各种连铸连轧生产线的比较
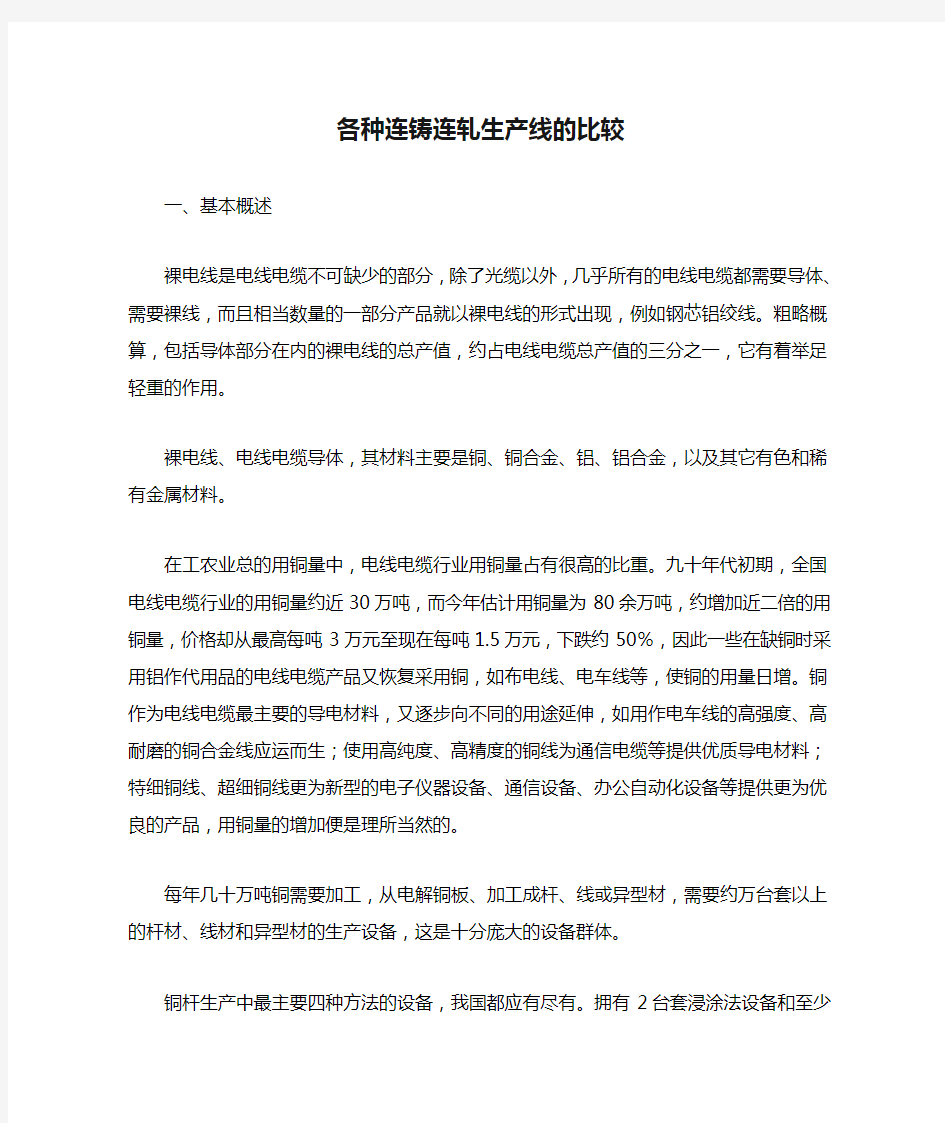

各种连铸连轧生产线的比较
一、基本概述
裸电线是电线电缆不可缺少的部分,除了光缆以外,几乎所有的电线电缆都需要导体、需要裸线,而且相当数量的一部分产品就以裸电线的形式出现,例如钢芯铝绞线。粗略概算,包括导体部分在内的裸电线的总产值,约占电线电缆总产值的三分之一,它有着举足轻重的作用。
裸电线、电线电缆导体,其材料主要是铜、铜合金、铝、铝合金,以及其它有色和稀有金属材料。
在工农业总的用铜量中,电线电缆行业用铜量占有很高的比重。九十年代初期,全国电线电缆行业的用铜量约近30万吨,而今年估计用铜量为80余万吨,约增加近二倍的用铜量,价格却从最高每吨3万元至现在每吨1.5万元,下跌约50%,因此一些在缺铜时采用铝作代用品的电线电缆产品又恢复采用铜,如布电线、电车线等,使铜的用量日增。铜作为电线电缆最主要的导电材料,又逐步向不同的用途延伸,如用作电车线的高强度、高耐磨的铜合金线应运而生;使用高纯度、高精度的铜线为通信电缆等提供优质导电材料;特细铜线、超细铜线更为新型的电子仪器设备、通信设备、办公自动化设备等提供更为优良的产品,用铜量的增加便是理所当然的。
每年几十万吨铜需要加工,从电解铜板、加工成杆、线或异型材,需要约万台套以上的杆材、线材和异型材的生产设备,这是十分庞大的设备群体。
铜杆生产中最主要四种方法的设备,我国都应有尽有。拥有2台套浸涂法设备和至少700余台套的上引法机组用于生产无氧铜杆,保守估计,设备年生产能力在180万吨至200万吨;从德国、美国、意大利引进的铜铸轧机组超过10台套,加上国产的连铸连轧机组,光亮铜杆的生产能力至少为50万吨至60万吨;至于原有常用的横列式轧机轧制黑铜杆,加上用水平连铸法制作型材的坯料,其年生产能力不低于30万吨至50万吨。也就是说,我国拥有的生产设备中,无氧、低氧铜杆的年生产能力在220万吨至250万吨左右。加上黑铜杆生产能力,将超过300万吨。由于乡镇企业的大量出现,一些简易的生产铜杆的方法,也就无法在此估计之中。80万吨的需要量和250万吨无氧、低氧铜装机能力之间,存在着很大的距离,因此相当大的部分设备就不得不处于减产或停产状态,以700余台套上引法机组为例,估计约1/3至1/4的机组由于各种原因而处于停产状态,而1/2的机组的产量尚未达到原设计的生产能力,但即使如此,由上引法机组生产的铜材,仍占有我国铜杆用量的半璧江山,起着重要的作用。
我国铜线拉线机约在万台左右,至少有一半是由电工机械厂制造的,少量由国外引进,这二部分设备的性能都较优,特别至九十年代中后期,国产大、中、小拉采用连续退火的水平,已与国外设备逐步靠近,差距大大缩小了。然而在乡镇企业中仍有土拉线机,这些机器能耗高、劳动强度高、效率低、粗糙,难以加工质优的产品,这部分设备数量估计约为总数的一半,需要给予彻底改造或弃之不用。
裸电线中大量采用铝,例如:铝绞线及钢芯铝绞线。九十年代初期,用铝量每年尚不超过20万吨,以后随着经济的增长逐年增加,由于以前国家在电力系统的政策上是重发电轻送电,使送电的增长赶不上发
电的增长速度。近年来开始的城市电网和农村电网改造,使送电的增长速度急剧加快,兼之九十年代开始建设的大型电站,像二滩电站、黄河小浪底电站和长江三峡电站,将相继逐步建成,送电便成为电站建设以后的重中之重,送电工程建设步入本世纪以来最辉煌、最灿烂的黄金时代。作为送电线路建设的最重要器材,铝绞线及钢芯铝绞线、铝包钢芯铝绞线的产量剧增。能提供500kV重要工程用的主要生产厂家,产量处于爆满程度,创下了历史最高纪录,预计今年输电线的产量为50万吨以上,可能达到60万吨。此外,我国钢芯铝绞线在电线电缆产品的出口中占有重要地位,因此在计入产量时,出口量是不能忽略的。
全国拥有80台套以上的铝连铸连轧机,除少量机组由国外引进外,主要由国内生产。近二年,每年可望新增约10台套。80台套机组将拥有生产80万吨以上铝杆的能力,能制成120万吨钢芯铝绞线;此外,利用原有半连续浇铸机生产方锭,用横列式轧机轧铝杆的生产方式和水平引铸铝杆方法,粗略估计,这二种方法尚可生产20万吨至30万吨的钢芯铝绞线。全国铝杆的生产能力远大于实际所需的数量,在主要生产厂任务十分饱满的情况下,其它有些工厂的连铸连轧机年产才只有1千至2千吨,尚未发挥应有效益,给企业带来不少麻烦。
我国至少拥有400台至500台铝线拉线机,绝大多数为国产的集线式拉线机,从五十年代开始使用以来,几乎没有什么本质上的改进,与国外现代拉制铝线的高速拉线机相比,差距是明显的。国内拥有为数不多的由国外引进的铝线高速大拉机,在生产中均发挥主力作用。国产的铝线高速大拉机,正在积极发展之中。在乡镇企业的小工厂中,低效的单模拉线机仍有一定数量,应予及早更换、改造或淘汰。
铝绞线及钢芯铝绞线的生产,由于工序较少,所以在价格组成中,主要是材料和动力。在供大于求的情况下,工厂之间竞相压价,使产品的利润很低,有时甚至达到无利可图的地步,这必须引起全行业的关注。
在重视送电的今天,单单依靠增加产量并不能增加工厂多大的效益,主要还是提高产品的技术含量,生产优质产品。九十年代中期,我国从英国引进的铝包钢生产线,制造优质的铝包钢线,结合500kV送电线路的建设,铝包钢芯铝绞线已作为重要的线种正在被越来越广泛的应用,现在四家生产优质铝包钢线的工厂,正成为提供高质量输电线的厂家,有着较好的经济效益和社会效益。高强度铝合金导线以其优良的特性,在国外已获得十分广泛的应用,然我国用量尚少。从技术经济比较结果证明,从线路建设、线路运行都有着良好的效果,因此可以预料,在五年后,我国高强度铝合金导线的年需要量,可能达到3万至4万吨,目前我国只有3家能生产高强度铝合金导线的工厂,生产能力约1万吨,那么未来的数年间可能会出现数家生产高强度铝合金导线的工厂,这是一个值得注意的新的经济增长点。
天使有残缺
2007-7-23 18:15:50
二、技术进步
1. 铜
⑴铜杆制造技术当前最主要的有四种,分别生产不同材质的铜杆。生产含氧量在20ppm以下的无氧铜杆,采用浸涂成型法和上引冷轧法;采用连铸连轧法制造的铜杆为光亮铜杆;采用铸锭、回线式(或称横列式)轧制的铜杆为黑铜杆。这四种方法生产铜杆,我国应有尽有。
六十年代末,美国通用电气公司开发浸涂成型法(Dip-forming)新工艺制造铜杆。浸涂成型是利用冷铜杆吸热的能力,用一根较细的冷纯铜芯杆(或称种子杆),垂直通过一只能保持一定液位高低的铜水池,使铜水与该移动的种子杆表面铜熔合在一起,并逐步凝固结合成较粗的铸造状态铜杆,然后经冷却、热轧、冷却、绕制成圈,整个过程是在封闭的、有惰性气体保护下进行的。哈尔滨电缆厂引进了浸涂法设备后,生产出质量优良的含氧量在20ppm以下的铜杆,在八十、九十年代中为该厂获得良好声誉与经济效益。
七十年代初,芬兰的Outokumpu公司成功的采用上引冷轧法制造无氧铜杆。它是利用一种管式铜套(即石墨结晶器)其下端伸入并浸没在熔化的铜液面下,上端与真空泵连通,开始时将结晶器内空气抽出,在真空作用下,使管内产生负压,铜液徐徐吸引向上,并在引升器附近很快凝固成光亮铸锭。然后经冷轧或冷拉成杆。上引法生产的铜杆含氧量在10ppm以下,表面光亮。自八十年代初,我国由芬兰引进上引法生产铜杆的机组以后,以上海电缆研究所为主对上引组仿制并国产化,获得很大成功。目前上引法铜产量占有我国用铜杆数量的一半。上海电缆研究所生产的上引法机组,产量世界第一,且由于质优价廉而畅销国内外。这是九十年代铜杆生产的很大成功。
国际上铜的连铸连轧生产线主要有:意大利的Properzi系统(缩称CCR系统)、美国的South Wire 系统(缩称SCR系统),德国的Krupp/Hazelett系统(缩称Contirod系统)、以及法国的SECIM系统。这些系统在原理上基本相同,其差别主要在铸机和轧机的形式和结构上。CCR系统采用双轮铸机和Y型轧机,对大截面锭子,在原轧机前加两平一立辊机架,箱式孔型。SCR系统采用一大四小的五轮铸机,平立辊连轧机,箱-椭-圆系统。Contirod系统与SCR基本相同,但铸机改为“无轮双钢带式”,即Hazelett 式。SECIM系统采用一大三小的四轮式连铸机,箱-扁-圆、扁-扁-圆系统。我国拥有CCR、SCR和Contirod 的铜连铸连轧机十余台,其中产量高的年产10万吨铜杆,而且这些连铸连轧机生产出来的铜杆质量都十分好,特别像Contirod系统生产的铜杆,深受用户喜爱,而且有很大的出口份额。我国还自己设计制造铜连铸连轧机,但采用者较少。
常规的、传统的铜杆生产法,是把铜液铸成船形锭后再加热,经横列式(或称回线式)轧机轧制而成黑铜杆。这种铜杆表面发黑有一层氧化皮,长度又受到铜船形锭重量的限制,含氧量超过200ppm至500ppm,因此影响以下工序加工的性能,特别拉细线时更受影响。拉线时断线事故更易发生。
现对上述四种方法生产的铜杆作一个比较:
浸涂成型法:能生产大长度光亮无氧铜杆、导电率为101~102%IACS,含氧量20ppm以下,铜杆圈重3.5~10吨。
上引冷轧法:能生产大长度光亮无氧铜杆、导电率为101~101.6%IACS,含氧量10ppm以下,铜杆圈重2吨。
连铸连轧法:能生产大长度光亮低氧铜杆、导电率为101~102%IACS,含氧量200~300ppm,铜杆圈重达5吨。
回线轧制法:生产短长度有氧化皮的黑铜杆,导电率为99.5~100.5%IACS,含氧量200~500 ppm,铜杆圈重只有86~136公斤。(因受船形铜锭重量的限制)
在欧洲曾对上述四种方法的下道工序和拉线结果进行调查。我国在九十年代中期为发展耐冷冻漆包线,对漆包线用铜材材质和加工工艺立题研究,经过大量的对比试验得出了几乎与欧洲试验相同的结论:用浸涂法生产的铜线断线的次数很少;用连铸连轧法生产的铜杆,由于含氧量适中,因此它的缺点很少,其中用Contirod法生产的铜杆,比SCR法或CCR法生产的铜杆更软,延伸率好,表面质量很好;用回线轧制法生产的铜杆,在拉制小直径的铜线时断头率高。上引冷轧法生产的铜杆质量也很好,但应防止在生产时渗入较多的废铜线或其它旧铜料而影响本来是良好质量的铜杆。
⑵用低品位铜生产优质铜杆如上所述,电线电缆行业每年需要用数十万吨铜,而且都要用高品位铜,如果能从工艺上或配方上给予合适处理,采用较低品位的铜或渗入一定数量的废铜线、杂铜,而仍能生产出优质铜杆,这将能获得巨大经济效益。为达到上述目的,九十年代我国已经采用二项措施,进行开发研究,这二项措施是:
①采用稀土优化处理改善铜杆材质我国稀土金属藏量极丰,在电工铝的研究中就采用稀土优化处理
的方法,获得成功。江苏近年就立题研究,在低品位的铜中加入适量的稀土,提高铜杆的质量,经初步试验,已证明有这种可能,现在尚未获得最终结论,一旦成功,将是一个很大成果,有着巨大的经济意义;
②用橄榄炉熔铜、连铸连轧铜杆根据国外有关的资料介绍,用橄榄炉熔铜、连铸连轧铜杆时,可以渗入比例较大的适当废铜线或较低品位的铜,而轧出优质铜杆。九十年代中期,上海电缆研究所在山东开始这项试验工作,目前熔铜、连铸连轧机组全部制作完成,并开始轧出铜杆。机组性能和铜杆质量仍需进一步完善。当这项成果达到预期的目标以后将可以用较为低廉的成本生产出优质铜杆,使铜杆生产技术向前提高一大步。
⑶特种铜线制造技术
