压铸模设计规范
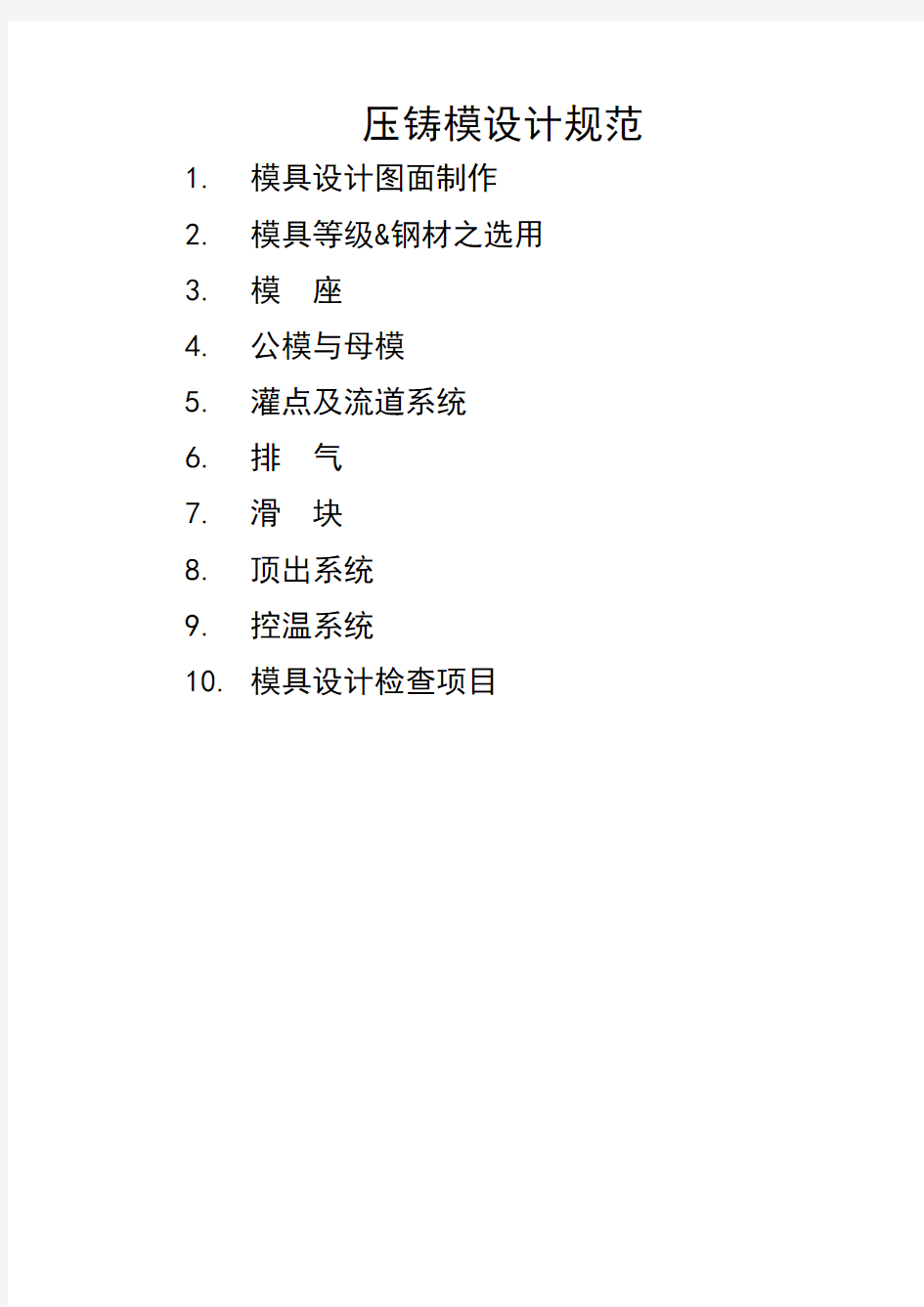

压铸模设计规范
1.模具设计图面制作
2.模具等级&钢材之选用
3.模座
4.公模与母模
5.灌点及流道系统
6.排气
7.滑块
8.顶出系统
9.控温系统
10.模具设计检查项目
模具设计图面制作
1.所有模具组立图需能完整表示出模具结构, 其图面应含一公,母模平面图, 纵向与
横向剖视图, 和其他足以清楚表示模具结构之详细及剖视图.
2.每张图面需有图框, 右下角要有标签栏.
3.每张模具组立图需有材料栏, 其内容应含零件名称, 材料尺寸, 硬度, 零件在图面
的编号及所需之数量.
4.标示出所有模板, 镶块尺寸及模座的长, 宽, 高.
5.标示”天侧”(TOP OF MOLD)于模具天侧及”基”(OFFSET)于偏移之导柱.
6.画出完整之水路于平面及剖视图上, 至少标示一个不同水路的尺寸及水管接头,并
标示”IN”,”OUT”及编号于水路进出侧. 水管应制成沉头型式.
7.每个进料点需以详图标示.
8.为易于辩认各零部件, 可使用下列代号:
(1) GB---导套 (2) GP---导柱 (3) RP---回位销
(4) ST---停止销 (5) SP---支撑柱
9.标示锁模块, 吊模孔位置与尺寸.
10. 标示主流道及分流道尺寸.
模具等级&钢材之选用
模具等级
1.CLASS A
1.1 要求寿命: 100万模次
说明: 用于要求快速生产或非常高之生产量, 产品尺寸要求严格, 模具以最高品质之钢材制造而成. 模具费用高昂.
钢材:
A)模座: RAMAX 不锈钢材料, HRC34~38°.
B)模仁: ELMAX, STAVAX或CORAX不锈钢材料,需热处理至HRC54°以上.
C)滑动件: 须与模仁不同材料(整面滑块可使用与模仁相同的钢材),硬度相差4°以
上,并作氮化处理. 耐磨块,压块须与滑块不同材料, 可与模仁材料相同. 所有滑动件必须开油沟.
D)附要求: 钢材于EDM加工或焊补后, 需再行热处理以消除应力及与始钢材硬度均
一.
2.CLASS B
2.1 要求寿命: 50万模次
说明: 用于中高产量, 及精密的公差要求. 这是高品质,高价格的模具.
2.3 钢材:
A)模座: P-20或AISI-4130, 硬度为HRC28~32°.
B)模仁: SKD61, S136. 硬度为HRC50°以上.
C)滑动件: TDAC,NAK80,DH2F或H-13, 热处理+氮化处理, 硬度为HRC48~52°, 需使
用耐磨块时,材质为SK3-SK5(HRC52~56°), 所有滑动件必须开油沟. 整面滑块可
使用与模仁相同的钢材.
D)附要求: 钢材于焊补后, 需再行热处理以消除应力及与始钢材硬度均一.
3.CLASS C
3.1 要求寿命: 30万模次
3.2 说明: 用于中低产量.
3.3 钢材:
A)模座: S50C或S55C, 硬度为HRB85~90°.
B)模仁: NAK80, TDAC, P20. 硬度为HRC38~42°.
C)滑动件:所有滑动件必须开油沟. 整体滑块可使用与模仁相同的钢材.
模座
1.模板需加装4支导柱及导套, 超过
2.5吨的模具加装黄油嘴.
2.支撑柱使用螺丝固定于公模板, 其数量及位置需足以抵挡射出压力而不致造成公模
板变形, 尤其灌嘴附近.
