红酸果案例
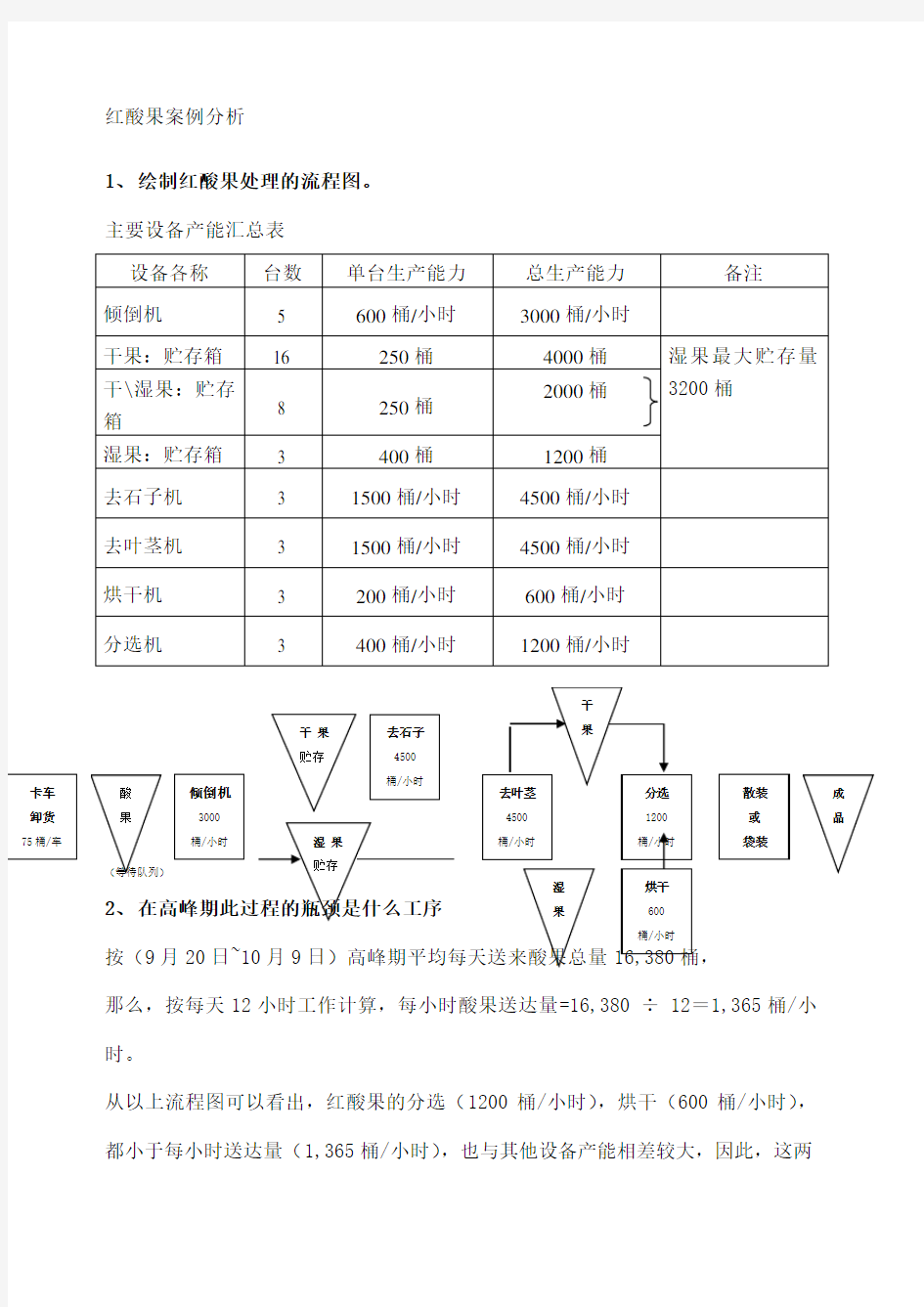

红酸果案例分析
1、绘制红酸果处理的流程图。主要设备产能汇总表
2、
按(9月20日~10月9
那么,按每天12小时工作计算,每小时酸果送达量=16,380 ÷ 12=1,365桶/小时。
从以上流程图可以看出,红酸果的分选(1200桶/小时),烘干(600桶/小时),都小于每小时送达量(1,365桶/小时),也与其他设备产能相差较大,因此,这两
个环节首先有可能是瓶颈环节。
再看看干、湿果送达比例情况:
1)由于烘干机和分选机的产能分别为600桶/小时和1200桶/小时,当湿果数在50%以下时,分选机是瓶颈工序,当湿果数量在50%以上时,烘干机是瓶颈工序。2)在高峰期,假设每天运来酸果总数为T桶,其中w%是湿果,分选机处理完所有红酸果的时间为S= T / 1200 (小时),烘干机处理完所有湿果的时间为D= T*w% /600 (小时)。
如果S > D,即w% < 50%,那么分选机所用时间就较长,分选机是瓶颈工序,反之,如果S < D,即w% > 50%,那么烘干机所用时间就较长,烘干机是瓶颈工序。3)如果以高峰期某日(10月1日)为例,酸果数量为18,018桶、湿果比例69%计,则该日烘干机工作时间=18018*69%/600=21(小时),分选机工作时间=18018/1200=15(小时),显然,烘干机是瓶颈工序。
4)按照来年预测,全年湿果的比例将达到70%,那么粗略预计在来年高峰期大多数日子,烘干机是瓶颈工序。
3、计算卡车的平均等待时间
截止到晚上七点,600*12=7200桶,12个小时已经处理了7200桶,
12600-7200=5400桶,即还有5400桶没处理完,3200桶已装进贮存箱,2200桶还在卡车上。
在卡车上(12600-3200)÷600=小时,湿果运来的速度为12600÷12=1050桶/小时
积压情况:1050-600=450桶/小时,存储箱装满为3200÷450=小时装满
如图阴影面积即为卡车等待时间,
贮存能力线于升降曲线之间。
S阴影=(5400-3200)×()÷2=9416桶·小时
平均每辆卡车等待时间为 9416÷75=126小时。
4、过程处理的安排是否有问题
根据目前高峰期处理红酸果的工序从卸完货第一小时(上午8点)开始,到烘干工序完成需要到第二天上午6点。根据目前计划,从上午11点开始处理红酸果,那么整个烘干工序的完成时间是第二天上午8点,这会对第二天的工作进度造成影响。但在非高峰期,平均每天运行的红酸果总量,仅相当于高峰期间2小时左右运达的数量,因此将红酸果的处理工序开始时间延后,有利于充分利用设备生产能力,避免机器空转造成浪费。
5、假设卡车等待成本是$10/小时卡车,计算高峰期(按18000桶,70%湿果汁)
的总成本是多少(假设卡车是均匀到达)
如第3题所述,按高峰期一日按18000桶,其中70%湿果计,卡车总的等待时间为126小时,按照US$10/小时计,则高峰期一日卡车等待总成本为US$1260。
6、对奥布里恩的建议你怎么看
奥布里恩方案针对性提出增加烘干机有助于解决瓶颈问题。
1)如果增加一台烘干机,产能为(3+1)×200=800桶/小时
按高峰期(18000*70%=)湿果数12600÷800=小时,即从早上7:00开始工作至晚上10:45可以处理完毕。
截止到晚上7:00,能处理12个小时×800=9600桶,剩余12600-9600=3000桶小于贮存容量3200桶,这样即可解决卡车等待问题,而且接收工序可在7点完成。2)如果增加两台烘干机,则处理能力为(3+2)×200=1000桶/小时。
12600÷1000=小时即可完成高峰期一天湿果的处理,可满足生产需要。
3)耗资240,000元改造干果贮存箱,表面上看似乎可以解决卡车长时间等候的问题,但是,由于烘干机作为瓶颈仍然未得到解决,因此生产过程中还是会因为烘干机无法及时加工完所有的湿果而产生积压。
7、你对整个作业系统有什么建议
1) 考虑先优化过程处理时间安排,在高峰期,处理工序调整在早上7时开始;非高峰期,处理工序可调整为下午3时上班,8时前下班;
2) 建议购置1台烘干机,否则考虑更换1个干/湿果贮存箱;
3) 减少产能过剩的加工设备,比如目前生产能力盈余较多的是倾倒机、去石机、去叶茎设备,如果能卖掉2台倾倒机、2台去石机和1台去叶茎设备,所得资金可用于购置烘干机或干/湿果贮存箱;
4) 在高峰期可增加临时用工的投入,尽可能安排工人8小时轮班制,尽量避免加班带来的人力成本增加;
5) 增加的设备可以购置,也可以采用融资租赁等方式减少资金占用压力。
(新)红酸果案例分析
红酸果加工厂案例分析
目录 一、面临的问题 二、加工流程图 三、各工序生产能力及瓶颈工序 四、高峰期完成所有加工的时间 五、最后一辆卡车的卸货时间及等待时间 六、评价奥布里恩的建议 七、合理性改进建议 一.案例回顾及工厂所面临的问题 位于马萨诸塞州的“红酸果之角”加工厂过去都是加工干收法采集的酸果,但是近些年来湿收法采集成为主要方式,这就给工厂过去的酸果加工程序带来了挑战。随着湿收法的推广和普及工厂面临着下面一些问题需要解决 背景条件 ●18,000 桶/天(高峰期) ●湿果:70%(12,600桶/天;1050桶/小时) 干果:30%(5400桶/天;450桶/小时) ●卡车装载75桶/车早七点起12小时均匀到达 ●卡车等待成本:$10/辆小时 ●工人平均工资是12.50美元/小时,8小时之外工厂要多付50% 所面临的问题 ●过多的加班问题 ●卡车排队现象 ●烘干、分选工序产能不足 ●存储罐容量不足 二.生产流程分析 红酸果的生产流程如下图所示:
三. 生产能力及瓶颈分析 从上面图中分析可以看出整个工序的瓶颈工序为烘干,其隐含利用率为175%,所以整个工序湿收法酸果的生产能力为600桶/小时。 四. 高峰期完成的加工时间 瓶颈工序(烘干)处理时间即可确定加工时间。 高峰期每天湿果的总量:12600桶 倾倒机 (5台) 去石子 (3台) 去茎叶 (3台) 烘干 (3台) 分选 (3条) 可供使用能力 3000 桶/小时 4500 桶/小时 4500 桶/小时 600 桶/小时 1200 桶/小时 湿收法 需求 1050 桶/小时 0 1050 桶/小时 1050 桶/小时 1050 桶/小时 干收法 需求 450 桶/小时 450 桶/小时 450 桶/小时 0 450 桶/小时 需求需要能力 1500 桶/小时 450 桶/小时 1500 桶/小时 1050 桶/小时 1500 桶/小时 隐含资源利用率 1500/3000 =50% 450/4500 =10% 1500/4500 =33% 1050/600 =175% 1500/1200 =125%
红酸果作业参考答案
红酸果案例作业参考答案1、绘制红酸果处理的流程图。 主要设备产能汇总表 2、 按(9月20日~10月9 那么,按每天12小时工作计算,每小时酸果送达量=16,380 ÷ 12=1,365桶/小时。 从以上流程图可以看出,红酸果的分选(1200桶/小时),烘干(600桶/小时),都小于每小时送达量(1,365桶/小时),也与其他设备产能相差较大,因此,这两
个环节首先有可能是瓶颈环节。 再看看干、湿果送达比例情况: 1)由于烘干机和分选机的产能分别为600桶/小时和1200桶/小时,当湿果数在50%以下时,分选机是瓶颈工序,当湿果数量在50%以上时,烘干机是瓶颈工序。2)在高峰期,假设每天运来酸果总数为T桶,其中w%是湿果,分选机处理完所有红酸果的时间为S= T / 1200 (小时),烘干机处理完所有湿果的时间为D= T*w% /600 (小时)。 如果S > D,即w% < 50%,那么分选机所用时间就较长,分选机是瓶颈工序,反之,如果S < D,即w% > 50%,那么烘干机所用时间就较长,烘干机是瓶颈工序。3)如果以高峰期某日(10月1日)为例,酸果数量为18,018桶、湿果比例69%计,则该日烘干机工作时间=18018*69%/600=21(小时),分选机工作时间=18018/1200=15(小时),显然,烘干机是瓶颈工序。 4)按照来年预测,全年湿果的比例将达到70%,那么粗略预计在来年高峰期大多数日子,烘干机是瓶颈工序。 3、计算卡车的平均等待时间 截止到晚上七点,600*12=7200桶,12个小时已经处理了7200桶, 12600-7200=5400桶,即还有5400桶没处理完,3200桶已装进贮存箱,2200桶还在卡车上。 在卡车上(12600-3200)÷600=小时,湿果运来的速度为12600÷12=1050桶/小时 积压情况:1050-600=450桶/小时,存储箱装满为3200÷450=小时装满 如图阴影面积即为卡车等待时间,
红酸果案例
红酸果案例 标准化管理处编码[BBX968T-XBB8968-NNJ668-MM9N]
红酸果案例分析 1、绘制红酸果处理的流程图。主要设备产能汇总表
(等待队列) 2、 在高峰期此过程的瓶颈是什么工序 按(9月 20日 ~10月9日)高峰期平均每天送来酸果总量16,380桶, 那么,按每天 12小时工作计算,每小时酸果送达量=16,380 ÷ 12=1,365 桶/ 小时。 从以上流程图可以看出,红酸果的分选(1200桶/小时),烘干(600桶 /小时),都小于每小时送达量(1,365桶/小时),也与其他设备产能相差较大,因此,这两个环节首先有可能是瓶颈环节。 再看看干、湿果送达比例情况: 1)由于烘干机和分选机的产能分别为600桶/小时和1200桶/小时,当湿果数在50%以下时,分选机是瓶颈工序,当湿果数量在50%以上时,烘干机是瓶颈工序。 2)在高峰期,假设每天运来酸果总数为T 桶,其中w%是湿果,分选机处理完所有红酸果的时间为S= T / 1200 (小时),烘干机处理完所有湿果的时间为D= T*w% /600 (小时)。
如果S > D,即w% < 50%,那么分选机所用时间就较长,分选机是瓶颈工序,反之,如果S < D,即w% > 50%,那么烘干机所用时间就较长,烘干机是瓶颈工序。 3)如果以高峰期某日(10月1日)为例,酸果数量为18,018桶、湿果比例69%计,则该日烘干机工作时间=18018*69%/600=21(小时),分选机工作时间=18018/1200=15(小时),显然,烘干机是瓶颈工序。 4)按照来年预测,全年湿果的比例将达到70%,那么粗略预计在来年高峰期大多数日子,烘干机是瓶颈工序。 3、计算卡车的平均等待时间 截止到晚上七点,600*12=7200桶,12个小时已经处理了7200桶, 12600-7200=5400桶,即还有5400桶没处理完,3200桶已装进贮存箱,2200桶还在卡车上。 在卡车上(12600-3200)÷600=小时,湿果运来的速度为12600÷12=1050桶/小时 积压情况:1050-600=450桶/小时,存储箱装满为3200÷450=小时装满 如图阴影面积即为卡车等待时间, 贮存能力线于升降曲线之间。 S阴影=(5400-3200)×()÷2=9416桶·小时 平均每辆卡车等待时间为 9416÷75=126小时。
生产运作与管理-红酸果案例分析