①电气化铁路接触网用接触线中国经济发展的地区趋向是北上西移,电气化铁路将起着很大作用,电气化列车向高速、重载发展,对接触线的材质和品种提出更高的要求。高速铁路,时速在200公里以上,京沪高速铁路初定时速350公里,近期按300公里实施,因此应有合适的接触线。
八十年代我国提供给铁路部门的电气化列车接触线,有纯铜线和钢铝电车线,由于技术上的原因只能提供单根长度不大于2000m的产品。以后采用浸涂法、上引冷轧法或连铸连轧法能提供大长度铜杆坯料,冶金行业能提供大长度型钢坯料以后,电车线的单根长度便达到和超过3000m,这是九十年代能提供的正式产品,为高速列车提供优质产品迈出一大步。
在九十年代我国又开发多种铜合金电车线,例如:CTHA-120银铜线,抗拉强度365N/mm2,导电率96.6%IACS;CTHB-120锡银铜线,抗拉强度367.5N/mm2,导电率90.0%IACS;CTHC-120锡银铜线,抗拉强度375.8N/mm2,导电率85.0%IACS;CTHB-120锡铜线,抗拉强度360.8 N/mm2,导电率70.0%IACS;CGLN-250钢铝线,抗拉强度216N/mm2,导电率46.3%IACS。但所有这些线种的参数与京沪高速列车要求的接触线性能:抗拉强度≥600 N/mm2,导电率≥80%IACS仍有较大距离,需要重新研制,以满足要求,其中采用复合金属可能是最可行的方案。
②电气设备用细铜线电磁线是电机、电器、家用电器、电子和通讯等产品的主要配套原材料,也是使用高质量铜线的大户,随着家用电器的更新换代,电子通信行业的高速发展,对漆包线、漆包线铜材要求更趋严格,也就是在九十年代通过对各种铜杆、铜线生产工艺和材质的筛选,使之能生产优质的漆包线。
细线和超细漆包线主要用于家电类,以1998年为例,电视机,3500万台需5万吨,21000台电风扇需6.43万吨,720万台冰箱和700台空调机需2万吨,1500万台洗衣机需1.55万吨,4200万台电动工具需
2.1万吨,10亿只扬声器约0.1万吨,收录机、音响设备等7.15亿只需
3.58万吨,2579万台袖珍收放机、
3.2亿只耳塞和送话器等需0.1万吨,15000万部电话机需0.06万吨,8.12亿电子手表需135吨,其它像脱排油烟机、吸尘器、电磁灶、微波炉、VCD等,还有电器控制柜中的接触器、继电器等,包括Ф0.04~Ф0.02mm的微细线总计3.5~5万吨。如此庞大数量的细和超细漆包线需要大量的优质铜线,用Contirod 法和浸涂法生产的铜杆、铜线将是首选的材料,而且应该特别严格把握住工艺过程。
天使有残缺
2007-7-23 18:16:15
⑷铜型材
①软铜扁线电机和变压器用绕组需采用软铜扁线,一般采用铜锭或铜杆经轧制、拉拔成型后,退火处理,这种方法生产的铜扁线较硬,回弹较大,线圈较难做得服贴;另一种方法采用挤压机挤压,但受挤压锭重量的限制,长度较短,在制造线圈时要焊接接长;上引法虽能制造大长度扁线,但因其是铸态组织,仍需经拉拔与热处理;近年浙江绍兴采用国产的Conform机组,用上引法铜杆经摩擦挤压后制造软铜扁线,表面光滑,性能均匀。这是国际上最新的制造法,能获得质量优良的产品,工艺上还需要进一步完善。
②空心导线双水内冷发电机的绕组用空心导线,需求有高的导电率、韧性、大长度,璧厚均匀等,以前采用挤压机穿孔挤压的方法获得坯料,经拉拔、热处理制为成品,但往往不能全部保证技术条件,所以只能向美国西屋公司购买。上海电缆研究所利用上引法制造管坯,经拉拔、热处理后获得成品,性能良好。在九十年代开创了这一新工艺,填补了优质空心导线国产化的空白,也为制造优质管材开辟了新途径。用上引法制造的空心导线已用于双水内冷发电机中,并获得满意效果。
⑸黄铜线用上引法制黄铜杆,与加工纯铜方法相同拉成黄铜线,方法简单、方便,是九十年代采用的一个新的加工方法。
2. 铝
⑴铝杆制造技术如上所述,铝杆的制造有三种方法,以竖炉熔铝、连铸连轧生产铝杆的方法最为先进,用得最为普遍,然而此法自六十年代诞生以来,很少有本质上的改进,但随着工业发展对铝杆的质量有更高要求后,特别用于制造高强度铝合金时就需要有更大改进。
九十年代初期至现在先后对制造铝杆的连铸连轧机组进行改进,其主要改进有:
①采用倾动式保温炉代替原有平炉,这样可以保证每一次开炉时能炉内的铝水倾倒倒干净,使每一炉的化学成份都获得满意的结果,这对于制造铝合金更为重要;
②连铸机由二轮式改为四轮式,使铸锭离开浇铸轮时不会发生扭转,保证进入轧机时平直、不偏斜。浇铸轮的冷却系统,采用四面都能冷却,喷嘴的流量可以调节,冷却水液面成扇状,使铸锭冷却十分均匀;
③用新式的辊型布置取代以前统一Y型结构;前二道为二辊式平立辊结构,以后各道仍有Y型结构,这样保证在前二道时有较大的、足够的压下量,因此铸锭的截面可以适当加大,铝杆能获得充分变形、性能较优;
④由于铸锭的截面适当加大,兼之有可能轧制高强度铝合金杆,这种杆强度较高、变形抗力较大,因此加大轧机主机的电机功率;
⑤铝杆制造时,铝液需要精炼除气,把对铝中有害的氢气排除,一般均采用熔剂精炼,这种除气的方法还不够彻底,现加上连续精炼除气装置,在熔剂精炼之后,铝液连续通过精炼装置,通入氯、氮混合气体,去除氢气,提高铝杆质量。
尽管通过上述的措施对铝杆生产进行改进,设备上仍存在一些问题,最明显的是尚无法进行全自动的双盘收线,这对下道工序仍带来麻烦。制造铝杆除了工艺装置以外,重要的还在于如何获得性能优良的电工铝杆,而且这项技术是应该结合中国国情的。
⑵稀土优化综合处理制造电工铝我国每年需要用几十万吨铝用作电线电缆产品,而我国的铝矿中因含硅量较高,缺少足够数量的电工铝锭,从八十年代开始,上海电缆研究所在研究电工铝导体时,利用我国丰富的稀土资源,对普通级铝锭进行处理,达到电工级的水平,这就是所谓稀土优化综合处理技术制造电工铝。
稀土优化综合处理技术是在电缆厂的生产条件下,采用铝连铸连轧机组,生产电工铝杆,然后通过拉制、绞制、生产出机电性能达到国际标准的电工铝线和由电工铝线绞制的架空导线。稀土优化综合处理方法的核心技术,包括稀土优化、硼化处理和控铁处理。稀土优化是降低杂质硅对导电率的有害作用,硼化主要针对减少钛、钒、锰、铬杂质对导电率的有害影响,控铁是少降低导电率、不影响耐腐蚀条件下以增加铝基的强度。这三种手段可根据材料来源不同,分别单独使用或组合应用,在于达到制造电工铝导体的结果。
自从采用稀土优化综合处理制造电工铝以来,社会上出现了一种误解,并通过某种场合和方法,规定500kV线路甚至200kV线路用导线非用“稀土铝导线”才行,这种误解是有害的,它模糊了很多科学的概念,应该给予纠正。经稀土优化综合处理制造的铝导体被宣传为“稀土铝导线”,其实加入稀土只是一种手段,在于通过综合处理以后使普通铝锭能制造出达到电工级铝导体的水平。所以在误导的舆论中认为的“稀土铝线”能提高了导电率,其实只是使普通铝锭制造的铝线达到了电工级水平,即导电率≥61%IACS,或电阻率≤0.028264Ω·mm2/m,与电工铝的标准一样,没有提高。舆论中认为“稀土铝线”能提高强度,其实为使普通铝导体达到电工铝导体的导电率所加入的稀土是很少的,在这样的稀土含量下,稀土铝线的强度并不比普通铝线和电工铝线高,只是达到了对电工铝线的强度要求。“稀土铝线”的耐腐蚀性能好也是一个含湖不清的概念,其比较的对象应该是电工铝线而不是普通铝线,其次要视不同的环境而定,在架空线中首先腐蚀的并非是铝线,而是钢芯,因此才出现了轻防腐、中防腐和重防腐钢芯铝绞线,在不同的场合下使用。
用非电工级铝锭,通过稀土优化综合处理,能生产出用电工铝锭才能生产出的导电率达61%IACS及以
上的电铝线;在生产中灵活应用,可改善金属加工的工艺性能,提高成品率;在普通铝锭由于铁硅比不够或倒置致使难于顺利生产的情况下,应用烯土优化处理可以顺利解决问题;可充分利用电缆厂工艺废铝制造铝-稀土中间合金再生用于生产。
稀土优化综合处理方法,使铝锭经处理后能获得电工级铝导体的各种性能,这个方法是我国独创的,从八十年代开始至九十年代,我国大部分生产铝导体的工厂都掌握了这种方法,使我国几十万吨的性能提高了一个新的水平。
⑶铝合金线及其制造技术在国际上,铝镁硅型的高强度铝合金导线已被使用七十余年的历史,由于它具有的优点和对其生产工艺的不断改进,使它更具有实际使用价值。在欧洲,以法国为代表,在输电线路上大量采用,占线路总长的绝大部分;日本采用铝合金的输电线路在50%以上;美国和加拿大也有很大的比例;即使东南亚发展中的国家,像印度、印度尼西亚、菲律宾等也都采用铝合金用于导线输电线路。
如果把全铝合金绞线与钢芯铝绞线作比较的话,在相同的单位重量下,铝合金导体的直流电阻小,载流量大、拉力大,拉力单重比大等优点;在具有相同载流量条件下比较,铝合金导线的重要轻,拉力大,拉力单重比更大等优点。兼之铝合金导线为单一材料的导线,易安装施工。它所具有的优点表现在线路建设中可加大档距,减少杆塔数目,或降低杆高度,总之它能降低工程造价,因此受到电力部门的欢迎。
我国自六十年代中期起,开始大规模系统的研究铝合金导线,从研究工艺配方、流程、专用设备、测试技术、架设运行等,历时30余年,积累了大量经验。并形成我国独特的若干技术。然而,在中国高强度铝合金导线并没有得到广泛的应用,而只局限于某些场合使用,究其原因,最主要的是合金性能不够稳定且价格偏高。所以产生这个原因是:在六十年代中期之后建设起来的铝合金生产工厂,在七十年代初的一场天灾中被毁灭,至七十年代中期重建另一家铝合金工厂时,又碰上那个年代,不可能拥有世界上生产铝合金的先进技术装备,这个局面维持至九十年代中期。
九十年代中期新建设的铝合金工厂中,生产设备采用了当代的新设备,又引入我国独特先进生产技术,生产的产品不仅能满足标准上的要求,而且有较大的裕度,深受用户好评。主要的技术进步有:
①铝连铸连轧除了采用倾动式保温炉、炉外连续除气精炼装置以外,还增加连续淬火装置,使生产铝杆的工序,连续地一次完成;
②连续式高速大拉机,使铝合金线拉制时不发生扭转。高速拉线的热量还将得到利用;
③连续时效炉,该炉有极高精度的炉温控制系统,并利用拉线机余热,热量获得充分利用;
④采用稀土处理,具有中国独创的特色。
在上述基础上,在九十年代末期,又在原有基础上进行改进,更具现代化,其技术进步有:
①采用特殊制造的铝合金连铸连轧机组,在总结以前优点基础上,增加了快速加热装置,使铝锭在进入轧机时保持恒温。增加了轧机前后的温度测量和显示装置,保证铝合金锭在轧制时处于最佳状态。良好的收线装置,使铝合金杆缠绕服贴,为下工序创造条件;
②高速拉线机与时效炉采用自动的轨道联接;
③连续时效炉,上下料采用机械手,炉温自动显示并能随意调整。
使用这些措施后,铝合金导线的品质将更料优良,更加稳定。当成批生产时,价格明显下降,这二点正好克服铝合金导线在中国采用受限制的弱点。
除铝镁硅型高强度铝合金以外,还发展了耐热铝合金。耐热铝合金共有二种型号,其导电率分别为58%IACS和60%IACS,抗拉强度为160N/mm2,长期工作温度为150℃。耐热铝合金导线用于电站、变电站;特别在城市改造时可用作增容导线,便于对老线路进行改造。铝合金另一个发展方向是高强度耐热铝合金,高强度高导电铝合金。总之铝合金品种已在我国形成系列,主要的问题是如何进一步在工程中推荐应用。
我国拥有生产高强度铝合金的专门工厂,从九十年代中期起生产铝合金质量完全符合IEC,ASTM和GB 标准中所规定的项目,性能良好。目前上海筹划建设另一家专门生产铝合金导线的工厂,将为电力行业提供优质铝合金线,预计2000年可供应。
