探伤人员要评片口诀

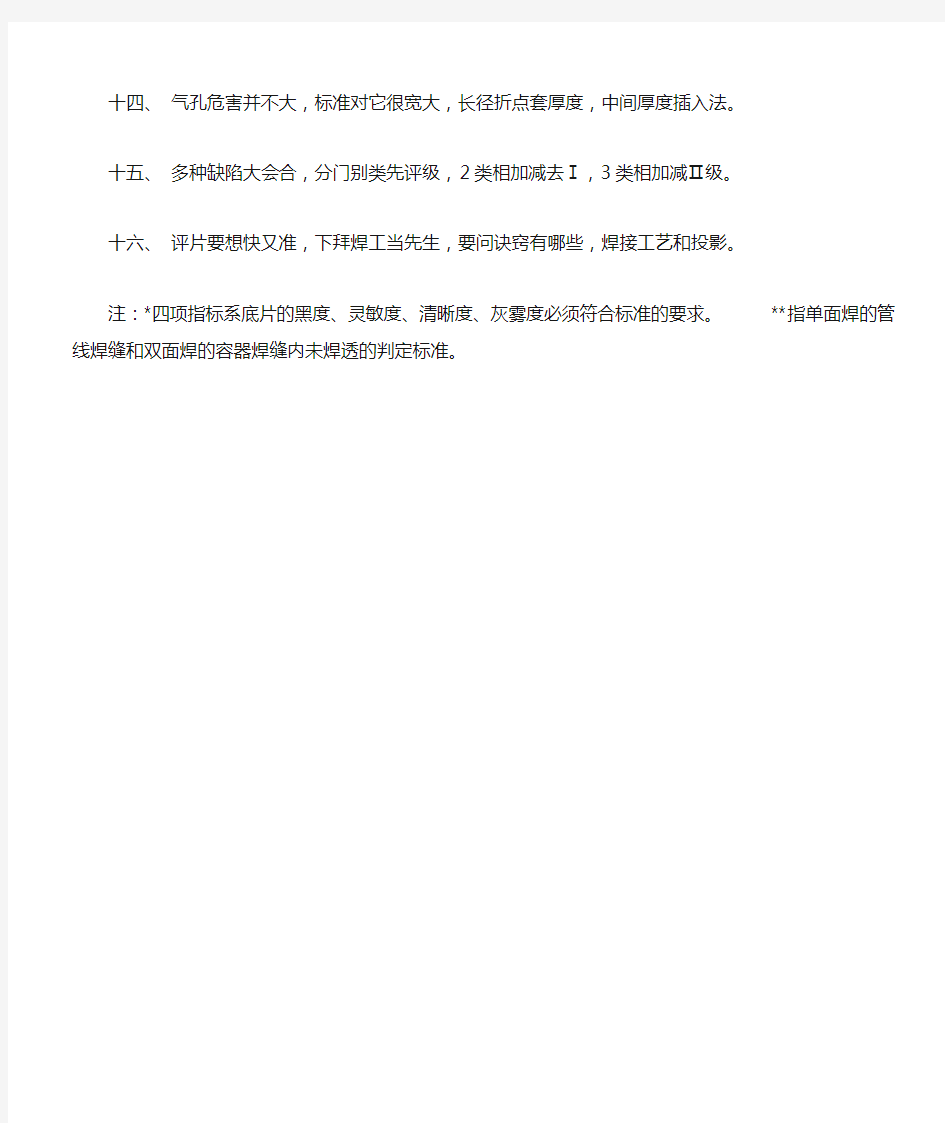
一、探伤人员要评片,四项指标放在先*,底片标记齐又正,铅字压缝为废片。
二、评片开始第一件,先找四条熔合线,小口径管照椭圆,根部都在圈里面。
三、气孔形象最明显,中心浓黑边缘浅,夹渣属于非金属,杂乱无章有棱边。
四、咬边成线亦成点,似断似续常相见,这个缺陷最好定,位置就在熔合线。
五、未焊透是大缺陷,典型图象成直线,间隙太小钝边厚,投影部位靠中间。
六、内凹只在仰焊面,间隙太大是关键,内凹未透要分清,内凹透度成弧线。
七、未熔合它斜又扁,常规透照难发现,它的位置有规律,都在坡口与层间。
八、横裂纵裂都危险,横裂多数在表面,纵裂分布范围广,中间稍宽两端尖。
九、还有一种冷裂纹,热影响区常发现,冷裂具有延迟性,焊完两天再拍片。
十、有了裂纹很危险,斩草除根保安全,裂纹不论长和短,全部都是Ⅳ级片。
十一、未熔和也很危险,黑度有深亦有浅,一旦判定就是它,亦是全部Ⅳ级片。
十二、危害缺陷未焊透,Ⅱ级焊缝不能有,管线根据深和长,容器跟着条渣走**。十三、夹渣评定莫着忙,分清圆形和条状,长宽相比3为界,大于3倍是条状。十四、气孔危害并不大,标准对它很宽大,长径折点套厚度,中间厚度插入法。十五、多种缺陷大会合,分门别类先评级,2类相加减去Ⅰ,3类相加减Ⅱ级。
十六、评片要想快又准,下拜焊工当先生,要问诀窍有哪些,焊接工艺和投影。
注:*四项指标系底片的黑度、灵敏度、清晰度、灰雾度必须符合标准的要求。 **指单面焊的管线焊缝和双面焊的容器焊缝内未焊透的判定标准。
无损检测基础知识
一、无损检测基础知识 1.1无损检测概况 1.1.1无损检测的定义和分类 什么叫无损检测,从文字上面理解,无损检测就是指在不损坏试件的前提下,对试件进行检查和测试的方法。但是这并不是严格意义上的无损检测的定义,对现代无损检测的定义是:在不损坏试件的前提下,以物理或化学为手段,借助先进的技术和设备器材,对试件的内部及表面的结构、性质、状态进行检查和测试的方法。在无损检测技术发展过程中出现三个名称,即:无损探伤(Non-destructive lnspction),无损检测(Non-destructive Testing),无损评价( Non-destructive Evaluation)。一般认为,这三个名称体现了无损检测技术发展的三个阶段,其中无损探伤是早期阶段的名称,其内涵是探测和发现缺陷;无损检测是当前阶段的名称,其内涵不仅仅是探测缺陷,还包括探测试件的一些其它信息。而无损评价则是即将进入或正在进入的发展阶段,无损评价包涵更广泛,更深刻的内容,它不仅要求发现缺陷,探测试件的结构、性质、状态,还要求获取全面的、更准确的、综合的信息。 射线检测(Radiographyic Testing,,简称RT),超声波检测(Uitrasonic Testing,简称UT),磁粉检测(Magnetic Testing 简称MT),渗透检测(Penetrant Testing,简称PT)是开发较早,应用较广泛的探测缺陷的方法,称为四大常规检测方法,到目前为止,这四种方法仍是锅炉压力容器制造质量检验和再用检验最常用的无损检测方法,其中RT和UT 主要用于检测试件内部缺陷。PT主要用于检测试件表面缺陷,MT主要用于检测试件表面及近表面缺陷。其它用于锅炉压力容器的无损检测方法有涡流检测(Eddy current Testing,简称ET)、声发射检测(Acoustic Emission,简称AE)。 1.1.2无损检测的目的 用无损检测技术,通常是为了达到以下目的: 1、保证产品质量; 2、保障使用安全; 3、改进制造工艺; 4、降低生产成本。 1.1.3无损检测应用的特点 无损检测应用时,应掌握以下几个方面的特点: 1、无损检测要与破坏性检测配合; 2、正确选用实施无损检测的时机;
射线评片技巧焊缝未熔合射线底片影像特点
2015-04-19?分类:解决方案?阅读(1933)?评论(0)? 根据GB6417-1986《金属熔化焊焊缝缺陷分类及说明》定义未熔合,在焊接过程中由于焊缝金属与母材金属未完全熔化结合,或者焊道金属与焊道金属之间未完全熔化结合产生的缺陷称为未熔合。本文讲述未熔合缺陷的分类、焊缝未熔合危害、焊缝未熔合的产生原因、焊缝未熔合在射线底片影像上的特征缺陷,以及讲解工作中射线检测的焊缝未熔合缺陷底片。 一、未熔合分类 焊缝未熔合可分为层间未熔合、坡口未熔合(侧壁未熔合)、根部未熔合,如下图所示为三类焊缝未熔合的示意图。未熔合常出现在焊缝根部形成根部未熔合、在焊道间层形成层间未熔合、在焊道和母材坡口之间形成坡口未熔合,以及在焊缝和母材溢流或焊瘤之间等位置。 坡口未融合示意图 层间未融合示意图 根部未融合示意图 二、未熔合危害 未熔合是一种面积型缺陷,坡口侧未熔合和根部未熔合明显减小了承载截面积,应力集中比较严重,其危害性仅次于裂纹。 三、未熔合的产生原因 (1)焊道清理不干净,存在油污或铁锈; (2)坡口设计加工不合理,液态金属流动有死角; (3)焊接电流过小,焊丝未完全熔化; (4)焊枪没有充分摆动,焊接位置存在死角; (5)焊工为了加快焊接速度,擅自提高电流等。 四、未熔合射线底片影像特征 (1)根部未熔合:典型影像是连续或断续的黑线,靠近母材侧影像轮廓整齐呈直线状且黑度较大,为坡口或钝边的机械加工痕迹。靠近焊缝中心测未熔合影像的轮廓可能较规则,也可能不规则,呈曲齿状的块状缺陷。 根部未熔合在底片上的位置就是焊缝根部的投影位置,若射线垂直焊缝透照,则缺陷一般在焊缝影像的中间。若斜角度透照或者母材坡口形状不对称(开单边坡口)可能偏向一边。 (2)坡口未熔合:典型影像是连续或断续的黑线,宽度不一,黑度不均匀,一侧轮廓较齐,黑度较大,另一侧轮廓不规则,黑度较小,在底片上的位置一般在中心至边缘的1/2处,沿焊缝纵向延伸。 坡口未熔合示意图和底片影像 (3)层间未熔合的典型影像是黑度不大的块状阴影,形状不规则,如伴有夹渣时,夹渣部位黑度较大。 层间未熔合与分层缺陷相似,在射线透照方向上透照厚度差较小,一般在射线照相检测中不易发现。 以下是未熔合缺陷影像