案例1 (1)年需求量D=10,000*12=120,000,最优订货批量EOQ=6324,年订购次数n=120,000/6324=18.97,约为20次,单位生产成本为2,年生产成本C1=2*120,000=240,000,P=3,年生产准备成本为250*20=5,000元,库存持有成本费为0.2*3*20=12,所以制造商年总成本为240,000+5,000+12=245,012,制造商+药品公司年总成本为3795+245,012=248,807元。 (2)用制造商一年的经济生产批量除以最优订货量得出订货次数,根据算出的订货次数,分别求出制造商的年总成本和药品公司的年总成本。其中制造商的年总成本计算如下:用订货次数乘以每次生产准备成本计算出年生产准备成本,用制造商年经济生产批量乘以每瓶维生素的生产成本得出制造年总成本,计算出库存成本,最后把年生产准备成本、制造年总成本、库存成本三者相加得出制造商年总成本。药品公司的年总成本同题一。 (3)假设订货批量为X,根据题一的计算思路,建立相关的函数关系式,当两者年总成本最小是,X满足的条件。 (4)比较最优订货量和总成本最低时的订货量,如果最优订货量较大,则制造商的生产成本会上升,反之则下降。 补偿:药品公司要对生产商每次的准备成本进行补偿,同时及时接货,减轻制造商的库存压力、减少库存成本。尽量减少订货次数,或者订货周期衔接。 (5)制造商减少单位生产成本,药品公司订货时给出每次订货的补贴。 案例2 (1)与机械加工类似的工艺专业化工厂,库存一般采用固定间隔期的方法去控制库存系统,虽然拥有较高的安全库存,但是会导致高库存的问题,从而增加库存为此费用。显然,这不适合原料容易变质、库存维持费用本来就高于其他公司的菲多利公司,因而它采用了固定量控制系统和固定间隔期相结合的方法,严格安排库存时间,每天交付固定量的原料,针对不同原料固定订货提前期,通过紧凑的计划安排进行生产,确保设备使用效率,以此降低在库存中的高投入。(2)库存有主原料库存、辅助原料库存、成品库存。这些物资通过直接建立起与零售商的联系,减少中间商的参与来加快快速移动,同时建立起了密集的分销渠道。 (3)固定量系统:每天交付固定量的原料。固定间隔期系统:食用油、调料、包装产品都按固定时间出库,同时也就固定了不同的订货提前期。最大最小系统:土豆储存区域每次只保存7.5小时所需量,当库存低于该需要量时则新的原料进入库存。综合控制系统 (4)综合,固定间隔期,固定量,最大最小 (5)生产与销售之间联系紧密,中间环节少,拥有完善的分销渠道,计划安排紧密科学。 (6)减少原料运输成本,接近原料地。产品性质决定必须有充足的生产能力和库存能力。接近销售市场,保证产品销售速度,确保产品新鲜。 (7)产品间存在差异,技术工艺、所需原料等不同,同时生产,设备的准备调试、原料的准备各方面会耽误大量时间,降低设备使用率,从而加大管理成本。库存管理也不方便。 1 生产流程图
科德角工厂案例分析知识交流
科德角工厂生产瓶颈分析报告 Q1:科德角工厂的主要问题是什么?造成这些问题的主要原因是什么? 主要问题: 1、车辆卸货排队时间过长 2、高峰期加班费支出过大 主要原因: 1、流程瓶颈限制了整个加工厂的产能,导致运来的红酸果无法及时处理; 2、工人的工作时间安排不合理,零时工的管理不佳,缺勤率高,影响生产过程补充问题一:加工红酸果的制作流程是线性流程——对象专业化布置。
流程图
Q2:分析该生产系统存在的瓶颈。如果湿果的比例有变化,瓶颈是否有变化呢? 瓶颈:由流程图可看出,此时烘干是瓶颈,为600桶/小时 烘干完成时间:12600/600=21小时>12小时 分选完成时间:18000/1200=15小时>12小时但<21小时 比例:烘干湿果的瓶颈能力为600桶/小时,而每小时运送红酸果数量为1500桶/小时,600/1500=40% 结论:当湿果所占比例小于40%时,分选是瓶颈;当湿果所占比例大于40%时,烘干是瓶颈。 补充问题二 干果比例为40% 45% 50% 55% 60% 时的瓶颈和生产成本以及再算增加一台烘干机的情况下卡车等待时间和加班成本 ①干果比例为40%,湿果比例为60%.(干果600个,湿果900个)此时的瓶颈仍然是烘干。 成本: 每小时湿果数量:900÷75=12辆 每小时烘干的能力:600÷75=8辆 湿贮藏室3200÷75=42.66辆,也就是42辆后湿贮藏室贮藏满,卡车需要等待因为42÷12=3.5,也就是说10点半之后卡车就需要等待
卡车等待费用(将每小时卡车等待车辆*10):6*10+10*10+14*10+18*10+22*10+26*10+30*10+34*10+38*10+30*10+22*10+14* 10+6*10=2720 每名工人加班费用:(23.75-11-8)*18.75=89.06 总的加班费用=89.06*38=3384.28 增加一台烘干机
红酸果作业参考答案
红酸果作业参考答案集团档案编码:[YTTR-YTPT28-YTNTL98-UYTYNN08]
红酸果案例作业参考答案 1、 绘制红酸果处理的流程图。 按(9月20日~10那么,按每天12桶/小时。 从以上流程图可以看出,红酸果的分选(1200桶/小时),烘干(600桶/小时),都小于每小时送达量(1,365桶/小时),也与其他设备产能相差较大,因此,这两个环节首先有可能是瓶颈环节。 再看看干、湿果送达比例情况: 1)由于烘干机和分选机的产能分别为600桶/小时和1200桶/小时,当湿果数在50%以下时,分选机是瓶颈工序,当湿果数量在50%以上时,烘干机是瓶颈工序。 2)在高峰期,假设每天运来酸果总数为T 桶,其中w%是湿果,分选机处理完所有红酸果的时间为S= T / 1200 (小时),烘干机处理完所有湿果的时间为D= T*w% /600 (小时)。