④铝型材电线电缆行业中的铝型材主要有:作为电缆线芯的扇形截面型材,作变压器用的扁线,作输电线用的拱形、Z形、人头形等型材。它们的长度需要数公里而无接头,电缆线芯还应为软线。这些产
品,通常是采用铝杆经辊压、拉制的方式制成,软线需经退火,这类产品表面都容易被擦伤。
七十年代,英国原子能局发明用摩擦方法制造铝材以后,以专利形式出让给英国BWE公司和HOLTON公司,二家公司先后都制成连续挤压机,即Comform机组,除都能挤压型材,采用径向挤压。BWE公司又开发了单轮双槽轮机组,HOLTON公司则开发双轮单槽机组,均可进行切向挤压,生产双金属线材或型材。我国八十年代后期开始,分别由二家公司提供约近20台套Comform机组,用于生产大长度型材,管材和双金属线材等,使我国生产铝型材的水平,一步便跨入世界先进行列。在引进国外设备基础上,我国自行开发Comform机组,能生产各种型材,其性能指标与国外设备相接近,现已有10余台套国产机器在使用。
天使有残缺
2007-7-23 18:16:38
3. 复合金属
⑴铝包钢线铝包钢线是一种双金属线,用连续挤压生产的铝包钢线有8μm厚的钢铝结合渗透层,结合力非常好;此外,包覆铝层后的高强度钢丝经双金属同步变形机深拉拔,其机械性能非常高;由于包覆的电工级铝层均匀牢固,因而耐腐蚀性能非常好;铝包钢线由于钢丝表面包覆的铝层,它的导电率比镀锌钢线优越得多,故电能损耗低,载流量大等各种优点而受到青睐。
铝包钢线特别适合于作大跨越导线、架空地线、避雷通讯线、输电线路的自阻尼线等。铝包钢线具有直流电阻小,绞线中铝包钢线的铝包层与铝接触不会产生电化腐蚀等优点,适用于容量大,有盐雾的海岸地带和有So2气体等的工业区作输电线路用导线;成批生产铝包钢线在500kV线路等重要工程中将用来取代镀锌钢线而被广泛使用。
八十年代开始,英国BWE公司研制成功采用Comform摩擦挤压机制造铝包钢线,生产的产品全面达到IEC 1232及ASTM B 415所规定的性能指标,是目前国际上最先进的生产方法。八十年代中期起天津大成五金厂按Comform机的工作原理,自行研制简易的Comform机制造铝包钢线,其产品的性能比压接法略优,但从生产效率、产品质量与国外的差距仍十分明显。1992年常州电线电缆厂率先从英国BWE 公司引进Comform机组和意大利的双金属同步变形机制造铝包钢线,其后邢台电缆厂、天津大成五金厂、江西新华金属制品厂均引进这种设备,制造铝包钢线及其延续的产品:铝包钢绞线和铝包钢芯铝绞线,其产品不单在国内各电压等级110kV、220kV、330kV、500kV上使用,而且远销国外,用于高压与超高压线路中。目前全国年产能力约为1.5万吨。
铝包钢线已形成系列,主要的技术性能:
直径:Φ1.24~Φ5.5mm
导电率:20.3%IACS;27%IACS;30%IACS;40%IACS。
用作架空线线芯的铝包钢线,Φ1.24~Φ3.25mm时,则其抗拉强度:σb≥1340Mpa;1%伸长率应力:σ1%≥1200Mpa。
铝包钢线还作为光纤复合架空地线的承力元件,其导电率为20.3%IACS,由于强度和短路电流容量的不同要求,往往也采用导电率为27%IACS、30%IACS和40%IACS。用作光纤复合架空地线的铝包钢线除圆截面以外,还可以是扇形截面。铝包钢线还可用作日用品和其它工业品,像金属网,公路护栏,衣架和挂钩等。上述这些产品,在九十年代起已经逐步被采用,特别在光纤复合架空地线中已成为不可缺少的材料。
优质的铝包钢线均采用BWE公司提供的Conform机组、意大利的双金属变形机制造,目前设备的易损件和各种备品备件、生产时所用的润滑液、拉拔粉等都在逐步国产化中。大连铁道学院已仿造BWE公司的Conform机组,制成国产的Conform机组,该机组已能挤压各种铝型材,但对于制作铝包钢线还在开发之中。
⑵铜包钢线铜包钢线是一种在钢线芯材表面包上铜的双金属线材。一般铜层的包覆比为13%~35%,导电率为21%IACS~40%IACS。
铜包钢线的主要用途是:可用作电力传输和电话线路的架空线;用于载波线路时与铜线具有同样的传输效果;在山区寒冷地带及农村用作架空电话线时,能承受冰冻负荷和大风冲击、架设跨距比铜线大一倍;
小直径铜包钢线可在电子工业中用作各种电子器件的引线、天线;用作同轴电缆、射频线圈、地球物理线等;在电气化铁道中用作讯号和通信线、讯号连接线、埋伏线、补偿线、屏蔽线、接地线、载流承力索、不载流承力索、滑接线等。由于铜包钢线的广泛用途,九十年代以来用量日增,效益明显。
铜包钢线主要有六种制造方法:铸造热压法、电镀法、热浸涂法、上引涂法、焊接包复法、连续挤压法(即Conform法)。铸造热压法工艺落后,材料利用率低,质量差,该法将淘汰。电镀法优点是设备占地小,制造长度长,但只能做导电率20%IACS~30%IACS各种规格铜包钢线,目前是国内大量生产铜包钢的方法。缺点是电镀液造成较严重公害,且制造大于30%IACS导电率较困难。热浸涂法是利用浸涂法制造铜杆设备制作,它可调整铜层厚度且能制成异型线,例如双钩形电车线,适宜大批量生产且无公害,缺点是小批量生产不经济。上引涂法是利用上引法设备制造铜包钢线,目前正在进行试验,生产工艺及装备尚不成熟。焊接包复法是铜带经过清洗处理后包复在光洁的钢线上,用氩弧焊捍接,之后经拉丝机、压力模深加工成型,这种工艺能获得不同导电率铜包钢线,性能优良,目前国内正在试产,即将可投入应用。连续挤压法是一种很好方法,能进行连续不断生产,钢、铜结合力好,目前国内外均停留在试验室试产中,尚未达到商业化阶段。
⑶铜包铝线铜包铝线是在铝芯线上同心地包覆铜层的双金属线。它是代替纯铜线制造CATV同轴射频电缆的良好内导体。由于集肤效应,在电视频段内具有与纯铜相同及更优的传输性能。铜包铝线的密度是纯铜的37%~40%,也即是在相同的条件下,铜包铝线的长度是纯铜线的2.45~2.7倍,可大大节约用铜;其次,同样长度的铜包铝线的电缆比纯铜轻,因而运输、安装都方便,降低敷设费用;第三,当CATV 同轴射频电缆用铝管作外导体时,由于铜包铝线与铝管的热膨胀和弹性模量相接近,从而提高电缆的稳定性和可靠性。
铜包铝线的重量较铜轻,还用于电焊机电缆、电池连接线、野战电缆、电机和变压器的绕组。细铜包铝合金线用作移动电话、办公用品设备的绕组线或连接线;它与纯铜一样具有良好的焊接或接续性能,是布电线线芯的良好材料;大截面的铜包铝制成排类,可在高频电器设备中应用。
铜包铝的优良特性在七十年代以来已被广泛重视,美、日、德、瑞典等国都在充分利用其特性。我国在九十年代也大力开展铜包铝的生产与应用。
铜包铝生产方法主要有三种:电镀法、焊接包复法及静液挤压法。目前国内已能用电镀法及焊接包复法生产铜包铝线,它的工艺均与铜包钢相似,目前国内仍属起步阶段。静液挤压法是瑞典ASEA公司设备,由于投资高未获推广,包复法及静液挤压法还可生产铜包铝排。
⑷镀锌钢线镀锌钢线是钢芯铝绞线的重要原材料,按IEC 888的规定,镀锌钢线按强度分有一般强度、高强度和特高强度。八十年代,我国用作钢芯铝绞线的钢线,几乎都是一般强度的钢丝,进入九十年代,冶金行业相继制成高强度和特高强度的钢丝,并已进入实用化阶段。镀锌钢线分一般镀锌和重镀锌之分。由于重镀锌钢线只有少数工厂能制造,而使用较少。为了提高镀锌钢线的耐蚀性,在钢芯铝绞线中采用涂防腐油的方法而较少用重镀锌钢线。
为了提高钢丝的耐蚀性能又不降低钢丝强度,国际上公认的有两种镀层配方可供使用。其一为含铝55%、硅1.6%、锌43.4%称为“Galvelume”,它具有高的耐蚀性能,但影响钢基体的力学性能。其二为含铝5%及微量稀土元素称“Galfan”,它兼有优良耐蚀和力学性能,用于钢丝行业,它的耐蚀性比镀锌钢线高2倍。
我国金属制品行业于八十年代末期开始约7~8家工厂开发锌5%铝稀土镀层钢丝,至九十年代中期只剩下2家工厂正式提供产品,其中一家采用单镀工艺,尽管镀层能提高耐蚀能力2~3倍,但镀层太薄有漏镀现象使实际上提高耐蚀能力有限而难以推广;另一家采用先热镀锌后再镀锌铝稀土合金,确保镀层质量,与国际铅锌组织的标准相一致而被广泛采用。杭州万胜钢缆集团公司能提供这种产品,最近天津引进国外技术也将生产这一产品。
⑸镀锡铜线镀锡铜线主要用于橡皮绝缘的矿用电缆。软电线、软电缆和船用电缆等的导电线芯,以及用作绝缘电线电缆的外屏蔽编织层和电刷线。
镀锡铜线主要生产方法有热镀法,电解镀锡法、真空镀锡法、多线电解镀锡法和整股镀锡法等,上述
这些方法都已被采用,而以热镀法和电解镀锡法用得最普遍。热镀锡法的设备较简单,容易制作。而电解镀锡法需采用专用镀锡机,九十年代,上海电缆研究所研制的镀锡机已获得良好的应用。
除镀锡铜线以外,还有镀锡铜包钢线,铜包钢线作为电子原器件的引接线,经镀锡以后,提高了可焊性。
镀锡铜线已是一种较成熟的产品,但九十年代完善了专用生产工艺与设备,使生产更为顺利。而且由于市场的需要使产量增加,生产厂能获得较好的经济效益。
⑹镀银铜线镀银铜线仅用于特殊产品,例如航空工业用镀银铜电刷线,射频电缆导电线芯,氟塑料绝缘耐高温电线的线芯等。因为银比铜除具有更优良导电性和导热性外,更具有优良的耐腐蚀性和在高温下的抗氧化性。
九十年代计算机更为普及,其插接线也使用经压扁的镀银铜线。国内已能正式生产。
⑺镀金铜线作为现代电子仪器设备中需要特殊的引接线,镀金铜线便是其中重要的一种,镀金铜线线径为0.02mm,并进行漆包。这是九十年代新开发的产品。
⑻镀镍铜线镀铜线目前广泛应用于高温航空导线中,九十年代随着高温自控温电缆开发,这种线也将使用于125℃以上自控温电缆线芯中。
天使有残缺
2007-7-23 18:17:04
4. 架空线
经过半个世纪的努力,全国35kV以上输电线路已达60万公里,其中110kV和220kV线路27万公里,330kV和500kV线路2100公里,线路建设规模和增长速度世界罕见。
加强各大区联网,正在建设的项目很多,500kV长距离线路及西北330kV主干线路已接近1万公里,随着长江三峡工程的起动,预计今后十年新增超高压线路总量将会超出以往二十几年所建总长的两倍。
我国发电装机容量已超过26000GW列世界第二位,本世纪末将达到30000GW,2020年达80000GW。电网建设赶不上装机容量的增长,电源效益得不到充分发挥,也影响到国民经济持续发展和人民生活的提高,因此电网建设将是电力建设中的重中之重。近年对城市电网和农村电网改造为线路建设带来了难得的大好时机。不单产量增加,新品种也得到充分应用。
⑴大截面导线长江三峡送往华东第一回直流输电工程,输送容量为300万千瓦,电压等级±500kV, 全线路径长890公里,将采用LGJ-720/50的钢芯铝绞线或相对应的铝包钢芯铝绞线,结构45/4.53的电工级铝线,成盘供货,单根长度为2500米。这种大容量、大截面、大长度导线为架空线生产前所未有,现在组织攻关中。
大截面导线的制造应有一整套配套措施,生产电工铝线的技术,特别对于大直径铝线更应从严把好质量关;连铸连轧和拉线技术;此外还应拥有630型54盘的大型绞线机和相应的绞线技术,才有可能完成大截面导线的制造。在九十年代末期,能为长江三峡输电工程大批量的提供大容量、大截面导线,使我国架空线制造水平和制造能力提高到一个崭新的水平。