3.导柱直径在合理范围内尽可能加大并且长度至少为模座厚度约减5mm.
4.导柱伸出模座部分不可超出总长的3/4.
5.当需要微动开关控制模具动作顺序, 以保护模具时, 必须确实将其安装妥当.
6.导套底部要有良好之排气槽.
8.模板之间连接至少需要3~4个沉头螺丝, 并且超过50磅的结合力.
9.每块模板四周边缘需加上C2倒角.
10.模具装置有油压缸, 冷却水路接头, 电子接头等时, 如妨碍模具安置则需有垫脚,
以确保模具正确放置方向.
11.开模行程必须容许成品可落下及机械手臂操作.
12.模脚于操作员侧面, 必须加工模具标签凹槽, 以便装置财产标签.
13.模具无论大小组, 公母模分模面处制作锁模块(1~4个), 以防止模具吊运过程中模
具开启.
14.锁模槽直接开在母模板和模脚上. 模具大小必须符合相应机台规格.
公模与母模
4.公模仁与母模仁须刻字表示出基准边.
5.公母模仁硬度必须高于HRC50, 易断裂的局部或较厚除外.
7.模仁尽可能不分割镶块, 以防止毛边过多.但一些RIB较深/较多的可以考虑加.
8.公母模仁固定螺丝至少需有50磅的结合力. 螺丝从反向固定.
9.所有拔模方向的产品侧壁均需加拔模角, 母模方向大于公模方向0.5~2°, 所有拔
模均需减肉加铁, 以便后续修模.
10.模具不可含有斜顶出结构, 对倒勾部分可另外加工. 可以含有滑块结构.
11.公模仁分模面处比模座表面高0.5mm, 母模仁分模面处与模座表面相平.
12.所有靠破面侧壁需有至少5°拔模角度.
13.公母模仁精加工前要测试硬度是否符合要求.
14.最后抛光方向须与脱模方向相同, 公模表面粗糙度比母模表面粗糙度至少低一级,
以便成品不黏母模.
15.BOSS孔底部可做成圆入子, 入子尺寸取整数遵循内大外小的原则. 入子与模仁间
隙不超过0.013~0.025mm.
16.重量超过20Kg的模仁要做至少2个工艺螺丝孔, 模仁四周倒C2角, 以便加工搬运.
17.产品肉厚尽可能均匀. 产品肉厚比超过1.2时, 不可直角转折, 须用R,角度或曲面
过渡, 以利淌流.产品肉厚比超过2.0时, 一般要做偷肉, 以防产生消水现象.
18.BOSS长径比一般不超过8. 长径比超过4时, 为便于充填, 开口周围倒0.3~0.5 C
角或R角.
19.RIB,定位柱肉厚一般不低于过0.5mm, 长径比一般不超过15, 长径比超过5时, 开
口周围倒0.1~0.3 C角或R角. 长径比=B/A或D/C
20.对于公母模相靠破部分, 为防止公母模错位, 公模部分单边可偷肉加铁0.05~
0.15mm.
灌点及流道系统
1.流道设计不可有直角转弯现象, 应以圆弧改变方向.
2.流道大小, 以成品重量,进料点数量及流道长度为考量依据.
3.流道断面形状采用梯形结构,宽厚比一般为3:1~1,底部倒R1~3,侧面单边做5~10°,
以利脱模. 灌口、分流子的斜度根据成品重量, 流道大小而定, 一般为5~10°.
4.流道系统以流动平衡为优先考量. 对于一些肉厚较大, 靠破,形状较多等不易充
填的部分, 须增加GATE或流道尺寸. 对于侧面进料的产品, 如中间有靠破部分,须采用搭接促进淌流, 并选在易于充填产品的地方.
5.流道,灌点尺寸位置需经由模流分析决定, 当无模流分析时, 由小尺寸做起. 模具
图面需有进料点放大图, 并详细标示尺寸.
6.流道末端, GATE对面, 大的靠破处及模流分析不易填饱的部分尽可能增加冷料井,
冷料井要有1~3mm的缓冲区. 冷料井有半圆形和梯形的形状.
7.進料點應選在有利於沖填、流程較短、不會對型芯產生直接沖擊的地方。
排气
1.气槽一般开在公模上, 而不开在母模. 气槽的深度在0.05~0.15mm.
2.流道的转折,尾端处, 冷料井处, 靠破处, 模流分析不易填饱的部分均需开气槽.
气槽不宜开在冷料井的中间处, 以防出现噴射或堵塞气槽的情况, 一般开在侧边.
3.BOSS部分如可能可加圆PIN增加排气.
滑块
1.滑块所用材质一般与模仁不同, 硬度相差4°左右. 耐磨块, 导块材质需与滑块不
同. 滑块, 耐磨块要开油沟. 滑块如允许尽可能加导块, 以定位和滑动.
2.滑块行程 = 成品脱出 + 3~5mm. 回位弹簧的数量及型号根据滑块的大小与行程而
定.
3.斜撑柱的直径,长度根据滑块的大小与行程而定, 一般选用标准规格. 其角度选在
10~25°,但一般不超过22°.斜撑柱的材料可选用SKD61或SUJ-2, 表面热处理.
4.滑块上一般不开流道, 如确实要开, 须用油压缸控制其开模顺序. 其它需要控
制开模顺序的滑块结构也需用油压缸. 油压缸要確實安装妥当.