如果S > D,即w% < 50%,那么分选机所用时间就较长,分选机是瓶颈工序,反之,如果S < D,即w% > 50%,那么烘干机所用时间就较长,烘干机是瓶颈工序。 3)如果以高峰期某日(10月1日)为例,酸果数量为18,018桶、湿果比例69%计,则该日烘干机工作时间=18018*69%/600=21(小时),分选机工作时间=18018/1200=15(小时),显然,烘干机是瓶颈工序。 4)按照来年预测,全年湿果的比例将达到70%,那么粗略预计在来年高峰期大多数日子,烘干机是瓶颈工序。 3、计算卡车的平均等待时间? 截止到晚上七点,600*12=7200桶,12个小时已经处理了7200桶, 12600-7200=5400桶,即还有5400桶没处理完,3200桶已装进贮存箱,2200桶还在卡车上。 在卡车上(12600-3200)÷600=15.67小时,湿果运来的速度为12600÷ 12=1050桶/小时 积压情况:1050-600=450桶/小时,存储箱装满为3200÷450=7.11小时装满 如图阴影面积即为卡车等待时间, 贮存能力线于升降曲线之间。 S阴影=(5400-3200)×(15.67-7.11)÷2=9416桶·小时 平均每辆卡车等待时间为 9416÷75=126小时。 4、过程处理的安排是否有问题? 根据目前高峰期处理红酸果的工序从卸完货第一小时(上午8点)开始,到烘干工序完成需要到第二天上午6点。根据目前计划,从上午11点开始处理红酸果,那么整个烘干工序的完成时间是第二天上午8点,这会对第二天的工作进度造成影响。但在非高峰期,平均每天运行的红酸果总量,仅相当于高峰期间2小时左右运达的数量,因此将红酸果的处理工序开始时间延后,有利于充分利用设备生产能力,避免机器空转造成浪费。 5、假设卡车等待成本是$10/小时卡车,计算高峰期(按18000桶,70%湿 果汁)的总成本是多少?(假设卡车是均匀到达) 如第3题所述,按高峰期一日按18000桶,其中70%湿果计,卡车总的等待时间为126小时,按照US$10/小时计,则高峰期一日卡车等待总成本为 US$1260。
红酸果案例答案
数据分析 根据案例中提供的去年高峰期间每天送到工厂的红酸果数量计算,高峰期平均每天的总量为16380桶,其中湿果占48.43%,干果占51.57,单日总量最多为18879桶(9月24日),单日湿果数量最多为12432桶(占69%,10月1日)。 案例中假定的数字:每天运达数量18000桶,其中70%为湿果,30%为干果,则平均每小时运达的数量为1500桶,其中湿果1050桶,干果450桶。 该厂目前的加工能力为(参见第4页流程图):接收3000桶/小时,去石子4500桶/小时,去叶茎4500桶/小时(其中干果3000桶/小时,湿果1500桶/小时),湿果烘干600桶/小时(占每小时运达湿果数量的57%),分选1200桶/小时(占每小时运达红酸果数量的80%)。 问题1不难发现,工厂大部分配置的生产能力高于实际工作的需求,但是存在两个环节严重延缓了工序的进展:一是湿果烘干每小时仅600桶,即每天必须工作21小时才能完成全部工作;二是分选每小时1200桶,即每天必须工作15小时才能完成全部工作。这两个环节中以烘干对整个工序的制约最大,也正是这个环节导致前面工序产生红酸果的积压,从而使卡车长时间等待。 问题2与上题相联系,由于整个工序中湿果烘干的步骤构成了瓶颈,必须用21个小时才能处理完所有的湿果,所以使得实际工作时间远远超过12小时。 问题3使用烘干机处理完一天内运来的所有湿果需要21小时,使用分选机理完一天内运来的所有红酸果需要15小时,我认为这两个步骤构成了整个工序的瓶颈,其中烘干机对整个流程的阻碍作用要大于分选机,只有使烘干机达到每小时
1050桶(即6台机器)的生产能力,分选机达到每小时1500桶(即4台机器)的生产能力,才能保证工作流程不产生积压。 问题4假如湿果比例为30%(即450桶),干果比例为70%(即1050桶),则烘干机能跟上工作流程,而分选机依然无法满足需要,此时,构成瓶颈的就是分选机。 按照目前工厂的设备配置情况,只有当湿果比例不高于40%的情况下,烘干机才能满足生产的需要,不构成瓶颈。 问题5时间安排上,假如高峰时期处理红酸果的工序从上午8点(即卸完第一个小时的货)开始,则整个烘干工序的完成时间是第二天上午6点;根据目前的工作计划,从上午11点开始处理红酸果,则整个烘干工序的完成时间是第二天上午8点,这将影响到第二天的工作开展。 从目前的情况来看,在高峰期,即使红酸果的处理工序从上午8点开始,等到一天的工作完成,也已经要到第二天上午8点之后,再加上打扫卫生维护设备的两个小时,第二天的工作也必定受到影响。 非高峰期平均每天运达的红酸果总量,仅相当于高峰期间2小时左右运达的数量,因此将红酸果的处理工序开始时间延后,有利于充分利用设备生产能力,避免机器空转造成浪费。 问题6奥布里恩提出的方案,看到了烘干机对整个生产过程的阻碍作用,因此提出增加烘干机,有助于问题的解决。增加一个烘干机,可以使每小时的生产能力提高到800桶,占每小时运达湿果数量的76%,即用15.75小时就可以完成一天中所有湿果的加工。假如增加两个烘干机,可以使每小时的生产能力提高到
MBA生产运营管理
红酸果案例分析报告 1、红酸果处理的流程 2、红酸果加工厂的主要问题及原因 红酸果加工厂的目前表现出来的问题主要有两个方面:一是运送红酸果的车辆卸货排队时间太长;二是高峰时期加班费的支出很多。 造成这些问题的原因主要有:一是红酸果厂的加工工序上各个环节的产能安
排不合理,某些环节的产能存在瓶颈,限制了整个加工厂的产能,导致运来的红酸果无法及时处理;二是对于临时工的管理不到位,缺勤率高,影响了生产效率。 3、分析瓶颈 按照案例中提供的数据和讨论题给出的假设, 每天运来的红酸果有18000桶, ⑴其中70%的湿果:18000桶×70%=12600桶,30%的干果:18000桶×30%=5400桶。 去石子完成时间(干):5400桶÷4500桶/小时=小时<12小时 去茎叶完成时间(干湿):18000桶÷4500桶/小时= 4小时<12小时 烘干完成时间(湿):12600桶÷600桶/小时=21小时>12小时 分选完成时间(干湿):18000桶÷1200桶/小时=15小时>12小时 此种情况下烘干机是瓶颈。 ⑵其中30%的湿果:18000桶×30%=5400桶,70%的干果:18000桶×70%=12600桶。 去石子完成时间(干):12600桶÷4500桶/小时=小时<12小时 去茎叶完成时间(干湿):18000桶÷4500桶/小时= 4小时<12小时 烘干完成时间(湿):5400桶÷600桶/小时=9小时<12小时 分选完成时间(干湿):18000桶÷1200桶/小时=15小时>12小时 此种情况下分选机是瓶颈。 ⑶烘干机每天完全释放产能时能够处理的湿果为600桶/小时×12小时=7200桶,(7200桶÷18000桶)×100%=40%。 结论:当湿果所占比例小于等于40%时,分选机是瓶颈,当湿果所占比例大于40%时,烘干机都是瓶颈。 4、关于卡车长时间等待 烘干机产能不足是造成红酸果无法及时处理的瓶颈,因此分析卡车等待的问题时,我们只需要分析湿红酸果的加工流程。 一天工作开始时,除了将第一批卸货的湿红酸果装进贮存箱里的,其他在卡车上要等待贮存箱里的红酸果进入下一工序后才能卸货,湿果运来的速度为12600÷12=1050桶/小时,积压情况:1050-600=450桶/小时,存储箱在经过3200