⑵大跨越导线我国水能和煤炭资源多集中于西部和北部人口稀少、经济发展较缓慢地区,而东部、南部沿海地区,人口密集、经济发展迅速,电力需求量大,能源资源缺乏,因此大容量、远距离的西电东送和北电南送势在必行。在远距离的送电中线路要跨越江湖峡谷,需要大跨越导线。
长江三峡送电工程就跨越汉江和长江,需要千米级大跨越导线和特大跨越导线,这些跨越导线研制成功为送电线制造跨上一个新台阶。我国大跨越导线已用得不少,跨越长江的南京大跨越、芜湖大跨越、镇江大跨越等部分导线采用国产、部分导线采用进口的,经多年的运行都能满足要求,安全可靠。现在我国导线制造水平已进一步提高,能生产符合IEC标准的电工铝线,高强度铝合金线、铝包钢线和特高强度钢线,它为大跨越导线制造提供了必要的条件。
汉江大跨越,跨越档距1200m,属千米级大跨越,采用全铝包钢绞线。铝包钢线用导电率为40%IACS 的线种,制造仍有较大的难度,在攻关中。
长江东西梁山大跨越导线将采用特高强度镀锌钢芯高强度铝合金绞线。大长度导线成盘供应。特高强
度镀锌钢线和高强度铝合金线其技术指标均很高,代表着当前国际先进水平。长江东西梁山大跨越线路建设将显示我国超高压输电线路的建设水平,将又一项攀登世界之最,在这九十年代末年,世纪之交时完成这一重要创举,将为我国输电线路的制造和建设,谱写一幅崭新的编章,也为今后我国西电东送、北电南送、特高电压输电线路建奠定了基础。现在正组织科技人员在攻关中。
长江镇江大跨越,是当前世界最大的大跨越线路工程,跨越档距2303m,跨越塔高350m,是世界上最高的输电塔。与之相关的导线选型,力学特性研究防振动、防舞动措施,以及在塔上架设OPGW都是十分重要,是世界瞩目的输电线路项目。
⑶扩径导线由于500kV线路建设日增,变电站需要有更多的扩径导线规格品种可供选用,为此于九十年代初期设计研制了新型软母线系列,共有4个规格,截面积分别为630、800、1000、1250mm2,软母线外径扩大至按500kV双分裂雨天不出现电晕设计。新型软母线不采用金属软管支撑,使其强度高、耐腐蚀、使用寿命长,便于质量控制,并能提高T型接头的连接质量,保证安全运行。电站用软母线还可以用耐热铝合金制造,以增大载流量,在安徽繁昌变电站的1440mm2耐热铝合金绞线,就开辟了一个新的品种。
⑷自阻尼导线在架空线路中导线因微风振动破坏是其主要失效的形式,自阻尼导线是一种能自行吸收能量的新型导线,使导线的振动降至安全水平,且可以提高架线张力,简化防振措施。1988年开发后,架设于广西大化水电站至马山县那落岭的110kV线路,经九十年代长期运行,进行观察,情况良好,安全可靠。
⑸耐蚀防振导线架空线的另一失效的形式是因腐蚀而破坏,特别是钢芯腐蚀破坏。耐蚀防振导线是采用一个无缝铝管挤在钢芯外,钢芯外径和铝管内径中有间隙,它既起到完全保护钢线不锈蚀,又起到防振作用,使架空导线二种失效的主要原因给予解决。这一新型线种已在九十年代获得国家专利。
⑹低弧垂导线这是一种钢芯软铝绞线型的低弧垂导线。加在导线上的力通过特殊方式由钢芯承担一部分,使运行以后弧垂量不会明显增加,蠕变量也很小。架线施工和运行还需进一步完善。八十年代末期开发至九十年代初期完成的。
⑺扩容导线由于工农业发展,电力需要量增加,为扩大输电系统,国家对城市电网和农村投入巨资进行改造,对于输电线路除建设新的线路以外,希望在原有线路上仅仅更换导线而不改变原有线路和杆塔情况下,增加输送50%的电能,即输送原有线路150%的能量,这种新型导线就是扩容导线。
扩容导线仍以高强度镀锌钢线作内芯线,起承力作用;外挤一个软铝管,或用拱型线绞成的软铝管,管外绞上经热处理后的铝线。用特殊的方法使铝导体的应力移至钢中。导线载流通电后,尽管温度升高也不影响导线的强度,而弧垂量却很小,可以利用原有杆塔,输送原有150%的电能,达到扩容目的。
此项技术自城市电网和农村电网改造起动之后着手研制的,已全部通过了试验研究阶段,现在正组织工厂化生产和在线路中实际使用。
⑻铝合金绞线与钢芯铝合金绞线按IEC 61089的规定,铝合金导线有二个型号:A2和A3,它们分别代表着不同的导电率和强度,以电阻率表示如下:
A2 32.530nΩ·m(对应于53%IACS)
A3 32.840nΩ·m(对应于52.5%IACS)
铝合金线可以单独制成绞线使用,也可以利用镀锌钢线作加强芯,组成钢芯铝合金绞线,也可以作加强芯与铝线绞合在一起,组成铝合金芯铝绞线。这种不同的组合用于各不同的用途,可以自由选用。
A2的铝合金绞线,规格号由16~1250(其相对截面18.4~1439mm2);A3的铝合金绞线,规格号由16~1120(其相对截面为18.6~1301mm2)。铝合金绞线是使用频率最高的的一种形式。九十年代中期,我国出口至印度的铝合金绞线共4500吨,均为全铝合金绞线。
⑼铝包钢绞线及铝包钢芯铝绞线在电力系统中,铝包钢绞线作为地线已被接受并被推广使用,在重要工程中也不例外。长江三峡输电线路就选用AS-80(即80 mm2的铝包钢绞线作地线,汉江大跨越的地线为AS-185,长江大跨越地线为AS-250。在输电线则大力采用铝包钢芯铝绞线代替钢芯铝绞线,江苏电网中的500kV线路便推广采用铝包钢芯铝绞线,获得良好结果。
在电气化铁道中,载流承力索和不载流承力索广泛采用铝包钢绞线,已形成为一个定型的产品。
由于铝包钢线具有的特性,强度高、耐腐蚀、载流量大等优点,在IEC 61089标准中已被正式列入,包括铝包钢绞线、铝包钢芯铝绞线和铝包钢芯铝合金绞线。我国最近编制的国标“圆线同心绞架空导线”也同样把铝包钢线及其系列产品列入标准中。
⑽光纤复合架空地线(OPGW) 高效的电力输配系统需要有一个通讯网络,这个通讯网络便于有效保护信号传输、控制数据的传输、远距离测量、通话等。用光纤复合架空地线比过去的载波、电话电缆系统和微波系统更可靠,而且容量大、不串音、不受干扰及环境影响。
光纤复合架空地线,因光纤受到金属线和管的良好保护,可以形成可靠的最佳结构。这种地线可以设计成与现有地线相匹配,安装于铁塔上不会增加负荷,而且可以保持现有的间距。光纤复合架空地线取代现有的地线,相对来说,价格较高,然而架设完毕,通讯线路开通后,增加投资超出的费用,将会很快获得补偿,并将得到更高的回报。在电力系统中建立一个高效的通讯网络时,光纤复合架空地线将被首选推荐使用。
七十年代末期,英国、日本等先进的工业化国家把光纤复合架空地线在电力系统中使用,由于它优良的特性逐年增加,发展十分迅速。在日本,半数的高压输电线路已架设了光纤复合架空地线,全世界迄今已使用数十万公里。
上海电缆研究所在八十年代中期率先在国内开展光纤复合架空地线的研制工作,一九八八年架设第一条运行线路,迄今已超过十年。随着技术进步,在九十年代生产OPGW的主要关键技术都有突破性的进展,包括采用高强度单模光纤,无缝铝管的连续挤压技术,高强度、高模量的铝包钢线生产,使OPGW的制造技术跃进一个新的台阶。当关键技术解决后,对世界上先进国家的OPGW进行剖析和仿制,摄取各家公司产品优点,形成自己独特的结构,并针对各电压等级、不同的容量,推出一个系列,在国内推广使用,现已在110kV、220kV和500kV的十几个工程,包括220kV的上海浦东国际机场、500kV上海石洞口电厂使用,均获得满意的结果。并将向国外出口。上海电缆研究所是我国目前唯一的国产生产单位,能进行从设计、产品制造、金具与附件、线路施工、开通运行等一系列服务的单位。
世界上大约有二十几家公司能制造OPGW,但是各家公司有自己的技术规范而世界上没有统一的标准,为此,九十年代开始,国际电工委员会第七技术委员会第八工作组(即IEC TC7 WG8)制订光纤复合架空地线的性能要求和试验方法标准。上海电缆研究所作为中国代表以通讯成员的身份参加该组的工作,参予制订IEC 1396“光纤复合架空地线的电气、机械和物理性能要求与试验方法”标准。在此基础上,又制订了中国机械行业标准“光纤复合架空地线”,以规范OPGW产品及其性能。上海电缆研究所已按IEC 1396所规定的各种试验方法,在研究所内建立起目前我国唯一能测试OPGW全性能的综合试验室,对的质量监视,提供了有力的保证。
我国于1985年葛洲坝电厂引进英国BICC公司生产的2km OPGW以来,其OPGW的用量逐年增加,截至1998年已架设1000km以上。监于OPGW具有的种种优点,国家电网公司决定对新建的500kV线路将全部架设OPGW,各省地方电网也都大力推广应用,预计在今后五年内,每年都将有3000~4000km的OPGW需要架设,而且今后还会逐年递增。当二十一世纪信息社会到来时,它将会起着更加积极的作用。
天使有残缺
2007-7-23 18:17:20
三、未来十年的展望
1. 结合重点工程建设,开发新产品,满足工程需要
长江三峡工程、南水北调工程和高速电气化铁路是我国跨世纪的三项重点项目,应该结合重点工程,开发新产品,满足工程需要。
⑴长江三峡工程长江三峡工程中的输电工程,将是三峡工程中重中之重,500kV线路交直流混合送电,全长9100km,是一项极为重大的工程。由三峡向华东送电的三峡至常州±500kV直流送电工程已经起动,对于输电线来说,应该满足线路的需求,将包括主干线路用的大截面、大容量钢芯铝绞线、铝包钢芯铝绞线;也包括跨汉江的千米级大跨越,它将是全铝包钢绞线,长江大跨越则是世界瞩目的,它的跨距和塔高将是世界之最,特高强度镀锌钢线和特高强度铝合金线绞成的导线,标志着我国导线的制造水平;这
二个大跨越的地线,均采用铝包钢绞线,拉力单重比超过18km。这些导线技术要求都很高,线种又多,所以应积极配合工程建设,当工程建成时,导地线的制造水平将跃上一个新的台阶。
⑵高速电气化铁路主要配合工程,提供接触网用接触线(电车线)。按京沪高速列车速度,目前我国能生产的接触线,纯铜、铜合金、钢铝线的性能指标都不能达到要求,需重新进行开发。法国在时速300~350公里的接触网中采用锡铜-120接触线;德国在时速360公里的接触网中使用镁铜-120接触线;日本在时速300公里的接触网中使用GT-CSD-110铜包钢接触线。这几种接触线对于京沪高速列车接触网都可能被采用接触线,应结合工程起动研制。
2. 为信息社会提供优质产品
二十一世纪将是一个信息的社会,未来应为信息社会提供优质产品。最主要的产品有:
⑴光纤复合架空地线(OPGW)由于光纤复合架空地线具有的特点,当它被架设在杆塔以后,既是避雷用的地线又是通信通道,二者兼备,因此受人们青睐,发展神速。我国在原有基础上也将大量采用。对于新建的500kV线路,其地线一律采用OPGW,而220kV和110kV线路,在可能的条件下也将使用,今后五年内每年至少需要3000~4000公里OPGW。在我国已架设的OPGW线路中,除了上海电缆研究所提供的部分产品以外,大都由国外进口。我国拥有生产光缆的良好设备,又引进制造地线的英国BWE公司的Conform 机,上海电缆研究所又掌握OPGW从设计、制造、金具与附件、架设施工、线路开通等技术,无疑建立一个年产2000公里OPGW的工厂是合适的,将为社会提供优质的OPGW产品。
⑵铜包钢线与铜包铝线作为同轴电缆内芯线(内导体)的铜包铝线与铜包钢线,要有专门的生产厂家提供优质产品。目前我国生产铜包钢线的厂家不少,大多是采用电镀法,对要求导电率为30%IACS或40%IACS的产品,往往制造有困难,而浸涂法、引涂法、铸轧法的产品,由于各种具体原因而在市场上难以见到其优质产品;铜包铝线也局限于电镀法。