射线评片技巧(一):气孔、夹渣、夹钨射线底片影像特点讲课稿
射线评片技巧(一):气孔、夹渣、夹钨射线底片影像特点
射线评片技巧(一):气孔、夹渣、夹钨射线底片影像特点 2015-04-17 分类:解决方案阅读(4103) 评论(0) 按照JB/T4730-2005《承压设备无损检测》第2部分射线(点击链接下载:NB/T47013.1~13-2015标准)检测篇介绍,焊接接头中的缺陷按性质区分为裂纹、未熔合、未焊透、条形缺陷和圆形缺陷五类。在《射线检测评片》栏目中将介绍该五类性质的缺陷成因、缺陷评片技巧、评级方法,分享在工作中遇见的射线检测案例。本文介绍圆形缺陷(气孔、密集气孔、夹渣、夹钨)评片技巧和缺陷定量评级。 一、圆形缺陷的评片 缺陷长宽之比小于等于3(L/N<=3),且非裂纹、未焊透和未熔合危害性缺陷。对接接头焊缝常见的圆形缺陷包括圆形气孔、非金属夹渣、夹钨等性质缺陷。 圆形缺陷示意图 1、气孔 (1)气孔成因
在《焊缝气孔形成机理及超声检测波形特性》文中详细介绍了焊缝气孔形成的原因。气孔分为单个气孔和密集性气孔。气孔降低了焊缝的金属致密性,降低焊接接头的强度、韧性等力学性能。 (2)气孔射线成像特点 气孔内部充满气体,射线穿过气孔几乎不会形成材质衰减。在射线底片上气孔呈暗色斑点,中心黑度较大。单个气孔边缘较浅平滑过渡,轮廓规则较清晰,密集气孔成团状。气孔大多是球形的,也可以有其它形状,气体的形状与焊接条件密切有关。 单个气孔缺陷 密集性气孔 2、非金属夹渣
(1)夹渣成因 焊缝夹渣形成原因主要有以下几点: ?在焊接每层焊道层间清渣不干净; ?焊接电流过小、焊接速度过快; ?焊接操作过程不当; ?母材坡口设计加工不当; ?液态金属冷却速度过快等; 第一条是焊缝产生夹渣的直接原因,第二到第五条原因是由于焊渣在液态金属中浮渣不及时而残留在焊缝中。焊缝中存在非金属夹渣,当焊缝承受应力过程中在夹渣周围会形成裂纹扩展,裂纹发展到一定程度焊缝开裂。夹渣严重降低了焊接件强度、韧性等力学性能。 (2)夹渣射线成像特点 焊缝金属包裹着非金属夹杂物形成夹渣、射线穿过夹渣有一定的衰减,但远远小于焊缝金属对射线的衰减。射线底片上夹渣呈暗色斑点,黑度分布无规律,轮廓不圆滑不规则,小点状夹渣轮廓较不清晰。
射线检测底片上各种影像的识别 后附评片口诀
射线检测底片上各种影像的识别 1、照相影像形成的原理 同样强度的射线入射,厚的地方底片黑度小,薄的地方黑度大。 2、焊缝结构的形象分析 (1)单面焊:底片上面只有两条边界。(图1) (2)单面焊双面成型:底片上面有四条边界,中间两条间距较小。(图2) (3)带垫板焊缝:四条边界,且最外面两条边界清晰整齐。(图2) 图1.单面焊图2.带垫板单面焊 (4)双面焊:四个边界,且左右两条边界相隔较近,甚至可能有部分重合。(图3) (图4) 图3.双面焊图4.双面焊 3、焊接方法的影像分析 (1)手工电弧焊:呈现鱼鳞纹,边界变化明显。(图5) (2)自动焊:鱼鳞纹不明显,且边界变化平缓。 (3)氩弧焊:焊缝中间有颜色很淡的亮斑。(图6) 图5.手工电弧横焊图6.自动焊 4、焊接位置影响分析 (1)横焊:多条焊缝组成,容易区别。(图7)
(2)立焊:鱼鳞纹较密,且焊缝宽度较大,存在亮斑。(图8) 图7.横焊图8.立焊 (3)仰焊:与立焊影像难区别,鱼鳞纹密度稍大于立焊,也存在亮斑。(图9) 图9.仰焊 5、焊缝中常见缺陷影像分析 (1)分析要点:形状、位置、黑度。 (2)常见缺陷:气孔、夹渣、未焊透、未熔合、裂纹、钨夹渣。其中未焊透、未熔合、裂纹、钨夹渣不参加评定。 a、气孔:(图10) 形状:圆形、椭圆形、斜气孔(弥散形气孔),特点是外部轮廓比较规则。黑度:气孔黑度较大,由中心向四周减淡(大气孔) 位置:一般位于焊道投影中心位置。 b、夹渣:(图11) (图12) 形状:圆形(点状)、长条形,特点是外部不规则。 黑度:黑度分布比较均匀,且黑度较淡。 位置:一般分布在焊道投影中心线到融合线之间。 图10.气孔图11.夹渣图12.线状夹渣
无损检测相关知识习题
无损检测相关知识培训习题 1.、下述指标中,哪个不属于材料的力学性能?( ) A.强度 B.塑性 C.韧性 D.热稳定性 2、衡量材料抵抗冲击载荷作用时断裂的力学性能指标是( ) A. 强度 B. 塑性 C. 韧性 D.硬度 3、以下哪一条不属于材料的使用性能?( ) A. 强度 B. 刚度 C. 耐蚀性 D. 焊接性 4、在金属材料的拉伸试验过程中,下列哪一个阶段材料所受应力不再增加而应变却在继续增加( ) A.弹性阶段 B.屈服阶段 C.强化阶段 D.颈缩阶段 5、承压壳体中工作应力的大小( ) A.与容器壁厚δ和直径 D 成正比,与压力 p 成反比; B.与压力 p 和容器壁厚δ成正比,与容器直径 D 成反比; C.与压力 p 成正比,与容器壁厚δ和容器直径 D 成反比; D.与压力 p 和容器直径 D 成正比,与容器壁厚δ成反比。 6、长期承受交变应力的构件,最可能发生的破坏形式是( ) A.脆性断裂破坏 B.失稳破坏 C.疲劳破坏 D.蠕变破坏 7、以下关于应力集中的叙述,哪一条是正确的( )