运营管理-红酸果案例分析报告
第一题 高峰时期11:00开工,这时候一共来了1800桶干果子和4200桶湿果子。但是我们只能存放3200桶湿果子。并且开工之后,生产线每小时只能够处理600桶湿果子,而送来的湿果子却有1050桶。 这样运行,所有果子处理完需要到次日10:00,最倒霉的车需要等13个小时左右,最多的时候积存了7800桶果子在等待的车上。 第二题 题里面的流程图有点不喜欢,下面画一个看着顺眼的。 图2.1 这样看起来就舒服多了,X代表去茎叶的电台极其用来处理干果子的比例。从速率上,我们可以明显看出,烘干机是瓶颈。根据烘干效率来计算,那么每天处理完所有的果子需要21h再加上2h的收拾屋子时间,还有线上流动的时间,中间的滞留,一天就过去了……
第三题 烘干机:21h 分选机:15h 根据图2.1,烘干和分选是瓶颈 第四题 图4.1 如果干、湿比例变成7:3那么就流程图就会变成图4.1的样子,那么只有分选过程是瓶颈。、 第五题 早一点开始运行可能会减少储存箱积满导致的货车等待的可能性,在高峰期可一定程度上提早下班时间,从而少付一些员工工资。但是挺费电的。 10-12月的低古时段,如果3点运行机器的话,晚上10:00才能完成当天的工作。不太现实。
9月初的低谷时段,如果三点运行的话,下午7:00左右就完成工作了,还挺合理的 最佳时间随接收量变化的原因是:运转机器是要付制造费用的,人工+水电其实挺贵的,所以能少开尽量少开。于是我们根据每天的接收量计算一下生产线多久能够处理完,尽量晚开一会儿,有利于降低成本。 第六题 优先考虑完成工作时间来安排生产,穷举了添加烘干机个数和改造储藏箱个数,形成了如下表格。
红酸果案例分析
红酸果案例分析 Prepared on 22 November 2020
红酸果加工厂案例分析 目录 一、面临的问题 二、加工流程图 三、各工序生产能力及瓶颈工序 四、高峰期完成所有加工的时间 五、最后一辆卡车的卸货时间及等待时间 六、评价奥布里恩的建议 七、合理性改进建议 一.案例回顾及工厂所面临的问题 位于马萨诸塞州的“红酸果之角”加工厂过去都是加工干收法采集的酸果,但是近些年来湿收法采集成为主要方式,这就给工厂过去的酸果加工程序带来了挑战。 随着湿收法的推广和普及工厂面临着下面一些问题需要解决 背景条件 ●18,000 桶/天 (高峰期) ●湿果:70%(12,600桶/天;1050桶/小时) 干果:30%(5400桶/天; 450桶/小时) ●卡车装载75桶/车早七点起12小时均匀到达 ●卡车等待成本:$10/辆小时 ●工人平均工资是美元/小时,8小时之外工厂要多付50% 所面临的问题 ●过多的加班问题
●卡车排队现象 ●烘干、分选工序产能不足 ●存储罐容量不足 二.生产流程分析 红酸果的生产流程如下图所示: 三.生产能力及瓶颈分析 从上面图中分析可以看出整个工序的瓶颈工序为烘干,其隐含利用率为175%,所以整个工序湿收法酸果的生产能力为600桶/小时。 四.高峰期完成的加工时间 瓶颈工序(烘干)处理时间即可确定加工时间。 高峰期每天湿果的总量:12600桶 瓶颈工序每天处理湿果所需要的时间:12600桶÷600桶/小时=21小时每天从11点开始不间断地加工红酸果要加工到第二天早上8点才能完全满足当天的需求,同时每天还需要2个小时来清理现场和维护设备。
红酸果案例[教育]
红酸果案例[教育] 这个案例的执笔人是耶鲁管理学院的教授阿瑟?J?斯沃塞。它是以哈佛商学院的一个有关全国酸果合作社的案例为基础的。 红酸果 此时的科德角正值隆冬季节,安?希金斯醒来时出了一身冷汗。她总是作这样的恶梦:卡车源源不断地开来,可是却无法将红酸果卸下来,因为贮存箱里早已装满了等待处理的果子。当工厂早晨那座旧钟的指针向午夜时,被处理的酸果还在分选机上跳着,月光照在工人们的脸上,泛起了奇异的红光。他们已经很疲劳了,但一想到能拿加班费,心里就美滋滋的,也就不觉得累了。 两个月之前,安?希金斯到马萨诸塞州普里茅斯的“红酸果之角”加工厂就任负责生产的副总裁。她当时辞去了康涅狄格州一个保健机构经理的职务,一心想摆脱管理工作带来的压力,到马萨诸塞州的海边享受清静的生活。可是,她没有想到在酸果加工厂会遇到难题,她明白在采取改进措施之前自己还将度过许多不眠之夜。 加工厂的情况 “红酸果之角”加工厂是当地数百个种植者合办的一个加工厂。过去,酸果都是采用“干收法”采收的,即用手从树上采摘下来。近几年,“湿收法”已成为主要采收方法。这是一种机械化程度较高的方法。人们用水冲酸果蔓,酸果就会从树上掉下来,这样一来就容易收集了,因为酸果都漂浮在水面上。去年,加工厂接收的酸果有58%是采用“湿收法”采收的,预计来年采用“湿收法”采收的浆果将达到70%。 红酸果是在9月初至12月采收的。高峰期从9月下旬开始,共持续约二十天。表1显示的是去年高峰期间(9月20日至10月9日)每天送到加工厂的酸果总