5.滑块上成品部分較大時,須開气槽。
顶出系统
1.至少需要2個機械頂出螺絲孔,頂出螺絲孔位置根據機台規格而定。
2.需安裝停止塊,以限制頂出行程超出實際必要行程。
3.支撐柱須比模腳高0.05~0.15mm,回位銷比分型面低0.02~0.05mm。
4.頂針須先排在脫模困難的地方,比如BOSS,RIB,較深的產品等處。頂針排置時要考
量頂出平衡。如水路排布干涉時,可將頂針適當移動。冷料井處須加頂針,如用頂針兼做冷料井時,其深度為1~1.5D。頂針的排布須足夠超過成品的包模力。
5.頂針直徑一般規格有1、1.5、2、2.5、3、3.5、4、4.5、5、6、7、8、10、12、14、
16等標准。根據產品面積盡可能排大尺寸的、標准規格的頂針,一般不小於3mm。
如頂針直徑小於2mm,須做成雙節形式。
6.用作頂料道,冷料井的頂針長度可比產品低並取整數外,其它頂產品的頂針要比產
品高0.03~0.10mm。如果頂針上有靠破部分,其長度與產品等高。
7.頂針端部如有形狀,其靠肩需做防呆。對於面積較大,表面平整的產品,如PANEL
BEZEL,为防止頂出時產品變形,四周頂針端部需做台階形狀,其深度一般為
0.2~0.5mm。
8.模板處的頂針孔須做偷肉。頂針直徑小於3mm的,偷肉0.5mm;直徑大於3mm的,
偷肉1mm。頂針與模仁滑配部分長度一般在20mm左右,超出部分做偷肉,滑配部分的間隙為0.02~0.03mm。頂針孔的最薄壁不得小於0.6mm。
控温系统
1.模具壓铸前,須先预熱以消除應力。预熱溫度镁鋁合金一般為230~280℃。
2.模具冷卻方式有直接冷卻(如水、油管冷卻)、間接冷卻(如銅棒冷卻)。一般采用直
接冷卻的方式,水管的排布方式有循環式和平行式,平行式要比循環式冷卻效果好,其進出溫差較小。對於一些較小的產品可以采用循環式,而大的產品則選擇平行式好些。
3.水管直徑一般在6~10mm間,水管牙为PT1/4。水路至側壁或產品面的最小距离為4mm。
距產品面的最大距离不超過2D(水管直徑)。產品肉較厚,灌口附近要排水路。灌口,分流子處的冷卻水管長度排至比頂面低5mm。
4.大的滑块或大的鑲截塊上須加冷卻系統。如果產生干涉,可采用雙層冷卻。
模具设计检查项目
压铸件设计规范
?压铸件设计规范 ?一、壁厚 压铸件的壁厚对铸件质量有很大的影响。以铝合金为例,薄壁比厚壁具有更高的强度和良好的致密性。因此,在保证铸件有足够的强度和刚性的条件下,应尽可能减少其壁厚,并保持壁厚均匀一致。 铸件壁太薄时,使金属熔接不好,影响铸件的强度,同时给成型带来困难;壁厚过大或严重不均匀则易产生缩瘪及裂纹。随着壁厚的增加,铸件内部气孔、缩松等缺陷也随之增多,同样降低铸件的强度。 压铸件的壁厚一般以2.5~4mm为宜,壁厚超过6mm的零件不宜采用压铸。 推荐采用的最小壁厚和正常壁厚见表1。 表1 压铸件的最小壁厚和正常壁厚 我司现使用的绝大多数为铝压铸件,其壁厚一般控制在2.0~2.5mm。 二、铸造圆角和脱模斜度 1)铸造圆角 压铸件各部分相交应有圆角(分型面处除外),使金属填充时流动平稳,气体容易排出,并可避免因锐角而产生裂纹。对于需要进行电镀和涂饰的压铸件,圆角可以均匀镀层,防止尖角处涂料堆积。 压铸件的圆角半径R一般不宜小于1mm,最小圆角半径为0.5 mm,见表2。 铸造圆角半径的计算见表3。
表2 压铸件的最小圆角半径(mm) 我司现采用的圆角一般取R1.5。 表3 铸造圆角半径的计算(mm) 说明:①、对锌合金铸件,K=1/4;对铝、镁、合金铸件,K=1/2。 ②、计算后的最小圆角应符合表2的要求。 2) 脱模斜度 设计压铸件时,就应在结构上留有结构斜度,无结构斜度时,在需要之处,必须有脱模的工艺斜度。斜度的方向,必须与铸件的脱模方向一致。推荐的脱模斜度见表4。
表4 脱模斜度 说明:①、由此斜度而引起的铸件尺寸偏差,不计入尺寸公差值内。 ②、表中数值仅适用型腔深度或型芯高度≤50mm,表面粗糙度在Ra0.1,大端与小端尺寸的单面差的最小值为0.03mm。当深度或高度>50mm,或表面粗糙度超过Ra0.1时,则脱模斜度可适当增加。 我司现采用的脱模斜度一般取1.5°。 一般采用的加强筋的尺寸按图1选取: t1=2 t /3~t;t2=3 t /4~t; R≥t/2~t; h≤5t;r≤0.5mm (t—压铸件壁厚,最大不超过6~8mm)。 四、铸孔和孔到边缘的最小距离 1)铸孔 压铸件的孔径和孔深,对要求不高的孔可以直接压出,按表5。 表5 最小孔径和最大孔深
铸件标准
JB/ZQ4000.7-86 JB/ZQ4000.5-86 JB/ZQ400.3-86 JB/ZQ4000.2-86 JB/ZQ4000.7-86 JB/ZQ4000.5-86 JB/ZQ400.3-86 JB/ZQ4000.2-86 1、锻件通用技术要求(JB/ZQ4000.7-86) 2、铸件通用技术要求(JB/ZQ4000.5-86) 3、焊接件通用技术要求(JB/ZQ400.3-86) 4、涂装通用技术条件(JB/ZQ4000.10-88) 5、切削加工件通用技术要求(JB/ZQ4000.2-86) 1、锻件通用技术要求(JB/ZQ4000.7-86) 1.锻件上不应有白点,根据图样、工艺文件或订货技术要求的规定进行白点检查, 当发现有白点时,该批所 有锻件必须经单个检查后,确定是否合格. 2.锻件的力学性能试验,按图样、工艺文件或订货技术要求的规定可在纵向、切向和横向的试样上进行,试 验的结果应符合JB/ZQ4287-86 (优质碳素结构钢)和JB/ZQ4288-86(合金结构钢)的规定. 3.锻件根据其用途和工作条件,按试验种类分为: Ⅰ、Ⅱ、Ⅲ、Ⅳ和Ⅴ五组.每组锻件除Ⅰ组外,其必要的试验范围按下表规定.设计部门或订货单位对锻件 力学性能有要求时,必须在图样或订货技术要求中注明.若未注明,则按Ⅰ组锻件处理. 一、锻件组别:Ⅰ 1.组别的基本标志 1)检验特性: 不试验. 2)组成批的条件: 同一钢号的锻件. 二、锻件组别:Ⅱ 1.组别的基本标志 1)检验特性: 测定每批中锻件的硬度. 2)组成批的条件: 根据同一规范进行热处理的同一钢号的锻件. 2.验收时的必要力学性能指标: HB 3.试验方法 1)力学性能: - 2)硬度: 每批中试验5%,但不少于5件.