A.缺陷形成的缺口越大,形状越尖锐,应力集中越严重; B.壳体截面不圆程度越大,应力集中越严重; C.外加载荷越大,应力集中越严重; D.材料脆性越大,应力集中越严重 8、碳钢和低合金钢焊后消除应力热处理,应加热到大致哪一温度?( ) A. 300~400℃ B.400~500℃; C. 500~650℃ D.650~800℃。 9、含碳量小于或等于多少的碳素钢称为低碳钢( ) A.0.15% B.0.20% C.0.25% D. 0.3% 10、如欲细化晶粒,均匀组织,降低内应力,应采用的热处理方法是( ) A. 退火 B 不完全退火 C.正火 D. 调质 11、合金总量在多少以下的合金钢称为低合金钢( ) A.0.5% B.2% C. 5% D.10% 12、低合金钢 16MnR 的( ) A.平均含碳量小于 0.16%,平均含锰量小于 1.5% B. 平均含碳量 0.16%,平均含锰量小于 1.5% C. 平均含碳量小于 0.16%,平均含锰量 1.5% D. 平均含碳量 0.16%,平均含锰量 1.5% 13、以下哪一条不属于埋弧自动焊的优点。()
射线评片技巧.
射线评片技巧目录 (一):气孔、夹渣、夹钨射线底片影像特点 (二):条形缺陷评片步骤与技巧、条形缺陷综合评级 (三):焊缝未熔合射线底片影像特点 (四):焊缝未焊透射线底片影像特点 (五):裂纹射线底片影像特点
(一):气孔、夹渣、夹钨射线底片影像特点 按照JB/T4730-2005《承压设备无损检测》第2部分射线检测篇介绍,焊接接头中的缺陷按性质区分为裂纹、未熔合、未焊透、条形缺陷和圆形缺陷五类。在《射线检测评片》栏目中将介绍该五类性质的缺陷成因、缺陷评片技巧、评级方法,分享在工作中遇见的射线检测案例。本文介绍圆形缺陷(气孔、密集气孔、夹渣、夹钨)评片技巧和缺陷定量评级。 一、圆形缺陷的评片 缺陷长宽之比小于等于3(L/N<=3),且非裂纹、未焊透和未熔合危害性缺陷。对接接头焊缝常见的圆形缺陷包括圆形气孔、非金属夹渣、夹钨等性质缺陷。 圆形缺陷示意图 1、气孔 (1)气孔成因 在《焊缝气孔形成机理及超声检测波形特性》文中详细介绍了焊缝气孔形成的原因。气孔分为单个气孔和密集性气孔。气孔降低了焊缝的金属致密性,降低焊接接头的强度、韧性等力学性能。 (2)气孔射线成像特点 气孔内部充满气体,射线穿过气孔几乎不会形成材质衰减。在射线底片上气孔呈暗色斑点,中心黑度较大。单个气孔边缘较浅平滑过渡,轮廓规则较清晰,密集气孔成团状。气孔大多是球形的,也可以有其它形状,气体的形状与焊接条件密切有关。 单个气孔缺陷
密集性气孔 2、非金属夹渣 (1)夹渣成因 焊缝夹渣形成原因主要有以下几点: ?在焊接每层焊道层间清渣不干净; ?焊接电流过小、焊接速度过快; ?焊接操作过程不当; ?母材坡口设计加工不当; ?液态金属冷却速度过快等; 第一条是焊缝产生夹渣的直接原因,第二到第五条原因是由于焊渣在液态金属中浮渣不及时而残留在焊缝中。焊缝中存在非金属夹渣,当焊缝承受应力过程中在夹渣周围会形成裂纹扩展,裂纹发展到一定程度焊缝开裂。夹渣严重降低了焊接件强度、韧性等力学性能。 (2)夹渣射线成像特点 焊缝金属包裹着非金属夹杂物形成夹渣、射线穿过夹渣有一定的衰减,但远远小于焊缝金属对射线的衰减。射线底片上夹渣呈暗色斑点,黑度分布无规律,轮廓不圆滑不规则,小点状夹渣轮廓较不清晰。 非金属夹渣
无损检测基础知识
无损检测概论 1、定义和分类: 就是指在不损坏试件的前提下,对试件进行检查和测试的方法。 现代无损检测的定义是:在不损坏试件的前提下,以物理或化学方法为手段,借助先进的技术和设备器材,对试件的内部及表面的结构、性质、状态进行检查和测试的方法。 2、无损检测方法有: 射线检测(RT)、超声波检测(UT)、磁粉检测(MT)、渗透检测(PT)、涡流检测(ET)和声发射检测(AT)等。在目前核工业上还有目视检测、检漏检测等。 3、无损检测的目的: 应用无损检测技术,是为了达到以下目的 A、保证产品质量。应用无损检测技术,可以探测到肉眼无法看到的试件内部的缺陷;在对试件表面质量进行检验时,通过无损检测方法可以探测出许多肉眼很难看见的细小缺陷。 B、保障使用安全。即使是设计和制造质量完全符合规范要求的设备,在经过一段时间使用后,也有可能发生破坏事故,这是由于苛刻的运行条件使设备状态发生变化,由于高温和应力的作用导致材料蠕变;由于温度、压力的波动产生交变应力,使设备的应力集中部位产生疲劳;由于腐蚀作用使材质劣化;这些原因有可能使设备中原来存在的制造规范允许的缺陷扩展开裂,或使设备中原来没有缺陷的地方产生新生的缺陷,最终导致设备失效。而无损检测就是在用设备定期检验的主要内容和发现缺陷最有效的手段。 C、改进制造工艺。在产品生产中,为了了解制造工艺是否适宜,必须事先进行工艺试验。在工艺试验中,经常对工艺试样进行无损检测,并根据检测结果改进制造工艺,最终确定理想的制造工艺。如,为了确定焊接工艺规范,对焊接试验的焊接试样进行射线照相,并根据检测结果修正焊接参数,最终得到能够达到质量要求的焊接工艺。 D、降低生产成本。在产品制造过程中进行无损检测,往往被认为要增加检查费用,从而使制造成本增加。可是如果在制造过程中间的环节正确地进行无损检测,就是防止以后的工序浪费,减少返工,降低废品率,从而降低制造成本。 一、射线检测基础知识 射线的种类很多,其中易穿透物质的X射线、γ射线、中子射线三种。这三种射线都被用于无损检测,其中X射线和γ射线广泛用于锅炉压力容器压力管道焊缝和其他工业产品、结构材料的缺陷检测,而中子射线仅用于一些特殊场合。 射线检测是工业无损检测的一个重要专业。最主要的应用是探测试件内部的宏观几何缺陷(探伤)。按照不同特征可将射线检测分为许多种不同的方法,例如使用的射线种类、记录的器材、探伤工艺和技术特点等。 射线照相法是指X射线或γ射线穿透试件,以胶片作为记录信息的无损检测方法,是最基本、应用最广泛的一种射线检测方法。 1、射线照相的原理: 射线照相法是利用射线透过物质时,会发生吸收和散射这一特征,通过测量材料中因缺陷存在影响射线的吸收来探测缺陷的。X射线和γ射线通过物质时,其强度逐渐减弱。一般认为是由光电效应引起的吸收、康普顿效应引起的散射和电子对效应引起的吸收三种原因造成的。射线还有一个重要性质,就是能使胶片感光,当X射线或γ射线照射胶片时,与普通光线一样,能使胶片乳剂层中的卤化银产生潜象中心,经过显影和定影后就黑化,接收射线越多的部位黑化程度越高,这个作用叫做射线的照相作用。因为X射线或γ射线使卤化银感光作用比普通光线小得多,所以必须使用特殊的X射线胶片,还使用一种能加强感光