近年出现的由国内单位自行开发用焊接包覆法制造铜包钢和铜包铝是一个很好的方法,相对于国外先进设备而言,国产开发的设备还应加大力度在工艺和设备中以改进提高,使之能生产优质产品。
3. 开发新一代的优质导体材料
⑴铜导体在九十年代,我国已经开始用低品位铜生产优质铜杆的试验工作,包括采用稀土优化处理方法,改善铜材质量,现此项工作已初露端倪,应投入力量,加强研究,期望获得新的突破,逐步用于实践中。
用橄榄炉熔铜,连铸连轧生产铜杆,可用适当的废铜或较低品位的铜,造出优质铜杆,尽管此法国外已有报导,然而变成现实仍有很大距离,应加强研制。
如果上述二项能获得实质性进展,并在实际中应用的话,那对铜导体加工将是一个很大的进步。
⑵铝导体
①进一步提高铝导体的导电性能,通过加入适当的合金元素,将铝的导电率从61%IACS提高到63%IACS。这在理论上是可行的,主要是如何寻找合金元素和工艺手段,然后进入实用化阶段。这项研究工作成功,将为输电网提供性能优良的铝导体,改善电网输电质量,其结果使国民经济受益匪浅。
②大力采用高强度铝合金用于输电线路建设,降低线路造价,提高线路输电水平。十年内,把现在国内年使用1000~2000吨,提高到年用量3~4万吨,即约占当年架空线使用量的8%左右时,再建5~6个年产5000吨铝合金工厂是完全应该的。其次,还将大力推广应用耐热铝合金,使应用铝合金的水平接近先进国家。
4. 贯彻产品质量第一,工程安全可靠
⑴执行ISO 9000 电线电缆行业要大力推行ISO 9000标准的贯彻,要打好质量的翻身仗。裸电线作为电线电缆产品的头道工序,更应抓紧质量关,否则将灾及各种产品。对于像架空线这样纯属裸电线的产品,由于关系到输电网,特别是500kV这样重要线路更是要抓好每一个环节,把好质量关。
⑵贯彻执行国家标准、国际标准与行业标准像架空线应执行国标“圆线同心绞架空导线”,这也是IEC 610889;执行IEC 1232“电工用铝包钢线”, IEC 1396“光纤复合架空地线的电气、机械和物理性能要求和试验方法”。以及它们相对应的国家标准和行业标准,贯彻所有有关的国际、国家和行业标准。
对于那些不注重产品质量、不执行标准的企业,应通过行业协会、国家技术监督局给予制裁,不准其产品在市场上销售。
⑶健全行业重点试验室结合长江三峡工程需要,改进完善架空线试验室,使之能够满足三峡工程送电工程用导地线(包括光纤复合架空地线)的性能测试要求;更新六十年代设备,完善拉力机的智能化,增加导线蠕变试验机、导线振动试验机、大电流试验装置、过滑车试验装置等。
棒材生产线工艺流程
轧钢生产工艺流程 1、棒材生产线工艺流程 钢坯验收→加热→轧制→倍尺剪切→冷却→剪切→检验→包装→计量→入库 (1)钢坯验收〓钢坯质量是关系到成品质量的关键,必须经过检查验收。 ①、钢坯验收程序包括:物卡核对、外形尺寸测量、表面质量检查、记录等。 ②、钢坯验收依据钢坯技术标准和内控技术条件进行,不合格钢坯不得入炉。 (2)、钢坯加热 钢坯加热是热轧生产工艺过程中的重要工序。 ①、钢坯加热的目的 钢坯加热的目的是提高钢的塑性,降低变形抗力,以便于轧制;正确的加热工艺,还可以消除或减轻钢坯内部组织缺陷。钢的加热工艺与钢材质量、轧机产量、能量消耗、轧机寿命等各项技术经济指标有直接关系。 ②、三段连续式加热炉 所谓的三段即:预热段、加热段和均热段。 预热段的作用:利用加热烟气余热对钢坯进行预加热,以节约燃料。(一般预加热到300~450℃) 加热段的作用:对预加热钢坯再加温至1150~1250℃,它是加热炉的主要供热段,决定炉子的加热生产能力。 均热段的作用:减少钢坯内外温差及消除水冷滑道黑印,稳定均匀加热质量。 ③、钢坯加热常见的几种缺陷 a、过热 钢坯在高温长时间加热时,极易产生过热现象。钢坯产生过热现象主要表现在钢的组织晶粒过分长大变为粗晶组织,从而降低晶粒间的结合力,降低钢的可塑性。 过热钢在轧制时易产生拉裂,尤其边角部位。轻微过热时钢材表面产生裂纹,影响钢材表面质量和力学性能。 为了避免产生过热缺陷,必须对加热温度和加热时间进行严格控制。 b、过烧 钢坯在高温长时间加热会变成粗大的结晶组织,同时晶粒边界上的低熔点非金属化合物氧化而使结晶组织遭到破坏,使钢失去应有的强度和塑性,这种现象称为过烧。 过烧钢在轧制时会产生严重的破裂。因此过烧是比过热更为严重的一种加热缺陷。过烧钢除重新冶炼外无法挽救。 避免过烧的办法:合理控制加热温度和炉内氧化气氛,严格执行正确的加热制度和待轧制度,避免温度过高。 c、温度不均 钢坯加热速度过快或轧制机时产量大于加热能力时易产生这种现象。温度不均的钢坯,轧制时轧件尺寸精度难以稳定控制,且易造成轧制事故或设备事故。 避免方法:合理控制炉温和加热速度;做好轧制与加热的联系衔接。 d、氧化烧损 钢坯在室温状态就产生氧化,只是氧化速度较慢而已,随着加热温度的升高氧化速度加快,当钢坯加热到1100—1200℃时,在炉气的作用下进行强烈的氧化而生成氧化铁皮。氧化铁皮的产生,增加了加热烧损,造成成材率指标下降。 减少氧化烧损的措施:合理加热制度并正确操作,控制好炉内气氛。 e、脱碳 钢坯在加热时,表面含碳量减少的现象称脱碳,易脱碳的钢一般是含碳量较高的优质碳素结
薄板坯连铸连轧(3)—邯钢CSP
薄板坯连铸连轧(3)—邯钢CSP https://www.360docs.net/doc/e61436966.html, 2006-12-19 邯钢薄板坯连铸连轧生产线于1997年11月18日开工建设,1999年12月10日生产出第一卷热轧卷板,建设工期历时两年零一个月。该生产线引进德国西马克90年代世界先进技术,总生产能力为250万t。 生产线的特点 1 主要工艺特点 邯钢薄板坯连铸连轧生产线主要包括薄板坯连铸机、1号辊底式加热炉、粗轧机(R1)、2号辊底式加热炉、精轧机组(F1~F5)、带钢层流冷却系统和卷取机 。产品规格为1.2~20mm厚、900~1680mm宽的热轧带钢钢卷。钢卷内径为762mm,外径为1100~2025mm,最大卷重为33.6t,最大单重为20kg/mm。工艺流程为:100t氧气顶底复吹转炉钢水—LF钢水预处理—钢包—中间包—结晶器—二冷段— 弯曲/拉矫—剪切—1号加热炉—除鳞—粗轧(R1)—2号加热炉—除鳞—精轧[F1~ F5(F6)]—冷却—卷取—出卷—取样—打捆—喷号—入库。 图邯钢CSP工艺流程示意图 2 主要技术参数
1)薄板坯连铸机 该连铸机为立弯式结构。中间包容量36t,结晶器出口厚度70mm,结晶器长度1100mm,铸坯厚度60~80mm,铸坯宽度900~1680mm,坯流导向长度9325~9705mm,铸速(坯厚70mm)低碳保证值最大4.8m/min、高碳保证值最大4.5m/min、最小2.8m/min,弯曲半径3250mm。 2)加热炉 该生产线包括两座辊底式加热炉,位于粗轧机前后。1号加热炉炉长178.8m,由加热段、输送段、摆动段、保温段组成,炉子同时具有加热、均热、储存(缓冲)的功能,可容纳4块38m长的板坯,单机生产的缓冲时间20~30min,最高炉温1200℃,铸坯入炉温度870~1030℃,出炉温度1100~1150℃。2号加热炉炉长66.8m,由一段构成,主要起均热、保温作用,最高炉温1150℃,铸坯最高入炉温度1120℃,最高出炉温度1130℃。加热炉燃料为混合煤气,烧嘴型式为热风烧嘴。 3)粗轧机 粗轧机为单机架四辊不可逆式轧机,其作用是将铸坯一道轧成所需坯厚。最大轧制力42000kN,工作辊尺寸 880/790mm×1900mm,支撑辊尺寸 1500/1350×1900mm,主电机功率8300kW,轧出坯厚33.0~52.5mm。 4)精轧机组 精轧机组有五架四辊不可逆式轧机(F1~F5),剪机为液压曲柄连杆式,除鳞为高压水除鳞,最大轧制力为4200kN,主电机功率均为8300kW,机架间距5500mm,F5最大出口速度12.6m/s,板带厚1.2~20mm,板带宽900~1680mm,终轧温度900~950℃。 5)冷却区 冷却方式为层流冷却,在一定时间内将带钢由终轧温度900~950℃冷却到550~650℃。冷却区长度为43200mm,另有一个4800mm的空冷段。最大水量约为5240m3/h,水压为0.07MPa(喷淋区水压为1MPa)。
世界及国内薄板坯连铸连轧生产线汇总
比较项目唐钢超薄带涟钢CSP马钢CSP包钢CSP珠钢CSP邯钢CSP本钢CSP 年产量/万吨250200200200180246150 带钢厚度/mm0.8-4(12.7)1(0.8)-81(0.8)-8 1.2-20 1.2-12.7 1.2-200.8-12.7(16)带钢宽度/mm850-1680900-1600900-1600980-15601000-1380900-1680850-1750 铸坯厚度/mm90/7070/50(90)70/5065/5050,60/50二流70/5090/70(100/85)最大卷重/t3028.828.82821.333.631.5铸机型式直弧式立弯式立弯式立弯式立弯式立弯式直弧式结晶器型式H2全长漏斗漏斗形漏斗形漏斗形漏斗形漏斗形H2直漏斗形供货厂家达涅利SMS SMS SMS SMS SMS达涅利液芯压下有有有有无,有(二流)有有 动态凝固软压下有无预留无无无有 冶金长度/mm142409705970572656340936514240大包容量/t150108120(130)210150100150铸机数量二机二流二机二流二机二流一机二流二机二流二机二流一机一流拉速/m min-1 2.8-63-63-6 5.5(7.0) 2.8-6 2.8-4.8 2.5-6电磁制动无有有无有(二流)无预留 均热炉长/m230.9291270200.8191.8178.8+66234.885 均热炉供货厂家布里克蒙布里克蒙布里克蒙德兴LOI LOI布里克蒙轧机架数2+577661+62+5 最高轧速/m·s-120232312.5612.612.622.77 工作辊尺寸/mm R1F1050/980X 1810R2F825/735 X1810F1- F3F825/735X 2100 F1-F2F950/820X 2000F3- F4F750/660X 2000F5- F7F620/540X 2000 F1-F2F950/820X 2000F3- F4F750/660X 2000F5- F7F620/540X 2000 F1-F3F800/720X 1950F4- F6F600/540X 1950 F1-F3F800/720X 1700F4- F6F600/540X 1700 R1F880/790X 1900F1- F3F800/720X 2100F4- F6F600/540X 2100 R1R2F950/850X 1800F1- F3F780/700X 1880F4- F6F600/530X 2080 支撑辊尺寸/mm F1250/1300X 1790 F1-F2F1500/1370 X1880F3- F7F1500/1350X 1800 F1-F2F1500/1370 X1880F3- F7F1500/1350X 1800 F1450/1300X 1790 F1350/1250X 1500 R1F1500/1350X 1900F1- F6F1500/1350X 1900 R1R2F1450/1300 X1860F1- F3F1450/1300X 1860F4- F6F1360/1230X 1860我国已投产的薄板坯连铸连轧生产线技术经济指标