铸造、压铸标准
铸造、压铸标准 技术标准是国际贸易中的准则,是作为设计、制造、验收产品的依据。广东省铸造学会、广东省压铸学会收录了部分标准:铸造和压铸的中国国家标准、行业标准,以及美、欧、日、澳、德、俄等国家的相应标准。 压铸标准包括:(一)通用标准;(二)压铸机标准;(三)压铸模标准;(四)合金及工艺标准,包括铝合金、镁合金、锌合金、铜合金、铅锡合金等。 铸造标准包括:(一)基础通用与铸造工艺技术标准;(二)铸钢标准;(三)铸铁标准;(四)铸造有色合金标准;(五)造型材料标准;(六)熔模铸造标准等。 压铸标准目录 一、通用标准 中国GB/T24001-1996 idt ISO 14001:1996 环境管理体系规范及使用指南GB/T19001-2000 idt ISO/FDIS9001:2000 质量管理体系––要求 GB/T5611-1998铸造术语 HB7578-1997铸件试制定型规范 GB/T8063-94 铸造有色金属及其合金牌号表示方法 GB/T13822-92 压铸有色合金试样 GB5678-85 铸造合金光谱分析取样方法 HB5343-94 铸造工艺质量控制 GB/T6414-1999 铸件尺寸公差及机械加工余量 GB/T15056-94 铸造表面粗糙度评定方法 二、压铸机标准 中国JB/T8083-1999 压铸机型式与基本参数 JB/T8084.1-1999 冷室压铸机精度 JB/T8084.2-1999 冷室压铸机技术条件 JB/T6039.2-92 热室压铸机精度 JB/T6039.3-92 热室压铸机技术条件 三、压铸模标准 中国GB8844-88 压铸模技术条件 GB8847-88 压力铸造模具术语 GB4678.1~15-84 压铸模零件
压铸件结构设计规范
压铸件结构设计 压铸件结构设计是压铸工作的第一步。设计的合理性和工艺适应性将会影响到后续工作的顺利进行,如分型面选择、内浇口开设、推出机构布置、模具结构及制造难易、合金凝固收缩规律、铸件精度保证、缺陷的种类等,都会以压铸件本身工艺性的优劣为前提。 1、压铸件零件设计的注意事项 ⑴、压铸件的设计涉及四个方面的内容: a、即压力铸造对零件形状结构的要求; b、压铸件的工艺性能; c、压铸件的尺寸精度及表面要求; d、压铸件分型面的确定;压铸件的零件设计是压铸生产技术中的重要部分,设计时必须考虑以下问题:模具分型面的选择、浇口的开设、顶杆位置的选择、铸件的收缩、铸件的尺寸精度保证、铸件内部缺陷的防范、铸孔的有关要求、收缩变形的有关要求以及加工余量的大小等方面; ⑵、压铸件的设计原则是: a、正确选择压铸件的材料; b、合理确定压铸件的尺寸精度; c、尽量使壁厚分布均匀; d、各转角处增加工艺园角,避免尖角。 ⑶、压铸件分类按使用要求可分为两大类,一类承受较大载荷的零件或有较高相对运动速度的零件,检查的项目有尺寸、表面质量、化学成分、力学性能(抗拉强度、伸长率、硬度);另一类为其它零件,检查的项目有尺寸、表面质量及化学成分。 在设计压铸件时,还应该注意零件应满足压铸的工艺要求。压铸的工艺性从分型面的位置、顶面推杆的位置、铸孔的有关要求、收缩变形的有关要求以及加工余量的大小等方面考虑。合理确定压铸面的分型面,不但能简化压铸型的结构,还能保证铸件的质量。 ⑷、压铸件结构的工艺性: 1)尽量消除铸件内部侧凹,使模具结构简单。 2)尽量使铸件壁厚均匀,可利用筋减少壁厚,减少铸件气孔、缩孔、变形等缺陷。 3)尽量消除铸件上深孔、深腔。因为细小型芯易弯曲、折断,深腔处充填和排气不良。 4)设计的铸件要便于脱模、抽芯。 5)肉厚的均一性是必要的。 6)避免尖角。 7)注意拔模角度。 8)注意产品之公差标注。 9)太厚太薄皆不宜。 10)避免死角倒角(能少则少)。 11)考虑后加工的难易度。 12)尽量减少产品内空洞。 13)避免有半岛式的局部太弱的形状。 14)太长的成形孔,或太长的成形柱皆不宜。 2、压铸件零件设计 ⑴、压铸件的形状结构 a、消除内部侧凹; b、避免或减少抽芯部位; c、避免型芯交叉;合理的压铸件结构不仅能简化压铸型的结构,降低制造成本,同时也改善铸件质量。 ⑵、壁厚 压铸件的壁厚对铸件质量有很大的影响。以铝合金为例,薄壁比厚壁具有更高的强度和良好的致密性。因此,在保证铸件有足够的强度和刚性的条件下,应尽可能减少其壁厚,并保持壁厚均匀一致。 铸件壁太薄时,使金属熔接不好,影响铸件的强度,同时给成型带来困难;壁厚过大或严重不均匀则易产生缩瘪及裂纹。随着壁厚的增加,铸件内部气孔、缩松等缺陷也随之增多,同样降低铸件的强度。 压铸件的壁厚一般以2.5 ~4mm为宜,壁厚超过6mm的零件不宜采用压铸。推荐采用的最小壁厚和正常壁厚见表1。
压铸件技术要求
压铸件技术要求 平面图上的未注尺寸按3D图做出。 1.0机械特性: 1.1本图上未标注的线性尺寸公差按下表(见图上的表格内的尺寸范围及选用公差),下表未 涵盖之处见标准NADCA S-4-1/2/3-94。 1.2中心线的误差为±0.12。 1.3除另有规定外,拔模斜度按1.5°±20′,壁厚小于1.5mm的侧壁的出模斜度见标准 NADCA S-4-4-94。 1.4图上显示为锐角的地方的倒角(包括倒直角、倒圆角)必须小于0.25mm。 1.5标识为“REF”的尺寸仅供参考。 1.6图上尺寸为喷涂、电镀前的尺寸。 2.0喷涂要求(不需喷涂的产品不适用) 2.1对指定的表面喷油,纹理结构(撒点处理)按客户的样板。 2.2 所有螺纹孔不可进油。 2.3 涂层厚度要符合规格要求。 2.4 对于有明确规定的要进行两次喷涂的表面上的螺纹孔必须用夹具保护住。 颜色:RAL 7012 纹理结构:精细的鹅卵石状(撒点处理) 3.0模具方面的要求 3.1在正式的模具设计之前,模具的水口及顶针位置必须与客户的机械工程部讨论决定,要 提供完整的模具图以备批复。 3.2模具至少要啤10万模次,所有表面抛光。 3.3新模及改模后要交样板(附全尺寸报告)给客户机械工程部批复。所有零件必须经得书面 批复后方可批量生产。 3.4如模具有多个模穴,则每模穴的样板都要经批复。 3.5内浇口残留量小于0.15mm。 3.6顶针痕凸起0.15mm以下,凹下0.4以下。 3.70.12mm以下可接受。 3.8 表示分模线。 3.9以下。 3.10在模上制作包含年、月的日期编码,日期编码外圆直径在8.0mm以下。 3.11若有需要,客户商标及模穴标记(多模穴的模具)必须铸出,字体清晰可见,字高3.5mm, 深0.2mm,字不可凸起于产品表面。 3.12模具及模具设计文件(包括图纸)归客户所有,虽然由供应商保养,但客户在有需要时, 可随时取回。 4.0品质控制及外观标准 4.1此产品为外观件,所有曲线及倒圆角处必须平滑过渡。 4.2外部(可视)表面不可有缩水、粘模、气孔、划伤及其它污渍。 4.3零件必须除净毛刺,不可有锐角及其它问题。 4.4标有“CPK”的尺寸为重要的设计参数,供应商要随机抽取5个计算CPK,CPK≥1.5 为合格。若不能满足,另外随机抽25个(总共30个)测验以确保CPK测定结果的有效性。每次交货时要提供打印好的CPK报告给客户的机械工程部。 4.5在零件上不可有供应商的商标及其它标识。 5.0包装要求 每件零件分开包装,避免搬运及运输过程中损坏。