ASME射线评片要点
焊缝射线检测通用工艺规程 ASME 规范篇(节选) 3.6.3像质计型号 使用SE-747中规定的1A、1B、1C线型像质计;特殊情况下也可使用JB4730中规定的R10系列像质计。常见透照厚度范围两种像质计钢丝线径和线编号的对应情况见表3.3。 3.7 透照厚度和像质计的选用 3.7.1部分透照范围应达到的像质计灵敏度见表3.3。 3.7.3 像质计的放置 线型像质计应放在射线源一侧的工件表面上被检焊缝区的一端(被检区长度的1/4左右部位)。金属丝应横跨焊缝并与焊缝方向垂直,且细丝置于外侧。当射线源一侧无法放置像质计时,也可放在胶片一侧的工件表面上,但可识别像质计的线编号应通过对比试验,使实际像质计灵敏度达到规定的要求。 像质计放在胶片一侧工件表面上时,应附加“F”标记以示区别。 像质计的放置原则见表3.5 在允许的底片黑度范围内,底片上被测量处的黑度与像质计灵敏度指定钢丝处的底片黑度,
b F b d Ug -= 当两者黑度变化超过-15%或+30%时,超差区域应放置像质计重新拍片。 由于工件原因造成底片黑度变化较大时(如管子环缝非中心法透照),应在底片有效评定区范围内允许黑度的最大部位和最小部位处各放置一个像质计,以测定不同黑度下的底片灵敏度。 3.7.4 像质计的观察 在底片上黑度均匀的部位能够清晰地看到长度不小于10 mm 的连续金属丝影像时,则认为该金属丝是可被识别的。 搭接标记的安放位置见表3.6 3.9.3 几何不清晰度规定 几何不清晰度由下式决定: 式中: Ug ——几何不清晰度,mm ; d ——焦点尺寸,mm ;
b Ug db F m in += b ——工件厚度,mm ; F ——焦距,mm 。 3.9.4 焦距F 、一次透照长度 L3 和最少透照次数 N 的计算 3.9. 4.1 纵缝透照(平板状工件) 最小焦距F min 由下式确定: 最少透照次数N min :不设定,所需透照次数按底片黑度进行控制。 在可以实施的情况下,应尽可能采用单壁透照技术。为了证实能充分覆盖,应进行足 够次数的曝光 3.9.4.2 环缝透照 a. 小径管(管子外径Do ≤89mm)双壁双影透照 最少透照次数N min : 1. 椭圆成像:N min =每个接头至少要进行二次互成90°的曝光。 2. 垂直成像:N min =每个接头至少要进行三次互成60°或120°的曝光。 b. 双壁双影透照时的最小焦距F min : 不同规格的小径管其透照时的最小焦距应不小于表3.9中的数值。 为便于现场使用,b 可近似看成管子外径Do ,而f (焦点到工件表面的距离)则用b 的倍数 来表示,焦距 F min = f + b 。(表中b 未包括余高,如精确计算则 b=D O + 双侧余高。) 表3.10 部分小径管双壁双影透照时的最小f 3.9. 4.3. 除小径管双壁双影外其它环缝透照:
特种设备无损检测相关知识(简答)
特种设备无损检测相关知识 三、问答题 1.简述应力腐蚀及其形成的特定条件? 答:由拉应力与腐蚀介质联合作用而引起的低应力脆性断裂称为应力腐蚀。 形成的特定条件: (1)受压元件承受拉应力的作用。 (2)具有与材料种类相匹配的特定腐蚀介质环境。 (3)材料应力腐蚀的敏感性与钢材成份、组织及热处理有关。 2.钢材的脆化现象有哪几种? 答:1、冷脆2、热脆3、氢脆4、苛性脆化5、应力腐蚀脆性断裂 3.钢中氢主要有哪些来源? 答:1、冶炼过程中溶解在钢水中的氢,在结晶冷凝时没有能即时逸出而存留在钢材中; 2、焊接过程中由于水分或油污在电弧高温下分解出的氢溶解入钢材中; 3、设备运行过程中,工作介质中的氢进入钢材中; 4、钢试件酸洗不当也可能导致氢脆。 4.何为消应力退火及消应力退火的目的? 答:消应力退火是将工件加热到A c1以下100~200℃温度,保温一定时间后缓慢冷却,以获得接近平衡状态组织的热处理工艺。 其目的是:消除焊接、冷变形加工、铸造、锻造等加工方法所产生的内应力,同时还能使焊缝中的氢较完全地扩散,提高焊缝的抗裂性和韧性,改善焊缝及热影响区的组织,稳定结构形状。 5.何为正火及正火的目的? 答:正火是将工件加热到A c3或A cm以上30~50℃,保持一定时间后在空气中冷却的热处理工艺。其目的是:细化晶粒,均匀组织,降低内应力。 6.什么叫奥氏体不锈钢的晶间腐蚀?如何防止? 答:晶间腐蚀是奥氏体不锈钢常见的破坏形式,晶间腐蚀沿晶界进行,使晶界产生连续性的破坏,这种腐蚀开始于金属表面,逐步深入内部,直接引起破裂。 措施是:①选用低碳、超低碳和加钛或铌的奥氏体钢种 ②通过热处理,如固溶处理和稳定化处理提高抗晶间腐蚀的性能。 7.什么叫冲击韧度?冲击韧度值如何获得?影响冲击韧度值的因素? 答:冲击韧度—-是指材料在外加冲击载荷(突然增加的载荷)作用下断裂时消耗能量大小的特性,抵抗冲击载荷作用破坏的能力。 冲击韧度通常是在摆锤式冲击试验机上测定的,冲击韧度ak=Ak/SN。 影响冲击韧度值的因素有: (1)试样的尺寸(承受外加冲击载荷作用的面积) (2)试样缺口的形式 (3)试验温度 (4)材料的化学成分,冶金质量,组织状态,内部缺陷等。
