湿坯成型含水率大于16%(干基以下均为干基)时,为塑性挤出成型。当湿坯成型含水率为14-16%时为半硬塑挤出成型。当湿坯成型含水率为12-14%时为硬塑挤出成型。坯体成型包括:原料进入成型车间未进入挤出成型砖机之前的供料、搅拌、加水与碾炼设备处理部分;经过成型砖机之后,成型出合格的泥条与湿坯部分。成型要做到制品的外形与结构,就是构成制品的形状与结构。因此常说成型是基础。也就是说要求的制品外部形状与结构是经过成型塑造出来的。即成型是制砖工艺中基础的含义。因为成型出来的坯体质量好坏与成品砖外观质量好坏有着直接关系。 当成型车间成型出来湿坯之后,这种湿坯要进行脱水干燥。在烧结砖生产工艺中湿坯干燥有自然干燥和人工干燥室干燥两种方式。湿坯采用自然干燥是将湿坯运码放在自然干燥场地的坯埂上成垛,并人工进行倒码花架,利用大气进行自然干燥。使湿坯凉晒成干坯。 湿坯采用人工干燥,是设有人工干燥室进行湿坯干燥。人工干燥室又分为大断面隧道式干燥室和小断面隧道式干燥室及室式干燥室三种形式进行人工干燥湿坯。这三种干燥形式不管采用哪一种都是人工或机械将湿坯码放在干燥车上成垛。这时将码成湿坯垛的干燥车进入干燥室进行干燥湿坯。干燥室的热介质一般来自烧结窑的余热或热风炉。湿坯干燥不管采用哪种干燥方式和哪一种人工干燥形式,都必须遵循在干燥过程中保证坯体不变形,不干裂。如果湿坯在干燥中出了问题不能保证制品的外观质量,废品率高,产量下降,成品砖的成本增大,企业经济效益就自然不好,所以,常称坯体干燥是保证。这说明湿坯干燥在制砖工艺过程中的重要性。 湿坯在干燥之后,残余含水率小于6%的情况下,就将坯体进入焙烧窑中烧成。焙烧用的窑型普遍采用轮窑和隧道窑。采用轮窑焙烧时由人工将砖坯码放在窑道里成垛。火在窑道里运行进行焙烧。采用隧道窑焙烧时由人工或机械将砖坯码放在窑车上成垛。码好砖坯垛的窑车从隧道窑窑头进入由窑尾出来窑车上的砖坯被焙烧成砖。窑里的焙烧火焰不运行,而是窑车载着坯垛又被焙烧砖垛