铸件打磨工艺要求规定
三相异步电动机 铸件打磨工艺要求规定 文件编号:050000028 版本编号:第一版 设计: ___________________ 审核: ___________________ 会签: ___________________ 标准: ___________________ 审定: ___________________
无锡中达电机有限公司 2013年6月
无锡童氏电机有限公司铸件打磨工艺要求规定 编制部门 标记处数更改文件号签字日期工艺科 、适用范围 本规定适用于铸铁件外观质量的打磨处理,同时适用于焊接件外观质量的打磨处理。 、目的 为有效提升电机铸件的外观质量,确保外观质量满足客户要求,降低因外观质量而 引起客户的投诉。 三、设备、工具及材料 1、阔、窄錾子 2、地控行车5T以上 3、百叶轮、砂轮片、 4、手提式模具电磨、角向砂轮机 5、圆锥磨头 6 2.5磅铁手锤 四、劳保用品穿戴及安全要求 1、劳保用品穿戴 操作员工必须正确穿戴工作服、防护眼镜、口罩、安全帽、手套、工作鞋等以确保在打磨过程中的安全。 2、安全要求 2.1根据铸件的规格型号不同及打磨部位不同等来选用和使用合理的砂轮机、砂轮 磨头及砂轮片。 2.2严格按照国家有关使用手提电动工具的安全操作规程进行。 五、工艺要求 1、机座出线孔打磨部位及要求 1.1打磨接线盒出口处全部(不含出口平面), 1.1.1毛边、粘砂或凸台存在于非加工区需用相应錾子去除并用相应磨头打磨光。 编制审核会签标准化审定 资料来源 自编
无锡童氏电机有限公司 铸件打磨工艺要求规定 共3页 第2页 编制部门 标准化 标记处数 更改文件号 签字 日期 工艺科 审定 1.1.2要求打磨后倒角处手感圆润光滑,直线处平整无毛刺、粘砂等; 毛边多肉 粘砂凸台 1.2机座散热片打磨部位及要求 1.2.1 打磨相邻散热片槽这间、散热片表面需用百叶轮轻轻打磨,去除粘砂及表面 氧化皮及其它 杂物。 1.2.2 毛边、粘砂或凸台需用相应錾子去除并用相应磨头打磨光滑。缺块应补焊。 1.2.3 打磨后目测应无任何大于 0.5mm 的凸台、漆瘤、毛边。手感应光滑平整< 散热片有缺块应补焊 粘砂需去除干净 1.3 机座底脚打磨部位及要求 1.3.1 机座底脚四侧、上平面及加强筋处,需用百叶轮轻轻打磨,去除粘砂及表面 氧化皮及其它杂物。
压铸件结构设计
压铸件结构创新设计(经验) 压铸件零件设计的注意事项 一、压铸件的设计涉及四个方面的内容:a、即压力铸造对零件形状结构的要求;b、压铸件的工艺性能;c、压铸件的尺寸精度及表面要求;d、压铸件分型面的确定; 压铸件的零件设计是压铸生产技术中的重要部分,设计时必须考虑以下问题:模具分型面的选择、浇口的开设、顶杆位置的选择、铸件的收缩、铸件的尺寸精度保证、铸件内部缺陷的防范、铸孔的有关要求、收缩变形的有关要求以及加工余量的大小等方面; 二、压铸件的设计原则是:a、正确选择压铸件的材料,b、合理确定压铸件的尺寸精度;c、尽量使壁厚分布均匀;d、各转角处增加工艺园角,避免尖角。 三、压铸件按使用要求可分为两大类,一类承受较大载荷的零件或有较高相对运动速度的零件,检查的项目有尺寸、表面质量、化学成分、力学性能(抗拉强度、伸长率、硬度);另一类为其它零件,检查的项目有尺寸、表面质量及化学成分。 在设计压铸件时,还应该注意零件应满足压铸的工艺要求。压铸的工艺性从分型面的位置、顶面推杆的位置、铸孔的有关要求、收缩变形的有关要求以及加工余量的大小等方面考虑。合理确定压铸面的分型面,不但能简化压铸型的结构,还能保证铸件的质量。 压铸件零件设计的要求 一、压铸件的形状结构要求:a、消除内部侧凹;b、避免或减少抽芯部位;c、避免型芯交叉; 合理的压铸件结构不仅能简化压铸型的结构,降低制造成本,同时也改善铸件质量, 二、铸件设计的壁厚要求:压铸件壁厚度(通常称壁厚)是压铸工艺中一个具有特殊意义的因素,壁厚与整个工艺规范有着密切关系,如填充时间的计算、内浇口速度的选择、凝固时间的计算、模具温度梯度的分析、压力(最终比压)的作用、留模时间的长短、铸件顶出温度的高低及操作效率; a、零件壁厚偏厚会使压铸件的力学性能明显下降,薄壁铸件致密性好,相对提高了铸件强度及耐压性; b、铸件壁厚不能太薄,太薄会造成铝液填充不良,成型困难,使铝合金熔接不好,铸件表面易产生冷隔等缺陷,并给压铸工艺带来困难; 压铸件随壁厚的增加,其内部气孔、缩孔等缺陷增加,故在保证铸件有足够强度和刚度的前提下,应尽量减小铸件壁厚并保持截面的厚薄均匀一致,为了避免缩松等缺陷,对铸件的厚壁处应减厚(减料),增加筋;对于大面积的平板类厚壁铸件,设置筋以减少铸件壁厚; 根据压铸件的表面积,铝合金压铸件的合理壁厚如下: 压铸件表面积/mm2 壁厚S/mm ≤25 1.0~3.0 >25~100 1.5~4.5 >100~400 2.5~5.0
铸件通用技术要求
铸件通用技术要求(JB/ZQ4000.5-86) 1.碳素铸钢应符合GB5678-85的规定; 合金铸钢应符合JB/ZQ4297-86的规定, 耐热铸钢应符合JB/ZQ4298的规定; 不锈钢应符合JB/ZQ4299及JB/ZQ6009-84的规定. 2.灰铸铁应符合GB5675-85的规定; 球墨铸铁应符合JB/ZQ4302-86的规定, 耐热铸铁应符合JB/ZQ4303-86的规定; 耐磨铸铁应符合JB/ZQ4303-86的规定. 3.铸件尺寸公差等级分16级,见1-175 铸件尺寸公差.plb, 单件小批生产一般按1-176 小批单件毛坯尺寸公差.plb选用.公差带应对称于毛坯铸件基本尺寸配置,即公差的一半位于正侧,另一半位于负侧. 有特殊要求时,公差带也可非对称配置,但应在图样上标注. 4.铸件内、外圆角公差用1-175铸件尺寸公差.plb 中公差值作为上限,使其下限为零;壁厚公差可比其它尺寸的一般公差降一级选用, 如图样上标明一般公差为CT10 级的话,则壁厚公差选用CT11级. 5.特殊要求的公差, 应直接标注毛坯件基本尺寸的后面,如95±1.1. 特殊要求的公差可比一般公差高或低.一般情况下不能低于1-176 小批单件毛坯尺寸公差.plb规定的公差等级范围,当要求的公差超过该库规定的范围时, 则经有关方面协商后从1-175铸件尺寸公差.plb中选取. 6.碳素钢和低合金钢(包括高锰钢)铸钢件缺陷的补焊按JB/ZQ4000.6-86(铸钢件补焊通用技术条件)规定执行. 7.当铸件补焊处的焊缝深度超过壁厚20%或25mm时,补焊后均应进行适当的消除应力热处理. 补焊大型缺陷时,焊缝金属量大,有必要时可在焊接到坡口的1/3-1/处时进行一次中间退火, 消除应力后再继续焊满坡口, 最后再做一次消除应力热处理.补焊大型或碳当量(碳当量的计算见本标准附录A)超过0.4%的铸钢件的缺陷时, 在补焊后应立即入炉进行消除应力的热处理. 8.设计人员根据铸件的技术要求填写下表,并将此表贴在铸件图样的右上部. (铸件技术要求) : ━━━━━━━━━━━━━━━━━━━ 通用技术要求JB/ZQ4000.5 铸件尺寸公差要求CT 密封试验是/否 耐压试验是/否 ━━━━━━━━━━━━━━━━━━━ 注:表中空格中可补充其它技术要求.