数和湿果所占比例。在这二十天里,平均每天送来的酸果的16,380桶。在采收季节其余的日子里,送来的果子就少多了。如表1所示,从9月1日至9月19日,送来的酸果为44,176桶,平均每天为2209桶,而从10月10日至12月10日,送来的酸果为238,413桶,平均每天为3845桶。根据果农的种植情况和历史数据分析,今年高峰期红酸果的数量将比去年多,每天将达到18000桶。 酸果用卡车运到之后,要在专用的传送装置经过几道工序的处理,去除石子和叶茎,烘干湿果,接着把果子分成三级:即一级品、二级品和不合格。然后再把它们包装起来,运送到生产厂,加工厂冻浆果、果汁或果酱。 接收与临时贮存 每星期七天从7:00至19:00,都有(种植者租用的)卡车陆陆续续开到加工厂。卡车的装载量从20至400桶不等,平均每辆卡车的装载量为75桶。卡车卸货时,先要倒到基瓦尼型倾倒机的平台上。然后这个平台倾斜,把酸果倒在通向加工厂贮存箱的快速运转带上。 卸一车酸果平均要用7.5分钟。加工厂共有五台基瓦尼型倾倒机,每台要有三名工人操作。每台倾倒机每小时可倾倒600桶酸果。第五台倾倒机是前一年花了200,000美元添加的。 酸果倾倒之后,通过传送装置被送到27个贮存箱中的一个。 1. #1~#16贮存箱——干果,每箱250桶 2. #25~#27贮存箱——湿果,每箱400桶 3. #17~#24——可湿,可干,每箱250桶 以上,高峰期时 在这种情况下,所具有的湿果贮存量可在达到3200桶(3个可存放400桶的贮存 箱,8个250桶的贮存箱)。如果没有存放的地方,到达的卡车就得等待。
红酸果案例分析
红酸果加工厂案例分析 目录 一、面临得问题 二、加工流程图 三、各工序生产能力及瓶颈工序 四、高峰期完成所有加工得时间 五、最后一辆卡车得卸货时间及等待时间 六、评价奥布里恩得建议 七、合理性改进建议 一.案例回顾及工厂所面临得问题 位于马萨诸塞州得“红酸果之角”加工厂过去都就是加工干收法采集得酸果,但就是近些年来湿收法采集成为主要方式,这就给工厂过去得酸果加工程序带来了挑战。随着湿收法得推广与普及工厂面临着下面一些问题需要解决 背景条件 ●18,000 桶/天(高峰期) ●湿果:70%(12,600桶/天;1050桶/小时) 干果:30%(5400桶/天;450桶/小时) ●卡车装载75桶/车早七点起12小时均匀到达 ●卡车等待成本:$10/辆小时 ●工人平均工资就是12、50美元/小时,8小时之外工厂要多付50% 所面临得问题 ●过多得加班问题 ●卡车排队现象 ●烘干、分选工序产能不足 ●存储罐容量不足 二.生产流程分析 红酸果得生产流程如下图所示:
三. 生产能力及瓶颈分析 从上面图中分析可以瞧出整个工序得瓶颈工序为烘干,其隐含利用率为175%,所以整个工序湿收法酸果得生产能力为600桶/小时。 四. 高峰期完成得加工时间 瓶颈工序(烘干)处理时间即可确定加工时间. 高峰期每天湿果得总量:12600桶 瓶颈工序每天处理湿果所需要得时间:12600桶÷600桶/小时=21 倾倒机 (5台) 去石子 (3台) 去茎叶 (3台) 烘干 (3台) 分选 (3条) 可供使用能力 3000 桶/小时 4500 桶/小时 4500 桶/小时 600 桶/小时 1200 桶/小时 湿收法 需求 1050 桶/小时 0 1050 桶/小时 1050 桶/小时 1050 桶/小时 干收法 需求 450 桶/小时 450 桶/小时 450 桶/小时 0 450 桶/小时 需求需要能力 1500 桶/小时 450 桶/小时 1500 桶/小时 1050 桶/小时 1500 桶/小时 隐含资源利用率 1500/3000 =50% 450/4500 =10% 1500/4500 =33% 1050/600 =175% 1500/1200 =125%
红酸果案例
红酸果案例分析 1、绘制红酸果处理的流程图。主要设备产能汇总表
(等待队列) 2、在高峰期此过程的瓶颈是什么工序 按(9 月20日 ~10月9日)高峰期平均每天送来酸果总量16,380桶, 那么,按每天 12小时工作计算,每小时酸果送达量=16,380 ÷ 12 =1,365 桶/小时。 从以上流程图可以看出,红酸果的分选( 1200桶 / 小时),烘干(600桶/小时),都小于每 小时送达量(1,365桶/小时),也与其他设备产能相差较大,因此,这两个环节首先有可能是瓶颈环节。 再看看干、湿果送达比例情况: 1)由于烘干机和分选机的产能分别为600桶/小时和1200桶/小时,当湿果数在50%以下时,分选机是瓶颈工序,当湿果数量在50%以上时,烘干机是瓶颈工序。 2)在高峰期,假设每天运来酸果总数为T桶,其中w%是湿果,分选机处理完所有红酸果的时间为S= T / 1200 (小时),烘干机处理完所有湿果的时间为D= T*w% /600 (小时)。如果S > D,即w% < 50%,那么分选机所用时间就较长,分选机是瓶颈工序,反之,如果S < D,即w% > 50%,那么烘干机所用时间就较长,烘干机是瓶颈工序。
3)如果以高峰期某日(10月1日)为例,酸果数量为18,018桶、湿果比例69%计,则该日烘干机工作时间=18018*69%/600=21(小时),分选机工作时间=18018/1200=15(小时),显然,烘干机是瓶颈工序。 4)按照来年预测,全年湿果的比例将达到70%,那么粗略预计在来年高峰期大多数日子,烘干机是瓶颈工序。 3、计算卡车的平均等待时间 截止到晚上七点,600*12=7200桶,12个小时已经处理了7200桶, 12600-7200=5400桶,即还有5400桶没处理完,3200桶已装进贮存箱,2200桶还在卡车上。 在卡车上(12600-3200)÷600=小时,湿果运来的速度为12600÷12=1050桶/小时 积压情况:1050-600=450桶/小时,存储箱装满为3200÷450=小时装满 如图阴影面积即为卡车等待时间, 贮存能力线于升降曲线之间。 S阴影=(5400-3200)×()÷2=9416桶·小时 平均每辆卡车等待时间为 9416÷75=126小时。 4、过程处理的安排是否有问题 根据目前高峰期处理红酸果的工序从卸完货第一小时(上午8点)开始,到烘干工序完成
papi酱营销案例分析