无氧铜杆连铸连轧生产线
无氧铜杆连铸连轧生产线 1.机组用途及组成 本机组是采用连铸连轧的工艺方法生产φ8mm低氧光亮铜杆,原材料为电解铜。本生产线由一台16吨/小时熔铜竖炉、一台12吨回转式保温炉、五轮式连铸机、牵引机、滚剪、校直刨角机、打毛机、连轧机、收杆装置、电控系统等组成。 2.简单工艺流程 电解铜──→竖炉────→回转式保温炉→流槽(熔体保护)→浇煲→连铸 机(铸坯)→铸坯处理装置(滚剪→校直→去角→除屑)→进轧装置(主动送料)→连轧机(轧杆)→铜杆冷却装置(表面还原)→连续绕杆装置(预成型)→梅花式收线装置(铜杆成卷) 3. 生产线主要技术参数 1). 生产铜杆直径:φ8 mm 2). 生产能力:14-16 t/h 3). 成圈重量: 3.0-5.0 t 4). 主要设备总尺寸: 40×7.8×6.1 m (不包括熔铜炉及循环冷却过滤系 统) 5). 主要设备总重量: 85 吨(不包括熔铜炉) 6). 主要设备总功率: 600 kW(不包括熔铜 炉) 4 .设备技术规范及组成 4.1熔铜炉一套 4.1.1熔化炉型:竖式冲天炉 4.1.2熔化炉最大铜熔化能力:16吨/小时 4.1.3熔铜炉上料机构最大装载量:5吨 4.1.4熔铜炉进料方式:提升式 4.1.5烧嘴单体最大燃烧能力:60万大卡/小时
4.1.6熔铜炉烧嘴数量:15只 4.1.7烧嘴冷却方式:水冷 4.1.8烧嘴点火方式:自动 4.1.9使用燃料:天然气、液化气、城市煤气 4.1.10保温炉炉型:液压回转式 4.1.11保温炉有效容量:12吨 4.1.12保温炉最高倾力角度:>70o 4.1.13烧嘴单体最大燃烧能力:60万大卡/小时 4.1.14保温炉烧嘴数量:1只 4.1.15燃烧控制方式:比例燃烧,具有保护装置 4.1.16燃气阀检漏方式:手动/自动 熔铜炉包括冲天式铜熔化炉、回转式保温炉、上下流槽、燃烧控制系统等四大部分。具有熔化速度快、铜水含氧量低、流量连续可调、铜水温度独立可控、单位铜水燃气消耗量低等特点。 ①冲天式铜熔化炉(竖炉) 熔化炉简称竖炉,由炉底、炉身、碰撞保护块、加料口、上料机构、烟囱、炉衬和冷却风机等部分组成。 炉底、炉身由优质钢板和型钢制作,炉底采用25mm钢板,中间用槽钢加固,使整个炉底可以承受100吨电解铜板的重量而不变形;炉身用16mm钢板圈成桶体,炉体内贴一层硅酸铝纤维毯,可大大降低炉壁温度,中间砌筑高铝耐火砖,最内层炉衬是直接触火焰和铜水的,采用SiC砖砌筑,荷重软化温度可达1700度,保证了炉衬的使用寿命。SiC砖采用纯度大于80%的SiC混合特殊的高温粘接剂,经压机预先压制成弧形砖,通过高温焙烧,使SiC砖形成半烧结状态,一方面增加了SiC砖的强度,便于运输、搬运、砌筑,同时在砌筑完成后,通过第二次烘烧,使竖炉内衬形成一个坚固的整体,使整个炉衬的强度大为提高。 炉体上部是防撞保护块,防止在加料时铜板撞在炉衬上,引起炉衬脱落破损甚至内衬倒塌。防撞保护块由耐热钢整体浇注而成,整体强度高,具有耐高温、耐冲击、不易脱落等优点,使用寿命长,可有效保护加料时铜板对炉身的冲击。 加料口设计在竖炉的上方,这种加料方式可以使铜板从炉底一直堆放到炉体加料口,延长了烧嘴
棒材生产线自动控制简介
三轧钢生产过程自动化控制系统运行情况介绍 一、自动化系统配置 本系统中的自动化控制系统采用SIEMENS的S7-400PLC,采用集中—分布式的网络结构构成满足热连轧的全过程的自动化系统,符合现代控制理论要求的标准、开放的控制思想。 采用工业计算机和HMI监控软件组成的二级计算机控制系统对轧制生产线的各种数据和信号进行显示和记录,HMI监控软件采用SIEMENS的最新的WINCC V6,它能够充分兼容和更有效地发挥西门子PLC的强大功能。 主轧操作台I/O都采用ET200M远程I/O系统,与CPU416构成PROFIBUS-DP工业现场总线系统。所有的远程I/O 的数据采集与传输都通过PROFIBUS-DP来完成,这样不仅节省了大量的电缆费用,而且大大提高了数据采集的可靠性。各个轧机的控制由6RA70全数字直流调速装置及辊道变频控制通过扩展PROFIBUS-DP总线模块CP443-5与S7-400PLC进行通讯。(注:PROFIBUS是一种用于工厂自动化现场级监控和现场设备层数据通讯与控制的现场总线技术。可实现现场设备层到车间级监控的分散式数字控制和现场通讯控制从而为实现工厂综合自动化和现场设备智能化提供了可行的解决方案。)HT1、HT2、HT3,HT4、HT5、HT6通过SIEMENS的6RA70全数字直流调速装置的S00软件来控制,减少了主轧线CPU的程序量。 二、传动系统配置 直流传动系统全部采用西门子公司最新一代的6RA70全数字直流调速装置.粗中轧机传动控制为磁场可逆,精轧机采用6RA70电枢可逆四象限,以西门子6RA70为核心,采用大功率柜结构,二者通过可靠的嫁接技术共同组成电机的调速装置。注:以上所有直流调速装置均已经过我公司的授权修改,不用向西门子公司购买密码就能够随意使用其内部的SOO自由功能块。6RA70装置本身提供了对传动系统完备的监控保护与故障自诊断功能。可检测缺相、过压、欠压、过流、过载、堵转、超速、测速故障、失磁、欠磁等各种控制系统故障。 三、6RA70扩容简介 6RA70装置的扩容改造方式随着国产可控硅技术水平、可靠性的不断提高而被越来越多的用户接受,低廉的价格,方便的维护使其在工业生产中充满了活力。 6RA70装置的扩容存在的方式根据各个自动化集成商的特点各有不同,但其基本构成是完全一致的。这就是触发脉冲的隔离与放大、检测信号的采集以及大功率整流柜等。其中涉及系统可靠性的关键有两个部分。 ?脉冲隔离与放大接口 ?功率柜 脉冲功率与放大接口是连接6RA70与功率柜的重要环节,其可靠性直接影响到设备的运行。众所周知当触发脉冲在系统运行时产生干扰,会使系统出现交流环流情况,此种情形下供电电网将被瞬时相间短路,烧毁可控硅。由于目前国内采用的可控硅为流控型晶闸管,因此其实际上为可控导通不可控关断,这样几种因素就能导致其出现逆变颠覆的危险。其中最可能出现的就是在正反组切换过程中脉冲的突然丢失。因此不难看出脉冲隔离与放大环节可靠性的重要。 大功率整流柜是直流传动系统的具体执行机构,可靠、出力大、耐冲击负荷也就成了检测功率柜的重要标准。因此在选择器件及压接工艺、风道设计上成了功率单元的关键技术。在这一点上,我们选择了国内合资公司生产的可控硅,并在散热器加工、压接、检测全程监控、保证可靠。功率柜风道及结构是我公司在总结国内较先进的几家大公司的基础上,从新优化设计出来的,具有风道短、体积小散热好的特点。 二、控制原理介绍 (一)速度级联控制 在钢材连轧机中,为保证成品质量,以成品机架(末机架)为基准机架,保持其速度不变,并作为基准速度设定,其前面机架速度根据金属秒流量相等的原理,自动按比例设定;在轧制过程中来自活套闭环控制的调节量、手动干预调节量,依次按逆轧制方向对其前面的各机架速度作增减,实现级联控制。速度级联控制是连轧生产线电气控制思想的精华。 根据各机架秒流量相等的原理有: S 1 ×V1 = S 2 ×V2 = ... = S n ?1 ×V n ?1 = S n ×V n (1) 式中S1 - Sn为各机架孔形截面积;V1 -Vn为各机架线速度;n为机架号。
30万吨连铸连轧型钢可行性报告
三十万吨连铸连轧型钢生产线可行性研究报告 二?一二年五月
1 项目提出枣庄市恒力机械制造有限公司坐落在煤城枣庄孟庄工业园区,注册资金2500 万元,现有员工200 余人,主要从事生铁、钢坯的生产销售经营活动,现年产各种材质的优质连铸钢坯50 余万吨。多年来一直遵循“质量第一,顾客至上”的原则,让每位客户希望而来,满意而归。因公司没有轧钢生产线,为适应市场需求,解决社会就业问题,同时也为企业创造更多的经济效益,公司领导班子与工程技术人员经过对市场的全方位调查研究,我公司欲投资3000 余万元,新上一条30 万吨连铸连轧型钢生产线,连铸连轧生产工艺是综合近年来炼钢、连铸和轧钢的最新技术成果而发展起来的一项新的钢铁生产方式,由于省却了钢坯二次加热环节,吨钢可以节约标煤90 余公斤, 大大节约了能源消耗。由于在线不用加热,省去了热脏煤气炉和加热炉,减少了环境污染,降低了生产成本。由于无二次加热氧化,金属收得率也显著提高,具有较高的经济效益。测算年利税2000 万元以上,利润可达1 亿元(见附表),项目完全符合国家节能减排的需要。 2 设计原则 2.1贯彻执行国家有关方针、政策、建设规范、标准等,达到质量、环保、安全三体系标准要求。 2.2优化设计,立足于国产化,采用先进、经济、适用、成熟可靠的工艺设备,实现生产线工艺技术装备水平的提升。 2.3对工艺线进行优化布置, 实现连铸连轧的要求,提高生产线的产量、质量,添补区域内产品空白。 2.4在工艺设备能力允许的前提下,尽量利用现有人力、物力,自制辊道、收集平台等设备,以节约投资。 2.5总体考虑、统一规划、分期分步实施,工艺设备配置、产品定位
薄板坯连铸连轧(5)—鞍钢ASP(1700)
薄板坯连铸连轧(5)—鞍钢ASP(1700) https://www.360docs.net/doc/e61436966.html, 2006-12-19 ASP生产线的研制及建设背景 1700中薄板坯连铸连轧生产线(Angang Strip Production,简称ASP),是我国第一条板坯厚度为135 mm 的连铸连轧短流程生产线,是第一条由国内自行负责工艺设计、设备设计、制造及研制和自主集成自动化系统的唯一一条具有我国自主知识产权的连铸连轧短流程生产线。ASP生产线的开发应用,使鞍钢成为一个既能从事大规模钢铁生产,又能从事中薄板坯连铸连轧生产线工艺设计、设备制造、自动化系统集成开发、施工、开工试运转系统工程总承包的钢铁企业。同时,带动了国内一重、二重等机械制造加工行业及电机制造业的发展。鞍钢ASP 工程的成功,标志着我国已成为世界上为数不多的、能进行连铸连轧短流程工艺、设备研制、设计、制造及集成自动控制系统的国家之一。 鞍钢ASP(1700)生产线的工程概况 (1)生产能力及产品规格 该生产线设计能力为年产250万t。ASP生产线是由2台单机单流铸机和连轧生产线组成。单台铸机设计能力144万t/a,实际生产能力已达149.5万t/a。 (2)板坯规格 中薄板坯厚度:135mm; 宽度:900---1550 mm; 长度:7.0~15.6 mm。 三炼钢板坯厚度:200 mm; 宽度:900~1550mm; 长度:4.O~9.0 mm。
(3)生产钢种(表1) 表1 鞍钢中薄板坯连铸连轧生产线生产的钢种 % (4)成品规格 带钢厚度:1.5~8.0 mm(已生产过1.3 mm); 带钢宽度:900~1 550 mm; 最大卷重:21 t; 最大单位卷重:16.4 kg/mm。 ASP生产线工艺流程 鞍钢ASP生产线工艺流程见图1。
全连轧棒材生产线工艺特点