压铸件的结构工艺性
压铸件的结构工艺性 1.熟练掌握工程制图标准和表示方法。掌握公差配合的选用和标注。 2.熟悉常用金属材料的性能、试验方法及其选用。掌握钢的热处理原理,熟悉常用金属材料的热处理方法及其选用。了解常用工程塑料、特种陶瓷、光纤和纳米材料的种类及应用。 3.掌握机械产品设计的基本知识与技能,能熟练进行零、部件的设计。熟悉机械产品的设计程序和基本技术要素,能用电子计算机进行零件的辅助设计,熟悉实用设计方法,了解现代设计方法。 4.掌握制订工艺过程的基本知识与技能,能熟练制订典型零件的加工工艺过程,并能分析解决现场出现的一般工艺问题。熟悉铸造、压力加工、焊接、切(磨)削加工、特种加工、表面涂盖处理、装配等机械制造工艺的基本技术内容、方法和特点并掌握某些重点。熟悉工艺方案和工艺装备的设计知识。了解生产线设计和车间平面布置原则和知识。 5.熟悉与职业相关的安全法规、道德规范和法律知识。熟悉经济和管理的基础知识。了解管理创新的理念及应用。 6.熟悉质量管理和质量保证体系,掌握过程控制的基本工具与方法,了解有关质量检测技术。 7.熟悉计算机应用的基本知识。熟悉计算机数控(CNC)系统的构成、作用和控制程序的编制。了解计算机仿真的基本概念和常用计算机软件的特点及应用。 8.了解机械制造自动化的有关知识。 Ⅱ.考试内容 一、工程制图与公差配合 1.工程制图的一般规定 (1)图框 (2)图线 (3)比例 (4)标题栏 (5)视图表示方法 (6)图面的布置 (7)剖面符号与画法 2.零、部件(系统)图样的规定画法 (1)机械系统零、部件图样的规定画法(螺纹及螺纹紧固件的画法齿轮、齿条、蜗杆、蜗轮及链轮的画法花键的画法及其尺寸标注弹簧的画法) (2)机械、液压、气动系统图的示意画法(机械零、部件的简化画法和符号管路、接口和接头简化画法及符号常用液压元件简化画法及符号) 3.原理图 (1)机械系统原理图的画法 (2)液压系统原理图的画法 (3)气动系统原理图的画法 4.示意图 5.尺寸、公差、配合与形位公差标注 (1)尺寸标注 (2)公差与配合标注(基本概念公差与配合的标注方法) (3)形位公差标注 6.表面质量描述和标注 (1)表面粗糙度的评定参数 (2)表面质量的标注符号及代号
设计铸件时,从哪几方面考虑压铸件的结构工艺性
设计铸件时,从哪几方面考虑压铸件的结构工艺性 1.熟练掌握工程制图标准和表示方法。掌握公差配合的选用和标注。 2.熟悉常用金属材料的性能、试验方法及其选用。掌握钢的热处理原理,熟悉常用金属材料的热处理方法及其选用。了解常用工程塑料、特种陶瓷、光纤和纳米材料的种类及应用。3.掌握机械产品设计的基本知识与技能,能熟练进行零、部件的设计。熟悉机械产品的设计程序和基本技术要素,能用电子计算机进行零件的辅助设计,熟悉实用设计方法,了解现代设计方法。 4.掌握制订工艺过程的基本知识与技能,能熟练制订典型零件的加工工艺过程,并能分析解决现场出现的一般工艺问题。熟悉铸造、压力加工、焊接、切(磨)削加工、特种加工、表面涂盖处理、装配等机械制造工艺的基本技术内容、方法和特点并掌握某些重点。熟悉工艺方案和工艺装备的设计知识。了解生产线设计和车间平面布置原则和知识。 5.熟悉与职业相关的安全法规、道德规范和法律知识。熟悉经济和管理的基础知识。了解管理创新的理念及应用。 6.熟悉质量管理和质量保证体系,掌握过程控制的基本工具与方法,了解有关质量检测技术。 7.熟悉计算机应用的基本知识。熟悉计算机数控(CNC)系统的构成、作用和控制程序的编制。了解计算机仿真的基本概念和常用计算机软件的特点及应用。 8.了解机械制造自动化的有关知识。 Ⅱ.考试内容 一、工程制图与公差配合 1.工程制图的一般规定 (1)图框 (2)图线 (3)比例 (4)标题栏 (5)视图表示方法 (6)图面的布置 (7)剖面符号与画法 2.零、部件(系统)图样的规定画法 (1)机械系统零、部件图样的规定画法(螺纹及螺纹紧固件的画法齿轮、齿条、蜗杆、蜗轮及链轮的画法花键的画法及其尺寸标注弹簧的画法) (2)机械、液压、气动系统图的示意画法(机械零、部件的简化画法和符号管路、接口和接头简化画法及符号常用液压元件简化画法及符号) 3.原理图 (1)机械系统原理图的画法 (2)液压系统原理图的画法 (3)气动系统原理图的画法 4.示意图 5.尺寸、公差、配合与形位公差标注 (1)尺寸标注 (2)公差与配合标注(基本概念公差与配合的标注方法) (3)形位公差标注
(新)压铸件零件设计的注意事项_
压铸件零件设计的注意事项 一、压铸件的设计涉及四个方面的内容:a、 即压力铸造对零件形状结构的要求;b、压铸件的工艺性能;c、压铸件的尺寸精度及表面要求;d、压铸件分型面的确定; 压铸件的零件设计是压铸生产技术中的重要部分,设计时必须考虑以下问题:模具分型面的选择、浇口的开设、顶杆位置的选择、铸件的收缩、铸件的尺寸精度保证、铸件内部缺陷的防范、铸孔的有关要求、收缩变形的有关要求以及加工余量的大小等方面; 二、压铸件的设计原则是:a、正确选择压 铸件的材料,b、合理确定压铸件的尺寸精度;c、尽量使壁厚分布均匀;d、各转角处增加工艺园角,避免尖角。 三、压铸件按使用要求可分为两大类,一类 承受较大载荷的零件或有较高相对运动速度的零件,检查的项目有尺寸、表面质量、化学成分、力学性能(抗拉强度、伸长率、硬度);另一类为其它零件,检查的项目有尺寸、表面质量及化学成分。在设计压铸件时,还应该注意零件应满足压铸的工艺要求。压铸的工艺性从分型面的位置、顶面推杆的位
置、铸孔的有关要求、收缩变形的有关要求以及加工余量的大小等方面考虑。合理确定压铸面的分型面,不但能简化压铸型的结构,还能保证铸件的质量。 压铸件零件设计的要求 一、压铸件的形状结构要求:a、消除内部侧凹; b、避免或减少抽芯部位; c、避免型芯交叉; 合理的压铸件结构不仅能简化压铸型的结构,降低制造成本,同时也改善铸件质量, 二、铸件设计的壁厚要求:压铸件壁厚度(通常称壁厚)是压铸工艺中一个具有特殊意义的因素,壁厚与整个工艺规范有着密切关系,如填充时间的计算、内浇口速度的选择、凝固时间的计算、模具温度梯度的分析、压力(最终比压)的作用、留模时间的长短、铸件顶出温度的高低及操作效率; a、零件壁厚偏厚会使压铸件的力学性能明显下降,薄壁铸件致密性好,相对提高了铸件强度及耐压性; b、铸件壁厚不能太薄,太薄会造成铝液填充不良,成型困难,使铝合金熔接不好,铸件表面易产生