Papi酱营销案例分析 2016年的一个月内,从获得千万投资、估值过亿,到一条贴片广告被卖出了2200万。papi酱,一个“集美貌与才华”的短视频内容创作者,为众人缔造了一出从无人知晓到全民热议的网红传奇。如今,这位被誉为“2016年第一网红”的女子,不仅是人气与话题的代名词,围绕她的还有资本市场的青睐,以及如潮水般涌来的争议。 不管你喜欢还是反感,这场被全民围观的喧嚣背后,是网红经济的彻底爆发——以papi酱和她所代表的网络内容生产者们,正以一往无前的气势走上了产业化之路。这背后既有网红们强大的变现能力,也展示出商业模式变革的来临。从个体创作到资本联姻,从一个papi酱到可容纳无数papi酱的papitube,资本主导下的内容创业时代或许已经正式到来。 仅仅半年时间,Papi酱就红了,红得发紫。 到了今天,如果还不知道Papi酱的话,那您可能是个60后。 要说网络炒作背后的秘密,我们从Papi酱这个案例可以找到一些答案。炒作不炒作?对于想火的人和事来说,已经是一个不言自明的问题。 是炒作还是运气?Papi酱怎么这样红? 29岁,已婚有老公,没有干爹,没有整容,没有大尺度照,这是Papi酱的标签。按常理来说,Papi酱是很难红起来的,但就是她在近段时间火遍了微博和朋友圈。 从Papi酱走红看网络炒作背后的秘密。
这是怎么一回事?是网络炒作做幕后推手,还是纯粹的运气好?据了解,Papi酱最近获得了1200万的投资,这里面涉及的大咖有真格基金的徐小平和罗辑思维的罗振宇,据说这两位各投资了500万! 罗辑思维不是一个微信公众号吗?怎么这么有钱?这是不是罗辑思维联手Papi酱进行网络炒作?他们之间有什么不可告人的秘密?有不少网友更是大呼:炒作! Papi酱到底是怎么红起来的? 首先,Papi酱让自己和竞争对手显得不一样,她借助变音器制造出快语速,以此和别人区别开来。正是因为在很短的时间里,Papi 酱为网友奉献了大量信息(包括视频里面的梗),这比较符合网友的口味。 从去年10月开始开通微信公众平台,到现在才半年时间,Papi 酱俘获了百万计的粉丝数,她的微博粉丝更是达到了让人瞠目结舌的800万人!想不想知道她是如何圈粉丝的?主要是靠“台湾腔×东北话”和“上海话×英语”两个系列视频。在网络上要想火起来,要么是貌若天仙,要么是逗逼到底、善于自黑和黑别人。 Papi酱之所以能红起来,主要原因是因为她善于自黑和黑别人,同时长得还不算差,这样下来的话,就容易制造矛盾冲突,视频也就有了看点。最为重要的是,Papi酱是中央戏剧学院毕业的,科班出身,这也能为她加分不少。 从Papi酱走红看网红炒作的秘密。 在网络炒作这个行业,业内人都清楚,那么有目的性的网络事件
运营管理-红酸果案例分析
山东师范大学 研究生学位课程作业答卷 姓名 学号 学科专业工商管理 科目运营管理 时间2013年5月29日 分数
红酸果案例作业 案例分析前,首先我们要将关键点和数据提取: 加工厂的情况 酸果都是采用分“干收法”和“湿收法”,去年,加工厂接收的酸果有58%是采用“湿收法”采收的,预计来年采用“湿收法”采收的浆果将达到70%。 红酸果是在9月初至12月采收的。高峰期从9月下旬开始,共持续约二十天。去年高峰期间(9月20日至10月9日),在这二十天里,平均每天送来的酸果的16,380桶。在采收季节其余的日子里,送来的果子就少多了。如表1所示,从9月1日至9月19日,送来的酸果为44,176桶,平均每天为2209桶,而从10月10日至12月10日,送来的酸果为238,413桶,平均每天为3845桶。根据果农的种植情况和历史数据分析,今年高峰期红酸果的数量将比去年多,每天将达到18000桶。每星期七天从早七点至晚七点,都有(种植者租用的)卡车陆陆续续开到加工厂。卡车的装载量从20至400桶不等,平均每辆卡车的装载量为75桶。卡车卸货时,先要倒到基瓦尼型倾倒机的平台上。然后这个平台倾斜,把酸果倒在通向加工厂贮存箱的快速运转带上。 卸一车酸果平均要用7.5分钟。加工厂共有五台基瓦尼型倾倒机,每台要有三名工人操作。每台倾倒机每小时可倾倒600桶酸果。第五台倾倒机是前一年花了200,000美元添加的。 酸果倾倒之后,通过传送装置被送到27个贮存箱中的一个。1号至16号贮存箱只存放干果,每个贮存箱可存放250桶。25号至27号贮存箱的贮存量为400桶,只存放湿果。其余的贮存箱(17号至24号)每个可以存放250桶,可用于存放干果,也可用于存放湿果。在高峰期时,如果需要处理的酸果以湿果为主,那么干湿兼用的贮存箱就用于存放湿果。在这种情况下,所具有的湿果贮存量可在达到3200桶(有三个可存放400桶的贮存箱,还有八个可存放250桶的贮存箱)。如果没有存放的地方,到达的卡车就得等待。 贮存箱和传送装置,是由一名工人在中央控制板上操纵着。打开贮存箱后,酸果就会落到通向各道工序的传送带上。采用“干收法”采收的酸果,先要经过一道工序以去除石子,而采用“湿收法”采收的酸果则无需经过这一道工序。现有三台去石子设备,每台设备每小时可以处理1500桶。采用“干收法”采收的浆果的第二道工序是去除叶茎和茎干。现有三台去叶茎设备,每台设备每小时可以处理1500桶。 湿收的酸果被从贮存箱送到三台去叶茎设备中的一台。去除叶茎之后,湿果被送到三台烘干机中的一台去烘干。每台烘干设备每小时可以处理200桶。接下来,酸果被分选为三级:即一级品、二级品和不合格品。分选工序所依据的原理是,好的酸果要比差的酸果弹得高。去掉叶茎的果子通过传送装置被送往三条大型分选线。分选设备每小时可以处理400桶。 在分选设备中,酸果从一个漏斗落到由斜面弹板组成的装置上,每块板都有一道门或隔栏。这种门栏有两个不同的高度。弹过高门栏的酸果为一级品;弹过低门栏的酸果为二级品;两道门栏都没有弹过的果子则为不合格品。不同的传送装置把一级酸果和二级酸果分别传送到装运区。酸果通过传送装置运送到装运区。在装运区,四个打包台和两个散装卡车装运台具有灵活而充足的装运能力。装进散装卡车的酸果被直接送到加工厂,袋装的果子被冷库存放。无论是哪种情况,它们最终都要被制作成果汁、果酱或冷冻水果。