本田五原则表
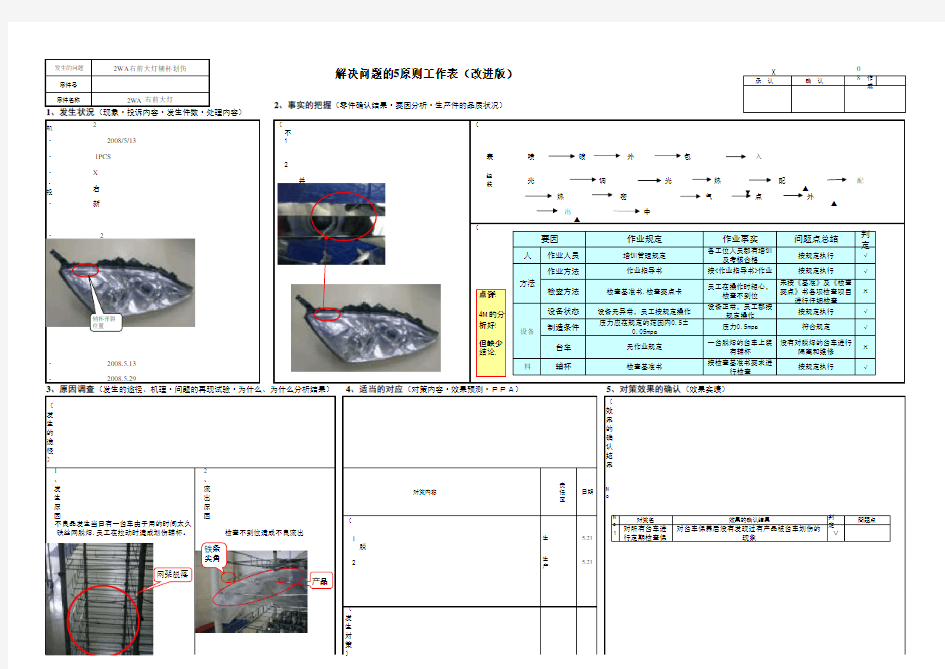
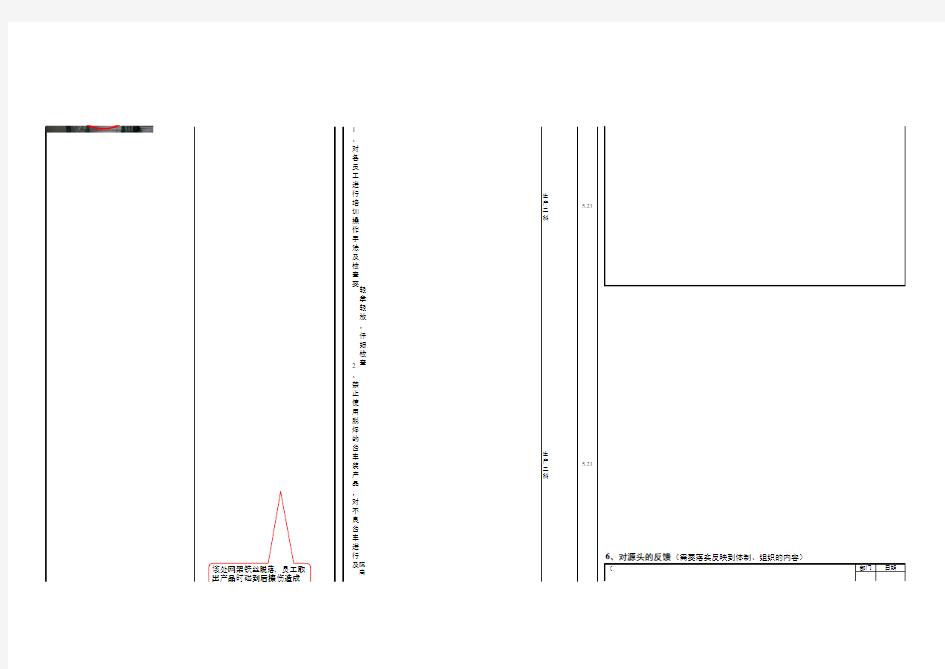
XXX有限公司
08年5月23日
作 成
·机种、型号:
2WA H/L R 前大灯
(零件确认结果)
(工序概要)
不良件的确认情况;
·发生年月日:
1.发生不良件的右大灯批组号是;HD17K
·发生件数:表面处理
喷底漆镀膜外观检查
包装放入台车入库
2.经解剖退回的不良大灯,此不良是辅杯外表面刮伤露底
·发生场所:XX4S 店
并非裂纹。
组装
光杯附件安装
调节螺钉安装
光杯压入
热熔胶涂布配光镜组件安装配光镜加压
·投诉内容
右前大灯内部开裂
▲
热熔胶冷却
密封后盖及灯泡安装
气密检查
点灯检查外观检查及包装
·现象
新车到店PDI检查时发现,右前大灯内部开裂。
▲
出货检查(抽检)中转仓
▲
(要因分析)
·GSE 生产日期:2008.4.17(HD17K )
·受理委托日期:·要求回复期限:(发生的途径)(效果的确认结果)
1、发生原因
2、流出原因
责任区
No (流出对策)
No
判定1、对GSE 工厂内所有台车进行检查,生产二科
脱焊的不良台车统一维修.