铸件外观标准
DKBA 技术有限公司内部技术规范 铸件质量要求 Specification for Casting Part’s Quality
修订声明Revision declaration 本规范拟制与解释部门:整机工程部 本规范的相关系列规范或文件:无 相关国际规范或文件一致性:无 替代或作废的其它规范或文件:压铸件技术规范 相关规范或文件的相互关系:无
目录Table of Contents 1铸件的分类6 2铸件的缺陷定义6 3质量要求8 3.1铸件的化学成分及力学性能 (8) 3.2铸件尺寸 (9) 3.3铸件的表面质量 (10) 3.4铸件的内部质量 (11) 3.4.1压铸件内部质量11 3.4.2金属型铸件内部质量11 3.5铸件修补及矫正 (12) 3.5.1压铸件的浸渗、整形和修补12 3.5.2金属型铸件的修补及矫正12 4试验方法和检验规则12 4.1检验项目 (12) 4.1.1压铸件检验项目12 4.1.2金属型铸件检验项目12 4.2化学成分 (13) 4.3力学性能 (13) 4.4铸件尺寸 (13) 4.5铸件重量 (13) 4.6外观质量 (14) 4.7内部质量 (14) 4.7.1压铸件内部质量14 4.7.2金属型铸件内部质量14 5质量保证14 6铸件的交付、包装、运输与储存14 7参考文献Reference Document 15 表目录List of Tables 表1 铸件常见缺陷特征6 表2 压铸铝合金化学成分和力学性能表8 表3 压铸锌合金化学成分和力学性能表8 表4 金属型铸造铝合金化学成分和力学性能表9 表5 铸件尺寸公差数值(mm)9 表6 压铸件平面度公差(mm)9 表7 压铸件的平行度公差(mm)9 表8 压铸件同轴度公差(mm)9 表9 铸件表面质量要求表10 表10 压铸件加工后加工面上允许孔穴缺陷表10 表11 金属型铸件表面孔洞限量11 表12 铸件机械加工后螺纹允许孔穴的规定11 表13 内部缺陷允许级别11 表14 压铸件检验项目12
铸造行业标准汇总
铸造行业准入条件 为引导铸造产业健康、有序和可持续发展,促进铸造行业产业结构优化升级,遏制低水平重复建设和产能盲目扩张,保护生态环境,推进节能减排,提高资源、能源利用水平,提升我国装备制造业整体实力,推进我国从世界铸造大国向铸造强国转变,根据有关法律法规和产业政策,制定本准入条件。 一、建设条件和布局 (一)铸造企业的布局及厂址的确定应符合国家产业政策和相关法律法规,符合各省、自治区、直辖市铸造业和装备制造业发展规划。 (二)国务院有关主管部门和省、自治区、直辖市人民政府划定的风景名胜区、自然保护区和水源地及其他需要特别保护的区域(一类区)的铸造企业不予认定;在二类区和三类区(一类区以外的其他地区),新(扩)建铸造企业和原有铸造企业的各类污染物(大气、水、厂界噪声、固体废弃物)排放标准与处置措施均应符合国家和当地环保标准的规定。 (三)新(扩)建铸造企业应通过“建设项目环境影响评价审批”及“职业健康安全预评估”,并通过项目环境保护和职业健康安全防护设施“三同时”验收。
二、生产工艺 (一)企业应根据生产铸件的材质、品种、批量,合理选择低污染、低排放、低能耗、经济高效的铸造工艺。 (二)不得采用粘土砂干型/芯、油砂制芯、七〇砂制型/芯等落后铸造工艺。 三、生产装备 (一)企业应配备与生产能力相匹配的熔炼设备和精炼设备,如冲天炉、中频感应电炉、电弧炉、精炼炉(AOD、VOD、LF炉等)、电阻炉、燃气炉等。炉前应配置必要的化学成分分析、金属液温度测量装备,并配有相应有效的通风除尘、除烟设备与系统。 (二)铸造用高炉应符合工业和信息化部颁布的《铸造用生铁企业认定规范条件》并通过工业和信息化部认定。 (三)企业应配备与生产能力相匹配的造型、制芯、砂处理、清理等设备。采用砂型铸造工艺的企业应配备旧砂处理设备。各种旧砂的回用率应达到:水玻璃砂(再生)≥60%,呋喃树脂自硬砂(再生)≥90%,碱酚醛树脂自硬砂(再生)≥70%,粘土砂≥95%。 (四)企业或所在产业集群、工业园区应具备与其产能和质量保证相匹配的试验室和必要的检测设备。 (五)落砂及清理工序应配备相匹配的隔音降噪和通风除尘设备。
压铸件设计规范
压铸件设计规范 Company number:【0089WT-8898YT-W8CCB-BUUT-202108】
?压铸件设计规范 ?一、壁厚 ?的壁厚对铸件质量有很大的影响。以铝为例,薄壁比厚壁具有更高的强度和良好的致密性。因此,在保证铸件有足够的强度和刚性的条件下,应尽可能减少其壁厚,并保持壁厚均匀一致。 ?铸件壁太薄时,使金属熔接不好,影响铸件的强度,同时给成型带来困难;壁厚过大或严重不均匀则易产生缩瘪及裂纹。随着壁厚的增加,铸件内部气孔、缩松等缺陷也随之增多,同样降低铸件的强度。 ?的壁厚一般以~4mm为宜,壁厚超过6mm的零件不宜采用压铸。推荐采用的最小壁厚和正常壁厚见表1。 ?表1 的最小壁厚和正常壁厚 我司现使用的绝大多数为铝,其壁厚一般控制在~。 二、铸造圆角和脱模斜度 1)铸造圆角 各部分相交应有圆角(分型面处除外),使金属填充时流动平稳,气体容易排出,并可避免因锐角而产生裂纹。对于需要进行和涂饰的,圆角可以均匀镀层,防止尖角处涂料堆积。 的圆角半径R一般不宜小于1mm,最小圆角半径为 mm,见表2。铸造圆角半径的计算见表3。 表2 的最小圆角半径(mm)
我司现采用的圆角一般取。 表3 铸造圆角半径的计算(mm) 说明:①、对锌铸件,K=1/4;对铝、镁、铸件, K=1/2。 ②、计算后的最小圆角应符合表2的要求。 2) 脱模斜度 设计时,就应在结构上留有结构斜度,无结构斜度时,在需要之处,必须有脱模的工艺斜度。斜度的方向,必须与铸件的脱模方向一致。推荐的脱模斜度见表4。表4 脱模斜度 说明:①、由此斜度而引起的铸件尺寸偏差,不计入尺寸公差值内。
压铸件设计规范