在收获季节(9月1日至12月15日),加工厂一周七天都开工。在大约二十天的高峰期,计划使用53人,而在其余的非高峰期时间里,只有27人上班。工人在每天前八个小时内拿固定的计时工资,加班则多加50%的工资。平均的工资水平是每小时12.50美元。按照高峰期工作计划和非高峰期工作计划,负责接收的工人每天都要从早上七点种工作到晚上七点钟。如表2所示。在非高峰期,其他的工人从下午三点钟开始上班,一直要工作到晚上11点钟。在高峰期,其他的工人被安排从上午11点一直工作到晚上11点。但是,工作时间超过晚上11点钟的情况是司空习惯的。在这种情况下,大约需要15名工作操纵贮存箱、通过整套系统来处理果子和进行散装。虽然干果可以在贮存箱内过夜,但湿果必须在下班前从贮存箱中倒出来。另外。还需要至少两个小时的时间打扫卫生和维护设备,因此该厂一天开工的时间从没有超过22个小时。虽然该厂有十五年工作的人员,但是大多数员工是根据季节雇用的外籍工人。由于缺勤,使得上班的工人只能延长工作时
红酸果案例
这个案例的执笔人是耶鲁管理学院的教授阿瑟·J·斯沃塞。它是以哈佛商学院的一个有关全国酸果合作社的案例为基础的。 红酸果! 此时的科德角正值隆冬季节,安?希金斯醒来时出了一身冷汗。她总是作这样的恶梦:卡车源源不断地开来,可是却无法将红酸果卸下来,因为贮存箱里早已装满了等待处理的果子。当工厂早晨那座旧钟的指针向午夜时,被处理的酸果还在分选机上跳着,月光照在工人们的脸上,泛起了奇异的红光。他们已经很疲劳了,但一想到能拿加班费,心里就美滋滋的,也就不觉得累了。 两个月之前,安·希金斯到马萨诸塞州普里茅斯的“红酸果之角”加工厂就任负责生产的副总裁。她当时辞去了康涅狄格州一个保健机构经理的职务,一心想摆脱管理工作带来的压力,到马萨诸塞州的海边享受清静的生活。可是,她没有想到在酸果加工厂会遇到难题,她明白在采取改进措施之前自己还将度过许多不眠之夜。 加工厂的情况 “红酸果之角”加工厂是当地数百个种植者合办的一个加工厂。过去,酸果都是采用“干收法”采收的,即用手从树上采摘下来。近几年,“湿收法”已成为主要采收方法。这是一种机械化程度较高的方法。人们用水冲酸果蔓,酸果就会从树上掉下来,这样一来就容易收集了,因为酸果都漂浮在水面上。去年,加工厂接收的酸果有58%是采用“湿收法”采收的,预计来年采用“湿收法”采收的浆果将达到70%。 红酸果是在9月初至12月采收的。高峰期从9月下旬开始,共持续约二十天。表1显示的是去年高峰期间(9月20日至10月9日)每天送到加工厂的酸果总数和湿果所占比例。在这二十天里,平均每天送来的酸果的16,380桶。在采收季节其余的日子里,送来的果子就少多了。如表1所示,从9月1日至9月19日,送来的酸果为44,176桶,平均每天为2209桶,而从10月10日至12月10日,送来的酸果为238,413桶,平均每天为3845桶。 酸果用卡车运到之后,要在专用的传送装置经过几道工序的处理,去除石子和叶茎,烘干湿果,接着把果子分成三级:即一级品、二级品和不合格。然后再把它们包装起来,运送到生产厂,加工厂冻浆果、果汁或果酱。 接收与临时贮存 每星期七天从早七点至晚七点,都有(种植者租用的)卡车陆陆续续开到加工厂。卡车的装载量从20至400桶不等,平均每辆卡车的装载量为75桶。卡车卸货时,先要倒到基瓦尼型倾倒机的平台上。然后这个平台倾斜,把酸果倒在通向加工厂贮存箱的快速运转带上。 卸一车酸果平均要用7.5分钟。加工厂共有五台基瓦尼型倾倒机,每台要有三名工人操作。第五台倾倒机是前一年花了200,000美元添加的。 酸果倾倒之后,通过传送装置被送到27个贮存箱中的一个。1号至16号贮存箱只
第十二讲 排队问题
第十二讲排队问题 第一节排队问题基础 一、排队问题的基本概念 顾客:有服务需求的实体(人、设备)。 服务台:向顾客提供服务的实体(人、设备)。 排队系统:顾客需要等待才能够获得服务的系统或场所。 队列中的顾客数:等待服务的顾客数。 系统中的顾客数:等待服务和接受服务的顾客总数。 队列中的等待时间: 系统中的等待时间: 顾客到达率:单位时间进入系统的顾客数。 服务台服务率:单位时间一个服务台提供的服务次数。 有效因子:顾客到达率与系统服务率之比。 平稳条件:排队系统在运行了一段时间后达到的稳定状态(有效因子稳定在一个小于1的固定值)。 顾客到达时间间隔的分布:相继两位顾客到达系统的时间间隔是一个随机变量,所以服从某 种分布。现实生活中最常见的顾客到达时间间隔分布为指数分 布。 服务时间分布:一个服务台对一位顾客提供一次服务时间的长短也是随机变量,它也服从某种分布,如指数分布、退化分布、爱尔朗分布等。 二、排队模型的符号表示及模型假设 排队模型一般表示为 M/M/1 表示顾客到达时间间隔服从指数分布、服务时间服从指数分布、只有一个服务台的排队系统(模型)。
M/M/s 表示顾客到达时间间隔服从指数分布、服务时间服从指数分布、有s个服务台的排队系统(模型)。M/M/s中,顾客到达时间间隔的均值与标准差大致相等、服务时间的均值与标准差大致相等。 M/D/s 表示顾客到达时间间隔服从指数分布、服务时间固定、有s个服务台的排队系统(模型)。 M/G/s 表示顾客到达时间间隔服从指数分布、服务时间任意(但有确定的均值与标准差)、有s个服务台的排队系统(模型)。 关于排队模型的基本假定: 1.到达时间间隔是独立的,服从某种特定的分布。 2.所有到达的顾客都进入系统并等待和接受服务直至服务结束。 3.排队系统可以有无限长的排队队列。 4.顾客服务优先规则是先到先服务。 5.排队系统有一定数量的服务台,每个服务台一次只为一位顾客提供服务。 6.一位顾客只能由一个服务台提供服务。 7.服务时间是独立的,服从某种特定的分布。 三、排队系统举例 四、排队系统的绩效测度 排队队列长 系统内顾客数 顾客等候服务的平均等待时间 顾客在系统内的平均等待时间 顾客需要等待的概率 第二节案例研究(杜皮特公司问题) 杜皮特公司主要生产现代办公用品,明星产品是彩色打印—复印机。