全连轧棒材生产线工艺特点 汪 涛 (重庆钢铁股份公司钢研所,重庆400013) 摘 要 介绍了重钢新建的年产40万吨全连轧棒材生产线的工艺特点,并指出了该生产线未来工艺技术发展的方向。 关键词 全连续轧制 工艺特点 发展 1 前言 以前重钢棒材的生产一直依靠落后的横列式轧机进行,其高能耗、低成材率、经济效益不显著等弊病已严重影响了重钢的发展。于是,重钢于2003年12月建成投产了全连轧棒材生产线。该套轧机设计生产能力为40万吨 年,终轧最高速度16m s ,具有20世纪90年代先进水平,整个设计任务由马鞍山钢铁公司设计院承担,所有主、辅设备全部国产化。该棒材生产线从设计到施工都本着投资少、建设快的原则,所以在未来产品的开发和规模的扩大方面存在局限性,需要进行不断的技术升级改造。2 生产线概况2.1 生产工艺流程 连铸方坯→加热炉→粗轧机组→1#飞剪→ 中轧机组→2#飞剪→精轧机组→倍尺飞剪→步进齿条式冷床→定尺冷剪→检查收集→打捆包装→称重→入库 2.2 工艺平面布置 工艺平面布置见图1 。3 坯料和产品大纲 坯料采用150mm ×150mm ×8000mm 连铸坯,坯重1404kg 。 产品:热轧圆钢、带肋钢筋。 规格:圆钢 14mm ~ 40mm ,带肋钢筋 12mm ~ 40mm 。 钢种:普通碳素结构钢、优质碳素结构钢、低合金钢、合金钢、锚链钢、标准件用钢等。4 工艺设备特点4.1 全连续轧制技术 本生产线为全连续棒材生产线,全轧线共有18架轧机,分为粗轧、中轧、精轧机组。各机组由6架平-立交替布置的短应力轧机组成,其中第16、18架为平-立可转换轧机,各机架均由直流电机单独传动。整个轧线采用全连续、全无扭轧制,粗、中轧机组采用微张力轧制,从第12架轧 图1 重钢全连轧棒材生产线工艺平面布置图 《重型机械科技》2004年第2期
棒材生产工艺
2、轧钢工艺 2.1 产品大纲及金属平衡 2.1.1 产品大纲 本车间设计为2条年产量80万吨的高速线材生产线。 主要产品规格为: 圆钢: Φ5.0—Φ20mm 光面线材 螺纹钢: Φ6.0—Φ18mm 螺纹钢筋 生产钢种为:普通碳素结构钢、优质碳素结构钢、锚螺钢、合金钢、不锈钢、 轴承钢等。 按品种规格和钢种分类的产品大纲见表2—1、2—2。 产 品 大 纲 表 2—1 产 品 大 纲 表 2—2 序号 产品规格范围 年产量(t ) 比例(%) 序号 钢种 代表钢号 年产量(t ) 比例(%) 1 普通碳素结构钢 Q235 400000 25 2 优质碳素结构钢 45# 80# 480000 30 3 焊条钢 320000 20 4 弹簧钢 60Mn 60Si 2Mn 64000 4 5 合金结构钢 40Gr 160000 10 6 冷镦优质钢 ML25—ML45 80000 10 7 不锈钢 8000 0.5 8 轴承钢 8000 0.5 7 合计(t ) 1600000 100 8 比例(%) 100
1 ф5-ф5.5 160000 10 2 ф6.0—ф9 400000 25 3 ф10—ф13 720000 45 4 ф14—ф18 240000 15 5 ф20 80000 5 合计100 2.1.2 产品质量及标准 (1)产品交货状态: 均以盘卷状态交货 (2)产品执行标准 —GB/T14981-94热轧盘条尺寸、外形、重量及允许偏差 —GB700-88碳素结构钢 —GB/T699-1999优质碳素结构钢技术条件 —GB6478-86冷镦钢技术条件 —GB/T3077-1999合金结构钢技术条件 —GB1222-84弹簧钢 2.1.3 原料 车间所用原料为连铸坯,全部由潍钢炼钢供给,钢坯规格尺寸为:150×150×12000mm,净重为2075kg,最小坯料长度为8000mm。 坯料应满足国家标准YB2011—83中规定和YB/T004—91中规定的内容。 连铸坯年需要量为166.4万吨。 2.1.4 金属平衡 车间原料用量为166.4万吨,成品量为160万吨,成材率为96%,金属平衡见表2—2。 车间金属平衡表表2-3 产品炉内烧损及二次氧化切损及轧废 原料量(t) 数量所占数量所占数量所占
各种连铸连轧生产线的比较
各种连铸连轧生产线的比较 一、基本概述 裸电线是电线电缆不可缺少的部分,除了光缆以外,几乎所有的电线电缆都需要导体、需要裸线,而且相当数量的一部分产品就以裸电线的形式出现,例如钢芯铝绞线。粗略概算,包括导体部分在内的裸电线的总产值,约占电线电缆总产值的三分之一,它有着举足轻重的作用。 裸电线、电线电缆导体,其材料主要是铜、铜合金、铝、铝合金,以及其它有色和稀有金属材料。 在工农业总的用铜量中,电线电缆行业用铜量占有很高的比重。九十年代初期,全国电线电缆行业的用铜量约近30万吨,而今年估计用铜量为80余万吨,约增加近二倍的用铜量,价格却从最高每吨3万元至现在每吨1.5万元,下跌约50%,因此一些在缺铜时采用铝作代用品的电线电缆产品又恢复采用铜,如布电线、电车线等,使铜的用量日增。铜作为电线电缆最主要的导电材料,又逐步向不同的用途延伸,如用作电车线的高强度、高耐磨的铜合金线应运而生;使用高纯度、高精度的铜线为通信电缆等提供优质导电材料;特细铜线、超细铜线更为新型的电子仪器设备、通信设备、办公自动化设备等提供更为优良的产品,用铜量的增加便是理所当然的。 每年几十万吨铜需要加工,从电解铜板、加工成杆、线或异型材,需要约万台套以上的杆材、线材和异型材的生产设备,这是十分庞大的设备群体。 铜杆生产中最主要四种方法的设备,我国都应有尽有。拥有2台套浸涂法设备和至少700余台套的上引法机组用于生产无氧铜杆,保守估计,设备年生产能力在180万吨至200万吨;从德国、美国、意大利引进的铜铸轧机组超过10
台套,加上国产的连铸连轧机组,光亮铜杆的生产能力至少为50万吨至60万吨;至于原有常用的横列式轧机轧制黑铜杆,加上用水平连铸法制作型材的坯料,其年生产能力不低于30万吨至50万吨。也就是说,我国拥有的生产设备中,无氧、低氧铜杆的年生产能力在220万吨至250万吨左右。加上黑铜杆生产能力,将超过300万吨。由于乡镇企业的大量出现,一些简易的生产铜杆的方法,也就无法在此估计之中。80万吨的需要量和250万吨无氧、低氧铜装机能力之间,存在着很大的距离,因此相当大的部分设备就不得不处于减产或停产状态,以700 余台套上引法机组为例,估计约1/3至1/4的机组由于各种原因而处于停产状态,而1/2的机组的产量尚未达到原设计的生产能力,但即使如此,由上引法机组生产的铜材,仍占有我国铜杆用量的半璧江山,起着重要的作用。 我国铜线拉线机约在万台左右,至少有一半是由电工机械厂制造的,少量由国外引进,这二部分设备的性能都较优,特别至九十年代中后期,国产大、中、小拉采用连续退火的水平,已与国外设备逐步靠近,差距大大缩小了。然而在乡镇企业中仍有土拉线机,这些机器能耗高、劳动强度高、效率低、粗糙,难以加工质优的产品,这部分设备数量估计约为总数的一半,需要给予彻底改造或弃之不用。 裸电线中大量采用铝,例如:铝绞线及钢芯铝绞线。九十年代初期,用铝量每年尚不超过20万吨,以后随着经济的增长逐年增加,由于以前国家在电力系统的政策上是重发电轻送电,使送电的增长赶不上发电的增长速度。近年来开始的城市电网和农村电网改造,使送电的增长速度急剧加快,兼之九十年代开始建设的大型电站,像二滩电站、黄河小浪底电站和长江三峡电站,将相继逐步建成,送电便成为电站建设以后的重中之重,送电工程建设步入本世纪以来最辉煌、
棒材剪切生产线安全操作规程
行业资料:________ 棒材剪切生产线安全操作规程 单位:______________________ 部门:______________________ 日期:______年_____月_____日 第1 页共5 页
棒材剪切生产线安全操作规程 1.操作人员应认真执行设备日常维护保养的规定。开机前应仔细检查设备电气线路、气动部分、机械部分有无异常、漏电、漏气及消音器堵塞现象;各紧固件是否牢固,传动链条是否正常,润滑油位是否符合要求,安全防护系统是否齐全可靠,确认无误后方可开机。 2.打开电源总开关、系统开关,空车试运转,搬动手动润滑把柄,润滑设备,班中润滑不得低于3次。 3.设置参数内剪切钢筋的直径和单次剪切根数,数据填写须准确完整。 4.系统内的初始距离,出料距离和料仓转向须认真填写,否则,易造成设备损坏。 5.设置画面2的内容为原始数据,不必填写,不得随意改动其数据,如有需要,可微调。 6.剪切参数画面,剪切钢筋长度、总根数,待剪钢筋总长度的填写必须准确完整。 7.操作中,当手动送料时,禁止用手扶送料链条,以免发生危险。 8.剪切机工作时产生的震动,易造成接近开关和磁性开关螺丝松动,影响设备运行动作,应注意观察,发现螺丝松动及时紧固。 9.操作中注意检查油水分离器的过滤情况,油位不得低于其下限;水位不得高于其上限,并及时将水放掉。 10.注意观察空压机气泵压力开关工作是否正常,如有异常及时排除。 11.工作结束,关闭总电源和系统电源,清理设备的铁屑、灰尘, 第 2 页共 5 页
成品料、余料、废料归类规范放置,清理工作场所。 森林旅游安全知识 森林内旅游观光不能吸烟。 不在森林公园、自然保护区和国有林场等重点林区内野炊、烧烤或进行其他野外用火活动。 二、注意行走安全 进入森林景区应注意大门入口、重要路段和特殊景点安全告示。 观景不走路,走路不观景。 登山以穿登山鞋、布鞋、球鞋为宜。登山时可携带一根长短、轻重合适且结实竹棍或手杖。 不要擅自到未开放的旅游景点和危险地带游玩。 注意塌方落石、泥石流、滑坡与路肩塌陷等警示标识。不攀越没有防护设施的陡坡峭壁。 不在无人员管理的深潭、溪流水域游泳及戏水。 雷雨时不要攀登高峰,不要手扶铁制栏杆,不要在大树下避雨,以防雷击。 走山间小路应靠山墙内侧行进,不跑不跳,不探身往下观看峡谷、瀑布或深潭。 景区拍照应防高处跌落。 三、注意自我保护和安全自救 第 3 页共 5 页
中国薄板坯连铸连轧生产线建设状况统计
中国薄板坯连铸连轧生产线建设状况统计 截止到2009年,中国已建成和正在建设各种不同类型的薄板坯连铸一连轧生产线合计14条,铸机30流,将形成年生产能力3530万t(见表),到2007年,中国的薄板坯连铸一连轧产量达3073万t,2008年产量达2927.3万t。 表:中国薄板坯连铸-连轧生产线建设状况 序号钢铁公司工艺类型铸机流数开发商铸坯规格(厚×宽)/mm 产品厚度/mm 设计年产量/万t 轧机投产期 1 珠钢CSP 2 SMS (50-60)×(1000-1380) 1.2-12.7 180 6CVC 1999.8 2 邯钢CSP 2 SMS (60-90)×(900-1680) 1.2-12.7 247 1+6CVC 1999.12 3 包钢CSP 2 SMS (50-70)×(980-1560) 1.2-20.0 200 7CVC 2001.8 4 唐钢FTSR 2 Danieli (70-90)×(1235-1600) 0.8-12.0 250 2+5PC 2002.12 5 马钢CSP 2 SMS (50-90)×(900-1600) 1.0-12.7 200 7CVC 2003.9 6 涟钢CSP 2 SMS (55-70)×(900-1600) 1.0-12. 7 240 7CVC 2004.2 7 鞍钢ASP 2 鞍钢100/135×(900-1550) 1.5-25.0 240 1+6ASP 2000.7 8 鞍钢ASP 4 鞍钢135/170×(900-1550) 1.5-25.0 500 1+6ASP 2005 9 本钢FTSR 2 Danieli (70-85)×(850-1605) 0.8-12.7 280 2+5PC 2004.11 10 通钢FTSR 2 Danieli (70-90)×(900-1560) 1.0-12.0 250 2+5PC 2005.12 11 酒钢CSP 2 SMS (52-70)×(850-1680) 1.5-25.0 200 6CVC 2005.5 12 济钢ASP 2 鞍钢(135-150)×(900-1550) 1.2-12.7 250 1+6ASP 2006.11 13 武钢CSP 2 SMS (50-90)×(900-1600) 1.0-12.7 253 7CVC 2009.2 14 梅钢FTSR 2 Danieli (70-90)×(900-1560) 1.0-6.35 250 2+5PC 2010.11 合计 30 3530 2009-2010年国内高炉预计投产情况统计(万吨) 省份公司新增设备情况新增能力(万吨/年) 投产时间 河北河北兴华钢铁公司550m3*1 70 2009年1月 河北唐山国丰1780m3*1 160 2009年2月 江西新钢2500m3*1 210 2009年2月 新疆八钢2500m3*1 210 2009年2月 江苏兴澄特钢3200m3*1 260 2009年3月 内蒙古乌兰浩特钢铁503m3*1 70 2009年4月 河北邯郸新区3200m3*1 260 2009年4月 辽宁鞍钢鲅鱼圈4038m3*1 350 2009年4月 上海宝钢梅钢3200m3*1 260 2009年5月 河北唐山路港钢铁公司1160m3*1 120 2009年5月 河北首钢京唐5500m3*1 400 2009年5月 河北唐山瑞丰金友1580m3*1 150 2009年5月 天津天铁2800m3*1 220 2009年6月