压铸件设计规范相关知识 压铸件设计规范相关知识 一、壁厚 压铸件的壁厚对铸件质量有很大的影响。以铝合金为例,薄壁比厚壁具有更高的强度和良好的致密性。因此,在保证铸件有足够的强度和刚性的条件下,应尽可能减少其壁厚,并保持壁厚均匀一致。 铸件壁太薄时,使金属熔接不好,影响铸件的强度,同时给成型带来困难;壁厚过大或严重不均匀则易产生缩瘪及裂纹。随着壁厚的增加,铸件内部气孔、缩松等缺陷也随之增多,同样降低铸件的强度。 压铸件的壁厚一般以2.5~4mm为宜,壁厚超过6mm的零件不宜采用压铸。推荐采用的最小壁厚和正常壁厚见表1。 表1 压铸件的最小壁厚和正常壁厚 二、铸造圆角和脱模斜度 1)铸造圆角 压铸件各部分相交应有圆角(分型面处除外),使金属填充时流动平稳,气体容易排出,并可避免因锐角而产生裂纹。对于需要进行电镀和涂饰的压铸件,圆角可以均匀镀层,防止尖角处涂料堆积。 压铸件的圆角半径R一般不宜小于1mm,最小圆角半径为0.5 mm,见表2。铸造圆角半径的计算见表3。 表2 压铸件的最小圆角半径(mm)
我司现采用的圆角一般取R1.5。 表3 铸造圆角半径的计算(mm) 说明:①、对锌合金铸件,K=1/4;对铝、镁、合金铸件,K=1/2。 ②、计算后的最小圆角应符合表2的要求。 2) 脱模斜度 设计压铸件时,就应在结构上留有结构斜度,无结构斜度时,在需要之处,必须有脱模的工艺斜度。斜度的方向,必须与铸件的脱模方向一致。推荐的脱模斜度见表4。 表4 脱模斜度 说明:①、由此斜度而引起的铸件尺寸偏差,不计入尺寸公差值内。 ②、表中数值仅适用型腔深度或型芯高度≤50mm,表面粗糙度在Ra0.1,大端与小端尺寸的单面差的最小值为0.03mm。当深度或高度>50mm,或表面粗糙度超过Ra0.1时,则脱模斜度可适当增加。
钣金件-压铸件-挤压件-塑胶件结构工艺设计指南
结构设计工艺手册
前言 公司现有零件中,不仅在打样过程中经常会有一些加工工艺性的问题,也有很多归档转产的零件存在加工困难的情况,不仅影响生产进度和交货,也影响结构件的质量。如钣金零件的折弯,经常会发生折弯碰刀的情况;落料的外圆角、半圆凸台、异型孔的规格太多,以及一些不合理的形状设计,导致加工厂要多开很多不必要的落料模,大大增加模具的加工和管理成本;插箱的钣金导轨、拉伸凸台等设计,品种越来越多,需要统一、规范;喷漆和丝印,也经常出现喷涂选择不合理导致废品率较高、无法丝印等问题;有些钣金零件的点焊完全可以适当增加定位,不增加成本也不影响美观,实际上大部分设计是靠生产的工装定位,不仅麻烦、效率低,精度也不好;很多可以避免焊接的钣金零件,往往设计成角焊的结构形式,焊接和打磨都非常麻烦,不仅效率较低,而且外观质量也经常得不到保证,等等。长期以来,这些相同的问题不断地重复发生,无论对产品质量还是产品的生产和进度,都会产生不良的影响。 编写这本《结构设计工艺手册》目的,就是为了方便工程师在结构设计时查阅一些常用的、关键的数据,更好地保证工程师设计出的零件有较好的加工工艺性,统一结构要素,减少不必要的开模,加快加工进度,降低加工成本,提高产品质量。编写这本手册的同时,对《钣金模具手册》标准进行了彻底的改编,对一些典型的结构形状进行了优化和系列化,减少了品种,并在intralink库里对相关的模具建模,不仅方便设计人员进行结构设计,对模具的统一,也会起到较好的效果。 手册中一些典型的数据主要来源于参考资料,一些工艺上的极限尺寸,主要来源于加工厂家提供的数据,是我们应尽可能遵照的。有些正在生产的零件,一些尺寸超出了手册中给出的极限尺寸,但并不能就能说明这些设计是有良好的工艺性,原则上是在满足产品性能的条件下,尽可能达到最好的加工工艺性。 由于时间和实际经验有限,手册中错误在所难免,恳请大家批评指正,希望经过一定时间的实践检验,经过将来补充、修订、完善之后,能够成为一部非常实用的参考书,对我们的设计工作起到很好的指导作用。考虑手册的篇幅和实用性,以及我们的设计主要是钣金零件设计,因此,本手册主要以钣金件为主。 手册编写得到中兴新的吉海青、胡兴胜、李道清、杜坚、巴新安等大力帮助,在此表示感谢! 顾问:张晖马庆魁何朝来何剑波冯力 编写人员:彭诗林:第一章:钣金零件设计工艺 颜斌鲁:第二章:金属切削件设计工艺 严冬:第三章: 压铸件设计工艺 杨涛:第四章:铝型材零件设计工艺 郑宁生:第五章金属的焊接设计工艺 尚玉其:第六章:塑料件设计工艺 刘彦明:第七章表面处理工艺 温存善、封智:第八章:结构图纸零部件的分级和代码申请 曹水春、陈进云、张向峰、刘肖:《结构设计工艺手册》修改、编辑、汇总
铸件基本要求
铸件通用技术要求 JB/ZQ4000.5-86 1.碳素铸钢应符合GB5678-85的规定; 合金铸钢应符合JB/ZQ4297-86的规定,耐热铸钢应符合JB/ZQ4298的规定; 不锈钢应符合JB/ZQ4299及JB/ZQ6009-84的规定. 2.灰铸铁应符合GB5675-85的规定; 球墨铸铁应符合JB/ZQ4302-86的规定,耐热铸铁应符合JB/ZQ4303-86的规定; 耐磨铸铁应符合JB/ZQ4303-86的规定. 3.铸件尺寸公差等级分16级,见1-175 铸件尺寸公差.plb, 单件小批生产一般按1-176 小批单件 毛坯尺寸公差.plb选用.公差带应对称于毛坯铸件基本尺寸配置,即公差的一半位于正侧,另一半 位于负侧. 有特殊要求时,公差带也可非对称配置,但应在图样上标注. 4.铸件内、外圆角公差用1-175铸件尺寸公差.plb中公差值作为上限,使其下限为零;壁厚公差可比 其它尺寸的一般公差降一级选用, 如图样上标明一般公差为CT10 级的话,则壁厚公差选用CT11级. 5.特殊要求的公差, 应直接标注毛坯件基本尺寸的后面,如95±1.1. 特殊要求的公差可比一般公差 高或低.一般情况下不能低于1-176 小批单件毛坯尺寸公差.plb规定的公差等级范围,当要求的 公差超过该库规定的范围时, 则经有关方面协商后从1-175铸件尺寸公差.plb中选取. 6.碳素钢和低合金钢(包括高锰钢)铸钢件缺陷的补焊按JB/ZQ4000.6-86(铸钢件补焊通用技术条件) 规定执行. 7.当铸件补焊处的焊缝深度超过壁厚20%或25mm时,补焊后均应进行适当的消除应力热处理. 补焊大型缺陷时,焊缝金属量大,有必要时可在焊接到坡口的1/3-1/处时进行一次中间退火, 消除 应力后再继续焊满坡口, 最后再做一次消除应力热处理.补焊大型或碳当量(碳当量的计算见本标 准附录A)超过0.4%的铸钢件的缺陷时, 在补焊后应立即入炉进行消除应力的热处理. 8.设计人员根据铸件的技术要求填写下表,并将此表贴在铸件图样的右上部. (铸件技术要求) : 通用技术要求JB/ZQ4000.5 铸件尺寸公差要求CT