江苏省射线二级复证考试评片技巧
底片上各种非缺陷影像的识别 ⑴伪缺陷的识别 ①底片表面的机械损伤和表面附着污物:如划痕、擦伤、指纹、折痕、压痕、水迹等,特征是底片表面有明显可见的损伤和污物。 ②化学作用引起的,如漏光、受曲静电、药物沾染,银粒子流动,霉点等,特征是底片上伪显示分布与缺陷有明显的不同。 ⑵底片上焊缝区域黑色圆形影像的分析 ①可能性分类: Ⅰ.气孔和点状夹渣 Ⅱ.弧坑(凹坑、内凹) Ⅲ.显影液飞溅斑 Ⅳ.压痕 Ⅴ.水迹 Ⅵ.银粒子流动 Ⅶ.霉点 ②主要特征和区分方法: Ⅰ.气孔、点渣略 Ⅱ.弧坑(凹坑、内凹)略 Ⅲ.显液飞溅斑:主要特征是圆形圆点外侧有一个黑度偏淡的圈圈。 Ⅳ.压痕:黑度大、形态不规则,底片表面黑影处局部变形明显可见。 Ⅴ.水迹:外貌如同水滴" ",轮廓模糊,边界黑度淡而可见,向中心逐渐减小(有时并会增大),表面明显可见污物(水垢)堆集。 Ⅵ.银粒子流动:呈弥散状的细小而均匀的黑点,分布面广,并出现在多张底片上。 Ⅶ.霉点:分散范围广,影像细小,黑度均匀,底片表面有霉烂开花现象。 ③.底片上焊缝区域黑线的分析 Ⅰ.可能性分析: a.裂纹 b.未熔合 c.未焊透 d.错口 e.线状气孔 f.咬边 g.擦 伤、划痕 h.金属增屏折裂 Ⅱ.主要特征和区分方法: a.裂纹、未熔合、未焊透、线状气孔、错边、咬边等略。 b.擦伤划痕:多为细而光滑的黑线,底片表面开口痕迹明显可见。 c.增感屏折裂:在底片上多为宽窄变化较大的黑色线纹,大多出现在底片的端部和边缘,重现性大,可能在数张底片上出现同一形态的影像。 ④.底片上出现白色的影像分析 Ⅰ.可能性分类 a.夹钨、夹铜和夹珠 b.焊瘤和塌漏 c.金属飞溅 d.垫板与母材之间的熔渣 e.潜影受挤压衰退 f.定影液飞溅或显影液中气泡所致斑 g.金属增感屏断裂和缺损 h金属增感屏凹凸不平。 Ⅱ.主要特征和区分方法; a.夹钨、夹铜、夹珠、金属飞溅、焊瘤和塌漏等略。
射线检测评片考试
射线检测评片考试内容简介 1评片考核内容 每人评定10张焊缝透视底片,其中有一张小径管双壁双影椭圆成像底片。时间60分钟。评定结果记录在评片考核记录表上。 2评片考核记录表格式 见另一Word文档《RT评片报告a》。 3评片记录表填写注意事项 以下内容系辅导老师整理仅供参考,以考委会规定为准。 3.1“底片编号”及“工件厚度”按底片左上角的标签顺序填写。 3.2“焊接方法”、“焊接位置”和“焊接形式”的填写 焊接方法、焊接型式和焊接位置需要根据对底片上影像的识别,逐项填写。 ⑴“焊接方法”根据考核底片判断后,手工焊填写“手”,自动焊填写“自”,既有自动焊又有手工焊填写“自+手”。 ⑵“焊接位置”和“焊接型式”根据考核底片判断后,在相应栏内打“√”。 3.3“可识别的最小线编号”填写所观察到的最细金属丝号,等径像质计填写所 标明的像质计丝号。 3.4“缺陷评定”栏中缺陷性质用符号表示:裂纹为A,未熔合为B,未焊透为 C,条形缺陷为D,圆形缺陷为E。 3.5“缺陷性质”、“定量”及“缺陷位置”的填写见下页图示例。 3.6小径管双壁双影评定时,应指出缺陷在源侧还是胶片测。 4有关注意事项 4.1当底片上同时存在危害性缺陷(裂纹、未熔合、未焊透)和非危害性缺陷(圆形 缺陷、条形缺陷)时,只评危害性缺陷。 4.2当底片上同时存在圆形缺陷和条形缺陷时(不存在危害性缺陷),要分别对两 者最严重处进行定性、定量和定位,并以最严重级别评级。 4.3底片两端有搭接标记时,评定搭接标记范围内的缺陷;底片两端无搭接标记 时,底片两端20mm范围内不评定。
未熔合 定义:未熔合是指焊缝金属与母材金属可焊缝金属之间未熔化结合在一起的缺陷。 影像特征:根部未熔合的典型影像是连续或断续的黑线,线的一侧轮廓整齐且黑度较大,为坡口或钝边的痕迹,另一侧轮廓可能较规则,也可能不规则。根部未熔合在底片上的位置就是焊缝根部的投影位置,一般在焊缝的中间,因坡口形状或投影角度等原因出可能偏向一边。坡口未熔合的典型影像是连续或断续的黑线,宽度不一,黑度不均匀,一侧轮廓较齐,黑度较大,另一侧轮廓不规则,黑度较小,在底片上的位置一般在中心至边缘的1/2处,沿焊缝纵向延伸。层间未熔合的典型影像是黑度不大的块状阴影,开关不规则,如伴有夹渣时,夹渣部位黑度较大。一般在射线照相检测中不易发现。 裂纹 ?定义:裂纹是指材料局部断裂形成的缺陷。 ?影像特征:底片上裂纹和典型影像是轮廓分明的黑线或黑丝。其细节特征包括:黑线或黑丝上有微小的锯齿,有分叉,粗细和黑度有时有变化,有些裂纹影像呈较粗的黑线与较细的黑丝相互缠绕状;线的端部尖细,端头前方有时有丝状阴影延伸。 未焊透与未熔合在X射线底片上的特征 未焊透的特征未焊透在X射线底片上呈连续或断续的较规则的黑线。但由于未焊透形成的部位不一致,或其间伴有夹渣或气孔,黑度变化可能深浅不一,都分布于焊缝根部,双面焊则于中间交接处。由于接头母材的加工面未被完全熔透,因此缺陷边界清晰。 未熔合的特征未熔合在X射线底片上常模糊不清,只有当射线透照方向垂直于未熔合面时,才有较深的黑化度,颜色深浅较均匀。层间未熔合多出现在厚板多层焊的焊缝中,其特征与片状夹渣相近;边缘未熔合在正常照相底片上位于焊缝宽度约1/3处,多呈月牙形,外边平直,内侧呈弧形,黑度逐渐变浅。当沿坡口方向透照时呈黑色条纹,分布于焊缝与母材交界处,较易发现。
承压设备特种设备无损检测相关知识