五系铝合金杆生产设备连铸连轧法生产线国产化分析研究
五系铝合金杆生产设备连铸连轧法生产线国产化分析研究 发表时间:2019-11-18T13:51:47.383Z 来源:《中国电业》2019年14期作者:邹林宏 [导读] 提出五系铝合金杆连铸连轧机生产线能够针对5系铝合金材料进行在线连续熔铸成坯且连续轧制成直径9.5mm五系铝合金杆。 摘要:该文旨在提出五系铝合金杆连铸连轧机生产线能够针对5系铝合金材料进行在线连续熔铸成坯且连续轧制成直径9.5mm五系铝合金杆,保证铝合金杆的质量品质较高的稳定轧制工艺 关键词:五系铝合金;连铸连轧;国产化;一四一机械厂 一、国内五系铝合金杆生产设备背景 目前国内生产五系铝合金主要采用1、连铸连轧法、2、立式半连续铸造挤压法,3、水平连铸连拉法。第2种方法的设备投资较大、工序多、占地面积大、工模具消耗和能耗较高,而且生产过程中的几何废料也高,产品成品率相对较低,且产量较低;第3种方法工艺存在严重缺陷,成品质量较差;第1种连铸连轧法,设备投资适中,产量大、成材率高达到%90以上、质量稳定。综上所述第1种连铸连轧法最适合生产牌号5356铝合金杆,但是该种方法只有美国南线、意大利普洛佩兹和德国西马克等少数国际大公司能够生产所需的连铸连轧生产线设备,这些年欧美国家对我国高端铝合金制造技术进行技术封锁,所以基本不愿卖该设备给我们国家的铝合金生产企业,就算卖给我们的企业,销售的价格也是敲诈式的高得离谱,基本单台售价都要上亿元,这严重制约了我国企业对5356铝合金杆的生产和研制。 二、五系铝合金杆生产设备连铸连轧法分析研究 我们需要的连铸连轧法生产设备需要达到的目标是:该种五系铝合金杆连铸连轧机生产线能够针对5系铝合金材料进行在线连续熔铸成坯且连续轧制成直径9.5mm五系铝合金杆,保证铝合金杆的质量品质较高的稳定轧制工艺。 该类五系铝合金杆连铸连轧机生产线设计方案工艺流程必须包含内容应该有以下设备组成:1、铝合金锭浇铸连续成形的浇铸机、2、用于整平校直的校直机、3、用于传送铝合金锭的牵引机、4、用于铝合金锭废料剪切的滚剪机、5、二次加热铝合金锭温度的加热炉、6、用于轧制铝合金杆的连轧机以及收杆机,7、另外还有润滑油系统和用于轧制的连轧机乳液润滑冷却系统,8、控制整套生产线联动生产的电气系统。 整套设计方案的难点和关键点分析: 第一个难点:铝合金锭浇铸连续成形的浇铸机:该设备是整套生产线轧制前H型线坯成形装置,我分析认为它的结晶器铜轮直径和结晶器铜轮用于成形铝合金锭的型腔截面积决定了整套设备轧制道次的设计、以及轧制铝合金杆的产量,最关键是它很大因素影响五系铝合金生产线能否通过后续轧机环节顺利轧制成直径9.5mm五系铝合金杆,所以重点参数设计就是围绕浇铸机结晶器上述两个内容。 第二个难点:用于轧制铝合金杆的连轧机以及收杆机:上述浇铸机定型以后,我们就需要研究用多少道次轧机进行连续轧制成直径9.5mm五系铝合金杆,我分析认为轧制道次的设计主要解决以下问题:1、首先是保证能保证质量品质的情况下轧制得出直径9.5mm的五系铝合金杆,意思就是能顺利通过轧机轧出来。2、再就是为了满足经济效益最大化,怎么样在保证产品品质的情况下最大限度挖掘产量最大化。生产线设计方案就需要结合上述两个问题设计出一套轧制铝合金杆的连轧机合理孔型,轧制孔型设计就决定了轧制道次设计,结合五系铝合金性能严格意义上轧制轧机道次越多,线坯温度降低得越多,五系铝合金温度越低强度越高,轧机轧制难度越大,另外定位成形杆直径为9.5mm五系铝合金杆,轧制道次数量多少决定了产量上限,设计范围内轧制道次越多产量相对较高。 第三个难点:用于轧制的连轧机乳液润滑冷却系统:上述问题全解决后,其他方面影响五系铝合金杆轧制过程的主要因素,就是轧制过程中用于冷却铝合金线坯和冷却轧机轧辊的乳化液了,乳化液会间接或者是直接和五系铝合金轧制线坯接触,乳化液的浓度和温度将直接影响五系铝合金杆的成品质量,我分析认为:实际生产的时候应该考虑将浓度在能保证正常生产的情况下越高越好,同时乳化液温度在能保证对轧机轧辊一定冷却效果的前提下越高越好。这样就能保证在维持设备正常运转的前提下,降低外界因素对五系铝合金杆的轧制工艺的干扰。 三、五系铝合金杆生产设备连铸连轧法相关企业情况 四川煤田地质局一四一机械厂从1993年开始从事铜、铝、铝合金连铸连轧生产线设备的生产,至今已经有25年的历史,以前生产的铝合金连铸连轧设备主要是针对除开五系铝合金之外的中低强度产品,近几年来该厂鉴于国内五系铝合金连铸连轧生产线国产化空白的契机,该企业花了大量人力和财力探索该种连铸连轧生产线的研制,在2019年终于完成整套设计方案编制和设备生产图纸绘制,期待这一成果能为我国五系铝合金连铸连轧生产线国产化做出巨大贡献。 参考文献: 【1】四川煤田地质局一四一机械厂(发明人:杨正国、闫成贵、邹林宏等)、一种铝合金杆连铸连轧机:中国、ZL 2018 2 1774814.0、2019-08-06。
棒材连轧生产设备特点概述
棒材连轧生产设备特点概述 字数:3206 字号:大中小 摘要:本文介绍了当代国际先进水平的小型棒材连轧设备特点及主要技术参数,其中包括:步进梁式加热炉采用汽化冷却、红圈轧机、控制冷却、连续定尺剪切全部轧机和飞剪采用变频调速交流电机驱动等情况。 关键词:棒材;连轧机;工艺参数;设备特点 1概况 棒材连轧车间的加热炉改为步进梁式,采用汽化冷却。轧机、飞剪、堆垛机、打捆机、液压及润滑设备由国外引进,全部交流主电机、电气设备及计算机系统从德国SIMENS 公司引进。这条连轧生产线的工艺及机、电设备都达到了90年代后期国际水平。 此条棒材生产线还为将来实现热送热装、高线大盘卷生产、型材生产、无头轧制、在线测径等工艺和技术预留了足够的位置。同时设备设计充分考虑了将来生产其它产品时设备的兼容问题。 一、生产设备布置特点 车间原料跨距连铸成品跨只有6m,连铸坯由运送小车送来,再由天车吊至+5.0m平台上的冷装料台架;热送时则由保温辊道直接送来,再由提升机提升至+5.0m平台上。当轧机产量不超过连铸机产量时可实现连续热装。从上料开始即对坯料进行全线自动跟踪,实现炉批号的自动化管理。采用汽化冷却的步进梁式加热炉、不仅可节能而且加热质量高,入出炉均采用炉内悬。全线18架轧机采用平-立交替布置,第14、16、18架为平/立转换机架,以实现带肋钢筋切分、扁钢及型钢生产工艺的最佳化。红圈轧机刚度高,可采用低温轧制工艺,不仅可节能而且金属烧损少,视钢种不同,开轧温度在900~950℃,相应的金属烧损为0.6%~0.7%。1~10架轧机为微张力控制,10~18架为立活套控制(切分时末2架也采用活套控制),实现无张力轧制,以保证产品精度,产品尺寸偏差可达到1/3DIN标准公差范围的水平。对带肋钢筋进行轧后余热淬火加芯热回火处理,可使带肋钢筋的综合力学性能提高1~2级。倍尺剪采用优化剪切技术,可使上
达涅利新一代棒材生产线经济效益显著
达涅利新一代棒材生产线经济效益显著 意大利AcciaierieBertoliSafau(ABS)工厂 以很高的生产率生产小规格棒材产品,以充分发挥加热炉生产能力,一直是全世界棒材生产商共同追求的一个目标。 对于中国市场来说,为实现这一目标,最常用的方式就是众所周知的多线切分轧制系统。它采用专用轧辊孔型设计和特殊的导卫设备,以使轧件成形,并纵向切分为2线、3线或4线棒材。然后,同时将各线棒材轧制到最终产品尺寸规格。 能够在中国的棒材轧机上应用的具有革命性创新意义的一项可选技术,将是超高速棒材精轧和通过达涅利HTC(High-speed Twin Channel )“高速双通道”输送系统,将精轧后的棒材高速送上冷床。 高速双通道输送系统最初由达涅利早在20世纪70年代初期研制开发,并申请专利,此后在全世界获得广泛应用。它将棒材输送到冷床上的速度也由最初几年的20m/s最大速度,逐渐发展到今天创纪录的50m/s。 HTC高速双通道输送系统非常适用于最新一代高效棒材轧机。高效棒材轧机在生产小规格棒材时,可在连续式预精轧机上进行切分轧制,然后在两个独立的Delta高速线材轧制机组,同时完成双线精轧。 本文将介绍超高速棒材精轧机组和高速输送系统的主要技术特点,它们的主要亮点和给用户带来的好处(其中最显著的特点是可以极高的生产效率,生产最小直径为?6mm的小规格螺纹钢棒材)。 高效生产小规格棒材 现代棒材轧机追求的主要目标之一,是能够以很高的生产率,生产符合市场需要的小规格棒材和钢筋。小规格棒材和钢筋通常占轧机设备总产量的一半以上。要实现这一目标,就意味着要充分发挥加热炉加热小规格坯料的生产能力,从而能够很好地平衡轧机的生产能力,充分发挥它的生产潜力。 要实现这一目标,可通过以下两种途径: 1)MSR多线切分轧制 该系统目前在中国使用最多,主要目的是用于实现上述目标。多线切分轧制系统利用同一根直方坯,通过两线或多线切分轧制,生产小规格棒材。其特点是,与单线轧制相比,可以减少轧制道次。 切分轧制技术采用特殊的轧辊孔型设计和专用导卫设备,以使轧件成形,并将来坯纵向切分为2线、3线、4线或5线棒材。然后由精轧机架将各线棒材,轧制到最终产品尺寸规格,并同时完成倍尺剪切。然后,通过传统“挡板式”入口输送辊道,以18~20m/s(用于2线切分轧制)或13~15m/s(用于3线或4线切分轧制)的最大速度,将这些棒材一起输送到冷床上。 这项工艺必然要涉及将两根或多根棒材送到冷床齿槽内(输送根数取决于轧机切分轧制线数)。随之而来的问题是,有可能使棒材在对中辊道区内头部对齐作业变得困难。 当采用4线切分轧制时,这个问题可能容易解决一些。这应该归功于双挡板式冷床入口输送辊道。由于配备了这种输送辊道,只需将两根棒材送入冷床上的每个齿槽内,从而使棒材头部对齐和料层成形变得容易一些。切分轧制工艺可用于生产?8~22mm圆钢和钢筋。