2.要求前工序对台车有专人负责并定期维修检查。
生产二科(发生対策)
1、对各员工进行培训操作手法及检查要点。生产二科轻拿轻放,仔细检查。
2、禁止使用脱焊的台车装产品,对不良台车进行及时。
生产二科
隔离修复(根本原因的改善)
1,对公司内部铁丝网台车进行全面彻底的检查维修,为什么、为什么分析
并找专人负责每周进行检查保养。
2,对员工的操作手法和检查要点再全面的培训教育。3,横向展开到各产品的装配工艺及操作手法上。
(发行品质信息)
部门
日期
5.23
检查不到位造成不良流出
辅杯
5.23
制造条件料
5
发生原因流出原因
2WA R辅杯划伤漏底
4组装员工在装配时未按检查基
准书要求全面检查。管理不足
部分台车由于用的时间久铁丝网脱焊台车没有专人负责保养,物料在运
输过程中碰伤。1PCS 2008.5.29
对策内容
2008.5.13人承 认
确 认
要因
按规定执行各工位人员都有培训
及考核合格
2008/5/13
零件名称
2WA 右前大灯
发生的问题2WA 右前大灯辅杯划伤
零件号日期
作业人员√√√检查基准书
对策名
效果的确认结果
1
对所有台车进行定期检查保5.23配光镜工位及点灯检查工位人员检查不全面而流出。 Step 没有定期对台车保养、隔离不
良台车
台车管理不足
3
2
1判定
作业规定
设备状态
作业方法
培训管理规定作业指导书设备无异常,员工按规定操作作业事实
问题点总结
問題点
对台车保养后没有发现过有产品被台车划伤的
现象
∨
员工在操作时粗心,检查不到位
未按《基准》及《检查
要点》书各项检查项目进行仔细检查
方法
检查方法
检查基准书.检查要点卡
×√按<作业指导书>作业
按规定执行
设备正常,员工都按规定操作
按规定执行压力应在规定的范围内0.5±0.05mpa
压力0.5mpa 符合规定按检查基准书要求进行检查
√
按规定执行
无作业规定一台脱焊的台车上装有辅杯没有对脱焊的台车进行
隔离和维修×不良品发生当日有一台车由于用的时间太久铁丝网脱焊,员工在拉动时造成划伤辅杯。
5.23
设备
台车
1、发生状況(现象·投诉内容·发生件数·处理内容)
2、事实的把握(零件确认结果·要因分析·生产件的品质状况)
3、原因调查(发生的途径、机理·问题的再现试验·为什么、为什么分析结果)
4、适当的对应(对策内容·效果预测·PPA)
5、对策效果的确认(效果实绩)
6、对源头的反馈(需要落实反映到体制、组织的内容)
解决问题的5原则工作表(改进版)
辅杯开裂位置
网架脱落
该处网架铁丝脱落,员工取出产品时碰到后擦伤造成
铁条尖角
产品
点评:
4M 的分析好!但缺少结论.