《承压设备特种设备无损检测相关知识》 第一部分金属材料及热处理基本知识 一,材料性能:通常所指的金属材料性能包括两个方面: 1,使用性能即为了保证机械零件、设备、结构件等能够正常工作,材料所应具备的性能,主要有力学性能(强度、硬度、刚度、塑性、韧性等),物理性能(密度、熔点、导热性、热膨胀性等)。使用性能决定了材料的应用围,使用安全可靠性和寿命。 2,工艺性能即材料被制造成为零件、设备、结构件的过程中适应的各种冷、热加工的性能,如铸造、焊接、热处理、压力加工、切削加工等方面的性能。 工艺性能对制造成本、生产效率、产品质量有重要影响。 二,材料力学基本知识 金属材料在加工和使用过程中都要承受不同形式外力的作用,当达到或超过某一限度时,材料就会发生变形以至于断裂。材料在外力作用下所表现的一些性能称为材料的力学性能。 承压类特种设备材料的力学性能指标主要有强度、硬度、塑性、韧性等。这些指标可以通过力学性能试验测定。 1,强度金属的强度是指金属抵抗永久变形和断裂的能力。材料强度指标可以通过拉伸试验测出。抗拉强度σb和屈服强度σs是评价材料强度性能的两个主要指标。一般金属材料构件都是在弹性状态下工作的。是不允许发生塑性变形,所以机械设计中一般采用屈服强度σs作为强度指标,并加安全系数。 2,塑性材料在载荷作用下断裂前发生不可逆永久变形的能力。评定材料塑性的指标通常用伸长率和断面收缩率。
伸长率δ=[(L1—L0)/L0]100% L0---试件原来的长度L1---试件拉断后的长度 断面收缩率φ=[(A1—A0)/A0]100% A0----试件原来的截面积A1---试件拉断后颈缩处的截面积 断面收缩率不受试件标距长度的影响,因此能够更可靠的反映材料的塑性。 对必须承受 强烈变形的材料,塑性优良的材料冷压成型的性能好。 3,硬度金属的硬度是材料抵抗局部塑性变形或表面损伤的能力。硬度与强度有一定的关系,一般情况下,硬度较高的材料其强度也较高,所以可以通过测试硬度来估算材料强度。另外,硬度较高的材料耐磨性也较好。 工程中常用的硬度测试方法有以下四种 (1)布氏硬度HB (2)洛氏硬度HRc(3)维氏硬度HV (4)里氏硬度HL 4,冲击韧性指材料在外加冲击载荷作用下断裂时消耗的能量大小的特性。 材料的冲击韧性通常是在摆锤式冲击试验机是测定的,摆锤冲断试样所作的功称为冲击吸收功。以Ak表示,Sn为断口处的截面积,则冲击韧性ak=Ak/Sn。 在承压类特种设备材料的冲击试验中应用较多。 三金属学与热处理的基本知识 1,金属的晶体结构--物质是由原子构成的。根据原子在物质部的排列方式不同,可将物质分为晶体和非晶体两大类。凡部原子呈现规则排列的物质称为晶体,凡部原子呈现不规则排列的物质称为非晶体,所有固态金属都是晶体。 晶体部原子的排列方式称为晶体结构。常见的晶体结构有:
最新射线评片技巧(一):气孔、夹渣、夹钨射线底片影像特点
射线评片技巧(一):气孔、夹渣、夹钨射线底片影 像特点 2015-04-17 分类:解决方案阅读(4103) 评论(0) 按照JB/T4730-2005《承压设备无损检测》第2部分射线(点击链接下载:NB/T47013.1~13-2015标准)检测篇介绍,焊接接头中的缺陷按性质区分为裂纹、未熔合、未焊透、条形缺陷和圆形缺陷五类。在《射线检测评片》栏目中将介绍该五类性质的缺陷成因、缺陷评片技巧、评级方法,分享在工作中遇见的射线检测案例。本文介绍圆形缺陷(气孔、密集气孔、夹渣、夹钨)评片技巧和缺陷定量评级。 一、圆形缺陷的评片 缺陷长宽之比小于等于3(L/N<=3),且非裂纹、未焊透和未熔合危害性缺陷。对接接头焊缝常见的圆形缺陷包括圆形气孔、非金属夹渣、夹钨等性质缺陷。 圆形缺陷示意图 1、气孔 (1)气孔成因 在《焊缝气孔形成机理及超声检测波形特性》文中详细介绍了焊缝气孔形成的原因。气孔分为单个气孔和密集性气孔。气孔降低了焊缝的金属致密性,降低焊接接头的强度、韧性等力学性能。 (2)气孔射线成像特点 气孔内部充满气体,射线穿过气孔几乎不会形成材质衰减。在射线底片上气孔呈暗色斑点,中心黑度较大。单个气孔边缘较浅平滑过渡,轮廓规则较清晰,密集气孔成团状。气孔大多是球形的,也可以有其它形状,气体的形状与焊接条件密切有关。
单个气孔缺陷 密集性气孔 2、非金属夹渣 (1)夹渣成因 焊缝夹渣形成原因主要有以下几点: ?在焊接每层焊道层间清渣不干净; ?焊接电流过小、焊接速度过快; ?焊接操作过程不当; ?母材坡口设计加工不当; ?液态金属冷却速度过快等; 第一条是焊缝产生夹渣的直接原因,第二到第五条原因是由于焊渣在液态金属中浮渣不及时而残留在焊缝中。焊缝中存在非金属夹渣,当焊缝承受应力过程中在夹渣周围会形成裂纹扩展,裂纹发展到一定程度焊缝开裂。夹渣严重降低了焊接件强度、韧性等力学性能。 (2)夹渣射线成像特点 焊缝金属包裹着非金属夹杂物形成夹渣、射线穿过夹渣有一定的衰减,但远远小于焊缝金属对射线的衰减。射线底片上夹渣呈暗色斑点,黑度分布无规律,轮廓不圆滑不规则,小点状夹渣轮廓较不清晰。 非金属夹渣 3、夹钨 (1)夹钨成因
射线评片技巧(三):焊缝未熔合射线底片影像特点
2015-04-19?分类:?阅读(1933)?评论(0)? 根据GB6417-1986《金属熔化焊焊缝缺陷分类及说明》定义未熔合,在焊接过程中由于焊缝金属与母材金属未完全熔化结合,或者焊道金属与焊道金属之间未完全熔化结合产生的缺陷称为未熔合。本文讲述未熔合缺陷的分类、焊缝未熔合危害、焊缝未熔合的产生原因、焊缝未熔合在射线底片影像上的特征缺陷,以及讲解工作中射线检测的焊缝未熔合缺陷底片。 一、未熔合分类 焊缝未熔合可分为层间未熔合、坡口未熔合(侧壁未熔合)、根部未熔合,如下图所示为三类焊缝未熔合的示意图。未熔合常出现在焊缝根部形成根部未熔合、在焊道间层形成层间未熔合、在焊道和母材坡口之间形成坡口未熔合,以及在焊缝和母材溢流或焊瘤之间等位置。 坡口未融合示意图 层间未融合示意图 根部未融合示意图 二、未熔合危害 未熔合是一种面积型缺陷,坡口侧未熔合和根部未熔合明显减小了承载截面积,应力集中比较严重,其危害性仅次于裂纹。 三、未熔合的产生原因 (1)焊道清理不干净,存在油污或铁锈; (2)坡口设计加工不合理,液态金属流动有死角; (3)焊接电流过小,焊丝未完全熔化; (4)焊枪没有充分摆动,焊接位置存在死角; (5)焊工为了加快焊接速度,擅自提高电流等。 四、未熔合射线底片影像特征 (1)根部未熔合:典型影像是连续或断续的黑线,靠近母材侧影像轮廓整齐呈直线状且黑度较大,为坡口或钝边的机械加工痕迹。靠近焊缝中心测未熔合影像的轮廓可能较规则,也可能不规则,呈曲齿状的块状缺陷。 根部未熔合在底片上的位置就是焊缝根部的投影位置,若射线垂直焊缝透照,则缺陷一般在焊缝影像的中间。若斜角度透照或者母材坡口形状不对称(开单边坡口)可能偏向一边。 (2)坡口未熔合:典型影像是连续或断续的黑线,宽度不一,黑度不均匀,一侧轮廓较齐,黑度较大,另一侧轮廓不规则,黑度较小,在底片上的位置一般在中心至边缘的1/2处,沿焊缝纵向延伸。 坡口未熔合示意图和底片影像 (3)层间未熔合的典型影像是黑度不大的块状阴影,形状不规则,如伴有夹渣时,夹渣部位黑度较大。 层间未熔合与分层缺陷相似,在射线透照方向上透照厚度差较小,一般在射线照相检测中不易发现。 以下是未熔合缺陷影像
无损检测与射线评片
无损检测与射线评片 1、什么是无损检测? 无损检测是在不破坏或损伤被检物体的条件下检查被被检测物体的状态的一种检测工艺方法。 2、无损检测的目的 ①、改进制造工艺②、降低制造成本③、保证产品质量④、确保设备安全运行 3、常规无损检测方法及代号 ①、射线检测(RT)②、超声波检测(UT)③、磁粉检测(MT)④、渗透检测(PT) ⑤、电磁(涡流)检测(ET) 除此之外,《特种设备无损检测人员考核与监督管理规则》还规定了以下两种方法的考核要求:⑥、声发射(AE)⑦、热像/红外(TIR) 4、无损检测方法的应用特点 ①选择合理的检测方法 工件材质 加工工艺和缺陷类型 质量要求 ②选择合理的检测时机 缺陷出现时机 工件表面状态 ③综合运用无损检测方法 缺陷类型和特征 检测方法的特点和适用性 二、无损检测方法及应用 1、射线检测(RT) 1)射线检测用的射线X射线γ射线中子射线 2)X射线和γ射线的性质 X射线和γ射线与可见光一样属于电磁波。主要性质: ·不可见,以光速沿直线传播 ·能穿透可见光不能穿透的物质 ·穿透物质时能被物质吸收和散射而发生衰减。 ·能使气体电离 ·光化学效应,能使胶片感光 ·荧光效应,能使某些荧光物质发荧光 ·生物效应,能杀死有生命的细胞 3)射线检测方法 按记录方式不同分为 -射线照相法 -荧光屏成像法 -气体电离法 -电视成像法 按射线源不同分为 -X射线探伤法 -高能X射线探伤法
-γ射线探伤法 4)射线照相法原理 射线穿透物质时,其强度会由于物质的吸收和散射而发生衰减,衰减的程度取决于物质厚度和密度。当物体中存在缺陷时,由于缺陷部位的厚度和密度发生变化,穿过无缺陷完好部位和有缺陷部位的射线强度不同,因而使胶片的感光程度不同,胶片处理后,就形成了黑白不同的影像。 5)射线检测主要设备器材 射线源:X射线机、高能X射线机、γ射线机、X射线胶片、增感屏、象质计、铅标记、胶片处理设备 6)射线照相法适用范围 适用于检查各种金属和非金属材料和工件的内部缺陷,常用于铸件和焊缝。 7)射线照相法的特点和局限性 优点: -不受材料及表面状态限制,适用广泛。-检测结果直观。-定性定量容易。 -底片可永久性保存 局限性: -检测成本高,检测速度慢。-检测灵敏度与材料厚度相关。-对细微的密闭性裂纹和未熔合类面状缺陷可能漏检。-射线对人体有害,需安全防护。 2、超声波检测(UT) 1)声波、超声波和次声波 机械振动在弹性介质中的传播叫机械波,机械波按振动频率分为声波、超声波和次声波。 次声波:频率≤20Hz,人耳听不到 声波:频率>20—20000Hz,人耳能听到 超声波:频率>20000Hz,人耳听不到 2)超声波的主要特性 -具有良好的方向性,可定向发射 -传播过程中会因扩散和介质吸收和散射而发生衰减 -在异质界面上能产生反射、折射和波型转换 -频率高能量高,在大多介质中传播能量损失小,穿透厚度大。 3)超声波的类型 按介质质点振动方向分类: ①、纵波:介质质点振动方向与传播方向平行的波。在固、液、气中传播; ②、横波:介质质点振动方向与传播方向垂直的波。只在固体中传播; ③、表面波:沿固体表面传播的波(靠表面的质点椭圆振动)。 ④、板波:在板厚与波长相当的薄板中传播的波(两表面质点椭圆振动,中间层平行或垂直振动)。 超声波检测方法 4)按原理分类:
射线底片评定技术(评片基本要求部分)
主讲人:夏福勇 主讲人简介 夏福勇,教授级高级工程师。原杭州市特种设备检测研究院副总工程师,现任杭州市锅炉压力容器技术协会秘书长,全国特种设备无损检测人员资格考核委员会考评人员,中国无损检测学会教育培训和科普工作委员会委员。持具有特种设备行业RTIII、UTIII、MTIII、PTIII级资质以及锅炉、压力容器、压力管道检验师(原高级检验师)资质;完成省部级涉及无损检测、特种设备检验科研项目七项,参加起草国家总局安全技术规范四部,出版著作三部,获得实用新型专利四项,在国内外发表专业论文二十余篇。获得过国家质检总局科技兴检奖等。 主要内容 一、底片评定的基本要求 1.底片质量要求 2.评片环境、设备等要求: 3.评片人员要求 4.相关知识要求 一、底片评定的基本要求 评片工作一般包括下面的内容: 1)评定底片本身质量的合格性; 2)正确识别底片上的影像; 3)依据从已知的被检工件信息和底片上得到的影像信息,按照验收标准或技术条件对工件质量作出评定; 4)记录和资料。 1.底片质量要求 (1)灵敏度:从定量方面而言,是指在射线底片可以观察到的最小缺陷尺寸或最小细节尺寸;从定性方面而言,是指发现和识别细小影像的难易程度。在射线底片上所能发现的沿射线穿透方向上的最小尺寸,称为绝对灵敏度,此最小缺陷尺寸与透照厚度的百分比称为相对灵敏度。用人工孔槽,金属丝尺寸(像质计)作为底片影像质量的监测工具而得到的灵敏度又称为像质计灵敏度。 要求:底片上可识别的像质计影像、型号、规格、摆放位置,可观察的像质丝号是否达到标准规定要求等,满足标准规定为合格。 (2)黑度: 为保证底片具有足够的对比度,黑度不能太小,但因受到观片灯亮度的限制,底片黑度不能过大。 底片黑度测定要求:按标准规定,其下限黑度是指底片两端搭接标记处的焊缝余高中心位置的黑度,其上限黑度是指底片中部焊缝两侧热影响区(母材)位
无损检测相关知识复习题[1]
无损检测相关知识复习题 一、单项选择题 1、下述指标中,哪个不属于材料的力学性能?(D) A、强度 B、塑性 C、韧性 D、热稳定性 2、长期承受交变应力的构件,最可能产生的破坏形式是(C) A、脆性断裂破坏 B、失稳破坏 C、疲劳破坏 D、蠕变破坏 3、衡量材料抵抗冲击载荷作用时断裂的力学性能指标是(C) A、强度 B、塑性 C、韧性 D、硬度 4、因应力腐蚀而产生的缺陷通常是(A ) A.表面裂纹; B.密集蚀孔; C.导致严重减薄的蚀坑; D.以上都是; 5、制造承压类特种设备所用的低碳钢属于(C) A.共析钢; B.过共析钢; C.亚共析钢; D.以上都对; 6、钢的C曲线位置右移即意味着(A ) A.淬硬组织更容易出现; B.等温转变所需时间更短; C.转变组织的塑性韧性相对较好; D.以上都不对; 7、淬火加高温回火的热处理称为(C ) A.退火; B.正火; C.调质; D.消氢处理; 8、含碳量小于或等于多少的碳素钢称为低碳钢(C ) A.0.15%; B.0.20%; C.0.25%; D.0.3%; 9、如欲使工件具有一定的强度,同时又有较高的塑性和冲击韧性,即有良好的综合机械性能,应采用的热处理方法是(D) A.退火; B.不完全退火; C.正火; D.调质; 10、合金总量在多少以下的合金钢称为低合金钢(C ) A.0.5%; B.2%; C.5%; D.10%; 11、低碳钢中不属于杂质的元素是(A) A. Fe和C B. Mn和Si; C. S和P; D. N和H; 12、以下哪一元素加入钢中能显著提高钢的高温强度,减少回火脆性(D )
A. Mn; B. Si; C. Ni; D. Mo; 13、低合金钢焊接减少热影响区淬硬倾向的有效措施是(B) A 烘烤焊条 B 预热焊件 C 提高焊速 D 焊后热处理 14、下列哪一因素不是导致冷裂纹产生的原因(D) A 焊缝和热影响区的含氢量B热影响区的淬硬程度 C 焊接应力的大小D焊缝中低熔点共晶物的含量 15、电渣焊焊缝进行超声波探伤应在(D) A 焊接36小时后B焊接24小时后 C消除应力热处理后D正火处理后 16、下列焊缝缺陷中属于面积性缺陷的有(C) A 气孔 B 夹渣 C 裂纹D夹钨 17、下列哪一种缺陷危害性最大( D) A 圆形气孔 B 未焊透 C 未熔合 D 裂纹 18、下述有关焊接变形和焊接应力的叙述,错误的是(B) A 使焊件上的热量尽量均匀可减小焊接变形和焊接应力 B 减少对焊缝自由收缩的限制可减小焊接变形和焊接应力 C 焊接线能量越大,产生的焊接变形或焊接应力亦增大 D 采用焊前预热和合理的装配焊接顺序可减小焊接变形和焊接应力 19、下述有关咬边缺陷产生原因的叙述,哪一条是错误的(C) A 焊接电流太大 B 焊条与工件角度不对 C 运条速度太快 D 直流焊时发生磁偏吹 20、坡口不清洁,有水、油、锈,最有可能导致的焊接缺陷是(A ) A、气孔 B、夹渣 C、未熔合 D、裂纹 二、填空题 1、过冷度是结晶的必要条件。 2、Ni 和Mn 是改善钢在低温下变脆现象的最有效的合金元素。 3、影响低温韧性的因素有晶体结构、晶粒尺寸、冶炼的脱氧方法、 热处理状态、钢板厚度、合金元素,其中以合金元素 的影响最为严重。
焊缝射线评片规律1
焊缝射线评片规律 一、探伤人员要评片,四项指标放在先*,底片标记齐又正,铅字压缝为废片。 二、评片开始第一件,先找四条熔合线,小口径管照椭圆,根部都在圈里面。 三、气孔形象最明显,中心浓黑边缘浅,夹渣属于非金属,杂乱无章有棱边。 四、咬边成线亦成点,似断似续常相见,这个缺陷最好定,位置就在熔合线。 五、未焊透是大缺陷,典型图象成直线,间隙太小钝边厚,投影部位靠中间。 六、内凹只在仰焊面,间隙太大是关键,内凹未透要分清,内凹透度成弧线。 七、未熔合它斜又扁,常规透照难发现,它的位置有规律,都在坡口与层间。 八、横裂纵裂都危险,横裂多数在表面,纵裂分布范围广,中间稍宽两端尖。 九、还有一种冷裂纹,热影响区常发现,冷裂具有延迟性,焊完两天再拍片。 十、有了裂纹很危险,斩草除根保安全,裂纹不论长和短,全部都是Ⅳ级片。 十一、未熔合也很危险,黑度有深亦有浅,一旦判定就是它,亦是全部Ⅳ级片。 十二、危害缺陷未焊透,Ⅱ级焊缝不能有,管线根据深和长,容器跟着条渣走**。十三、夹渣评定莫着忙,分清圆形和条状,长宽相比3为界,大于3倍是条状。 十四、气孔危害并不大,标准对它很宽大,长径折点套厚度,中间厚度插入法。 十五、评定区内有多种,圆形条形分别评,2类相加减去Ⅰ,其它缺陷不可用。 十六、气孔长径要注意,大于T/2为Ⅳ级, 深孔造方评片定,定为深孔即Ⅳ级 。 十七、评片要想快又准,下拜焊工当先生,要问诀窍有哪些,焊接工艺和投影。注:*四项指标系底片的黑度、灵敏度、清晰度、灰雾度必须符合标准的要求。 **指单面焊的管线焊缝和双面焊的容器焊缝内未焊透的判定标准。T为公称厚度—既受检工件名义厚度,不考虑材料制造偏差和加工减薄。